PFMEA的S O D打分表
FMEA打分标准
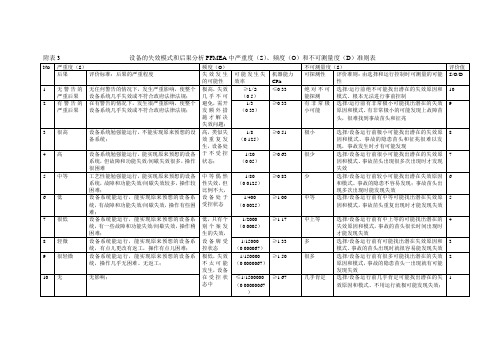
9
3
很高
设备系统勉强能运行,不能实现原来预想的设备系统;
高,类似失效重复发生,设备处于不受控状态;
1/8
(0.125)
≥0.51
极小
选择/设备运行前极小可能找出潜在的失效原因和模式、事故的隐患苗头和征兆很难以发现,事故发生时才有可能发现
中等
选择/设备运行前有中等可能找出潜在失效原因和模式,事故苗头重复出现时才能发现失效
5
7
很低
设备系统能运行,能实现原来预想的设备系统,有一些故障和功能失效/间歇失效,操作稍困难;
低,只有个别个案发生的失效,设备牌受控状态
1/2000
(0.0005)
≥1.17
中上等
选择/设备运行前有中上等的可能找出潜在的失效原因和模式,事故的苗头很长时间出现时才能发现失效
1/150000
(0.0000067)
≥1.50
很多
选择/设备运行前有很多可能找出潜在的失效原因和模式,事故的隐患苗头一出现就有可能发现失效
2
10
无
无影响;
≤1/1500000
(0.00000067)
≥1.67
几乎肯定
选择/设备运行前几乎肯定可能找出潜在的失效原因和模式、不用运行就极可能发现失效;
1
极高,失效几乎不可避免,需开发额外措施才解决失效问题;
≥1/2
(0.5)
≤0.33
绝对不可能探测
选择/运行前绝不可能找出潜在的失效原因和模式、根本无法进行事前控制
10
2
有警告的严重后果
在有警告的情况下,发生很严重影响,使整个设备系统几乎失效或不符合政府法律法规;
PFMEA评分表(新版)
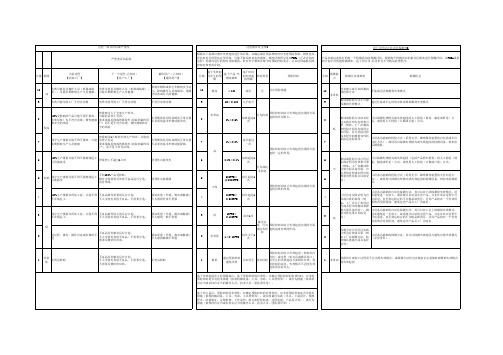
3
部分生产批量在再加工前,可能不得 不良品触发较小的反应计划。
感知质量(外观、噪音或触感)
不在线返工。
不太可能有其他不良品,不需要分选。 令人感到一般不舒服
低
2
对过程、操作、操作员造成轻微的不 便
不良品没有触发反应计划。 不太可能有其他不良品,不需要分选。 要求反馈给供应商。
感知质量(外观、噪音或触感) 令人感到略微不舒服
过程一般评价标准严重度 严重度评估标准
过程潜在发生度0
根据以下标准对潜在失效起因进行的评级。在确定最佳预估频度时应考虑预防控制。频度是在 评估时进行的预估定型评级,可能不能反映真实的频度。频度评级得分是在FMEA(正在评估的 过程)范围内进行的相对评级数值。针对多个频度评级中的预防控制而言,可以使用最能反映 控制有效性的评级。
分级
探测能 力
探测方法成熟度
探测机会
10
尚未建立或已知的测试 或检验方法
不能或无法探测到失效模式
非常低
9
测试或检验方法不可能 探测到失效模式
通过任意或不定时的审核很难探测到失效模式
停线时间大于全部生产班次。
8
100%受影响的产品可能不得不报废。 失效导致厂内不符合法规,慢性健康 和安全的风险
可能的话停止发货。 要求现场返修或替换组件(组装到最终用 户)而不是不符合法规。慢性健康和安
在预期的使用寿命期间正常行驶 所必需的基本车辆功能丧失。
较高
全的风险
停线时间1小时到全部生产班次。可能的
7
部分生产批量可能不得不报废,可能 话停止发运
在预期的使用寿命期间正常行驶
长期Байду номын сангаас响生产人员健康
要求现场返修或替换组件(组装到最终用 所必需的基本车辆功能降级。
pfmea的SOD评分的标准

pfmea的SOD评分的标准
SOD评分(Severity,Occurrence,Detection)是PFMEA(过程风险分析)中最重要的参数,用来衡量特定失效模式的重要性。
总体而言,该评分是基于专家认知而发展出来的,从而找出需着手处理的最高危险因素。
Severity(严重程度):它反映的是失效模式有多严重,通常取决于它对制造过程和最终性能的影响。
它包括了可能出现的危害和对结果的影响,其分值介于1-10之间,其中1代表极低的危害,10代表最大危害。
Occurrence(发生可能性):它反映的是某个失效模式有多可能发生,即模式发生的频率,值从1-10,其中1代表非常可能发生,10代表不太可能发生。
Detection(检测能力):它反映的是某个失效模式是否很容易被检测出来,值从1-10,其中1代表容易检测,10代表不容易检测。
PFMEASOD评分表(3)

探测失效模式,
3
当场 - 自动控制探测缺陷零件和自动扣留零件
以防止进入下工序
探测错误(原因),当场 - 自动控制探测错误和防 2 止产生缺陷零件
防止错误(原因),夹具、机器或零件设计
1
过程/产品设计了防错法,不会产生缺陷零件
探测可能性
中等
中上 高 很高 几乎肯定
可替代RPN的风险顺序评估方法
SOD
绿色区域:没有必要采取措施;
黄色区域:不强求一定要采取措 施;应该采取适当的措施以降低 此类风险;
红色区域:需要采取措施,必须 采取适当的措施以降低此类风险。
BIQS中推荐的方法
Q&A
7 降级
主要功能降级(车辆能运行,表现水平下降)
6 次级功能丧失或 次级功能丧失(车辆能运行,但舒适/方便性的功能不运行)
5 降级
次级功能降级(车辆能运行,但舒适/方便性的功能表现水平下降)
4
外观或能听到的噪音,车辆能运行,不符合,大部分客户都能察觉 (大于75%)
3 烦恼
外观或能听到的噪音,车辆能运行,不符合,很多顾客能察觉 (50%)
等级 探测可能性
没有探测的机会
没有现行过程控制;无法探测或没有分析 10
几乎不可能
几乎在任何阶段都不 失效模式或错误(原因)不容易探测(例: 9
能探测
随机审核)
很微小
在过程后探测问题 在源头探测问题
在过程后探测问题
探测失效模式,
8
过程后 - 操作员目视/触觉/听声方法
探测失效模式
7
当场 - 操作员目视/触觉/听声方法,
2 ≤ 0.001件 / 每1000件
1
失效可用预防控制消除
FMEA SOD 打分表

高
50次每1000个
1次每20辆中
9
20次每1000个
1次每50辆中
8
10次每1000个
1次100辆中
7
一般
2次每1000个
1次每500辆中
6
0.5次每1000个
1次每2000辆中
5
0.1次每1000个
1次每10000辆中
4
低
0.01每1000个
1每100000辆中
3
≤0.001每1000个中
1每1000000
9
可能在有预警下危害操作(机械或装配)
基本功能的损失或降级
基本功能损失(车辆不能操作,但不影响车辆安全操作)
8
大规模中断
100%的产品是废品。流水线停止或停止出货
基本功能损失(车辆可操作,但降低了功能的等级)
7
显著中断
生产运转一定会产生部分废品。背离最初过程包括流水线速度降低或增加
舒适功能的损失或降级
3
在加工前部分须在位置上加工
外观或听见噪音,车辆可操作,不符合项被有辨别能力的顾客注意到(<25%
2
微小中断
过程,操作或操作者的轻微不便利
没有影响
没有可辨别的后果
1
没有后果
没有可辨别的后果
二发生率(O)评分准则
失效可能性
准则:FMEA要因发生率
(事件每项目/车辆)
等级
非常高
≥100次每1000时问题探测
操作者通过直观/目测/排列/耳听法在位置上做失效模式探测或操作者通过使用特性测量(/行/不行、手动转矩检查等)做加工后探测。
7
非常低
加工后问题探测
操作者通过使用变量测量或操作者在位置上通过使用特性测量事后失效模式探测,(行/不行、手动转矩检查等)
FMEA评分

探测度( ) 探测度(D)评分表
效 應 絕對不肯定 很極少 極少 很少 少 中等 中上 多 很多 幾乎肯定 評價準則: 評價準則:被設計控制偵測的可能性 設計控制將不能和/或不可能找出潛在的起因`及後續的失效模; 或根本沒有設計控制。 設計控制只有很極少的機能找出潛在的起因`及後續的失效模。 設計控制只有極少的機能找出潛在的起因`及後續的失效模。 設計控制只有很少的機能找出潛在的起因`及後續的失效模。 設計控制只有較少的機能找出潛在的起因`及後續的失效模。 設計控制只有中等機能找出潛在的起因`及後續的失效模。 設計控制只有中上的機能找出潛在的起因`及後續的失效模。 設計控制只有較多的機能找出潛在的起因`及後續的失效模。 設計控制只有很很多的機能找出潛在的起因`及後續的失效模。 設計控制幾乎肯定能找出潛在的起因`及後續的失效模。 級別 10 9 8 7 6 5 4 3 2 1
发生度( ) 发生度(O)评分表
失效發生可能性
可能的失效率 ≧100件/每千件 50件/每千件 20件/每千件 10件/每千件
級別 10 9 8
很高:的失 效 低:相對很少 發 生的失 效 極低:失效不 可能發 生
5件/每千件 2件/每千件 1件/每千件 0.5件/每千件 0.1件/每千件 ≦0.010件/每千件
严重度( ) 严重度(S)评分表
效 應 無警告的嚴 重危險 有警告的嚴 重危險 很高 高 中等 低 很低 輕微 很輕微 無 判定準則: 判定準則:效應的嚴重度 嚴重級別很高。潛在失效模式影響安全和包含不符合政府法規。 失效發生時無預警。 嚴重級別很高。潛在失效模式影響安全和包含不符合政府法規。 失效發生時有預警。 系統無法運作(喪失基本功能) 系統能運作, 但性能下降。顧客很不滿意。 系統能運作, 方便性方面失效。顧客不滿意。 系統能運作, 方便性方面性能下降。顧客有些不滿意。 裝備和最後完工,噪聲不符合要求,多數顧客發現有缺陷(多於 75%) 裝備和最後完工,噪聲不符合要求,50%顧客發現有缺陷 裝備和最後完工,噪聲不符合要求,有市辨識能力的顧客發現缺 陷(少於25%) 沒有可識別的影響 級別 10 9 8 7 6 5 4 3 2 1
PFMEA严重度打分规则

影响不符合安全性或者法规要求基本功能的丧失或功能降低次要功能丧失或功能降低干扰标准:对产品影响的严重度(对顾客的影响)潜在失效模式影响了汽车的安全运行;或者包含不符合政府法规法规的情形,失效发生时无预警。
潜在失效模式影响了汽车的安全运行;或者包含不符合政府法规法规的情形,失效发生时有预警。
基本功能损失(汽车无法运行,不影响汽车安全运行)。
基本功能损失(汽车可以运行,但是性能下降)。
次要功能丧失(汽车可以运行,但舒适 / 便捷功能不可实施)。
次要功能丧失(汽车可以运行,但舒适/ 便捷功能下降)。
有外观或听见噪音,车辆可操作项目上的问题,并且被绝大多数顾客(> 75%)察觉到。
有外观或听见噪音,车辆可操作项目上的问题,并且被许多顾客( 50%)察觉到。
级别后果10不符合安全9性或者法规要求严重中断8显著中断7中等中断65中等中断43标准:对过程影响的严重度(对制造 / 装配的影响)会使操作员身处危险(机械或装配),失效发生时无预警。
会使操作员身处危险(机械或装配),失效发生时有预警。
产品需要被 100%的废弃。
生产线关闭或中止发运。
一部分产品必须废弃。
偏离基本过程,包括降低生产线速度或增人力。
100%的产品必须离线返工后再被接受。
一部分产品必须离线返工后再被接受。
100%的产品在处理前,必须在线返工。
一部分产品在处理前,必须在线返工。
外观或听见噪音,车辆可操作项目上的问题,但只被少数 微小中断对过程,操作或操作员造成轻微的不便。
识别能力敏锐的顾客(< 225% )察觉到。
没有影响 没有可识别的影响1 没有影响 没有可识别的影响。
TS16949PFMEA评分标准

TS/16949 PFMEA评分标准1.2.3.4.5.6.7.表7.推荐的PFMEA频度评价准则*有关PpKR 的计算和数值,见附录I。
16)现行过程控制现行的过程控制是对尽可能地防止失效模式或其起因/机理的发生或者将发生的失效模式或其起因/机理的控制的说明。
这些控制可以是诸如防失误/防错、统计过程控制(SPC)或过程后的评价,等。
评价可以在目标工序或后续工序进行。
有两类过程控制可以考虑:预防:防止失效的起因/机理或失效模式出现,或者降低其出现的几率。
探测:探测出失效的起因/机理或者失效模式,导致采取纠正措施。
如果可能,最好的途径是先采用预防控制。
假如预防性控制被融入过程意图并成为其一部分,它可能会影响最初的频度定级。
探测度的最初定级将以探测失效起因/机理或探测失效模式的过程控制为基础。
对于过程控制,本手册中的过程FMEA表中设有两栏(即单独的预防控制栏和探测控制栏),以帮助小组清楚地区分这两种类型的过程控制。
这便可迅速而直观地确定这两种过程控制均已得到考虑。
最好采用这样的两栏表格。
过程控制如果使用单栏表格,应使用下列前缀。
在所列的每一个预防控制前加上一个字母“P”。
在所列的每一个探测控制前加上一个字母“D”。
一旦确定了过程控制,评审所有的预防措施以决定是否有需要更改的频度数。
17)探测度(D)探测度是与过程控制栏中所列的最佳探测控制相关的定级数。
探测度是一个在某一FMEA范围内的相对级别。
为了获得一个较低的定级,通常计划的过程控制必须予以改进。
假定失效模式已经发生,然后,评价所有的“现行过程控制”的能力,以防止具有此种失效模式或缺陷的零件被子发运出去。
不要因为频度低就自动地假定探测度值也低(如当使用控制图时)。
但是,一定要评定探测发生频度低失效模式的过程控制的能力或者是防止它们在过程中进行一步发展的过程控制的能力。
随机的质量抽查不太可能探测出一个孤立的缺陷的存在并且不应该影响探测度数值的大小。
PFMEA潜在失效模式SOD分级表

后 果
评定准则:后果的严重度
严重度级
当潜在失效模式导致最终顾客和/或一个制造/装配厂产生缺陷时便得出相应的定级后果。最终顾客永远是要首先考虑的
。如果两种可能都存在的,采用两个严重度值中的较高者。
顾客后果的严重度
制造/装配后果的严重度
无警告的危害
当潜在的失效模式在无警告的情况下影响整机安全运行和/ 或涉及不符合政府法规的情形时,严重度定级非常高
2
很高
肯定能检测出来
√
由于有关项目已通过过程/产品设计采用了防错措施,有差异的零件不可能生产出
1
检验类 : A:防错 B:量具 C:人工检验
或可能在无警告的情况下,生产过程中产品引发的对操作者造成危害
10
有警告的危害
当潜在的失效模式在有警告的情况下影响整机安全运行和/ 或涉及不符合政府法规的情形时,严重度定级非常高
或可能在有警告的情况下,生产过程中产品引发的对操作者造成危害
9
很高
整机不能工作(丧失基本功能)
或100%的产品可能需要报废,或产品很难维修
8
高
整机可运行但性能水平下降。顾客非常不满意
或产品需治具进行分检、一部分(小于100%)需报废,或产品较难维修
7
中等
整机可运行但舒适性/便利性项目不能运行。顾客不满意
或一部分(小于100%)产品可能需要报废,不需治具分检,或产品较易维修
6
低
整机可运行但舒适性/便利性项目性能水平有所下降。
或100%的产品可能需要返工,且容易维修
5
很低
配合和外观、组装等项目不舒适。很容易发现缺陷。
或产品可能分检(需治具),但部分产品(小于100%)需维修且容易维修
FMEA评估分析的级别标准【S、O、D】
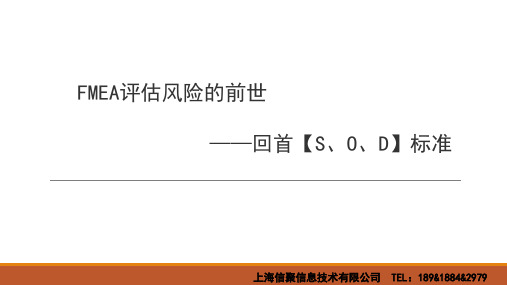
FMEA评估风险的前世 ——回首【S、O、D】标准
上海信聚信息技术有限公司 TEL:189&1884&2979
评估
评估每一个失效模式、起因和影响,以便对风险进行估计。评估风险的级别 标准如下:
♦ 严重度(S):代表失效影响的严重程度 ♦ 频度(O):代表失效起因的发生频率 ♦ 探测度(D):代表已发生的失效起因和/或失效模式的可探测程度
探测度评级最初是对任何尚未被证实的控制的有效性进行的预测。在探测控制完成后,可以对 其有效性进行验证和重新评估。然而,探测控制(例如:测试)的完成或取消也会影响对频度 的估计。
在确定该估计时,应当考虑以下问题: • 探测失效起因或失效模式的最有效测试是什么? • 探测失效所需要的使用记录/工作周期是什么? • 探测失效需要多少样品? • 探测该起因/失效模式的测试程序是否已得到证明?
探测度(D)
探测度评级(D)是对探测控制有效性的估计,用于在项目交付生产前,可靠地证明失效起因 或失效模式。探测评级与最有效的探测控制相关。
探测度是一个相对的评级,且在单个FMEA范围内进行评级,它的确定不考虑严重度或频度。应 当使用表D3中的标准对探测度进行评估。这个表格可以用公司常用的探测方法进行补充。FMEA 项目团队应当就评估标准和评级体系达成一致,即使针对个别产品分析作了修改,该标准和体 系也是一致的。
严重度应当使用严重度表D1中的标准进 行估计。该表可以扩充,以包括特定产 品的示例。FMEA项目团队应当就评估标 准和评级体系达成一致,即使根据单个 设计分析做了修改,该标准和体系也是 一致的。
如果需要,失效影响的严重度评估应当 由顾客转移给供应商。
频度评级是根据评级标准对预防控制有效性的衡量。
频度评级应当使用频度表D2中的标准进行估计。该表 可以扩充,以包括特定产品的示例。FMEA项目团队应 当就评估标准和评级体系达成一致,即使根据单个设 计分析(例如客车、卡车、摩托车等)做了修改,该 标准和体系也是一致的。
PFMEA的严重度SOD的评分和优先级别

表P1—PFMEA严重度(S)
过程一般评估标准严重度(S)
根据以下标准潜在失效影响进行评级
空白,由使用人员填写
S
影响
对你的工厂的影响
对发运至工厂的影响
(在已知情况下)
对最终用户的影响
(在已知情况下)
公司或产品系列示例
10
高
失效可能会导致从事生产或组装作业的工人面临严重的健康和/或安全风险
预防控制在防止失效起因出现的方面可以起到高度有效的作用
2
非常低
1
极低
基础控制
预防控制在预防失效起因设计(例如:零件形状)或过程(如夹具或模具设计)而发生的失效起因方面极其有效。预防控制的目的—失效模式不会因失效起因而实际发生。
预防控制的有效性:在确定预防控制的有效性时,应当考虑预防控制是否为技术措施(依靠机械设备、工具寿命、(工具材料等),或应用最佳实践(夹具、工装设计、校准程序、防错验证、预防性维护、作业指导书、统计流程控制表、过程监视、产品设计等),或行为措施(依靠持有证书或未持有证书的操作人员、技术工人、团队领导等)。
7
基于设备的检验方式(采用光学、蜂鸣器等装置的自动化或半自动化方式),或使用可 探测失效或失效起因的检验设备,例如坐标测量机
6
中
测试或检验方法已经经过实践证明为有效和可靠(例如:工厂在测试或检验方法方面具备经验,有关类似过程或本程序的测量可重复性和再现性结果可能接受等)
可以检验失效模式或失效起因(包括产品样本检验)的人工检验(视觉、触觉、听觉)方法,或使用手动仪器测量(计数型或计量型)方式
非常高
1
H
高
6-7
低—非常低
7-10
H
PFMEA潜在失效模式(S)(O)(D)评价标准

严重度 10
有警告的 严重危害
非常高的严重等级,将危害机器或组装作业员 。失效模 式影响到产品操作安全和 / 或牵涉到违反法律法规时, 但有警告产生。
很高
严重瓦解生产线,100%产品须报废;产品无法使用,更新 丧失基本功能,客户非常不满意。
高
轻微影响生产线,产品须筛选和部份报废;产品可以使 用,但降低功能等级,客户不满意。
5个/每1000件 1个/每1000件
极低﹕ (失效不太可能发生) 拟制/
≦0.1个/每1000件
批准/ 日
9
8
7
6
5
4
3
2 1
频度 10 9 8 7 6 5 4 3 2 1
宁波瑞能智慧科技有 限公司
三、 PFMEA
探测度 绝对不肯定
很极少 极少 很少 少 中等 中上 多 很多 几乎肯定
PFMEA中RPN风险等级评价标准
探测度定级 10 9 8 7 6 5 4 3 2 1
四、 风4险.1风险优先数是严重性(S)、发生频率(O)、和可探测性(D)的乘积
RPN值=(S) ╳ (O) ╳ (D)
4.2 RRPPNN是 值 的结
4.2.1
4.2.2
高﹕一般与经常发生失效的前制程相似制程联系在一起 (经常性失效)
200个/每1000件 100个/每1000件
中等﹕一般与曾经历过偶然失效但比例高的前制程相似 之制程相联系
50个/每1000件 20个/每1000件 10个/每1000件
低﹕与极相似或几利相同制程联系的孤立的失效 (相对 很少发生的失效)
轻微
轻微影响生产线,部份产品在在线重工,装备整修或各 种杂音造成不舒适,这些缺点可能被客户发现。
PFMEA第五版表格模板 自己整理(带实例)--2020.2.3
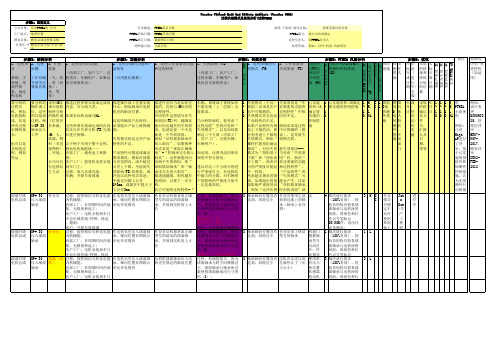
工厂地点: 地理位置
顾客名称: 顾客名或过程族名称 车型年/平 顾客车型年型/平台/款
台: 型
任务描述: PFMEA项目名称 PFMEA开始日期: PFMEA开始日期 PFMEA修订日期: 最新修订日期
跨职能小组: 小组名单
Process Failure Mode and Effects Analysis (Process FMEA) 过程失效模式及效果分析(过程FMEA)
# 批次放行要求
3 H C 作业 Joh 进
电机总成 压入球面
为机械能;
承,轴向位置在图纸公 型号的清洁的球面轴 球面轴承与转子间摩擦过 达到,间距过小 掉到过地上的轴
(100%有效),检
C 指导 n
行
轴承
内部工厂:在周期时间内装 差允许范围内
承,并放到压机的上止 大,球面轴承与轴承座过
承(轴承上有异
验员用检具检查球
书规 Doe 中
配,无报废和返工;
位
紧使得球面轴承内尺寸变
物)
面轴承与电机座的
定不 (生
客户工厂:电机安装到车门Fra bibliotek形(8);
间距,用绿色和红
允许 产
不会出现停线/停顿、拣选
内部工厂:无
色记号笔标记
使用 工
、遏制;
客户工厂:无;
OK/NOK件,再由作
掉到 程
用户:升降车窗玻璃
用户:车窗玻璃升降困难
为无需
0~3mm,或最多不能大于 析。
一定是最高的。
级影响严重度的话 “从料箱拿轴承
额外行
上公差3mm
其它可能的过程特性-“
PFMEA的S-O-D打分表

很稀少
在后工序探测问题
操作员通过视觉/触觉/听觉方式,在后工序探测。
8
少
在来源处探测问题
1、操作员在本岗位上实施失效模式的探测,通过视觉/触觉/听觉方式。
2、或者在后工序探测,通过计数型量具(通/止规、手动扭矩检查/扳手等)。
7
很低
在后工序探测问题
1、操作员在后工序探测,通过计量型量具探测。
2、或者操作员在本岗位上实施探测,通过计数型量具(通/止规,手动扭矩检查/扳手等)。
4
中等中断
100%的产品在处理前,必须在线返工。
有外观、可听噪音、汽车操作项目上的问题,并且被多数顾客(50%)察觉到。
3
一部分产品在处理前,必须在线返工。
有外观、可听噪音、汽车操作项目上的问题,但只被少数识别能力敏锐的顾客(<25%)察觉到。
2
微小中断
对过程,操作或操作员造成轻微的不便。
没有影响
没有可识别的影响。
推荐的PFMEA严重度S评分
影响
标准:对产品影响的严重度
(对使用顾客的影响后果)
等级
影响
标准:对过程影响的严重度
(对制造/装配的影响后果)
不符合安全或者法规要求
潜在失效模式影响了汽车的安全运行;或者包含不符合政府法规的情形,失效发生时无预警。
10
不符合安全或者法规要求
会使操作员身处危险(机械或装配),失效发生时无预警。
7
显著中断
一部分产品必须废弃。偏离基本过程,包括降低生产线速度或增人力。
次要功能丧失或功能降低
次要功能丧失(汽车可以运行,但舒适/便捷功能不可实施)。
6
中等中断
100%的产品必须离线返工后再被接受。
FMEA评分表

8
≥1%,<2%
7
中等:一般与以前时有失效发生,但不占主要比例的过程相类似的工艺有关
≥0.2%,<1%
6
≥0.05%,<0.2%
5
≥0.01%,<0.05%
4
低:很少几次与相似过程有关的失效
≥0.001%,<0.01%
3
很低:很少几次与几乎完全相同的过程有关的失效
≥0.0001,<0.001 %
几乎肯定
1
9
后加工问题探测
在处理(加工)后由操作员通过目测、触觉和听觉方法对失效模式进行探测
微小
8
在来源处探测问题
由操作员通过目测,触觉和听觉方法站内失效模式探测或在处理(加工)后利用计数型工具(止/通规,数显工具)
很低
7
在加工后探测问题
在处理(加工)后由操作员利用计量型工具对失效模式进行探测或通过站内操作员利用计数型工具(止/通规,数显工具)
上等偏高
4
在源头探测问题
于站内通过自动控制模式进行失效模式探测,并自动锁定有差异部分于站内的预防进一步处理
高
3
错误探测和/或问题预防
于站内通过自动控制进行错误(原因)探测,探测到错误部分并防止有缺陷零件生产
非常高
2
探测方法不运用错误预防
透过工装夹具设计,机器设计或零件设计,进行错误(原因)预防;通过过程/产品设计防错,有缺陷零件不可能产生
≥0.001%,<0.01%
3
几乎一样的设计中,无可观察到的失效
≥0.0001,<0.001 %
2
非常低
通过预防措施消减失效的可能性
≤0.0001
1
3.DFMEA探测度评分表(D):
PFMEA严重度评分准则
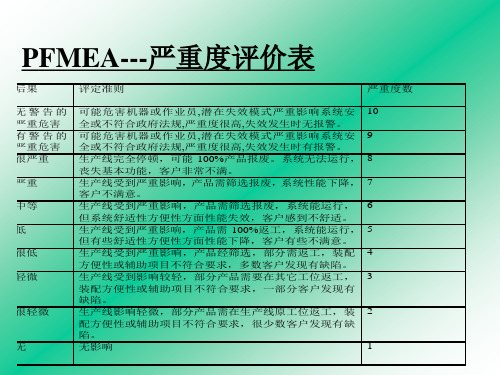
1
PFMEA---严重度评价表
后果 无警告的 严重危害 有警告的 严重危害 很严重 严重 中等 低 很低 轻微 评定准则 可能危害机器或作业员,潜在失效模式严重影响系统安 全或不符合政府法规,严重度很高,失效发生时无报警。 可能危害机器或作业员,潜在失效模式严重影响系统安 全或不符合政府法规,严重度很高,失效发生时有报警。 生产线完全停顿,可能 100%产品报废。系统无法运行, 丧失基本功能,客户非常不满。 生产线受到严重影响, 产品需筛选报废, 系统性能下降, 客户不满意。 生产线受到严重影响,产品需筛选报废,系统能运行, 但系统舒适性方便性方面性能失效,客户感到不舒适。 生产线受到严重影响,产品需 100%返工,系统能运行, 但有些舒适性方便性方面性能下降,客户有些不满意。 生产线受到严重影响,产品经筛选,部分需返工,装配 方便性或辅助项目不符合要求,多数客户发现有缺陷。 生产线受到影响较轻,部分产品需要在其它工位返工, 装配方便性或辅助项目不符合要求,一部分客户发现有 缺陷。 生产线影响轻微,部分产品需在生产线原工位返工,装 配方便性或辅助项目不符合要求,很少数客户发现有缺 陷。 无影响 严重度数 10 9 8 7 6 5 4 3
PFMEA评价准则

.PFMEA评价准则一、目的:规范严重度、频度和探测度的评价准则。
二、范围:适用于PFMEA。
三、术语严重度:一给定失效模式最严重的影响后果的级别。
频度:一特定的起因 / 机理发生的可能性。
探测度:与过程控制中最佳探测控制相关的定级数。
四、评价准则:严重度数评价准则( S)后果评定准则:后果的严重度评定准则:后果的严重度严重度无警告的当潜在的失效模式在无警告的情况下或可能在无警告的情况下对(机器影响车辆安全运行和 / 或涉及不符合政10危害或总成)操作者造成危害府法规的情形时,严重度定级非常高有警告的当潜在的失效模式在有警告的情况下或可能在有警告的情况下对(机器影响车辆安全运行和 / 或涉及不符合政9危害或总成)操作者造成危害府法规的情形时,严重度定级非常高或 100%的产品可能需要报废 , 或者很高车辆 / 项目不能工作 ( 丧失基本功能 )车辆 / 项目需在返修部门返修 1 小时8以上或产品需进行分检、一部分(小于高车辆 / 项目可运行但性能水平下降。
100%)需报废,或车辆 / 项目在返修7顾客非常不满意。
部门进行返修的时间在 0.5-1 小时之内车辆 / 项目可运行但舒适性/ 便利性项或一部分(小于 100%)产品可能需中等要报废,不需分检或车辆 / 项目需在6目不能运行。
顾客不满意返修部门进行返修少于 0.5 小时车辆 / 项目可运行但舒适性/ 便利性项或 100%的产品可能需要返工 , 或者低车辆 / 项目在线下返修,不需送往修5目性能水平有所下降理部门处理很低配合和外观 / 尖响和卡嗒响项目不舒或产品可能需要分检,无需报废,4服。
多数( 75%以上)顾客能发觉缺陷但部分产品(小于 100%)需返工。
配合和外观 / 尖响和卡嗒响项目不舒或部分(小于 100%)产品可能需要轻微返工,无需报废,在生产线上其它3服。
多数( 50%以上)顾客能发觉缺陷工位返工配合和外观 / 尖响和卡嗒响项目不舒或部分产品(小于 100%)产品可能很轻微服。
PFMEA评级

7
很低
6
低
探测度(D)推荐评价准则表(续): 探测度( )推荐评价准则表(
探测几率 标准: 标准:通过过程控制来探测的可能性 等 级 探测可能性 操作员通过计量型量具, 在来源处探测 操作员通过计量型量具,在岗位上实施失效 模式或错误(原因)的探测,或者通过自动 问题 模式或错误(原因)的探测, 控制来探测不规范的部件, 控制来探测不规范的部件,并通知操作员 灯光,警报器等), ),测量针对安装设置和 (灯光,警报器等),测量针对安装设置和 首件检查(只针对设置原因)。 首件检查(只针对设置原因)。 在后工序探测 通过在后工序的自动控制来实现失效模式的 探测,探测不规范的零件,封锁零件,防止 问题 探测,探测不规范的零件,封锁零件, 零件进入下一个流程。 零件进入下一个流程。 通过通过自动控制来探测不规范的零件, 在来源处探测 通过通过自动控制来探测不规范的零件,自 动封锁零件,防止零件进入下一个流程, 问题 动封锁零件,防止零件进入下一个流程,在 本岗位上实施失效模式的探测。 本岗位上实施失效模式的探测。 错误探测和/ 错误探测和/ 或问题预防 通过自动控制防止不规范的零件的生产, 通过自动控制防止不规范的零件的生产,在 岗位上实施错误(原因)的探测。 岗位上实施错误(原因)的探测。
PFMEA严重度 严重度(S) 推荐评价准则表 严重度
影响 标准: 标准: 对产品影响的严重度 对顾客的影响) (对顾客的影响) 等 影响 级 标准: 标准: 对过程影响的严重度 对制造/装配的影响 装配的影响) (对制造 装配的影响)
不符 合安 全性 或法 规要 求 基本 功能 丧失 或功 能降 低
5
中等
4
中等偏高
3 2 1
高 很高 几乎可以确 定
TS16949PFMEA评分标准

TS/16949 PFMEA评分标准1.2.3.4.5.6.表7.推荐的PFMEA频度评价准则*有关PpKR 的计算和数值,见附录I。
16)现行过程控制现行的过程控制是对尽可能地防止失效模式或其起因/机理的发生或者将发生的失效模式或其起因/机理的控制的说明。
这些控制可以是诸如防失误/防错、统计过程控制(SPC)或过程后的评价,等。
评价可以在目标工序或后续工序进行。
有两类过程控制可以考虑:预防:防止失效的起因/机理或失效模式出现,或者降低其出现的几率。
探测:探测出失效的起因/机理或者失效模式,导致采取纠正措施。
如果可能,最好的途径是先采用预防控制。
假如预防性控制被融入过程意图并成为其一部分,它可能会影响最初的频度定级。
探测度的最初定级将以探测失效起因/机理或探测失效模式的过程控制为基础。
对于过程控制,本手册中的过程FMEA表中设有两栏(即单独的预防控制栏和探测控制栏),以帮助小组清楚地区分这两种类型的过程控制。
这便可迅速而直观地确定这两种过程控制均已得到考虑。
最好采用这样的两栏表格。
过程控制如果使用单栏表格,应使用下列前缀。
在所列的每一个预防控制前加上一个字母“P”。
在所列的每一个探测控制前加上一个字母“D”。
一旦确定了过程控制,评审所有的预防措施以决定是否有需要更改的频度数。
17)探测度(D)探测度是与过程控制栏中所列的最佳探测控制相关的定级数。
探测度是一个在某一FMEA范围内的相对级别。
为了获得一个较低的定级,通常计划的过程控制必须予以改进。
假定失效模式已经发生,然后,评价所有的“现行过程控制”的能力,以防止具有此种失效模式或缺陷的零件被子发运出去。
不要因为频度低就自动地假定探测度值也低(如当使用控制图时)。
但是,一定要评定探测发生频度低失效模式的过程控制的能力或者是防止它们在过程中进行一步发展的过程控制的能力。
随机的质量抽查不太可能探测出一个孤立的缺陷的存在并且不应该影响探测度数值的大小。
在统计学基础上的抽样是一种有效的探测控制。
- 1、下载文档前请自行甄别文档内容的完整性,平台不提供额外的编辑、内容补充、找答案等附加服务。
- 2、"仅部分预览"的文档,不可在线预览部分如存在完整性等问题,可反馈申请退款(可完整预览的文档不适用该条件!)。
- 3、如文档侵犯您的权益,请联系客服反馈,我们会尽快为您处理(人工客服工作时间:9:00-18:30)。
很稀少
在后工序探测问题
操作员通过视觉/触觉/听觉方式,在后工序探测。
8
少
在来源处探测问题
1、操作员在本岗位上实施失效模式的探测,通过视觉/触觉/听觉方式。
2、或者在后工序探测,通过计数型量具(通/止规、手动扭矩检查/扳手等)。
7
很低
在后工序探测问题
1、操作员在后工序探测,通过计量型量具探测。
2、或者操作员在本岗位上实施探测,通过计数型量具(通/止规,手动扭矩检查/扳手等)。
潜在失效模式影响了汽车的安全运行;或者包含不符合政府法规的情形,失效发生时有预警。
9
会使操作员身处危险(机械或装配),失效发生时有预警。
基本功能丧失或功能降低
基本功能丧失(汽车无法运行,不影响汽车安全运行)。
8
严重中断
产品需要被100%的废弃。生产线关闭或中止发运。
基本降低(汽车可以运行,但是性能下降)。
推荐的PFMEA严重度S评分
影响
标准:对产品影响的严重度
(对使用顾客的影响后果)
等级
影响
标准:对过程影响的严重度
(对制造/装配的影响后果)
不符合安全或者法规要求
潜在失效模式影响了汽车的安全运行;或者包含不符合政府法规的情形,失效发生时无预警。
10
不符合安全或者法规要求
会使操作员身处危险(机械或装配),失效发生时无预警。
7
显着中断
一部分产品必须废弃。偏离基本过程,包括降低生产线速度或增人力。
次要功能丧失或功能降低
次要功能丧失(汽车可以运行,但舒适/便捷功能不可实施)。
6
中等中断
100%的产品必须离线返工后再被接受。
次要功能下降(汽车可以运行,但舒适/便捷功能下降)。
5
一部分产品必须离线返工后再被接受。
干扰
有外观、可听噪音、汽车操作项目上的问题,并且被绝大多数顾客(>75%)察觉到。
1
没有影响
没有可识别的影响。
推荐的PFMEA发生度O评分
可能性
原因的发生频度
(每个项目/每辆车的事件)
分数
很高:持续发生失效
≥10/100
10≥5/Βιβλιοθήκη 009高:经常发生失效
≥2/100
8
≥1/100
7
中等:偶尔发生失效
≥0.2/100
6
≥0.05/100
5
≥0.01/100
4
低:相对较少失效
≥0.001/100
6
低
在来源处探测问题
1、操作员在岗位上实施失效模式或错误(原因)的探测,通过计量型量具,
2、或者操作员在岗位上通过自动控制来探测不规范的部件,并通知操作员(灯光、警报器等)。测量针对安装设置和首件检查(只针对设置原因)。
5
中等
在后工序探测问题
在后工序的自动控制来实现失效模式的探测,探测不规范的零件,封锁零件,防止零件进入下一个流程。
1
几乎可以确定
4
中等偏高
在来源处探测问题
在本岗位上实施失效模式的探测,通过自动控制探测不规范的零件,自动封锁零件,防止零件进入下一步流程。
3
高
错误探测和/或问
题预防
在岗位上实施错误(原因)的探测,通过自动控制防止不规范零件的生产。
2
很高
探测不适用;错误
预防
有预防错误(原因)的夹具设计,机械设计或零件设计。由于过程/产品的防错设计,不规范零件无法生产。
3
0.0001/100
2
很低:不太可能发生失效
通过预防控制消除了失效
1
推荐的PFMEA探测度D评分
探测几率
标准:通过过程控制来探测的可能性
等
级
探测
可能性
没有探测几率
没有现行过程控制;不能探测或并未分析。
10
几乎不可能
在任何阶段(入厂、过程、出厂)都不容易探测
失效模式和/或错误(原因)不容易被探测到(比如:随机审核)。
4
中等中断
100%的产品在处理前,必须在线返工。
有外观、可听噪音、汽车操作项目上的问题,并且被多数顾客(50%)察觉到。
3
一部分产品在处理前,必须在线返工。
有外观、可听噪音、汽车操作项目上的问题,但只被少数识别能力敏锐的顾客(<25%)察觉到。
2
微小中断
对过程,操作或操作员造成轻微的不便。
没有影响
没有可识别的影响。