数控车削加工工艺分析之我见(2)
数控加工工艺个人总结

数控加工工艺个人总结
数控加工工艺是一种利用计算机控制系统对材料进行加工加工的方法。
在这个过程中,需要通过计算机编程来控制机床的运动,实现对加工过程的精确控制。
以下是我对数
控加工工艺的个人总结:
1. 精度高:由于数控机床是由计算机控制的,可以实现精确的运动控制,因此加工的
精度相对较高。
同时,由于计算机可以实时监控和调整加工过程,可以及时纠正加工
误差,进一步提高加工精度。
2. 生产效率高:数控机床具有高速度、高功率、高刚性和高准确度的特点,可以大大
提高生产效率。
而且,由于计算机控制的加工过程可以自动进行,减少了人工操作的
时间和成本。
3. 适应性强:数控机床具有较强的适应性,可以加工各种形状和复杂度的工件。
只需
通过编程进行设置,即可实现不同形状的工件加工,大大提高了加工的灵活性和多样性。
4. 节约材料:使用数控加工工艺可以最大限度地节约材料。
由于计算机编程可以实现
最优切割和排布,减少了材料的浪费,提高了材料的利用率。
5. 减少人为因素:数控加工工艺大大减少了人为因素的影响。
由于加工过程由计算机
自动控制,不需要过多的人工干预,减少了操作错误和人为疲劳对加工结果的影响。
总之,数控加工工艺在工业生产中具有重要的作用。
它不仅提高了加工精度和生产效率,还节约了材料和人力资源,为工业生产带来了巨大的便利和经济效益。
关于数控车床螺纹车削的加工工艺常见问题分析及解决办法探讨

关于数控车床螺纹车削的加工工艺常见问题分析及解决办法探讨数控车床螺纹车削作为数控加工的一种常见工艺,广泛应用于机械制造、航空航天、汽车制造等领域。
在实际生产中,常常会出现一些问题,影响加工效率和产品质量。
本文将对数控车床螺纹车削的加工工艺常见问题进行分析,并提出解决办法,以期能够帮助广大生产人员更好地掌握这一工艺,提高加工效率和产品质量。
一、加工工艺常见问题分析1. 螺纹精度不高在数控车床螺纹车削过程中,螺纹精度不高是一个常见问题。
这会直接影响到螺纹的配合质量和使用性能,严重影响产品质量。
2. 刀具磨损严重刀具磨损严重是另一个常见问题,这会导致刀具寿命缩短,加工效率低下,甚至造成加工质量不稳定。
3. 加工过程中出现振动在数控车床螺纹车削过程中,振动是一个常见问题,严重影响加工质量,甚至可能导致加工失效。
4. 加工余量不足加工余量不足是因为工艺参数设置不合理,导致产品尺寸不稳定,甚至无法满足要求。
5. 加工表面粗糙度不合格表面粗糙度不合格是另一个常见问题,这直接影响到产品的外观和使用性能。
二、解决办法探讨要解决螺纹精度不高的问题,首先要选择合适的加工参数,保证切削速度和进给速度适当。
要选择合适的刀具,并严格控制刀具的安装和刀具槽道的精度。
要加强对数控车床的维护保养,确保设备的精度和稳定性。
刀具磨损严重的问题可以通过选择合适的刀具材料和刀具类型来解决。
加强刀具的冷却和润滑,合理选择刀具的切削速度和进给速度,延长刀具的使用寿命。
加工余量不足的问题主要是由工艺参数设置不合理导致,因此要优化加工参数设置,保证加工余量符合要求。
要对数控车床进行定期检查和维护,确保各个参数的准确性和稳定性。
表面粗糙度不合格的问题可以通过选择合适的切削参数来解决,包括切削速度、进给速度和切削深度。
要确保刀具和工件的质量,严格控制刀具的磨损情况,确保加工表面的光洁度。
数控车床螺纹车削的加工工艺常见问题是可以通过合理的解决办法来避免的。
数控车削加工工艺分析

数控车削加工工艺分析【摘要】:零件的数控加工质量包括加工精度和表面质量。
【关键词】:数控车削工艺分析控制质量在市场竞争激烈的情况下,数控车床的应用越来越广泛。
为合理地发挥数控车床的加工特点,保证加工质量,如何保证和提高数控车床的加工质量是十分重要的。
工艺性分析是对工件进行数控加工的前期准备工作,它必须在数控程序编制前完成,因为工艺方案确定之后,编程才有依据。
如果工艺性分析不全面,工艺处理不当,将可能造成数控加工的错误,直接影响加工的顺利进行,甚至出现废品。
因此数控加工的编程人员首先要把数控加工的工艺问题考虑周全,才进行程序编制。
合理进行数控车削的工艺处理,是提高零件的加工质量和生产效率的关键。
因此应根据零件图纸对零件进行工艺分析,明确加工内容和技术要求,确定加工方式和加工路线,选择合适刀具及切削用量等参数。
未标注处倒角:1x45°,棱边倒钝0.2x45°,要求在数控车床上完成加工小批量生产1、零件图的加工工艺分析。
该零件表面由圆柱,圆锥,顺圆弧,逆圆弧及普通螺纹等表面组成。
其中多个直径尺寸有较严格的尺寸精度和表面粗糙度等要求。
2、零件图的加工工艺处理。
(1)对图样上给定的几个精度要求较高的尺寸,因其公差数值较小,故编程时不必取平均值,而全部取其基本尺寸即可。
(2)在轮廓曲线上,有两处为既过象限有改变进给方向的轮廓曲线,加工时应进行机械间隙补偿,以保证轮廓曲线的准确性。
(3)为便于装夹,坯件左端应预先车出夹持部分,右端面也应该先粗车出并钻好中心孔。
毛坯选φ32mm棒料。
(4)确定装夹方案。
确定坯件轴线和左端大端面(设计基准)为定位基准。
左端采用三爪定心卡盘加紧,右端采用活动顶尖支承的装夹方式。
(5)确定加工顺序及进给路线。
按由精到粗,由近及远(由右到左)的原则确定。
3、刀具材料的合理选择。
刀具材料在切削中一方面受到高压高温和剧烈的摩擦作用,要求其硬度高、耐磨性和耐热性好;另一方面又要受到压力、冲击和振动,要求其强度和韧性足够。
对于数控车削加工工艺分析

对于数控车削加工工艺分析数控车削加工是一种智能化的机械加工技术,它通过计算机程序控制旋转切削刃进行精密加工工艺。
这种工艺应用广泛,例如在机械零件加工、汽车零件加工、航空航天零件加工等领域都有广泛的应用,目前已经成为现代化生产制造的重要组成部分。
为了加深对数控车削加工工艺的了解,本文将对其原理、工艺特点以及影响加工质量的因素进行分析。
一、数控车削加工的原理数控车削加工采用计算机程序控制旋转切削刃的切入切出轨迹,在由精密控制系统控制旋转刀具和旋转工件期间,以非常高效和准确的方式切割材料,从而精密的完成机械零件的加工过程。
二、数控车削加工的工艺特点1. 具有良好的加工精度,能够加工出高精度的工件。
2. 高效率、高精度的加工速度和工艺性能,可适应不同工件的要求。
3. 可以对复杂的形状进行加工,不受常规工具的限制。
4. 可以进行多种立体加工,将一些复杂的形状在三维环境下加工成工件。
5. 可以进行长周期的连续加工,而且可靠性强。
三、影响加工质量的因素影响数控车削加工工艺质量的因素有很多,在设计和操作过程中需要进行充分考虑和控制,这样才能够保证加工出来的工件有稳定的质量、快速的加工速度、高效的生产效率。
1. 材料的性质材料的性质是决定加工工艺的一个重要因素。
因为不同材料的硬度和韧性特性不同,需要在数控车削加工过程中采用不同的切削参数。
材料越硬,加工难度越大,刀具寿命也会受到影响。
2. 设备选择设备选择是另一个影响加工质量的因素。
不同的数控车削加工设备有不同的处理能力,操作熟练程度也会影响最终的加工质量。
3. 加工环境加工环境是影响加工精度的另一个因素。
加工环境中产生的光、温、震动等因素都会对加工精度产生影响。
尤其是在高精度加工时,需要保持温度和光线等因素尽量稳定,以确保加工精度。
4. 物理和化学参数螺纹角、工件直径、转速、切削宽度等物理参数自然会影响到加工质量,需要根据具体情况调整。
此外,切削液、切削油等物化参数也是影响加工质量的因素,这会直接影响到工具的磨损和寿命。
数控车削加工工艺分析
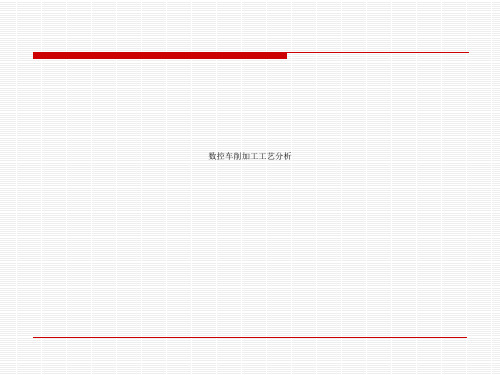
数控车加工尺寸范围
有效切削长度
外圆加工时有效切削长度主要受Z向行程极限的制约,而内孔加工时, 为确保刀具的退出,其有效切削长度大约为Z向行程范围的1/2
数控车加工工艺分析
数控车削加工零件工艺性分析包括: 零件结构形状的合理性 几何图素关系的确定性 精度及技术要求的可实现性 工件材料的可切削性能等
3).表面粗糙度要求 表面粗糙度是合理安排车削工艺、选择机床、刀具及确定切削用量的重
要依据。例如,对表面粗造度要求较高的表面,应选择刚性好的机床并 确定用恒线速度切削。一般地,粗车的表面粗糙度Ra为 25μm~12.5μm ,半精车Ra为6.3μm~3.2μm,精车Ra为 1.6μm~0.8μm(精车有色金属Ra可达0.8μm~0.4μm)。
(2)切削平面:过主切削刃上的一 点,与主切削刃相切并垂直于基面 的平面,用Ps表示。
(3)正交平面:垂直于主切削刃在 基面上投影的平面,又称主剖面, 用Po表示。
➢ 切削平面、基面、正交平面(主剖 面)在空间相互垂直,构成一个空 间直角坐标系,是车刀几何角度的 测量基准。
刀具的几何角度
在正交面中测量 1)前角(g0):前刀面(Ag)与基
数控车加工尺寸范围
有效车削直径
后置式刀盘机床,以刀具安装孔轴线与主轴轴线重合(轴端钻孔)时为X=0 刀盘+X最大移动距离为180mm,-X向最大移动距离为=80mm 行程范围260mm 安装外圆车刀时刀杆探出长度一般为刀杆厚度的1~1.5倍,若TL为55mm 则外圆车刀的有效移动范围为180-55=125mm,能加工轴类零件的最大 有效直径约为250mm。
(Pr)的夹角。当刀尖为最高点时, ls为正值;当刀尖为最低点时, ls 为负 值;当主切削刃与基面平行时, ls为零 在副正交平面(垂直于副切削刃在基面上 投影的平面)内测量 副后角( α0’ ):副后刀面与副切削平 面的夹角。 副前角( g0’ )、副刃倾角( ls‘ ):可 通过换算得到,故称派生角度。 车刀的六个基本角度: 前角( g0 )、后角( α0 )、刃倾角( ls ) 主偏角(Кr)、副偏角(Кr‘)、副后角(α0’ )
数控车加工工艺总结(共6篇)

数控车加工工艺总结第1篇答:数控加工工序的划分一般可按下列方法进行:(1)刀具集中分序法就是按所用刀具划分工序,用同一把刀具加工完零件上所有可以完成的部位。
在用第二把刀、第三把完成它们可以完成的其它部位。
这样可减少换刀次数,压缩空程时间,减少不必要的定位误差。
(2)以加工部位分序法对于加工内容很多的零件,可按其结构特点将加工部分分成几个部分,如内形、外形、曲面或平面等。
一般先加工平面、定位面,后加工孔;先加工简单的几何形状,再加工复杂的几何形状;先加工精度较低的部位,再加工精度要求较高的部位。
(3)以粗、精加工分序法对于易发生加工变形的零件,由于粗加工后可能发生的变形而需要进行校形,故一般来说凡要进行粗、精加工的都要将工序分开。
综上所述,在划分工序时,一定要视零件的结构与工艺性,机床的功能,零件数控加工内容的多少,安装次数及本单位生产组织状况灵活掌握。
另建议采用工序集中的原则还是采用工序分散的原则,要根据实际情况来确定,但一定力求合理。
数控车加工工艺总结第2篇对切削过程进行监控主要考虑以下几个方面:1.加工过程监控粗加工主要考虑的是工件表面的多余余量的快速切除。
在机床自动加工过程中,根据设定的切削用量,刀具按预定的切削轨迹自动切削。
此时操作者应注意通过切削负荷表观察自动加工过程中的切削负荷变化情况,根据刀具的承受力状况,调整切削用量,发挥机床的最大效率。
2.切削过程中切削声音的监控在自动切削过程中,一般开始切削时,刀具切削工件的声音是稳定的、连续的、轻快的,此时机床的运动是平稳的。
随着切削过程的进行,当工件上有硬质点或刀具磨损或刀具送夹等原因后,切削过程出现不稳定,不稳定的表现是切削声音发生变化,刀具与工件之间会出现相互撞击声,机床会出现震动。
此时应及时调整切削用量及切削条件,当调整效果不明显时,应暂停机床,检查刀具及工件状况。
3.精加工过程监控精加工,主要是保证工件的加工尺寸和加工表面质量,切削速度较高,进给量较大。
数控车削加工工艺分析之我见(2)
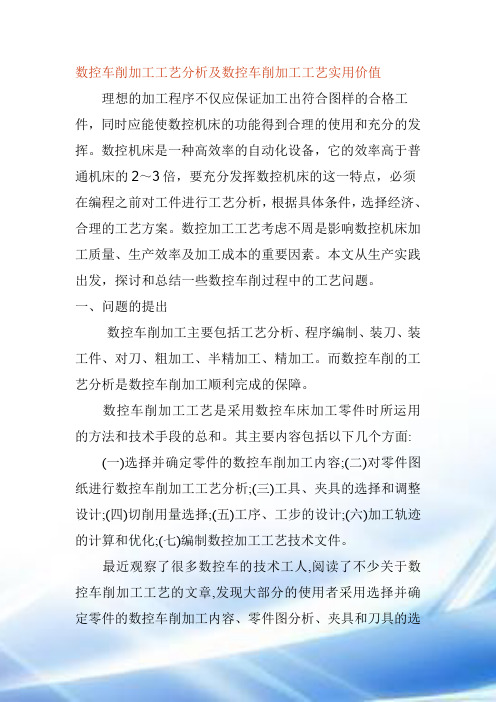
数控车削加工工艺分析及数控车削加工工艺实用价值理想的加工程序不仅应保证加工出符合图样的合格工件,同时应能使数控机床的功能得到合理的使用和充分的发挥。
数控机床是一种高效率的自动化设备,它的效率高于普通机床的2~3倍,要充分发挥数控机床的这一特点,必须在编程之前对工件进行工艺分析,根据具体条件,选择经济、合理的工艺方案。
数控加工工艺考虑不周是影响数控机床加工质量、生产效率及加工成本的重要因素。
本文从生产实践出发,探讨和总结一些数控车削过程中的工艺问题。
一、问题的提出数控车削加工主要包括工艺分析、程序编制、装刀、装工件、对刀、粗加工、半精加工、精加工。
而数控车削的工艺分析是数控车削加工顺利完成的保障。
数控车削加工工艺是采用数控车床加工零件时所运用的方法和技术手段的总和。
其主要内容包括以下几个方面:(一)选择并确定零件的数控车削加工内容;(二)对零件图纸进行数控车削加工工艺分析;(三)工具、夹具的选择和调整设计;(四)切削用量选择;(五)工序、工步的设计;(六)加工轨迹的计算和优化;(七)编制数控加工工艺技术文件。
最近观察了很多数控车的技术工人,阅读了不少关于数控车削加工工艺的文章,发现大部分的使用者采用选择并确定零件的数控车削加工内容、零件图分析、夹具和刀具的选择、切削用量选择、划分工序及拟定加工顺序、加工轨迹的计算和优化、编制数控加工工艺技术文件的顺序来进行工艺分析。
但是分析了上述的顺序之后,发现有点不妥。
因为整个零件的工序、工步的设计是工艺分析这一环节中最重要的一部分内容。
工序、工步的设计直接关系到能否加工出符合零件形位公差要求的零件。
工序、工步的设计不合理将直接导致零件的形位公差达不到要求。
换言之就是工序、工步的设计不合理直接导致产生次品。
二、分析问题目前,数控车床的使用者的操作水平非常高,并且能够独立解决很多操作上的难题,但是他们的理论水平不是很高,这是造成工艺分析顺序不合理的主要原因。
造成工艺分析顺序不合理的另一个原因是企业的工量具设备不足。
浅谈数控车削加工工艺分析

浅 谈 数 控 车 削 加 工 工 要 : 普通 车床 曲加 工工 艺是 由操 作者操 作 机床 实现 的, 数 控机 床 曲工 艺是 预先 在所 辖制 的程 序 中体现 曲, 而 由程序 控 制机床 自动 实现 . 理 的加 工 工 艺对提 高 数控 机 床 的加工 效 率和 加 工精 度 至关 重要 . 合 本文 从 生产 实 践 出发 , 讨和 总结一 些 探 数控 车 削过 程 中 的加工 工 艺分 析 。 关键词 : 数控车床 车 削加 工工 艺 工艺分析 车 削
前 言 夹具 除 了 使 用 通 用 的 三 爪 自动 定 心 卡盘 、 精 确 , 夹误 差 越 小 ; ) 装 ( 程序 段 最 少 。 ) 5 ( 走 6 数控 机床作为一 种高效率 的设备 , 欲 四爪 卡盘 、 液压 、 动 及 气 动 夹 具 外 , 有 刀 路 线 最短 。 刀 路 线最 短 , 电 还 走 不仅 可 以节 省 充 分 发挥 其 高 性 能 、 精 度 和 高 自动 化 的 多 种 通 用 性 较 好 的 专 用 夹具 。 际 操 作 时 整 个 加 工 过程 的 执 行 时 间 , 能 减 少 一 些 高 实 还 特点 , 了必 须 掌握 机 床 的性 能 、 点及 操 应 合 理 选 择 。 除 特 不 必 要 的刀 具 消 耗 及 机床 进 给 机 构 滑动 部 作方 法 外 , 应 在 编 程 前 进 行 详 细 的工 艺 还 4 工 件 原 点 的 选 择 、 件 的 磨 损 等 。 工 路 线 的 确 定 首 先 必 须 保 加 分 析 , 据 具 体 条 件 , 择 经 济 、 理 的 工 根 选 合 同一 个 零 件 , 样 的 加 工 , 同 由于 原 点 选 证 被 加 工 零 件 的 尺 寸精 度 和 表 面 质 量 , 其 艺方案 , 以得
数控车工实训心得体会(通用10篇)
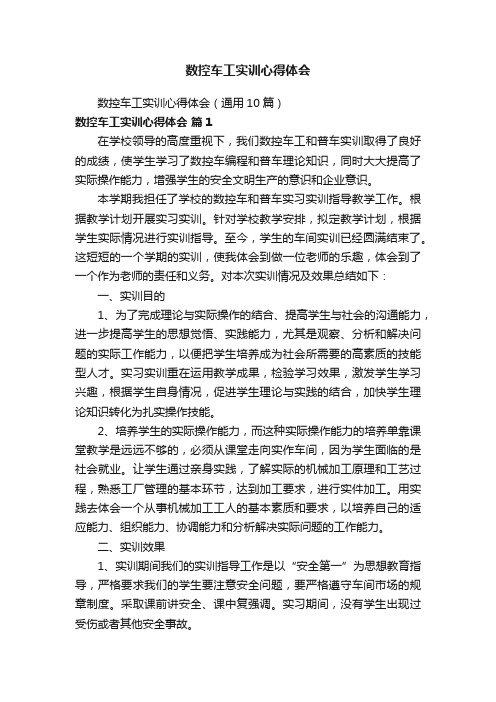
数控车工实训心得体会数控车工实训心得体会(通用10篇)数控车工实训心得体会篇1在学校领导的高度重视下,我们数控车工和普车实训取得了良好的成绩,使学生学习了数控车编程和普车理论知识,同时大大提高了实际操作能力,增强学生的安全文明生产的意识和企业意识。
本学期我担任了学校的数控车和普车实习实训指导教学工作。
根据教学计划开展实习实训。
针对学校教学安排,拟定教学计划,根据学生实际情况进行实训指导。
至今,学生的车间实训已经圆满结束了。
这短短的一个学期的实训,使我体会到做一位老师的乐趣,体会到了一个作为老师的责任和义务。
对本次实训情况及效果总结如下:一、实训目的1、为了完成理论与实际操作的结合、提高学生与社会的沟通能力,进一步提高学生的思想觉悟、实践能力,尤其是观察、分析和解决问题的实际工作能力,以便把学生培养成为社会所需要的高素质的技能型人才。
实习实训重在运用教学成果,检验学习效果,激发学生学习兴趣,根据学生自身情况,促进学生理论与实践的结合,加快学生理论知识转化为扎实操作技能。
2、培养学生的实际操作能力,而这种实际操作能力的培养单靠课堂教学是远远不够的,必须从课堂走向实作车间,因为学生面临的是社会就业。
让学生通过亲身实践,了解实际的机械加工原理和工艺过程,熟悉工厂管理的基本环节,达到加工要求,进行实件加工。
用实践去体会一个从事机械加工工人的基本素质和要求,以培养自己的适应能力、组织能力、协调能力和分析解决实际问题的工作能力。
二、实训效果1、实训期间我们的实训指导工作是以“安全第一”为思想教育指导,严格要求我们的学生要注意安全问题,要严格遵守车间市场的规章制度。
采取课前讲安全、课中复强调。
实习期间,没有学生出现过受伤或者其他安全事故。
2、通过直接参与加工的运作过程,学到了实践知识,同时进一步加深了对理论知识的理解,达到理论联系实际,使理论与实践知识都有所提高,到达了实训基本目的。
首先是让学生了解、复习理论知识。
数控机床加工工艺技术分析

数控机床加工工艺技术分析数控机床是一种自动化程度较高的机床,具有高精度、高效率、高灵活性等特点,广泛应用于各个领域的加工生产中。
在数控机床加工中,工艺技术是非常重要的一环,涉及到加工参数的选择、刀具路径的规划、加工策略的制定等方面,关系到产品的成品率、质量和生产效率。
以下是对数控机床加工工艺技术的分析:首先,数控机床加工的工艺技术包括:加工对象的特征分析、工序分析、加工参数的选择、刀具路径的规划、加工策略的制定等。
加工对象的特征分析是工艺技术的第一步,它对加工对象的尺寸、材料、形状等进行综合分析,确定了加工的难度和复杂性,并为后续的工艺技术提供了依据。
工序分析是对产品进行工艺划分,将整个加工过程划分为若干个工序,每个工序负责完成产品的一些加工环节,确定了各个工序之间的关系和顺序。
加工参数的选择是根据加工对象的特点和要求,选择合适的切削速度、进给量、切削深度等参数,以保证加工过程的稳定性和合理性。
刀具路径的规划是在数控机床上进行的,根据产品的形状和加工要求,确定了刀具移动轨迹和加工路径,以保证加工的准确性和效率。
加工策略的制定是在确定了刀具路径之后,根据材料的特点和加工要求,选择合适的切削方式、切削深度、切削速度等,以达到高效率和高质量的加工效果。
在数控机床加工中,工艺技术的优化是非常重要的。
通过合理的工艺技术优化,可以提高加工效率和产品质量,减少加工成本,提高企业的竞争力。
总之,数控机床加工的工艺技术分析对于提高产品加工质量、生产效率和降低成本具有重要作用。
只有通过综合分析加工对象的特征、合理选择加工参数、规划刀具路径和制定合理的加工策略,才能实现高效、高质量的数控机床加工。
数控车削加工工艺与分析
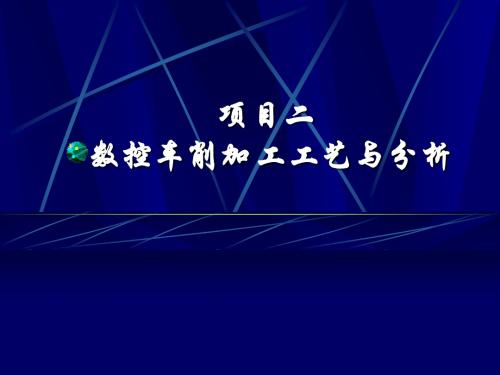
数控加工工艺分析的一般步骤与 方法
10.工艺加工路线的确定
工艺加工路线是指数控加工过程中 刀位点相对于被加工零件的运动轨迹。 编程时,确定工艺加工路线的原则是: (1)保证零件的加工精度和表面粗糙度; (2)方便数值计算,减少编程工作量; (3)缩短加工运行路线,减少空运行行程。
数控车削工艺
1. 选择正确数控车削加工内容
(c)“矩形”进给路
数控加工工艺分析的一般步骤与 方法
5. 零件的安装
1、设计基准、工艺基准和编程计算基准统一。 2、尽量减少装夹次数,尽可能在一次定位装夹 后,加工出全部待加工表面。 3、避免采用占机人工调整加工方案,以便能充 分发挥出数控机床的效能。
数控加工工艺分析的一般步骤与 方法
6. 夹具的选择
3. 加工方法的选择与加工方案的确定 1.加工方法的选择 数控车削内、外回转表面的加工方案的确定,应 注意以下几点。 (1)加工精度为IT8~IT9级、表面粗糙度Ra1.6~3.2 m、 除淬火钢以外的常用金属,可采用普通型数控车床,按粗车、 半精车、精车的方案加工。 (2)加工精度为 IT6~IT7级、表面粗糙度Ra0.2~0.63 m、 除淬火钢以外的常用金属,可采用精密型数控车床,按粗车、 半精车、精车、细车的方案加工。 (3)加工精度为IT5级、表面粗糙度Ra<0.2 m的除淬火 钢以外的常用金属,可采用高档精密型数控车床,按粗车、 半精车、精车、精密车的方案加工。
只需确定每次背吃刀量 也需计算粗车时终刀距S。 ap ,而不需计算终刀距 , 按此种加工路线,刀具切 编程方便。但在每次切 削运动的距离较短,精车 削中背吃刀量 是变化的 , 时背吃刀量相同。 且刀具切削运动的路线 较长。
数控加工工艺分析的一般步骤与 方法
浅谈数控车削加工工艺性分析
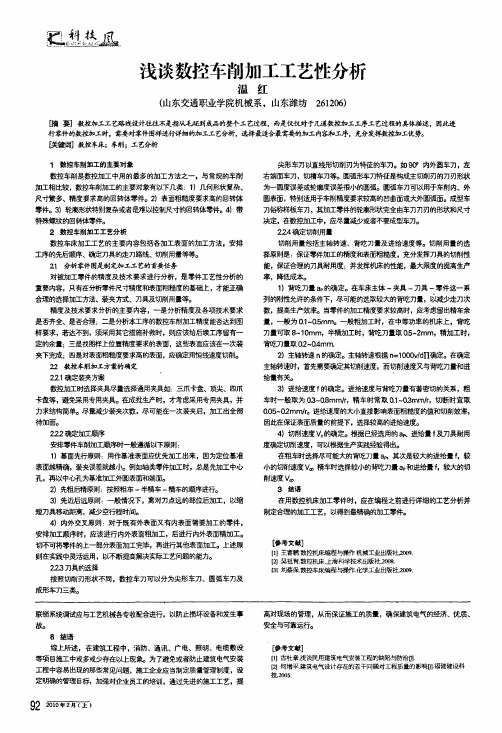
鲑塑龃.浅谈数控车削加工工艺性分析温红(山东交通职业学院机械系,山东潍坊261206)喃要】数控加工工艺路线设计往往不是指酞毛坯到成品的整个工艺过程,而是仅饭砖于凡道数控咖工工序工艺过程的具体描述,因此进行零件的数控加工时,需要对零件图样进行详细的加-r-r艺分析,选择最适合最需要妁加工内容和工序,充分发挥数控加工优势。
拱键阑】敷控车床;车鲥;工艺分析1数控车削加工的主要对象数控车削是数拗Ⅱ工中用的最多的加工方法之一,与常规的车削加工相比较,数控车削加工的主要对象有以下几类:1)几何形状复杂、尺寸繁多、精度要求高的回转体零件。
2)表面相糙度要求高的回转体零件。
3)轮廓形状特另0复杂或者是难以控制尺寸的回转体零件。
4)带特殊螺纹的回转体零件。
2数控车削加工工艺分析数控车床加工工艺的主要内容包括各加工表面的加工方法,安排工序的先后顺序、确定刀具的走刀路线、切肖4用量等等。
2.1分析零件图是制定加工工艺的首要任务对被力l IT零件的精度及技术要求进行分析,是零件工艺性分析的重要内容,只有在分析零件尺寸精度和表面粗糙度的基础上,才能正确合理的选择加工方法、装夹方式、刀具及切削用嚣等。
精度及技术要求分析的主要内容,一是分析精度及各项技术要求是否齐全、是否合理:二是分析本工序的数控车削加工精度能否达到图t'4-要求,若达不到,须采用其它措施补救时,则应该给后续工序留有一定的余量;三是找图样上位置精度要求的表面,这些表面应该在一次装夹下完成;四是对表面旧糙度要求高的表面,应确定用恒线速度切削。
22数控车削加工方案的确定22_1确定装夹方案釜起腔加工时选择夹具尽量选择通用夹具如:三爪卡盘、顶尖、四爪卡盘等,避免采用专用夹具。
在成批生产时,才考虑采用专用夹具,并力求结构简单。
尽量减少装夹次数,尽可能在一次装夹后,)JoT出全部待加面。
Z猃确定加工顺序安排零件车削加工JI酾耐—般遵循以下原则:1)基面先行原则:用作基准表面应优先]b0"r出来,因为定位基准表面越精确,装夹误差就越小。
浅谈数控车削加工工艺性分析

2 0 1 3 年 第6 期I 科技创 新 与应用
浅谈 数控 车 削加工 工艺性 分析
吕雅 妍
( 哈 尔滨空调股份有 限公 司, 黑龙 江 哈 尔滨 1 5 0 0 7 8 )
摘 要: 数控 机 床是 我 国机 械 设 备 领域 的 高精 度设 备 之 一 , 其 自动化 程 度 较 高 , 属 于 高科技 产品 , 目前 已成 为机械 设 备 领 域 的主 流设 备 。数 控机 床 的 高精 准性使 其成 为 加 工行 业 的 重要 设 备 , 同 时其加 工工 艺 虽 然传 承 了普 通 机床 设 备 的 诸 多优 点 , 但 还是 有 许 多不 同之 处的 。为 此 , 对数 控 车 削加 工 工 艺的 内容 进 行 了分 析 , 并进 一 步 对数 控加 工工 艺进 行 了具 体 的 阐述 。 关键 词 : 数控 车床 ; 车 削加 工 工 艺 ; 工 艺分析 ; 车削 来, 所 切 削 的力 量 越 大 , 因此 在切 削零 件 时 尽 可 能选 择 直 径 大 的刀 数控机床作为一种高效率 的自动化设备 , 其工作效率是普通机 具 , 这样 不 仅 有 利 于 切 削效 率 的提 高 , 同时 对延 长刀 具 的寿 命 也 具 床所无法 比拟 的, 因此在使用时要对其功 能进行充分的发挥 , 需要 有 积 极 的作 用 。 数 控 车 削常 用 的刀 具一 般 分 为 3类 。 即尖 形 车刀 、 圆 在编程之前就做好工艺分析 , 确保数控J J U T的工艺更加详细 , 从 而 弧 形 车刀 和 成 型车 刀 。 对充分提高数控机床的加工质量、 生产效率及除低加工成本。 ( 1 ) 尖形车刀 。以直线形切削刃为特征 的车刀一般称为尖形车 1数控 车 削加 工 工艺 的内容 刀 。其刀 尖 由直 线 性 的主 、 副切 削 刃 构成 。 数控车床在加工零件 时需要运用一定 的方法 和技术手段来完 ( 2 ) 圆弧 形车 刀 。 除 可车 削 内外 圆表 面 外 , 特别 适 宜于 车 削各 种 成加工任务 , 这即是数控车削加工工艺 。 其具体包含以下几个方面 : 光 滑 连接 的成 型面 。 ( 1 ) 选 择并 确 定 零件 的数 控 车 削加 工 内容 ; ( 2 ) 对零 件 图纸进 行 ( 3 ) 成 型 车刀 。即所 加 工 零件 的轮 廓形 状 完 全 由车 刀 刀刃 的形 数 控 车削 加 工工 艺 分 析 ; ( 3 )工 具 、夹 具 的 选择 和 调 整设 计 ; ( 4 ) 工 状 和 尺寸 决 定 。数 控车 削 加工 中 , 常 用 的成 型 车 刀有 小 半 径 圆弧 车 序、 工步的设计 ; ( 5 ) 加工轨迹 的计算和优化 ; ( 6 ) 数控车削加工程序 刀 、 车 槽 刀 和螺 纹 车刀 等 的编写 、 校验与修改 ; ( 7 ) 首件试加工与现场问题 的处理 ; ( 8 ) 编制数 2 - 3切 削 用量 选 择 控 加工 工 艺 技术 文 件 。 数控 车削 加 工 中的 切 削 用 量包 括 背 吃刀 量 a p 、 主轴转速 S ( 或 总之 , 数控加工工艺 内容较 多, 虽然部分 与普通机床有很多相 切 削 速度 ) 及 进 给速 度 F ( 或进 给 量 f ) 。 似 的 地方 , 但 因其 精度 高 , 自动 化程 度 较 高 等 特 点 与普 通 加 要 还 有 数控 车床 的加 工质 量 与切 削 用 量 的选 择 有十 分 重要 的关 系 , 因 许 多 区别 的地 方 。 此 在 数控 车床 的加 工 中 , 合 理 的选 用 切 削 用量 具 有重 要 意 义 。 因此 2 数控 车削 加工 工 艺分 析 在数控车床加工 中可以根据车床的说 明书规定 的要求 , 同时根据刀 工艺分析是根据 图纸上对零件加工要求分析其合理性 , 同时确 具 的 耐用 度来 选 择 , 也 可结 合实 际经验 采 用类 比法来 确 定 。 定加工零件在数控车床上采取何处装夹方式 , 并对零件各表面的加 2 . 4划分工序及拟定加工顺序 工顺序 、 进给路线及用量等进行合理 的选择 。这是车削加工的前期 2 . 1工序 划 分 的原 则 准备阶段 , 对工艺制定 的分析直接影响着 以后编程 、 加工效率和零 在数控车床上加工零件, 常用的工序的划分原则有两种 。 件加 工 精 度 。 同时车 削 加工 工 艺 中对 于程 度 的 编制 非 常 严格 , 对 编 ( 1 ) 保持精度原则。 在加工工序中通常情况下会要求把粗 、 精加 程者的要求较高 , 为了保证程度 的合理和实用性 , 要求 编程者不仅 工在一次装夹 中全部完成 , 但为了保持切削的精度 , 应该把粗 、 精加 要 熟 悉程 序语 言 还 要 对 数 控 车 床 的工 作 原 理 、 性能 、 加 工 工 艺 熟 练 工 分 开进 行 , 这样 就 能 在很 大程 度 上 减 少热 变 形 和切 削 力 变形 对 所 掌握 , 这样才能保证加工工艺的合理 、 实用性。因此 , 在对数控车削 加 要 的零 件 的形 态 、 精度 和 粗糙 度 的影 响。 工艺分析时要根据数控车床的特点和加工工艺原则进行 , 确保其加 ( 2 ) 提高生产效率原则 。一把刀能加工 的加工部位需要在换刀 工 工艺 合 理 、 实用 。 前全部完成 , 这样就有效 的减少了换刀的时间, 对生产效率的提高 2 . 1零 件 图分 析 起 到促 进 作用 , 同 时在换 刀 时尽 量 避免 空 行 程 。 2 . 1 . 1尺寸 标 注方 法 分析 2 . 4 . 2 确定 加 工顺 序 零件图上 的尺寸标注方法应适应数控车床 的加工特点 , 以同一 制定 加工 顺 序一 般 遵循 下 列原 则 : 基准标注尺寸或直接给出坐标尺寸。这种标注方法既便 于编程 , 又 ( 1 ) 先粗后精 。在加工过程 中应该按照粗车 、 半精车、 精车 的顺 有利 于设 计基 准 、 工 艺基 准 、 测 量基 准 和 编程 原 点 的统 一 。 序进行 , 不可能一次就达到精车的目的, 应该逐步提高加工精度。 2 . 1 . 2 轮廓 几何 要 素 分析 ( 2 ) 先 近 后远 。 这 是针 对 对刀 点 近 的位 置来 说 的 , 对 于 离对 刀 点 在手工编程时 , 要计算每个节点坐标。在 自动编程时要对零件 近 的 部 位 要先 加 要 , 这 样 刀 具 移 动 的距 离 会 有 所 缩 短 , 避 免 了 刀 具 轮廓 的所有几何元素进行定义 。因此在零件图分析时 , 要分析几何 的空 程时 间 , 同 时对 车 削 的半成 品的 刚 性和 改 善切 削 条 件都 是 具 有 元 素 的给定 条 件 是否 充 分 。 十 分 重要 意义 的。 2 . 1 . 3精度和技术要求分析 ( 3 ) 内外 交叉 。 对 于 内外 表面 都 需要 进 行加 工 的零 件 , 则需 要 先 对 被 加工 零 件 的精 度 和技 术 进行 分 析 , 是 零 件工 艺 性 分 析 的重 进 行粗 加 工 , 然后 再 进行 精 加工 。 要内容 , 只 有 在 分 析零 件 尺 寸 精 度 和表 面 粗 糙 度 的 基 础 上 , 才 能 正 ( 4 ) 基 面先 行 。 首 先应 把 用作 精 基准 的表 面先 加工 出来 , 这 样 就 确合 理 地 选择 加 工方 法 、 装 夹方 式 、 刀 具及 切 削用 量 等 。 其 主 要 内容 有 效 的减 少 了装 夹 的误 差 。 包括 : 分 析 精度 及 各 项技 术 要求 是 否 齐 全 、 是否 合 理 ; 分 析 本 工序 的 3结束 语 数控车削加工精度能否达到图纸要求 , 若达不到 , 允许采取其他加 随着 数控 机 床 的不 断发 展 , 其 做 为 一种 高科 技 技 术集 于一 身 的 工方式弥补时 , 应 给后续工序留有余量 ; 对图纸上有位置精度要求 全 自动化机械设备 , 其 自身的高性能、 高精度和高 自动化 的特点使 的表 面 , 应 保证 在 一 次装 夹 下完 成 ; 对 表 面 粗糙 度 要 求较 高 的表 面 , 其在使用过程 中需要具有较强的专业知识 , 熟练掌握数控的编程程 应采 用 恒线 速 度 切削 。 序, 对加工工艺进行详细的分析 , 从 而确定最优 的加工方案 , 提高机 2 . 2夹 具 和刀 具 的选 择 床加工工艺的合理性和实用性 , 从而确保加工的零件满足规定 的质 2 . 2 . 1工 件 的装 夹 与定 位 量 要求 。 数控车削加工中的装夹对加工效率和精度 的影响都较大 , 因此 参 考 文献 尽量做到一次装夹即完成需要加工的全部零部件的加工表面 , 这样 [ 1 ] 杜 国臣. 机床数控技术『 M ] . 北京: 中国林业出版社 , 2 0 0 6 . 不仅提高了加工的效率 , 同时也能保证加工 的精准度 。同时对于不 [ 2 ] 孙 文诚 . 高速切 削加 工模 具 的 关键 技 术研 究l J 1 . 机 械 制 造 与 自动 化 同类 型 的零 件 其选 择 定位 的基 准 也不 一 样 ,其 中轴类 以外 圆 柱 面 、 2 0 0 8 ( 5 ) . 套类 以内孔为定位基准。另外对 于数控车床的夹具也有多种选择, [ 3 】 邱 小 燕. 数 控 车 削加 工 工 艺性分 析 科技 风 . 2 0 1 1 年0 1 期. 可根据实际操作和 自己的需要选择合理的夹具 。
对数控车削加工课程的学习体会

对数控车削加工课程的学习体会
在学习数控车削加工课程的过程中,我深刻体会到了其重要性和实用性。
数控车削加工作为现代制造业中的核心技术之一,对于提高产品质量、降低成本具有重要意义。
数控车削加工课程为我提供了理论知识和实践技能的全面培养。
通过学习,我了解到数控车床的基本原理、操作方法以及常见的加工工艺。
在实践环节中,我亲手操作数控车床进行编程和加工,进一步巩固了所学知识,培养了实际操作的能力。
数控车削加工课程培养了我良好的观察和分析能力,在加工过程中,我需要仔细观察加工件的形态、尺寸和表面质量,及时调整机床参数和工艺,以保证最终产品的质量要求。
这种观察和分析的能力在实际工作中尤为重要,能够帮助我快速定位问题并解决。
数控车削加工课程让我了解到了数字化制造的发展趋势,在现代工业中,数控技术的应用已经成为一种趋势。
通过数控车削加工课程的学习,我明白了数字化制造的优势,例如提高生产效率、减少人工干预、降低生产成本等。
这些知识将对我未来的职业发展产生积极的影响。
数控车削加工课程的学习让我深入了解了数控车削加工的原理和技术,并培养了实践操作能力和观察分析能力。
我相信这些知识和技能将为我未来的职业发展打下坚实的基础,使我在制造业领域中具备竞争力。
数控车削实践心得体会

一、前言随着现代制造业的不断发展,数控技术已经成为制造业的重要支柱。
数控车削作为数控技术的重要组成部分,广泛应用于机械加工领域。
在我国,数控车削技术的研究和应用取得了显著成果。
本人有幸参与了数控车削实践,通过亲身体验,对数控车削技术有了更深入的了解。
以下是我在数控车削实践过程中的心得体会。
二、数控车削概述数控车削是利用计算机数控系统对车床进行控制,实现自动化、高精度加工的一种先进加工方法。
数控车削具有以下特点:1. 高精度:数控车削加工精度高,可以达到0.001mm,甚至更高。
2. 高效率:数控车削加工速度快,生产效率高,能够满足大批量生产的需要。
3. 易于实现复杂形状加工:数控车削可以加工各种复杂形状的零件,如螺纹、曲线、曲面等。
4. 操作简便:数控车削操作简单,只需编写好加工程序,即可实现自动化加工。
5. 节能环保:数控车削加工过程中,能耗低,对环境友好。
三、实践过程1. 学习数控车削基础知识在实践之前,我首先学习了数控车削的基本知识,包括数控车床的结构、工作原理、编程方法等。
通过学习,我对数控车削有了初步的认识。
2. 编写加工程序在掌握了基本知识后,我开始学习编写加工程序。
编程过程中,我遇到了很多困难,如坐标系选择、刀具路径规划、加工参数设置等。
在老师和同学的帮助下,我逐渐掌握了编程技巧。
3. 车削实践在编写好加工程序后,我开始进行车削实践。
在实践过程中,我遵循以下步骤:(1)安装工件:将工件安装在卡盘上,确保工件与卡盘的接触良好。
(2)调整机床参数:根据加工程序,调整机床参数,如转速、进给速度、刀具参数等。
(3)装夹刀具:根据加工要求,选择合适的刀具,并安装到机床刀架上。
(4)启动机床:启动机床,运行加工程序,进行车削加工。
(5)检查工件:加工完成后,检查工件尺寸、形状是否符合要求。
4. 总结经验在实践过程中,我总结了一些经验:(1)熟悉机床性能:在操作机床之前,要熟悉机床的性能,了解机床的极限参数,避免因操作不当导致机床损坏。
车削加工心得体会

车削加工心得体会车削加工是一种常见的金属加工方法,通过旋转切削工件来改变其形状和尺寸。
在我从事车削加工工作的过程中,我积累了一些心得体会。
首先,工艺规范十分重要。
在进行车削加工之前,需要仔细研究和制定工艺规范。
这包括确定切削参数、选择合适的刀具和夹具,并设计出合理的刀具路径等。
合理的工艺规范能够提高加工效率,减少切削力和磨损,并确保加工质量。
其次,刀具选择关键。
不同的工件材料和形状需要选择不同类型的刀具。
刀具的质量和性能直接影响到加工的效果和刀具寿命。
在选择刀具时,要考虑到切削力、切削稳定性和刀具寿命等因素,以确保最佳的加工效果。
另外,加工过程中要保持机床的良好状态。
机床是进行车削加工的基础设备,它的性能和状态直接影响到加工质量和效率。
因此,及时进行机床维护和保养是非常重要的。
保持机床的润滑、调整和清洁,能够减少故障发生,提高机床的稳定性和可靠性。
此外,加工过程中要保持良好的操作习惯。
操作人员要熟悉加工工艺和机床设备,按照规范要求进行操作。
在加工过程中,要注意保持安全,避免操作中发生意外。
同时,要保持专注和集中,及时发现和解决加工中的问题,确保加工质量。
对于我个人来说,从事车削加工工作让我深刻体会到了“细节决定成败”的道理。
在车削加工过程中,每一个细小的环节都会对最终的加工效果产生重要的影响。
因此,我注重做好每一个操作环节,严格按照工艺规范进行加工。
当然,这也要求我具备良好的技术素质和职业道德,不断学习和提高,以确保自己能够胜任各种复杂的车削加工任务。
在实际的车削加工中,我发现刀具的钝化和磨损是常见的问题。
为了延长刀具的使用寿命,我探索了一些有效的方法。
首先,我对刀具进行合理的切削参数调整,使得切削力和磨损降到最低。
其次,我注重对刀具进行定期的检查和维护,及时更换损坏的刀具,保持刀具的良好状态。
这些方法的实施使得刀具的使用寿命得到了明显的延长,减少了生产成本。
通过从事车削加工工作,我也深刻认识到了团队合作的重要性。
南京工业大学数控车削加工工艺分析
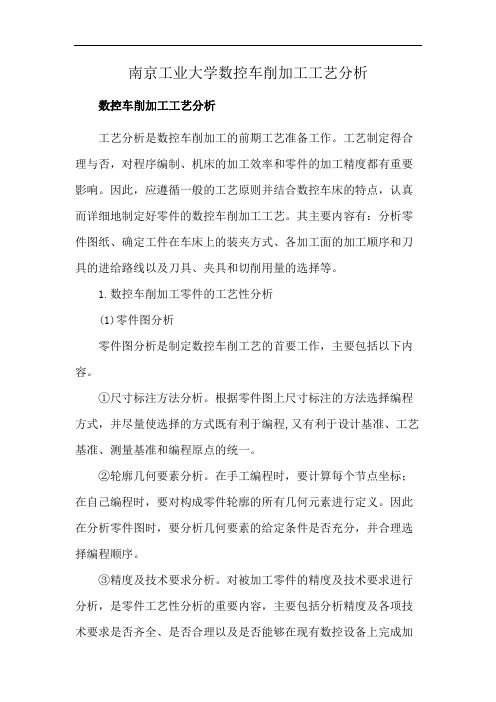
南京工业大学数控车削加工工艺分析数控车削加工工艺分析
工艺分析是数控车削加工的前期工艺准备工作。
工艺制定得合理与否,对程序编制、机床的加工效率和零件的加工精度都有重要影响。
因此,应遵循一般的工艺原则并结合数控车床的特点,认真而详细地制定好零件的数控车削加工工艺。
其主要内容有:分析零件图纸、确定工件在车床上的装夹方式、各加工面的加工顺序和刀具的进给路线以及刀具、夹具和切削用量的选择等。
1.数控车削加工零件的工艺性分析
(1)零件图分析
零件图分析是制定数控车削工艺的首要工作,主要包括以下内容。
①尺寸标注方法分析。
根据零件图上尺寸标注的方法选择编程方式,并尽量使选择的方式既有利于编程,又有利于设计基准、工艺基准、测量基准和编程原点的统一。
②轮廓几何要素分析。
在手工编程时,要计算每个节点坐标;在自己编程时,要对构成零件轮廓的所有几何元素进行定义。
因此在分析零件图时,要分析几何要素的给定条件是否充分,并合理选择编程顺序。
③精度及技术要求分析。
对被加工零件的精度及技术要求进行分析,是零件工艺性分析的重要内容,主要包括分析精度及各项技术要求是否齐全、是否合理以及是否能够在现有数控设备上完成加
工,若不能完成,需采取其他措施(如磨削)弥补时,则应给后续工序留有余量;
对表面粗糙度要求较高的表面,应确定用恒线速切削。
数控车削加工工艺分析

数控车削加工工艺分析【摘要】理想的数控车削加工工艺不仅能保证加工出符合图样的合格工件,同时能使数控车床的功能得到合理的应用和充分的发挥。
【关键词】数控车床;车削工艺;加工质量;生产效率数控车床是一种高效率的自动化设备,它的效率高于普通车床的2~3倍,要充分发挥数控车床的这一特点,必须在编程之前对工件进行工艺分析,根据具体条件,选择经济、合理的工艺方案。
数控加工工艺考虑不周将影响数控车床加工质量、生产效率及加工成本。
本文从生产实践出发,探讨和总结一些数控车削过程中的工艺问题。
1.数控加工工序的划分在数控车床上加工零件,工序比较集中,一次装夹应尽可能完成全部工序,常用的工序划分原则有以下两种。
1.1 保证精度原则数控加工具有工序集中的条件,粗、精加工常在一次装夹中完成,以保证零件的加工精度,当热变形和切削力变形对零件的加工精度影响较大时,应将粗、精加工分开进行。
1.2 提高生产效率的原则数控加工中,为减少换刀次数,节省换刀时间,应将需用同一把刀加工的加工部位全部完成后,再换另一把刀来加工其它部位。
同时应尽量减少空行程,用同一把刀加工工件的多个部位时,应以最短的路线到达各加工部位。
实际生产中,数控加工常按刀具或加工表面划分工序。
2.车刀刀位点的选择数控加工中,数控程序应描述出刀具相对于工件的运动轨迹。
在数控车削中,工件表面的形成取决于运动着的刀刃包络线的位置和形状,但在程序编制中,只需描述刀具系统上某一选定点的轨迹即可。
刀具的刀位点即为在程序编制时,刀具上所选择的代表刀具所在位置的点,程序所描述的加工轨迹即为该点的运动轨迹。
在数控车削中,从理论上讲可选择刀具上任意一点作为刀位点,但为了方便编程和保证加工精度,刀位点的选择有一定的要求和技巧。
在数控加工中,刀位点的选择一般遵循以下规则:立铣刀应是刀具轴线与刀具底面的交点:球头铣刀是球头的球心:钻头应是钻尖:车刀应是假想刀尖或刀尖圆弧中心,刀具刀位点在选择时应注意:选择刀具上能够直接测量的点,刀位点与刀具长度预调时的测定点应尽量一致:在可能的情况下,刀位点应直接与精度要求较高的尺寸或难于测量的尺寸发生联系,所选择的刀位点能使刀具极限位置直接体现于程序的运动指令中:编程人员应有习惯性的刀位点选择方法,不宜多变。
车削实训体会

车削实训体会车削实训是机械加工专业的一项重要技能训练,它对学生的实践操作和技术应用能力有着重要的促进作用。
通过参与车削实训,我深刻体会到了学习和实践的重要性,并且对车削加工的技术和过程有了更加全面的认识。
以下是我在车削实训中的一些体会和心得。
1. 学习理论知识的重要性在车削实训前,我首先学习了车削加工的基本理论知识,包括切削力、刀具选择、切削速度等。
这些理论知识对于我理解车削加工的原理和操作规范起到了重要的指导作用。
在实际操作中,只有准确地应用这些理论知识,才能够保证操作的准确性和安全性。
因此,学习理论知识是进行车削实训的第一步,也是非常重要的一步。
2. 实践操作的技能培养车削实训的核心是实践操作,通过亲自操作车床、选择刀具、调整切削参数等,我深入了解了车削加工的具体过程。
通过实际操作,我更加熟悉了机床的结构和使用方法,提高了自己的操作技能。
同时,我也学会了如何判断加工质量和加工精度,以及如何解决操作中出现的问题。
实践操作是提高车削技术的关键,只有通过多次实际操作,才能够熟练掌握车削加工的技能。
3. 团队协作与沟通能力在车削实训中,我有幸与其他同学一起组成小组进行实践操作。
通过团队协作,我们相互帮助、相互学习,共同完成实训任务。
每个人都负责不同的工作环节,要求我们在操作过程中进行有效的沟通和协作。
通过与团队成员的合作,我不仅学到了更多的车削技巧,还提高了团队协作和沟通能力。
团队合作是实践能力的重要表现,也是未来工作中必不可少的能力。
4. 安全意识与责任心的培养车削加工是一项高风险的操作,要求我们时刻保持安全意识,确保自身和他人的安全。
在车削实训中,我们必须严格遵守操作规程,正确使用个人防护设备,并保持清醒的头脑和稳定的情绪。
此外,在实践操作中,我还要对操作过程的安全性进行评估,及时发现和排除潜在的安全隐患。
通过车削实训,我意识到安全问题是车削加工中必不可少的一环,也深深体会到了责任心的重要性。
5. 持续学习和自我提升的重要性车削实训只是机械加工专业学习的一个起点,对于我们的学习和职业发展来说,只有持续学习和自我提升,才能够不断适应和应对工作中的挑战。
- 1、下载文档前请自行甄别文档内容的完整性,平台不提供额外的编辑、内容补充、找答案等附加服务。
- 2、"仅部分预览"的文档,不可在线预览部分如存在完整性等问题,可反馈申请退款(可完整预览的文档不适用该条件!)。
- 3、如文档侵犯您的权益,请联系客服反馈,我们会尽快为您处理(人工客服工作时间:9:00-18:30)。
数控车削加工工艺分析及数控车削加工工艺实用价值理想的加项目序不仅应保证加工出符合图样的合格工件,同时应能使数控机床的功能得到合理的应用和充分的发挥。
数控机床是一种高效率的自动化设备,它的效率高于普通机床的2~3倍,要充分发挥数控机床的这一特点,必须在编程之前对工件进行工艺分析,根据具体条件,选择经济、合理的工艺方案。
数控加工工艺考虑不周是影响数控机床加工质量、生产效率及加工成本的重要因素。
本文从生产实践出发,探讨和总结一些数控车削过程中的工艺问题。
一、问题的提出数控车削加工主要包括工艺分析、程序编制、装刀、装工件、对刀、粗加工、半精加工、精加工。
而数控车削的工艺分析是数控车削加工顺利完成的保障。
数控车削加工工艺是采用数控车床加工零件时所运用的方法和技术手段的总和。
其主要内容包括以下几个方面:(一>选择并确定零件的数控车削加工内容。
(二>对零件图纸进行数控车削加工工艺分析。
(三>工具、夹具的选择和调整设计。
(四>切削用量选择。
(五>工序、工步的设计。
(六>加工轨迹的计算和优化。
(七>编制数控加工工艺技术文件。
最近观察了很多数控车的技术工人,阅读了不少关于数控车削加工工艺的文章,发现大部分的使用者采用选择并确定零件的数控车削加工内容、零件图分析、夹具和刀具的选择、切削用量选择、划分工序及拟定加工顺序、加工轨迹的计算和优化、编制数控加工工艺技术文件的顺序来进行工艺分析。
但是分析了上述的顺序之后,发现有点不妥。
因为整个零件的工序、工步的设计是工艺分析这一环节中最重要的一部分内容。
工序、工步的设计直接关系到能否加工出符合零件形位公差要求的零件。
工序、工步的设计不合理将直接导致零件的形位公差达不到要求。
换言之就是工序、工步的设计不合理直接导致产生次品。
二、分析问题目前,数控车床的使用者的操作水平非常高,并且能够独立解决很多操作上的难题,但是他们的理论水平不是很高,这是造成工艺分析顺序不合理的主要原因。
造成工艺分析顺序不合理的另一个原因是企业的工量具设备不足。
三、解决问题其实分析了工艺分析顺序不合理的现象和原因之后,解决问题就非常容易了。
需要做的工作只要将对零件的分析顺序稍做调整就可以。
认为合理的工艺分析步骤应该是:(一>选择并确定零件的数控车削加工内容。
(二>对零件图纸进行数控车削加工工艺分析。
(三>工序、工步的设计。
(四>工具、夹具的选择和调整设计。
(五>切削用量选择。
(六>加工轨迹的计算和优化。
(七>编制数控加工工艺技术文件。
本文主要对二、三、四、五三个步骤进行详细的阐述。
(一>零件图分析零件图分析是制定数控车削工艺的首要任务。
主要进行尺寸标注方法分析、轮廓几何要素分析以及精度和技术要求分析。
此外还应分析零件结构和加工要求的合理性,选择工艺基准。
1.选择基准零件图上的尺寸标注方法应适应数控车床的加工特点,以同一基准标注尺寸或直接给出坐标尺寸。
这种标注方法既便于编程,又有利于设计基准、工艺基准、测量基准和编程原点的统一。
2.节点坐标计算在手工编程时,要计算每个节点坐标。
在自动编程时要对零件轮廓的所有几何元素进行定义。
3.精度和技术要求分析对被加工零件的精度和技术进行分析,是零件工艺性分析的重要内容,只有在分析零件尺寸精度和表面粗糙度的基础上,才能正确合理地选择加工方法、装夹方式、刀具及切削用量等。
(二>工序、工步的设计1.工序划分的原则在数控车床上加工零件,常用的工序的划分原则有两种。
(1>保持精度原则。
工序一般要求尽可能地集中,粗、精加工通常会在一次装夹中全部完成。
为减少热变形和切削力变形对工件的形状、位置精度、尺寸精度和表面粗糙度的影响,则应将粗、精加工分开进行。
(2>提高生产效率原则。
为减少换刀次数,节省换刀时间,提高生产效率,应将需要用同一把刀加工的加工部位都完成后,再换另一把刀来加工其他部位,同时应尽量减少空行程。
2.确定加工顺序制定加工顺序一般遵循下列原则:(1>先粗后精。
按照粗车半精车精车的顺序进行,逐步提高加工精度。
(2>先近后远。
离对刀点近的部位先加工,离对刀点远的部位后加工,以便缩短刀具移动距离,减少空行程时间。
此外,先近后远车削还有利于保持坯件或半成品的刚性,改善其切削条件。
(3>内外交叉。
对既有内表面又有外表面需加工的零件,应先进行内外表面的粗加工,后进行内外表面的精加工。
(4>基面先行。
用作精基准的表面应优先加工出来,定位基准的表面越精确,装夹误差越小。
(三>夹具和刀具的选择1.工件的装夹与定位数控车削加工中尽可能做到一次装夹后能加工出全部或大部分代加工表面,尽量减少装夹次数,以提高加工效率、保证加工精度。
对于轴类零件,通常以零件自身的外圆柱面作定位基准。
对于套类零件,则以内孔为定位基准。
数控车床夹具除了使用通用的三爪自动定心卡盘、四爪卡盘、液压、电动及气动夹具外,还有多种通用性较好的专用夹具。
实际操作时应合理选择。
2.刀具选择刀具的使用寿命除与刀具材料相关外,还与刀具的直径有很大的关系。
刀具直径越大,能承受的切削用量也越大。
所以在零件形状允许的情况下,采用尽可能大的刀具直径是延长刀具寿命,提高生产率的有效措施。
数控车削常用的刀具一般分为3类。
即尖形车刀、圆弧形车刀和成型车刀。
(四>切削用量选择数控车削加工中的切削用量包括背吃刀量ap、主轴转速S(或切削速度υ>及进给速度F(或进给量 f >。
切削用量的选择原则,合理选用切削用量对提高数控车床的加工质量至关重要。
确定数控车床的切削用量时一定要根据机床说明书中规定的要求,以及刀具的耐用度去选择,(下转第90 页> (上接第81 页>也可结合实际经验采用类比法来确定。
一般的选择原则是:粗车时,首先考虑在机床刚度允许的情况下选择尽可能大的背吃刀量ap。
其次选择较大的进给量f。
最后再根据刀具允许的寿命确定一个合适的切削速度υ。
增大背吃刀量可减少走刀次数,提高加工效率,增大进给量有利于断屑。
精车时,应着重考虑如何保证加工质量,并在此基础上尽量提高加工效率,因此宜选用较小的背吃刀量和进给量,尽可能地提高加工速度。
主轴转速S(r/min >可根据切削速度υ(mm/min>由公式S=υ1000/πD(D为工件或刀/具直径mm>计算得出,也可以查表或根据实践经验确定。
数控车削加工工艺实用价值1 数控加工工序数控加工工序的划分在数控机床上加工零件,工序比较集中,一次装夹应尽可能完成全部工序,常用的工序划分原则有以下两种。
保证精度原则数控加工具有工序集中的条件,粗、精加工常在一次装夹中完成,以保证零件的加工精度,当热变形和切削力变形对零件的加工精度影响较大时,应将粗、精加工分开进行。
提高生产效率的原则:数控加工中,为减少换刀次数,节省换刀时间,应将需用同一把刀加工的加工部位全部完成后,再换另一把刀来加工其它部位。
同时应尽量减少空行程,用同一把刀加工工件的多个部位时,应以最短的路线到达各加工部位。
实际生产中,数控加工常按刀具或加工表面划分工序。
2 车刀刀位点的选择数控加工中,数控程序应描述出刀具相对于工件的运动轨迹。
在数控车削中,工件表面的形成取决于运动着的刀刃包络线的位置和形状,但在程序编制中,只需描述刀具系统上某一选定点的轨迹即可。
刀具的刀位点即为在程序编制时,刀具上所选择的代表刀具所在位置的点,程序所描述的加工轨迹即为该点的运动轨迹。
在数控车削中,从理论上讲可选择刀具上任意一点作为刀位点,但为了方便编程和保证加工精度,刀位点的选择有一定的要求和技巧。
在数控加工中,刀位点的选择一般遵循以下规则:立铣刀应是刀具轴线与刀具底面的交点:球头铣刀是球头的球心:钻头应是钻尖:车刀应是假想刀尖或刀尖圆弧中心,刀具刀位点在选择时应注意:选择刀具上能够直接测量的点,刀位点与刀具长度预调时的测定点应尽量一致:在可能的情况下,刀位点应直接与精度要求较高的尺寸或难于测量的尺寸发生联系:所选择的刀位点能使刀具极限位置直接体现于程序的运动指令中:编程人员应有习惯性的刀位点选择方法,不宜多变。
3 分层切削时刀具的终止位置当某外圆表面的加工余量较多需分层多次走刀切削时,从第二刀开始要注意防止走刀至终点时背吃刀量的突增。
如图2所示,设以90°主偏角的刀具分层车削外圆,合理的安排应是每一刀的切削终点依次提前一小段距离e(e=0.05>。
如果e=0,即每一刀都终止在同一轴向位置上,车刀主切削刃就可能受到瞬时的重负荷冲击。
如分层切削时的终止位作出层层递退的安排,有利于延长粗加工刀具的使用寿命。
4 “让刀”时刀补值的确定对于薄壁工件,尤其是难切削材料的薄壁工件,切削时“让刀”现象严重,导致所车削工件尺寸发生变化,一般是外圆变大,内孔变小。
“让刀”主要是由工件加工时的弹性变形引起,“让刀”程度与切削时的背吃刀量密切相关。
采用“等背吃刀深度法”,用刀补值作小范围调整,以减少“让刀”对加工精度的影响。
如图3所示,设欲加工的外圆尺寸为a,双面余量为2t。
试切削时,取t值的一半作为切削时的背吃刀量,试切削在该表面的全长上进行,试切削后,程序安排停车,测量该外圆尺寸是否等于a+t,按出现的误差大小调整刀具的刀补值,然后继续运行程序,完成精加工走刀。
因为精加工过程与试切削过程采用相同的背吃刀量和同样的切削速度和进给速度,切削抗力相同,工件相应的弹性变形相同,所输入的刀补值刚好能抵消“让刀”所产生的变形,保证车削工件的尺寸精度。
5 车削时的断屑问题数控车削是自动化加工,如果刀具的断屑性能太差,将严重妨碍加工的正常进行。
为解决这一问题,首先应尽量提高刀具本身的断屑性能,其次应合理选择刀具的切削用量,避免产生妨碍加工正常进行的条带形切屑。
数控车削中,最理想的切屑是长度为50~150mm,直径不大的螺卷状切屑,或宝塔形切屑,它们能有规律地沿一定方向排除,便于收集和清除。
如果断屑不理想,必要时可在程序中安排暂停,强迫断屑:还可以使用断屑台来加强断屑效果。
使用上压式的机夹可转位刀片时,可用压板同时将断屑台和刀片一起压紧:车内孔时,则可采用刀具前刀面朝下的切削方式改善排屑。
6 可转位刀具刀片形状的选择与普通机床加工方法相比,数控加工对刀具提出了更高的要求,不仅需要刚性好、精度高,而且要求尺寸稳定,耐用度高,断屑和排屑性能好:同时要求安装调整方便,这样来满足数控机床高效率的要求。
数控机床上所选用的刀具常采用适应高速切削的刀具材料(如高速钢、超细粒度硬质合金>并使用可转位刀片。
数控车削中广泛采用机夹可转位刀具,它是提高数控加工生产率,保证产品质量的重要手段。