深孔钻加工管理规范
钻孔工序管理制度
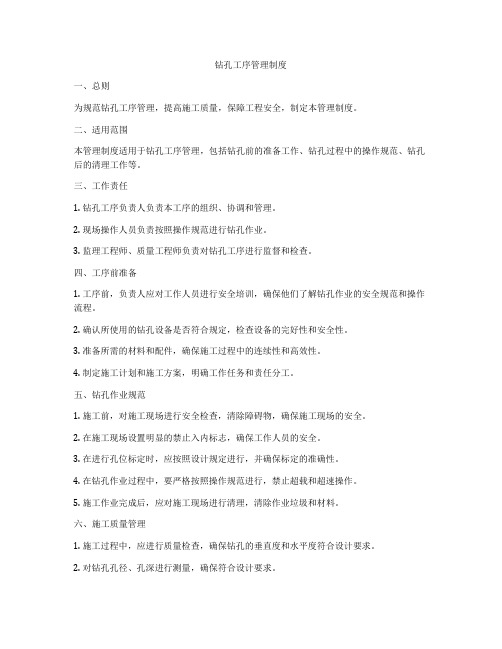
钻孔工序管理制度一、总则为规范钻孔工序管理,提高施工质量,保障工程安全,制定本管理制度。
二、适用范围本管理制度适用于钻孔工序管理,包括钻孔前的准备工作、钻孔过程中的操作规范、钻孔后的清理工作等。
三、工作责任1. 钻孔工序负责人负责本工序的组织、协调和管理。
2. 现场操作人员负责按照操作规范进行钻孔作业。
3. 监理工程师、质量工程师负责对钻孔工序进行监督和检查。
四、工序前准备1. 工序前,负责人应对工作人员进行安全培训,确保他们了解钻孔作业的安全规范和操作流程。
2. 确认所使用的钻孔设备是否符合规定,检查设备的完好性和安全性。
3. 准备所需的材料和配件,确保施工过程中的连续性和高效性。
4. 制定施工计划和施工方案,明确工作任务和责任分工。
五、钻孔作业规范1. 施工前,对施工现场进行安全检查,清除障碍物,确保施工现场的安全。
2. 在施工现场设置明显的禁止入内标志,确保工作人员的安全。
3. 在进行孔位标定时,应按照设计规定进行,并确保标定的准确性。
4. 在钻孔作业过程中,要严格按照操作规范进行,禁止超载和超速操作。
5. 施工作业完成后,应对施工现场进行清理,清除作业垃圾和材料。
六、施工质量管理1. 施工过程中,应进行质量检查,确保钻孔的垂直度和水平度符合设计要求。
2. 对钻孔孔径、孔深进行测量,确保符合设计要求。
3. 对钻孔的现场记录和报告进行管理,建立施工档案。
4. 对现场的施工人员进行质量管理培训,不断提高施工质量和技术水平。
七、安全生产管理1. 严格执行安全操作规程,加强对施工现场的安全监督。
2. 建立健全安全生产管理制度,确保施工现场的安全。
3. 对施工人员进行安全生产教育和培训,提高他们的安全意识和自我保护能力。
4. 加强现场安全防护措施,确保施工现场的安全和人身安全。
八、检查和验收1. 工序负责人应定期对钻孔作业进行检查和整改,确保施工质量和安全。
2. 监理工程师应对钻孔工序进行监督和检查,及时发现问题并提出整改意见。
深孔钻加工工艺规范
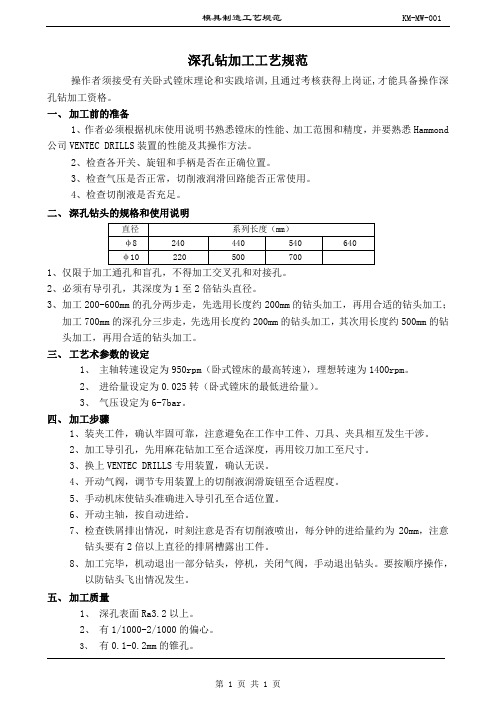
模具制造工艺规范 KM-MW-001深孔钻加工工艺规范操作者须接受有关卧式镗床理论和实践培训,且通过考核获得上岗证,才能具备操作深孔钻加工资格。
一、加工前的准备1、作者必须根据机床使用说明书熟悉镗床的性能、加工范围和精度,并要熟悉Hammond 公司VENTEC DRILLS装置的性能及其操作方法。
2、检查各开关、旋钮和手柄是否在正确位置。
3、检查气压是否正常,切削液润滑回路能否正常使用。
4、检查切削液是否充足。
二、深孔钻头的规格和使用说明1、仅限于加工通孔和盲孔,不得加工交叉孔和对接孔。
2、必须有导引孔,其深度为1至2倍钻头直径。
3、加工200-600mm的孔分两步走,先选用长度约200mm的钻头加工,再用合适的钻头加工;加工700mm的深孔分三步走,先选用长度约200mm的钻头加工,其次用长度约500mm的钻头加工,再用合适的钻头加工。
三、工艺术参数的设定1、主轴转速设定为950rpm(卧式镗床的最高转速),理想转速为1400rpm。
2、进给量设定为0.025转(卧式镗床的最低进给量)。
3、气压设定为6-7bar。
四、加工步骤1、装夹工件,确认牢固可靠,注意避免在工作中工件、刀具、夹具相互发生干涉。
2、加工导引孔,先用麻花钻加工至合适深度,再用铰刀加工至尺寸。
3、换上VENTEC DRILLS专用装置,确认无误。
4、开动气阀,调节专用装置上的切削液润滑旋钮至合适程度。
5、手动机床使钻头准确进入导引孔至合适位置。
6、开动主轴,按自动进给。
7、检查铁屑排出情况,时刻注意是否有切削液喷出,每分钟的进给量约为20mm,注意钻头要有2倍以上直径的排屑槽露出工件。
8、加工完毕,机动退出一部分钻头,停机,关闭气阀,手动退出钻头。
要按顺序操作,以防钻头飞出情况发生。
五、加工质量1、深孔表面Ra3.2以上。
2、有1/1000-2/1000的偏心。
3、有0.1-0.2mm的锥孔。
第 1 页共 1 页。
钻孔管理制度(精选6篇)

钻孔管理制度(精选6篇)钻孔管理制度篇1一、回采工作面、综掘面卸压钻孔验收由通风队跟机瓦检员负责验收。
普掘面卸压钻孔由瓦检员负责验收。
二、生产队组严格按防突措施要求的布置方式、角度、深度施工卸压钻孔,如队组未按措施要求施工钻孔,不合格的钻孔不计必须重新补打钻孔。
瓦检员汇报通风调度,班后组织分析考核。
三、因地质构造或其它原因导致卸压钻孔施工深度不够,上一班瓦检员必须向下一班瓦检员交接清楚并汇报通风调度,下一班队组在钻孔深度不够区域,按卸压钻孔措施要求补打钻孔。
如队组不按规定施工钻孔,严禁生产。
瓦检员汇报通风调度,班后组织分析考核。
四、每天卸压钻孔施工完,瓦检员向通风调度详细汇报钻孔施工情况。
五、严禁生产队组由防突测试孔(要求直径42毫米)代替措施孔(要求直径不小于75毫米)。
六、每班瓦检员交接班后,要详细检查卸压钻孔预留深度,预留深度达不到措施要求,责令队组按要求补打钻孔,并汇报通风调度,班后组织分析考核。
七、防突组负责各采掘工作面悬挂防突进度控制牌,并上锁管理。
生产队组严格按允许推进度组织生产。
八、通风工区防突组每月对全矿各采掘面进行不少于2次的'卸压钻孔施工质量抽查,对抽查结果要进行全矿通报。
九、相关考核1、虚报、假报钻孔深度考核打钻工每人10000元,株连瓦检员20xx元,队组跟班队干、工长各20xx元,队长、书记各20xx元。
2、工作面超割导致卸压钻孔预留深度不够,考核瓦检员、跟班队干、工长各20xx元,株连队长、书记各1000元。
3、生产队组随意倒移防突进度控制牌,考核责任人5000元,株连瓦检员1000元,队组跟班队干、工长各20xx元,队长、书记各1000元。
4、每周防突例会对全矿本周卸压钻孔质量进行排名,第一名奖励队长、书记各500元,第二名奖励队长、书记各300元。
倒数第一名考核队长、书记各500元,倒数第二名考核队长、书记各300元。
钻孔管理制度篇21、钻孔方位角、倾角、孔间距符合规定,有下列情况,按200元扣分:(1)方位角误差超过规定;(2)倾角误差超过规定;(3)孔间距超过规定。
深孔钻床钻孔专机安全操作及保养规程
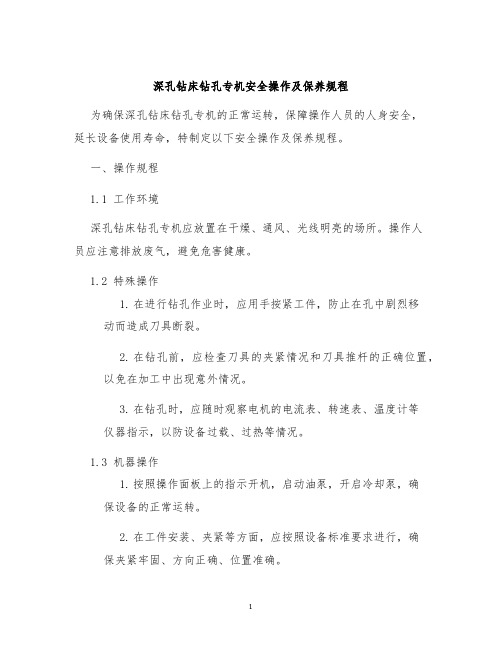
深孔钻床钻孔专机安全操作及保养规程为确保深孔钻床钻孔专机的正常运转,保障操作人员的人身安全,延长设备使用寿命,特制定以下安全操作及保养规程。
一、操作规程1.1 工作环境深孔钻床钻孔专机应放置在干燥、通风、光线明亮的场所。
操作人员应注意排放废气,避免危害健康。
1.2 特殊操作1.在进行钻孔作业时,应用手按紧工件,防止在孔中剧烈移动而造成刀具断裂。
2.在钻孔前,应检查刀具的夹紧情况和刀具推杆的正确位置,以免在加工中出现意外情况。
3.在钻孔时,应随时观察电机的电流表、转速表、温度计等仪器指示,以防设备过载、过热等情况。
1.3 机器操作1.按照操作面板上的指示开机,启动油泵,开启冷却泵,确保设备的正常运转。
2.在工件安装、夹紧等方面,应按照设备标准要求进行,确保夹紧牢固、方向正确、位置准确。
3.在调整刀具等操作时,先关闭电机并安全锁定。
4.操作人员应站稳,双手握紧操作手柄,操作时应注意腿部和身体远离咬合处,同时不可离开机器,以免发生意外。
1.4 停机操作1.当加工结束后,应按操作面板上的指示关机,关闭冷却泵,停止油泵,对设备进行清洁保养。
2.停机时应先关闭电机后,再安全锁定设备,必要时注明危险区域。
二、保养规程2.1 常规保养1.对设备元器件、周边设施进行维护保养,如电源线、传动带、润滑系统、冷却系统等。
2.定期检查设备底座、紧固螺丝、安全键、限位开关、断路器等机械部件的松动情况,及时做好清理调整工作。
3.对设备定期进行全面检查、清洗、调整并进行润滑保养。
2.2 特殊保养1.在更换刀具时,应注意清洗磨损之处并及时涂抹润滑剂。
2.定期清洗设备内部及底座、利用空气压力对机器中润滑油进行清洗除尘。
3.对电气系统进行定期检查,检查接线端子是否松动,是否有烧损等情况出现。
三、应急处理1.当设备发生故障时,应立即按操作面板上的按钮将机器停机,同时做好相应的报修工作。
2.在设备突然停机、过载等情况出现时,应立即关闭电源,依照相应的工作流程处理事件。
钻孔施工管理制度

钻孔施工管理制度1. 前言本规章制度旨在规范和引导钻孔施工过程中的管理工作,确保施工过程安全、高效、质量可控。
本制度适用于公司内全部相关钻孔施工项目,全部部门和人员均必需遵守本制度。
2. 施工前准备2.1 施工前评估:施工前应进行地质勘察和工程量评估,以确定施工方法和工期。
2.2 施工方案编制:钻孔施工方案应依据地质情况、设计要求和技术标准进行编制,并经专业人员审批。
2.3 施工人员培训:施工人员应接受相关培训,掌握施工方法、安全操作规程和紧急处理措施等知识。
2.4 施工设备准备:确保施工需要的设备、工具、料子等准备充分,并经过检验合格。
3. 施工过程管理3.1 动态监测:施工过程中应进行动态监测,及时掌握钻孔质量、设备运行状态等信息,并依据监测结果及时调整施工方案。
3.2 安全管理:确保施工现场符合安全生产要求,施工人员应佩戴个人防护装备,设立警示标志,并进行安全警示教育。
3.3 环境保护:施工现场应采取必需的环境保护措施,掌控噪音、扬尘、废水等对周边环境的污染。
3.4 质量掌控:钻孔施工过程中应进行质量掌控,检查施工质量,确保钻孔位置、直径、深度等符合设计要求。
3.5 进度管理:订立施工进度计划,并监督施工进度的执行情况,确保定时完成施工任务。
3.6 风险掌控:识别施工过程中的风险,采取相应的防控措施,确保施工安全。
4. 质量验收与记录4.1 施工质量验收:施工完成后应进行质量验收,检查钻孔质量是否符合设计和技术标准要求。
4.2 施工记录管理:施工过程中应及时记录施工情况、质量掌控信息、安全事故及处理情况等,并保存相关证据文件。
4.3 整改措施:如发现施工质量存在问题,应及时订立整改方案,并实施整改措施,确保问题得到及时解决。
4.4 工程交接:施工完成后,应进行工程交接手续,包含施工报告、验收报告和资料交接等。
5. 监督与评估5.1 监督检查:公司内部应设立特地部门或人员负责钻孔施工的监督检查工作,定期进行检查,发现问题及时矫正。
钻机钻孔管理制度

钻机钻孔管理制度第一章总则第一条为规范钻机钻孔作业,提高钻孔效率,保障施工安全,保护环境,维护设备,并根据《钻孔管理规范》等有关法规,制定本制度。
第二条本制度适用于公司钻机钻孔作业。
第三条钻孔管理应该遵循安全第一的原则,严格执行操作规定,确保作业人员的生命安全和设备的正常运行。
第四条钻孔作业应遵循“先防范、预防为主”的原则,加强对事故、灾害及其他危险因素的管理。
第五条钻孔作业人员必须具备相关的钻孔技能,持有相应的证书,接受过必要的培训并严格遵守相关的操作规定。
第六条本制度应当与《井下作业管理制度》、《井下通风制度》等有关管理制度配套实施。
第二章钻孔前准备第七条钻孔前,需要对钻机进行全面检查,确保各项设备完好,无任何故障。
第八条确认钻孔地点的地质情况和环境特点,为后续钻孔作业做好准备。
第九条制定钻孔施工方案,明确施工的具体步骤和要求,以及所需的设备和材料。
第十条确定钻孔作业的起止时间,明确作业人员的任务分工和责任。
第十一条做好安全防护措施,配备必要的安全设备,保证作业人员的人身安全。
第三章钻孔作业第十二条遵守钻孔操作规程,操作人员必须严格按照操作规定进行钻孔作业,禁止违章操作。
第十三条定期检查钻孔设备,保证设备的正常运行,发现异常及时处理。
第十四条钻孔作业期间,加强现场管理,维护施工现场的秩序,确保安全生产。
第十五条钻孔作业中,必须随时配备专业的安全人员,负责现场的安全管理和应急处置。
第十六条钻孔作业人员在操作过程中,要严格遵守相关的安全操作规定,不得因个人原因随意操作。
第四章钻孔作业后第十七条钻孔作业结束后,要对作业现场进行整理清理,彻底清除作业中的垃圾和材料。
第十八条将钻孔设备进行全面检查和维护,确保设备完好,以备下次作业使用。
第十九条结束钻孔作业后的数据的整理与归档,做好相关的记录和报告。
第二十条钻孔作业结束后,要对作业现场进行安全检查,确保没有安全隐患。
第五章钻孔事故与风险管理第二十一条钻孔作业中,如遇到事故需及时报告并采取相应的应急处置措施。
深孔钻床安全操作规程和操作规程

深孔钻床安全操作规程和操作规程深孔钻床是一种专门用于加工深孔的机床,由于其加工过程需要高速旋转的工具和较大的切削力,因此必须严格按照安全操作规程进行操作,以确保操作人员的安全和机床的正常运行。
深孔钻床的安全操作规程如下:1. 操作人员必须穿戴适当的劳动保护用具,包括防护眼镜、手套、防护服等。
同时,操作人员必须确保身体干燥,以防止发生意外。
2. 在操作前,必须对深孔钻床进行全面的检查。
检查包括机床本体的机械装置是否正常、配套液压装置是否正常、刀具磨损情况等。
如发现问题,必须及时通知维修人员进行处理。
3. 操作人员必须正确使用深孔钻床的操作手册,并严格按照其要求进行操作。
在操作过程中,不得擅自修改机床的参数和设定值。
4. 深孔钻床操作人员必须具备一定的机床操作技能和安全意识。
在操作时,要特别注意刀具的位置和工件的夹紧情况,避免发生意外。
5. 在操作过程中,不得随意触摸机床的运动部件和刀具。
同时,不得使用损坏的刀具进行加工,以免引起事故。
6. 在操作过程中,切忌将手伸入机床的作业区域,以免受伤。
如需接触机床内部部件,必须在停机状态下进行,并戴好防护手套。
7. 操作人员在操作过程中要保持专注,不得随意喧哗或与他人交谈,以免分散注意力。
8. 操作人员在操作结束后,必须切断电源,清理工作台和机床,保持工作环境整洁。
深孔钻床的操作规程如下:1. 根据加工要求,选择合适的刀具和切削参数。
同时,根据工件的尺寸和形状,合理安排工件的夹紧方式。
2. 将工件夹紧在工作台上,并进行对中调整。
确保工件和刀具的相对位置正确。
3. 启动深孔钻床主电源,开启机床控制系统。
设置切削相关参数,如切削速度、进给速度等。
4. 按照操作手册的要求,打开冷却润滑泵,并确保冷却润滑液的供给正常。
在加工过程中要及时检查润滑液的供给情况,防止润滑不良引起过热。
5. 执行加工程序,确保切削过程平稳。
在加工过程中,要密切注意机床的运行情况,包括刀具的振动情况、切削力的大小等。
深孔钻作业规范

3.10机床出现故障时,应由有修理资格的专业人员检修,严禁私自拆卸机床的任何零件。
批准:作成:
1.操作方法:
1.1打开电气控制柜门上的总电源开关。
1.2操作面板电源指示灯亮,电柜风扇开始旋转。
1.3按下操作面板NC起动按钮,几秒钟后显示器显示,当NC准备好之后各轴均可运动。
2.保养方法:
2.1每班加68#液压导轨油一次。
2.2每班开机前清洁机室。
2.3每天清洁电器箱空气过滤网一次。
2.4每周清洁机身一次。
2.5每周清洁油过滤网一次。
2.6每月清洁电箱内尘埃一次。
2.7 每半年调整机床水平一次。
2.8 每半年更作机床,在操作前要熟读机床操作手册以及机床上所有警告牌。
3.2机床为自动启动数控机床,严禁靠近或接触机床的运动部件。
3.3工作时必须载安全眼睛,穿安全鞋,严禁戴手套,严禁敞开衣服。
3.4开机前先检查油位是否在“H”横线处,空压表压力为6公斤以上,确保机室内无杂物防碍机械运转才可以开机。
3.5机床开启后,首先让机床自动加归原点。
3.6加工时要确保工件及切削刀具完全夹紧,严禁超速进给,严禁主轴超速运转。
3.7主轴未停稳,严禁安装或拆卸工件、刀具,更不可触摸主轴。
3.8必须保证机床只由一个人单独操作,机械进行切削加工时,操作员不准离开工作岗位。
深孔钻加工店规章制度

深孔钻加工店规章制度第一章总则第一条为规范深孔钻加工店的生产经营活动,维护员工利益,确保产品质量和安全生产,制定本规章制度。
第二条深孔钻加工店是指专门从事深孔钻精密加工的企业,生产过程中需要严格遵守规章制度,确保生产和服务质量。
第三条深孔钻加工店的所有工作人员都应遵守本规章制度,做到规范操作,服从管理,确保生产和工作环境的安全。
第四条深孔钻加工店负责人对本规章制度的解释权,对违反规定的员工进行相应处罚。
第二章人员管理第五条深孔钻加工店应对聘用的员工进行严格的考核和培训,确保其具备相应的技术和能力。
第六条员工应遵守加工店的工作制度,服从管理,不得擅自调动加工设备或私自将加工设备带离工作场所。
第七条员工不得利用工作之便侵占加工店的财产,否则将承担相应的责任。
第八条加工店要建立健全管理人员和员工的奖惩制度,对工作表现良好的员工给予相应奖励,对违规违纪的员工进行处罚。
第九条员工应保护加工店的商业机密和技术秘密,不得私自泄露给竞争对手。
第三章安全生产第十条加工店要制定完善的安全生产规章制度,加强员工的安全教育和培训,提高员工的安全意识。
第十一条加工设备必须经过定期检测和维护,发现问题要及时处理,确保设备的正常运行和安全性。
第十二条加工店要定期组织安全演练和应急预案,提高员工在突发情况下的应变能力。
第十三条员工在作业过程中应按规定佩戴安全防护设备,严禁擅自违反安全规定。
第四章质量管理第十四条加工店要建立完善的质量管理体系,确保产品质量稳定和符合客户需求。
第十五条产品出厂前必须经过严格的质量检验和监控,不合格品不得出厂,确保产品的质量合格。
第十六条加工店要增强质量意识,不断提高员工的质量管理水平,提高产品质量和市场竞争力。
第五章环境保护第十七条加工店要遵守国家的环保法律和规定,监测和处理生产过程中产生的废水、废气、废渣等污染物。
第十八条加工店要合理使用资源,降低排放,推广清洁生产技术,减少对环境的影响,保护生态环境。
深孔钻设备安全操作规程

深孔钻设备安全操作规程深孔钻是一种用于加工大型钢铁构件的高精度机械,由于其操作具有一定的危险性,在使用过程中必须注意安全操作规程。
以下是深孔钻设备安全操作规程:一、操作前的准备工作1. 检查机器设备是否完整,有无损坏或松动现象,确保设备正常运转。
2. 清理工作台面和加工物料,并保持工作环境整洁干净。
3. 穿戴适合的工作服装和防护用品,如安全帽、安全眼镜、防护面罩、手套等,以避免工作时受到伤害。
4. 防止深孔钻工作过程中发生的火灾、爆炸等事故,需要将一切易燃、易爆物品移开,严禁在加工区域内吸烟、使用明火等操作。
二、正常操作流程1. 深孔钻加工过程中,必须保持机器设备原动力开关处于关闭状态,避免设备出现操作失误而导致安全事故。
2. 操作人员必须了解深孔钻加工的相关技术,熟悉加工程序、加工工艺及设备操作流程,以保证深孔钻工作的安全和正常进行。
3. 操作时必须保持机器设备周围干净整洁,防止加工杂物等异物与机器设备接触而导致操作事故。
4. 深孔钻加工过程中,操作人员必须确保自身在安全位置,避免被工件或加工刀具等物料卡住,从而导致安全事故。
5. 如果出现设备异常情况,如设备噪音过大、振动过大等现象,操作人员应及时停止操作并进行检修,以免对操作人员造成危害。
三、设备停机及清洗1. 在深孔钻停机前,必须先关闭加工材料的供给和原动力开关,并按照规范操作程序进行停机和清洗。
2. 清洗时必须注意,不能使用矿物油等易燃、易爆物品,并使用指定的清洗液清洗,当清洗液内含有易燃、易爆材料时,应该避免使用或妥善处理。
3. 设备停止加工后,必须清理加工区域内的加工材料和废料,将设备内的工作液和杂物请涨干净,并保持机器设备表面干净整洁。
加工剩余的材料也要放置在指定的仓库内归位,对于设备损坏等问题应及时通知技术人员进行维修设计。
以上就是深孔钻设备的安全操作规程。
加工中如果出现设备实时卡住、噪音过大、振动过大等异常情况,必须直接停机,观察设备中是否存在卡住的异常物品,并及时处理,以免对设备造成进一步的损坏。
工程施工钻孔管理制度

工程施工钻孔管理制度第一章总则第一条为规范工程钻孔施工行为,确保工程质量和安全,保障工程顺利进行,制定本制度。
第二条适用范围:本制度适用于工程施工中的钻孔作业管理。
工程施工包括建筑工程、市政工程、园林工程等。
第三条本制度适用于所有相关人员,包括施工单位、监理单位、钻孔作业人员等。
第四条钻孔施工应遵循“安全第一、预防为主、综合治理、全员参与”的原则。
第五条钻孔人员应执行本制度,认真履行职责,做好钻孔作业管理工作。
第二章钻孔施工前的准备工作第六条施工单位应在确定钻孔方案前,进行详细的勘察和分析,综合考虑地质条件、建筑结构等因素,制定合理的钻孔方案。
第七条施工单位应向相关部门报备钻孔方案,等待审批后方可开始施工。
第八条施工单位应对钻孔设备和工具进行检查和维护,确保设备完好,避免因设备故障而影响工程进度。
第九条施工单位应制定安全生产计划和应急预案,确保施工过程中的安全。
第十条施工单位应组织施工人员参加相关安全培训,了解施工现场的安全要求和应急处理措施。
第三章钻孔施工的技术要求第十一条钻孔作业人员应持有效证件,具有相关技术资质,且经过培训合格的人员才能参与钻孔作业。
第十二条钻孔作业人员在进行钻孔作业前,应熟悉钻孔设备和工具的操作规程,保证操作的正确性和安全性。
第十三条钻孔作业人员在进行钻孔作业时,应遵循钻孔方案,按照规定的深度和直径进行作业,避免出现偏差。
第十四条钻孔作业人员在进行钻孔作业时,应随时注意作业周围的安全情况,确保周围人员和设施的安全。
第十五条钻孔作业人员应及时清理孔口,防止孔口堵塞,确保钻孔作业的顺利进行。
第四章钻孔施工的质量要求第十六条钻孔作业人员在进行钻孔作业时,应按规定确定孔洞的深度和直径,保证孔洞的质量符合要求。
第十七条钻孔作业人员应使用合格的钻头和钻杆,确保孔洞的圆润度和平直度。
第十八条钻孔作业人员应对孔洞的质量进行检验,及时发现问题并进行处理。
第十九条钻孔作业人员应及时向监理单位报告孔洞的情况,确保监理单位对孔洞的质量进行审核。
钻孔车间管理制度范本

钻孔车间管理制度范本第一章总则第一条为了规范钻孔车间的生产管理,提高生产效率和产品质量,保障员工的生命财产安全,根据国家有关法律法规和公司管理制度,特制定本制度。
第二条本制度适用于钻孔车间全体员工,包括管理人员、技术人员和操作人员。
第三条本车间管理工作应遵循科学管理、规范操作、持续改进、安全生产的原则。
第二章人员管理第四条车间管理人员应具备相应的管理能力和专业技能,严格执行公司的各项管理制度。
第五条车间员工应按照操作规程进行作业,严格遵守劳动纪律,服从管理,积极参与车间管理。
第六条车间员工应定期参加安全培训,掌握安全知识和操作技能,提高安全意识。
第七条车间员工应保持良好的工作态度,爱护设备,节约材料,提高工作效率。
第三章设备管理第八条车间设备应按照规定的周期进行维护和保养,确保设备正常运行。
第九条车间设备操作人员应熟练掌握设备操作规程,严格按照操作规程进行操作。
第十条车间设备应定期进行检查和调试,确保设备的精度和稳定性。
第四章质量管理第十一条车间应建立健全质量管理体系,严格按照产品质量标准进行生产。
第十二条车间应加强过程质量控制,及时发现和解决生产过程中的质量问题。
第十三条车间应定期对产品质量进行统计和分析,持续改进生产工艺和操作规程。
第五章安全生产管理第十四条车间应建立健全安全生产责任制,明确安全生产管理职责。
第十五条车间应定期进行安全检查,发现安全隐患及时整改。
第十六条车间应加强危险化学品的管理,严格按照危险化学品的安全操作规程进行操作。
第十七条车间应制定应急预案,定期组织应急演练,提高应对突发事件的能力。
第六章环境管理第十八条车间应加强环境保护,严格按照环保法规进行生产。
第十九条车间应加强废弃物的处理和管理,防止环境污染。
第二十条车间应定期进行环境检查,发现问题及时整改。
第七章卫生管理第二十一条车间应定期进行卫生清理,保持工作环境的整洁和卫生。
第二十二条车间应加强员工的个人卫生管理,要求员工养成良好的卫生习惯。
钻孔工序管理制度

钻孔工序管理制度第一章总则第一条为规范和加强钻孔工序管理,保障工程施工的安全与质量,提高企业的经济效益,制定本制度。
第二条本制度适用于企业内进行基础工程、地质勘探、矿山开采等涉及钻孔工序的施工管理。
第三条钻孔工序管理制度是企业的内部管理制度,所有岗位人员必须遵守并执行,凡对本制度提出修改建议的,须按规定的程序报经公司领导批准后方可实施。
第四条公司应建立健全钻孔工序管理体系,形成科学、规范、有效的管理机制。
第二章责任分工第五条公司领导负责钻孔工序管理工作的全面领导和重大决策,制定公司的钻孔工序管理制度和相关规章制度,确保其合理、科学、有效。
第六条工程部门负责公司钻孔工序管理事项的组织协调和实施,组织编制钻孔工序管理计划,指导、监督、检查和评估全公司的钻孔工序管理工作。
第七条技术部门负责对钻孔工序进行技术指导和管理,制定技术标准、规范和操作流程,指导施工人员进行工作。
第八条生产部门负责实施钻孔工序管理计划,保障施工的顺利进行,采取有效措施,预防和解决施工中的问题。
第九条安全环保部门负责组织、监督、检查公司钻孔工序施工中的安全和环保工作,确保施工符合相关的法律法规和标准。
第十条质量部门负责制定公司的质量管理计划和施工的质量检查,对施工中的质量问题进行跟踪和整改。
第三章施工准备第十一条施工前,应组织相关人员进行施工前的安全、技术、质量交底和培训,确保施工人员对施工环境、设备使用、作业程序、安全要求、质量标准等有充分了解。
第十二条进入施工现场的人员应进行安全培训,穿着符合安全要求的工装,戴好安全帽、安全鞋,佩戴相关的安全防护设备,严守作业的安全规程。
第十三条施工前,需要做好相关设备的检查和维护工作,确保设备的安全、有效,并经过技术部门的验收和确认。
第十四条施工前,应做好现场标识、警示标志和管控措施,确保施工现场的安全和秩序。
第四章施工程序第十五条施工开始前,应由相关技术人员根据施工的要求和钻孔的技术规范进行施工方案的制定,明确施工的程序、工艺、设备等内容,编制施工方案,并报技术部门审批。
深孔钻操作加工的注意事项汇总

一、使用之前检查电机主轴冷却中冷却液的储存量,开启电机的主轴冷却,保证冷却液循环正常。
开启正压密封,以避免加工废液、冷却液等进入电机主轴轴承。
二、装卡材料一定要牢固,必须遵循“装实、装正、装平”的原则,严禁在材料悬空的地方进行雕刻。
三、装卡工具时,须先将卡头里的灰尘及杂物清理干净,把卡头装入压帽内并放正,再一起装到电机主轴上并将刀具插入卡头,最后再销紧压帽。
上下刀松紧压帽的时候严禁采用推拉方式而须用旋转方式。
下刀时应先清理压帽和转上的废屑,松开压帽将刀具拿下再拧下压帽拿出卡头。
四、装卡刀具时,刀具露出卡头的长度须参照雕刻深度文件,夹具而定。
在满足条件情况下露出卡头的长度尽量的短,当刀具的总长度小于22mm时,严禁继续使用。
五、装卡刀具时,刀柄伸入卡头内的长度必须大于18mm。
六、在加工时如用切削液必须冲到刀具上。
七、雕刻过程中,严禁近距离观察,以防止切屑飞入眼睛。
观察时要暂停雕刻,关闭电机主轴并确定电机主轴不再旋转。
雕刻过程中,严禁用手摸切削表面,禁止使用棉丝擦拭工作表面。
八、严禁将任何物品放置在机床台面或横梁上;严禁手扶在横梁和防护罩等机床床体上;禁止身体倚靠在机床床体上。
九、严禁敲击,撞击电机主轴,卸刀时严禁敲打。
十、禁止在过热或过冷状态下使用机床。
深孔钻十一、深孔钻机是一种轻型加工设备。
工装夹具、工件重量与加工废屑之和不要超过机床额定承重量。
十二、雕刻前要认真检查所使用刀具的尺寸,性能是否满足加工编程要求。
十三、在加工前要认真检查刀具路径是否正确。
十四、在开始加工前一定要再次确认各轴起刀点(工作原点)是否正确。
十五、每天必须让电机主轴休息2h。
十六、严禁带电拨插电线,板卡和电器件;加工有机材料等易燃品时,工作现场要有有效的防火措施。
十七、每天下班前10分钟,对机床加油润滑及擦洗清洁机床。
确认机床停止运转,将机床停在指定位置,关闭电源,确认所有开关己断开,方可离开。
深孔钻加工管理规范

9.2.2对照图纸编写程式或使用电脑编写,5条以上必须使用自动编程,手工编程时要仔细确认X.Y.Z深度。
9.2.3先用较低速度加工5mm后再提升到正常速度,调整进给时优先加大进给量,再加切削速度,发现铁屑变色时说明以至极限,适当向下调。
7.2.2确认刀具锋利无破损,磨损,刀杆不弯曲,刀头长度在25mm以上。
7.2.3先在工件的导柱等其他不发生干涉的位置加工100mm,同时确定好进给,转数等参数(按标准进给的80%)。
7.2.4对加工的试刀孔进行位置和孔径精度检测,如OK则正式加工,NG则进行调整,重新碰数(位置不准)或更换刀具(孔径超差)后重复上一步(孔径用标准件检测滑配)。
13、相关记录:
13.1[深孔钻加工记录表](QR-139-02)13.2[钻床加工记录表](QR-139-03)
13.3[设备点检保养记录表](QR-033)
核准: 审核: 制订:日期:
8.2.2工件放置在工作台时须根据钻床大小及工件大小评估是否需要锁紧,工件太大直接放置在地面上时要用水平仪找平。
8.2.3根据图纸选用合适钻头,确保刀刃锋利,角度合理,无崩坏,根据材料及所加工孔的实际情况修磨钻头。
8.2.4根据图纸用卷尺卡尺测量NC点孔,确认加工位置,如未打点,则用高度尺划线后用样冲打点,打点时先用较小力敲一下,移开看是否在十字线中间OK则将样冲尖对准刚打的小点敲到位,有偏差则调整后重敲,不可一次敲到位。
7.2.5加工时仔细核对图纸的孔径,位置,深度,调用程式的须要细心核对程式号,并核对每个孔的座标值,随时注意切削情况,有振动及异响时要停机检查刀具,并每做5个孔就要用标准件测试孔径。
深孔工操作规程

深孔工操作规程
1.深孔工必须经过培训懂熟悉深孔钻机的结构、原理、性能,本工作面的放顶措施经考试合格后方可整地上岗作业。
2.深孔认识工在下井前应了解井下实际情况,带齐所需材料、工具。
3.深孔钻眼应严格按照措施订明规定施工,严把质量关。
并
用实际爆破参数日志每个爆破参数。
4.每次放炮前,必须将工作面的人员撤至安全地点,同时要
求在其要求一切能进入工作面的通道内架设警戒,回风巷内严禁留人。
5.每班上下班时,都必须先检查钻机各种管路。
泵站情况、
钻机角度,必须先紧钻机后才开机。
而且在钻眼过程中随时注意角度
和立钻情况,有反常必须关机处理,处理好后才能重新钻研。
6.人员一律炮孔停留。
7.此时退回钻石时必须使用专用卡子,必须先选择听话自己
应处的安全位置,以防工具、材料飞出伤人。
8.必须坚持湿式打眼,严禁干打眼。
9.操作时,先开水后开风,停在钻时先停水在停风。
10.下班时必须将各种推车手把打到零位,关闭压风和水管,
并闭锁电源开关。
深孔钻安全操作规程
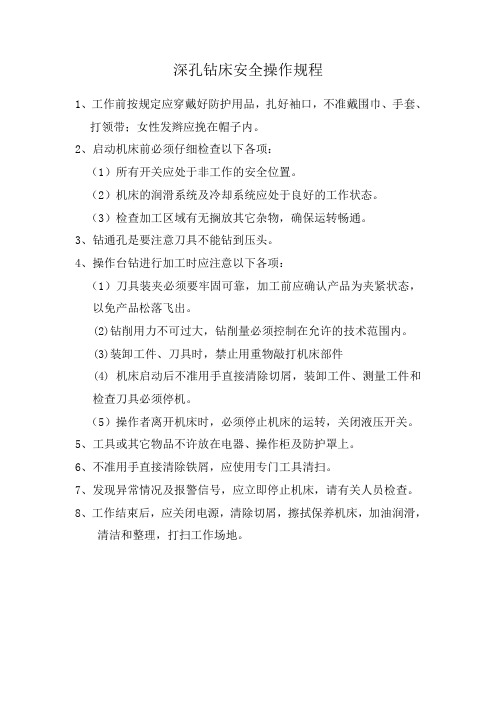
深孔钻床安全操作规程
1、工作前按规定应穿戴好防护用品,扎好袖口,不准戴围巾、手套、
打领带;女性发辫应挽在帽子内。
2、启动机床前必须仔细检查以下各项:
(1)所有开关应处于非工作的安全位置。
(2)机床的润滑系统及冷却系统应处于良好的工作状态。
(3)检查加工区域有无搁放其它杂物,确保运转畅通。
3、钻通孔是要注意刀具不能钻到压头。
4、操作台钻进行加工时应注意以下各项:
(1)刀具装夹必须要牢固可靠,加工前应确认产品为夹紧状态,以免产品松落飞出。
(2)钻削用力不可过大,钻削量必须控制在允许的技术范围内。
(3)装卸工件、刀具时,禁止用重物敲打机床部件
(4) 机床启动后不准用手直接清除切屑,装卸工件、测量工件和
检查刀具必须停机。
(5)操作者离开机床时,必须停止机床的运转,关闭液压开关。
5、工具或其它物品不许放在电器、操作柜及防护罩上。
6、不准用手直接清除铁屑,应使用专门工具清扫。
7、发现异常情况及报警信号,应立即停止机床,请有关人员检查。
8、工作结束后,应关闭电源,清除切屑,擦拭保养机床,加油润滑,
清洁和整理,打扫工作场地。
深孔钻工艺规范和自检标准

深孔钻工艺规范和自检标准
编
号
版本\修改号
页
码
发布日期
ቤተ መጻሕፍቲ ባይዱ
A/0 第1页共1页 2008 年 7 月 1 日
为了规范深孔钻加工,减少加工出错率,提高深孔钻加工的有效 利用。特要求操机人员加强自检,制定以下工艺规范和自检标准: 1、 要求模具组在工件到达放置区时随带深孔钻工序图。工序图上要有工
艺章。 2、 操机人员跟模具组一起分析工序图,彻底弄清楚需加工尺寸的位置、
大小,明白设计基准与加工基准的关联性。 3、 按工序图要求合理选取加工面,合理选取基准面、导柱或导套孔等分
中。 4、 按图选取对应的钻头,钻顶杆孔的一定要与钻水路的分开放置使用。 5、 调整钻头固定套与加工面的垂直度;如果加工面在可加工的斜度范围
内,必须做好钻头固定套的密封,避免因漏油导致钻头磨损、烧伤等。 6、 工件校调完成后,开始加工; 7、 孔径检测,合理选取加工参数,加工顶孔深约 30mm 时退出钻头,去
钻孔作业管理制度

钻孔作业管理制度一、总则为做好钻孔作业管理工作,保障工程质量和工人安全,制定本规定。
二、适用范围本制度适用于公司内所有钻孔作业。
三、主管部门公司生产部门负责对钻孔作业进行管理,指导并审核钻孔作业的执行情况。
四、作业人员1. 所有参与钻孔作业的人员必须经过专业培训,并具备相关证书。
2. 所有作业人员必须严格遵守工作制度,不得违反相关操作规定。
3. 作业人员必须经常检查和维护自己的工作工具,确保工具的完好无损。
五、设备管理1. 所有钻孔设备必须定期进行检查,确保设备正常运转。
2. 设备使用人员必须经过专业培训,并持有相应的操作证书。
3. 设备管理人员负责设备的定期保养和维护,及时发现并处理设备故障。
六、安全管理1. 所有参与钻孔作业的人员必须具备相关安全知识,严格遵守安全操作规程。
2. 钻孔作业现场必须设置警示牌和防护设施,确保现场安全。
3. 作业人员必须定期进行安全培训,并及时了解最新的安全规定。
七、施工计划1. 钻孔作业必须根据施工计划进行,确保工程进度和质量。
2. 施工计划必须经过相关部门审核,并明确责任人和监督人。
3. 施工过程中出现问题必须立即报告上级领导,及时进行整改。
八、质量管理1. 钻孔作业必须符合相关标准和要求,确保施工质量。
2. 作业人员必须严格按照施工规范进行操作,保证施工质量。
3. 施工过程中出现质量问题必须立即停工进行整改,并及时报告。
九、环境保护1. 钻孔作业必须遵守相关环保法规,不得产生污染。
2. 施工现场必须设置污水和废渣处理设施,保证环境卫生。
3. 施工过程中出现环境问题必须立即处理,并及时报告。
十、管理制度1. 本制度由公司生产部门负责解释和执行,必须严格执行。
2. 钻孔作业管理制度必须定期进行评估和审查,及时进行修订。
3. 对于违反本制度的人员和行为,必须进行严肃处理。
以上便是关于钻孔作业管理制度的详细规定,希望每一位从事钻孔作业的人员都能严格遵守,确保施工质量和工程安全。
深孔钻操作规程

深孔钻操作规程深孔钻是一种精密加工工艺,用于加工长孔或深孔。
在进行深孔钻加工时,必须严格遵守操作规程,以确保加工质量和安全性。
本文将介绍深孔钻操作规程的相关内容。
一、设备准备1. 确认深孔钻设备是否处于正常工作状态,并及时进行维护保养。
2. 对所需的深孔钻刀具、润滑液、冷却液、夹具等进行充分准备。
3. 对原材料进行严格的检查,确保其符合要求并没有缺陷。
4. 对加工件进行检查,确认其尺寸和表面粗糙度符合要求。
二、工艺流程1. 根据加工要求选择或设计加工方案,并制定加工工艺流程。
2. 根据深孔钻设备的特点和加工件的要求,选择合适的刀具,并进行安装和调试。
3. 根据加工深度和直径,确定初始切削速度和进给速度,并逐步调整。
4. 启动深孔钻设备,并调整冷却液和润滑液的流量和温度,确保加工过程中不会因摩擦和热量产生变形或断裂。
5. 对加工过程进行监测和控制,确保其满足工艺要求。
6. 完成加工任务后,关闭深孔钻设备并进行清洗和维护保养,以便下一次使用。
三、安全防护1. 在深孔钻加工过程中,操作人员必须戴上防护手套和安全眼镜等防护装备。
2. 在加工过程中,严禁将手伸入刀具或工作件旁边的夹具中。
3. 在进行刀具更换和加工件夹紧时,要确保设备已经完全停止,并将控制器切换到手动模式。
4. 当深孔钻刀具出现故障或异常时,要立即停止加工,并进行维护保养。
5. 在进行深孔钻加工过程中,要时刻注意冷却液和润滑液是否正常供应,并及时加注。
四、质量检查1. 在进行深孔钻加工过程中,要时刻检查加工件的直径和深度,以确保其符合要求。
2. 对加工出的孔进行外观质量检查,如表面粗糙度和直线度等,以确保加工质量。
3. 对加工过程中的数据进行记录和分析,以便进行工艺改进和优化。
总之,深孔钻操作规程是保证加工质量和安全性的关键。
只有严格遵守操作规程,才能使深孔钻加工达到最佳效果。
同时,密切关注每一个细节和过程,可以使深孔钻加工技术水平不断提高,达到更高的精度和效率。
- 1、下载文档前请自行甄别文档内容的完整性,平台不提供额外的编辑、内容补充、找答案等附加服务。
- 2、"仅部分预览"的文档,不可在线预览部分如存在完整性等问题,可反馈申请退款(可完整预览的文档不适用该条件!)。
- 3、如文档侵犯您的权益,请联系客服反馈,我们会尽快为您处理(人工客服工作时间:9:00-18:30)。
8.3.1加工时除特殊情况外均需充分浇注切削液。
8.3.2钻螺纹底孔时需严格按照《螺纹底孔标准查询表》选用钻头及确定加工深度。
8.3.3大的钻头过小孔时先用小钻头分次扩到位。
8.3.4无论孔径大小,找好中心后必须锁紧摇臂。
9、运水加工作业规范
9.1流程图
9.2运水加工作业标准
8.2.2工件放置在工作台时须根据钻床大小及工件大小评估是否需要锁紧,工件太大直接放置在地面上时要用水平仪找平。
8.2.3根据图纸选用合适钻头,确保刀刃锋利,角度合理,无崩坏,根据材料及所加工孔的实际情况修磨钻头。
8.2.4根据图纸用卷尺卡尺测量NC点孔,确认加工位置,如未打点,则用高度尺划线后用样冲打点,打点时先用较小力敲一下,移开看是否在十字线中间OK则将样冲尖对准刚打的小点敲到位,有偏差则调整后重敲,不可一次敲到位。
9.2.4中间有穿孔时须将进给量降至6-8mm/min至刀头全部进入另一侧方可提速。如果需要穿过导柱,斜水井等大孔导致刀具全长距离无支撑时必须用材料将需要穿过的孔补起来后方可加工。
9.2.5加工斜度过大的孔时需要紧配斜度刀套或用铁、铝等做材料补齐,不可使用木头,如无法补齐需铣导向孔。加工水井时一般侧面运水已加工,退刀时极易卡刀,必须仔细观察。对照图纸仔细检查X,Y,Z座标值,基础进给转数参照参数表。
8.2.5加工时先用中心钻加工5MM以上再换钻头加工,孔很大时须分次钻出,逐步扩大钻头,钻头找好中心后须锁紧摇臂,将钻尖碰到工件表面时松开刻度盘,设定好深度。并用记号笔做标记,孔较深时同时在钻头上做好标记,以免发生钻深。
8.2.6每做完一种孔径就对照图纸检查一遍有没有钻错位置,漏钻,确认好后再换钻头做下一孔径,全部做完后要再一次对照图纸确认有无漏,错加工,深度用圈尺测量即可。
6.2.2对照图纸确认使用的丝锥规格,类型,如PT,G,或NPT,做头攻丝锥可以是崩坏后磨过的,最终加工的丝锥必须是无磨损,崩坏,烂牙。将丝锥对准底孔,将主轴打反转施加一定压力后锁紧摇壁。
6.2.3丝锥顶上工件表面后松开刻度盘,依图纸标识设定深度,没有标识的以螺纹大径2倍设定深度,M30以上以1.7倍设定深度。对于管牙,图纸有标识深度的以深度设定,没有标识的以丝锥的3/4处为攻牙深度。
10.2.6检验孔径大小和深度是否符合要求,孔径可用卡尺.深度可使用卷尺。
10.3热嘴避空加工作业注意事项
10.3.1如没有刚好的刀具可选用略大于,但不可以小。
10.3.2使用暴力钻如出现意外损坏刀具则该孔必须先将底铣平再加工。
10.3.3正面加工放电排油孔,不可使钻头或铁屑损伤唧嘴孔壁。
10.3.4暴力钻加工不可有斜面或大于中心钻的中心孔。
7.2.2确认刀具锋利无破损,磨损,刀杆不弯曲,刀头长度在25mm以上。
7.2.3先在工件的导柱等其他不发生干涉的位置加工100mm,同时确定好进给,转数等参数(按标准进给的80%)。
7.2.4对加工的试刀孔进行位置和孔径精度检测,如OK则正式加工,NG则进行调整,重新碰数(位置不准)或更换刀具(孔径超差)后重复上一步(孔径用标准件检测滑配)。
7.3.2加工避空时可单边放大1mm。
7.3.3刀套必须紧配,绝不可使用加长套,击入面不可是斜面或弧面。
7.3.4加工避空时堵孔不可使用螺丝等坚硬材料,以免损坏孔壁。
8、钻孔加工作业规范
8.1流程图
8.2钻孔加工作业标准
8.2.1彻底清理工作台面用抹布擦净,保证无铁屑杂物,用锉刀修好工件边缘毛刺并擦干净。
5.2.5校表时应使用铜棒或铝棒,不可使用铁棒等坚硬材料敲打工件,校表时先校正"Y"方向,在校"X"方向,校"Y"方向时可不松开行车。
5.2.6夹紧时需对称夹紧,即两边同时拧紧,不可先拧一边再拧另一边。夹紧后再用表确认工件有没有移动。
5.3装夹作业需注意事项
5.3.1清理要特别仔细,确保放置面无凸起不平,否则不易对正夹紧。
6.3螺纹加工作业注意事项:
6.3.1攻牙除铸铁外必须用丝攻油,不可用机油,切削油等代替。
6.3.2如发现有轻微烂牙,可用手工拿一个新的丝攻重新过一下,绝不可使用机攻(仅限管牙)。
6.3.3每攻一外牙须将丝攻清干净再加工下一个。
7、顶针加工作业规范
7.1流程图
7.2顶针加工作业标准
7.2.1加工顶针孔前先用表测试机床精度,保证在按比例计算低于0.02/100mm(机头精度)。
11、其他要求:
11.1上班必须穿工衣、劳保鞋,戴厂牌;开行车必须要戴安全帽;
11.2不得迟到或早退,所有请假的必须要当事人到现场请假,方可生效,否则按旷工处理;
11.3班组长或主管于巡视时确认点检保养被执行并签名于“点检表”的查核栏。
12、相关文件:
12.1《螺纹底孔标准查询表》(SOP-MD10)
13、相关记录:
13.1[深孔钻加工记录表](QR-139-02)13.2[钻床加工记录表](QR-139-03)
13.3[设备点检保养记录表](QR-033)
核准: 审核: 制订:日期:
5.2.2用锉刀修理干净工件上的毛刺和边角不平变形处,毛刺很大的状况需用打磨机粗修后用锉刀精修,需用手确认无刮手现象。
5.2.3工件上机时先确定摆放面,吊装时要平稳,放下时尽量避免冲击床面,摆放时目测尽量和工作台平行。
5.2.4上压板时注意压紧位置,压紧点应靠近垫块并位于垫块所构成的支撑平面内,压板数量要满足锁紧要求,且不可使工件变形(支撑块高度要略高于工件,螺杆尽量靠近工件)。
9.2.6对照图纸仔细检查X,Y,Z座标值,进给转数参照参数表。
9.3运水加工作业注意事项
9.3.1加工对接孔时要观察接通程度。
9.3心即可。
9.3.3如不慎断刀必须马上敲出,并清理相接孔。
9.3.4不可忘记水路孔沉台。
9.3.5当加工孔在工件和所补材料上各占一半时垫材硬度要接近工件硬度,绝不可使用木头。
10、热嘴避空加工作业规范
10.1流程图
10.2热嘴避空加工作业标准
10.2.1对照图纸或3D仔细确认热嘴避的孔径和深度。
10.2.2根据孔大小选用合适的刀具(大小,长度)使用暴力钻时刀片要无破损,中心钻无大的磨损,无法加工到位时先开粗后用钻床扩孔,开粗刀具尽可能选大.孔不是整数时,可选用接近规格的刀具,如48可选用50和刀具。但不可差别过大,差距大时要向上级询问确认。
5.3.2吊装时注意安全,大型工件必须使用4根铁链,两人配合时要呼应一致,方可避免造成人员伤害。
5.3.3需使用符合公司标准的垫块、螺杆,不可随便替代。
6、螺纹攻牙加工作业规范
6.1流程图
6.2螺纹加工作业标准
6.2.1用卡尺测量底孔大小是否符合标准,《螺纹底孔标准查询表》(HYS-SOP-MD10)位置是否正确,深度是否足够,(位置和深度可用卷尺确认)底孔深度M24以下为2.5倍大径深度,M30以上为2倍大径深度。
9.2.1对照图纸或3D,确认要加工孔径大小及深度。选用符合要求的刀具(直径、长度)刀具不可有崩坏,严重磨损,刀杆不可有较大弯曲,刀头不可短于5mm。
9.2.2对照图纸编写程式或使用电脑编写,5条以上必须使用自动编程,手工编程时要仔细确认X.Y.Z深度。
9.2.3先用较低速度加工5mm后再提升到正常速度,调整进给时优先加大进给量,再加切削速度,发现铁屑变色时说明以至极限,适当向下调。
7.2.5加工时仔细核对图纸的孔径,位置,深度,调用程式的须要细心核对程式号,并核对每个孔的座标值,随时注意切削情况,有振动及异响时要停机检查刀具,并每做5个孔就要用标准件测试孔径。
7.2.6加工完成后用标准件逐孔检测是否达到要求。
7.3顶针加工作业注意事项
7.3.1击穿面不可是斜面,弧面,如有此种应及时向上级汇报并确定加工工艺。
4.2交接班后需重新检查机器加工状态,若有异常需及时调整,若调整有困难及时报告班组长或主管进行处理。
4.3白班接好班后要检查机器的各项功能是否正常并如实填写[设备点检保养记录表](QR-033),要将每天、每周、每月的点检情况落实到位;月初第一天将上月填写完整的“点检表”交组长或主管审核,并取回本月需使用的“点检表”及时进行点检和记录。
4.4每台机的状态指示牌必须要以机台的实际情况调拨到指定的位置。机台的状态需与指示牌一致。
4.5按要求填写对应机台的加工报表[深孔钻加工记录表](QR-139-02)和 [钻床加工记录表](QR-139-03)。
5、工作装夹作业规范
5.1流程图
5.2装夹作业标准
5.2.1清理工作台上的铁屑及其他杂物,用碎布擦干净,有毛刺的用锉刀和油石修理,放垫块位置需用手确认无刮手现象。垫块摆放要合理,尽量在四周边角和长向中间,且均超出工件10-20mm。
1、目的:使深孔钻操作规范化、标准化、提高加工效率,保证工件品质,人员和设备的安全,降低成本。
2、范围:深孔钻操作加工均属之
3、职责:
3.1深孔钻班组长或主管:按本规范要求教导、督导、查核操作员作业过程和结果;
3.2深孔钻操作员:按此规范进行加工操作及自检。
4、操作员作业要求:
4.1接班时要检查设备及周围区域5S符合要求,若不合格,则由交班者打扫干净方可下班。。
10.2.3根据图纸手工编程或使用电脑编写,编写时注意位置和深度,深度加工到圆锥开始处。
10.2.4加工时先用较低速度进给至10mm深,再用正常速度进给至深度,过程中注意观察,核对X.Y.Z。如开粗后使用钻床扩孔需在钻头上用色笔涂好标记,并在刻度盘相应刻度做好标记,以防钻深。
10.2.5加工放电排油孔时必须从正面NC加工过的唧嘴孔内用至少小于唧嘴孔5mm的钻头加工穿,对好中心后必须锁紧摇臂.不可从背面加工。
6.2.4攻牙时需先锁紧摇臂,在攻入前三个牙时适当施加压力,否则易造成牙口部被拉坏,攻牙时每攻数牙就反转断屑,,不可一攻到底,对大的牙需用1.2.3.攻依次攻出,不可直接用3攻攻牙,以免成牙和丝锥损坏,二次攻牙时必先用手将丝锥转入数圈后方可使用机攻,以免造成重牙。