折叠式舱口盖装配工艺简述
57000DWT液压折叠式舱盖安装工艺

57000DWT液压折叠式舱盖安装工艺( 57000 DWT 散货船)液压折叠式舱盖安装工艺汇编:校对:审核:一,舱口盖的准备工作1,货舱盖制作货舱盖已由舱盖制造厂家制作及安装完成(包括盖板结构和盖板上的舾装件),并已有盖板尺寸测量记录和舱盖完整性(按舱盖装置图)检验报告。
2,货舱盖在地面胎架上装配和划线(反装—以舱盖面板为基面)2-1将一个舱两对盖板置于地面胎架上,用临时拉紧器将一对两块盖板拼合成对并安装中间铰链,此拼合缝称中间缝。
通过成对盖板折叠试验检验其折叠功能,应控制舱盖钢结构与铰链眼板不会发生碰撞,同时,应检验中间铰链的连线是否水平(可按图491—0007“折叠试验”)。
2-2将两对盖板重新定位对拼,用临时拉紧器将两对盖板拼合,此拼合缝称分离缝。
2-3上述各缝对合过程中,须根据中间缝和分离缝的橡胶条压缩量要求均为15mm (+3/-5mm)进行测量和对合。
在测量两缝橡胶条压缩量时,须从橡胶槽底部到压紧扁钢底部测量水平距离,每隔1米进行测量并记录压缩量(见图491—1050“NO.1-5舱舱盖橡皮布置图”)。
同时使两条中间缝(铰链轴线)及分离缝相互平行(此时一个舱两对盖板处于固定状态);2-4在舱盖盖板上标记出舱盖的基准线(中线、分离缝开档标记线、中间缝开档标记线)及标识;二,舱口围上的准备工作1,在船上分舱进行舱口围的开口尺寸及舱口围面板水平度测量,记录测量结果,如超差则需矫正(见‘图491--0008舱盖制造公差’要求;以下各项安装,舱盖制造公差中如有适用项,亦须执行);2,在舱口围面板上用洋冲作舱口纵/横向中心线标记;3,以舱口围面板上舱口中心线为基准线,按盖板两侧滚轮实际横向尺寸在舱口围两侧纵向面板上作滚轮导轨基准线,将导轨点焊在相应的位置处(见图491-1142、1242导轨布置图)。
4,端铰链“铰链底座(甲板座)”可同时定位及安装。
三,吊装舱盖板到舱口围上1,将舱盖吊装到舱口围面板上,并使盖板中心线与舱口围面板对应的仓口纵中心线对准;2,用临时拉紧器分别将配对盖板在中间铰链处拉至对合到盖板胎架安装验收的标记尺寸,并装好盖板中间铰链;3,用临时拉紧器将两对盖板在分离缝处拉至使盖板对合调整到盖板胎架安装验收的标记尺寸;同时用临时垫块予调平舱盖,并在舱口围上安装临时限位块定位,以防止盖板在水平X/Y方向上移动。
浅析舱口盖结构的加工及安装

浅析舱口盖结构的加工及安装舱口盖结构的加工及安装是一个非常重要的环节,它关系到整个舱口盖的质量和使用功能。
下面将从加工和安装两个方面对舱口盖结构进行浅析。
舱口盖结构的加工主要包括以下几个步骤:1. 材料准备:首先要根据设计要求选择合适的材料,通常舱口盖采用金属材料,如钢板、铝合金等。
然后根据设计要求进行切割和开料,得到所需形状和尺寸的工件。
2. 表面处理:对切割和开料后的工件进行表面处理,如打磨、除锈、喷涂等,以提高工件的表面光洁度和防腐蚀性能。
3. 成型加工:根据设计要求,将工件进行成型加工,包括折弯、冲孔、压铆等。
其中最重要的是舱口盖的折弯加工,它直接影响到舱口盖的密封性能和承载能力。
4. 焊接:对成型加工后的工件进行焊接处理,以增强工件的强度和刚度。
常用的焊接方法有电弧焊、气体保护焊等。
5. 检测与修整:对焊接后的工件进行检测,如尺寸检测、缺陷检测等。
如果有缺陷或不合格的地方,需要进行修整和修复,以确保舱口盖的质量。
1. 安装前准备:在安装之前,需要对舱口盖和安装位置进行清洁,确保无杂物和污垢。
检查舱口盖和安装位置的尺寸是否匹配,确保安装的顺利进行。
2. 位置定位:根据设计要求,使用合适的定位工具和方法,在舱口盖和安装位置上做好标记和定位。
如果有需要,可以使用临时固定装置,确保舱口盖的位置准确。
3. 固定连接:根据舱口盖的结构和设计要求,选择合适的固定连接方式,如螺栓连接、焊接连接等。
在进行固定连接时,需注意力的均匀分布和连接的紧固度,以确保舱口盖的稳定性和安全性。
4. 密封处理:根据舱口盖的要求,选择合适的密封材料,如橡胶密封条、密封胶等。
在安装时,要确保密封材料的正确放置和压实,以达到良好的密封效果。
舱口盖结构的加工和安装是一个复杂而重要的过程,它需要在设计要求和工艺要求的指导下进行,以保证舱口盖的质量和使用效果。
只有通过科学的加工和安装过程,才能确保舱口盖能够正常运行并满足使用需求。
57000DWT散货船折叠式舱口盖安装技术

装 比其 它 类 型 安 装 要 求 高 。现 就 5 0 W 散 货 船 折 叠 70 0D T
作者 简 介 :唐 广 概 ( 9 1 1 8 一),男 ,助 理 工程 师 ,从 事 船 舶 舾装 设 计 工作 。
折 叠 式 、单 拉 式 、 吊离 式 、侧 移 式 、背 载 式 等 , 不 同种 类 的舱 盖 安 装 流程 和 工 艺 不尽 相 同,其 中折 叠 式舱 盖 安
设 备 。另 一 部 分 是舱 盖 按 图制 作 部 分 附件 。对 于前 者 , 需 要根 据 合 同和 设 计 要 求 核对 数 量 和 外观 。对 于制 作 部 分 附件 ,要 按 以下 要 求进 行检 验 :
最 重 的3 货 舱 同 时 作 为 压 载 舱 使 用 ,4 体 总 重 量 达 号 片 1 O t 自首 制 船 交 付 以 来 , 我 厂 已 自行 制 造 和 安 装 了 2多 。
多 套舱 盖 ,为进 入 散 货 船 制造 领 域 打下 了坚 实 的基 础 。 从 开 关 运 动 型式 上 分 ,常见 的散 货 船 货 舱舱 口盖 有
A bs r t I de o pr i he p od c i e rm e tw ih b te n tu ton,t i pe n l esa d t ac : n or rt ov de t r u ton d pa t n t e t r i sr c i h spa ra a yz n s um m a i e he i t la i n t c no og f f d ng ha c c e nd a s r po est e q c s nd e on rz st nsa l to e h l y o ol i th ov ra l o p o s h uike ta c om i a c l
舱口盖建造工艺
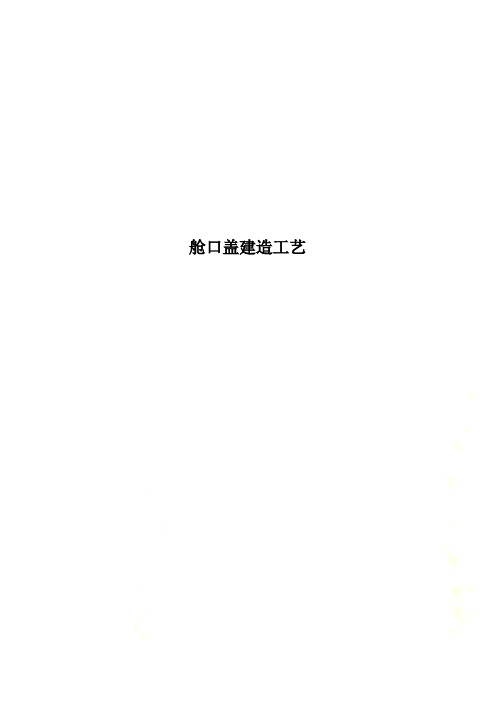
舱口盖建造工艺审 定 日 期 标 检审 核校 对 描 校编 制描 打 施工设计 舱口盖建造工艺标记 数量 修改单号 签 字日 期 总面积 m 2 0.6 共 页 8 第 页 2 会 签旧底图登记号 底图登记号1、概述本船舱盖为钢质风雨密、液压启闭式舱口盖。
全船共设三个货舱。
每个货舱由四块舱盖板组成,以两块一组收藏方式向艏、艉两端折叠收藏。
四个货舱的舱盖尺寸相同。
各舱舱盖均由液压油缸驱动,通过中间铰链、行走滚轮、导板等主要部件来完成舱口盖的开启和关闭工作。
舱口盖与货舱围栏之间设有支承块、横向限位装置、横向限位器、纵向定位装置、快速压紧器、橡胶密封装置、橡皮压紧条。
同时配有舱盖折叠收藏的收藏钩装置及撬棍。
舱口盖施工及检验程序:放样→下料→拼板自动焊→纵、横梁预制→盖板顶板上胎架定位→构架划线→装配结构→焊接→脱胎→翻身补焊及整体火工矫正→上拼装胎架进行组合拼装→附件定位→焊接→翻身补焊→折叠试验→除锈油漆→压入密封橡皮→吊运上船。
舱盖实船定位→定位安装导轨、压紧器、支撑块等舱盖附件→液压系统、管路、油缸安装→液压开舱→定位安装收藏购、限位器、橡皮压紧条等舱盖附件→附件烧焊→液压系统调试→舱盖启闭试验→舱盖水密试验→交货。
2、舱盖板制造2.1通则2.1.1本船舱盖板制造质量标准应符合CB/T 4000-2005(中国造船质量标准)的要求,除此还应符合图纸的要求。
2.1.2舱盖所用的钢板及型钢材料均应满足船用钢材要求,并具有合格证书。
施工过程中,对特殊钢材应进行及时标注与跟踪管理。
2.1.3本舱盖所有零件,均应放样确定其正确尺寸,经检查合格后方可投入加工制造。
结构和线型零件必须经专职检验。
2.1.4 本舱盖的组合部件实行无余量组合装配,装配前后均须专职检验。
2.1.5 本舱盖实行以舱为单位进行整体反造,而后分离成单块盖板。
2.1.6 为控制焊接变形,确保纵横间距和舱盖的几何尺寸,放样时,横梁之间每档加放1.0mm、纵桁之间每档加放2.0mm的焊接收缩量。
折叠式舱盖舾装工艺流程
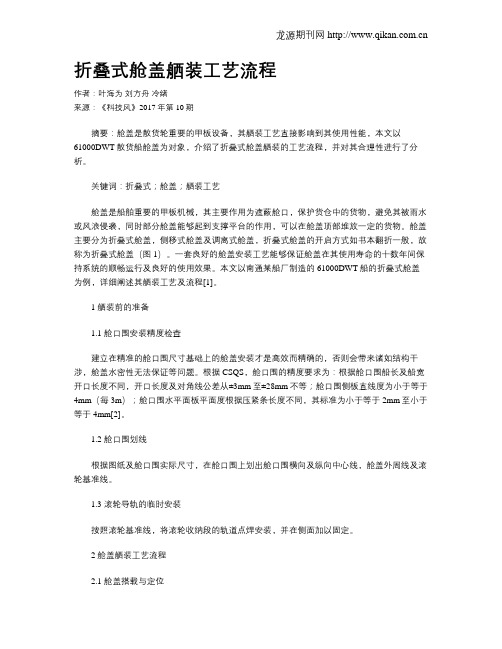
折叠式舱盖舾装工艺流程作者:叶海为刘方舟冷绪来源:《科技风》2017年第10期摘要:舱盖是散货轮重要的甲板设备,其舾装工艺直接影响到其使用性能,本文以61000DWT散货船舱盖为对象,介绍了折叠式舱盖舾装的工艺流程,并对其合理性进行了分析。
关键词:折叠式;舱盖;舾装工艺舱盖是船舶重要的甲板机械,其主要作用为遮蔽舱口,保护货仓中的货物,避免其被雨水或风浪侵袭,同时部分舱盖能够起到支撑平台的作用,可以在舱盖顶部堆放一定的货物。
舱盖主要分为折叠式舱盖,侧移式舱盖及调离式舱盖,折叠式舱盖的开启方式如书本翻折一般,故称为折叠式舱盖(图1)。
一套良好的舱盖安装工艺能够保证舱盖在其使用寿命的十数年间保持系统的顺畅运行及良好的使用效果。
本文以南通某船厂制造的61000DWT船的折叠式舱盖为例,详细阐述其舾装工艺及流程[1]。
1 舾装前的准备1.1 舱口围安装精度检查建立在精准的舱口围尺寸基础上的舱盖安装才是高效而精确的,否则会带来诸如结构干涉,舱盖水密性无法保证等问题。
根据CSQS,舱口围的精度要求为:根据舱口围船长及船宽开口长度不同,开口长度及对角线公差从±3mm至±28mm不等;舱口围侧板直线度为小于等于4mm(每3m);舱口围水平面板平面度根据压紧条长度不同,其标准为小于等于2mm至小于等于4mm[2]。
1.2 舱口围划线根据图纸及舱口围实际尺寸,在舱口围上划出舱口围横向及纵向中心线,舱盖外周线及滚轮基准线。
1.3 滚轮导轨的临时安装按照滚轮基准线,将滚轮收纳段的轨道点焊安装,并在侧面加以固定。
2 舱盖舾装工艺流程2.1 舱盖搭载与定位1)准备好临时支撑垫块,置于舱盖外周裙边下,用于在支撑块未安装情况下的舱盖临时承重,避免因舱盖密封橡皮接触舱口围导致的橡皮损坏。
2)将舱盖按照P1和P2盖、P3和P4盖成对吊装上船,大致保证舱盖中心线和舱口围中心线对其,滚轮与滚轮基准线对齐。
3)参照舱盖中心线,滚轮,铰链等实际尺寸,利用小千斤顶在舱盖侧面及艏艉部对舱盖位置进行微调,直至符合图纸要求,并将舱盖实际外周线划记在舱口围上。
舱口盖的安装工艺及控制要点
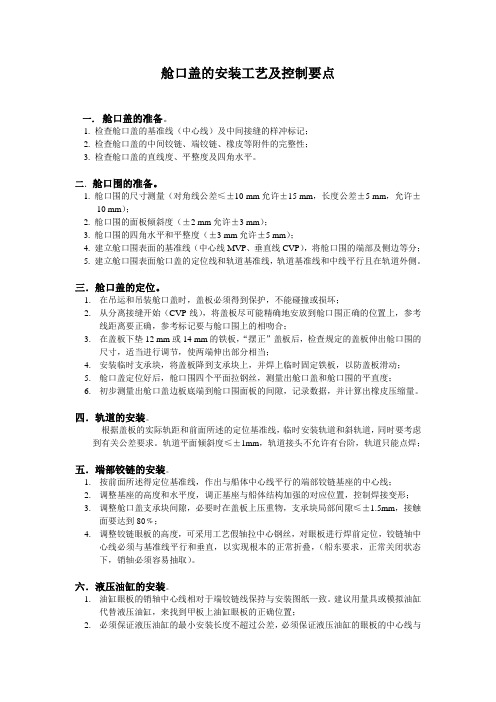
舱口盖的安装工艺及控制要点一.舱口盖的准备。
1. 检查舱口盖的基准线(中心线)及中间接缝的样冲标记;2. 检查舱口盖的中间铰链、端铰链、橡皮等附件的完整性;3. 检查舱口盖的直线度、平整度及四角水平。
二.舱口围的准备。
1. 舱口围的尺寸测量(对角线公差≤±10 mm允许±15 mm,长度公差±5 mm,允许±10 mm);2. 舱口围的面板倾斜度(±2 mm允许±3 mm);3. 舱口围的四角水平和平整度(±3 mm允许±5 mm);4. 建立舱口围表面的基准线(中心线MVP、垂直线CVP),将舱口围的端部及侧边等分;5. 建立舱口围表面舱口盖的定位线和轨道基准线,轨道基准线和中线平行且在轨道外侧。
三.舱口盖的定位。
1.在吊运和吊装舱口盖时,盖板必须得到保护,不能碰撞或损坏;2.从分离接缝开始(CVP线),将盖板尽可能精确地安放到舱口围正确的位置上,参考线距离要正确,参考标记要与舱口围上的相吻合;3.在盖板下垫12 mm或14 mm的铁板,“摆正”盖板后,检查规定的盖板伸出舱口围的尺寸,适当进行调节,使两端伸出部分相当;4.安装临时支承块,将盖板降到支承块上,并焊上临时固定铁板,以防盖板滑动;5.舱口盖定位好后,舱口围四个平面拉钢丝,测量出舱口盖和舱口围的平直度;6.初步测量出舱口盖边板底端到舱口围面板的间隙,记录数据,并计算出橡皮压缩量。
四.轨道的安装。
根据盖板的实际轨距和前面所述的定位基准线,临时安装轨道和斜轨道,同时要考虑到有关公差要求。
轨道平面倾斜度≤±1mm,轨道接头不允许有台阶,轨道只能点焊;五.端部铰链的安装。
1.按前面所述得定位基准线,作出与船体中心线平行的端部铰链基座的中心线;2.调整基座的高度和水平度,调正基座与船体结构加强的对应位置,控制焊接变形;3.调整舱口盖支承块间隙,必要时在盖板上压重物,支承块局部间隙≤±1.5mm,接触面要达到80﹪;4.调整铰链眼板的高度,可采用工艺假轴拉中心钢丝,对眼板进行焊前定位,铰链轴中心线必须与基准线平行和垂直,以实现根本的正常折叠,(船东要求,正常关闭状态下,销轴必须容易抽取)。
舱口盖制造

舱口盖制造、安装操作规程(之一)-------------安装部分一、范围本标准规定了舱口盖上船安装阶段的施工方法、工艺方法和质量要求;本标准适用于本企业的民品船舶液压折叠式舱口若悬河盖。
因各型船厂的舱口盖制造、按照杂黄方法不尽相同施工时主要以各型船的详细施工工艺为准。
二、引用标准:QG/WH15-717-2005生产运作操作程序QG/WH15-722-2005关键过程控制程序三、工程控制要求及操作方法1、上道工序转来的工件(包括外购件)必须检验,要有检验表示或合格证书。
为避免误差积累,必要时要求下道貌岸然工序提前介入上道工序,参与质量控制。
2、过程控制2.1 开舱前的安装工作2.1.1定位定位工作是舱口盖最为基础的工作,定位的好坏直接影响舱口盖在舱口围上的状态,应将舱口围和舱口盖的误差予以均衡,达到最佳配合效果。
2.1.1.1 以舱口若悬河盖上提供的中心线,划出舱品盖的中心线,作为舱品盖定位的基础。
舱品盖定位应尽量方正,避免为附件施工带来影响。
2.1.1.2 将舱口盖总体尺寸回复到胎架尺寸,符合各条缝胎架复们所定的对合线,作为舱口若悬河盖定位基准。
2.1.1.3 中间铰链安装、清洗、加油误码保证中间铰链轴轻松自由地转动。
2.1.1.4 检查橡皮槽底的直线度,避免出现折线现象,要求误差在-2--+3㎜以内。
用经纬仪在舱口盖纵向做好直线标记,根据该直线来检查,通过调节舱口盖之间的隙进行调整,调整时应尽可能考虑压紧条(板)安装高度。
2.1.1.5 将舱口盖前后左右固定,全面复查2.1.1.1-2.1.1.42.1.1.6 拉主铰链眼板中心线,测量主较链眼板高度尺寸,并提交内场加工,或根据工艺规定,在船上进行镗孔。
2.1.1.7 提交定位专检2.1.2 油缸下眼板装焊2.1.2.1 根据油缸眼板位置划出油缸下眼位置线并测量油缸眼板高度,复查中心与主铰链孔之间距离,保证上下眼板中心距离,尽可能使用样棒,保证油缸最小安装长度。
舱口盖施工工艺

仓盖施工工艺一.建造顺序下料、拼板、划线分段车间内场制作、胎架制作、报验焊前报验焊接焊后报验脱胎前数据测量总装胎上整体调平装四周胶槽胶槽焊接仓盖应力、火工调平测量、二次划线切割回周余量总装胎上试装箱座及舾装件安装焊接整体报验、数据交验。
二.具体施工工序及要求1.下料采用半自动及仿形切割进行切割,划线要保证精度,标注好零件号,做好号切、记录。
2.拼板拼板板缝焊接采用埋弧自动焊,焊前板材最好刨边,控制拼板间隙,减少变形。
3.小组装⑴.纵向T型材的面板腹板对接拼焊,采用埋弧自动焊正面焊好后反面清根后自动焊施焊,调直后拼装焊接,焊接后清理焊道,进行火工调正,调反变形值。
⑵.横向T型材拼焊后,进行调直、打磨。
⑶.角钢必须调直后方可使用。
⑷.端板应先在平台上拼接,自动焊焊接后,调出的变形值,划线开孔。
4.胎架制作胎架制作全部采用模板连成与内部结构相应的方格,模板采用δ=14×200的板条、立柱采用≥75×125角铁,模板上胎架前需进行调直,模板纵横向平直度不得大于是1.5mm,胎架反变形量在15‰,胎架在制作完一批仓盖后必须调整报验后方可二次使用,封胎必须采用小铁板封胎,以减少分段顶板及胎架的变形。
5.顶板上胎上胎后封胎、划线,划线时横向加放1‰的补偿量,纵向3‰的补偿量,划线必须交验并做好记录。
6.结构安装角钢安装点焊、定位,横向结构安装定位,纵向结构吊装定位,全部吊装到位后,先做纵向结构,后做横向加强结构,再做角钢,然后安装箱座加强,两端的箱座加强先焊接,处理完毕后进行端板安装及定位系统的安装,完毕进行数据测量,焊前交验,做好记录。
7.结构焊接焊接时应由中心向四周分格局部施焊,尽量减少变形,坚持焊工工艺,做好先焊对接,再焊立焊、后焊平的。
8.焊接完工后,进行数据测量,脱胎后再次测量数据并做好记录,以便下次施工中进行调整及对火工参考。
9.分段脱胎后到总装胎进行初步火工调整,合格后进行胶槽的划线安装、焊接,完工后对仓盖的内部结构进行整体报验,合格后分段方可返身,返身后对整个仓盖进行调平。
折叠式舱盖舾装工艺流程

机械化工
科技风 %&'( 年 ) 月下
角形压紧板"完成点焊安装后在压紧扁钢上涂抹粉笔"并关闭 舱盖"压紧扁钢上的压粉会印在舱盖的密封橡皮上"通过密封 橡皮上的粉印来判断压紧扁钢的安装位置是否正确"并根据之 前支撑块及裙边高低数据来调整压紧扁钢高度以保证橡皮压 缩量"如无问题则对压紧扁钢开始烧焊安装#
可仅参照舱盖上的限位卡爪位置对中安装" 调节垫片 暂 不 安装#
)( 完成调整后按照舱口 围 和 舱 盖 支 撑 板 之 间 的 距 离 确 定 6Y限位' 即支撑块( 的高度"并记录支撑块及裙边数据用于后 续密封橡皮压紧扁钢高度的调整#
. All Rights Reserved.
图 $ 舱盖的总体布置图 #舾装前的准备 $&$ 舱口围安装精度检查 建立在精准的舱口围尺寸基础上的舱盖安装才是高效而 精确的"否则会带来诸如结构干涉"舱盖水密性无法保证等问 题# 根据 7OiO"舱口围的精度要求为!根据舱口围船长及船宽 开口长度不同"开口长度及对角线公差从 h(PP至 h)JPP不 等)舱口围侧板直线度为小于等于 3PP' 每 (P( )舱口围水平面 板平面度根据压紧条长度不同"其标准为小于等于 )PP至小 于等于 3PP*)+ # $&) 舱口围划线 根据图纸及舱口围实际尺寸"在舱口围上划出舱口围横向 及纵向中心线"舱盖外周线及滚轮基准线# $&( 滚轮导轨的临时安装 按照滚轮基准线"将滚轮收纳段的轨道点焊安装"并在侧 面加以固定# %舱盖舾装工艺流程 )&$ 舱盖搭载与定位 $( 准备好临时支撑 垫 块"置 于 舱 盖 外 周 裙 边 下"用 于 在 支 撑块未安装情况下的舱盖临时承重"避免因舱盖密封橡皮接触 舱口围导致的橡皮损坏# )( 将舱盖按照 8$ 和 8) 盖$8( 和 83 盖成对吊装上船"大 致保证舱盖中心线和舱口围中心线对其"滚轮与滚轮基准线 对齐# (( 参照舱盖中心线"滚轮"铰链等实际尺寸"利用小千斤顶 在舱盖侧面及艏艉部对舱盖位置进行微调"直至符合图纸要 求"并将舱盖实际外周线划记在舱口围上# )&) 安装限位装置 图 ) $( 完成调整后将 6k"6E限位点焊安装"8) 及 8( 盖 6E限位
舱口盖安装通用工艺

舱口盖制造安装通用工艺一、适用范围1.本工艺适用于集装箱船的舱口盖制造安装工艺2.本工艺根椐舱口盖的设计要求编制,共分为三大部分;2.1 舱口盖制造工艺;2.2 折叠式舱口盖安装工艺;2.3 吊离式舱口盖安装工艺;在建造中除遵循本原则工艺外,还应满足施工图纸的具体要求。
二、工艺内容钢质货舱口盖是重要的船体舾装装置,它用来遮蔽舱口,保护舱内货物不受风浪、雨水的侵袭。
在船舶装卸货物时,能便于开启和关闭。
货舱口盖应具有足够的强度,以保证在规定的风浪或其他设定的负荷下不致变形,影响使用。
(一)舱口盖制造工艺1、舱口盖的主要技术要求1.1 舱口盖按照船级社认可的设计图纸制造。
1.2 舱口盖的建造及检验应满足船级社规范要求。
1.3 舱口盖的建造质量标准应满足船级社认可的《舱口盖制造公差及检测表要求》。
1.4 舱口盖本体材料及焊接材料应满足船级社规范要求。
2、钢质水密舱口盖制造2.1 原材料检验核查货舱口盖所用的原材料质量证书,并在原材料号料前抽查原材料的表面质量。
无论是号料前抽查或加工过程中发现材质数据不合格或表面质量不合格,检验员应及时制止该批材料设入生产或继续加工和组装。
2.2 钢材表面预处理2.2.1 舱口盖的钢材。
型材均应进行表面预处理。
2.2.2 钢材表面预处理等级符合Sa2.5级。
2.2.3 经表面预处理钢材.型材的牌号,规格,材料等应及时标注跟踪。
2.3 放样下料2.3.1 舱口盖放样采用计算机数学放样和少量的手工放样相结合。
2.3.2 舱口盖顶板,侧板,端板,纵.横梁腹板.面板,侧.端板面板,肘板采用数控切割下料,并且下料人员要仔细检查下料的尺寸,平整度是否符合图纸和技术精度要求,严格控制切割质量,不合格零件不准转入下道工序,所有零件的缺陷应修补,打磨,自由边打磨光顺,合格后方可转入下道工序。
2.3.3 为控制因焊接引起的收缩变形,确保纵横间距和舱口盖的几何尺寸。
放样时,横梁之间每档加放0.5~1.0mm,纵桁之间每档加放0.5~1.0mm焊接收缩量,下料及构件划线装配时相应作此处理。
折叠式装配式建筑的施工与折叠技术探究

折叠式装配式建筑的施工与折叠技术探究随着城市化进程的加快和人们对住房需求的增加,传统的建筑施工方式面临许多挑战。
而折叠式装配式建筑作为一种新型的建筑形式,具备了更快速、更经济、更环保的特点,因此在近年来得到了广泛关注和应用。
本文将探讨折叠式装配式建筑的施工过程以及其中涉及到的折叠技术。
一、折叠式装配式建筑施工过程1. 设计阶段:在设计阶段,需要根据项目需求进行详细规划,并确定建筑结构和参数。
这包括选择合适的材料、确定模块化尺寸等。
同时,在设计中需要考虑到整体结构稳定性和可持续性。
2. 制造与预制:折叠式装配式建筑通常采用先制造后组装的方法进行施工。
首先,各个组件会在生产线上进行预制,包括墙板、地板、屋顶等。
这些组件会通过机器人或自动化设备进行精确制作,以保证其质量和精度。
在制造过程中,折叠技术发挥了重要作用。
3. 运输与组装:预制完成后的建筑组件会通过运输工具送往施工现场。
由于折叠式装配式建筑采用模块化设计,因此运输过程相对更加简便。
在施工现场,各个组件会被组装成整体结构,并使用折叠技术进行连接。
4. 完善与预验收:在完成基本结构搭建后,需要进行内外部的完善工作。
这包括电器设备安装、水电线路铺设等。
随后对整体建筑进行预验收,并进行测试和调试,以保证其性能符合规范要求。
二、折叠技术的探究1. 材料选择:折叠式装配式建筑中使用的材料应具备一定的柔韧性和强度。
通常采用的是轻质钢材料和可塑性较好的复合材料,如钢板、玻璃纤维等。
这些材料能够在经历多次折叠后恢复原状,并且具备良好的防水防火性能。
2. 折叠连接方式:折叠连接方式是实现折叠式装配式建筑的核心技术之一。
目前主要采用的连接方式有机械连接和液压连接。
机械连接通过精密制作的零部件,使得组件能够在不同角度进行折叠和展开。
液压连接则通过液体的力量实现构件之间的可动性,从而达到折叠效果。
3. 折叠模式设计:在折叠式装配式建筑中,折叠模式设计是关键环节。
通过合理规划每个模块的运动轨迹、角度以及相互间的连贯性,确保整体建筑能够在折叠和展开过程中实现平稳转换。
浅析舱口盖结构的加工及安装

浅析舱口盖结构的加工及安装舱口盖是船舶或飞机等大型交通工具上的一个重要部件,其结构设计和加工安装至关重要。
本文将从舱口盖的结构设计、加工工艺和安装过程等方面进行浅析,希望能够为相关行业的从业人员提供一些参考和帮助。
一、舱口盖的结构设计舱口盖通常由复合材料、金属或者玻璃钢等材料制成,其结构设计需要考虑到舱口盖的功能、使用环境以及安全性等多方面因素。
舱口盖需要具有一定的强度和刚度,以保证在高速运行状态下能够承受住外部气流的冲击和压力。
舱口盖还需要具有一定的耐腐蚀性和耐磨损性,尤其是在海洋环境下船舶舷窗舱口盖需要能够抵挡海水的侵蚀和长时间的暴露。
舱口盖还需要具有一定的防火性能,以及能够承受住航海或飞行中的振动和冲击。
在舱口盖的结构设计中需要考虑到材料的选用、层压结构、铆钉、焊接等方面的设计。
二、舱口盖的加工工艺舱口盖的加工工艺主要包括材料成型、结构加固、表面处理和配件安装等过程。
1.材料成型舱口盖的材料成型通常采用复合材料制造工艺、玻璃钢模压工艺或者金属冲压工艺。
复合材料制造工艺是将预浸料经过模压、热固化等工艺形成舱口盖的整体结构,该工艺具有成型速度快、强度高、造型自由度大等特点。
而玻璃钢模压工艺则是将玻璃纤维增强塑料和树脂等材料通过模具压制成舱口盖的结构。
金属冲压工艺则是将金属板料通过冲裁、折弯、焊接等工艺制作成舱口盖的结构。
2.结构加固舱口盖的结构加固通常采用填充件、植入件、层压材料等方式进行,以增强其强度和刚度。
填充件是指在舱口盖内部填充密度适当的泡沫、木质芯等材料,以减轻重量和增加强度。
植入件则是将金属、复合材料等材料嵌入舱口盖的内部结构中,以增强整体的连接性和耐冲击性。
层压材料则是在舱口盖的外部表面覆盖一层特殊的复合材料,以增加其耐腐蚀性和防火性能。
3.表面处理舱口盖的表面处理通常包括喷涂、镀层、磨削、抛光等工艺,以保证其外观质量和耐候性。
喷涂是将特殊的防腐蚀漆或者特种涂料喷涂到舱口盖表面,以增加其耐腐蚀性和抗氧化性。
浅析舱口盖结构的加工及安装

浅析舱口盖结构的加工及安装
舱口盖是指飞机、火车、船舶等交通工具上用于关闭载货舱或驾驶舱口的盖子。
舱口盖具有重要的功能,可以保护货物或乘员免受外界环境影响,确保运输的安全。
舱口盖的加工过程主要包括设计、材料选择、制造和调试等步骤。
首先需要根据所需的盖子形状和尺寸进行设计,通常通过计算机辅助设计软件进行。
然后选择适合的材料用于制造舱口盖,常见的材料有铝合金、钢板等。
材料选择的关键因素包括重量、强度和耐腐蚀性能等。
接下来进行制造过程,包括下料、冲压、焊接、抛光等工序,最后进行调试和检验,确保舱口盖的质量达到要求。
舱口盖的安装也是一个重要的环节。
首先需要确定舱口盖的安装位置和方式,通常可以通过螺栓进行固定。
然后按照安装要求进行操作,包括清理安装位置、涂抹密封胶、对齐安装孔等。
在安装过程中需要注意舱口盖的平整度和密封性,确保盖子与舱口的契合度。
舱口盖在加工和安装过程中需要注意一些关键技术和要点。
首先是选用合适的材料,根据盖子的功能要求选择合适的材料,确保盖子的质量和性能。
其次是加工工艺的控制,特别是焊接和抛光等工序,需要严格控制温度和压力,以避免对材料造成损伤。
舱口盖的安装应该严格按照相关规范和要求进行,以确保盖子的稳固和密封性能。
舱口盖的加工和安装是一项复杂的工作,需要严格控制材料的选择和加工工艺,以确保舱口盖的质量和性能。
在安装过程中也需要注意盖子与舱口的契合度和密封性,以保证运输的安全和货物的质量。
舱口盖的安装工艺及控制要点

舱口盖的安装工艺及控制要点舱口盖的安装工艺及控制要点一.舱口盖的准备。
1. 检查舱口盖的基准线(中心线)及中间接缝的样冲标记;2. 检查舱口盖的中间铰链、端铰链、橡皮等附件的完整性;3. 检查舱口盖的直线度、平整度及四角水平。
二.舱口围的准备。
1. 舱口围的尺寸测量(对角线公差≤±10 mm允许±15 mm,长度公差±5 mm,允许±10 mm);2. 舱口围的面板倾斜度(±2 mm允许±3 mm);3. 舱口围的四角水平和平整度(±3 mm允许±5 mm);4. 建立舱口围表面的基准线(中心线MVP、垂直线CVP),将舱口围的端部及侧边等分;5. 建立舱口围表面舱口盖的定位线和轨道基准线,轨道基准线和中线平行且在轨道外侧。
三.舱口盖的定位。
1.在吊运和吊装舱口盖时,盖板必须得到保护,不能碰撞或损坏;2.从分离接缝开始(CVP线),将盖板尽可能精确地安放到舱口围正确的位置上,参考线距离要正确,参考标记要与舱口围上的相吻合;3.在盖板下垫12 mm或14 mm的铁板,“摆正”盖板后,检查规定的盖板伸出舱口围的尺寸,适当进行调节,使两端伸出部分相当;4.安装临时支承块,将盖板降到支承块上,并焊上临时固定铁板,以防盖板滑动;5.舱口盖定位好后,舱口围四个平面拉钢丝,测量出舱口盖和舱口围的平直度;6.初步测量出舱口盖边板底端到舱口围面板的间隙,记录数据,并计算出橡皮压缩量。
四.轨道的安装。
根据盖板的实际轨距和前面所述的定位基准线,临时安装轨道和斜轨道,同时要考虑到有关公差要求。
轨道平面倾斜度≤±1mm,轨道接头不允许有台阶,轨道只能点焊;五.端部铰链的安装。
1.按前面所述得定位基准线,作出与船体中心线平行的端部铰链基座的中心线;2.调整基座的高度和水平度,调正基座与船体结构加强的对应位置,控制焊接变形;3.调整舱口盖支承块间隙,必要时在盖板上压重物,支承块局部间隙≤±1.5mm,接触面要达到80﹪;4.调整铰链眼板的高度,可采用工艺假轴拉中心钢丝,对眼板进行焊前定位,铰链轴中心线必须与基准线平行和垂直,以实现根本的正常折叠,(船东要求,正常关闭状态下,销轴必须容易抽取)。
浅析舱口盖结构的加工及安装

浅析舱口盖结构的加工及安装舱口盖是指船舶、汽车或飞机等交通工具的货舱、发动机舱等部位的盖子,是保护货物或发动机的重要部件。
舱口盖结构的加工和安装对于交通工具的安全运行至关重要,下面我们就来浅析一下舱口盖结构的加工及安装。
一、舱口盖结构的加工1. 材料选择舱口盖一般采用轻型金属材料制作,如铝合金、镁合金等,这些材料轻质、耐腐蚀、具有较高的强度和刚度,非常适合用于舱口盖的加工制作。
2. 加工工艺(1) 切割:将所选材料根据图纸要求切割成相应形状的零件。
(2) 成型:利用压铸、模压等工艺将零件成型成舱口盖所需的形状。
(3) 表面处理:对成型后的舱口盖进行氧化、电镀、喷涂等表面处理,以增加其耐腐蚀性能。
(4) 加工:对舱口盖进行开孔、折弯等加工工艺,以便安装配件和连接零部件。
3. 质量控制舱口盖是交通工具的重要部件,因此在加工过程中需要严格控制质量,确保舱口盖具有良好的强度、刚度和密封性能。
同时需要进行外观检测,保证舱口盖外表面的光洁度和表面处理效果。
1. 安装前的准备工作在安装舱口盖之前,需要对舱口盖的安装位置进行检查和准备工作。
确保舱口盖的安装位置平整、清洁,并且无潜在的安全隐患。
2. 安装步骤(1) 将舱口盖提升至安装位置,并进行初步对位。
(2) 调整舱口盖的位置,使其与安装位置完全对齐。
(3) 使用螺栓、螺母等连接件将舱口盖牢固地固定在安装位置上。
(4) 进行最终的调整和检查,确保舱口盖安装牢固、位置正确,并且密封性良好。
3. 安装后的测试舱口盖安装完成后,需要进行相关的测试工作,例如密封性测试、抗风压测试等,以确保舱口盖安装后能够满足交通工具的使用要求。
总结:舱口盖是交通工具重要的保护部件,其结构的加工及安装对于交通工具的安全运行至关重要。
加工过程中需要严格控制质量,安装过程中需要进行严谨的操作,以确保舱口盖能够发挥其预期的功能。
希望本文对舱口盖结构的加工及安装有所帮助,谢谢。
- 1、下载文档前请自行甄别文档内容的完整性,平台不提供额外的编辑、内容补充、找答案等附加服务。
- 2、"仅部分预览"的文档,不可在线预览部分如存在完整性等问题,可反馈申请退款(可完整预览的文档不适用该条件!)。
- 3、如文档侵犯您的权益,请联系客服反馈,我们会尽快为您处理(人工客服工作时间:9:00-18:30)。
Internal Combustion Engine & Parts• 57•
折叠式舱口盖装配工艺简述
郭润平
(江苏润邦重工股份有限责任公司,南通226010)
摘要:本文介绍了折叠式舱口盖的装配工艺,以及如何在实际制造过程中去控制装配尺寸,以达到舱盖的最后尺寸全部在允许公 差之内。
关键词:舱口盖;装配工艺
1概述
折叠式舱口盖多用于散货船,起着密封、保护货物的
作用,它直接关系到货物运输过程中的安全。
折叠式舱口
盖附件比较多,比如端铰链、中铰链、油缸眼板、滚轮、限位
装置等等,尺寸精度要求高,水密性要求高,水平度及平行
度要求高均是制造难点,鉴于上述原因,如何在施工前消
化结构图,编制一套适合现场质量控制的装配工艺至关重
要,最终确保舱口改的整体完工建造质量。
2折叠式舱口盖详细节点的装配顺序及注意事项
2.1端铰链及油缸眼板小组装配
端铰链及油缸眼板是折叠式舱口盖重要的附件,一
般此结构要先制作成先行小组立,然后再安装在舱盖
上,统一调整装配在舱盖上的尺寸,此小组装配及要点
见图1。
2.2中铰链的装配
中铰链的装配一般是在中组装配母铰链,公铰链在总
装与之配装,同时要注意焊接的顺序,详见图2、图3。
作者简介:郭润平(1981-),男,山西朔州人,中级工程师,本科,开究方向为机械设计。
图5
2.5 滚轮座(WHEEL ARM)(图 6、图 7 )
3附件装配检验的控制
3.1此类型舱盖的附件安装较多,因此在装配前要控 制好主尺度,平行度,垂直度,同轴度,装配间隙,坡口角度 等。
精度示意详见图8。
3.2中铰链中心线与橡皮槽距离公差:±2mm(图9 )
3.3侧板上滚轮中心与橡皮槽距离公差:±2m m(图10
)
• 58 •
内燃机与配件
图6
图7
注:A 1/A 2/A 1,/A 2: B 1~B 4/B 1'~B 4,:偏差:±3m m C 1~C 2/C 1,~C 2, 偏差为±5m m
3.5中铰链及其他眼板同心度偏差最大倾斜度:/ 1000(图 12)
图8图
12
Internal Combustion Engine & Parts• 59•
带垫板环焊缝X射线检测工艺分析
郭优
(抚顺市特种设备监督检验所,抚顺113006 )
摘要:带有垫板环焊缝的焊接难度较大,在焊接过程中如果处理不当极易造成焊接质量不合格。
为了有效地检测环焊缝的焊接质 量,可以将X射线检测技术应用于带垫板环焊缝的质量检测中,本文对垫板焊缝在底片上的影像进行了比较深入的分析研究,在此 基础上,论述了恰当的射线检测工艺能够有效提高环焊缝的检测质量,确保焊接部件的焊接质量符合要求,对于从事相关检验检测工 作的技术人员具有一定的借鉴意义。
关键词:带垫板环焊缝;X射线检测;缺陷影像
0引言
在压力容器的制造过程中,由于直径和组装工艺造成 部分压力容器无法进行双面焊接,而只能采取单面焊接的 方式。
为了保证焊接质量符合要求以及容器内部免受污 染,在筒体之间、筒体和封头之间、接管与接管之间进行组 焊时,一般会采取增加垫板的方式进行单面焊接,其焊接 接头如图1所示。
在进行组焊时,首先要把垫板的一半紧贴在筒体、封 头或者接管的内侧,并进行适当的点焊确保焊接过程稳 固。
再将筒体、封头或者接管的另一半套进去,调整到准确 的位置后即可进行对接焊接。
采取这种焊接方式,会受到 焊材受力不均、垫板和筒体以及接管的圆度存在差异等因 素的影响,极易造成焊缝间隙过大,进而影响到实际的焊 接质量。
由于垫板的影响增加了环焊缝X射线的检测难度,
作者简介:郭优(1985-),女,天津人,研究生,毕业于东北大学,工程师,研究方向为特种设备。
造成缺陷的检测率大大降低,会给压力容器的后期使用埋 下安全隐患。
因此必须运用专用的射线检测技术进行检 测,以提高危害性缺陷的检出率。
1垫板焊缝在底片上的影像
采用X射线对带垫板的环焊缝进行扫描时,所形成 的影像一般是多条连续或间断的黑色影像,呈一定的规 律性分布,能够较简单的辨别出。
在X射线底片上的是 一条直线,能够形成这种影像的缺陷主要有内咬边、内表 面气孔或者夹渣、焊缝根部裂纹以及未焊透等。
其中,环焊缝的根部裂纹和未焊透缺陷在X射线底片上能够形 成具有一定规律的影像,前者主要表现为较细的锯齿状 或者直线状,后者主要表现为规则的直线状,且通常情况 下缺陷的黑度比较均匀。
环焊缝的内咬边和内表面气孔 所形成的X射线影像一般情况下没有明显的规律,并且 其黑度也并不均匀,尤其是靠近母材的影像,没有呈现出 任何的规律性。
2射线检测技术要求及缺陷识别
2.1应力过大造成的影响
在对带垫板的环焊缝进行焊接时,两部分进行组焊会 受到外界较大的应力,尤其是对筒体的卷圆的焊接。
对于 强度较高的合金钢,处于焊缝热影响区内部的板材和T型接头的纵焊缝处受到的应力较大,极易造成裂缝的出现。
由于在焊接过程中增加了垫板,就会造成其透照厚度差较 大,如果仍采用一般的探伤工艺对环焊缝进行探伤就会造 成母材的黑度过高,而焊缝的黑度相对较低,这就会严重
3.6侧板上的滚轮之间间距偏差:±3mm,垂直度偏 差:3/1000(图 13)4小结
综上所述,一般的折叠式舱盖均可按照上述装配工 艺来制作,我厂安装上述装配制作工艺制作舱
□盖,均能确保精度要求。
当然,舱盖制作工艺
还有很多,我们要持续不断去改进生产装配工
艺,不断的为提高生产效率,降低生产成本而
努力。
参考文献:
[1]唐广概.57000 DWT散货船折叠式舱□盖安装
技术广东造船,2010(05).
[2]唐广概.吊离式改装为折叠式舱□盖技术研究
J].广东造船,2017(01)
.。