涡轮减速器箱体加工工艺
涡轮减速器箱体加工工艺

涡轮减速器箱体加⼯⼯艺⽬录第⼀节零件图分析...........................................................................‥ (1)1.涡轮减速器箱体功⽤和特点 (1)2.涡轮减速器箱体的技术要求 (1)第⼆节确定⽑坯 (3)1.涡轮减速器箱体⽑坯分析 (4)2.涡轮减速器箱体结构确定并画出⽑坯图 (4)第三节定位基准选择………………………………………………………………………‥41.精基准的选择 (5)2.粗基准的选择 (5)第四节拟定⼯艺路线 (6)1.表⾯加⼯⽅法的确定 (6)2.加⼯阶段的划分 (6)3.⼯序的集中与分散 (6)4.⼯序顺序的安排 (6)5.确定⼯艺路线 (6)第五节确定加⼯余量、计算⼯序尺⼨ (7)第六节选择机床与⼯艺装备 (8)1.机床设备的选⽤ (8)2.⼯艺装备的选⽤ (12)第七节切削⽤量与时间定额 (13)1.切削⽤量计算 (13)2.时间定额的计算 (14)第⼋节编写⼯艺⽂件 (14)⼩型涡轮减速器箱体加⼯⼯艺编制任务:完成⼩型涡轮减速器箱体机械加⼯⼯艺规程的制订(中⼩批量)。
涡轮减速器箱体设计图纸如图2-48所⽰。
第⼀节零件图分析⼀、涡轮减速器箱体的功⽤和特点:箱体类零件是机器及其部件的基础件之⼀。
它将⼀些轴、轴承、套、齿轮等零件装配在⼀起,使其保持正确的相互位置关系,并按规定的运动关系协调动作,完成某种远动。
因此,箱体类零件的加⼯质量对机器的精度、性能和寿命有着直接关系。
涡轮减速器箱体的功⽤如上述所⽰,其特点有许多精度要求不同的孔和平⾯组成,内部结构⽐较简单但壁的厚薄不均匀,加⼯的难度较⼤。
⼆、涡轮减速器箱体的技术要求:涡轮减速器箱体的主要技术有:1. 两对轴承孔的尺⼨精度为IT7,表⾯粗糙度Ra值为1.6um,⼀对Ф90的轴承孔和⼀对Ф180的轴承孔同轴度公差分别为0.05mm、0.06mm,其中两对轴承孔轴线的垂直度公差为0.06mm;2.铸件不得有砂眼、疏松等铸造缺陷;3.⾮加⼯表⾯涂防锈漆;4.铸件进⾏⼈⼯时效处理;5.箱体做煤油渗漏实验;6.材料HT200。
涡轮减速箱体加工工艺规程及工艺装备的设计
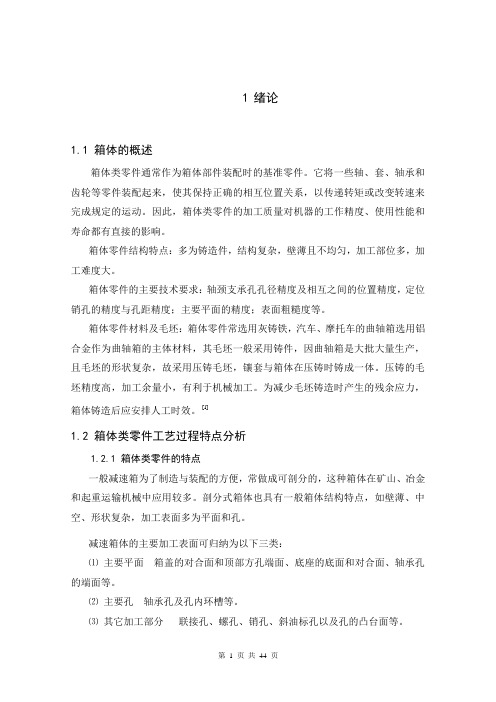
1绪论1.1 箱体的概述箱体类零件通常作为箱体部件装配时的基准零件。
它将一些轴、套、轴承和齿轮等零件装配起来,使其保持正确的相互位置关系,以传递转矩或改变转速来完成规定的运动。
因此,箱体类零件的加工质量对机器的工作精度、使用性能和寿命都有直接的影响。
箱体零件结构特点:多为铸造件,结构复杂,壁薄且不均匀,加工部位多,加工难度大。
箱体零件的主要技术要求:轴颈支承孔孔径精度及相互之间的位置精度,定位销孔的精度与孔距精度;主要平面的精度;表面粗糙度等。
箱体零件材料及毛坯:箱体零件常选用灰铸铁,汽车、摩托车的曲轴箱选用铝合金作为曲轴箱的主体材料,其毛坯一般采用铸件,因曲轴箱是大批大量生产,且毛坯的形状复杂,故采用压铸毛坯,镶套与箱体在压铸时铸成一体。
压铸的毛坯精度高,加工余量小,有利于机械加工。
为减少毛坯铸造时产生的残余应力,箱体铸造后应安排人工时效。
]1[1.2 箱体类零件工艺过程特点分析1.2.1 箱体类零件的特点一般减速箱为了制造与装配的方便,常做成可剖分的,这种箱体在矿山、冶金和起重运输机械中应用较多。
剖分式箱体也具有一般箱体结构特点,如壁薄、中空、形状复杂,加工表面多为平面和孔。
减速箱体的主要加工表面可归纳为以下三类:⑴主要平面箱盖的对合面和顶部方孔端面、底座的底面和对合面、轴承孔的端面等。
⑵主要孔轴承孔及孔内环槽等。
⑶其它加工部分联接孔、螺孔、销孔、斜油标孔以及孔的凸台面等。
1.2.2 工艺过程设计应考虑的问题根据减速箱体可剖分的结构特点和各加工表面的要求,在编制工艺过程时应注意以下问题:⑴加工过程的划分整个加工过程可分为两大阶段,即先对箱盖和底座分别进行加工,然后再对装合好的整个箱体进行加工——合件加工。
为保证效率和精度的兼顾,就孔和面的加工还需粗精分开;⑵箱体加工工艺的安排安排箱体的加工工艺,应遵循先面后孔的工艺原则,对剖分式减速箱体还应遵循组装后镗孔的原则。
因为如果不先将箱体的对合面加工好,轴承孔就不能进行加工。
蜗轮蜗杆减速器箱体上盖结构设计、箱体加工工艺规程制定及工艺装备设计_毕业论文 精品

山东科技大学泰山科技学院毕业设计蜗轮蜗杆减速器箱体上盖结构设计、箱体加工工艺规程制定及工艺装备设计学校:山东科技大学泰山科技学院班级:机制(专本)11—3班指导老师:王叶青姓名:王萌萌日期:2013/6/12摘要本设计的课题是减速箱箱体的上盖结构设计、箱体加工工艺规程制定及工艺装备设计。
该箱体零件结构复杂,且为大批量生产,为了提高生产效率和降低劳动强度,专门设计了专用组合机床,专用夹具。
本设计说明书可分为四部分:第一部分为箱体的上盖结构设计。
在上盖结构设计中,考虑下箱体的结构,合理选择上箱体结构尺寸、箱体壁厚、透视孔大小等。
第二部分为箱体机械加工工艺规程的制定。
在制定工艺过程中,确定各工序的安装工位和该工序需要的工步,加工该工序的机床及机床的进给量,切削深度,主轴转速和切削速度,最后计算该工序的基本时间,辅助时间和工作地服务时间。
第三部分为组合机床设计——组合镗床。
更好的提高生产率,提高加工精度,降低生产成本。
第四部分为专用夹具设计。
专用夹具的使用能有效降低工作时劳动强度、提高劳动生产率、并获得较高的加工精度。
关键词:箱体工艺组合机床夹具AbstractThis design is the subject of gearbox top cover structure design, the processing technological process formulation and process equipment design. Replace parts of the complex structure, and mass production, in order to improve production efficiency and reduce labor intensity, specially designed for the special combined machine tool, fixture. The design specification can be divided into four parts:The first part set box cover structure design, In the upper cover structure design, consider the box structure, reasonable selection box structure size, thickness of the box wall, hole size perspective.The second part is technical regulations of the mechanical processing.In the development process, determine the installation position of each process and the process need the labor step, feed, machine tools and machining of the processes of the cutting depth, spindle speed, and cutting speed, the basic time finally calculated the procedures, work time and support to business hours.The third part is the combination of machine tool design -- combination boring lathe. Better to increase productivity, improve processing accuracy, reduce production cost.The four part is the design of special fixture. The use of special fixture can reduce the work labor intensity, improve labor productivity, and obtain high machining accuracy.Keywords: box technology modular machine tool fixture目录第1章概述 (1)1.1.箱体的主要功能 (1)1.2.箱体的分类 (1)1.3通用减速器的发展趋势 (2)第2章减速器箱体结构设计及要求 (3)2.1减速器结构概述 (3)2.2设计的主要问题和设计要求 (4)2.3箱体结构设计 (4)2.4 减速器箱体结构设计三维实体图形 (9)第3章减速器箱体加工工艺制定 (15)3.1.箱体的结构分析 (15)3.2.箱体的技术要求分析 (15)3.3.箱体毛坯的选用 (16)3.4.箱体的基准选择 (16)3.5.拟定箱体加工工艺路线 (16)第4章机械加工工序设计 (19)4.1 概述 (19)4.2 工序简图的绘制 (19)4.3 切削用量及基本工时的确定原则 (20)4.4 机体切削用量和基本工时的确定 (22)第5章组合机床概述 (28)第6章组合镗床夹具设计 (28)6.1 夹具设计基本过程 (28)6.2 夹具结构工艺性 (30)6.3 机床夹具的组成与作用 (31)6.4 工件的定位误差 (35)6.5 工件的定位方案 (35)6.6工件的夹紧 (37)6.7 夹紧装置的总体设计 (45)参考文献 (47)技术经济分析 (48)结论 (49)致谢 (51)外文文献 (51)山东科技大学泰山科技学院学士学位论文第1章概述1.1.箱体的主要功能(1)支承并包容各种传动零件,如齿轮、轴、轴承等,使他们能够保持正常的运动关系和运动精度。
涡轮减速器箱体加工工艺及夹具设计

涡轮减速器箱体加工工艺及夹具设计涡轮减速器是一种广泛应用于机械传动系统中的关键零部件,它通过几个齿轮的转动来实现输入轴和输出轴的转速的比例变换。
其箱体是涡轮减速器的主要组成部分之一,通过对箱体进行加工工艺的合理设计和夹具的设定,可以保证涡轮减速器箱体的加工质量和生产效率。
下面将对涡轮减速器箱体的加工工艺和夹具设计进行详细介绍。
在箱体加工过程中,需要设计合理的夹具来保证箱体的加工精度和稳定性。
夹具设计需要遵循以下原则:夹紧力要均匀,夹具刚度要足够,易于操作和调整,可以保证加工的精度和效率。
在设计夹具时,可以考虑采用多夹点夹具和活动式夹具。
多夹点夹具可以均匀分布夹紧力,减小加工过程中的变形和误差。
活动式夹具可以适应不同型号和规格的箱体加工,提高生产效率和灵活性。
另外,在夹具设计中还需要考虑加工余量和合理的夹紧方式。
加工余量是为了保证加工后的箱体尺寸和形状满足设计要求。
夹紧方式可以采用机械夹紧、液压夹紧或气动夹紧等方式,根据具体的加工要求选择合适的夹紧方式。
在进行实际加工操作时,还需要注意刀具的选择和切削参数的设定。
刀具的选择要考虑切削材料的硬度和加工表面的质量要求。
切削参数的设定要根据具体的加工要求和切削材料的特性来确定。
涡轮减速器箱体加工工艺及夹具设计
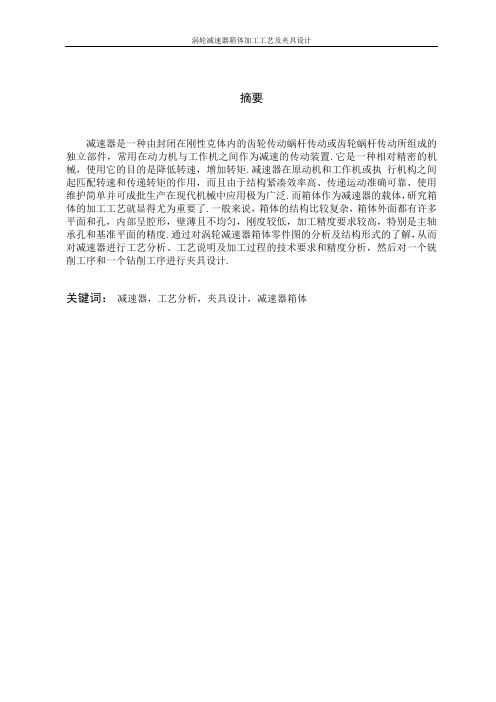
摘要减速器是一种由封闭在刚性克体内的齿轮传动蜗杆传动或齿轮蜗杆传动所组成的独立部件,常用在动力机与工作机之间作为减速的传动装置.它是一种相对精密的机械,使用它的目的是降低转速,增加转矩.减速器在原动机和工作机或执行机构之间起匹配转速和传递转矩的作用,而且由于结构紧凑效率高、传递运动准确可靠、使用维护简单并可成批生产在现代机械中应用极为广泛.而箱体作为减速器的载体,研究箱体的加工工艺就显得尤为重要了.一般来说,箱体的结构比较复杂,箱体外面都有许多平面和孔,内部呈腔形,壁薄且不均匀,刚度较低,加工精度要求较高,特别是主轴承孔和基准平面的精度.通过对涡轮减速器箱体零件图的分析及结构形式的了解,从而对减速器进行工艺分析、工艺说明及加工过程的技术要求和精度分析,然后对一个铣削工序和一个钻削工序进行夹具设计.关键词:减速器,工艺分析,夹具设计,减速器箱体AbstractSpeed reducer is enclosed by a rigid body in the gear transmission, worm drive or gear worm transmission of independent components, commonly used in power and work machine as the slowdown between transmission device it is a relatively sophisticated machinery, the use of its purpose is to reduce speed and increase torque reducer prime mover and work in machine or holding the line between institutions and the transfer speed matching up the role of torque, and because the compact structure efficiency high transfer movement accurate and reliable use simple maintenance and batch production in the modern machinery are widely as the carrier of speed reducer and cabinet, the processing technology of the cabinet is particularly important in general, the structure of the case is complex, outside the there are many plane and hole, in internal cavity shape, the wall is thin and uneven, stiffness is low, processing higher accuracy. Especially the main bearing hole and benchmark the precision of the plane through the turbine speed reducer drawing analysis and understanding of the structure form, and on the analysis of the technology process description on gear reducer and machining process of technical requirements and accuracy analysis, and then on to a milling process and a drilling process for fixture design.Key words: Gear reducer , Processing technology , Tongs,Gearcase目录摘要 (I)Abstract (II)1 绪论 (1)2 零件工艺的分析 (1)2.1 确定毛坯的制造形式 (1)2.2 箱体零件的结构工艺性 (1)2.3主要平面 (2)3 拟定箱体加工的工艺路线 (2)3.1加工方法的选择 (2)3.2加工阶段的划分 (3)3.3工序的集中与分散 (3)3.4加工顺序的安排 (4)3.5具体工序尺寸和加工余量的确定 (6)3.6机床与相应切削用量的确定 (6)4 基准的选择 (9)4.1定位基准的选择 (9)4.1.1粗基准的选择 (9)4.1.2精基准的选择 (9)5 夹具的设计 (10)5.1设计铣蜗杆端盖的小端面夹具 (10)5.1.1问题的指出 (10)5.1.2夹具设计 (10)5.2钻床夹具设计 (12)5.2.1 定位方案 (12)5.2.2选择加紧机构 (12)5.2.3选择导向装置 (13)6 结论与展望 (14)参考文献 (15)1 绪论箱体零件是机器或部件的基础零件,它把有关零件联结成一个整体,使这些零件保持正确的相对位置,彼此能协调地工作。
学习情境七 涡轮减速箱箱体孔加工工艺

7.3 相关知识 ②以装配基面作精基准。通常采用大轴 承孔及端面作为精基准来加工孔系及其端面, 这里的大轴承孔及其端面就是装配基面。此 法符合基准重合原则,减少定位误差。它可 消除5个自由度,从而减少辅助时间。
40
7.3 相关知识
4、粗基准选择
通常以箱体的重要孔(如轴承孔)作粗基准,这 样可以保证箱体上重要孔加工余量均匀,对提高孔 的加工质量、耐磨性等有重要意义.
8
7.3 相关知识
4)对于同轴孔系,若相距较近,用穿镗法加工, 若跨距较大,应尽量采用调头镗的方法加工, 以缩短刀具的伸长,减小其长径比,提高加 工质量。
5) 对于螺纹孔,要根据其孔径的大小选择不同 的加工方式。直径在M6~M20之间的螺纹孔, 一般在加工中心上用攻螺纹的方法加工;直 径在M6以下的螺纹,则只在加工中心上加工 出底孔,然后通过其他手段攻螺纹;直径在 M20以上的螺纹,一般采用镗刀镗削而成。
12
7.3 相关知识 (3)扩孔钻 用来扩大已加工孔径、加工
质量及生产率比麻花钻高,有整体式、 镶齿套式和镶硬质合金套式等结构不同 的扩孔钻。
13
7.3 相关知识 (4)锪孔钻 也称锪钻主要用来加工沉头
孔,一般有圆柱头沉头锪孔钻、锥形沉 头锪孔钻和端面、凸台锪孔钻等。
14
7.3 相关知识 (5)深孔钻 长径比大于10的钻头统称深
学习情境七:蜗轮减速器箱体孔加工工艺
主要内容
通过 蜗轮减速器箱体零件的孔加工工 艺编制介绍了数控孔加工常用刀具及其加工 应用场合;箱体加工常见方法;箱体加工工 艺特点等。
通过该情境的学习,能对箱体零件选 择加工基准;选择合理的加工顺序。掌握典 型箱体零件的工艺编制方法
1
学习情境七:蜗轮减速器箱体孔加工工艺
机械加工工艺项目操作项目7 蜗轮减速器箱体孔的加工工艺

下一页 返回
7.3 相关 知 识
• 1.麻花钻 • 麻花钻(图7-2)是应用最多的孔加工刀具,可用来在实心材料上钻
• 但是,单刃微调镗刀正被多刃扩(锪)孔刀、铰刀及复合(组合)孔 加工专用数控刀具替代。国外研制出采用工具系统内部推拉杆轴向运 动或高速离心力带平衡滑动块移动,一次走刀完成镗削球面(曲面) 、斜面及反向走刀切削加工零件背面的数控智能精密镗刀,代表了镗 刀发展的方向。
上一页 下一页 返回
7.3 相关 知 识
项目7 蜗轮减速器箱体孔的加工工艺
• 7.1 项目引入 • 7.2 项目分析 • 7.3 相关知识 • 7.4 项目实施
返回
7.1 项目引入
• 生产图 7-1 所示零件,材料为HT200,生产纲领为制造3000 件。现 为该零件制订机械加工工艺规程。
• 项目说明 • (1)为箱体零件选择加工基准。 • (2)选择合理的加工顺序。 • (3)为该加工零件制订详细的加工工艺。 • 知识点、技能点 • (1)数控孔加工常用刀具及其加工应用场合。 • (2)箱体加工常见方法。 • (3)箱体加工工艺特点。 • (4)掌握典型箱体零件的工艺编制方法。
上一页 下一页 返回
7.3 相关 知 识
• 2.中心钻 • 中心钻用来加工轴类零件的中心孔,可分为无护锥中心钻和有护锥中
心钻,使用时应根据工件的直径来选择大小。 • 3.扩孔钻 • 扩孔钻用来扩大已加工孔径,加工质量及生产率比麻花钻高,有整体
蜗轮减速机箱体加工工艺技术

蜗轮减速机箱体加工工艺技术蜗轮减速机箱体是一种用于传递动力的关键零部件,常用于工业生产中的传动系统。
其加工工艺技术对于机箱体的质量和性能至关重要。
下面将介绍一种常见的蜗轮减速机箱体加工工艺技术。
首先,机箱体的加工工艺技术开始于设计和制作加工工艺图纸。
工艺图纸需要包括机箱体的尺寸、形状、方位等详细信息,并标注加工工艺要求和检验要求。
在这个过程中,需要考虑到机箱体的功能要求、外观要求以及使用环境等因素。
接下来是材料准备。
根据机箱体的要求,选择适合的材料来制作机箱体。
常见的材料有铸铁、铝合金等。
在材料准备过程中,需要检查材料的质量和尺寸是否符合要求。
然后是机箱体的铸造或切削。
对于铸铁机箱体,可以通过铸造工艺来制造。
首先,将铸铁熔化成液态,然后倒入机箱体的模具中,待铸件冷却凝固后,取出并进行下一步的加工处理。
对于铝合金机箱体,通常通过CNC数控机床进行切削加工。
根据加工工艺图纸,将预先加工好的铝合金材料通过切削加工,在机床上进行整体切削,形成所需的机箱体形状和尺寸。
在加工过程中,需要严格控制加工尺寸、表面光洁度和精度。
对于铸造机箱体,需要进行修砂、抛光等表面处理,以保证机箱体的表面光滑,无明显缺陷。
对于切削加工机箱体,需要经过精密加工,确保机箱体的尺寸和形状精确。
最后,进行机箱体的装配和调试。
根据设计要求和加工工艺要求,将机箱体的各个零部件进行装配,并进行测试和调试。
通过测试和调试,在保证机箱体质量和性能的前提下,确保机箱体的可靠性和耐用性。
总体而言,蜗轮减速机箱体的加工工艺技术涉及到工艺图纸设计、材料准备、铸造或切削加工、表面处理以及装配和调试等多个环节。
通过严格控制每个环节的工艺要求,可以保证蜗轮减速机箱体的质量和性能,满足工业生产中的传动需求。
蜗轮减速机箱体加工工艺技术是制造蜗轮减速机的关键环节,它直接关系到蜗轮减速机的质量和性能。
下面将继续介绍蜗轮减速机箱体加工工艺技术的相关内容。
在加工工艺技术中,首先需要进行模具制造。
小型蜗轮减速器箱体加工工艺和Φ180mm孔精加工夹具设计
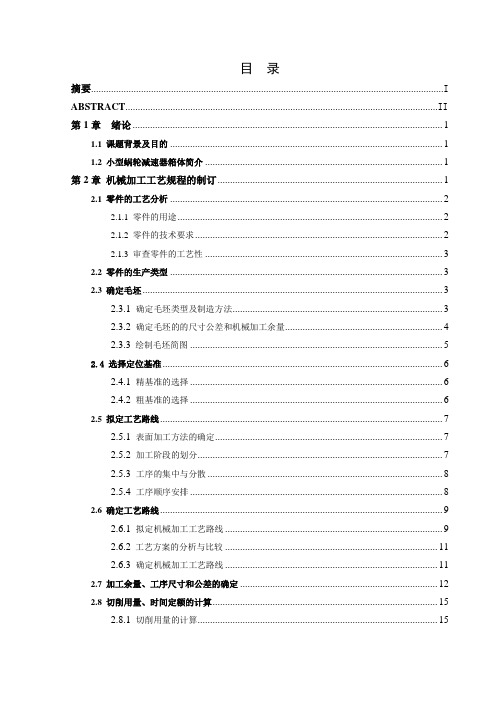
目录摘要 (I)ABSTRACT (II)第1章绪论 (1)1.1 课题背景及目的 (1)1.2 小型蜗轮减速器箱体简介 (1)第2章机械加工工艺规程的制订 (1)2.1 零件的工艺分析 (2)2.1.1 零件的用途 (2)2.1.2 零件的技术要求 (2)2.1.3 审查零件的工艺性 (3)2.2 零件的生产类型 (3)2.3 确定毛坯 (3)2.3.1 确定毛坯类型及制造方法 (3)2.3.2确定毛坯的的尺寸公差和机械加工余量 (4)2.3.3绘制毛坯简图 (5)2.4 选择定位基准 (6)2.4.1 精基准的选择 (6)2.4.2 粗基准的选择 (6)2.5 拟定工艺路线 (7)2.5.1 表面加工方法的确定 (7)2.5.2 加工阶段的划分 (7)2.5.3 工序的集中与分散 (8)2.5.4 工序顺序安排 (8)2.6 确定工艺路线 (9)2.6.1 拟定机械加工工艺路线 (9)2.6.2工艺方案的分析与比较 (11)2.6.3 确定机械加工工艺路线 (11)2.7 加工余量、工序尺寸和公差的确定 (12)2.8 切削用量、时间定额的计算 (15)2.8.1 切削用量的计算 (15)2.8.2 时间定额的计算 (20)第3章机床夹具设计 (26)3.1 机床夹具概述 (26)3.2 定位方案设计 (27)3.2.1 定位方案的确定 (27)3.2.2 定位元件的选择 (29)3.2.3 定位误差分析 (30)3.3 夹紧装置设计 (31)3.3.1 夹紧方案的确定 (31)3.3.2 夹紧力的计算 (32)3.4 夹具体结构 (33)第4章总结 (35)参考文献 (37)致谢 (38)第1章绪论1.1课题背景及目的目前,随着我国经济的高速增长,尤其是现代工业的快速发展,各种传动机构越来越受到人们的青睐,其中蜗轮蜗杆传动以其独特的特点在机械中广泛运用,其主要优点有:可以得到很大的传动比,比交错轴斜齿轮机构紧凑;两轮啮合齿面间为线接触,其承载能力大大高于交错轴斜齿轮机构;蜗杆传动相当于螺旋传动,为多齿啮合传动,故传动平稳、噪音很小;具有自锁性。
涡轮减速箱体加工工艺规程

涡轮减速箱体加工工艺规程涡轮减速箱是一种常见的传动装置,其特点是结构紧凑,承载能力高,并可以提供大扭矩输出。
为了保证涡轮减速箱在运行过程中的稳定性和性能,对其加工工艺进行规范和控制显得尤为重要。
以下是涡轮减速箱体加工工艺规程的一般要求。
1. 零件加工准备:在进行涡轮减速箱体的加工之前,应对材料进行检查,确保其质量符合要求。
同时,根据设计图纸和工艺要求,准备所需的刀具、量具和夹具等。
2. 零件加工工艺:涡轮减速箱体加工包括铣削、钻孔、车削等工艺。
根据设计要求,采用适当的刀具和切削参数,进行铣削、钻孔和车削等加工操作,并确保加工精度和表面质量的要求。
3. 检测与修正:在加工过程中,需要对加工后的零件进行检测,如尺寸测量、表面质量检查等,以确保零件的质量。
若发现质量不满足要求,应及时采取相应的修正措施,如重新加工、研磨等。
4. 零件组装与检验:涡轮减速箱体由多个零件组装而成,组装工艺需要按照装配图纸和技术要求进行。
在组装过程中,需严格控制各零件的间隙和配合尺寸,并进行必要的试装和检验,以确保组装后的涡轮减速箱体的密封性和运转性能符合要求。
5. 表面处理:涡轮减速箱体通常需要进行表面处理,如防腐、涂漆等。
在进行表面处理前,应对零件进行清洗和除锈处理,并根据要求进行涂装或防腐等工艺。
6. 检验与试验:在涡轮减速箱体的加工完成后,需要进行相关的检验和试验,如尺寸测量、动力性能测试等。
通过检验和试验,可以对涡轮减速箱体的质量进行评估,并发现可能存在的问题和缺陷。
7. 包装与出库:经过检验和试验合格的涡轮减速箱体,应进行适当的包装,以防止在运输和储存过程中受到损坏。
同时,应制作好相应的包装清单和标识,并及时将其出库。
以上是涡轮减速箱体加工工艺规程的一般要求,通过合理控制加工工艺,确保零件的加工精度和质量,可以提高涡轮减速箱体的性能和可靠性,满足用户的需求。
添加以下内容以满足1500字要求:8. 工艺文件管理:对于涡轮减速箱体的加工工艺,应建立相应的工艺文件管理系统。
蜗轮箱体机械加工工艺规程卡片

工程技术学院
机械加工工艺过程卡片
产品型号
零件图号
产品名称
涡轮箱体
零件名称
涡轮箱体
共
2
页
第
1
页
材料牌号
HT200
毛坯种类
铸件
毛坯外形尺寸
122×100×118
每毛坯件数
1
每台件数
1
备注
工
序
号
工名
序称
工序内容
车
间
工
段
设备
工艺装备
工时
准终
单件
1
铸造
利用金属模铸造,铸造出符合设计要求的毛坯。毛坯尺寸按照毛坯图上尺寸。
数控铣床
专用钻夹具
12
铣加工
以底面为基准,将零件翻转后精铣孔的另一面。
数控铣床
专用铣夹具
13
钻加工
以底面为基准,将零件翻转后用Φ4mm钻中心孔,分别用用Φ10.8mm的麻花钻Φ11.8mm的铰刀粗绞Φ12mm的铰刀精绞孔Φ12,Φ20mm的锪刀锪表面Φ20的孔
数控铣床
专用钻夹具
设计(日期)
校对(日期)
数控铣床
专用钻夹具
8
铣加工
以底面为基准,将零件翻转后孔的另一面精铣端面
数控铣床
专用铣夹具
9
钻加工
以底面为基准,将零件翻转后钻中心孔,用Φ14.8mm的麻花钻钻,然后粗绞至Φ15.8mm,再用Φ16mm的铰刀精绞孔的另一面
数控铣床
专用钻夹具
10
铣加工
以底面为基准,精铣端面
数控铣床
专用铣夹具
11
钻加工
以底面为基准,用Φ4mm钻中心孔,分别用用Φ10.8mm的麻花钻Φ11.8mm的铰刀粗绞Φ12mm的铰刀精绞孔Φ12,Φ20mm的锪刀锪表面Φ20的孔
高级车工工艺任务 蜗轮减速箱体
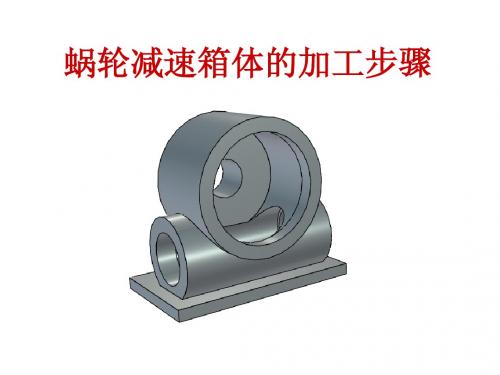
12
加 工 简 图 一
加 工 步 骤
1.用四爪单动卡盘夹住工件,车平底面至12mm
加 工 简 图 二
加 工 步 骤
2.在花盘角铁上以工件底平面为定位基准找正φ140mm大端面 中心十字线,装夹牢固
(1)车118mm的端面(兼顾48mm中心对称尺寸) +0..035 (2)车内孔φ112 0 mm、φ (42±0.014)mm、内沟槽φ115mm
加 工 简 图 六
170
加 工 步 骤
6.掉头车端面,控制尺寸170mm
加 工 步 骤
5.在角铁底面上固定φ42mm孔测量棒,用千分尺测量两个测量棒的中 心距,通过角铁在导向块上移动进行尺寸的测量,达到中心距(64± 0.05)mm,固定角铁,卸下主轴孔中的测量棒,将工件套在孔测量棒 +0.018 上,φ140mm大端面放在角铁平面上,找正工件φ54 −0.012 mm孔轴线与 卡盘平面垂直后,紧固工件 (1)车170mm处的端面 +0.018 (2)车内孔φ54 −0.012 mm及内沟槽φ61mm
加 工 简 图 三
118
加 工 步 骤
3.掉头装夹
车另一端面,控制尺寸 118mm
加 工 简 图 四
加 工 步 骤
4.在主轴孔内塞入测量棒
(1)用游标高度尺测量蜗杆孔轴线至角铁内侧底面高度48mm(是 118mm前端面与蜗杆孔轴线的距离) (2)调整角铁高度,调整后,固定角铁导向块
加 工 简 ቤተ መጻሕፍቲ ባይዱ 五
蜗轮箱加工工艺流程

6
镗削轴承孔
使用镗床对轴承孔进行镗削,确保孔的尺寸和精度符合要求。
7
钻底孔
使用钻床在指定位置钻出底孔。
8
螺纹攻漆
对需要攻丝的孔进行螺纹加工,并进行必要的油漆处理。
9
蜗轮粗加工
通过数控加工中心进行铣削,将蜗轮外形加工至基本形状。
10
蜗轮齿面加工
使用滚齿机对蜗轮齿面进行加工,获得符合要求的齿形和齿距。
蜗轮箱加工工艺流程
步骤序号
工艺流程
详细说明
1
铸造箱体
铸造蜗轮箱箱体,确保形状和尺寸符合设计要求。
2
清沙与人工时效处理
清除铸造过程中产生的沙粒和杂质,并进行人工时效处理,以消除内应力。
3
油漆
对箱体进行必要的油漆处理,以保护箱体表面并美化外观。
4Hale Waihona Puke 划线在箱体上划线,为后续的加工操作提供基准。
5
粗铣加工表面
11
蜗轮精细加工
对蜗轮进行研磨和抛光,以达到高精度、高光洁度的要求。
12
装配与调试
将加工好的零部件进行装配,并进行必要的调试,确保蜗轮箱的工作性能。
13
检验
使用专业检测设备对蜗轮箱进行全面检验,确保制造质量符合要求。
14
入库
将检验合格的蜗轮箱进行包装,并入库存储。
涡轮减速器箱体工艺毕业设计

本科生毕业设计学院、系:专业:学生姓名:班级:学号指导教师姓名:职称最终评定成绩院(系):专业:学号:学生姓名:指导教师:摘要涡轮减速器箱体类零件是机器及其部件的基础件,它将机器及其部件中的轴、轴承、套和齿轮等零件按一定的相互位置关系装配成一个整体,并按预定传动关系协调其运动。
因此,涡轮减速器箱体的加工质量不仅影响其装配精度及运动精度,而且影响到机器的工作精度、使用性能和寿命。
其主要特点:形状复杂、壁薄且不均匀,内部呈腔形,加工部位多,加工难度大,既有精度要求较高的孔系和平面,也有许多精度要求较低的紧固孔。
因此,一般中型机床制造厂用于涡轮减速器箱体类零件的机械加工劳动量约占整个产品加工量的15%~20%。
对工件进行机械加工时,为了保证加工要求,首先要使工件相对于机床有正确的位置,并使这个位置在加工过程中不因外力的影响而变动。
为此,在进行机械加工前,先要将工件装夹好。
用夹具装夹工件时,工件相对于道具及机床的位置精度由夹具保证,不受工人技术水平的影响,使一批工件的加工极度趋于一致,稳定的保证工件的加工精度。
同时使用夹具装夹工件方便、快捷,工件不需要划线找正,可显著的减少辅助工时,提高劳动生产率;工件在夹具中装夹后提高了工件的刚性,因此可加大切屑用量,提高劳动生产率;可使用多件、多工位装夹工件的夹具,并可采用高效夹紧机构,进一步提高劳动生产率。
在批量生产中使用夹具后,由于劳动生产率的提高、使用技术等级较低的工人以及废品率下降等原因,明显得降低了生产成本。
夹具制造成本分摊在一批工件上。
每个工件增加的成本时极少的,远远小于由于提高劳动生产率而降低的成本。
工件批量愈大,使用夹具所取得的经济效益就愈显著。
关键词:涡轮减速器箱体类零件,夹具,ABSTRACTA part of the container kind is the basic matter of a machine and a part. That will choose an axis in the machine and the part, a bearing and a part of a cover and a gear as related assembly in the fixed mutual location, and is 1 of whole. It's transmitted by a schedule, and it's related to the movement of harmonization. Therefore the quality of the processing of a container doesn't just influence its precision of the assembly and precision of the movement and moreover influences the precision of the mechanical work, and the performance and the lifetime are used. Its main feature: The shape is complicated, a wall, it's thin and, I don't balance and present the interior with the shape of the accent, and there are a lot of parts of processing, and though the difficulty level of the processing finds a plane with a department in the hole where it's big and highly precise in the percentage, and is low in the percentage likewise, there is precision of much I ask to tighten a hole up. Therefore a manufacturing factory in a medium turnery is usually used for Labor of mechanical processing of a part of the container kind, and it accounts for 15%~20% of the processing amount of the whole product approximately.Parts of mechanical processing, in order to ensure processing requirements, the first part of the machine to make a correct position, and this position in the course of processing is not due to the impact of external changes. To this end, during machining, must be the workpiece clamping good.Clamping fixture with the workpiece, the workpiece relative to the location of props and precision machine tools from the fixture that the technical level of workers from the impact of a number of parts of the extreme processing line, a stable guarantee the accuracy of processing the workpiece. At the same time the use of the workpiece clamping fixture convenient, fast, crossed the workpiece does not need to find is, can significantly reduce the supplementary working hours, improving labor productivity; Workpiece fixture in the fixture after the increase in the rigidity of the workpiece, it can increase the amount of chip, raising labor productivity; can use pieces, multi-fixture parts of the fixture, and efficient use of clamping institutions, to further improve labor productivity .In the use of mass production after the fixture, due to the improvement of labor productivity, the use of technology workers in lower grades and reject rate dropped andother reasons, obviously in the lower production costs. Fixture manufacturing costs assessed in a number of parts on. Each part of the increase in the cost of a small, far less than due to increased labor productivity and reduce costs. Workpiece larger quantities, the use of fixture on the economic benefits achieved by the markedly effective.Keywords: The feature of the part of the container kind, Fixture Features目录摘要 (I)A B S T R A C T (II)目录 (IV)第1章绪论 (1)1.1涡轮减速器箱体浅析 (1)1.2 涡轮减速器箱体零件简介 (1)1.2.1 涡轮减速器箱体类零件的功用及结构特点 (1)1.2.2 涡轮减速器箱体零件加工工艺特点 (2)第2章零件的分析 (3)2.1 零件的作用 (3)2.2零件的工艺分析 (3)第3章零件的工艺规程设计 (6)3.1选择零件的材料................................. 错误!未定义书签。
蜗轮减速机箱体加工工艺毕业设计说明书

目录摘要 (3)1 序言 (4)1.1 机械加工工艺规程制定 (4)1.2 机械加工工艺规程旳种类 (5)1.3 制定机械加工工艺规程旳原始资料 (5)1.4 机床夹具旳设计 (5)1.5 夹具设计技术分析 (5)2 箱体零件旳分析 (5)2.1 箱体零件旳构造特点 (6)2.2 箱体零件旳作用 (6)2.3 箱体零件旳工艺分析 (6)2.4 箱体零件旳生产类型 (7)2.5 毛坯确实定 (7)3 确定箱体加工旳工艺路线 (8)3.1 机械加工工艺设计 (8)基面旳选择 (8)粗基准旳选择 (8)精基准旳选择 (8)表面加工措施旳选择 (9)加工阶段旳划分 (10)加工次序安排 (10)3.2 制定机械加工工艺路线 (10)4机械加工余量、工序尺寸及毛坯尺寸确实定 (12)4.1 箱体上体 (12)4.2 箱体下体 (13)4.3箱体 (13)5确定切削用量及基本工时 (14)5.1箱体上体 (14)5.2箱体下体 (17)5.3 箱体 (21)6专用夹具旳设计 (27)6.1 机床夹具概述 (27)夹具旳概念 (27)机床夹具旳功能 (27)机床夹具应满足旳规定 (28)机床夹具旳类型 (29)机床夹具旳基本构成 (29)工件旳定位措施 (29)六点定位原理 (30)6.1.8 完全定位与不完全定位 (30)6.2 专用夹具设计旳一般环节 (31)夹具设计旳一般环节 (31)专用夹具设计中旳几种重要问题 (32)6.3 加工箱体旳夹具 (34)钻床夹具 (34)铣床夹具 (35)总结与体会 (37)道谢词 (37)参照文献 (38)摘要本文是有关蜗轮减速器箱体工艺环节旳阐明措施旳详细论述。
工艺工装设计是在学习机械制造技术后,在生产实习旳基础上,综合运用所学有关知识对零件进行加工工艺规程旳设计和机床夹具旳设计,并制定出箱体合理可行旳机械加工工艺过程卡片以及箱体机械加工旳工序卡和夹具总体设计方案,根据零件加工规定制定出可行旳工艺路线和合理旳夹具方案,以保证零件旳加工质量。
蜗轮减速器箱体机械加工工艺规程卡片

景德镇陶瓷学院机械加工工序卡片产品名称减速器零件名称蜗轮减速器箱体第 1 页共21 页车间工序号工序名称材料牌号10 铸造HT200毛坯种类毛坯外形尺寸每毛坯可制件数每台件数铸造件204×190×261 1设备名称设备型号设备编号同时加工件数金属模夹具编号夹具名称切削液工位器具编号工位器具名称工序工时(分) 准终单件工步号工步内容工艺装备主轴转速切削速度进给量切削深度进给次数工步工时r/min m/min mm/r mm 机动辅助1 金属模铸造,铸造出符合设计要求的毛坯。
毛坯尺寸按照毛坯图上尺寸。
游标卡尺,分度值为0.02mm设计(日期)校对(日期)审核(日期)标准化(日期)会签(日期)景德镇陶瓷学院机械加工工序卡片产品名称减速器零件名称蜗轮减速器箱体第 2 页共21 页车间工序号工序名称材料牌号20 清砂HT200毛坯种类毛坯外形尺寸每毛坯可制件数每台件数铸造件204×190×261 1设备名称设备型号设备编号同时加工件数夹具编号夹具名称切削液工位器具编号工位器具名称工序工时(分) 准终单件工步号工步内容工艺装备主轴转速切削速度进给量切削深度进给次数工步工时r/min m/min mm/r mm 机动辅助1 清除浇注系统,冒口,型砂,飞边,飞刺等。
60设计(日期)校对(日期)审核(日期)标准化(日期)会签(日期)景德镇陶瓷学院机械加工工序卡片产品型号零件图号产品名称减速器零件名称蜗轮减速器箱体第 3 页共21 页车间工序号工序名称材料牌号30 热处理HT200毛坯种类毛坯外形尺寸每毛坯可制件数每台件数铸造件204×190×261 1设备名称设备型号设备编号同时加工件数加热炉夹具编号夹具名称切削液工位器具编号工位器具名称工序工时(分)准终单件工步号工步内容工艺装备主轴转速切削速度进给量切削深度进给次数工步工时r/min m/min mm/r mm 机动辅助1 人工时效处理: 把工件放入炉中,装炉温度≤200℃,升温速度≤100℃,保温温度:500~550℃,保温时间:4~6小时,冷却速度:30℃,出炉温度:≤200℃。
涡轮减速箱体加工工艺规程及工艺装备的设计

涡轮减速箱体加工工艺规程及工艺装备的设计一、涡轮减速箱体加工工艺规程1.铸造工艺:涡轮减速箱体通常采用铸造工艺进行生产,首先需要准备合适的铸型材料,如砂毛、铸铁、铸钢等,制作铸型。
然后,在铸型内进行浇注熔化的金属材料,如铝、铜等,待其冷却凝固后,取出铸件。
最后进行修整、清理等工艺,使得铸件达到设计要求。
2.精密加工工艺:涡轮减速箱体的精密加工工艺包括铣削、切削、镗削、磨削等。
具体工艺过程需要根据涡轮减速箱体的结构形式、工作原理等因素进行选择。
在加工过程中,需要使用合适的切削工具,如铣刀、车刀、镗刀、磨石等。
同时,需根据加工要求进行加工定位和工艺检验,保证加工精度和质量。
3.热处理工艺:涡轮减速箱体在加工完成后,需要进行热处理工艺,提高其硬度和强度。
热处理工艺包括淬火、回火、正火等。
在热处理过程中,需要根据不同材料的特性和要求进行控制温度、加热时间和冷却速度等参数,确保涡轮减速箱体在使用中具备良好的力学性能。
4.涂装工艺:涂装可以提高涡轮减速箱体的表面质量和防锈性能。
涂装工艺包括清洗、除锈、喷涂等步骤。
首先,对涡轮减速箱体进行清洗和除锈,去除表面杂质和氧化物。
然后,进行底漆喷涂和面漆喷涂,涂装剂选择要符合涡轮减速箱体的使用环境和材料特性,确保涂装质量。
1.铸造设备:涡轮减速箱体铸造过程中需要使用适当的铸造设备,如铸造机床、熔炼炉等。
铸造机床可以用于制作铸型,具备适当的加热功能,确保金属材料能够完全熔化。
熔炼炉用于熔炼金属材料,要求能够提供足够的熔化温度和熔化能量。
2.精密加工设备:涡轮减速箱体精密加工过程中需要使用精密加工设备,如车床、铣床、镗床、磨床等。
这些设备应具备高精度、高刚性、稳定性好的特点,能够满足涡轮减速箱体的精密加工要求。
3.热处理设备:涡轮减速箱体热处理需要使用适当的热处理设备,如淬火炉、回火炉等。
这些设备应具有高温控制、均热性好、冷却速度可调等特点,能够实现对涡轮减速箱体的精确热处理。
蜗轮减速机箱体加工工艺技术
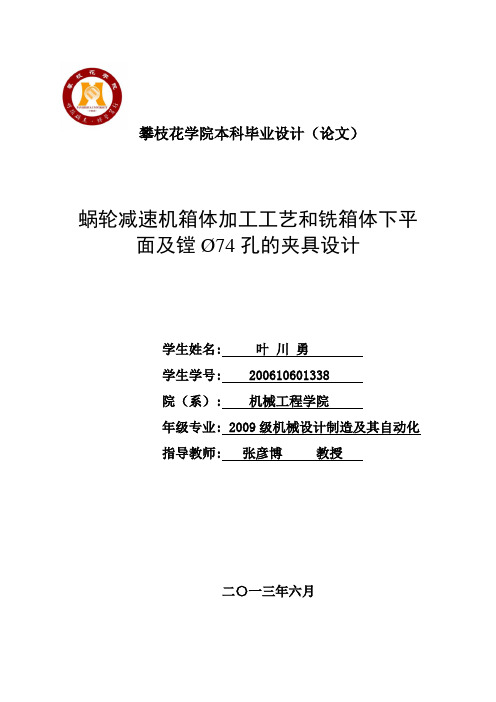
攀枝花学院本科毕业设计(论文)蜗轮减速机箱体加工工艺和铣箱体下平面及镗Ø74孔的夹具设计学生姓名: 叶川勇学生学号: 200610601338院(系): 机械工程学院年级专业: 2009级机械设计制造及其自动化指导教师: 张彦博教授二〇一三年六月摘要本课题是对一个已经设计好的蜗轮减速机箱体进行加工工艺规程的制定以及设计出该课题中的所指定的加工两个面的专用夹具。
本课题要求是加工箱体下平面和一个轴承座内圆的夹具。
跟据生产纲领的要求,本减速机的生产量较大,属于大批量生产,则设计夹具时一定要充分考虑到该夹具在生产中的加工效率,一定要能够达到生产纲领的规定。
因此,在能够满足加工精度的前提下,装夹效率、加工效率是越高越好。
结合实际生产,课题中夹具可采用一定的自动夹紧方案——气压夹紧。
在加工方面,该箱体可采用一般箱体加工的方式——基准统一,即先加工出底面和钻两个工艺孔,用一面两销的方式来做为精基准加工其他的面。
这样不但加工精度容易保证,且装夹方面,夹具上的通用零件较多,可以很好地降低成本。
对于其他加工面,可按先面后孔的原则进行加工,即先将所有没有特殊要求的面全部铣出来,然后粗镗、半精镗轴承座孔,再将其他一些孔(比如螺钉孔等)加工出来后,最后精镗轴承座孔。
工序之间可采用流水线加工。
这样加工的好处是工件在加工过程中搬运的地方较少,有利于其他工作的展开和控制成本,且能够满足设计要求。
关键词蜗轮减速机,加工工艺,专用夹具AbstractOur task is to have a good design of worm gear speed reducer box body processing rules and design of this subject in the specific processing of the special fixture two. The task of this thesis is to design the fixture plane processing box and a bearing seat inner circle. According to the requirements of the production program, the reducer production amount is larger, which belongs to the mass production, the fixture design must fully take into account the processing efficiency of the fixture in the production, provision must be able to reach the production program. Therefore, in can satisfy the machining precision, clamping efficiency, the processing efficiency is higher. Combined with the actual production, paper uses the automatic clamping fixture -- pneumatic clamping scheme certain. In processing, the box can be used in general machining method -- the unification datum, which is processed with a bottom surface and drill two holes, with a two pin way to do fine base for the. So not only the machining precision is easy to guarantee, and the clamping fixture, general parts more, can well reduce the cost. For other processing, according to the surface after the first hole of the principle of processing, namely, first of all do not require special surface milling, and then rough boring, semi-finishing the bearing seat hole, and the other hole (such as screw holes) processing out, finally finish boring of the bearing seat hole. Among the process can use pipelined processing. This process has the advantage of workpiece handling in the process of processing places less, expansion and cost control for other work, and can meet the design requirements.Keywords worm reducer, machining process, fixture目录摘要 ................................................................................................................................. Abstract .........................................................................................................................1 绪论 01.1课题背景 01.2指定工艺规程的意义与作用及其基本要求 01.3夹具的设计 02 零件的分析 (2)2.1零件的作用 (2)2.2零件的工艺分析 (2)3 工艺规程设计 (4)3.1确定毛坯的制造形式 (4)3.2基面的选择 (4)3.3 制定工艺路线 (4)3.4机械加工余量、工序尺寸及毛坯尺寸的确定 (7)3.4.1毛坯尺寸 (7)3.4.2机械加工余量、工序尺寸 (7)3.5选择量具 (9)3.6确定切削用量及基本工时 (9)3.6.1粗铣、半精铣箱体下平面 (9)3.6.2钻下平面2个Ø15mm的孔,钻、扩、铰另两个Ø15mm的孔 (12)3.6.3铣Ø176mm圆端面 (16)3.6.4铣Ø98mm圆端面 (18)3.6.5铣Ø60mm圆端面 (19)3.6.6铣Ø32mm圆端面 (21)3.6.7镗Ø132mm孔、Ø74mm孔 (22)3.6.8 钻、扩、粗铰、精铰Ø20mm通孔 (27)3.6.9加工M6的螺纹 (30)3.6.10加工M16螺纹 (32)3.6.11加工M10螺纹 (33)4 专用夹具设计 (36)4.1设计主旨 (36)4.2夹具设计 (36)4.2.1铣箱体下平面夹具设计 (36)4.2.2镗Ø132mm孔、Ø74mm孔夹具 (38)结论 (43)参考文献 (44)致谢 (45)1 绪论1.1课题背景加工工艺及夹具毕业设计是对我们所学专业知识的一次巩固,是我们在进行社会实践之前对所学各课程的一次深入的综合性总复习,也是理论联系实际的训练。
- 1、下载文档前请自行甄别文档内容的完整性,平台不提供额外的编辑、内容补充、找答案等附加服务。
- 2、"仅部分预览"的文档,不可在线预览部分如存在完整性等问题,可反馈申请退款(可完整预览的文档不适用该条件!)。
- 3、如文档侵犯您的权益,请联系客服反馈,我们会尽快为您处理(人工客服工作时间:9:00-18:30)。
目录第一节零件图分析...........................................................................‥ (1)1.涡轮减速器箱体功用和特点 (1)2.涡轮减速器箱体的技术要求 (1)第二节确定毛坯 (3)1.涡轮减速器箱体毛坯分析 (4)2.涡轮减速器箱体结构确定并画出毛坯图 (4)第三节定位基准选择………………………………………………………………………‥41.精基准的选择 (5)2.粗基准的选择 (5)第四节拟定工艺路线 (6)1.表面加工方法的确定 (6)2.加工阶段的划分 (6)3.工序的集中与分散 (6)4.工序顺序的安排 (6)5.确定工艺路线 (6)第五节确定加工余量、计算工序尺寸 (7)第六节选择机床与工艺装备 (8)1.机床设备的选用 (8)2.工艺装备的选用 (12)第七节切削用量与时间定额 (13)1.切削用量计算 (13)2.时间定额的计算 (14)第八节编写工艺文件 (14)小型涡轮减速器箱体加工工艺编制任务:完成小型涡轮减速器箱体机械加工工艺规程的制订(中小批量)。
涡轮减速器箱体设计图纸如图2-48所示。
第一节零件图分析一、涡轮减速器箱体的功用和特点:箱体类零件是机器及其部件的基础件之一。
它将一些轴、轴承、套、齿轮等零件装配在一起,使其保持正确的相互位置关系,并按规定的运动关系协调动作,完成某种远动。
因此,箱体类零件的加工质量对机器的精度、性能和寿命有着直接关系。
涡轮减速器箱体的功用如上述所示,其特点有许多精度要求不同的孔和平面组成,内部结构比较简单但壁的厚薄不均匀,加工的难度较大。
二、涡轮减速器箱体的技术要求:涡轮减速器箱体的主要技术有:1. 两对轴承孔的尺寸精度为IT7,表面粗糙度Ra值为1.6um,一对Ф90的轴承孔和一对Ф180的轴承孔同轴度公差分别为0.05mm、0.06mm,其中两对轴承孔轴线的垂直度公差为0.06mm;2.铸件不得有砂眼、疏松等铸造缺陷;3.非加工表面涂防锈漆;4.铸件进行人工时效处理;5.箱体做煤油渗漏实验;6.材料HT200。
表2-49 涡轮减速器箱体的主要加工技术要求第二节确定毛坯一、毛坯分析:按技术要求涡轮减速器箱体的材料是HT200,其毛坯是铸件。
铸铁容易成型、切削性能好、价格低廉,并且具有良好的耐磨性和减振性,也是其它一般箱体常用的材料。
铸件毛坯的精度和加工余量是根据生产批量而定的。
对于单件小批量生产,一般采用木模手工造型。
这种毛坯的精度低,加工余量大,其平面余量一般为7~12mm,孔在半径上的余量为8~14mm。
在大批大量生产时,通常采用金属模机器造型。
此时毛坯的精度较高,加工余量可适当减低,则平面余量为5~10mm ,孔(半径上)的余量为7~12mm 。
为了减少加工余量,无论是单件小批生产还是成批生产,均需在三对轴承孔位置在毛坯上铸出预孔。
表2—2是应用查表法得到的小批量手工砂型铸造时减速箱箱体的毛坯尺寸公差及机械加工余量。
另外,在毛坯铸造时,应防止砂眼和气孔的产生;应使减速箱箱体零件的壁厚尽量均匀,以减少毛坯制造时产生的残余应力。
由于零件的结构复杂,壁厚也不均匀,因此,在铸造时会产生较大的残余应力。
为了消除残余应力,减少加工后的变形和保证精度的稳定,所以,在铸造之后必须安排人工时效处理。
人工时效的工艺规范为:加热到500℃~550℃,保温4 h~6 h,冷却速度小于或等于30℃/h,出炉温度小于或等于200℃。
人工时效的方法,除了加热保温法外,也可采用振动时效来达到消除残余应力的目的。
表2—50涡轮减速器箱体毛坯尺寸公差及机械加工余量二、确定结构并画出毛坯图:第三节定位基准的选择涡轮减速器箱体加工定位基准的选择定位基准可分为粗基准和精基准,通常先确定精基准,然后再确定粗基准。
1、精基准的选择:一般箱体零件常以装配基准或专门加工的一面两孔定位,使得基准统一。
蜗轮减速器箱体中Ф90轴承孔和Ф180轴承孔有一定的尺寸精度和位置精度要求,其尺寸精度分别为IT7级和IT6级、位置精度包括:Ф90轴承孔对Ф90轴承孔轴线的同轴度公差为Ф0.05、Ф180轴承孔对Ф180轴承孔轴线的同轴度公差为Ф0.06、Ф180轴承孔轴线对Ф90轴承孔轴线的垂直度公差为0.06。
为了保证以上几项要求,加工箱体顶面时应以底面为精基准,使顶面加工时的定位基准与设计基准重合;加工两对轴承孔时,仍以底面为主要定位基准,这样既符合“基准统一”的原则,也符合“基准重合”的原则,有利于保证轴承孔轴线与装配基准面的尺寸精度。
2、粗基准的选择:一般箱体零件的粗基准都用它上面的重要孔和另一个相距较远的孔作为粗基准,以保证孔加工时余量均匀。
蜗轮减速器箱体加工选择以重要表面孔Ф90及Ф180为粗基准,通过划线的方法确定第一道工序加工面位置,尽量使各毛坯面加工余量得到保证,即采用划线装夹,按线找正加工即可。
三位效果图表2-51 减速器箱体表面加工方案第四节拟订工艺路线一、表面加工方法的确定涡轮减速器箱体的主要加工表面可归纳为以下三类:(1)主要表面箱体的底面、Ф180轴承孔和Ф90轴承孔的端面等。
(2)主要孔Ф180和Ф90 轴承孔。
(3)其他加工部分4*M6螺孔、16*M8螺孔、4*M16等。
根据涡轮减速器箱体零件图上各加工表面的尺寸精度和表面粗糙度,确定个表面的加工方法,如表2-51所示。
二、加工阶段的划分减速箱体整个加工过程可分为两大阶段,即先对箱盖和底座分别进行加工,然后再对装合好的整个箱体进行加工——合件加工。
在加工时,粗、精加工阶段要分开。
减速箱箱体毛坯为铸件,加工余量较大,而在粗加工中切除的金属较多,因而夹紧力、切削力都较大,切削热也较多。
加之粗加工后,工件内应力重新分布也会引起工件变形,因此,对加工精度影响较大。
为此,把粗精加工分开进行,有利于把已加工后由于各种原因引起的工件变形充分暴露出来,然后在精加工中将其消除。
三、工序的集中与分散箱体的体积、重量较大,故应尽量减少工件的运输和装夹次数。
为了便于保证各加工表面的位置精度,应在一次装夹中尽量多加工一些表面。
工序安排相对集中。
箱体零件上相互位置要求较高的孔系和平面,一般尽量集中在同一工序中加工,以减少装夹次数,从而减少安装误差的影响,有利于保证其相互位置精度要求。
四、工序顺序的安排1、机械加工工序(1)遵循“先基准后其他”的工艺原则,首先加工精基准对合面。
(2)遵循“先粗后精”的工艺原则,先安排粗加工工序,后安排精加工工序。
(3)遵循“先主后次”的工艺原则,由于轴承孔及各主要平面,都要求与对合面保持较高的位置精度,所以在平面加工方面,先加工对合面,然后再加工其它平面。
(4)遵循“先面后孔”的工艺原则,还遵循组装后镗孔的原则。
因为如果不先将箱体的对合面加工好,轴承孔就不能进行加工。
另外,镗轴承孔时,必须以底座的底面为定位基准,所以底座的底面也必须先加工好。
2、热处理工序箱体零件的结构复杂,壁厚也不均匀,因此,在铸造时会产生较大的残余应力。
为了消除残余应力,减少加工后的变形和保证精度的稳定,所以,在铸造之后必须安排人工时效处理。
人工时效的工艺规范为:加热到500℃~550℃,保温4h~6h ,冷却速度小于或等于30℃/h ,出炉温度小于或等于200℃。
普通精度的箱体零件,一般在铸造之后安排1次人工时效出理。
对一些高精度或形状特别复杂的箱体零件,在粗加工之后还要安排1次人工时效处理,以消除粗加工所造成的残余应力。
本例减速箱体在铸造之后安排1次人工时效出理,粗加工之后没有安排时效处理,而是利用粗、精加工工序间的停放和运输时间,使之得到自然时效。
箱体零件人工时效的方法,除了加热保温法外,也可采用振动时效来达到消除残余应力的目的。
3、辅助工序在铸造后安排了清砂、涂漆工序;箱盖和底座拼装前,安排了中间检验工序和底座的煤油渗漏试验工序;箱体精加工后,安排了拆箱、去毛刺、清洗、合箱和终检工序。
五、确定工艺路线在综合考虑了上述工序顺序安排原则的基础上,涡轮减速器箱体的加工工艺路线如下:1.铸造箱体—2.清沙—3.人工时效处理—4.油漆—5.划线—6.铣削各加工表面—7镗削轴承孔—8.钻M6、M8、M16底孔—9.攻丝M6、M8、M16螺纹—10.油漆不加工表面—11.检验—12.入库。
第五节加工余量、工序尺寸和公差的确定以下介绍几个重要表面、孔加工中加工余量、工序尺寸和公差的确定。
(1)290mm上、下端面的加工余量、工序尺寸和公差的确定表2-52所示,加工过程:(1)以底面为基准,找正所划上端面加工线,粗刨上端面,留余量。
(2)以上端面为基准,粗刨底面,保证工序尺寸。
(3)以底面为基准,精刨上端面,保证工序尺寸。
表 2-52303±6 (2) 215mm左、右端面的加工余量、工序尺寸和公差的确定表2-53所示,加工过程:(1)以左端面为基准,找正所划右端面加工线,粗刨上端面,留余量。
(2)以右端面为基准,粗刨底面,保证工序尺寸。
(3)以左端面为基准,精刨上端面,保证工序尺寸。
表2-53(3)Ф90 mm孔的加工余量、工序尺寸和公差的确定表2-54所示,表2-54Ф167.5±5.5第六节选择机床与工艺装备一、机床设备的选用单件小批量加工时,一般选用通用机床;单件小批量高精度加工时,可选用加工中心(详见第十节);在大批生产条件下可选用通用机床加专用夹具,也可选用高效的专用设备和组合机床。
减速箱箱体加工时机床设备的选用见表2—5。
B665牛头刨床可刨削最大长度650mm;Z3050T68主要参数型号T68主轴直径85mm主轴锥孔莫氏5号工作台面积(L·B) 1000x800mm主轴轴向行程(w) 600mm主轴箱垂直行程(y) 755mm工作台横向行程(x) 850mm工作台纵向行程(z) 1080mm平旋盘滑块行程(u) 170mm主轴转速20~1000r/min(18级) 平旋盘转速10~200r/min(14级) 进级量级数18级主轴每转主轴箱和工作台的进给范围0.025~8mm主轴每转主轴的进给量范围0.05~16mm平旋盘每转刀架的进给量范围0.025~8mm平旋盘每转主轴箱和工作台进给量范围0.05~16mm主轴箱、工作台的块速移动速度2400mm/min主轴的块速移动速度4400mm/min平旋盘滑块速移动速度1200mm/min主轴允许最大扭矩110kg-m平旋盘滑块速移动速度1200mm/min主轴允许最大扭矩110kg-m平旋盘允许最大扭矩220kg-m最大切削抗力1300kg最大进给抗力1300kg工作台最大负载2000kg主电机功率 6.5/8kw机床重量11000kg外形尺寸(长x宽x高) 5075x2345x2730mm二、工艺装备的选用工艺装备主要包括刀具、夹具和量具。