机械设计之机械零件的疲劳强度
机械零件的疲劳强度与疲劳断裂
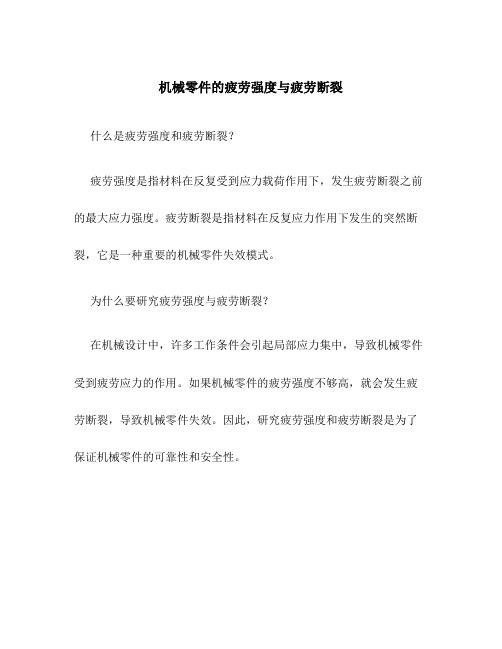
机械零件的疲劳强度与疲劳断裂什么是疲劳强度和疲劳断裂?疲劳强度是指材料在反复受到应力载荷作用下,发生疲劳断裂之前的最大应力强度。
疲劳断裂是指材料在反复应力作用下发生的突然断裂,它是一种重要的机械零件失效模式。
为什么要研究疲劳强度与疲劳断裂?在机械设计中,许多工作条件会引起局部应力集中,导致机械零件受到疲劳应力的作用。
如果机械零件的疲劳强度不够高,就会发生疲劳断裂,导致机械零件失效。
因此,研究疲劳强度和疲劳断裂是为了保证机械零件的可靠性和安全性。
影响机械零件疲劳强度与疲劳断裂的因素机械零件的疲劳强度和疲劳断裂受到许多因素的影响,以下是一些常见的因素:1.材料特性:材料的强度、韧性和疲劳寿命等特性会影响机械零件的疲劳强度和疲劳断裂。
一些金属材料具有较高的疲劳强度和疲劳韧性,而一些非金属材料则较低。
2.载荷特性:载荷的频率、幅值和载荷类型(拉伸、压缩、扭转等)对机械零件的疲劳强度和疲劳断裂有着重要影响。
高频率和大幅度的载荷容易导致疲劳断裂。
3.制造工艺:制造过程中的缺陷(如裂纹和夹杂物)会使机械零件的疲劳强度降低,从而增加疲劳断裂的风险。
4.工作环境:工作环境中的温度、湿度和腐蚀等因素也会影响机械零件的疲劳强度和疲劳断裂。
如何评估机械零件的疲劳强度与疲劳断裂?评估机械零件的疲劳强度和疲劳断裂是一个复杂的过程,通常需要借助实验和数值模拟等方法。
1.实验方法:通过设计和进行疲劳试验,可以获取机械零件在不同应力载荷下的疲劳寿命和断裂情况。
实验方法可以帮助工程师确定不同材料和设计方案的疲劳强度,并提供实际应用中的可靠性数据。
2.数值模拟:利用计算机仿真方法,可以预测机械零件在特定工况下的疲劳强度和疲劳断裂情况。
数值模拟方法可以节省时间和成本,并帮助工程师在设计阶段优化零件的几何形状和材料选择。
如何提高机械零件的疲劳强度?为了提高机械零件的疲劳强度,可以从以下几个方面进行优化:1.材料选择:选择具有较高疲劳强度和疲劳韧性的材料,例如高强度钢、铝合金等。
第三章 机械零件的疲劳强度计算

m
max min
2
200 100 2
50
a
max min
2
200 100 2
150
200
a
50
0
-100
min
max
m
t
机械设计 第三章 机械零件的疲劳强度计算
机械设计
3.2 材料的疲劳特性
3.2.1 材料的疲劳曲线
表示N次循环和疲劳极限间的关系曲线,称为疲劳曲线。
机械设计
曲线的BC段,随着循环次数的增加, 使材料疲劳破坏的最大应力不断下降。 C点相应的循环次数大约为104。把这一 阶段的疲劳现象称为应变疲劳。由于 应力循环次数相对很少,所以也叫低 周疲劳。
机械设计 第三章 机械零件的疲劳强度计算
机械设计
当N≥104时,称为高周循环疲劳。曲
线CD代表有限疲劳阶段。D点对应的 疲劳极限ND称为循环基数,用N0表示。 曲线CD段上任何一点所代表的疲劳极 限,称为有限寿命疲劳极限。
机械设计
1.稳定循环变应力
1) 对称循环变应力
最大应力σmax和最小应力σmin的
绝对值相等而符号相反
即σmax=-σmin
例如,转动的轴上作用一方向 不变的径向力,则轴上各点的弯曲 应力都属于对称循环变应力
机械设计 第三章 机械零件的疲劳强度计算
机械设计
2) 脉动循环变应力 脉动循环变应力中
σmin=0
劳极限。连接A′、D′得
直线A′D′
机械设计 第三章 机械零件的疲劳强度计算
机械设计
取C点的坐标值等于材料的 屈服极限σS,并自C点作一直 线与直线CO成45°的夹角, 交A′D′的延长线于 G′, 则CG′上的任何一
机械零件的疲劳强度设计

累积循环次数
疲劳寿命
--寿命损伤率
显然,在 的单独 作用下,
当 , 寿命损伤率=1 时,就会发生疲劳破坏。
受变幅循环应力时零件的疲劳强度
Minger法则:在规律性变幅循环应力中各应力的作用下,损伤是独 立进行的,并且可以线性地累积成总损伤。当各应力的寿命损伤率 之和等于1时,则会发生疲劳破坏。
即:
上式即为Miner法则的数学表达式,亦即疲劳损伤线性累积假说。
注:在计算时,对于小于 的应力,可不考虑。
二、疲劳强度设计
损伤等效
根据Miner法则,将规律性变幅循环应力 等效恒幅循环应力
(简称等效应力)
--等效应力的大小 --等效循环次数
受变幅循环应力时零件的疲劳强度
在计算中,上述三个系数都只计在应力幅上,故可将三个系数 组成一个综合影响系数:
零件的疲劳极限为:
用表面状态系数 、 计入表面质量的影响。
( 、 的值见教材或有关手册 )
屈服强度线
§2-4 受恒幅循环应力时零件的疲劳强度
疲劳强度设计的主要内容之一是计算危险剖面处的安全系数,以 判断零件的安全程度。安全条件是:S ≥ 。
概 述
C)疲劳破坏是一个损伤累积的过程,需要时间。寿命可计算。 d) 疲劳断口分为两个区:疲劳区和脆性断裂区。
二、循环应力的类型
脆性断裂区
疲劳区
疲劳源
疲劳纹
循环应力可用smax 、 smin 、 sm 、 sa 、 这五个参数中的任意两个参 数表示。
概 述
规律性变幅循环应力
按最大应力计算的安全系数为:
≥
受恒幅循环应力时零件的疲劳强度
受恒幅循环应力时零件的疲劳强度
注:1)应力增长规律为 时,按应力幅计算的安全系数 等与按最大应力计算的安全系数。
机械设计中的疲劳强度分析

机械设计中的疲劳强度分析在机械设计领域,疲劳强度是一个至关重要的考量因素。
当机械零部件在循环载荷作用下工作时,即使所承受的应力远低于材料的屈服强度,经过一定的循环次数后,也可能会发生突然的断裂,这种现象被称为疲劳失效。
疲劳失效是机械零件和结构失效的主要形式之一,它往往会带来严重的后果,如设备损坏、生产停滞甚至人员伤亡。
因此,在机械设计过程中,对疲劳强度进行准确的分析和评估具有极其重要的意义。
要理解疲劳强度,首先需要了解疲劳破坏的特点。
与静态载荷下的破坏不同,疲劳破坏具有以下几个显著特征。
其一,疲劳破坏是在循环载荷作用下逐渐发展的,其破坏过程通常经历了裂纹萌生、裂纹扩展和最终断裂三个阶段。
在初始阶段,微观裂纹在材料表面或内部的缺陷处形成,随着循环次数的增加,裂纹逐渐扩展,直到达到临界尺寸时发生突然的断裂。
其二,疲劳破坏时,零件所承受的最大应力通常远低于材料的抗拉强度,甚至可能低于屈服强度。
这是因为疲劳破坏是由循环应力引起的累积损伤导致的,而不是一次性的过载。
其三,疲劳破坏对零件的表面状态和内部缺陷非常敏感。
零件表面的粗糙度、划痕、腐蚀等都会加速疲劳裂纹的萌生和扩展,而内部的夹杂物、气孔等缺陷也会降低材料的疲劳强度。
那么,如何对机械零件的疲劳强度进行分析呢?目前,常用的方法主要有两种:试验法和分析法。
试验法是通过对实际零件或试样进行疲劳试验来确定其疲劳强度。
这种方法直观可靠,但成本较高,且试验周期长。
在疲劳试验中,通常将试样或零件在特定的加载条件下进行循环加载,直到发生疲劳破坏。
通过记录加载次数和应力水平,可以得到零件的疲劳寿命曲线,即 SN 曲线。
SN 曲线反映了应力水平与疲劳寿命之间的关系,是评估零件疲劳强度的重要依据。
然而,由于试验条件的限制,试验法往往难以完全模拟零件在实际工作中的复杂载荷和环境条件。
分析法则是基于材料的力学性能和零件的几何形状、载荷条件等,通过理论计算或数值模拟来预测零件的疲劳强度。
第3章机械零件的疲劳强度

(kt ) D
说明
t t
kt
应力集中、零件尺寸和表面状态都只对应力幅有影 响,即疲劳极限主要受应力幅的影响
第三节 许用疲劳极限应力图
稳定变应力和非稳定变应力 许用(零件)疲劳极限应力图 工作应力增长规律
一、稳定变应力和非稳定变应力
稳定变应力:在每次循环中,平均应力σm、应力幅σa
和周期T都不随时间变化的变应力
2
45°
O
s0
2
45°
F S
sS
sm
sB
三、工程中的简化极限应力图(2)
sa
A B
疲劳塑性失 效区
s -1 s 0
疲劳和 塑性安 全区
2
45°
O
s0
2
F
sS
S
sm
sB
三、工程中的简化极限应力图(3)
sa
A B
疲劳塑性失 效区
s -1 s 0
疲劳和 塑性安 全区
2
45°
O
s0
2
45°
F
sS
S
sm
sB
sa
A
B
E
s -1
s0
2
45°
O
s0
2
45°
sS
S
sm
F
sB
s AE上各点: max s lim s m s a
如果 s max s max 不会疲劳破坏
s ES上各点: lim s m s a s s 如果 s max s s 不会屈服破坏
第三章 机械零件的疲 劳强度
机械零件的疲劳强度设计方法
1、安全——寿命设计
机械设计-疲劳强度
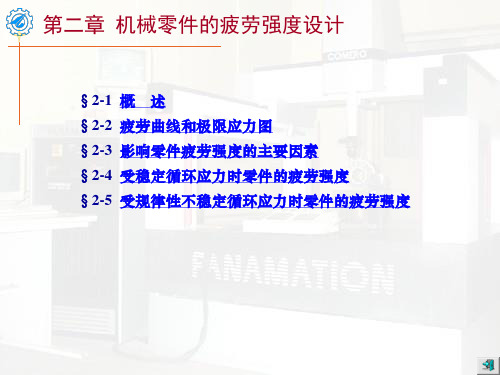
前边提到的各疲劳极限 ,实际上是材料的力学性能指标,是用 §2-3影响 疲劳强度的 试件通过试验测出的。 因素 而实际中的各机械零件与标准试件,在形体,表面质量以及绝 对尺寸等方面往往是有差异的。因此实际机械零件的疲劳强度与用 试件测出的必然有所不同。
影响零件疲劳强度的主要因素有以下三个: 一、应力集中的影响
第二章 机械零件的疲劳强度设计
§2-1 概 述
§2-2 疲劳曲线和极限应力图 §2-3 影响零件疲劳强度的主要因素
§2-4 受稳定循环应力时零件的疲劳强度
§2-5 受规律性不稳定循环应力时零件的疲劳强度
§2-1
一、疲劳破坏
概
述
脆性断裂区
§2-1 概 述
机械零件在变应力作用下,应力的每次 作用对零件造成的损伤累积到一定程度时, 首先在零件的表面或内部将出现(萌生)裂
疲劳强度线
§2-4 受稳定循环应力时
a
A
1
K D 2 K D
A0, 1
B(
0 0
2 ,
D
2
)
注:由于DG段
属于静强度,而 静强度不受
B
屈服强度线
D
0
KD
的影响,故不需修正。
o
G s ,0
0
2
m
受稳定循环应力时零件的疲劳强度
疲劳强度线 AD 的方程为:
机械零件上的应力集中会加快疲劳裂纹的形成和扩展。从而导致零件 的疲劳强度下降。
响 。( K
用疲劳缺口系数 K σ 、 K τ (也称应力集中系数)计入应力集中的影
σ
、 K τ 的值见教材或有关手册)
影响零件疲劳强度的主要因素
影响疲劳强 注:当同一剖面上同时有几个应力集中源时,应采用其中最大的疲劳缺 度的主要因 口系数进行计算。 素2 二、尺寸的影响 零件的尺寸越大,在各种冷、热加工中出现缺陷,产生微观裂纹等疲 劳源的可能性(机会)增大。从而使零件的疲劳强度降低。 用尺寸系数 εσ 、ε τ ,计入尺寸的影响。 ( εσ 、ε τ 见教材或有关手册 ) 三、表面质量的影响 表面质量:是指表面粗糙度及其表面强化的工艺效果。表面越光滑, 疲劳强度可以提高。强化工艺(渗碳、表面淬火、表面滚压、喷丸等)可 显著提高零件的疲劳强度。
机械设计基础-机械零件的强度
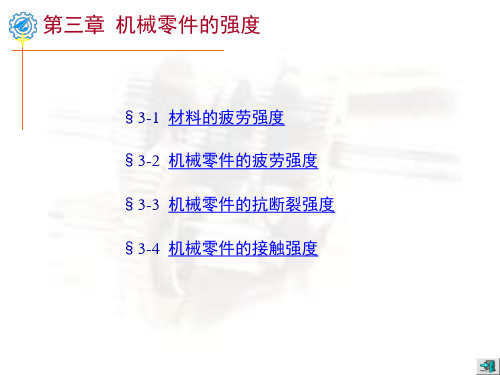
用统计方法进行疲劳强度计算
不稳定变应力
非规律性
规律性
按损伤累积假说进行疲劳强度计算
详细分析
机械零件的疲劳强度
四、双向稳定变应力时的疲劳强度计算
当零件上同时作用有同相位的稳定对称循环变应力sa 和ta时,由实验得出的极限应力关系式为:
有限寿命区间内循环次数N与疲劳极限srN的关系为:
式中, sr、N0及m的值由材料试验确定。
二、 s-N疲劳曲线
s-N疲劳曲线
详细说明
≤
≤
m
材料的疲劳强度
三、等寿命疲劳曲线(极限应力线图)
机械零件材料的疲劳特性除用s-N曲线表示外,还可用等寿命曲线来描述。该曲线表达了不同应力比时疲劳极限的特性。
接触应力是不同于以往所学过的挤压应力的。挤压应力是面接触引起的应力,是二向应力状态,而接触应力是三向应力状态。接触应力的特点是仅在局部很小的区域内产生较大的应力。
式中,ρ1和ρ2分别为两零件初始接触线处的曲率半径, 其中正号用于外接触,负号用于内接触。
对于线接触的情况,其接触应力可 用赫兹应力公式计算。
更多图片
§3-1 材料的疲劳强度
§3-2 机械零件的疲劳强度
§3-3 机械零件的抗断裂强度
§3-4 机械零件的接触强度
第三章 机械零件的强度
材料的疲劳强度
一、交变应力的描述
sm——平均应力; sa ——应力幅值;
smax ——最大应力; smin ——最小应力;
r ——应力比(循环特性)
描述规律性的交变应力可有5个参数,但其中只有两个参数是独立的。
为了度量含裂纹结构体的强度,在断裂力学中运用了应力强度因子KI(或KⅡ、KⅢ)和断裂韧度KIC (或KⅡC、KⅢC)这两个新的度量指标来判别结构安全性,即:
机械零件的疲劳强度.

M' ('me,'ae)
B’
E E’
/K
0/2K
45° O
135° S (s,0)
m
K N 1 1 a m (k ) D (k ) D
直线E’S方程:
2 1 0
0
' max
m s a
按静强度计算 当
10 3 (10 4 ) N N 0 ——高周循环疲劳
N
有限寿命区 无限寿命区
随循环次数↑疲劳极限↓
N
O
N
N0
N
2
N ——持久极限
对称循环:
无限寿命区 N N0
1 1
有限寿命区
脉动循环:
0 0
注意:有色金属和高强度合金钢无无限寿命区。
3、 无明显塑性变形的脆性突然断裂
4 、破坏时的应力(疲劳极限)远小于材料的屈服极限 三、疲劳破坏的机理:
损伤的累积 四、影响因素: 不仅与材料性能有关,变应力的循环特性,应力循环
次数,应力幅(应力集中、表面状态、零件尺寸)都
对疲劳极限有很大影响。
§ 3—2 材料的疲劳曲线和极限应力图
N ( N )——疲劳极限,循环变应力下应力循环N次后
第三章 机械零件的疲劳强度
疲劳强度计算方法: 1、安全——寿命设计 2、破损——安全设计
§ 3—1 疲劳断裂的特征
一、失效形式:疲劳断裂
二、疲劳破坏特征: 1、断裂过程:① 产生初始裂纹 (应力较大处) ② 裂纹尖端在切应力作用下,反复扩 展,直至产生疲劳裂纹。 2 、断裂面:① 光滑区(疲劳发展区) ② 粗糙区(脆性断裂区)
第2章机械零件的疲劳强度计算机械设计课件
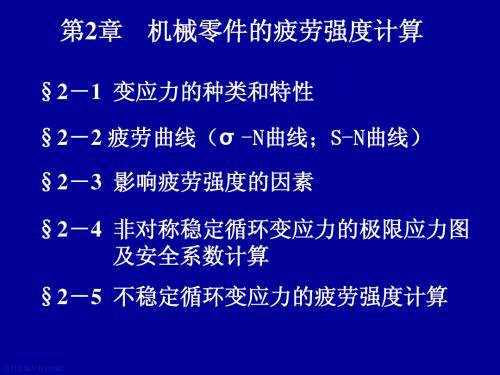
作σ
自用盘编号JJ321002
r∞
,通常用N0次数下的σ r取代,σ r值由实验得到。
σ
rN
轻合金材料的循环基数通常取为: N0≈2.5×108 σ
r
0
N0
N
图2—5 轻合金材料的σ—N曲线 N0称为循环基数,对应的疲劳极限σ r称为该材料的疲
劳极限。 对于钢材:当HB≤350时:N0≈106~107;
α
σ
、α
τ
——理论应力集中系数,查教材P39 ~ P41附表
自用盘编号JJ321002
3—1 ~ 附表3—3或查手册和其它资料。 若一个剖面上有几个不同的应力集中源,则零件的疲劳 强度由各kσ (kτ )中的最大值决定。
3、尺寸效应的影响 材料的疲劳强度极限是对一定尺寸的光滑试件进行实验 得出的,考虑到零件尺寸和试件的尺寸不同,其疲劳强度 也不一样,故引入一个尺寸系数ε: 1d 1d 直径d的 ; 1 1 标准试件的 εσ 、ετ的值可查教材P42 ~ P43附图3—2、3—3,附 表3—7或查手册及有关资料。 4、表面质量的影响 零件表面的加工质量,对疲劳强度也有影响,加工表面 的粗糙度值越小,应力集中越小,疲劳强度越高。因此引 入一个表面质量系数β 来考虑零件表面的加工质量不同对 疲劳强度的影响。 β可查教材P44附图3—4
max
自用盘编号JJ321002
min r max
称r为应力循环特性,表示了变应力 的变化性质。
σa σ r=-1
r=-1 t
σ
r=0 t t r=+1 t + σm
t 左边区域: σ 压应力为主, Ⅱ区: 零件在压缩 - 1 < r <0 变应力时破 σ 坏的情况较 Ⅰ区: 少,故不予 0 <r <+ 1 以分析。 45° - σm σ 0 0
机械设计之机械零件的疲劳强度

机械设计之机械零件的疲劳强度引言在机械设计中,疲劳强度是评估机械零件是否能够在长时间使用过程中承受载荷和弯曲等作用力的重要指标之一。
疲劳强度不仅关乎机械零件的寿命和可靠性,还直接影响到机械装置的安全性能。
本文将介绍机械零件的疲劳强度分析方法,包括疲劳寿命预测、疲劳极限分析、疲劳强度评估等内容。
疲劳寿命预测疲劳寿命是机械零件在特定载荷下能够承受的循环次数。
疲劳寿命预测的目的是为了确定机械零件在特定工作条件下的可靠性。
常用的疲劳寿命预测方法有下面几种:1. 基于SN曲线的方法SN曲线(Stress Number Curve)揭示了应力与循环次数之间的关系。
通过测试材料在不同应力水平下的循环寿命,并绘制SN曲线图,可以预测不同应力水平下的寿命。
这种方法适用于不同材料在常温下的疲劳寿命预测。
2. 基于应力途径的方法应力途径是指机械零件在循环载荷下的相对应力历程和持续时间。
通过测量机械零件在不同应力途径下的寿命,并绘制应力途径图,可以预测不同应力途径下的寿命。
这种方法适用于复杂加载情况下的疲劳寿命预测。
3. 基于损伤积分的方法损伤积分是指在单位时间内损伤累积的指标。
通过测量机械零件在不同加载条件下的损伤积分,并与材料的损伤裕度相比较,可以预测机械零件的寿命。
这种方法适用于快速变化的加载情况下的疲劳寿命预测。
疲劳极限分析疲劳极限是指机械零件在循环载荷下的最大承载能力。
疲劳极限分析的目的是为了确定机械零件能够承受的最大载荷和疲劳寿命。
常用的疲劳极限分析方法有如下几种:1. 基于拉伸试验的方法拉伸试验是测量材料在拉伸载荷下的应变和应力变化的试验。
通过拉伸试验和应力-应变曲线,可以确定材料的疲劳极限。
这种方法适用于静态或低周疲劳加载条件下的疲劳极限分析。
冲击试验是测量材料在动态或高速加载条件下的力学性能的试验。
通过冲击试验和载荷-位移曲线,可以确定材料的疲劳极限。
这种方法适用于动态或高速加载条件下的疲劳极限分析。
机械零件的疲劳强度设计

数值模拟
使用计算机模型模拟零件受 循环载荷后的疲劳行为。
统计分析
通过分析样本数据,推导疲 劳寿命的概率分布。
疲劳试验与数据分析
1
试验设计
制定疲劳试验方案,包括加载方式、载荷幅值和试验样本数。
2
试验执行
进行疲劳试验,记录试验数据,如载荷响应和失效时间。
3
数据分析
对试验数据进行统计分析,得出寿命曲线和可靠性评估。
疲劳强度设计是确保机械零件可靠性和安 全性的关键步骤。
疲劳强度设计的工度钢。
几何设计
优化零件几何形状,减少应力集中和裂纹生成的可能性。
加工和热处理
精确控制加工过程和热处理参数,提高零件的疲劳强度和寿命。
案例分析及总结
案例1 案例2 总结
通过疲劳强度设计,延长了某机械组件的 使用寿命。
疲劳断裂导致一架飞机的事故,强调了疲 劳强度设计的重要性。
机械零件的疲劳强度设计
欢迎来到本次精彩的演讲!我们将探讨机械零件的疲劳强度设计,包括定义、 重要性、原因及机理、寿命评估方法、试验与数据分析、工程实践和案例分 析。
机械零件疲劳强度的定义
1 什么是疲劳强度?
疲劳强度是指机械零件在循环加载下能够承受的最大应力水平。
2 为什么疲劳强度重要?
了解疲劳强度有助于预测零件的寿命和避免意外损坏。
3 如何计算疲劳强度?
疲劳强度可以通过诸如疲劳极限、材料强度、载荷频率等参数的计算得出。
疲劳断裂的原因及机理
原因
• 不适当的设计 • 材料缺陷 • 过载或振动
机理
• 疲劳裂纹的生成和扩展 • 应力集中导致断裂 • 裂纹逐渐扩展导致零件失效
疲劳寿命评估方法
试验法
通过对零件进行疲劳试验来 评估其寿命。
机械设计第三章机械零件强度
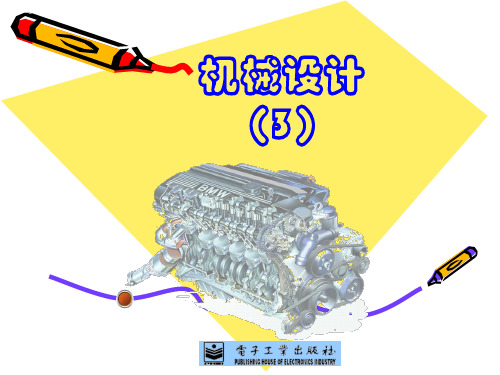
45° B
C
σm
σS σB
AG直线上任意点代表了一定循环特性时的疲劳极限。
已知C点坐标:(σS , 0) CG直线的斜率: k=tan135°=-1
CG直线的方程:
a m s
CG直线上任意点的最大应力达到了屈服极限应力。
§3.1 材料的疲劳特性
疲劳破坏的判据:
1. 当循环应力参数( σm,σa )
静应力只能由静载荷产生。 注意: 静载荷和变载荷均可能产生变应力。
绝大多数机械零件都是处于变应力状态下工作的。
§3.1 材料的疲劳特性
四、 变应力的描述
平均应力:
m
max
min
2
应力幅值:
a
max
min
2
-1,对称循环应力
应力比 (循环特性):
r
min max
=
0,脉冲循环应力 描述规律性的变应力有5个参数,但
由于实际零件的几何形状、尺寸大小、加工质量及强化因素等与材料 标准试件有区别,使得零件的疲劳极限要小于材料标准试件的疲劳极限。
1. 应力集中
由于零件形状突然变化而引起的局部应力增大现象。 应力集中的存在会降低零件的疲劳极限。
2. 零件尺寸
其他条件相同的情况下,零件的绝对尺寸越大,其疲劳强度 越低。
零件的表面状态包括表面粗糙度和表面处理。
二、名义载荷与计算载荷
➢名义载荷Fn :根据额定功率用力学公式计算出作用在零件上的载荷。 ➢计算载荷Fca:考虑载荷的时间不均匀性、分布的不均匀性以及其它
影 响因素对名义载荷进行修正得到的载荷。
Fca K Fn
K—— 载荷系数
§3.1 材料的疲劳特性
三、应力
机械零件的疲劳强度

机械零件的疲劳强度1. 引言疲劳是机械零件在长期循环载荷下发生破坏的一种现象。
在工程实践中,对机械零件的疲劳强度进行准确评估和预测是至关重要的。
本文将介绍机械零件的疲劳强度及其评估方法。
2. 疲劳强度的定义疲劳强度是指材料在循环载荷作用下承受的最大应力达到相应标准下的寿命。
在机械零件的设计和使用中,疲劳强度决定了零件的可靠性和寿命。
3. 影响疲劳强度的因素疲劳强度受多种因素影响,包括材料的性能、应力水平、循环载荷的频次、温度等。
以下是影响疲劳强度的主要因素:3.1 材料的性能材料的强度、韧性、硬度、断裂韧性等性能对疲劳强度有重要影响。
一般情况下,强度越高、韧性越佳的材料具有更高的疲劳强度。
3.2 应力水平应力水平是指机械零件在工作状态下承受的最大应力值。
应力水平越高,机械零件的疲劳强度相应较低。
3.3 循环载荷的频次循环载荷的频次是指机械零件在工作过程中受到应力循环的次数。
频次越高,机械零件的疲劳强度相应较低。
3.4 温度温度对材料的性能有直接影响,高温会导致材料的强度降低,从而影响疲劳强度。
4. 评估疲劳强度的方法为了准确评估机械零件的疲劳强度,工程师可以采用以下几种方法:4.1 经验公式法经验公式法是基于实验数据和经验公式来评估疲劳强度的一种方法。
通过统计分析和归纳,可以得到适用于不同材料和零件的经验公式,并进行计算和预测。
4.2 数值模拟方法数值模拟方法是利用计算机建立机械零件的有限元模型,并通过有限元分析软件对零件进行疲劳强度分析。
该方法可以较精确地评估零件的疲劳强度,但需要依赖于准确的材料性能和载荷条件。
4.3 实验方法实验方法是通过设计和进行疲劳试验来评估机械零件的疲劳强度。
通过在实验中施加不同的载荷条件和监测零件的变形和破坏情况,可以获得零件的疲劳强度。
5. 结论机械零件的疲劳强度是一个复杂的问题,在机械设计和使用中具有重要的意义。
疲劳强度的评估可以通过经验公式法、数值模拟方法和实验方法来进行。
机械设计第3章机械零件的强度

根据零件载荷的变化规律以及零件与相邻零件互相约 束情况的不同,可能发生的典型的应力变化规律通常 有下述三种:
a)变应力的应力比保持不变,即r=C(例如绝大 多数转轴中的应力状态);
b)变应力的平均应力保持不变,即σm=C(例如 振动着的受载弹簧中的应力状态);
c)变应力的最小应力保持不变, σmin=C(例如 紧螺栓联接中螺栓受轴向变载荷时的应力状 态)。以下分别讨论这三种情况。
(3—9)
直线CG的方程为
σa'+σm'=σs
(3—10)
式中:σae'——零件受循环弯曲应力时的极限应力幅; σme'——零件受循环弯曲应力时的极限平均应力; e ——零件受循环弯曲应力时的材料常数。
e 可用下式计算
e
K
1 K
2 1 0 0
(3 11)
Kσ——弯曲疲劳极限的综合影响系数
S a
ae a
1 m K a
对应于N点的极限应力由N2'点表示,它位于直线CG上,故 仍只按式(3—18)进行静强度计算,分析图3—7可知,凡是工 作应力点位于CGH区域内时,在σm=C的条件下,极限应力 统为屈服极限,也是只进行静强度计算。
3.σmin=C的情况
当σmin=C时,需找到一个其最小应力与零件工 作应力的最小应力相同的极限应力。因为
分别是: 1 K ae m e
1 K ae m
ae
1
m
K
m ax
ae
m e
1
m
K
m
1
K
K
m
Sca
lim
m ax max
1 (K ) m
K
也有文献上建议,在σm=C的情况下,按照应力幅来 校核零件的疲劳强度,即按应力幅求得安全系数计算 值为
3 第三章 机械零件的疲劳强度《机械设计》
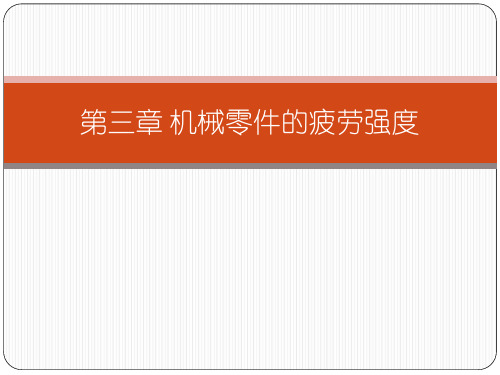
C点的极限应力为
计算安全系数及疲劳强度条件为:
σ′ k N σ -1 max Sσ = = ≥ [S] σ max (Kσ ) Dσa + ψσ σ m
N点的极限应力点N’位于直线 E’S上, 有: σ'm a x = σ′ α + σ′ m = σs
这说明工作应力为N点时,首 先可能发生的是屈服失效。故 只需要进行静强度计算即可。 σS σS = ≥ [S] 强度计算公式为: Sσ = σ max σ a + σ m
三、规律性非稳定变应力时的疲劳强度计算 按损伤累积假说进行疲劳强度计算 不稳定 规律性 如汽车钢板弹簧的载荷与应力受载重量、行车速度、轮胎充气成都、路面状况、驾驶员水平等因素有关。 变应力 非规律性 用统计方法进行疲劳强度计算
σmax σ1 σmax σ2 σ3 σ4 n2 n3 σ1 σ2
σ-1∞ O n 1
2)当应力作用顺序是先小 后大时,等号右边值 >1; z ni 0 .7 ~ 2 .2 一般情况有: i 1 N i 极限情况:
ni 1 i 1 N i
z
1 m m m i 1 ( n n ... n ) 1 1 1 2 2 z z m m N 0 1 N 0 1
§机械零件的工艺性及标准化
1 何为工艺性?
所设计的零件便于加工且加工费用低
25
2、标准化
对产品的品种、规格、质量、检验等制订标准并加以实施。 1)产品品种规格的系列化: 2)零部件的通用化: 3)产品质量标准化: 标准化的意义:
在制造上可实行专业化大量生产,既可提高产品质量,又 可降低成本;
在设计方面可减小设计工作量; 在管理维修方面,可减小库存和便于更换损坏的零件。
机械零件的疲劳强度
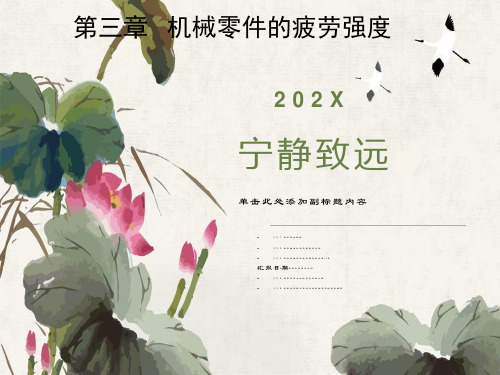
单击此处添加正文,文字是您思想的提炼,为了演示发布的良好效果,请言简意赅地阐述您的观点。您的内容已经 简明扼要,字字珠玑,但信息却千丝万缕、错综复杂,需要用更多的文字来表述;但请您尽可能提炼思想的精髓, 否则容易造成观者的阅读压力,适得其反。正如我们都希望改变世界,希望给别人带去光明,但更多时候我们只需 要播下一颗种子,自然有微风吹拂,雨露滋养。恰如其分地表达观点,往往事半功倍。当您的内容到达这个限度时, 或许已经不纯粹作用于演示,极大可能运用于阅读领域;无论是传播观点、知识分享还是汇报工作,内容的详尽固 然重要,但请一定注意信息框架的清晰,这样才能使内容层次分明,页面简洁易读。如果您的内容确实非常重要又 难以精简,也请使用分段处理,对内容进行简单的梳理和提炼,这样会使逻辑框架相对清晰。
02
LgσrN
N0
03
04
σr
σrN
m lgN0 lgN
05
N
06
lgN
07
m
08
1
lgrNlgr
❖ 2.循环基数N0 据材料性质不同N0取值也不同。通常金属的 N0取为107,随着材料的硬度↑,N0↑。有色金属及高强度合 金钢的疲劳曲线没有无限寿命区。
❖ 3. 不同循环特性r时的疲劳曲线如图所示,r↑→σrN↑、 (τrN↑)
a(kkN)D1(k1)Dm
21 0 0
m
m
a
a
m
m
a
a
a
(k
kN1 )D
m a
Saaa(k)DkNa1amkNa1eSa
2(ks )D
C m, a
c1
c
' 1
塑性安全区
O
H
G
机械设计之机械零件的疲劳强度

注意点:
1) rN , rH 与 rN 相似
2) N 0 为循环基数,与材料有关
3) r不同,同一材料疲劳曲线不同
2. 无限寿命区 N N0
疲劳曲线为一水平线,疲劳极限不随N的增加而降低。
3.2.3 极限应力图 m a(表示材料在不同的循环特性
下不同的疲劳极限)
是根据光滑小试件的试验结果绘制的。试验是在不同循环特 性(r =-1~+1)和相同循环次数(等寿命)的条件下进行。通 常取N0为107或106。试验结果即为材料的疲劳极限
1. 循环特性等于常数 如:轴的弯曲应力
O
循环特性相同的变应力都在同一射线上
tg a 1 r const m 1 r
r=1 tg 0 00
r=0 tg 1 450 r=-1 tg 900
零件的工作应力C( m , a ), m + a = max ,C点距O愈远,
例:已知某机械零件的材料的屈服极限σs=600MPa, σ-1=300MPa,(kσ)D=1.5,m=9,ψσ=0.2,实际应力循环 为106,(取N0=107),当零件截面上的最大应力为 200MPa,最小应力为-40MPa,(1)画出零件的疲劳极 限应力图;(2)求该零件的安全系数(r=常数)
k
D
k
k
D
k
应力集中、尺寸和表面状态都只对 a有影响,而对 m影响不大
3.4 许用疲劳极限应力图
3.4.1 稳定变应力和非稳定变应力
稳定变应力, a 、 m周期不 随时间变化(单向,复合)
非稳定变应力, a 、 m周期随 时间变化 (周期性,随机性 )
3.4.2 许用疲劳极限应力图
3.4.3 工作应力增长规律
解:
- 1、下载文档前请自行甄别文档内容的完整性,平台不提供额外的编辑、内容补充、找答案等附加服务。
- 2、"仅部分预览"的文档,不可在线预览部分如存在完整性等问题,可反馈申请退款(可完整预览的文档不适用该条件!)。
- 3、如文档侵犯您的权益,请联系客服反馈,我们会尽快为您处理(人工客服工作时间:9:00-18:30)。
3.1 疲劳断裂的特征
在交变应力作用下零件
主要失效形式之一为疲劳断
轴
裂。
发生过程:
交变 应力
表面小 裂纹
应力 集中
裂纹 扩展
宏观疲 劳纹
初始裂纹
疲劳区 (光滑) 粗糙区
局部 b
断裂
反复 作用
表3.1
3.2 疲劳曲线和疲劳极限应力图
3.2.1 疲劳极限
在一定的循环特性r下,变应力循环N次后,不发生 疲劳破坏的最大应力。
解:
kN
m
N0 N
9
107 106
1.29
0
2 1 1
2 300 500MPa 1 1.2
m
max min
2
80MPa
a
max min
2
120MPa
A(0, σ-1)=(0,300)
B (σ0/2, σ0/2)=(250,250)
S( s , 0) (600, 0)
强度条件:σ≤ [σ] lim
s
σlim = ?
3.2.2 疲劳曲线(固定r)
N — 应力循环次对应于N) σr
N
σr — 持久极限
N
N0
N0 — 循环基数
有限寿命区
变应力时,取 σlim = σr(无限寿命)
或
σlim = σrN(有限寿命)
则 [ ] r 或 rN 各种材料的σr可从有关手册中查取
例:已知某机械零件的材料的屈服极限σs=600MPa, σ-1=300MPa,(kσ)D=1.5,m=9,ψσ=0.2,实际应力循环 为106,(取N0=107),当零件截面上的最大应力为 200MPa,最小应力为-40MPa,(1)画出零件的疲劳极 限应力图;(2)求该零件的安全系数(r=常数)
A'(0, kN 1 ) (0,258)
(k )D
B'( kN 0 , kN 0 ) (322.5,215)
1)塑性材料
疲劳极限图
简化图:ABEGS折线 注意:
(1)ES—塑性极限曲线,其上各点 s m a (2)阴影BEG部分不安全,其余偏安全
2)脆性材料(见教材)
3.3 影响机械零件疲劳强度的主要因素
1、应力集中的影响 k ,k
2、尺寸的影响 , 3、表面状态的影响 ,
, 4、综合影响系数
机械设计
第3章 机械零件的疲劳强度
在交变应力作用下即使应力低于极限应力,塑性很好的 材料也会发生破坏(疲劳破坏)。疲劳破坏占破坏的80%以 上。在交变应力下是以σrN作为极限应力。
零件疲劳强度计算方法有两种:
安全—寿命设计:在规定的工作期限内,不允许出 现疲劳裂纹,一旦出现即认为零件失效。
破损—安全设计:允许零件存在裂纹,但须保证在 规定的工作期限内能安全可靠地工作。
'max max
'm 'a m a
平均应力安 全系数:
S m
m m
应力幅安全 系数:
S a
a a
(1) 图解法:
(a)工作点为C点时
最大应力安全系数:
S
'max max
'm 'a m a
OG GC ' OH HC
OC ' OC
应力幅安全系数:
S a
a a
GC ' HC
(b)工作点为C1点时 屈服安全系数:
S
s max
OL LC '1 OM MC1
OL OM
OC '1 OC1
(2) 解析法:
(a)工作点位 于疲劳安全区:
由A'E'的 直线方程:
σa
k N σ1 (kσ )D
1 (kσ )D
ψσσm
ψσ
2σ1 σ0 σ0
ψσ
——平均应力折合为应力幅的等效系数,表示材料 对循环不对称性的敏感程度。
s
s
1. 有与限应寿力命状的态高有周关 循环的区指数
rN m N 常数 r m N0
rN r m N0 / N
lgσrN
有限寿命区
无限寿命区
低周循环
高周循环
A
B
rN
m
N0 N
r
KN r
0
103 (10 4)
N0
lgN
K N —寿命系数
N N0
KN
m N0 N
1
N N 0 K N =1 rN r
OC的直线方程:
σm σ
σσa
m
a
得:
σa
(kσ
k N σ1 )D ψσσσma
则:
Sσa σσa a
kσ
(kσ
N
)σ Da
-1
ψσσm
S σa
(b)工作点位于塑性安全区:
Sσ
σ
σ a
s
σm
S σ
同理(对剪应力):
Sτa
ττaa
k Nτ1 (kτ)Dτa ψττm
S τa
Sτ
τ
τ a
注意点:
1) rN , rH 与 rN 相似
2) N 0 为循环基数,与材料有关
3) r不同,同一材料疲劳曲线不同
2. 无限寿命区 N N0
疲劳曲线为一水平线,疲劳极限不随N的增加而降低。
3.2.3 极限应力图 m a(表示材料在不同的循环特性
下不同的疲劳极限)
是根据光滑小试件的试验结果绘制的。试验是在不同循环特 性(r =-1~+1)和相同循环次数(等寿命)的条件下进行。通 常取N0为107或106。试验结果即为材料的疲劳极限
1. 循环特性等于常数 如:轴的弯曲应力
O
循环特性相同的变应力都在同一射线上
tg a 1 r const m 1 r
r=1 tg 0 00
r=0 tg 1 450 r=-1 tg 900
零件的工作应力C( m , a ), m + a = max ,C点距O愈远,
max 愈大,但 max≤ r零件才不
会破坏。
2. 平均应力等于等于常数 如:车辆减振弹簧
3. 最小应力等于常数 如:汽缸盖的螺栓联接
3.5 稳定变应力时的安全系数计算
3.5.1 单向应力状态时的安全系数
1. r = 常数 tg a
m
1 r const 1 r
最大应力安全系数: S
k
D
k
k
D
k
应力集中、尺寸和表面状态都只对 a有影响,而对 m影响不大
3.4 许用疲劳极限应力图
3.4.1 稳定变应力和非稳定变应力
稳定变应力, a 、 m周期不 随时间变化(单向,复合)
非稳定变应力, a 、 m周期随 时间变化 (周期性,随机性 )
3.4.2 许用疲劳极限应力图
3.4.3 工作应力增长规律
s
τm
S τ
说明:(1)上述公式对脆性材料也适用 (2)对于切应力方法相同,公式一致 (3)工作点作用在不同区域计算方法不同, 若区域不能确定两个区域都要计算。 (4)在N未知时作∞,KN=1
2.σm=常数
计算公式见书p49页,公式3.13~3.15
3.σmin=常数
计算公式见书p49页,公式3.16~3.18