管道检测机器人_毕设论文
管道检测机器人的运动学建模【论文】

管道检测机器人的运动学建模摘要:本文针对管道检测问题,首先介绍了管道检测机器人的系统组成,在此基础上,根据真实的圆柱形管道,推到了单个轮子在管道曲面上满足纯滚动和无侧滑条件下轮心速度的数学描述。
此外,根据机器人在圆管中的几何约束,建立了姿态坐标和空间位置坐标之间的关系,最终完成了管道机器人的运动学建模。
关键词:管道;检测机器人;运动约束;运动学模型.引言管道是当前普遍采用的一种油气输送方式[1]。
长时间使用过程中受腐蚀、重压等作用影响,管道不可避免地会出现裂纹、变形等现象,影响生产安全。
由于管道环境极其恶劣,很多检测工作是人工无法完成的,管道检测机器人则成为一种非常必要的检测设备[2-4]。
管道检测机器人集成有多种检测仪器,可以自主或人为地沿着管线进行工况检测工作。
本文介绍了管道检测爬行机器人的组成,建立了管道约束下机器人的运动学建模,为后续的设计分析提供理论指导。
一、管道机器人总体组成为了满足管道检测的工作要求,管道检测机器人应具有良好的定心性、较高的越障能力、良好的通过性、较大的驱动输出特性和较高的驱动效率等特性。
本文所述机器人的系统组成如图1所示,各部分的组成及功能如下:图 1. 机器人系统组成1.机器人本体机器人本体是指机器人进入管道内的移动作业部分,载体为四轮双驱动方式。
本体内部承载有电机驱动、通讯、控制等设备,可以实现本体的前进、后退、左转、右转等动作并且具有防水、耐压、耐腐蚀等功能。
2.电力供给系统根据机器人的供电需求,电力供给方案采用外部光电复合缆直流供电,该直流电来自上位机控制箱的开关电源将交流电转换为直流电、AC/DC 转换及多路输出,实现机器人工作的电力需求。
3.扫描仪云台系统将二维激光扫描仪安装在由电机驱动的旋转轴上就可以实现对管道的三维扫描,将扫描到的管道点云,通过坐标变换、ICP算法等实现管道的三维重建。
扫描仪云台的高度也可以实现自动调节。
4.摄像头云台系统摄像头云台系统携带有可自动变焦的CCD摄像机[5],摄像头运动由两个电机驱动:旋转电机和俯仰电机,能实现摄像头的整周旋转和俯仰运动,从而完成CCD对被检测管道的全方位的视角调整能力。
管道履带式机器人毕业论文
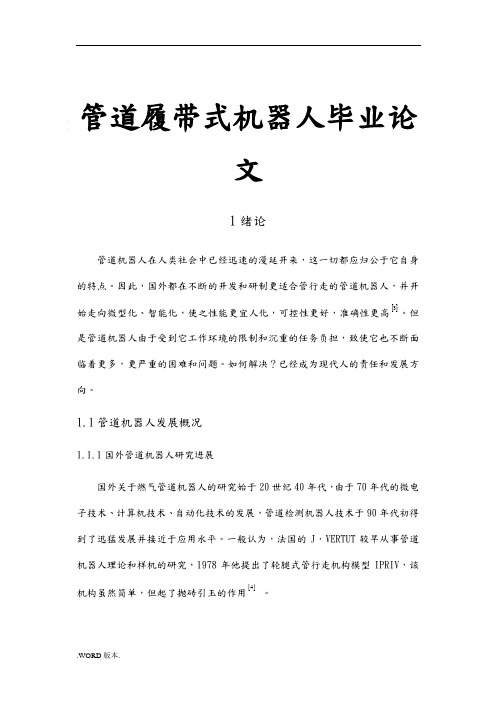
管道履带式机器人毕业论文1绪论管道机器人在人类社会中已经迅速的漫延开来,这一切都应归公于它自身的特点。
因此,国外都在不断的开发和研制更适合管行走的管道机器人,并开始走向微型化、智能化,使之性能更宜人化,可控性更好,准确性更高[]3。
但是管道机器人由于受到它工作环境的限制和沉重的任务负担,致使它也不断面临着更多,更严重的困难和问题。
如何解决?已经成为现代人的责任和发展方向。
1.1管道机器人发展概况1.1.1国外管道机器人研究进展国外关于燃气管道机器人的研究始于20世纪40年代,由于70年代的微电子技术、计算机技术、自动化技术的发展,管道检测机器人技术于90年代初得到了迅猛发展并接近于应用水平。
一般认为,法国的J.VERTUT较早从事管道机器人理论和样机的研究,1978年他提出了轮腿式管行走机构模型IPRIV,该机构虽然简单,但起了抛砖引玉的作用[]4。
日本机器人的发展经过了60年代的摇篮期,70年代的实用期,到80年代进入普及提高期,开始在各个领域广泛推广使用机器人。
日本管道机器人众多,东京工业大学航空机械系Shigeo Hirose和Hidetaka Ohno等于1993年开始研究管道机器人,先后研制成功适用于直径50mm管道的Thes-Ⅰ、Thes-Ⅱ型管道机器人和适用于直径150mm管道的Thes-Ⅲ型管道机器人。
Thes-Ⅰ型管道机器人的主要特点是轮子的倾斜角可以随着阻力大小的改变而改变,当机器人的负载较大时,轮子的倾斜角将产生变化,从而减小行走速度,增加推进力。
Thes-Ⅱ型管道机器人的总长为300mm,质量只有3l0g。
Thes-Ⅱ型管道机器人的每一节机器人单元的左右两侧分别布置着由弹簧板支撑的一对轮子,轮子由带减速齿轮箱的电动机驱动,从而实现机器人在管道中的前进和后退运动,Thes-Ⅱ型管道机器人可以很容易地在带有几个弯管接头的管道中运动。
Thes-Ⅲ型管道机器人如图1-1所示,其采用“电机一蜗轮蜗杆一驱动轮”的驱动方案,同时每个驱动轮都有一个倾斜角度测量轮,通过测量轮探测机器人的倾斜角度,并反馈给电机从而保证管道机器人的驱动轮以垂直的姿态运动。
地下管道检测机器人设计论文

一、地下管道检测机器人发展现状按照行走机构的类型,可将管内作业机器人行走机构分为轮式、履带式、蠕动式等几类。
轮式行走机构图1(a)轮式行走机构轮式机构管内作业机器人的基本形式如图1(a)所示。
对此类机器人的研究相对较多。
机器人在管内的运动,有直进式的(即机器人在管内平动),也有螺旋运动式的(即机器人在管内一边向前运动,一边绕管道轴线转动);轮的布置有平面的,也有空间的。
一般认为,平面结构的机器人结构简单,动图1(b)自来水管道检测轮式机器人作灵活,但刚性、稳定性较差,而空间多轮支撑结构的机器人稳定性、刚性较好, 但对弯管和支岔管的通过性不佳。
图1(b)为英国的PEARPOINT有限公司开发的自来水管道检测轮式机器人,可在以φ135~375mm的管径内直线行走,行走速度为0~12m/min。
履带式行走机构图2(a)履带式行走机构图2(b)海水管道检测履带式机器人图2(a)是履带式行走机构的基本形式。
这种类型的管内机器人在油污、泥泞、障碍等恶劣条件下达能到良好的行走状态,但由于结构复杂,不易小型化,转向性能不如轮式载体等原因,此类机器人应用较少。
图2(b)是日本关西电力株式会社开发的适用于管径Φ288~388mm、管长100m的海水管道检查履带式机器人,该机器人通过沿径向分布的履带在水平管和垂直管内自主行走,移动速度为5m/min。
整个地下输气管道检测维修用移动机器人系统由三大部分组成:(1)履带式移动机器人。
机器人小车上装有CCD摄像机,并可根据需要加挂其它检测单元。
(2)圆盘式收放线装置。
移动机器人通过电缆进行控制,视觉等信号也通过该线缆传输到控制计算机。
(3)控制单元。
其主体为一台工业控制计算机,负责整个机器人系统的控制、显示及信息存储等工作。
操作人员通过界面完成所有操作。
控制单元与收放线装置安装在一个专门设计的手推车体上,便于移动。
蠕动式行走机构图3 蠕动式行走机构蠕动式行走机构如图3所示。
毕业设计-管道检测作业机器人(总体设计)
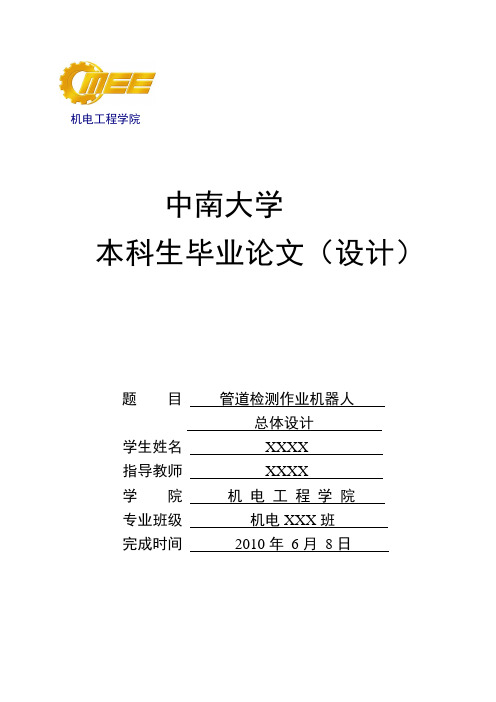
机电工程学院中南大学本科生毕业论文(设计)题目管道检测作业机器人总体设计学生姓名XXXX指导教师XXXX学院机电工程学院专业班级机电XXX班完成时间2010年6月8日中南大学毕业论文(设计)任务书毕业论文(设计)题目管道检测作业机器人总体设计题目类型]1[工程设计题目来源[1]___教师科研题毕业论文(设计)时间从2010年3 月1 日至2010年6 月8 日毕业论文(设计)内容要求:(1)技术指标:(a)自适应管道直径为270-300mm,驱动力>800N;(b)在管道内的移动速度大于10cm/s;(c)能通过曲率半径600mm,总长为10m的倒U型管道;(4)能够搭载微型CCD和无损检测传感器对管道内的裂纹和腐蚀缺陷等进行检测与修补作业。
(2)完成总体方案设计、总体布局和结构确定,行走机构原理设计、控制电机选型等。
(3)要求具有电缆控制和遥控两种功能。
完成传感检测原理与检测作业功能装置设计与控制系统方案。
1.具体完成下列设计工作:(1)查阅文献和实习,了解国内外管道检测作业机器人的现状和发展趋势,并翻译相关资料一篇;(2)按要求完成管道检测作业机器人功能设计与总体方案设计;(3)完成管道检测作业机器人总体布局、结构设计计算与行走方式确定;(4)完成传感检测系统方案、传感器选型与检测功能布置设计;(5)整理相关资料,撰写设计说明书。
要求设计图纸不少于4张1#图,设计说明书不少于50 页。
[1]题目类型:(1)理论研究(2)实验研究(3)工程设计(4)工程技术研究(5)软件开发[2]题目来源:(1)教师科研题(2)生产实际题(3)其它2.主要参考资料1)成大先主编.机械设计手册.北京:化学工业出版社,20022)刘政华,何将三.机械电子学.长沙:国防科技大学出版社,1999.103)杨培元,朱福元主编. 液压系统设计简明手册. 北京:机械工业出版社,19944)《电气工程师手册》第二版编辑委员会编. 电气工程师手册. 北京:机械工业出版社,20005)沈红卫编著. 单片机应用系统设计实例与分析. 北京:北京航空航天大学出版社,20036)黄菊生编著. 单片机原理与接口技术. 北京:国防工业出版社,20073.毕业论文(设计)进度安排指导教师(签名)____________ 时间:__________________系(所)主任(签名) ____________ 时间:_________________主管院长(签名)______________ 时间:__________________中南大学毕业论文(设计)成绩评定表(一)指导教师评语XXX同学在毕业设计过程中,态度较积极主动,工作较扎实认真,较好地完成了毕业设计任务书规定的工作任务——管道检测机器人总体设计。
(智能制造)论文正文管道履带式机器人
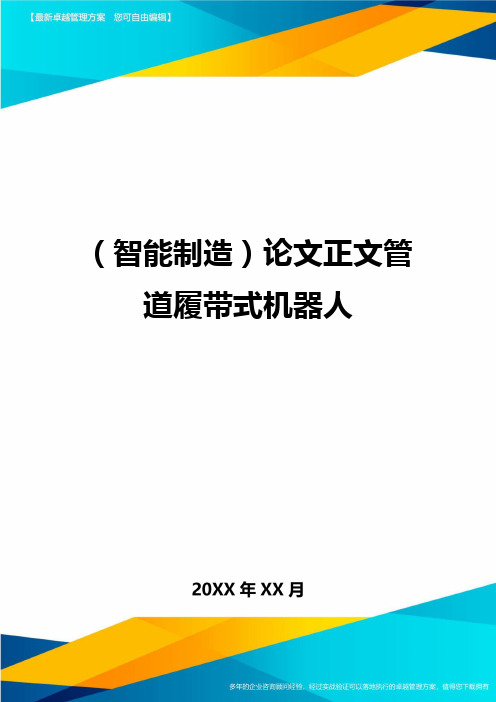
(智能制造)论文正文管道履带式机器人管道射线探伤机器人结构设计前言油气管道输送是与铁路、公路、水运、航运并列的五大运输行业之一,长输油气管道作为一种特殊设备广泛应用于石油、石化、化工等工业领域以及城市燃气系统中,在国民经济中占有重要地位。
随着“开发大西部”以及“西气东输”的战略指导方针,长输油气管道的数量在不断增加。
由于历史原因,国内在役长输油气管道中部分管材制管质量较差,加上施工建设过程中存在部分焊接缺陷和涂层缺陷,这给管道的安全运行埋下隐患,即使部分投产验收合格的管道,在运行过程中也难免受到介质、温度、疲劳、腐蚀、局部载荷等因素影响,服役一段时间后产生缺陷或导致缺陷扩展,并可能最终发生失效,给人民生命财产、工业生产和社会稳定构成威胁。
如何检测发现管道缺陷,事前对含缺陷管道进行评价和预测(含缺陷管道的剩余强度评价,含缺陷管道的剩余寿命预测),确保在役油气长输管道安全可靠运行是目前世界各国普遍关注和迫切需要解决的重大课题。
由于在前面所述的一般工业、石油天然气、军事装备等领域中,管道作为一种有效的物料输送手段而广泛应用。
为提高管道的寿命、防止泄漏等事故的发生,就必须对管道进行有效的检测维护等。
而目前管道检测和维护多采用管道机器人来进行。
所谓管道机器人就是一种可沿管道内部或外部自动行走、携带一种或多种传感器件如位置和姿态传感器、超声传感器、涡流传感器等以及操作机械如管道裂纹与管道接口焊接装置、防腐喷涂装置、操作手、喷枪、刷子等。
在工作人员的遥控操纵或计算机控制下可在极其恶劣的环境中.能够完2成一系列管道检测维修作业的机电一体化系统。
管道机器人可完成的管道作业有:生产、施工过程中的管道内外质量检测;管道内部清扫、抛光、焊接、喷涂等维护;对接焊缝的探伤、补口作业;旧管道腐蚀程度、破损情况检测和泄漏预报等等。
基于目前管道探伤机器人的研究现状,本课题主要研究目的是通过对管道X射线无损检测探伤机器人设计,及相关技术的查阅和应用,能够研制一台具有良好的弯道通过能力、视觉定位能力并能适应较长距离检测作业的实用样机。
管道清洗机器人_毕业论文
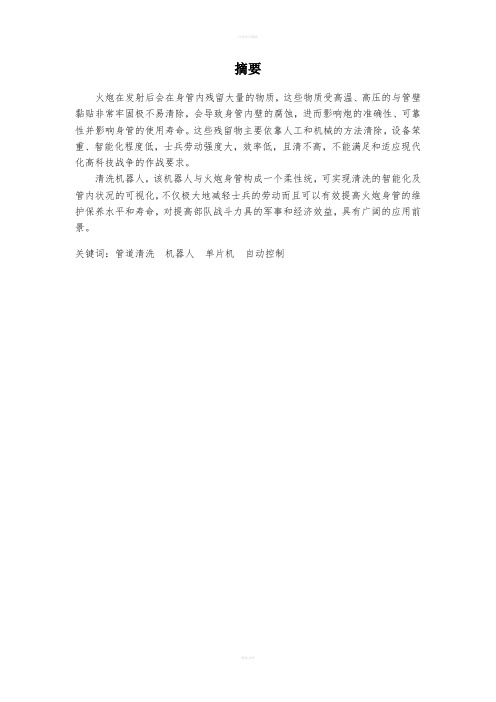
摘要火炮在发射后会在身管内残留大量的物质,这些物质受高温、高压的与管壁黏贴非常牢固极不易清除,会导致身管内壁的腐蚀,进而影响炮的准确性、可靠性并影响身管的使用寿命。
这些残留物主要依靠人工和机械的方法清除,设备笨重、智能化程度低,士兵劳动强度大,效率低,且清不高,不能满足和适应现代化高科技战争的作战要求。
清洗机器人,该机器人与火炮身管构成一个柔性统,可实现清洗的智能化及管内状况的可视化,不仅极大地减轻士兵的劳动而且可以有效提高火炮身管的维护保养水平和寿命,对提高部队战斗力具的军事和经济效益,具有广阔的应用前景。
关键词:管道清洗机器人单片机自动控制AbstractDue to high temperature and pressure, the remaining substances in the bore after the gun is launched will adhere to the bore firmly and can't be removed easily, which will result in erosion of the bore and have an impact on the veracity and reliability of the gun launching as well as its operating life. These substances are removed with manual and mechanical cleaning mainly, which can't meet and accommodate with the campaign need of modernization high-tech wars because of unwieldy equipment, low intelligentization, over laboring intension of soldiers, low efficiency and cleaning extent.Robot and bore achieves in intelligentization of cleaning and visualization of inner bore, which not only greatly lessens laboring tension of soldiers, but advances maintenance level and operating life of bore as well. It is of bright future in expansive application and of great military and economic benefit in enhancing battle effectiveness of the army.Key words: bore cleaning; robot;single chip microcomputer;automationAbstract (II)第一章绪论 (1)1.1课题研究背景及关键技术 (1)1.1.1课题的研究背景 (1)1.1.2课题的关键技术 (2)1.2国内外管道机器人的研究现状和发展方向 (3)1.2.1管道机器人的研究现状 (3)1.2.2管道机器人的发展方向 (5)1.3课题的研究意义 (5)第二章炮管擦洗机器人总体方案设计 (7)2.1需求分析与设计思路 (7)2.2移动功能模块设计 (8)2.2.1运动方式分析与选择 (8)2.2.2自适应机构设计 (9)2.3擦洗功能模块设计 (11)2.3.1炮膛擦洗过程分析与研究 (11)2.3.2轴向往复式擦洗头设计 (11)2.4控制功能模块设计 (13)2.4.1主控制系统 (13)2.4.2传感器 (13)2.4.3驱动系统 (13)第三章管道清洗机器人详细设计 (15)3.1移动功能模块设计与分析 (15)3.1.1传动机构设计 (15)3.1.2连接件设计 (16)3.2擦洗功能模块的设计 (18)3.2.1旋转式清洗头设计 (18)3.3控制系统的设计 (18)3.3.1主控制芯片 (19)3.3.2 ATmega128介绍 (20)3.3.3电机控制技术 (21)3.4最小系统电路设计 (23)3.4.1时钟/复位模块设计 (23)3.4.2电源模块设计 (23)3.5人机接口电路设计 (24)3.5.1 LCD显示模块 (24)3.5.2键盘电路 (25)3.5.3蜂鸣器电路 (25)3.5.4串口通信模块 (26)3.6电机控制电路设计 (26)第四章系统软件设计 (28)4.1系统软件架构 (28)4.1.1 PWM调速程序设计 (28)结论 (31)5.1论文总结 (31)5.2工作展望 (31)参考文献 (32)附录 (34)第一章绪论1.1课题研究背景及关键技术1.1.1课题的研究背景现代国防工业日新月异,武器装备制造及维护的技术水平直接决定了国家的军事实力。
管道检测机器人_毕业设计
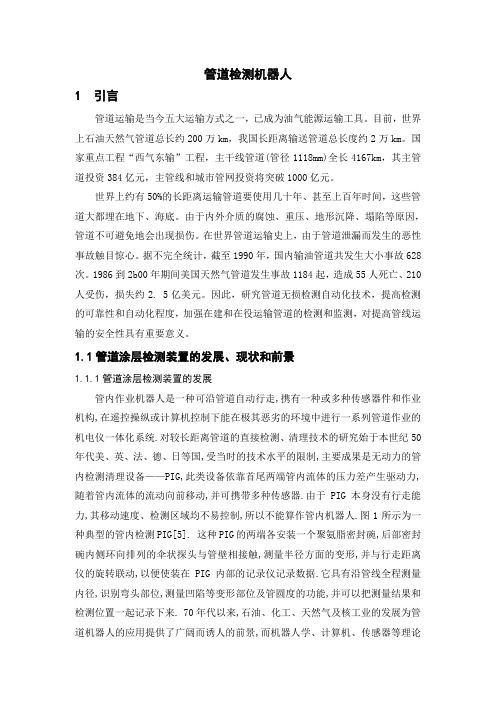
管道检测机器人1 引言管道运输是当今五大运输方式之一,已成为油气能源运输工具。
目前,世界上石油天然气管道总长约200万km,我国长距离输送管道总长度约2万km。
国家重点工程“西气东输”工程,主干线管道(管径1118mm)全长4167km,其主管道投资384亿元,主管线和城市管网投资将突破1000亿元。
世界上约有50%的长距离运输管道要使用几十年、甚至上百年时间,这些管道大都埋在地下、海底。
由于内外介质的腐蚀、重压、地形沉降、塌陷等原因,管道不可避免地会出现损伤。
在世界管道运输史上,由于管道泄漏而发生的恶性事故触目惊心。
据不完全统计,截至1990年,国内输油管道共发生大小事故628次。
1986到2b00年期间美国天然气管道发生事故1184起,造成55人死亡、210人受伤,损失约2. 5亿美元。
因此,研究管道无损检测自动化技术,提高检测的可靠性和自动化程度,加强在建和在役运输管道的检测和监测,对提高管线运输的安全性具有重要意义。
1.1管道涂层检测装置的发展、现状和前景1.1.1管道涂层检测装置的发展管内作业机器人是一种可沿管道自动行走,携有一种或多种传感器件和作业机构,在遥控操纵或计算机控制下能在极其恶劣的环境中进行一系列管道作业的机电仪一体化系统.对较长距离管道的直接检测、清理技术的研究始于本世纪50年代美、英、法、德、日等国,受当时的技术水平的限制,主要成果是无动力的管内检测清理设备——PIG,此类设备依靠首尾两端管内流体的压力差产生驱动力,随着管内流体的流动向前移动,并可携带多种传感器.由于PIG本身没有行走能力,其移动速度、检测区域均不易控制,所以不能算作管内机器人.图1所示为一种典型的管内检测PIG[5]. 这种PIG的两端各安装一个聚氨脂密封碗,后部密封碗内侧环向排列的伞状探头与管壁相接触,测量半径方面的变形,并与行走距离仪的旋转联动,以便使装在PIG内部的记录仪记录数据.它具有沿管线全程测量内径,识别弯头部位,测量凹陷等变形部位及管圆度的功能,并可以把测量结果和检测位置一起记录下来. 70年代以来,石油、化工、天然气及核工业的发展为管道机器人的应用提供了广阔而诱人的前景,而机器人学、计算机、传感器等理论和技术的发展,也为管内和管外自主移动机器人的研究和应用提供了技术保证.日、美、英、法、德等国在此方面做了大量研究工作,其中日本从事管道机器人研究的人员最多,成果也最多。
【论文】管道检测机器人结构设计及运动仿真

摘 要管道检测机器人主要包括三大系统:机械系统、控制系统和检测系统。
本文在分析了机器人总体机械结构和检测原理的基础上,通过精确的力学计算和细致的结构分析,利用AutoCAD软件对机器人的机械部分,包括整体结构、电机、齿轮、轴等进行了选择与设计,并对设计方案进行分析与计算。
然后利用Solid Edge软件将管道检测机器人的总体机械结构绘制成三维立体模型。
所设计的机器人机械系统,可通过履带式移动机构满足城市排水管道的工况,并通过加装支撑臂进行30度的爬坡。
通过细致研究,确定了机器人所使用的摄像系统和超声波检测系统。
关键词:排水管道,履带式机器人,超声波无损检测AbstractA pipeline inspection robot mainly consists of three parts, the mechanical system, the control system and the detecting system. This paper, based on the analysis of overall mechanical structure and detecting principle of the robot, by accurate mechanical calculation together with comprehensive structure analysis, the author has worked out a unique design for overall structure in AutoCAD software, motor, gears as well as axles of the robot, and the design scheme has been analyzed and calculated. Then built overall mechanical structure of pipeline inspection robot 3-D models in Solid Edge software. The design of mechanical system of the pipeline inspection robot is equipped with the tracked mobile mechanism moves along the urban drainage pipelines and two support arms can climb maximum gradient of 30 degrees. And after careful study, the camera system and the ultrasonic inspection system of the robot are also determined in the paper.Key words: Drainage pipeline, Tracked robot, Ultrasonic nondestructive inspection目 录第一章 绪 论 (1)1.1课题研究意义及背景 (1)1.2管道检测机器人的发展 (3)1.2.1管道检测机器人发展情况 (3)1.2.2 管道检测机器人类型介绍 (7)1.3管道检测机器人的技术 (9)1.4 课题研究主要内容 (9)1.5本章小结 (10)第二章 管道检测机器人机械结构设计方案确定 (11)2.1管道检测机器人移动方式结构设计 (11)2.1.1管道检测机器人移动方式分析比较 (11)2.1.2管道检测机器人移动方式选择 (13)2.2管道检测机器人总体机械结构设计 (14)2.3本章小结 (15)第三章 管道检测机器人机械结构设计计算 (16)3.1 管道检测机器人力学分析计算 (16)3.2 管道检测机器人执行机构设计 (18)3.2.1传动齿轮的设计计算 (18)3.2.2传动轴的设计计算 (25)3.3 管道检测机器人驱动系统设计 (29)3.3.1步进电机的选择 (31)3.4 本章小结 (33)第四章 管道检测机器人附属配置 (35)4.1能源供给方式的选择 (35)4.2 摄像系统的选择 (35)4.3检测系统的选择 (36)4.4电源装置的选择 (38)4.5控制装置的选择 (38)III4.6本章小结 (38)第五章 管道检测机器人三维模型设计 (39)5.1移动机构三维模型设计 (39)5.2 支撑臂机构三维模型设计 (41)5.3车体结构三维模型设计 (41)5.3.1车体内部结构三维模型设计 (41)5.3.2车体上方结构三维模型设计 (42)5.3.3车体前方结构三维模型设计 (43)5.4整体结构三维模型设计 (43)5.5本章小结 (45)第六章 管道检测机器人稳定性分析 (46)6.1承载能力 (46)6.2检测系统 (47)6.3质量优化 (47)6.4本章小结 (48)第七章 经济技术分析报告 (49)第八章 总结与展望 (50)8.1总结 (50)8.2展望 (50)参考文献 (52)致 谢 (54)声 明 (55)IV第一章 绪 论1.1 课题研究意义及背景近年来,随着我国经济的快速发展,城市发展的步伐也逐渐加快,煤气、输水、油气、通讯、化工以及其他用途的管道急剧增加。
- 1、下载文档前请自行甄别文档内容的完整性,平台不提供额外的编辑、内容补充、找答案等附加服务。
- 2、"仅部分预览"的文档,不可在线预览部分如存在完整性等问题,可反馈申请退款(可完整预览的文档不适用该条件!)。
- 3、如文档侵犯您的权益,请联系客服反馈,我们会尽快为您处理(人工客服工作时间:9:00-18:30)。
1 引言管道运输是当今五大运输方式之一,已成为油气能源运输工具。
目前,世界上石油天然气管道总长约200万km,我国长距离输送管道总长度约2万km。
国家重点工程“西气东输”工程,主干线管道(管径1118mm)全长4167km,其主管道投资384亿元,主管线和城市管网投资将突破1000亿元。
世界上约有50%的长距离运输管道要使用几十年、甚至上百年时间,这些管道大都埋在地下、海底。
由于内外介质的腐蚀、重压、地形沉降、塌陷等原因,管道不可避免地会出现损伤。
在世界管道运输史上,由于管道泄漏而发生的恶性事故触目惊心。
据不完全统计,截至1990年,国内输油管道共发生大小事故628次。
1986到2b00年期间美国天然气管道发生事故1184起,造成55人死亡、210人受伤,损失约2. 5亿美元。
因此,研究管道无损检测自动化技术,提高检测的可靠性和自动化程度,加强在建和在役运输管道的检测和监测,对提高管线运输的安全性具有重要意义。
1.1管道涂层检测装置的发展、现状和前景1.1.1管道涂层检测装置的发展管内作业机器人是一种可沿管道自动行走,携有一种或多种传感器件和作业机构,在遥控操纵或计算机控制下能在极其恶劣的环境中进行一系列管道作业的机电仪一体化系统.对较长距离管道的直接检测、清理技术的研究始于本世纪50年代美、英、法、德、日等国,受当时的技术水平的限制,主要成果是无动力的管内检测清理设备——PIG,此类设备依靠首尾两端管内流体的压力差产生驱动力,随着管内流体的流动向前移动,并可携带多种传感器.由于PIG本身没有行走能力,其移动速度、检测区域均不易控制,所以不能算作管内机器人.图1所示为一种典型的管内检测PIG[5]. 这种PIG的两端各安装一个聚氨脂密封碗,后部密封碗内侧环向排列的伞状探头与管壁相接触,测量半径方面的变形,并与行走距离仪的旋转联动,以便使装在PIG内部的记录仪记录数据.它具有沿管线全程测量内径,识别弯头部位,测量凹陷等变形部位及管圆度的功能,并可以把测量结果和检测位置一起记录下来. 70年代以来,石油、化工、天然气及核工业的发展为管道机器人的应用提供了广阔而诱人的前景,而机器人学、计算机、传感器等理论和技术的发展,也为管内和管外自主移动机器人的研究和应用提供了技术保证.日、美、英、法、德等国在此方面做了大量研究工作,其中日本从事管道机器人研究的人员最多,成果也最多。
图1管内检测典型PIG样机在已实现的管内作业机器人中,按照其行动方式可分为轮式、履带式、振式、蠕动式等几类:(1) 轮式管内机器人由于轮式驱动机构具有结构简单,容易实现,行走效率高等特点,对此类机器人的研究比较多.机器人在管内的运动,有直进式的(即机器人在管内平动)也有螺旋运动式的(即机器人在管内一边向前运动,一边绕管道轴线转动);轮的布置有平面的,也有空间的.一般认为,平面结构的机器人结构简单,动作灵活,但刚性、稳定性较差,而空间多轮支撑结构的机器人稳定性、刚性较好,但对弯管和支岔管的通过性不佳.轮式载体的主要缺点是牵引力的提高受到封闭力的限制.图2所示为日本的M.Miura等研制的轮式螺旋推进管内移动机器人。
(2) 履带式管内机器人履带式载体附着性能好,越障能力强,并能输出较大的牵引力.为使管内机器人在油污、泥泞、障碍等恶劣条件下达到良好的行走状态,人们又研制了履带式管内机器人.但由于结构复杂,不易小型化,转向性能不如轮式载体等原因,此类机器人应用较少.图2所示为日本学者佐佐木利夫等研制的履带式管内移动机器人[13],其驱动轮可变角度以适应管径的变化,可通过圆弧过渡的90度弯管.图2轮式螺旋推进管内移动机器人总体结构图图3 轮式螺旋推进管内移动机器人驱动系统图(3) 振动式管内机器人振动可以使物体的位置改变,根据这一原理,日本学者森光武则等提出了的振动式管内移动机器人。
其原理为:在机器人的外表面装有若干与机体成一定角度的弹性针,靠弹性针的变形使其压紧在管壁上.机身内装有偏心重物,由电机驱动.当偏心重物旋转时,离心力使弹性针变形,滑动,从而带动机器人移动.振动式管内机器人结构简单,容易小型化,但行走速度难以控制,而且振动使机器人沿圆周方向自转,姿态不稳定,另外,振动对传感器的工作和寿命均会产生影响.(4) 蠕动式管内机器人参考蚯蚓、毛虫等动物的运动,人们研制了蠕动式管内机器人。
其运动是通过身体的伸缩(蠕动)实现的:首先,尾部支承,身体伸长带动头部向前运动,然后,头部支承,身体收缩带动尾部向前运动,如此循环实现机器人的行走.图3所示为日本日历制作所研制的蠕动式管内机器人,其前后两部分各有8条气缸驱动的可伸缩支撑足,中部有一气缸作为蠕动源。
国内在管道机器人方面的研究起步较晚,而且多数停留在实验室阶段。
哈尔滨工业大学邓宗全教授在国家863”计划课题“X射线检测实时成像管道机器人的研制”的支持下,开展了轮式行走方式的管道机器人研制,如图3所示。
该机器人具有以下特点: (1)适应大管径(大于或等于900mm)的管道焊缝X射线检测。
(2)一次作业距离长,可达2km。
(3)焊缝寻址定位精度高为±5mm。
(4)检测工效高,每道焊缝(900mm为例)检测时间不大于3min;实现了管内外机构同步运动作业无缆操作技术, 并研制了链式和钢带式两种新型管外旋转机构,课题研究成果主要用于大口径管道的自动化无损检测[8]。
上海大学研制了“细小工业管道机器人移动探测器集成系统”。
其主要包含20mm内径的垂直排列工业管道中的机器人机构和控制技术(包括螺旋轮移动机构、行星轮移动机构和压电片驱动移动机构等)、机器人管内位置检测技术、涡流检测和视频检测应用技术,在此基础上构成管内自动探测机器人系统。
该系统可实现20mm管道内裂纹和缺陷的移动探测[9]。
图4 蠕动式管内移动机器人1.1.2测量方法的研究进展按有无破坏性,表面涂镀层厚度测试方法可分为有损检测和无损检测。
有损检测方法主要有计时液流测厚法、溶解法、电解测厚法等,这种方法一般比较繁琐,主要用于实验室。
目前也有便携式测厚仪,适合在现场使用。
常用的无损检测方法有库仑-电荷法、磁性测厚法、涡流测厚法、超声波测厚法和放射测厚法等,各种无损测厚法均有成型的仪器设备,使用起来方便简单,且无需对表面涂镀层进行破坏[1]。
因此,该类方法在管道涂层的测量中已得到了广泛的应用。
常用的无损涂层测量方法有磁性测厚﹑电涡流测厚﹑磁性/涡流测厚﹑超声波测厚等(1)磁性测厚磁性测厚法可分为2 种:磁吸力测厚法和磁感应测厚法。
磁吸力测厚法的测厚原理: 永久磁铁(测头)与导磁钢材之间的吸力大小与处于这两者之间的距离成一定比例关系,这个距离就是覆层的厚度。
利用这一原理制成测厚仪,只要覆层与基材的导磁率之差足够大,就可进行测量。
测厚仪基本结构由磁钢、接力簧、标尺及自停机构组成。
磁钢与被测物吸合后,将测量簧在其后逐渐拉长,拉力逐渐增大。
当拉力刚好大于吸力,磁钢脱离的一瞬间记录下拉力的大小即可获得覆层厚度[2]。
新型的产品可以自动完成这一记录过程。
磁感应测厚法的基本原理:利用基体上的非铁磁性涂覆层在测量磁回路中形成非铁磁间隙,使线圈的磁感应强度减弱;当测量的是非铁磁性基体上的磁性涂镀层厚度时,则随着涂镀层厚度的增加,其磁感应强度也会增加。
利用磁感应原理的测厚仪,原则上可以测量导磁基体上的非导磁覆层厚度,一般要求基材导磁率在500 H /m以上。
如果覆层材料也有磁性,则要求与基材的导磁率之差足够大(如钢上镀镍) 。
磁性原理测厚仪可用来精确测量钢铁表面的油漆层,瓷、搪瓷防护层,塑料、橡胶覆层,包括镍铬在内的各种有色金属电镀层以及化工石油行业的各种防腐蚀涂层。
其特点是操作简便、坚固耐用、不用电源、测量前无须校准、价格较低,适合车间做现场质量控制。
(2)电涡流测厚涡流测厚仪是根据涂镀层与基体材料的导电性有足够的差异来进行金属基材上涂覆层的物性膜厚来测量的。
该方法实质上也属于电磁感应原理,但能否采用该方法进行厚度测定,与基体及涂镀层材料的导电性有关,而与其是否为磁性材料无关。
其工作原理为:高频交流信号会在测头线圈中产生电磁场,当测头靠近导体时,就在其中形成涡流。
测头离导电基体愈近,则涡流愈大,反射阻抗也愈大。
这个反馈作用量表征了测头与导电基体之间距离的大小,也就是导电基体上非导电覆层厚度的大小。
由于这类测头专门测量非铁磁金属基材上的覆层厚度,所以通常称之为非磁性测头。
非磁性测头采用高频材料做线圈铁芯,例如铂镍合金或其他新材料。
与磁感应原理比较,主要区别是不同的测头、不同的信号频率和大小及不同的标度关系。
采用电涡流原理的测厚仪,主要是对导电体上的非导电体覆层厚度的测量,但当覆层材料有一定的导电性时,通过校准也同样可以测量,只是要求两者的导电率之比至少相差3~5倍(如铜上镀铬) 。
(3)磁性/涡流测厚磁性测厚和涡流测厚均有缺点,为此,很多厂家将两者综合在一起进行测定,采用的探头有3种: F型、N型和FN型。
其中F型探头采用磁感应原理,可用于钢铁上的非磁性涂镀层,如油漆、塑料、搪瓷、铬和锌等; N型探头采用涡流原理,用于有色金属(如铜、铝、奥氏体不锈钢)上的绝缘层,如阳极氧化膜、油漆和涂料等;而FN型探头同时具有F 和N型探头的功能,利用两用型探头,可实现在磁性和非磁性基体上自动转换测量[3] 。
目前开发比较成熟的磁性测厚仪有时代公司的TT220, 德国EPK 公司开发的M IN ITEST4100 /3100 /2100 /1100系列测厚仪和PHYN IX公司的Surfix/Pocket2Surfix 便携式涂镀层测厚仪,可以方便地实现各种条件下的无损测厚。
(4)超声波测厚超声波测厚仪是利用超声波脉冲反射原理,通过发射的超声波脉冲至涂层/ 基材, 计算脉冲通过涂层/ 基材界面反射回发射器所花的时间来计算涂层的厚度。
仪器通过一个发射器发射高频超声波进入涂层,振动波会穿透涂层,遇上不同力学性能的材料(如基材) 时,振动波会在不同材料的界面部分反射和传递。
反射部分会被感应器接收,传递的振动波继续传递到底材,同样经历着所有材料界面间的反射、传递过程。
传感器将反射波转换成电信号,这些信号会被仪器数码化,数码化反射波被分析后,便得到振荡波所花的确切传递时间[5]。
从而计算出涂层的厚度。
超声波测厚仪可用于测量多种材料的厚度,如钢、铁、塑料和玻璃等。
新型的超声波测厚仪可以一次测量即可测定多层涂层的总厚度及指定的各层厚度,且精度很高。
1.1.3管内作业机器人的发展前景为了使管内作业机器人能够尽快地走出实验室,进入实用化阶段,必须在以下几个方面有所突破。
(1)灵活可靠的行走机构前面已经提到,管内作业机器人在弯管、支岔管中的通过性问题仍未解决。