印制板V型槽工艺规程
V槽机操作规程 2
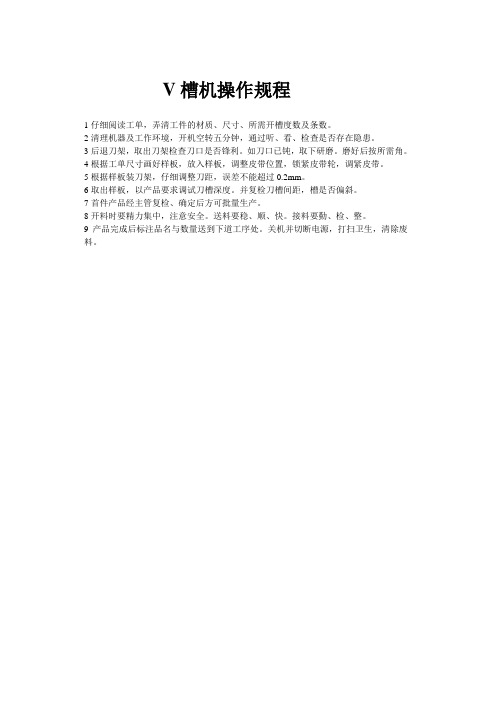
V槽机操作规程
1仔细阅读工单,弄清工件的材质、尺寸、所需开槽度数及条数。
2清理机器及工作环境,开机空转五分钟,通过听、看、检查是否存在隐患。
3后退刀架,取出刀架检查刀口是否锋利。
如刀口已钝,取下研磨。
磨好后按所需角。
4根据工单尺寸画好样板,放入样板,调整皮带位置,锁紧皮带轮,调紧皮带。
5根据样板装刀架,仔细调整刀距,误差不能超过0.2mm。
6取出样板,以产品要求调试刀槽深度。
并复检刀槽间距,槽是否偏斜。
7首件产品经主管复检、确定后方可批量生产。
8开料时要精力集中,注意安全。
送料要稳、顺、快。
接料要勤、检、整。
9产品完成后标注品名与数量送到下道工序处。
关机并切断电源,打扫卫生,清除废料。
PCB工艺设计规范
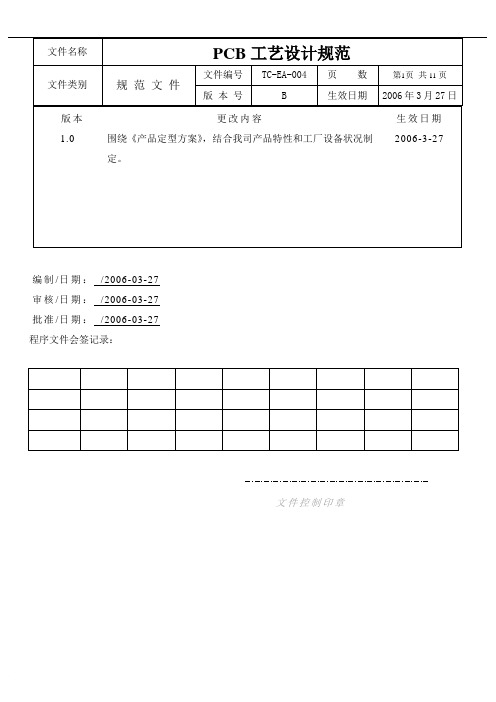
3.6点数:通常用于衡量自动装贴设备和自动光学检测设备动作效率的数值,应用到PCB上就定义为:凡是四个或四个脚位以下的单个器件为一个点,IC或排阻每四个脚位为一个点。
4.规范内容
4.1 SMT段工艺要求,凡设计有SMD器件的PCB必须满足以下要求。
2)器件间距的摆放要求如表4;
说明:表示跳线表示卧式器件
式中D为器件直径,d为器件引脚直径。
表4
4.2.8卧式器件焊盘的设计要求跳线和卧式元件机插时引脚内弯方式,焊盘设计应为元件孔靠焊盘外侧。(如图8)
图8
4.2.9立式器件的摆放要求:(目前我公司没有立式器件自动插件机,暂不作要求)。
4.3插件作业(含波峰焊接工艺、测试工艺)的PCB设计要求:
3.定义
3.1 Mark点:也叫基准点,为自动贴装,自动检测设备提供共同的可测量点,保证了自动贴装和自动检测的每个设备能精确地定位电路图案。
3.2定位孔:为自动插件设备(如AI/JV)和各类检测设备(如ICT,AOI,FCT等)对产品精确定位而专门设计的孔。
3.3过孔:从印制板的一个表层延展到另一个表层的导通孔。
2)相同类型器件应尽量放在同一区域;
3)不同位置的线材应选用不同颜色的线材;
4)对于TO-92封装的三极管的脚位应以品字形排列。
4.3.6插件元件孔设计要求:
1)插件4148、0.5W稳压二级管、1/6W、1/4W电阻、瓷片电容、8050、8550、D667等常用三级管、常用普温和高温电解电容、标准DIP封装等器件孔径应为:0.9MM;
图14
3)不能将SMD元件的焊盘作为测试点;
4)测试点的位置都应在焊接面上;
印制板制作工艺规程

3.3工艺方面
3.3.1布线方向
从焊接面看,元件的排列方位尽量可能保持与原理图一致,布线方向最好与电路图走线方向一致,以便调试与维修.
3.3.2元件分布
所有直插件采用卧式,设计布线图时应注意管脚的排列顺序,元件之间间距要合理.
b)元器件离板边距离应大于5mm,这样可避免波峰焊接时链爪碰到元器件.
c)晶振及晶体应放置于印制板的中心位置,不可在印制电路板板边处,这样一来可以避免分板时产生的震动而造成的损坏.
d)如果SMD元件排列在板边位置,SMD元件的纵向排列坐标应与分板槽平行.SMD元件排列不易太密,零件焊盘与零件焊盘纵向之间的距离不能小于2.5mm.
3.1.2印制板尺寸大小的确定要尽量从本公司印制板尺寸大小系列中选取,尽量不增加尺寸规则,以减少工装数量和生产设备调节次数.
3.1.3受波峰焊接机的限制,印制板最大宽度不得超过300mm;最大长度不得超高400mm.
3.1.4如果板面过小应将多个板面合并成一件。应注意保留零件空位,如:排插、连接器、开关等零件的突出位.同时加宽印制板的板边,其宽度大约10mm(含邮票孔或V型分板槽).
3.2.4元件排列
磁性元件(电感、变压器、晶振等)不宜放在一起,避免其彼此之间产生干扰;另点电容方面应注意其的分布状况.一般来讲旁路电容应分布在接地线旁边,这样可以减少其线性;偶合/协振一般应排放在其本身电路的最近位置.
3.2.5针对无背板机盘,其负48V、220V等高压电源线的走线和过孔应距离板边缘≥10mm处,这样可以避免因老室防静电机架绝缘电阻不够大的问题.强电流线(公共地线、功放电源引线等)应尽量宽些,以降低其分布电阻及其压降,减少其寄生偶合而产生的自激.
印制板设计工艺标准

4.3.5.2.1
4.3.5.2.2红胶工艺的印制板还需满足Bottom层贴装器件的外形距印制板传输边距离不小于7mm。
4.3.5.2.3插装器件高度不高于60mm。
4.3.5.3 V型槽的工艺限制条件
4.3.5.3.1器件边缘距离印制板V形槽应≥2mm,避免切板时对V型槽周围器件造成损害。
4.3.4.3印制板垂直传输边方向的后端建议为直边,不能为斜边、尖角或圆弧。如果因设计要求必须是异形线路板时,则缺口在垂直传输边方向的宽度不能超过10mm。
4.3.4.4印制板四周应设计成圆角,如图9所示。
V-CUT测试点(防呆点)由线路板生产厂家自行设计,我公司在线路板打孔图中进行标注要求,描述方法:要求增加V-CUT测试点。
温度参数
承受时间
备注
1
洄流焊锡机
240℃~250℃
30S~60S
器件应同时满足温度参数与承受时间。
2
波峰焊锡机
255℃~275℃
10S
4.3.10.2新采用的贴片器件应提供给生产技术部确认现有设备是否满足贴片工艺要求。
4.3.10.3大批量生产时,SMD器件的包装必须选用编带形式或托盘形式。
4.3.10.4当SMD器件和THC器件性能一致,价格相符时尽量选用SMD器件。
4.2.2THC:Through Hole Components通孔插装元件。
4.2.3
4.2.4QFP:Quad Flat Package方型扁平式封装,零件四边有脚,零件脚向外张开。
4.2.5Chip:矩形片状元件(rectangular chip component),两端无引线,有焊端,外形为薄片矩形的表面组装元件。
A面施加焊膏贴装SMD洄流焊A面插装THC B面波峰焊。
v-cut作业指导书
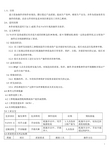
1.0、目的建立设备操作详细作业规范,籍以稳定产品质量,提高生产效率,确保生产安全,并作为设备保养及操作的依据,此份文件同时也是本岗位新进员工培训之教材。
2.0、适用范围本作业规范适用于加工-成型.手动V-CUT机的操作及保养。
3.0、定义和职责3.1 V-CUT是将成型后有多连片或带折断边的PCB板,做V型槽切割.确保一定的余留厚度,以方便客户插件后分割拆解的加工要求。
3.2 制造部职责:3.2.1 员工按研发部提供之参数制造符合要求的产品并做好相关的记录,组长对此进行监督和审核。
3.2.2 员工按规定的要求进行机器操作和设备的日常保养、维护、点检,并做好相应的记录,组长对此进行监督和审核。
3.2.3 组长负责对员工进行安全生产操作的培训和考核。
3.3 品保部职责:3.3.1 IPQC人员负责监督实施力度,对制造部的质量、保养、操作.作业参数和作业环境稽核并保证产品符合客户要求。
3.4 维修部职责:3.4.1 机器的周、月、年的保养和维护并按要求做好相关的记录。
3.5 研发部职责:3.5.1 评估和提供生产过程中各种参数要求及其实现方法。
4.0参考文件和数据4.1制作流程工单。
4.2工程机械成型机构图或客户提供成型图。
4.3工程变更通知单(ECN)。
4.4具体特别操作指示。
7.1操作示意图7.2 V-CUT 机开机操作流程8.0 工艺操作过程及操作要求:N/A 9.0 操作要求9.1 V-CUT 机操作要求流程 操作要求9.2 异常现象原因分析及改善措施9.2.1 露铜、露线、偏位原因:在生产过程中此类异常是较为常见的,造成此异常的主要原因是V-CUT机前后挡板松动及锣板在生产过程中有板大小不一造成。
改善措施:操作员在生产操作过程中要做到定时自检,定时查看V-CUT机文挡板是否有松动,在生产锣板的尺寸有不一致的须将尺寸不一的板挑出分开V-CUT并做到3-5SET自检一次。
9.2.2 跳刀原因:造成板在V-CUT过程中跳刀主要是因为刀具上有缺口和压板胶轮不转造成改善措施:操作员在调刀前必须有对胶轮进行检查,对废弃和有缺口的刀具应分开放置或打报废,胶轮须经常保养使其润滑表面无锈。
印刷开槽工序作业指导书

印刷开槽工序作业指导书印刷开槽工序作业指导书印刷开槽工序作业指导书1、目的根据不同产品结构,提高印刷效果,开槽尺寸精确,成型良好。
2、适用范围适应本车间产品印刷开槽过程质量控制。
3、职责3.1、认真做好班前检查、准备工作,班中坚持勤观察,班后坚持做到清扫、清洗、整理。
3.2、坚持质量第一,做好标记,做到纸片检查、尺寸测量、唛头对照,对不合格品不转不接,发现质量问题及时查找原因,采取措施。
3.3、对设备做到勤观察、勤保养。
3.4、搞好安全生产,出现事故保护现场及时报告、及时分析,找出原因,吸取教训。
3.5、加强岗位练兵,严格执行交货期。
4、程序4.1、设备操作要点4.1.1、开机前检查设备的润滑是否良好,推纸部、开槽部、刀具紧度、对中度。
一切正常后方可开车进入运行,开机时操作警铃先报警警告。
4.1.2、电气开关在操作中,不得随意碰撞,停机后墨辊清洗后将墨辊松开。
4.1.3、设备运行中,车速禁止急增急减,发生异常应立即停车检查。
4.2.1、印刷流程:纸板——推纸——印刷——开槽——堆码4.2.2、来料三层、五层纸板,按照工艺要检查纸板备料尺寸,碰线尺寸及平整度,平整度要求如下表,否则应平压定型处理后方可使。
4.2.3、推纸进料,在调整推板时,推板左右平行误差不超过0.5mm,纸板与推板间隙控制在0.5—1mm之间。
4.2.4、印刷效果不存在漏底铺边和位置波动,位置波动范围控制在±1.5mm内,卷尺测量,铺边漏底,目测检查或样品对照,否则应进行压力调整、更换印版或检查纸板的平面度。
4.2.5、印刷色样,符合样箱要求和用户审定要求,误差大时应立即停机调整压力或对油墨进行调整。
4.2.6、纸板开槽尺寸符合工艺文件要求,槽口波动控制在±2mm,槽口平齐,无毛边,要求开槽刀锋利、间隙小,否则应进行调整和更换,压痕线深度是否合格。
开槽部操作者应对印刷效果、波动以及开槽的波动、毛边进行全面控制,及时提供和反馈信息,及时停车纠正。
V型槽技术要求
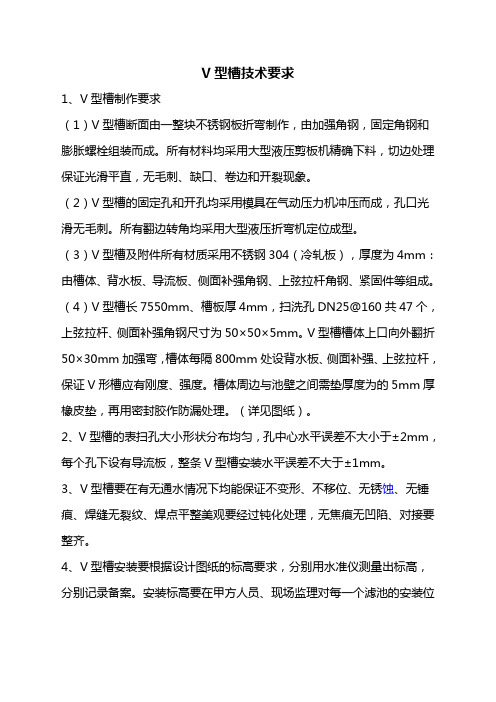
V型槽技术要求
1、V型槽制作要求
(1)V型槽断面由一整块不锈钢板折弯制作,由加强角钢,固定角钢和膨胀螺栓组装而成。
所有材料均采用大型液压剪板机精确下料,切边处理保证光滑平直,无毛刺、缺口、卷边和开裂现象。
(2)V型槽的固定孔和开孔均采用模具在气动压力机冲压而成,孔口光滑无毛刺。
所有翻边转角均采用大型液压折弯机定位成型。
(3)V型槽及附件所有材质采用不锈钢304(冷轧板),厚度为4mm:由槽体、背水板、导流板、侧面补强角钢、上弦拉杆角钢、紧固件等组成。
(4)V型槽长7550mm、槽板厚4mm,扫洗孔DN25@160共47个,上弦拉杆、侧面补强角钢尺寸为50×50×5mm。
V型槽槽体上口向外翻折50×30mm加强弯,槽体每隔800mm处设背水板、侧面补强、上弦拉杆,保证V形槽应有刚度、强度。
槽体周边与池壁之间需垫厚度为的5mm厚橡皮垫,再用密封胶作防漏处理。
(详见图纸)。
2、V型槽的表扫孔大小形状分布均匀,孔中心水平误差不大小于±2mm,每个孔下设有导流板,整条V型槽安装水平误差不大于±1mm。
3、V型槽要在有无通水情况下均能保证不变形、不移位、无锈蚀、无锤痕、焊缝无裂纹、焊点平整美观要经过钝化处理,无焦痕无凹陷、对接要整齐。
4、V型槽安装要根据设计图纸的标高要求,分别用水准仪测量出标高,分别记录备案。
安装标高要在甲方人员、现场监理对每一个滤池的安装位
置进行统一核对后确认,标高确定无误方可进行安装。
安装完成后要对V 型槽精度、质量进行复测。
(要求滤池V型槽标高一致)。
V法造型操作规程123

“V”法造型工艺操作规程1 范围本规程规定了本公司“V”法铸造生产中的通用操作要求。
本规程适用于“V”法铸造生产中的各工序过程。
2 “V”法生产准备2.1 涂料配制:鳞片石墨(>200目)10%,土状石墨(>200目)30 %,锂基膨润土 %,松香 %,酒精适量。
2.2 芯砂配制: 70~140目石英砂(含水量≤1%)100%,煤粉 %,水玻璃 %。
按混制工艺混制后使用,可使用时间:夏季<4小时,冬季<7小时。
2.3 型砂要求:70~140目石英砂(含水量≤1%),砂温<40℃。
2.4 覆模薄膜:EVA 0.10~0.18(根据铸件材质及结构选择)。
2.5 各种冷铁:要求表面光滑,平整,无锈蚀,无孔洞,使用次数不超过7炉次。
2.6 辅料:胶粘带,石棉线,泥条,专用浇口杯等。
3 造型3.1 覆模前操作者应仔细检查设备,模具,薄膜是否正常,并对设备进行加油保养和安全检查。
3.2 将负压调到0.01~0.03MPa,并保压。
将薄膜加热至显示温度90~120度,软化发亮时进行覆膜。
在覆膜时一定要将薄膜牵伸,两人同时徐徐将薄膜均匀覆盖在模具上,覆好后仔细检查是否到位,特别检查转角和深凹部位。
3.3 粘接浇冒口,用刀片割去浇冒口位置薄膜,安放好浇冒口(预先包好薄膜).并仔细进行粘接,确保不能漏气。
3.4 分两次上涂料,务使涂料均匀,保证涂层厚度在0.5—2.5mm间。
待自然干燥后对浇,冒口部位和重要厚大及漏刷位置进行补刷。
对不易干燥的部位用电吹风吹干。
3.5 待涂料充分干燥后按工艺要求摆放冷铁。
摆放冷铁时不得划破薄膜,放好后通过砂箱定位销放好砂箱,放时注意不得碰动浇冒口。
3.6 连砂箱型板,抽气室吊放于振动台,注意不得使抽气管脱落,造成漏气,安放好后将负压调至0.03~0.05Mpa,加干砂并振实.振动时间为30~60秒。
3.7 振实后刮平型砂,覆上薄膜,关闭负压室。
接上砂箱负压并打开(压力为0.04~0.06MPa)保压.粘好浇冒口,加好压砂层(30~50mm),进行脱模,脱模后对划破处漏气的地方立刻补好,下型则翻箱后进行下芯操作。
折弯v槽[最新]
![折弯v槽[最新]](https://img.taocdn.com/s3/m/010a87948e9951e79a89275e.png)
折弯v槽[最新]折床加工事项1. 折床的工作原理将上、下模分别固定于折床的上、下工作台,利用液压传输驱动工作台的相对运动,结合上、下模的形状,从而实现对板材的折弯成形. 2. 折床的结构折床由四大部分构成:1.机械部4.NC电气控制部分分,2.电气部分,3.液压部分3. 折床的运动方式有两种:(1)上动式:下工作台不动,由上面滑块下降实现施压; (2)下动式:上部机台固定不动,由下工作台上升实现施压. 4. 折弯加工顺序的基本原则:4.1 由内到外进行折弯.4.2 由小到大进行折弯.4.3 先折弯特殊形状,再折弯一般形状.4.4 前工序成型后对后继工序不产生影响或干涉.5. 折床的用途:抽凸包,压垫脚,成形自攻芽,压线,印字,铆钉,铆静电导轨,压接地符,抽孔,铆合,压平,三角补强等.折床的加工工艺及注意事项: 6.6.1 折床使用的下模V槽通常为5TV,如果使用5T-1V则折弯系数也要相应加大, 如果使用5T+1V则折弯系数也要相应减小.(T表示料厚,具体系数参见折床折弯系数一览表) 6.2折弯的加工范围:折弯线到边缘的距离大于V槽的一半.如 1.0mm的材料使用4V的下模则最小距离为2mm.下表为不同料厚的最小折边:折弯角度90? 折弯角度30? 料厚最小折边 V槽规格最小折边 V槽规格0.1~0.4 1.0 2V0.4~0.6 1.5 3V 2.2 3V0.7~0.9 2.0 4V 2.5 4V0.9~1.0 2.5 5V 3.4 6V 1.1~1.2 3.0 6V1.3~1.4 3.5 7V 5.0 8V1.5~1.6 4.0 8V1.7~2.0 5.0 10V2.1~2.5 6.0 12V2.6~3.2 8.0 16V3.3~5.0 12.5 25V5.1~6.4 16.0 32V注:如折边料内尺寸小于上表中最小折边尺寸时,折床无法以正常方式加工,此时可将折边补长至最小折边尺寸,折弯后再修边,或考虑模具加工. 6.3 折床折弯时,由于孔边到折弯线的尺寸过小此时必须作适当工艺处理:(1)LASER在相对应的折弯在线作割线处理.(2)NCT在相对应的折弯在线作压线处理(此方法优先考虑).(3)将孔加大至折弯在线(此方法必须与客户进行确认).注:当靠近折弯线的孔距折弯线小于表中所列最小距离时,折弯后会发生变形: 板料厚度 0.6,0.8 0.9,1.0 1.1,1.2 1.3,1.4 1.5 1.6,2.0 2.2,2.4 最小距离2.0 2.5 3.0 3.5 4.0 5.0 5.56.4 反折压平:当凸包与反折压平方向相反,且距折弯线距离L?2.5t,压平会使凸包变形,工艺处理:在压平前,将一个治具套在工件下面,治具厚度略大于或等于凸包高度,然后再用压平模压平.6.5 抽孔离折弯线太近时(?3T+R)必须在折弯线处压线或割线处理.以免折弯时使抽孔变形.6.6 电镀工件的折弯必须注意压痕及镀层的脱落(在工程图上应作特别说明).6.7段差陰影部分為無干涉加工區域加工工件陰影部分為無干涉加工區域从图中可看出段差的干涉加工范围.根据成形角度分为直边断差和斜边断差,加工方式则依照断差高度而定.直边断差:当断差高度h小于3.5倍料厚时采用断差模或易模成形,大于3.5倍料厚时采用正常一正一反两折完成.斜边断差:当斜边长度l小于3.5倍料厚时采用断差模或易模成形,大于3.5倍料厚时采用正常一正一反两折完成.直边断差斜边断差 6.8 折床铆静电导轨的间距为25.15mm, 一次可铆15个点(各铆合冲子可卸下,因此可进行单铆与间隔铆),当静电导轨的边缘与折弯线的距离L?1+V/2mm时(V是折床的下模V 槽宽度)可先铆静电导轨再折弯,小于1+V/2mm时则必须先折弯再铆静电导轨.如1.2mm的材料可用5V折.如下图所示静电导轨的宽度为7.12mm, 型号:700-02776-01 注:6.9 薄材,弹性极强的材料或折弯角度非常重要通常可考虑在折弯在线作压线处理,或在折弯在线开工艺孔或在折弯在线压加强筋.以避免折弯后出现回弹,导致尺寸误差. 如果易模加工则在设计易模时,必须考虑回弹量.6.10 易模压凸包时,如果对凸包的高度要求很严则可考虑采用回压方式来保证其精度.6.11 折床的后定规种类:普通型,长双点型,短双点型,加长型,垫片型,单点型,料内点靠位型, 料内面靠位型.作用:(1) 普通后定规: 面靠位用于工件端面的靠位和工件的左右侧向定位.点靠位用于于工件的两点或多点的靠位,亦可用于一点靠位(必须有辅助设施 (2) 长双点后定规: 小宽度工件的靠位折弯.普通后定规即使后座靠在一起,其前部后定规之间还有70mm的间隙,而用此后定规可使前部间隙缩小到10mm: 躲避毛刺靠位此点同单点后定规功能,但它的适应范围主要是小宽度靠位工件:基面兼有后定规功能(3) 短双点后定规基本功能同长双点后定规,只是适用范围不一样,它可用于更短工件的靠位:适用于NCT下料的工件,用于避开毛刺点,保证折弯精度.(4) 加长后定规利用加长特性,进行小尺寸或负尺寸的间接靠位.此后定规长,它可以伸出机床59.5得到靠位尺寸-59.5.可用于一些靠难度较高的小折,间接靠位折弯;左右定位工件.由于它长于普通后定规,所以工件在用普通后定规靠位时,它可用作工件的左右定位.(5) 垫片后定规用于小尺寸折弯靠位,一般小尺寸折弯的靠位需垫垫片,以免上模压坏后定规,但加垫片时垫片易跑动,影响安全操作,此后定规的突出部分就起垫片的作用.使用方法:突出部分朝下安装;大尺寸或反靠位时支撑工件靠位.折弯大尺寸时,一般需要两个人将手伸进机床抓住工件靠位,极不安全且尺寸不稳定,用此后定规可支撑工件靠位,单人操作,使用方法同上;它的基面等同于普通后定规,所以兼有普通后定规功能.(6) 单点后定规用于多毛刺面的长边靠位,一般NCT下料或切边之产品,边缘有毛刺点,用此后定规或躲过毛刺点,提高折弯精度;用于工件的左右定位,因其基体平面与普通后定规相同,所以此后定规两边可与普通后定规混合使用,其突起部分可用于工件的左右定位,实现工件与模具之间的准确避位,基面有普通后定规的功能(7) 料内点靠位后定规由于此后定规的突点突出于后定规延伸出另一平面,所以它可用于工件内小方孔的靠位.(8) 料内面靠位后定规因其上端有一突出结构,此突出平面与基体平面平齐,且宽度仅为基体的1/3.此点可用于:宽度小于普通后定规宽度的窄缝靠位;将其突出部分向下装夹,可用于料内折弯之直接靠位;最佳适应范围:内部折弯宽度大于20而小于150mm;亦可用于不规则外缘的小面靠位.注:其后定规的一般尺寸为60*9mm.折弯时的定位均紧靠后定规 (即平行于后定规),如果工件的定位面是斜面,此时应视工件的大小(定位的稳定性)设计定位治具,通常L?10mm时均要考虑用定位治具(通常设计易模)来补助定位,除非特别小的工件,当然特别大的工件10mm的定位其稳定性也是欠佳. 如下图所示:7.12 折床压三角补强三角补强的模具规格:刀模型号 117 107 202成形宽度(mm) 3.0 5.0 3.0 5.0 3.0 5.0刀具宽度(mm) 10 20 10 20 10 20 10 20 10 20 10 20模具数量各2支各2支各2支各2支各4支各4支三角补强的成型有两种:1.与折弯刀具同时共享,即折弯与三角补强同时加工2.工件折弯后再压三角补强. 注:成形三角补强的处数与模具数量有关,从上表中可知,目前同一规格最多能成形四处,如超过此数须与相关人员协商解决.。
V法铸造概述
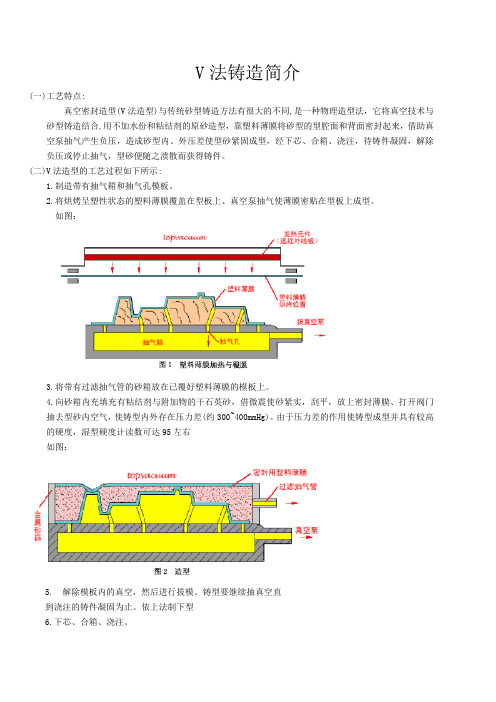
V法铸造简介(一)工艺特点:真空密封造型(V法造型)与传统砂型铸造方法有很大的不同,是一种物理造型法,它将真空技术与砂型铸造结合,用不加水份和粘结剂的原砂造型,靠塑料薄膜将砂型的型腔面和背面密封起来,借助真空泵抽气产生负压,造成砂型内、外压差使型砂紧固成型,经下芯、合箱、浇注,待铸件凝固,解除负压或停止抽气,型砂便随之溃散而获得铸件。
(二)V法造型的工艺过程如下所示:1.制造带有抽气箱和抽气孔模板。
2.将烘烤呈塑性状态的塑料薄膜覆盖在型板上、真空泵抽气使薄膜密贴在型板上成型。
如图:3.将带有过滤抽气管的砂箱放在已覆好塑料薄膜的模板上。
4.向砂箱内充填充有粘结剂与附加物的干石英砂,借微震使砂紧实,刮平,放上密封薄膜、打开阀门抽去型砂内空气,使铸型内外存在压力差(约300~400mmHg)。
由于压力差的作用使铸型成型并具有较高的硬度,湿型硬度计读数可达95左右如图:5. 解除模板内的真空,然后进行拔模。
铸型要继续抽真空直到浇注的铸件凝固为止。
依上法制下型6.下芯、合箱、浇注。
如图:7.待金属凝固后,停止对铸型抽气,型内压力接近大气压时,铸型就自行溃散。
(三)V法造型的特点:1、提高铸件质量:表面光洁、轮廓清晰、尺寸准确。
用较细干砂,铸型硬度高且均匀,拔模容易。
2、简化设备、节约投资、减少运行各维修费用。
省去有关粘合剂、附加物及混砂设备。
旧砂回用率在95%以上。
模具及砂箱使用寿命长3、金属利用率高。
V法造型中,金属活动性较好,充填能力强,可以铸出3mm的薄壁件。
铸型硬度高、冷却慢;利用补缩,减少冒口的尺寸。
工艺出品率提高,减少了加工余量。
二、基本工艺装备及设备1、SK型水环式真空泵:为V法铸造提供真空环境。
2、震实台:紧实砂型3、薄膜烧烤器:加热薄膜,管式电加热器作加热元件,也可用火焰或电阻元件加热远红外线板。
4、模板及芯盒:抽气孔ф2~3mm,要保证薄膜密贴模板,薄膜成型欠佳的部位需要加钻小孔。
5、有过滤抽气装置的砂箱及芯盒抽气方式:导管式、复合式、侧箱式。
- 1、下载文档前请自行甄别文档内容的完整性,平台不提供额外的编辑、内容补充、找答案等附加服务。
- 2、"仅部分预览"的文档,不可在线预览部分如存在完整性等问题,可反馈申请退款(可完整预览的文档不适用该条件!)。
- 3、如文档侵犯您的权益,请联系客服反馈,我们会尽快为您处理(人工客服工作时间:9:00-18:30)。
其它 V 型槽工艺要求见上述要求。
3)针对特殊要求的 LED 双面长条形灯板 V 割后剩余厚度为(0.2-0.4)mm,V 槽角度为 30º±5º,上、下
(贴片面、空白面) V 槽深度 h1>h2,但上下 V 槽深度偏差须≤0.2mm,分离后单板宽度公差控制在
±0.1mm 范围内,其它具体见拼板图工艺要求。
0.5mm
±0.1mm ≤0.1mm h1≥h2
1.6mm
≥0.3mm
0.7mm
±0.1mm ≤0.1mm h1>h2
CEM-1/CEM-3 1.2mm
≥0.2mm
0.6mm
±0.1mm ≤0.1mm h1>h2
1.0mm
≥0.2mm
0.5mm
±0.1mm ≤0.1mm h1≥h2
1.6mm
≥0.3mm
0.6mm
±0.1mm ≤0.1mm h1>h2
FR-4
1.2mm
≥0.2mm
0.5mm
±0.1mm ≤0.1mm h1>h2
1.0mm
≥0.2mm
0.4mm
±0.1mm ≤0.1mm h1>h2
CEM-1/CEM-3/ FR-4
(1.0~1.6)mm
比以上标准 +0.1mm
比以上标准 -0.1mm
4)对于印制板需要承重较重或板材较柔软的可取上限值,而对于承重较轻的可取下限值,其它有特殊
要求按拼板图纸工艺要求。
拟制
审核
校对
更改标记 数 量 更改单号 签 描 图: 描 校:
名日
标准化 期 批准
第1页 共1页
1)V 槽平直无偏移,V 槽面光滑无明显毛刺,除 V 槽进刀及出刀外,其它部分要求深度均匀。
2) 常规单面板(双面板)V 槽角度以 30º为主,偏差 ±5º;上、下(插件面、焊接面) V 槽深度 h1>h2,
但上下 V 槽深度偏差须≤0.2mm,尤其针对机插板(有腰形孔的拼板)h1 必须大于 h2 约 0.2mm 左右,
表所示:
版本
旧底图总号 底图总号
日期 签名
材质
板厚 (δ)
V 槽深度 (h1/h2)
剩余厚度 (H)
公差 (mm)
偏移量 (d)
备注
1.6mm
≥0.3mm
0.7mm±0.1mm源自≤0.1mm h1>h2FR-1
1.2mm
≥0.2mm
0.6mm
±0.1mm ≤0.1mm h1>h2
1.0mm
≥0.2mm
通用 印制板 V 型槽工艺规程 文件编号
版本
产品图号
图号
1.适用范围: 为了使印制板供应商符合我司对印制板的生产加工工艺要求,以及提供加工、检验及判定的参考依据,
保证原材料的质量,特制定本工艺规程。 本规程适用于本公司内各种线路板的 V 型槽工艺要求。 印制板厚度δ,插件面 V 槽深度 h1,底层 V 槽深度 h2,剩余厚度 H,刀尖偏移量 d 的尺寸要求如图、
±0.1mm
≤0.1mm
针 对 ≥ 250mm 的长板
CEM-1/CEM-3/ FR-4
(1.0~1.6)mm
比以上标准 -0.1mm
比以上标准 +0.1mm
±0.1mm
≤0.1mm
针对铣外形加 搭扣连接板
铝基板
(1.0~1.6)mm 板厚 1/4
板厚 1/2
±0.1mm ≤0.1mm h1≈h2
2.工艺要求: