轧钢常见缺陷.docx
轧制钢板表面缺陷类型、特征、原因、影响
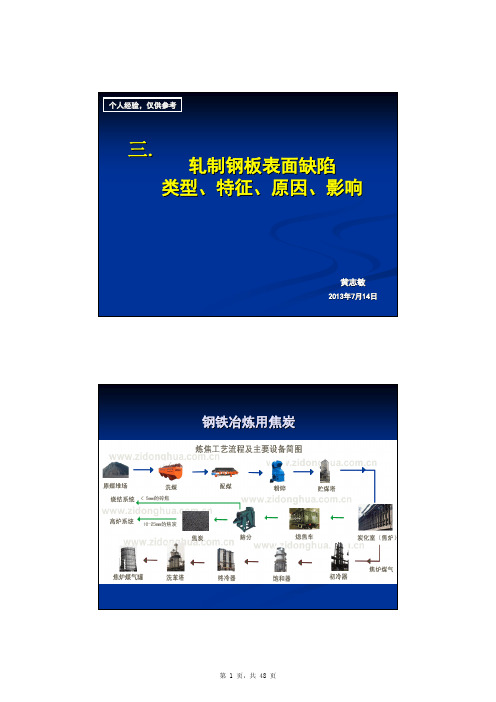
加-成分、时机、温度、时间、杂质、烧损,搅拌-浮渣、沉渣、匀度, 工艺-成分、时机、温度、时间、杂质、烧损,焦炭-有害气氛、粉尘, 电弧/电炉-温度、时间、烧损、有害气氛,转炉-温度、时间、烧损、 有害气氛,吹氧-温度、时间、氧量、烧损、有害气氛,沸腾/镇静-温 度、时间、浮渣、沉渣,脱气-温度、时间、强度,外来杂物;
锻制:加热-方式、有害气氛、温度、时间、脱气、氧化物,冷却,
匀度,温度,时间,锻制比,方向,锤锻/模锻,氧化物,有害气氛, 外来杂物,表面和取样检验;
冷轧:轧坯-表面、尺寸、状态,轧制量,轧制次数,温度,轧辊,
表面硬度,粗糙度;
轧制和锻制关键:轧/锻制比、去氧化皮、温度、时机、外来杂物
第 10 页,共 48 页
5.1 纵向裂缝(常见缺陷)
特征: 沿轧制方向有两种:片状裂开小裂口,一定宽度粗黑 线状裂缝; 原因: 钢坯凝固时内应力不匀;轧制时薄弱处应力过大;且 在拉伸时应力过大;内部大量气泡,轧制时沿受力方 向产生裂缝并延展; 影响: 根据裂缝长度、分布、数量和深度情况判断,很可能 被判报废;
第 21 页,共 48 页
横向裂缝 (常见缺陷)
第 23 页,共 48 页
横向裂缝 (常见缺陷)
5.3 皴裂
特征: 数量较多、面积较大、较为短粗、不连续的横向裂 缝; 原因: 钢坯加热超过临界温度时,晶粒过于粗大,晶界结合 力减弱,热塑性下降,钢坯表面原微裂缝被高温氧 化,在表面和角部产生裂缝; 影响: 数量多,面积大,修磨或补焊工作量极大,外观形象 极差,很难续用直至报废;
第 27 页,共 48 页
微裂纹
5.7 带状裂纹
特征: 分布狭长、形状不同、大小不一、相互渗透、面积不 等,整体表现为沿轧制方向的条状或带状且有一定的 富集,呈现在单区域或多区域; 原因: 原钢坯表面上较为密集的细小裂纹所致,热轧时暴露 和扩展,同时使不同形态裂纹渗透、混合,导致密集 区域的产生; 影响: 多数情况下,出现多条条状或带状,均有一定深度, 往往超过厚度负偏差,严重时出现槽沟形态,报废率 很高;
轧制缺陷分析
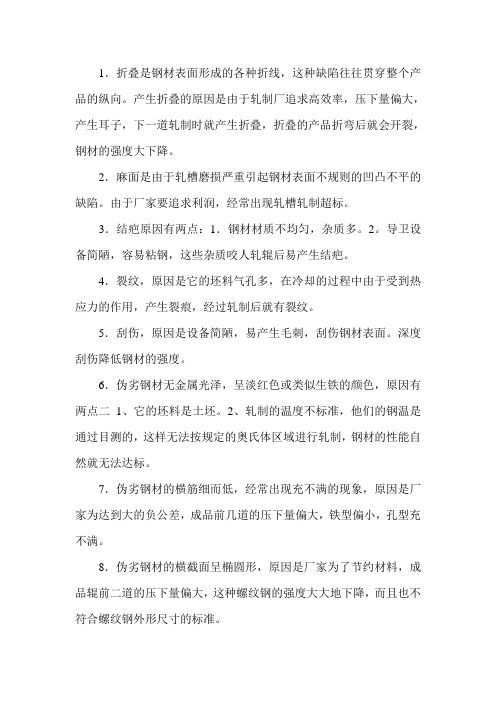
1.折叠是钢材表面形成的各种折线,这种缺陷往往贯穿整个产品的纵向。
产生折叠的原因是由于轧制厂追求高效率,压下量偏大,产生耳子,下一道轧制时就产生折叠,折叠的产品折弯后就会开裂,钢材的强度大下降。
2.麻面是由于轧槽磨损严重引起钢材表面不规则的凹凸不平的缺陷。
由于厂家要追求利润,经常出现轧槽轧制超标。
3.结疤原因有两点:1.钢材材质不均匀,杂质多。
2。
导卫设备简陋,容易粘钢,这些杂质咬人轧辊后易产生结疤。
4.裂纹,原因是它的坯料气孔多,在冷却的过程中由于受到热应力的作用,产生裂痕,经过轧制后就有裂纹。
5.刮伤,原因是设备简陋,易产生毛刺,刮伤钢材表面。
深度刮伤降低钢材的强度。
6.伪劣钢材无金属光泽,呈淡红色或类似生铁的颜色,原因有两点二1、它的坯料是土坯。
2、轧制的温度不标准,他们的钢温是通过目测的,这样无法按规定的奥氏体区域进行轧制,钢材的性能自然就无法达标。
7.伪劣钢材的横筋细而低,经常出现充不满的现象,原因是厂家为达到大的负公差,成品前几道的压下量偏大,铁型偏小,孔型充不满。
8.伪劣钢材的横截面呈椭圆形,原因是厂家为了节约材料,成品辊前二道的压下量偏大,这种螺纹钢的强度大大地下降,而且也不符合螺纹钢外形尺寸的标准。
9.优质钢材的成分均匀,冷剪机的吨位高,切头端面平滑而整齐,而伪劣材由于材质差,切头端面常常会有掉肉的现象,即凹凸不平,并且无金属光泽。
而且由于伪劣材厂家产品切头少,头尾会出现大耳子。
10.伪劣钢材材质含杂质多,钢的密度偏小,而且尺寸超差严重,所以在没有游标卡尺的情况下,可以对它进行称量核对。
比如对于螺纹钢20,国家标准中规定最大负公差为5%,定尺9M时它的单根理论重量为120公斤,它的最小的重量应该是:22 X(l-5%)=20.9公斤,称量出来单根的实际重量比20.9公斤小,则是伪劣钢材,原因是它负公差超过了5%。
一般来说整相称量效果会更好,主要考虑到累积误差和概率论这个问题。
11.伪劣钢材的内径尺寸波动较大,原因是;l、钢温不稳定有阴阳面。
钢在轧制中常见的缺陷总结

2)腰厚、腰薄产生的主要原因 是:如按孔型设计头部压下量为 77-=6.7mm:腹部斥下量为16 —= 1.5mm,如果六孔压下虽:加 大l.5mm,则头部尺寸为75.5m m 压下虽由6.7mm 减少到5.2m m.腰部压下虽由l ∙5mm 减少 到6自然头部对腰部有拉伸加 之腰部无斥下而宽展•所以腰变 薄.反之腰部变厚。
(3) 底大主要是由成品孔腰卑, 上腿长引起及六孔开口腿磨损 严重等。
(4) 底小主要是帽形孔未能将腿 部宽展到足够的长度•或由腰簿 引起。
(5) 轨高、轨低主要是由于轧件 的温度商.低,成品前孔轨头部 分或成品孔轨头部分磨损情况 引起。
(6) 腹高、腹低主要是导卫板安 装不良•孔型严重磨损造成C钢轨在冷状态娇直、圧直过程中,产生的直线形或折线形的裂纹。
其裂口棱角尖锐,呈银亮色,严重时劈裂成碎断。
线材常见缺陷缺陷名称缺陷特征 产生原因耳子盘条表而沿轧制方向的条状凸起称为耳子,有取边耳子,也有双边耳 子。
在商速线材轧机(连轧)生产中•最终产品头尾两端很难避免耳子 的产生。
1)轧槽导卫安装不正及放偏过钢,使轧件产生耳子。
(2) 轧制温度的波动或局部不均匀.彩响轧件的宽展虽,产生耳 子。
(3) 坯料的缺陷.如缩孔、偏析.分层厦外來夹朵物•影响轧件的 正常变形,形成耳子。
折叠盘条表面沿轧制方向平直或弯曲的细线.在横断面上与表倆呈小角度(1)前道次的耳子及其他纵向凸过正偏差的叫底宽,超过负偏差的叫底小C 轨腰商度超过正偏差 的叫腹1⅛∙超过负偏差的叫腹低。
轨的岛度超过正偏差的叫轨商, 超过负偏差的叫轨低。
断面不与其垂直轴线对称的叫不对称(又叫 偏称)。
娇裂(矫断、压断)(1) W^式或立式娇直机调整操 作不当•将钢轨矫断。
(2) 钢质不好•如局部夹杂、偏析,在矫直过程中被矫(压)裂 (断)。
彩涂板(卷)常见缺陷。
热轧钢管产品缺陷一览表

热轧钢管产品缺陷一
缺陷名称产生原因
产生工序
管坯表面砸伤,管坯表面有裂
纹
来料单位轧辊表面有异物穿孔导板材质不好
供货单位导板磨损严重或粘钢穿孔导板的形状和轧辊的形状不吻合
工艺设计导向口或受料槽不光穿孔托辊、抱辊、料钩等表面不光
滑穿孔
内孔刮伤顶头或顶杆上有凸起的部分,
束节不光滑或匹配不当
穿孔钢温偏低司炉顶头冷却水太大穿孔顶头位置过后穿孔管坯剪切斜度过大剪切钢温过低、阴阳面司炉、拔料
顶头偏离中心太多
穿孔模子磨损严重打头职工操作不规范
打头尺寸超差
责任心不够,量具不齐全,取
样不及时
穿孔
壁厚不均
打头不好外折叠
导板印
外表碰划
伤内孔折叠
缺陷一览表
预防措施及解决方法备注
严格检查进厂的管坯质量
修磨轧辊
更换供货厂家,确保导板质量
修磨或更换导板
根据辊形设计导板的尺寸
修磨或更换导向口,受料槽,多
在尾部
修磨或更换
修磨或更换
经常观察仪表,保证炉温
把水开小点
进一点顶头位置
更换剪切刀片(头部)
保证钢温、及时拨料
正确调整抱辊,轧辊左右位
置,保证轧辊中心
堆焊或更换模子
加强锻炼,提高责任心
配备各种量具,加强职工责任
心。
冷轧产品常见缺陷图谱与判断(doc40页).doc

冷轧产品常见缺陷图谱与判断目录结疤(4)表面夹杂(5)分层(6)氧化铁皮压入(7)辊印(8)压痕(压印、压坑)(9)扁卷 (10)瓢曲 (11)镰刀弯 (12)折迭(13)边裂(14)气泡(15)折皱(16)刮伤(17)擦伤(划伤、划痕)(18)撞伤(19)切斜(20)欠酸洗(21)过酸洗(22)停车斑(23)浪形(24)氧化色(25)振动纹(26)平整斑(27)粘结(28)塔形(29)溢出边(30)卷取擦伤(31)锈蚀(32)松卷(33)凸包(起筋、隆起、鼓包)(34)厚度不合(35)长度不合(36)平整纹(37)孔洞(38)黄斑(39)黑斑(40)1.缺陷名称:结疤定义与外观:附着在钢带表面,形状不规则翘起的金属薄片称结疤。
呈现叶状、羽状、条状、鱼鳞状、舌端状等。
结疤分为两种,一种是与钢的本体相连结,并折合到板面上不易脱落叫闭口结疤;另一种是与钢的本体没有连结,但粘合在板面上,易于脱落,脱落后形成较光滑的凹坑称为开口结疤。
成因:●冷轧基板表面原有的结疤、翘皮等缺陷未挑出,经冷轧后残留在钢带表面上;●冷轧时钢板表面粘附异物,经轧制压入钢带表面。
危害:导致后续加工使用过程中出现金属剥离或产生孔洞。
预防及消除方法:加强冷轧基板的检查,检查判断:●用肉眼检查;●不允许存在结疤缺陷,一般判利用品或以下等级,对局部结疤缺陷,允许切除带有结疤部分带钢的方法清除。
如结疤已脱落,则比照压痕缺陷处理,若深度没有超出相关标准规定,可以参照相应标准进行判定。
2.缺陷名称:表面夹杂定义与外观:冷轧基板皮下或表面非金属夹杂、夹渣在冷轧加工过程中破裂而暴露在钢带表面,一般呈点状、块状、线状或长条状无规律的分布在薄板的表面。
其颜色一般呈棕红色、黄褐色、灰白色或灰黑色。
成因:冷轧基板皮下夹杂轧后暴露或基板的表面原有夹杂轧后残留在带钢表面(炼钢浇铸原因)。
危害:可能导致后续加工过程中产生孔洞、开裂、分层。
预防及消除方法:●严格遵守浇铸制度●加强冷轧基板表面质量检查。
轧钢车间产品质量缺陷标准(供参考)
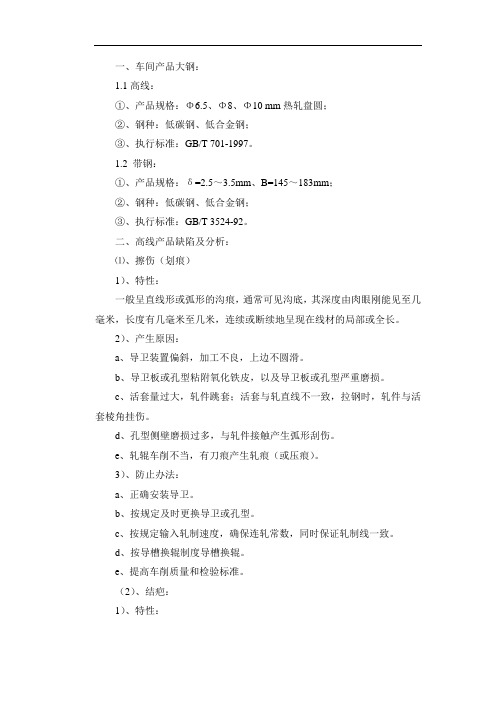
一、车间产品大钢:1.1高线:①、产品规格:Φ6.5、Φ8、Φ10 mm热轧盘圆;②、钢种:低碳钢、低合金钢;③、执行标准:GB/T 701-1997。
1.2 带钢:①、产品规格:δ=2.5~3.5mm、B=145~183mm;②、钢种:低碳钢、低合金钢;③、执行标准:GB/T 3524-92。
二、高线产品缺陷及分析:⑴、擦伤(划痕)1)、特性:一般呈直线形或弧形的沟痕,通常可见沟底,其深度由肉眼刚能见至几毫米,长度有几毫米至几米,连续或断续地呈现在线材的局部或全长。
2)、产生原因:a、导卫装置偏斜,加工不良,上边不圆滑。
b、导卫板或孔型粘附氧化铁皮,以及导卫板或孔型严重磨损。
c、活套量过大,轧件跳套;活套与轧直线不一致,拉钢时,轧件与活套棱角挂伤。
d、孔型侧壁磨损过多,与轧件接触产生弧形刮伤。
e、轧辊车削不当,有刀痕产生轧痕(或压痕)。
3)、防止办法:a、正确安装导卫。
b、按规定及时更换导卫或孔型。
c、按规定输入轧制速度,确保连轧常数,同时保证轧制线一致。
d、按导槽换辊制度导槽换辊。
e、提高车削质量和检验标准。
(2)、结疤:1)、特性:一般呈舌头形或指甲形,其宽而厚的一端与钢材基本相连,有时结疤外形呈一封闭的曲线,它嵌在线材表面,面积较大。
轧制产生的结疤容易翘起和张口,一般下面都有夹杂物。
2)、产生原因:a、在轧制过程中前一道次孔型有砂眼或因故损坏,当轧件通过该孔型后表面形成凸块,再轧制后,在成品线材表面产生周期性生根结疤。
b、在轧制过程中,由外界金属物落在轧件表面上,同时被带入孔型变形区,压入轧件表面,产生结疤,这样的结疤是不生根且无规律性。
c、轧件在孔型中打滑,使金属堆积于变形区周围表面上,再轧制时造成的。
d、由于轧辊表面刻痕不良,在轧件的表面上形成较高的凸起金属,再轧制时产生有规律的结疤。
e、钢坯表面有较大的翻皮和较大的皮下气泡破裂。
f、原料表面处理不良,有尖锐的棱角边产生。
3)防止办法:a、按导槽换辊制度导槽换辊,同时严格控制轧辊进厂检验。
轧钢常见缺陷之欧阳德创编
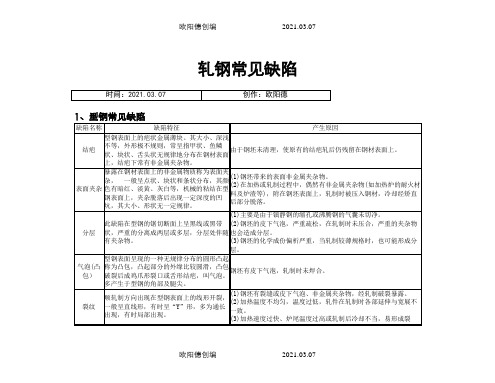
(3)成品孔出口卫板过低,锯齿磨损太老,垫板太低,在辊道运送速度过快时,碰撞档板等都容易产生弯头。
尺寸超差(规格不合)
钢轨断面几何尺寸不符合标准规定,统称尺寸超差。
其中:钢轨头部超过正偏差的叫头大,超过负偏差的叫头小。轨腰厚度超过正偏差的叫腰厚.超过负偏差的叫腰薄。轨底宽度超过正偏差的叫底宽,超过负偏差的叫底小。轨腰高度超过正偏差的叫腹高,超过负偏差的叫腹低。轨的高度超过正偏差的叫轨高,超过负偏差的叫轨低。断面不与其垂直轴线对称的叫不对称(又叫偏称)。
(1)卫板安装不良,使钢轨产生力偶,形成扭转。
(2)轧件温度不均或压下量不均,造成各部延伸不一致。
(3)矫直机调整不当,钢轨受力偶作用。
(4)在冷却台架上翻钢时因温度较高也会出现扭转。
弯曲
钢轨沿垂直或水平方向呈现不平直的现象叫弯曲,一般呈镰刀形或波浪形,仅在端部的弯曲又叫弯头。
(1)由于重轨的头、腰、底面积相差较大,使轧制、冷却等工序操作易产生弯曲。
(2)钢坯的皮下气泡,严重疏松,在轧制时未压合,严重的夹杂物也会造成分层。
(3)钢坯的化学成份偏析严重,当轧制较薄规格时,也可能形成分层。
气泡(凸包)
型钢表面呈现的一种无规律分布的圆形凸起称为凸包,凸起部分的外缘比较圆滑,凸包破裂后成鸡爪形裂口或舌形结疤,叫气泡。多产生于型钢的角部及腿尖。
钢坯有皮下气泡,轧制时未焊合。
(1)钢坯带来的表面非金属夹杂物。
(2)在加热或轧制过程中,偶然有非金属夹杂物(如加热炉的耐火材料及炉渣等),附在钢坯表面上,轧制时被压入钢材,冷却经矫直后部分脱落。
分层
此缺陷在型钢的锯切断面上呈黑线或黑带状,严重的分离成两层或多层,分层处伴随有夹杂物。
轧钢常见缺陷
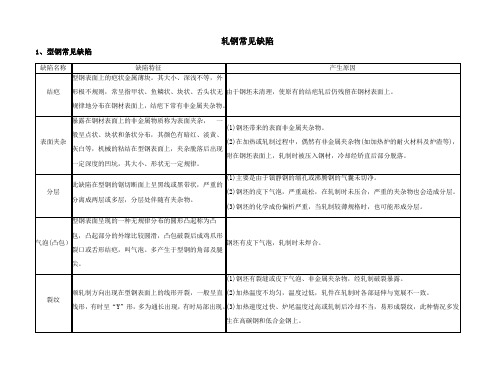
2)腰厚、腰薄产生的主要原因是:如按孔型设计头部压下量为77—=6.7mm;腰部压下量为16一=1.5mm,如果六孔压下量加大l.5mm,则头部尺寸为75.5mm压下量由6.7mm减少到5.2mm,腰部压下量由1.5mm减少到0,自然头部对腰部有拉伸加之腰部无压下而宽展,所以腰变薄,反之腰部变厚。
(1)因辊式或立式矫直机调整操作不当,将钢轨矫断。
(2)钢质不好,如局部夹杂、偏析,在矫直过程中被矫(压)裂(断)。
3、线材常见缺陷
缺陷名称
缺陷特征
产生原因
耳子
盘条表面沿轧制方向的条状凸起称为耳子,有单边耳子,也有双边耳子。在高速线材轧机(连轧)生产中,最终产品头尾两端很难避免耳子的产生。
1)轧槽导卫安装不正及放偏过钢,使轧件产生耳子。
(1)卫板安装不良,使钢轨产生力偶,形成扭转。
(2)轧件温度不均或压下量不均,造成各部延伸不一致。
(3)矫直机调整不当,钢轨受力偶作用。
(4)在冷却台架上翻钢时因温度较高也会出现扭转。
弯曲
钢轨沿垂直或水平方向呈现不平直的现象叫弯曲,一般呈镰刀形或波浪形,仅在端部的弯曲又叫弯头。
(1)由于重轨的头、腰、底面积相差较大,使轧制、冷却等工序操作易产生弯曲。
(1)钢坯带来的表面非金属夹杂物。
(2)在加热或轧制过程中,偶然有非金属夹杂物(如加热炉的耐火材料及炉渣等),附在钢坯表面上,轧制时被压入钢材,冷却经矫直后部分脱落。
分层
此缺陷在型钢的锯切断面上呈黑线或黑带状,严重的分离成两层或多层,分层处伴随有夹杂物。
(1)主要是由于镇静钢的缩孔或沸腾钢的气囊未切净。
(1)主要因钢坯缩孔部分未切净。
轧钢 基础(常见缺陷)培训材料
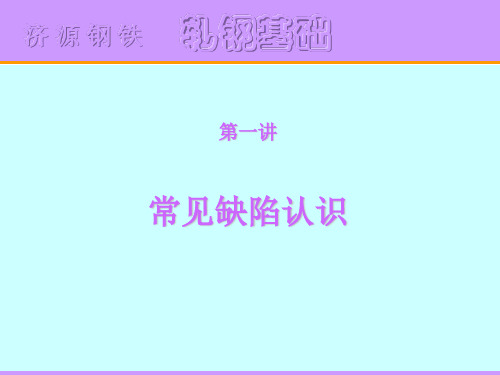
济 源 钢 铁 轧钢基础
温度不均:如果钢坯的各部分都同样地加热到规程规定 的温度,那么钢的温度就均匀了。这时轧制所耗电力小, 并且轧制过程容易进行。但要达到钢温完全一致是不可能 的,只要钢坯表面温度和最低部分温度差不超过50℃,就 可以认为是加热均匀了。
由于钢的加热温度不均,就会产生不均匀变形,使变 形体内各部分变形不同。这样的材料经再结晶退火后,各 处的晶粒度也不同,使组织和性能不均匀,因此生产中必 须尽可能地减少加热的温度不均匀性。
济 源 钢 铁 轧钢基础
过烧:如果钢加热温度过高,时间又长,使钢的晶粒之 间的边界上开始熔化,有氧渗入,并在晶粒间氧化,这样 就失去了晶粒间的结合力,失去其本身的强度和可塑性, 在钢轧制时或出炉受震动时,就会断为数段或裂成小块脱 落,或者表面形成粗大的裂纹,这种现象称为钢的过烧。
过烧的钢无法挽救,只好报废,回炉重炼。生产中有 局部过烧,这时可切掉过烧部分,其余部分可重新加热轧 制。
当导板、卫板或夹板质量不好,就会在轧件的表面上 划出很深的伤痕。这种划痕有时是局部的,有时遍及轧件 全长,经轧制后划伤部分被压入轧件内部造成折叠。这在 轧制钢质软的、塑性好的碳钢时最易产生。因此,若发现 导板有粘挂铁皮,卫板夹起刺等情况应立即更换。
济 源 钢 铁 轧钢基础
成品尺寸不合格 成品垂直直径尺寸不合格
图2 连铸坯疏松照片
济 源 钢 铁 轧钢基础
白点:钢液中末逸散的氢原子在压力加工时的组织应力, 加上加工后冷却速度过快等外因,容易从原子态转变成分 子态,导致其体积急剧增大,其应力超过了钢的极限强度 就形成开裂,即是白点,也称发裂。钢材不允许有白点。 (图3)
图3 白点照片
济 源 钢 铁 轧钢基础
济 源 钢 铁 轧钢基础
轧钢常见缺陷之欧阳歌谷创编

(3)坯料的缺陷,如缩孔、偏析、分层、外来夹杂物,影响轧件的正常变形,形成耳子。
折叠
盘条表面沿轧制方向平直或弯曲的细线,在横断面上与表面呈小角度交角状的缺陷多为折叠。折叠两侧伴有脱碳层或部分脱碳层,折缝中间常存在氧化铁夹杂。
(1)前道次的耳子及其他纵向凸起物折倒轧入本体所造成。再轧形成折叠。
轧痕(凸、凹、压印)
在钢轨表面出现的各种不连续的伤痕叫轧痕。各种轧痕都存在热加工的痕迹、般呈周期性出现,有时无规律分布。
(1)由于轧槽掉肉,使轧件表面呈现周期性的凸包。
(2)孔型内粘结铁皮,结疤等,使轧件产生周期性的口坑,又称缺肉。
(3)在轧制过程中,氧化铁皮压入轧件表面,冷却或矫直后脱落。形成无规律的压痕。
(2)切深孔切人太深,造成腿长无法消除。
(3)轧辊不水平或有轴向串动,以及800咬入不正,成品孔夹板上偏等都会造成一腿长,一腿短等。
(4)腰的厚、薄主要是成品孔及成品前孔压下量不合理所造成。
划伤(刮伤、擦伤、划痕)
一般呈直线或弧形的沟槽,其深度不等,通长可见沟底,长度自几毫米到几米,连续或断续地分布于钢材的局部或全长,多为单条,有时出现多条。
耳子
在型钢表面上与L型开口处相对应的地方,出现顺轧制方向延伸的凸起部分称为耳子。有单边的,也有双边的,有时耳子产生在型钢的全长,也有局部或断续的,方、圆钢产生较多。
(1)轧机调整不当或孔型磨损严重,使成品前孔来料过大或成品孔压下量过大,产生过充满,多产生双边耳子。
(2)进入成品孔前因事故造成温度过低,进入成品孔时延伸降低,宽展过大,多产生双边耳子。
(2)导卫板安装不当,有棱角或粘有铁皮使轧件产生划痕,再轧形成折叠。
钢材轧制缺陷及原因
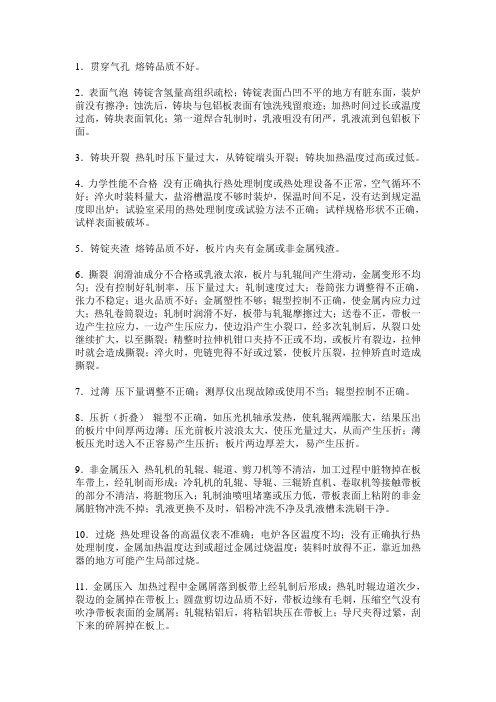
1.贯穿气孔熔铸品质不好。
2.表面气泡铸锭含氢量高组织疏松;铸锭表面凸凹不平的地方有脏东面,装炉前没有擦净;蚀洗后,铸块与包铝板表面有蚀洗残留痕迹;加热时间过长或温度过高,铸块表面氧化;第一道焊合轧制时,乳液咀没有闭严,乳液流到包铝板下面。
3.铸块开裂热轧时压下量过大,从铸锭端头开裂;铸块加热温度过高或过低。
4.力学性能不合格没有正确执行热处理制度或热处理设备不正常,空气循环不好;淬火时装料量大,盐浴槽温度不够时装炉,保温时间不足,没有达到规定温度即出炉;试验室采用的热处理制度或试验方法不正确;试样规格形状不正确,试样表面被破坏。
5.铸锭夹渣熔铸品质不好,板片内夹有金属或非金属残渣。
6.撕裂润滑油成分不合格或乳液太浓,板片与轧辊间产生滑动,金属变形不均匀;没有控制好轧制率,压下量过大;轧制速度过大;卷筒张力调整得不正确,张力不稳定;退火品质不好;金属塑性不够;辊型控制不正确,使金属内应力过大;热轧卷筒裂边;轧制时润滑不好,板带与轧辊摩擦过大;送卷不正,带板一边产生拉应力,一边产生压应力,使边沿产生小裂口,经多次轧制后,从裂口处继续扩大,以至撕裂;精整时拉伸机钳口夹持不正或不均,或板片有裂边,拉伸时就会造成撕裂;淬火时,兜链兜得不好或过紧,使板片压裂,拉伸矫直时造成撕裂。
7.过薄压下量调整不正确;测厚仪出现故障或使用不当;辊型控制不正确。
8.压折(折叠)辊型不正确,如压光机轴承发热,使轧辊两端胀大,结果压出的板片中间厚两边薄;压光前板片波浪太大,使压光量过大,从而产生压折;薄板压光时送入不正容易产生压折;板片两边厚差大,易产生压折。
9.非金属压入热轧机的轧辊、辊道、剪刀机等不清洁,加工过程中脏物掉在板车带上,经轧制而形成;冷轧机的轧辊、导辊、三辊矫直机、卷取机等接触带板的部分不清洁,将脏物压入;轧制油喷咀堵塞或压力低,带板表面上粘附的非金属脏物冲洗不掉;乳液更换不及时,铝粉冲洗不净及乳液槽未洗刷干净。
轧制缺陷图谱、形成原因分析以与预防措施方案
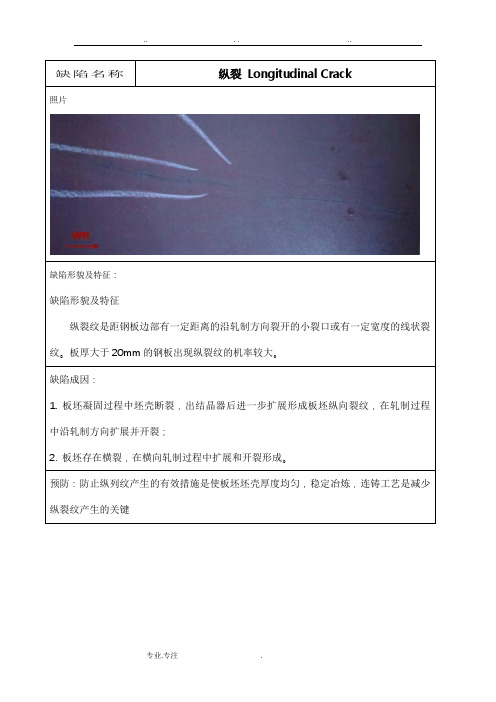
可能混淆的缺陷:
星形裂纹
缺陷名称
夹渣Slag
照片
缺陷形貌及特征:
夹渣是钢板表面嵌入钢板本体的非金属物质,呈点状,片状或条状分布。通常非金属夹渣露出部分呈白色或灰白色。
照片
缺陷形貌及特征:
在钢板的切割断面上呈现一条或多条平行的缝隙,即钢板局部存在基本平行于钢板表面的未焊合界面。
缺陷成因:
1.板坯中的夹杂物,在轧制后延展为片状并逐渐长大,直至形成分层;
2.板坯中心区域低溶质物质富集,中心偏析带内存在硫化物聚集,形成夹杂性裂纹;
3.板坯内部本身存在内裂,分层,疏松或缩孔等缺陷,轧制后形成分层;
预防:
提高轧机除鳞系统的除鳞效能。
推荐处理措施:
1.对缺陷程度进行确认,不满足合同要求的缺陷可通过修磨去除,当修磨处剩余厚度不满足合同要求时可采取厚度改规或切除缺陷后改尺的方法。
2.面积较大或深度较深的缺陷也可直接采用切除缺陷改尺的方法或直接判废次。
3.出现批量氧化铁皮时应及时通知轧钢。
可能混淆的缺陷:
氧化铁渣压入
照片
缺陷形貌及特征:
氧化铁渣压入是钢板表面点状或块状不规则分布的铁氧化物压入,缺陷颜色一般呈黑色,缺陷表面通常高于钢板本体。
缺陷名称
纵裂Longitudinal Crack
照片
缺陷形貌及特征:
缺陷形貌及特征
纵裂纹是距钢板边部有一定距离的沿轧制方向裂开的小裂口或有一定宽度的线状裂纹。板厚大于20mm的钢板出现纵裂纹的机率较大。
缺陷成因:
1.板坯凝固过程中坯壳断裂,出结晶器后进一步扩展形成板坯纵向裂纹,在轧制过程中沿轧制方向扩展并开裂;
钢在轧制中常见的缺陷总结
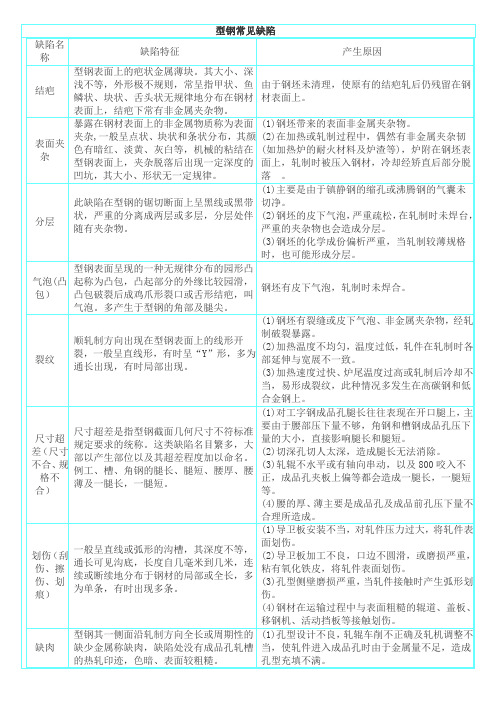
开裂_{V_8uk_ $
钢坯在轧制中,自动裂开称开裂。工业轨尤为多见。_\#_F>_R,
sN_M_F(TY
(1)由于钢锭中心部位集中大量气体和非囊属夹杂物所致。`-?`H>+OG_
(2)由于钢“内裂”或“穿孔”所致。ZQ_-6n1O_
8~B___LT_Z
过烧G_ 6x__N R
因钢坯加热不当,钢轨表面出现的横向粗糙裂口叫“过烧”。裂口多出现在轨头和轨底侧边,金相观察裂口处金属晶粒粗大。7Rc>LI*'
(1)轧机操作调整不当或成品前孔磨损严重,造成成品孔压下量过大。=c%gV]>_G
(2)钢坯温度低,造成轧制过程中的宽展大。Ow__v}l_J_
(3)入口导板安装偏斜、松动,轧件进孔不正。l7_Wdbx5x0
zh_Y]__!
轧痕(凸、凹、压印)__t"5ZYa__
在钢轨表面出现的各种不连续的伤痕叫轧痕。各种轧痕都存在热加工的痕迹、般呈周期性出现,有时无规律分布。R{6_M__(!x
一般呈直线或弧形的沟槽,其深度不等,通长可见沟底,长度自几毫米到几米,连续或断续地分布于钢材的局部或全长,多为单条,有时出现多条。xr7}@rq"U<
)#_cZ_& O_
(1)导卫板安装不当,对轧件压力过大,将轧件表面划伤。F8"J_<_VJ7
(2)导卫板加工不良,口边不圆滑,或磨损严重,粘有氧化铁皮,将轧件表面划伤。!'p
(1)钢坯带来的表面非金属夹杂物。1_vdG \$_
(2)在加热或轧制过程中,偶然有非金属夹杂韧(如加热炉的耐火材料及炉渣等),炉附在钢坯表面上,轧制时被压入钢材,冷却经矫直后部分脱落_U#|6n ,_。cp_6I]#_X
轧钢常见缺陷
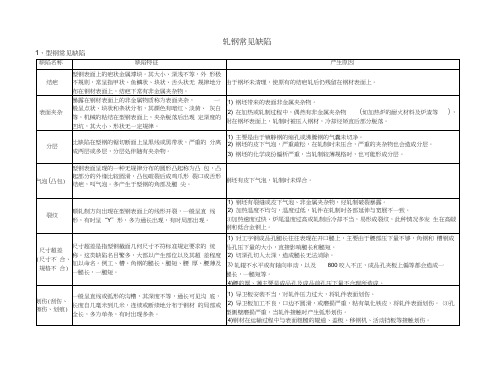
在型钢表面上与L型开口处相对应的地方,出现顺轧 制方向延伸的凸起部分称为耳子。有单边的,也有双 边的,有时耳子产生在型钢的全长,也有局部或断续 的,方、圆钢产生较多。
(1)轧机调整不当或孔型磨损严重,使成品前孔来料过大或成品孔压下量过大,产 生过充满,多产生双边耳子。
(2)进入成品孔前因事故造成温度过低,进入成品孔时延伸降低,宽展过大,多产 生双边耳子。
(3)轧件温度不均匀,使金属延伸不一致。
(4)冷床拉钢小车不冋步或滑轨不光滑。
(5)运输辊道速度过快,容易把钢材头部撞弯。
(6)矫直温度过高,冷却后容易产生弯曲。
(7)成品捆扎长短不齐较大。在运输中装卸不当。
(8)堆垛时不按规定进行。
(9)锯片用的太老,也容易产生弯头。
形状不止
型钢断面几何形状歪斜不正,这类缺陷对不冋品种各 异,名称繁多。如工槽钢的内并外斜,弯腰挠度,角 钢顶角大、小腿不平等。
轧钢常见缺陷
1
缺陷名称
缺陷特征
产生原因
结疤
型钢表面上的疤状金属溥块。其大小、深浅不等,外 形极不规则,常呈指甲状、鱼鳞状、块状、舌头状无 规律地分布在钢材表面上,结疤下常有非金属夹杂物。
由于钢坏未清理,使原有的结疤轧后仍残留在钢材表面上。
表面夹杂
暴露在钢材表面上的非金属物质称为表面夹杂,一
般呈点状、块状和条状分布,其颜色有暗红、淡黄、 灰白等,机械的粘结在型钢表面上,夹杂脱落后出现 定深度的凹坑,其大小、形状无一定规律。
(1)钢坯带来的表面非金属夹杂物。
(2)在加热或轧制过程中,偶然有非金属夹杂物(如加热炉的耐火材料及炉渣等),
附在钢坏表面上,轧制时被压入钢材,冷却经矫直后部分脱落。
分层
钢铁材料常见缺陷及其产生原因(doc 21页)
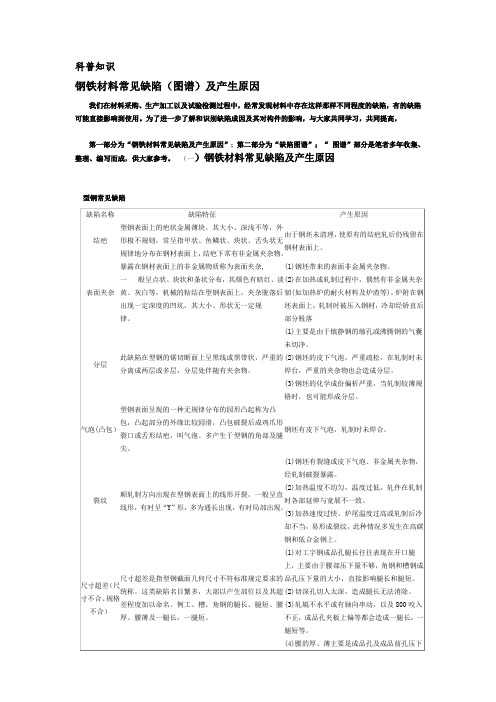
科普知识钢铁材料常见缺陷(图谱)及产生原因我们在材料采购、生产加工以及试验检测过程中,经常发现材料中存在这样那样不同程度的缺陷,有的缺陷可能直接影响到使用。
为了进一步了解和识别缺陷成因及其对构件的影响,与大家共同学习,共同提高,第一部分为“钢铁材料常见缺陷及产生原因”; 第二部分为“缺陷图谱”;“图谱”部分是笔者多年收集、整理、编写而成,供大家参考。
(一)钢铁材料常见缺陷及产生原因型钢常见缺陷重轨常见缺陷线材常见缺陷中厚板常见缺陷热轧板(卷)常见缺陷冷轧板(卷)常见缺陷镀锌板(卷)常见缺陷镀锡板(卷)常见缺陷彩涂板(卷)常见缺陷硅钢产品常见缺陷结瘤带钢表面粘附有细小坚硬的颗粒物,呈星星点点地分布。
少量轻微点状压印。
严重的压印,使带锕面凹入,另一面相应凸起。
(1)在高温氧化气氛中石墨碳套辊的孔隙被逐渐氧化扩大,带铜带人炉内的细铁粉在孔隙处堆积起来,高温下结成瘤。
(2)由于碱洗工艺(碱液温度、浓度、洗刷辊磨损)达不到规定要求,使带钢表面上的轧制油没有洗干净,从而带进炉内的铁粉多并堆积在碳套的孔隙处。
碳套在高温和过氧化气氛下加速碳套的孔隙氧化,并使其逐渐扩大易于堆积铁粉。
涂层不良成品钢带(片)表面呈花斑,淙布不均,发粉,发粘起皮,漏涂等。
(1)潦层液质量差或涂液污染。
(2)涂层辊压下控制不当或涂层辊辊面损伤。
(3)涂层工艺执行不当。
(4)涂层前板面底层不良。
氧化色(无取向硅钢)产品涂层前、后带钢表面有兰色、黑色,或涂层后有浑苇色出现。
(1)炉内的露点高或吸人空气。
(2)保护气体的含氧量高或保护气体使用中断。
涂层过烧(无取向硅钢)绝缘层起泡、剥离、无玻璃光泽,有时伴有板型发生改变(不平坦)。
电气、机械故障跑偏断带等造成停机,带钢在炉内时间长。
露晶带钢表面上可看到隐约可见的晶粒。
(1)CA3线MgO底层含水率较高。
(2)带钢在CA3线过氢化或油污清洗不净。
(3)CB炉露点高。
保护气体中的含氧量高或含有水份。
带钢轧制常见缺陷原因分析

带钢轧制常见缺陷原因分析结疤(M01)图7-1-1图7-1-21. 缺陷特征附着在钢带表面,形状不规则翘起的金属薄片称结疤。
呈现叶状、羽状、条状、鱼鳞状、舌端状等。
结疤分为两种,一种是与钢的本体相连结,并折合到板面上不易脱落;另一种是与钢的本体没有连结,但粘合到板面上,易于脱落,脱落后形成较光滑的凹坑。
2. 产生原因及危害产生原因:①板坯表面原有的结疤、重皮等缺陷未清理干净,轧后残留在钢带表面上;②板坯表面留有火焰清理后的残渣,经轧制压入钢带表面。
危害:导致后序加工使用过程中出现金属剥离或产生孔洞。
3. 预防及消除方法加强板坯质量验收,发现板坯表面存在结疤和火焰清理后残渣应清理干净。
4. 检查判断用肉眼检查;不允许存在结疤缺陷,对局部结疤缺陷,允许修磨或切除带有结疤部分带钢的方法消除,如结疤已脱落,则比照压痕缺陷处理。
7.2 气泡(M02)图7-2-1 闭合气泡图7-2-2 开口气泡图7-2-3 开口气泡1. 缺陷特征钢带表面无规律分布的圆形或椭圆形凸包缺陷称气泡。
其外缘较光滑,气泡轧破后,钢带表面出现破裂或起皮。
某些气泡不凸起,经平整后,表面光亮,剪切断面呈分层状。
2. 产生原因及危害产生原因:①因脱氧不良、吹氩不当等导致板坯内部聚集过多气体;②板坯在炉时间长,皮下气泡暴露或聚集长大。
危害:可能导致后序加工使用过程中产生分层或焊接不良。
3. 预防及消除方法①加强板坯质量验收,不使用气泡缺陷暴露的板坯;②严格按规程加热板坯,避免板坯在炉时间过长。
4. 检查判断用肉眼检查;不允许存在气泡缺陷。
7.3 表面夹杂(M03)图7-3-1图7-3-21. 缺陷特征板坯中的夹杂或夹渣经轧制后在钢带表面暴露的块状或长条状的夹杂缺陷称表面夹杂。
其颜色一般呈棕红色、黄褐色、灰白色或灰黑色。
2. 产生原因及危害产生原因:板坯皮下夹杂轧后暴露或板坯原有的表面夹杂轧后残留在带钢表面。
危害:可能导致后序加工过程中产生孔洞、开裂、分层。
型钢常见轧制缺陷_周建明

收稿日期:1997-04-29第18卷第4期 1998年8月江 西 冶 金JIAN GXI M ET AL LU RGY V ol.18,No.4 August 1998型钢常见轧制缺陷新余钢铁有限责任公司 周建明在轧钢生产中,由于孔型设计不当、轧辊和导卫装置安装不正、工人调整技术欠佳、金属加热不均及钢质变化等原因,均会造成轧制产品的缺陷。
轻则影响产品的质量,重则导致钢材(坯)报废。
轧制缺陷的种类很多,在简单断面型钢的生产中,常见的轧制缺陷有耳子、扭转、弯曲等。
1 耳子耳子缺陷可分为一侧耳子和两侧耳子。
1 1 一侧耳子产生在轧件断面一侧的耳子称为一侧耳子,产生原因及消除办法主要有3种。
(1)入口导板安装偏向一侧,造成金属在孔型中一侧过充满,而另一侧欠充满(图1),产生耳子的一侧即入口导板偏向的一侧。
消除办法是向相反方向调整入口导板。
图1 入口导板安装不正产生一侧耳子(2)入口导板倾斜使孔型与导板中心线相交成一定角度,造成轧件中垂线不与孔型中垂线重合,轧件朝孔型的一侧倾斜,产生一侧耳子(图2)。
导板倾斜是由于横梁安装不正或入口导板高低不平引起。
因此,必须将横梁安装水平,高低适当,保证导板与孔型中心线重合,防止一侧耳子的产生。
(3)由于入口导板松动,轧件弯曲,咬入后,导板随弯曲轧件左右摆动,出现间断性耳子。
解决办法是将导板对正后紧固。
图2 入口导板倾斜产生一侧耳子1 2 两侧耳子产生于轧件断面两侧的耳子称为两侧耳子。
产生的原因及消除办法也有3种。
(1)轧件在孔型中压下量过大,或者前一孔轧出的轧件过厚,翻钢进入本孔轧制便出现两侧耳子。
消除办法是减少本孔压下量,或者增加前一孔压下量。
防止轧件在孔型中过充满是消除两侧耳子的主要措施。
(2)轧件温度过低,轧制时金属的宽展量增加,形成过充满而产生两侧耳子;同时,轧件温度过低,金属变形抗力增大,导致轧辊弹跳增加,翻钢进入下一道次亦容易形成两侧耳子。
应根据温度变化,及时调整压下量,以保证成品不出耳子。
轧钢常见缺陷

(3)成品孔出口卫板过低,锯齿磨损太老,垫板太低,在辊道运送速度过快时,碰撞档板等都容易产生弯头。
尺寸超差(规格不合)
钢轨断面几何尺寸不符合标准规定,统称尺寸超差。
其中:钢轨头部超过正偏差的叫头大,超过负偏差的叫头小。轨腰厚度超过正偏差的叫腰厚.超过负偏差的叫腰薄。轨底宽度超过正偏差的叫底宽,超过负偏差的叫底小。轨腰高度超过正偏差的叫腹高,超过负偏差的叫腹低。轨的高度超过正偏差的叫轨高,超过负偏差的叫轨低。断面不与其垂直轴线对称的叫不对称(又叫偏称)。
(1)导卫板安装不当,对轧件压力过大,将轧件表面划伤。
(2)导卫板加工不良,口边不圆滑,或磨损严重,粘有氧化铁皮,将轧件表面划伤。
(3)孔型侧壁磨损严重,当轧件接触时产生弧形划伤。
(4)钢材在运输过钢其一侧面沿轧制方向全长或周期性的缺少金属称缺肉,缺陷处没有成品孔轧槽的热轧印迹,色暗、表面较粗糙。
(4)孔型磨损严重,也能产生表面轧痕。
折叠
沿钢轨的轧制方向出现的长条形金属重叠缺陷叫折叠。折叠呈直线状,也有呈锯齿状。多出现在钢轨头部、底部边沿等处,沿钢轨全长或局部分布。
(1)主要是由于成品孔前某一道次出现耳子,再轧后形成折叠。
(2)由于轧辊车削不良,锁口过宽。
(3)帽形孔压下量过大,底部宽度过大,进轨形切深孔形成耳子,再轧时形成折叠。
(1)主要因钢坯缩孔部分未切净。
(2)钢坯中心聚集大量的非金属夹杂物,在轧制中不能使金属焊合。
开裂
钢坯在轧制中,自动裂开称开裂。工业轨尤为多见。
(1)由于钢锭中心部位集中大量气体和非囊属夹杂物所致。
(2)由于钢“内裂”或“穿孔”所致。
过烧
因钢坯加热不当,钢轨表面出现的横向粗糙裂口叫“过烧”。裂口多出现在轨头和轨底侧边,金相观察裂口处金属晶粒粗大。
- 1、下载文档前请自行甄别文档内容的完整性,平台不提供额外的编辑、内容补充、找答案等附加服务。
- 2、"仅部分预览"的文档,不可在线预览部分如存在完整性等问题,可反馈申请退款(可完整预览的文档不适用该条件!)。
- 3、如文档侵犯您的权益,请联系客服反馈,我们会尽快为您处理(人工客服工作时间:9:00-18:30)。
轧钢常见缺陷1、型钢常见缺陷缺陷名称缺陷特征产生原因型钢表面上的疤状金属薄块。
其大小、深浅不等,外结疤形极不规则,常呈指甲状、鱼鳞状、块状、舌头状无由于钢坯未清理,使原有的结疤轧后仍残留在钢材表面上。
规律地分布在钢材表面上,结疤下常有非金属夹杂物。
暴露在钢材表面上的非金属物质称为表面夹杂,一(1)钢坯带来的表面非金属夹杂物。
般呈点状、块状和条状分布,其颜色有暗红、淡黄、表面夹杂在加热或轧制过程中,偶然有非金属夹杂物(2)( 如加热炉的耐火材料及炉渣等) ,灰白等,机械的粘结在型钢表面上,夹杂脱落后出现附在钢坯表面上,轧制时被压入钢材,冷却经矫直后部分脱落。
一定深度的凹坑,其大小、形状无一定规律。
(1)主要是由于镇静钢的缩孔或沸腾钢的气囊未切净。
此缺陷在型钢的锯切断面上呈黑线或黑带状,严重的分层(2) 钢坯的皮下气泡,严重疏松,在轧制时未压合,严重的夹杂物也会造成分层。
分离成两层或多层,分层处伴随有夹杂物。
(3)钢坯的化学成份偏析严重,当轧制较薄规格时,也可能形成分层。
型钢表面呈现的一种无规律分布的圆形凸起称为凸包,凸起部分的外缘比较圆滑,凸包破裂后成鸡爪形气泡 ( 凸包)钢坯有皮下气泡,轧制时未焊合。
裂口或舌形结疤,叫气泡。
多产生于型钢的角部及腿尖。
(1)钢坯有裂缝或皮下气泡、非金属夹杂物,经轧制破裂暴露。
顺轧制方向出现在型钢表面上的线形开裂,一般呈直(2) 加热温度不均匀,温度过低,轧件在轧制时各部延伸与宽展不一致。
裂纹线形,有时呈“ Y”形,多为通长出现,有时局部出现。
(3) 加热速度过快、炉尾温度过高或轧制后冷却不当,易形成裂纹,此种情况多发生在高碳钢和低合金钢上。
(1)对工字钢成品孔腿长往往表现在开口腿上,主要由于腰部压下量不够,角钢和尺寸超差尺寸超差是指型钢截面几何尺寸不符标准规定要求的槽钢成品孔压下量的大小,直接影响腿长和腿短。
(尺寸不统称。
这类缺陷名目繁多,大部以产生部位以及其超(2)切深孔切人太深,造成腿长无法消除。
合、规格不差程度加以命名。
例工、槽、角钢的腿长、腿短、腰(3)轧辊不水平或有轴向串动,以及800 咬入不正,成品孔夹板上偏等都会造成一合)厚、腰薄及一腿长,一腿短。
腿长,一腿短等。
(4)腰的厚、薄主要是成品孔及成品前孔压下量不合理所造成。
(1)导卫板安装不当,对轧件压力过大,将轧件表面划伤。
一般呈直线或弧形的沟槽,其深度不等,通长可见沟划伤(刮伤、导卫板加工不良,口边不圆滑,或磨损严重,粘有氧化铁皮,将轧件表面划伤。
(2)底,长度自几毫米到几米,连续或断续地分布于钢材孔型侧壁磨损严重,当轧件接触时产生弧形划伤。
擦伤、划痕)(3)的局部或全长,多为单条,有时出现多条。
(4)钢材在运输过程中与表面粗糙的辊道、盖板、移钢机、活动挡板等接触划伤。
(1)孔型设计不良,轧辊车削不正确及轧机调整不当,使轧件进入成品孔时由于金属量不足,造成孔型充填不满。
(2)轧槽错牙或入口导板安装不当,造成轧件某一面缺少金属,再轧时孔型充填不型钢其一侧面沿轧制方向全长或周期性的缺少金属称满。
缺肉缺肉,缺陷处没有成品孔轧槽的热轧印迹,色暗、表前、后孔磨损程度不一样。
(3)面较粗糙。
(4)圆轧件弯、扭造成进孔不正。
(5)对于工、槽钢,困钢坯不清理,往往出现结疤掉到闭口腿内,在轧制过程中便会出现周期性的腿尖缺肉。
在型钢表面上与 L 型开口处相对应的地方,出现顺轧(1)轧机调整不当或孔型磨损严重,使成品前孔来料过大或成品孔压下量过大,产耳子制方向延伸的凸起部分称为耳子。
有单边的,也有双生过充满,多产生双边耳子。
边的,有时耳子产生在型钢的全长,也有局部或断续(2)进入成品孔前因事故造成温度过低,进入成品孔时延伸降低,宽展过大,多产的,方、圆钢产生较多。
生双边耳子。
(3)成品孔入口夹板向孔型一侧安偏或松动。
金属挤人孔型一侧辊缝里,产生单面耳子。
(4)成品入口夹板间隙过大或松动,进钢不稳,易产生双面断续耳子。
(1)卫板安装不良,使轧件出孔时受到力偶的作用产生扭转。
(2)两侧延伸不一致,主要是压下不均或辊子有轴向串动。
(3)方、圆钢由于入口夹板安装不正确,使钢料进孔不正,造成延伸不一致。
扭转型钢绕其轴线扭成螺旋状称为扭转(4)轧辊安装不正确,上、下轧辊轴线不在同一垂直平面内,即上、下辊成水平投影交叉,使轧件扭转。
(5)矫直机调整不当。
(1)轧机调整不当,轧辊倾斜或跳动,上、下辊径差大,造成速度差大。
(2)出口卫板安装不正确,卫板梁过低或过高。
(3)轧件温度不均匀,使金属延伸不一致。
(4)冷床拉钢小车不同步或滑轨不光滑。
型钢沿垂直或水平方向呈现不平直的现象称为弯曲,弯曲(弯头)运输辊道速度过快,容易把钢材头部撞弯。
(5)一般为镰刀形或波浪形,仅只头部的弯曲叫弯头。
(6)矫直温度过高,冷却后容易产生弯曲。
(7)成品捆扎长短不齐较大。
在运输中装卸不当。
(8)堆垛时不按规定进行。
(9)锯片用的太老,也容易产生弯头。
型钢断面几何形状歪斜不正,这类缺陷对不同品种各(1)矫直辊孔型设计不合理。
形状不正异,名称繁多。
如工槽钢的内并外斜,弯腰挠度,角矫直机调整操作不当。
(2)钢顶角大、小腿不平等。
(3) 矫直辊磨损严重。
(4)轧辊磨损或成品孔出口卫板安装不良。
2、重轨常见缺陷缺陷名称缺陷特征产生原因在钢轨的头、腰底部等处局部粘附的金属蒲片状疤皮为重轨结疤,结疤外形轮廓不规则,有闭合和不闭合的,有生根和不生根的,结疤下由于钢坯未清理,钢坯原有的结疤经热轧变形后残留在钢勒表面上。
面常有肉眼可见的非金属夹杂物。
(1)钢坯原有的裂纹经热轧变形后,演变在钢轨表面上。
在钢轨表面上呈现的与轧制方向一致的直线形缝隙叫“裂纹”,长(2)加热工艺不台理,即温度过高或加热速度过快,造成热应力,形成裂纹短不一,多出现在轨头。
裂纹通常较深,缝底尖细,有氧化铁皮和裂纹。
非金属夹杂物(3)轧制过程中冷却不当,即因事故浇水时间过长或孔型冷却水开得太大,低温轧制易形成裂纹。
暴露在钢轨表面上的非金属物质称为表面夹杂。
一般呈点状、块状表面夹杂钢坯有夹杂。
和条状,其大小、深浅无规律,颜色有暗红、淡黄、灰白等。
轨腰断面中心线附近显露的金属分离层叫分层。
常呈现黑线或黑(1)主要因钢坯缩孔部分未切净。
分层带,内有大量非金属夹杂物。
钢坯中心聚集大量的非金属夹杂物,在轧制中不能使金属焊合。
(2)(1)由于钢锭中心部位集中大量气体和非囊属夹杂物所致。
开裂钢坯在轧制中,自动裂开称开裂。
工业轨尤为多见。
(2)由于钢“内裂”或“穿孔”所致。
因钢坯加热不当,钢轨表面出现的横向粗糙裂口叫“过烧”。
裂口(1)主要是由于加热温度过高或在高温区停留时间太长。
过烧多出现在轨头和轨底侧边,金相观察裂口处金属晶粒粗大。
加热操作不当或炉内氧化性气氛过强。
(2)(1)轧机操作调整不当或成品前孔磨损严重,造成成品孔压下量过大。
在钢轨的外表面上沿长度方向出现一条金属凸起称耳子,多出现在耳子钢坯温度低,造成轧制过程中的宽展大。
(2)轨头中央开口处及轨底边端等部位。
(3)入口导板安装偏斜、松动,轧件进孔不正。
(1)由于轧槽掉肉,使轧件表面呈现周期性的凸包。
(2)孔型内粘结铁皮,结疤等,使轧件产生周期性的口坑,又称缺肉。
轧痕(凸、在钢轨表面出现的各种不连续的伤痕叫轧痕。
各种轧痕都存在热加(3)在轧制过程中,氧化铁皮压入轧件表面,冷却或矫直后脱落。
形成凹、压印)工的痕迹、般呈周期性出现,有时无规律分布。
无规律的压痕。
(4)孔型磨损严重,也能产生表面轧痕。
(1)主要是由于成品孔前某一道次出现耳子,再轧后形成折叠。
(2)由于轧辊车削不良,锁口过宽。
(3)帽形孔压下量过大,底部宽度过大,进轨形切深孔形成耳子,再轧沿钢轨的轧制方向出现的长条形金属重叠缺陷叫折叠。
折叠呈直线时形成折叠。
折叠状,也有呈锯齿状。
多出现在钢轨头部、底部边沿等处,沿钢轨全轨形切深孔压下量过大.轨底侧压过大,使轧件出现耳子。
再轧时(4)长或局部分布。
形成折叠。
(5)有时由于孔型严重磨损.将轧件表面啃伤后再轧时形成折选。
(6)导卫板安装不当.有棱角或粘有铁皮使轧件划伤,再轧后形成折叠。
(1)卫板安装不良,使钢轨产生力偶,形成扭转。
钢轨上某部分相对另一部分,沿长度方向绕其轴线旋转定角度称扭(2)轧件温度不均或压下量不均,造成各部延伸不一致。
扭转转,严重时象麻花.扭转分全长和局部扭转两种。
矫直机调整不当,钢轨受力偶作用。
(3)(4)在冷却台架上翻钢时因温度较高也会出现扭转。
(1)由于重轨的头、腰、底面积相差较大,使轧制、冷却等工序操作易产生弯曲。
钢轨沿垂直或水平方向呈现不平直的现象叫弯曲,一般呈镰刀形或弯曲矫直机操作调整不良或矫直温度过高。
(2)波浪形,仅在端部的弯曲又叫弯头。
(3)成品孔出口卫板过低,锯齿磨损太老,垫板太低,在辊道运送速度过快时,碰撞档板等都容易产生弯头。
(1)头太、头小产生的主要原因是轧制温度和轴瓦的磨损及轧机部件的松动等造成。
2) 腰厚、腰薄产生的主要原因是:如按孔型设计头部压下量为钢轨断面几何尺寸不符合标准规定,统称尺寸超差。
77—=6.7mm;腰部压下量为 16 一= 1.5mm,如果六孔压下量加大l.5mm,其中:钢轨头部超过正偏差的叫头大,超过负偏差的叫头小。
轨腰则头部尺寸为 75.5mm 压下量由 6.7mm减少到 5.2mm,腰部压下量由尺寸超差1.5mm减少到 0,自然头部对腰部有拉伸加之腰部无压下而宽展,所以厚度超过正偏差的叫腰厚.超过负偏差的叫腰薄。
轨底宽度超过正(规格不偏差的叫底宽,超过负偏差的叫底小。
轨腰高度超过正偏差的叫腹腰变薄,反之腰部变厚。
合)高,超过负偏差的叫腹低。
轨的高度超过正偏差的叫轨高,超过负底大主要是由成品孔腰厚,上腿长引起及六孔开口腿磨损严重等。
(3)偏差的叫轨低。
断面不与其垂直轴线对称的叫不对称( 又叫偏称 ) 。
(4)底小主要是帽形孔未能将腿部宽展到足够的长度,或由腰薄引起。
(5)轨高、轨低主要是由于轧件的温度高、低,成品前孔轨头部分或成品孔轨头部分磨损情况引起。
(6)腹高、腹低主要是导卫板安装不良,孔型严重磨损造成。
矫裂(矫钢轨在冷状态矫直、压直过程中,产生的直线形或折线形的裂纹。
(1)因辊式或立式矫直机调整操作不当,将钢轨矫断。
断、压断)其裂口棱角尖锐,呈银亮色,严重时劈裂成碎断。
(2)钢质不好,如局部夹杂、偏析,在矫直过程中被矫( 压 ) 裂( 断 ) 。
3、线材常见缺陷缺陷名称缺陷特征产生原因1) 轧槽导卫安装不正及放偏过钢,使轧件产生耳子。
盘条表面沿轧制方向的条状凸起称为耳子,有单边耳子,也有双边耳(2)轧制温度的波动或局部不均匀,影响轧件的宽展量,产生耳子。
耳子子。
在高速线材轧机 ( 连轧 ) 生产中,最终产品头尾两端很难避免耳子(3)坯料的缺陷,如缩孔、偏析、分层、外来夹杂物,影响轧件的正的产生。