SMTbar_BGA制程探讨之(二)
BGA组装制程能力分析

BGA组装制程能力分析由于BGA组装与现在的焊接装配技术完全兼容,芯片规模的BGA栅格间距为0.5mm、0.65mm、0.80mm,塑料或陶瓷的BGA具有相对较宽的接触间距(1.50mm、1.27mm、1.00mm),密间距的BGA比密间距的引脚包装IC较不容易受损坏,且BGA标准允许选择地去掉接触点以满足特定的I/O要求。
BGA技术已发展为SMT 制造业的前沿技术,BGA封装正迅速成为密间距和超密间距技术所选择的封装,在提供一个可靠的装配工艺的同时达到高密度的互连,使得在工业范围内越来越多地采用这种封装形式。
X射线断层照相检查设备在BGA组装中的应用直到BGA使用到产品应用设计中的时候,大多数PCB与电子制造商还没有发现将X光检查使用到其生产过程中的太多需要。
传统的方法,诸如人工视觉检查(MVI)和电气测试,包括制造缺陷分析(MDA)、在线测试(ICT)和功能测试(FBT),已经足够。
可是,这些方法不足以检查隐蔽的焊锡点问题,诸如空洞、冷焊和焊锡附着差。
X光检查系统是一个被证实的、检查隐蔽的焊锡点、帮助建立与控制制造过程、分析原型、确认过程缺陷的工具。
它们效率高、并且与MDA、ICT和AOI系统不一样,它们可以迅速确认短路、开路、空洞和BGA及其它区域排列组装在板上的锡球不对准,监测过程品质和提供统计过程控制(SPC)所要求的即时反馈数据。
X射线断层照相设备可以把焊球分层,产生断层照相的结果。
X射线断层照相的图片能够根据CAD原始设计数据和用户设置的参数进行自动分析焊点,它实时地进行断层扫描,能够在几十秒或2min之内对PCB两面的所有元件的所有焊点进行精确的对比分析,得出焊接合格与否的结论。
BGA组装过程及其变异来源为了更有效地使用X光检查系统,我们必须明确BGA组装过程的控制参数和参数控制极限。
BGA组装过程概述如下:锡膏印刷→检查→BGA放置→回流焊→检查。
在生产过程中,具有共晶锡球的BGA贴装在锡膏中时,其位置通常在回流期间通过液态焊锡的自我对中得到纠正,因此贴装精度不象密脚引脚型元件那么关键,故BGA器件组装工艺中主要的控制环节是锡膏印刷和回流焊。
SMT表面安装技术系列之2

SMT表面安装技术系列之2表面安装元器件(电阻)表面安装元器件称无端子元器件,问世于20世纪60年代,习惯上人们把表面安装无源元器件,如片式电阻、电容、电感称之为SMC(Surface Mounted Component),而将有源器件,如小外形晶体SOT及四方扁平组件(QFT)称之为SMD(Surface Mounted De-Vices)。
无论是SMC还是SMD,在功能上都与传统的通孔安装元件相同,最初是为了减小体积而制造,最点出现在电子表中,使电子表微型化成为可能。
然而,它们一经问世,就表现出强大的生命力,体积明显减小,高频特性提高、耐振动、安装紧凑等优点是传统通孔元器件所无法比拟的,从而极大地刺激了电子产品向多功能、高性能、微型化、低成本的方向发展。
例如,片式器件组装的手提摄像机,掌上电脑和手机等,不仅功能齐全,而且低,现已在人们日常生活中广泛使用。
同时,这些微型电子产品又促进了SMC和SMD 向微型发展。
片式电阻电容已由早期的3.2mm×1.6mm缩小到0.2mm×0.3mm,IC 的端子中心距已由1.27mm减小到0.3mm,且随着裸芯片技术的发展,BGA和CSP 类高端子数器件已广泛应用到生产中。
此外,一些机电元件,如开关、继电器、延迟线、热敏和压敏电阻,也都实现了片式化。
如今,表面安装元器件品种繁多、功能各异,然而器件的片式化发展却不平衡,阻容器件,三极管,IC发展快,异型器件,插座,振荡器发展迟缓,并且片式化的元器件,又未能标准化,不同国家以至不同厂家均有不同的差异,因此,在设计选用元器件时,一定要弄清楚元器的型号、厂家及性能等,以避免出现互换性差的缺陷。
当然,表面安装元器件也存在着不足之处,例如,元器件与PCB表面非常贴近,与基板间隙小,给清洗造成困难,元器体积小,电阻、电容一般不设标记,一旦弄乱就不易搞清楚,特别是元器件与PCB之间热膨胀系数的差异也是SMT产品中应注意的问题。
BGA新制程简介 2
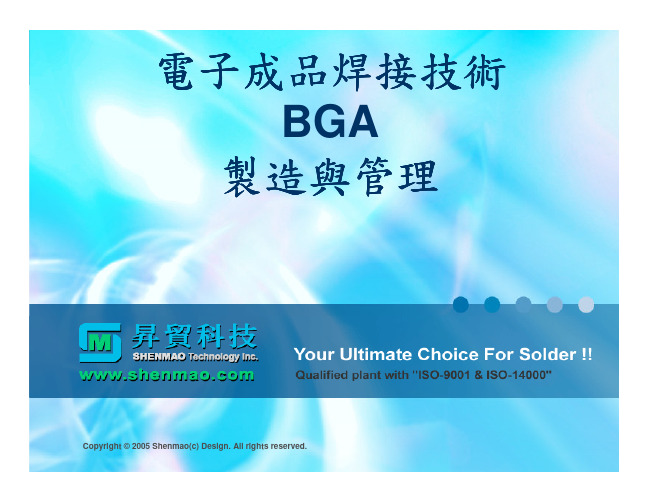
注意事項
每10pcs中有2pcs有 污染,立即驗退 每 次 檢 測 中 有 CPK<1.66, 立 即 驗 退 錫球成分不符合JIS 標準,立即驗退 含 氧 量 >30ppm, 立 即驗退 振動條 件:6mins/1000次 /25g
錫球表面檢驗 錫球球徑檢驗 錫球成分分析檢測 含氧量檢測 錫球抗氧測試
利用DSC儀器檢驗錫球液 相溫度,每1KKpcs抽驗1次
液相溫度不符標準, 立即驗退
7
高溫錫球加熱測試
利用烘箱加熱至240℃烘 烤10分鐘每1KKpcs抽測 1次
顏色變黃立即驗退
2.13 OQC
品質檢測 1.錫球表面 2.錫球球徑檢驗
2.13 OQC
品質檢測 3.錫球成分分析檢測 4.含氧量檢測
2
CPK>1.66
3 4
JIS標準 O2<30ppm 顏色觀察 檢測標準: Sn63錫球183℃±1℃Sn62錫球179℃±2℃ PF603錫球221℃±1.5℃ PF604錫球227℃±3℃ PF606/PF607/PF608/PF610錫球 219℃±1.5℃ 錫球不因加熱而改變顏色
5
6
錫球熔點(DSC)檢測 檢測 錫球熔點
2.11 包裝
品質要點 1.外箱 2.瓶罐標籤 3.瓶罐顏色 4.尺寸標籤 5.重量、數量 6.乾燥劑
2.12 出貨
品質要點 1.外箱麥頭 2.麥頭顏色 3.出貨數量 4.出貨報告 5.出貨項目 6.外箱包裝
2.13 OQC
品質檢測
操作程序
1
品質要點
表面乾淨度
自主檢查
利用金相顯微鏡觀察球體 表面,每1KKpcs.抽檢1次 利用3D畫像測定儀測量 錫球球徑尺寸,每1KKpcs 抽測1次 利用火花放射儀檢驗錫球 成分,每1KKpcs抽測1次 利用氧氮分析儀檢驗錫球 含氧量,每1KKpcs抽測1次 利用振動測試機進行錫球 抗氧測試,每1KKpcs抽測1 次
SMT制程与设备能力介绍

課程內容
SMT簡介 各工序介紹 波峰焊 SMT周邊設備介紹 ESD防護
SMT簡介
1.SMT定義 表面貼裝技術Surface Mounting Technology簡稱SMT是新一代電子組裝技術,它將傳統的電子元器件壓縮成為體積只有幾十分之一的器件,從而實現了電子產品組裝的高密度、高可靠、小型化﹑低成本﹐以及生產的自動化.這種小型化的元器件稱為:SMD器件(或稱SMC、片式器件).將元件裝配到印刷線路板或其他基板上的工藝方法稱為SMT工藝.相關的組裝設備則稱為SMT設備.
各工序介紹--貼片
3複合式 複合式貼片機從拱架式機器發展而來,集合了轉塔式和拱架式特點,動臂上安裝有轉盤,又稱閃電頭,可實現每小時60000片貼片速度.
各工序介紹--貼片
4大型平行系統 大規模平行系統(又稱模組機),使用一系列單獨小貼裝單元.各單元有獨立絲杆位置系統、安裝有相機和貼裝頭.各貼裝頭可吸取部分的帶式送料,貼裝PCB一定區域,PCB以固定間隔時間在機器內步進.單獨地各個單元機器運行速度較慢,但其連續或平行運行會有很高的效率.
各工序介紹--錫膏印刷
6.重要耗材-錫膏 1.何為錫膏
2.錫膏主要組成成份 錫粉顆粒+助焊膏/劑
各工序介紹--錫膏印刷
3.錫膏的存儲和使用 錫膏是一種化學特性很活躍的物質,因此它對環境的要求是很嚴格的.一般在溫度為0℃-10℃,濕度為20%-21%的條件下有效期為6個月,在使用時要注意幾點: A.保存的溫度 B.使用前應先回溫(一般>4小時) C.使用前應先攪拌3-4分鐘 D.最佳作業環境溫度25+/-3℃濕度為50+/-10%RH E.儘量縮短進入回流焊的等待時間 F.在開瓶24小時內必須使用完,否則做報廢處理
关于SMDBGA生产制程控制的几点建议
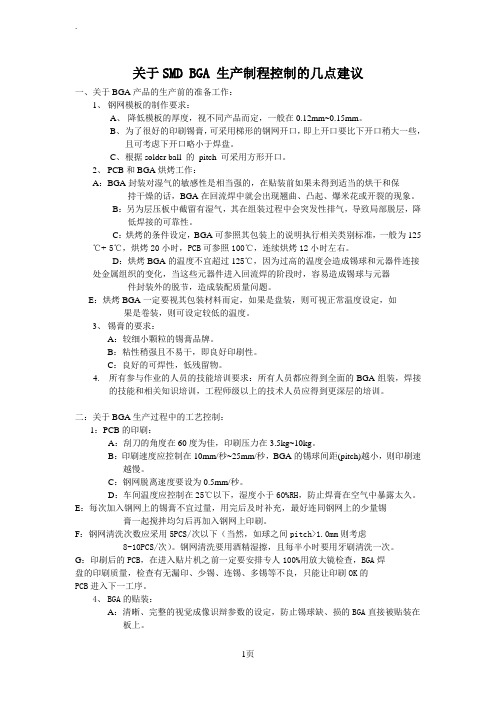
关于SMD BGA 生产制程控制的几点建议一、关于BGA产品的生产前的准备工作:1、钢网模板的制作要求:A、降低模板的厚度,视不同产品而定,一般在0.12mm~0.15mm。
B、为了很好的印刷锡膏,可采用梯形的钢网开口,即上开口要比下开口稍大一些,且可考虑下开口略小于焊盘。
C、根据solder ball 的pitch 可采用方形开口。
2、PCB和BGA烘烤工作:A:BGA封装对湿气的敏感性是相当强的,在贴装前如果未得到适当的烘干和保持干燥的话,BGA在回流焊中就会出现翘曲、凸起、爆米花或开裂的现象。
B:另为层压板中截留有湿气,其在组装过程中会突发性排气,导致局部脱层,降低焊接的可靠性。
C:烘烤的条件设定,BGA可参照其包装上的说明执行相关类别标准,一般为125 ℃+-5℃,烘烤20小时,PCB可参照100℃,连续烘烤12小时左右。
D:烘烤BGA的温度不宜超过125℃,因为过高的温度会造成锡球和元器件连接处金属组织的变化,当这些元器件进入回流焊的阶段时,容易造成锡球与元器件封装外的脱节,造成装配质量问题。
E:烘烤BGA一定要视其包装材料而定,如果是盘装,则可视正常温度设定,如果是卷装,则可设定较低的温度。
3、锡膏的要求:A:较细小颗粒的锡膏品牌。
B:粘性稍强且不易干,即良好印刷性。
C:良好的可焊性,低残留物。
4.所有参与作业的人员的技能培训要求:所有人员都应得到全面的BGA组装,焊接的技能和相关知识培训,工程师级以上的技术人员应得到更深层的培训。
二:关于BGA生产过程中的工艺控制:1:PCB的印刷:A:刮刀的角度在60度为佳,印刷压力在3.5kg~10kg。
B:印刷速度应控制在10mm/秒~25mm/秒,BGA的锡球间距(pitch)越小,则印刷速越慢。
C:钢网脱离速度要设为0.5mm/秒。
D:车间温度应控制在25℃以下,湿度小于60%RH,防止焊膏在空气中暴露太久。
E:每次加入钢网上的锡膏不宜过量,用完后及时补充,最好连同钢网上的少量锡膏一起搅拌均匀后再加入钢网上印刷。
bga基板全制程简介

检测误差的原因主要包括检测设备的精度问题、检测方法的 不当、检测人员的技能水平不足等。为了解决检测误差问题 ,可以采取多种措施,如提高检测设备的精度、优化检测方 法、进行检测人员的技能培训等。
05 bga基板全制程发展趋势与挑战
制程技术进步趋势
01 02
精细化制造
随着电子产品向更小、更轻薄方向发展,BGA基板的焊球间距不断缩小 ,对制程技术的要求也越来越高。为了实现更精细的制造,需要采用更 高精度的模具和更严格的制程控制。
对基板表面进行研磨、抛光等 处理,以提高焊接性能和电气 性能。
芯片贴装
芯片选择
根据产品要求选择合适的 芯片,确保功能和性能符 合要求。
芯片贴装设计
依据基板结构和芯片尺寸 ,进行芯片贴装设计,制 定合理的布局和间距。
芯片贴装工艺
将芯片按照设计要求贴装 到基板上,采用适当的粘 结剂和焊接技术。
焊接
焊接材料选择
其他辅助材料
如焊锡、胶水、标记材料 等。
基板制造
制作模具
根据设计图纸制作模具,用于 后续基板制作。
纤维编织
将混合好的材料放入模具中, 进行纤维编织,形成基板的框 架结构。
设计和制图
依据产品要求进行基板设计, 并制作成工程图纸。
配料与搅拌
将树脂、玻璃纤维等材料按照 一定比例混合,并搅拌均匀。
表面处理
汽车电子领域
由于BGA基板具有高可靠性和耐高 温性能,因此在汽车电子领域也有 广泛应用,如发动机控制芯片、安 全气囊控制芯片等。
02 bga基板全制程工艺流程
原材料采购
01
02
03
基板材料
包括树脂、玻璃纤维、铜 箔等,需根据产品要求选 择合适的材料。
BGA器件在SMT焊接工艺中的控制对策

BGA器件在SMT焊接工艺中的控制对策发布时间:2022-09-08T06:17:11.261Z 来源:《科学与技术》2022年第9期第5月作者:黄楠熊定贵[导读] 随着国内不断引进国外先进表面贴装设备、我国表面贴装技术自主研发的不断推进黄楠熊定贵中国电子科技集团公司第五十研究所摘要:随着国内不断引进国外先进表面贴装设备、我国表面贴装技术自主研发的不断推进,在我国电子制造行业内表面贴装制造工艺已经不是一个高不可攀的工艺难点。
然而随着BGA封装器件在表面贴装技术中应用的增多以及大众对于设备小型化、微型化所带来的BGA 焊球间距逐步缩小的现状,对表面贴装工艺又带来了新的挑战。
从可能影响BGA焊接的各个方面着手,针对性的找出控制对策进行质量管控,从根本上解决问题并提高BGA的焊接可靠性。
关键词:BGA;印制电路板;回流焊温度曲线;印刷工艺引言随着科学技术的日新月异,各种各样复杂化、精细化和小型化的设计思路逐步被应用在各类新型产品上,电子产品逐渐向着外观轻、薄、短、小以及多功能集成的方向进化。
在整个SMT生产焊接过程中,发现哪些因素会对BGA焊接产生影响,从而采取有针对性的措施来有效的保证焊接质量以及产品的可靠性是生产者迫切需要解决的问题。
1.BGA封装技术BGA 封装方式是在器件外壳底面或上表面焊有许多球状凸点(焊球),通过这些焊料凸点实现封装体与基板之间互连的一种先进封装技术,其具有封装面积小、引脚数目多、焊接时能自行对中、电性能好、可靠性高和整体成本低等特点。
在SMT表面贴装生产过程中,由于在高温状态下的情况下BGA芯片的焊球会呈现熔融状态,因此基本消除了器件在焊接中由于引线而引起的共面性差和翘曲等问题。
然而因BGA的焊接位置位于封装体的下面其所带来的缺点也很明显,其焊接质量的好坏无法依靠原有的可见焊点的外观形状来进行判断,给BGA焊点检测和返修带来了不小的困难。
2.在生产过程中影响BGA焊接质量的因素汇总SMT表面贴装焊接BGA的生产过程和影响BGA焊接质量的相关因素我们可以用图1所示的鱼骨分析图来形象表示。
BGA基板制程简介课件

• PP胶片:将玻纤布含浸树脂后烘干形成半固化胶片 (B-stage),在压合的高温下其会融化成黏状流体再 慢慢硬化成固化的绝缘层(C-stage)。
2020/11/16
BGA基板制程简介
18
发料烘烤 线路形成
线路形成(內层) AOI自动光学检测
AOI自动光学检测
压合
蚀薄铜
钻孔
Deburr
绿漆
镀Ni/Au
上PIN
薄化
烘烤BT板 导R角
机械钻孔
2020/11/16
BGA基板制程简介
15
发料烘烤 线路形成
线路形成(內层) AOI自动光学检测
AOI自动光学检测
压合
蚀薄铜
钻孔
Deburr
绿漆
镀Ni/Au
成型
O/S电测
FVI/AVI
镀铜 包裝
塞孔 出货
压合站(Lamination)
• 将棕化后之内层板经由迭合覆上胶片(PP)及铜箔而 形成多层铜面,进行压合程序而成多层板。
Customer design 放置电子元件
2020/11/16
BGA基板制程简介
9
BGA基BG板A基名板词全解製释程製造流程
Power
groun d
2020/11/16
BGA基板制程简介
10
BGA基板名词解释
Fiducial mark
于封装厂Wire Bond 制程机台扫瞄对位用
2020/11/16
2020/11/16
BGA基板制程简介
3
BGA概述
1.BGA(Ball Grid Array,球阵列封装)即以基板及锡球代替传统QFP封 装型态(以金属导线架作为IC引脚),而锡球采矩阵方式排列在封装体 底部。 2.由于BGA单位面积可容纳之I/O数目更多,晶粒到电路板的路径较短, 且无QFP之平行排脚,其优点为电容电感引发噪声较少、散热性及电性 较好、可接脚数增加,且可提高良率,1995年Intel采用之后,逐渐开 始普及。目前主要应用于接脚数超过300 PIN之IC产品,如CPU、芯片 组、绘图芯片及Flash、SRAM等。 3.依载板材质,可分为PBGA(Plastic BGA)、CBGA(Ceramic BGA)、 TBGA(Tape BGA) 等。 4.PBGA为以BT树脂及玻纤布复合而成,材料轻且便宜,玻璃转移温度高, 可承受封装时打线接合及灌胶制程之高温,为目前应用最广泛之基板
BGA制程

BGA SMT制程技术数据REFLOW焊接温度设定:( 1 )BGA焊接时芯片表面温度峰值应稳定保持在210 – 235度间且不得超过235度。
( 2 )BGA焊接时芯片融锡温度在183度以上应在60 – 90秒的范围内较佳,但不得少于45秒。
BGA焊接时芯片融锡温度在200度以上应在20 –60秒的范围内较佳。
BGA焊接时芯片融锡温度在210度以上应在10秒的范围内较佳。
( 3 )BGA焊接时芯片融锡温度在235度以上的高温范围不得超过10秒,否则……………..。
( 4 )一般焊接时预热不要加热过急,一般预热时间约定在90—120秒,热完成时温度在150--170度。
预热不足易发生较大的焊珠或组件立碑等现像,预热过热会产生较细或较大焊珠密集分布在组件四周。
预热温度过低会产生锡不融的现像。
( 5 ) 一般焊接时温度峰值应稳定保持在210 – 240度间且温度在200度以上的时间为20--60秒。
BGA及PQFP库存温湿度管理:CHIPSET本身为一对湿度相当敏感的零件,吸湿信性相当强;当它曝露在湿度过高的环境下,会吸收空气中的水份;如此时进行SMT作业REFLOW的高温会使零件内部所吸收的水份瞬间急速气化,导致CHIPSET内部结构受损及影响焊接熔锡状况。
(1) 密封时储存条件及使用期限:BGA 低于40度,90%RH,12个月PQFP 低于40度,90%RH,12个月(2) 开封后使用要求及使用期限:BGA LEVEL 4,低于30度,60%RH,72小时上线BGA LEVEL3,低于30度,60%RH,168小时上线(3) 需作烘烤状况:开封后湿度显示适配器大于20%RH,违反开封后使用要求及使用期限(4) 烘烤方式及条件:24小时,125度BGA SMT制程注意事项:锡膏印刷务必要求对以下项目作100%检验------PCB变形;BGA焊垫,防焊,线路;印刷锡量不良时的处理------PAD单点补锡膏;PCB清除锡膏重印BGA材料务必要求对以下项目作100%检核------开封后使用要求及使用期限;型号;上料方向不良时的处理-------重新烘烤;更正错误BGA置装务必要求对以下项目作100%检验------置装在PCB上的型号,方向;位置偏移大于0.6m/m不良时的处理-------移除BGA后PCB过REFLOW,千万不可以移位方式调整偏移BGA 焊接务必每日要求对以下项目作检核-------PROFILE检核;REFLOW温度数参不良时的处理-------立即停止生产调整或检修REFLOWBGA检验务必要求对以下项目作100%检验------置装在PCB上的型号,方向;位置偏移;电气特性不良时的处理-------于24小时内使用BGA拔焊设备拔去使用新品置换焊接,千万不可以使用植球的旧品BGA不良处理后的PCB应作标示区分并作全制程追踪,计录良品率。
BGA 设计 制程 焊接问题分析
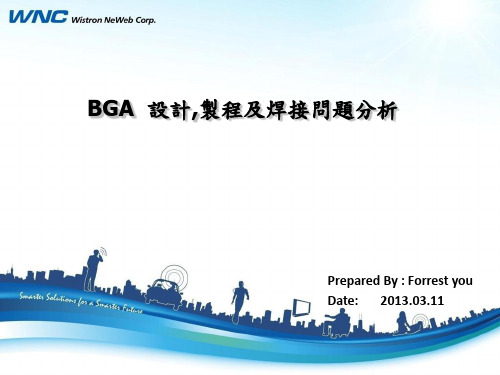
27
BGA 焊點開裂案例:---Pb 污染
28
BGA 焊點開裂案例:---Pb 污染
29
如何辨別Crack 的原因?
black pad related failure
associated with mechanical stress
Crack location for a) black pad related failure (b) interfacial fracture when using ENIG surface finish
30
BGA 焊點開裂案例:---應力過大
對PCBA 測試&組裝過程進行Strain 量測
31
(BGA CRACK)造成IMC异常破裂的常間原因
32
PCB 厚度與應變量/應變率關係
33
增加BGA 可靠度( 減少Solder crack) :
OSP Surface finish for BGA pad
BGA 封裝的吸濕性.
9
Popcorn: 受潮或多次rework
Popcorning causes the BGA package to expand below the die; resulting in an increase in size (and possibly bridging) of the solder balls in the center of the package as they are squished between the package and the board.
BGA 設計,製程及焊接問題分析
Prepared By : Forrest you Date: 2013.03.11
富士康BGA不良分析讲义

BGA不良現象分析
不良現象(九) :
表面粗糙之金屬結構( Poor grain structure )﹕焊點表面上 出現不均勻,粗糙,顆粒狀或多孔狀. 焊點非呈現濕潤平滑光 亮之外表而是灰暗且表面粗糙.
• 原因﹕ a.熱量不足:迴焊開始時未獲得足夠熱量 以致未達完全吃錫. b.過熱:過多的加熱時間與熱量會 導致焊點上錫與鉛在固化後不易 生成共混化合物而產生粗粒結構, 且在相同的方式中不會如同平滑
BGA不良現象分析
不良現象(七)
放置的偏移( Misregistration )﹕零件移開焊墊, 如:未按規格說明或IPC 標
準工作手冊調整 (BGA 為1/2 pad 大小) • 原因﹕ a.高速機或泛用機工作錯誤 (未照光學點或 機台對位不正) b.在迴焊過程中零件漂移(Reflow 機台或Conveyor 未調整恰當之水平) • 解決方法﹕ a. 在置放後與迴焊前檢視零件位置調整 是否正確 b. 減少在迴焊爐輸送帶所造成 的振動與 整個Reflow 機台之水平誤差.
BGA不良現象分析
不良現象(十三)
濺錫( Solder Splash )﹕在 PCB 表面上有微小的錫球其靠近或介於兩焊點
間
• 原因﹕
a.錫膏黏稠度不理想,在迴焊過程中錫膏太乾或
太濕就會產生小錫球或者粒徑選擇不正確. b. 溫度升溫太快就會導致微小的爆炸效應以產 生微小的錫球
• 解決方法﹕
a.檢查錫膏耐儲時間與儲存條件,進行Slump 試驗以吻合指導方針 b.降低升溫曲線以確保錫膏內溶劑不要揮發過 快,致使Solder Paste Slump 或產生濺錫之現象
BGA不良現象分析
不良現象(八) :
• 原因﹕如果溫度曲線不正確, 如:太長,那麼共熔的焊錫會 影響高焊點的焊錫之熔錫溫 度與金屬結構. 因此,降低其 共熔時的焊點接近至共晶熔 合溫度,可避免產生㆒個高度 敏感介面金屬而易生裂痕擴 展的脆性區域α 金屬. • 解決方法﹕調整溫度曲 線
SMTbar_回流焊接工艺的发展历程
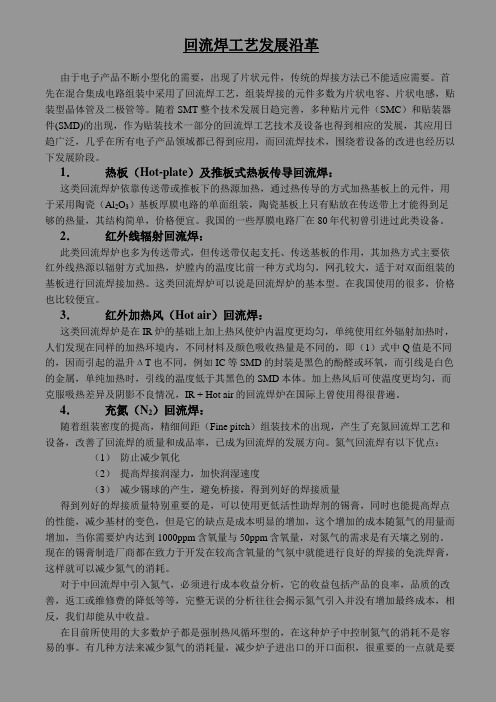
回流焊工艺发展沿革由于电子产品不断小型化的需要,出现了片状元件,传统的焊接方法已不能适应需要。
首先在混合集成电路组装中采用了回流焊工艺,组装焊接的元件多数为片状电容、片状电感,贴装型晶体管及二极管等。
随着SMT整个技术发展日趋完善,多种贴片元件(SMC)和贴装器件(SMD)的出现,作为贴装技术一部分的回流焊工艺技术及设备也得到相应的发展,其应用日趋广泛,几乎在所有电子产品领域都已得到应用,而回流焊技术,围绕着设备的改进也经历以下发展阶段。
1.热板(Hot-plate)及推板式热板传导回流焊:这类回流焊炉依靠传送带或推板下的热源加热,通过热传导的方式加热基板上的元件,用于采用陶瓷(Al2O3)基板厚膜电路的单面组装,陶瓷基板上只有贴放在传送带上才能得到足够的热量,其结构简单,价格便宜。
我国的一些厚膜电路厂在80年代初曾引进过此类设备。
2.红外线辐射回流焊:此类回流焊炉也多为传送带式,但传送带仅起支托、传送基板的作用,其加热方式主要依红外线热源以辐射方式加热,炉膛内的温度比前一种方式均匀,网孔较大,适于对双面组装的基板进行回流焊接加热。
这类回流焊炉可以说是回流焊炉的基本型。
在我国使用的很多,价格也比较便宜。
3.红外加热风(Hot air)回流焊:这类回流焊炉是在IR炉的基础上加上热风使炉内温度更均匀,单纯使用红外辐射加热时,人们发现在同样的加热环境内,不同材料及颜色吸收热量是不同的,即(1)式中Q值是不同的,因而引起的温升ΔT也不同,例如IC等SMD的封装是黑色的酚醛或环氧,而引线是白色的金属,单纯加热时,引线的温度低于其黑色的SMD本体。
加上热风后可使温度更均匀,而克服吸热差异及阴影不良情况,IR + Hot air的回流焊炉在国际上曾使用得很普遍。
4.充氮(N2)回流焊:随着组装密度的提高,精细间距(Fine pitch)组装技术的出现,产生了充氮回流焊工艺和设备,改善了回流焊的质量和成品率,已成为回流焊的发展方向。
BGA基板全制程简介

塞孔流程圖解
刷磨
去除銅顆粒 及整平銅面
B處理 刷磨
粗化銅面以利 塞孔劑附著
整平面銅減 少塞孔劑附 著於面銅
塞孔網印
塞孔
烘烤 刷磨
使塞孔劑硬 化完全
將塞孔劑突 出部分研磨 乾淨
乾膜前處理
(清潔銅面,增加乾 膜與銅面的密著性)
刷磨(option)
高壓水洗 超音波水洗
水洗
去膠渣
膨鬆劑槽(將孔內樹脂 膨鬆軟化以利KMnO4咬蝕)
水洗
KMnO4槽(將鑽
孔產生的孔壁膠渣咬
蝕除去)
水洗
中和槽(將KMnO4
槽反應產生之Mn7+, Mn4+還原成Mn2+
∵Mn2+易溶於水)
水洗
鍍銅
化學銅
清潔槽(清潔銅
面及將孔壁改為 正電荷以利帶負
電Pd膠體吸附)
水洗
微蝕槽(去除銅 面氧化)
鑽靶孔 (作為鑽孔用之定位孔)
裁板
(將壓合後多餘邊料切除)
流程圖解(2Layer)
1.基材
BT樹脂
2.鑽孔
銅箔
流程圖解(2Layer)
3.鍍銅
4.壓乾膜
流程圖解(2Layer)
5.曝光
UV Exposure
6.顯影
光罩 MASK
流程圖解(2Layer)
7.蝕刻
8.剝膜
流程圖解(2Layer)
脫脂
水洗
酸洗
水洗
烘乾
線路形成
壓乾膜
曝光
(形成線路圖形)
線路蝕刻
(形成線路)
顯影 水洗 蝕刻 水洗 酸洗 剝膜
项目二SMT组装过程的质量检测与分析

1.0×0.5
0.6×0.3
MOUNT
阻容元件识别方法 2.片式电阻、电容识别标记
电 阻
电 容
标印值
电阻值
标印值
电阻值
2R2
5R6
102
682
333
104
564
2.2Ω
5.6Ω
1KΩ
6800Ω
33KΩ
100KΩ
560KΩ
0R5
010
110
471
332
MOUNT
解决贴装缺陷可以从以下方面着手
贴装压力是否太低或太高? 贴装加速度、速度是否太高? 贴装机精度是否足够? 传感器工作是否正常? 焊膏的黏性是否足够? 焊膏暴露在空气中的时间是否太长? 外部环境是否有变化?
MOUNT
贴片速度与加速度
01
贴片速度与加速度不仅影响生产率,而且影响贴片质量。 如果PCB工作台在工作过程中快速移动,元器件质量越大,受的冲击越大,从而造成移位,降低贴装精度。
Hale Waihona Puke 02MOUNT4. 元器件
元器件越小,对贴片的精度要求就越高,很小的旋转误差或平移就会使元器件贴偏甚至完成偏离焊盘。在实际的生产线,一般都配置了至少两台贴片机,即高速贴片机、高精度贴片机。
MOUNT
有些元器件在贴装时发生了很小的偏移,就单个元器件来说这种偏移是可以接受的,但是当相临两个元器件相对偏移时,这种很小的偏移可能不满足最小电气间隙,而这种情况往往让人们忽略,造成严重的后果。
元器件贴偏
01
元器件贴偏一般是由于贴片机精度不够或振动冲击造成的,包括X-Y轴的传动误差、Z轴的旋转精度、视觉系统及其分辨率\、PCB的精度等因素有关。
BGA、TAB、零件、封装及Bonding制程
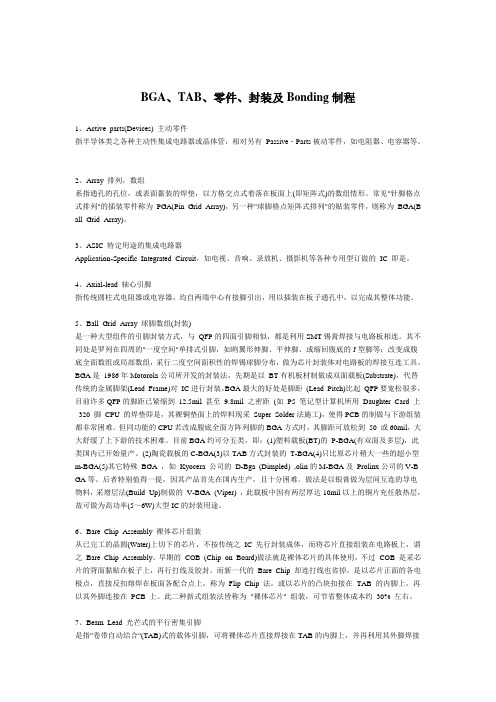
BGA、TAB、零件、封装及Bonding制程1、Active parts(Devices) 主动零件指半导体类之各种主动性集成电路器或晶体管,相对另有Passive﹣Parts被动零件,如电阻器、电容器等。
2、Array 排列,数组系指通孔的孔位,或表面黏装的焊垫,以方格交点式着落在板面上(即矩阵式)的数组情形。
常见"针脚格点式排列"的插装零件称为PGA(Pin Grid Array),另一种"球脚格点矩阵式排列"的贴装零件,则称为BGA(B all Grid Array)。
3、ASIC 特定用途的集成电路器Application-Specific Integrated Circuit,如电视、音响、录放机、摄影机等各种专用型订做的IC 即是。
4、Axial-lead 轴心引脚指传统圆柱式电阻器或电容器,均自两端中心有接脚引出,用以插装在板子通孔中,以完成其整体功能。
5、Ball Grid Array 球脚数组(封装)是一种大型组件的引脚封装方式,与QFP的四面引脚相似,都是利用SMT锡膏焊接与电路板相连。
其不同处是罗列在四周的"一度空间"单排式引脚,如鸥翼形伸脚、平伸脚、或缩回腹底的J型脚等;改变成腹底全面数组或局部数组,采行二度空间面积性的焊锡球脚分布,做为芯片封装体对电路板的焊接互连工具。
BGA是1986年Motorola公司所开发的封装法,先期是以BT有机板材制做成双面载板(Substrate),代替传统的金属脚架(Lead Frame)对IC进行封装。
BGA最大的好处是脚距(Lead Pitch)比起QFP要宽松很多,目前许多QFP的脚距已紧缩到12.5mil 甚至9.8mil 之密距(如P5 笔记型计算机所用Daughter Card 上320 脚CPU 的焊垫即是,其裸铜垫面上的焊料现采Super Solder法施工),使得PCB的制做与下游组装都非常困难。
BGA机器使用方法详谈

★基本知识1目前smt常用的锡有两种即有铅和无铅成份为:铅Pb锡SN 银AG 铜CU。
有铅锡珠Sn63Pb37融点183°;无铅锡珠Sn96.5Ag3Cu0.5融点217°3.调整温度时我们应该把测温线插进BGA和PCB之间,并且确保测温线前端裸露的部分都插进去。
4.植球时,在对BGA表面要涂少量的助焊膏,钢网、锡球、植球台要确保清洁干燥。
5.助焊膏和锡膏在保存时都应该放在10℃的冰箱保存。
6.在做板之前要确保PCB和BGA都没有潮气,是干燥、烘烤过的。
7.国际上的环保标示是ROSS ,如果PCB中含有此标示,我们也可以认为此PCB为无铅制程所做。
8.在焊接BGA时,要在PCB上涂抹均匀助焊膏,无铅铅芯片焊接时可以稍多涂些。
9.在焊接BGA时,要注意PCB的支撑,卡板时不要卡的太紧,要预留出PCB受热膨胀的间隙。
10.有铅锡与无铅锡的主要区别:熔点不一样。
(有铅183℃无铅217℃)有铅流动性好,无铅较差。
危害性。
无铅即环保,有铅非环保11.助焊膏的作用(1). 助焊(2). 去除BGA和PCB表面的杂质和氧化层,使焊接效果更加良好。
12.底部暗红外发热板清洁时不能用液体物质清洗,可以用干布、镊子、进行清洁!★看图(1)假设此图为有铅测温线测到的实际曲线焊接图,D点到C点称之为“预热区”,B点到A点称之为“回焊区”,E点称之为“最高温度”即“峰值”(a).D点温度值为(有铅130 ;无铅150)C点的温度值为(有铅180 ;无铅190 )B点的温度值为(有铅183;无铅217 )A点的温度值为(有铅183;无铅217 )E点最高温度值为:有铅205-215。
最佳210;235-245最佳238)(b).D点到C点的时间应该满足60秒到110秒的要求,B点A点的时间应该满足40-90。
(2)假设此图为无铅曲线焊接图,D点到C点称之为“预热区”,B点到A点称之为“回焊区”,E点称之为“最高温度”即“峰值”(a).D点温度值为150 °C点的温度值为190°B点的温度值为217 °A点的温度值为217°E点温度值为235°(b).D点到C点的时间应该满足60秒到110 秒的要求,B点A点的时间应该满足40 到90秒的要求。
SMT作业流程简介及常见问题
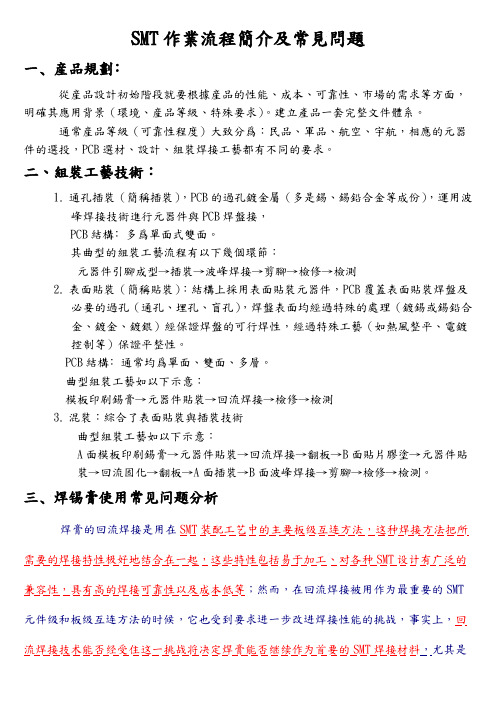
SMT作業流程簡介及常見問題一﹑産品規劃﹕從産品設計初始階段就要根據産品的性能、成本、可靠性、市場的需求等方面,明確其應用背景(環境、産品等級、特殊要求)。
建立產品一套完整文件體系。
通常産品等級(可靠性程度)大致分爲:民品、軍品、航空、宇航,相應的元器件的選投,PCB選材、設計、組裝焊接工藝都有不同的要求。
二、組裝工藝技術:1.通孔插裝(簡稱插裝),PCB的過孔鍍金屬(多是錫、錫鉛合金等成份),運用波峰焊接技術進行元器件與PCB焊盤接,PCB結構﹕多爲單面式雙面。
其曲型的組裝工藝流程有以下幾個環節:元器件引腳成型→插裝→波峰焊接→剪腳→檢修→檢測2.表面貼裝(簡稱貼裝):結構上採用表面貼裝元器件,PCB覆蓋表面貼裝焊盤及必要的過孔(通孔、埋孔、盲孔),焊盤表面均經過特殊的處理(鍍錫或錫鉛合金、鍍金、鍍銀)經保證焊盤的可行焊性,經過特殊工藝(如熱風整平、電鍍控制等)保證平整性。
PCB結構﹕通常均爲單面、雙面、多層。
曲型組裝工藝如以下示意:模板印刷錫膏→元器件貼裝→回流焊接→檢修→檢測3.混裝:綜合了表面貼裝與插裝技術曲型組裝工藝如以下示意:A面模板印刷錫膏→元器件貼裝→回流焊接→翻板→B面貼片膠塗→元器件貼裝→回流固化→翻板→A面插裝→B面波峰焊接→剪腳→檢修→檢測。
三﹑焊锡膏使用常见问题分析焊膏的回流焊接是用在SMT装配工艺中的主要板级互连方法,这种焊接方法把所需要的焊接特性极好地结合在一起,这些特性包括易于加工、对各种SMT设计有广泛的兼容性,具有高的焊接可靠性以及成本低等;然而,在回流焊接被用作为最重要的SMT 元件级和板级互连方法的时候,它也受到要求进一步改进焊接性能的挑战,事实上,回流焊接技术能否经受住这一挑战将决定焊膏能否继续作为首要的SMT焊接材料,尤其是在超细微间距技术不断取得进展的情况之下。
下面我们将探讨影响改进回流焊接性能的几个主要问题,为发激发工业界研究出解决这一课题的新方法,我们分别对每个问题简要介绍。
SMT培训课程

※锡膏印刷過後2hr內須過Reflow,如超過時間須重新清洗。
2019/12/12
10
锡膏印刷機注意事項
1. 锡膏開罐時間是否符合 锡膏製程管理 條件。 2. 刮刀壓力、速度、角度。 3. 鋼版與刮刀印刷間隙。 4. 鋼版擦拭使用之有機溶劑、擦拭方式、次數。 6. 印刷後品質判定。 7. 鋼版版本之正確性。 8. 參考各機型之锡膏印刷製程參數表。
8
锡膏攪拌及使用注意事項
1. 解冻时间为4小时,搅拌为2分钟。 2. 用量的原则,保证网面上有1—1。5CM的锡膏在网面上作滚动,低于此高度
时则添加新锡膏来维持。 3. 锡膏在使用过程中往两边跑的锡膏要在30分钟内收回到刮刀下面,防止静止
过久,影响其内部成分配比或干化。 4. 锡膏瓶在不用时必须内外盖密封,防止其它空气或水份进入而引起氧化或变
钢网开口要求:
2019/12/12
3
开口要求列表
2019/12/12
4
防锡珠开口方式
2019/12/12
5
烘烤的要求
序号 1
2
防潮等级 无限制,
一年,
拆封后存放条件及最大时间 ≤85%RH(相对湿度)
≤30℃/60%RH(相对湿度)
2.1
4周
≤30℃/60%RH(相对湿度)
3
168小时, ≤30℃/60%RH(相对湿度),
Printer
Chip-shooter I
Mid-Mounter
Unloader
Reflow
Work station
IC Mounter
Chip-shooter II
2019/12/12
2
Unloader