42109损失率总结
16大损失指数定义及公式说明

阻碍原物 能源损失
给他们带 来增值的
料效率化 成品率损失 的3大损 工具损失
那些资源
完成后批量等待
沟通差
没有综合
频率不理想
时间损失
安全库存大
没有同步
设备效率低
试机时间长
运输效率低
产品价值
价值损失
服务价值 要求与质量绩效表现
交货服务
定义 计划内停机时间损失=(日历时间-计划生产时间)
4项停机时间损失=(计划生产时间-实际生产时间)
损失 基本分类 类别 16大损失
பைடு நூலகம்
停机损失
故障损失(故障停机)
更换产品、规格、材料损失(准备与调整)
阻碍设备 工具更换损失
效率化的 热机损失(含清洁)
8大损失 短暂闲置损失
速度下降损失
缺陷损失
成本损失
返工损失
管理损失
阻碍人效 操作动作损失
率化的5 编程损失
损失:指
大损失 物流损失
未被最终
测算调试损失
客户认可
短停闲置损失(极小损失)=(设备非运转时间-计划停机时间-4项停机时间损失) 速度下降损失=(1-产能速度/理想产能速度)*实际生产时间-短停闲置损失 属于机器时间缺陷损失,且=(1-合格率)*(纯轧制时间-速度损失时间-短停闲置损失)
指材料等待损失 设备停机时间损失(维修) 自动操作失灵损失 材料不足、移动损失 缺陷人工时间损失 热机损失、超载损失、温度损失、辅助材料的损失 质量缺陷损失、生产过程损失、重量损失、过度使用的损失 备品备件、工具、夹具的损失 产品发运前等待 沟通时间长、信息不正确产生延误 两个组织之间的复制,重复工作 造成配合间下工序的等待时间。 对未料事件的额外保护(备件库存、产品库存) 由于计划不好导致没能在正确的时候连续开展活动 总体设备效率低导致的加工时间厂 由于复杂的试机活动导致的准备时间长 物流阶段之间的运输时间太长 与产品质量服务有关 与售后服务有关 与产品服制造过程有关 与制造过程业务过程有关
谈谈设备六大损失,保持零故障

谈谈设备六大损失,保持零故障
一、概念认识
1.设备效率
设备效率是指利用设备进行生产施工所产生的附加值的一种测度。
附加值是由全部收入减去全部资源成本(材料和劳动力等)而形成的,然后分解为利润、工资和税金。
2.设备综合效率
设备综合效率=时间开动率×性能开动率×合格品率
时间开动率、性能开动率、合格品率是由每一工作中心决定的,但每个因素的重要性,因产品、设备和涉及生产系统的特征不同而异。
例如,若机器故障率很高,那么时间开动率会很低;若设备的短暂停机很多,则性能开动率就会很低,只有三者数值都很大时,设备综合效率才会提高。
二、找到设备六大损失
设备综合效率。
这个指标与六大损失相关联,所以首先必须认识设备的六大损失,这六大损失是指:
故障/停机损失
换装和调试损失
空闲和暂停损失
减速损失
质量缺陷和返工
启动损失
对于以上六种损失,人们往往对于故障这种显性的损失能够一眼发现,但是对后面五种损失,很多人都是熟视无睹,甚至都没有把它们当作一种损失来看待。
三、改善慢性损失,向零故障挑战
明确了六大损失,也就有了三个可以测量的指标,第一个是时间开动率指标,第二个是性能开动率指标,第三个是合格品率指标。
计算公式分别如下: 时间开动率=净运行时间/运行时间
性能开动率=实际生产数量/理想生产数量
合格品率=合格品数/总产品数
企业可以通过这三个可测量的指标去改善以上六大损失,向零故障进军。
生产LOSS分析(CN)
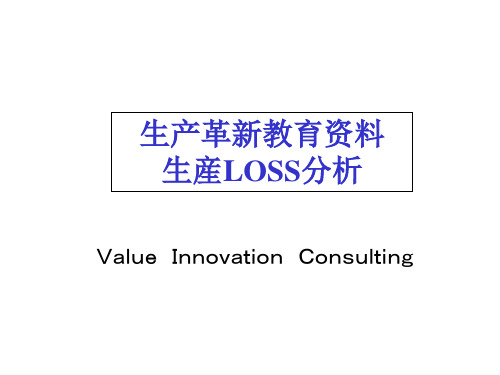
作业效率 产量H
投入H
→1.08(108%) 60%提高
目标展开
現状値
目標値
0.67(675%) → 0.87(87%)
7590分 → 11185分
ST/台
1.9分
=30sec
⑤ 稼动损失
=(PT-CT)×人员×良品数=(60-45sec)×5人×460台
=34,500sec(575分)
⑥ 编制损失
=(CT-AT)×人员×良品数=(45-39sec)×5人×460台
=13,800sec(230分)
⑦ 技能损失
=(AT-MT)×人员×良品数=(39-30sec)×5人×460台
手顺2 制作产线配置表 ② 产线配置表(1/100)
手顺3 制作产线编制效率表 ③ 间隔图表
手顺4 进行产线稼动实况调查 ④ 稼动实况调查表
手顺5 进行生产损失分析 ⑤ 生产损失分析表 ⑥ 产线作业损失分析表
手顺6 设定目标值,进行目标展开 ⑦ 目标值设定表 ⑧ 目标展开表
手顺7 整理行动计划 ⑨ 行动计划
H2= A/P×N 表示包括管理损失在内的编制程度
生产线平衡性的基本概念
关于生产线平衡性,通过以下对策来实现目标。
作业的分工、结合、类似作业的汇总 作业的改善(作业手顺、方法的改善、治工具的使用) 先行顺序・考虑难易度不均衡 考虑了作业者能力的配置(技能损失) 领跑者的设置 发生转产、不良、瞬间停机情况的对应
0 1
间隔时间:60DM (瓶颈时间)
4工序的 损失时间 (停机时 间):
各种损失率计算公式[会计实务优质文档]
![各种损失率计算公式[会计实务优质文档]](https://img.taocdn.com/s3/m/171568fb9b89680203d825ad.png)
财会类价值文档精品发布!
各种损失率计算公式[会计实务优质文档]
提到损失率,各行各业都有,本文主要介绍质量损失率、坏账损失率,以及采矿损失率和矿石贫化率的计算公式。
一、质量损失率
质量损失率是一定时期内企业内部和企业外部质量损失成本之和占同期
工业总产值的比重,是表征质量经济性的指标。
为降低废品、减少损失,企业工艺要在设计、工艺技术等软件方面和材料、设备等硬件方面进行协调配套创新。
质量损失率的计算公式为:
质量损失率=(配件价格+返工费)/同批次产品的市场价值
二、坏账损失率
坏账率的公式其计算公式为:坏账率=年坏账额/年赊销总额分析这个指标时,主要是企业自己现在与历年对比,看是否下降。
如果与同行业别的企业作横向比较时,要注意计算口径的不同。
有的企业把全部销售额作分母,对坏账的定义也有差别,有的企业把逾期6个月视为坏账,有的把逾期一年视为坏账。
企业应参照财务规定制定自己的计算口径。
坏账核算坏账准备是企业对预计可能无法收回的应收票据、应收账款、预付账款、其他应收款、长期应收款等应收预付款项所提取的坏账准备金。
计提坏账准备的方法由企业根据历史经验,债务单位财务情况及相关信息,合理估计,提出目录和提取比例经企业董事会批准执行。
计提坏账准备金是通过“坏账准备”账户进行核算的,企业在年度终了时,应对应收账款进行全面检查,预计各项应收款项发生减值的,应当计提坏账准备。
其账务处理如下:1.企业在提取坏账准备时,应借记“资产减值损失——计提坏账准备”账户;。
事故复杂率计算公式

事故复杂率计算公式事故是指在生产、工作、生活等活动中,由于人为或自然原因所造成的不幸事件。
事故的发生对个人、家庭甚至整个社会都会造成不同程度的影响,因此预防事故的发生至关重要。
为了更好地预防事故,需要对事故的复杂程度进行评估和分析。
事故复杂率是评估事故复杂程度的一个重要指标,它可以帮助我们更好地了解事故的性质和影响,从而采取相应的措施进行预防和应对。
事故复杂率计算公式是评估事故复杂程度的一种数学模型,它可以通过对事故发生的各种因素进行综合分析,得出一个具体的数值,用以表示事故的复杂程度。
事故复杂率计算公式通常包括事故的严重程度、事故的影响范围、事故的原因等多个方面的因素,通过对这些因素进行综合考量和权衡,得出一个综合的复杂率指标。
事故的严重程度是评估事故复杂率的重要因素之一。
事故的严重程度可以通过事故造成的人员伤亡和财产损失来衡量。
一般来说,造成人员伤亡和财产损失较大的事故,其复杂率也会相对较高。
因此,在计算事故复杂率时,需要对事故的严重程度进行充分考量,以确保评估结果的客观性和准确性。
事故的影响范围也是评估事故复杂率的重要因素之一。
事故的影响范围可以通过事故对周围环境和社会造成的影响来衡量。
一般来说,影响范围较大的事故,其复杂率也会相对较高。
因此,在计算事故复杂率时,需要对事故的影响范围进行充分考量,以确保评估结果的全面性和准确性。
事故的原因也是评估事故复杂率的重要因素之一。
事故的原因可以通过事故发生的背景和诱因来衡量。
一般来说,由于多种原因导致的事故,其复杂率也会相对较高。
因此,在计算事故复杂率时,需要对事故的原因进行充分考量,以确保评估结果的科学性和准确性。
事故复杂率计算公式的具体形式可以根据实际情况进行调整和完善。
一般来说,事故复杂率计算公式可以采用加权平均法,通过对事故的严重程度、影响范围和原因等因素进行加权平均,得出一个综合的复杂率指标。
在具体计算时,可以根据不同的事故类型和特点,确定不同的权重系数,以确保评估结果的科学性和准确性。
OEE计算及损失分析

LOSS
12 . 速度损失 12.1 速度减慢 12.2 空转和短暂停机
质量合格率
定 义
良品在实际产出中的占比
公 实际产出 –不良品数量
式
实际产出
LOSS
14 . 质量损失 14.1 不良品
OEE 结构图解释
1. 日历时间
日 历 时 间
间法 定 非 工
作
时
1.
2.
日历上理论的天数时间. •每周168 小时 (24*7) •每年8,760 小时( 24*365 )
• 是指从一种产品至另一种产品 换产导致的停机损失
• 包括:
首次清洁消毒 再次清洁消毒 产品批次转换调整
备注: 1. 产品转换是指不同产品之间的转换,清洁消毒的停机
损失,停机代码记为08 2. 同样的产品隔了一段时间重新开订单的清洁消毒的停
机损失,停机代码记为11
9. 计划停机损失
生
清
(闰年为8,784 小时)
2. 法定非工作时间
日 历 时 间
间法 定 非 工
作
时
1.
2.
•因政府法规规定不允许 工作的时间
•包括:
法定假日 周未
3. 法定工作时间
法 定 工 作 时
间非 负 荷 时
负 荷 时 间
用 餐
间
•法定可用于生产的时间: • 法定工作时间 = 日历时 间 –法定非工作时间
OEE 计算及损失分析
内容
OEE 结构图 生产线利用率的定义 OEE 的定义 OEE 结构图解释 OEE 的计算 OEE 的损失 OEE 的图表 案例
OEE 结构图
生产线利用率
日 间法
OEE计算及损失分析

生产线利用率的定义
生产线利用率:用于衡量一条产线的有效利用时间。
生产线利用率 =
负荷时间 法定工作时间(24*249)
•负荷时间= 运行时间+停机时间+用餐时间 •法定工作时间 = 24小时/天 * 249天/年
= 5,976 小时/年
OEE的定义
定义 公式
OEE(设备综合效率) 用来表现实际的生产能力相对于理论产能的比率
5.
6.
• 非纽崔莱用餐时间= 40分钟
• 纽崔莱用餐时间= 50分钟
• 用餐超过40分钟(非纽崔莱)或 50分钟(纽崔莱)的时间为非计 划停机时间
7. 生产时间
• 是指计划排产后可用于生产的时间
生
清
产
洁
计
时
消
划
间
毒
停
损
机
失
损
失
非 计 划 停 机
运 行 时 间
损
失
7.
8.
9.
10. 11.
• 生产时间 = 负荷时间 – 用餐时间
3. 4.
5.
6.
–每天,每周,或每月的计划维护保养或清洁卫生 –与生产计划不相关的活动
➢ 非售卖产品的试产及返工(例如: R&D 试产) ➢ 管理停止
–行政管理活动(例如: 消防演习) –由管理层决定的暂停生产(例如:盘点) –外部原因造成的停水、停电
5. 负荷时间
法
定 工 作
非 负 荷
时 间
时 间
• 设备PQ的UPM • 设备达到并可维持的最好UPM • 依据类似设备经验的估计值(如业界标准)
备注: 1. UPM由IE小组进行更新及维护。
安全系统工程事故树分析3

? 在目前情况下,可以通过系统长期的运行经验, 或若干系统平行运行过程粗略地估计平均故障 间隔期,其倒数就是所观测对象 (元件或部件 )的 故障率。故障率数据举例于下页表。
事故树定量分析
4 事故树分析
4.8 最小割集和径集在事故树分析中的作用 4.9 结构重要度分析 4.10 基本事件的发生概率 4.11 顶上事件发生概率的计算 4.12 概率重要度和临界重要度分析 4.13 事故树分析的应用
事故树定量分析
4.11.1 最小割集法
? 用最小割集可以表示原事故树的等效图,等效 图的标准结构形式是:顶上事件 T 与最小割集 Ei的逻辑连接为或门,每个最小割集 Ei 与其包 含的基本事件 xi 的逻辑连接为与门。 例:
事故树定量分析
人为失误的情况
?1961年,斯文(Swain)和鲁克(Rock) 提出了
“人的失误率预测法”(THERP) ,其分析步 骤为:
(1)调查被分析者的操作程序; (2)把整个程序分成各个操作步骤; (3)把操作步骤再分成单个动作; (4)根据经验或实验,适当选择每个动作的可 靠度; 如阅读技术说明书的可靠度 R = 0.9918, 读电流计和流量计的 R = 0.9945,安装安全锁线 的R = 0.9961 ,分析锈蚀和腐蚀的 R = 0.9963 。
4.10.1 机械设备的故障概率 1)可修复系统
?单元(部件或元件 )的故障概率为:
q?
MTTR
MTTR? MTBF
事故树定量分析
生产线平衡率

生產線平衡率比較單一,而如果是產品工序或制造工序平衡率就比較復雜。
生產線平衡定義:就是對這條線的全部工序(工位)進行平均化,調整各工序(工位)作業負荷,以使各工序(工位)作業時間盡可能相近。
如果計算生產線平衡率或者是損失率的話,首先要理解兩個概念:節拍與瓶頸節拍:就是我們平時“散裝”英語所說Cycle time,也就是完成一個工序(工位)的生產周期時間﹔瓶頸:就是我們平時“散裝”英語所說Bottleneck,也就是整個工序(工位)里面最慢的那個工序(工位)生產線平衡率=各工序(工位)時間總和/bottleneck Cycle time*工序(工位)數*100%例如A生產線生產A機種有5個工位,每個工位Cycle time分別是10秒.8秒.9秒.10秒.11秒,那么Bottleneck Cycle time就是11秒。
計算公式:A生產線生產A機種平衡率=(10+8+9+10+11)/(11*5)*100%=48/55*100%=87.27%生產線損失率=1-平衡率﹔A生產線生產A機種損失率=1-87.27%=12.73%由以上例子可以看出,工序(工位)作業時間平衡有多重要了...產品工序或制造工序平衡率也是這個思路,慢慢想想也就通了...生产线平衡即是对生产的全部工序进行平均化,调整作业负荷,以使各作业时间尽可能相近的技术手段与方法。
目的是消除作业间不平衡的效率损失以及生产过剩。
生产线平衡是一门很大的学问,生产线平衡直接关系到生产线的正常使用。
生产线平衡指南主要包括生产线平衡的相关定义、生产线平衡的意义、工艺平衡率的计算、生产线平衡的改善原则和方法。
(Line Balancing)如何指派工作予工作站的决策过程,及使各个工作站负荷一样,便称之为生产线平衡。
Line Balancing (LB), is the problem of assigning operations to workstations along an assembly line, in such a way that the assignment be optimal in some sense.节拍、瓶颈、空闲时间、工艺平衡的定义流程的“节拍”(Cycle time)是指连续完成相同的两个产品(或两次服务,或两批产品)之间的间隔时间。
质量损失率与相对动弹模
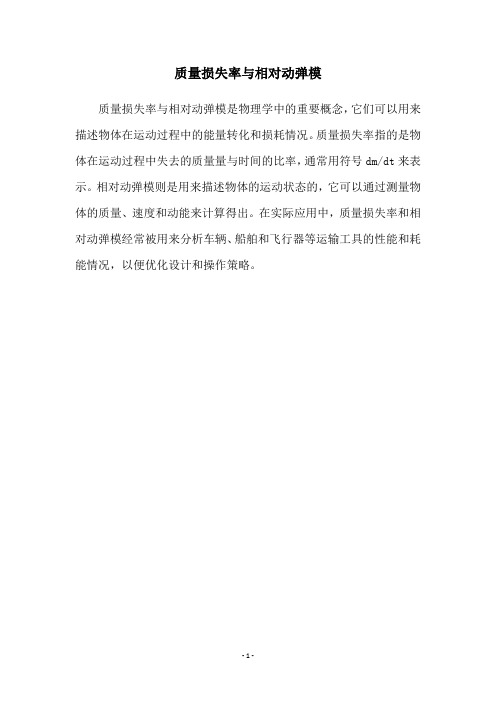
质量损失率与相对动弹模
质量损失率与相对动弹模是物理学中的重要概念,它们可以用来描述物体在运动过程中的能量转化和损耗情况。
质量损失率指的是物体在运动过程中失去的质量量与时间的比率,通常用符号dm/dt来表示。
相对动弹模则是用来描述物体的运动状态的,它可以通过测量物体的质量、速度和动能来计算得出。
在实际应用中,质量损失率和相对动弹模经常被用来分析车辆、船舶和飞行器等运输工具的性能和耗能情况,以便优化设计和操作策略。
- 1 -。
输变电设备故障引起要素损失概率的取值表

输变电设备故障引起要素损失概率的取值表一、统计原则:样本数量越多越能够逼近故障损失发生概率的真实值。
样本涉及范围越广越能涵盖所有故障部件四个要素的损失概率。
样本数据要真实可靠。
二、样本的统计步骤:第一步,统计样本,按照故障部件,设备损坏、人身安全、供电可靠性和社会影响四个要素的损失程度组织,用简短的语句描述。
第二步,统计每一个样本,确定样本是属于七个部件中的哪一个故障部件,并在对应的部件上加1,确定样本的设备损坏、人身安全、供电可靠性、社会影响等级,在对应位置加1。
例如:样本01x><#>主变是%>变压器厂XX年XX月生产,电压等级为110kV,在元月1 日风冷改自冷主变吊罩检查中,发现A、B、C三相高压线圈端部第一线饼导线扭曲,B相上部压环破碎,经返厂解体检查发现b相低压线圈中部已严重变形,要求XX压器厂重绕三相高低线圈。
非计划停运事件为768小时。
1)故障部件属于绕组。
2)四个要素的损失程度等级(1)设备损坏:因为重绕三相高低线圈,且电压等级为110kV,直接经济损失大于500 万人民币,因此属于重大设备损坏事故。
(2)人身安全:无人身伤亡事故。
⑶供电可靠性:非计划停运事件为768小时〉一周。
(4)社会影响:因为设备停电时转移了负荷,没有造成用户停电,没有发生火灾灯恶性事件,因此无社会影响。
即:第三步,将所有样本统计后,按照下式计算部件的损失概率n ikPOF jk 」100%n式中n i - 故障发生总次数POF jk - 要素在某一损失等级下的概率j - 损失要素k - 要素的损失等级第四步,按照统计原则,不断加入新的样本,以逼近部件损失概率的真实值。
三、统计范例1统计时间尺度:2004〜2007年第一季度。
2、统计范围:某省范围内110 (66) kV及以上变压器。
3、统计内容:发生在某省范围内的变压器非计划停运、故障、返厂解体事件,剔除统计范围内样本的重复部分。
损失率报告和总结
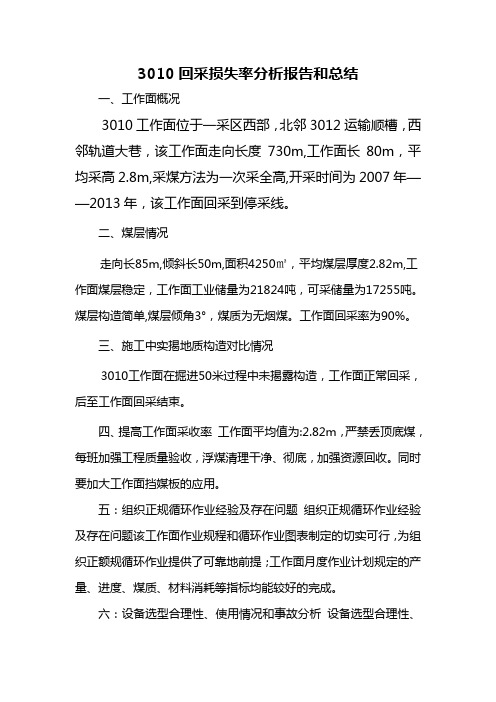
3010回采损失率分析报告和总结
一、工作面概况
3010工作面位于一采区西部,北邻3012运输顺槽,西邻轨道大巷,该工作面走向长度730m,工作面长80m,平均采高2.8m,采煤方法为一次采全高,开采时间为2007年——2013年,该工作面回采到停采线。
二、煤层情况
走向长85m,倾斜长50m,面积4250㎡,平均煤层厚度2.82m,工作面煤层稳定,工作面工业储量为21824吨,可采储量为17255吨。
煤层构造简单,煤层倾角3°,煤质为无烟煤。
工作面回采率为90%。
三、施工中实揭地质构造对比情况
3010工作面在掘进50米过程中未揭露构造,工作面正常回采,后至工作面回采结束。
四、提高工作面采收率工作面平均值为:2.82m,严禁丢顶底煤,每班加强工程质量验收,浮煤清理干净、彻底,加强资源回收。
同时要加大工作面挡媒板的应用。
五:组织正规循环作业经验及存在问题组织正规循环作业经验及存在问题该工作面作业规程和循环作业图表制定的切实可行,为组织正额规循环作业提供了可靠地前提;工作面月度作业计划规定的产量、进度、煤质、材料消耗等指标均能较好的完成。
六:设备选型合理性、使用情况和事故分析设备选型合理性、
使用情况和事故分析该工作面选型合理,在回采过程中设备使用基本正常。
加强対刮板司机的培训和监督,严禁司机在开车时睡觉,加强设备检修,以确保设备的正常运转。
3010工作面2007 年开始正常回采,由于我矿对本工作面的重视,加强现场管理和安全教育培训,切实提高职工的技能水平和按章操作意识,于2013年结束,实现了安全回采。
{品质管理品质知识}质量损失函数

{品质管理品质知识}质量损失函数质量损失函数日本质量管理学家田口玄一(Taguchi)认为产品质量与质量损失密切相关,质量损失是指产品在整个生命周期的过程中,由于质量不满足规定的要求,对生产者、使用者和社会所造成的全部损失之和。
田口用货币单位来对产品质量进行度量,质量损失越大,产品质量越差;反之,质量损失越小,产品质量越好。
一、质量特性产品质量特性是产品满足用户要求的属性,包括产品性能、寿命、可靠性、安全性、经济性、可维修性和环境适应性等。
(与前描述是否一致)(一)质量特性分类田口先生为了阐述其原理,对质量特性在一般分类的基础上作了某些调整,分为计量特性和计数特性,如图1所示。
1、望目特性。
设目标值为m,质量特性y围绕目标值m波动,希望波动愈小愈好,则y就被称为望目特性,例如加工某一轴件图纸规定φ10±0.05(mm),加工的轴件的实际直径尺寸y就是望目特性,其目标值m=10(mm)。
2、望小特性。
不取负值,希望质量特性y愈小愈好,波动愈小愈好,则y 被称为望小特性。
比如测量误差,合金所含的杂质、轴件的不圆度等就属于望小特性。
3、望大特性。
不取负值,希望质量特性y愈大愈好,波动愈小愈好,则y 被称为望大特性。
比如零件的强度、灯泡的寿命等均为望大特性。
(二)质量特性波动产品在贮存或使用过程中,随着时间的推移,发生材料老化变质、磨损等现象,引起产品功能的波动,我们称这种产品由于使用环境,时间因素,生产条件等影响,产品质量特性y偏离目标值m,产生波动。
引起产品质量特性波动的原因称为干扰源。
主要有以下三种类型:1、外干扰(外噪声)使用条件和环境条件(如温度,湿度,位置,输入电压,磁场,操作者等)的变化引起产品功能的波动,我们称这种使用条件和环境条件的变化为外干扰,也称为外噪声。
2、内干扰(内噪声)材料老化现象为内干扰,也称为内噪声。
3、随机干扰(产品间干扰)在生产制造过程中,由于机器、材料、加工方法、操作者、计测方法和环境(简称5MIE)等生产条件的微小变化,引起产品质量特性的波动,我们称这种在生产制造过程中出现的功能波动为产品间波动。
核辐射探测相关知识
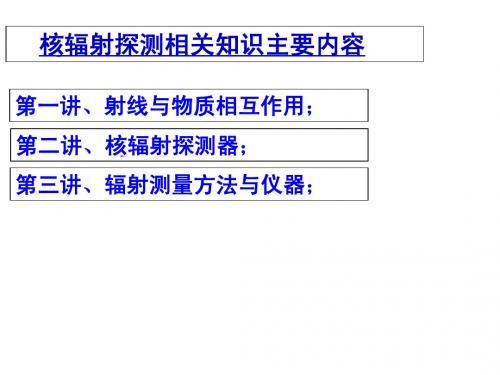
常用中子探测器
1. 硼电离室和裂变室 辐射体:常用10B和235U;
工作状态:一般工作于电流工作状态,裂变室 也可工作于脉冲工作状态。 硼电离室还常工作于补偿型状态,通过补偿 消除本底的影响。
I I1 I 2 I n
I n I
I
2.
10BF 和3He正比计数器 3
工作气体:含10B的BF3或高丰度3He的氦气。
电离室的工作方式可分为:
1) 脉冲型工作状态 记录单个入射粒子的电离效应,处于 这种工作状态的电离室称为:脉冲电离 室 2) 累计型工作状态 记录大量入射粒子平均电离效应,处 于这种工作状态的电离室称为:累计电 离室。
电离室的基本结构
不同类型的电离室在结构上基本相同. 典型结构有平板型和圆柱型。 均包括:
3. 含锂闪烁体
常用6LiI(Eu)晶体;铈激活的锂玻璃等。
4. 利用质子反冲效应的探测器
1) 含氢正比计数管——气体介质含H2或CH4。 2) 有机闪烁体——富含H和C,还可以运用n/脉 冲形状甄别技术,在较强的场中测量中子。
5. 自给能探测器
中心辐射体是中子活化材料,活化后具有 放 射性。 粒子作为荷电粒子在极板间运动而在 外回路中产生输出信号。不需要外加电源,称 为自给能探测器。 输出信号: i n e
电子与离子在气体中在外电场作用下的 漂移速度的主要区别为: (1)电子漂移速度一般为:10 cm s 3 cm 离子漂移速度一般为: 10 s
6
(2)电子的漂移速度对组成气体的组分极为 灵敏
在单原子分子气体中(如卤素)加入少量 多原子分子气体(如CO2、H2O等)时, 电子的漂移速度有很大的增加。
2 2 0 0
ln hv c hv 2
G0302质量损失率DOC
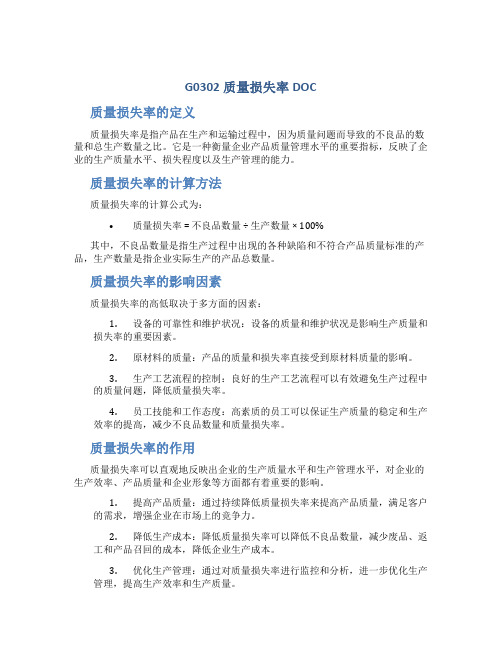
G0302质量损失率DOC质量损失率的定义质量损失率是指产品在生产和运输过程中,因为质量问题而导致的不良品的数量和总生产数量之比。
它是一种衡量企业产品质量管理水平的重要指标,反映了企业的生产质量水平、损失程度以及生产管理的能力。
质量损失率的计算方法质量损失率的计算公式为:•质量损失率 = 不良品数量 ÷ 生产数量 × 100%其中,不良品数量是指生产过程中出现的各种缺陷和不符合产品质量标准的产品,生产数量是指企业实际生产的产品总数量。
质量损失率的影响因素质量损失率的高低取决于多方面的因素:1.设备的可靠性和维护状况:设备的质量和维护状况是影响生产质量和损失率的重要因素。
2.原材料的质量:产品的质量和损失率直接受到原材料质量的影响。
3.生产工艺流程的控制:良好的生产工艺流程可以有效避免生产过程中的质量问题,降低质量损失率。
4.员工技能和工作态度:高素质的员工可以保证生产质量的稳定和生产效率的提高,减少不良品数量和质量损失率。
质量损失率的作用质量损失率可以直观地反映出企业的生产质量水平和生产管理水平,对企业的生产效率、产品质量和企业形象等方面都有着重要的影响。
1.提高产品质量:通过持续降低质量损失率来提高产品质量,满足客户的需求,增强企业在市场上的竞争力。
2.降低生产成本:降低质量损失率可以降低不良品数量,减少废品、返工和产品召回的成本,降低企业生产成本。
3.优化生产管理:通过对质量损失率进行监控和分析,进一步优化生产管理,提高生产效率和生产质量。
4.增强企业形象:在质量损失率和产品质量上获得成功,将有助于提升企业形象,增强市场竞争优势。
如何降低质量损失率降低质量损失率需要全面从多个方面入手,以下几点可以作为参考:1.建立完善的生产管理系统,对原材料、生产工艺、设备进行严格的控制和监督,降低产品质量问题的发生概率。
2.对员工进行培训,提升员工技能和工作态度,降低人为失误造成的不良品数量。
- 1、下载文档前请自行甄别文档内容的完整性,平台不提供额外的编辑、内容补充、找答案等附加服务。
- 2、"仅部分预览"的文档,不可在线预览部分如存在完整性等问题,可反馈申请退款(可完整预览的文档不适用该条件!)。
- 3、如文档侵犯您的权益,请联系客服反馈,我们会尽快为您处理(人工客服工作时间:9:00-18:30)。
42109工作面采后损失率分析
报告和总结
根据地测质量标准化考核实施细则的要求,为进一步加强煤炭资源管理,做到精采细掘,降低我矿井资源损失率,最大能力地延长矿井寿命,现针对我矿井42109工作面损失率做具体分析、总结,报告如下:
一、工作面概况
42109工作面位于煤矿南面,现采4#煤层,工作面标高为667-680米。
该工作面对应的地面位于康家沟对面300米的山坡、山梁、山沟地段。
地表为耕地、沟谷,有电线杆、双枣疙瘩村等建筑物。
42109工作面煤层赋存相对稳定,工作面走向长度为2225m,工作面倾向长度为166m,煤层厚度2.9~4.2m,平均3.6m。
煤层倾角3°~8°,平均5°。
工作面顶板为中细沙岩,底板直接底为砂质泥岩。
该工作面于2011年8月由采一队进行回采,2013年9月回采工作面结束。
二、工作面开采及资源储量动用情况
42109工作面于2011年8月开始回采,至2013年9月结束。
工作面实际倾角3°~8°,平均5º,实际平均采高3.6m,工作面走向长度为2225m,工作面倾向长度为166m,容重为1.4m3/t,开采斜面积369350㎡,实际动用储量2601087t,实际采出煤量为1951236吨,损失量为649851t,工作面回采率为93.5%。
三、42109回采工作面损失情况
42109回采工作面回采结束后,工作面采出量195.1万吨,工作面损失64.9万吨。
42109工作面损失见表一。
各采区采出量情况表
表一 单位:万吨
四、42109回采工作面损失情况
我矿现开采的4#煤层均为中厚煤层,煤层厚度为2.7m ~4.2m 之间,42109煤厚平均为3.6m ,矿井地质构造简单,但在回采时,任采取各种措施,做到损失降到最低,工作面回采率超过了上级部门规定的不低于93%标准,实际工作面回采率为93.5%。
42109工作面的实际损失率见表二。
42109作面回采率情况表
工作面名称
煤层
名称 工作面 采出量
工作面
损失量
备注
42109工作面
4# 195.1 64.9
合计
﹨
195.1
64.9
表二 单位:万吨 采区回采率超过了上级部门规定的不低于75%标准,实际采区回采率为76%。
采区工作面损失主要是:顺槽煤柱损失28万吨、隔离煤柱损失3.1万吨、落煤损失14.1万吨、丢煤损失1.9万吨。
五、42109工作面损失率分析总结
在工作中,我们要总结经验,强化管理,理清思路,开拓创新。
在井下现场条件极为复杂的情况下,42109工作面损失率为5﹪。
同时我矿在资源储量管理方面做了大量工作,增加了矿井储量,从而延长了矿井寿命,在采掘过程中做到了精采细掘,最大限度地降低了煤炭资源的损失率。
工作面名称
煤 层 名 称
顺槽煤
柱损失 隔离煤 柱损失 落煤 损失 丢煤 损失 损失
率(%) 备注
42109工作面
4# 28 3.1 14.1 1.9 7 合计
28
3.1
14.1
1.9
42109工作面结束后损失率分析
报告和总结
地
测
防
治
水
科
2013年10月
二○一二年矿井前半年损失率
分析总结报告
地
测
科2012年7月。