某地铁车站主体结构缺陷整治专项修补施工技术交底
地铁车站主体结构混凝土施工交底(DOC)

地铁车站主体结构混凝土施工交底(DOC)1.施工部位本次施工涉及地铁车站主体结构混凝土施工,包括车站墙体、地板、顶板以及相关基础等。
2.施工流程1.施工前准备:组织人员、材料准备、施工机械设备(如混凝土搅拌机、输送泵、打捣棒机等)的检查和调试。
2.浇注混凝土:按照设计要求浇注混凝土,并严格控制浇注高度、浇注速度和浇注面积等参数。
3.打捣和养护:在混凝土浇注后及时进行打捣处理,以确保混凝土型井自密实度符合要求。
同时进行养护,保持混凝土适宜的湿度和温度,以确保混凝土的强度和耐久性。
3.注意事项1.混凝土应按照设计标准掺配,严禁私自调整混凝土配合比。
2.浇注混凝土时,应密切关注混凝土流动性和浇注速度,确保混凝土浇注质量。
3.在混凝土浇注过程中,应注意对浇注面积进行适当控制,防止一次性浇注面积过大导致混凝土流失或过早凝固。
4.打捣处理应适时进行,并根据混凝土的硬化程度、温度和湿度等条件控制打捣力度和频次。
5.养护期间,应严格控制混凝土的湿度和温度,以达到最佳养护效果。
同时,避免触碰混凝土表面,以免影响其井自密实度。
4.安全注意事项1.施工过程中,应注意安全,严格遵守安全规定和操作流程,防止发生事故。
2.在混凝土浇注前,应对现场环境进行检查和清理,确保施工现场无障碍物和危险源。
3.混凝土泵车线路、操作板等设备应牢固可靠,严禁漏电、漏油等现象出现。
4.操作人员应接受专业培训和考核,掌握相关知识和技能,严格遵守工作规范。
5.质量控制1.混凝土应按照设计要求进行掺配,确保强度、密实度和耐久性满足相关标准。
2.浇注混凝土时,应对浇注高度、浇注速度、浇注面积等参数进行严格控制,确保混凝土均匀、密实、无裂隙。
3.打捣处理应根据混凝土的硬化程度、温度和湿度等条件,采用适当的力度和频率进行,以保证混凝土型井自密实度合格。
4.养护期间应按照相关要求进行,保持混凝土适宜的湿度和温度,以达到最佳养护效果。
6.检验标准本次混凝土施工应符合国家相关标准,具体包括但不限于以下标准:1.普通混凝土(GB/T 50107-2010)2.建筑结构用混凝土(GB/T 50080-2016)3.混凝土技术规范(GB 50082-2009)7.混凝土施工是地铁车站主体结构建设的重要环节,需要严格按照相关标准和要求进行施工。
地铁车站主体结构混凝土的施工交底

地铁车站主体结构混凝土的施工交底一、施工前的准备工作1.进行地下隧道的出土施工,确保安全、顺利进行。
2.检查施工所需的材料和设备,确认无误后可以进入施工阶段。
3.根据设计图纸和施工规范,确定混凝土配合比和施工工艺。
二、混凝土配合比的确定1.根据设计要求和材料性能,确定混凝土的配合比,包括水泥、砂、石、水和外加剂的比例。
2.配合比应满足混凝土的强度、耐久性和施工性能的要求,同时考虑成本和资源的利用。
三、模板的安装和调整1.根据设计要求和施工图纸,安装合适的模板和支撑体系。
2.检查模板的平整度和刚度,进行必要的调整和处理。
3.确保模板的内外表面涂有防粘剂,以便于拆模时的顺利脱模。
四、钢筋的加工和安装1.根据设计图纸和构造要求,预先加工好钢筋,包括弯曲、剪切和焊接等工序。
2.按照施工图纸和施工工艺,将预制好的钢筋安装到模板内,确保钢筋的位置准确、固定可靠。
五、混凝土的搅拌和浇筑1.根据搅拌站提供的配合比,将水泥、砂、石和水按照一定比例加入搅拌罐内进行搅拌。
2.搅拌过程中需要确保搅拌时间、搅拌速度和搅拌量的合理控制,以保证混凝土质量的稳定。
3.在搅拌完成后,将混凝土从搅拌罐输送到施工现场,进行浇筑和坑槽的密实工作。
六、混凝土的振捣和养护1.在混凝土浇筑后,立即使用振动器对混凝土进行振捣,以排除空隙和提高混凝土的密实度。
2.在振捣过程中需要控制振动时间、振动频率和振动力度,以确保混凝土的质量。
3.在混凝土养护期间,采取适当的措施,如喷水、遮阳等,以保持混凝土的湿润和适度的温度。
七、施工质量的检验和验收1.在混凝土养护期结束后,对施工质量进行检验,包括强度、平整度、尺寸和外观等方面。
2.根据设计要求和施工规范,对施工质量进行验收,符合要求的方可通过。
八、施工安全的注意事项1.在施工现场设置必要的安全警示和防护措施,包括围栏、标识和防护网等。
2.进行必要的安全培训,确保施工人员具备相应的安全知识和技能。
3.在施工过程中,严格遵守相关的安全操作规程,确保施工安全。
地铁车站主体结构防水施工技术交底一级

地铁车站主体结构防水施工技术交底一级
一、施工前的准备工作
1.1完善施工方案和技术交底,明确施工的目标和要求。
1.2对施工现场进行勘察,了解地铁车站主体结构的特点和材料的性质,为施工工作做好准备。
1.3确定施工人员和设备要求,保证施工人员的素质和设备的先进性。
二、防水材料的选择与调试
2.1根据地铁车站主体结构的特点和要求,选择适合的防水材料。
2.2对选定的防水材料进行调试,确保其性能指标符合要求。
三、基础处理与处理层施工
3.1对地铁车站主体结构的基础进行处理,确保基础的平坦和稳固。
3.2在基础上进行处理层施工,采用适当的材料和工艺,确保处理层
的平整和稳定。
四、防水层施工
4.1在处理层的基础上施工防水层,使用适合的防水材料和工艺。
4.2确保防水层的平整和完整,防止防水层的开裂和漏水。
五、交叉部位的处理
5.1对地铁车站主体结构的交叉部位进行处理,包括墙面与地面的交接、立柱与墙面的交接等。
5.2使用适合的处理材料和工艺,确保交叉部位的防水效果。
六、防水施工质量控制
6.1施工过程中进行质量检查和控制,确保施工质量符合要求。
6.2对已施工的防水层进行验收,确保防水层的质量符合要求。
七、施工后的维护与保养
7.1对已施工的防水层进行保养,确保防水层的长期稳定。
7.2定期检查和维护防水层,及时发现问题并进行处理。
以上是地铁车站主体结构防水施工技术交底一级的内容,通过合理的施工准备、材料选择和施工工艺,可以有效地保证地铁车站主体结构的防水效果,确保地铁车站的结构安全稳定。
地铁车站主体结构混凝土施工交底
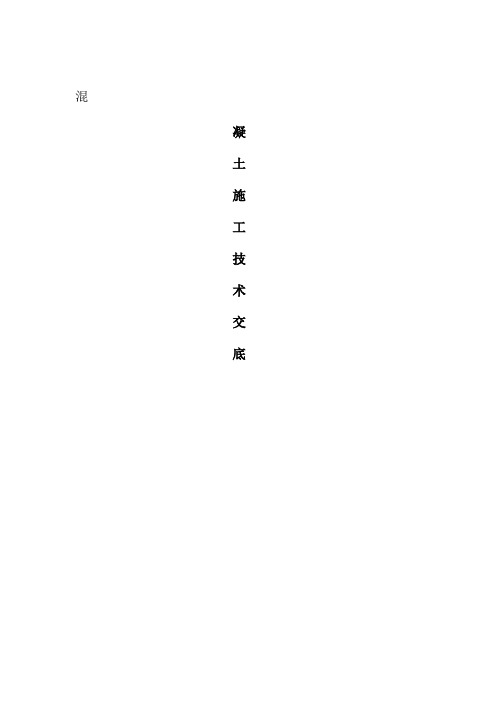
混凝土施工技术交底一、工程概况车站有效站台中心里程为XXXX,主体总长度XXXm,采用明挖法施工,其结构形式为双层三跨矩形框架结构。
标准段总宽度XXXm,基坑深度XXXm,覆土厚度XXXm。
盾构端头井段基坑西侧宽度为XXXm,平均深度为XXXm,东侧宽度为XX,平均深度为XX。
车站共设4个出入口,2组风亭。
围护结构采用桩撑+锚索支撑体系,主体结构采用钢筋混凝土箱型结构,结构外侧设全包防水层,与钻孔桩一起组成复合墙体系。
本车站明挖主体结构工程所使用混凝土强度等级如下:底板、底纵梁、边墙及顶板、顶纵梁:C40、P10;中柱:C30;中板、中纵梁:C40;楼梯及站台板:C30;框架立柱:C30;底板混凝土垫层:C13。
2.1设计概况1 建筑面积9230m22 层数地下 2 地上03 层高(m)B1(m) 3.33、3.63 B2(m) 3.33、4.53 非标准层(m) 5.365、4.50 标准层(m) 6.44、6.234 结构形式结构类型框架结构3 结构断面尺寸底板厚度(mm) 500侧墙厚度(mm) 630、400柱断面(mm) 400×400、400×900、400×1000梁断面(mm)500×1400、500×1000、500×1200、500×1400、400×430、2329×530、2330×530、500×1040、500×930、400×430、1400×400、1200×400、1000×400、1400×400、1130×400、900×2300 楼板厚度(mm)330、400、5006 抗震等级工程设防烈度5度地下结构抗震等级三级二、施工准备2.1技术准备2.1.1现场养护室设置要求及设备的准备工作由试验室负责准备试验委托,填写委托单,准备测试器具、试块模具以及其他有关工具,完成试验准备工作。
地铁车站主体结构混凝土施工交底

混凝土施工技术交底一、工程概况车站有效站台中心里程为XXXX,主体总长度XXXm,采用明挖法施工,其结构形式为双层三跨矩形框架结构。
标准段总宽度XXXm,基坑深度XXXm,覆土厚度XXXm。
盾构端头井段基坑西侧宽度为XXXm,平均深度为XXXm,东侧宽度为XX,平均深度为XX。
车站共设4个出入口,2组风亭。
围护结构采用桩撑+锚索支撑体系,主体结构采用钢筋混凝土箱型结构,结构外侧设全包防水层,与钻孔桩一起组成复合墙体系。
本车站明挖主体结构工程所使用混凝土强度等级如下:底板、底纵梁、边墙及顶板、顶纵梁:C40、P10;中柱:C30;中板、中纵梁:C40;楼梯及站台板:C30;框架立柱:C30;底板混凝土垫层:C13。
2.1设计概况二、施工准备2.1技术准备2.1.1现场养护室设置要求及设备的准备工作由试验室负责准备试验委托,填写委托单,准备测试器具、试块模具以及其他有关工具,完成试验准备工作。
混凝土抗压、抗渗试件在浇筑地点实行见证取样制作,同一配合比的留置组数按下列规定执行。
具体试件留置个数如下:1)抗压强度试件垫层混凝土每灌注一次留置1组。
每段结构的底板、侧墙及中板、顶板,车站主体各留置4组,附属建筑物结构各留置2组。
柱子混凝土结构,每灌注10根留置一组,一次灌注不足10根者,也留置1组。
2)抗渗强度试件:每段结构,车站留置2组,附属建筑物留置1组。
3)同条件养护强度试件底板:3组;中板:3组/层;顶板:3组。
2.2机具准备由现场生产经理负责现场内混凝土浇注中大型机械设备的准备工作,并综合考虑施工要求安排场地路线,以满足混凝土罐车停车要求和行走需要。
生产经理同时负责协调混凝土搅拌站生产设备、运输车辆等。
现场配备12台振捣棒,5台用于现场振捣,4台备用。
并配备4个临时配电箱,保证每个配电箱中引出插头不大于2个,塌落度桶3个。
三、主要施工方法及措施3.1流水段划分及施工操作顺序本车站为明挖基坑,施工时流水作业。
地铁车站主体结构混凝土施工交底

地铁车站主体结构混凝土施工交底一、施工准备工作1.组织施工人员,明确施工任务和责任;2.准备施工机械设备,包括混凝土搅拌站、泵车、砼运输车等;3.检查混凝土原材料的质量,确保符合设计和规范要求;4.检查施工现场的准备工作是否完成,包括地基处理、模板搭设等;5.制定施工方案和操作规程,明确施工的具体步骤和注意事项;6.安排好施工队伍的作业区域和通行路线,确保施工的安全和顺利进行。
二、模板的安装1.根据设计要求和模板图纸,组织施工人员进行模板的搭设;2.在地基上设置铺设防水层,确保混凝土浇筑过程中不发生渗漏;3.按照模板图纸的尺寸和位置要求,安装模板和支撑架,保证其牢固和稳定;4.检查模板的水平和垂直度,调整支撑架和水平仪,保证模板的准确性;5.安装好模板后,进行验收,确保其符合设计要求和规范要求。
三、钢筋的安装1.根据设计图纸和钢筋加工图进行钢筋的预制和加工,包括弯曲、剪切等工序;2.将预制好的钢筋进行分类、堆放,确保钢筋的承载能力和安全性;3.按照设计要求和构造图纸,将钢筋按照一定的间隔和要求进行焊接和绑扎;4.在焊接和绑扎过程中,要注意保护好钢筋的质量和表面处理,防止锈蚀和腐蚀;5.完成钢筋的安装后,进行验收,确保其符合设计要求和规范要求。
四、混凝土的浇筑1.将搅拌好的混凝土送到施工现场,确保施工的连续性和正常进行;2.在开始浇筑之前,要进行试块的制作和检测;在浇筑过程中,要进行工作面的处理和抹光;3.在开始浇筑之前,要调整好泵车和砼运输车的位置,将混凝土送到指定位置;4.控制好混凝土的坍落度和浇筑的速度,确保混凝土能够充分振实和填满模板空隙;5.混凝土浇筑过程中要及时控制温度和湿度,防止混凝土出现开裂和渗漏;6.浇筑完一层后,要进行密实处理和除气处理,保证混凝土的质量和密实性;7.完成混凝土的浇筑后,进行初始养护,避免早期龟裂和变形。
五、模板的拆除1.混凝土达到设计强度后,可以开始进行模板的拆除;2.拆除模板时要注意安全,使用专用工具进行拆除,防止对结构产生损坏;3.拆除模板时要逐层进行,先拆除顶部,再逐渐拆除底部,并注意保护好施工现场的清洁。
地铁车站主体结构混凝土缺陷修复方案

地铁车站主体结构混凝土缺陷修复方案地铁车站作为城市重要交通枢纽的一部分,需经常使用和维护。
由于长期受到重载、震动和湿度等因素的影响,地铁车站主体结构中的混凝土常常会出现各种缺陷,例如裂纹、蜂窝、空鼓、掉皮等。
这些缺陷如果得不到及时修复,会对车站的安全和使用寿命产生重大影响。
因此,制定一套有效的混凝土缺陷修复方案具有重要的实际意义。
1.确定缺陷的严重程度和原因:通过对地铁车站主体结构进行全面的检测和评估,确定混凝土缺陷的类型和严重程度。
同时,分析造成缺陷的原因,例如施工不当、材料质量问题等,以便修复方案的制定和预防措施的改进。
2.修复前的准备工作:在开始修复混凝土缺陷之前,需要进行一系列的准备工作。
首先是清理和清除缺陷部位的杂物和旧有涂层,确保操作的便利性和准确性。
其次是对缺陷部位进行打磨、修整和加固,以便为后续的修复工作提供良好的基础。
3.填补和修复缺陷:根据缺陷的不同类型和严重程度,选择合适的修复材料和方法进行修复。
对于小面积的裂缝和蜂窝,可以使用快速硬化的修补混凝土进行填补。
对于大面积的缺陷和掉皮,可以采用喷涂混凝土修复或者使用修复胶进行填补。
修复之后,需要进行充分的养护,以确保修补材料的性能和使用寿命。
4.强化和防护措施:在进行混凝土缺陷修复的同时,需要考虑增加主体结构的强度和耐久性。
可以使用加固材料(如碳纤维片、钢筋等)进行加固,以提高主体结构的受力性能。
此外,还可以对修复后的混凝土表面进行防护处理,使用涂层或者覆盖层来提高混凝土的抗渗透性和耐久性。
5.定期检测和维护:地铁车站主体结构的混凝土缺陷修复并不是一次性的工作,需要进行定期的检测和维护。
通过定期检测,及时发现和修复混凝土缺陷,可以避免缺陷扩大和破坏车站的主体结构。
综上所述,地铁车站主体结构混凝土缺陷修复方案应包括确定缺陷严重程度和原因、修复前的准备工作、填补和修复缺陷、强化和防护措施以及定期检测和维护等五个方面。
通过科学合理的修复方案和维护措施,可以延长地铁车站的使用寿命,保障乘客的安全出行。
地铁站主体结构施工安全技术交底
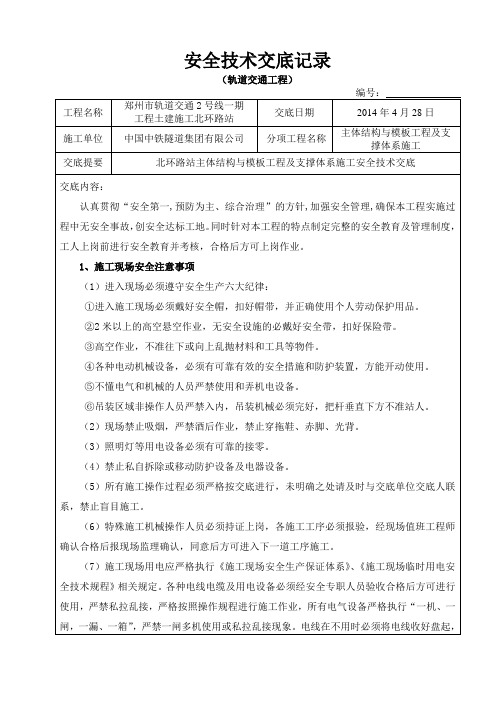
(9)施工现场电线电气设备设施采取防护措施,增设屏障、遮栏、围栏、保护网,必须有专业电工经常检查、维护、管理,发现问题及时解决。
(14)正确使用个人防护用品,进入施工现场必须戴好安全帽、扣好帽带,不得穿拖鞋,高跟鞋或光脚上班;不得穿硬底和带钉易滑鞋上高空。
(15)施工现场的种种设施,“四口”防护,安全标志,警示牌、安全操作规程牌等,不得任意拆除或挪动,要移动必须经现场施工负责人同意方可。
(16)施工现场设的效能指示标志,不得随意拆拿,场内工作要注意车辆来往及机械吊装。
⑤不懂电气和机械的人员严禁使用和弄机电设备。
⑥吊装区域非操作人员严禁入内,吊装机械必须完好,把杆垂直下方不准站人。
(2)现场禁止吸烟,严禁酒后作业,禁止穿拖鞋、赤脚、光背。
(3)照明灯等用电设备必须有可靠的接零。
(4)禁止私自拆除或移动防护设备及电器设备。
(5)所有施工操作过程必须严格按交底进行,未明确之处请及时与交底单位交底人联系,禁止盲目施工。
3、其他安全注脚手架搭设人员必须经过特殊工种的培训工作,坚持持证上岗,未持证人员坚决不能上岗工作。
(2)认真执行安全操作规程,严禁违章指挥,违章作业。
3.2支架及模板施工安全注意事项
(1)施工人员必须戴好安全帽,从事高空作业要系好安全带。
(2)脚手架的构配件质量与搭设质量符合规范《建筑施工扣件式钢管脚手架安全技术规程》(JGJ166-2008)、《建筑施工碗扣式脚手架安全技术规范》(JGJ166-2008)相关要求,并进行检查验收,合格后方可使用。
地铁车站主体结构混凝土施工交底..

地铁车站主体结构混凝土施工交底1. 前言本文档是针对地铁车站主体结构混凝土施工交底的技术规范,目的是确保施工质量和安全。
此次施工将完成地铁车站主体结构混凝土的浇筑和基本钢筋安装。
本文档将介绍具体的施工要求和流程。
2. 确定施工区域在进行混凝土浇筑前,需要清理好施工区域。
施工区域必须满足以下要求:•地面水平,不得有明显的高低差。
•环境温度不得低于5度。
•必须采取防止混凝土流失的措施,防止混凝土流向其他地方或下降到地下。
•施工区域需符合现场施工图规定的大小。
3. 基础钢筋的安装在混凝土浇筑之前,必须按照设计图纸要求安装钢筋。
施工区域必须满足以下要求:•保证钢筋的安装位置、数量和规格符合图纸要求。
•钢筋的设施初始状态必须与图纸要求一致。
•竖向钢筋的穿肚距离需符合设计要求。
4. 混凝土浇筑4.1 材料送浇场混凝土应在施工前进行质量检查。
施工前的做法如下:•首先检查混凝土的供应商和配送车辆。
•检查混凝土搅拌时间、搅拌次数和含水率。
•检查混凝土中的杂物、岩石和土壤。
4.2 测量混凝土浇筑高度在浇筑混凝土之前,必须先测量需要浇筑的高度。
必须按以下步骤进行:•在需要测量的区域上方的固定高度标记高度。
作为参考点。
•使用水平仪器在参考点与地面上测量所需高度,并标记一个线条。
4.3 浇筑混凝土•质量检查完成后,即可开始混凝土的浇注。
•保证施工周期不得超过两小时,以防止混凝土振捣性过小。
•浇筑混凝土时必须使用振动器和电锤振压,振动时间不得少于两分钟。
5. 混凝土养护混凝土浇筑完成后,必须在养护期内持续维持适质的湿度来使混凝土能够充分硬化。
具体要求如下:•混凝土覆盖必须保持湿润,防止混凝土出现裂缝。
•一般情况下,养护时间应在根据现场温度、地形和气象情况与专家确认后确定,并不得少于28天。
6. 整理现场混凝土养护完成后,必须进行现场清理。
现场整理工作包括以下内容:•将用过的工具,废弃物和简单设备移到指定位置进行妥善处理。
•清理浇筑混凝土的防渗材料。
地铁车站主体结构混凝土缺陷处理施工方案

地铁车站主体结构混凝土缺陷处理施工方案批准:审核:校对:编写:2014年4月目录一、编制依据 (3)二、工程概况 (3)三、存在的主要缺陷 (3)四、缺陷产生的原因 (4)五、缺陷处理要求及措施 (7)5.1、处理要求 (7)5.2、材料选择 (8)5.3、缺陷处理流程及处理措施 (9)5.3.1 缺陷处理施工工艺流程图 (9)5.3.2 施工准备 (9)5.3.3处理措施 (9)5.3.4渗水处理方法 (12)六、混凝土缺陷的预防措施 (15)6.1通过控制模板制作及安装质量预防 (15)6.2通过控制混凝土施工工艺 (16)6.2.1混凝土搅拌 (16)6.2.2混凝土浇筑与振捣 (16)6.2.3养护及拆模 (17)七、处理后检测 (17)八、资源配置 (17)8.1施工人员及人力准备 (17)九、现场安全文明施工措施 (18)9.1 安全生产措施 (18)9.2 文明施工措施 (19)9.3 环境保护措施 (19)一、编制依据1、《混凝土质量控制标准》GB50164-2011;2、《混凝土结构工程施工质量验收规范》(2011版)GB50204-2002;3、深圳市城市轨道交通7号线工程×××站设计图纸;4、《混凝土外加剂应用技术规程》GB5019-2003;5、《铁路混凝土工程施工质量验收标准》TB10424-2010;6、《地下防水工程质量验收规范》(GB50208-2002);7 、《砼结构加固设计规范》(GB50367-2006);8、《砼强度检验评定标准》(GBJ107-87);9、《砼泵送施工技术规范》(JGJ/T10-95);10、《地下铁道工程施工及验收规范》(GB50299-1999)。
二、工程概况×××站南端围护结构采用1000mm连续墙,主体结构采用盖挖逆作法施工。
主体结构为地下三层四跨现浇钢筋混凝土矩形框架结构,地下一层为站厅层,地下二层为设备层、地下三层为站台层。
地铁车站堵漏技术交底
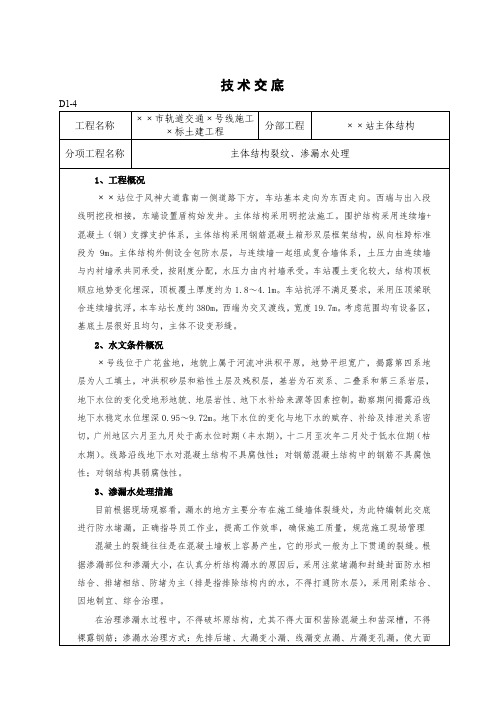
交底单位: 交底人: 复核人: 签发人:
承接单位或班组: 负责人(工长):
施工现场副经理: 负责人(领工员): 年月日
(5)拆嘴:灌浆完毕 24 小时,确认不漏即可去掉或敲掉外露的灌浆嘴。清理干净已 固化的溢漏出的灌浆液。
3.2 结构裂缝处理 (1)沿裂缝开槽钻孔,开 V 型槽,槽深 3~4 cm,孔深 10~15cm,孔径 1.0cm。 (2)采用快凝水泥封闭缝面并埋封灌浆管,要求压贴紧密。 (3)沿缝涂刷环氧界面剂,要求涂刷均匀,采用早强水泥埋管,压填紧密。 (4)依孔序进行施灌,施灌压力 0.4~0.8Mpa,要求进行二次或多次重复灌浆,以 确保注浆效果。
(4)灌浆:使用高压灌浆机试压,不得超过砼结构受压范围。向灌浆孔内灌注化学 灌浆料。单孔逐一连续进行。当相邻孔开始出浆后,保持压力 3~5 分钟,即可停止本孔灌 浆,改注相邻灌浆孔。待所有的孔都灌完后,回到先前第一个灌浆孔,再次灌浆以保证压 力最大化。墙面灌浆顺序则为由下向上;待所有的孔灌完后同样也是回到先前第一个灌浆 孔回灌一次。
积渗漏水汇集一点或几点,最后集中封堵。 3.1 蜂窝处渗漏水的治理 根据该项目工程结构特点和渗漏水的特征,在选用施工工艺和堵漏材料上应全衡利
弊、扬长避短,综合考虑,修补时所用的水泥砂浆颜色应与其周边颜色一致以防影响整体 美观。
(1)清理:详细检查、分析渗漏情况,确定灌浆孔位置及间距。清理干净需要施工 的区域,凿除砼表面析出物,确保表面干净。
(2)钻孔:使用钻孔工具沿孔洞四周钻泄压孔,钻头直径为 14mm,钻孔角度宜≦45°, 钻孔深度≦结构厚度的 2/3,钻孔必须斜穿过主漏水孔。但不得将结构打穿,因动水较大 孔洞内的粉尘会自行冲洗干净。墙面慢渗则分别在渗水面钻梅花孔。用清洗机冲洗灌浆孔, 直至灌浆孔出水清澈则可进行下一步工作。
地铁车站主体结构缺陷处理施工技术交底二级
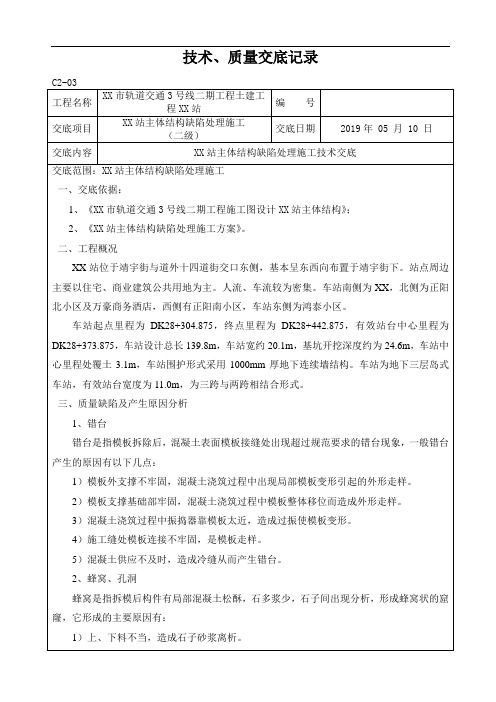
技术、质量交底记录
交底项目XX站主体结构缺陷处理施工
(二级)
交底日期2019年 05 月 10 日
交底内容XX站主体结构缺陷处理施工技术交底
3)混凝土接头部位产生收缩造成开裂。
4)施工缝防水施工不良造成防水失效。
5)混凝土中的杂物较大形成过水通道。
6)混凝土收缩或结构裂缝。
7)浇注时振捣不良导致不密实、内部空洞等原因形成积水。
四、缺陷处理流程
图4.1-1缺陷处理施工工艺流程图
五、缺陷处理方法
1、错台缺陷处理方法
对于凹凸错台的质量缺陷尽可能采用凿除、打磨等防范进行;如果凹陷较严重,凿除、打磨方法不能满足要求,则对凹陷部位表面进行凿毛,并用比原混凝土设计强度等级高一级的细石混凝土或预缩砂浆填补。
2、蜂窝、孔洞缺陷处理方法
交底项目XX站主体结构缺陷处理施工
(二级)
交底日期2019年 05 月 10 日
交底内容XX站主体结构缺陷处理施工技术交底
渗漏缝
钻孔。
地铁车站主体结构混凝土施工交底

混之樊仲川亿创作凝土施工技术交底一、工程概况车站有效站台中心里程为XXXX, 主体总长度XXXm, 采纳明挖法施工, 其结构形式为双层三跨矩形框架结构.标准段总宽度XXXm, 基坑深度XXXm, 覆土厚度XXXm.盾构端头井段基坑西侧宽度为XXXm, 平均深度为XXXm, 东侧宽度为XX, 平均深度为XX.车站共设4个收支口, 2组风亭.围护结构采纳桩撑+锚索支撑体系, 主体结构采纳钢筋混凝土箱型结构, 结构外侧设全包防水层, 与钻孔桩一起组成复合墙体系.本车站明挖主体结构工程所使用混凝土强度品级如下:底板、底纵梁、边墙及顶板、顶纵梁:C40、P10;中柱:C30;中板、中纵梁:C40;楼梯及站台板:C30;框架立柱:C30;底板混凝土垫层:C13.二、施工准备2.1技术准备2现场养护室设置要求及设备的准备工作由试验室负责准备试验委托, 填写委托单, 准备测试器具、试块模具以及其他有关工具, 完成试验准备工作.混凝土抗压、抗渗试件在浇筑地址实行见证取样制作, 同一配合比的留置组数按下列规定执行.具体试件留置个数如下:1)抗压强度试件垫层混凝土每灌注一次留置1组.每段结构的底板、侧墙及中板、顶板, 车站主体各留置4组, 附属建筑物结构各留置2组.柱子混凝土结构, 每灌注10根留置一组, 一次灌注缺乏10根者, 也留置1组.2)抗渗强度试件:每段结构, 车站留置2组, 附属建筑物留置1组.3)同条件养护强度试件底板:3组;中板:3组/层;顶板:3组.2.2机具准备由现场生产经理负责现场内混凝土浇注中年夜型机械设备的准备工作, 并综合考虑施工要求安插场地路线, 以满足混凝土罐车停车要求和行走需要.生产经理同时负责协调混凝土搅拌站生产设备、运输车辆等.现场配备12台振捣棒, 5台用于现场振捣, 4台备用.并配备4个临时配电箱, 保证每个配电箱中引出插头不年夜于2个, 塌落度桶3个.三、主要施工方法及办法3.1流水段划分及施工把持顺序本车站为明挖基坑, 施工时流水作业.施工顺序见图2-1:具体施工流水段划分见图2-2.3.2混凝土的运输3商品混凝土质量控制(1)混凝土采用罐车运输至现场, 现场泵送浇筑.拌混凝土自搅拌机卸出后应及时送到浇筑地址, 在运输过程中, 要防止混凝土离析、水泥浆流失、坍落度变动以及发生初凝现象, 若发现离析或分层应进行二次搅拌.(2)混凝土运输车的搅动转速应保证为2~4r/min, 整个输送过程中拌桶的总转数控制在300转内.(3)由于主体结构各部位申请混凝土的塌落度分歧则搅拌站应根据路程距离、运输时间和塌落度损失情况综合考虑商品混凝土初始塌落度, 并要求混凝土运输车在规按时间内进入施工现场.具体把持可参照下表:(4)混凝土运至浇筑地址, 最高温度不得超越25度, 最低不得低于3度.(3)对参加的混凝土罐车要逐车检验塌落度, 对不符合之前砼运输通知单上塌落度要求的必需退厂, 退厂车辆3小时内不得再次进场.(6)如果在震捣后发现混凝土有离析、泌水现象要向搅拌站随车技术人员反映, 及时进行调整, 对接缝部位及钢筋较密砼不容易进行震捣的部位现场混凝土的检验更要严格进行.3现场混凝土输送方式的选择本车站场地狭小, 只有在基坑北侧以及基坑西北侧具备安设泵车和输送泵条件, 因此根据现场条件现场混凝土输送方式如下:1~6流水段底板、中板、顶板及上下翻梁、构造柱等在基坑北侧由混凝土输送泵泵送砼浇筑;4、5流水段由于距离较远, 因此底板、中板、顶板及上下翻梁、构造柱等在输送泵不能满足要求的时候采纳地泵泵送砼浇筑.3.3混凝土浇筑3一般要求模板、钢筋、预埋件的隐预检:在混凝土浇筑前为保证结构尺寸, 隐敝构件的准确位置需要质检人员认真检查, 车站结构钢筋呵护层背水面4cm, 迎水面3cm.立模后必需保证钢筋呵护层厚度以免发生露筋和呵护层超厚问题.呵护层厚度通过混凝土垫块或塑料卡环进行控制.底板、中板、顶板、翻梁采纳木模, 木模采纳多层板制作面前用槽钢做肋, 增强木模刚度, 支撑采纳斜三角撑, 在施工底板混凝土时预埋地脚螺栓.木模概况涂刷色拉油以保证混凝土面的光洁度.车站构造柱采纳年夜块钢模板, 四周采纳方钢柱箍, 地板预埋螺栓张拉.浇筑砼前必需认真检查模板稳定水平, 如有松动必需让工人重新校正后方可浇筑砼.认真熟悉图纸内容, 车站预留空洞特别多尤其是中板上空洞较多, 空洞边多有暗梁施工时一定预留准确.另外, 结构预埋件较多例如电梯井预埋吊钩、站台板预埋插筋等.这些预埋件在教柱砼时必需同图纸核对保证万无一失后方可进行混凝土浇筑.如采纳泵送混凝土, 泵送混凝土前, 应首先泵送与将要泵送混凝土内除粗骨料外其他成份相同配比的水泥砂浆, 起到润湿泵管的作用;开始泵送时, 混凝土泵应处于慢速, 然后逐渐加快, 同时观察混凝土泵的压力和各系统的工作情况, 待各系统运转顺利后, 再按正常速度进行泵送.正常泵送过程中, 混凝土泵的活塞应尽可能坚持在最年夜行程运转, 这样可以提高输出效率, 同时有利于机械呵护.在浇筑过程中, 随时观察模板是否发生变形.包括模板平整度、倾斜度以及是否发生错台、跑模情况.3施工缝在继续浇筑前的处置及要求①在施工缝部位上一段的预留筋在上一次浇筑时会被砼沾染,必需用钢刷子将浮浆刷失落, 已浇老砼概况重新浇砼前, 应清除垃圾、硬化的水泥浆乳皮、概况松动砂石等, 清除后在老砼面上凿毛, 然后再用清水冲刷干净.②对防水资料加强呵护, 外贴式和中埋式止水带如果在上一段砼浇筑过程中外露部份小于12cm必需对混凝土进行凿除直到满足要求为止.③对施工缝部位的防水资料在浇筑混凝土前应妥善呵护, 用木板进行覆盖, 浇筑前再将呵护层裁撤.3混凝土浇筑与振捣3.1混凝土浇筑混凝土浇筑采纳汽车泵和地泵输送, 坍落度宜为:板、梁及框柱160~150mm, 侧墙140~160mm.①砼下料重点应防止分层离析, 出料点距浇筑面自由倾落高度一般不宜超越2m, 若因条件限制年夜于2m, 必需采纳助溜筒(串筒)、斜槽等设施下料.对仓面狭窄, 钢筋密集, 结构高度年夜于3m的墙, 不具备条件设溜筒、溜槽时, 应在模板适当部位开下料窗口, 使砼下料自由倾落高度在2m以内.②浇筑混凝土连续进行.如间歇, 其间歇时间尽量缩短, 并在前层混凝土初凝前, 将次层混凝土浇筑完毕, 间歇的最长允许时间按试验确定, 如超越最年夜允许间歇时间按施工缝处置.③浇筑混凝土时派专人观察模板钢筋、预留孔洞、预埋件等有无位移变形或梗塞情况, 发现问题立即处置, 并在已浇筑的混凝土初凝前处置完成.④混凝土分层浇筑振捣, 每层浇筑厚度控制在300mm左右, 混凝土下料点分散安插循环推进, 连续进行, 并严格控制好混凝土浇筑的延续时间.⑤车站中板厚度只有40cm, 混凝土浇筑时先浇筑中板两侧边墙处P10抗渗混凝土, 和中板普通混凝土接茬处留成43度斜坡.中板混凝土浇筑采用由一端向另一端斜向薄层推进, 用泵送骨料.⑥车站底板和顶板浇筑时, 沿车站纵向由一端向另一端推进.每层混凝土浇筑厚度控制在30cm以内, 一层浇筑完成后再反向浇筑, 以此类推直到浇筑究竟板上概况, 待底板混凝土初凝后开始浇筑腋脚和上翻梁部位, 防止混凝土未初凝招致振捣上翻梁和腋角时板混凝土鼓包.⑦车站侧墙浇筑时由于侧墙较高采纳泵送软管伸入模板底部再进行浇筑防止混凝土自由塌落高度年夜于2米.3.2混凝土振捣①使用拔出式振动器要做到快插慢拔, 快是为了防止先将概况砼振实而与下面未振实的砼发生分层、离析;慢拔目的是使振动棒抽出时的空间砼能填满.插点均匀排列, 逐点移动, 按顺序进行, 不得遗漏, 做到均匀振实.拔出振捣器防止碰撞钢筋, 更不得放在钢筋上, 在施工缝处应充沛振捣, 且严禁触碰止水带;振捣机头开始转动以后才华拔出混凝土中, 振完后, 徐徐提出, 不能过快或停转后再拔出来, 振捣靠近模板时, 拔出式振捣器机头须与模板坚持3~10cm距离.振捣时间:一般每点振捣时间为20~30秒, 使用高频振动器, 最短不应少于10秒.肉眼观察, 振捣合格应视砼概况呈水平不再显著下沉, 不再呈现气泡, 概况泛出灰浆为准.移动间距不年夜于振动棒作用半径的1.3倍(一般为300~400mm), 振捣上一层时拔出下层混凝土面30mm, 以消除两层间的接缝.概况振动器在同一位置上连续振动时间一般为23~40秒, 也可以砼概况均匀泛出浆液为准, 作业时前后位置搭接应有30mm左右, 防止漏振.附着式振动器应待砼入模后才华启动, 接受附着式振动器的模板支撑应考虑附着振动器工作的情况.②混凝土振捣均由专业振捣手负责, 并防止漏振, 班前对振捣区域进行责任承包, 施工员给振捣手讲解注意事项, 相对分条块浇筑时, 振捣人员在分界处振捣过界线不小于30cm.3.4重点、难点部位的控制主体结构混凝土施工采纳分段浇筑, 施工缝较多, 施工缝部位处置欠好, 会成为防水的薄弱环节, 影响接缝的混凝土质量和防渗漏效果;同时在车站明挖主体结构同附属结构、两端区间隧道接口处, 如何预留洞口, 如何进行模板施工, 如何在洞口预留防水卷材和止水带为施工难点;另外, 在主体结构混凝土施工过程中, 存在分歧强度品级及抗渗品级的混凝土浇筑(梁柱节点处), 设计要求此时应浇筑高强度品级和高抗渗品级的混凝土,如何按设计要求进行此处的混凝土浇筑, 并尽量减少高品级混凝土的使用方量亦为一施工难点.⑴施工缝、变形缝处置在施工缝位置按设计文件的要求装置好镀锌钢板止水带, 在混凝土浇筑前, 镀锌钢板止水带应装置牢固, 并在施工缝位置使用厂家提供的“T”字或“十”字接头搭接预留;在明挖主体结构与其它结构(盾构区间、附属结构)接口位置, 沿洞口轮廓预埋木板, 作为预留防水卷材及止水带的呵护层, 然后铺设预留搭接防水卷材及止水带, 外部在铺设0.5mm后钢板作为隔离层, 防止混凝土浇筑时与之粘贴.此处模板使用定做钢模板, 以便更好的保证混凝土外观质量.在浇筑下一段混凝土时, 应对上一段浇筑的混凝土概况进行凿毛处置, 凿除概况浮浆, 在水平施工缝处浇筑前应先铺一层净浆, 对施工缝处的混凝土必需认真振捣, 确保混凝土结合紧密, 同时应防止振捣棒直接接触止水带.⑵梁柱节点处的混凝土浇筑梁板钢筋绑扎时, 定好框柱位置及尺寸, 在其周边30cm范围使用收口网封堵, 收口网外侧使用钢筋固定, 高度范围对应纵梁高度, 形成封闭区域;浇筑混凝土时, 首先使用C30、P10混凝土进行框柱浇筑, 至底板设计顶标高后, 为防止收口网受混凝土侧压力较年夜而破坏, 开始浇筑附近区域底板及底纵梁混凝土, 使用C40、P10标号, 待板梁混凝土到达设计要求底板标高后, 再次进行框柱混凝土施工直至梁顶标高位置.3.5混凝土制品的养护及呵护(1)混凝土浇筑完毕后, 对板面赔偿收缩混凝土, 采纳塑料布加草帘保湿覆盖养护, 坚持混凝土概况湿润, 养护时间很多于14d;对墙体赔偿收缩混凝土, 从顶部设水管喷淋;拆模后用湿麻袋贴墙覆盖, 并浇水养护, 坚持混凝土概况湿润, 养护时间很多于14d.(2)浇水次数, 以坚持混凝土处于湿润状态为准.(3)采纳塑料布覆盖养护的砼, 其敞露的全部概况应覆盖严密, 并应坚持塑料布内有凝结水.(4)年夜体积混凝土的养护, 应根据气候条件及混凝土自己的温度采用控温办法, 两者温差不宜超越20℃.(3)模板裁撤后, 对现浇混凝土结构除严格按设计规范要求进行养护外, 还需对制品结构进行需要的呵护.梁、柱结构在现浇混凝土到达一定强度后, 裁撤模板, 但此时其棱角部位仍较薄弱, 容易在进行其它工序施工时被碰撞破损;为更好的保证混凝土外观, 保证结构质量, 在梁、柱及其它带有棱角的混凝土结构拆模后, 及时将加工成直角的竹胶板固定于结构棱角处, 作为护角板呵护结构棱角部位.如图:四、质量要求4.1质量控制要点⑴模板板缝、模板与预埋件之间间隙和模板与上一次混凝土面接缝处间隙加设防漏浆胶条, 如模板拼缝宽度超越 1.0mm时, 用泡膜塑料填封, 再在接缝处贴专用胶带纸, 以防混凝土概况漏浆呈现蜂窝麻面..⑵混凝土灌筑前应对模板、支架、钢筋、预埋件、预留孔洞、施工缝、变形缝止水带等进行检查, 清除模板内杂物, 隐蔽验收合格后, 方可灌筑混凝土;混凝土灌筑过程中应随时观察模板、支撑、防水板、钢筋、预埋件、预留孔洞等情况, 发现问题及时处置.⑶按规定使用和移动振动器, 防止振捣不实或漏振, 中途停歇后再浇捣时, 新旧接缝范围小心振捣.并注意不得过振, 以防止混凝土概况翻砂影响外观质量.⑷模板平整光滑, 装置前把粘浆清除干净, 并满涂隔离剂, 浇捣前对模板充沛浇水湿润.⑸在钢筋较密部位, 分次下料, 缩小分层振捣的厚度, 以防止呈现孔洞.4.2车站混凝土结构的允许尺寸偏差及检查方法现浇混凝土结构不应有影响结构性能和使用功能的尺寸偏差.因为过年夜的尺寸偏差可能影响结构构件的受力性能、使用功能,也可能影响设备在基础上的装置、使用, 使结构不能满足设计要求.对结构的尺寸、净空控制, 在结构施工前, 首先根据规范、设计要求及经验数据, 讨论确定其相应外放值, 然后在钢筋绑扎、模板装置时严格控制其相应尺寸线, 混凝土浇筑前, 对模板的控制尺寸线及垂直度严格检查.为确保结构竣工验收时满足要求, 在模板裁撤后, 根据规范要求的各结构尺寸偏差使用仪器进行全面检查.现浇结构和混凝土设备基础拆模后的尺寸偏差及检验方法如下表:现浇结构尺寸偏差和检验方法注:检查轴线、中心线位置时, 应沿纵、横两个方向量测, 并取其中的较年夜值.检查数量:按楼层、结构缝或施工段划分检验批.在同一检验批内, 对梁、柱和自力基础, 抽查构件数量的10%, 且很多于3件;对墙、板结构, 墙按相邻轴线高度3m 左右划分检查面, 板按纵、横轴线划分检查面, 抽查10%, 且均很多于3面;对电梯井, 全数检查.对设备基础, 全数检查. 4.3混凝土施工的质量通病及防治办法每次混凝土浇筑完成待拆模后, 由项目经理或总工组织工程部、质安部、施工员、模板及混凝土作业班长进行现场验评, 查找缺乏, 认真总结;针对本次混凝土施工所发生的通病, 分析原因, 召开讨论会, 研究预防办法, 并对可能呈现问题的每一环节落实到部份或个人, 严格把关.主要从以下几个方面进行分析:(1)麻面为有效防止此问题的发生, 工程部指派专人——进行全程监督模板清理及涂刷模板漆工作, 要求立模前模板清理干净, 模板漆按要求配比涂刷均匀, 并在涂漆后及时立模, 模板漆干燥过程中, 做好防护;模板加固后, 工程部和质安部共同检查模板垂直度及模板拼缝处的平整度和密实性;混凝土浇筑前(如使用泵车), 要求项目部当天值班人员现场监控, 必需首先泵送同准备浇筑混凝土相同强度品级的水泥砂浆, 并严格依照技术交底进行振捣.(2)蜂窝为有效防止此问题, 要求项目部现场值班人员, 严格检查商品混凝土的随车资料, 仔细核对各配料的参数, 发现与规范或设计要求不符的, 要求该车退回;同时要求混凝土作业班组严格依照技术交底进行分层浇筑和振捣, 并要求木工班组安插两人进行现场巡视, 发现模板松动或漏浆部位, 立即进行加固封堵.(3)凹洞为预防现浇混凝土结构呈现凹洞, 对混凝土作业班组仔细交底, 详细解释混凝土浇筑时的振捣方法, 严格要求混凝土的自由倾落高度, 并要求项目部当天值班人员全程监控, 加强技术和质量管理.(4)露筋为预防露筋现象的发生, 并防止粘模, 派专人进行现场监督模板漆的涂刷工作, 并在模板检查时, 重点检查钢筋呵护层的厚度, 严格依照设计规范执行, 加密垫块或塑料卡环并固定牢固;拆模时前, 应向实验工程师许晨提交拆模申请, 根据同条件养护试块的实验结果, 确定拆模日期.五、平安注意事项5.1一般要求⑴所有进入施工现场的人员必需戴好平安帽, 并按规定配戴劳动呵护用具, 加平安带等平安工具.⑵作业人员不得穿拖鞋、高跟鞋、硬底易滑鞋进入施工现场.⑶在基坑边缘设置护栏并挂设护网, 且不低于 1.2m, 并要稳固可靠.⑷施工现场平安设施平安网、围护、洞口盖板、护栏、防护罩、竖井防护栏杆等, 各种限制装置齐全、有效, 不得擅自移动.⑸施工现场除设置平安宣传口号牌外, 危险地段必需悬挂依照GB2593—52《平安色》和GB2594—52《平安标识表记标帜》规定的标牌, 主要作业场所和平安疏散通道设立24小时的36伏平安照明, 夜间有人经过的坑洞等设红灯示警.⑹雷雨天钢筋施工人员禁绝进行钢筋绑扎和焊接作业, 以防雷电伤人.5.2泵送的平安要求泵送机具使用时必需由专职人员负责进行检查和维修, 确保状况良好.各技术工种必需经过培训考核取得合格证, 方可持证上岗把持, 根绝违章作业.⑴砼输送管就位依照要求进行, 转弯处固定牢固, 接头处管箍上紧、密封圈齐全、最前端软管由专人负责看管固定, 防止伤创作时间:二零二一年六月三十日人事故发生.⑵把持人员必需持证上岗, 必需按规程要求进行把持, 并作好作业记录.⑶各类平安(包括制动) 装置的防护罩、盖等要齐全可靠.⑷机械与输电线路(垂直、水平方向) 须按规定坚持距离.⑸作业时, 机械停放稳固, 臂杆幅度指示器灵敏可靠.⑹电缆线绝缘良好, 不得有接头, 不得乱拖、乱拉.⑺必需严格按期调养制度, 做好把持前和把持后设备的清洁润滑、坚固、调整和防腐工作.严禁机械设备超负荷使用、带病运转和在作业运转中进行维修.⑻机械设备夜间作业必需有良好的照明设备, 有充分的照明.⑼雨、夏季车辆行驶时要防冻、防滑.⑽车站在前期土方施工时运输机械车辆较多, 在施工中要作好统筹安插及平面规划, 进、进场路途分离, 统一调度指挥.创作时间:二零二一年六月三十日。
地铁车站主体结构防水施工技术交底(一级)[详细]
![地铁车站主体结构防水施工技术交底(一级)[详细]](https://img.taocdn.com/s3/m/7e8341a702768e9950e73867.png)
技术、质量交底记录
交底项目清真寺站主体结构防水施工(一级) 交底日期2021年 05 月 10 日
交底内容清真寺站主体结构防水施工技术交底
序号工种名称人数
1 卷材铺装队 4
2 止水带安装队 2
3 顶板聚氨酯队 4
合计10
五、施工方法
1、施工工艺流程
图5.1-1防水施工工艺总流程图
2、高分子自粘胶膜防水卷材施工工艺流程:
基层找平处理→阴阳角倒角→铺设加强层→防水卷材铺设→固定、压边→验收。
3、聚氨酯涂膜防水施工工艺流程:
基层找平压光→阴阳角倒角→涂刷涂膜加强层→粘贴聚酯布增强层→涂膜防水层施工→验收→保护层。
4、自粘聚合物改性沥青防水卷材施工流程:
清理基层→涂刷基层处理剂→铺贴附加层卷材→铺贴自粘橡胶沥青防水卷材→卷材搭接缝的粘结和密封→防水层质量检查及质量处理→覆盖沥青油毡隔离层→浇筑细石混凝土
交底项目清真寺站主体结构防水施工(一级) 交底日期2021年 05 月 10 日
交底内容清真寺站主体结构防水施工技术交底
2、工作场地四周排水沟要及时疏通,并备好抽水机。
雨期加强抽水,确保施工正常进行。
工作场地、运输道路等应采取适当的防滑措施确保安全。
6、在大风来临之前对塔吊、脚手架等加强安全检查,确保附墙与缆风绳安全牢固,必要时要加缆风绳临时固定。
车站标准段防水构造图
交底项目清真寺站主体结构防水施工(一级) 交底日期2021年 05 月 10 日交底内容清真寺站主体结构防水施工技术交底
车站施工缝防水构造图
车站诱导缝防水构造图。
地铁车站主体结构安全技术交底二级
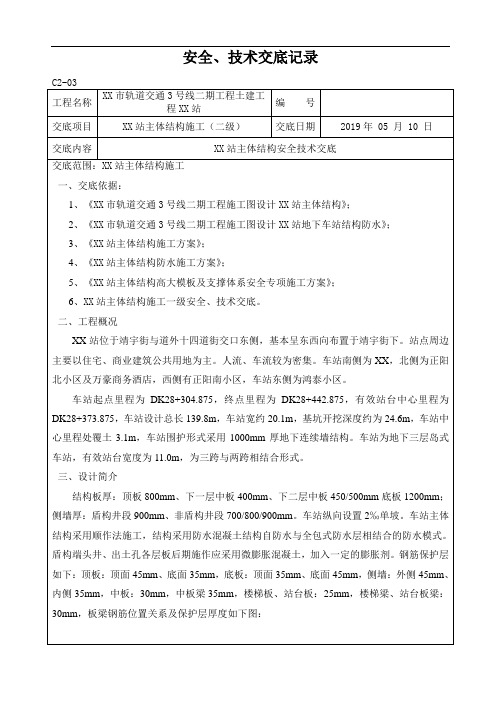
安全、技术交底记录
交底项目XX站主体结构施工(二级)交底日期2019年 05 月 10 日交底内容XX站主体结构安全技术交底
图3-1板梁钢筋位置关系及保护层厚度
表3-1XX站主体结构参数表
项目材料及规格结构尺寸
素砼垫层C20混凝土200mm
顶板C35钢筋混凝土P8 800mm
中板C35钢筋混凝土400mm、450mm
底板C35钢筋混凝土P10 1200mm
顶板梁C35钢筋混凝土P8 1000×1800、1200×2000、
中板梁C35钢筋混凝土900×1000、600×800、800×1000、800×900、1000×550、700×550、700×900、800×450、1200×450、700×1000、700×700、800×1400、900×1400
底板梁C35钢筋混凝土P10 1000×2800、1200×1710 框架柱C45钢筋混凝土800×1400、700×1200 负一层侧墙C35钢筋混凝土P8 700mm
负二层侧墙C35钢筋混凝土P8 800mm
负三层侧墙C35钢筋混凝土P10 900mm
交底项目XX站主体结构施工(二级)交底日期2019年 05 月 10 日
交底内容XX站主体结构安全技术交底
四、施工方法
图4.1-1主体结构施工工艺流程图
五、常规安全要求
1、进入施工现场人员必须正确戴好合格的安全帽,系好下颚带,锁好带扣;
2、作业时必须按规定正确使用个人防护用品,着装要整齐,严禁赤脚和穿拖鞋、高跟鞋进入施工现场;。
- 1、下载文档前请自行甄别文档内容的完整性,平台不提供额外的编辑、内容补充、找答案等附加服务。
- 2、"仅部分预览"的文档,不可在线预览部分如存在完整性等问题,可反馈申请退款(可完整预览的文档不适用该条件!)。
- 3、如文档侵犯您的权益,请联系客服反馈,我们会尽快为您处理(人工客服工作时间:9:00-18:30)。
市政基础设施工程
施工技术交底记录
轨道管-12
编号:
工程名称分部名称主体结构
分项名称修补工程交底日期年月日交底人交底人职务
专职安全员现场监理
技术交底内容:
某地铁车站主体及附属结构缺陷整治专项修补施工技术交底
1、工程概况
车站主体长度307.55m,标准段宽为38.5m,标准段基坑深度约为28m,顶板覆土厚3m,底板埋深约25.7m,有效站台中心底板埋深23.85m,车站为地下四层三柱四跨结构,站台为15.1m岛式站台,基坑保护等级为一级,明挖基坑支护体系采用地连墙+混凝土内支撑形式。
图1.1 某地铁车站设计纵剖面图
2、设计概况
2.1车站结构设计
车站使用年限为100年,重要性系数为1.1;防水等级为一级,采用全包防水方式即车站采用结构自防水外还有附加防水层;地下结构抗震等级为三级,结构抗震设防烈度为7度;主体结构及通道、风道结构的安全等级均按一级设计,主要受力结构构件采用一级防火标准,并满足防水、杂散电流防护、耐久性等要求;结构构件的裂缝控制等级为三级,即允许出现裂缝。
结构迎水面最大裂缝宽度不大于0.2mm、并不得贯通;结构背水面最大裂缝宽度不大于0.3mm;人防为一般设防车站,按6级抗力
等级设防,防化按丙级设计。
2.2车站结构形式和尺寸
某地铁车站为标准的箱形三柱四跨结构,车站共四层,标准段车站高度为22.61米。
车站顶板板厚900mm,底板厚1100mm,中板标准厚为400mm,中板位于隧道下方加强为1200mm,侧墙负一至负三层均为700mm厚,负四层为1000mm,车站标准断面图见图2-1。
图2-1 车站标准段结构剖面图
3、施工准备
3.1、材料准备
锤子、砂纸、鉄抹子、铁锹、水泥、修补胶、107胶、环氧树脂等,以及安全防护用品:安全带、安全帽、反光背心、口罩、手套、护目镜等。
3.2、机械准备
空压机、手砂轮、注浆机、搅浆桶等,所有设备必须具有合格证书并经报检通过后方可投入使用。
3.3、人员准备
修补人员有4人,其中管理人员1个,技术工3个,根据进度适当增加人员,所有的人员均须体检合格,并进行三级教育后方可进场施工。
4、混凝土质量缺陷分析及修补措施
4.1混凝土缺陷处理操作平台
主体结构缺陷处理需用到临时操作平台,以楼板为基础,搭设盘扣架作为缺陷修补施工平台,立杆采用Φ60×3.2mm无缝钢管,立杆间距1500mm,排距900mm,水平杆
步距1200mm,纵向剪刀撑满布,剪刀撑钢管与水平方向夹角为45°至60°,操作平台上部满铺脚手板并设置1.5m高的栏杆。
图4.1-1 支撑拆除脚手架立面示意图
4.2表面颜色不均匀修补(包括表面锈蚀处理)
影响混凝土表面颜色不均匀的主要原因是混凝土的振捣情况、脱模剂的使用情况、模板的表面锈蚀等引起。
修补措施:对于颜色不均匀的混凝土表面首先用水冲洗混凝土表面,如粘附有隔离剂、尘埃或其他不洁物,则应用尼龙织布擦洗干净。
紧接着用白水泥1袋,25kg,黑水泥15kg,胶水一桶20kg(按照结构原颜色进行配比),将混凝土全面披刮一遍,待面干发白时,用棉纱头擦除全部浮灰。
再遵循上述方法进行两遍补浆,待达到干凝状态后,再对补浆而作第一次打磨,打磨后洒水养生。
完成后的第二天,甚至第三天,再次重复上述程序方法对补浆面进行第二次、第三次补浆、磨平、擦灰,最后继续保养维护。
4.3混凝土表面局部麻面现象
摸板拼缝不严,局部漏浆、模板隔离剂涂刷不匀,或局部漏刷或失效、混凝土表面与模板粘结造成麻面、混凝土振捣不实,气泡未排出、停留在模板等原因表面形成麻点。
修补措施:在混凝土面上用粉笔圈划出不规则的蜂窝麻面实际面积,并沿其周边外延2-3cm列为修饰范围。
使用小型锤斧工具,把修饰范围内的表皮砼剔掉,剔深2-3cm(至少消掉水泥皮),并挖除麻面部分的表面浮浆。
浇水湿润后进行打磨,最后对局部或连同大面范围,采用白水泥1袋(25kg),黑水泥15kg,胶水一桶20kg(按
用聚乙烯醇缩甲醛胶(107胶)。
图4.9-1 拉杆孔封堵示意图
聚合物水泥砂浆配置:
采用P·O42.5普通硅酸盐水泥,黑白水泥按1:1进行拌合,视结构物砼外观颜色适当调配。
施工前先试配,待砂浆干硬后,观察颜色。
若颜色与结构物颜色一致,则进行施工,若颜色不一致,则找出原因,重新配制。
根据试验室配合比参数,确定每立方水泥用量中掺入20%“107胶”。
在配制浆液时,应进行试验检验,同时在施工前进行水泥浆的试配。
为确保砂浆质量,应做到随拌随用。
4.9.2施工方案
①拉杆孔清理
混凝土结构物混凝土达到拆模强度后,按照安装钢模板的相反顺序拆出钢模板。
拆除时应注意应先拆除拉杆螺栓,在撤出钢模,自上而下,先外后里。
图4.9-2 套管截除示意图
②施工工艺
(1)洒水湿润清洁基层后,聚合物水泥砂浆配制将拉杆孔填充密实,初凝后面层用铁抹子压光。
(2)将配制好的聚合物水泥砂浆充分拌和好,采用自制的砂浆水平导向槽插入拉杆孔口位置,通过砂浆填充棒将砂浆塞入拉杆孔内。
图4.9-3 砂浆填充示意图
(3)砂浆填充采用砂浆进行填塞密实,先填塞中间PVC管部分。
(4)待中间PVC套管部分砂浆强度达到一定强度后,在一端采用高压注水,查看另外一端是否有渗水、水印,以便检测拉杆填塞孔是否密实、渗水。
(5)检测合格后,方可进行表面300mm拉杆孔封堵。
封堵完毕后将砂浆抹平、收面,确保外观颜色一致。
(6)封堵完成后,养护不小于7d,不得出现开裂现象。
③施工注意事项
(1)在剔除PVC套管30mm时,要注意不得破坏混凝土结构物。
(2)在拌制聚合物砂浆时,砂浆的强度与结构物强度相同,严格控制砂浆稠度,满足施工要求即可。
(3)在封堵过程中,要用力均匀,封堵分遍塞紧、密实。
(4)封堵前,一定要清理PVC套管内的杂物,专人负责。
4.10局部存在裂缝、渗水现象
养护不及时,混凝土产生水化热而致使面层混凝土产生拉应力导致出现裂缝,拆模过早,内外温差过大,混凝土应力松弛效应不得以充分反发挥而致使产生裂缝,施工速度过快,上荷早;混凝土早期强度不足的情况下进行支架搭设及后续工序开展,上荷载过早而导致早期混凝土受损。
混凝土原材砂石料含泥量过大,导致水泥与碎石间内摩擦力减小,内应力增加,产生滑动最终开裂。
修补措施:(1)对于细微裂缝向裂缝加以清洗,干燥后涂刷两遍环氧胶泥或水泥基渗透结晶型防水涂料进行表面封闭。
(1)渗水裂缝(顶板、中板、侧墙结构内侧)
施工工艺流程:清理裂缝表面→钻孔→清洗注浆孔→嵌入注浆嘴→注浆→切割注浆嘴→封堵打磨→表面恢复。
1)用小铲刀把表面渗水处水锈污渍清理干净,仔细找出渗水裂缝;
2)在裂缝两侧交叉布置进行钻孔,钻孔应斜穿裂缝,垂直深度为结构厚度h的1/3;钻孔与裂缝水平距离为100mm~250mm,孔间距为200mm~250mm,孔径不大于20mm,斜孔倾角为45°~60°。
图4.9-1钻孔注浆示意图
3)用高压清洗机向孔内注清水清洗;
4)嵌入注浆嘴,用扳手拧紧,以防高压注浆时浆液流出;
5)高压注浆机注入高渗透改性环氧止渗材料,注浆时严密注视注浆压力及流量,如出现浆液渗漏过大,则立即停止,需对裂缝表面进行封堵后再进行二次注浆;
6)待注浆材料硬化后,利用角磨机进行注浆嘴切割,并采用高强度防水砂浆将注浆嘴进行封堵;
7)磨光机打磨裂缝缝隙处,使表面与原墙体基本一致,确保外观质量。
(2)结构顶板及中板顶面裂缝:
裂缝清理、洒水湿润(不得有明水),涂刷两遍水泥基渗透结晶型防水涂料,首层与次层遍垂直,浆料随拌随用,30分钟内用完,搅拌时间不得小于5分钟。
涂料干后及时进行洒水养护,养护时间为2-3次/天;养护至防水涂料渗透填充裂缝后再按设计要求施作顶板聚氨酯防水涂料。