07.MRB作业办法
MRB作业办法

5.1特采处置方式
5.1.1会议决定通过对物料进行特采时。
5.1.2IQC对特采物料贴上特采物料标签,并在标签上注明特采原因,及使用条件。并发出《材
料不良通知单》给供应商分析改善。
5.1.3货仓在发特采物料给给生产时,必须在发料单上写明原因,使用条件。
5.1.4生产在领用特采物料上线时,必须通知工程和品管并依据工程的特采物料加工规范进行
加工。
5.1.5品管IPQC对特采物料上线需作特别追踪,一旦发生不良或异常,即通知停线,以免造成报废。
5.2返工处理方式
5.2.1会议决定通过对物料进行返工时。
5.2.2在第一时间通知供应商过来返工,若供应商未到我司处理,则由我司人员进行挑选,按14元/小时的单价,向供应商扣除返工工时费用。
5.2.3由IQC发出《材料不良通知单》要求供应商分析改善。
1.0目的
界定不良或可疑问题物料的处理方式,以免误用,造成品质问Байду номын сангаас。
2.0范围
适用于物料不良而无法判定处理方式。
3.0定义
MRB:(Material Review Board)物料评审委员会。
4.0权责
4.1成员构成:IQC+PMC+工程+采购
4.1.1IQC:将REJ之物料检验单立即交PMC并立即发出CAR。
4.1.2PMC:
a.填上材料上线日期。
b.依据材料紧急程度,决定是否召开MRB会议。如果是,则通知相关人员开会;如果不是,则将单据退还IQC,由IQC办理退货事宜。
4.1.3工程:做相关之实验,以作为WAIVE(特采)或其它决定依据。
4.1.4参与讨论执行MRB之结论(如向厂商扣款及要求及时补货等)。
MRB作业指导书 -
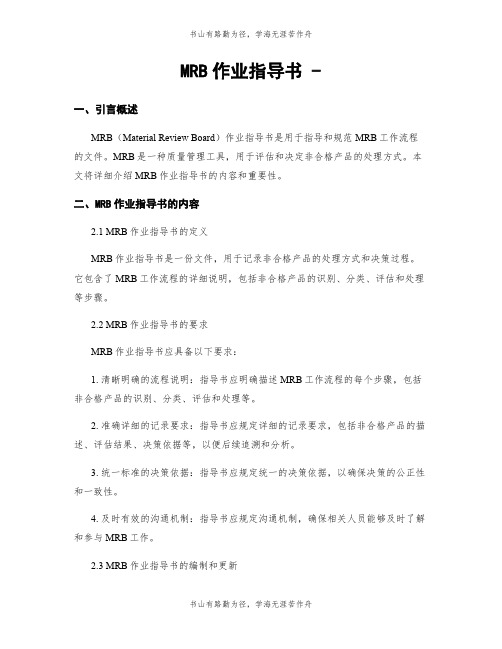
MRB作业指导书 -一、引言概述MRB(Material Review Board)作业指导书是用于指导和规范MRB工作流程的文件。
MRB是一种质量管理工具,用于评估和决定非合格产品的处理方式。
本文将详细介绍MRB作业指导书的内容和重要性。
二、MRB作业指导书的内容2.1 MRB作业指导书的定义MRB作业指导书是一份文件,用于记录非合格产品的处理方式和决策过程。
它包含了MRB工作流程的详细说明,包括非合格产品的识别、分类、评估和处理等步骤。
2.2 MRB作业指导书的要求MRB作业指导书应具备以下要求:1. 清晰明确的流程说明:指导书应明确描述MRB工作流程的每个步骤,包括非合格产品的识别、分类、评估和处理等。
2. 准确详细的记录要求:指导书应规定详细的记录要求,包括非合格产品的描述、评估结果、决策依据等,以便后续追溯和分析。
3. 统一标准的决策依据:指导书应规定统一的决策依据,以确保决策的公正性和一致性。
4. 及时有效的沟通机制:指导书应规定沟通机制,确保相关人员能够及时了解和参与MRB工作。
2.3 MRB作业指导书的编制和更新编制MRB作业指导书时,应由质量管理部门负责,结合实际情况进行调整和完善。
指导书应定期进行更新,以适应质量管理工作的变化和发展。
三、MRB作业指导书的重要性3.1 提高决策的准确性MRB作业指导书规定了决策的标准和流程,能够帮助决策者更加准确地评估非合格产品,并做出合理的处理决策。
这有助于避免主观因素对决策的影响,提高决策的准确性和可靠性。
3.2 保证质量管理的一致性MRB作业指导书规定了统一的工作流程和决策依据,能够保证质量管理工作的一致性。
无论是哪个部门或个人进行MRB工作,都能按照指导书的要求进行操作,避免了因个人主观因素而导致的不一致性。
3.3 提高工作效率MRB作业指导书规定了清晰明确的工作流程,能够帮助相关人员快速了解和掌握MRB工作的要求和步骤。
这有助于提高工作效率,减少决策的时间和成本。
MRB作业流程范文

MRB作业流程范文MRB(Material Review Board)是一种用于处理非符合性材料的流程,旨在确保公司的产品质量和安全性。
本文将详细介绍MRB作业流程,包括定义、流程步骤、成员职责和案例分析等内容。
一、定义MRB是一种用于处理供应商提供的非符合产品或公司内部制造的非合格产品的流程。
当发现产品不符合规格要求,或者供应商提供的原材料没有达到公司的质量标准时,就需要通过MRB流程进行处理。
MRB流程对于确保公司产品质量和安全性具有重要意义。
二、流程步骤1.收集信息:当发现非符合材料或产品时,必须及时收集相关信息,包括产品规格、质量标准、供应商信息等。
2.建立MRB小组:根据非符合材料的类型和严重程度,建立相应的MRB小组。
通常,MRB小组由质量经理、工艺工程师、供应商负责人等组成。
3.审查非合格材料/产品:MRB小组对非合格材料/产品进行审查,确定非合格的原因和严重程度。
审查过程中,可能需要对材料/产品进行测试、测量和分析等。
4.制定纠正措施:根据审查结果,制定相应的纠正措施。
这些措施可能包括修复、更换供应商、修改工艺流程等。
5.执行纠正措施:对于纠正措施,MRB小组负责执行,并确保纠正措施的有效性和可行性。
6.监控纠正措施:MRB小组需要监控纠正措施的实施过程,并定期评估其有效性。
如发现纠正措施无效,需要重新制定并执行新的纠正措施。
7.记录和报告:整个MRB流程的过程和结果都需要进行记录和报告,以供以后参考和审查。
三、成员职责1.质量经理:负责监督和协调整个MRB流程的执行,确保纠正措施的正确性和有效性。
2.工艺工程师:负责对非合格材料/产品进行技术分析,确定非合格的原因,并提供建议和支持纠正措施的制定和实施。
4.质量控制员:负责执行纠正措施,并监控其有效性。
同时,确保符合产品能够满足公司的质量要求。
四、案例分析公司在生产过程中发现原材料不符合公司的质量标准,需要进行MRB处理。
1.收集信息:收集有关原材料、供应商和质量标准的相关信息。
MRB作业管理办法

MRB作业管理办法1.背景介绍MRB指的是Material Review Board,即物料评审委员会。
在制造业中,MRB作为一个重要的管理机构,负责处理各类物料和工件的问题,确保产品质量和工程流程正常进行。
为了更好地规范和管理MRB的工作,制定MRB作业管理办法是非常必要的。
2.目的和范围MRB作业管理办法的目的在于明确MRB的职责和权限,并规范MRB的工作流程,确保评审过程的公正性和有效性。
该管理办法适用于所有涉及物料评审的部门和人员。
3.职责和权限3.1 MRB的职责包括但不限于以下内容:- 对于出现的物料问题或相关突发事件进行评审,并及时做出处理决策;- 确定问题物料的分类和处理方式,如报废、维修、退货等;- 监督和协调相关部门进行问题物料的处置,并跟踪处理结果;- 提出改善建议和措施,减少问题物料的发生。
3.2 MRB的权限包括但不限于以下内容:- 对物料问题进行评审,决定是否需要进行总体评审;- 根据评审结果,决定是否进行进一步的物料测试、分析和验证;- 对于问题物料的处置方式,如报废、维修等,有决策权;- 对评审结果进行审批,并监督相关部门执行。
4.工作流程4.1 问题发现和报告- 员工或部门发现物料问题,立即向MRB提交问题报告;- 问题报告中需要包括物料的具体问题描述、影响范围和后果等信息。
4.2 评审和处理决策- MRB收到问题报告后,立即召开评审会议,对问题进行评审和讨论;- 根据评审结果,MRB决定是否需要进行总体评审,并做出处理决策。
4.3 总体评审- MRB组织相关部门的代表参与总体评审;- 总体评审主要针对重大问题或涉及多个部门的问题进行综合评估。
4.4 处理措施和执行- MRB根据评审结果和总体评审结论,决定问题物料的处置方式;- MRB指定相关部门负责问题物料的处置,并监督处理措施的执行;- 处置方式可能包括报废、维修、退货等。
4.5 改善建议和措施- MRB根据问题的发生和处理情况,提出改善建议和措施;- MRB与相关部门合作,推动改善措施的实施,并定期评估改善效果。
物料审查委员会(MRB)运作及物料报废作业指引
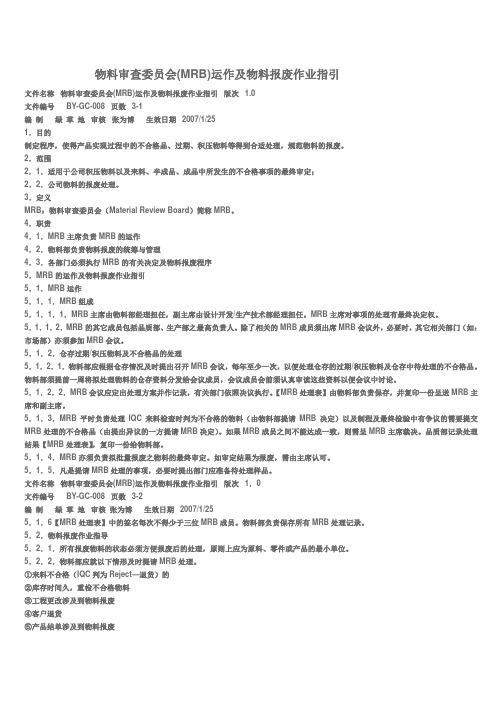
物料审查委员会(MRB)运作及物料报废作业指引文件名称物料审查委员会(MRB)运作及物料报废作业指引版次 1.0文件编号BY-GC-008 页数3-1编制绿草地审核张为博生效日期2007/1/251.目的制定程序,使得产品实现过程中的不合格品、过期、积压物料等得到合适处理,规范物料的报废。
2.范围2.1.适用于公司积压物料以及来料、半成品、成品中所发生的不合格事项的最终审定;2.2.公司物料的报废处理。
3.定义MRB:物料审查委员会(Material Review Board)简称MRB。
4.职责4.1.MRB主席负责MRB的运作4.2.物料部负责物料报废的统筹与管理4.3.各部门必须执行MRB的有关决定及物料报废程序5.MRB的运作及物料报废作业指引5.1.MRB运作5.1.1.MRB组成5.1.1.1.MRB主席由物料部经理担任,副主席由设计开发/生产技术部经理担任。
MRB主席对事项的处理有最终决定权。
5.1.1.2.MRB的其它成员包括品质部、生产部之最高负责人。
除了相关的MRB成员须出席MRB会议外,必要时,其它相关部门(如:市场部)亦须参加MRB会议。
5.1.2.仓存过期/积压物料及不合格品的处理5.1.2.1.物料部应根据仓存情况及时提出召开MRB会议,每年至少一次,以便处理仓存的过期/积压物料及仓存中待处理的不合格品。
物料部须提前一周将拟处理物料的仓存资料分发给会议成员,会议成员会前须认真审读这些资料以便会议中讨论。
5.1.2.2.MRB会议应定出处理方案并作记录,有关部门依照决议执行。
【MRB处理表】由物料部负责保存,并复印一份呈送MRB主席和副主席。
5.1.3.MRB平时负责处理IQC来料检查时判为不合格的物料(由物料部提请MRB决定)以及制程及最终检验中有争议的需要提交MRB处理的不合格品(由提出异议的一方提请MRB决定)。
如果MRB成员之间不能达成一致,则需呈MRB主席裁决。
MRB特采作业管理办法

MRB特采作业管理办法1.0 目的1.1建立不良品信息沟通及处理平台,及时处理不良品,加强品质管控;1.2快速合理的进行品质缺陷判定,明确品质责任承担;2.0范围2.1 本文件适用于生产急用但与品质标准存在差异,需承担客诉风险之物料,且制造加工单位(含供应商)自身无法处理的物料管理,包括下述内容:2.1.1进料类【外协加工/采购物料经检验判退物料】;2.1.2制程在途类【制程加工在途物料/半成品及配件经检验判退物料】;2.1.3仓储类【仓储半成品及配件等物料经检验判退物料】;3.0 权责3.1 MRB小组组长:判定不合格物料处理结果以及责任承担单位;3.2 MRB小组成员:参与不合格物料评估并执行MRB决议,明确品质异常经济责任承担;4.0 管理办法内容4.1 MRB小组成员4.1.1 MRB小组组长—品质部经理;4.1.2 MRB小组成员—生产部经理、计划科主任、采购科主任、技术部经理、相关业务员;4.1.3必要时将临时邀请相关人员;4.2物料异常产生及MRB提出4.2.1公司所有外协加工/采购物料由品质部IQC人员予以检验,如发现来料与品质标准存在差异,但属于生产急用之物料,由采购科/计划科填写《紧急放行单》,品质部召集召开MRB会议;4.2.2制程在途与仓储异常物料,本车间无法修补的,由车间填写《产品质量异常信息反馈单》反馈至品质部,由品质部判定是否召集召开MRB会议;4.3 MRB评估4.3.1计划科:提供客户交期、计划编制、出货排程及补单安排;4.3.2 生产部:提供异常物料所造成进度影响,明确执行单位能否协助代加工/挑选,并承诺完成时间;4.3.3 技术部:评估异常物料能否正常使用,并提供技术支持;4.3.4 采购科:供应商信息沟通,供应商生产状况及供应商之回复,明确MRB产生费用归属,回复供应商返工之完成时间并办理退货、补货手续;4.3.5 业务部:客户沟通及确认;4.3.6 品质部:明确异常物料品质影响程度,判定结果【特采/返工/代加工/挑选/退货/正常使用】,判定责任承担单位并跟进MRB执行结果确认;4.3.7责任承担按《品质异常经济责任承担管理办法》实施;4.4 MRB评估决议及决议执行4.4.1 MRB评估内容须达成决议【特采/返工/代加工/挑选/退货/正常使用】并由品质部以《MRB评审记录表》记录存档,并通过公司邮箱传递相关部门;4.4.2 MRB小组成员须在《MRB评审记录表》签名确认;4.4.3 属生产部协助供应商代加工/挑选,则由生产部记录耗损的成本【工时/材料】,并填写《返修耗时/耗料记录表》上报采购科/财务部门;4.4.4 属品质部MRB全检执行挑选或代加工的(包括本厂制程产生的不良),由品质部负责将MRB产生费用及责任进行划分,并填写《返修耗时/耗料记录表》上报采购科/财务部,财务部执行扣款;4.5 MRB执行结果监督及确认4.5.1 品质部对MRB决议执行之结果予以监督,并判定是否符合要求;4.6 MRB全检组成人员4.6.1品质部品检科下属检验人员为主要实施人员;4.6.2 生产执行车间属MRB临时实施人员;4.7 实施4.7.1《MRB作业管理办法》自颁发日起实施;5.0 附件5.1《产品质量异常信息反馈单》;5.2《MRB评审记录表》;5.3《返修耗时/耗料记录表》;5.4《紧急放行单》;5.5《品质异常经济责任承担管理办法》;。
MRB物料评审作业办法
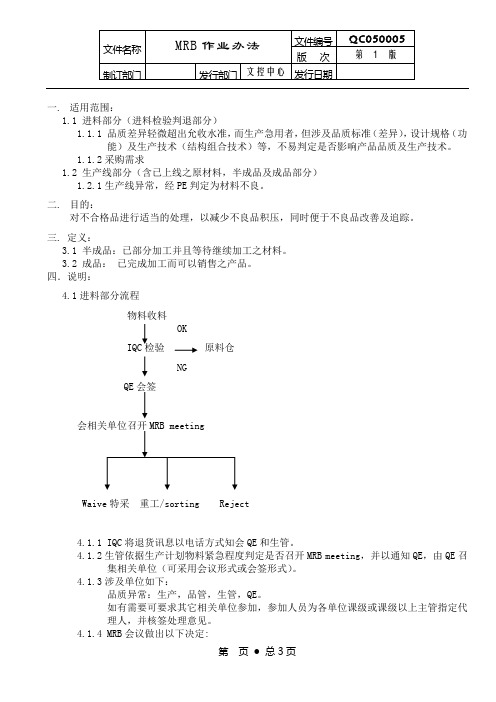
一. 适用范围:1.1 进料部分(进料检验判退部分)1.1.1 品质差异轻微超出允收水准,而生产急用者,但涉及品质标准(差异),设计规格(功能)及生产技术(结构组合技术)等,不易判定是否影响产品品质及生产技术。
1.1.2采购需求1.2 生产线部分(含已上线之原材料,半成品及成品部分)1.2.1生产线异常,经PE判定为材料不良。
二. 目的:对不合格品进行适当的处理,以减少不良品积压,同时便于不良品改善及追踪。
三. 定义:3.1 半成品:已部分加工并且等待继续加工之材料。
3.2 成品:已完成加工而可以销售之产品。
四.说明:4.1进料部分流程物料收料OKIQC检验原料仓NGQE会签Waive特采重工/sorting Reject4.1.1 IQC将退货讯息以电话方式知会QE和生管。
4.1.2生管依据生产计划物料紧急程度判定是否召开MRB meeting,并以通知QE,由QE召集相关单位(可采用会议形式或会签形式)。
4.1.3涉及单位如下:品质异常:生产,品管,生管,QE。
如有需要可要求其它相关单位参加,参加人员为各单位课级或课级以上主管指定代理人,并核签处理意见。
4.1.4 MRB会议做出以下决定:4.1.4.1针对退货之不良批,IQC依《不合格品控制程序》处理,由IQC通知生管于2日内要求厂商运回.4.1.4.2重工或SORTING针对原材料重工/SORTING,经MRB会议于“不合格品处理单”注明重工/SORTING方式,由生管通知厂商处理,需经IQC再次检验,如第二次检验仍判退,IQC有权拒收该LOT.4.1.4.3特采原材料,半成品,成品不符合原定规格而判定不会影响最终品质者依“特采申请单“特采,并由IQC于材料外箱贴附”特采”标签并注明MRB NO.如确属原材品质不良导致, 可经MRB会议决定追加扣款.4.1.5如因材料未承认退货依以下方式作业:A.用于or test阶段的材料,由台湾公司转售之材料,生管于“不合格品处理单”上注明“此批材料用于新机种试投”字样后, 生管部门主管签字即可.B.量产后未承认:由生管会签工程并Release to IQC.4.2生产线品质异常生产线品质异常IPQC判定原材料品质不良QE相关单位召开MRB meetingWaive特采 Rework/Sorting4.2.1生产线异常,由生管提出会议需求并通知QE.IPQC依据在开出“不合格品处理单“的同时暂停使用产品并贴附“不良标签”,由QE 召集相关单位召开MRB meeting.4.2.2涉及单位如下:QE 生管 IQC 仓库生产如有需要可要求其他相关单位参加。
MRB特采作业管理办法
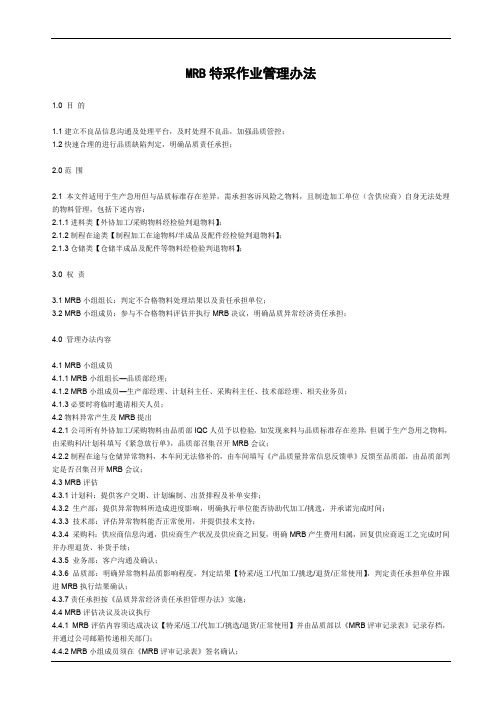
MRB特采作业管理办法1.0 目的1.1建立不良品信息沟通及处理平台,及时处理不良品,加强品质管控;1.2快速合理的进行品质缺陷判定,明确品质责任承担;2.0范围2.1 本文件适用于生产急用但与品质标准存在差异,需承担客诉风险之物料,且制造加工单位(含供应商)自身无法处理的物料管理,包括下述内容:2.1.1进料类【外协加工/采购物料经检验判退物料】;2.1.2制程在途类【制程加工在途物料/半成品及配件经检验判退物料】;2.1.3仓储类【仓储半成品及配件等物料经检验判退物料】;3.0 权责3.1 MRB小组组长:判定不合格物料处理结果以及责任承担单位;3.2 MRB小组成员:参与不合格物料评估并执行MRB决议,明确品质异常经济责任承担;4.0 管理办法内容4.1 MRB小组成员4.1.1 MRB小组组长—品质部经理;4.1.2 MRB小组成员—生产部经理、计划科主任、采购科主任、技术部经理、相关业务员;4.1.3必要时将临时邀请相关人员;4.2物料异常产生及MRB提出4.2.1公司所有外协加工/采购物料由品质部IQC人员予以检验,如发现来料与品质标准存在差异,但属于生产急用之物料,由采购科/计划科填写《紧急放行单》,品质部召集召开MRB会议;4.2.2制程在途与仓储异常物料,本车间无法修补的,由车间填写《产品质量异常信息反馈单》反馈至品质部,由品质部判定是否召集召开MRB会议;4.3 MRB评估4.3.1计划科:提供客户交期、计划编制、出货排程及补单安排;4.3.2 生产部:提供异常物料所造成进度影响,明确执行单位能否协助代加工/挑选,并承诺完成时间;4.3.3 技术部:评估异常物料能否正常使用,并提供技术支持;4.3.4 采购科:供应商信息沟通,供应商生产状况及供应商之回复,明确MRB产生费用归属,回复供应商返工之完成时间并办理退货、补货手续;4.3.5 业务部:客户沟通及确认;4.3.6 品质部:明确异常物料品质影响程度,判定结果【特采/返工/代加工/挑选/退货/正常使用】,判定责任承担单位并跟进MRB执行结果确认;4.3.7责任承担按《品质异常经济责任承担管理办法》实施;4.4 MRB评估决议及决议执行4.4.1 MRB评估内容须达成决议【特采/返工/代加工/挑选/退货/正常使用】并由品质部以《MRB评审记录表》记录存档,并通过公司邮箱传递相关部门;4.4.2 MRB小组成员须在《MRB评审记录表》签名确认;4.4.3 属生产部协助供应商代加工/挑选,则由生产部记录耗损的成本【工时/材料】,并填写《返修耗时/耗料记录表》上报采购科/财务部门;4.4.4 属品质部MRB全检执行挑选或代加工的(包括本厂制程产生的不良),由品质部负责将MRB产生费用及责任进行划分,并填写《返修耗时/耗料记录表》上报采购科/财务部,财务部执行扣款;4.5 MRB执行结果监督及确认4.5.1 品质部对MRB决议执行之结果予以监督,并判定是否符合要求;4.6 MRB全检组成人员4.6.1品质部品检科下属检验人员为主要实施人员;4.6.2 生产执行车间属MRB临时实施人员;4.7 实施4.7.1《MRB作业管理办法》自颁发日起实施;5.0 附件5.1《产品质量异常信息反馈单》;5.2《MRB评审记录表》;5.3《返修耗时/耗料记录表》;5.4《紧急放行单》;5.5《品质异常经济责任承担管理办法》;。
MRB作业管理办法
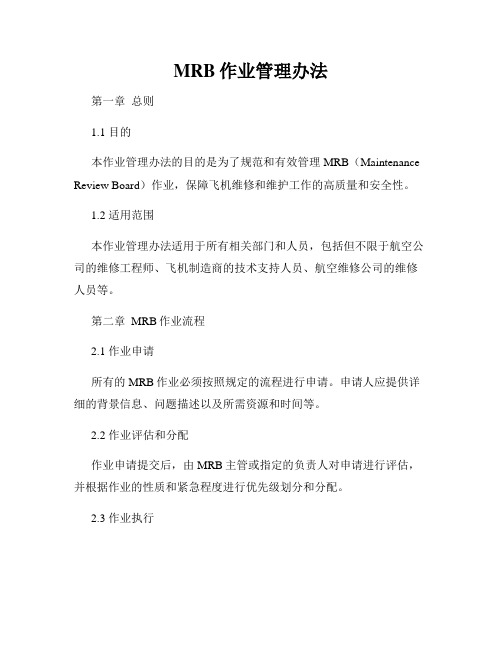
MRB作业管理办法第一章总则1.1 目的本作业管理办法的目的是为了规范和有效管理MRB(Maintenance Review Board)作业,保障飞机维修和维护工作的高质量和安全性。
1.2 适用范围本作业管理办法适用于所有相关部门和人员,包括但不限于航空公司的维修工程师、飞机制造商的技术支持人员、航空维修公司的维修人员等。
第二章 MRB作业流程2.1 作业申请所有的MRB作业必须按照规定的流程进行申请。
申请人应提供详细的背景信息、问题描述以及所需资源和时间等。
2.2 作业评估和分配作业申请提交后,由MRB主管或指定的负责人对申请进行评估,并根据作业的性质和紧急程度进行优先级划分和分配。
2.3 作业执行作业执行包括问题分析、解决方案的制定与评估、实施和验证等环节。
作业执行人员应按照规定的要求和流程进行操作,并记录相关的数据和信息。
2.4 作业审查作业执行完成后,应进行作业审查。
审查过程中,应对作业的合规性、质量和安全性进行评估,并记录审查结果和意见。
2.5 作业关闭和文档存档作业审查通过后,作业应进行关闭,并将相关文档进行存档。
存档的文档应按照规定的要求进行整理、归类和保存,以备将来参考和审查。
第三章作业管理要求3.1 作业规范所有的MRB作业必须按照相关的技术规范和标准进行操作。
作业执行人员应严格遵守规范,确保操作的准确性和可靠性。
3.2 问题分析与解决方案对于作业中出现的问题,应进行全面细致的分析,并提出合理可行的解决方案。
解决方案应考虑技术、经济和安全等方面的因素,并经过评估和验证确认后方可实施。
3.3 数据管理作业过程中产生的数据和信息应进行有效的管理和记录。
相关人员应确保数据的准确性和完整性,并妥善保存数据以供参考和汇总分析。
3.4 作业报告每个MRB作业应编写相应的作业报告。
作业报告应包括作业的目的、过程、结果和评估等内容,并按照规定的格式进行编写和提交。
第四章质量控制与改进4.1 质量控制MRB作业的质量控制是保障作业质量的重要环节。
MRB作业办法

结果反馈 IQC 记录。 5.9.3 判〝直接特采使用〞者,可直接上线使用,IPQC 须作质量追踪并及时反映异常。
5.10 QE 工程师在最终判定时可视需要决定是否发行《来料品质异常反馈单》;
5.11 MRB 的时效为 3 个工作日.逾期则作退货处理. 六、参考文件:
6.1 SPK-P18《进料检验管理程序》 6.2 SPK-P23 《不合格品管理程序》 七、使用表单: 7.1 SPK-P18-R04《来料品质异常反馈单》
草拟 审核 核准
品质
会ห้องสมุดไป่ตู้
生产
签
研发
营销
采购执行 资源开发 计划物控 生产工程
作业规范
编号 SPK-P18-W01 名称 MRB 作业办法 依据 进料检验管理程序
版本
A
页次
3/2
一、目的:
当进料检验发生材料不符合规格或不良超过 AQL 时,在不影响产品质量及保证生产的 条件下决定该材料是否可以上线使用的管理办法;
二、范围:
本办法适用于当进料检验时,发现原材料、半成品、自制品之检验被判定为不合格之情 况;
三、权责: 3.1 IQC: 来料质量的检验、判定; 3.2 其它部门:MRB 讨论的参与;
四、定义: 无
五、作业内容:
5.1 IQC 检验员在入料检验时发现材料不良超出要求规定时,该批材料将被判为不合格,
即开立不合格「进料检验报告」,并附不良样品送 QE 工程师审核;
5.2 QE 工程师确认无误后,IQC 在材料外包装上加贴 “不合格”标签;
5.3 由 IQC 填写「不合格材料审核记录表」,其中必须包含以下项目: 不良项目、不良数
量或不良率、AQL 值等。
5.4 IQC 将「不合格材料审核记录表」送计划物控处理;
MRB

MRBMRBabbr.1. =Material Review Board (美国)材料审查委员会2. =Mutual Reinsurance Bureau 再保险互助局3. =Maintenance review board 维修审查委员会品质会议:MRB的全称是Material Review Board, 中文意思是材料审查会议。
它是针对所有检验工作站发现产品异样状态暂时不能确定是否为缺陷的一种处理办法。
这里的工作站包括进料检验,过程检验,出货检验以及客户退回的产品。
根据不确定缺陷发现的位置,MRB会议可由不同的人召集。
如在进料检验过程中发现原材料有异常,当进料检验工程师不能确定时,他可召集MRB会议。
MRB可邀请项目经理,采购工程师,过程控制工程师,计划参加,如有必要可以邀请质量经理和生产经理加入以加速问题的解决。
通过MRB会议一般可得出下列结论:1.继续使用; 2.需要返工后使用; 3. 报废; 4.退回供应商要求换货。
其对应的英文说法分别为:1、Use as it(简写为UAI);2、Use after reworking or sorting;3、Scrap;4、Return to vendor(RTV)。
MRB能使相关的人在第一时间知道问题的存在,并且能加快问题的解决。
RMA与MRB悬赏分:30 |解决时间:2010-7-20 13:18 |提问者:我的宝贝玲一次与客户的交流会议上客户针对我们的订单提出了这两个问题!我不太明白,有了解的请回答下,要详细的哦最佳答案RMA:return material to Authorization是指把不良品退运到厂商指定的授权点/维修中心。
通常说的RMA即为这整个退运的一个过程,在制定整个RMA流程时需包括几个部分:1)物流路径;2)双方责任义务,包括报关/运费的运费划分;3)还货要求,是否为维修品或者新品?多久之内必须归还?等等跟RMA相对的还有的DOA(dead on arrival) 一到就死的那些产品,处理方式基本上跟RMA相同MRB:Material Review Board 原意是“材料审查委员会”在一般的企业里面通常会设立一个MRB仓,主要是用来对检验过程中发现的异样产品或者在客户端检验的过程中被批退的,但是又不能确认是否为缺陷品所管理的一种方式和仓别物料审查委员会(MRB)运作及物料报废作业指引默认分类2007-05-10 09:09:15 阅读38 评论0 字号:大中小订阅物料审查委员会(MRB)运作及物料报废作业指引文件名称物料审查委员会(MRB)运作及物料报废作业指引版次 1.0文件编号 BY-GC-008 页数 3-1编制绿草地审核张为博生效日期 2007/1/251.目的制定程序,使得产品实现过程中的不合格品、过期、积压物料等得到合适处理,规范物料的报废。
MRB作业细则
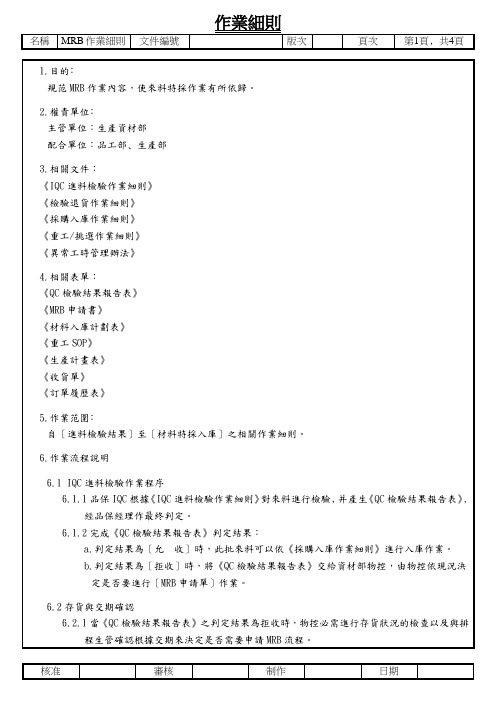
1.目的﹕規范MRB作業內容,使來料特採作業有所依歸。
2.權責單位﹕主管單位:生產資材部配合單位:品工部﹑生產部3.相關文件:《IQC進料檢驗作業細則》《檢驗退貨作業細則》《採購入庫作業細則》《重工/挑選作業細則》《異常工時管理辦法》4.相關表單:《QC檢驗結果報告表》《MRB申請書》《材料入庫計劃表》《重工SOP》《生產計畫表》《收貨單》《訂單履歷表》5.作業范圍﹕自〔進料檢驗結果〕至〔材料特採入庫〕之相關作業細則。
6.作業流程說明6.1 IQC進料檢驗作業程序6.1.1品保IQC根據《IQC進料檢驗作業細則》對來料進行檢驗﹐并產生《QC檢驗結果報告表》,經品保經理作最終判定。
6.1.2完成《QC檢驗結果報告表》判定結果:a.判定結果為〔允收〕時,此批來料可以依《採購入庫作業細則》進行入庫作業。
b.判定結果為〔拒收〕時,將《QC檢驗結果報告表》交給資材部物控,由物控依現況決定是否要進行〔MRB申請單〕作業。
6.2存貨與交期確認6.2.1當《QC檢驗結果報告表》之判定結果為拒收時,物控必需進行存貨狀況的檢查以及與排程生管確認根據交期來決定是否需要申請MRB流程。
6.2.2物控確認庫存狀況時,要比對:a.生產《生產計畫表》及《訂單履歷表》之出貨交期b. 倉庫的存貨資料6.2.3物控確認庫存狀況的目的在於確認此批材料一旦退貨是否會影響生產《生產計畫表》。
a.不會影響生產《生產投料投程表》,則由物控在《QC檢驗結果報告表》資材確認欄位勾選不急用并簽核至資材經理﹐并將《QC檢驗結果報告表》退回 IQC﹔b.若影響《生產計畫表》,且交期無法變更的﹐則由物控開立MRB申請需求﹐簽核至工程﹑生產﹑品保單位﹐再由協理根據工程﹑生產﹑品保意見做出最終栽決材料是否允收﹔6.2.4《MRB申請單》共一式五聯第一聯:倉庫聯第二聯:品保(IQC)聯第三聯:資材過賬員第四聯:生產聯第五聯﹕資材留檔6.3檢驗退貨作業程序6.3.1一旦《QC檢驗結果報告表》被品保經理判定〔拒收〕且物控判定為〔不急用〕,則物控將《QC檢驗結果報告表》退回品保(IQC)。
MRB作业管理办法

1.目的为确保本公司所有的不良品评审流程有所依据,故制订此作业指导书。
2.适用范围适用于本公司所有生产线上所有不良品的评审、处置。
3. 权责3.1品保:评估不合格项目对客户品质特性的影响;处理结果结案确认;3.2制造:负责线上不良品典型样品的收集、不良数量统计、评审结果执行;3.3生技:不良品重工处理;3.4业务:客户端特采申请;3.5生管:主持MRB鉴审会,开立《重工单》、《特采申请单》,不良品处理结果追踪;3.6采购:原材料不良处理。
4.作业内容4.1制造部将每日生产线上超品保部检验标准书、外观检验规范之规格的不良品以不同产品、不同缺陷类别按不同等级标识隔离,放置在评审区域待判。
4.2制造部将不良品中典型样品收集好,并作不良数量的统计,每周由生管单位组织各部门相关评审人员执行MRB鉴审会。
4.2.1 MRB鉴审会一般一周执行一次,如遇下列情况可临时召开MRB会议:4.2.1.1 进料异常影响到生产排程的;4.2.1.2 制程批量性不良影响交货的;4.2.1.3成品出货时发现重大品质异常影响出货的;4.2.1.4引起品质争议的。
4.2.2 各部门相关评审人员接到通知后,立即到指定地点参加MRB鉴审会议,评审参加人员为:制造部、品保部、生技、业务、生管、采购(非原材料不良采购可以不参加)。
4.2.3会议由生管单位主持,评审时参照不合格典型样品进行描述,以及不合格品对客户产品的性能、可靠性、安全性及外观的影响程度,经过PE、品保、生管、业务、采购、制造生技部门评审人员对不合格品的分析、评判,必要时进行实际组装及特性试验,相关单位提出意见后作出退货、特采、重工、报废、全检之决议,做成《会议记录》分发到个相关单位。
4.3不合格品如可申请特采由业务向客户提出申请,如客户同意,生管及时开立《特采申请单》请个部门会签,并在成品外箱上标识特采品或由客户提供标签标识其状态后正常出货。
4.4不合格品如可进行重工由生管开出《重工单》,制造生技提出重工方法,对重工人员教育训练,执行重工作业流程。
MRB作业管理办法

检验报表
MRB申请
由相关单位提出MRB处理表
急用料的优先处理
采购部 生产部 PMC
MRB处理表
MRB会签
MRB处理表位先将申请单交给品质部经理会签,再由品质部经理根据具体的异常状况,决定需会签部门。
当有严重的品质事件或同样的品质问题重复发生时,品质部需针对此问题开出8D改善报告交责任单位改善;最终判定由总经理签核。
7.1 《MRB处理表》
7.2 《质量索赔通知单》
8.0附件
8.1 MRB作业流程图
步骤
作业内容
管理要点
负责
单位
相关表单
需求提出
原物料、逾期物料、挪用物料的申请由采购提出,委外加工品由PMC提出,半成品,成品的由生产部提出。
☆当IQC或IPQC检验发现原材料不良但为急料时;半成品,成品有瑕疵,不影响产品性能但客户急需时;逾期物品再检不合格;挪用物料采购提出申请处置时。
3.0定义
3.1 MRB:材料审查小组
3.2 MRB成员:工程和品质必需参与,生产、采购、PMC、销售等与不合格物品审查及处理相关之单位主管或其代理人也可参与审查。
3.3 MRB会议:针对申请MRB检讨之原物料、半成品、成品、挪用物料或逾期物品由MRB成员参加而举行之研判会。
3.4 重要的不良:指MRB所处理的,由于产品的功能与工程文件要求不符合造成的,或是由客户收到产品后所通知的外观不良。
5.2.3逾期物品再验不合格,使用单位提出申请处置时;
5.2.4挪用物料,提出申请处置时。
5.3 特采之限制---下列情况者应限制,不能裁决同意特采使用:
5.3.1有影响安全或影响产品电气性能或使用性能;
5.3.2有遭客户抱怨或经向客户申请而未被同意时;
MRB作业流程范文

MRB作业流程范文MRB(Materials Review Board)作为一个重要的制造工艺控制手段,对于产品制造过程中的原材料选择和使用具有关键性的作用。
本文将详细介绍MRB的工作流程。
一、MRB作业流程概述1.问题发现:问题可以由多个渠道发现,如质量抽样检测、自行发现等。
问题发现可以包括产品不合格、零部件损坏、制造过程中的异常等。
2.问题报告:问题被发现后,需要将问题报告提交给MRB团队。
问题报告应包括问题的详细描述、触发问题的原因和发现问题的具体位置等信息。
3.问题分析:MRB团队负责对问题进行详细的分析。
分析包括原材料的制造工艺、生产过程中的工艺参数、设计规范和质量要求等方面。
4.问题解决:根据问题分析结果,MRB团队将提出相应的解决方案。
解决方案可以包括原材料的更换、制造工艺的调整、生产工艺参数的变更等。
5.问题关闭:经过一段时间的实践验证,如果解决方案有效并得到确认,MRB团队将关闭该问题。
如果问题仍存在或解决方案不可行,则需要重新进入问题解决流程。
二、MRB作业流程详细解析1.问题发现问题发现可分为内部发现和外部发现两种情况。
内部发现:公司内部通过生产质量抽样检测、过程异常统计等方式发现问题。
外部发现:供应商、客户或第三方检测机构通过检测报告、客户投诉等方式发现问题。
2.问题报告问题报告需要包括以下内容:问题描述:清楚描述问题的性质、影响范围和可能的原因。
问题位置:指出问题所在的部件、工序、供应商等。
影响程度:描述问题对产品质量和制造周期的影响,以及可能引起的额外成本。
3.问题分析问题分析是MRB的核心环节,对问题进行深入分析,为解决方案的制订提供依据。
总体分析:全面了解问题的性质、影响范围,并确定解决问题的必要性。
根本原因分析:通过追溯问题发生的根本原因,如质量不合格的原因、工艺参数设置错误等。
影响评估:对问题的影响范围、可能引起的成本和时间延误进行评估。
4.问题解决问题解决是MRB的目标,需要提出解决方案并实施。
07.MRB作业办法.doc

一.适用范围:1.1 进料部分(进料检验判退部分)1.1.1 品质差异轻微超出允收水准,而生产急用者,但涉及品质标准(差异),设计规格(功能)及生产技术(结构组合技术)等,不易判定是否影响产品品质及生产技术。
1.1.2采购需求1.2 生产线部分(含已上线之原材料,半成品及成品部分)1.2.1生产线异常,经PE判定为材料不良。
二.目的:对不合格品进行适当的处理,以减少不良品积压,同时便于不良品改善及追踪。
三. 定义:3.1 半成品:已部分加工并且等待继续加工之材料。
3.2 成品:已完成加工而可以销售之产品。
四.说明:4.1进料部分流程物料收料OKIQC检验原料仓NGQE会签会相关单位召开MRB meetingWaive特采重工/sorting Reject4.1.1 IQC将退货讯息以电话方式知会QE和生管。
4.1.2生管依据生产计划物料紧急程度判定是否召开MRB meeting,并以通知QE,由QE召集相关单位(可采用会议形式或会签形式)。
4.1.3涉及单位如下:品质异常:生产,品管,生管,QE。
如有需要可要求其它相关单位参加,参加人员为各单位课级或课级以上主管指定代理人,并核签处理意见。
4.1.4 MRB会议做出以下决定:4.1.4.1针对退货之不良批,IQC依《不合格品控制程序》处理,由IQC通知生管于2日内要求厂商运回.4.1.4.2重工或SORTING针对原材料重工/SORTING,经MRB会议于“不合格品处理单”注明重工/SORTING方式,由生管通知厂商处理,需经IQC再次检验,如第二次检验仍判退,IQC有权拒收该LOT.4.1.4.3特采原材料,半成品,成品不符合原定规格而判定不会影响最终品质者依“特采申请单“特采,并由IQC于材料外箱贴附”特采”标签并注明MRB NO.如确属原材品质不良导致, 可经MRB会议决定追加扣款.4.1.5如因材料未承认退货依以下方式作业:A.用于or test阶段的材料,由台湾公司转售之材料,生管于“不合格品处理单”上注明“此批材料用于新机种试投”字样后, 生管部门主管签字即可.B.量产后未承认:由生管会签工程并Release to IQC.4.2生产线品质异常生产线品质异常IPQC判定原材料品质不良QE相关单位召开MRB meetingWaive特采 Rework/Sorting4.2.1生产线异常,由生管提出会议需求并通知QE.IPQC依据在开出“不合格品处理单“的同时暂停使用产品并贴附“不良标签”,由QE召集相关单位召开MRB meeting.4.2.2涉及单位如下:QE 生管 IQC 仓库生产如有需要可要求其他相关单位参加。
MRB作业流程需要修改

MRB作業流程一、目的:瞭解不良品資訊並及時處理不良品,快速有效確認品質缺陷,明確品質責任並降低損失,特制定本制度。
二、定義:1、MRB:Material Review Board 材料審查委員會,主要負責進料檢驗,過程檢驗,出貨檢驗以及客戶退回的産品的相關處理,一般由質量部、工程部、銷售部、採購部、PMC及生産部相關人員參與。
根據不確定缺陷發現的位置,MRB會議可由不同的人召集。
2、特采:未確認或不合格品,經一定之申請與核准,予以特采使用,稱之特采。
3、挑選:對判定不合格之原材料、半成品及成品,對不合格專案予以100%全檢,以區分良品與不良品,稱之挑選。
4、重工:對部份不良品可用重新加工或維修之方式,予以修理使其成爲合乎規格之産品,稱之重工。
5、報廢:對判定不合格之原材料、半成品及成品無法重新且又不符合乎特采之原則,經一定之程式予以銷毀及除帳。
6、退貨:已知材料無法按照2-4處理時則退回供應商處理。
三、三、範圍:適用於生産急用但與品質標準存在差異,需承擔客訴風險之物料,且生産部(含供應商和外協廠商)自身無法處理的物料管理,包括下述內容:1、進料類【外協加工/採購物料經檢驗判退物料】;2、制程或在途類【制程加工在途物料/半成品及配件經檢驗判退物料】;3、倉儲類【倉儲半成品及配件等物料經檢驗判退物料】。
四、職責許可權1、MRB小組組長:一般由質量部經理擔任,主要負責判定不合格物料處理結果及明確責任承擔部門;2、MRB小組成員:由生産部、PMC、採購部、工程部、銷售部參加,必要時將臨時邀請相關人員。
主要參與不合格物料評估並執行MRB決議,明確品質異常經濟責任承擔及改善執行。
五、職責許可權1、物料異常産生及MRB提出:1)公司所有外協加工/採購物料由品質部IQC人員檢驗,如發現來料與品質標準存在差異,但屬於生産急用之物料,由採購科/PMC/生産部填寫《緊急放行單》,品質部召集召開MRB會議;2)制程、在途或倉儲異常物料,生産部無法重工、挑選的,由生産部填寫《品質異常聯絡單》MRB作业流程版本:A.0文件编号:2013-HM-Q/QG- 实施日期:2013/10/25 编制:总办/范丽娟页数:反饋至品質部,由品質部判定是否召集召開MRB會議。
MRB作业指导书 -

MRB作业指导书 -引言概述:MRB(Material Review Board)作业指导书是一份重要的文档,用于指导MRB 团队在产品质量问题浮现时的处理流程。
本文将从五个大点出发,详细阐述MRB 作业指导书的内容和重要性。
正文内容:1. MRB作业指导书的概述1.1 MRB作业指导书的定义和目的1.2 MRB作业指导书的适合范围和使用对象1.3 MRB作业指导书的重要性和作用2. MRB作业指导书的组成部份2.1 问题描述和分类2.2 MRB团队的组成和职责2.3 问题解决流程和决策制定2.4 数据分析和记录2.5 问题解决方案的评估和验证3. MRB作业指导书的具体步骤3.1 问题发现和报告3.2 MRB团队的召集和会议3.3 问题分析和数据采集3.4 解决方案的制定和评估3.5 解决方案的实施和验证4. MRB作业指导书的注意事项4.1 保持信息的准确性和及时性4.2 持续改进和更新指导书4.3 建立有效的沟通和合作机制4.4 遵守相关法规和标准5. MRB作业指导书的效益和应用案例5.1 优化问题解决流程,提高效率5.2 提高产品质量和客户满意度5.3 降低成本和风险总结:MRB作业指导书是一份重要的文档,它指导MRB团队在产品质量问题浮现时的处理流程。
本文从概述、组成部份、具体步骤、注意事项和效益等方面详细阐述了MRB作业指导书的内容和重要性。
通过合理使用MRB作业指导书,企业可以提高问题解决效率,优化产品质量,降低成本和风险,从而提升竞争力和客户满意度。
因此,建议企业建立和完善MRB作业指导书,并持续改进和更新,以适应不断变化的市场需求和质量管理要求。
- 1、下载文档前请自行甄别文档内容的完整性,平台不提供额外的编辑、内容补充、找答案等附加服务。
- 2、"仅部分预览"的文档,不可在线预览部分如存在完整性等问题,可反馈申请退款(可完整预览的文档不适用该条件!)。
- 3、如文档侵犯您的权益,请联系客服反馈,我们会尽快为您处理(人工客服工作时间:9:00-18:30)。
一.适用范围:
1.1 进料部分(进料检验判退部分)
1.1.1 品质差异轻微超出允收水准,而生产急用者,但涉及品质标准(差
异),设计规格(功能)及生产技术(结构组合技术)等,不易判
定是否影响产品品质及生产技术。
1.1.2采购需求
1.2 生产线部分(含已上线之原材料,半成品及成品部分)
1.2.1生产线异常,经PE判定为材料不良。
二.目的:
对不合格品进行适当的处理,以减少不良品积压,同时便于不良品改善及追踪。
三.定义:
3.1 半成品:已部分加工并且等待继续加工之材料。
3.2 成品:已完成加工而可以销售之产品。
四.说明:
4.1进料部分流程
物料收料
OK
IQC检验原料仓
NG
QE会签
Waive特采重工/sorting Reject
4.1.1 IQC将退货讯息以电话方式知会QE和生管。
4.1.2生管依据生产计划物料紧急程度判定是否召开MRB meeting,并以
通知QE,由QE召集相关单位(可采用会议形式或会签形式)。
4.1.3涉及单位如下:
品质异常:生产,品管,生管,QE。
如有需要可要求其它相关单位参加,参加人员为各单位课级或课级
以上主管指定代理人,并核签处理意见。
4.1.4 MRB会议做出以下决定:
4.1.4.1针对退货之不良批,IQC依《不合格品控制程序》处理,由IQC
通知生管于2日内要求厂商运回.
4.1.4.2重工或SORTING
针对原材料重工/SORTING,经MRB会议于“不合格品处理单”注
明重工/SORTING方式,由生管通知厂商处理,需经IQC再次检验,
如第二次检验仍判退,IQC有权拒收该LOT.
4.1.4.3特采
原材料,半成品,成品不符合原定规格而判定不会影响最终品质
者依“特采申请单“特采,并由IQC于材料外箱贴附”特采”标
签并注明MRB NO.如确属原材品质不良导致, 可经MRB会议决
定追加扣款.
4.1.5如因材料未承认退货依以下方式作业:
A.用于or test阶段的材料,由台湾公司转售之材料,生管于“不
合格品处理单”上注明“此批材料用于新机种试投”字样后, 生管
部门主管签字即可.
B.量产后未承认:由生管会签工程并Release to IQ
C.
4.2生产线品质异常
生产线品质异常
IPQC判定
原材料品质不良
QE相关单位召开MRB meeting
Waive特采 Rework/Sorting
4.2.1生产线异常,由生管提出会议需求并通知QE.
IPQC依据在开出“不合格品处理单“的同时暂停使用产品并贴附“不
良标签”,由QE召集相关单位召开MRB meeting.
4.2.2涉及单位如下:
QE 生管 IQC 仓库生产
如有需要可要求其他相关单位参加。
生产:须提供在制部分,成品/半成品/物料数量;
仓库:须提供库存材料,成品/半成品/准确数量;
生管:提供出货排程。
4.2.2.1重工或Sorting
在制品,半成品及成品重工/SORTING,由生产制定REWORK
PROCESS,由生管安排重工/SORTING.
4.2.2.2 Waive特采
原材料,半成品,成品不符合原定规格而经判定不会影响最终
品质者于“不合格品处理单”记录特采,并由IQC材料外箱贴
附“特采”标签并注明MRB NO,如确属原材品质不良导致,
可经MRB会议决定追加扣款。
4.3 IQC综合各单位意见,由IQC将“不合格品处理单”发文于各单位(制造,
品管,生管,IQC)并存档,各单位须依会议结论执行.
4.4 IQC针对品质不良部分依据《不合格品控制程序》执行,开具“纠正和预
防措施表”给生管转交厂商并跟催其回复.
五.参考文件:
5.1 《不合格品控制程序》
5.2《纠正和预防措施控制程序》。