不锈钢薄板坯连铸中采用液芯压下技术防止铸坯产生裂纹
连铸坯缺陷的产生与防止措施 Microsoft Word 文档1

连铸坯裂纹的产生与防止措施连铸坯裂纹的分类 :铸坯表面裂纹包括表面纵裂纹、表面横裂纹、网状裂纹(星裂)、发裂、角部纵裂纹、角部横裂纹等;铸坯内部裂纹包括中间裂纹、角部裂纹、中心线裂纹、三角区裂纹、皮下裂纹、矫直裂纹等。
1.1 铸坯表面裂纹部纵裂纹等几种主要的缺陷形式。
铸坯表面裂纹主要有表面纵裂纹、表面横裂纹、网状裂纹、角部横裂纹、边铸坯表面裂纹是在结晶器内产生的,在二冷段得到扩展。
它会导致轧制板材表面的微细裂纹,影响最终产品的表面质量。
图1为表面裂纹示意图图 1 铸坯表面裂纹示意图1-表面纵裂纹;2-表面横裂纹;3-网状裂纹;4-角部横裂纹;5-边部纵裂纹1.1.1 表面纵裂纹连铸坯表面纵裂纹是指沿着拉坯方向在铸坯表面上发生的裂纹。
它可由工艺因素或设备因素引起。
由工艺因素引起的纵裂,大多出现在铸坯宽面的中央部位,是表面裂纹中最常见的一种裂纹缺陷。
纵裂主要是由于初生坯壳在结晶器内冷却强度不均匀,造成应力的集中,在坯壳相对较薄的地方坯壳厚度不足以承受这种应力,致使坯壳裂开而产生裂纹,并在二冷区得到扩展,形成表面纵裂纹。
图2 图3 图4为表面纵裂纹示意图图2图3 图41.影响连铸坯表面纵裂纹因素:实际生产过程中,主要有以下因素影响连铸坯表面纵裂纹的产生:1) 成品成分及钢水质量(1) 成品钢中碳含量处在亚包晶和包晶反应区时,由于初生坯壳在结晶器弯月面内激冷时收缩较大,容易造成初生坯壳厚薄不均,从而使铸坯发生纵裂纹的倾向增加。
因此,在实际生产中各连铸厂家都尽量控制其成品钢中碳含量,使其避开亚包晶和包晶反应区,从而减少铸坯纵裂纹的发生机率。
(2) 成品钢中硫、磷含量也会影响铸坯纵裂纹的产生。
钢中硫、磷含量增加时,钢的高温强度和塑性明显降低,在应力作用下就容易产生裂纹,因此,在实际生产中各连铸厂家都尽量控制其成品钢中硫、磷含量,尽量控制在0.02%以内。
(3) 钢中微合金如铌、钒等对铸坯纵裂纹的产生也有重要影响,因为微合金而产生的铸坯纵裂纹在铸坯表面上分布不规则,缺陷较短、数量较多。
薄板坯连铸连轧技术及其ESP工艺
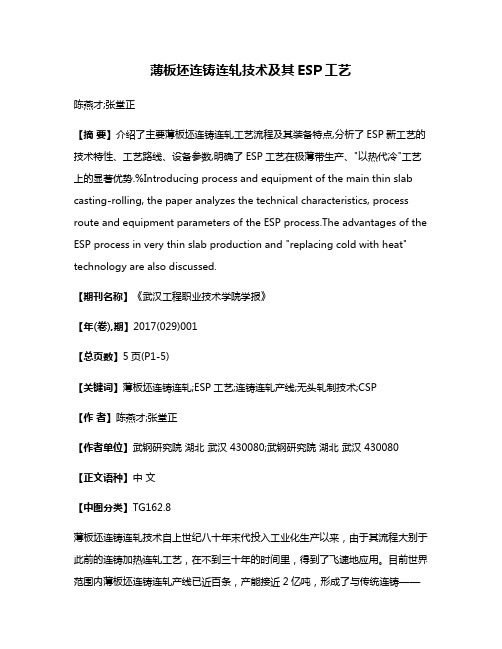
薄板坯连铸连轧技术及其ESP工艺陈燕才;张堂正【摘要】介绍了主要薄板坯连铸连轧工艺流程及其装备特点,分析了ESP新工艺的技术特性、工艺路线、设备参数,明确了ESP工艺在极薄带生产、"以热代冷"工艺上的显著优势.%Introducing process and equipment of the main thin slab casting-rolling, the paper analyzes the technical characteristics, process route and equipment parameters of the ESP process.The advantages of the ESP process in very thin slab production and "replacing cold with heat" technology are also discussed.【期刊名称】《武汉工程职业技术学院学报》【年(卷),期】2017(029)001【总页数】5页(P1-5)【关键词】薄板坯连铸连轧;ESP工艺;连铸连轧产线;无头轧制技术;CSP【作者】陈燕才;张堂正【作者单位】武钢研究院湖北武汉 430080;武钢研究院湖北武汉 430080【正文语种】中文【中图分类】TG162.8薄板坯连铸连轧技术自上世纪八十年末代投入工业化生产以来,由于其流程大别于此前的连铸加热连轧工艺,在不到三十年的时间里,得到了飞速地应用。
目前世界范围内薄板坯连铸连轧产线已近百条,产能接近2亿吨,形成了与传统连铸——热连轧工艺齐头并进的势头。
相比传统连铸——热连轧工艺,薄板坯连铸连轧技术将连铸、加(均)热和热连轧三大流程有机整合到一条产线内,优势十分明显:投资省,占地少,能耗低,成材率高,运行成本低,且通过无头轧制技术可生产传统热连轧工艺无法生产的薄材、极薄材,实现部分品种规格的“以热代冷”。
在不锈钢连铸薄板坯生产中应用液芯压下技术的探讨

在不锈钢连铸薄板坯生产中应用液芯压下技术的探讨张家涛 邢长虎 翟启杰(上海大学材料科学与工程学院,上海20072) 李烈军(广州钢铁集团股份有限公司) 【摘要】 分析了连铸条件下不锈钢的凝固特性,结合薄板坯连铸生产中的液芯压下技术特点,对采用液芯压下技术生产不锈钢的可能性及其对铸坯质量的影响进行了探讨,指出国内不锈钢薄板坯生产采用带液芯压下技术的连铸连轧技术具有重大技术经济价值。
【关键词】 不锈钢 薄板坯 连铸 液芯压下作者简介:张家涛(1970~),男,博士后,主要从事冶金工艺及新材料开发等方面研究APPLICATION OF LCR IN PRODUCTION OF STAIN L ESS STEE L THIN SLAB BY CONTINUOUS CASTING AN D ROLLINGZhang Jiatao X ing Changhu Zhai Qijie (Shanghai University ) Li Liejun(G uangzhou Iron and Steel C o.,Ltd.) 【Abstract 】 Thes olidification characteristics of stainless steel in continuous casting wereanalyzed.Ass ociated with the LCR technology ,the possibility of stainless steel production by continuous casting with LCR ,as well as the effect of LCR on product quality were discussed.It was presented that the production of stainless steel by continuous casting and rolling processes with LCR was of great im portance in technology and economics.【K ey Words 】 Stainless Steel ,Thin Slab ,C ontinuous Casting ,LCR 1 前 言目前,液芯压下技术(Liquid C ore Reduction ,简称为LCR )已在ISP 、CSP 、FTSR 以及CPR 等连铸生产线上得到应用。
薄板坯连铸带液芯轻压下技术

第39卷 第2期2004年2月 钢 铁I RON AND ST EELV o l.39,N o.2Feb ruary2004薄板坯连铸带液芯轻压下技术袁集华(钢铁研究总院连铸技术国家工程研究中心,北京100081)摘 要 就薄板坯连铸带液芯轻压下过程的设备条件、控制系统、工艺要求、生产操作方式、铸坯的质量等做了简要的概述。
结构合理的扇形段和能力恰当的液压缸、先进的PL C控制系统是轻压下的技术关键;稳定及合适的连铸工艺亦是带液芯轻压下不可缺少的基本前提;扇形段采用平行缓慢方式挤压带液芯的铸坯是稳定生产的有效措施;薄板坯连铸带液芯轻压下对铸坯质量的影响比较小。
关键词 薄板坯连铸 带液芯轻压下中图法分类号 T F77717 文献标识码 ATH IN S LAB CAST ING W ITH L IQU I D CORE RED UCT I ONYU AN J ihua(N ati onal Engineering and R esearch Cen ter fo r Con tinuou s Casting T echno logy,Cen tral Iron and Steel R esearch In stitu te,Beijing100081)ABSTRACT T he equ i pm en t,con tro l system,techn ical requ irem en ts,op erati on m ode and p rod2 uct quality of th in slab casting w ith liqu id co re reducti on(L CR)are in troduced1T he segm en ts w ith reasonab le design,cylinders w ith su itab le cap acity,and advanced PL C system are the key p arts fo r L CR1T he stab le and su itab le casting techno logies are also the p reconditi on s fo r L CR1 In the segm en ts the liqu id co re th in slab shou ld be squeezed slow ly and p arallelly1L CR has a lit2 tle effect on th in slab quality1KEY WORD S th in slab casting,liqu id co re reducti on1 前言带液芯轻压下技术已成为薄板坯连铸连轧工艺流程中的一个重要组成部分,并已成熟地应用于实际生产过程中。
连铸坯表面裂纹形成及防止(蔡开科)
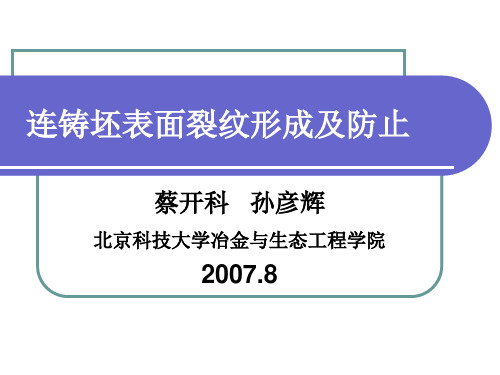
图2-17 结晶器锥度和钢成分对皮下内裂的影响 (断面尺寸240x240mm,拉速0.7m/min)
2 铸坯表面纵裂纹
(7) 结晶器振动
振痕浅,无角部纵裂纹; 振痕深,角部纵裂纹增加; 负滑脱时间值增大,板坯表面纵裂升高;=0.2~0.3s,纵裂降低。 (8) 结晶器钢液流动 水口对中,防止产生偏流;水口材质浸蚀,出口流股不对称,造 成偏流。 水口插入深度合适
图2-8 结晶器液面波动对纵裂纹的影响
图2-9 液面控制方式对纵裂纹的影响
2 铸坯表面纵裂纹
(5) 结晶器热流和冷却
如图2-10所示,90×1000mm 板坯结晶器弯月面以下45mm热流 与纵裂纹指数关系。 ◆低碳钢(0.05%C),结晶器热 流>60Cal/cm2· s(2.1MW/ M2), 纵裂纹增加; ◆中碳钢(0.11%C),结晶器热 流>41Cal/cm2· s(1.7MW/M2),纵裂 纹增加。
3 铸坯(1) 钢成分 C=0.10~0.15%,坯壳厚度不均 匀性强,振痕深,表面易产生凹陷 或横裂纹;生产实践表明,C= 0.15~0.18%或0.15~0.20%时, 振痕浅了,铸坯边部横裂减少; 降低钢中[N],防止氮化物沉淀; (2) 结晶器振动特点 振痕深度增加,横裂纹增加(图 3-4); 振动频率f增加,振痕变浅,横裂纹 减少(图3-5); 负滑脱时间增加,振痕深度增加 (图3-6),方坯tN=0.12~0.15s, 板坯tN=0.20s。
2 铸坯表面纵裂纹
(2) 结晶器钢水流动的合理性
液面波动±3~±5mm
浸入式水口对中,防止偏流 合理的浸入式水口设计(合适的出口直径,倾角) 合适的水口插入深度
(3) 结晶器振动
冶金特有连铸工高级工考试题库(附答案)

答案:√20.>小方坯铸机事故冷却水的水量应能保证铸机的一定压力供水15min以上。
( )答案:√21.>温坯清理的概念是清理时铸坯的温度大于50℃。
( )答案:×22.>为提高拉速及铸坯质量,连铸钢水过热度以偏低为好。
( )答案:√23.>为防止液压串油,连铸机液压油温越低越好。
( )答案:×为发挥冶炼设备的能力,保证连铸与炼钢匹配,连铸的能力应大于炼钢的能力10%~20%。
( ) 为保证轧材内部组织致密,具有良好的机械性能,不同产品要求不同的压缩比。
( )碳素结构钢按技术条件所分的A级钢是指保证化学成份但不保证机械性能的钢。
( )为保证结晶器的传热效果,其水缝中冷却水的流速应保持在3~5m/s为宜。
( )所有的钢种都可以采取连铸浇注。
( )所谓固相矫直是指铸坯进入矫直区业已全部凝固时进行的矫直。
( )适当降低过热度的浇注温度,可缩小铸坯中的柱状晶区,扩大等轴晶区。
( )事故冷却水的水量应不小于正常水量的1/5。
( )事故冷却水的冷却部位有结晶器冷却水和机械闭路水。
( )全面质量管理是一种全员共同参与、全过程控制的质量管理方法。
( )轻压下技术可以减少铸坯纵裂。
( )全面质量管理的五大要素是人、机、料、法、环。
( )普碳钢按技术条件所分的甲类钢是指保证化学成份,但不保证机械性能的钢。
( )内混式切割枪比外混式切割枪不易产生回火。
( )硫在钢中与锰形成MnS有利于切削加工。
( )菱变是方坯所特有形状缺陷。
( )连铸用的PLC及仪表必须使用稳压装置。
( )连铸坯鼓肚是造成铸坯严重中心偏析的重要原因。
( )42.>连铸坯硫印检验是利用放大镜观察铸坯中心硫偏析痕迹的方法。
( )答案:×43.>连铸坯低倍组织由表面细小等轴晶.柱状晶和中心粗大的等轴晶组成。
( )答案:√44.>连铸坯的柱状晶越发达,质量就越好。
黑色冶金技术《连铸中级答案B》

职业技能鉴定国家题库统一试卷连铸工中级工试卷B答案卷一、判断题1>× 2>× 3>√ 4>√ 5>√ 6>√ 7>× 8>√ 9>× 10>√ 11>× 12× 13√ 14√ 15√ 16× 17× 18√ 19√ 2021二、选择题1>B 2>C 3>B 4>B 5>B 6>B 7>B 8>C 9>A10>A 11>C 12>C 13>A 14>A 15>B 16>B 17>A 18>B 19>B 2021三、填空题1>稳定 2>兴旺 3>位移 4>过热度 5>溢钢 6>宏观7>煤气开关 8>直形结晶器 9>矫直点 10>三倍 11>高温脆性曲线 12>收得率 13>气隙 14>上装式 15>软水 16>多点矫直 17>大于 18>外表质量 19>中心偏析 2021质形核四、计算题1>解:T L=1537℃-88%C8%Si5%Mn30%in,再大火烘烤90min以上。
铝碳质制品在烘烤过程中,其强度变化规律是:随着烘烤温度的上升,其强度下降,到500~600℃时强度最低,当温度继继上升,春强度又增加,到1300℃左右恢复原状,再升高温度,其强度又下降,所以水口、塞棒应快速烘烤到1000~1100℃。
2>在钢液的凝固过程中,由于温度起伏的液相穴内钢液流动的影响,使局部的柱状晶可能比邻近的柱状晶优先生长,优先生长的柱状晶一方面它本身生长速度快,另一方面沉降下来的晶片可能落到它上面,于是这局部柱状晶开展更快,产生穿晶,形成搭桥。
薄板坯连铸连轧的液芯压下技术

l I oI d eo i 】 0 r utn q耐 ee l
1 前
言
在 技 术经 济 上 的优 势 。而 从 连 铸 角 度 考 虑 , 产 生 薄 板坯 会 给结 晶器 和 浸入 式 水 口带 来 负 担 。如果 结 晶 器 内腔 厚 度 太 小 , 不 利 于 浸 入 式 水 口的插 会 入 , 且 结 晶器 内 的熔 池 也 太 小 , 加 了钢 水铸 流 而 增 对 凝 壳 的 冲刷 , 剧 了结 晶器 内 钢 液 面 的波 动 , 加 不 利 于保 护 渣 液 渣 层 的 形 成 和 稳 定 , 加 了浇 铸 的 增 难 度 , 以结 晶器 内腔 的厚 度不 应 太 小 。这 样 , 所 在 连 铸 和 连 轧之 间存 在 着对 铸 坯 厚 度 有 不 同要求 的
液 芯 压 下 技 术 最 早 应 用 于 常 规 厚板 坯 和大 方 坯连 铸 机 , 目的 是 为 了 改 善 铸 坯 中 心 疏 松 和 宏 其 观 偏 析 , 高 铸 坯 的 内部 质 量 。因 为 在 凝 固末 期 , 提 铸 坯 中 心 固化 时 产 生 收 缩 , 方 面 在 中 心 部 位 形 一
维普资讯
20 0 2年 1 2月
De e e 2 O c mb r O2
・
钢
铁
研
究
第 6期 ( 总第 19期 ) 2
N . (u 2 ) o6 Sm19
R s a c n Io & Se l e e r h o rn te
科研与实践 ・
中 心 疏 松 和宏 观 偏 析 … 。
在 薄 板坯 连 铸 中 , 于 铸 坯 较 薄 , 却 较 快 , 由 冷 其 中 心 出 现 偏 析 的 程 度 比 常 规 厚 板 坯 和 大 方 坯
中级连铸工技能鉴定考试卷

中级连铸工技能鉴定考试卷一、判断题(每题1分,共60分)1.使用耐火砖中间包与绝热板中间包相比,钢水中夹杂物含量较少。
( )答案:×2.连铸二冷水量的分配原则是指铸机高度从上到下逐渐减少。
( )答案:√3.同样条件下,冷却强度越大,拉坯速度越快。
( )答案:√4.结晶器长度,主要取决于拉坯速度,结晶器出口安全坯壳厚度和结晶器的冷却强度。
( )答案:√5.疏松属于内部缺陷。
( )答案:√6.夹杂物对钢性能只有危害。
( )答案:×7.钢中的氢是白点产生的根本原因,降低钢的断面收缩率。
( )答案:√8.钢水包在使用过程中要保证砖衬稍有膨胀性,使整个砖衬成为一体,不开裂、不剥落。
( )答案:√9.火焰切割断面的下边缘常留有残渣,即毛刺,在轧钢时对轧辊表面的板坯质量不会有影响。
( ) 答案:×10.提高铸坯质量的措施主要是采用提高铸坯柱状晶的比率。
( )答案:×11.硅质绝热板的主要化学成份是SiO2。
( )答案:√12.研究表明:振痕处容易形成裂纹和成份偏析,且随着振痕的深度加深而加重,因此减少振痕深度是改善铸坯质量的重要措施。
( )答案:√13.Al-C质耐火材料的主要成分是Al2O3含量不同。
( )答案:×14.浇注温度是指中间包内的钢水温度。
( )答案:√15.结晶器的倒锥度是指结晶器的上口尺寸小于下口尺寸。
( )16.中间包覆盖渣能防止钢液二次氧化,而且还能吸附中间包钢液上浮的非金属夹杂物,减少中间包内钢液的温度降。
( )答案:√17.对连铸钢水要求Mn/Si≤3为好。
( )答案:×18.钢包敞开浇铸,影响保护渣的性能,但对质量影响不大。
( )答案:×19.铸坯矫直时的表面温度,应避开脆性敏感区。
( )答案:√20.铸坯由三个带组成的低倍结构由外向里分别为激冷层(细小等轴晶),柱状晶和中心等轴晶。
连铸板坯中心裂纹的成因及控制

总第101期2006年第1期山西冶金SHANXIMETALLURGYTotal101No.1.2006文章编号:1672—1152(2006)叭-0022—03连铸板坯中心裂纹的成因及控制卫晓霞t,z毛卫民,富平原z张保师z(1.北京科技大学材料科学与工程学院,北京100083;2.太钢集团临汾钢铁有限公司,山西临汾04l000)摘要:根据连铸机检测结果和生产记录,对太钢集团临汾钢铁有限公司的连铸板坯中心裂纹产生的原因进行了分析,并提出了相应的改进措施及建议。
分析表明:板坯中心裂纹的形成主要是因为连铸机扇形段的辊子开口度变化严重,导致铸坯鼓肚,产生中心裂纹;连铸拉速波动较大,浇注温度偏高且不稳定,导致柱状晶发达和中心偏析加重,明显促进了板坯中心裂纹的产生;m√m。
和m√m。
偏低,铸坯中夹杂物较多,造成铸坯开裂。
关键词:连续铸造板坯中心裂纹中图分类号:TG249.7文献标识码:A收稿日期:2006—01—17连铸板坯中心裂纹发生于凝固末端的铸坯心部,此时少量的钢水被完全凝固的部分所包围,凝固收缩得不到外来钢水的补充…。
当连铸板坯存在中心裂纹时,在轧前加热过程中该中心裂纹可能被氧化,即使经过轧制,该氧化后的裂纹也很难焊合,导致板材出现分层缺陷,钢卷或薄板的表面呈中间波浪形缺陷。
在轧制过程中,即使一些氧化后的中心裂纹暂时焊合,用户对这些钢材进行弯曲变形时也可能会出现分层缺陷,引起钢材的质量异议[2]。
太钢集团临汾钢铁有限公司(以下简称临钢)的连铸机型号为R6.5r11/8lTl/12—n/22m,生产的连铸钢坯宽度为1260mm,厚度分别为150mm、180mm和200mm,连铸拉速为O.8“min~1.1In/min,连铸钢种以普通碳素钢为主。
随着钢材市场竞争的日益激烈,对钢材的质量要求越来越严格,因此,通过改善连铸坯内部质量,进而提高钢材质量一直是临钢的主要努力方向。
目前,临钢连铸板坯中心裂纹相对其它缺陷的出现机率较高,比例约为50%。
连铸表面裂纹产生的原因和改进的技术措施

姓名:陈守汪班级: 冶094班学号:099014214 2018年5月14日连铸表面裂纹产生地原因和改进地技术措施摘要:连铸坯表面裂纹地产生主要取决于:钢成分对裂纹敏感性、浇铸工艺条件及连铸机设备状况•带液芯地连铸坯在连铸机内运行过程中受到外力作用是坯壳产生裂纹地外因,钢地高温力学行为是产生裂纹地内因,而设备和工艺因素是产生裂纹地条件•根据所浇钢种,对连铸机设备地调整应符合钢水凝固收缩规律,以坯壳不发生变形为原则.优化工艺参数,使其处于能够保证连铸坯不产生裂纹或不足以造成废品地允许范围内,得到合理地铸坯凝固结构.b5E2RGbCAP关键词:铸坯表面纵裂纹、铸坯表面横裂纹主要内容:铸坯裂纹是影响连铸机产量和铸坯质量地主要缺陷.据统计,铸坯各类缺陷中有50汹裂纹缺陷.铸坯出现裂纹,轻者需进行精整,重者会导致漏钢和废品,既影响连铸坯生产率,又影响产品质量,增加生产成本. plEanqFDPw1铸坯表面纵裂纹1. 1 板坯表面纵裂纹特征表面纵裂纹可能在板坯宽面中心区域或宽面到棱边地任一位置产生.综合分析表明,纵裂纹有以下特征:(1>产生纵裂纹地表面常伴有凹陷(depression>, 纵裂纹地严重性与表面凹陷相对应.(2>裂纹沿树枝晶干方向扩展.(3>裂纹内发现有硅、钙、铝等元素地夹杂物.(4>在裂纹周围发现有P, S, Mn地偏析.(5>裂纹边缘出现一定地脱碳层,说明裂纹是在高温下形成扩展地.1.2 表面纵裂纹产生地原因板坯表面纵裂纹在连铸机内产生原因如下(1>板坯横断面低倍检验表明,纵裂纹起源于激冷层薄弱处(约2〜3mm> .(2>结晶器地模拟实验表明,纵裂纹起源于结晶器弯月面区(几十毫M到150mm>周边坯壳厚度薄弱处.这说明纵裂纹起源于结晶器地弯月面区初生凝固壳厚度地不均匀性. DXDiTa9E3d坯壳受下列所述力地作用:( 1> 板坯凝固壳四周温度不均匀而产生地收缩力。
薄板坯连铸连轧的液芯压下技术

第34卷 第9期1999年9月钢 铁IRON AN D STEELVol.34,No.9September1999·综合论述·薄板坯连铸连轧的液芯压下技术彭晓华(重庆钢铁设计研究院)摘 要 介绍了国内外薄板坯连铸连轧流程中液芯压下技术的发展与应用情况,分析了液芯压下过程中铸坯的凝固机理以及变形和应变特点,并根据铸坯的凝固机理和坯壳凝固前沿的应变条件,提出了确定单辊压下量、压下量分配和总压下量的基本方法。
关键词 薄板坯连铸连轧 液芯压下⒇S OFT REDUCTION WITH LIQUID C ORE IN THIN S LABCONTINUOUS CASTING/ROLLING PROCESSPEN G Xiao hua(Chong qing Iro n and Steel Desig ning Institute)ABSTRACT The paper introduces the dev elo pm ent and applica tion of soft reduction with liquid co re in thin slab co ntinuo us casting/ro lling process abroad,the principle of solidifica-tio n,the deforma tion and strain of slab during soft reductio n w ith liquid co re is a naly zed,the basic method of determining the total reductio n ratio,the reductio n ratio at o ne roll and the distributio n o f reduction amo ng seg ments is put forw ard.KEY W ORDS thin slab continuous casting/ro lling,liquid core soft reduction1 前言液芯压下技术最早应用于常规厚板坯和大方坯连铸机,其目的是为了改善铸坯中心疏松和宏观偏析,提高铸坯的内部质量。
薄板连铸连轧工艺技术的研究分析 -颜莉 - 副本
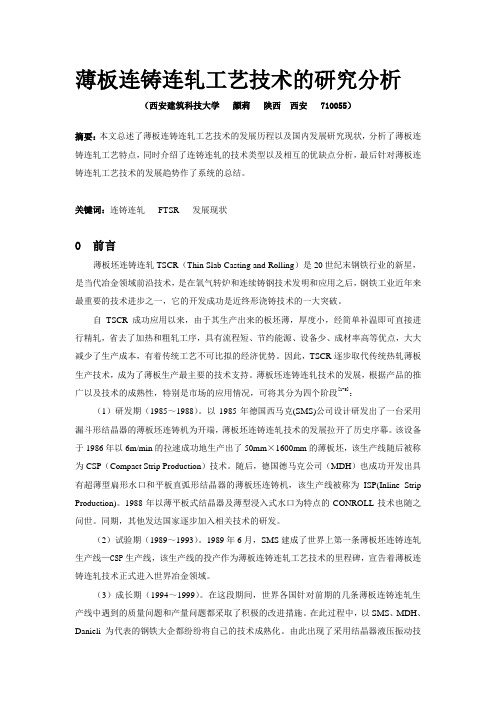
薄板连铸连轧工艺技术的研究分析(西安建筑科技大学颜莉陕西西安 710055)摘要:本文总述了薄板连铸连轧工艺技术的发展历程以及国内发展研究现状,分析了薄板连铸连轧工艺特点,同时介绍了连铸连轧的技术类型以及相互的优缺点分析,最后针对薄板连铸连轧工艺技术的发展趋势作了系统的总结。
关键词:连铸连轧FTSR 发展现状0 前言薄板坯连铸连轧TSCR(Thin Slab Casting and Rolling)是20世纪末钢铁行业的新星,是当代冶金领域前沿技术,是在氧气转炉和连续铸钢技术发明和应用之后,钢铁工业近年来最重要的技术进步之一,它的开发成功是近终形浇铸技术的一大突破。
自TSCR成功应用以来,由于其生产出来的板坯薄,厚度小,经简单补温即可直接进行精轧,省去了加热和粗轧工序,具有流程短、节约能源、设备少、成材率高等优点,大大减少了生产成本,有着传统工艺不可比拟的经济优势。
因此,TSCR逐步取代传统热轧薄板生产技术,成为了薄板生产最主要的技术支持。
薄板坯连铸连轧技术的发展,根据产品的推广以及技术的成熟性,特别是市场的应用情况,可将其分为四个阶段[1-5]:(1)研发期(1985~1988)。
以1985年德国西马克(SMS)公司设计研发出了一台采用漏斗形结晶器的薄板坯连铸机为开端,薄板坯连铸连轧技术的发展拉开了历史序幕。
该设备于1986年以6m/min的拉速成功地生产出了50mm×1600mm的薄板坯,该生产线随后被称为CSP(Compact Strip Production)技术。
随后,德国德马克公司(MDH)也成功开发出具有超薄型扁形水口和平板直弧形结晶器的薄板坯连铸机,该生产线被称为ISP(Inline Strip Production)。
1988年以薄平板式结晶器及薄型浸入式水口为特点的CONROLL技术也随之问世。
同期,其他发达国家逐步加入相关技术的研发。
(2)试验期(1989~1993)。
本钢BSP薄板坯连铸机概述1

本钢BSP薄板坯连铸机概述陶力群李秉强(本溪钢铁集团公司炼钢厂)摘要介绍薄板坯连铸机生产工艺及技术状况。
关键词薄板坯连铸机,H2漏斗型结晶器,带LPCS的动态软压下。
Summaries of Bengang BSP Flexible Thin Slab CasterLiu Jun Tao Liqun Li Bingqiang(Steel Making Plant of Benxi Iron &Steel (Group) Co.Ltd)Abstract This paper introduced production process and technology of flexible thin slab caster.Key words flexible slab caster H2 funnel mould dynamic soft reduction with LPCS1 前言自八十年代末美国纽柯公司的克里福兹维尔厂投产世界上第一台连铸—连轧短流程生产线,经济效益显著,引起国际冶金界的重视。
薄板坯连铸连轧技术与传统连铸连轧技术相比较,具有生产流程短,节约能源,降低生产成本及劳动强度等优点。
目前,随着薄板坯连铸连轧技术的日臻成熟,它所能生产的钢种已扩大到包括包晶钢、硅钢、汽车用钢、低碳钢、中碳钢、高碳钢、高强度合金钢等多个种类,产品结构越来越广泛。
本钢BSP薄板坯连铸机技术由Danieli公司提供:应用H2漏斗型结晶器、带LPCS的动态软压下、结晶器漏钢预报和热相图等技术,使BSP薄板连铸机的工艺技术和设备性能达到世界一流水平。
以下对本钢BSP薄板坯连铸机的工艺技术及设备性能做以介绍。
2本钢BSP薄板坯连铸连轧工艺简介BSP连铸--连轧短流程生产线生产厚度为90/70mm和100/85mm的铸坯。
连铸机采用H2漏斗型结晶器,结晶器长度1200mm,结晶器下部为2对带辊型的足辊,扇型0段前5对为带辊型的夹持辊,将出结晶器后有凸度的铸坯压平。
第六讲_连_铸_坯_裂_纹_控_制

连 铸 坯 裂 纹 控 制
连 铸 坯 质 量 控 制
在连铸生产实践中,裂纹是铸坯的一种主要缺陷,据统计,铸坯各类 缺陷中有50 %为裂纹[1 ] 。铸坯中存在裂纹,严重的会影响到铸坯 的后续加工以及最终产品的质量,甚至造成废品。浇注过程中,裂纹 还会造成拉漏事故发生,影响连铸机的正常生产,造成钢水浪费。裂 纹还会使铸坯热送技术和连铸连轧技术的采用受到影响。因此,防 止铸坯裂纹产生,对稳定连铸生产、提高产品质量具有重要意义。 按照连铸坯裂纹产生的位置和形态可分为表面裂纹和内部裂纹。 绝大多数内裂纹都是在凝固过程中形成的,故有时也称为“凝固裂 纹”[2 ] 。从概念上讲,铸坯中从皮下一直到中心部位出现的裂纹 都可以称为内裂纹,因此,内裂纹不仅包括凝固裂纹,也应该包括那 些在凝固温度以下由于A1N、Nb (C ,N)等质点在奥氏体晶界析出 引起晶界脆化、在外力作用下形成的裂纹,只是后者所占比例很小 [3 ] 。
连 铸 坯 质 量 控 制
(3) 辊子不对中应变:
300s m m l2
m =0.2~0.4%,由模型计算的结果如图2-7。 m =0.5~1.5mm,
图2-7 辊子不对中应变沿铸流方向的分布
连 铸 坯 质 量 控 制
(4) 热应力应变: t 0.1~0.2%
总应变
如应变可以线性叠加,那么凝固前沿发生的总应变
连 铸 坯 质 量 控 制
1 连铸坯裂纹概论
1.1 连铸坯裂纹类型
(1) 连铸坯表面裂纹(图1-1)
◆ 纵裂纹 ◆ 横裂纹 ◆ 网状裂纹 ◆ 皮下针孔
图1-1 铸坯表面缺陷示意图 1-表面纵裂纹;2-表面横裂纹;3-网状裂纹; 4-角部横裂纹;5-边部纵裂纹;6-表面夹渣; 7-皮下针孔;8深振痕
连铸工考技师无纸化试题及答案2

A.碱 B.酸 C.中 D.三种均可
正确答案:A 您的答案:
55 、
在高速拉坯时,会出现带液芯矫直,为防止( ),办法之一就是压缩铸造,其本质是在矫直过程对铸坯施加一个压缩力。
A.内裂 B.表面纵裂 C.表面横裂 D.偏析
A.30/(3×0.16×0.20×7.4×0.9)
B.30/(3×160×200×7.4×0.9)
C.30/(3×160×200×0.9)
D. 30/(3×0.16×0.20×0.9)
正确答案:A 您的答案:
54 、
为提高包龄,浇铸高锰钢宜使用( )性中间包。
中间包钢水重量15t,浇注板坯200mm×1200mm,拉速为1.2m/min,问钢水在中间包内停留时间为( )min。(钢水比重为7.4kg/m3)
A.4 B.7 C.9 D.12
正确答案:B 您的答案:
52 、
为什么中间包用耐火材料向碱性材料发展?()
正确答案:√ 您的答案:
11 、 钢中含碳量降低时,硬度、强度提高。
正确答案:× 您的答案:
12 、 小方坯中间包水口的材质主要是铜质。
正确答案:× 您的答案:
13 、 不锈钢的铸坯切割必须加铁屑,才能切断。(
正确答案:A 您的答案:
56 、
结晶器保护渣对铸坯( )缺陷影响较大。
A.表面纵裂 B.中心裂纹 C.鼓肚 D.形状缺陷
正确答案:A 您的答案:
57 、
CPU的概念下列正确叙述的是( )。
19 、 薄板坯连铸可用于中、小型钢厂。
正确答案:√ 您的答案:
20 、 ISP技术是德国德马克公司开发的。
技术比武题库(连铸工)

技术比武题库一、选择题1、( )连铸机型冷却最均匀。
A.立式B.立弯式C.全弧形D.椭圆形2、高质量板坯连铸趋向于采用( )连铸机型。
A.立式B.立弯式C.全弧形D.多点弯曲多点矫直弧形3、某钢厂小方坯连铸机,平均拉速为2.6m/min,正弦振动频率100次/min,振幅17mm,负滑脱率为( )。
A.20B.23C.31D.334、两流板坯连铸机,铸坯断面为250X1800mm2,平均拉坯速度为0.9m/min,铸坯密度为7.6t/m3,二冷水流量为1800l/min,比水量为( )l/kg。
A.1.0B.1.2C.0.80D.0.585.在钢水连铸过程中,有时发生水口堵塞,一般认为堵塞是()A、SiO2B、Al2O3C、 CaOD、都不是6.从铸坯纯净度来分析,那种机型可更好的降低大型夹杂物( )A.弧型B.水平型C.直结晶弧型D.椭圆型7.结晶器热流最大的区域是()A.弯月面区B.弯月面以下5-10cm C.弯月面以下50-100cmD.弯月面以下100-500cm8、连铸坯坯壳厚度与凝固时间( )。
A.成正比B.成反比C.平方成正比D.平方根成正比9、连铸机液芯长度与凝固系数( )。
A.成正比B.成反比C.平方成正比D.平方成反比10、压缩比是指( )。
A 钢材断面/铸坯断面B 铸坯断面/钢材断面C 铸坯长度/钢材长度D 钢材长度/铸坯长度11、板坯和方坯的区别是宽厚比,宽厚比( )是板坯。
A.>1 B.>2 C.>3 D.>412、大方坯和小方坯的区别是断面长度,断面长度≧( )mm是大方坯。
A.100 B.120 C.150 D.20013、钢包加保护套管的主要目的是()。
A、防止降温B、减少污染C、减少二次氧化D、防止溅钢14、以下不属于近终形连铸的是( )A.CSP连铸工艺 B.ISP连铸工艺 C.CPR连铸技术 D.CREM连铸技术15、钢包的渣线位置所需要的耐火材料要比其它部位( )A 耐侵蚀性好B 耐高温性好C 导热性好D 强度高16、中间包工作层不用烘烤就可使用的是( )包。
邯钢连铸工题库
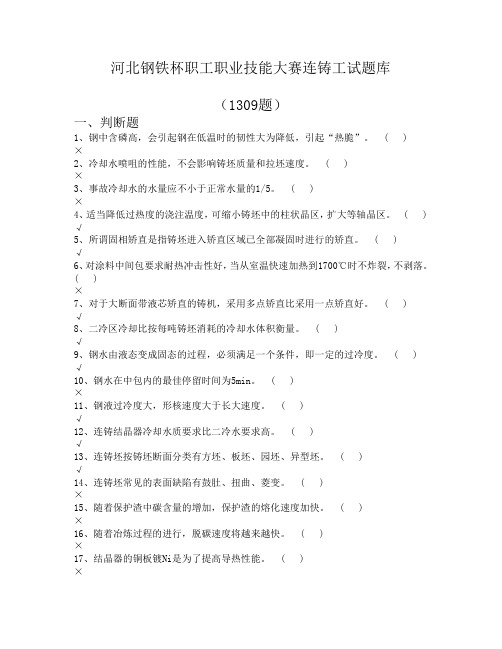
河北钢铁杯职工职业技能大赛连铸工试题库(1309题)一、判断题1、钢中含磷高,会引起钢在低温时的韧性大为降低,引起“热脆”。
( )×2、冷却水喷咀的性能,不会影响铸坯质量和拉坯速度。
( )×3、事故冷却水的水量应不小于正常水量的1/5。
( )×4、适当降低过热度的浇注温度,可缩小铸坯中的柱状晶区,扩大等轴晶区。
( ) √5、所谓固相矫直是指铸坯进入矫直区域已全部凝固时进行的矫直。
( )√6、对涂料中间包要求耐热冲击性好,当从室温快速加热到1700℃时不炸裂,不剥落。
( )×7、对于大断面带液芯矫直的铸机,采用多点矫直比采用一点矫直好。
( )√8、二冷区冷却比按每吨铸坯消耗的冷却水体积衡量。
( )√9、钢水由液态变成固态的过程,必须满足一个条件,即一定的过冷度。
( ) √10、钢水在中包内的最佳停留时间为5min。
( )×11、钢液过冷度大,形核速度大于长大速度。
( )√12、连铸结晶器冷却水质要求比二冷水要求高。
( )√13、连铸坯按铸坯断面分类有方坯、板坯、园坯、异型坯。
( )√14、连铸坯常见的表面缺陷有鼓肚、扭曲、菱变。
( )×15、随着保护渣中碳含量的增加,保护渣的熔化速度加快。
( )×16、随着冶炼过程的进行,脱碳速度将越来越快。
( )×17、结晶器的铜板镀Ni是为了提高导热性能。
( )×18、铸坯振痕深度与结晶器振动负滑脱时间有关,负滑脱时间越短,振痕深度越深。
( )×19、结晶器冷却水较二冷区冷却水压力低。
( )×20、沸腾钢比镇静钢的表面质量好,但成材率低。
( )×成份的含量不同。
( )21、刚玉、高铝和粘土质耐火材料的区别在于SiO2×22、钢包保护套管的作用是改善劳动条件。
( )×23、保护渣水份不会对保护渣的质量造成影响。
连铸工答辩题题目

连铸工答辩题题目、答案及评分标准一、保护渣具有哪些作用?1.固态渣层将钢液面和液渣层绝热。
(4分)2.液渣层可以防止钢液面被空气氧化,吸收从钢液中浮出的Al2O3。
(4分)3.液态膜润滑坯壳与结晶器之间的界面,防止粘结。
(4分)4.固态渣膜调节传往结晶器的热流,使传热减少和传热均匀。
(4分)二、为什么要有准确的对弧?对连铸机来说,对弧准确性,对铸坯形状和质量都有很大影响,(10分)如对弧误差过大,会对坯壳产生附加变形而出现内裂(10分)。
三、防止粘结漏钢有哪些对策?1.监视保护渣的使用状况,确保保护渣有良好的性能。
(7分)2.提高操作水平,控制液位波动。
(7分)3.确保合适的拉速,拉速变化幅度要小。
(6分)四、如何预防连铸坯中心偏析?为防止中心偏析,从冶金角考虑,就是设法扩大铸坯中心的等轴晶区,如采用低温浇注、电磁搅拌等。
(10分)从连铸设备上考虑,就是设法避免凝固坯壳的变形,控制好夹辊的间距,辊子严格对中等,这是防止铸坯鼓肚,消除中心偏析的有效措施。
(10分)五、对连铸钢水质量的基本要求是什么?1.钢水温度:高温、稳定、均匀。
(5分)2.钢水纯净度:最大限度的降低有害杂质和夹杂物含量,以保障铸机的顺行和提高铸坯质量。
(5分)3.钢水成分:保证加入钢水中的合金元素能均匀分布,且把成分控制在较窄的范围内,保障产品性能的稳定性。
(5分)4.钢水的可浇性,要保障适宜的稳定的钢水温度和脱氧程度,以满足钢水的可浇性。
(5分)六、小方坯连铸机二冷区喷嘴布置有哪两种?环管式(10分)和单管式(10分)七、起步漏钢的原因有哪些?出苗时间不够(4分);起步升速过快;铁钉屑撒的太少或撒放不均匀(4分);堵引锭头铜板未放好,落入格栅内与坯壳卡住(4分);保护渣加的过早且大量推入造成卷渣(4分);结晶器与二冷区首段不对弧等都可能导致开浇起步漏钢(4分)。
八、中间包注流对结晶器钢水流动的要求?1、不应把结晶器保护渣卷入钢液底部。
- 1、下载文档前请自行甄别文档内容的完整性,平台不提供额外的编辑、内容补充、找答案等附加服务。
- 2、"仅部分预览"的文档,不可在线预览部分如存在完整性等问题,可反馈申请退款(可完整预览的文档不适用该条件!)。
- 3、如文档侵犯您的权益,请联系客服反馈,我们会尽快为您处理(人工客服工作时间:9:00-18:30)。
不锈钢薄板坯连铸中采用液芯压下技术防止铸坯产生裂纹
一般认为,其中对铸坯内部裂纹影响较大的主要参数有单辊压下量,压下量的分配和总压下量,因此液芯压下需制订正确的工艺参数。
(1)单辊压下量。
对带液芯的铸坯来说,由于温度很高,坯壳强度低,特别是在坯壳的凝固前沿处的强度和塑性都很低。
在这个区域内很容易因坯壳受力变形而在枝晶间的切口处形成裂纹。
当这些裂纹被残余的钢液充填后,由于偏析的作用会增加晶界的脆性,使裂纹继续扩展,最终在铸坯中形成内裂。
因此带液芯的铸坯在二冷区运行过程中应尽量避免发生较大
的变形,将变形限制在允许的范围内。
(2)压下量的分配。
按照不同的工艺条件,液芯压下常常需要实施连续的压下来完成。
这样总压下量在各扇形段中的分配对控制铸坯内部质量很重要。
铸坯距离结晶器近的区段其凝壳较薄,在相同的变形率条件下,允许的压下量可以较大,且由于坯壳的温度较高,对于抑制应变和应力的积累较有利,因此,在液芯压下的前期应采用较大的压缩速率。
在液芯压下的后期,由于凝壳厚,凝固前沿的应变较大,同时由于铸坯温度降低,对于抑制应变和应力的
积累不利,所以应采用较小的压缩速率。
(3)最大形变量和形变速率。
最大形变量越大,对铸坯连铸连轧越有利,但同时导致铸坯产生内裂纹的危险性增大。
对于不同的冶金条件,如何确保不产生内裂纹的情况下最大限度提高生产率、获得最佳的最大变形量等问题有待深入研究解决。
此外,侧边变形速度分配也很重要,压下区段内辊列的对数、行程、辊列的锥度等必须满足内部及侧边铸坯质量要求。