PFMEA -TRIM 防水膜 过程失效模式分析
PFMEA 10
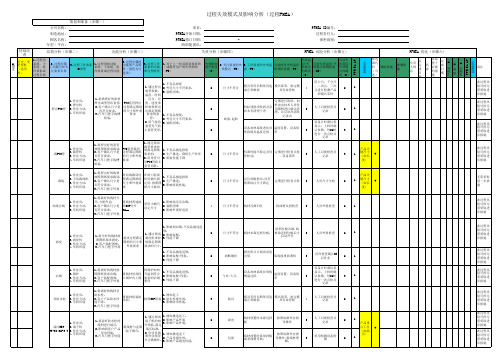
3
人员尺寸全检
6
L
键尺寸 (如长
▼
度)
绞线分线
1.作业员. 2.作业方法. 3.车间环境
1.将裁好的线材分 开,方便作业. 2.客户确认尺寸是 否符合要求. 3.汽车门把手外观
将线材两端按 照SOP分开 25mm
采用小钢尺 设定尺寸
1.影响端压及沾锡. 2.装配困难 3.影响外观舒适度
4
尺寸不符合 线材反弹归位
失效分析(步骤四)
PFMEA 风险分析(步骤五)
1.对于上一较高级别要素和 /或最终用户的失效影响 (PE)
失效起
当前失
失效影响 的严重度
(S)
2.关注要素的失 效模式(FM)
3.工作要素的失效起 当前的对失效起因
因(FC)
的预防措施(PC)
因/失 效模式 的频度
当前失效起因/失 效模式探测措施 (DC)
组装.
1.通过调试 裁管机来控 制满足图纸 1.不良品挑选报废 要求的. 2.生产挑选,降低生产效率 2.用导管引 3.组装性能下降 导PVC管防止 套管切斜.
6
尺寸不符合
机器性能不稳定及导 定期进行检查点检
管松动.
、设备保养
3
人工目视检查并 记录
3
产品关
L
键尺寸 (如长
▼
度)
裁线
1.作业员. 2.手动裁线机 3.作业方法. 4.车间环境
效起因/ 失效模 式探测
(O)
度(D)
筛选 器代 码 预防措施 (可 选)
探测措 施
PFMEA 优化(步骤六)
目
负责 人姓 名
标 完 成 日
期
状 态
采取 基于 证据 的措 施
电动汽车充电机过程潜在失效模式及后果分析PFMEA

5 8 5
漏打螺钉 / ★ 风机线脱位
/ 线有弹性
客户拒收
6 / 网罩漏打螺钉
螺丝刀点检 机器打完检查
3 全检
安装前整理,设备优 先打带线端螺钉
2
全检
点胶后拉扯别在V卡 孔
2 全检
机器打完检查
3 全检
网罩不良 客户不满意
5
/ 网罩螺钉不到位
螺丝机/螺丝刀设备 点检
4 全检
防水透气阀 不到位
机器进水,性 能下降,客户 拒收 机器进水,性 能下降 机器进水,性 能下降 机器进水,性 能下降 机器进水,性 能下降
70
无
70
无
72
电烙铁加 入点检
90
更换模具 时记录
72
无
72
无
28
无
108
自检,互 检
EV-JL-702-YF-033(A/0)
威海天力电源有限公司
A4(210mm*297mm)
微卡尺寸大 安装困难
6
模具尺寸不合适 模具首次/定期检查
/
温度/压力不合适
温度/压力设置检查 开机试制
3
首件检查,100条检 查
无
4 64
无
4 80
无
4
120
工装清理 、检查
3 42
无
3 18
无
4 24
无
4 72
无
4 24
无
4 24
无
3 21
无
4 96 增加标识
2 16
无
4 32
无
EV-JL-702-YF-033(A/0)
威海天力电源有限公司
线束DFMEA浅析
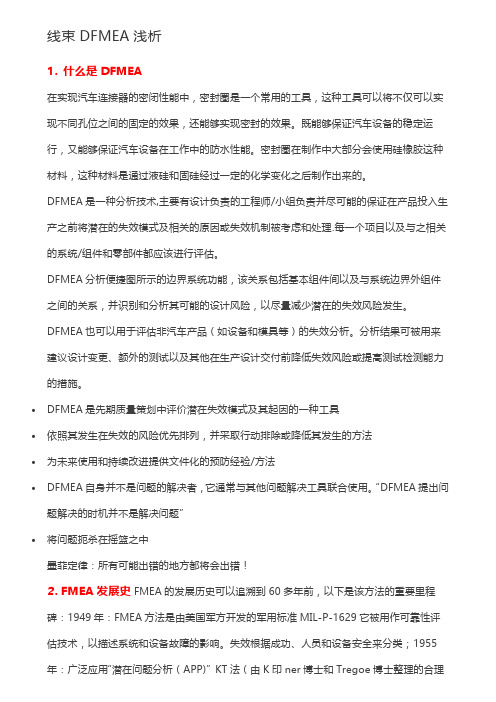
线束DFMEA浅析1. 什么是DFMEA在实现汽车连接器的密闭性能中,密封圈是一个常用的工具,这种工具可以将不仅可以实现不同孔位之间的固定的效果,还能够实现密封的效果。
既能够保证汽车设备的稳定运行,又能够保证汽车设备在工作中的防水性能。
密封圈在制作中大部分会使用硅橡胶这种材料,这种材料是通过液硅和固硅经过一定的化学变化之后制作出来的。
DFMEA是一种分析技术,主要有设计负责的工程师/小组负责并尽可能的保证在产品投入生产之前将潜在的失效模式及相关的原因或失效机制被考虑和处理.每一个项目以及与之相关的系统/组件和零部件都应该进行评估。
DFMEA分析便捷图所示的边界系统功能,该关系包括基本组件间以及与系统边界外组件之间的关系,并识别和分析其可能的设计风险,以尽量减少潜在的失效风险发生。
DFMEA也可以用于评估非汽车产品(如设备和模具等)的失效分析。
分析结果可被用来建议设计变更、额外的测试以及其他在生产设计交付前降低失效风险或提高测试检测能力的措施。
•DFMEA是先期质量策划中评价潜在失效模式及其起因的一种工具•依照其发生在失效的风险优先排列,并采取行动排除或降低其发生的方法•为未来使用和持续改进提供文件化的预防经验/方法•DFMEA自身并不是问题的解决者,它通常与其他问题解决工具联合使用。
“DFMEA提出问题解决的时机并不是解决问题”•将问题扼杀在摇篮之中墨菲定律:所有可能出错的地方都将会出错!2. FMEA发展史FMEA的发展历史可以追溯到60多年前,以下是该方法的重要里程碑:1949年:FMEA方法是由美国军方开发的军用标准MIL-P-1629它被用作可靠性评估技术,以描述系统和设备故障的影响。
失效根据成功、人员和设备安全来分类;1955年:广泛应用“潜在问题分析(APP)”KT法(由K印ner博士和Tregoe博士整理的合理想法/思考方法的模型);1963年:美国国家航空航天局(NASA)制定了“失败模式、影响和关鍵性分析“(FMECA)应用于阿波罗项目;1965年:广泛用于航空和航天应用,食品工业和核技术应用领域;1975年:这种方法被部署在核电工程以及其他领域;1977年:FMEA方法开始由福特汽车公司引入汽车行业使用;1980年:在德国失效模式和影响分析以“FMEA(DIN 25448)”为标题进行了标准化,在德国汽车工业协会中,该方法是专门应用于汽车领域。
FMEA
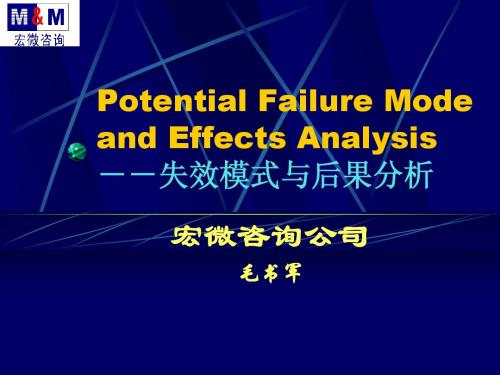
子系统
车架总成
功能1:稳固支撑座椅 功能 潜在的失效模式: -支撑结构失效 -支撑过度倾斜 功能2:提供满意外观 功能 潜在的失效模式: -抛光恶化 -涂装瑕疵 ······
零部件
车架上横管
功能1:提供支撑结构 潜在的失效模式: -结构失效; -过度倾斜 功能2:······
车把总成 ······
下前管 ······
如何进行FMEA- 如何进行FMEA-功能 FMEA
功能-系统能够完成或必需完成的任务事项。 功能-系统能够完成或必需完成的任务事项。 做什么用的? “做什么用的?” -发动机提供动力 发动机功能: -发动机功能:提供动力 “做什么所必需的?” 做什么所必需的? -帮助飞机上升需要可变机翼 可变机翼功能: -可变机翼功能:标准飞机上升
如何进行FMEA-系统、子系统、零部件 如何进行FMEA 系统、子系统、
接口和相互作用
子系统 A 子系统B 子系统B 子系统D 子系统 环境 子系统 C
系统
如何进行FMEA 系统、子系统、 如何进行FMEA-系统、子系统、零部件
接口: 接口:子系统直接通过接口连接 子系统与环境的“环境接口” 子系统与环境的“环境接口” 子系统之间的接口 A-B、D; - 、 ; B-A、D、C - 、 、 C-B、D - 、 D-A、B、C - 、 、
如何进行FMEA- 如何进行FMEA-概念重温 FMEA
设计意图( 对既定产品, 设计意图(design intent):对既定产品,希望或不希望做什么的 对既定产品 清单。 清单。 设计寿命( 设计所预期执行其功能的时间间隔( ห้องสมุดไป่ตู้计寿命(design life):设计所预期执行其功能的时间间隔(如 设计所预期执行其功能的时间间隔 周期、时间、里程等)。 周期、时间、里程等)。 特性( 一种可测量的产品特性( ),或过 特性(feature):一种可测量的产品特性(半径、硬度等),或过 一种可测量的产品特性 半径、硬度等), 程特性(温度、压力等)。 程特性(温度、压力等)。 过程的特殊特性( 过程的特殊特性(special process characteristic):过程的特殊 过程的特殊 特性(如关键、重点、重要、主要)是在生产制造过程中, 特性(如关键、重点、重要、主要)是在生产制造过程中,针对 针对过程特性变异的一些目标数值,所做的必须控制要求。 针对过程特性变异的一些目标数值,所做的必须控制要求。旨在 确保该变异在过程或特殊的产品特性在被控制之下, 确保该变异在过程或特殊的产品特性在被控制之下,以达到目标 值。 产品的特殊特性( 产品的特殊特性(special product characteristic):产品的特殊 产品的特殊 特性(如关键、重点、重要、主要)是合理地预料到, 特性(如关键、重点、重要、主要)是合理地预料到,会对产品 的政府标准或法规的安全性或符合性产生重大影响的, 的政府标准或法规的安全性或符合性产生重大影响的,或可能使 顾客对产品的满意度产生重大影响的一种产品特性。 顾客对产品的满意度产生重大影响的一种产品特性。
设计失效模式和影响分析_DFMEA

5
November 01, 2013
_Sector
Confidential
FMEA : 失效模式及其后果分析
风险管理: 识别并减轻失效风险
目标
识别新产品、新工艺或者新的服务流程中可能出现的失效 模式,从而设法改进设计,使产品在实际应用中更稳健。
6
November 01, 2013
输出: 风险, 提高过程能力/过程控制的措施 举例: 过程步骤: 连接风道和电机外壳 过程需求: 确保气密性 失效模块: 气密性差 起因: 空气导管直径过大/变形
设计FMEA 产生风险
过程步骤
过程FMEA 过程能力:
提高过程能力 (控制预防)
14
November 01, 2013 _Sector
改善风管的注射成型工艺
5. 生产
3
3
November 01, 2013
_Sector
Confidential
FMEA步骤与FMEA方法
准备
头脑风暴
分析 时间
跟踪
准备 :
策划FMEA 搜集必要输入信息 准备参数图和功能/结构框图等等
头脑风暴 : 分析 :
列出FMEA中可能存在的失效模式和后果 识别原因 确定风险级别
降低风险措施 定期更新风险级别
过程 FMEA
过程步骤: 连接风道和电机外壳 需求 (目的): 气密连接 失效模式:气密连接性能不好 原因:空气导管直径太大或已变形 (过程)
• • •
设计FMEA不依靠过程控制来克服设计缺陷,但应考虑制造过程(如过程能力)技术的局限性 过程FMEA 不依靠产品设计变更来克服过程缺陷,但应考虑与装配相关的产品设计特性 因此,设计FMEA不关注诸如“操作者风管安装不当”或“风管直径超差”的原因,但如有与设计相关的因素导致 连接不当,就需加以考虑
PFMEA范本
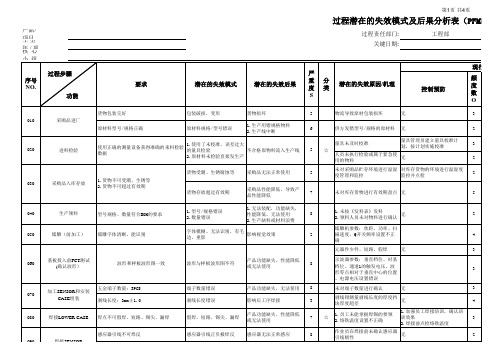
5
75
物料发运现场前,确认是否有IQC 检验标识
2
20
每月盘点货物的受损情况
2
20
每月对库存货物进行有效期盘
点,超出有效期的货物,由IQC检 2
70
验合格后重新张贴检验标识。
领料员对照《发料表》对物料规
格/型号/数量进行确认
5
80
镭雕字体外观全检 FCT测试,确认波形
5
40
4
96
在测试前对示波器参数点检
量具管理员建立量具校准计 划,按计划实施校准
☆
人员未执行检验或属于紧急使 用的物料
无
3 2
030
采购品入库存放
1.货物不可受潮、生锈等 2.货物不可超过有效期
货物受潮、生锈腐蚀等
采购品无法正常使用
5
货物存放超过有效期
采购品性能降低,导致产 品性能降低
7
未对采购品贮存环境进行温湿 对库存货物的环境进行温湿度
090
过程步骤
功能
焊接SENSOR
100
注胶前FCT测试 (调试波形)
110
基板焊接点检查
120
感应距离测试
130
注胶
140
注胶后测试波形
150 160
编制:
成品检验 包装
第2页 共4页
过程潜在的失效模式及后果分析表(PFMEA)
过程责任部门: 关键日期:
工程部
要求
潜在的失效模式
潜在的失效后果
严 重分 度类
度管理和监控
监控并点检
2
未对库存货物进行有效期盘点 无
5
040
生产领料
型号规格、数量符合BOM的要求
汽车驾驶室主线束PFMEA过程失效模式分析
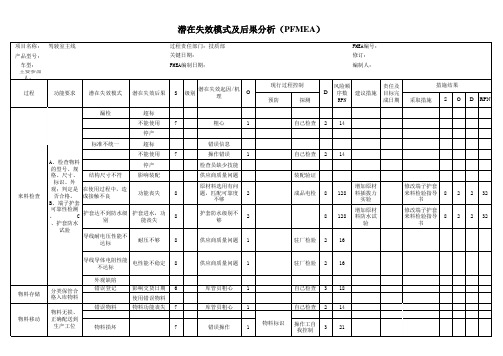
项目名称:产品型号:车型: 主要参加人:预防探测采取措施SODRPN漏检超标不能使用7粗心1自己检查214停产标准不统一超标错误信息不能使用7操作错误1自己检查214停产检查员缺少技能结构尺寸不符影响装配供应商质量问题装配验证在使用过程中,造成接触不良功能丧失8原材料选用有问题,匹配可靠度不够2成品电检8128增加原材料插拔力实验修改端子护套来料检验指导书82232护套达不到防水级别护套进水,功能丧失8护套防水级别不够28128增加原材料防水试验修改端子护套来料检验指导书82232导线耐电压性能不达标耐压不够8供应商质量问题1驻厂检验216导线导体电阻性能不达标电性能不稳定8供应商质量问题1驻厂检验216外观缺陷错误登记影响交货日期6库管员粗心1自己检查318使用错误物料错误物料物料功能丧失7库管员粗心1自己检查214物料损坏7错误操作1操作工自我控制321责任及目标完成日期DOS建议措施风险顺序数RPN 潜在失效起因/机理物料标识A、检查物料的型号、规格、尺寸、标识、外观;判定是否合格。
B、端子护套可靠性检测。
C、护套防水试验分类保管合格入库物料物料无损、正确配送到生产工位来料检查物料存储物料移动FMEA编制日期:编制人:现行过程控制措施结果过程功能要求级别潜在失效模式潜在失效后果驾驶室主线过程责任部门:技质部FMEA编号:关键日期:修订:项目名称:产品型号:车型: 主要参加人:预防探测采取措施SODRPN责任及目标完成日期DOS 建议措施风险顺序数RPN 潜在失效起因/机理FMEA编制日期:编制人:现行过程控制措施结果过程功能要求级别潜在失效模式潜在失效后果驾驶室主线过程责任部门:技质部FMEA编号:关键日期:修订:断线芯,伤线芯。
性能下降6设备设置错误3100%自检236首件检验下错导线不能使用6缺标识2100%自检224切线、波纹管不能使用7设备设置错误1321尺寸过短下料尺寸超差长影响组装5输入值错误5培训操作者8200首末检查52220剥皮过长影响外观及 组装6设备设置错误1培训操作者318首件检验剥皮过短影响拉脱力7设备设置错误2培训操作者228首件检验线体波纹管影响外观4原材料缺陷2操作者100%自检216表面有缺陷压接拉力过小拉脱力不够,导线脱落搭铁9模具调整错误3首件/过程检验381设专人调整模具92354压接拉力过大断线芯7模具调整不当2过程控制342线芯伸出过长影响装配7操作失误2100%自检342线芯伸出过短影响拉脱力7操作失误2100%自检342压绝缘皮,压断导线电路不通8送料不到位2培训操作者100%自检348端子压接操作失误2100%检验342首件检验培训操作者检查标识培训操作者不能装配7按照裁线压接工艺表标注的导线数量、型号、颜色、长度、剥皮方向及长度加工按照裁线压接工艺表压接端子、超声波焊★切线剥皮 波纹管切断★端子压接、超声波焊项目名称:产品型号:车型: 主要参加人:预防探测采取措施SODRPN责任及目标完成日期DOS 建议措施风险顺序数RPN 潜在失效起因/机理FMEA编制日期:编制人:现行过程控制措施结果过程功能要求级别潜在失效模式潜在失效后果驾驶室主线过程责任部门:技质部FMEA编号:关键日期:修订:不能装配7接工艺表压接端子、超声波焊超声波焊项目名称:产品型号:车型: 主要参加人:预防探测采取措施SODRPN责任及目标完成日期DOS建议措施风险顺序数RPN潜在失效起因/机理FMEA编制日期:编制人:现行过程控制措施结果过程功能要求级别潜在失效模式潜在失效后果驾驶室主线过程责任部门:技质部FMEA编号:关键日期:修订:86.0mm 2导线压接状态,影响整车对插装配3端子插接听“咔”声,轻轻回拉确认100%自检248专用模具压接首件装配验证目视9119平齿影响电性能9端子压接搬运3插接原则38192236造成操作不规范锁紧件未上可靠性能下降8操作失误1100%自检216作业工艺卡未按规定布线影响外观线束6导线无理顺1返修自检318尺寸端子插反影响客户装配7拿错方向1100%目测214护套方向错影响客户装配5拿错方向1案板直观注明210零件正反易混淆方向目测检查漏装线影响电路6未进行检查1按案板示意318图进行组装100%目视自检插错孔位混路烧车9未进行检查4100%电检272100%自检92236波纹管装配影响分支尺寸6未装配到位1装配图标明318有偏差影响客户装配长度,直径位置100%自检按照产品图纸,把分装子件组合成线束组装线束项目名称:产品型号:车型: 主要参加人:预防探测采取措施SODRPN责任及目标完成日期DOS 建议措施风险顺序数RPN 潜在失效起因/机理FMEA编制日期:编制人:现行过程控制措施结果过程功能要求级别潜在失效模式潜在失效后果潜在失效模式及后果分析(PFMEA )驾驶室主线过程责任部门:技质部FMEA编号:关键日期:修订:穿波纹管时绝缘性能下降7导线未防护1装波纹管时214纸,把分装子件组合成线束项目名称:产品型号:车型: 主要参加人:预防探测采取措施SODRPN责任及目标完成日期DOS建议措施风险顺序数RPN 潜在失效起因/机理FMEA编制日期:编制人:现行过程控制措施结果过程功能要求级别潜在失效模式潜在失效后果潜在失效模式及后果分析(PFMEA )驾驶室主线过程责任部门:技质部FMEA编号:关键日期:修订:全尺寸功。
IATF16949质量记录控制程序
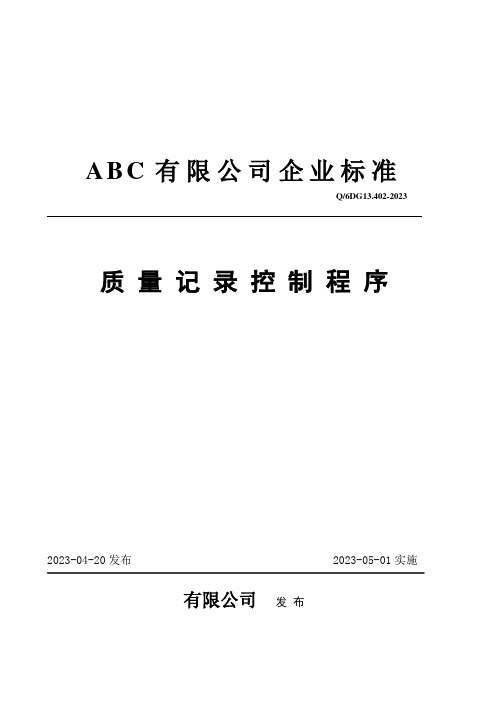
《产品标识和可追溯性程序》
成零件领用单
使用单位
3年
155
工艺路线记录卡
156
配单
159
《顾客财产管理程序》
顾客财产标识卡
使用单位
3年
160
顾客财产管理表
161
外购外协件检验报告单
162
《产品搬运、贮存、包装与防护管理程序》
零组件移交单
使用单位
3年
163
89
供应商和分包商的产品/工艺评定情况(10.3)
90
逻辑流动程序/调节/标签/安全存放(11.1)
91
产品评定/工艺评定计划(12.1)
92
《顾客需求管理程序》
合同订单汇总一览表
经理部和
分厂
3年
93
豫新机械有限公司合同(合同修订)评审表
94
豫新机械有限公司口头订单评审
表
95
《成本核算报价管理程序》
4 术语和定义
质量记录:是指公司按照质量体系文件实施过程的文件化的证据和记录的结果。
日历年:指从一年的1月1日到年底的12月31日共365天
5 职责
各单位负责相关质量记录的标识、收集、编目、归档、贮存、防护、保管、处理和销毁等管理。
6工作流程和内容
工作流程
工作内容说明
使用表单
6.1.表单由各使用单位设计,经质量部核准后编入《程序文件表单集》,按程序文件中的要求选用。
6.5.2各单位按第8条的保存期限要求保管(可参考附件一)。
6.5.3质量记录的防护须注意保管环境(如防火、防水等),避免受潮、损坏、遗失;对于电子媒体的记录应至少备份二份。
《程序文件表单集》
工作流程
汽车线束PFMEA
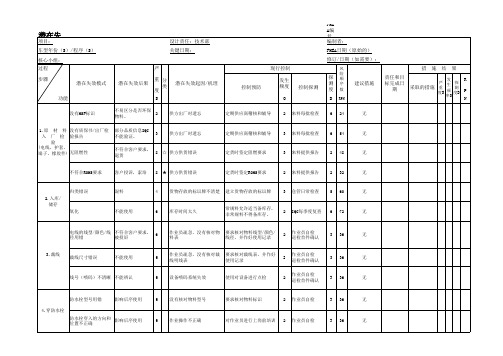
3
105
对刀片进行寿命 管制
6.中间检查 不良件流出 7.热缩 电线烧伤
漏检查 电线漏电
6
过程没流转没有进行管控
填写过程流程卡,检验合 格后才充许流入下道工序
2 每批自检、巡检 6
72
无
6 操作工操作失误
对操作工培训教育
2 检验员首巡检 2 24
无
8.分线 线号分错
影响后序使用
5 没有核对标识
按要求核对标识
货物存放的标识牌不清楚 建立货物存放的标识牌
3 仓管日常检查 5 60
无
6 库存时间太久
常规料允许适当备库存, 非常规料不得备库存。
2 IQC每季度复查
6 72
无
电线的线型/颜色/线 不符合客户要求,
径用错
被投诉
6
作业员疏忽,没有核对物 要求核对物料线型/颜色/
料表
线径,并作好使用记录
2
作业员自检 巡检首件确认
的位置没有调试好
的位置
2
操作工自检,检 验员首巡检
5
60
无
芯线漏出造成漏 电,或接触到别的 6 端子造成短路
拉力不足
6
造成装配不紧密, 不到位,产品容易 6 出现脱落
不能使用
6
压接过程中,电线芯线散 检查外切刀是否损坏,调
乱
节切刀位置
2
操作工自检,检 验员首巡检
7
84
在压线时再脱去 剥头冒
压接过程中,电线芯线散 乱,压接部位由于铜丝 少,间接影响端子拉力。
6 拣货员拣货错误 6 没有做到先进先出 3 封口胶粘性不好 6 装箱单与实物不符
对拣货员培训
2 装货检查
经典的电子产品PFMEA资料
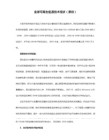
过程责任部门:技术部 编制者: 编制日期: 最新修订日期:
编号:2012-01 潜在的失效模式及后果分析(PFMEA) QR-QP07-62PFMEA
过程责任部门:技术部 编制者: 编制日期: 最新修订日期:
/车辆:CX30 核心小组: 关键日期:
过程 功能 要求 潜在 失效模式 潜在 失效后果 严 重 度 (S) 分 类 潜在失效起因/机理 现行预防 过程控制 频 度 (O) 现行探测 过程控制 探 测 度(D) R P N 建议措施 责任 及目标 完成日期 措 施 结 果 采取 的措施 过程:001进货检验 功能:检查确认供应商提供的物料与进货单一致,保证物料质量可靠 要求:物料规格、型号、数量准确、质量合格 没检 产品合格率未知、影响下道工序 6 检验员操作失误、工作不认真 对检验员进行培训和指导 3 3 54 无 检错 合格品判为不合格品 3 27 漏检 不合格品判为合格品 5 45 检验不及时 影响下到工序、影响生产进度 3 27
/车辆:CX30 核心小组: 关键日期:
过程 功能 要求 潜在 失效模式 潜在 失效后果 严 重 度 (S) 分 类 潜在失效起因/机理 频 度 (O) 现行预防 过程控制 现行探测 过程控制 探 测 度(D) R P N 建议措施 责任 及目标 完成日期 措 施 结 果 采取 的措施 严重度 频度 探测度 R P N. 过程:100 领料 功能:从仓库领取生产所用物料。确保物料规格/型号、数量准确。 要求:确保物料规格/型号、数量准确。 领错料 物料错误,影响下道工序 4 1物料员疏忽 2没有与BOM、更新工程变更通知书(ECN)核对 3 培训教育物料员 至少安排两人进行物料确认、核对BOM和ECN 2 24 无 BOM、ECN描述错误 BOM制作人完成后由工程师核对所有内容 来料实物与料盘标识的描述不符 及时通知进货检验人员更换正确的物料 多领料 浪费资源 2 没有严格按照BOM进行领料 2 培训教育物料员 8 少领料 影响下道工序 4 12
汽车线束DFMEA过程失效模式

8
、护套防水
试验
导线耐电压性能不 达标
耐压不够
8
操作错误
1
检查员缺少技能 供应商质量问题
原材料选用有问 题,匹配可靠度 2
不够
护套防水级别不 够
2
供应商质量问题 1
FMEA编号: 修订: 编制人:
现行过程控制
探测度
风险顺 序数
预防
探测 (D) RPN
3 18 自己检查 3 24
3 18
建议 措施
责任及 目标
频度
现行过程控制
探测度
风险顺 序数
(O) 预防
探测 (D) RPN
2
培训操作 100%自
者
检
1
14
建议 措施
责任及 目标
完成日 期
采取措施
措施结果 (S) (O) (D) RPN
潜在失效模式及后果分析(PFMEA)
项目名称: 产品型号: 车型:驾驶室主线
主要参加人:
过程
功能要求
潜在失效 模式
端子热缩管 绝缘
库和发往客户 户处
数量不准 印字不清 印错标识 包装箱损坏 型号拿错
影响客户装车 6
影响客户产品 7 区分不清
产品丢失
7
影响客户装配
操作失误
1
操作失误
1
搬运操作失误
1
操作者失误
专人装箱 3 18
二次复查
100%自 2
14
提高检质量
意识
操作工自 己控制
3
21
仓库备货 员自检
2
72
16.8.15 100%自检
9
2
2
36
线束DFMEA浅析
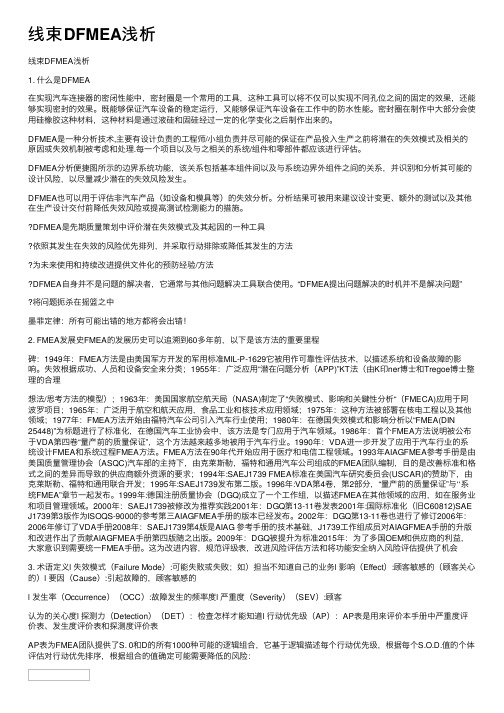
线束DFMEA浅析线束DFMEA浅析1. 什么是DFMEA在实现汽车连接器的密闭性能中,密封圈是⼀个常⽤的⼯具,这种⼯具可以将不仅可以实现不同孔位之间的固定的效果,还能够实现密封的效果。
既能够保证汽车设备的稳定运⾏,⼜能够保证汽车设备在⼯作中的防⽔性能。
密封圈在制作中⼤部分会使⽤硅橡胶这种材料,这种材料是通过液硅和固硅经过⼀定的化学变化之后制作出来的。
DFMEA是⼀种分析技术,主要有设计负责的⼯程师/⼩组负责并尽可能的保证在产品投⼊⽣产之前将潜在的失效模式及相关的原因或失效机制被考虑和处理.每⼀个项⽬以及与之相关的系统/组件和零部件都应该进⾏评估。
DFMEA分析便捷图所⽰的边界系统功能,该关系包括基本组件间以及与系统边界外组件之间的关系,并识别和分析其可能的设计风险,以尽量减少潜在的失效风险发⽣。
DFMEA也可以⽤于评估⾮汽车产品(如设备和模具等)的失效分析。
分析结果可被⽤来建议设计变更、额外的测试以及其他在⽣产设计交付前降低失效风险或提⾼测试检测能⼒的措施。
DFMEA是先期质量策划中评价潜在失效模式及其起因的⼀种⼯具依照其发⽣在失效的风险优先排列,并采取⾏动排除或降低其发⽣的⽅法为未来使⽤和持续改进提供⽂件化的预防经验/⽅法DFMEA⾃⾝并不是问题的解决者,它通常与其他问题解决⼯具联合使⽤。
“DFMEA提出问题解决的时机并不是解决问题”将问题扼杀在摇篮之中墨菲定律:所有可能出错的地⽅都将会出错!2. FMEA发展史FMEA的发展历史可以追溯到60多年前,以下是该⽅法的重要⾥程碑:1949年:FMEA⽅法是由美国军⽅开发的军⽤标准MIL-P-1629它被⽤作可靠性评估技术,以描述系统和设备故障的影响。
失效根据成功、⼈员和设备安全来分类;1955年:⼴泛应⽤“潜在问题分析(APP)”KT法(由K印ner博⼠和Tregoe博⼠整理的合理想法/思考⽅法的模型);1963年:美国国家航空航天局(NASA)制定了“失败模式、影响和关鍵性分析“(FMECA)应⽤于阿波罗项⽬;1965年:⼴泛⽤于航空和航天应⽤,⾷品⼯业和核技术应⽤领域;1975年:这种⽅法被部署在核电⼯程以及其他领域;1977年:FMEA⽅法开始由福特汽车公司引⼊汽车⾏业使⽤;1980年:在德国失效模式和影响分析以“FMEA(DIN 25448)”为标题进⾏了标准化,在德国汽车⼯业协会中,该⽅法是专门应⽤于汽车领域。
FMEA实用培训

实用培训FMEA介绍INTRODUCTION OF THE FMEA设计FMEA的执行EXECUTION OF THE DESGIN FMEA过程FMEA的执行EXECUTION OF THE PROCESS FMEA总结SUMMARY01 FMEA介绍INTRODUCTION OF THE FMEA什么是FMEA?INTRODUCTION OF THE FMEAFMEA(Potential F ailure M ode and E ffects A nalysis)潜在失效模式和后果分析,是在产品设计阶段和过程设计阶段,对构成产品的子系统、零件,对构成过程的各个工序逐一进行分析,找出所有潜在的失效模式,并分析其可能的后果,从而预先采取必要的措施,以提高产品的质量和可靠性的一种系统化的活动。
什么是FMEA?INTRODUCTION OF THE FMEA1. FMEA是一种事前行为,在开发中完成(预防),是一个动态文件。
2. FMEA是可靠性的风险分析方法之一。
3. FMEA是一个风险分析的工具,包括风险评估和风险控制两部分。
4. FMEA与风险评估有关的三个问题:严重度:是评估失效对顾客影响的等级。
发生频度:是指一个失效原因可能的发生频率。
探测度:是评估产品和过程控制对失效原因或失效模式的探测能力。
★ FMEA最显著的成果是将跨职能小组的集体知识文件化。
INTRODUCTION OF THE FMEA1早期概念阶段,用于分析系统和子系统系统FMEA (SFMEA)2产品生产之前,设计阶段,由设计缺陷产生的故障模式设计FMEA (DFMEA)3在生产之前,针对生产和组装过程缺陷的故障模式过程FMEA (PFMEA)4在产品使用之前,对系统或过程产生的缺陷引起的故障模式的分析服务FMEA (SFMEA)5对设备系统、分系统、组件、部件的使用过程的潜在失效模式分析设备FMEA (MFMEA)6监视及系统响应补充FMEA (FMEA-MSR)为了保持系统或产品(如车辆)处于安全状态或法规符合性状态而进行的有关操作(驾驶、保养、维修等)时,而进行的一种诊断探测和失效缓解的分析方法。
LED显示屏 PFMEA
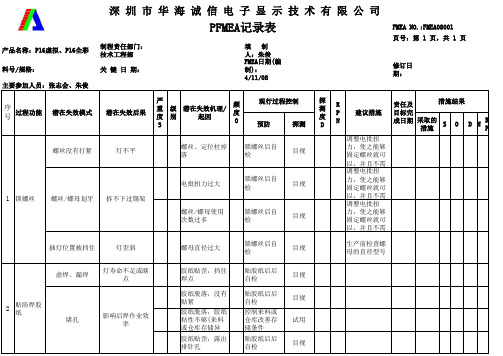
制程责任部门:技术工程部填 制 人:朱俊关 键 日 期:FMEA日期(编制):4/11/08修订日期:预防探测采取的措施S O DR P N螺丝没有打紧灯不平螺丝、定位柱掉落锁螺丝后自检目视调整电批扭力,使之能够固定螺丝就可以,并且不需电批扭力过大锁螺丝后自检目视调整电批扭力,使之能够固定螺丝就可以,并且不需螺丝/螺母使用次数过多锁螺丝后自检目视调整电批扭力,使之能够固定螺丝就可以,并且不需插灯位置被挡住灯歪斜螺母直径过大锁螺丝后自检目视生产前检查螺母的直径型号虚焊、漏焊灯寿命不足或瞎点胶纸贴歪,挡住焊点贴胶纸后后自检目视胶纸脱落,没有贴紧贴胶纸后后自检目视胶纸脱落,胶纸粘性不够(来料或仓库存储异控制来料或仓库改善存储条件试用胶纸贴歪,露出排针孔贴胶纸后后自检目视锁螺丝贴防焊胶纸责任及目标完成日期现行过程控制序号探测度D潜在失效模式12过程功能PFMEA记录表FMEA NO.:FMEA08001深 圳 市 华 海 诚 信 电 子 显 示 技 术 有 限 公 司页号:第 1 页,共 1 页频度O产品名称:P16虚拟、P16全彩措施结果R P N建议措施料号/规格:堵孔螺丝/螺母划牙拆不下过锡架影响后焊作业效率潜在失效后果严重度S级别潜在失效机理/起因8波峰焊13焊灯板13贴焊驱板13插焊驱板13焊驱板。
连接器常用英语汇整
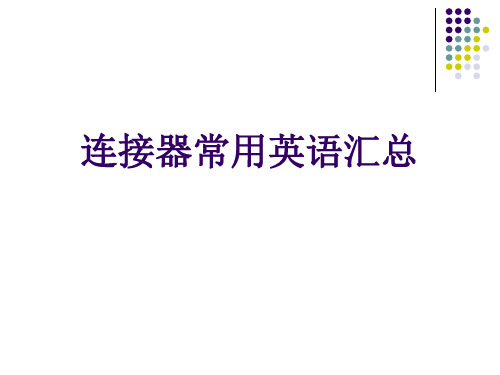
A.连接器 连接器 connector / conn. 卧式类型(也称90度) Right Angle Type (RA) 直立式类型(也称180度) Vertical Type 侧插式(也称侧立式) Flag Type 破板式类型(也称沉板式) Offset Type 穿孔式 DIP Type 表面粘着技术 SMT 母端 Female/ Receptacle 公端 Male/ Plug PCB线路图 PCB Layout 冲压 stamping 成型 molding 组装 assembly 自动机 Auto machine 治具 Fixture/JIG 塑模 mold tooling 冲模 die 电镀 plating 闪镀金 Gold flash(GF) 尺寸 Dimensions 公差 Tolerance 设计失效模式分析 DFMEA 过程失效模式分析 PFMEA
2.连接器测试常用英语 连接器测试常用英语
A.ELECTRICAL 电气要求 Contact Resistance 接触阻抗 Low Level Contact Resistance (LLCR) 低电压接触阻抗 Insulation Resistance 绝缘阻抗 Current Rating 额定电流 Voltage Rating 额定电压 Dielectric strength /Dielectric Withstanding Voltage 耐电压 B.MECHANICAL 机械要求 Insertion & Withdrawal Force / Mating & un-mating force 插入力/拔出力 Normal Force (端子)正向力 Durability 寿命、耐久 Vibration 震动 Mechanical Shock 机械振动 Retention Force (端子)保持力 Solder-ability 沾锡性 C. ENVIRONMENTAL 环境要求 Thermal Shock 冷热冲击 Salt Spray 盐雾 Humidity 耐湿性、恒温恒湿 Solder heat resistance 耐焊性
摄像头 PFMEA

5
40
A003(SMT加 元件贴错、贴反、漏 贴等不良 工)
影响后续生产
5
贴片位置不正确、装 错、装反物料、机器 程序角度错
3
对作业员进行培训、 首件要进行全检、物 料要核对好后上线
3
45
A004(装镜头 图像不正、不清晰、 影响图像效果、功能 不镜像 与要求不一样 、调焦距)
3
镜头装歪、焦距没有 调好、程序不对
严重度数起因机理q1来料检验没有核对好规格尺寸型号等w1物料仓储物料没有放好到指定货架划分区放置并且每个物料要做好物料标识卡a001领料a002程序烧入作业方式不当ic不良程序错乱放置不当写作业流程说明加强来料检验烧写前确认好程序按作业说明放置ic后进行元件贴错贴反漏贴等不良贴片位置不正确装错装反物料机器程序角度对作业员进行培训首件要进行全检物料要核对好后上线a004装镜头调焦距图像不正不清晰不镜影响图像效果功能与要求不一样镜头装歪焦距没有调好程序不对镜头要装到位图像调到最清晰确认好烧录的程序a005加工前盖后盖不防水端子线的护线套破损没有有防水功能易导致短漏装防水圈热风枪温度过高或吹的时间过长加强作业的培训作业前要检查热风枪的温度控制好作业时间a006装配灯板摄像机板焊接温度过高或过低焊定柱破损出现烫伤或焊点不良界面回路功能无法正常工作报废物料焊接方式不当电烙铁温度设定不当电批力度不对作业员进行培训使用恒温洛铁调节电批力度a007合壳前盖与后盖之间松动不防水螺丝漏打或没有打前后盖没有合到位密封胶没有打到位均匀作业员疏忽电批力度过大或打滑对作业员进行培训作业前调节好电批力度a008调试图像不清晰不感红外画面不同步或扭曲端子线接触不良镜头焦距没有装好光敏电阻没有焊好端子线接头处松动镜头焦距要调到位检查好焊点接头处a009老化老化电压过高或过低漏老化会烧掉一些部件易损坏产品无法检出先期老化元件电源供应调整不当作业疏漏加强作业的培训上电前核对好电压a010成品测试图像不清晰色彩度差不感红外画面不同步或扭曲端子线接触不良镜头焦距没有装好老化测试中器件损坏光敏电阻没有焊好端子线接头处松动镜头焦距要调到位检查好焊点接头处a011贴标签标签内容不对标签贴歪漏贴标签标签内容模糊不清来料检验作业员的疏忽加工不良加强来料检验加强作业员培训a012检验包支架松动外壳刮花包装盒破损来料检验作业员的疏忽加工不良加强来料检验加强作业员培训w2成品仓储成品没有归类且没有摆放在指定的区内成品数量不正确仓库员没有归类放好入库前没有清点成品数量加强仓库管理入库前核对成品数量d货物运输运输后产品出现不良货没有按时到达测试检验不到位地址没写清楚加强检验多次做振动自由落体实验rs返修作废漏作标识没有收到不良标签做多个标识标识不完整清晰标识位置不一致维修品没有给到流水线上重新测试检验后工序无法识别状态需重复确认影响维修作业可疑品呗使用不良标签丢失作业员重复
产品喷印pfmea分析范例 (1)
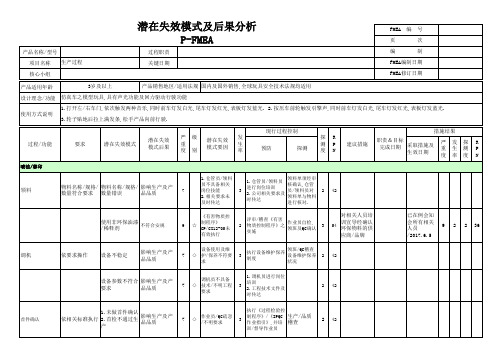
5
5
压力过高
3 调低压力
漆末过滤,有杂 物
3 油漆过滤干净
作业员业自 2 30
检,IPQC巡
检
2 30
5
喷具不洁
3 清洁喷具
2 30
渗色 露底色 泛白
影响生产及产 品品质
5
影响生产及产 品品质
5
5
影响生产及产 品品质
5
5
5
喷叠色时,底漆 末干就喷面漆
3
开油水挥发及干燥 作业员业自
时间控制
检,IPQC巡检
过程职责
关键日期
FMEA 编 号
页
次
编
制
FMEA编制日期
FMEA修订日期
产品适用年龄
3岁及以上
产品销售地区/适用法规 国内及国外销售,全球玩具安全技术法规均适用
设计理念/功能 仿真车之模型玩具,具有声光功能及回力驱动行驶功能
1.打开左/右车门,依次触发两种音乐,同时前车灯发白光,尾车灯发红光,表板灯发蓝光. 2.按压车前轮触发引擎声,同时前车灯发白光,尾车灯发红光,表板灯发蓝光. 使用方式说明
产品名称/型号 项目名称 生产过程 核心小组
潜在失效模式及后果分析 P-FMEA
过程职责
关键日期
FMEA 编 号
页
次
编
制
FMEA编制日期
FMEA修订日期
产品适用年龄
3岁及以上
产品销售地区/适用法规 国内及国外销售,全球玩具安全技术法规均适用
设计理念/功能 仿真车之模型玩具,具有声光功能及回力驱动行驶功能
领料单须经审 核确认,仓管 员/领料员对 领料单与物料 进行核对.
2
42
- 1、下载文档前请自行甄别文档内容的完整性,平台不提供额外的编辑、内容补充、找答案等附加服务。
- 2、"仅部分预览"的文档,不可在线预览部分如存在完整性等问题,可反馈申请退款(可完整预览的文档不适用该条件!)。
- 3、如文档侵犯您的权益,请联系客服反馈,我们会尽快为您处理(人工客服工作时间:9:00-18:30)。
堆码太高
训
检
受压变形
ects Analysis of Process / SQAP-E10-01"
Key date: Original date: Core team: Revision: Develop. / Date: Approval / Date: Current design controls - detection Resp. & Recommended target action(s) comple. date Detection Action results Action(s) taken Sev. Occ. Det. Sev. Occ. Det. RPN RPN RPN 63
品不易装 配,顾客抱 怨 Nonconformity
作不当
训
பைடு நூலகம்
样板比对
The raw material not complied with DBL requirement
3
合
的阻燃性不 符合
原材料不符合 DBL 要求
see inspection and testing report
Horizontal burning machine 水平燃烧箱
Form Sheet "Potential Failure Mode & Effects Analysis o
Part no.: Part name: TRIM RH/LST 、 TRIM/HK 、 TRIM SLIDING DOOR P 、 LH Engin. change level: Supplier code: Supplier name: Manufact. location: Step no. Function / requirement Potential failure mode Potential effect(s) of failure Potential cause(s) / mechanism(s) of failure Equipment 、 the issue of the production process Occurrenc Severity Class.
Difficult to logistical management
2
Error of operator 操
标识 或标识 错误
物流管理困 难
作者操作不当
Pre-service 2 training岗前培
Individual inspection 专
训
检
Go Production odor moldy,wetted is too strong 产 5 5. Warehousing
2.
Stamping
Difficult to Nonconformity assemble with of the appearance product;Custom 5 and dimension er complaints产
Improper operation of worker操作者操
Pre-service 3 training岗前培
Compared with sample
外观尺寸不 符合
Nonconformity of flame of the flame retardant for the 7 retardant 阻燃性不符 product 产品 3. Finished Difficult to quality control Nonconformity assemble with 成品检验 of the product;Custom appearance er complaints产 5 and dimension
Individual inspection专
训
检
2
Error of operator 操
标识 或标识 错误
物流管理困 难
作者操作不当
Pre-service 2 training岗前培
Individual inspection 专
训
检
4.
Packaging 包
装
unidentified or wrong indentified 无
See testing Horizontal burning report 检验报告 machine 水平燃烧仪
Step no.
Function / requirement
Potential failure mode
Current design Current design controls controls - detection - prevention
Key date
Core team
Revision
Develop. / Date
Approval / Date Current design Current design controls controls - detection - prevention
IQC(PP-film) 1.
进货检验 ( PP 膜)
The enviroment fo the storage is bad
2
Individual inspection 专
发霉 受潮
品气味太强
仓储环境太差
Stacking too high Pre-service 3 training岗前培
检
Individual inspection专
仓储
Distortion of Unable to the production install;scrapped 6 under 不易安装 报 pressure 产品 废
Customer complaints 顾
6
Error of operator 操
品数量不符 合 Packaging 包 装 unidentified or
wrong indentified 无
客抱怨
Difficult to logistical management
作者操作不当
Pre-service 2 training岗前培
见检验报告
Improper operation Pre-service of worker操作者操 3 training岗前培
Compared with sample
外观尺寸不 符合
Insufficient quantity of production 产 4.
品不易装 配,顾客抱 怨
作不当
训
样板比对
Flammability too bad (阻
燃性能差)
The flammability of production is 7 unsastification
3
产品阻燃性
Potential effect(s) of failure Severity Class.
供应商设备、工 艺问题
Potential cause(s) / mechanism(s) of failure Occurrence