锌焙烧矿的浸出
锌焙烧矿热酸浸出工艺

3.3 浸出的生产实践(3)3.3.3热酸浸出工艺锌焙烧矿热酸浸出是20世纪60年代后期随着各种除铁方法的研制成功而发展起来的。
采用热酸浸出使铁酸锌分解后,浸出溶液中的铁含量高达30g/L左右,由于这种高铁溶液的铁能用黄钾铁矾法、针铁矿法以及赤铁矿法等从锌溶液中有效分离,使焙砂热酸浸出得到了广泛应用。
目前,国内外采用的沉铁方法以黄钾铁矾法的最多,有二十多家,其它都是在少数工厂采用。
热酸浸出的实质是锌焙烧矿的中性浸出渣经高温、高酸浸出,在低酸中难以溶解的铁酸锌以及少量其它尚未溶解的锌化合物得到溶解,进一步提高锌的浸出率。
一般是将常规浸出法的酸性浸出改为高温、高酸浸出,使浸出过程成为不同酸度、多段逆流的浸出过程。
其特点是浸出的酸度逐段增加,浸出渣量逐段减少。
由于铁酸锌及其他化合物溶解,浸出渣数量显著减少,使浸出渣中的铅、银、金等有价金属得到较大的富集,从而有利于这些金属的进一步回收。
3.3.3.1热酸浸出工艺流程热酸浸出工艺是在常规浸出工艺的基础上再增加一段或多段热酸浸出过程(并相应增加除铁过程)。
热酸浸出锌的浸出率较高,可达97%以上,两段热酸浸出锌的浸出率可达99%。
目前国内外热酸浸出工艺流程由于各生产企业的条件不同、除铁方式不同,各工厂的热酸浸出工艺流程亦不尽相同。
热酸浸出工艺可按浸出段数分成一段热酸浸出和多段热酸浸出工艺流程。
我国四川西昌炼锌厂采用一段热酸浸出工艺流程,(见图3—5),其优点是热酸浸出段处理量较少,可以节约设备和热能消耗。
我国西北铅锌冶炼厂年产电锌10×104t,采用热酸浸出—黄钾铁矾法沉铁的浸出流程,属于多段热酸浸出工艺流程,见图3—6。
该流程的特点如下:1)氧化液的配制是将电解废液与沉铁后液按一定比例混合,并在其中加入适量的氧化剂(主要是软锰矿和电解阳极泥)。
其作用是保证溶液中的Fe2+充分氧化为Fe3+,配制氧化液是在一个80m3的搅拌槽(俗称氧化槽)中进行,控制其酸度为60~90g/L,反应时间约0.5h,最终溶液含铁低于1g/L,其中Fe2+<0.1g/L,然后将配制好的氧化液送中性浸出工序进行焙砂的浸出。
湿法炼锌的浸出过程

濕法煉鋅的浸出過程一、鋅焙燒礦的浸出目的與浸出工藝流程(一)鋅焙燒礦浸出的目的濕法煉鋅浸出過程,是以稀硫酸溶液(主要是鋅電解過程產生的廢電解液)作溶劑,將含鋅原料中的有價金屬溶解進入溶液的過程。
其原料中除鋅外,一般還含有鐵、銅、鎘、鈷、鎳、砷、銻及稀有金屬等元素。
在浸出過程中,除鋅進入溶液外,金屬雜質也不同程度地溶解而隨鋅一起進入溶液。
這些雜質會對鋅電積過程產生不良影響,因此在送電積以前必須把有害雜質盡可能除去。
在浸出過程中應儘量利用水解沉澱方法將部分雜質(如鐵、砷、銻等)除去,以減輕溶液淨化的負擔。
浸出過程的目的是將原料中的鋅盡可能完全溶解進入溶液中,並在浸出終了階段採取措施,除去部分鐵、矽、砷、銻、鍺等有害雜質,同時得到沉降速度快、過濾性能好、易於液固分離的浸出礦漿。
浸出使用的鋅原料主要有硫化鋅精礦(如在氧壓浸出時)或硫化鋅精礦經過焙燒產出的焙燒礦、氧化鋅粉與含鋅煙塵以及氧化鋅礦等。
其中焙燒礦是濕法煉鋅浸出過程的主要原料,它是由ZnO和其他金屬氧化物、脈石等組成的細顆粒物料。
焙燒礦的化學成分和物相組成對浸出過程所產生溶液的品質及金屬回收率均有很大影響。
(二)焙燒礦浸出的工藝流程浸出過程在整個濕法煉鋅的生產過程中起著重要的作用。
生產實踐表明,濕法煉鋅的各項技術經濟指標,在很大程度上決定於浸出所選擇的工藝流程和操作過程中所控制的技術條件。
因此,對浸出工藝流程的選擇非常重要。
為了達到上述目的,大多數濕法煉鋅廠都採用連續多段浸出流程,即第一段為中性浸出,第二段為酸性或熱酸浸出。
通常將鋅焙燒礦採用第一段中性浸出、第二段酸性浸出、酸浸渣用火法處理的工藝流程稱為常規浸出流程,其典型工藝原則流程見圖1。
圖1 濕法煉鋅常規浸出流程常規浸出流程是將鋅焙燒礦與廢電解液混合經濕法球磨之後,加入中性浸出槽中,控制浸出過程終點溶液的PH值為5.0~5.2。
在此階段,焙燒礦中的ZnO 只有一部分溶解,甚至有的工廠中性浸出階段鋅的浸出率只有20%左右。
锌焙烧矿浸出工艺操作规程
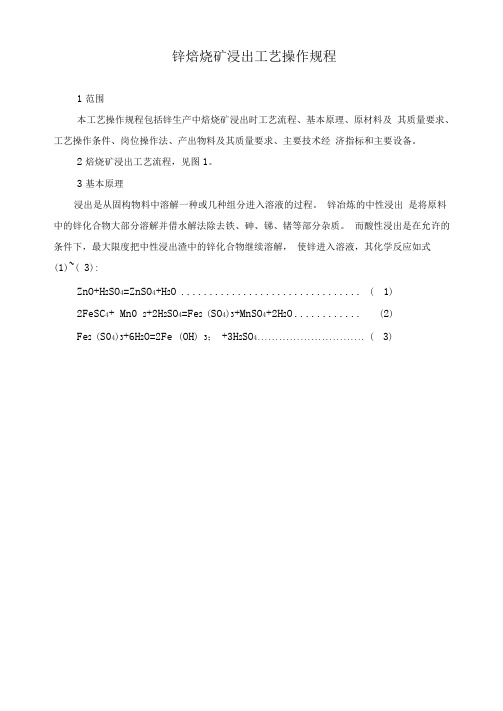
锌焙烧矿浸出工艺操作规程1范围本工艺操作规程包括锌生产中焙烧矿浸出时工艺流程、基本原理、原材料及其质量要求、工艺操作条件、岗位操作法、产出物料及其质量要求、主要技术经济指标和主要设备。
2焙烧矿浸出工艺流程,见图1。
3基本原理浸出是从固构物料中溶解一种或几种组分进入溶液的过程。
锌冶炼的中性浸出是将原料中的锌化合物大部分溶解并借水解法除去铁、砷、锑、锗等部分杂质。
而酸性浸出是在允许的条件下,最大限度把中性浸出渣中的锌化合物继续溶解,使锌进入溶液,其化学反应如式(1)~( 3):ZnO+H2SO4=ZnSO4+H2O ................................ ( 1)2FeSC4+ Mn0 2+2H2SO4=Fe2 (SO4)3+MnSO4+2H2O (2)Fe2 (S04)3+6H2O=2Fe (OH) 3;+3H2SO4 .............................. ( 3)锌烧焙矿图1锌焙烧矿浸出工艺流程图4原材料及其质量要求4.1锌焙烧矿化学成份(%)Zn 55~60 Sb w 0.15 SiO2 可w 2.50 Fe 可3.0~5.0Pb w 1.50 As< 0.30 Ge< 0.005 Zn 可》91.00 F+CI v 0.02粒度要求—200目时不小于80%,—80耳100%。
4.2 锌电解废液(g/L)Zn 40~50, H2SO4 150~200。
4.3锰矿浆锰矿浆液:固=40~50:1 锰矿浆颜色为黑色,浆化后粒度不大于5mm。
4.43#聚凝剂聚丙烯酰胺含量为8%。
4.5焙烧矿酸浸滤液(g/L)Zn 100~130,含固量w 5,湿度,抽干开裂。
4.6氧化锌中性浓缩上清液(g/L)含固量w 5, PH 值5.0~5.2, Zn 100~130As w 0.008, Sb w 0.008, Ge w 0.008。
4.7 贫镉液(g/L)Zn100~120, Cd 0.05~0.15清亮,不带黑色。
第四章锌焙砂的浸出

第四章锌焙砂的浸出第一节概述硫化锌精矿经过沸腾焙烧后,得到的锌焙砂由ZnO和其它金属氧化物以及脉石组成,外表为暗红色的细物料,下一步就需从锌焙砂中把锌溶浸出来。
浸出时,不同厂家采用的炼锌工艺流程不尽相同,因而对锌焙砂成份要求也各不相同。
表4-1列出了国内一些厂家对焙砂成份的要求实例。
蒙自矿冶公司锌焙砂成份如表4-2。
表4-1 锌厂对焙砂成份要求实例,%表4-2 蒙自锌厂锌焙砂化学成份, %浸出是从固体物料中溶解一种或几种组分进入溶液的过程,锌焙砂的浸出目的就是使焙砂中的锌化合物尽可能多地溶解进入浸出液,并借助水解法除去铁、砷、锑、锗等部分杂质,得到满足下道工序要求的合格中性浸出液。
浸出工序是整个湿法炼锌生产过程液体、固体两种物料的大吞吐口。
所产出的溶液源源不断地从这里输出,而电解后的废液又连续流回这里,形成一个溶液循环回路。
固体转运也主要发生在该工序,即焙砂的输入和浸出后残渣的排出。
浸出工序的工艺流程选择以及技术条件控制在很大程度上决定了一个湿法炼锌厂的主要经济技术指标。
根据所使用原料中有价金属及杂质含量的不同,各湿法炼锌厂选择了不同类型的浸出工艺,较有代表性的有常规法浸出工艺,热酸浸出——黄钾铁钒工艺,热酸浸出——针铁矿工艺等。
第二节锌焙砂浸出过程的物理化学变化一、金属氧化物的溶解当含有H2SO4的稀溶液与焙砂一道在浸出槽内搅拌浸出时,焙砂中的各种金属氧化物将与H2SO4反应生成硫酸盐,一般反应方程式为:MeO+H2SO4=MeSO4+H2O锌、铁、铜、镉、镍、钴等的氧化物将发生这类反应,生成易溶于水的硫酸盐,如:ZnO+ H2SO4=ZnSO4+ H2OCuO+ H2SO4= CuSO4+H2O铅和钙也发生此类反应,但生成的硫酸盐难溶于水。
如PbSO4在室温下溶度积为2.3×10-8,溶解度为4.2×10-2g/L,CaSO4则为2.3×10-4和2.0g/L。
锌焙砂浸出理论分析
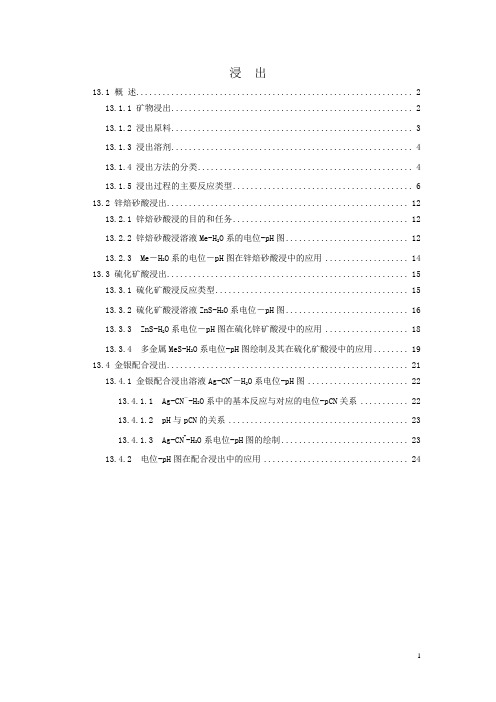
浸出13.1 概述 (2)13.1.1 矿物浸出 (2)13.1.2 浸出原料 (3)13.1.3 浸出溶剂 (4)13.1.4 浸出方法的分类 (4)13.1.5 浸出过程的主要反应类型 (6)13.2 锌焙砂酸浸出 (12)13.2.1 锌焙砂酸浸的目的和任务 (12)13.2.2 锌焙砂酸浸溶液Me-H2O系的电位-pH图 (12)13.2.3 Me-H2O系的电位-pH图在锌焙砂酸浸中的应用 (14)13.3 硫化矿酸浸出 (15)13.3.1 硫化矿酸浸反应类型 (15)13.3.2 硫化矿酸浸溶液ZnS-H2O系电位-pH图 (16)13.3.3 ZnS-H2O系电位-pH图在硫化锌矿酸浸中的应用 (18)13.3.4 多金属MeS-H2O系电位-pH图绘制及其在硫化矿酸浸中的应用 (19)13.4 金银配合浸出 (21)13.4.1 金银配合浸出溶液Ag-CN--H2O系电位-pH图 (22)13.4.1.1 Ag-CN--H2O系中的基本反应与对应的电位-pCN关系 (22)13.4.1.2 pH与pCN的关系 (23)13.4.1.3 Ag-CN--H2O系电位-pH图的绘制 (23)13.4.2 电位-pH图在配合浸出中的应用 (24)浸出13.1 概述什么是浸出?利用适当的溶剂,在一定的条件下使矿石或精矿焙烧中的一种或几种有价成分溶出。
浸出的目的?尽可能使主金属转变、选溶剂。
13.1.1 矿物浸出矿物浸出的实质:在于利用适当的溶剂使原料中的一种或几种有价成分优先溶出,达到有价成分与脉石和杂质分离的目的。
浸出原料通常是由一系列矿物组成的复杂多元体系,其中有价矿物多为硫化物、氧化物、碳酸盐等化合物。
在浸出之前通常要对原料进行物理、化学处理,以改善其性质,使有价成分能够转变为可溶性物质。
浸出前对原料的准备工作:对原料进行物理、化学处理,以及改善其性质,使有价成分能够转变为可溶性物质。
湿法炼锌的浸出过程

湿法炼锌的浸出过程一、锌焙烧矿的浸出目的与浸出工艺流程(一)锌焙烧矿浸出的目的湿法炼锌浸出过程,是以稀硫酸溶液(主要是锌电解过程产生的废电解液)作溶剂,将含锌原料中的有价金属溶解进入溶液的过程。
其原料中除锌外,一般还含有铁、铜、镉、钴、镍、砷、锑及稀有金属等元素。
在浸出过程中,除锌进入溶液外,金属杂质也不同程度地溶解而随锌一起进入溶液。
这些杂质会对锌电积过程产生不良影响,因此在送电积以前必须把有害杂质尽可能除去。
在浸出过程中应尽量利用水解沉淀方法将部分杂质(如铁、砷、锑等)除去,以减轻溶液净化的负担。
浸出过程的目的是将原料中的锌尽可能完全溶解进入溶液中,并在浸出终了阶段采取措施,除去部分铁、硅、砷、锑、锗等有害杂质,同时得到沉降速度快、过滤性能好、易于液固分离的浸出矿浆。
浸出使用的锌原料主要有硫化锌精矿(如在氧压浸出时)或硫化锌精矿经过焙烧产出的焙烧矿、氧化锌粉与含锌烟尘以及氧化锌矿等。
其中焙烧矿是湿法炼锌浸出过程的主要原料,它是由ZnO和其他金属氧化物、脉石等组成的细颗粒物料。
焙烧矿的化学成分和物相组成对浸出过程所产生溶液的质量及金属回收率均有很大影响。
(二)焙烧矿浸出的工艺流程浸出过程在整个湿法炼锌的生产过程中起着重要的作用。
生产实践表明,湿法炼锌的各项技术经济指标,在很大程度上决定于浸出所选择的工艺流程和操作过程中所控制的技术条件。
因此,对浸出工艺流程的选择非常重要。
为了达到上述目的,大多数湿法炼锌厂都采用连续多段浸出流程,即第一段为中性浸出,第二段为酸性或热酸浸出。
通常将锌焙烧矿采用第一段中性浸出、第二段酸性浸出、酸浸渣用火法处理的工艺流程称为常规浸出流程,其典型工艺原则流程见图1。
图1湿法炼锌常规浸出流程是将锌焙烧矿与废电解液混合经湿法球磨之后,加入中性浸出槽中,控制浸出过程终点溶液的PH值为5.0~5.2。
在此阶段,焙烧矿中的ZnO只有一部分溶解,甚至有的工厂中性浸出阶段锌的浸出率只有20%左右。
高硅锌焙砂湿法浸出试验

沉矶品种 Zn Zn 水 Pe
胁
含量地 2.70 1.17 26.09 0.33
At:"
SS
”fuO
1
将单位为 git.
2 铐烽砂全流程浸出试验
内蒙古莱铮冶炼厂采用热酸提出偏低污染黄 钢铁矶法除铁湿法炼铮工艺,其工艺流程见图 lo
Mn 02/阳极泥
r 满丁 l >::
甲
甲
Ill !~渣
铁矶渣
圈 1 铸锦砂温法漫出工艺流程
0.001
表 2 蜡砂磨后粒度分布
Table 2 Size distribution d配 calcmation
编号粒度/皿n +0.8
” 1番 占炜比钞/% 1
6.5
16.39.8 47.5 Nhomakorabea8
再磨 3 血面 占比/%
2.0
4.2
206
212 52.0
再磨5 皿n 占比/%
06
08
17.0
26.6 55.0
关键i司 E 湿法炼铮;高雅铮缔砂:全流程浸出
doi: I0.3969/j.issn. I000-6532.2019.OS.0I0 中团分类号: τD952 文献标志码: A 文章编号 1000」·6532 (2019) 05-0048-04
在湿法炼辛辛工艺中,硅为主要的有害元素。 在通常的流态化熔烧条件下,铃精矿中的硅有 40协60% 转变成了酸溶性的硅酸盐,在焰砂浸出 过程中容易形成溶胶,甚至凝胶,造成矿浆澄清 困难,浸出渣过滤性能恶化等情形,因此传统工艺 要求钵物料二氧化硅含量低于 3%[1]。目前工业上处 理高硅钟培砂应用较成熟的工艺有. V.M 法、田法 和 Radina 法。但 V.M 法与 b曲回法浸出结晶时间 长达 8 ~! Oh ,且使用原矿作为中和剂,浸出中和渣 含镑较高(Z.n5.0% ~ 9仍心,导致铸浸出率偏低 i E 法浸出絮凝时间相对较短(3.5 ~ 6.0 时,使用石
锌焙烧矿的浸出

3 锌焙烧矿的浸出-概述3 锌焙烧矿的浸出3.1概述硫化锌精矿经过沸腾焙烧后,所得焙烧矿基本是ZnO和其他金属氧化物、脉石等组成的细颗粒物料。
温法炼锌的下一步冶金过程,就是用稀硫酸(电解废液)作溶剂,将锌的化合物从焙烧矿中溶解出来,达到与不溶解的固体残渣分离的目的,这个过程叫做锌焙烧矿的浸出。
浸出的目的是使焙烧矿中的锌化合物尽可能迅速而完全地溶解于溶液中,而有害杂质如铁、砷、锑、锗等尽可能少地进入溶液。
浸出后期控制适当的终点pH值,使已溶解的大部分铁、砷、锑,锗等水解除去,以利于矿浆的澄清和硫酸锌溶液的净化。
实际上在一般浸出条件下,要把锌焙烧矿中锌的化合物全部溶解出来是不可能的,浸出后的漫出渣一般还含有18~22%的锌。
这种浸出渣除舍锌外,还有其它多种有价金属必须进一步处理,以回收其中的锌和其它有价金属。
经过浸出后所得到的是由硫酸锌水溶液和浸出渣相混合而构成的矿浆,需要进行渡固分离。
分离的方法有澄清浓缩和过滤两种。
从浸出过程的实质和要达到的目的来看,浸出过程在整个温法炼锌的生产过程中起着决定性的作用。
生产实践表明,湿法炼锌的各种技术经济指标,在很大程度上决定于浸出过程所选择的工艺流程和操作过程中所控制的技术条件。
因此,对浸出流程的选择非常重要。
近代温法炼锌工厂,根据各厂的具体情况,采用许多不同的工艺流程。
根据浸出过程连续与否,分连续浸出与间断浸出。
连续浸出是浸出过程连续在几个浸出槽内进行;间断浸出是指锌焙烧矿在浸出槽中分批间断进行浸出。
与间断浸出相比,连续浸出具有很多优点:设备利用率高;能利用锌焙烧矿的物理热,浸出过程的酸度较高,劳动条件较好,易于实现机械化和自动化操作。
但连续浸出一般只适宜处理质量高、化学成分稳定的锌精矿。
而间断浸出的优点是。
对锌焙烧矿的适应性较好;技术条件易控制,能确保硫酸锌水溶液的质量。
无论是连续浸出,还是间断浸出,根据浸出终点的pH值不同,分为中性浸出与酸性浸出。
当浸出终点的pH值在5.2~5.4之间者叫中性浸出;当浸出终点溶液含硫酸庄1~5g/L以上者叫酸性浸出。
湿法炼锌中浸出过程的基础理论

湿法炼锌中浸出过程的基础理论浸取浸取是湿法炼锌中的主要过程。
在此过程中一方面要将原料中的锌及锡等有价金属尽可能地完全溶解,使其进入溶液,以求得高的金属回收率。
另一方面要在浸出终了阶段,使一些有害杂质(例如Fe,As,Sb,Si等)从锌浸液中分离留在浸出渣中。
同时还力求获得沉降速度快,过滤性能好、易于液固分离的浸出矿浆。
湿法炼锌中,使用浸出的原料主要包括:硫化锌精矿经过焙烧所得到的焙烧料(焙砂及烟尘)、氧化锌精矿,硫化锌精矿以及冶炼厂在生产过程中,产出的粗氧化锌粉及氧化锌烟尘等。
在浸出中,虽然有用盐酸溶液浸出的报道,但主要是用硫酸溶液浸出。
由于浸出原料的性质差异浸出方法也有不同。
根据原料的组成及性质不同,因而有:(1)焙烧料常规浸出工艺;(2)焙烧料热酸浸出工艺;(3)硫化锌精矿氧压浸出工艺;(4)氧化矿酸浸工艺;(5)粗氧化锌及铅锌烟尘的酸浸工艺。
但在上述几种浸出工艺中,焙烧料的酸浸工艺目前居主要地位。
浸出过程的基础理论焙烧料的浸出热力学A 电位E-pH图和金属离子在水溶液中的稳定性各种金属离子在水溶液中的稳定性与溶液中金属离子的电位,pH值、离子活度、温度和压力等有关,湿法冶金广泛使用电位E-pH图来分析浸出过程的热力学条件,电位E-pH 图是将水溶液中基本反应的电位与pH值的变化关系表示在图上。
从图上不仅可以看出各种反应的平衡条件和各组分的稳定范围,还可判断条件变化时平衡移动的方向和限度。
下面简要说明在常温(25℃)下,浸出时固液相间多相反应的吉布斯自由能变化和平衡式,及电位E-pH图的绘制与应用。
浸出过程的有关化学反应可用下列通式表示。
aA+nH++ze ==== bB+cH20根据反应的特点,可将反应分为(a) (b)、(c)三类,第(a)类反应中仅有电子迁移,H+或OH-没有变化,即电位E与pH值无关的氧化还原反应,其反应的吉布斯自由能变化为这时吉布斯自由能的变化转变为对外所作最大有用功,因氢标为零,式中可用φ电动势E,即—△Gө= zFEө前一种反应(a)可以看成是后一种反应(b)的特例,即m=n,表明M(m-n)+不是离子而是金属状态,因而方程式最后一项为零。
热酸浸出湿法炼锌
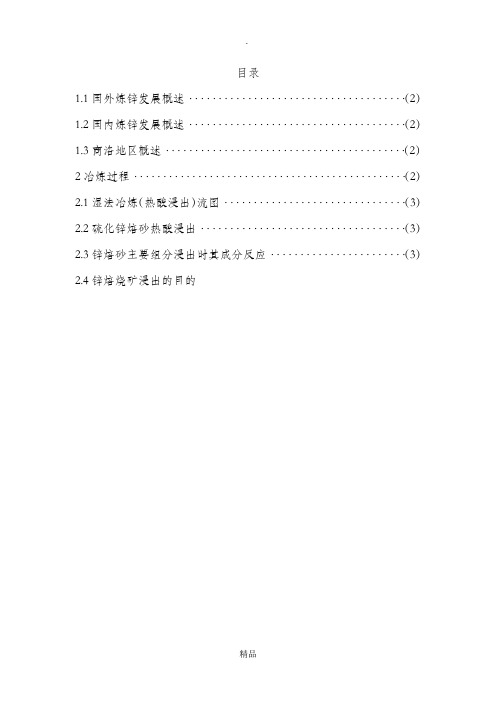
目录1.1国外炼锌发展概述 (2)1.2国内炼锌发展概述 (2)1.3商洛地区概述 (2)2冶炼过程 (2)2.1湿法冶炼(热酸浸出)流图 (3)2.2硫化锌焙砂热酸浸出 (3)2.3锌焙砂主要组分浸出时其成分反应 (3)2.4锌焙烧矿浸出的目的 (4)2.5焙烧矿浸出的工艺流程 (5)2.6黄铁钒法除铁 (5)2.7硫酸锌溶液的净化 (6)2.7.1锌粉置换法 (6)2.7.2β一萘酚除钴工艺 (6)2.8硫酸锌电解沉积 (7)2.8.1主要设备及反应···································(7)3参考文献 (7)湿法炼锌工艺1.锌概述锌主要以硫化物形态存在于自然界,氧化物形态为其次。
在硫化矿中,锌的主要矿物是闪锌矿和高铁闪锌矿,它们经选矿后得到硫化锌精矿;而氧化矿主要以菱锌矿和异极锌矿为主,其它还有少量的红锌矿等。
通过这些炼锌矿物生产出锌锭的工艺被分为两个大类:火法炼锌工艺和湿法炼锌工艺。
而目前世界上主要炼锌方法是湿法炼锌,有80%以上的原生锌锭是通过湿法炼锌的工艺方法生产出来的。
传统的湿法炼锌主要由焙烧、烟气制酸、浸出、净液、电积、熔铸等工序组成。
针对浸出渣火法处理能耗高、过程复杂、劳动条件差、耐火材料消耗高等弊病冶金工作者相继研究成功了热酸浸出黄钾铁钒法、热酸浸出针铁矿法、热酸浸出赤铁矿法处理新工艺,解决了湿法炼锌长期以来的关键问题既强化了浸出过程,又简化了渣处理过程,使锌回收率大幅度提高,促进了湿法炼锌的高速发展。
影响锌焙烧矿浸出反应速度的因素
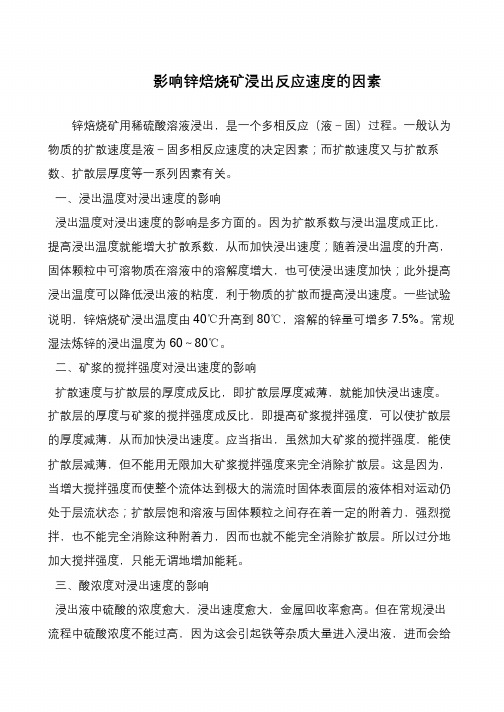
立志当早,存高远
影响锌焙烧矿浸出反应速度的因素
锌焙烧矿用稀硫酸溶液浸出,是一个多相反应(液-固)过程。
一般认为物质的扩散速度是液-固多相反应速度的决定因素;而扩散速度又与扩散系数、扩散层厚度等一系列因素有关。
一、浸出温度对浸出速度的影响
浸出温度对浸出速度的影响是多方面的。
因为扩散系数与浸出温度成正比,提高浸出温度就能增大扩散系数,从而加快浸出速度;随着浸出温度的升高,固体颗粒中可溶物质在溶液中的溶解度增大,也可使浸出速度加快;此外提高浸出温度可以降低浸出液的粘度,利于物质的扩散而提高浸出速度。
一些试验说明,锌焙烧矿浸出温度由40℃升高到80℃,溶解的锌量可增多7.5%。
常规湿法炼锌的浸出温度为60~80℃。
二、矿浆的搅拌强度对浸出速度的影响
扩散速度与扩散层的厚度成反比,即扩散层厚度减薄,就能加快浸出速度。
扩散层的厚度与矿浆的搅拌强度成反比,即提高矿浆搅拌强度,可以使扩散层的厚度减薄,从而加快浸出速度。
应当指出,虽然加大矿浆的搅拌强度,能使扩散层减薄,但不能用无限加大矿浆搅拌强度来完全消除扩散层。
这是因为,当增大搅拌强度而使整个流体达到极大的湍流时固体表面层的液体相对运动仍处于层流状态;扩散层饱和溶液与固体颗粒之间存在着一定的附着力,强烈搅拌,也不能完全消除这种附着力,因而也就不能完全消除扩散层。
所以过分地加大搅拌强度,只能无谓地增加能耗。
三、酸浓度对浸出速度的影响
浸出液中硫酸的浓度愈大,浸出速度愈大,金属回收率愈高。
但在常规浸出流程中硫酸浓度不能过高,因为这会引起铁等杂质大量进入浸出液,进而会给。
锌的冶炼工艺流程
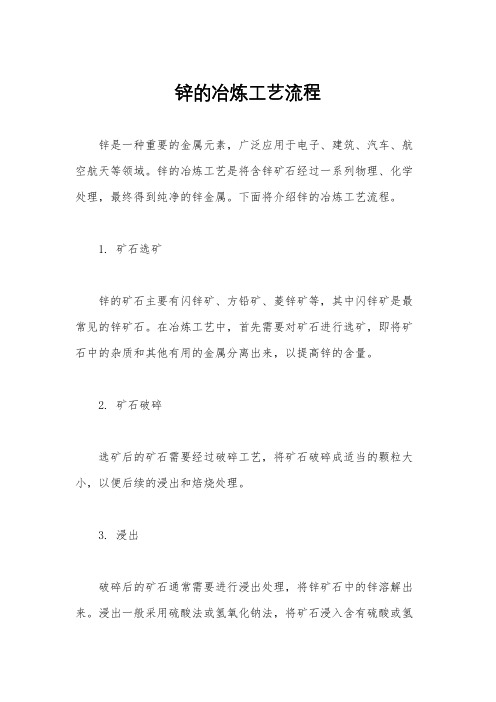
锌的冶炼工艺流程
锌是一种重要的金属元素,广泛应用于电子、建筑、汽车、航空航天等领域。
锌的冶炼工艺是将含锌矿石经过一系列物理、化学处理,最终得到纯净的锌金属。
下面将介绍锌的冶炼工艺流程。
1. 矿石选矿
锌的矿石主要有闪锌矿、方铅矿、菱锌矿等,其中闪锌矿是最常见的锌矿石。
在冶炼工艺中,首先需要对矿石进行选矿,即将矿石中的杂质和其他有用的金属分离出来,以提高锌的含量。
2. 矿石破碎
选矿后的矿石需要经过破碎工艺,将矿石破碎成适当的颗粒大小,以便后续的浸出和焙烧处理。
3. 浸出
破碎后的矿石通常需要进行浸出处理,将锌矿石中的锌溶解出来。
浸出一般采用硫酸法或氢氧化钠法,将矿石浸入含有硫酸或氢
氧化钠的溶液中,使锌溶解在溶液中。
4. 沉淀
通过浸出处理后,得到含锌的溶液,需要进行沉淀处理,将溶液中的杂质和其他金属沉淀出来,以提高锌的纯度。
5. 电解精炼
沉淀后的溶液中得到的锌粗品质量较低,需要进行电解精炼。
电解精炼是利用电解池,将锌溶液中的锌电解析出来,得到纯净的锌金属。
6. 熔炼
经过电解精炼后得到的锌金属需要进行熔炼处理,将锌金属熔化成液态,然后进行除杂和精炼,得到纯净的锌金属。
7. 铸造
最后,经过熔炼和精炼处理后得到的锌金属可以进行铸造,制成各种规格和形状的锌制品,如锌板、锌管等,以满足不同领域的
需求。
以上就是锌的冶炼工艺流程,通过选矿、破碎、浸出、沉淀、
电解精炼、熔炼和铸造等一系列工艺处理,最终得到纯净的锌金属,为各行业提供了重要的原材料。
锌浸出渣的处理
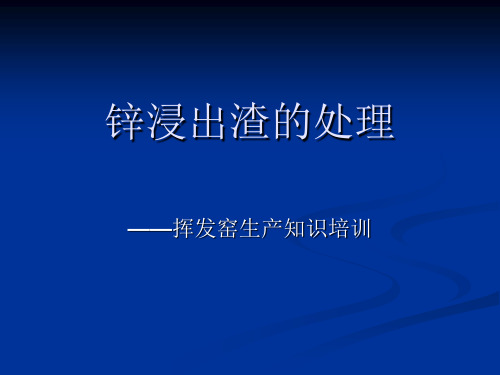
硫化锌:
在焙烧中未被氧化的硫化锌,不溶于稀硫酸而残 留在浸出渣中。硫化锌在渣中约占含锌量的25~ 30%,它在窑内的主要反应是与强制送入的空气 接触,被氧化,再被还原而挥发。此外也可与窑 内还原产出的金属铁和浸出渣中的氧化钙相互作 用产生锌蒸气。 ZnS+Fe=Zn(气)+FeS ZnS+CaO+C=Zn(气)+CaS+CO 但这两个反应是固相与固相接触,且需要温度较 高,故ZnS较难挥发。所以,当炉料中含ZnS过高 时,需要强制鼓风,才能达到较好的效果。
2、其他注意事项 窑头回火 拆除窑砖 打粘帮
十、新技术应用
低温带整体浇筑技术 富氧的运用
氧化锌:
以游离态存在渣中的氧化锌,数量很少, 其中一部分是由于来不及溶于稀硫酸而留 在渣中,它在窑内被还原: ZnO+C=Zn(气)+CO ZnO+CO=Zn(气)+CO2
硅酸锌:
焙烧过程形成的硅酸锌溶解于硫酸溶液中, 只有少量形成胶体物质而残留在浸出渣中, 在1100~1200℃时被还原,其反应如下: ZnO· SiO2+C=Zn(气)+SiO2+CO ZnO· SiO2+CO=Zn(气)+SiO2+CO2 当物料中含CaO时可加速ZnO· SiO2的还原: ZnO· SiO2+CaO+CO=Zn(气)+CaO· SiO2+CO2
锌直接回收率:92~95% 铅直接回收率:85~95% 窑生产能力:1.1~1.3t混合料/(m3· d) 窑渣含锌:<1.5% 窑渣含铅:0.5~0.7% 窑渣含碳:15~25% 窑渣率:64~68% 收尘效率:>99%
九、安全注意事项
1、 回转窑烘炉油枪使用安全注意事项
(1).油枪必须保证明火点燃。 (2)用油枪烘窑时,必须经常观察喷油及燃烧情况,保证油的正常燃烧。 如出现油灭火时,立即关闭油路阀门和油泵,防止发生爆炸。 (3)观察油枪燃烧情况时必须戴好口罩,要从观察孔侧面观察,不能正 对观察孔。 (4)出现回火现象时(风机停转、钟罩突然落下等造成),迅速离开窑 头罩观察孔、人孔门等位置,并关闭油泵,待处理好后,再按点油 枪操作要求重新点火。 (5)使用油枪时,调整油、风阀门,确保油的充分燃烧,观察烟囱不能 冒黑烟。 (6)按升温曲线进行升温。
锌精矿氧压浸出工艺浅述

工程设计与研究总第119期2006年6月锌精矿氧压浸出工艺浅述骆建伟1摘要2 介绍了锌精矿氧压浸出的工艺过程、工艺特点和工艺优势。
1关键词2 锌精矿;浸出;氧压浸出;二段氧压浸出1前言为处理碱金属硫化物和难熔金矿,加拿大Sherritt Gordon公司在上世纪50年代开发了氧压浸出工艺,最初用于处理镍精矿和铜精矿,后来推广到处理硫化锌精矿的工艺过程中。
上世纪80年代,硫化锌精矿氧压浸出工艺得到进一步发展,加拿大Dy natec公司开发了二段氧压浸出工艺处理锌精矿。
经过多年的技术改造,我国锌冶炼的技术装备水平有了很大提高。
但我国大部分锌冶炼企业年产量在2万t以下,整体而言与世界水平还有很大差距,锌冶炼仍处于粗放式生产阶段,低水平重复建设,规模小,工艺落后,生产成本高,环境污染严重,资源浪费大。
随着环境保护法规的日益严格,以及激烈的市场竞争形势,我国锌冶炼的发展方向将是朝着保护环境、减少能耗和降低成本三方面进行。
因此,加快技术进步,采用世界先进的新技术、新工艺,将是企业生存发展至关重要的因素。
2锌精矿氧压浸出的原理在氧压浸出工艺中,硫化锌或铅锌混合精矿直接加压氧化成硫酸锌溶液,硫酸锌溶液的净化和金属锌的电解沉积通过传统工艺来完成。
硫化锌精矿氧压浸出工艺是靠一个简单的基本反应来完成的。
硫化锌精矿与加入的废电解液中的硫酸在一定氧压下反应,以硫化物形式存在的硫被氧化为单质硫、锌转化到溶液中成为可溶性硫酸盐。
ZnS+H2SO4+1/2O2y ZnSO4+H2O+S(1)在缺乏加速氧传递介质的情况下,反应进行得很慢,这种传递介质为溶解的铁,一般精矿含有大量可溶的铁以满足浸出需要,反应通常是按以下两个步骤进行的。
ZnS+Fe2(SO4)3y ZnSO4+2FeSO4+S(2)2FeSO4+H2SO4+1/2O2yFe2(SO4)3+H2O(3)当溶液中没有足够的游离酸保持铁的溶解时,在锌浸出过程中将发生水解反应,铁的沉积物在溶液中以水合氧化铁和黄钾铁矾混合而成。
锌焙砂浸出(leachingofzinccalcine)

锌焙砂浸出(leachingofzinccalcine)用稀硫酸浸出剂选择性地将锌焙砂中的锌溶解到溶液中的过程,为锌浸出的常规方法。
锌焙砂浸出是湿法炼锌中最重要的环节,湿法炼锌厂的主要技术经济指标在很大程度上取决于所选择的浸出工艺及操作条件。
锌焙砂是硫化锌精矿流态化焙烧的产物。
稀硫酸浸出剂实际上是来自锌电解沉积车间的废电解液。
方法锌焙砂浸出一般在空气搅拌槽或机械搅拌槽(见浸出槽)内进行。
根据浸出作业所控制的最终溶液酸度,可将锌焙砂浸出分为中性浸出、酸性浸出和高温高酸浸出(热酸浸出)。
按浸出过程连续与否又可将锌焙砂浸出分为连续浸出和间断浸出。
按浸出过程的段数,还可将锌焙砂浸出分为一段浸出法、二段浸出法和三段浸出法;一段浸出法只采用中性浸出,这种方法可以避免锌焙砂中大量的可溶硅进入溶液,但金属回收率较低。
二段浸出法由一段中性浸出和一段酸性浸出或两段中性浸出组成。
三段浸出法由一段中性浸出和二段酸性浸出或二段中性浸出一段酸性浸出组成。
无论何种浸出工艺,都包含有中性浸出。
中性浸出中性浸出的任务是使锌焙砂中的大部分锌进入溶液,并利用中和沉淀法(见沉淀)除去从锌焙砂中进入溶液的铁、砷、锑和锗等杂质。
当锌焙砂与稀硫酸浸出剂接触时,锌焙砂中的锌和硫酸反应进入溶液:ZnO+H2SO4=ZnSO4+H2O同时也有部分杂质进入溶液。
为保证浸出过程迅速达到终点pH5.0~5.2。
一般控制浸出过程的锌浸出率低于60%。
常采用中和沉淀法除去进入溶液的铁、砷、锑、锗等杂质。
中和沉淀法是通过控制溶液的pH值,使杂质离子生成氢氧化物和同时生成的胶体氢氧化铁共沉淀除去。
在中性浸出控制pH5.0~5.4的条件下,只有Fe3+能以Fe(OH)3形态沉淀。
为此,在浸出作业中,通常用鼓入空气、加软锰矿(MnO2)或加锌电解沉积返回的阳极泥的方法,使Fe2+氧化成Fe3+。
为在沉淀铁的同时除去溶液中的砷和锑,要控制溶液中的含铁量为含砷量的10~15倍,为含锑量的20~40倍。
湿法冶锌工艺流程

湿法冶锌工艺流程概述:湿法炼锌是当今世界最主要的炼锌方法,其产量占世界总锌产量的85%以上。
近期世界新建和扩建的生产能力均采用湿法炼锌工艺。
湿法炼锌技术发展很快,主要表现在:硫化锌精矿的直接氧压浸出;硫化锌精矿的常压富氧直接浸出;设备大型化,高效化;浸出渣综合回收及无害化处理;工艺过程自动控制系统等几个方面。
湿法炼锌是用稀硫酸(即废电解液)浸出锌焙烧矿得硫酸锌溶液,经净化后用电积的方法将锌从溶液中提取出来。
当前,湿法炼锌具有生产规模大、能耗较低、劳动条件较好、易于实现机械化和自动化等优点在工业上占主导地位,锌总产量的80~85%来自湿法炼锌。
锌焙砂的浸出湿法冶锌的浸出是以稀硫酸溶液作为溶剂,控制适当的酸度、温度和压力条件,将含锌物料(如锌焙砂、锌烟尘、锌氧化矿、锌浸出渣、硫化锌精矿等)中的新华无溶解撑硫酸锌进入溶液,不容固体形成残渣的过程。
浸出所得的混合矿浆在经浓缩、过滤将溶液与残渣分离。
锌焙砂浸出的原则工艺流程:锌焙砂浸出是用稀硫酸溶液去溶解砂浸中的氧化锌。
作为溶剂的硫酸溶液实际上是来自锌电解车间的废电解液。
锌焙砂浸出分为中心浸出和酸性浸出的两个阶段,常规浸出流程采用一段中性浸出和一段酸性浸出或两端中性浸出的复浸出流程。
锌焙砂首先用来自酸性浸出阶段的溶液进行中性浸出。
中性浸出实际是用锌焙砂来中和酸性浸出溶液中的游离酸,控制一定的酸度(Ph=5.2~5.4),用水解法除去溶解的杂质(主要是Fe、Al、Si、As、Sb),得到的中心溶液经净化后送去电积回收锌。
中性浸出仅有少部分ZnO溶解,锌的浸出率为75%~80%,因此浸出残渣中还含有大量的锌,必须用含酸度较大的废电解液(含100g/L左右的游离酸)进行二次酸性浸出。
酸性浸出的目的是使浸出渣中的锌尽可能完全溶解,进一步提高锌的浸出率;同时还要得到过滤性良好的矿浆,以利于下一步进行固液分离。
为避免大量杂质同时溶解,终点酸度一般控制在H2SO4浓度为1~5g/L。
- 1、下载文档前请自行甄别文档内容的完整性,平台不提供额外的编辑、内容补充、找答案等附加服务。
- 2、"仅部分预览"的文档,不可在线预览部分如存在完整性等问题,可反馈申请退款(可完整预览的文档不适用该条件!)。
- 3、如文档侵犯您的权益,请联系客服反馈,我们会尽快为您处理(人工客服工作时间:9:00-18:30)。
3.3 浸出的生产实践(3)3.3.3热酸浸出工艺锌焙烧矿热酸浸出是20世纪60年代后期随着各种除铁方法的研制成功而发展起来的。
采用热酸浸出使铁酸锌分解后,浸出溶液中的铁含量高达30g/L左右,由于这种高铁溶液的铁能用黄钾铁矾法、针铁矿法以及赤铁矿法等从锌溶液中有效分离,使焙砂热酸浸出得到了广泛应用。
目前,国内外采用的沉铁方法以黄钾铁矾法的最多,有二十多家,其它都是在少数工厂采用。
热酸浸出的实质是锌焙烧矿的中性浸出渣经高温、高酸浸出,在低酸中难以溶解的铁酸锌以及少量其它尚未溶解的锌化合物得到溶解,进一步提高锌的浸出率。
一般是将常规浸出法的酸性浸出改为高温、高酸浸出,使浸出过程成为不同酸度、多段逆流的浸出过程。
其特点是浸出的酸度逐段增加,浸出渣量逐段减少。
由于铁酸锌及其他化合物溶解,浸出渣数量显著减少,使浸出渣中的铅、银、金等有价金属得到较大的富集,从而有利于这些金属的进一步回收。
3.3.3.1热酸浸出工艺流程热酸浸出工艺是在常规浸出工艺的基础上再增加一段或多段热酸浸出过程(并相应增加除铁过程)。
热酸浸出锌的浸出率较高,可达97%以上,两段热酸浸出锌的浸出率可达99%。
目前国内外热酸浸出工艺流程由于各生产企业的条件不同、除铁方式不同,各工厂的热酸浸出工艺流程亦不尽相同。
热酸浸出工艺可按浸出段数分成一段热酸浸出和多段热酸浸出工艺流程。
我国四川西昌炼锌厂采用一段热酸浸出工艺流程,(见图3—5),其优点是热酸浸出段处理量较少,可以节约设备和热能消耗。
我国西北铅锌冶炼厂年产电锌10×104t,采用热酸浸出—黄钾铁矾法沉铁的浸出流程,属于多段热酸浸出工艺流程,见图3—6。
该流程的特点如下:1)氧化液的配制是将电解废液与沉铁后液按一定比例混合,并在其中加入适量的氧化剂(主要是软锰矿和电解阳极泥)。
其作用是保证溶液中的Fe2+充分氧化为Fe3+,配制氧化液是在一个80m3的搅拌槽(俗称氧化槽)中进行,控制其酸度为60~90g/L,反应时间约0.5h,最终溶液含铁低于1g/L,其中Fe2+<0.1g/L,然后将配制好的氧化液送中性浸出工序进行焙砂的浸出。
图3—5四川西昌炼锌厂浸出工艺流程图2)中性浸出是在氧化液中加入焙砂,在串联的四台80m3的搅拌槽中进行,温度保持65~70℃,焙砂按一定比例加入中浸第一槽与第三槽,反应时间为2h,最终中浸浆化液的pH值控制在4.8~5.2之间,尽可能使焙砂中的锌进入溶液,而其中的铁、砷、锑等有害杂质被水解除去。
浆化液经φ21m浓密机液固分离后,合格的中浸上清(含Znl60~170g/L、含Fe<20mg/L)送去净化电积。
中浸渣含锌20%~25%,送热酸浸出。
3)热酸浸出分为I段高温高酸浸出和Ⅱ段高温超高酸浸出。
I段酸浸是在串联的四台80m3搅拌槽中进行。
温度保持90~95℃、反应3h,控制其酸度为40~50g/L。
I段酸浸出的浆化液经φ15m的浓密机液固分离后,上清液送预中和工序,而底流渣进入Ⅱ段酸浸。
Ⅱ段酸浸是在四台串联的80m3的搅拌槽中进行。
通过第一槽调节电解废液量和浓硫酸加入量来控制酸度,实现超高酸浸出,使铁酸锌和硫化锌进一步溶解,其反应为:ZnFe2O4+4H2SO4=ZnSO4+Fe(SO4)3+4H2OZnS+Fe2(SO4)3=ZnSO4+2FeSO4+S0锌被浸出的同时也有大量的Fe被溶解出来。
保持浸出温度95~98℃,反应时间4h,控制浆化液最终酸度在120~150g/L,经φ15m浓密机液固分离后,上清液返回I段酸浸以补充所需要的含酸溶液。
Ⅱ段底流经浆经过滤产出Pb-Ag渣,堆干后送铅系统QSL炉回收有价金属。
铅银渣的化学成分如下:成分Zn Pb Cu Cd SiO2Fe MgO Ag含量(%)4.3410.460.020.0731.1412.560.070.0295图3—6 西北铅锌冶炼厂热酸浸出—黄钾铁矾法工艺流程4)通过I段热酸浸出,由I段产生的上清液含酸为40~50g/L,送去预中和。
其操作是在两个串联的80m3搅拌槽中进行。
为了降低I段热酸浸出上清液的酸度,在预中和第一槽添加适量焙砂来中和酸。
控制温度为80~90℃,反应时间2h,最终预中和浆化液酸度为15~25g/L。
含铁约5~15g/L的浆化液经φ15m浓密机液固分离,底流返回I段酸浸继续浸出,而上清液送沉铁工序。
5)沉铁在连续串联的7台80m3搅拌槽中进行。
在第一槽和第三槽适量添加ZnO粉或锌焙砂作中和剂,并在第一槽按比例加入锰矿粉和硫酸钠添加剂,控制温度为90~95℃、反应时间为6h、pH值为1.5~2.0,同时控制钠离子的浓度并添加适量晶种以达到沉矾除铁的技术要求。
从沉铁第七槽流出的浆化液含酸约8~10g/L,含铁低于1g/L。
在沉矾中提高碱离子浓度可加速铁矾水解沉淀,常压下温度接近100℃时,几个小时内沉淀可接近完全。
形成黄钾铁矾的理想pH值为1.5~1.6,这就必须控制中和速度,若结晶过快,颗粒太细或溶液局部酸度过低,可导致Fe(OH)2沉淀生成。
由于黄钾铁矾晶体的生成比较缓慢,所以在沉矾过程中加入晶种,以缩短诱发期,能显著地促进铁矾的沉淀。
黄钾铁矾法能除去90%~95%的铁,残存的铁将在中性浸出过程中被进一步除去。
沉矾浆化液经φ21m浓密机液固分离,上清送中浸去配制氧化液;底流的1/3返回沉矾第一槽作为晶种;2/3送φ15m的三段逆向洗涤塔进行酸洗,酸洗上清返回沉矾系统,底流送过滤系统浆化,经圆筒过滤机进行一次过滤和折带过滤机进行二次过滤后产生铁矾渣。
铁矾渣的化学成分如下:成分Zn Pb Cu Cd SiO2Fe CaO MgO Ag含量(%)6.474.580.050.0712.0024.65 1.880.010.01253.3.3.2热酸浸出溶液沉铁铁酸锌虽然不溶解于常温下的稀硫酸溶液中,但当温度和酸度提高以后,就能很好的溶解。
这种技术称为高温高酸浸出,或者简称热酸浸出。
但是在热酸浸出的过程中,在锌溶解的同时,也有大量的铁随之溶解而进入溶液中,从而污染了溶液。
从溶液中除去铁,最通用的方法是前面所述的中和水解法。
在此,如果仍用中和水解法来除热酸浸出溶液中的铁,势必将产生大量的氢氧化铁胶体,而使澄清、过滤和洗涤产生很大困难,渣中并含有相当多的未起反应的焙烧矿。
所以,必须要采用更有效的方法来处理。
(1)黄钾铁矾沉淀法这个方法的实质就是在一定的温度和酸度的条件下,让溶液中的三价铁离子成为黄钾铁矾晶体而沉淀下来。
这种黄钾铁矾晶体既不溶解于硫酸,又容易沉淀、洗涤和过滤,从而解决了从浸出液中除去大量铁的困难。
黄钾铁矾是一种含水的碱性硫酸盐矿物,其通式为AFe3(SO4)2(OH)6,A可以是Na+、K+、Rb+、NH+、Ag+或H3O+等阳离子。
如果A是K+,则称黄钾铁矾,是Na,则称黄钠铁矾;是NH4+,则称黄铵铁矾;是H3O+,则称草黄铁矾。
人们习惯于将它们统称为黄铁矾或黄钾铁矾。
黄钾铁矾沉淀过程中发生的基本反应为:Fe2(SO4)3+6H2O = 6Fe(OH)SO4+H2SO44Fe(OH)SO4+4 H2O = Fe2(OH)4SO4+2 H2SO4从这些反应可知,当铁矾化合物沉淀时,都产生一定量的硫酸,需要用中和剂中和。
在湿法炼锌厂,最方便的中和剂是锌焙砂。
焙砂中的ZnO、Fe2O3均参与反应。
所需NH4+以NH3形式加入较好,加入量应比沉铁理论量多5~8%,因溶液中的其它物质参加反应。
因此,沉淀的产物往往也是几种黄钾铁矾的混合物。
铁沉淀的完全程度取决于过程的温度、溶液中的NH4+、K+、Na+等离子的浓度以及溶渡的酸度。
升高温度和增加溶液中NH4+、K+、Na+等离子的浓度时,都有利于使铁沉淀完全。
随着溶液pH值的降低,铁的沉淀率便降低。
黄钾铁矾法对除砷、锑、锗的效果不如中和除铁法,因此在处理含砷、锑、锗高的原料时,还应使一定数量的铁以氢氧化铁形态除去,以保证除砷、锑、锗等的效果。
进入黄钾铁矾中SO42-离子量约与铁量相等。
由于沸腾焙烧矿含硫酸盐形态的硫较高,往往引起锌湿法冶炼系统中硫酸过剩,黄钾铁矾中带走一定量的硫酸盐形态的硫,对生产过程中硫酸的平衡是有利的。
上面已经说到,黄钾铁矾法并不能把铁完全除掉,要将剩余的铁除去,必须要在其后用中和水解法除之;或将溶液送往中性浸出阶段中和;或插入一单独的中和阶段,在溶液中加入焙砂中和;或在澄清分离之前加以中和。
为了减少黄钾铁矾中锌的损失,可把沉淀物返回热酸浸出,也可用硫酸处理分离出来的黄钾铁矾渣。
黄钾铁矾法的主要优点是:能够提高锌、铜、镉的回收率;液固容易分离过滤;铅和贵金属可富集到较少的“二次渣”中,便于回收,可在常规流程的设备和厂房中进行,试剂消耗低,中和剂的作用比别的沉淀法彻底;可控制硫酸盐的积累,起平衡作用;浸出渣可作炼铁原料。
此法的缺点是:沉淀过程必须在酸性溶液中进行,得到的溶液中还残留一定量的铁,需进一步除铁,才能进去净化,造成流程复杂化,焙砂中的稀散金属在过程中较分散,不易回收;消耗钠盐和氨的量较大。
(2)针铁矿沉淀法针铁矿沉淀法是在高温中性硫酸锌溶液内通入分散的空气,使其中的Fe2+氧化为Fe3+,同时形成与天然针铁矿在品形和化学成分上相同的化合物沉淀。
针铁矿晶体易沉淀和过滤。
其反应是:4FeSO4+O2+6H2O=4FeOOH+4H2SO4在硫酸铁溶液中沉淀铁时,随Fe2(SO4)3的浓度不同,可以在硫酸铁溶液中形成各种化合物。
在很稀的溶液中:生成α—FeOOH(针铁矿);在浓溶液中:生成Fe2(SO4)3·5Fe2O3·15H2O;在更浓溶液中则生成4Fe2(SO4)3·5Fe2O3·27H2O(草黄铁矾)在生产上得到的高温高酸浸出液中一般含有30~40g/L的Fe2+,此浓度唯一能生成的沉淀将是不利于沉淀和过滤的草黄铁矾。
所以,要想采用空气氧化法得到α—FeOOH,就必须将溶液中的Fe3+全部还原成Fe2+,而后再向溶液中通入分散的空气,使Fe2+氧化成Fe3+,同时形成针铁矿沉淀。
从硫酸亚铁溶液中用分散空气来氧化Fe2+时,硫酸亚铁氧化成硫酸铁的水解产物,将随溶液的pH值不同而异。
当pH值降低时,溶液中的Fe3+升高,这时将生成一种像草黄铁矾一样的碱式硫酸盐;当pH值升高时,溶液中Fe3+降低.这时将生成a—FeOOH,即针三价氧化铁的水合物,故分子式又可以a—Fe2O3·H2O来表示,一般为棕黄色针状结晶。
另有一种γ型三价氧化铁的水合物γ—FeOOH,叫做臂状针铁矿,为红色鳞状结晶。
针铁矿是三价氧化铁中比较最为固定的一种。
a—FeOOH叫偏氢氧化铁,在水溶液中呈酸性,其等电点的pH值为5.2,而γ—FeOOH也叫正氢氧化铁,在水溶液中呈碱性,其等电点的pH值为7.7。