石灰石的预处理和煅烧
烧石灰流程

烧石灰流程
石灰烧制是将石灰石(即钙碳酸石)在高温环境下进行煅烧,分解成氧化钙(石灰)。
石灰的烧制流程如下:
1. 原料准备:选用高纯度的石灰石作为原料,并将其破碎成适当大小的颗粒。
2. 石灰石预处理:将破碎的石灰石送入预处理设备,通过篩网去除其中的杂质和过大或过小的颗粒。
3. 石灰石烘干:将预处理后的石灰石送入烘干设备,在适当温度和湿度下进行烘干,以去除其中的水分。
4. 石灰石煅烧:将干燥的石灰石送入石灰窑(也称为煅烧炉),通过加热设备升温至800-1200的高温环境。
5. 石灰石分解:在高温石灰窑内,石灰石开始分解,产生氧化钙(CaO)和二氧化碳(CO2)。
6. 除尘处理:在石灰石煅烧过程中,还会产生一些固体颗粒和气体排放物。
通过除尘设备进行处理,将颗粒物和气体排放控制在规定范围内,以保护环境。
7. 采集石灰:煅烧后的石灰石,在石灰窑底部形成石灰石灰渣,将其收集起来。
8. 石灰降温:将采集到的石灰石灰渣放置一段时间进行降温,以便后续的存储和运输。
9. 石灰石石灰:将降温后的石灰石灰渣进行破碎和研磨,得到所需的粒度和质量的石灰石。
以上就是石灰烧制的基本流程,不同工艺和设备有所不同,具体步骤可能会有些差异。
生石灰的生产工艺

生石灰的生产工艺
生石灰是指煅烧石灰石(CaCO3)而成的产物,它是建筑行业常用的一种基础建材。
下面将介绍生石灰的生产工艺。
生石灰的生产工艺主要包括石灰石的破碎、炉料的预处理、煅烧和石灰的处理四个步骤。
首先,石灰石在上层土壤的覆盖下,通过爆破、钻孔和拆迁等方式进行石灰石的采矿。
采矿完毕后,将石灰石进行破碎,使其从原有较大的颗粒状变成小块的石灰石。
其次,对石灰石的预处理工序主要包括筛分、洗涤和破碎。
筛分过程是将石灰石进行分级,分离出较大和较小的石灰石块。
洗涤工序用于清除石灰石中的杂质,如泥浆、沙土等。
破碎过程是将石灰石进一步破碎成所需尺寸。
然后,将经过预处理的石灰石送入石灰窑进行煅烧。
石灰窑一般采用回转窑或立窑,石灰石从窑口进入窑内进行煅烧。
煅烧温度高达900℃-1200℃,在这个温度下,石灰石中的碳酸钙
分解成氧化钙和二氧化碳。
通过窑内高温的环境和流动的煤气,使石灰石充分煅烧,得到优质的生石灰。
最后,煅烧完毕的生石灰进行冷却处理后,送入石灰仓进行存储。
在进行冷却处理时,通过冷却器等设备,将高温的生石灰迅速降温至环境温度,以保证石灰的质量。
然后将生石灰运输到建筑工地或工厂进行使用,或者送入石灰砂厂进行混合生产石灰砂或其他石灰制品。
总结来说,生石灰的生产工艺包括石灰石的破碎、炉料的预处理、煅烧和石灰的处理四个步骤。
通过这些步骤,石灰石经过多次加工和处理,最终得到优质的生石灰产品,以满足各个行业对石灰的需求。
石灰窑悬浮煅烧工艺流程

石灰窑悬浮煅烧工艺流程一、引言石灰窑悬浮煅烧是一种常见的工业生产过程,用于将石灰石转化为消化石灰。
本文将详细介绍石灰窑悬浮煅烧的工艺流程,包括原料准备、炉内反应过程、熟料处理和烟气处理等。
二、原料准备石灰窑悬浮煅烧的原料主要是石灰石。
在生产过程中,需要将石灰石进行破碎和粉碎,以确保粒度适合反应过程的需求。
破碎后的石灰石通过输送设备送入窑炉。
三、炉内反应过程炉内反应过程是石灰窑悬浮煅烧的核心环节。
在窑炉内,将石灰石暴露在高温环境中,通过煅烧将其转化为消化石灰。
具体步骤如下:1.预热区石灰窑的上部是预热区,石灰石在这个区域被逐渐预热至较高温度。
预热区的温度通常在800°C左右,预热的目的是提高石灰石的反应活性。
2.煅烧区煅烧区是石灰窑的主要部分,温度高达1300°C以上。
在这个区域,石灰石发生分解反应,将其转化为消化石灰。
石灰窑内部采用悬浮煅烧技术,即石灰石通过气流的作用悬浮在窑内,并与高温烟气进行充分接触,使反应更加充分。
3.冷却区冷却区是石灰窑的下部,用于冷却煅烧后的石灰石。
煅烧后的消化石灰通过输送设备进入冷却区,在与冷却气体的接触中逐渐降温。
冷却后的消化石灰成为最终产品,通过输送设备送至后续处理环节。
四、熟料处理熟料处理是将煅烧后的消化石灰进行研磨和加工,以满足不同工业领域的需求。
处理过程包括碎石机的破碎、筛分和分级等步骤,最终得到符合规格要求的消化石灰产品。
五、烟气处理石灰窑悬浮煅烧过程中会产生大量的烟气,其中含有二氧化硫等有害物质。
为减少对环境的影响,需要对烟气进行处理。
常见的处理方法包括烟气脱硫、脱尘和脱氮等技术,确保煅烧过程的环保合规。
结论石灰窑悬浮煅烧是一种重要的工业生产过程,通过将石灰石转化为消化石灰,为各个行业提供了重要的原材料。
在工艺流程中,原料准备、炉内反应、熟料处理和烟气处理等环节都起到至关重要的作用。
通过科学优化工艺流程,可以提高生产效率和产品质量,同时降低对环境的影响,实现可持续发展。
石灰石煅烧化学方程式

石灰石煅烧化学方程式石灰石,也称为方解石或石灰岩,是一种常见的矿石和建筑材料。
它主要由碳酸钙(CaCO3)组成,在高温下可以通过煅烧过程进行分解。
石灰石煅烧是一种重要的工业过程,用于生产生石灰(氧化钙)以及其他相关产物。
下面是石灰石煅烧的化学方程式:石灰石的分解反应方程式为:CaCO3(s) → CaO(s) + CO2(g)这个方程式表明,石灰石在加热的条件下,会分解成氧化钙和二氧化碳。
在这个反应中,一个碳酸根离子(CO3^2-)分解为氧化钙(CaO)和二氧化碳(CO2),同时释放出能量。
这个化学方程式可以进一步细化,考虑反应的平衡。
方程式可以表示为:CaCO3(s) ↔ CaO(s) + CO2(g)这个方程式告诉我们,石灰石的分解反应是一个可逆反应,即氧化钙和二氧化碳可以重新结合形成石灰石。
在正常的条件下,分解反应占优势,因此产生氧化钙和二氧化碳的过程是主要的。
然而,在特定的条件下,比如高温和高压,反向的反应也可以发生。
石灰石的煅烧过程是通过加热石灰石到高温来实现的。
通常,石灰石会放置在一个烧炉中,炉内提供足够的热量来加热石灰石。
加热石灰石的温度通常在900°C至1000°C之间。
在这个温度范围内,石灰石开始分解,产生氧化钙和二氧化碳。
氧化钙可以被收集和用于生产生石灰。
石灰石的煅烧过程在许多工业应用中起着重要作用。
生石灰是一个重要的工业原料,广泛应用于建筑、冶金、化工和环境保护等领域。
氧化钙的化学性质使其成为一种理想的碱性物质,可用于中和酸性废水和气体,用于工业废水处理和废气处理。
在工业生产中,石灰石的煅烧是一个重要的过程,需要控制温度、时间和反应条件,以确保高效的分解和产物的纯度。
此外,废气处理也是一个关键的环节,在石灰石煅烧过程中产生的二氧化碳等废气需要进行收集和处理,以减少对环境的影响。
总结起来,石灰石的煅烧是一个重要的工业过程,通过加热石灰石到高温来分解它,产生氧化钙和二氧化碳。
煅烧石灰石的操作方法

煅烧石灰石的操作方法
煅烧石灰石是指将石灰石加热至高温下,使其分解成氧化钙和二氧化碳的过程。
以下是煅烧石灰石的基本操作方法:
1. 准备设备:首先,需要准备好石灰石煅烧的设备,如石灰窑或石灰石炉等。
这些设备需要具备承受高温的特性。
2. 石灰石装载:将石灰石装载到石灰窑或石灰炉中。
通常使用机械设备或人工装载的方式。
3. 控制燃料:选择合适的燃料,如煤、天然气、石油等,并根据石灰石煅烧所需的高温程度来控制燃料的投放量。
4. 点火:在石灰窑或石灰石炉中点火,开始加热过程。
5. 煅烧过程:随着加热的进行,石灰石逐渐达到高温,石灰石中的碳酸钙开始分解,生成氧化钙和二氧化碳。
6. 收集产物:氧化钙是煅烧石灰石得到的主要产物,可以通过设备设置收集。
7. 控制温度:在整个煅烧过程中,需要根据实际情况及时调整燃料的投放量,以控制石灰石的温度。
8. 冷却:煅烧过程完成后,将石灰石冷却到合适的温度。
可以使用自然冷却或加水冷却等方式。
需要注意的是,煅烧石灰石的具体操作方法可能会因设备的不同而有所差异。
在实际操作中,应遵循相关安全规范和操作流程。
石灰石工艺流程
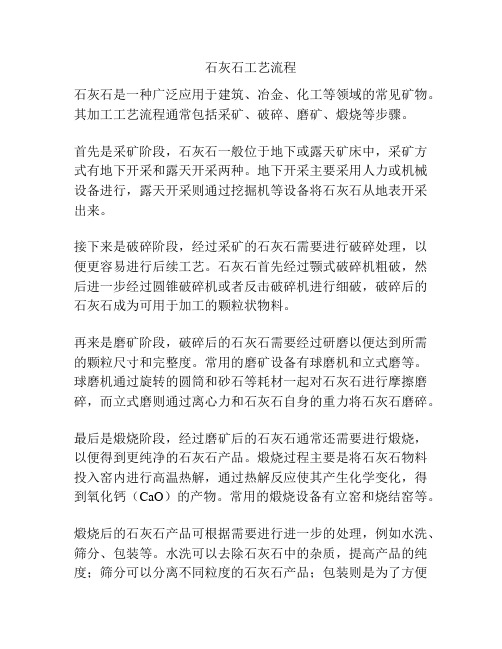
石灰石工艺流程
石灰石是一种广泛应用于建筑、冶金、化工等领域的常见矿物。
其加工工艺流程通常包括采矿、破碎、磨矿、煅烧等步骤。
首先是采矿阶段,石灰石一般位于地下或露天矿床中,采矿方式有地下开采和露天开采两种。
地下开采主要采用人力或机械设备进行,露天开采则通过挖掘机等设备将石灰石从地表开采出来。
接下来是破碎阶段,经过采矿的石灰石需要进行破碎处理,以便更容易进行后续工艺。
石灰石首先经过颚式破碎机粗破,然后进一步经过圆锥破碎机或者反击破碎机进行细破,破碎后的石灰石成为可用于加工的颗粒状物料。
再来是磨矿阶段,破碎后的石灰石需要经过研磨以便达到所需的颗粒尺寸和完整度。
常用的磨矿设备有球磨机和立式磨等。
球磨机通过旋转的圆筒和砂石等耗材一起对石灰石进行摩擦磨碎,而立式磨则通过离心力和石灰石自身的重力将石灰石磨碎。
最后是煅烧阶段,经过磨矿后的石灰石通常还需要进行煅烧,以便得到更纯净的石灰石产品。
煅烧过程主要是将石灰石物料投入窑内进行高温热解,通过热解反应使其产生化学变化,得到氧化钙(CaO)的产物。
常用的煅烧设备有立窑和烧结窑等。
煅烧后的石灰石产品可根据需要进行进一步的处理,例如水洗、筛分、包装等。
水洗可以去除石灰石中的杂质,提高产品的纯度;筛分可以分离不同粒度的石灰石产品;包装则是为了方便
储运和销售。
总之,石灰石工艺流程包括采矿、破碎、磨矿和煅烧等步骤,在每个步骤中都需要相应的设备和工艺来完成。
石灰石的加工工艺对于产出的产品质量和性能具有重要影响,合理的工艺流程和设备选择可以提高石灰石加工的效率和产出的产品质量。
石灰石制备生石灰方程式
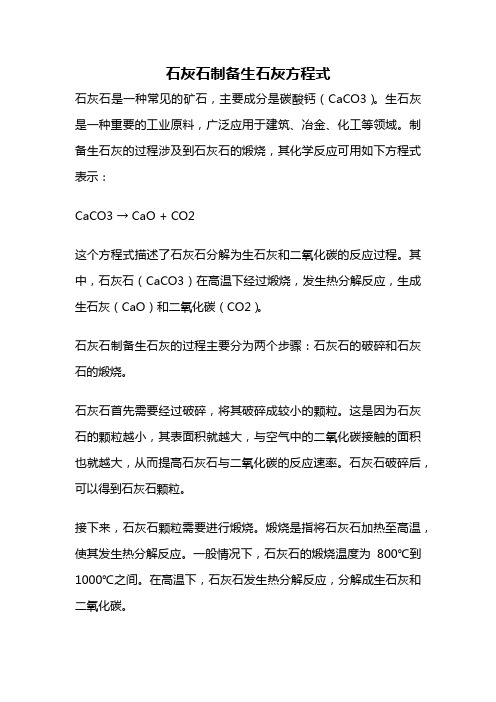
石灰石制备生石灰方程式石灰石是一种常见的矿石,主要成分是碳酸钙(CaCO3)。
生石灰是一种重要的工业原料,广泛应用于建筑、冶金、化工等领域。
制备生石灰的过程涉及到石灰石的煅烧,其化学反应可用如下方程式表示:CaCO3 → CaO + CO2这个方程式描述了石灰石分解为生石灰和二氧化碳的反应过程。
其中,石灰石(CaCO3)在高温下经过煅烧,发生热分解反应,生成生石灰(CaO)和二氧化碳(CO2)。
石灰石制备生石灰的过程主要分为两个步骤:石灰石的破碎和石灰石的煅烧。
石灰石首先需要经过破碎,将其破碎成较小的颗粒。
这是因为石灰石的颗粒越小,其表面积就越大,与空气中的二氧化碳接触的面积也就越大,从而提高石灰石与二氧化碳的反应速率。
石灰石破碎后,可以得到石灰石颗粒。
接下来,石灰石颗粒需要进行煅烧。
煅烧是指将石灰石加热至高温,使其发生热分解反应。
一般情况下,石灰石的煅烧温度为800℃到1000℃之间。
在高温下,石灰石发生热分解反应,分解成生石灰和二氧化碳。
石灰石的煅烧过程是一个放热反应,需要提供热能来加热石灰石。
通常,可以使用石油、天然气或煤炭等作为燃料,通过燃烧产生的热能来加热石灰石。
在工业生产中,石灰石和燃料一般被放入回转窑或竖立窑中,通过燃料的燃烧,使窑内温度升高,从而实现石灰石的煅烧。
石灰石煅烧过程中生成的生石灰可以通过降温,将其从高温状态转变为常温下的固体物质。
这样,生石灰就可以进行包装、储存和运输等后续处理。
生石灰具有一定的应用价值。
它可以用于建筑材料的制备,例如制作石灰砂浆、石灰石膏等。
此外,生石灰还可以用于水处理、冶金反应、化学试剂等方面。
总结起来,石灰石制备生石灰的过程是通过煅烧石灰石,使其发生热分解反应,生成生石灰和二氧化碳。
这个过程需要经过石灰石的破碎和煅烧两个步骤。
石灰石破碎后,得到石灰石颗粒;石灰石颗粒经过煅烧,在高温下发生热分解反应,生成生石灰。
石灰石制备生石灰是一个重要的工业过程,广泛应用于建筑、冶金、化工等领域。
石灰石的预处理和煅烧

状态,适合于配煤率大的立窑。
煅烧工艺条--件-风量(一):
风量是指送入窑内的空气量,风量取决于无烟 煤完全燃烧所需的理论空气消耗量。
根据计算,如果配煤率为100:15,则煅烧1kg 石灰石所需空气量约为1.07m³
煅烧工--艺-无条烟件煤的粒度(三):
无烟煤的粒度太大: 1、无法在煅烧区内完全燃烧,使得煅烧区下移, 容易造成石灰过烧; 2、一定的配煤率下,易分布不匀,也易产生生烧 或过烧;
煅烧工艺条件---配煤率:
配煤率就是100kg石灰石所配无烟煤的质量(kg)。 配煤率的大小主要取决于无烟煤中固定碳含量
煅烧的原理---碳的燃烧:
碳燃烧过程的反应式: C+O2 → CO2↑ ----------氧气充足时的主要反应
2C+O2 → 2CO ↑-----------氧气不足时的主要反应 2CO+O2 → 2CO2 ↑--------------一氧化碳的氧化反应 CO2 +C===2CO ↑--------------二氧化碳的还原反应
碳酸钙的分解速度用分解反应面的移动速度来 表示。分解反应面是指已分解的氧化钙和未分解的 碳酸钙之间的分界面。
反应速度与粒度无关, 与温度有关。温度越高,反 应速度越快。因此,一定粒 度的石灰石,煅烧温度越高, 反应速度越快,煅烧时间也 就越短。
煅烧的原理---碳酸镁的分解
△
分解反应式为:MgCO3 === MgO + CO2 ↑ 碳酸镁的分解温度为640 ℃ 。 氧化镁的活性低,因此,氧化镁基本不参与其他 杂质反应,对煅烧过程影响不大。
煅烧工艺条--件-风量(二):
高温锻烧石灰石

高温锻烧石灰石高温锻烧石灰石是一种常见的建筑材料,它在高温下进行锻烧处理,以改变其组成结构,使其具有更高的强度、耐久性、韧性和耐磨性。
由于其具有独特的加工性能,石灰石锻烧通常用于各种建筑项目中,如大型水利工程、坝、墙、桥梁、港口码头和其他建筑物。
石灰石的高温锻烧处理通常分为三个步骤:烧制、淬火和冷却。
首先,将原料石灰石放入高温炉,温度控制在1200℃至1400℃之间,保持约2小时,直至石灰石充分变得透明,并发出橙红色的光芒。
然后,将石灰石从高温炉中取出,并将其放入淬火炉,控制温度在800℃至1000℃之间,保持约3小时,在此过程中,石灰石会呈现出蓝绿色的光芒,表明石灰石已经完成淬火处理。
最后,将石灰石从淬火炉中取出,放入冷却炉,在此过程中,石灰石会变得更加坚硬,获得更高的强度、耐久性、韧性和耐磨性。
石灰石的高温锻烧处理具有良好的加工性能,可以根据客户的不同需求定制各种不同形状的石灰石。
同时,高温锻烧处理能使石灰石的表面光洁度提高,使其具有更高的抗腐蚀性、耐热性和耐冻性,因此,石灰石锻烧后的产品可以更加耐用,更能承受各种恶劣环境的攻击,更能满足建筑项目的要求。
石灰石的高温锻烧处理还具有一定的环保性,它可以有效减少污染物的排放,减少对环境的污染。
与传统的石灰石锻烧方法相比,高温锻烧处理可以有效降低二氧化碳和其他有害气体的排放,从而节约能源,减少对环境的影响。
此外,高温锻烧处理还可以提高石灰石的强度,使其能够抵抗更大的破坏力,而传统的处理方法则无法提供这样的性能。
同时,高温锻烧处理还可以改变石灰石的外观,使其看起来更加美观,并提高其装饰性。
要总结,石灰石的高温锻烧处理是一种有效的建筑材料加工方法,可以提高石灰石的强度、耐久性、韧性和耐磨性,并且可以有效减少污染物的排放,减少对环境的污染。
因此,石灰石的高温锻烧处理是一种有效的建筑材料加工方法,能够满足各种建筑项目的要求。
石灰的生产工艺

石灰的生产工艺
石灰的生产工艺主要包括以下几个步骤:
1. 原料准备:首先需要选取合适的石灰石原料,通常要求石灰石纯度较高,含杂质较少。
石灰石会经过破碎机进行初步破碎,以便于后续处理。
2. 预加热:破碎后的石灰石会被送入预热器进行预加热。
这一步骤可以提高石灰窑的热效率,同时也有助于减少燃料消耗。
3. 煅烧:预加热后的石灰石会送入石灰窑内部进行煅烧。
石灰窑的类型有很多,常见的有梁式窑、立式窑和回转窑等。
在高温下石灰石会发生分解反应,生成氧化钙(石灰)和二氧化碳。
4. 冷却:煅烧完成的石灰需要迅速冷却,以防止其吸湿和硬化。
冷却后的石灰可以通过冷却器和胶带输送机进行输送。
5. 分级和包装:冷却后的石灰会经过振动筛分选,去除不合格的大块物料,然后按照粒度要求进行分级。
合格的石灰会被打包储存或直接送往使用地点。
在整个石灰生产过程中,质量控制非常关键。
需要严格监控石灰窑的温度、时间和原料的质量,确保石灰的活性和纯度。
此外,还需注意环保措施,如粉尘收集和二氧化碳排
放控制,以减少对环境的影响。
石灰石煅烧氧化钙
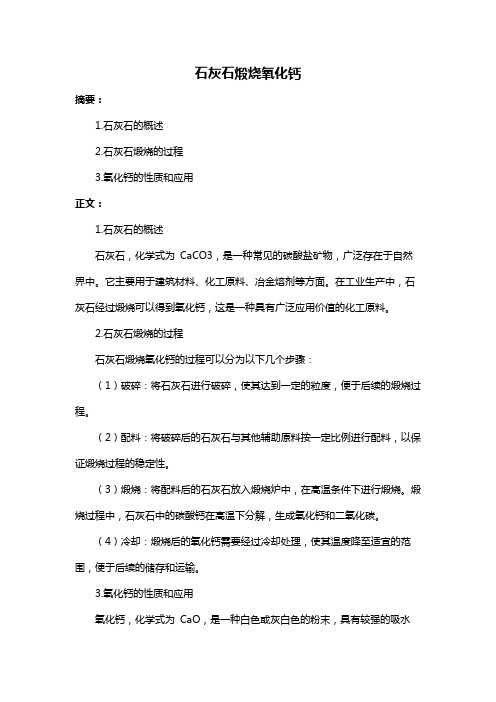
石灰石煅烧氧化钙
摘要:
1.石灰石的概述
2.石灰石煅烧的过程
3.氧化钙的性质和应用
正文:
1.石灰石的概述
石灰石,化学式为CaCO3,是一种常见的碳酸盐矿物,广泛存在于自然界中。
它主要用于建筑材料、化工原料、冶金熔剂等方面。
在工业生产中,石灰石经过煅烧可以得到氧化钙,这是一种具有广泛应用价值的化工原料。
2.石灰石煅烧的过程
石灰石煅烧氧化钙的过程可以分为以下几个步骤:
(1)破碎:将石灰石进行破碎,使其达到一定的粒度,便于后续的煅烧过程。
(2)配料:将破碎后的石灰石与其他辅助原料按一定比例进行配料,以保证煅烧过程的稳定性。
(3)煅烧:将配料后的石灰石放入煅烧炉中,在高温条件下进行煅烧。
煅烧过程中,石灰石中的碳酸钙在高温下分解,生成氧化钙和二氧化碳。
(4)冷却:煅烧后的氧化钙需要经过冷却处理,使其温度降至适宜的范围,便于后续的储存和运输。
3.氧化钙的性质和应用
氧化钙,化学式为CaO,是一种白色或灰白色的粉末,具有较强的吸水
性。
在工业生产中,氧化钙具有广泛的应用:
(1)在建筑行业中,氧化钙可以用作干燥剂、防水剂等,提高建筑物的性能。
(2)在冶金行业中,氧化钙可以用作熔剂,提高金属的纯度和回收率。
(3)在环保行业中,氧化钙可以用于废气脱硫、废水处理等方面,减少污染物的排放。
(4)在农业行业中,氧化钙可以用作土壤改良剂,提高土壤的肥力和作物的产量。
总之,石灰石经过煅烧氧化钙的过程,可以得到具有广泛应用价值的化工原料。
石灰烧制过程
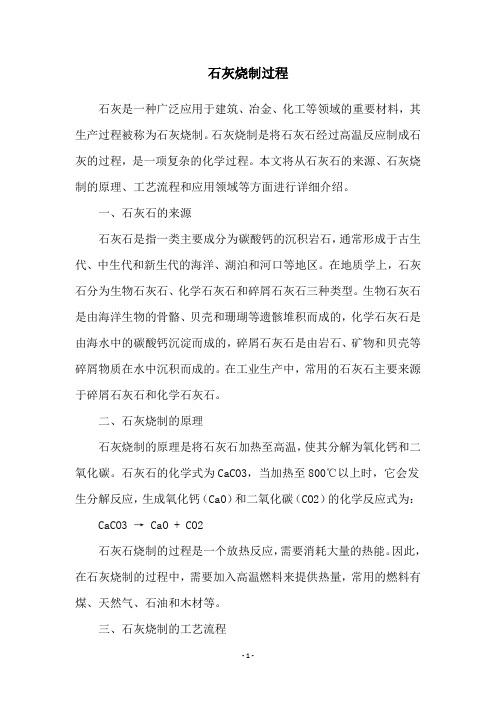
石灰烧制过程石灰是一种广泛应用于建筑、冶金、化工等领域的重要材料,其生产过程被称为石灰烧制。
石灰烧制是将石灰石经过高温反应制成石灰的过程,是一项复杂的化学过程。
本文将从石灰石的来源、石灰烧制的原理、工艺流程和应用领域等方面进行详细介绍。
一、石灰石的来源石灰石是指一类主要成分为碳酸钙的沉积岩石,通常形成于古生代、中生代和新生代的海洋、湖泊和河口等地区。
在地质学上,石灰石分为生物石灰石、化学石灰石和碎屑石灰石三种类型。
生物石灰石是由海洋生物的骨骼、贝壳和珊瑚等遗骸堆积而成的,化学石灰石是由海水中的碳酸钙沉淀而成的,碎屑石灰石是由岩石、矿物和贝壳等碎屑物质在水中沉积而成的。
在工业生产中,常用的石灰石主要来源于碎屑石灰石和化学石灰石。
二、石灰烧制的原理石灰烧制的原理是将石灰石加热至高温,使其分解为氧化钙和二氧化碳。
石灰石的化学式为CaCO3,当加热至800℃以上时,它会发生分解反应,生成氧化钙(CaO)和二氧化碳(CO2)的化学反应式为: CaCO3 → CaO + CO2石灰石烧制的过程是一个放热反应,需要消耗大量的热能。
因此,在石灰烧制的过程中,需要加入高温燃料来提供热量,常用的燃料有煤、天然气、石油和木材等。
三、石灰烧制的工艺流程石灰烧制的工艺流程包括石灰石的预处理、石灰石的烧制、石灰的冷却、石灰的破碎和石灰的贮存等步骤。
1. 石灰石的预处理石灰石的预处理包括石灰石的运输、石灰石的破碎和筛分等步骤。
石灰石在运输过程中容易受到震动和撞击而破碎,因此需要采取适当的包装和运输方式。
石灰石在烧制前需要破碎和筛分,以保证石灰石的均匀性和烧制效果。
2. 石灰石的烧制石灰石的烧制是将石灰石放入石灰窑中,加入高温燃料进行加热,使其发生分解反应,生成氧化钙和二氧化碳。
石灰窑分为立式石灰窑和横式石灰窑两种,立式石灰窑又分为周期窑和连续窑。
周期窑是指将石灰石和燃料按照一定比例放入石灰窑中,加热一段时间后取出石灰,再加入新的石灰石和燃料,如此循环。
高温煅烧石灰石的反应现象
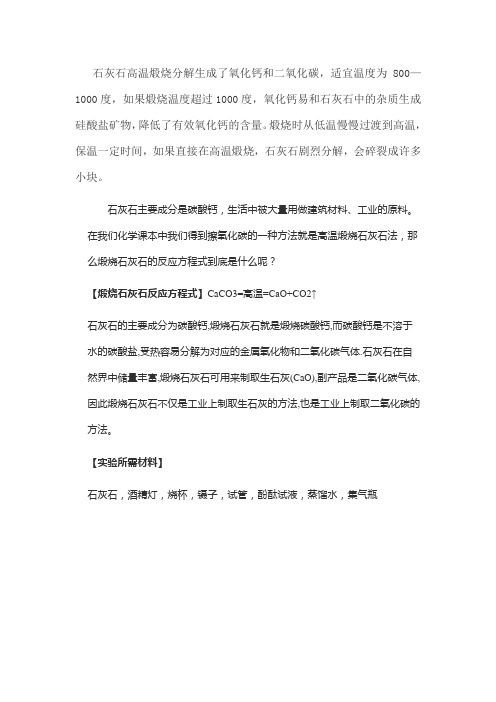
石灰石高温煅烧分解生成了氧化钙和二氧化碳,适宜温度为800—1000度,如果煅烧温度超过1000度,氧化钙易和石灰石中的杂质生成硅酸盐矿物,降低了有效氧化钙的含量。
煅烧时从低温慢慢过渡到高温,保温一定时间,如果直接在高温煅烧,石灰石剧烈分解,会碎裂成许多小块。
石灰石主要成分是碳酸钙,生活中被大量用做建筑材料、工业的原料。
在我们化学课本中我们得到擦氧化碳的一种方法就是高温煅烧石灰石法,那么煅烧石灰石的反应方程式到底是什么呢?【煅烧石灰石反应方程式】CaCO3=高温=CaO+CO2↑石灰石的主要成分为碳酸钙,煅烧石灰石就是煅烧碳酸钙,而碳酸钙是不溶于水的碳酸盐,受热容易分解为对应的金属氧化物和二氧化碳气体.石灰石在自然界中储量丰富,煅烧石灰石可用来制取生石灰(CaO),副产品是二氧化碳气体,因此煅烧石灰石不仅是工业上制取生石灰的方法,也是工业上制取二氧化碳的方法。
【实验所需材料】石灰石,酒精灯,烧杯,镊子,试管,酚酞试液,蒸馏水,集气瓶反应类型分解反应反应物CaCO3生成物CO2,CaO反应条件高温开始加热过程不能达到碳酸钙分解的温度,所以开始没有二氧化碳气体生成,需要过一段时间才能有气体反应现象生成,而且生成的气体的质量也是逐渐增加的。
【实验步骤】1 点燃酒精灯,打开沉浮式贮气瓶的活塞导管,把细长的铁导管由下向上插进酒精灯的焰心位置,铁导管与酒精灯火焰成45°角,火焰在氧气流的吹动下,形成向上倾斜45°角的高温焰锋.22 用坩埚钳夹持石灰石薄片(或贝壳)在高温焰锋上灼烧1min,而后把石灰石薄片(或贝壳)投入滴加了酚酞的水里,搅拌,水呈现红色【煅烧石灰石反应知识点总结】【煅烧石灰石反应中会遇到的问题】1.煅烧石灰石是吸热反应还是放热反应?解答:高温煅烧石灰石,碳酸钙在高温条件下慢慢吸热分解,是吸热反应。
【实验小结】煅烧石灰石反应是化学实验中典型的分解反应,在实验刚开始加热过程中,由于还未达到碳酸钙分解温度,在最开始是没有二氧化碳气体生成的,但是随着温度的升高与实验进行中,二氧化碳气体逐渐增加,释放出大量的热量。
煅烧石灰石的产物

煅烧石灰石的产物介绍煅烧石灰石是一种广泛应用的工业过程,用于将石灰石加热至高温并转变成不同的产物。
煅烧石灰石的产物对于建筑、钢铁以及环境保护等领域都有重要的作用。
本文将深入探讨煅烧石灰石的过程和产物,以及它们在不同领域的应用。
煅烧石灰石的过程煅烧石灰石的过程主要包括碳酸石灰的分解和氧化。
具体步骤如下:1.石灰石采矿:首先,石灰石通过采矿的方式获取。
矿石通常存在于地下,需要进行开采和破碎。
2.石灰石破碎:采矿后的石灰石需要经过破碎工艺,将其粉碎成适合后续处理的颗粒。
3.煅烧:破碎后的石灰石颗粒在高温下进行煅烧。
其目的是通过分解碳酸石灰来制备石灰石的产物。
4.石灰石产物:经过高温煅烧后,石灰石会转化为不同的产物,如生石灰、消石灰或水合石灰。
石灰石的产物生石灰生石灰,也称氧化钙,是煅烧石灰石的一种主要产物。
它是白色的固体,由氧化钙构成。
生石灰在水中具有较强的碱性,并且能与水发生剧烈的反应。
消石灰消石灰,也称氢氧化钙,是由生石灰与水反应得到的产物。
与生石灰相比,消石灰的碱性更弱。
消石灰广泛用于建筑行业,作为建筑材料的一部分。
水合石灰水合石灰,也称钙羟基石灰,是由生石灰与水反应而成。
与生石灰和消石灰相比,水合石灰具有更强的粘合性。
因此,它在建筑和建材行业中得到广泛应用,如制作砂浆和砂浆。
石灰石灰石灰石灰,也称熟石灰,是通过煅烧石灰石后再与水反应形成的。
石灰石灰具有较高的比表面积和较强的吸湿性,因此在干燥环境下使用较为常见。
它通常用作干燥剂、防潮剂和净化剂。
煅烧石灰石的应用领域建筑业煅烧石灰石产物在建筑业中有广泛应用。
生石灰、消石灰和水合石灰常用于制作砂浆、砌块和灰浆。
这些石灰石产物能够提供强度和持久性,使其成为建筑材料的理想选择。
钢铁产业石灰石在钢铁产业中扮演着重要的角色。
它与矿石一起被用作炼铁的原料,通过冶炼过程将铁从氧化物中提取出来。
石灰石能够与杂质反应并形成矿渣,从而提高炉石的质量和效率。
环境保护煅烧石灰石的产物在环境保护方面也有重要应用。
石灰膏的制作方法
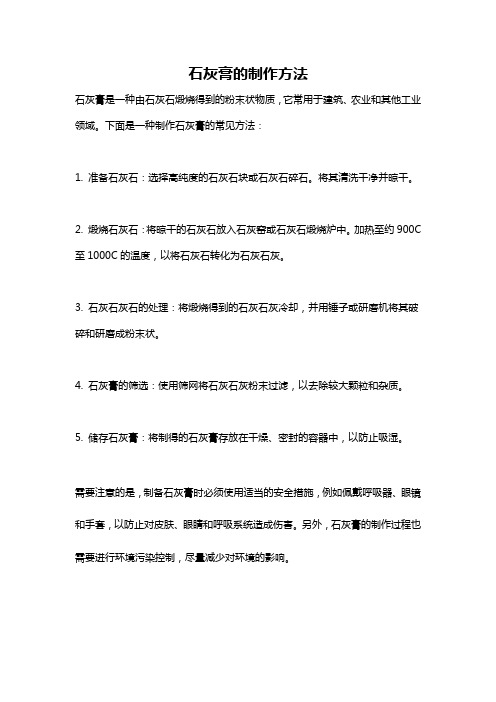
石灰膏的制作方法
石灰膏是一种由石灰石煅烧得到的粉末状物质,它常用于建筑、农业和其他工业领域。
下面是一种制作石灰膏的常见方法:
1. 准备石灰石:选择高纯度的石灰石块或石灰石碎石。
将其清洗干净并晾干。
2. 煅烧石灰石:将晾干的石灰石放入石灰窑或石灰石煅烧炉中。
加热至约900C 至1000C的温度,以将石灰石转化为石灰石灰。
3. 石灰石灰石的处理:将煅烧得到的石灰石灰冷却,并用锤子或研磨机将其破碎和研磨成粉末状。
4. 石灰膏的筛选:使用筛网将石灰石灰粉末过滤,以去除较大颗粒和杂质。
5. 储存石灰膏:将制得的石灰膏存放在干燥、密封的容器中,以防止吸湿。
需要注意的是,制备石灰膏时必须使用适当的安全措施,例如佩戴呼吸器、眼镜和手套,以防止对皮肤、眼睛和呼吸系统造成伤害。
另外,石灰膏的制作过程也需要进行环境污染控制,尽量减少对环境的影响。
石灰生产工艺

石灰生产工艺石灰是一种常用的建筑材料,广泛应用于建筑、冶金、化工、环保等行业。
石灰生产工艺可以分为旧工艺和新工艺两种。
旧工艺:旧工艺主要采用石灰石或石灰土为原料,经过石灰石的挖掘、运输和石灰石的破碎、烧结、石灰石的煅烧等工序,得到成品石灰。
其中,石灰石的破碎和石灰石的煅烧是石灰生产中最关键的环节。
石灰石的破碎一般采用石灰石破碎机进行,将石灰石块破碎成小颗粒,便于石灰石的后续处理。
石灰石的煅烧一般采用石灰窑进行,将破碎后的石灰石颗粒送入石灰窑进行加热,使其产生化学反应,得到石灰。
然而,旧工艺存在一些问题。
首先,石灰石的开采对环境造成严重破坏,不符合可持续发展的原则。
其次,传统石灰生产工艺存在能耗高、产量低的问题,不能满足现代建筑行业对石灰的需求。
新工艺:新工艺主要采用工业废渣或废弃物为原料,通过新的工艺方法制备石灰。
常用的工业废渣包括高炉矿渣、磷矿石渣、硅酸盐渣等。
新工艺的生产流程相对简单,一般包括原料预处理、石灰窑煅烧和成品石灰的包装等环节。
首先,将工业废渣进行预处理,去除杂质和控制原料中的含水量。
然后,将预处理后的原料送入石灰窑进行煅烧。
在石灰窑中,废渣经过高温煅烧,产生化学反应,生成石灰。
最后,将煅烧后的石灰产品经过包装,可以直接应用于建筑等行业。
新工艺有许多优点。
首先,新工艺能够利用工业废渣,减少环境污染和能源消耗。
其次,新工艺具有高效、高产的特点,可以满足现代建筑行业对石灰的需求。
同时,新工艺还具有良好的经济效益,能够带动废渣资源的综合利用。
总之,随着科技的进步和环保意识的增强,新工艺逐渐取代了旧工艺,成为石灰生产的主要方式。
新工艺不仅解决了传统石灰生产存在的问题,而且能够更好地保护环境和实现可持续发展。
随着石灰在建筑、冶金、化工、环保等行业的广泛应用,新工艺将会继续发展,为社会经济的可持续发展做出更大贡献。
石灰的制作过程

石灰的制作过程
石灰是一种广泛应用于建筑、农业、化工等领域的重要材料。
它的制作过程可以分为石灰石的采集、石灰石的煅烧和石灰的熟化三个步骤。
石灰石的采集是石灰制作的第一步。
石灰石是一种由钙碳酸盐组成的矿物质,通常存在于地下或山脉中。
在采集石灰石时,需要先进行勘探,确定石灰石的位置和储量。
然后,使用爆破或钻孔等方式将石灰石从地下或山脉中取出。
采集到的石灰石需要进行初步的加工,去除杂质和不需要的部分,以便后续的煅烧。
石灰石的煅烧是石灰制作的关键步骤。
在煅烧过程中,石灰石中的钙碳酸盐会被分解成氧化钙和二氧化碳。
煅烧的温度通常在800℃到1000℃之间,需要使用高温炉或窑炉进行。
在煅烧过程中,石灰石会逐渐变成白色或灰色的氧化钙粉末。
煅烧的时间和温度会影响氧化钙的质量和产量,需要根据具体情况进行调整。
石灰的熟化是石灰制作的最后一步。
在熟化过程中,氧化钙会与水反应,生成氢氧化钙。
这个过程也被称为“消火”,因为熟化时会产生大量的热量和蒸汽。
熟化的时间通常在几天到几周之间,需要将氧化钙和水充分混合,并保持湿润的状态。
熟化后的石灰会变成白色或灰色的粉末,可以用于建筑、农业、化工等领域。
石灰的制作过程虽然简单,但是需要严格控制各个环节的温度、
时间和湿度等参数,以保证石灰的质量和产量。
同时,石灰制作也会产生大量的二氧化碳和烟尘等污染物,需要采取相应的措施进行治理和减排。
在未来,随着环保意识的提高和技术的进步,石灰制作将会更加环保和高效。
- 1、下载文档前请自行甄别文档内容的完整性,平台不提供额外的编辑、内容补充、找答案等附加服务。
- 2、"仅部分预览"的文档,不可在线预览部分如存在完整性等问题,可反馈申请退款(可完整预览的文档不适用该条件!)。
- 3、如文档侵犯您的权益,请联系客服反馈,我们会尽快为您处理(人工客服工作时间:9:00-18:30)。
.
煅烧工艺条件
石灰石的粒度、形状、装窑方法
窑气的温度、压力和密封
煅烧的温度、碳酸钙的分 解率和二氧化碳浓度
无烟煤粒 度、配煤
率
预热区: 对流传热。 700-900℃
煅烧区:辐射 为主,传导对 流为辅。1050-
1150℃石灰石的粒度越均 匀,源自烧成的石灰质量 越稳定。.
煅烧工艺条件 ---石灰石的形状:
各边尺寸比 煅烧时间h
1:1:1 1
1:1:2 1.23
1:1.5:2 1.6
1:2:3 2.2
名义尺寸相同,各边尺寸比例不同的石灰石煅烧时间
1:3:4 2.6
球形或者立方形的 石灰石煅烧时间最 短
.
煅烧工艺条件 ---无烟煤的粒度(一):
.
煅烧的原理
煅烧中提供热源的燃料有:煤炭,煤气,天然气 等。
我们选用的是无烟煤,其特点是密度大,含碳量 高,挥发分少,发热量大(约29308KJ/kg),灰分少, 含硫量低。
煤的主要可燃性元素是:碳,其次是氢。
.
煅烧的原理
影响燃料完全燃烧并释放高温的因素之一是空气 的存在和使用。
空气由78%的氮和21%的氧,以及少量的二氧化碳 和二氧化硫等组成。有效助燃的成分是氧气。
石灰石的预处理和煅烧
.
.
煅烧:活性石灰生产 1、石灰石的预处理 2、煅烧原理 3、煅烧石灰石的区段划分 4、煅烧的工艺条件 5、煅烧的工艺流程 6、回转窑煅烧系统工艺及结构
.
石灰石的预处理
根据石灰石的形状和粒度的大小以及污染情况等 各项入窑煅烧的理化指标,必须对石灰石进行预处理。
达到理化指标的石灰石可直接进入生产车间准备 煅烧,不达到要求要求的石灰石就要进行预处理。
.
煅烧石灰石时区段的划分 ---煅烧区:
生烧:就是石灰石在煅烧过程中,内部温度没有 达到898℃,碳酸钙没有完全分解就被冷却卸出,这 样的石灰就是生烧石灰,也叫轻烧石灰。其特点是白 度高,活性好,体积收缩性小,易消化,消化后的氢 氧化钙悬浮粒子小,生产出来的PCC或纳米碳酸钙的 沉降体积值高等。
.
.
煅烧工艺条件 ---无烟煤的粒度(三):
无烟煤的粒度太大: 1、无法在煅烧区内完全燃烧,使得煅烧区下移, 容易造成石灰过烧; 2、一定的配煤率下,易分布不匀,也易产生生烧 或过烧;
.
煅烧工艺条件---配煤率:
配煤率就是100kg石灰石所配无烟煤的质量(kg)。 配煤率的大小主要取决于无烟煤中固定碳含量
碳的实际燃烧过程: 氧气充足时,碳与氧气先进行碳的完全燃烧反应
C+O2 → CO2↑ ,然后生成的CO2与上部赤热的碳进 行CO2的还原反应CO2 +C==2CO ,之后产物CO又与 氧气进行CO的氧化反应 2CO+O2 → 2CO2 ↑。由于上 述的CO2还原反应比CO氧化反应的反应速度慢得多, 还原反应生成的CO立即与氧气氧化生成CO2;当上部 的碳温度下降时,还原反应的速度慢慢减小,而氧化 反应的速度却没有减弱,所以,氧气充足时燃烧得到 的CO是少量的。
.
煅烧工艺条--件-煅烧的温度:
提高煅烧温度可以提高 生产能力,但温度过高容易 导致结瘤事故且热损耗高。 一般控制煅烧区温度为 1050-1150 ℃。
提高煅烧区温度的方法: 1、提高配煤率; 2、加大风量; 3、采用粒度均匀的石
灰石。
.
煅烧工艺条件 ---石灰石的粒度:
相同的煅烧温度下, 石灰石的粒度越小,所 需的煅烧时间越短。
.
煅烧的原理---碳的燃烧:
碳燃烧的热力学: 根据碳燃烧的热力学得知,在碳的实际燃烧,氧
气充足时,反应生成的CO会和氧气O2继续反应生成 CO2 。所以氧气充足时碳燃烧得到的气体中CO是少 量的。
.
煅烧的原理---碳的燃烧:
碳燃烧的动力学: 影响碳燃烧反应速度的因素: 1、碳与氧气的化学反应速度; 2、氧气向碳表面扩散的速度。 实际生产中,碳的燃烧反应都是在高温下进行,
所以碳燃烧反应的速度受扩散速度的控制。
.
煅烧的原理---碳的燃烧:
碳燃烧的动力学: 加快碳燃烧反应速度的办法:
1、减小无烟煤的粒径,增加气固相接触面积; 2、通过增加空气量来提高气体中氧气浓度加大扩散 的速度; 3、通过鼓风机增加空气量的同时也提高空气流速, 减小气膜厚度。
.
煅烧的原理---碳的燃烧:
.
煅烧工艺条--件-风量(二):
.
煅烧石灰石时区段的划分 ---冷却区:
烧成的石灰离开煅烧区,或者煤中的碳不再燃烧, 石灰石中的碳酸钙不再分解且温度开始下降,这个区 段物料经历的过程主要是冷却。而本阶段的的气体因 为在冷却石灰的同时进行热交换后升温,升温后的气 体导入窑中作为二次风参加燃烧。
.
煅烧石灰石时区段的划分 ---煅烧过程的4个步骤:
.
石灰石的预处理 ---预处理的方法(三)
分级: 根据煅烧的工艺条件,对
石灰石的粒度有一定的要求, 所以,破碎和清洗后的石灰石 必须进行分级。不符合要求的 另作他用。
常用的分级设备是振动筛。
.
石灰石的预处理
.
煅烧的原理
被煅烧的物料是:石灰石。 石灰石的主要成分是碳酸钙CaCO3 ,少量的碳酸 镁MgCO3以及一些二氧化硅SiO2,三氧化二铝Al2O3 和三氧化二铁Fe2O3杂质。 煅烧时,主要是石灰石中碳酸钙CaCO3和碳酸镁 MgCO3的分解反应,无烟煤中碳C的燃烧反应和氧化 物的结瘤反应。
.
煅烧的原理---碳的燃烧:
碳燃烧过程的反应式: C+O2 → CO2↑ ----------氧气充足时的主要反应
2C+O2 → 2CO ↑-----------氧气不足时的主要反应 2CO+O2 → 2CO2 ↑--------------一氧化碳的氧化反应 CO2 +C===2CO ↑--------------二氧化碳的还原反应
.
煅烧的原-理--氧化钙的结瘤:
氧化钙的结瘤是指在煅烧过程中,温度达到 800℃以上时,二氧化硅,三氧化二铝和三氧化二铁 等杂质会与氧化钙反应生成熔点低而又粘稠的硅酸钙, 铝酸钙,铁酸钙,铁铝酸钙等半融物质,这些物质会 把石灰石粘成大块并烧结成瘤块,部分会黏在窑壁上, 形成结瘤事故。
.
煅烧的原理 ---氧化钙结瘤的反应式:
的大小和煅烧温度的高低。 配煤率过高,则窑气中的CO2浓度低,会使石灰
石过烧甚至导致结瘤事故; 配煤率过低,则会使石灰石生烧。 无烟煤中固定碳含量为78%~82%时,配煤率为
100:12~100:15。
.
煅烧工艺条件 ---装窑方法:
装窑方法有混和装窑法和分层装窑法 混合的优点:石灰石和无烟煤混合比较均匀,
.
煅烧的原理---氧化钙的结瘤:
1、会使煅烧紊乱,使石灰石或烧成的石灰粘 在窑壁,形成结瘤或者结圈,造成石灰的生烧或者 过烧。
2、会覆盖在烧成的石灰表面,降低石灰的消 化性能。
.
煅烧石灰石时区段的划分
石灰窑在煅烧石灰石时,窑内的物料和气体在不 同的区段有不同的温度和发生不同的反应。根据物料 和气体所经历的物理、化学过程的不同,将石灰石在 窑内煅烧分为三个区段:
硅酸钙的生成: SiO2 +xCaO=xCaO·SiO2 铝酸钙的生成: Al2O3+xCaO=xCaO·Al2O3 铁酸钙的生成: Fe2o3+xCaO=xCaO·Fe2O3 铁铝酸钙的生成:
Al2O3+Fe2O3+xCaO=xCaO·Al2O3·Fe2O3 亚硫酸钙的生成: S+O2=SO2 SO2+CaO=CaSO3
煅烧石灰石时区段的划分 ---煅烧区:
过烧:就是石灰石在煅烧过程中,内部温度达到 898℃,碳酸钙完全分解后继续停留在煅烧区,使得 温度持续升高,这样就容易产生过烧石灰,也叫死烧 石灰。其特点是结晶单元逐渐规则排列整齐,体积比 生烧石灰的体积缩小43%,且表面发黑,具有硬度大, 密度大,活性差,消化后的氢氧化钙粒子粗,生产出 来的PCC或纳米碳酸钙的沉降体积值小等。
破碎: 常用设备有颚式破碎机、冲击式破碎机和回旋
式破碎机; 常用的二级破碎设备有锤式破碎机、反击式破
碎机和辊式破碎机。
.
石灰石的预处理 ---预处理的方法(二)
清洗: 常用的洗石设备是转筒洗石机。 净水从出料端引入,脏水从进料端排出,因而
洗石过程是逆流的。
清洗后的石灰 石表面附有一层脏 水膜,可在振动筛 或运输设备上喷水 除去。
碳酸钙的分解速度用分解反应面的移动速度来 表示。分解反应面是指已分解的氧化钙和未分解的 碳酸钙之间的分界面。
反应速度与粒度无关, 与温度有关。温度越高,反 应速度越快。因此,一定粒 度的石灰石,煅烧温度越高, 反应速度越快,煅烧时间也 就越短。
.
煅烧的原理---碳酸镁的分解
分解反应式为:MgCO3
无烟煤的粒度应使其燃烧时间和石灰石煅烧时 间相适应,而石灰石的煅烧时间主要取决于石灰石 的粒度。因此,无烟煤的大小与石灰石的大小成正 比。
回转窑使用的燃烧器的燃料是煤粉。无烟煤粒 度在0.08mm,
.
煅烧工艺条件 ---无烟煤的粒度(二):
无烟煤的粒度太小: 1、燃烧时间过短,温度达不到,石灰石易生烧; 2、造成透气性差,通风不良,增加能耗; 3、部分太小的碎粒还可能被吹走或顺缝隙下漏, 造成窑气粉尘含量增加或冷却区温度升高等。
适合于配煤率小,一次加入燃烧量不多的立窑。 分层的优点:便于调节无烟煤在窑截面的分布
状态,适合于配煤率大的立窑。
.
煅烧工艺条--件-风量(一):
风量是指送入窑内的空气量,风量取决于无烟 煤完全燃烧所需的理论空气消耗量。