加氢催化剂硫化方案
T202C(二甲基二硫)硫化方案

T202C有机硫加氢催化剂硫化方案T202C有机硫加氢催化剂硫化就是利用焦炉气中高浓度H2S或低浓度焦炉气加二甲基二硫,将催化剂的金属组分由氧化态转化成相应的硫化态的过程。
硫化的关键是要避免金属氧化态在与H2S反应转化成硫化态之前被热氢还原。
所以,催化剂硫化时,必须控制好温度与循环气中H2S含量,在H2S未穿透催化剂床层前,床层最高点温度不应超过230℃。
一、利用低硫煤气加二甲基二硫硫化方案1、硫化条件:气源:焦炉气硫化空速:一般控制在300~400h-1,2、升温硫化流程及曲线(1)流程:焦炉气——压缩机——升温炉——2台预加氢反应器并联——一级加氢反应器——放空(2)升温硫化及放硫曲线:见表1二、硫化说明及注意事项1、系统用氮气(氮气纯度>99.9%)置换合格后(主要指氧含量小于0.5%),点燃升温炉,根据升温曲线调节燃气量,一般控制升温炉出口温度不大于床层温度50℃,床层到200℃并拉平后,引入低硫煤气(经湿脱),并配入二甲基二硫,控制床层最高温度≤400℃。
用煤气升温也可以,只是对催化剂有一定影响。
2、铁钼反应器床层到200℃,开始有硫化反应,为了加速硫化,系统压力可逐渐提到1.0Mpa,另外开始滴加二甲基二硫。
(每吨催化剂约需二甲基二硫65Kg),3、硫化时注意提温不提氢,提氢不提温原则。
4、硫化初期,二甲基二硫配入后分析入口H2S≤10g/Nm3,硫化主期,逐步增加二甲基二硫加入量,使入口H2S达到10-20g/Nm3。
5、370℃时开始有放硫反应,为了加速放硫,在370℃恒温后,压力逐步降到0.1-0.2Mpa并停止加二甲基二硫。
6、硫化及放硫期间,每小时分析一次铁钼反应器进出口H2S和H2含量,当进出口H2S和H2含量基本相等时硫化结束,当出口H2S≤300mg/Nm3时,放硫结束。
7、硫化结束后将压力提到0.8Mpa、关闭进出口阀,使铁钼反应器保温、保压。
8、床层在120度以前主要是脱催化剂吸附水的过程,故应每半小时开导淋一次放水。
T202有机硫加氢催化剂硫化方案
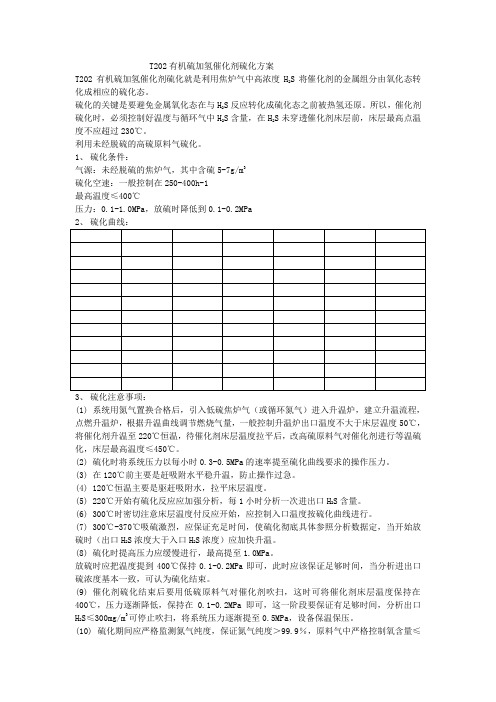
T202有机硫加氢催化剂硫化方案T202有机硫加氢催化剂硫化就是利用焦炉气中高浓度H2S将催化剂的金属组分由氧化态转化成相应的硫化态。
硫化的关键是要避免金属氧化态在与H2S反应转化成硫化态之前被热氢还原。
所以,催化剂硫化时,必须控制好温度与循环气中H2S含量,在H2S未穿透催化剂床层前,床层最高点温度不应超过230℃。
利用未经脱硫的高硫原料气硫化。
1、硫化条件:气源:未经脱硫的焦炉气,其中含硫5-7g/m3硫化空速:一般控制在250-400h-1最高温度≤400℃压力:0.1-1.0MPa,放硫时降低到0.1-0.2MPa(1)系统用氮气置换合格后,引入低硫焦炉气(或循环氮气)进入升温炉,建立升温流程,点燃升温炉,根据升温曲线调节燃烧气量,一般控制升温炉出口温度不大于床层温度50℃,将催化剂升温至220℃恒温,待催化剂床层温度拉平后,改高硫原料气对催化剂进行等温硫化,床层最高温度≤450℃。
(2)硫化时将系统压力以每小时0.3-0.5MPa的速率提至硫化曲线要求的操作压力。
(3)在120℃前主要是赶吸附水平稳升温,防止操作过急。
(4)120℃恒温主要是驱赶吸附水,拉平床层温度。
(5)220℃开始有硫化反应应加强分析,每1小时分析一次进出口H2S含量。
(6)300℃时密切注意床层温度付反应开始,应控制入口温度按硫化曲线进行。
(7)300℃-370℃吸硫激烈,应保证充足时间,使硫化彻底具体参照分析数据定,当开始放硫时(出口H2S浓度大于入口H2S浓度)应加快升温。
(8)硫化时提高压力应缓慢进行,最高提至1.0MPa。
放硫时应把温度提到400℃保持0.1-0.2MPa即可,此时应该保证足够时间,当分析进出口硫浓度基本一致,可认为硫化结束。
(9)催化剂硫化结束后要用低硫原料气对催化剂吹扫,这时可将催化剂床层温度保持在400℃,压力逐渐降低,保持在0.1-0.2MPa即可,这一阶段要保证有足够时间,分析出口H2S≤300mg/m3可停止吹扫,将系统压力逐渐提至0.5MPa,设备保温保压。
加氢催化剂预硫化-16页文档资料

—生产四部培训小组
预硫化的目的
催化剂的加氢脱硫活性主要是在它的硫化状态下,而催化 剂的主要成分是钴、钼的氧化态,所以开工时必须对其预 硫化 即:
9CoO+8H2S → Co9S8+9H2O MoO3+2H2S+H2 → MoS2+3H2O
催化剂预硫化的主要方法
预硫化技术是加氢催化剂开发应用的关键步骤之一,使加 氢催化剂保持最佳的活性和稳定性,提高选择性,延长使 用寿命,在国内外受到广泛的关注。因此,深人研究加氢 催化剂的预硫化方法对开发高活性的催化剂有重要意义。 目前,工业上使用的加氢催化剂常用的硫化方法有很多种 .从介质相态上可分为干法硫化和湿法硫化两类,从介质 来源上可分为强化硫化和非强化硫化两种情况.从预硫化 的位置又可分为器内预硫化和器外预硫化
[ I ] - TIC-06089和FIC-06045串级控制 [ I ] - 缓慢调节TIC-06089, [ I ] - 按升温曲线升温(速率不大于20℃/小时) ( P ) - 确认E-0613开始产生蒸汽,将蒸汽排空几小时至合格 [ P ] 一 缓慢关闭放空阀逐渐提高蒸汽压力 ( I ) - 确认PI-06057稍高于PI-06029压力 [ I ] - 缓慢打开E-0613至PV-06029的手阀, [ I ] - 调整发汽并内部低低压蒸汽管网 [ I ] - PIC-06029A自动操作 [ I ] - 设定SV=0.55MPa [ P ] 一 完全关闭放空阀 [ P ] 一 启动加药设施(见加药计量泵操作), [ P ] 一 废锅连续加药 [ P ] 一 连续排污投用 ( I ) - 确认TIC-06089升温至200℃
加氢反应器R-0603催化剂预硫化
1、 预硫化前准备 2、 引氢气进反应器 3、 引再生酸性气进反应器 4、 加氢催化剂预硫化
2#加氢裂化催化剂湿法硫化

2#加氢裂化催化剂湿法硫化摘要加氢裂化催化剂的预硫化。
钨、镍、钼等金属作为反应器中保护剂和催化剂的活性金属组份,他们多是以氧化态形式存在的。
在反应器内氧化态的钨、镍、钼等金属组份难以发挥其应有的活性,硫化态时金属组份才能发挥其应有的活性。
把活性金属由氧化态转化为硫化态正是催化剂硫化的最终目的。
二硫化碳、二甲基二硫等都可以作为硫化剂。
预硫化的条件决定预硫化的效果,硫化温度一般在280~300℃左右。
经过硫化后的催化剂活性很高,为使装置操作平稳,需对催化剂进行钝化。
催化剂钝化的主要目的是抑制加氢裂化催化剂的初活性。
常用的钝化剂为无水液氨。
无水液氨的注入位置既可在精制反应器R101入口,也可在裂化反应器R102入口,但以在裂化反应器入口注入为最佳。
[1]关键词:加氢裂化;催化剂;湿法硫化技术中国石油化工股份有限公司天津分公司180万吨/年加氢裂化装置于2009年10月一次开车成功。
2020年2#加氢裂化在检修期间对上周期使用的FF-66和FC-52/FC-80催化剂进行了器外再生后回填使用。
其中精制段补充了部分FF-66新剂,裂化段使用了FC-76加氢裂化催化剂作为补充,后精制全部装填新鲜FDS-4催化剂。
催化剂装填于2020年6月7日开始至6月17日结束,共计装填FF-66(新剂)55.00吨;FTX(新剂)1.94吨;FC-76(新剂)39.00吨;FDS-4(新剂)19.72吨;FBN-03B04保护剂7.91吨;FBN-03B05保护剂5.50吨;FBN-03B06保护剂2.20吨。
为了确保装置一次开车成功,要求反应原料、反应系统气密、催化剂硫化、催化剂钝化、换进原料油等主要步骤必须严格按规定执行。
1 催化剂正常使用条件及有关注意事项1.1 原料油与新氢原料油的馏程、残炭、氮含量、硫含量和金属杂质等会直接影响催化剂的反应性能和寿命。
原料油质量很差时,容易氧化生成胶质,并在催化剂上结焦积碳,催化剂床层压降上升过快,进而导致装置计划外停工,同时还会影响催化剂寿命。
加氢催化剂的预硫化及其影响因素
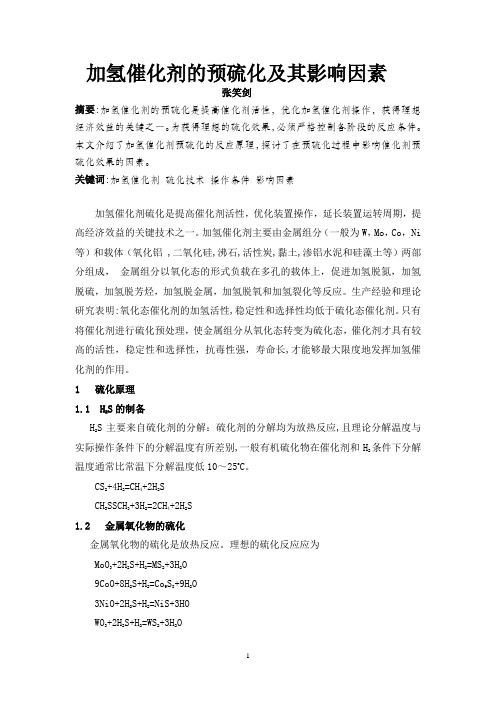
加氢催化剂的预硫化及其影响因素张笑剑摘要:加氢催化剂的预硫化是提高催化剂活性,优化加氢催化剂操作,获得理想经济效益的关键之一。
为获得理想的硫化效果,必须严格控制各阶段的反应条件。
本文介绍了加氢催化剂预硫化的反应原理,探讨了在预硫化过程中影响催化剂预硫化效果的因素。
关键词:加氢催化剂硫化技术操作条件影响因素加氢催化剂硫化是提高催化剂活性,优化装置操作,延长装置运转周期,提高经济效益的关键技术之一。
加氢催化剂主要由金属组分(一般为W,Mo,Co,,Ni 等)和载体(氧化铝 ,二氧化硅,沸石,活性炭,黏土,渗铝水泥和硅藻土等)两部分组成,金属组分以氧化态的形式负载在多孔的载体上,促进加氢脱氮,加氢脱硫,加氢脱芳烃,加氢脱金属,加氢脱氧和加氢裂化等反应。
生产经验和理论研究表明:氧化态催化剂的加氢活性,稳定性和选择性均低于硫化态催化剂。
只有将催化剂进行硫化预处理,使金属组分从氧化态转变为硫化态,催化剂才具有较高的活性,稳定性和选择性,抗毒性强,寿命长,才能够最大限度地发挥加氢催化剂的作用。
1硫化原理1.1 H2S的制备H2S主要来自硫化剂的分解:硫化剂的分解均为放热反应,且理论分解温度与实际操作条件下的分解温度有所差别,一般有机硫化物在催化剂和H2条件下分解温度通常比常温下分解温度低10~25o C。
CS2+4H2=CH4+2H2SCH3SSCH3+3H2=2CH4+2H2S1.2金属氧化物的硫化金属氧化物的硫化是放热反应。
理想的硫化反应应为MoO3+2H2S+H2=MS2+3H2O9CoO+8H2S+H2=Co9S8+9H2O3NiO+2H2S+H2=NiS+3HOWO3+2H2S+H2=WS2+3H2O在H2和H2S存在下,金属氧化物存在还原和硫化的竞争。
硫化效果直接影响到催化剂的使用性能。
影响催化剂硫化效果的因素有催化剂的载体性质、负载的金属种类、硫化方法、硫化温度、硫化时间、硫化压力、硫化剂的浓度和种类等。
加氢催化剂预硫化方案

1. 引言加氢催化剂是广泛应用于石化工业领域的关键催化剂之一。
为了提高加氢催化剂的活性和稳定性,预硫化技术被广泛应用。
本文将从预硫化的原理、影响因素以及常见的预硫化方案等方面进行探讨。
2. 预硫化的原理预硫化是指在加氢催化剂使用之前,使用硫化物溶液进行处理,使其表面形成一层硫化物膜。
这一膜可以防止催化剂表面被氧化物或其他不活性物质占据,从而提高催化剂的活性和稳定性。
预硫化的原理可以归结为两个方面:•活性金属硫化物的形成:活性金属如镍、钼等能够与硫化物反应形成硫化物,这种硫化物能够促进加氢反应的进行,提高催化剂的反应活性。
•表面硫化膜的形成:硫化物膜可以阻隔外界氧气和不活性物质的侵蚀,减少催化剂的表面被氧化的机会,提高催化剂的稳定性。
3. 预硫化的影响因素预硫化的效果受到多种因素的影响,下面列举了一些主要的影响因素:3.1 硫化剂的选择预硫化过程中使用的硫化剂对催化剂的性能起着至关重要的作用。
常用的硫化剂包括硫化氢(H2S)、二硫化碳(CS2)等。
不同的硫化剂在反应中会产生不同的硫化物,并对催化剂表面的化学状态产生影响。
3.2 预硫化温度和时间预硫化温度和时间是影响预硫化效果的关键因素。
一般来说,高温和长时间的预硫化会使硫化剂更充分地与催化剂发生反应,生成更完善的硫化物膜。
然而,过高的温度可能会导致催化剂的部分活性成分被分解或损失,因此需要根据具体情况选择合适的预硫化温度和时间。
3.3 氛围条件预硫化过程中的气氛条件也会对催化剂的预硫化效果产生影响。
一般情况下,加氢环境中的氢气浓度越高,硫化剂与催化剂的反应速度越快,硫化物膜形成的效果也越好。
4. 常见的预硫化方案4.1 H2S气体预硫化H2S气体预硫化是一种常用的预硫化方式。
预硫化过程中,将催化剂放入加热炉中,通入含有H2S气体的加硫气体。
通过控制炉内温度和气氛浓度,使硫化剂与催化剂表面反应生成硫化物。
4.2 溶液浸泡预硫化溶液浸泡预硫化是另一种常见的预硫化方式。
加氢催化剂硫化方案

制氢装置催化剂硫化方案硫化前准备:1、催化剂已按填装方案填装完毕2、压缩机已试机完成,达到开机条件,所有仪表已联校完成3、制氢系统已用氮气置换合格(O2<0.5%)、气密完成4、准备好硫化剂(DMDS)并注入至硫化剂罐,硫化剂线已试压、吹扫干净(用蒸汽、风彻底吹扫干净)5、准备好硫化用工具:硫化氢检测管、计量水器具、画好升温曲线、记录纸、对讲机消防器具等6、干气、氮气、循环水等已准备就绪LYT-701/LYT-702加氢催化剂硫化1、硫化机理LYT—701/702加氢催化剂活性组份氧化钴、氧化镍、三氧化钼在使用前需将其转化为硫化物才具有活性,这一过程为硫化,其机理为:DMDS(或CS2)+4H2=2H2S+CH4MoO3+2H2S+H2=MoS2+3H2OCoO+H2S=CoS+H2ONi0+ H2S=NiS+H2O硫化时,用干N2-H2(H2≥10%,O2<0.5%)作为硫化原料气,配以适量的CS2或者DMDS,经加热达到一定温度后进入催化剂床层,通常采用循环硫化或一次放空硫化方法。
2、硫化过程1、反应系统气密合格,建立氢气-氮气循环后,进行催化剂硫化。
硫化条件:氢压,MPa ≦0.5MPa循环介质,% N2-H2混合气氢气含量,%(v/v) 30-50空速,h-1 200-500第一个恒温硫化阶段床层温度和时间 230℃恒温6小时第二个恒温硫化阶段床层温度和时间 300℃恒温4-6小时第三个恒温硫化阶段床层温度和时间 350℃恒温4小时硫化剂二甲基二硫或二硫化碳理论需硫量,m %(对催化剂) 约8.0吸硫量计算公式为:⎥⎦⎤⎢⎣⎡⨯+⨯⨯+⨯⨯=C B A c s M C M B M A w w 06.329/806.32306.32s w :理论吸硫量c w :催化剂装量A:MoO 3的百分含量;A M :MoO 3的分子量,143.94B :CoO 的百分含量B M :CoO 的分子量,74.93C:NiO 的百分含量C M :NiO 的分子量,74.70理论生成水重量为:DMDS (或CS 2)注入量计算式:(催化剂量)×8%×94(DMDS 分子量或CS 2)/64(硫分子量)=硫注入量 硫注入量×1.1(10%的余量)=实际硫注入量0.452 吨 气体含硫量计算式:X (气体循环量Nm3)/22.4×0.5%(硫含量)×94(DMDS 分子量或CS2)/64(硫分子量)=X’ Kg 二甲基二硫性质:分子式:CH3SSCH3 分子量:94.20 CAS :624-92-0 淡黄色透明液体。
加氢裂化催化剂预硫化操作规程

加氢裂化催化剂预硫化操作规程一、催化剂预硫化的目的加氢裂化催化剂的活性金属组分主要是Mo、Ni、Co和W,同其它新催化剂或再生后的催化剂一样,其所含的活性金属组分(Mo、Ni、Co、W)都是以氧化态的形式存在。
大量的研究和工业实践证明,催化剂经过硫化,活性金属组分由氧化态转化为硫化态,具有良好的加氢活性和热稳定性。
因此,在加氢催化剂接触原料油汽之前,先进行预硫化,将催化剂活性金属组分由氧化态转化为硫化态。
本装置使用的FZC系列保护剂为Mo-Ni系活性金属氧化物,FF-20精制催化剂活性金属为W-Mo-Ni系金属氧化物,FC-14裂化催化剂的活性金属为W-Ni系金属氧化物,予硫化能使MoO3、WO3和NiO转变为具有较高活性的MoS2、WS2和Ni3S2金属硫化物。
催化剂硫化一般分为湿法硫化和干法硫化两种,湿化硫化为在氢气存在下,采用硫化物或馏分油在液相或半液相状态下的预硫化;干法硫化为在氢气存在下,直接用含有一定浓度的H2S或直接向循环氢中注入有机硫化物进行的预硫化。
湿法硫化分为两种:一种为催化剂硫化过程所需要的硫油外部加入的硫化物而来,一种为依靠硫化油自身的硫进行预硫化。
本装置预硫化工艺为干法气相硫化。
使用二甲基二硫化物C2H6S2(DMDS)作为硫化剂。
二、催化剂预硫化的原理催化剂预硫化是基于硫化剂(DMDS)临氢分解生成硫化氢(H2S),H2S与催化剂活性金属氧化态反应转化成相应金属硫化态的反应。
其相关的硫化反应如下:(CH3)2S2+3H2→ 2H2S+2CH4MoO3 + 2H2S + H2→ MoS2 + 3H2O3NiO + 2H2S + H2→ Ni3S2 + 3H2OWO3 + 2H2S + H2→ WS2 + 3H2O三、具备条件(1)经过气密检验和紧急泄压试验,确认系统严密性和联锁系统性能安全可靠。
(2)供氢系统确保稳定可靠,1401-K-101及1401-K-102运转正常。
加氢催化剂预硫化

状态确认
o o o o o ( M ) - 加氢反应器250-320℃恒温 ( M ) - 急冷塔出口气体中氢气浓度稳定在1.5-5% ( I ) - 急冷塔液位LIC-06033稳定为40-60 ( I ) - E-0613的液位LIC-06030稳定为40-60 ( I ) - 预硫化的主要方法
干法硫化是指催化剂在氢气存在下,直接与一定浓度的 硫化氢或其他有机硫化物接触而进行的气相硫化。湿法硫 化是指含有硫化物的硫化油在氢气存在下直接与催化剂进 行的硫化过程。湿法硫化可以防止催化剂床层中“干区” 的存在,防止活性金属氧化物被氢气还原。并且避免水分 对催化剂的影响。但是与干法硫化相比,湿法硫化容易造 成催化剂积炭,反应放热比较剧烈,不易控制温升。因此 有研究在低温区使用干法,在高温区使用干法+湿法技术。
加氢催化剂预硫化
o o o o o o o o o o o o o o o o o o o o o o [ I ] - 调节加氢反应器的入口温度,TIC-06089为200℃ ( I ) - 观察加氢反应器的温升,直到反应不再剧烈 [ P ] 一 联系化验室,采样化验反应器入口和出口再生酸性气的含量 ( I ) - 确认入口和出口再生酸性气的含量基本相同,H2S的浓度为2% [ P ] 一 保持入口气体中H2S的浓度为2% [ I ] - 保持急冷塔出口气体中氢气浓度稳定在2.5% [ I ] - 以不大于25℃/小时的速率提高入口温度 ( I ) - 观察当某个温度梯度开始形成时,停止升温 ( I ) - 确认该温度梯度通过整个催化剂床层 [ I ] - 继续提高入口温度,直到TIC-06089为338℃ ( I ) - 确认该温度梯度通过整个催化剂床层 [ P ] 一 联系化验室,采样化验反应器入口和出口再生酸性气的含量 ( I ) - 确认入口和出口再生酸性气的含量基本相同,继续预硫化4小时 [ P ] 一 降低入口气体中H2S流量,保证入口气体中H2S的浓度不大于2% [ I ] - 将反应器的入口温度降到290℃ [ P ] 一 关闭D-1001出口去预硫化再生酸性气的阀门 [ P ] 一 打开氮气吹扫阀进行吹扫 [ P ] 一 5分钟后,关闭预硫化再生酸性气到主线的阀门 [ P ] 一 关闭预硫化再生酸性气FI-06044的后手阀 [ P ] 一 关闭氮气吹扫阀 ( I ) - 确认急冷塔出口气体中氢气浓度稳定在2.5% ( I ) - 确认反应器的入口温度为290℃
石油加氢处理—加氢处理催化剂的预硫化和再生
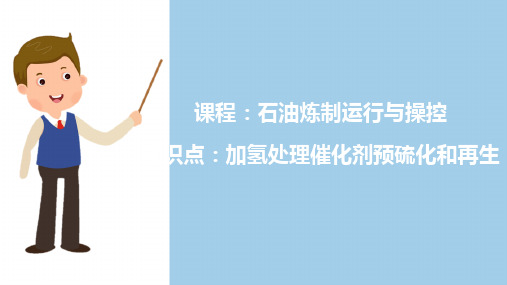
一、加氢处理催化剂预硫化
温度对硫化过程影响最大
✓ 温度升高,硫化速度增加 ✓ 工业上,预硫化温度一般在230~300 oC之间,温度过高对催化剂活性不利
硫化剂:H2S或能在硫化条件下分解成H2S的不稳定硫化物(CS2、CH3SSCH3) 预硫化过程按介质相态分:湿法硫化和干法硫化
✓ 湿法硫化:将CS2溶于石油馏分,形成硫化油,进反应器进行硫化,CS2的浓度1~2% ✓ 干法硫化:将CS2直接注入反应器入口处与H2混合后进入催化剂床层进行硫化
NiS + Ni3S2 + 4H2O Co9S8 + 9H2O WS2 + 3H2O MoS2 + MoS3 + 6H2O
预硫化是提高加氢 处理催化剂活性和 稳定性的重要步骤
预硫化反应是强放热反应,且反应速度快
预硫化的关键问题:避免催化剂床层飞温”;避免催化剂中活性金属氧化物
在与硫化氢反应前被热氢还原,降低催化剂的活性
课程:石油炼制运行与操控 知识点:加氢处理催化剂预硫化和再生
一、加氢处理催化剂预硫化
预硫化
H2S 活性金属的氧化物形态
活性金属的硫化物形态
(加氢活性较低)
(加氢活性较高)
4NiO + 3H2S + H2 9CoO + 8H2S + H2 WO3 + 2H2S + H2 2MoO3 + 5H2S + H2
预硫化过程按预硫化的位置分:器内预硫化和器外预硫化
✓ 器内预硫化:在反应器内将氧化态催化剂转化成硫化态 ✓ 器外预硫化:在催化剂制造过程中将氧化态催化剂预先制成半预硫化或硫化态催化剂
二、加氢处理催化剂再生
加氢处理催化剂的失活
有机硫加氢(HDS)催化剂的预硫化
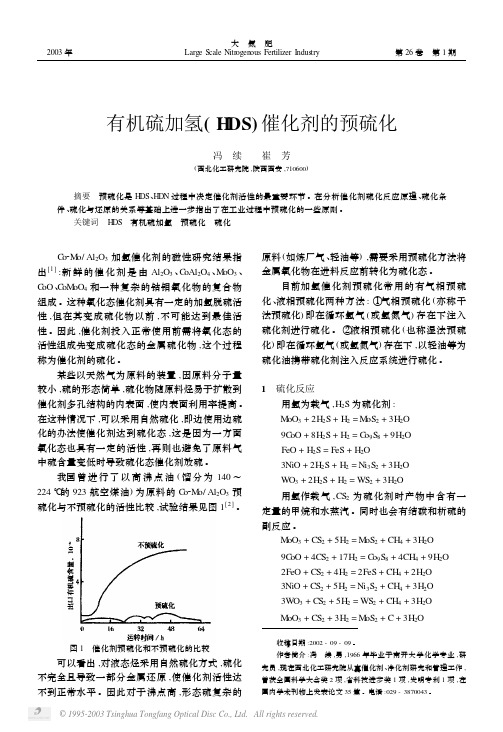
有机硫加氢(H DS)催化剂的预硫化冯 续 崔 芳(西北化工研究院,陕西西安,710600) 摘要 预硫化是H DS 、H DN 过程中决定催化剂活性的最重要环节。
在分析催化剂硫化反应原理、硫化条件、硫化与还原的关系等基础上进一步指出了在工业过程中预硫化的一些原则。
关键词 H DS 有机硫加氢 预硫化 硫化收稿日期:2002-09-09。
作者简介:冯 续,男,1966年毕业于南开大学化学专业,研究员,现在西北化工研究院从事催化剂、净化剂研究和管理工作,曾获全国科学大会奖2项,省科技进步奖1项,发明专利1项,在国内学术刊物上发表论文35篇。
电话:029-*******。
C o 2M o/Al 2O 3加氢催化剂的磁性研究结果指出[1]:新鲜的催化剂是由Al 2O 3、C oAl 2O 4、M oO 3、C oO 、C oM oO 4和一种复杂的钴钼氧化物的复合物组成。
这种氧化态催化剂具有一定的加氢脱硫活性,但在其变成硫化物以前,不可能达到最佳活性。
因此,催化剂投入正常使用前需将氧化态的活性组成先变成硫化态的金属硫化物,这个过程称为催化剂的硫化。
某些以天然气为原料的装置,因原料分子量较小,硫的形态简单,硫化物随原料烃易于扩散到催化剂多孔结构的内表面,使内表面利用率提高。
在这种情况下,可以采用自然硫化,即边使用边硫化的办法使催化剂达到硫化态,这是因为一方面氧化态也具有一定的活性,再则也避免了原料气中硫含量变低时导致硫化态催化剂放硫。
我国曾进行了以高沸点油(馏分为140~224℃的923航空煤油)为原料的C o 2M o/Al 2O 3预硫化与不预硫化的活性比较,试验结果见图1[2]。
图1 催化剂预硫化和不预硫化的比较可以看出,对液态烃采用自然硫化方式,硫化不完全且导致一部分金属还原,使催化剂活性达不到正常水平。
因此对于沸点高,形态硫复杂的原料(如炼厂气、轻油等),需要采用预硫化方法将金属氧化物在进料反应前转化为硫化态。
一种硫化型加氢裂化催化剂的钝化方法
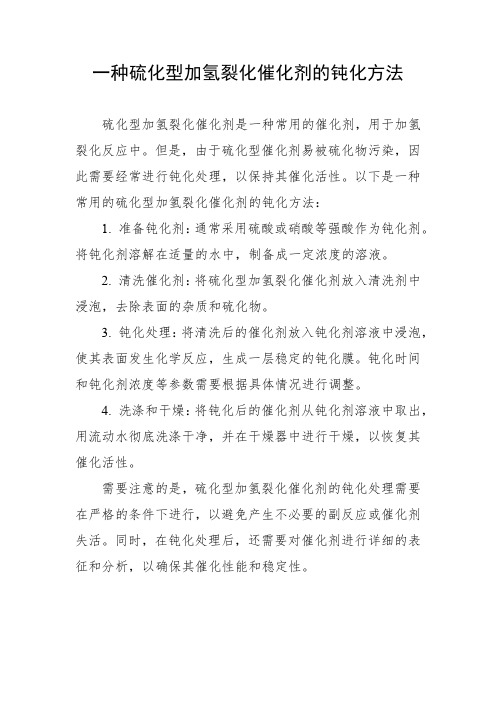
一种硫化型加氢裂化催化剂的钝化方法
硫化型加氢裂化催化剂是一种常用的催化剂,用于加氢裂化反应中。
但是,由于硫化型催化剂易被硫化物污染,因此需要经常进行钝化处理,以保持其催化活性。
以下是一种常用的硫化型加氢裂化催化剂的钝化方法:
1. 准备钝化剂:通常采用硫酸或硝酸等强酸作为钝化剂。
将钝化剂溶解在适量的水中,制备成一定浓度的溶液。
2. 清洗催化剂:将硫化型加氢裂化催化剂放入清洗剂中浸泡,去除表面的杂质和硫化物。
3. 钝化处理:将清洗后的催化剂放入钝化剂溶液中浸泡,使其表面发生化学反应,生成一层稳定的钝化膜。
钝化时间和钝化剂浓度等参数需要根据具体情况进行调整。
4. 洗涤和干燥:将钝化后的催化剂从钝化剂溶液中取出,用流动水彻底洗涤干净,并在干燥器中进行干燥,以恢复其催化活性。
需要注意的是,硫化型加氢裂化催化剂的钝化处理需要在严格的条件下进行,以避免产生不必要的副反应或催化剂失活。
同时,在钝化处理后,还需要对催化剂进行详细的表征和分析,以确保其催化性能和稳定性。
加氢催化剂预硫化技术

加氢催化剂预硫化技术化工学院化学工程颜志祥202215081421随着原油重质化、劣质化的日趋严重,以及环保和市场对石油产品质量要求的日益提高,加氢过程成为炼油工业中非常重要的环节。
它对于合理利用石油资源,改善产品质量,提高轻质油收率,深度脱除油品中的硫、氮、氧杂原子及金属杂质,以及烯烃饱和、芳烃加氢、提高油品安定性等都具有重要意义。
工业上常用的加氢催化剂大多数采用Mo,Co,Ni,W等金属元素作活性组分,并以氧化态分散在多孔的载体上。
这种形态的催化剂加氢活性低,稳定性差,催化剂以这种形态投人使用,那么在几周内催化剂就会失活到运转末期的状态。
将催化剂进行预硫化处理,使金属氧化物转化为金属硫化物,才能表现出较高的加氢活性,较好的稳定性,较佳的选择性和抗毒性,延长使用寿命。
且催化剂的硫化度越高,其活性越大。
因此,加氢催化剂在使用前必须进行预硫化。
一、催化剂预硫化的方法及原理1.1预硫化方法干法硫化是指催化剂在氢气存在下,直接与一定浓度的硫化氢或其他有机硫化物接触而进行的气相硫化。
湿法硫化是指含有硫化物的硫化油在氢气存在下直接与催化剂进行的硫化过程。
湿法硫化可以防止催化剂床层中“干区”的存在,防止活性金属氧化物被氢气还原。
并且避免水分对催化剂的影响。
但是与干法硫化相比,湿法硫化容易造成催化剂积炭,反应放热比较剧烈,不易控制温升。
因此有研究在低温区使用干法,在高温区使用湿法的干法+湿法技术。
1.1.2强化硫化与非强化硫化-1-若在国内外从介和非强两种工艺。
强化硫化是采用外部加入的硫化物进行预硫化(例如加入二硫化碳、二甲基二硫等),非强化硫化是依靠硫化油中自身的硫化物完成的预硫化。
尽管非强化硫化可以节省硫化剂及硫化剂注入系统,但是依靠硫化油中自身的硫进行硫化,硫化过程时间较长,硫化后催化剂活性、稳定性较差,硫化过程容易造成催化剂积炭。
1.1.3器内预硫化器内预硫化是指将氧化态的催化剂装人反应器中,在一定的温度下同时通人氢气和硫化剂或氢气和含硫化剂的馏分油进行硫化,使加氢活性金属转化为硫化态。
器内预硫化之湿法硫化和干法硫化
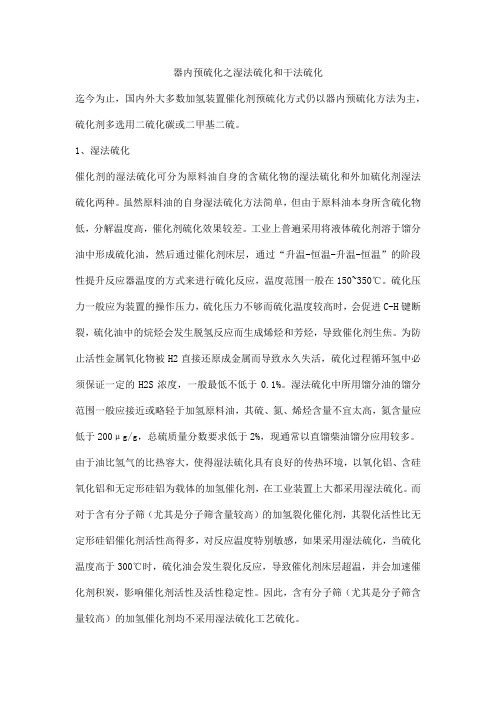
器内预硫化之湿法硫化和干法硫化迄今为止,国内外大多数加氢装置催化剂预硫化方式仍以器内预硫化方法为主,硫化剂多选用二硫化碳或二甲基二硫。
1、湿法硫化催化剂的湿法硫化可分为原料油自身的含硫化物的湿法硫化和外加硫化剂湿法硫化两种。
虽然原料油的自身湿法硫化方法简单,但由于原料油本身所含硫化物低,分解温度高,催化剂硫化效果较差。
工业上普遍采用将液体硫化剂溶于馏分油中形成硫化油,然后通过催化剂床层,通过“升温-恒温-升温-恒温”的阶段性提升反应器温度的方式来进行硫化反应,温度范围一般在150~350℃。
硫化压力一般应为装置的操作压力,硫化压力不够而硫化温度较高时,会促进C-H键断裂,硫化油中的烷烃会发生脱氢反应而生成烯烃和芳烃,导致催化剂生焦。
为防止活性金属氧化物被H2直接还原成金属而导致永久失活,硫化过程循环氢中必须保证一定的H2S浓度,一般最低不低于0.1%。
湿法硫化中所用馏分油的馏分范围一般应接近或略轻于加氢原料油,其硫、氮、烯烃含量不宜太高,氮含量应低于200μg/g,总硫质量分数要求低于2%,现通常以直馏柴油馏分应用较多。
由于油比氢气的比热容大,使得湿法硫化具有良好的传热环境,以氧化铝、含硅氧化铝和无定形硅铝为载体的加氢催化剂,在工业装置上大都采用湿法硫化。
而对于含有分子筛(尤其是分子筛含量较高)的加氢裂化催化剂,其裂化活性比无定形硅铝催化剂活性高得多,对反应温度特别敏感,如果采用湿法硫化,当硫化温度高于300℃时,硫化油会发生裂化反应,导致催化剂床层超温,并会加速催化剂积炭,影响催化剂活性及活性稳定性。
因此,含有分子筛(尤其是分子筛含量较高)的加氢催化剂均不采用湿法硫化工艺硫化。
2、干法硫化干法硫化不需要硫化油,因此又称气相硫化,通常在装置的操作压力、循环氢压缩机全量循环的条件下进行,一般起始硫化温度为175℃,终止温度为370℃。
硫化过程与湿法硫化类似,但相对较快和均匀,由于没有硫化油致使硫化过程中放出大量的热不易及时排出,易使反应飞温,必须控制好硫化阶段的升温速率、循环氢中的硫化氢浓度、床层温升等关键指标。
加氢催化剂釜式预硫化方案

加氢催化剂釜式预硫化及反应方案
(1)加氢催化剂预硫化
将100g 200#溶剂油加入高压反应釜中,然后称取一定质量的CS 2(1%~2%)加入其中,然后将25g 催化剂加入反应釜,体系密闭后用H 2吹扫3遍,充H 2到4~5MPa 。
开始加热,加热电压为220V 。
加热至100℃开始搅拌,搅拌速率300r/min ,然后升温到硫化温度280℃硫化8~10h 。
反应过程中不停止搅拌,温度波动范围控制在±1℃,需连续补充H 2。
待反应完成,自然冷却。
石油炼制与工程P412
硫化剂通常CS 2,1%~2%。
CS 2+4H 2——CH 4+2H 2S
NiO+H 2+2H 2S ——Ni 3S 2+3H 2O
MoO 3+H 2+2H 2S ——MoS 2+3H 2O
Co 3O 4+H 2+3H 2S ——3CoS+4H 2O
(2)加氢反应
打开反应釜,迅速清洗溶剂油后,尽快将80g 原料油加入高压反应釜中,密封后用H 2吹扫3遍,充H 2到8.0MPa 。
按正常操作步骤进行加氢反应。
主反应:
副反应:2
+。
- 1、下载文档前请自行甄别文档内容的完整性,平台不提供额外的编辑、内容补充、找答案等附加服务。
- 2、"仅部分预览"的文档,不可在线预览部分如存在完整性等问题,可反馈申请退款(可完整预览的文档不适用该条件!)。
- 3、如文档侵犯您的权益,请联系客服反馈,我们会尽快为您处理(人工客服工作时间:9:00-18:30)。
内蒙庆华20万吨/年甲醇装置
JT-8焦炉气加氢催化剂予硫化方案
一、催化剂装填前准备
1.检查反应器内清洁无水无杂质;
2.准备好内件、填料及催化剂,其中有:
①2mm不锈钢丝网16张左右(直径与反应器直径相同);
②瓷球约数吨左右;
③催化剂;JT-8 装填数量:87M3其中:予加氢反应器D61201A、B各14.5 M3
一级加氢反应器D61202:29.06 M3;二级加氢反应器D61205:29 M3
④φ300、6.5-10.5米长帆布筒子2根、剪刀2把;
⑤装料漏斗(需预制);
⑥500×700轻质木板2块;
⑦葫芦2只或吊车。
⑧在设备内的工作人员以及所需的人孔值班人员在装填作业开始前必须具备具有认可的安全培训,所有时候进入设备内工作都须持有进入许可证以及反应器内气体测试报告。
⑨装填前要对设备进行检验以确保所需的内件都已正确的安装好,特别是温度计导管和取样管,还要检验所有的施工材料是否都已拆掉并且反应器壁已清除氧化物和铁屑。
钢丝网除锈,用白布擦净,检查各测温热电偶管,取样管的安装及连接管口方位是否符合图纸要求,特别注意固定筛网支架。
二、装填作业
1、检查反应器内清洁无水无杂质;
2、底部格栅安装牢固;
3、画出催化剂装填上下界限标记及中间分段标记;
4、底部格栅上面平铺1层不锈钢丝网;
5、装入填料(瓷球)至标志线铺平;瓷球上面平铺2层不锈钢丝网
6关闭下部人孔;
7装催化剂
装填催化剂时应避免阴天,下雨,以防催化剂受潮而影响其使用活性。
催化剂装填之前
应先筛去粉尘。
催化剂装填时,从上人孔放入加料帆布筒10.0米左右和漏斗连接;催化剂装填时视装填设备及人员情况,可进行一台或多台反应器的装填作业。
①漏斗内倒入催化剂0.5-1.0吨;可根据具体情况确定。
并用吊车吊至反应器人
孔上方,漏斗与帆布筒相连,放入催化剂。
②视吊装催化剂的量,取出漏斗和帆布筒由软梯进入反应器,用木板刮平催化剂;
③刮平后,根据具体装填高度,帆布筒剪掉约1米,继续装催化剂,装量根据第
一次实际装填情况可调节。
在整个装填过程中,要求均匀平整,防止粉碎变潮,
勿在催化剂上直接踩踏。
④装入催化剂至分段标记高度后,均匀平整,然后继续装入催化剂。
⑤装入催化剂至额定高度后,扒平后铺2层不锈钢丝网,再装瓷球;
⑥瓷球装到预定高度,扒平后铺一层不锈钢丝网;
7、安装并固定填料压实格栅;
8、安装上人孔。
各加氢反应器催化剂的装填方法基本相同。
三、JT-8型焦炉气加氢催化剂的硫化
催化剂在正常使用之前,为获得较高的加氢转化活性,应对其进行硫化。
采用H2S为硫化剂时,发生如下反应:
MoO3+2H2S+H2→MoS2+3H2O
系统在试压、试漏结束后,以氮气或其它惰性气体吹净置换后,开始催化剂的升温。
升温时,可用氮气或氢氮气。
在对处理有机硫含量较高,硫形态较复杂的焦炉气原料时,为了获得较高的加氢转化活性,催化剂首次使用时,应进行预硫化,预硫化结束时,催化剂吸硫量约为本身重量的4-5%左右。
预硫化条件推荐如下:
气源:氢氮气或含氢的焦炉气中配入CS2
催化剂床层温度升至180℃以上时可在硫化用气中配入CS2。
空速:200~500h-1,压力:常压或低压(≤0.5MPa)
气体中含硫量:0.5~1.5%(体积)氧含量<0.2%
边升温边预硫化(升温速度20℃/小时),260℃、300℃分别恒温2小时,最终升温至正常的操作温度,再恒温,按催化剂理论吸硫量将CS2加完为止,可认为预硫化结束,然后系统逐步升压到正常操作压力,转入正常操作。
采用CS2为硫化剂时,硫化过程发生的主要反应如下:
CS2+4H2=CH4+2H2S
M0O3+2H2S+M0S2+3H2O
可能出现的副反应有:
CS2+2H2=C+2H2S
CS2+2H2=CH4+S2
四、JT-8升温硫化曲线
(1)、装填完毕后,用气密置换合格,使系统残余氧含量<0.2%,用氮气其它惰性气体升温,升温条件:升温速率为20~30℃/hr;空速300-500h-1;压力为0.3-.0.5MPa;
当温度升至160-180℃时,恒定2-3小时,待温度稳定后,切换焦炉气。
(2)、切换焦炉气后,注意床层温度的变化,适时调节入口温度,在160-180℃温度下恒定1-2小时,要求焦炉气中氧含量<0.2%以下。
(3)、在温度恒定之后,开始注硫,气体中含硫量:0.5~1.5%(体积)初期2-4小时气体中硫含量0.5-0.8%(体积),之后可控制在1.0-1.5%(体积)。
待出口气中检测出硫时,开始升温,升温速率20~30℃/小时,220℃恒温,待出口气中检测出硫时,继续升温,升温速率20~30℃/小时,260-280℃恒温,待出口气中检测出硫时,继续升温,升温速率20~30℃/小时,350-380℃恒温,待出口气中检测出0.1%的硫时,或按催化剂理论吸硫量将CS2加完后,可认为预硫化结束,然后降温吹扫,降温速率20~30℃/小时,等温度降至280℃,出口气中硫含量低于50ppm时,逐步升压到正常操作压力(升压速率不高于0.5Mpa/10min),转入正常操作。
催化剂干燥硫化升温曲线
50
100
150
200
250300
350
400
05101520253035
时间 h
温度 ℃
CS 2注入量计算式:
催化剂量×5%×76(CS 2分子量)/64(硫分子量)=硫化剂( 吨)
硫化剂×1.1(10%的余量)= 实际用硫化剂(吨)
气体含硫量计算式:
X (气体量Nm 3)/22.4×0.5%(硫含量)×76(CS 2分子量)/2=X ’ Kg
硫化时温度控制可采用如下方法:
a 、 调节加热或换热付线 ,以控制入反应器的温度
b 、 调节气量及压力的大小
c 、 控制焦炉气中烯烃含量
d 、 根据出口气中烯烃含量进行调控
e 、 调节注硫量,焦炉气中的氧含量要控制在0.2%以下。
五、建议
本次铁钼加氢催化剂原始开车采用予硫化的方法使催化剂硫化。
本此所有加氢催化剂的予硫化应准备硫化剂的注入设备(小型计量泵及小储槽),并在每一反应器入口管道上留一接口,以备硫化剂的注入。
小型计量泵的流量应在0-120升/小时内可调,硫化剂管道应在ф16-20mm ,管道的具体走向现场确定
本方案为原则方案在具体装填及开车时,应根据工艺流程及现场装置等条件制定详细的方案。
西北化工研究院催化剂公司。