高效率生产-工厂七大浪费
工厂中的七大浪费
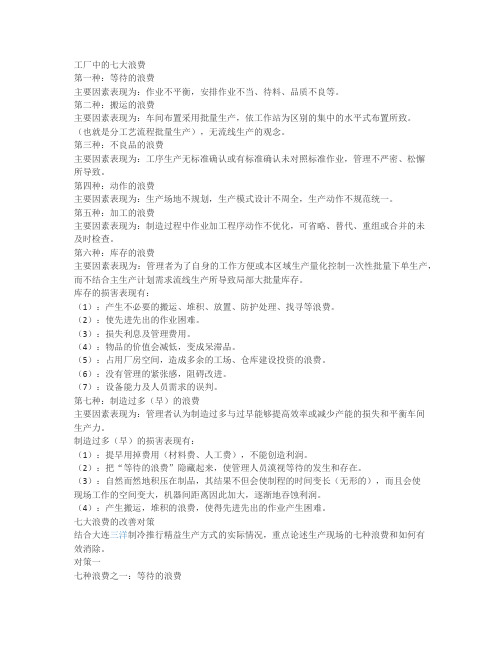
工厂中的七大浪费第一种:等待的浪费主要因素表现为:作业不平衡,安排作业不当、待料、品质不良等。
第二种:搬运的浪费主要因素表现为:车间布置采用批量生产,依工作站为区别的集中的水平式布置所致。
(也就是分工艺流程批量生产),无流线生产的观念。
第三种:不良品的浪费主要因素表现为:工序生产无标准确认或有标准确认未对照标准作业,管理不严密、松懈所导致。
第四种:动作的浪费主要因素表现为:生产场地不规划,生产模式设计不周全,生产动作不规范统一。
第五种:加工的浪费主要因素表现为:制造过程中作业加工程序动作不优化,可省略、替代、重组或合并的未及时检查。
第六种:库存的浪费主要因素表现为:管理者为了自身的工作方便或本区域生产量化控制一次性批量下单生产,而不结合主生产计划需求流线生产所导致局部大批量库存。
库存的损害表现有:(1):产生不必要的搬运、堆积、放置、防护处理、找寻等浪费。
(2):使先进先出的作业困难。
(3):损失利息及管理费用。
(4):物品的价值会减低,变成呆滞品。
(5):占用厂房空间,造成多余的工场、仓库建设投资的浪费。
(6):没有管理的紧张感,阻碍改进。
(7):设备能力及人员需求的误判。
第七种:制造过多(早)的浪费主要因素表现为:管理者认为制造过多与过早能够提高效率或减少产能的损失和平衡车间生产力。
制造过多(早)的损害表现有:(1):提早用掉费用(材料费、人工费),不能创造利润。
(2):把“等待的浪费”隐藏起来,使管理人员漠视等待的发生和存在。
(3):自然而然地积压在制品,其结果不但会使制程的时间变长(无形的),而且会使现场工作的空间变大,机器间距离因此加大,逐渐地吞蚀利润。
(4):产生搬运,堆积的浪费,使得先进先出的作业产生困难。
七大浪费的改善对策结合大连三洋制冷推行精益生产方式的实际情况,重点论述生产现场的七种浪费和如何有效消除。
对策一七种浪费之一:等待的浪费等待就是闲着没事,等着下一个动作的来临,这种浪费是无庸置疑的。
工厂七大浪费

员工行动浪费
降低员工工作效率和士气,增加管理难度和人力成本。
占用企业资金,可能导致库存积压和贬值,增加仓储成本和管理难度。
制造过多浪费
导致生产线拥堵和产品质量下降,同时可能产生过多的库存和增加仓储成本。
工厂七大浪费普遍存在于各类工厂中,无论是大型制造企业还是中小型加工厂,都可能存在这些浪费现象。
案例一
某服装加工企业生产线上的员工缝制衣物时需要频繁地弯腰和起身,导致生产效率低下。经过分析,发现生产线上的工作台高度不合理,员工需要频繁地弯腰和起身才能完成工作任务。通过调整工作台高度,让员工能够更加舒适地完成工作任务,提高了生产效率。
案例二
工厂七大浪费之五:加工浪费
加工浪费的产生原因
03
优化生产计划
该企业在生产过程中,由于生产计划变动频繁,导致物料需要不断调整位置。为了解决这个问题,企业加强了生产计划管理,尽量保持物料的稳定性,减少了物料的搬运次数和距离,从而提高了生产效率。
某电子制造企业
某机械制造企业
工厂七大浪费之三:不良品浪费
生产流程设计不合理
生产流程设计不当,导致不良品率较高。
员工操作失误
合理安排生产计划
通过合理安排生产计划,减少物料的频繁搬运。
合理配置设备
通过合理配置设备,减少物料在不同设备之间的搬运次数。
采用自动化搬运方式
采用自动化搬运方式,如使用机器人、输送带等,可以减少人力搬运的浪费。
该企业在生产过程中,由于生产线之间的距离较远,导致物料需要频繁地搬运。为了解决这个问题,企业重新规划了生产线布局,将距离较近的生产线安排在一起,减少了物料的搬运次数和距离,从而提高了生产效率。
工业工程 七大浪费

1七 大 浪 费1、价值与浪费在实际生产与工作中,精益生产将所有的工作都被定义为增值活动(Value-added)与非增值活动(Non Value-added )价值指的就是增值活动,而增值活动的定义有三条,满足任何一条均认为是有价值的,即增值活动。
1) 顾客愿意为之支付的活动 2) 产品和工作有物理或实质上的改变 3) 工作在第一次就被做对举例:1)因为客户的原因,将产品的设计弄错,而导致工厂整批产品不能按期交货,而且需要延期返工才能交货,而此时客户愿意支付返工费和延长交货期。
则这样的返工则是增值活动,他同样为工厂创造了价值,因为是顾客愿意为之支付。
但如果是工厂方因为疏忽导致产品延期交货的,则客户不但不会支付返工费,还要追究因延期交货而带来的损失。
即使客户愿意返工,也是工厂来承担返工费,所以这样的则被认为是不增值的。
2)将客户提供的需求订单,通过计算机处理转变为各个部门的生产计划; 产品的组装和拆分均被认为是增值活动,因为信息的形式发生了变化,产品也发生了物理的变化,被认为是增值。
3)对产品的检查要在第一次就能发现问题,而不是待到最终组装时才发现问题,则此时的发现则是不增值的,因为在这个时间段内产2精益生生了更多的不良品。
浪费(MUDA )指的就是不增值的活动。
在我们的生产中有很多活动是不增值的活动,这其中包括搬运、检验、储存等。
因为在企业的实际生产中这些浪费有些事必不可少的,同时从某种意义上,他们的存在也是必须的,因为往往被忽视,而把这样的浪费看成一种常态。
只有通过工业工程的专业工具才能分析出这些浪费,从而得到改善。
但精益生产则将这些浪费归纳为7大浪费,从而在现场中更容易识别和发现。
客户将订单发至给工厂端生产,工厂端开始采购原材料,生产车间开始加工,加工后品质部门检验合格后,告知发货单位,将成品发至客户指定的地点。
在这一系列的过程中,真正的价值很少,而绝大部分都是MUDA ,所以为了更好的为客户创造价值,应尽可能减少浪费,从而使整个成本更低,交货时间更短。
工厂管理七大浪费

八大浪费1.不良、修理的浪费所谓不良、修理的浪费,指的是由于工厂内出现不良品,需要进行处置的时间、人力、物力上的浪费,以及由此造成的相关损失。
这类浪费具体包括:材料的损失、不良品变成废品;设备、人员和工时的损失;额外的修复、鉴别、追加检查的损失;有时需要降价处理产品,或者由于耽误出货而导致工厂信誉的下降。
2.加工的浪费加工的浪费也叫过分加工的浪费,主要包含两层含义:第一是多余的加工和过分精确的加工,例如实际加工精度过高造成资源浪费;第二是需要多余的作业时间和辅助设备,还要增加生产用电、气压、油等能源的浪费,另外还增加了管理的工时。
3.动作的浪费动作的浪费现象在很多企业的生产线中都存在,常见的动作浪费主要有以下12种:两手空闲、单手空闲、作业动作突然停止、作业动作过大、左右手交换、步行过多、转身的角度太大,移动中变换“状态”、不明技巧、伸背动作、弯腰动作以及重复动作和不必要的动作等,这些动作的浪费造成了时间和体力上的不必要消耗。
4.搬运的浪费从JIT的角度来看,搬运是一种不产生附加价值的动作,而不产生价值的工作都属于浪费。
搬运的浪费具体表现为放置、堆积、移动、整列等动作浪费,由此而带来物品移动所需空间的浪费、时间的浪费和人力工具的占用等不良后果。
国内目前有不少企业管理者认为搬运是必要的,不是浪费。
因此,很多人对搬运浪费视而不见,更谈不上去消灭它。
也有一些企业利用传送带或机器搬运的方式来减少人工搬运,这种做法是花大钱来减少工人体力的消耗,实际上并没有排除搬运本身的浪费。
5.库存的浪费按照过去的管理理念,人们认为库存虽然是不好的东西,但却是必要的。
JIT的观点认为,库存是没有必要的,甚至认为库存是万恶之源。
如图1-1,由于库存很多,将故障、不良品、缺勤、点点停、计划有误、调整时间过长、品质不一致、能力不平衡等问题全部掩盖住了。
例如,有些企业生产线出现故障,造成停机、停线,但由于有库存而不至于断货,这样就将故障造成停机、停线的问题掩盖住了,耽误了故障的排除。
精益生产七大浪费
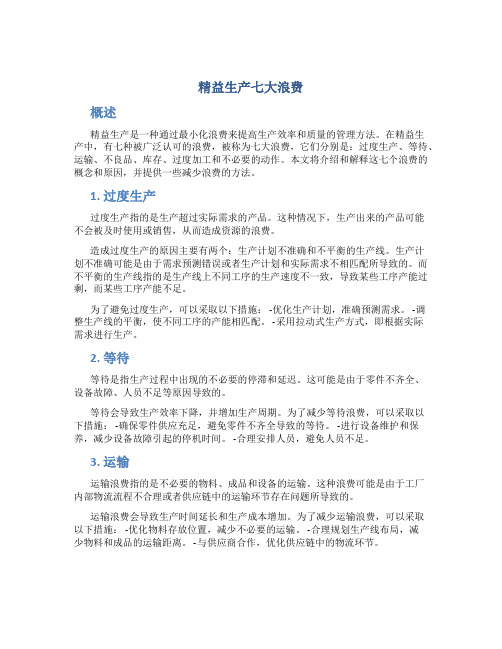
精益生产七大浪费概述精益生产是一种通过最小化浪费来提高生产效率和质量的管理方法。
在精益生产中,有七种被广泛认可的浪费,被称为七大浪费,它们分别是:过度生产、等待、运输、不良品、库存、过度加工和不必要的动作。
本文将介绍和解释这七个浪费的概念和原因,并提供一些减少浪费的方法。
1. 过度生产过度生产指的是生产超过实际需求的产品。
这种情况下,生产出来的产品可能不会被及时使用或销售,从而造成资源的浪费。
造成过度生产的原因主要有两个:生产计划不准确和不平衡的生产线。
生产计划不准确可能是由于需求预测错误或者生产计划和实际需求不相匹配所导致的。
而不平衡的生产线指的是生产线上不同工序的生产速度不一致,导致某些工序产能过剩,而某些工序产能不足。
为了避免过度生产,可以采取以下措施: -优化生产计划,准确预测需求。
-调整生产线的平衡,使不同工序的产能相匹配。
-采用拉动式生产方式,即根据实际需求进行生产。
2. 等待等待是指生产过程中出现的不必要的停滞和延迟。
这可能是由于零件不齐全、设备故障、人员不足等原因导致的。
等待会导致生产效率下降,并增加生产周期。
为了减少等待浪费,可以采取以下措施: -确保零件供应充足,避免零件不齐全导致的等待。
-进行设备维护和保养,减少设备故障引起的停机时间。
-合理安排人员,避免人员不足。
3. 运输运输浪费指的是不必要的物料、成品和设备的运输。
这种浪费可能是由于工厂内部物流流程不合理或者供应链中的运输环节存在问题所导致的。
运输浪费会导致生产时间延长和生产成本增加。
为了减少运输浪费,可以采取以下措施: -优化物料存放位置,减少不必要的运输。
-合理规划生产线布局,减少物料和成品的运输距离。
-与供应商合作,优化供应链中的物流环节。
4. 不良品不良品是指在生产过程中产生的不合格产品。
不良品可能是由于工艺问题、材料质量不合格、操作失误等原因导致的。
不良品会增加返工和废品处理的成本,并降低生产效率。
生产制造七大浪费
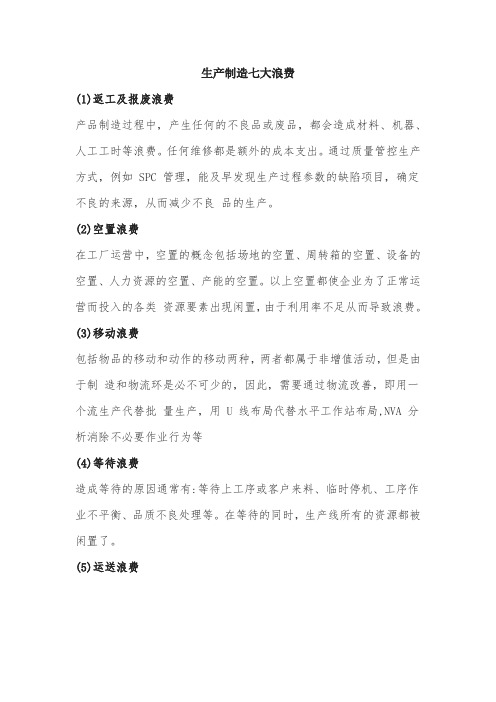
生产制造七大浪费(1)返工及报废浪费产品制造过程中,产生任何的不良品或废品,都会造成材料、机器、人工工时等浪费。
任何维修都是额外的成本支出。
通过质量管控生产方式,例如 SPC 管理,能及早发现生产过程参数的缺陷项目,确定不良的来源,从而减少不良品的生产。
(2)空置浪费在工厂运营中,空置的概念包括场地的空置、周转箱的空置、设备的空置、人力资源的空置、产能的空置。
以上空置都使企业为了正常运营而投入的各类资源要素出现闲置,由于利用率不足从而导致浪费。
(3)移动浪费包括物品的移动和动作的移动两种,两者都属于非增值活动,但是由于制造和物流环是必不可少的,因此,需要通过物流改善,即用一个流生产代替批量生产,用 U 线布局代替水平工作站布局,NVA 分析消除不必要作业行为等(4)等待浪费造成等待的原因通常有:等待上工序或客户来料、临时停机、工序作业不平衡、品质不良处理等。
在等待的同时,生产线所有的资源都被闲置了。
(5)运送浪费运送是非增值活动,通过外部整合供应商和客户送货流程优化方案,内部厂从设计、生产线布局,尽量把运输过程优化,减少不必要的运输浪费。
(6)库存浪费库存会进一步造成下列的浪费;A.产生不必要的搬运、堆积、放置、防护处理、找寻等浪费;B.使先进先出的作业困难;C.损失利息及管理费用;D.物品的价值随着时间的推移会减低,变成呆滞品;E.占用厂区、造成工场、仓库建设投资的浪费。
(7)过量生产浪费过量生产是工厂营运中最不必要的流程,它一方面造成了企业资源的大量浪费,另一方面又产生了其他不必要的流程和投入,包括:A.过剩的库存损失和再加工风险;B.虚假生产负荷,造成增加设备投资的假象;C.占用周转和库存场地;D.导致不必要的搬运,以及增加在搬运中的损坏风险。
七大浪费

五、库存浪费
库存量越大资金积压越大,利息负担越重,仓 库管理需求增加,产品变质、失效等……浪费.
当库存的水位高涨时,管理者就感受不到 问题的严重性,像质量的问题、机器故障、 及员工缺勤,也因此而失去了改善的机会.
六、等待浪费
由于生产原料供应中断、作业不平衡和生产计 划安排不当等原因造成的无事可做的等待.
消除等待浪费
1.CELL生产方式;
3.人机工作分离; 5.切换的改善;
2.生产线平衡法;
4.全员生产性维护;
七、动作浪费
生产操作动作上的不合理导致的时间浪费,如: 生产作业时调整位置﹑翻转产品﹑取放工具物 料等不必要的动作浪费
动作经济原则的四条基本原则: 减少动作的数量 双手同时进行动作 缩短动作的距离 轻松动作
7
大浪费Байду номын сангаас
一、不良浪费
由于工厂内出现不良品,需进行处置的时间、 人力和物力的浪费,以及由此造成的相关损失。 对待不良三不政策:
Don’t accept 不接受 Don’t make 不制造 Don’t deliver 不传递
二、过量生产浪费
是由突发事件预防﹑自动化应用不当﹑制程设 定过长﹑生产计划未平准化﹑工作负荷不平 衡﹑多余检验等造成的制造过多于下一制程需 求的浪费.
劳模
三、加工浪费
也叫过分加工的浪费, 多余的加工和过分精确的 加工,造成资源的浪费. 四大类型:
品质过剩 检查过剩 加工过剩 设计过剩
四、搬运浪费
是一项无生产附加价值的工作,包含移动、堆 积、整列、放置等……浪费. 改善方法:
合理化布局 合理化搬运工具 合理化搬运方法
精益生产的效率与七大浪费

精益生产的效率与七大浪费精益生产是一种以提高效率和消除浪费为目标的管理方式。
在精益生产中,有七大浪费被视为效率的根本敌人,它们分别是:过产出、等待、不必要的运输、过度加工、库存、不必要的动作和不必要的缺陷。
下面将逐一介绍这七大浪费及其对效率的影响,以及消除这些浪费的方法。
第一个浪费是过产出。
过产出指的是生产超过实际需求的产品或服务。
这会导致库存过剩,并增加了不必要的成本和风险。
解决这个问题的方法是通过精准预测,避免生产过多的产品。
同时,采用柔性生产方式和及时调整产能,以适应市场的实际需求。
第二个浪费是等待。
等待指的是等待时间过长,例如等待原材料、机器设备等。
这会导致生产过程中的停滞和延迟,并降低了效率。
减少等待时间的方法包括优化供应链,确保原材料的及时到达;同时,合理安排生产计划和生产线布局,避免机器设备的瓶颈和拥堵。
第三个浪费是不必要的运输。
不必要的运输指的是在生产过程中,产品或材料的运输距离过长或频繁。
这会增加运输成本和交付时间,降低效率。
减少不必要运输的方法包括优化物料搬运路径和方式,合理布局生产线,减少运输距离和次数。
第四个浪费是过度加工。
过度加工指的是对产品进行不必要的加工或处理。
这样做既增加了生产时间和成本,也增加了不必要的风险。
减少过度加工的方法包括优化工艺流程,消除不必要的工序和处理环节,确保产品的加工与客户需求一致。
第五个浪费是库存。
库存指的是多余的产品或材料存放在仓库中,这会增加仓储成本和风险。
减少库存的方法包括精确的需求预测,及时的生产计划和物料供应,以及有效的库存管理和控制。
第六个浪费是不必要的动作。
不必要的动作指的是工人在生产过程中进行的不必要的移动或动作,这会浪费时间和能量。
减少不必要动作的方法包括优化工作流程和工位布局,减少工人的不必要移动和转移。
第七个浪费是不必要的缺陷。
不必要的缺陷指的是在生产过程中出现的不符合质量要求的产品或材料。
这不仅会增加成本和风险,还会影响生产效率和客户满意度。
生产现场常见浪费及识别方法(浪费的概念,生产现场七大浪费,相关术语,识别浪费)

✓ 产品停滞在仓库的情况也是等待浪费
• 生产线的品种切换。 • 时常因缺料而使机器闲置。 • 机器设备时常发生故障。 • 生产线未能取得平衡。 • 有劳逸不均的现象。
二、生产现场的七大浪费
2、加工本身的浪费
加工本身的浪费
现在正做的作业是否真的 必要?为什么要这么做?
摈弃现有的想法、方式、基准。
到现场,看现物,掌握现象。
[三现原则] 到
现 场
看 现 物
掌握 现象
三、相关术语
要认识潜在浪费要素在哪里发生?发生多少? 怎么发生?是否一定要发生?
不可信, 再检查!
工具在哪?
还是不良!
又没电了!
累死了
XX毛坯 在哪?
什么、在哪里、有多少、 怎么、为什么发生?
三、相关术语
二、生产现场的七大浪费
虽然制造的产品不同,但在工厂发现的典型的浪费类型是类似的
1 等待浪费 2 加工本身的浪费 3 动作浪费 4 库存浪费
5 制造不良的浪费 6 生产过剩浪费 7 搬运浪费
二、生产现场的七大浪费
1、等待浪费
对不起, 请少等 会儿...
还没 好 吗?.
人
等
设备
待
物
作业
✓ 只把人或设备的等待,看做等待浪费 的情况较多
库存的浪费
利用库存回避工厂 的许多问题。
在这种意识下发生的。
• 产生不必要的搬运、堆积、放置、防护、 寻找等浪费的时间、空间和动作。
• 资金占用(损失利息)及额外的管理费用。 • 物品的价值衰减,变成呆料、废料。 • 占用空间和通道,造成多余的仓库建设投
资或租金投入。
精益生产之七大浪费

七大浪费目录1.精益生产的效率2.浪费的定义3.七大浪费4.动作研究精益生产的效率传统的效率v简单化v高速大量生产精益生产的效率:v消除浪费-- 库存/等待-- 搬运--摆放生产过剩是最大的浪费浪费v浪费是指那些导致成本增加的因素v虽然增加价值,但耗用资源过高• 一种浪费通常能够导致另外一种浪费发现浪费和认识浪费的能力很重要隐性浪费/显性浪费v显性浪费定义为可见的浪费这些浪费很容易签别如:在流程中引起不良品的错误等待时间浪費v隐性浪费定义为看不见的浪費这些浪費不易被签别这些工作看起来非常有价值直到使用新的策略发现其中很大的浪费.如:工作分配不充分高耗性增值工作七种浪费1. 不良品浪费4. 搬运浪费6. 动作浪费2. 过量生产浪费3. 过分加工浪费5. 库存浪费7. 不平衡浪费1. 不良品浪费1.人为操作失误2.设备/工具不稳定3.不按照标准作业4.来料不稳定5.设计没考虑装配需求6.环境温度/湿度/静电7.存放周期长2. 过量生产浪费1.超出下一操作的需求量2.提前生产下一操作的需求3.设备速度过快3. 过分加工浪费1.超出/低于产品特定需求的精度2.多余的作业项目质量成本概念4. 搬运浪费v也就是说“每个工位都从手工操作开始”. -- 找到、拿起、移动,用手放,然后 -- 从手推车移到货板 -- 从货仓到工厂-- 从工厂到生产线-- 从生产线到机械化车间 --从机械化车间到操作工位讨论:自动化搬运的误区5. 库存浪費v存货过多-- 过多的原材料• 交货周期过长?• 错误的订货量?-- 过多的成品• 是因为生产过剩?• 是因为生产排期错误?6. 移動浪費1.动作太大2.单手空闲3.转身动作过大4.操作动作不流畅5.重复/不必要的动作6.不必要的弯腰动作动作经济原则7. 不平衡浪费1.人员工作分配不合理2.计划对人员需求不均匀3.设备产能搭配不合理4.设备故障5.物料短缺6.信息流与物流不同步动作经济原则共二十二项并归纳为下列三大类1.关于人体之运用:(1)双手应同时开始并同时完成其动作。
工厂中的七大浪费

工厂中的七大浪费工厂中的七大浪费指的是生产过程中存在的七个浪费问题,即:超生产、库存积压、等待、运输、过度加工、不良品、不合理的动作。
这些浪费不仅会浪费宝贵的资源,还会导致时间和成本的浪费,对工厂的高效运作造成不利影响。
本文将详细介绍这七大浪费及其解决方案。
首先,超生产是指不合理地高于市场需求的生产,这将导致产品的积压,徒增成本和浪费资源。
解决这个问题的方法是进行精确的市场需求预测,并根据预测结果合理安排生产计划。
库存积压是指生产过程中过多地储存产品,这既会增加存储成本,也会增加不良品的可能性。
解决这个问题的方法是实施及时生产,按需制造,并与供应链进行紧密协调,避免过度储存。
等待是指生产过程中人员或设备的空闲等待时间。
这将导致生产的延误和资源的浪费。
解决这个问题的方法是合理调度生产线和工作流程,避免瓶颈和能力不足的情况,提高生产效率和资源利用率。
运输是指产品从一个地方到另一个地方的物流环节中的浪费。
这将增加运输成本和交付时间,降低生产效率。
解决这个问题的方法是优化物流路径,减少运输距离和时间,使用先进的物流技术和设备。
过度加工是指对产品进行不必要的加工,徒增成本和时间的浪费。
解决这个问题的方法是进行价值流分析,剔除不必要的工序和环节,优化生产工艺和流程。
不良品是指产品在生产过程中存在质量问题或缺陷。
这将导致资源和时间的浪费,降低产品的价值和质量。
解决这个问题的方法是引入精益生产和质量管理技术,强调预防控制和持续改进,提高产品质量和生产效率。
不合理的动作是指生产过程中存在的无意义或多余的动作,这将增加工人的劳动强度和生产时间,影响工作效率。
解决这个问题的方法是进行工作站布局优化,改善工作环境,减少不必要的动作和体力劳动,提高工人的工作效率和满意度。
综上所述,工厂中的七大浪费是产生在生产过程中的一系列问题,对工厂的高效运作造成不利影响。
通过精确的市场需求预测、及时生产、合理调度、优化物流路径、价值流分析、质量管理和工作环境优化等解决方案,可以有效减少这些浪费问题,提高生产效率,降低成本,提升工厂的竞争力。
生产过程中的七大浪费
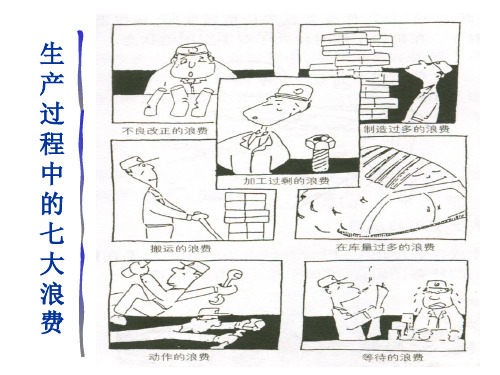
最迟精选的课浪件 费
5
五、不良改正的浪费
是指在工厂内发生不良品,需要进行处置的时间、人力 和物力上的浪费。
最差精的选课浪件费
6
六、加工的浪费
是指加工过程中存在的一些多余的加工,如机械行程过长 、检查标准不明确或过高等
最深的精选浪课件费
7
七、十二种动作的浪费
步行的浪费
精选课件
10
动作的浪费
转身角度太大的浪费
作业动作太大的浪费
精选课件
11
动作的浪费
伸臂动作的浪费
弯腰动作的浪费
精选课件
12
对工作的安排,应该精益求精,寻求最佳的配合方法
精选课件
13
精选课件
14
发现、解决浪费的方法
用5W2H提问方式找出问题点
项目 疑问 1. Why 2. Where 3. When 4. Who 5. What 6. How 7.How much
生 产 过 程 中 的 七 大 浪 费
精选课件
1
一、制造过多(早)的浪费
必要的东西在必要的时候做出必要的数量,此外都是浪费。
最坏的浪费
精选课件
2
二、库存的浪费
库存是万恶之源,库存量越大,资金 积压就越厉害。
最大的浪费
精选课件
3
三、搬运的浪费
取、放、运、还有点数后重新装货
最长精的选课浪件 费
4
四、等待的浪费
两手空闲的浪费 单手作业的浪费 作业动作停止的浪费
作业动作太大的浪费 拿的动作交替的浪费 步行的浪费
转身角度太大的浪费 动作之间没有配合好的浪费 不了解作业技巧的浪费
工厂中的七大浪费.

工厂中的七大浪费
七、动作的浪费
是指不必要的动作,不能产出盈利的动作,动作慢. 它导致人员·
工数的增加和工作的不稳定,机能的隐蔽要素,例如装模时错装
不合格模具、安装倒角不良的刀片等平时看不到感受不到的动 作浪费,还包括生产过程中的动作浪费,如提重物、玩手机、 重复搬运物料、生产明天的工作量、等待(在机台旁边无所事 事)、找寻工具或物料等。
工厂中的七大浪费
镍锌制造部制品工序 邓志强
提
1、什么是浪费
纲
2、工厂中的七大浪费
3、发现、解决浪费的方法
何为浪费
什么是浪费:
不增加附加价值的活动,是浪费 ◆ 尽管是增加附加价值的活动,所用的资源超过了 “绝对最少”的界限,也是浪费 例如用低合格率压制出来的产品(需要过规的) 在生产过程中,只有实体上改变了物料的活动 才能在生产过程中增加价值,如:制粉、压制、烧 结、分拣包装、套管加胶壳等。不过,工厂中很多 常见的活动并不增加价值,如:盘点、产品库存、 产品检验、搬运等。
工厂中的七大浪费
十二种典型动作的浪费
1、两手空闲的浪费:指从作业开始到结束,作业 者两手都处于等待的状态。如:压机旁边等待产 品出来检验的压制工、进炉工、出炉工在烧结炉 前后等待产品、倒角工在等待称量产品。
工厂中的七大浪费
七、十二种动作的浪费
2、单手空闲的浪费,指在工作或作业过程中, 作业人员是否只有一只手在操作,另外一只手 是空闲状态,如压坯倒角时一只手倒角,另外 一只手在拿产品,就属于单手空闲
本公司发生的浪费调查
号码 19 20 21 妨碍成本降低的事项 工艺、标准出错较多 不进行粉料的检验就开始使用 工作方法不好 我或者是他人的问题 是否能看到 是人还是物
详解精益生产的七大浪费

详解精益生产的七大浪费①物料供应不及或前一道工序的能力不足,导致停工待料;②检验作业的过程中,虽然能够管控产品的品质,但是检验时,造成后道工序作业停顿;③因设备故障造成生产停顿、因发现品质问题造成停工待料;④生产型号切换造成生产停顿。
比如一个生产鞋子的工厂,在生产线的传送带上画一个网格。
正常生产时,每格要放一双鞋。
假设生产时中间有很多网格,说明之前的生产过程肯定有问题。
这时候生产线的主管要尽早处理,减少等待浪费。
2.搬运浪费在搬运过程中产生过多的放置、堆积、移动、整理,不仅费时费力,同时会造成搬运上的浪费。
例如:一间公司生产线的布置.从铸造到磨床,磨床之后到铣床,铣床之后到钻床,接着到焊接,最后到涂装部,完成之后进行检验,检验合格之后才送到包装部进行包装,最后入库。
在这些过程中,移动的次数高达八次之多,所以,在整个流程中,我们应该思考如何减少搬运次数,如何缩短搬运距离,其中,工厂的布置就显得尤为重要。
3.不良浪费在生产过程中,不可避免地会出现产品质量差的情况,而这些差的情况又会造成额外的成本,比如材料的损耗、设备的折旧、劳动力的损耗等。
这时候产品的价格也会受到影响,也许订单会流失,甚至公司的声誉也会受损。
这时候就要利用一系列的检验,比如进货检验、过程检验、产品检验(出货检验),把不良品降到最低,减少不良浪费。
4.动作浪费多余的动作会增加我们的工作强度,降低生产效率。
常见的12个浪费动作是:两只手闲着,一只手闲着,作业停止,动作幅度过大,左右手互换,走路过多,转弯角度过大,边走边换动作,作业技巧没有掌握,背伸动作,弯腰动作,重复或不必要的动作。
有些公司在生产线组装的时候,每道工序的移转都必须要借助一个用手按按键的动作,让每道工序的完成品得以转移到下一个工序,所以,“用手按按键”这个动作就是浪费。
假如今天不用手,改用脚来按按键,就能够移转到下一道工序,这时双手还能持续进行组装的动作,这样就不会造成动作的浪费。
(2)精益生产之解读七大浪费

空白页,请跳过阅读
汉语类:《烛光里的妈妈》、《征服》、《小 野曲》、《摇篮曲》、《壮志在我胸》、 《从头再来》、《被遗忘的时光》、《不见 不散》、《真心英雄》、《众人划浆开大 船》、《感恩的心》、《父亲和我》、《在 你面前我好想流泪》、《有多少爱可以重 来》、《忙与盲》、《感谢你》、《有你有 我》、《明天更美好》、《同一首歌》、 《斗牛士之歌》、《思念谁》、《我这个你 不爱的人》、《朋友别哭》、
① 只是提早用掉了费用(材料费、 人工费)而已,并不能得到什么好 处。 ② 也会把“等待的浪费”隐藏起来, 使管理人员漠视等待的发生和存在。 ③ 会自然而然地积压在制品,其结 果不但会使生产周期变长(无形 的),而且会使现场工作的空间变 大,机器间的距离因此加大,要求 增加厂房和硬件投入,这样在不知 不觉中将逐渐地吞蚀我们的利润。 ④ 也会产生搬运、堆积的浪费,并 使得物料先进先出的作业产生困难。
精益生产之解读七大浪费
浪费之三:不合理运输的浪费
不合理运输的浪费定义:
任何不为生产过程所必需的物料搬 动或信息的流转。
不合理运输的浪费若分解开来,又 包含放置、堆积、移动、整理等浪费。
明显的现象,比如:
过多的搬运活动、过度的搬运设
备、大面积储存区、过量配送人员、
仓储质量降低、过度能源消耗、损坏
—某企业老总对不合理运输的改善提出了 一个非常精辟的要求。
库存掩盖所有问题 通过降库存暴露问题
精益生产之解读七大浪费
浪费之二:制造过多(早)的浪费
制造过多(早)的浪费定义:
生产了过多或过早的超出客户或下游工序所需要的量。
制造过多或提早完成在精益化的制造企业内部则被视为最大的浪费。精益生
浅谈工厂的七大浪费

车间的七大浪费一、等待的浪费:等待就是闲着没事,等着下一个动作的来临,这种浪费在生产过程中是存在的。
造成等待的原因通常有:作业不平衡、安排作业不当、停工待料、品质不良等。
除了在直接生产过程中的等待外,在管理工作中也有等待这种浪费发生,例如在新产品试制过程中,由于技术问题不能及时解决造成的等待的浪费。
二、搬运的浪费:大部分人都知道搬运是一种无效的动作,但搬运又是必须的动作,因为没有搬运,如何做下一个动作?关键是我们如何去减少生产中不必要的搬运,例如可以利用容器将小件一次搬运到指定位置,将车间按工艺过程布局等减少重复搬运。
三、不良品的浪费:产品制造过程中,任何的不良品产生,都造成材料、机器、人工等的浪费。
任何返修都是额外的成本支出。
因此在生产过程中,要尽早发现不良品,确定不良的来源,从而减少不良品的产生。
四、动作的浪费:要达到同样操作的目的,会有不同的动作,哪些动作是不必要的呢?是不是要拿上、拿下如此频繁?有没有必要有转身的动作、步行的动作、弯腰的动作等?因此我们应该反思一下日常工作中有哪些动作不合理?如何改进?能动手指完成的不用手腕,能用手腕的不用手臂,尽量减少动作的幅度,减轻操作强度,提高工作效率。
五、加工的浪费:在制造过程中,为了达到作业的目的,有一些加工程序是可以省略、替代、重组或合并的,若是仔细地加以检查,就可发现有不少的浪费等着你去改善。
六、库存的浪费:精益生产方式认为:“库存是万恶之源”,因为库存会产生不必要的搬运、堆积、放置、防护处理、找寻等浪费;先进先出的作业困难;损失利息及管理费用;物品的价值会减低,变成呆滞品;占用厂房空间,造成多余的工场、仓库建设投资的浪费;设备能力及人员需求的误判。
七、制造过多(早)的浪费:也许有人不理解,制造过多(早)也是浪费,普遍认为制造过多(早)可以满足销售的需求,但不知道它提早用掉了材料费、人工费,并不能得到什么好处。
它也会把“等待的浪费”隐藏起来,漠视等待的发生和存在。
生产过程中的七大浪费

生产过程中的七大浪费一、七种浪费之一:等候的浪费等候就是闲着没事,等着下一个动作的到临,这类浪费是无庸置疑的。
造成等候的原由往常有:作业不均衡、安排作业不妥、歇工待料、质量不良等。
以制造部性能试验课等候电控盘为例,因为电控盘不可以按要求实时入厂,有可能没法如期交货,而当电控盘入厂后,又需要抢进度,可能会出现加班、质量问题等。
还有一种就是“监督机器”的浪费,有些工厂买了一些速度快、价钱高的自动化机器,为了使其能正常运行或其余原由,比如:清除小故障、增补资料等等,往常还会此外安排人员站在旁边监督。
所以,固然是自动设施,但仍需人员在旁照料,特称之为“闲视”的浪费。
比如在产品检测过程中,调试人员和氦检人员站在产品旁边等候,这类状况能否还有?除了在直接生产过程中有等候外,其余管理工作中就没有等候这类浪费发生吗?当制造部在生产新产品发生一些问题时,技术部和质量保证部能否能立刻解决而不需要现场人员长时间等候?如何减少这类等候?二、七种浪费之二:搬运的浪费大多半人皆会认可搬运是一种无效的动作,也有人会认为搬运是一定的动作,因为没有搬运,如何做下一个动作?好多人都有这类想法。
正因为这样,大多半人默认它的存在,而不想法除去它。
有些人想到用输送带的方式来战胜,这类方式仅能称之为花大钱减少体力的耗费,但搬运自己的浪费并无除去,反而被隐蔽了起来。
搬运的浪费若分解开来,又包括搁置、聚积、挪动、整理等动作的浪费。
今年以来,生产管理部和制造部每个月均对总生产工时进行汇总剖析,发此刻实质作业时间减少的同时,总工时却在增加,经认真剖析后发现,是两个工厂间的运输工时居高不下,特别是由二工厂向一工厂搬运原资料的工时占大多半。
怎么样战胜?日本三洋大型课为减少搬运,把四个车间归并成两个,一些零零件的加工由本来在别处加工变为在生产线旁进行加工,从而减少搬运。
在不行能完整除去搬运的状况下,应从头调整生产布局,尽量减少搬运的距离。
大家能够考虑一下本公司的生产布局应当如何更改?如何最大限度地减少搬运?三、七种浪费之三:不良品的浪费产品制造过程中,任何的不良品产生,皆造成资料、机器、人工等的浪费。
- 1、下载文档前请自行甄别文档内容的完整性,平台不提供额外的编辑、内容补充、找答案等附加服务。
- 2、"仅部分预览"的文档,不可在线预览部分如存在完整性等问题,可反馈申请退款(可完整预览的文档不适用该条件!)。
- 3、如文档侵犯您的权益,请联系客服反馈,我们会尽快为您处理(人工客服工作时间:9:00-18:30)。
場 形
• D﹒搬運的浪費
形 • E﹒在庫量過多的浪費
色 色
• F﹒等待的浪費
的 浪
• G﹒動作的浪費
費
12種動作上的浪費
• A﹒兩手空閒的浪費
生 產
• B﹒單手空閑的浪費
現 • C﹒作業動作停止的浪費
場 形
• D﹒作業動作太大的浪費
形 • E﹒拿的動作交替的浪費
色 色
• F﹒步行的浪費
的 浪
• G﹒轉身角度太大的浪費
生 • E﹒管理﹐監控過剩﹒
產
生產布局
生
(消除搬運的浪費)
產
布
局
合理化布局的重要性
• 合理的生產布局能夠保証物流的順
暢﹐減少無价值的搬運動作﹐提高現場
生
的管理透明度和生產效率﹒
產•
布
局•
搬運是所有作業中附加的動作﹐其
本身并不產生附加价值﹒
合理化布局的重要性
• 無任何附加价值的搬運動作包括﹕
生 • A﹒搬運
產•
•
•
•
•
•
一般加工過剩會造成以下几點危害﹕ 1﹒人員﹐工時浪費 2﹒設備﹐机械浪費 3﹒零部件﹐材料浪費 4﹒修理浪費 5﹒修理﹐滯留空間的浪費 6﹒修理造成新問題的發生 7﹒不能按時完成造成生產力低下 8﹒造成交貨延誤 9﹒無法批量生產影響市場占有率
合 理 化 生 產-過剩的种類和原因
• 過剩按區域來分﹐可分為以下几种﹕
場
產進程或指導生產
形
形 • D﹒生產現場明确標示作業區域﹐規范
色
作業
色 的
• E﹒推行“一目了然的管理“等視覺管
浪
理手法
費
零缺陷生產
零 缺
(消除不良的浪費)
陷 生
零庫存管理
產
(消除在庫的浪費)
与
零
庫
存
管
理
零缺陷生產-不良產生的原因
• 制造不良的浪費是指﹕有不良發生或
零 持續的制造不良的浪費﹒一般來源以下几
零 庫
•
C﹒認為有大量庫存才保險
存
管
理
零庫存管理-庫存產生的根源
• “在庫“作為資產本來是有价值的﹐
零 但過多的話會面臨以下風險﹒
缺
陷•
A﹒降低資金的周轉速度
生 產
•
B﹒占用大量流動資金
与•
C﹒增加保管費用
零
庫•
D﹒利息損失
存•
管
理•
E﹒面臨過時的市場風險 F﹒容易變質劣化等
零庫存管理-零部件庫存改善方法
管
5.直方圖(Histogram)
理
6.管制圖(Control chart)
7.層別法(Stratification)
零庫存管理-庫存產生的根源
• 制造業的工厂﹐存在原材料﹐零部
零 件﹐半成品﹐成品等在庫﹒在庫發生的原
缺 陷
因一般有﹕
生•
產
与•
A﹒空閒時多制造的部分 B﹒認為提前生產是高效率的表現
• A﹒根据生產計划及交貨期分批購入原
零
材料
缺
陷 • B﹒對市場上通用的生產物料可考慮即
生
時生產即時送貨方式﹐降低庫存
產 与
• C﹒做好在庫管理﹐控制在庫金額
零 庫
• D﹒定期盤點
存
• E﹒庫存警示方法
管
理
合理化生產
合
(消除加工過剩的浪費)
理
化
生
產
合 理 化 生 產-過剩的危害
•
•
合 理
•
化•
生
兩种生產方式比較表
項目
工程順配置
机器別配置
生產的連續性 以物流為中心的連續生產 以設備為中心的斷續
生
產
使用
多品种大批量生產
多品种少量生產
布
生產類型 以預測性生產為主 預測性生產和臨時性生產
局
產品庫存
大
中
半成品
少
多
பைடு நூலகம்
生產周期
短
長
標准化程度
高
低
設備運轉率
中
高
人員運轉率
高
中
切還時間
少
多
布局設計的要點
• 1﹒輔助生產線的終點﹐應盡量接近供 給對象的主線工序﹒
缺 陷
個方面﹐
生•
產
与•
A﹒設計不良而導致品質不良 B﹒工藝設計不合理而導致品質不良
零•
C﹒制造階段的管理而影響產品品質
庫 存
•
管•
D﹒使用不合格的零部件而產生品質不良 E﹒對已發生的不良處理不當
理
零缺陷生產-不良之浪費
• 不良的改正導致時間﹐人力和物力浪
零
費﹕
缺
陷•
A﹒產品報廢
生 產
•
B﹒降价處理
生
生產現場形形色色的浪費
產
現
場
形
形
色
色
的
浪
費
浪費的三種形態
• 1﹒勉強﹕超過能力界限的超負荷狀
生
態
產
現
場 形
•
2﹒浪費﹕有能力﹐但未給予足夠的
形
工作量的未飽和狀態
色
色
的 • 3﹒不均衡﹕有時超負荷有時又不飽
浪
和的狀態
費
工厂內的七大浪費
• A﹒不良改正的浪費
生 產
• B﹒制造過剩的浪費
現 • C﹒加工過剩的浪費
費 • H﹒動作之間沒有配合好的浪費
• I﹒不了解作業技巧的浪費
12種動作上的浪費
• J﹒伸背動作的浪費
生 產
• K﹒彎腰動作的浪費
現 • L﹒重复動作的浪費
場
形
形
色
色
的
浪
費
避免七大浪費的基本對策
• A﹒創造看得見浪費的現場(徹底的7S)
生 產
• B﹒制定作業標准﹐嚴守標准化作業
現 • C﹒以看板管理的生產方式﹐來規定生
合 理 化
• A﹒品質過剩﹐指品質要求太高﹐超 過了顧客的預期使用目標﹒
生 產
• B﹒檢查過剩﹐沒有系統設置合理的 檢查點﹐往往同一個項目多道工序檢
查﹔或是對保証程度不高的項目也進行
重點檢查﹒
合 理 化 生 產-過剩的种類和原因
• C﹒加工過剩﹐產品本身沒有要求或
要求不高時﹐采用了高于標准的 加工要
与•
C﹒材料損耗
零
庫•
D﹒人工設備資源損失
存•
管
理•
E﹒出貨延誤取消訂單 F﹒信譽下降
零缺陷生產-品質管理
QC七大手法
零
缺
1.查檢表(Check list)
陷
生
2.柏拉圖(Pareto chart)
產 与
3.特性要因圖(Cause and effect
零
diagram)
庫 存
4.散佈圖(Scatter diagram)
合
求﹒其主要原因有﹕
理 化
•
1>保險思想
生•
產
•
2>精益求精的思想 3>迷信精密机械
• 4>工時利用率不高﹐反正不是很 忙﹐就慢工出細活
• 5>期望太高﹐要求過嚴
合 理 化 生 產-過剩的种類和原因
• D﹒設計過剩﹐指設計方案超出了預 期使用效果﹒
合 • 比如﹐使用壽命5年的机械采用了10
理 化
年壽命的發動机﹒
生 • 2﹒充分探討供應各工序零件的方法﹒
產 布 局
• 3﹒研究空卡板﹐包裝箱﹐夾具等發回 的方法﹒
• 4﹒沿生產線設置大小适當的零件暫放
區﹒
• 5﹒不要忘記在生產線中設置檢查工 序和修理工序﹒
布局設計的要點
• 6﹒确保設備的保養和修理的所需空 間﹒
生 • 7﹒考慮生產線的形狀受到產品和場
產 布
• B﹒倒路讓路
局 • C﹒排除障礙
• D﹒堆碼﹐清點﹐整列和尋找
• E﹒停下與返回
決定生產布局的因素
• 1﹒生產方式決定布局
•
生 • 加工﹐組裝生產線的机器配置一般可
產
分為兩种﹕
布
局•
A﹒將相同的机器聚集在一起的“机
器別配置“
• B﹒按工程順序﹐將不同的机器排列 起來的“工程順配置“
決定生產布局的因素