紧密纺高支纱关键工艺影响因素的优化
细绒棉纺高支纱的工艺研究

国 理,合理制定各工序的温湿度的控制范围,并加强管理,在保证生活好做,各工序不粘、缠
的情况下,湿度以偏大控制为宜,使各工序半制品及成品均有较高的回潮率,为保证成纱强
2014'中 力及减少毛羽提供了保障。
工序
线网 高峰 温度
清花 25° C~28°C
各工序温湿度冬季的控制范围 表六
梳棉
准备
精梳
并粗
25°
1.35 14mm 230m/min
末并 15.5g/5m
8 8.7 1.23 10mm 230m/min
纱 术 3.6 粗纱工序
国 技 在粗纱工序采取的是:集中前区牵伸的工艺,采取较小的后区牵伸倍数,能保证喂入须
条的良好的结构状态和原棉条的条干均匀度不受破坏,并能提高纤维在粗纱中的平行度和分
中 纺 离度。同时为减轻细纱机的牵伸负担,粗纱定量设计以偏轻掌握。采用较大的粗纱捻系数,
干。因精梳条中纤维的分离度平行伸直度均较好,且弯钩、短绒均少,因此在并条工艺中还
中 纺 采用了较大的后区隔距及较小的后区牵伸配置,以防止棉结增加。
国棉 项目 2014'中 并条定量
并合数:根 总牵伸倍数:倍 后区牵伸倍数:倍
网 峰 后区隔距: 线 高 出条速度:
主要工艺配置 表三 头并
16.5g/5m 6 6.6
纤维得到进一步的伸直分离。预并工艺配置:并合数:5 根,后区隔距:16mm,总牵伸倍数:
5 倍左右。
议 条并卷工艺措施:采用较大的总牵伸,较小的后牵伸,总并合根数较多,进一步提高纤
会 维的伸直度。工艺配置为:并合数:20 根,后牵伸:1.2 倍左右。实践证明,采用此工艺:
网 峰 既保证了预并条的条干得到了改善,同时还有效地解决了粘卷以及预并后棉结的增长,为精
纺纱过程中出现的问题及解决措施

纺纱过程中出现的问题及解决措施纺纱疵点及解决措施1. 纱线不匀原因:原料品质不佳、梳理不充分、牵伸不均匀、锭子质量差解决措施:采用优质原料、加强梳理、优化牵伸工艺、更换或维修锭子2. 毛羽原因:原料纤维过短、梳理不足、牵伸过度、加捻不当解决措施:选用较长纤维原料、加强梳理、调整牵伸工艺、优化加捻参数3. 太紧原因:牵伸过大、加捻过多、锭子调整不当解决措施:减少牵伸倍数、降低加捻强度、调整锭子4. 太松原因:牵伸不足、加捻过少、锭子调整不当解决措施:增加牵伸倍数、提高加捻强度、调整锭子5. 粗细不均原因:原料纤维粗细不均、牵伸不均匀、加捻不均匀解决措施:选用均匀原料、优化牵伸工艺、调整加捻参数6. 结头原因:原料中有杂质、梳理不充分、牵伸不均匀、加捻过大解决措施:去除原料中的杂质、加强梳理、优化牵伸工艺、降低加捻强度7. 条痕原因:原料染色不均匀、混纺原料不匹配、牵伸不均匀、加捻不均匀解决措施:均匀染色原料、选择匹配的混纺原料、优化牵伸工艺、调整加捻参数8. 花疵原因:原料中有杂色纤维、梳理不充分、牵伸不均匀、加捻不均匀解决措施:去除原料中的杂色纤维、加强梳理、优化牵伸工艺、调整加捻参数9. 脆硬原因:原料纤维成熟度差、梳理不足、加捻过度解决措施:选用成熟度高的原料纤维、加强梳理、降低加捻强度10. 棉结原因:原料中有棉结、梳理不充分、牵伸不均匀、加捻过大解决措施:去除原料中的棉结、加强梳理、优化牵伸工艺、降低加捻强度11. 裂口原因:原料纤维强度低、梳理过度、牵伸过大、加捻过大解决措施:选用强度高的原料纤维、加强梳理、优化牵伸工艺、降低加捻强度12. 僵硬原因:原料纤维弹性差、梳理不足、牵伸过大、加捻过度解决措施:选用弹性好的原料纤维、加强梳理、优化牵伸工艺、降低加捻强度13. 刺毛原因:原料纤维中含有短纤维、梳理不足、牵伸不均匀、加捻过度解决措施:去除原料中的短纤维、加强梳理、优化牵伸工艺、降低加捻强度14. 络筒时断头原因:原料强度低、梳理不足、牵伸不均匀、加捻不足、络筒张力过大解决措施:选用强度高的原料纤维、加强梳理、优化牵伸工艺、调整加捻参数、降低络筒张力。
紧密纺高支纱关键工艺影响因素的优化
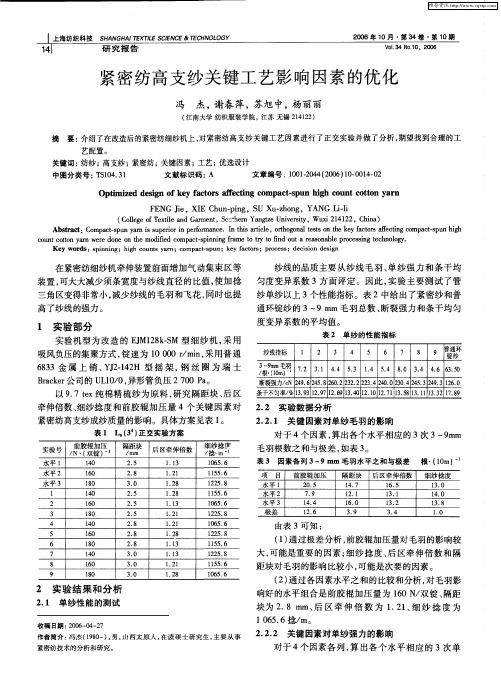
牵伸倍数、 细纱捻 度和前胶辊加压量 4个关键 因素对 2 2 实验 数据 分析 .
2 21 关 键 因素对 单纱 毛羽 的影 响 ..
对于4个因素 , 出各个水平相应的 3 3 9 m 算 次 ~m 毛羽根数之和与极差 , 如表 3 。
表 3 因素各 列 3— l 羽水 平之 和与极差 根・ 1m) 9i n毛 n (0
维普资讯
I 上海纺织科技
S A G A E T ES I C H N H I X I C N E&T C N L G T L E EH OO Y
兰
!星: 堂: 蔓 蔓!塑
V 13 01 0 . 4 N .O。2 0 06
Байду номын сангаас1l 4
研 究 报告
紧密纺高支纱关键工艺影 响因素 的优化
冯 杰, 谢春 萍,苏旭 中, 杨丽 丽
( 江南大学 纺织 服装学 院,江苏 无锡 2 4 2 ) 1 12
摘
要: 介绍 了在改造后的紧密纺细纱机上 , 对紧密纺高支纱 关键 工艺因 素进 行 了正交实验 并做 了分析 , 望找到 合理 的工 期
K e wo d y r s:s i n n p n i g:hih C U t a n;c mp c— p n;ke a tr g O n sy r o a ts u y f co s;p o ( s;d cso e in r c ̄ s e iin d sg
在紧密纺细纱机牵伸装置前面增加气动集束 区等
艺配置。
关键 词 : 纺纱 ; 高支纱 ;紧密纺;关键因素 ;工艺 ; 优选设 计 中图分 类号 : S0 . 1 T 14 3 文献标识码 : A 文章编号 : 0 124 20 1— 04 0 10 — 4(06)00 1 —2 0
《细纱工序产生细节的因素分析和改进措施》

《细纱工序产生细节的因素分析和改进措施》细纱工序产生的中短片段细节对后道工序的生产会造成不利的影响,使织造工序断头增加,给生产效率的提高带来困难,同时使布面质量和风格受到影响。
所以最大程度地减少细节就尤为重要。
1细节的产生机理1.1纤维在牵伸过程中,由于受到各因素的影响,纤维不在同一界面上变速而产生移距偏差。
如在牵伸区内,须条的某一截面上有较多的纤维提前变速,便会产生粗节,在粗节的后面就是细节;反之,若有较多的纤维变速较晚,便会产生细节,在细节的后面就是粗节。
当纤维的变速位置越分散,则移距偏差值越大,粗细节越多。
1.2在粗纱进入牵伸区后,纤维所受到的力是多方面的,理想的状态是这些作用力始终不发生变化,设备状态保持如一,使每根纤维的变速点趋于一致,而实际情况是或多或少都存在差异,控制和减少这种差异就是我们要努力的目标和方向。
2产生细节的因素2.1前牵伸区,纤维在此区域运动最为激烈,罗拉和胶辊的状态直接影响纤维的运动。
罗拉弯曲、晃动、齿型不良以及前胶辊铁壳游隙过大、胶辊表面有凹槽、不光滑,摇架压力或大或小等因素都会造成对纤维的控制力不断的发生变化,易产生8cm机械波;胶辊表面粗糙,纤维易粘附在胶辊表面,造成纤维散失,产生细节。
2.2中区牵伸,如该部位对纤维控制不当,使纤维在上下皮圈间的运动不规则,发生位移。
如浮游区过大、上下皮圈龟裂、上下肖变形、表面不光滑、中铁壳表面生锈、皮圈内积花、皮圈跑偏、下皮圈张力架弹簧失效等,这些会造成皮圈的回转速度不匀,产生皮圈顿挫,使从后罗拉钳口输送过来的纱条不能被有效拉伸,而发生扭曲;上肖变形极易造成上皮圈起拱,使纤维在上下皮圈之间失去控制而产生30-40cm机械波;浮游区过大会增加浮游纤维的数量,使纤维的变速位置紊乱而产生细节。
2.3横动装置不良(小于5mm)或者整个装置失灵、无左右移动,使纤维在同一点上连续牵伸、摩擦,没有恢复弹性的时间,均会造成胶辊、胶圈出现凹槽,影响纤维在牵伸过程中的运动。
紧密纺高支棉纱关键影响因素的优化设计

1 实 验
实验机型为改造 的 E M1 8 -S 型 细纱机 , 用吸 风负 J 2k M 采
压的集聚方式 , 锭速为 1 0 /a , 00 0rri 采用普通 63 n 8 3金属上销 、 Y 2 4 H型摇架和瑞 士 B ak r J —1 2 rc e 公司钢丝圈 。 以 7 3tx紧密纺纯棉精梳纱为例 , . e 研究 分析 了 4个紧密纺 高支棉纱 的关键影响因素 , 别为前 胶辊压力 、 分 隔距 块 、 风压和 钢丝 圈。结合实际情况 , 利用正 交表进 行了 4因素 3 平正交 水
匀度测试 分析仪。测试 条件 为; 环境相对湿度 5 . , 2 0 温度 2. 4 0℃。表 3 给出 了实验 紧密纱和陪纺普通环 锭纱 的 3 l毛 ~9mi l
羽总数 、 断裂强力和条干均匀度变异系数 。 表 3 单纱主要性能指标
纱线指标 1
.
2
3
4
5
160 2.
1.9 78
表 1 因素水平
2 2 实验 数 据 分 析 . 2 2 1 关 键 因素 对 单 纱 毛 羽 的 影 响 . .
对 于各 因素列 , 出各个水平相应 3次 3 算 ~9mm的毛羽 总 数之和与极差 , 结果 见表 4 。根 据表 4 作 出各 因素与 毛羽之 间 ,
() 3 从表 图可 以看 出风压对毛羽影响呈单调递减趋 势 , 幅 但 度不是很大 , 综合能耗情况考虑 , 风压不需要再加 大。
2 2 2 关 键 因素 对 单 纱 断 裂 强 力 的 影 响 . .
四罗拉紧密纺精梳棉纱关键工艺优化设计
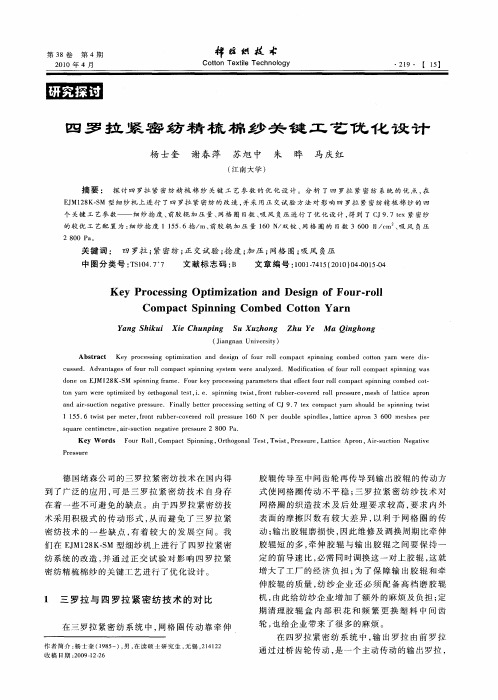
纺 系统 的改造 , 通 过 正 交 试 验 对 影 响 四罗拉 紧 并 密纺 精梳 棉纱 的关 键工 艺进 行 了优 化设 计 。
伸胶 辊 的质 量 , 纺纱 企 业 还必 须 配备 高档 磨 胶 辊
1 三 罗 拉 与 四 罗拉 紧 密 纺 技 术 的 对 比
在 三 罗拉 紧密 纺 系统 中 , 格 圈传 动 靠 牵 伸 网
.
脚 一 ~ 一 一 ~~ 一 A“ { 一 ; E一 ~ 一一 胁 Ⅵy . 一 Ⅲ
摘 要 : 探 讨四 罗拉 紧密 纺精梳 棉 纱 关键 工 艺参 数 的优 化设 计。分 析 了四 罗拉 紧密纺 系统 的优 点 , 在
E M1 8 —M 型 细 纱 机 上 进 行 了 四 罗拉 紧 密 纺 的 改 造 , J 2 KS 并采 用 正 交 试 验 方 法 对 影 响 四 罗拉 紧 密 纺 精 梳 棉 纱 的 四 个 关键 工 艺 参 数— — 细 纱捻 度 、 胶 辊 加 压 量 、 前 网格 圈 目数 、 风 负压 进 行 了优 化 设 计 , 到 了 C . x紧 密 纱 吸 得 J 7t 9 e
金 属 上 销 、 J . 2 型 摇 架 , 丝 圈 为 C L u r Y 21 H 4 钢 1E d
之 , 是 积极 式 传 动 , 网格 圈 的磨 损 较少 , 网 其 对 使 格 圈使 用 寿命变 长 。
型 、0 0号 , 压 吸 风 口的 倾 角 7 , 距 块 2 5 1/ 负 。隔 . m 后 区牵伸 1 2 倍 。 m, .1
3 纺 纱 试 验
原料 与品种 : 采用 定量 为 3 0 g 1 l . / 0I 的纯 棉 I 精梳 粗纱 , 纺纱 品种 为 C . e 。 J9 7t x
紧密纺纱技术及紧密纺纱特性分析

第3期2005年9月化纤与纺织技术ChemicalFiber&TextileTechnology文章编号:1672—500X(2005)03—001l一03紧密纺纱技术及紧密纺纱特性分析陶珏(淮安东方清棉纺织有限公司,江苏淮安223002)摘要:介绍紧密纺纱技术如何消除纺纱三角区来提高成纱质量,介绍紧密纺纱技术的纺纱机理及其特性。
关键词:紧密纺纱纺纱三角区毛羽环锭纺条干中图分类号:TS103.27+7文献标识码:B1引言一种在普通环锭纺纱机纺纱原理的基础上发展而成的紧密纺纱技术已被成功地研制和推广。
紧密纺作为一种新型纺纱方法,以其独特的纺纱原理,改善了环锭纺成纱的结构,其优越的纱线性能,显著的经济效益,引起了国内外纺织行业的密切关注。
据统计国内引进紧密纺纱设备已有几十万纱锭,国内各纺机厂也相继开发研制紧密纺纱机。
除个别厂大都有以网眼(格)胶圈加吸风槽为基本形式。
现就国产紧密纺纱机进行研究和分析。
2传统纺纱机的缺陷和紧密纺纱技术的纺纱机理传统环锭纺细纱机就是在牵伸区对粗纱施加一定的牵伸比,以获得所需要的纱线支数。
为了使纱线获得所要的强度必须加上捻度,束纤维在细纱前罗拉输出处到加捻成细纱加捻点之间形成纺纱加捻三角区。
当纤维进入三角区时几乎失去控制,完全处于松散状态,边缘纤维在加捻前脱离主体成为飞花,据统计细纱车间约有80%以上的飞花由此处造成,也有的可能成为毛羽,是因为纤维一端被捻入纱体,另一端就造成毛羽,另外在纺纱三角区中,’三角形两边的纤维比三角形中间的纤维所受的张力大,纺出的纱在受力时纤维不能平均负担,两边的纤维先断,成纱断裂强度达不到应有的水平,造成强力或高或低不稳定,因此普通环锭纺加工过程还得进一步改善。
紧密纺是在环锭纺纱细纱机上进行重大革新和创造的纺纱技术,在环锭纺纱机上的牵伸与加捻之间加上一种特殊的新型纺纱装置——集聚装置,来彻底消除环锭纺中存在的加捻三角区。
即扁平的须条从前罗拉输出时,纤维束受空气负压气流的压缩与控制,在负压气流与一定角度的吸风口复合作用下,很快地把一定宽度的纤维束横向收缩,使纤维束的宽度柔和地转化为成纱的宽度,边缘纤维向中间集聚,须条在纤维排列平顺、紧密、受力均匀的情况下被加捻,纤维之间的抱合力大大增加,成纱的结构和机械物理性能及纤维的强力利用情况都将得到明显的改善。
高支高密Tencel紧密纺家纺面料的生产

高支高密Tencel紧密纺家纺面料的生产蔡永东【摘要】为在ZAX9100-340型喷气织机上开发高支高密Tencel紧密纺家纺面料.特采用细特低原纤化Tencel纤维原料,优选纺纱各工序工艺参数并采取必要的技术措施.成功纺制出Tencel 7.3 tex紧密纺纱线,纱线质量达到了喷气织造的用纱水平.织造前通过对浆料配方和浆纱工艺参数进行优化,解决了毛羽多、织造过程开口不清的问题.喷气织造采用"小双层梭口、短梭口长度、大张力"的工艺原则.织机效率达到95%,下机合格率90%.【期刊名称】《南通纺织职业技术学院学报》【年(卷),期】2011(011)001【总页数】4页(P4-6,47)【关键词】Tencel;紧密纺;家纺面料;上浆工艺;喷气织造【作者】蔡永东【作者单位】南通纺织职业技术学院,南通,226007【正文语种】中文【中图分类】TS106.81高档喷气织机以车速快、入纬率高、大批量生产原色纱线织物而著称,用其开发与生产高档家纺面料有其得天独厚的优势.而Tencel纤维作为一种绿色环保纤维,其高支高密织物具有吸湿性好、缩水率小和丝质感强的风格特点,适宜用作高档家纺面料.为适应市场需求,充分发挥企业设备与技术优势,采用低原纤化(LF型)细特Tencel纤维纺制出Tencel7.3tex紧密纺纱线,并在ZAX9100-340型喷气织机上成功开发出一种高支高密Tencel紧密纱家纺面料.现将有关产品研制与生产情况介绍如下.1 织物规格与生产工艺流程(1)织物规格. 织物规格为:Tencel(LF)7.3tex×Tencel(LF)7.3tex ,551×551 根/10cm,幅宽267cm,1/1平纹组织.由于该织物纱支细,经纬密度大,总紧度达85%,为保证能在喷气织机上顺利生产,必须采用紧密纺纱线.(2)纺织生产工艺流程.①纺纱流程为:FA002型自动抓棉机→SFA035C型混开棉机→FA106型梳针开棉机→SFA161B型振动给棉机→A076E型单打手成卷机→FA231A型高产梳棉机→FA311F型并条机(两道)→FA423A型粗纱机→FA506型细纱机.②织造流程为:AC338型自动络筒机→ZS-98型贝宁格整经机→贝宁格-泽尔型浆纱机→半自动穿经机→ZAX9100-340型喷气织机→下机织物整理.2 主要纺纱工艺及其技术措施(1)原料选用与预处理.Tencel纤维从结构特性分有A100型(非原纤化)、G100型(原纤化)和LF型(低原纤化).由于我们生产的是细特天丝紧密纺纱线,故采用1.0D×38mm Tencel LF型纤维,其具有高强低伸、高湿模量、干湿强度高的特点.由于细特Tencel LF型纤维卷曲少,纤维间抱合力差,纺纱过程不易成卷,退卷时黏卷现象严重,生产前需对原料进行预处理,即原料需提前进入生产车间开包,在生产环境中放置时间一般不少于24 h,以平衡纤维的回潮率.(2)开清棉.由于细特Tencel LF型纤维的初始模量高,纤维比表面积大,断裂伸长小,回弹差,同时细特Tencel纤维卷曲少,纤维间抱合力差,因此纺纱过程中,易产生静电、脆断和扭结.为此开清棉工序采取“多松少打、薄层快喂、低速度、大隔距”的工艺原则,以减少纤维损伤和棉结的产生.其主要工艺参数:抓棉机打手伸出肋条高度2.5 cm;SFA035C型混开棉机跳过小豪猪只过平行打手;FA106型开棉机采用梳针打手,转速控制在450 r/min;A076E型成卷机综合打手转速780 r/min,棉卷罗拉转速10 r/min;天平罗拉与综合打手隔距10mm;棉卷定量428 g/m;棉卷长度为30.6m.(3)梳棉.细特Tencel LF型纤维细度细,表面滑顺,抱合力差,纺纱过程中不易转移,成网较困难,处理不当易使棉结、短绒增加.因此,梳棉工序采取“轻定量、大隔距、低速度、小张力”的工艺原则,选用化纤专用金属浅齿针布,适当降低梳理速度,保证少伤纤维和顺利转移,提高棉网清晰度.其主要工艺参数:生条定量每5米15g,锡林转速350 r/min,刺辊转速600r/min,道夫转速20r/min,盖板速度97mm/min.锡林~盖板5 点隔距为0.35、0.35、0.32、0.32、0.35mm,刺辊~锡林 0.18mm,刺辊~锡林 0.22mm,刺辊~给棉板 0.38mm.(4)并条.细特Tencel LF型纤维比表面积大,摩擦系数大,纤维牵伸力大,纺纱过程中易产生静电,造成吸花疵点,因此,要控制好车间的相对湿度,防止纤维因吸湿而绕罗拉.并条工序定量应适当偏大控制,采用“大隔距、低速度、小张力”的工艺原则.同时,为了降低熟条的重量不匀和条干CV值,要选用带自调匀整的并条机,熟条重量不匀控制在0.4%,条干CV控制在2.2%.为使纤维得到良好的平行度和伸直度,消除弯钩纤维,同时又保证条干均匀度,头、二道采用8条并合,其定量分别为每5米16g和15.5g,并采用头道较大的后区牵伸倍数,二道并条后区牵伸倍数要小,即头、二道并条后区牵伸倍数分别为1.75、1.47倍,总牵伸倍数分别为8.86、8.04倍;并条各道罗拉中心距为46mm×43mm×52mm,各道前罗拉转速为1330r/min.(5)粗纱.细特Tencel LF型纤维抱合力差,粗纱捻系数应偏大掌握,以避免细节问题的出现,但要避免在细纱出硬头现象.粗纱工序采用“重定量、高捻度、低速度、重加压”的工艺原则,生产过程中应注意机后劈条现象.其主要工艺参数如下:粗纱定量5.0g/10m,后区牵伸倍数为1.19,罗拉中心距38mm×53mm×70mm,隔距块规格3.5mm,锭翼转速600r/min,捻系数75.在以上工艺条件下,粗纱的Uste条干CV值为3.65%.(6)细纱.由于细特Tencel LF型纤维比较膨松,表面光滑,易造成须条滑脱,意外牵伸大,细节毛羽多,故采用德昌紧密纺设备,选用低硬度高弹性胶辊、镀氟钢领和镀氟钢丝圈,以改善成纱条干和强力,减少成纱毛羽的产生[1].由于Tencel LF型纤维牵伸力较大,容易造成细纱后罗拉扭振,因此选用小的后区牵伸倍数和大的后区罗拉隔距,并选用高精度无机械波罗拉,避免罗拉扭振,提高成纱条干.细纱工序主要工艺参数:总牵伸67.7倍,后区牵伸1.21倍,罗拉隔距18mm×35 mm,清洁器隔距1.6mm,肖子隔距2.5mm,锭速13500 r/min,捻系数325.经检测Tencel(LF)7.3 tex紧密纺纱线质量指标达到了喷气织机生产的用纱水平:百米质量CV1.52%,断裂强度25.3cN/tex,单强CV9.17%,条干CV10.75%,细节6个/km,粗节18个/km,棉结35个/km,3mm毛羽3.67根/10m.3 主要织造工艺及其技术措施(1)络筒.采用AC338型自动络筒机.由于Tencel LF型纤维表面光滑,结构蓬松,易产生毛羽,为此络筒时纱线通道要光滑,利于纱线在退绕过程中降低与设备之间的摩擦,以降低毛羽的恶化程度.络筒时采用“低速度、轻张力、小伸长、保弹力”的工艺原则,主要工艺参数为:车速为1000r/min,卷绕密度为0.45g/m3;电清工艺设置:N(棉结)通道250%,S(短粗)通道截面增量为150%、长度为2.5cm,L(长粗)截面增量为40%、长度为40cm,T(长细)通道截面增量为-30%、长度为60cm;张力器示数为12;捻接器参数设定:解捻气压0.5MPa,加捻气压0.6MPa.(2)整经.选用ZS-98型贝宁格整经机.该整经机采用V形筒子架,张力棒导纱,夹纱片夹纱.V形筒子架能保证整经时经纱不同区域的张力较为均匀,并且纱线退绕时因包围角小而摩擦小,可减少纱线的再生毛羽.考虑到Tencel(LF)7.3 tex单纱强力小、纱线伸长及弹性回复性较差等因素,整经时采用较低速度和张力偏小配置,以减少纱线的伸长,故整经工艺以最大限度减少原纱伸长损失为原则进行设计[2].具体工艺如下:总经根数为7350×2根,整经头份525×14,整经速度600m/min,张力棒隔距5mm,张力棒打开延时2s,夹纱片开启延时1s. (3)浆纱.由于经纱为纯Tencel特细号纱紧密纺纱线,织物经纬密度高,织造紧度大,在织造时经纱间相互摩擦严重,并且紧密纺纱体中纤维排列紧密,上浆时纱线不易吸附浆液,从而导致表面上浆和浆膜黏附不牢等现象出现.另外高速喷气织造具有“小开口、大张力、强打纬”的特点,其要求经纱能承受更多的反复拉伸、摩擦和较好的梭口清晰度,故Tencel特细号紧密纺纱线浆纱时宜采用“小张力、低粘度、中压力、重浸透、低上浆”等工艺原则,以提高浆纱耐磨与毛羽贴伏性能,减少浆纱弹性损失.① 浆料配方.Tencel纤维是亲水性的纤维素纤维,浆料配方应采用易糊化的变性淀粉和聚丙烯类浆料为主、适量混用溶解性好的低聚合度PVA-205MB的混合浆料.因PR-Su属马铃薯变性淀粉,其对纤维素纤维具有较好的粘附力、成膜性,有利于提高耐磨性能,避免产生再生毛羽,并且调浆方便,退浆废液容易降解,是一种绿色环保浆料,故PR-Su在取代PVA上浆方面具有明显的性能优势[3].故浆料配方工艺:PR-Su马铃薯变性淀粉为 50kg,CD-50E 为 40kg,PVA-205MB 为 12.5kg,JFC 浸透剂为 2.5kg,TW-46 蜡片为 2kg,体积0.8m3,煮浆温度95℃,浆液黏度9±1s.②上浆工艺.采用贝宁格-泽尔型浆纱机.该浆纱机采用先进的七单元独立驱动,在慢车和常速运行时,其喂入伸长及湿区伸长可分开设定,可使浆纱打慢车时分开的片纱相互豁连打绞少.由于品种为高支高密织物,浆纱覆盖系数为86%,为保证上浆均匀、减小覆盖系数,采用双浆槽、分层预烘的上浆路线,但两个浆槽及两组预烘、烘筒的工艺参数设置要一致.为保证浆膜的完整率和良好的浸透,应适当加大压浆力.故上浆工艺参数:上浆率为14±1%;回潮率为10±1%;喂入伸长为0.2%,湿区伸长为0.4%,干区伸长为0.8%,总伸长小于1.5%;浆槽温度为95℃,浆槽黏度为8~9s;湿区烘筒温度为105℃,干区合并烘筒温度为100℃;压浆压力13~16kN,退解张力500N,喂入张力300N,干纱张力1100N,卷取张力1600N,托纱张力2500N;车速为45m/min.(4)穿经.由于该织物经密大且为平纹织物,采用6页综框,均匀分布各页综上的综丝根数,以减少单页综丝密度.用134#钢筘,每筘齿2入,筘长290cm,穿经幅宽278.6 cm.地组织穿法为135246飞穿,落片穿法为112233445566,以减少经纱间摩擦.(5)喷气织机织造.采用日本津田驹ZAX9100-340型喷气织机.根据Tencel特细号紧密纱和产品风格及织造调试要求,采用“小双层梭口、短梭口长度、大张力”工艺配置.采用小双层梭口,有利于前部梭口纱线分层,减少交织时的相互摩擦断经.但小双层梭口易导致开口不清,必须采用大张力,以保证引纬时梭口清晰.而采用大张力后,会导致断纬停台率增高,并且开车档、稀密路、波浪纹等织疵出现机率变高.为此,应合理调整经位置线,将后梁与停经架前移,其数值分别为3.5、2cm,缩短前部梭口长度,以减少经纱间的横动和综丝与经纱间的摩擦,使前部梭织强制开清,从而降低断纬停台次数,提高织造效率,并降低织疵率[4].上机织造工艺参数设计为:纬密系数设定为318;车速设定为650 r/min;引纬时间为70°~265°,主喷气压为2.0N,辅喷气压为2.4N;上机张力设为1200N;开口时间135综平综285°、246综平综290°;吊综高度分别为 136mm、134mm、132mm、130mm、128mm、126mm,1~6 页的开口量分别为 70mm、65mm、60mm、55mm、50mm、50mm;后梁高度80mm档,深度9格;停经架度高2mm档,深度8格;松经时间为310°,松经量为10mm.由于经、纬纱均为Tencel特细号紧密纱,在织造过程中易产生边撑疵和破洞,须及时更换边撑及其刺环,减少对纤维的伤害和破洞的产生.Tencel纤维为高湿模量纤维,对温湿度变化敏感,故织造车间湿度控制80%以上,以减少经纱的断头次数,提高织造效率.4 结语经采用上述一系列技术措施后,Tencel特细号紧密纱高密织物的开发与生产相当顺利,上机织造效率达95%以上,下机一等品率达90%,入库一等品率达99%,经检测产品各项物理性能指标均达到优等品标准.该产品因手感挺爽、吸湿透气性好、光泽幽雅柔和而具有独特的豪华美感,产品一投放市场,便深受客户青睐.参考文献:[1]雒书华,刘俊芳,李向东,等.Tencel4.9 tex紧密纱的生产体会[J].棉纺织技术,2010,38(4):44-46.[2]眭健华.Tencel纤维面料开发[J].国外丝绸,2003(5):14-16.[3]史博生,郑力.PR-Su浆料完全取代PVA上浆的工艺探讨(上)[J].棉纺织技术,2008(6):24-28.[4]王荣根.高密羽绒布设计及有关生产技术问题的探讨(上)[J].棉纺织技术,2006,34(5):26-31.。
成纱强力的影响因素及改进措施

成纱强力的影响要素及改良举措要使织物拥有必定的强力和坚牢度,一定使纱线拥有必定的强力,纱线强力是评论纱线质量的重要指标。
表示纱线强力的指标可分为绝对强力和相对强力两大类。
绝对强力是指纱线受外力直接拉伸到断裂时所需要的力,也叫断裂强力。
用牛顿(N)或厘牛(CN)表示..。
纱线断裂的原由:纱线断裂是由一部分纤维断裂、一部分纤维滑脱。
也就是断面纤维滑脱根数减少、断面处单根纤维强力低、不匀率大;纱中纤维之所以滑脱,主假如因为纤维长度短、短绒齐集,纤维卷曲少、纤维柔度差、纤维之间抱协力差。
影响成纱的强力要素:1原料性能、如长度、的线密度、断裂长度等;2、纺纱工艺过程对影响性能影响程度;3、成纱构造,如纤维的挺直平行及在纱线的摆列散布状况,纱线的捻度大小等;4、成纱均匀度,如重量不匀率和条干不匀率以及捻度不匀率等。
因为断裂老是在最纤弱处发生。
提升成纱强力主要应从合理选择原料、减少混淆差别、提升前纺半制质量量、改良半制品与成纱构造、提升细纱条干以及合理选择捻系数等方面着手。
纱线强力也是一个系统工程,重要的是解决强力衰环。
解决强力衰环,看拟简单,实质是比较难做到的一件事。
涵盖方面太广。
一句话:细节决定成败!1/7原纱的强力特点包含均匀强力、强力不匀率、均匀伸长及伸长不匀率。
一般经纱均匀强力在15cN/tex,强力CV%在9%~10%左右,纬纱均匀强力12cN/tex,强力CV%9%~10%左右。
均匀断裂伸长,一般都控制在2%之内。
喷气织机停台的重要强力指标是强力衰环即最低强力,一般以为纱线细度仅为正常纱的40%时,这类细节弱环必定惹起断头,造成停台,假如强力衰环在4cN/tex,伸长率低于2%,必定会造成断头。
其强力衰环除了细节疵点占61%之外,其余弱捻、接头不良,含杂粗节等也会造成经纬间停台,约占39%。
原纱上的细节主要有三类:一种短绒细节,一种是粗细节结头处,另一种长细节或多个短细节连在一起的都会惹起断头。
紧密纺条干CVb的影响因素及措施

近年来纺纱设备不断高速化,其结构、配置、性能等都发生了很大的变化,特别是客户对棉纱高品质的要求与日俱增,控制成纱条干的均匀度成为重点。
为保证成纱条干水平的稳定性,减小细纱CVb,是每个纺织行业必须长期面对的问题,笔者对条干CVb的影响因素及解决措施谈点自己的看法。
一、温湿度的影响温湿度对条干CVb有着较大的影响。
温湿度过高时纤维发软,黏附力上升,前纺工序在生产过程中易形成索丝和棉结,出现牵伸不开、条干恶化的现象;温湿度过低时,纤维变脆易断裂,饱和力小易发生缠绕、飞散等,影响成纱条干均匀度,严重影响条干CVb的波动,为此必须加强温湿度管理,合理掌握各工序的温湿度,才能收到较好的效果(如表1所示)。
表1各工序相对湿度的控制标准二、原料的影响纤维物理特性的变化是引起牵伸力变化的主要因素之一,它包括纤维的长度、细度、短绒率、断裂强度、刚度、卷曲度、纤维间的摩擦因数、整齐度、棉结、杂质、含糖、纤维的伸直平行度、纤维在须条中的排列状况等,这些纤维物理特性的变化会影响纤维相互间摩擦因数的变化,摩擦因数的不一致和不稳定,使作用在每根纤维上的控制力和引导力不尽相同。
每根纤维的变速点截面发生变化,会造成移距偏差而影响条干CVb,纤维中的短绒率,对条干CVb的影响较为显著。
以紧密纺JC60为试验标准(如表2所示)。
表2梳棉生条短绒率对成纱条干影响的对比试验从表2试验结果可以看出,随着生条短绒的降低,成纱条干CVb明显降低。
在实际工作中应尽量减少配棉纤维间的物理指标差异,为提高产品质量,降低条干CVb,笔者做了以下几方面的工作:1.由于各产地原棉包型不一、密度差异大,上盘后高低差异大的特点,及时与车间沟通,采用高包削平填空与低包找平的原则,努力提高混棉均匀度。
2.原料进入车间使用前,对于原料回潮率差异较大的成包预先松包,采取加湿去湿措施,平衡回潮率,保证上机原料的回潮率基本相同。
3.原料在分类使用时,要考虑季节变化和构棉趋势,并结合考虑各种原棉的库存量,做到瞻前顾后、留有余地,原棉成分尽量做到勤调少调。
紧密纺使用关键技术

1。
紧密纺概述1。
1紧密纺技术优点把紧密纱的优点描述为只有一个“紧密”,并不全面。
根据用户的需要,可以“紧密",也可以不紧密,例如不需要太高强度的纱线,可以采用降低捻度来提高产量而取得经济效益(不管那一种类型的紧密纺机构都可以).只要工艺设计合理,紧密纱织物可以做得手感很好。
紧密纺主要技术优点可以概述为:对使用多年的细纱机进行局部改造还可以用于生产低捻紧密纺纱,有利吸收染料及整理助剂,从而改善织物外观及特性;毛纺后整理省去烧毛工序,采用较快进布速度,明显提高修理工工作效率,降低生产成本,但真正的高档次,还是要烧毛的,比如120英支以上紧密纺还是要烧毛的,但是烧毛的市场本身就比不烧毛纺纱要小得多;适合半精纺及化纤混纺织物,在半精纺色织纱有些纤维先染色后纺纱,经水洗漂后强力损失大,加上后道对毛羽棉结的高要求,利用紧密纺技术优势得到弥补,如再配以赛络纺纱,毛羽更少,最终降低织物起球、起毛;目前市场上较为热销的是60支以上的纱,利用紧密纺技术可有效减少长绒棉用量,达到降低成本的目的;应用紧密纺技术还可以广开思路,在机织产品中用普梳紧密纺或半精梳紧密纺来代替传统环锭纺半精梳纱或精梳纱,已证明是可行的。
1。
2紧密纺应用价值:从细纱程序来看,改造紧密纺装置后用工、机物料、耗能是有所增加的,但是在同等质量要求前提下在整个纺纱流程中所带来的配棉等级下降、梳棉(精梳)落棉降低、产品附加值增加的经济效益要远远大于细纱工序增加的成本,所以说当前改造紧密纺的投入产出比还是非常划算的。
1.3紧密纺纱的运用必须遵从的原则紧密纱的质量优势是众所周知的,但如果仅仅依赖紧密纺技术作为提升纺纱质量的捷径,而大量的相关工作没有配套跟上的话,反而会得不偿失。
因此,不同于普通环锭纺纱,紧密纺纱的运用必须遵从以下的原则:(1)合理配棉和工艺优化:一般情况下客户使用紧密纱,因其价格相对较高,均是用在质量要求较高的品种上,所以对纱线的质量要求也更为苛刻.常规的工艺思路设计难以满足要求,必须进行系统性考虑,从原料、工艺上不断优化,最大限度发挥紧密纺的优势。
高支高密Tencel紧密纺家纺面料的生产

第 1 期
蔡 永 东 : 支 高 密 T n e 紧 密 纺 家 纺 面 料 的 生 产 高 ec1
高档 喷气 织机 以车 速快 、 纬率高 、 批量 生产 原色 纱线 织物 而著 称 , 入 大 用其 开发 与 生产 高档 家纺 面 料 有其得 天独 厚的优 势.而 T n e 纤维 作 为一种 绿色环 保纤 维 。 高支 高密 织物 具有 吸湿性 好 、 水 率小和 e cl 其 缩 丝质 感强 的风格 特 点 , 宜用作 高档家 纺 面料 .为适 应 市场 需求 , 分 发挥 企 业 设备 与技 术优 势 , 用低 适 充 采
经 机一 贝宁格 一 尔型浆 纱机一 半 自动 穿经机- Z X 10 3 0型 喷气 织机一 下机 织物 整理 . 泽 - A 9 0— 4 -  ̄
2 主 要 纺 纱 工 艺 及 其 技 术 措 施
( 原 料选 用 与预 处理 .T n e 纤 维 从结 构特 性 分有 A1 0型 ( 原纤 化 )G10型 ( 1 1 e cl 0 非 、 0 原纤 化 ) L 和 F型 ( 低原 纤化 ) .由于我们 生产 的是 细特 天 丝紧 密纺纱 线 , 采用 1 D 3 m T n e L 故 . x 8 m e cl F型 纤维 , 具有 高 强 O 其
原纤 化 ( F型 ) L 细特 T n e 纤维 纺 制 出 T n e . e 密 纺 纱线 , 在 Z X 1 0 3 0型 喷气 织 机 上 成 功 ecl e cl 3 x紧 7t 并 A 90 —4
成纱强力影响因素及提高措施

成纱强力影响因素及提高措施胡振龙赵卫华(东营市宏远纺织有限公司)纱线强力是评价纱线质量的重要指标,有绝对强力和相对强力之分。
影响成纱强力的主要因素有:原料性能(纤维长度、细度、单纤维强力等)、纺纱工艺、成纱结构(纤维伸直度、平行度、排列分布、纱线捻度等)、成纱均匀度(条干不匀率、捻度不匀率)等。
因此提高成纱强力要从合理选择原料、改善须条结构、提高成纱条干、合理选择捻系数等方面入手。
1 原料与成纱强力的关系1.1 纤维长度及整齐度与成纱强力的关系纤维长度长,整齐度好、短纤维少,则成纱光洁,强力高,见表1。
表1纤维长度及整齐度与成纱强力的关系1.2 纤维线密度与成纱强力的关系在其它条件相同的条件下,纤维的线密度小,成纱截面内纤维根数多,分布均匀,成纱条干均匀,纤维间接触面积大,摩擦力大,纱线在拉伸断裂时,滑脱纤维的根数将会减少,纱线强力就高。
1.3 单纤维断裂长度与成纱强力的关系单纤维断裂长度大,则成纱强力高。
单纤维强力差时,在纺纱过程中易断裂而形成短绒,被搓揉成结粒,恶化成纱条干,从而使成纱强力降低。
1.4 棉纤维性能与成纱强力的关系表棉纤维主要指标与成纱强力的关系见表2。
表2 棉纤维主要指标与成纱强力的关系2 纺纱工艺对成纱强力的影响2.1 清梳工艺在保证原料充分开松的情况下,尽可能避免猛烈打击,避免损伤纤维、增加短绒。
保证各种成分混合均匀,提高各单机运转效率,在保证前后供应的条件下,单机运转效率越高越好,尽量达到98%以上。
开清工序各单机要优化工艺参数,做到薄喂快给、柔和开松,以梳代打,合理减少打击点。
做到棉结、杂质、短绒兼顾。
实践中证明:开清工序的总除杂效率,在原棉含杂率小于1.5%时应保持在30-40%;原棉含杂率在1.5-2%之间时应保持在40-50%;原棉含杂率大于2.0%时应保持在40-60%,最基本的要求是要保证筵棉含杂率不高于1.0%。
确定了开清工序的总除杂效率后,要合理分配各单机的除杂率,控制棉结和短绒增长率。
浅析影响纱线质量的主要因素及解决方案

■7 z 璧 锰 广 一
条干 C V 值 一 般 在 1 3 %左 右 , 而 C 1 4 . 6 t e x条 干C V 值 一 般 在 1 6 . 5 左右 , 其 主要 原 因就 是 由于棉 条 中短绒 率 的含 量 不 同所 造成 的 , 因此 严 格 控制 短绒 率是 十分 必要 的 。精梳 纱 与普梳 纱 比
( 3 ) 内在 状态 : 强力、 伸长 、 捻度、 纤维 伸 直平 行度 、 纤 维分 离度 等 。
熟度 等产 品指 标 , 如 果 原 棉产 地 不 同又 可 分 为 地 产棉 、 新 疆 棉 和进 口棉 , 部 分 地 区原 棉 含 糖率 , 也
是一 项重 要检 测 指标 , 上 述这 些 指 标 在 原 棉 进 厂 时必 须 由专业 棉检 人 员 进 行 实 验 , 是 技 术科 确 定 配棉 比例 的主要 参 考指标 。 3 . 1 . 1 短 绒率 的影 响 原 棉 中 一 般 短绒 率 控 制 在 9 ~1 2 为好 , 纺纱 过程 中短绒 变 成 浮 游 纤 维 , 无 法 控 制造 成 纱 线条 干不 匀 , 清梳 两 工 序增 长 率 也 要 严 格 控 制 在 4 以下 。经验 可知 , 纺 细号 纱精 梳条 内短 绒率 约 每增 加 2 . 5 , 成 品条 干 C V 值 增 加 1 %。
此不再 逐 一详述 , 只 针对 总 的纱 线 质 量影 响 因素 进行 粗略 的分 析 。
2 . I 因素分析 用 鱼刺 图进行 分解 【 见图 I )
技能 索
= 茎 三 二 二 二 二 二 三 二 二 二 二 = = : ; : = : — — — = = = 二 。 产 品 质 量 { 员工 的工 机槭 状节 ; 甚 温度 管理 一
后区牵伸倍数对紧密纺高支棉纱成纱质量的影响

作者简 介 :苏旭 中 , 男,18 年 生 ,硕 士在 读 ,无锡 ,24 2 92 1 12
于 无害毛 羽; 3nr以上 的是长 毛 羽 , 而 t t l 属于 有害 毛 羽 。 纱
2 纺织导报 C i et a e . 0 6N . h a xi L d r 2 0 o nT l e e 7
也 有 利于纤 维在 加捻 卷绕 时有 再一 次伸 直 的机 会 , 而提 从 高 纤维 强 力的利 用 系数 ,提高 了成纱 强 力 。
钳口隔紧密纺高支棉纱成纱质量的
影响
3 1 成纱毛羽 .
在环 锭纺 纱 条加捻 过程 中 大 多数纤 维端 都伸 出在 纱
区中须 条扁平 分散 , 薄均 匀一 致 . 牵伸 区握持 牢 固稳 厚 主
定。 同时 主牵伸 区中须 条的 牵伸 力相 对较小 . 且波 动缓 慢 . 从而避 免 了 因喂入 粗纱 条 干不匀在 传统 环锭 细纱机 上牵伸 时 牵伸 力剧烈 波动 .使 浮游 纤维 集束 形成粗 细 节 。同时 由 于 主牵伸 区前 钳 口处须 条 扁平分 散 . 则慢速 浮 游纤维 所 受 引导 力相 对较 弱 . 有利 于慢 速浮 游纤维 尽 可能 接近 前钳 口 变速 .从 而使 浮游 纤维 运动 的 变速点相 对 集 中 ,减 小 了浮
喂入粗纱定量 /( (0 ) g・ 1 m) 喂入粗纱捻系数
风 压/ Pa
集聚 作用 , 使须 条较 集聚 地排 列 , 大大 减小 了传 统细纱 机 加捻 三角 区 中须条 带 的宽度 , 有利 于将 须条 中 的纤维 可靠 地 捻卷 到纱 条 中 , 而可 较大 幅度 地减 少毛 羽 。同时 吸风 从
维普资讯
y纺 纱 技 术
模糊正交法在优化紧密纺高支纱工艺中的应用
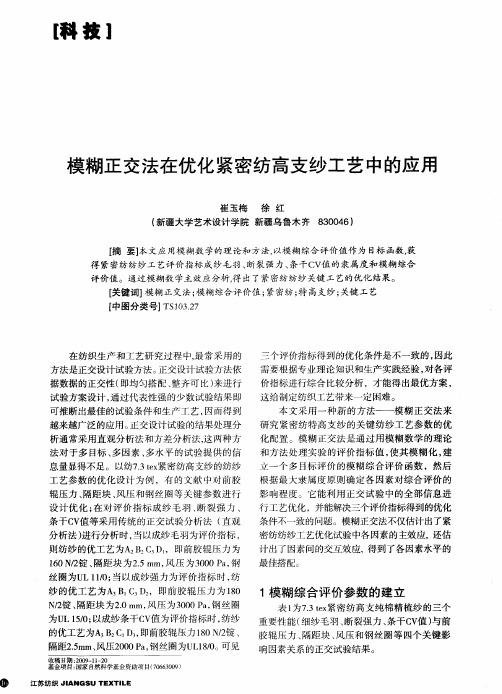
1
2 3
4 5 6
(= , , ,) B n l2 … 9为 的隶 属 度 , 即模糊 综 合 评 价值 ,
钢
3 am 断裂强 条于  ̄m 毛羽 总 0
/N o
具体 值见 表2 。 表2 :正 交试 验设 计 及评 价指 标 的隶属 度 和模 糊
条 干C 值 等采 用 传统 的正 交试验 分析 法 ( 观 V 直
分 析法 ) 进行分 析时 , 当以成纱 毛羽 为评价 指标 ,
影响程度 。它能利用正交试验 中的全部信息进 行工艺 优化 ,并能解决三个评 价指标得到 的优化 条件不 一致 的问题 。模 糊正交法不仅估计 出了紧
密 纺纺纱工艺 优化试验 中各 因素 的主效 应,还估
综合 评价 值表
实验号 前 搬 隔 距 脏 c H 压尢 ^ 块B / 锭 /m N积 m 钢丝圈D 3
数
1 10 4 2O 3 ㈨ l/ 5o 0 0 g 42 023 g 0 0 l l7
1( 0 1 ) 4
2 (6 ) 10 3 (8 ) 10
1 2 3
1(.) 20
l 1
2 ( ) 25 2 2
3f 。) 2( /) 7 3 0 0 1 0 .0 5
1 0 0) l( l O 2 3 0 1/ ) . 2 5 0) 3 (8 O 3 5 O 1/ ) .
2 3 1 1 3 2 65 . 12 . 41 .
[ 关键词 】 糊正 交法 ; 糊综合评 价值 ; 模 模 紧密纺 ; 高支纱 ; 特 关键 工 艺 【 中图分 类号】 S 0 .7 T 13 2
浅析紧密纺细纱CVb的控制措施

半制品质量控制要求:(1)梳棉标准重量控制在±1.0g以内,超出±2g,通知轮班长,追溯已经纺出的条子并隔离处置。
(2)精梳整套进行落棉测试,要求整套落棉率控制在±0.5%以内,超出封车;整套棉结按照平均+3粒控制,超出封车;单机台棉结按照内控标准进行控制。
(3)末并重量控制在±0.2g以内,超出±0.3g的条子不能使用,并需要追溯已经纺出的所有条子,包括粗纱机后条子,如已经纺出粗纱,也要全部追回。
(4)粗纱重量控制在标准重量±0.15g以内,超出标准的粗纱不能使用,并需要追溯所有已经纺出的所有粗纱,包括细纱已经上机的粗纱,已经纺出的管纱要进行隔离处置。
(5)各工序所有的机械波高度不能超出基波的两倍,超出基波的3/2封锭处理,超出2倍的,追溯已经纺出的成品、半成品。
(6)细纱重量超出±1.2%封车处理,超出±2.2%必须落纱,单独隔离,重新做开车试验,直至试验合格,才能开车。
(7)细纱捻度超出标准±5捻必须落纱单独隔离,直至开车试验合格方能开车。
(8)细纱条干控制在平均条干±0.5%以内,超出标准封车处理,直至合格方能开车。
2.2 前纺精细化管理前纺精细化管理主要体现在对隐形质量因素的控制。
清花各单机要做到精细化开松,严格控制回条、再用棉的使用比例,一般原则是精梳纱回用比例不超过3.5%,7.3tex 及以下号数不超过1.5%。
使用过程中要重视再用棉本身的打包密度和排包位置。
密度最好是与棉包接近或一致,回条必须扯断后再回用,建议扯断的长度低于30cm,回花包摆放在中间预留的有效包位上,保证混合均匀。
在各工序的条子要采用可追溯制管理措施,每一筒条子均能够找到生产台位、责任人及生产时间,以利于不合格半成品的追溯,同时杜绝同台并合,要采用大交叉混合方式,以保证混合均匀度。
精梳台差落棉率控制在0.5%以内,眼差控制在0.2%以内,逐眼对梳理隔距、落棉隔距及毛刷隔距进行校正,保证设备状态的一致性。
提高纱线强力的具体措施

提高纱线强力的具体措施1.增强原材料选择与管理:优质的原材料是生产高强度纱线的基础。
提高原材料的强力可以通过选择纤维长度、直径和强度等参量来实现。
此外,合理管理原材料也非常重要,包括对原材料的存储、保养和处理等方面,以确保不受湿度、温度等影响。
2.优化纺丝工艺:纺丝工艺对纱线强力有着直接的影响。
通过优化纺丝机的调整和控制,可以提高纱线的均匀性和强力。
例如,合理设定纺纱机的转速、张力等参数,确保纤维在纺纱过程中得到充分拉伸,提高纱线的断裂强度。
3.采用特殊纺纱方法:一些特殊的纺纱方法可以提高纱线的强力。
例如,空气纺纱可以通过高速旋转的喷嘴将纤维打散,并在空气流中重新结合,形成较强的纱线。
此外,还有自旋纺纱、喷丝纺纱等方法也可以用于提高纱线的强度。
4.强化拓扑结构设计:纱线的拓扑结构也会对其强力产生影响。
合理设计纱线的组织结构,例如增加捻度、改变纱线的交叉方式等,可以提高纱线的抗撕裂和抗拉伸能力。
同时,通过选择合适的纺纱技术和纱线类型,也可以提高纱线的强力。
5.引入强化剂:纱线的强力还可以通过引入一些强化剂来实现。
例如,可以添加纺织助剂、增加纤维的拉伸性能,提高纱线的强度。
或者,可以采用纳米纤维增强剂等技术,增加纱线的结合力和拉伸能力。
6.质量控制和检测:强力的提高离不开对纱线质量的严格控制和检测。
在生产过程中,应建立完善的质量管理体系,包括对原材料、中间检验和成品检验等环节进行监控。
定期检测纱线的强力参数,例如断裂强度、弯曲性能等,及时发现问题并采取措施进行纠正。
7.加强员工培训和技术交流:纺织行业是一个技术密集型行业,人力资源的素质和技术水平直接影响纱线强力的提高。
加强员工培训和技术交流,提高员工的专业技能和纺织知识,同时也鼓励员工参与相关行业的研讨会、展会等,积极学习和借鉴先进的纺织技术和生产经验。
总之,提高纱线强力需要综合考虑原材料选择与管理、纺丝工艺优化、特殊纺纱方法应用、拓扑结构设计、引入强化剂、质量控制和检测等方面。
紧密塞络纺棉纱关键影响因素的优化设计
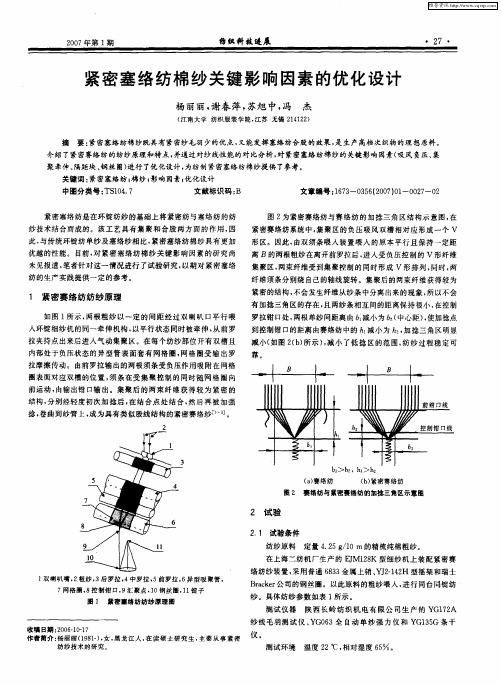
中图分 类号 : S0+ T 147
文献标识码 : B
文章编 号 :63 0 5(O7O一O2一O 17- 3620)1 07 2 图2 为紧密赛络纺与赛 络纺 的加捻三 角区结 构示意 图, 在
紧密赛络纺系统 中, 聚区 的负压吸风 双槽 相对 应形成 一个 V 集
紧密塞络纺是在环 锭纺纱的基础上将 紧密纺与塞络 纺的纺 纱技术结合而成的 。该 工艺 具有集 聚和 合股 两方面 的作用 , 因 此, 与传统环锭纺单纱 及塞络纱相 比,控制 的 同时形成 V形 排列 , 同时 。 两 纤维须条分别绕 自己的轴线旋转。集聚后的两束 纤维获得较为
紧密 的结构 。 不会 发生纤维从纱条 中分离 出来 的现 象, 以不会 所
1 紧密赛络纺纺纱原理
如图 1所示 , 两根 粗纱 以一定 的间距 经过双 喇叭 口平行 喂 入环锭 细纱机的同一牵伸机 构, 以平行状态 同时被牵 伸 , 前罗 从
维普资讯
20 年第 1 07 期
纺织科 技避 展
・ 2 7・
紧密 塞络纺棉 纱关键 影响 因素 的优化设计
杨 丽丽, 谢春 萍 , 苏旭 中, 杰 冯
( 江南大学 纺织服装学院, 江苏 无锡 2 4 2 ) 112
摘
要: 紧密塞络 纺棉 纱既具有 紧密纱毛羽少的优 点 , 又能发 挥塞络纺合股 的效果 , 是生产 高档 次织物的理 想原料 。
卜 — +
、
…
结构 , 分别经轻度初 次加 捻后 , 结合点 处结 合 , 后再 被加 强 在 然
捻, 卷曲到纱管上 , 为具有类似股线结构 的紧密赛络纱 _ 。 成 1 ]
2 b
… —钳 —口 l I 线 — 一 一 — 前
环锭纺改紧密纺,纺纯棉高支纱的功能

环锭纺改密纺纺纯棉高支纱的功能在纺织行业中,环锭纺改密纺纺纯棉高支纱是一个备受关注的话题。
通过对这一主题的深入探讨,我们可以更好地理解纺纱技术的发展与应用。
本文将从纺织工艺、纺纱机械、产品功能等方面展开讨论,以全面评估环锭纺改密纺纺纯棉高支纱的功能。
1.纺织工艺纺织工艺是指纺纱、织造和印染等生产工艺的总称。
而在纺纱方面,环锭纺和临界密度纺纱是两种主要的纺纱技术。
环锭纺是一种传统的纺纱技术,它适用于纤维长度短、纤维强度低的原料。
而密纺则是一种先进的纺纱技术,通过调整纱线的结构和形态,提高纺纱密度,增加纱线的紧凑度和强度。
环锭纺改密纺纺纯棉高支纱可以在提高产品品质的降低生产成本,提高效率。
2.纺纱机械对于纺纱机械来说,环锭纺改密纺需要更先进的机械设备来实现。
从纤维进料、预并条、精梳预并、前纺、织布和印染等多个环节都需要进行技术更新和设备优化。
密纺技术的应用可以提高纱线的成形度和整齐度,减少纱线的断头和断代现象,提高纱线的生产效率。
3.产品功能对于纺纱产品的功能,环锭纺改密纺纺纯棉高支纱的功能有以下几个方面:产品的手感更加柔软,穿着舒适,吸湿透气,对皮肤友好;纱线的强力和抗张性能更强,使得面料更加牢固耐磨;再次,纱线的细度更高,纺织的面料稠密度更大,达到更好的遮阳性能和防晒效果。
总结回顾纺织的环锭纺纱改密纺技术在纺织行业中的应用,对于产品品质和性能的提升起到了积极的作用。
通过先进的纺纱机械设备和工艺技术,生产出的高支纱产品在柔软、强力、细度和透气等方面都达到了更高的要求。
这在一定程度上改变了传统纺织品的功能和品质,也提高了消费者对纺织产品的体验和需求。
个人观点从我个人的角度来看,环锭纺改密纺的技术应用不仅提高了纺织品的功能和性能,也促进了纺织行业的发展。
随着科技的不断进步,纺织技术也在不断创新和改进,我们有理由相信,在未来的发展中,环锭纺改密纺技术会有更广阔的应用前景。
在文章讨论中,我多次提到了指定的主题“环锭纺改密纺纺纯棉高支纱”的相关内容,以确保文章内容的丰富性和观点的深刻性。
- 1、下载文档前请自行甄别文档内容的完整性,平台不提供额外的编辑、内容补充、找答案等附加服务。
- 2、"仅部分预览"的文档,不可在线预览部分如存在完整性等问题,可反馈申请退款(可完整预览的文档不适用该条件!)。
- 3、如文档侵犯您的权益,请联系客服反馈,我们会尽快为您处理(人工客服工作时间:9:00-18:30)。
紧密纺高支纱关键工艺影响因素的优化
冯杰,谢春萍,苏旭中,杨丽丽
(江南大学纺织服装学院,江苏无锡214122)
摘要:介绍了在改造后的紧密纺细纱机上,对紧密纺高支纱关键工艺因素进行了正交实验并做了分析,期望找到合理的工艺配置。
关键词:纺纱;高支纱;紧密纺;关键因素;工艺;优选设计
中图分类号:TSl04.31 文献标识码:A 文章编号:11301-2044(2006)10—0014—02 Optimized design of key factors affecting compact—spun high count cotton yarn FENG Jie,XIE Chun—ping,SU Xu—zhong,YANG Li—li
(College of Textile and Garment,Se~:thern Yangtze University,Wuxi 214122,China) Abstract:Compact—spun yarn is superior in performance.In this article,orthogonal tests on the key factors affecting compact—spun highcount cotton yarn were done on the modified compact—spinning frame to try to find out a reasonable processing technology.
Key words:spinning:high counts yarn:compact—spun;key factors;process;decision design 在紧密纺细纱机牵伸装置前面增加气动集束区等装置,可大大减少须条宽度与纱线直径的比值,使加捻三角区变得非常小,减少纱线的毛羽和飞花,同时也提高了纱线的强力。
1 实验部分
实验机型为改造的EJMl28k—SM型细纱机,采用吸风负压的集聚方式,锭速为10 000 r/min,采用普通6833金属上销、YJ2—142H型摇架,钢丝圈为瑞士Bracker公司的ULl0/0,异形管负压2 700 Pa。
以9.7 tex纯棉精梳纱为原料,研究隔距块、后区牵伸倍数、细纱捻度和前胶辊加压量4个关键因素对紧密纺高支纱成纱质量的影响。
具体方案见表1。
(34)正交实验方案
表1 L
2.1 单纱性能的测试
纱线的品质主要从纱线毛羽、单纱强力和条干均匀度变异系数3方面评定。
因此,实验主要测试了管纱单纱以上3个性能指标。
表2中给出了紧密纱和普通环锭纱的3—9 mm毛羽总数、断裂强力和条干均匀度变异系数的平均值。
表2单纱的性能指标
2.2实验数据分析
2.2.1关键因素对单纱毛羽的影响
对于4个因素,算出各个水平相应的3次3~9mm毛羽根数之和与极差,如表3。
表3 因素各列3毛羽水平之和与极差根·(10m)-1
由表3可知:
(1)通过极差分析,前胶辊加压量对毛羽的影响较大,可能是重要的因素;细纱捻度、后区牵伸倍数和隔距块对毛羽的影响比较小,可能是次要的因素。
(2)通过各因素水平之和的比较和分析,对毛羽影响好的水平组合是前胶棍加压量为160 N/双锭、隔距块为2.8 mm、后区牵伸倍数为1.21、细纱捻度为l 065.6捻/m。
2.2.2关键因素对单纱强力的影响
对于4个因素各列,算出各个水平相应的3次单纱强力之和与极差,见表4。
表4 因素各列单纱强力水平之和与极差
由表4可知:
(1)通过极差分析,前胶辊加压量、细纱捻度、后区牵伸倍数和隔距块对单纱强力的影响都比较大,说明4个因素都比较重要;尤其是隔距块和前胶辊加压对单纱强力的影响更为突出。
(2)通过各因素水平之和的比较和分析,对单纱强力影响好的水平组合是前胶棍加压量为180 N/双锭、隔距块为2.5 mm,后区牵伸倍数为1.21,细纱捻度为1 155.6桫m。
(3)前胶棍压力对单纱强力的影响呈单调递增性。
但是前胶棍压力180 N/双锭是前胶辊的最大加压,结合使用寿命考虑,不适合长期使用,所以选用前胶辊压力为160 N/双锭。
2.2.3关键因素对单纱条干均匀度变异系数的影响
对于4个因素各列,算出各个水平相应的3次单纱均匀度变异系数之和与极差,见表5。
(1)通过极差分析表明,前胶辊加压、细纱捻度和隔距块对单纱均匀度变异系数的影响都比较大,说明是重要的因素;后区牵伸倍数对单纱均匀度变异系数的影响比较小,可能是次要的因素。
(2)通过各因素水平之和的比较和分析,对单纱强力影响好的水平组合是前胶辊加压量为160 N/双锭、隔距块为2.8.mm、后区牵伸倍数为1。
21、细纱捻度为l 225.8捻/m。
从以上的讨论分析可知,根据摇架的寿命、能耗等要求,最后确定最好的水平组合是前胶辊加压量为160 N/双锭、隔距块为2.5 mm、后区牵伸倍数为1.21、细纱捻度为1 225.8捻/m。
在这一水平下所纺纱线的性能指标是:3—9rnm毛羽总数1.9根/10m,断裂强力236.9 cN,条干Cyl2.40%。
3 结论
(1)前胶辊加压量对毛羽的影响较大,好的水平组合是前胶辊加压量为160 N/双锭、隔距块为2.8 mm、后区牵伸倍数为1.21、细纱捻度为l 065.6捻/m。
(2)前胶辊加压量、细纱捻度、后区牵伸倍数和隔距块对单纱强力的影响都比较大,说明4个因素都比较重要,好的水平组合是前胶辊加压量为180 N/双锭,隔距块为2.5 mm,后区牵伸倍数为1.21,细纱捻度为1 155.6捻/m。
(3)前胶辊加压、细纱捻度和隔距块对单纱均匀度变异系数的影响都比较大,好的水平组合是前胶辊加压量为160 N/双锭、隔距块为2.8 mm、后区牵伸倍数为1.2l、细纱捻度为1225.8捻/m。
参考文献:
[1] 吴有炜.实验设计与数据处理[M].苏州:苏州大学出版社,2002.。