船机零件的疲劳破坏讲义
Chapter2 船机零件的磨损

Chapter2 船机零件的磨损
§2-1 摩擦(Friction)
摩擦磨损是船机零件的故障模式之一,是影响船舶机器正常运转和船舶安全航行的主要因素。
据资料介绍:世界能源的1/3~1/2是以不同形式消耗在克服机械零件对偶表面相互作用的摩擦上。对于船用柴油机来说,目前无论是二冲程的低速机还是四冲程的中速机,燃油消耗率已降至163 g/(kW·h)左右,热效率达到50 %以上,但能量消耗在运动副的摩擦上约占10 %左右。
摩擦磨损→故障→能源浪费→必须重视
1 摩擦表面的性质
1.1摩擦表面的形貌(Surface Layer morphology)和表示方法
外圆表面粗车会使表面产生100μm~25μm的粗糙度,抛光或超精研磨加工产生0.1μm~0.012μm的粗糙度。
零件表面的几何形态称为表面形貌。零件表面形貌分
为宏观几何形状、表面波度和粗糙度(微观几何形状)三部分。
宏观几何形状——宏观所见表面的轮廓线产生偏离名义几何形状的粗大偏差;
表面波度——形成周期性的波状表面峰和谷,是由于机床加工系统振动的结果,为介于形状误差与粗糙度之间的误差;
粗糙度——表面轮廓微观几何形状误差。
实际表面与理想表面存在一定的几何形状误差,表现在两个方面:
(1)几何形状误差(宏观上):用圆度、圆柱度、平面度表示。
(2)表面微观几何形状误差:粗糙度。Ra
评定表面粗糙度的方法很多,常用的一种方法是轮廓算术平均偏差Ra,表面粗糙度分为14级。
1.2表面层的结构(Surface Layer Composition)
金属表面一出现,就会与空气中的各种其它起作用而形成各种膜,这些膜的结构性质对摩擦性能的影响很大。一般讲,这些膜是有益的,有利于减少摩擦磨损。
机械设计中的疲劳分析
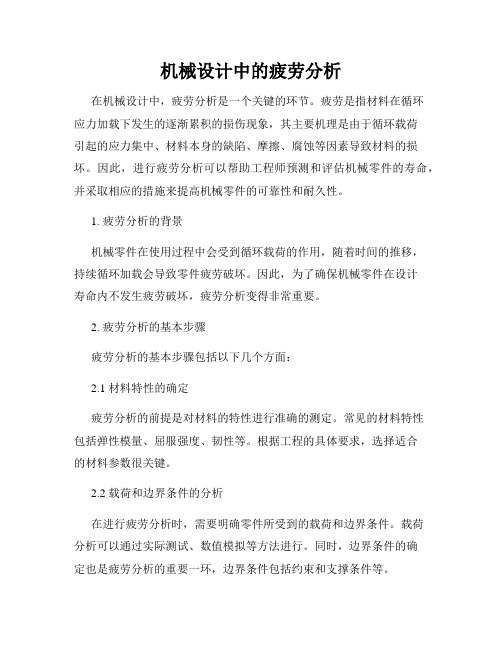
机械设计中的疲劳分析
在机械设计中,疲劳分析是一个关键的环节。疲劳是指材料在循环
应力加载下发生的逐渐累积的损伤现象,其主要机理是由于循环载荷
引起的应力集中、材料本身的缺陷、摩擦、腐蚀等因素导致材料的损坏。因此,进行疲劳分析可以帮助工程师预测和评估机械零件的寿命,并采取相应的措施来提高机械零件的可靠性和耐久性。
1. 疲劳分析的背景
机械零件在使用过程中会受到循环载荷的作用,随着时间的推移,
持续循环加载会导致零件疲劳破坏。因此,为了确保机械零件在设计
寿命内不发生疲劳破坏,疲劳分析变得非常重要。
2. 疲劳分析的基本步骤
疲劳分析的基本步骤包括以下几个方面:
2.1 材料特性的确定
疲劳分析的前提是对材料的特性进行准确的测定。常见的材料特性
包括弹性模量、屈服强度、韧性等。根据工程的具体要求,选择适合
的材料参数很关键。
2.2 载荷和边界条件的分析
在进行疲劳分析时,需要明确零件所受到的载荷和边界条件。载荷
分析可以通过实际测试、数值模拟等方法进行。同时,边界条件的确
定也是疲劳分析的重要一环,边界条件包括约束和支撑条件等。
2.3 使用应力历程进行分析
应力历程是指在给定载荷和边界条件下零件所受到的应力变化情况。通过计算应力历程,可以得到零件在不同工况下的应力状况,进而评
估疲劳寿命。
2.4 使用疲劳曲线进行分析
疲劳曲线是描述应力与寿命之间关系的图形表示。通过将实测的应
力历程与疲劳曲线进行比对,可以得到零件在给定工作条件下的疲劳
寿命。
3. 疲劳寿命评估
通过上述步骤的分析,可以得到零件的疲劳寿命。疲劳寿命评估对
于机械设计的合理性和可靠性至关重要,它关系到机械零件的安全性、稳定性和经济性。
4-1第一节 疲劳破坏
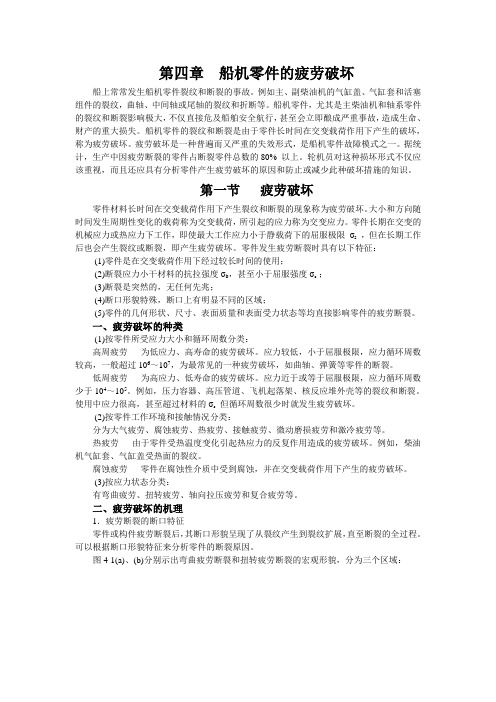
第四章船机零件的疲劳破坏
船上常常发生船机零件裂纹和断裂的事故。例如主、副柴油机的气缸盖、气缸套和活塞组件的裂纹,曲轴、中间轴或尾轴的裂纹和折断等。船机零件,尤其是主柴油机和轴系零件的裂纹和断裂影响极大,不仅直接危及船舶安全航行,甚至会立即酿成严重事故,造成生命、财产的重大损失。船机零件的裂纹和断裂是由于零件长时间在交变载荷作用下产生的破坏,称为疲劳破坏。疲劳破坏是一种普遍而又严重的失效形式,是船机零件故障模式之一。据统计,生产中因疲劳断裂的零件占断裂零件总数的80% 以上。轮机员对这种损坏形式不仅应该重视,而且还应具有分析零件产生疲劳破坏的原因和防止或减少此种破坏措施的知识。
第一节疲劳破坏
零件材料长时间在交变载荷作用下产生裂纹和断裂的现象称为疲劳破坏。大小和方向随时间发生周期性变化的载荷称为交变载荷,所引起的应力称为交变应力。零件长期在交变的机械应力或热应力下工作,即使最大工作应力小于静载荷下的屈服极限σs,但在长期工作后也会产生裂纹或断裂,即产生疲劳破坏。零件发生疲劳断裂时具有以下特征:
(1)零件是在交变载荷作用下经过较长时间的使用;
(2)断裂应力小干材料的抗拉强度σb,甚至小于屈服强度σs ;
(3)断裂是突然的,无任何先兆;
(4)断口形貌特殊,断口上有明显不同的区域;
(5)零件的几何形状、尺寸、表面质量和表面受力状态等均直接影响零件的疲劳断裂。
一、疲劳破坏的种类
(1)按零件所受应力大小和循环周数分类:
高周疲劳为低应力、高寿命的疲劳破坏。应力较低,小于屈服极限,应力循环周数较高,一般超过106~107,为最常见的一种疲劳破坏,如曲轴、弹簧等零件的断裂。
第一章机械零件失效的模式及其机理
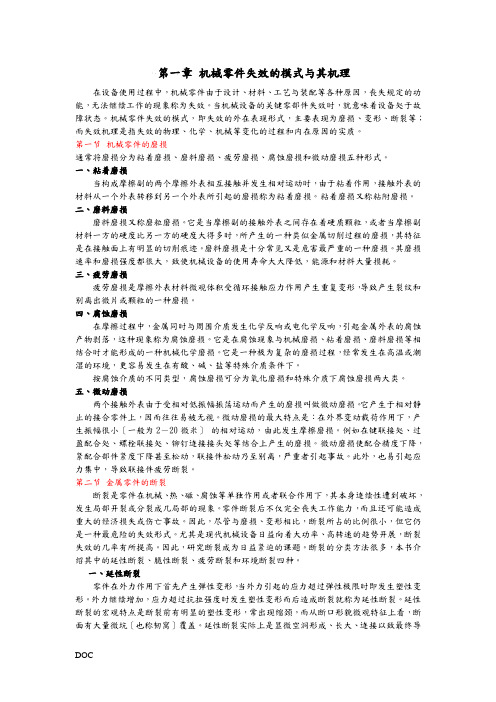
第一章机械零件失效的模式与其机理
在设备使用过程中,机械零件由于设计、材料、工艺与装配等各种原因,丧失规定的功能,无法继续工作的现象称为失效。当机械设备的关键零部件失效时,就意味着设备处于故障状态。机械零件失效的模式,即失效的外在表现形式,主要表现为磨损、变形、断裂等;而失效机理是指失效的物理、化学、机械等变化的过程和内在原因的实质。
第一节机械零件的磨损
通常将磨损分为粘着磨损、磨料磨损、疲劳磨损、腐蚀磨损和微动磨损五种形式。
一、粘着磨损
当构成摩擦副的两个摩擦外表相互接触并发生相对运动时,由于粘着作用,接触外表的材料从一个外表转移到另一个外表所引起的磨损称为粘着磨损。粘着磨损又称粘附磨损。二、磨料磨损
磨料磨损又称磨粒磨损。它是当摩擦副的接触外表之间存在着硬质颗粒,或者当摩擦副材料一方的硬度比另一方的硬度大得多时,所产生的一种类似金属切削过程的磨损,其特征是在接触面上有明显的切削痕迹。磨料磨损是十分常见又是危害最严重的一种磨损。其磨损速率和磨损强度都很大,致使机械设备的使用寿命大大降低,能源和材料大量损耗。
三、疲劳磨损
疲劳磨损是摩擦外表材料微观体积受循环接触应力作用产生重复变形,导致产生裂纹和别离出微片或颗粒的一种磨损。
四、腐蚀磨损
在摩擦过程中,金属同时与周围介质发生化学反响或电化学反响,引起金属外表的腐蚀产物剥落,这种现象称为腐蚀磨损。它是在腐蚀现象与机械磨损、粘着磨损、磨料磨损等相结合时才能形成的一种机械化学磨损。它是一种极为复杂的磨损过程,经常发生在高温或潮湿的环境,更容易发生在有酸、碱、盐等特殊介质条件下。
三等职务船员培训轮机教学大纲
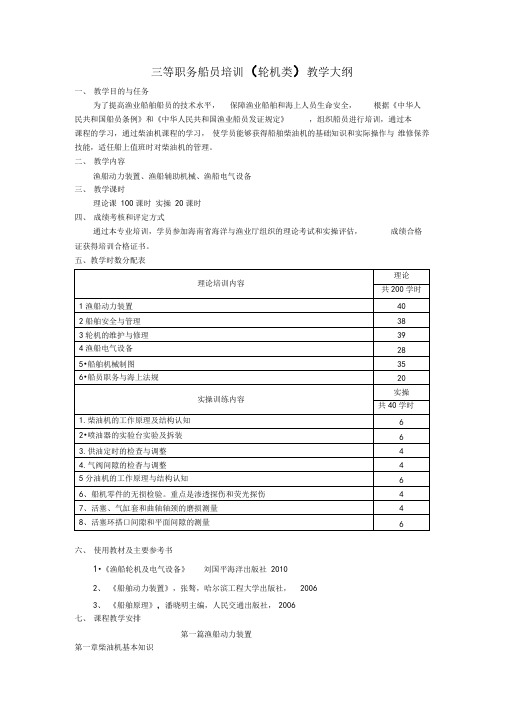
三等职务船员培训(轮机类)教学大纲
一、教学目的与任务
为了提高渔业船舶船员的技术水平,保障渔业船舶和海上人员生命安全,根据《中华人民共和国船员条例》和《中华人民共和国渔业船员发证规定》,组织船员进行培训,通过本
课程的学习,通过柴油机课程的学习,使学员能够获得船舶柴油机的基础知识和实际操作与维修保养技能,适任船上值班时对柴油机的管理。
二、教学内容
渔船动力装置、渔船辅助机械、渔船电气设备
三、教学课时
理论课100课时实操20课时
四、成绩考核和评定方式
通过本专业培训,学员参加海南省海洋与渔业厅组织的理论考试和实操评估,成绩合格证获得培训合格证书。
五、教学时数分配表
六、使用教材及主要参考书
1•《渔船轮机及电气设备》刘国平海洋出版社2010
2、《船舶动力装置》,张骜,哈尔滨工程大学出版社,2006
3、《船舶原理》,潘晓明主编,人民交通出版社,2006
七、课程教学安排
第一篇渔船动力装置
第一章柴油机基本知识
第一节柴油机的工作原理。
第二节柴油机的性能指标。
第三节现代船用柴油机提高有效功率和经济性的主要途径。二章柴油机的结构和主要部件
第一节现代船用柴油机的结构特点。
第二节活塞。
第三节气缸。
第四节气缸盖。
第五节燃烧室部件承受的机械负荷、热负荷及分析。
AW 、,FH 燃烧室部件的管理及其故障。
第七节连杆。
第八节曲轴和主轴承。
第九节曲柄连杆机构的故障和管理。
第十节推力轴承的工作原理。
第十一节十字头组件的组成、作用和结构特点。
第十二节柴油机固定部件。
第三章燃油的喷射与燃烧
第一节燃油的理化性能指标及影响。
第二节燃油的喷射及可燃混合气的形成过程。
轮机维护与修理 第二章(培训教材)讲解

重庆交通大学航海学院
09:23
轮机维护与修理
ChongQing JiaoTong University
油性剂、极压剂(抗磨剂)
20
• 油性剂、极压剂都能在边界润滑条件下起到减磨作用。各自机理是: 1)油性剂: • 带极性基团的活性物质,能定向吸附在金属表面上形成不易破坏的边界
边界膜类别:
吸附膜和化学反应膜。
特点:
a.边界膜的厚度很小(0.1μm),可使摩擦系数大大降低(0.05~0.5)。
b.摩擦磨损特性不取决于润滑剂的粘度,而是取决于表面膜的特性。
减少边界摩擦的方法:
• a.在普通工作条件的润滑剂中,加入油性添加剂,如:油酸、甘油等。
• b.在低速、重载的“极压条件”下的润滑剂中,加入极压添加剂,如: 酯。
重庆交通大学航海学院
09:23
轮机维护与修理
ChongQing JiaoTong University
②干摩擦 (Dry Friction)
定义:
• 表面既无润滑剂,又无湿气时的摩擦。
特点:
• 摩擦系数最大,约0.1~1.5。
机理:
• 粘着理论
结果:
• 干摩擦→磨损
•
→表面性质变化(塑性变形→加工硬化;
大连海事大学成教教学日历-大连海事大学继续教育学院
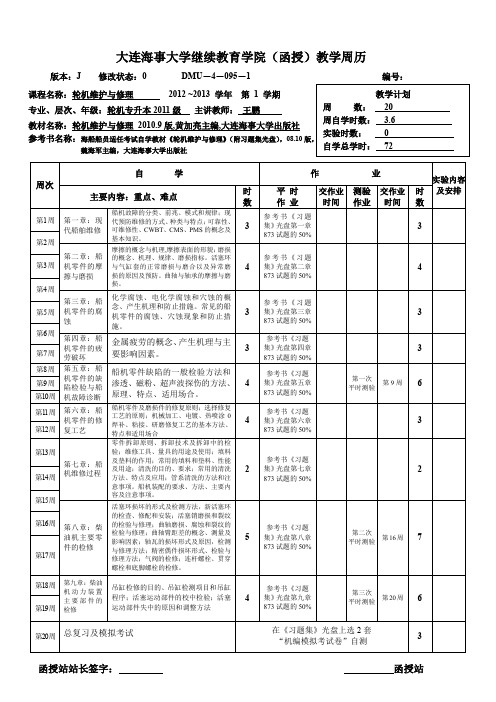
大连海事大学继续教育学院(函授)教学周历
版本:J 修改状态:0 DMU -4-095-1 编号:
课程名称:轮机维护与修理 2012 ~2013 学年 第 1 学期
专业、层次、年级:轮机专升本2011级 主讲教师: 王鹏
教材名称:轮机维护与修理 2010.9版,黄加亮主编,大连海事大学出版社
参考书名称:海船船员适任考试自学教材《轮机维护与修理》(附习题集光盘),08.10
魏海军主编,大连海事大学出版社 函授站站长签字: 函授站
连海事大学继续教育学院(函授)教学周历
版本:J 修改状态:0 DMU -4-095-1
课程名称:船舶电气设备及系统 2012 ~2013 学年 第1学期 专业、层次、年级:轮机工程专升本11级 主讲教师: 赵殿礼 教材名称:《船舶电气设备及系统》
函授站站长签字:函授站注:此表由各函授站保存
大连海事大学继续教育学院(函授)教学周历
版本:J 修改状态:0 DMU-4-095-1 编号:
教研室主任签字:陈海泉函授站站长签字:函授站
平时作业
第一次作业
1 .用50Hz交流电的电动往复泵如接60Hz电源,下列说法错的是:
A.泵阀敲击加重
B.吸、排压力脉动率增大
C.流量约提高50%
D.泵阀关闭滞后角增大
2 . 往复泵流量(单位为m3/h)估算式是(K为泵作用数;A为活塞有效工作面积,单位为m2;S为活塞行程,单位为m;n为曲轴转速,单位为r/min;η是泵的效率;ηv是泵的容积效率)
A.Q=KASnηv B.Q=KASnηC.Q=60KASnηD.Q=60KASnηv
3 .提高往复泵的()可避免产生“气穴”
船机零件的疲劳破坏

3)疲劳缺口敏感度
零件上开有键槽、油孔、台阶、螺纹等各种几何形状的 缺口时,在使用中就会在缺口的根部产生应力集中,使 材料的疲劳强度降低。采用缺口敏感度来表示疲劳强度 降低的程度。材料的缺口敏感度0<q<1。q值越小,缺口 越不敏感。铸铁对缺口极不敏感,q<0.1。一般结构钢对 缺口较为敏感,q=0.55~0.80
第四章 船机零件的疲劳破坏
在船机零件断裂中,疲劳断裂占80~90%。
曲轴、活塞、缸盖、齿轮、连杆螺栓等承受交变载荷的零件。
断裂危害
船机零件,尤其是主柴油机零件和轴系传动轴的 裂纹和断裂影响极大,不仅危及船舶的正常营运, 甚至会立即酿成严重事故,造成生命和财产的重 大损失。
本章重难点
重点:疲劳破坏的机理 难点:气缸盖和曲轴的疲劳破坏 要求掌握的知识点: ① 疲劳破坏的特征、种类、机理 ② 零件材料的疲劳强度影响因素 ③ 气缸盖和曲轴的疲劳破坏
2)表面状态和尺寸因素
(粗糙度、应力状态、成分和性能的变化等)
表面粗糙度越低,表面越粗糙,疲劳极限越低。 表面变形强化处理使表面塑性变形抗力增加,在表面层内形 成残余压应力,有效的提高疲劳极限。 材料的疲劳极限随试样尺寸增大而降低, 这种现象称为疲 劳强度的尺寸效应。
1-3-零件在交变载荷下的疲劳断裂解析
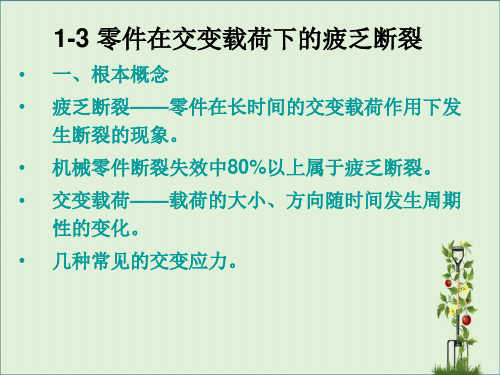
• 麻点磨损——接触疲乏。零件两接触面作滚动或滚 动加滑动时,在交变接触压应力的长期作用下,引 起外表疲乏剥落破坏。
• 特征:接触外表上消逝很多针状或痘状的凹坑,称 为麻点。
• 接触疲乏也是裂纹形成和扩展的过程。依据裂纹源 产生的部位不同,接触疲乏破坏有三种形式:裂纹 源于表层的麻点剥落;裂纹源于次表层的麻点剥落; 硬化层剥落。
• 氧化磨损——两零件外表相对运动时(不管是滑动摩擦或 是滚动摩擦),在发生塑性变形的同时,由于已形成的氧 化膜在摩擦接触点处遭到破坏,紧接着在该处又马上形 成新的氧化膜。
• 这样,便不断有氧化膜自金属外表脱离,使零件外表物 质渐渐损耗,这样的过程便称为氧化磨损。
• 是工程中最普遍存在的一种磨损形式。和其他类型磨损 比较,氧化磨损具有最小磨损速度。
产生塑性变形的现象。
• 蠕变断裂——由蠕变变形产生的断裂。 • 典型的蠕变曲线,图1-27。
分三个阶段:减速蠕变、恒速蠕变和加速蠕变
• 蠕变极限——高温长期载荷作用下材料反抗塑性变 形的力气。〔防止高温下过量塑性变形〕
• 两种表现方法:〔1〕在规定温度下,使试样产生规 定稳态蠕变速率的应力值бεT,〔2〕给定温度下和 规定时间内使试样产生确定蠕变总变形量的应力值 бδ/tT 。
• 二、高温氧化腐蚀:
• 金属的氧化过程包括三个步骤:〔1〕金属原子失 去电子成为金属离子;〔2〕氧原子吸取电子成为 氧离子;〔3〕金属离子和氧离子结合形成金属氧 化物。
第六章船机零件的修复工艺课件
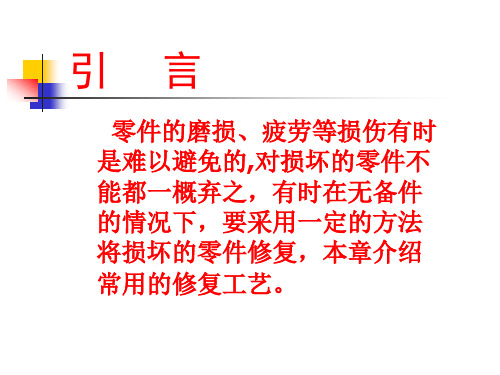
(7)喷涂层厚度可从0.05mm至几毫米。喷熔层的 最小厚度为0.8mm,一步法喷熔层厚度一般不大 于2mm;二步法每次喷熔层厚度为0.2~0.3mm, 可多次实施获得较大厚度的喷熔层。
二、粉末火焰喷涂
一、热喷涂工艺的种类
喷涂:有电弧喷涂、等离子喷涂、火焰 喷涂(包括爆炸喷涂、超音速喷涂)等。 喷涂材料为丝状或粉末状。
喷熔:有火焰粉末喷熔、等离子粉末喷 熔等。
热喷涂工艺的特点
(1)适用的材料范围广。各种金属或非金属 材料的表面均可获得预定性能的涂层。
(2)热喷涂材料广。金属及其合金、陶瓷、 有机树脂等均可作为涂层的材料。
修理尺寸等于磨损件实测尺寸加上(或减去)为消除 缺陷所需的最小加工余量
修理尺寸法简单、经济,可延长零件的使用寿命。 但使零件失去原有的互换性,给备件供应带来麻烦
最小加工余量修理;分级修理
尺寸选配法
集中一小批相同机型的已过度磨损的配合 件,分别进行机械加工消除配合表面的缺 陷和几何形状误差,再按原配合间隙值重 新配合成对。组成一些具有不同基本尺寸 但具有相同配合间隙的新的配合件。
(3)工艺简单下操作容易,涂层形成速度快, 加工时间短,生产率高。
(4)喷涂零件受热温度低,热应力小,变形 非常小。喷熔零件温度高,热应力大,容 易产生变形或裂纹。
疲劳强度模型和S-N曲线
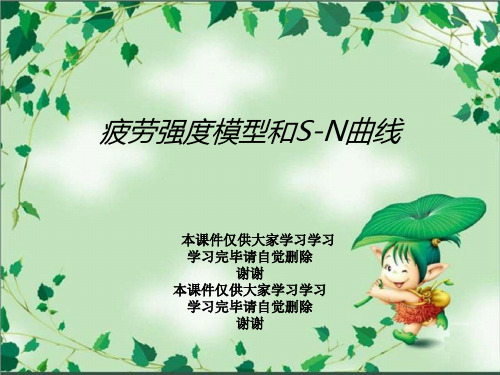
4、影响疲劳性能的若干因素 1)载荷形式 材料的疲劳极限随载荷形式的不同有下述
变化趋势: S(弯)>S(拉)>S(扭)
假定作用应力水平相同,拉压时高应力区 体积等于试件整个试验段的体积;弯曲情 形下的高应力区体积则要小得多。我们知 道疲劳破坏主要取决于作用应力的大小 (外因)和材料抵抗疲劳破坏的能力(内 因)二者,即疲劳破坏通常发生在高应力 区或材料缺陷处。假如图中的作用的循环 最大应力Smax相等,因为拉压循环时高应 力区域的材料体积较大,存在缺陷并由此 引发裂纹萌生的可能性也大。
a)载荷循环频率的影响显著
无腐蚀环境作用时,在相当宽的频率范围 内(如200Hz以内),频率对材料S-N曲线 的影响不大。但在腐蚀环境中,随着频率 的降低,同样循环次数经历的时间增长, 腐蚀的不利作用有较充分的时间显示,使 疲劳性能下降的影响明显。
b)在腐蚀介质(如海水)中,半浸入状态 (或海水飞溅区)比完全浸入更不利。
表面渗氮或渗碳处理,可以提高表面材料 的强度并在材料表面引入压缩残余应力, 这两种作用对于提高材料疲劳性能都是有 利的。试验表明,渗氮或渗碳处理可使钢 材疲劳极限提高一倍。对于缺口试件,效 果更好。
5) 环境和温度的影响
材料的S-N 曲线一般是在室温、空气环境 下得到的。在诸如海水、酸碱溶液等腐蚀 介质环境下的疲劳称为腐蚀疲劳。腐蚀介 质的作用对疲劳是不利的。腐蚀疲劳过程 是力学作用与化学作用的综合过程,其破 坏机理十分复杂。影响腐蚀疲劳的因素很 多,一般有如下趋势:
轮机维护与修理学习资料 第二章
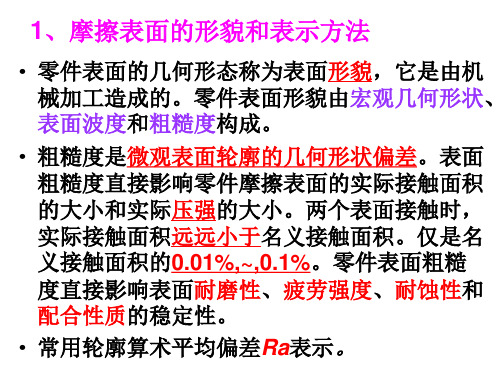
在元素周期表中相距较远的元素互溶性小。
• (2)金属的晶体结构 具有密排六方晶格的金属粘 着倾向大;体心和面心立方晶格的金属粘着倾向大;
• 单晶体粘着倾向大于多晶体;单相合金的粘着倾向大 于多相合金;固溶体的粘着倾向大于化合物;塑性材 料粘着倾向大于脆性材料。
• 2、磨粒磨损 在工业中磨粒磨损 是重要的磨损形式, 约占便50%。特别是矿山、建筑、粮食加工等机械。
• 三、气缸套的异常磨损
• 1、异常磨损Biblioteka Baidu特征
• (1)铸铁缸套磨损率>0.1mm/Kh,活塞环磨损率> 0.5mm/Kh。
• (2)缸套表面脏污,有明显划痕、擦伤、撕裂、拉缸、 咬缸等,缸壁表面有发蓝、烧灼等现象。
(3)磨损产物颗粒较大,磨屑直径达30μm • 异常磨损可通过测量缸径计算:磨损率、内径
磨损量
• 2)正常磨合期 特点是磨损速度降低 • 磨损量下且稳定。主要工作是 • 维护保养工作。
磨合期
正常磨 损期
急剧磨 损期 C
A
B
0
时间
3)急剧磨损阶段 零件的磨损量和几何形状误差较大,运
• 副配合间隙增大,配合性质变坏,以致振动、冲击,温度升 高,磨损加剧,进入急剧磨损期。应立即停机检修。
• 3、磨合是运动副正常运转的前提 • 磨合是运动副摩擦表面的形貌和性质从初始状态过度到使用
船机故障及船舶维修体系(船舶管理课件)
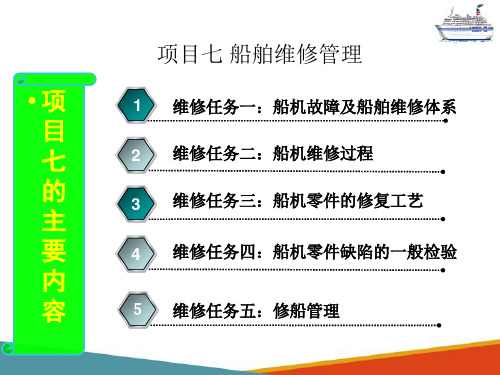
(在机舱听到异常的敲击声。如柴油机的敲缸声、拉缸声,增压器喘振 声。此外还有螺旋桨鸣音及各种工作不正常的声音等。)
船机故障及船舶维修体系
四、故障模式
指妨碍产品完成规定任务的某种可能方式,即产品的故障或失效 的表现形式。
船舶机械的故障模式:主要磨损、腐蚀、疲劳破坏等 。电
器的故障模式有短路、漏电、电路不通等
(2)工艺性故障:
制造、安装质量不佳造成的故障。轴系校中安装质量 不良引起 的轴系振动、轴承发热或 过度磨损
(3)磨损性故障:
正常磨损导致间隙变大。 例如,由于过度磨损使活塞一气缸间隙过大而产生
敲缸、窜气等故障
(4)管理性故障:
人为故障。例如,滑油长期不化验、不更换,变质滑油造成轴瓦合金熔化的 故障
故障率λ(t)是反映系统、设备、机械或零部件在给定工作时间内由完好状态转向 故障状态的概率。
统计分析表明,并非所有的机械、设备等产品的故障率规律都是呈浴盆曲线关系, 有些产品呈如图1-2所示的五种故障率曲线。
曲线A、B有明显的磨损故障期,通常显示机械设备发生磨损、疲劳和材料老化等 故障,可采用定时维修方式延长使用寿命期。往复式发动机的气缸、轴承,船体和飞机 机体等大最单体部件具有此种故障律。
船机故障及船舶维修体系
2.船机外观显示方面 (1)外观反常
(船机运转中油、水、气等有跑、冒、滴、漏等现象。排烟异常,如冒 黑烟、蓝烟或白烟等。)
疲劳破坏的规律、特点及疲劳断口的宏观特征
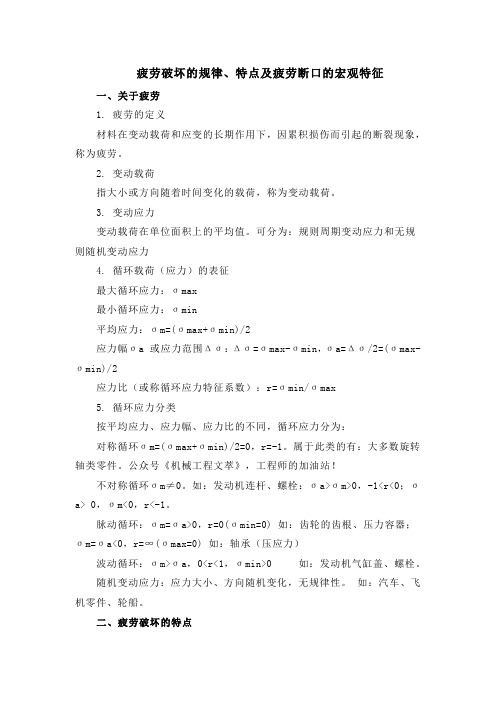
疲劳破坏的规律、特点及疲劳断口的宏观特征
一、关于疲劳
1. 疲劳的定义
材料在变动载荷和应变的长期作用下,因累积损伤而引起的断裂现象,称为疲劳。
2. 变动载荷
指大小或方向随着时间变化的载荷,称为变动载荷。
3. 变动应力
变动载荷在单位面积上的平均值。可分为:规则周期变动应力和无规则随机变动应力
4. 循环载荷(应力)的表征
最大循环应力:σmax
最小循环应力:σmin
平均应力:σm=(σmax+σmin)/2
应力幅σa 或应力范围Δσ:Δσ=σmax-σmin,σa=Δσ/2=(σmax-σmin)/2
应力比(或称循环应力特征系数):r=σmin/σmax
5. 循环应力分类
按平均应力、应力幅、应力比的不同,循环应力分为:
对称循环σm=(σmax+σmin)/2=0,r=-1。属于此类的有:大多数旋转轴类零件。公众号《机械工程文萃》,工程师的加油站!
不对称循环σm≠0。如:发动机连杆、螺栓:σa>σm>0,-1<r<0;σa> 0,σm<0,r<-1。
脉动循环:σm=σa>0,r=0(σmin=0) 如:齿轮的齿根、压力容器;σm=σa<0,r=∞(σmax=0) 如:轴承(压应力)
波动循环:σm>σa,0<r<1,σmin>0 如:发动机气缸盖、螺栓。
随机变动应力:应力大小、方向随机变化,无规律性。如:汽车、飞机零件、轮船。
二、疲劳破坏的特点
第4章 船机零件的疲劳破坏资料.

3、疲劳断裂的种类
§4-1 疲劳破坏
1)根据应力大小和循环周数分 ★高周疲劳破坏——低应力、高寿命疲劳断裂; 特点:最大工作应力应力< s,应力循环次数较高,一般超过106~107 例子:如曲轴、弹簧等的断裂。 ★低周疲劳破坏——高应力、低寿命疲劳断裂 特点:最大工作应力≥s,应力循环次数< 104~105 例子:如压力容器、高压管道等的疲劳断裂。
§4-1 疲劳破坏
2、疲劳断裂的过程
疲劳断裂的过程包含三个过程:疲劳裂纹的形成、裂纹的扩展和断裂。 (1)疲劳裂纹的形成 疲劳源一般位零件表面的应力最大处(多为应力集中处或严重缺陷处)。如金属 表面的油孔、台阶、过渡圆角键槽等截面突变、有切槽的地方及加工缺陷处等。 零件近表面材料内部萌生微裂纹的原因有: ➢零件材料在冶炼、毛坯加工过程中产生的气孔、夹杂、损伤等冶金缺陷; ➢晶体滑移产生裂纹; ➢相界面处产生裂纹; ➢晶界处产生裂纹。
§4-1 疲劳破坏Fra Baidu bibliotek
2)过载抗力 过载抗力一般可用通过试验建立的过载损害区和损害界来表示。
cde——过载损害区 cd——过载损害界 ed——过载持久线,表示在超过疲 劳极限的应力下直到断裂所能经受 的最大应力循环周数
由图可以看出,材料的过载损害区越狭窄,或过载持久线ed越陡直,则过载抗力 越高。由于零件短时间过载不可避免,所以零件选材时宜选用过载损害区狭窄而又 较陡直的材料。
第3章 船机零件的腐蚀讲解
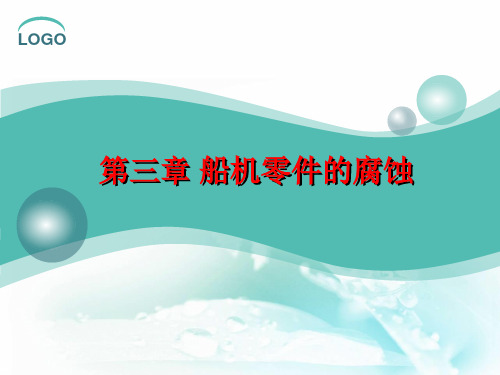
§3-2
2、腐蚀电池的种类
电化学腐蚀
在电化学腐蚀中,腐蚀电池起着重要作用。按构成腐蚀电池的电极大小不同,可
将腐蚀电池分为宏观腐蚀电池和微观腐蚀电池。 (1)宏观腐蚀电池——肉眼可见电极构成的宏观大电池。常见的有异金属接触电 池和浓差电池两种。 A.异金属接触电池——两种不同电位的金属或合金相互接触(直接接触或用导 线连接),并处于同一电解质溶液中,使电位较低的金属受到腐蚀的现象。又称
或片状从金属表面脱落,一般发生在型材和板材上。
§3-2
二、电化学腐蚀原理 1、电化学腐蚀的原理
电化学腐蚀
金属在电解质溶液中发生电化学腐蚀的原理为电池原理 形成腐蚀电池的基本条件是:电解质溶液;有阴、阳两个电极且在同一溶液中;
阴阳两极间产生电流。
阳极反应:失去电子,放电,发生 氧化反应,电位低,被腐蚀; 阴极反应:得到电子,发生还原反 应,电位高,受到保护。
电偶腐蚀。
特点;两种金属的电极电位差越大,电偶腐蚀越严重。 例子:螺旋桨与尾轴组成的电池,尾轴被腐蚀; 冷凝器中的碳钢壳体与黄铜管构成的电池。
§3-2
2、腐蚀电池的种类
电化学腐蚀
B.浓差电池——同一金属的不同部位与浓度或温度不同的介质接触形成的腐蚀电 池,造成局部腐蚀。常见的有氧浓差电池、温差电池、盐浓差电池等。 金属与含氧量不同的介质接触。在氧浓度较低处金属的电极电位较低为阳极,在 氧浓度较高处金属的电极电位较高为阴极,从而构成氧浓度差电池,阳极区的金 属遭到腐蚀。例如铁棒埋于土壤中,因土壤深度不同含氧量不同,故在铁棒埋得 最深部位的金属腐蚀最严重。
- 1、下载文档前请自行甄别文档内容的完整性,平台不提供额外的编辑、内容补充、找答案等附加服务。
- 2、"仅部分预览"的文档,不可在线预览部分如存在完整性等问题,可反馈申请退款(可完整预览的文档不适用该条件!)。
- 3、如文档侵犯您的权益,请联系客服反馈,我们会尽快为您处理(人工客服工作时间:9:00-18:30)。
第四章船机零件的疲劳破坏
(Fatigue Fracture )
很多柴油机零件(如曲轴、活塞、缸盖、齿轮、连杆螺栓等)承受交变载荷的作用,经过长时间运行后会发生断裂,在这些断裂中,疲劳断裂占80~90%。
§4-1 金属疲劳的概念
1 疲劳断裂的概述
1.1 定义
零件或材料在交变载荷的长时间作用下,会在应力小于σb (甚至小于σs )的情况下产生裂纹或
突然断裂,这种现象称为疲劳断裂。
说明:(1)应力:机械应力和热应力(交变)。
交变应力:
平均应力:()min max 2/1σσσ+=m
应力幅值:()min max 2/1σσσ-=a 应力循环特征:m ax
m in σσγ=;当1-=γ时,为对称循环。 (2)破坏:裂纹和断裂。
(3)特征:
零件发生疲劳断裂时具有以下特征:
(1)零件是在交变载荷作用下经过较长时间的使用;
(2)断裂应力小于材料的抗拉强度σb ,甚至小于屈服强度σs ;
(3)断裂是突然的、无任何先兆;
(4)断口形貌特殊,断口上有明显不同的区域;
(5)零件的几何形状、尺寸、表面质量和表面受力状态等均直接影响零件的疲劳断裂。
1.2 种类
1)根据应力大小和循环次数分:
★高周疲劳破坏
特点:σ小,应力循环次数大(>105),最常见(曲轴、弹簧等的断裂)。 ★低周疲劳破坏
特点:应力大(>σs ),低频加载,应力循环次数104~105
2)根据工作环境等分类:
★热疲劳:由于零件受温度的变化引起热应力的反复作用造成的疲劳破坏。如缸盖疲劳裂纹。 ★ 腐蚀疲劳:由于交变应力与腐蚀介质的共同作用而导致的疲劳破坏。
★ 接触疲劳破坏: 由于接触应力的反复作用,导致形成金属剥落,形成麻点。如滚动轴承、齿轮等的破坏。
★ 其它疲劳形式:如接触疲劳、微动磨损疲劳和激冷疲劳等。
3)按应力种类分:弯曲疲劳、扭转疲劳、复合疲劳等。
1.3 疲劳抗力指标
表征零件材料抗疲劳性能的力学参数,主要有:疲劳极限、超载抗力、疲劳缺口敏感度等。
1)疲劳极限(MPa ):当应力低于某一数值时,循环无限次,材料也不会发生疲劳断裂,该应力称为材料的疲劳极限。材料的疲劳极限是由试验测定。例如,常温下的碳钢、合金结构钢和铸铁,在N 达107后曲线出现水平阶段。所以这类材料是以N =107时不断的最大应力作为疲劳极限。
2)过载抗力:是衡量过载对材料疲劳抗力的影响指标。例如,柴油机紧急刹车、起动或超负荷运转等。不适当过载(包括过载的大小和过载循环次数的多少)将会造成过载损伤,降低材料的疲劳极限,导致零件的疲劳破坏。这是由于过载引发了材料内部的微裂纹扩展达到了一定尺寸,在过载后的正常运转中不断扩展导致疲劳断裂。由图可以看出,材料的过载损害区越狭窄,或过载持久线ed 越陡直,则过载抗力越高。过载持久值ed 表示在超过疲劳极限的应力下直到断裂所能经受的最大应力循环周数。由于零件短时间过载不可避免,所以零件选材时宜选用过载损害区狭窄而又较陡直的材料。
3)疲劳缺口敏感度:零件表面开有键槽、油孔、螺纹等各种缺口时,就会在缺口的根部产生应力集中,使材料的疲劳强度降低。
q =(K f -1)/(K t -1)
式中:K t ——静力理论应力集中系数,K t =σmax /σ;
K f ——疲劳应力集中系数,K f =σ-1/σ-1H
K t 是试件缺口根部处的最大应力σmax 与光滑试件横截面上均匀应力σ之比,与缺口的几何形
状、尺寸及缺口曲率半径有关,与材料性能无关。K t 值可从机械工程手册中查得。
K f 是光滑试件的疲劳极限σ-1与缺口疲劳极限σ-1H 之比,其与缺口的形状、尺寸和材料性能有
关。在中等强度范围内,材料强度越高,K f 值越大。一般K f ≤K t 。当K f =K t 时,q =1,表示此时疲
劳应力集中最严重,缺口最敏感;当K f =1时,σ-1=σ-1H ,则q=0,表明零件虽有缺口但不影响
材料的疲劳极限σ-1,缺口最不敏感。
材料的缺口敏感度q 在0~1之间。q 值越小,缺口越不敏感。铸铁对缺口极不敏感,q <0.1;一般结构钢对缺口较为敏感,q =0.55~0.80。
2 疲劳断裂的机理
2.1疲劳断裂的断口特征
零件或构件疲劳断裂后,其断口形貌呈现了从裂纹产生到裂纹扩展,直至断裂的全过程。可以根据断口形貌特征来分析零件的断裂原因。
图4-3a )、b )分别示出弯曲疲劳断裂和扭转疲劳断裂的宏观形貌,分为三个区域:
(1)疲劳源 用肉眼或低倍放大镜在断口上可以找到一个或多个疲劳裂纹的开始点,称为疲劳源。疲劳源一般出现在零件表面或近表面处。
(2)裂纹扩展区 呈光滑状或贝纹状,一般占有较大面积。光滑状是两个断裂表面长时间互相研磨所致;贝纹是负荷变化时裂纹前沿线扩展遗留下的痕迹。贝纹从疲劳源开始后向四周扩展并与裂纹扩展方向垂直。
(3)最后断裂区域称脆断区零件瞬间突然断裂,断口晶粒较粗大,与发暗的裂纹扩展区明显不同。脆性材料呈结晶状;塑性材料呈纤维状。交变应力的反复作用→产生微观疲劳裂纹→裂纹扩展(时而扩展,时而停止)→承载面积减少→最后断裂。
因此,疲劳断裂的过程包含三个过程:疲劳裂纹的形成、裂纹的扩展和断裂。
1) 疲劳裂纹的形成:
形成部位:应力最大、薄弱环节。在截面突变、有切槽的地方、加工缺陷处等有较大应力集中。
2) 疲劳裂纹的扩展:
第一阶段:切向扩展阶段。沿最大切应力(与正应
力成45o角)的方向金属内部扩展,深度较浅(0.1mm),
扩展速度很小。
第二阶段:裂纹改变方向,沿与正应力垂直方向扩
展,正应力对裂纹的扩展起重要作用。
3) 疲劳断裂
最后断裂区的面积与所受载荷有关,面积大,说明
过载越重。当其面积小于断口面积的一半时,说明零件
无过载或过载很小。
3 疲劳断裂的特点
1) 突发性:断裂前无明显的塑变;
2) 疲劳断裂前零件一般经较长时间的使用;
3) 工作应力小于材料的强度极限,甚至小于屈服强度;
4) 零件的几何形状、尺寸、表面质量和表面受力状态直接影响零件的疲劳断裂;
5) 断口形貌特殊:分三个区(每个区对应一个过程)。
(1)疲劳源。一般出现在零件的表面。一般有1~2个。
(2)裂纹扩展区:呈贝纹状,是裂纹扩展留下的痕迹。
以上两部分由于受长时间的研磨,呈磨光状态。若疲
劳源区与裂纹扩展区断面粗糙、疲劳源数较多和贝纹线间
距较大时,可能是应力集中较严重和有较大的过载作用。
(3)最后断裂区:晶粒粗大。
甚至超过断口面积一半以上,
其寿命也越短。若所占面积较小,小于断口面积之半时,
说明零件无过载或过载很小。
在相同条件下,高应力状态零件的最后断裂区面积大于低应力状态零件;疲劳源数目不同,单
相弯曲仅有1个,而双向弯曲有2个;最后断裂区形状不同,单相弯曲与扭转弯曲相比,后者的疲
劳源与最后断裂区相对位置发生偏转,同时由于零件上缺口应力集中的影响较大,最后断裂区很小
且与零件断面呈同心状。
4 影响疲劳强度的因素
零件材料疲劳强度的大小受诸多因素的影响,外部因素主要是零件的形状、尺寸、表面粗糙度
和使用条件等;内部因素主要是材料的成分、组织、夹杂物和表面应力状态等。而疲劳强度是零件
设计、选材和制订加工工艺时的重要参数,直接关系到零件的使用寿命。