第六章 金属液态成型(三-砂型铸造)
无损检测教学大纲.
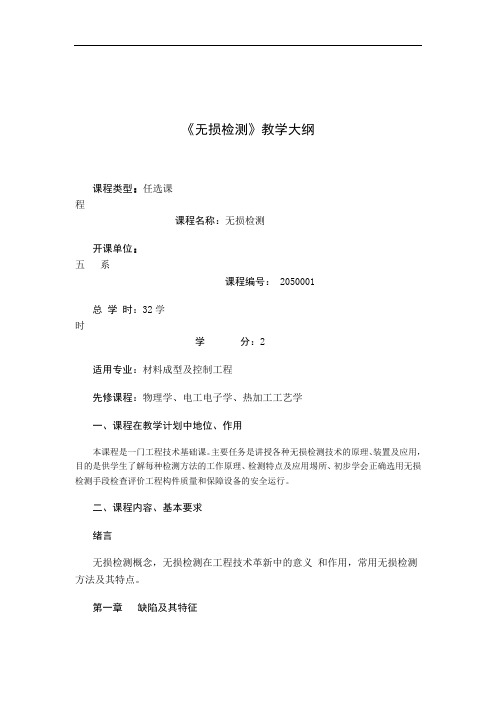
《无损检测》教学大纲课程类型:任选课程课程名称:无损检测开课单位:五系课程编号: 2050001总学时:32学时学分:2适用专业:材料成型及控制工程先修课程:物理学、电工电子学、热加工工艺学一、课程在教学计划中地位、作用本课程是一门工程技术基础课。
主要任务是讲授各种无损检测技术的原理、装置及应用,目的是供学生了解每种检测方法的工作原理、检测特点及应用埸所、初步学会正确选用无损检测手段检查评价工程构件质量和保障设备的安全运行。
二、课程内容、基本要求绪言无损检测概念,无损检测在工程技术革新中的意义和作用,常用无损检测方法及其特点。
第一章缺陷及其特征1.铸造缺陷2.热处理缺陷3.锻造缺陷4.焊接缺陷5.工件服役中形成的缺陷第二章射线探伤1.射线探伤概述2.X—射线的发生及其性质3.X—射线探伤装置简介4.射线照像法5.实时成像法及CT技术简介6.射线的防护与安全第三章超声检测1.超声检测的基础知识2.超声检测装置3.超声探伤方法概述4.缺陷信号的定性分析5.超声探伤的应用例第四章电磁检测1.磁粉及漏磁检测原理2.磁粉检测及其装置3.漏磁检测及其装置4.涡流检测原理5.涡流检测方法简介6.涡流检测装置7.电磁检测的特点及其应用第五章其它检测方法1.渗透检测2.声发射技术3.磁超声检测4.磁巴氏噪声及磁声发射技术三、实验实验一超声波探伤中回波信号的观察与分析实验二涡流检测中缺陷与图形花样的观察与分析四、学时分配《机械制造基础》教学大纲课程类型:技术基础教育课程课程名称:机械制造基础开课单位:五系课程编号:2050101总学时:64学时学分: 4适用专业:机械学科各专业先修课程:机械制图、金工实习一、课程在教学计划中的地位、作用《机械制造基础》是一门研究金属材料及金属制造工艺方法的综合性技术科学。
在高等工业学校中,《机械制造基础》是一门综合性的技术基础课,在教学计划中是机械类各专业必修课程之一。
它的作用是使学生了解常用金属材料的性能,基本掌握金属材料加工工艺的基础知识,为学习其它有关课程及以后从事机械设计和制造方面的工作,奠定必要的金属工艺学的基础。
金属液态成形
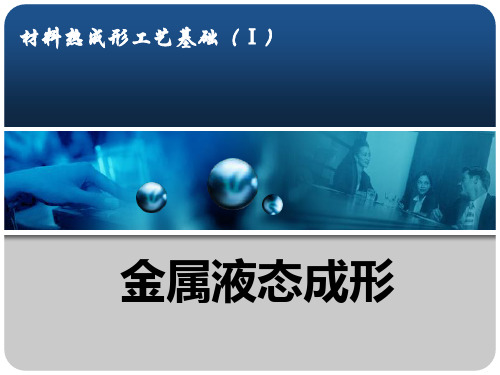
1、液态金属的充型能力
• a、金属的流动性
– 流动性的概念:
• 浇注时液态金属充填铸型 的能力。 • 流动性好,充型能力强, 可得到形状复杂、轮廓清 晰的铸件,缺陷少,补缩 好;流动性差,易于产生 浇不足、冷隔。 • 以浇注螺旋试样的长度来 测定
– 影响流动性的因素
• 1、合金的种类:合金的流动性与合金的熔点、导热系数、 合金液的粘度等物理性能有关。合金的熔点越高,流动性 越差(铸钢);合金的导热性好,流动性也较差(铝合金 )。 • 2、合金的成分:同种合金中,成分不同时,流动性不同。 纯金属和共晶成分的合金,由于是在恒温下进行结晶,液 态合金以逐层凝固的方式从表层逐渐向中心凝固,固液界 面比较光滑,对液态合金的流动阻力较小,同时,共晶成 分合金的凝固温度最低,可获得较大的过热度,推迟了合 金的凝固,故流动性最好。 • 其它成分的合金是在一定温度范围内结晶的,由于初 生树枝状晶体与液体金属两相共存,粗糙的固液界面使合 金的流动阻力加大,合金的流动性大大下降,合金的结晶 温度区间越宽,结晶按糊状凝固方式进行,合金的流动性 越差 。
金属液态成形实例
司母戊大方鼎
藏于国家博物馆的商代晚期(公元前13~前 11世纪)青铜器,通高133cm,口长116cm、 宽79cm,重832.84kg,是迄今发掘出土最大、 最重的青铜礼器
编钟
1978年出土于湖北省随县擂鼓墩1号墓的曾侯乙 编钟,全套65件编钟按大小和音高编成8组悬挂 在3层钟架上,总重量达2500多千克,音律准确, 音色优美,合瓦形的钟可以敲出两个不同的音, 是世界音乐史上的奇迹
常用铸造合金的流动性
合金 铸型 浇注温度 /℃ 螺旋线长度/mm
铸铁:w(C+Si)=6.2%
w(C+Si)=5.9% w(C+Si)=5.2% w(C+Si)=4.2% 铸钢:w(C)=0.4% 砂型 砂型
金属液态成形工艺概述

铸造产品称为: 铸件、铸锭、铸坯、铸带等
一、金属液态成形工艺特点
1. 适应性强
铸件重量:几克 ~ 几百吨 铸件壁厚:0.5 毫米 ~ 1 米 铸件长度:几毫米 ~ 十几米 铸件材质:铁碳合金(鋳铁、鋳钢)、铝合金、铜合金、
镁合金、锌合金、钛合金、复合材料等
速箱体(灰口铸铁)
精密铸造件(不锈钢)
水轮机铸件(铜合金)
箱体(铝合金)
叶轮(钛合金)
一、金属液态成形工艺特点
1. 适应性强
铸件重量:几克 ~ 几百吨 铸件壁厚:0.5 毫米 ~ 1 米 铸件长度:几毫米 ~ 十几米 铸件材质:铁碳合金(鋳铁、鋳钢)、铝合金、铜合金、
镁合金、锌合金、钛合金、复合材料等
铸造方法几乎不受零件大小、形状和结构复杂程度的限制。
轧辊
异型件
装饰件
工艺品
一、金属液态成形工艺特点
2. 尺寸精度高
铸件比锻件、焊接件的尺寸精度高,更接近于零件的尺 寸,可节约大量的金属材料和机械加工工时。
一、金属液态成形工艺特点
2. 尺寸精度高
铸件比锻件、焊接件的尺寸精度高,更接近于零件的尺 寸,可节约大量的金属材料和机械加工工时。
形成的先进铸造技术
精密、优质化
精密成形与加工 近无缺陷成形
数字、网络化
数字造型 虚拟制造
网络制造
精确铸造成形 金属熔体的纯净化、致密化
铸造工艺CAD,铸造模具CAD/CAM一体化 铸造过程宏观模拟及工艺优化 铸件组织微观模拟及性能预测 分散网络化铸造系统
高效、智能化
快速制造 自动化制造系统
智能制造
快速原形及快速制模 铸造过程自动检测与控制,铸造机器人的应用
金属铸造工艺详解

金属铸造工艺详解液态金属浇注到与零件形状、尺寸相适应的铸型型腔中,待其冷却凝固,以获得毛坯或零件的生产方法,通常称为金属液态成形或铸造。
工艺流程:液体金属→充型→凝固收缩→铸件工艺特点:1、可生产形状任意复杂的制件,特别是内腔形状复杂的制件。
2、适应性强,合金种类不受限制,铸件大小几乎不受限制。
3、材料来源广,废品可重熔,设备投资低。
4、废品率高、表面质量较低、劳动条件差。
铸造分类:(1)砂型铸造(sand casting)砂型铸造:在砂型中生产铸件的铸造方法。
钢、铁和大多数有色合金铸件都可用砂型铸造方法获得。
工艺流程:砂型铸造工艺流程技术特点:1、适合于制成形状复杂,特别是具有复杂内腔的毛坯;2、适应性广,成本低;3、对于某些塑性很差的材料,如铸铁等,砂型铸造是制造其零件或,毛坯的唯一的成形工艺。
应用:汽车的发动机气缸体、气缸盖、曲轴等铸件(2)熔模铸造(investmentcasting)熔模铸造:通常是指在易熔材料制成模样,在模样表面包覆若干层耐火材料制成型壳,再将模样熔化排出型壳,从而获得无分型面的铸型,经高温焙烧后即可填砂浇注的铸造方案。
常称为“失蜡铸造”。
工艺流程:熔模铸造工艺流程工艺特点优点:1、尺寸精度和几何精度高;2、表面粗糙度高;3、能够铸造外型复杂的铸件,且铸造的合金不受限制。
缺点:工序繁杂,费用较高应用:适用于生产形状复杂、精度要求高、或很难进行其它加工的小型零件,如涡轮发动机的叶片等。
(3)压力铸造(die casting)压铸:是利用高压将金属液高速压入一精密金属模具型腔内,金属液在压力作用下冷却凝固而形成铸件。
工艺流程:工艺特点优点:1、压铸时金属液体承受压力高,流速快2、产品质量好,尺寸稳定,互换性好;3、生产效率高,压铸模使用次数多;4、适合大批大量生产,经济效益好。
缺点:1、铸件容易产生细小的气孔和缩松。
2、压铸件塑性低,不宜在冲击载荷及有震动的情况下工作;3、高熔点合金压铸时,铸型寿命低,影响压铸生产的扩大。
第六章 金属液态成型(三-砂型铸造)
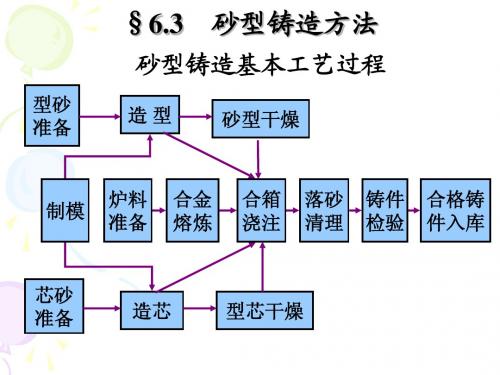
备和验收的最基本的工艺文件。 备和验收的最基本的工艺文件。图纸上需 要表示出铸型分型面、浇注系统、 要表示出铸型分型面、浇注系统、型芯结 构尺寸、铸件加工余量、 构尺寸、铸件加工余量、控制凝固措施等 内容。 内容。
圆锥齿轮的零件图, 圆锥齿轮的零件图,铸造工艺图及模样图
1.浇注位置的选择 1.浇注位置的选择
(2)最小铸孔尺寸
灰口铸铁的最小铸孔尺寸 ( mm) 名 称 最小铸孔尺寸(mm) 最小铸孔尺寸 Ф 30~50 ~ Ф 15~30 ~ Ф 12~15 ~
单件、 单件、小批量生产 成批量生产 大量生产
(3)铸造收缩率( K ) L 模样 – L 铸件 K= L 模样
铸件在凝固过程中, 它的各部分尺寸一般都 要缩小, 铸件尺寸缩小 的百分率, 叫做铸造线 收缩率或铸造收缩率。
(a)垂直安置 垂直安置 (b)水平安置 水平安置
型 芯 的 各 种 形 式
型芯撑的应用示意图
5.浇注系统、 5.浇注系统、冒口和冷铁的设计 浇注系统
浇注系统: 浇注系统:是 引导液态金属 进入铸型的一 系列通道的总 称。
浇注系统示意图
冒口的设置
冷铁的设置
灰口铸铁的机械加工余量 灰口铸铁的机械加工余量 ( mm )
铸件最大 浇注时 加工面与基准面的距离 ( mm ) 尺寸( mm ) 位置 尺寸( <50 50~120 ~ 120~260 ~ ~ ~ 顶 面 3.5~4.5 4.0~4.5 <120 ~ ~ 底、侧 2.5~3.5 3.0~3.5 5.0~5.5 ~ ~ ~ 顶 面 4.0~5.0 4.5~5.0 120~260 ~ 4.0~4.5 ~ ~ ~ 底、侧 3.0~4.0 3.5~4.0 6.0~7.0 ~ ~ ~ 顶 面 4.5~6.0 5.0~6.0 260~500 ~ 4.5~5.0 ~ ~ ~ 底、侧 3.5~4.5 4.0~4.5
06 BA 金属液态成形

充型能力——液体金属充满铸型型腔,获得尺 寸精确、轮廓清晰的成形件的能力。
充型能力不足的缺陷:浇不足、冷隔、夹渣、气孔等。 影响因数:
一、液态合金的流动性
合金的流动性是: 液态合金本身的流动能力。
流动性测定试样 浇口杯 出气口
合金流动性主要由合金结晶特点决定
温度(℃) 300 200 100 0 流动性(cm) 80 60 40 20 0
二零厂
汽车覆盖件冲模、阀类大型 铸件,铝合金发动机齿轮室、 进出气管。 自硬砂消失模造型;低压铸 造机及重力铸造机;
熔化炉:大件用冲天炉、小铸 铁件及铝合金件用感应电炉;
主要产品
精密铸造厂
变速箱拨叉、管接头、门绞链、拖钩等汽车碳素钢及部
分耐热钢和不锈钢铸件。
东风有色铸件有限公司 概况
压铸件生产面积 10000 平方米,压铸机 58 余台 ( 1600 吨~ 63 吨),铸锭机 2 台,熔炼炉 13 台。 生产能力按铝当量计约 9000 吨 / 年,现生产铜、
第二章 常用液态成形合金及其熔炼
§2-1 铸铁件生产
铸铁是含碳量大于2.11%(通常为2.5%-4.0%)的铁碳合金。
依碳在铸铁中存在形式,铸铁可分为:
1.白口铸铁:C以Fe3C的形式存在,断口呈银色。 白口铸铁有良好耐磨性,用来制造一些耐磨件,如轧辊等。
2.灰口铸铁:C大部或全部以石墨形式存在,断口呈暗灰色。
铸件缩孔或缩松的原因。 铸件产生应力、变形、 裂纹原因。
线收缩率: L
2. 缩孔与缩松
液体金属冷凝时,液态收缩和凝固收缩所缩减的容积 得不到补充,在铸件最后凝固的部位形成一些孔洞 。大而 集中的为缩孔,细小而分散的为缩松。
1)缩孔和缩松的形成
液态金属成型

液态金属成型金属液态成型论文作者:刘永星摘要:金属液态成型又称为铸造,是将液态金属在重力或外力作用下充填到型腔中,待其冷却凝固后,获得所需形状和尺寸的毛坯或零件,即铸件的方法,它是成形毛坯或机器零件的重要方法之一。
工程材料除切削加工以外有各种成型方法,包括金属液态成型、金属塑性成形、材料连接成型、粉末冶金成型以及塑料、橡胶、陶瓷等非金属材料成型及复合材料成型等。
材料成型技术主要讲述金属材料成型和非金属材料成型,现对金属液态成型进行详细论述。
关键词:金属液态成型、成型方法、生产流程、成型原理、选择成型依据一、金属液态成形金属材料在液态下成形,具有很多优点:(1)最适合铸造形状复杂、特别是复杂内腔的铸件。
(2)适应性广,工艺灵活性大。
(3)成本较低。
但液态成形也有很多不足,如铸态组织疏松、晶粒粗大,铸件内部常有缩孔、缩松、气孔等缺陷产生,导致铸件力学性能、特别是冲击性能低于塑形成行件;铸件涉及的工序很多,不易精确控制,铸件质量不稳定;由于目前仍以砂型铸造为主,自动化程度还不够高,工作环境较差;大多数铸件只是毛坯件,需经过切削加工才能成为零件。
砂型铸造是将熔融金属浇入砂质铸型中,待凝固冷却后,将铸型破坏,取出铸件的铸造方法,是应用最为广泛的传统铸造方法,它适用于各种形状、大小及各种常用合金铸件的生产。
砂型铸造的工艺过程称为造型。
造型是砂型铸造最基本的工序,通常分为手工造型和机器造型两大类。
手工造型时,填砂、紧实和起模都用手工和手动完成。
其优点是操作灵活、适应性强、工艺装备简单、生产准备时间短。
但生产效率低、劳动强度大、铸件质量不易保证。
故手工造型只适用于单件、小批量生产。
机器造型生产率很高,是手工造型的数十倍,制造出的铸件尺寸精度高、表面粗糙度小、加工余量小,同时工人劳动条件大为改善。
但机器造型需要造型机、模板以及特质砂箱等专用机器设备,一次性投资大,生产准备时间长,故适用于成批大量生产,且以中、小型铸件为主。
铸造工艺基础知识及理论

4
铸造材料
1
工艺基础 工艺性能
2
铸件生产
铸造工艺
3 工艺方法
1. 金属液态成形(铸造)工艺基础
什么是金属的液态成形:
将熔炼好的液态金属浇入与零件形 状相适应的铸型空腔中,待其冷却凝固, 以获得毛坯或零件的工艺方法,亦称铸造.
金属的液态成形的方法:
金属的液态成形是制造毛坯、零件的重要方法之一。按铸型材 料的不同,金属液态成形可分为砂型铸造和特种铸造(包括压力铸 造、金属型铸造等).其中砂型铸造是最基本的液态成形方法,所生 产的铸件要占铸件总量的80%以上.特种铸造较适用于大批量生产, 应用范围逐渐增加。
松
的 方
方法
合理布置内浇道及确定浇铸工艺。
法
合理应用冒口、冷铁和补贴等工艺措施。
3. 铸件的生产工艺
整模造型
分模造型
手工造型
砂型铸造
活块造型 三箱造型
液
挖砂造型
态
机器造型
刮板造型
成
铸造工艺图的绘制
型
砂型铸造的工艺设计
分型面的选择
工
工艺参数的确定 浇注位置的确定
艺
金属型铸造
熔模铸造
压力铸造
特种铸造
低压铸造 陶瓷型铸造
内是由表及里的逐层凝固。在凝固过程中,如得不到合金液的 补充,在铸件最后凝固的地方就会产生缩孔.
2. 铸件的生产—缩松的形成 缩松的形成原因:
铸件最后凝固的收缩未能得到补充,或者结晶温度范围宽的 合金呈糊状凝固,凝固区域较宽,液、固两相共存,树枝晶发 达,枝晶骨架将合金液分割开的小液体区难以得到补缩所致。
合金的收缩的过程:
合金从液态冷却至室温的过程中,其体积或尺寸缩减的 现象。合金的收缩给液态成形工艺带来许多困难,会造成许 多铸造缺陷。(如:缩孔、缩松、裂纹、变形等)。
液态成形铸造

液态成形——铸造
(三)填充压力
增大填充压力,可以使液态金属充型能力增强。
(四)铸型导热能力
铸型导热能力越差,液态金属处于高温下的时间越长, 有利于液态金属的流动和充型。
(五)铸型阻力
铸型型腔狭窄、形状复杂或铸型材料的发气量大,型腔内气 体量就显著增加,如果铸型排气又不通畅,则造成铸型内 气体反压力增大,导致铸型对金属液流动阻力增加,从而 降低合金流动性。
第五章
液态成型(铸造)
液态成形——铸造
教学目的与要求:
1.了解铸造的基本பைடு நூலகம்理。 2.掌握常用铸造方法的主要工艺过程、特点及应用条件。
教学内容:
1.铸造成形的基本原理。
2.各种常用铸造方法。 3.各种常用铸造方法的综合比较。
重点:常用铸造方法的工艺特点及应用条件。 难点:铸造的基本原理。
液态成形——铸造
线收缩率:
• 合金的固态收缩,直观地表现为铸件轮廓尺寸的减小, 因而常用铸件单位长度上的收缩量,即线收缩率来表示,是 铸件产生内应力、变形和裂纹的基本原因。
液态成形——铸造
(二)影响合金收缩的因素
1. 化学成分
2. 浇注温度
3. 铸件结构和铸型条件
液态成形——铸造
(三)铸件中的缩孔与缩松
⑴ 缩孔的形成
加大结晶压力液态成形铸造型砂模型熔化砂型铸造的工艺过程砂型铸造动画演示过程一砂型铸造第二节重力作用下的液态成形工艺方法液态成形铸造液态成形铸造常见的砂型铸造方法演示1整模造型2分模造型3三箱造型4挖砂造型5活块造型6机器造型液态成形铸造返回液态成形铸造返回液态成形铸造返回液态成形铸造返回液态成形铸造返回液态成形铸造返回液态成形铸造1概念液态金属在重力作用下注入金属型中成形的方法称为金属型铸造习惯上亦称之为硬模铸造
液态成形(砂型铸造)

22
Ch1 金属液态成形
二、砂型铸造工艺设计
§2 砂型铸造
(一)浇注位置的选择
2.铸件的大平面应朝下
型腔的上表面除了容易产生砂眼、气孔、夹渣等 缺陷外,大平面还常容易产生夹砂缺陷。因此,对平 板、圆盘类铸件的大平面应朝下。
2023/12/14
23
Ch1 金属液态成形
二、砂型铸造工艺设计
§2 砂型铸造
2023/12/14
11
Ch1 金属液态成形
§2 砂型铸造
一、砂型铸造造型(造芯)方法
(二)机器造型 大批量生产,劳动生产率高,劳动条件好,铸件尺
寸精度高、表面质量好,加工余量小。
2023/12/14
12
Ch1 金属液态成形
§2 砂型铸造
一、砂型铸造造型(造芯)方法 (二)机器造型 1.紧砂方法
自硬砂型
经过烘干的高粘土含量 铸型强度和透气性较高,发气量小,故铸造 单件、小批生产品质要求较
(粘土质量分数为12 缺陷较少;但生产周期长,设备投资较大、 高,结构复杂的中、大型铸
%~14%)的砂型
能耗较高,且难于实现机械化与自动化
件
浇注前用适当方法将型
兼有湿砂型和干砂型的优点
单件、小批生产中、大型铝
2023/12/14
37
Ch1 金属液态成形
图1-27 起模斜度
§2 砂型铸造
2023/12/14
38
Ch1 金属液态成形
§2 砂型铸造
二、砂型铸造工艺设计
(三)工艺参数的确定
3.收缩率
铸件冷却后的尺寸比型腔尺寸略为缩小,为保证铸件 的应有尺寸,模样尺寸必须比铸件放大一个该合金的收
缩率。铸造收缩率K:
液态金属加工中的砂型铸造技术

液态金属加工中的砂型铸造技术是一种传统的铸造方法,它通过使用砂作为模具来制造各种形状的铸件。
砂型铸造技术具有许多优点,如成本低、生产效率高、适应性广等,因此在许多行业中得到了广泛应用。
首先,砂型铸造技术可以制造出复杂的铸件。
由于砂型是由砂粒粘合而成,因此可以根据设计要求制作出各种形状的模具,从而制造出各种复杂的铸件。
这使得砂型铸造技术在许多领域中具有广泛的应用,如机械、汽车、航空航天、电子等。
其次,砂型铸造技术具有较高的生产效率。
与其他的铸造方法相比,砂型铸造技术不需要使用昂贵的模具材料,也不需要复杂的工艺过程。
因此,砂型铸造技术可以大大缩短生产周期,提高生产效率。
此外,砂型铸造技术还具有较高的适应性,可以在不同的生产条件下进行生产,从而满足不同客户的需求。
然而,液态金属加工中的砂型铸造技术也存在一些缺点。
首先,砂型铸造技术的生产成本相对较高,需要使用大量的砂粒和粘合剂等材料。
其次,砂型铸造技术的铸件质量受到砂粒的均匀性和粘合剂的质量等因素的影响,因此需要严格控制生产过程。
此外,砂型铸造技术对环境也有一定的影响,需要采取相应的环保措施。
为了解决这些问题,一些新的技术和方法正在被开发和应用。
例如,使用新型的模具材料和工艺方法可以提高铸件的质量和生产效率。
此外,数字化技术和智能化技术的应用也可以提高砂型铸造技术的自动化和智能化水平,从而提高生产效率和降低成本。
综上所述,液态金属加工中的砂型铸造技术是一种传统的铸造方法,具有许多优点和缺点。
为了提高生产效率和降低成本,我们需要不断探索新的技术和方法,以提高铸件质量和降低环境影响。
同时,我们也应该意识到砂型铸造技术在许多行业中仍然具有广泛的应用前景。
金属液态砂型成形工艺知到章节答案智慧树2023年南昌航空大学

金属液态砂型成形工艺知到章节测试答案智慧树2023年最新南昌航空大学绪论单元测试1.铸造的本质是为了获得铸件,首先必须熔配出符合化学成分要求的液态金属(具有流动性),然后将液态金属注入铸型之中,使其在铸型中凝固、冷却,形成铸件。
()参考答案:对2.铸造的特点(优点、缺点)有()参考答案:适应范围广;尺寸均一性差、内部质量不如锻件等不足;成本低廉;尺寸精度较高3.按形成铸型的方法分,分为____,____和____。
参考答案:null第一章测试1.普通型砂主要原砂、()和水等按一定比例混制成。
参考答案:2.粘土中哪种形式的水与粘土质点的结合力最强()参考答案:矿物组成水3.产生化学粘砂的先决条件是金属表面的()参考答案:氧化4.形成侵入气孔的条件()参考答案:P气>P阻+P静+P型5.金属与铸型的相互作用有()参考答案:机械作用;化学和物理化学作用;热作用6.铸型内由于湿分迁移形成哪几个区()参考答案:;水分饱和凝聚区;正常区;水分不饱和凝聚区7.以下哪些伴生现象是由金属与铸型相互的热作用产生的()。
参考答案:型腔表面层的水分迁移;型壁强度发生变化;石英砂发生同质异构转变8.铸型中由于湿分迁移,产生的干燥区的特点有()参考答案:水蒸气压高;水分少;强度高;温度高9.铸型中由于湿分迁移,产生的水分饱和凝聚区的特点有()参考答案:湿分高;强度低;透气性低10.金属液的浇注温度越高,流动性越好,对铸型表面的冲刷作用越弱。
()参考答案:错11.水分饱和凝聚区与水分不饱和凝聚区的界面,称为蒸发界面。
()参考答案:错12.β石英向α石英转变时,体积膨胀率较小,仅为0.82%,所以对铸件影响不大。
()参考答案:错13.化学粘砂层的厚度越厚,越难清除。
()参考答案:错14.选用SiO2含量少的原砂,有利于防止夹砂缺陷的产生。
()参考答案:对15.湿分迁移是指铸型中水分和水蒸气从型腔表面层向铸型内部迁移的现象。
()参考答案:对16.根据砂层粘结在铸件表面的粘结物质的性质,粘砂可分为____和____。
液压 第六章 金属的液态成型
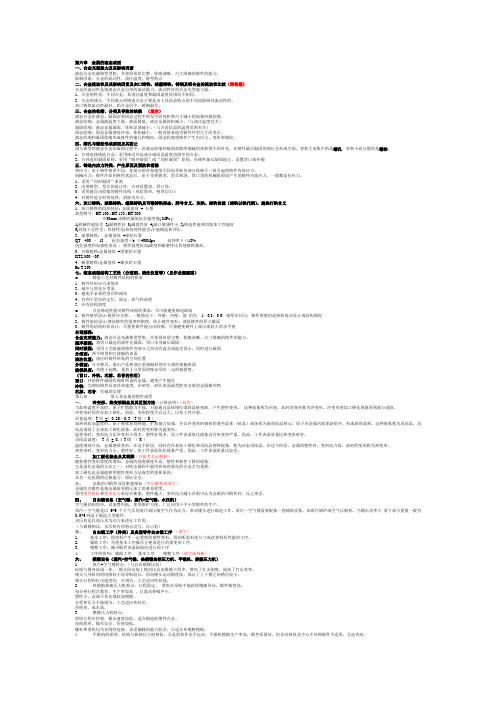
一、合金充型能力及其影响因素液态合金充满铸型型腔,并获得形状完整、轮廓清晰、尺寸准确的铸件的能力。
影响因素:合金的流动性、浇注温度、铸型特点二、合金流动性及其影响因素及灰口铸铁、球墨铸铁、铸钢及铝合金的流动性比较(简答题)合金的流动性是指液态合金自身的流动能力,流动性好的合金充型能力强。
1、合金的种类,不同合金,其浇注温度和凝固温度范围均不相同。
2、合金的成分,不同成分的铸造合金主要是由于其结晶特点的不同而影响其流动性的。
灰口铸铁流动性最好,铝合金居中,铸钢最差。
三、合金的收缩、分类及导致的缺陷(填空)液态合金在液态、凝固态和固态过程中所发生的体积和尺寸减小的现象叫做收缩。
液态收缩:金属液温度下降,液面降低,液态金属体积减小。
(与浇注温度有关)凝固收缩:液态金属凝固,体积显著减小。
(与合金结晶的温度范围有关)固态收缩:固态金属继续冷却,体积减小。
一般直接表现为铸件外型尺寸的变小。
液态收缩和凝固收缩形成铸件的缩孔和缩松,固态收缩使铸件产生内应力、变形和裂纹。
四、缩孔与缩松形成原因及其防止浇入铸型的液态合金在凝固过程中,若液态收缩和凝固收缩所缩减的体积得不到补充,在铸件最后凝固的部位会形成空洞,容积大而集中的是缩孔,容积小而分散的是缩松。
1、合理选择铸造合金。
采用接近共晶成分或结晶温度范围窄的合金。
2、合理选用凝固原则。
采用“顺序凝固”或“同时凝固”原则,在铸件最后凝固地方,设置冒口来补缩五、铸造内应力种类、产生原因及预防和消除热应力:由于铸件壁厚不均,各部分的冷却速度不同而导致各部分收缩不一致引起的铸件内部应力。
机械应力:铸件冷却到弹性状态后,由于受到铸型、型芯和浇、冒口等的机械阻碍而产生的铸件内部应力。
一般都是拉应力。
1、采用“同时凝固”原则2、改善铸型、型芯的退让性,合理设置浇、冒口等;3、采用能自由收缩的铸件结构(形状简单,壁厚均匀);4、对铸件进行时效处理,消除内应力。
六、灰口铸铁、球墨铸铁、蠕墨铸铁及可锻铸铁形态、牌号含义,灰铁、球铁性能(球铁以铁代钢),趁热打铁含义1、灰口铸铁的组织特征: 金属基体+ 石墨典型牌号:HT 100 ; HT 150 ; HT 200Φ30mm试棒的最低抗拉强度值( MPa )1)机械性能较差2)耐磨性好3)减震性好4)缺口敏感性小5)铸造性能和切削加工性能好6)其他工艺性差:焊接性差;热处理性能差;不能锻造和冲压。
液态金属成型

越大,充型能力越差。
(三)铸型充填条件
1. 铸型的蓄热系数 铸型的蓄热系数表示铸型从其中的 金属吸取热量并储存在本身的能力。
液态金属成型的工艺基础
2.铸型温度 铸型温度越高,液态金属与铸型的温差
越小,充型能力越强。 3.铸型中的气体 铸型有一定的发气能力,能在金属液与 铸型之间形成气膜,可减小流动的摩擦阻力,有利于充型。
充型能力——液体金属充满铸型型腔,获得尺寸精确、 轮廓清晰的成形件的能力。
充型能力不足时,会产生浇不足、冷隔、夹渣、气孔等缺陷。
(一)液态合金的流动性
合金的流动性是: 液态合金本身的流动能力。
液态金属成型的工艺基础
浇口杯
出气口
0.45%C 铸钢: 200mm 4.3%C 铸铁: 1800mm
液态金属成型的工艺基础
压力铸造
熔模铸造
熔模铸造就是在蜡模(也可用树脂模)表 面涂覆多层耐火材料,待硬化干燥后,加热 将蜡模熔化,而获得具有与蜡模形状相应形 状的型壳,再经焙烧之后进行浇注而获得铸 件的一种方法,故又称为失蜡铸造(Lost Wax Casting)。
熔模铸造
熔模铸造工艺流程
熔模铸造
离心铸造
离心铸造是将液体金属浇入旋转的铸型中,在离 心力的作用下,完成金属液的充填和凝固成形的一种 铸造方法。离心铸造必须在专门的设备—离心铸造机 (使铸型旋转的机器)上完成。根据铸型旋转轴在空 间位置的不同,离心铸造机可分为卧式离心铸造机和 立式离心铸造机两种。
(四)铸件结构
(1)折算厚度 折算厚度也叫当量厚度或模数,为铸件体积 与 表面积之比 。 折算厚 度大 , 热 量散失慢 ,充型能 力就 好。铸件壁厚相同时,垂直壁比水平壁更容易充填。 (2)铸件复杂程度 铸件结构复杂,流动阻力大,铸型的 充填就困难。
第六章 金属液态成型(理论基础)
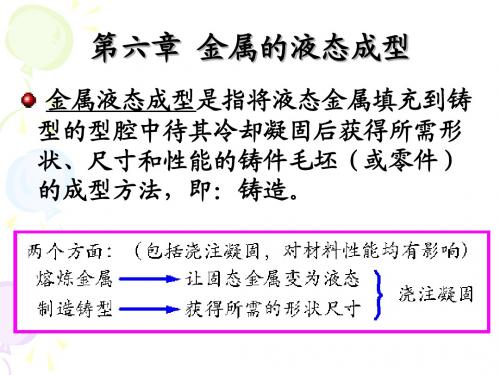
中间凝固:多数合金的凝固介于两者之间,为 中间凝固方式。
三种凝固方式示意图
铸件质量与其凝固方式密切相关。一般,逐层凝
固时,合金的充型能力强,便于防止缩孔和缩松;糊
状凝固,则难以获得结晶紧密的铸件。
影响凝固方式的因素
合金的结晶温度范围 合金的结晶温度范围愈小, 凝固区愈窄,愈倾向于逐层凝 固;反之,则倾向于糊状凝固。 铸件的温度梯度 当合金成分已确定,凝固 区的宽窄,取决于其内外层的 温度梯度。铸件的温度梯度愈 大,凝固区愈窄,愈倾向于逐 层凝固。铸件的温度梯度愈小, 凝固区愈宽,愈倾向于糊状凝 固。
退让性;内浇口设置应符合“同时凝固”原则; 减少硫含量等。
冷裂
产生:在较低的温度下,由于热应力和机械应 力的综合作用,使铸件的应力大于金属的强度 极限而产生冷裂。冷裂往往出现在铸件受拉应 力的部位,尤其是应力集中处。
防止:尽量减小铸造内应力;降低材料的脆性, 主要是减少S、P 的含量。
Hale Waihona Puke 四. 合金的偏析和吸气性形来减小内应力,逐渐趋于稳定。
防止铸件变形的方法:
*尽量减少铸件内应力; *使铸件结构对称,内应力互相平衡而不易变形; *采用反变形法以补偿铸件变形; *在铸件上设置拉筋来承受一部分应力,待铸件经热 处理后再去掉。
铸件的裂纹
热裂
产生:凝固末期,金属的强度和塑性都很低,若 铸件收缩受阻产生的很小应力也能超过该温度 下金属的强度,即发生热裂。热裂分布在应力 集中部位或热节处。 防止:采用合理的铸件结构;改善铸型、型芯的
2.影响合金收缩的因素
(1)化学成分
不同种类的合金,收缩率不同;同类合金,
化学成分不同,收缩率也不同。
C、Si:强烈促进铸铁石墨化,铸铁体收缩减
金属的液态成形
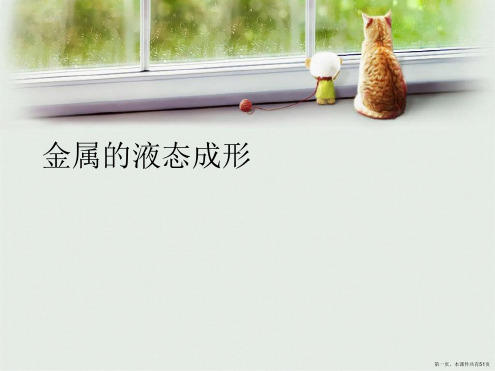
第三十七页,本课件共有51页
4.铸造应力-热应力
室温下: 先冷受压
后冷受拉
第三十八页,本课件共有51页
第三类缺陷:变形、裂纹
除了正常收缩变形
铸件外形不规则变形 外形破坏:裂纹
成因
铸件不均匀的内应力
热应力 机械应力
铸件强度降低
第三十九页,本课件共有51页
防止铸造应力:同时凝固
同时凝固
第四十五页,本课件共有51页
第四类缺陷:气孔
来源:
空气,炉料或铸型所带 的气体、铁锈、油渍、 煤粉、木屑和水分等有 机物
气孔种类:
析出性气孔 侵入性气孔 反应性气孔
第四十六页,本课件共有51页
小结:共晶铸铁
共晶成分铸铁具有优良的铸造性能
恒温下结晶(1148°C)-结晶温度范围为0
铸造缺陷导致铸件报废
铸件表面胀起及热裂纹
铸件内部大量气孔
晶间腐蚀
冷裂纹 、冷隔裂纹
第八页,本课件共有51页
古钱币-咸丰通宝背拾文雕母钱
第九页,本课件共有51页
古钱币 -宣统通宝宫钱背天下太平阔缘
第十页,本课件共有51页
古钱币-顺治连水治母钱
第十一页,本课件共有51页
常见铸造缺陷
析出气孔 多肉
铸型排气能力
铸型的排气能力影响型腔气压
浇注条件
浇注温度
温度高,保持流动的时间长(浇注温度)
充型压力
压力高有利于充型
▪ 压力铸造、低压铸造、离心铸造
铸件结构条件
铸件大小
铸件壁厚(壁厚)
第二十一页,本课件共有51页
合金流动性实验
液态金属的充型 能力
合金的流动性
第二十二页,本课件共有51页
- 1、下载文档前请自行甄别文档内容的完整性,平台不提供额外的编辑、内容补充、找答案等附加服务。
- 2、"仅部分预览"的文档,不可在线预览部分如存在完整性等问题,可反馈申请退款(可完整预览的文档不适用该条件!)。
- 3、如文档侵犯您的权益,请联系客服反馈,我们会尽快为您处理(人工客服工作时间:9:00-18:30)。
铸件 铸件 铸件
(1) 铸件的重要工作面、主要的加 工面应朝下或侧立放置
床身
锥齿轮
吊车卷筒
(2)铸件的大平面应朝下放置。
(3)应将铸件薄而大的平面放在下部、 侧面或倾斜位置。
(4)应将铸件的厚大部分放在上部或 侧面
(5)确定浇注位置时应尽量减少型芯 的数量, 要有利于型芯的安装、 固定、检查和排气
2.铸型分型面的选择
铸型分型面:是指两半铸型相互接触的 表面。
(1)分型面应选在铸件的最大截面上
(2)分型面应尽量选用平面
(3)应尽量减少分型面的数目
(4)分型面的选择应尽量减少型芯 及活块的数量
(5)尽可能使铸件的全部或大部分、或者 加工基准面与重要的加工面处于同一半型内
(6)应尽量使型腔及主要型芯位于下箱
3.工艺参数的确定Байду номын сангаас
(1)机械加工余量
灰口铸铁的机械加工余量 ( mm )
铸件最大 浇注时 加工面与基准面的距离 ( mm ) 尺寸( mm ) 位置 <50 50~120 120~260 顶 面 3.5~4.5 4.0~4.5 <120 底、侧 2.5~3.5 3.0~3.5 5.0~5.5 顶 面 4.0~5.0 4.5~5.0 120~260 4.0~4.5 底、侧 3.0~4.0 3.5~4.0 6.0~7.0 顶 面 4.5~6.0 5.0~6.0 260~500 4.5~5.0 底、侧 3.5~4.5 4.0~4.5
K=
L 模样
合金种类
× 100%
铸造收缩率 % 自由收缩 1.0 1.6~2.0 1.4 受阻收缩 0.8 1.3~1.7 1.2
灰口铸铁 碳 钢 锡青铜
(4)拨模斜度与结构斜度
为便于起模,垂 直于分型面的壁 必须有一定的倾 斜度。
(5) 铸造圆角( R )
R=(a+b)/2
4.型芯及其固定方式
震压造型机工作过程示意图
二.造型材料
型砂 用来制造砂型和型芯的材料,由硅砂(石英 砂,主要成分为SiO2)、粘结剂、水和附加物 混合而成。 型砂应具备的主要性能 1) 要有一定的强度。 2) 具有良好的透气性。 3) 应有足够的耐火性。 4) 具备较好的退让性。
型砂组成示意图
三.造型工艺设计
任务 :根据零件的结构特点、技术要求以
(2)最小铸孔尺寸
灰口铸铁的最小铸孔尺寸 ( mm) 名 称 最小铸孔尺寸(mm) Ф 30~50 Ф 15~30 Ф 12~15
单件、小批量生产 成批量生产 大量生产
(3)铸造收缩率( K )
L 模样 – L 铸件
铸件在凝固过程中, 它的各部分尺寸一般都 要缩小, 铸件尺寸缩小 的百分率, 叫做铸造线 收缩率或铸造收缩率。
型芯:在砂型铸造中,为了形成铸件的内 腔形状或为了简化模型的外形轮廓 , 而 专门制作的砂体。 芯头:型芯的外伸部分。 芯座:铸型中用于支撑型芯的空腔。
型芯头的构造
(a)垂直安置 (b)水平安置
型 芯 的 各 种 形 式
型芯撑的应用示意图
5.浇注系统、冒口和冷铁的设计
浇注系统:是 引导液态金属 进入铸型的一 系列通道的总 称。
及生产批量等条件,确定铸造工艺,绘制 铸造工艺图。
铸造工艺图 :制造模样、铸型,进行生产准
备和验收的最基本的工艺文件。图纸上需 要表示出铸型分型面、浇注系统、型芯结 构尺寸、铸件加工余量、控制凝固措施等 内容。
圆锥齿轮的零件图,铸造工艺图及模样图
1.浇注位置的选择
浇注位置:是指浇注时铸型所处的空间位 置。
§6.3
型砂 准备
砂型铸造方法
砂型铸造基本工艺过程
造型 砂型干燥
制模
炉料 准备
合金 熔炼
合箱 浇注
落砂 清理
铸件 检验
合格铸 件入库
芯砂 准备
造芯
型芯干燥
一.砂型铸造的造型方法
手工造型 – 两箱造型、三箱造型、 地坑造型、脱箱造型、 整模造型、挖砂造型、 常见的 假箱造型、分模造型、 造型方法 活块造型、刮板造型。
浇注系统示意图
冒口的设置
冷铁的设置
机器造型 – 震压造型、高压造型、 射压造型、抛砂造型。
1.手工造型
全部用手工或手动工具完成的造型工序。特 点是:适应性强,成本低,但铸件质量难保证, 生产率低。主要用于单件、小批生产。
2. 机器造型
机器造型时紧砂和 起模的基本操作是用机 器来完成的。特点是: 生产率高,铸件的质量 好,成本高。只适用于 中、小铸件的成批或大 量生产。