抽样检验培训教材精选幻灯片
合集下载
抽样方案培训教材PPT(共 37张)
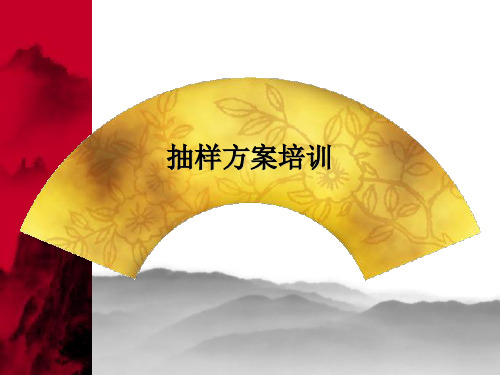
GB/T 2828.1的表1给出了三个
一般检验水平,Ⅰ、Ⅱ、Ⅲ,
检
四个特殊检验水平S-1、S-2、
验
S-3、S-4。水平Ⅱ是最常用的。
过程平均:一定时间或一定量
产品范围内的过程水平平均值 称为过程平均。
过
Pbar =(D1+D2+…+Dk) / (N1+N2+…+Nk) * 100%
程
注: 在实践中,P值是不易得到的,一般可以利用抽样检
平
验的结果来估计; P值可用来预测最近将要交检的产品不合格率;
均
经过返修或挑选后,再次交检的批产品的检验数据以 及截尾检验结果都不能用来估计P值;
抽样方案培训
抽样检验的基本概念
计数标准型抽样方案
计数调整型抽样方案
孤立批抽样检验以及
目
GB/T2828.1的使用
录
其他抽样检验
讨论:抽样检验与供应商管理
抽
样
检
抽样检验定义
验
抽样检验用途
的
计数抽样检验与计量抽样检验 定义
基
本
概
念
破坏性检验
何
流程性材料或散装物料
量小的批的检验
批的包装应便于运输与摆放, 便于抽样。
单 位 产 品
item 批 量
可用来单独考量或观察的事务 批量:N表示
不合格:单位产品的特性不符合规定;
不合格分类:
A类不合格:单位产品的关键质量特性
(critical
不
)不符合规定,或单位产品的质量特
合
性极严重不符合规定; B类不合格:单位产品的重要质量特性
抽样检验ppt课件

筛选批
对方案的履行不起作用
由于误差则被拒收
第一部分 抽样检验的基本概念
5. 抽样检验的分类定义: 5.1 、计件抽样检验是根据被检验样本中的不合格产品数,推 断整批产品的接收与否;而计点抽样检验是根据被检验样本 中的产品包含的不合格数,推断整批产品的接收与否;计量 抽样检验是通过测量被检验样本中的产品质量特性的具体数 值并与标准进行比较,进而推断整批产品的接收与否; 5.2、一次抽样检验就是从检验批中只抽取一个样本就对该批 产品做出是否接收的判断;二次抽样检验是一次抽样检验的 延伸,它要求对一批产品抽取至多两个样本即做出批接收与 否的结论,当从一个样本不能判定批接收与否时,再抽第二 个样本,然后由两个样本的结果来确定批是否被接收。多次 抽样就是二次抽样的进一步推广,例如五次抽样,则允许最 多抽取5个样本才最终确定批是否接收。序贯抽样检验不限次 数,每次抽取一个单位产品,直到按规则做出是否接收批的 判断为止。
为什么要抽样检验而不做全检
一、抽样检验 1、产品检验就是对产品一个或多个质量特性进行的诸
如观察,适当时进行测定、试验或度量并将结果同 规定要求进行比较以确定合格与否所进行的活动。 2、在产品制造过程中,为了保证产品符合标准,防止 不合格品流入下道工序或出厂,最好对产品进行全 数检验即100%检验。但是,在许多情况下全数检验 是不现实的也是没有必要的,例如破坏性检验、批 量大、检验时间长或检验费用高的产品,就不能或 不宜采用全数检验. 此时抽样检验是一种有效且可 行的方法。抽检检验是质量管理工作的一个重要组 成部分。
工序情报
不合格百分率
除不合格品百分率外,还可得到工序平均 值与工序变差的情报,以便采取补救措施
严格性
对一已知种类的所有不合格品 对每一不合格品按其最接近的规格所检验
《抽样检验培训教材》PPT课件

• 樣本量代碼 MIL-STD-105E用英文大些字母A、B、C……R表示樣本 量代碼。
• 檢驗水平 MIL-STD-105E的檢驗水平分為特殊檢驗水平S-1、S-2、 S-3、S-4和一般檢驗水平Ⅰ、Ⅱ、Ⅲ,共七個級別。
不合格:沒有滿足某個規定要求。
不良品:偏離(或完全喪失)開發設計(或契約) 明確規定的部分(或全部)項目的規格的實體。 (一般指產品、半成品、零部件、原材料)
ppt课件
11
抽樣檢驗的簡介
• 基本概念及術語
7、缺陷
沒有滿足某個預期的使用要求(規格、圖面、說
明書)者,稱之為缺陷。一個產品的任何一個特 征不符合指定的技術要求(標準值)都可以說有 缺陷。缺陷一般分為:
計量抽樣檢驗:是指從批中隨機抽取的樣本,
利用樣本中各單位產品的特征值,來判斷這批產 品是否合格的檢驗判定方法。
計數抽樣檢驗與計量抽樣檢驗的根本區別在于,
前者是以樣本中所含的不合格品(或缺陷)個數為
依據,后者是以樣本中各單位產品的特征值為依
據。
ppt课件
13
計數值抽樣檢驗的歷史
1950年,美國軍方發布了MIL-STD-105A,幾 次修訂后于1963年發布了MIL-STD-105D。此標 準為美、英、加聯合采用,也叫做ABC-STD105D。ISO將它改正為ISO2859。我國以 ISO2859為基礎,將七次抽樣改為五次抽樣,發 布了GB2828。
群體中的個體,被抽取的機會要均等。
數據的可信賴性還取決于測定的真實性及紀 錄的真實性,這一點是理所當然的。
ppt课件
9
抽樣檢驗的簡介
• 基本概念及術語
5、交貨方與顧客
交貨方,也稱供方,即提供產品的一方。可以
• 檢驗水平 MIL-STD-105E的檢驗水平分為特殊檢驗水平S-1、S-2、 S-3、S-4和一般檢驗水平Ⅰ、Ⅱ、Ⅲ,共七個級別。
不合格:沒有滿足某個規定要求。
不良品:偏離(或完全喪失)開發設計(或契約) 明確規定的部分(或全部)項目的規格的實體。 (一般指產品、半成品、零部件、原材料)
ppt课件
11
抽樣檢驗的簡介
• 基本概念及術語
7、缺陷
沒有滿足某個預期的使用要求(規格、圖面、說
明書)者,稱之為缺陷。一個產品的任何一個特 征不符合指定的技術要求(標準值)都可以說有 缺陷。缺陷一般分為:
計量抽樣檢驗:是指從批中隨機抽取的樣本,
利用樣本中各單位產品的特征值,來判斷這批產 品是否合格的檢驗判定方法。
計數抽樣檢驗與計量抽樣檢驗的根本區別在于,
前者是以樣本中所含的不合格品(或缺陷)個數為
依據,后者是以樣本中各單位產品的特征值為依
據。
ppt课件
13
計數值抽樣檢驗的歷史
1950年,美國軍方發布了MIL-STD-105A,幾 次修訂后于1963年發布了MIL-STD-105D。此標 準為美、英、加聯合采用,也叫做ABC-STD105D。ISO將它改正為ISO2859。我國以 ISO2859為基礎,將七次抽樣改為五次抽樣,發 布了GB2828。
群體中的個體,被抽取的機會要均等。
數據的可信賴性還取決于測定的真實性及紀 錄的真實性,這一點是理所當然的。
ppt课件
9
抽樣檢驗的簡介
• 基本概念及術語
5、交貨方與顧客
交貨方,也稱供方,即提供產品的一方。可以
《抽样检验》PPT课件
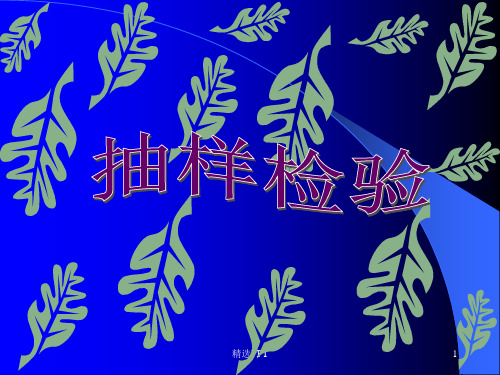
二项分布计算法:无限总体计件抽检
L(p)
=∑ A
d=0Cndຫໍສະໝຸດ Pd(1-p)n-d
( )n d p
从样本量n中抽取d个不合格品的全部组合数; 批不合格品率
•P(X=x)=Cnx
x n-X p (1-p)
.
X=0.1.2…
当有限总体n / N≤0.1时,可用二项概率去近似超几何概率.
泊松分布计算法: 计点抽检
2. 计量检验:根据给定的技术标准,将单位产品的 质量特性(如长度、重量等)用连续尺度测量出 具体数值并与标准对比的检验。
3. 单位产品:为实施抽样检验而划分的单位体或单 位量。
4. 检验批:作为检验对象而汇集起来的一批产品, 也称交检批。一个检验批应由基本相同的制造条 件一定时间内制造出来的同种单位产品构成。
5. 批量:指检验批中单位产品的数量;
6. 不合格:在抽样检验中,不合格是指单位产品的任何一 个质量特性不符合规定要求;
7. 不合格品:有一个或一个以上不合格的单位产品,称 为不合格品;
8. 抽样方案:规定了每批应检验的单位产品数(样本量 或系列样本量)和有关接收准则(包括接收数、拒收数、 接收常数和判断规则等)的一个具体方案;
用给定的抽样方案(n , A)(n - 样本量, A - 批合格判定数)去验收批量N和批质 量p已知的连续检验批时,把检验批判为 合格而接收的概率,记为L(p)。
接收概率的计算方法:
1. 超几何分布计算法
2. 二项分布计算法
3. 泊松分布计算法
精选PPT
7
超几何分布计算法:有限总体计件抽检
A
L(p) =∑
P(X=x)=CN-Mn-x CMx / CNn =0,1,2 P(X=0)=C12-34-0 C30 / C124 =0.255
抽样检验PPT课件
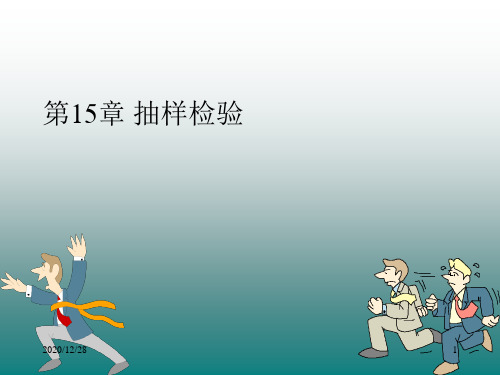
• (2)被判定为合格的产品,并不等于批中每个产 品都合格;被判定为不合格的批,也不等于批中 每个产品都不合格
• (3)并非任何抽样检验都能达到正确的判断整批 产品质量的目的
2020/12/28
质量管理
8
15.2统计抽样方案的分类
• 按统计抽样检验的目的分类
预防性抽 样检验
半成品制造过程中的抽样检验,目的是及时发现过程中的 不稳定因素。
2020/12/28
质量管理
11
15.2计数抽样原理与方案
• 抽样方案的两个参数: – 抽取的样本容量n – 对样本进行检验时,判断批合格与否的合格判 断数(对称接收数)c
2020/12/28
质量管理
12
• 根据抽样方案是抽取一个还是多个样本可分为:一 次抽样、二次抽样、多次抽样、序贯抽样等几种。
2020/12/28
质量管理
19
(2)接受概率曲线(OC曲线,Operating Characteristic Curve)
2020/12/28
质量管理
20
• 例:设一批产品的批量为N=100,给定的抽样方案 为n=10, Ac=0,这表明我们从这批产品中随机抽 取10件产品进行检验,如果没有不合格品,则接收 这批产品,否则就拒收这批产品。
2020/12/28
质量管理
3
15.1基本概念
• 单位产品(sample size, n):为了实施抽样检验而划 分的单位量。
• 批(检验批)(lot or batch ):指作为检验对象而 被汇集起来的 一批产品。
• 批量(lot size, N):指检验批所包含的单位产品数 量。
• 缺陷:质量特性未满足预期的使用要求。 • 不合格与不合格品:不合格是指单位产品的任何
• (3)并非任何抽样检验都能达到正确的判断整批 产品质量的目的
2020/12/28
质量管理
8
15.2统计抽样方案的分类
• 按统计抽样检验的目的分类
预防性抽 样检验
半成品制造过程中的抽样检验,目的是及时发现过程中的 不稳定因素。
2020/12/28
质量管理
11
15.2计数抽样原理与方案
• 抽样方案的两个参数: – 抽取的样本容量n – 对样本进行检验时,判断批合格与否的合格判 断数(对称接收数)c
2020/12/28
质量管理
12
• 根据抽样方案是抽取一个还是多个样本可分为:一 次抽样、二次抽样、多次抽样、序贯抽样等几种。
2020/12/28
质量管理
19
(2)接受概率曲线(OC曲线,Operating Characteristic Curve)
2020/12/28
质量管理
20
• 例:设一批产品的批量为N=100,给定的抽样方案 为n=10, Ac=0,这表明我们从这批产品中随机抽 取10件产品进行检验,如果没有不合格品,则接收 这批产品,否则就拒收这批产品。
2020/12/28
质量管理
3
15.1基本概念
• 单位产品(sample size, n):为了实施抽样检验而划 分的单位量。
• 批(检验批)(lot or batch ):指作为检验对象而 被汇集起来的 一批产品。
• 批量(lot size, N):指检验批所包含的单位产品数 量。
• 缺陷:质量特性未满足预期的使用要求。 • 不合格与不合格品:不合格是指单位产品的任何
抽样检验ppt课件

4. 检索抽样方案(n,A)
精选课件ppt
15
计数挑选型抽样检验
• 计数挑选型抽样检验是指用预先的抽样方案对 批进行初次检验,判为合格的批直接接收,判 为不合格的批必须经过全数检验,将批中不合 格品一一挑出换成合格品后再提交检验的过程。
相关标准:GB/T 13546-92 ;ISO2859-2
计数挑选型抽样检验适用于: 1. 产品一批接一批入库; 2. 各工序间的半成品交接; 3. 向指定的用户连续供货
不合格分级: 1. A类不合格:单位产品的极重要的质量特性不符合规定,或单位产品的质量特性极严重不符合规定; 2. B类不合格:单位产品的重要的质量特性不符合规定,或单位产品的质量特性严重不符合规定; 3. C类不合格:单位产品的一般质量特性不符合规定,或单位产品的质量特性轻微不符合规定。
3. 批的组成:同一批内的产品应当是在同一制造条件下生产的。批量大小应 适宜。
式中
• P——过程平均不合格率; •Ni——第i批产品的批量; •Di——第i批产品的不合格品数; •k——批数
注: •在实践中,P值是不易得到的,一般可以利用抽样检验的结果来估计; •P值可用来预测最近将要交检的产品不合格率; •经过返修或挑选后,再次交检的批产品的检验数据以及截尾检验结果都不能用来估计P 值; •批数一般不应少于20批;如是新产精品选,课开件始pp时t 可以用5~10批的抽检结果估计,以后2应3 不少于20批。
精选课件ppt
1
抽样检验一般适用于下述情况:
1. 破坏性检查验收; 2. 测量对象是流程性材料;
3. 希望节省单位检验费用和时间。
精选课件ppt
2
基本概念
• 名词术语
1. 计数检验:根据给定的技术标准,将单位产品简 单地分成合格品或不合格品的检验;或是统计出
抽样检验培训课程(ppt 54页)

0 . 0299
P( 3 )
5
3
0 . 06
3( 0 . 94 )2
0 . 0019
泊松分布
计算公式
P a
=
Ac d=0
n p d e -np d!
(e = 2.71828)
P( 0 )
(5 0 . 06 )0 e 5 0.06
0!
0 . 7428
按照国际惯例,通常默认设定值为5%,即是把一批合格品错判为不合格批的概 率是5%,或者说是每的 显形检验P值所设定的临界值0.05。
(2)第Ⅱ类错误 (取伪错误) 发生概率为
= Pa (p1)
所谓犯第Ⅱ类错误是指将该拒收的批误判为接收
计数抽样包括: 1.计点(不合格数)——泊松分布 2.计件(不合格品数)——“超几何分布”或“二项式分布”
泊松分布
P a
=
Ac d=0
n p d e -np d!
(e = 2.71828)
【例2】今对批量为 50 的外购产品批作抽样验收,其中包含 3 个不 合格品,求采用的抽样方案为(5,1)时的接收概率 Pa 是多少?
挑选型
检测后,凡达到抽样方案判定基准合格的就接收;达不到判 定基准的,则进行挑选检验
标准型
是在抽样方案中对供、购双方都规定质量保护和质量保证值 ,具有可满 足供、购双方要求的特点的抽样检验
三、批可接受性的判断
批质量的判断过程是:
从批量N中随机抽取n 个单位产品组成一个样本,然后对 样本中每一个产品进行逐一测量,记下其中的不合格品数d, 如果d≤Ac,则认为该批产品质量合格,予以接收;如果 d≥Ac+1,则认为该批产品质量不合格,予以拒收
抽样方法及技巧培训教材(PPT 30页)

例题
例题1
问:工厂生产的某种产品用传输带将产品送入包装车间, 检验人员从传送带上每隔5分钟抽一件产品进行检验,问 这是一种什么抽样法?
答:这是将总体分成均衡的若干部分,再从每一部分按照 预先订出的规则抽取一个个体,得到所需要的样本,故它 是系统抽样 。
例题
例题2
问:已知甲、乙、丙三个车间一天内生产的产品分别是 150件、130件、120件,为了掌握各车间产品质量情况, 从中取出一个容量为40的样本,该用什么抽样方法?简述 抽样过程?
抽取一人为调查对象
非概率抽样的优点 简单易行、成本低、省时间,在统计上也比概 率抽样简单。但由于无法排除抽样者的主观性, 无法控制和客观地测量样本代表性,因此样本不 具有推论总体的性质。非概率抽样多用于探索性 研究和预备性研究,以及总体边界不清难于实施 概率抽样的研究。在实际应用中,非概率抽样往
往与概率抽样结合使用
例题
例题1
问:批量1000,level一般检验水平Ⅱ级 ,AQL0.065,正 常检验一次抽样方案,查询样本量和Ac/Re 答:样本量200,Ac/Re 0/1。
例题2
问:批量1000,level特殊检验水平S-1级 ,AQL4.0,正 常检验一次抽样方案,查询样本量和Ac/Re 答:样本量3,Ac/Re 0/1。
对角抽样:
来货摆放横竖分明、 整齐一致的,如使 用托盘等盛装或平 铺放置的来料等
三角抽样:
来货若摆放在同一 平面时。
S行抽样:
来货若摆放在同一 平面时。
概率抽样
分层抽样(类型抽样)
分层抽样是先把总体按一定标志分成不同类型或层次,然 后从各种不同类型中随机抽取若干单位组成样本 。
分层标准
⑴以调查所要分析和研究的主要变量或相关的变量作为分 层的标准。 ⑵以保证各层内部同质性强、各层之间异质性强、突出总 体内在结构的变量作为分层变量。 ⑶以那些有明显分层区分的变量作为分层变量。
抽样检验知识培训(PPT 41页)_7258

10、计量检验:
根据给定的技术标准,将单位产品的质量特性(如重量、 长度、强度等)用连续尺度测量出其具体数值并与标准对比的 检验。
计数抽样检验与计量抽样检验的根本区别在于,前者是以样本 中所含不合格品(或缺陷)个数为依据;后者是以样本中各单位产 品的特征值为依据。
抽样检验知识培训 企画推进课
(四)抽样检验的形态分类
①轻缺陷 A、几乎不影响制品使用目的。 B、部分规格略微偏规格。 C、不太可能影响客户愉快感的缺陷。
抽样检验知识培训 企画推进课
②重缺陷(也称B级缺陷) A、不能达到产品的使用目的,或者主要规格严重偏离。 B、导致客户使用时较为不愉快的缺陷,或者使用时需改造和交 换零部件等多余麻烦。 C、在使用初期尽管没有大的障碍,但导致缩短产品寿命的缺陷。 ③致命缺陷 A、产品机能有重大影响,使客户无法使用。 B、危极生命 C、预测有可能导致不安全状况。
注意:我们从成品、或半成品、或零部件中抽取一部分样本 加以测定分析时,决不是仅为获取抽出样本的情报或状况。而是 要从样本的检验结果判定批络的状态,以便对批络采取措施。
4、样本(n)
我们从批中抽取的部分个体。常用n来表示。
抽样检验知识培训 企画推进课
图1:检验批、样本及数据的关系
目的
群体
样本 数据
关于生产工程 工程管理 工程改善
抽样检验知识培训 企画推进课
所以,除非产品的品质时好时坏、波动较大 必须采用较小的批以保证批的合理外,当产品品 质较稳,采用大批量是经济的。当然在使用大批 量时,应当考虑到仓库场地限制以及不合格批的 返工等可能造成的困难。
提交检验的批在放置时,应尽量考虑使检验 员能够比较方便地从各部位抽取样品。
抽样检验知识培训 企画推进课
根据给定的技术标准,将单位产品的质量特性(如重量、 长度、强度等)用连续尺度测量出其具体数值并与标准对比的 检验。
计数抽样检验与计量抽样检验的根本区别在于,前者是以样本 中所含不合格品(或缺陷)个数为依据;后者是以样本中各单位产 品的特征值为依据。
抽样检验知识培训 企画推进课
(四)抽样检验的形态分类
①轻缺陷 A、几乎不影响制品使用目的。 B、部分规格略微偏规格。 C、不太可能影响客户愉快感的缺陷。
抽样检验知识培训 企画推进课
②重缺陷(也称B级缺陷) A、不能达到产品的使用目的,或者主要规格严重偏离。 B、导致客户使用时较为不愉快的缺陷,或者使用时需改造和交 换零部件等多余麻烦。 C、在使用初期尽管没有大的障碍,但导致缩短产品寿命的缺陷。 ③致命缺陷 A、产品机能有重大影响,使客户无法使用。 B、危极生命 C、预测有可能导致不安全状况。
注意:我们从成品、或半成品、或零部件中抽取一部分样本 加以测定分析时,决不是仅为获取抽出样本的情报或状况。而是 要从样本的检验结果判定批络的状态,以便对批络采取措施。
4、样本(n)
我们从批中抽取的部分个体。常用n来表示。
抽样检验知识培训 企画推进课
图1:检验批、样本及数据的关系
目的
群体
样本 数据
关于生产工程 工程管理 工程改善
抽样检验知识培训 企画推进课
所以,除非产品的品质时好时坏、波动较大 必须采用较小的批以保证批的合理外,当产品品 质较稳,采用大批量是经济的。当然在使用大批 量时,应当考虑到仓库场地限制以及不合格批的 返工等可能造成的困难。
提交检验的批在放置时,应尽量考虑使检验 员能够比较方便地从各部位抽取样品。
抽样检验知识培训 企画推进课
4抽样检验(PPT122页)

2、抽样方案的优化设计
•既然理想的OC曲线不存在,在实践中是否可以 设计出抽样特性比较好的OC曲线呢?回答是肯定 的,它可以通过设计适当的OC函数来实现。优良 的OC曲线应具有下列形状特征: ❖一个好的抽样方案对应的OC曲线是:当这批 产品的质量较好p≤p0时,要以高概率判断它合格, 予以接收;当这批产品的质量不好p≥p1时,要以 高概率判断它不合格,予以拒收;当产品的质量 变坏,p0<p<p1时,被接收的概率迅速减小。
《质量管理》-4
3
检验的分类
• 根据检验的数量分类: – 全数检验与抽样检验
• 根据流程分类: – 购入检验、中间检验、成品检验、出厂检验、 库存检验、监督检验
• 根据检验的内容分类: – 试制品检验、性能检验、可靠性检验、苛刻检 验、分解检验
• 根据检验差别的方法分类: – 计量检验、计数检验
• 另外还有破坏性检验与非破坏性检验等。
《质量管理》-4
17
(3)理想的OC曲线
所谓理想的OC曲线应 1.00
具有如下特征:当产 接
品的不合格率小于规 收
定值p0时,以概率1接
概 率
收;当产品的不合格
L(p)
品率大于规定值p0时, 以概率1拒收,即如右
图所示。但是,所谓 0 理想的OC曲线是不存
在的。
p0 100 p%
《质量管理》-4
18
先观察下面几个图: 由后面的a,b,c三图可以看到,产品批量N 对OC曲线的影响不大,而样本量n 及合格 判断数c是影响OC曲线的两个主要因素。
《质量管理》-4
25
a、抽样方案不变,N对OC曲线的影响
N 1000 n 20 c 3
N 100 n 20 c 3
《抽样常识培训资料》PPT课件
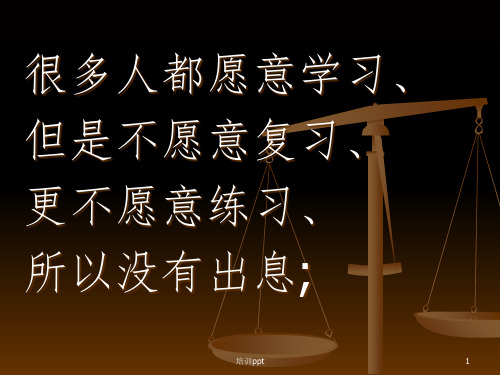
少?允收数是多少?
培训ppt
18
培训ppt
19
来货若为分层摆放或次序排 列的,则可采用层次抽样法 进行抽样。见下图示。如电 阻、电容等贴片料多卷摆放 在一起,卡通箱等分层叠放 等,则适用之。
2、对角抽样法
对于来货摆放横竖分明、整齐 一致的,则可采用对角抽样法 进行抽样。见下图示。如使用 托盘等盛装或平铺放置的来料, 则适用此法
培训ppt
12
培训ppt
10
七、样本的抽取
7.1按简单随机抽样标准从批中随机抽取样本 做为检验的对象,当批由子批或层组成时, 抽样应保证各子批或层的样本数量与子批 或层的大小成正比例。
7.2正常、加严和放宽检验
7.3除非部门主管/部长另有指示或规定,开始 检验时应釆用单次抽样正常检验。
培训ppt
11
七、常用抽样手法 1、层次抽样法
GB/T 2828.1-2003 /ISO 2859-1:1999计数 抽样检验程序。
GB/T 3358.1-1993简单随机抽样标准。
四、定义
缺陷:指不能满足预期使用要求的特性。
培训ppt
6
4.1缺陷分类
4.4.1致命缺陷(CR): 指产品无主要功能或 缺少50%以上次要功能、危害人身安全及 影响客户购买欲望等之缺陷。
抽样 判定
取样检验
外观、尺寸等检测(图纸,检验标准, 功能检测(试装确认) 可靠性检测(必要时)
恢复包装 OK
贴合格品标签
开进货检验报告单
恢复包装
开进料检验不合格报告单
NG
贴不合格品标签
培训ppt
进料检验报告(评审单14 )
九、正常检验、加严检验及放宽检验的转移 流程:
培训ppt
18
培训ppt
19
来货若为分层摆放或次序排 列的,则可采用层次抽样法 进行抽样。见下图示。如电 阻、电容等贴片料多卷摆放 在一起,卡通箱等分层叠放 等,则适用之。
2、对角抽样法
对于来货摆放横竖分明、整齐 一致的,则可采用对角抽样法 进行抽样。见下图示。如使用 托盘等盛装或平铺放置的来料, 则适用此法
培训ppt
12
培训ppt
10
七、样本的抽取
7.1按简单随机抽样标准从批中随机抽取样本 做为检验的对象,当批由子批或层组成时, 抽样应保证各子批或层的样本数量与子批 或层的大小成正比例。
7.2正常、加严和放宽检验
7.3除非部门主管/部长另有指示或规定,开始 检验时应釆用单次抽样正常检验。
培训ppt
11
七、常用抽样手法 1、层次抽样法
GB/T 2828.1-2003 /ISO 2859-1:1999计数 抽样检验程序。
GB/T 3358.1-1993简单随机抽样标准。
四、定义
缺陷:指不能满足预期使用要求的特性。
培训ppt
6
4.1缺陷分类
4.4.1致命缺陷(CR): 指产品无主要功能或 缺少50%以上次要功能、危害人身安全及 影响客户购买欲望等之缺陷。
抽样 判定
取样检验
外观、尺寸等检测(图纸,检验标准, 功能检测(试装确认) 可靠性检测(必要时)
恢复包装 OK
贴合格品标签
开进货检验报告单
恢复包装
开进料检验不合格报告单
NG
贴不合格品标签
培训ppt
进料检验报告(评审单14 )
九、正常检验、加严检验及放宽检验的转移 流程:
- 1、下载文档前请自行甄别文档内容的完整性,平台不提供额外的编辑、内容补充、找答案等附加服务。
- 2、"仅部分预览"的文档,不可在线预览部分如存在完整性等问题,可反馈申请退款(可完整预览的文档不适用该条件!)。
- 3、如文档侵犯您的权益,请联系客服反馈,我们会尽快为您处理(人工客服工作时间:9:00-18:30)。
与AQL的关系 LTPD保护使用方,AQL保护生产方 产品质量<AQL,高概率接收 产品质量>AQL,高概率拒收
品质源于改善!
20
品质源于改善!
21
定义:调查对象总体中每个部分都有同等被抽中 的可能,是一种完全依照机会均等的原则进行的 抽样调查,被称为是一种“等概率 。
方法: 简单随机抽样;(=随便抽样?) 等距抽样; 类型抽样(按?类 按?层) 整群抽样 。
品质源于改善!
பைடு நூலகம்13
以不合格品百分数或每百万单位产品不合格 数表示。
批不合格率P:
p=D/N
批不合格品百分数
100p=D/N*100
每百单位产品不合格数
C/N*100
品质源于改善!
14
一批零件批量为N=10000件,已知其中包含的不 合格品数为D=20件,则批不合格品率、不合格品 数?
品质源于改善!
17
AQL:也称可接受质量水平,是可连续交验批的过程平
均不合格率上限值,是用户所能接受的质量水平(最差 的水平)。
确定AQL的原则:
以产品为核心,根据质量特性和重要程度分类
AQL(A类)<AQL(B类)<AQL(C类) 检验项目:AQL(少) < AQL(多) AQL(军用产品)<AQL(民用产品) AQL(电器性能)<AQL(机械性能)<AQL(外观) AQL(零部件)< AQL(成品)
品质源于改善!
15
检验一批产品的外观质量,批量N=2000,其中10 件每件有2个不合格,5件各有1处不合格,则
批每百单位不合格数为?
品质源于改善!
16
过程平均:一定时间或一定量产品范围内的过
程水平平均值称为过程平均。
Pbar =(D1+D2+…+Dk) / (N1+N2+…+Nk) * 100%
品质源于改善!
4
零部件 成品 在制品 半成品 过程 管理程序 记录 库存品 维修操作
品质源于改善!
5
GB2828.1-2003是计数 调整型抽样检验!
计数型抽样检验:把抽取样本后通过离散尺度
衡量的方法称为计数抽样检验。 计件:不合格品数 计点:不合格数
7
批 单位产品 批质量水平 过程平均 不合格 不合格品 可接收质量水平(AQL) 批允许最大不合格率(LTPD) 抽样 生产方风险 使用方风险
品质源于改善!
8
定义:同一种原材料、工艺、设备、时间生产出 来的产品的总和。
注意事项 抽样的批必须是生产批,而非交验批 批量大的批的检验要经济于批量小的批的检验 批的包装应便于运输与摆放,便于抽样。
C类不合格:单位产品的一般质量特性(mineral) 不符合规定,或单位产品的质量特性轻微不符合规 定。
品质源于改善!
11
A类不合格品:有一个或一个以上A类不合格,
也有可能还有B类不合格和或C类不合格的单位产 品;
B类不合格品:有一个或一个以上B类不合格,
也有可能还有C类不合格,但没有A类不合格的单 位产品;
注: 在实践中,P值是不易得到的,一般可以利用抽样检验 的结果来估计; P值可用来预测最近将要交检的产品不合格率; 经过返修或挑选后,再次交检的批产品的检验数据以及 截尾检验结果都不能用来估计P值; 批数一般不应少于20批;如是新产品,开始时可以用 5~10批的抽检结果估计,以后应不少于20批。
品质源于改善!
9
可用来单独考量或观察的事务 批量:N表示
品质源于改善!
10
不合格:单位产品的特性不符合规定;
不合格分类:
A类不合格:单位产品的关键质量特性(critical
)不符合规定,或单位产品的质量特性极严重不符 合规定;
B类不合格:单位产品的重要质量特性(major)不 符合规定,或单位产品的质量特性严重不符合规定;
.
1
抽样检验的基本概念 计数标准型抽样方案 计数调整型抽样方案 孤立批抽样检验以及GB/T2828.1的使用 其他抽样检验 讨论:抽样检验与供应商管理
品质源于改善!
2
抽样检验定义 抽样检验用途 计数抽样检验与计量抽样检验定义
品质源于改善!
3
破坏性检验 流程性材料或散装物料 检验成本较高或周期较长时 批量较大,实施全检不经济
AQL是对生产方过程质量提出的要求。一定要符 合过程平均 P ,也可按国内相同行业的过程平 均
品质源于改善!
18
对于一个孤立批,限制在某一低接收概率的 质量水平
是不应接收的批质量(不合格品率)的最小 值。
品质源于改善!
19
定义
是指抽样方案认为不可接受而应当拒收的质量水 平. 其接收概率为0.1(使用方风险)时的批的质 量, 即这样的批只有10%的机会被接收。
计量型抽样检验:用抽取样本的连续尺度定量地
衡量一批产品质量的方法。
品质源于改善!
6
抽样检验的目的
决定是否接收该批,而非估计该批的质量。 即使相同质量的批,抽样的结果也可能不同。 最有效的抽样不是检验,而是改进过程使其符合
顾客的要求。 抽样检验出的不合格品如何处理?
品质源于改善!
C类不合格品:有一个或一个以上C类不合格,
但没有A类和B类不合格的单位产品;
品质源于改善!
12
某车间从生产线上抽取1000个零件进行检验,发 现5个产品有A类不合格,4个产品有B类不合格, 2个产品有A、B类不合格,3个产品有A、B、C类 不合格,5个产品有C类不合格。试问ABC类不合 格和不合格品各有多少?
品质源于改善!
22
品质源于改善!
23
超几何分布(随机抽取不放回地抽取N个 产品)
二项分布(OK,NG) 泊松分布(计点)
品质源于改善!
24
Np N Np
L(
p)
A
d
d 0
n d
N n
L(
p)
d
A 0
n d
p
d
(1
p)nd
L( p) A (np)d enp
d0 d!
品质源于改善!
25
已知N=3000的一批产品提交外观检验,若用 (20,1)的抽样方案,当p=1%时,求接收概
品质源于改善!
20
品质源于改善!
21
定义:调查对象总体中每个部分都有同等被抽中 的可能,是一种完全依照机会均等的原则进行的 抽样调查,被称为是一种“等概率 。
方法: 简单随机抽样;(=随便抽样?) 等距抽样; 类型抽样(按?类 按?层) 整群抽样 。
品质源于改善!
பைடு நூலகம்13
以不合格品百分数或每百万单位产品不合格 数表示。
批不合格率P:
p=D/N
批不合格品百分数
100p=D/N*100
每百单位产品不合格数
C/N*100
品质源于改善!
14
一批零件批量为N=10000件,已知其中包含的不 合格品数为D=20件,则批不合格品率、不合格品 数?
品质源于改善!
17
AQL:也称可接受质量水平,是可连续交验批的过程平
均不合格率上限值,是用户所能接受的质量水平(最差 的水平)。
确定AQL的原则:
以产品为核心,根据质量特性和重要程度分类
AQL(A类)<AQL(B类)<AQL(C类) 检验项目:AQL(少) < AQL(多) AQL(军用产品)<AQL(民用产品) AQL(电器性能)<AQL(机械性能)<AQL(外观) AQL(零部件)< AQL(成品)
品质源于改善!
15
检验一批产品的外观质量,批量N=2000,其中10 件每件有2个不合格,5件各有1处不合格,则
批每百单位不合格数为?
品质源于改善!
16
过程平均:一定时间或一定量产品范围内的过
程水平平均值称为过程平均。
Pbar =(D1+D2+…+Dk) / (N1+N2+…+Nk) * 100%
品质源于改善!
4
零部件 成品 在制品 半成品 过程 管理程序 记录 库存品 维修操作
品质源于改善!
5
GB2828.1-2003是计数 调整型抽样检验!
计数型抽样检验:把抽取样本后通过离散尺度
衡量的方法称为计数抽样检验。 计件:不合格品数 计点:不合格数
7
批 单位产品 批质量水平 过程平均 不合格 不合格品 可接收质量水平(AQL) 批允许最大不合格率(LTPD) 抽样 生产方风险 使用方风险
品质源于改善!
8
定义:同一种原材料、工艺、设备、时间生产出 来的产品的总和。
注意事项 抽样的批必须是生产批,而非交验批 批量大的批的检验要经济于批量小的批的检验 批的包装应便于运输与摆放,便于抽样。
C类不合格:单位产品的一般质量特性(mineral) 不符合规定,或单位产品的质量特性轻微不符合规 定。
品质源于改善!
11
A类不合格品:有一个或一个以上A类不合格,
也有可能还有B类不合格和或C类不合格的单位产 品;
B类不合格品:有一个或一个以上B类不合格,
也有可能还有C类不合格,但没有A类不合格的单 位产品;
注: 在实践中,P值是不易得到的,一般可以利用抽样检验 的结果来估计; P值可用来预测最近将要交检的产品不合格率; 经过返修或挑选后,再次交检的批产品的检验数据以及 截尾检验结果都不能用来估计P值; 批数一般不应少于20批;如是新产品,开始时可以用 5~10批的抽检结果估计,以后应不少于20批。
品质源于改善!
9
可用来单独考量或观察的事务 批量:N表示
品质源于改善!
10
不合格:单位产品的特性不符合规定;
不合格分类:
A类不合格:单位产品的关键质量特性(critical
)不符合规定,或单位产品的质量特性极严重不符 合规定;
B类不合格:单位产品的重要质量特性(major)不 符合规定,或单位产品的质量特性严重不符合规定;
.
1
抽样检验的基本概念 计数标准型抽样方案 计数调整型抽样方案 孤立批抽样检验以及GB/T2828.1的使用 其他抽样检验 讨论:抽样检验与供应商管理
品质源于改善!
2
抽样检验定义 抽样检验用途 计数抽样检验与计量抽样检验定义
品质源于改善!
3
破坏性检验 流程性材料或散装物料 检验成本较高或周期较长时 批量较大,实施全检不经济
AQL是对生产方过程质量提出的要求。一定要符 合过程平均 P ,也可按国内相同行业的过程平 均
品质源于改善!
18
对于一个孤立批,限制在某一低接收概率的 质量水平
是不应接收的批质量(不合格品率)的最小 值。
品质源于改善!
19
定义
是指抽样方案认为不可接受而应当拒收的质量水 平. 其接收概率为0.1(使用方风险)时的批的质 量, 即这样的批只有10%的机会被接收。
计量型抽样检验:用抽取样本的连续尺度定量地
衡量一批产品质量的方法。
品质源于改善!
6
抽样检验的目的
决定是否接收该批,而非估计该批的质量。 即使相同质量的批,抽样的结果也可能不同。 最有效的抽样不是检验,而是改进过程使其符合
顾客的要求。 抽样检验出的不合格品如何处理?
品质源于改善!
C类不合格品:有一个或一个以上C类不合格,
但没有A类和B类不合格的单位产品;
品质源于改善!
12
某车间从生产线上抽取1000个零件进行检验,发 现5个产品有A类不合格,4个产品有B类不合格, 2个产品有A、B类不合格,3个产品有A、B、C类 不合格,5个产品有C类不合格。试问ABC类不合 格和不合格品各有多少?
品质源于改善!
22
品质源于改善!
23
超几何分布(随机抽取不放回地抽取N个 产品)
二项分布(OK,NG) 泊松分布(计点)
品质源于改善!
24
Np N Np
L(
p)
A
d
d 0
n d
N n
L(
p)
d
A 0
n d
p
d
(1
p)nd
L( p) A (np)d enp
d0 d!
品质源于改善!
25
已知N=3000的一批产品提交外观检验,若用 (20,1)的抽样方案,当p=1%时,求接收概