第六章_摩擦材料产品的标准和检验分析
摩擦 标准

摩擦标准摩擦标准是指在各种工程设计和材料制造中,对摩擦性能的要求及评估方法的统一规范。
它旨在确保材料、零部件或产品在摩擦过程中的可靠性、稳定性和安全性。
根据不同的应用领域和目的,摩擦标准可以分为摩擦材料标准、摩擦副零部件标准和摩擦产品标准三类。
2.1 摩擦材料标准摩擦材料标准主要针对在摩擦磨损过程中使用的材料,如金属、陶瓷和高分子材料等。
这些标准规定了材料的化学成分、物理性能、摩擦系数和磨损性能等指标,以确保其在特定工况下的可靠性和寿命。
2.2 摩擦副零部件标准摩擦副零部件标准主要涉及机械设备中的摩擦传动装置,如轴承、齿轮和传动带等。
这些标准规定了摩擦副的结构参数、精度要求、摩擦系数和使用寿命等指标,以确保其在传递力量过程中的高效性、平稳性和安全性。
2.3 摩擦产品标准摩擦产品标准主要包括摩擦材料和摩擦副零部件的组合产品,如刹车片、离合器和摩擦片等。
这些标准规定了产品的结构设计、摩擦性能、安全性能和耐久性等指标,以确保其在特定工况下的可靠性和安全性。
3. 摩擦标准的制定过程摩擦标准的制定过程通常包括调研、技术论证、试验验证和标准修订四个阶段。
在调研阶段,相关领域的专家会收集和分析各类摩擦问题,并整理各国和行业的相关标准和规范。
在技术论证阶段,专家团队会对摩擦性能的评估方法和指标进行深入研究和讨论。
在试验验证阶段,实验室会进行一系列摩擦试验,并获取相关数据进行分析。
最后,在标准修订阶段,制定单位会根据实验数据和专家意见,对标准进行修订和完善。
4. 摩擦标准的应用价值摩擦标准的应用可以有效确保产品的质量和安全性,同时降低生产成本和提高生产效率。
通过遵循摩擦标准,企业能够选择符合要求的材料和零部件,提高产品的可靠性和耐久性,减少维修和更换费用。
对于消费者而言,摩擦标准可以保障产品的使用安全和性能稳定,提供产品质量的可靠保证。
5. 摩擦标准的发展趋势随着科技的不断进步和工业化水平的提高,对摩擦性能的要求也越来越高。
摩擦材料研究报告
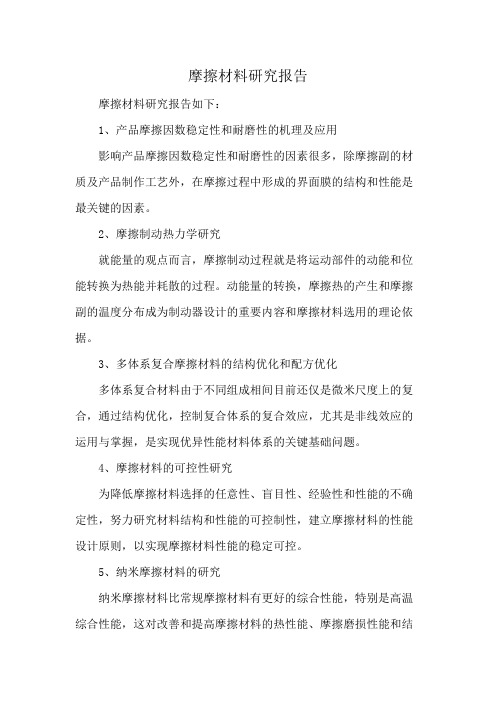
摩擦材料研究报告
摩擦材料研究报告如下:
1、产品摩擦因数稳定性和耐磨性的机理及应用
影响产品摩擦因数稳定性和耐磨性的因素很多,除摩擦副的材质及产品制作工艺外,在摩擦过程中形成的界面膜的结构和性能是最关键的因素。
2、摩擦制动热力学研究
就能量的观点而言,摩擦制动过程就是将运动部件的动能和位能转换为热能并耗散的过程。
动能量的转换,摩擦热的产生和摩擦副的温度分布成为制动器设计的重要内容和摩擦材料选用的理论依据。
3、多体系复合摩擦材料的结构优化和配方优化
多体系复合材料由于不同组成相间目前还仅是微米尺度上的复合,通过结构优化,控制复合体系的复合效应,尤其是非线效应的运用与掌握,是实现优异性能材料体系的关键基础问题。
4、摩擦材料的可控性研究
为降低摩擦材料选择的任意性、盲目性、经验性和性能的不确定性,努力研究材料结构和性能的可控制性,建立摩擦材料的性能设计原则,以实现摩擦材料性能的稳定可控。
5、纳米摩擦材料的研究
纳米摩擦材料比常规摩擦材料有更好的综合性能,特别是高温综合性能,这对改善和提高摩擦材料的热性能、摩擦磨损性能和结
构强度提供了新的技术途径。
6、工艺的研发
研发“优质、高效、节能、低耗、少或无污染”的摩擦材料制品生产工艺,对提高技术经济效益意义重大
7、摩擦材料表面工程研究
通过表面工程处理,可有效提高相对运动的两物体即摩擦副的耐磨性和减少运动时的摩擦损耗,到达减少摩擦和控制磨损的目的。
产品质量监督抽查实施细则——摩擦材料

产品质量监督抽查实施细则——摩擦材料产品质量监督抽查是国家监管部门对市场上的产品进行定期抽样检验,以确保产品的质量和安全符合相关标准和法规规定。
摩擦材料作为一类重要的工业材料,其质量直接关系到产品的性能和使用寿命,因此在产品质量监督抽查实施细则中应给予特别关注。
一、抽样方法1.采用随机抽样的方法进行抽样,即按照一定的概率,从生产企业、销售商、市场等渠道中选择样本。
2.抽样时应注意产品的批次,对同一批次的产品进行抽样,以便推断整个批次产品的质量情况。
3.抽样时应保证样品的代表性,既要涵盖不同规格、型号的产品,也要覆盖不同生产企业、销售商的产品。
4.抽样时应考虑产品销售量、市场份额等因素,优先选择销售量大、市场份额高的产品进行抽样。
二、检验项目与方法1.外观检验:对摩擦材料的外观进行检验,包括表面是否平整、无裂纹、无气泡等。
2.尺寸检验:检验摩擦材料的尺寸是否符合标准要求,包括厚度、宽度、长度等。
3.力学性能检验:检验摩擦材料的抗拉强度、硬度等力学性能指标是否符合标准要求。
4.摩擦性能检验:对摩擦材料进行摩擦试验,测量其摩擦系数、磨损量等指标。
三、检验标准1.国家相关标准:按照国家发布的相关标准进行检验,例如GB/T2578《摩擦材料力学性能试验方法》等。
2.行业标准:摩擦材料行业协会或专业组织制定的行业标准,如《摩擦材料尺寸与外观检验方法》等。
3.企业标准:企业自行制定的标准,要求企业对产品的质量进行自我控制和检验。
四、抽样与检验频次1.抽样频次应由国家监管部门根据市场情况和产品特点确定,一般每年至少进行一次。
2.对于市场上销售量较大、市场份额较高的摩擦材料,可以增加抽样频次,保证产品的质量稳定。
3.对于发现问题较多的生产企业或销售商,应加大抽样频次,并在发现问题后进行追踪抽查。
五、结果处理与措施1.对于抽样所得样品,按照检验结果判断其是否合格,同时对不合格样品要进行进一步调查和处理。
2.不合格样品应按照相关法规规定,要求生产企业或销售商进行整改、下架等处理措施。
_摩擦材料产品的标准和检验22页PPT

21、静念园林好,人间良可辞。 22、步步寻往迹,有处特依依。 23、望云惭高鸟,临木愧游鱼。 24、结庐在人境,而无车马喧;问君 何能尔 ?心远 地自偏 。 25、人生归有道,衣食固其端。
61、奢侈是舒适的,ຫໍສະໝຸດ 则就不是奢侈 。——CocoCha nel 62、少而好学,如日出之阳;壮而好学 ,如日 中之光 ;志而 好学, 如炳烛 之光。 ——刘 向 63、三军可夺帅也,匹夫不可夺志也。 ——孔 丘 64、人生就是学校。在那里,与其说好 的教师 是幸福 ,不如 说好的 教师是 不幸。 ——海 贝尔 65、接受挑战,就可以享受胜利的喜悦 。——杰纳勒 尔·乔治·S·巴顿
谢谢!
摩擦材料质量检验管理制度

质量检验管理制度WR/ZC—11—2009质检部门负责贯彻严格落实本制度、质检人员负责执行、实施。
工序质量检验执行“三检制”即首件必检、中间巡检、完工入库检.1、首件必检:(1)生产人员每批加工的零件的第一个件为首件。
(2)操作者首件自检合格后交检查员检查,首件合格后方可继续加工,无合格首件私自加工出现的问题由操作者负全部经济责任.2、中间巡检:在首件合格的基础上,操作者在加工过程中应经常抽检所加工的零件是否符合图样和工艺要求,是否和首件一样合格,检验员应定期或不定期进行巡检,(每工作日至少巡检三次)对抽检件按产品标识制度做好标记,以免重复检查,发现违犯工艺要求的行为应及时制止,发现质量问题应及时告诉操作者,大的质量问题应及时报告主管技术、质量负责人并落实解决。
3、完工入库检验:一批零件完工并自检合格后交检查员全面检查,检验员、检验合格后,在零件入库单上签字、盖章后方可作工序传递或办理入库手续。
4、工序流程检验实行三级检验制度,即自检、互检、专检。
自检即本序生产的产品必须自检,自检符合相关规程的要求后按产品标识制度进行标识才能转入下序。
互检是指本序对上序转入的产品要按照相关检验规程进行检验;本序转出的产品由下序按照相关检验规程进行检验;专检是指质检员按照相关检验规程进行抽检或全检,检验不合格的按不合格品控制办法及产品标识制度进行处理。
生产过程质量管理制度1、岗位操作人员必须经过培训.培训人员经评审、考核合格后方能上岗。
2、操作人员必须进行设备的结构、性能及工装、模具的操作、方法的学习和应用,科学规范操作,重要工序须定人、定机、定工种。
3、设备、工装在安装使用前均须验证其精度。
对满足不了质量要求的应修理或更新.4、计量器具、实验仪器必须到计量部门定期计量,计量合格的方能使用,严禁超期使用各类计量器具及实验仪器等.5、各工序严格执行质量管理制度,认真执行生产工艺、作业指导书,树立“质量第一,预防为主"的观念,正确处理“质”与“量"的关系,支持、落实质量部门的否决权。
摩擦材料

填料
摩擦材料组分中的填料,主要是由摩擦性能调节剂和配合剂组成。使用填料的目的,主要有以下几个方面: (1)调节和改善制品的摩擦性能、物理性能与机械强度。 (2)控制制品热膨胀系数、导热性、收缩率,增加产品尺寸的稳定性。 (3)改善制品的制动噪音。 (4)提高制品的制造工艺性能与加工性能。 (5)改善制品外观质量及密度。 (6)降低生产成本。 在摩擦材料的配方设计时,选用填料必须要了解填料的性能以及在摩擦材料的各种特性中所起到的作用。正 确使用填料决定摩擦材料的性能,在制造工艺上也是非常重要的。 根据摩擦性能调节剂在摩擦材料中的作用,可将其分为“增磨填料”与“减磨填料”两类。摩擦材料本身属 于摩阻材料,为能执行制动和传动功能要求具有较高的摩擦系数,因此增摩填料是摩擦性能调节剂的主要成分。 数
物理性能
摩擦系数
摩擦系数是评价任何一种摩擦材料的一个最重要的性能指标,关系着摩擦片执行传动和制动功能的好坏。它 不是一个常数,而是受温度、压力、摩擦速度或表面状态及周围介质因素等影响而发生变化的一个数。理想的摩 擦系数应具有理想的冷摩擦系数和可以控制的温度衰退。由于摩擦产生热量,增高了工作温度,导致了摩擦材料 的摩擦系数发生变化。
介绍
介绍
摩擦材料是一种高分子三元复合材料,是物理与化学复合体。它是由高分子粘结剂(树脂与橡胶)、增强纤 维和摩擦性能调节剂三大类组成及其它配合剂构成,经一系列生产加工而制成的制品。
摩擦材料的特点是具有良好的摩擦系数和耐磨损性能,同时具有一定的耐热性和机械强度,能满足车辆或机 械的传动与制动的性能要求。它们被广泛应用在汽车、火车、飞机、石油钻机等各类工程机械设备上。民用品如 自行车、洗衣机等作为动力的传递或制动减速用不可缺少的材料。
摩擦材料标准
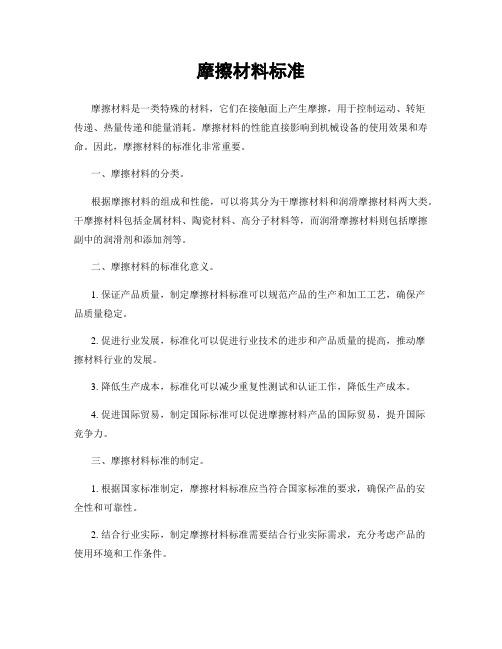
摩擦材料标准摩擦材料是一类特殊的材料,它们在接触面上产生摩擦,用于控制运动、转矩传递、热量传递和能量消耗。
摩擦材料的性能直接影响到机械设备的使用效果和寿命。
因此,摩擦材料的标准化非常重要。
一、摩擦材料的分类。
根据摩擦材料的组成和性能,可以将其分为干摩擦材料和润滑摩擦材料两大类。
干摩擦材料包括金属材料、陶瓷材料、高分子材料等,而润滑摩擦材料则包括摩擦副中的润滑剂和添加剂等。
二、摩擦材料的标准化意义。
1. 保证产品质量,制定摩擦材料标准可以规范产品的生产和加工工艺,确保产品质量稳定。
2. 促进行业发展,标准化可以促进行业技术的进步和产品质量的提高,推动摩擦材料行业的发展。
3. 降低生产成本,标准化可以减少重复性测试和认证工作,降低生产成本。
4. 促进国际贸易,制定国际标准可以促进摩擦材料产品的国际贸易,提升国际竞争力。
三、摩擦材料标准的制定。
1. 根据国家标准制定,摩擦材料标准应当符合国家标准的要求,确保产品的安全性和可靠性。
2. 结合行业实际,制定摩擦材料标准需要结合行业实际需求,充分考虑产品的使用环境和工作条件。
3. 强化质量控制,标准化需要强化对原材料、生产工艺、产品检测等方面的质量控制,确保产品符合标准要求。
四、摩擦材料标准的内容。
1. 材料成分,标准应明确摩擦材料的成分和配比要求,确保产品的稳定性和可靠性。
2. 技术要求,标准应包括摩擦材料的物理性能、化学性能、摩擦性能等技术要求,以保证产品的使用效果。
3. 检测方法,标准应明确摩擦材料的检测方法和标准,以保证产品检测结果的准确性和可靠性。
4. 标识和包装,标准应规定摩擦材料的标识和包装要求,以便用户正确选择和使用产品。
五、摩擦材料标准的推广和应用。
1. 推广宣传,摩擦材料标准的制定需要通过各种渠道进行推广宣传,提高行业从业人员和用户的认知度。
2. 应用指导,制定摩擦材料标准后,需要及时向行业内的生产企业和用户提供应用指导和技术支持。
3. 完善体系,摩擦材料标准的推广和应用需要建立完善的标准体系,确保标准的贯彻执行和实施效果。
摩擦材料试验方法

摩擦材料试验方法摩擦材料试验方法主要涉及到以下几个方面:摩擦系数测试、磨损试验、磨粒试验、摩擦噪声测试等。
具体试验方法可以根据实际需要选择合适的试验设备和试验标准。
以下将分别介绍这几个方面的试验方法。
摩擦系数测试是衡量材料摩擦性能的重要指标之一。
常用的试验方法包括横向滑动试验、直线摩擦试验和环状摩擦试验。
横向滑动试验是将试样放在滑动台上,施加一定的力,通过测量滑动台的位移和力的大小计算摩擦系数。
直线摩擦试验是将试样安装在一根直线上,通过施加一定的力,测量试样在直线上滑动的阻力和位移来计算摩擦系数。
环状摩擦试验是将试样制成环形,放在摩擦试验机上,通过施加一定的力,测量摩擦力和位移来计算摩擦系数。
这些试验方法可以根据实际需要选择合适的试验设备和试验条件进行。
磨损试验是评价摩擦材料的耐磨性能的重要方法。
常用的试验方法包括滑动磨损试验、滚动磨损试验和磨粒磨损试验。
滑动磨损试验是将试样安装在摩擦试验机上,施加一定的载荷和滑动速度,通过测量试样的质量损失、尺寸变化和表面形貌来评价材料的磨损性能。
滚动磨损试验是将试样制成滚动体或轴承,在一定负载和转速下进行滚动,在一定的时间内测量试样的质量损失和表面形貌来评估材料的耐磨性能。
磨粒磨损试验是将一定数量的磨粒添加到试样和滑动界面中,通过测量试样的磨损量和表面形貌来评价材料的耐磨性能。
这些试验方法可以根据实际需要选择合适的试验设备和试验条件进行。
磨粒试验是评估摩材料抗磨特性的一种重要方法。
常用的试验方法包括磨损试验、摩擦试验和颗粒磨损试验。
磨损试验是将试样安装在试验机械中,施加一定的力和速度,通过测量试样的质量损失和表面形貌来评价材料的抗磨性能。
摩擦试验是将试样和摩擦体放在试验设备中,施加一定的载荷和速度,通过测量摩擦系数和磨损量来评估材料的抗磨性能。
颗粒磨损试验是将一定数量的颗粒添加到试样和摩擦界面中,通过测量试样的磨损量和颗粒的质量损失来评价材料的抗磨性能。
这些试验方法可以根据实际需要选择合适的试验设备和试验条件进行。
- 1、下载文档前请自行甄别文档内容的完整性,平台不提供额外的编辑、内容补充、找答案等附加服务。
- 2、"仅部分预览"的文档,不可在线预览部分如存在完整性等问题,可反馈申请退款(可完整预览的文档不适用该条件!)。
- 3、如文档侵犯您的权益,请联系客服反馈,我们会尽快为您处理(人工客服工作时间:9:00-18:30)。
谢谢!
6.6 显微组织检验
烧结摩擦材料的显微组织由金属基体、不与金属基 体相互作用的金属和非金属夹杂和孔隙组成。零件的物 理机械性能和使用性能在很大程度上取决于基体组织的 性质、相组成及其他成分的分布。因此,对烧结摩擦材 料的显微组织必须进行检验,可是在某些情况下,烧结 制品的生产者对材料显微组织的检验还没行给予应有的 重视。
• 无打击密实矫正:矫正不要求专门的工具。在进行此 项操作时,加压应避免冲击。因此,矫正是在放在液 压机柱塞下面的淬过火的钢板上进行的,而且柱塞的 行速不得超过30毫米/秒。矫正时所采用的单位压力 不得超过材料的抗压强度。经矫正处理后零件的高度 降低(对铁基制品来说平均为0.1-0.3毫米),而其密 度和硬度得到提高。此外,硬度的提高取决于其原始 值:原始硬度越低,矫正时的改变值就越大。矫正不 仅能提高零件的硬度而且能消除翘曲。在某些情况下。 矫正还能减小烧结制品的厚度,使之达到图纸的要求。
摩擦粉末片的熔化; 摩擦粉末片在钢背上的位移; 摩擦粉末片的缺陷(割裂、裂纹、凹陷、分层、疏松); 氧化; 摩擦粉末片变扁; 摩擦粉末片油槽不够深等。
6.2 几何尺寸的检查
• 零件几何尺寸的检查一般是用精度为0.01-0.10毫米的 普通测量工具(测微器、卡尺)来进行的。由于多数零件 要进行机加工,因此,要留有一定的余量,一般为 0.3-0.7毫米。 • 零件尺寸应当与图纸相符,零件翘曲超过给定极限便视 作烧结废品。该类废品的原因是采用变了形的垫盘或在 无压情况下将零件从高温冷却,翘曲零件可通过无打击 矫直或复烧来补救。如果这些工序都不能矫正,零件便 报废。 • 对那些在烧结过程中压出油槽的摩擦盘还要进行油槽几 何形状及尺寸的检查。违反最佳烧结参数以及使用不标 准的造形垫环均能引起油槽尺寸偏离给定尺寸。该类废 品是不可补救的。
摩擦材料硬度的测定方法:
• • • • 测定青铜基摩擦材料的硬度多用布氏硬度计; 测定铁基材料的硬度则多用布氏硬度计和洛氏硬度计; 烧结件的硬度在机加工前测定; 至少测定三个点,取平均值作为测定值。
6.5 粉末片与钢背的结合质量
• 结合质量检测方法:弯曲法。用压力机或人工将零件弯曲。 在某些情况下,弯曲是在钢辊上进行的,弯曲时钢背与钢 辊接触,钢辊的直径取决于所测定零件的尺寸。在用弯曲 法检查摩擦粉末片与钢背结合质量的同时也检查了钢背塑 性。 超声波法
• 零件的弯曲角度:取决于材料的成分,材料的塑性以及零 件的几何形状和尺寸。铜基材料:90-160°,铁基材料: 15°。
• 检验结果:青铜基摩擦零件,结合质量不合格——报废; 铁基摩擦零件——复烧。
摩擦粉末片与钢背结合不良原因:
钢背电镀层的质量不高; 烧结时使用了氧化了的钢背和粉末片; 违返了给定的烧结制度(首先是烧结时所加压力); 使用了翘曲变形的装置。
6.7 材料的摩擦性能和磨损性能
摩擦材料的主要使用性能——摩擦系数及耐 磨性取决于摩擦材料及配对零件的化学成分及组 织,也取决于摩擦部件的结构特点及摩擦部件的 使用参数及条件。因此,为了确定摩擦偶的使用 性能,要进行一系列的预先试验,这些试验应能 使预先的估价试验接近于制动装置或传动装置的 实际使用条件下的估价。
显微组织研究方法:显微磨片法。 设备:金相显微镜(彩色为佳),三维形貌仪,电子显 微镜。 腐蚀剂: 铁基摩擦材料——4%的硝酸酒精 铜基材料——第一种——2克重铬酸,8毫升硫酸(比 重1.84克/厘米3),4毫升氯化钠(饱和溶液)及 100毫升蒸馏水;第二种——25克二氯化铁,25毫升 盐酸(比重1.19克/厘米3及100毫升蒸馏水。
• 孔隙同样应当均匀地分布在材料的整个体积中。孔隙 度不应超过该材料的允许极限。垂直照明腐蚀磨片及 未腐蚀过的磨片均可很好地看出孔隙度。在制备良好 的磨片上,孔隙很容易与灰色的鳞片状石墨分辨开来, 正如前面已经指出的,孔隙形状取决于材料的烧结方 法:无压烧结时孔隙呈圆形,加压烧结时孔隙的取向 与压力方向相垂直。 • 在研究钢背和粉末片之间的中间区域结构时,要检验 钢背上形成的电镀层的厚度与均匀度、中间层的厚度 及均匀度;是否存在有凹陷、杂质和疏松等现象。为 了使烧结摩擦层与钢背有良好的结合,大部分情况下, 在它们之间必须有显微硬度不小于材料基体显微硬度 的一定厚度的完整过渡中间层(不得有非金属夹杂物和 孔隙)。
摩擦材料产品的标准和 检验
前言
检验标准:
• 为了检测摩擦材料是否合格,人们根据具体摩擦材料 的使用条件、制备工艺、材料组分等特点,制订了摩 擦材料的检测标准。例如BS ISO 15484-2008标准 就是专门为道路车辆、制动衬面摩擦材料制订的产品 定义和质量保证标准,它是参照国际ISO标准,并根 据我国具体情况制订并下发严格执行的一个摩擦材料 产品的标准。另外,在国际或国家标准里,还有一些 是专门针对摩擦材料某方面性能的检测标准,如 GB/T 10430-2008(烧结金属摩擦片粘结性能检验 方法),就是针对摩擦片粘结性能进行检测的文件。
检验项目:
• 在烧结摩擦制品生产过程中,半成品(粉料、压件)要 进行按工序的质量检查,成品也要经过质量检查。检 查有以下各项目:外观、几何尺寸、化学成分、硬度、 摩擦层与钢背的结合质量、显微组织、摩擦性能等。 在某些情况下,还检验钢背的硬度和塑性。
6.1零件的肉眼观察
对成品进行肉眼观察可发现下列废品:
摩擦磨损试验建议按如下程序进行:
• 测定材料的物理机械性能,以便在计算确定材料的摩 擦性能时加以考虑; • 在实验室进行摩擦和磨损试验,以便估价物理机械性 能及摩擦制度(速度、压力、温度)对材料的摩擦系数 及磨损的影响; • 进行摩擦试件台架试验,这种试验可确定各种结构参 数对材料摩擦性能的影响; • 现场试验,以便确定整个机构的可靠性和使用寿命; • 为了检验大批量生产的制品的摩擦性能,既进行从成 品上切割的试件的实验室试验,也进行成品的台架试 验,用摩擦试验机来进行摩擦性能和磨损性能的实验 室试验或模拟试验。
检验方法:
• 化学分析法 • 光谱法。
6.4 硬度的测定
烧结材料的硬度能说明烧结过程进行的完全程度,它 首先取决于孔隙度。孔隙度最终又影响制品的物理机械 性能和使用性能。测定硬度的方法取决于零件的几何形 状,尺寸以及摩擦材料的成分,通常在相应的技术条件 中都有说明。 偏离给定硬度的原因: 压制时的粉末称量不准确, 偏离了正常的烧结(或热处理)工艺, 烧结时使用了翘曲装置, 将制品叠装入容器内时发生了倾斜及一些其他原因。
硬度不合格的补救措施:
• 复烧:复烧及无打击密实矫正都会提高材料的密度, 用来补救硬度低的零件。复烧制度是根据材料成分、 零件的几何尺寸及第一次烧结时所达到的硬度来确定 的。此时还必须考虑到摩擦粉末片的成分变化(如由于 石墨的烧损、铅的熔出等),钢背的渗碳及由此产生的 脆化,保持零件尺寸及摩擦粉末片上油槽的几何形状 的必要性。 • 退火:铁基摩擦材料的硬度比较高,这是因为材料的 密度大,又因为其显微组织发生了变化,摩擦粉末片 组织中珠光体和渗碳体增多就会使硬度增高,而铁素 体和石墨增多则会降低其硬度。硬度过高的零件需要 退火,零件的性能取决于退火工艺。
6.3摩擦材料的化学成分
在摩擦零件制造过程中,粉料、压件、烧结粉末片以 及热处理片都要进行化学成分的检验。其中粉料和烧结件 的化学成分检验是必须进行的,压件进行化学分析是不合 算的。 • 对铜基摩擦材料在工艺过程各阶段的化学成分的专门研究 表明只有铅含量变化最大,石墨很少变化,而其余成分(铁、 石墨、锡)的含量则仍保持在材料的允许误差范围内。因此, 建议只测定铅在烧结摩擦粉末片中的含量,其余成分的含 量视作与原始粉料中的相同。 • 显然,对铁基材料来说,也是只检验那些在烧结过程中含 量会发生变化的成分才是合算的。属于这类元素的有:石 墨、金属硫化物、易熔金属。
注意事项:
• 在进行烧结制品的组织分析时,首先要考虑的是个别结 构成分的分布和大小。通过金属粉末在烧结过程中扩散 所形成的金属基体(钢和锡及铜和锌等)如是合格制品,必 须是能够保证基体强度的完整骨架。结合力不强的骨架 由于表面颗粒聚集体被剥落会降低材料的强度和耐磨性。 • 在含有鳞片状石墨的摩擦材料中,石墨颗粒在压制时会 取与压制方向相垂直的方向。单向压制时会形成层状结 构使材料的摩擦剂(例如二氧化硅)应当均匀地分布在金属 基体中。同时,颗粒形状和粒度也很重要,对于青铜基 材料来说,采用粉碎粒度为30-60微米的棱角状的二氧 化硅顺粒最为适宜;用浮选和沉降法所得到的球状颗粒 以及更细粒度的颗粒均不适宜,因为用这种二氧化硅制 成的材料摩擦性能差。氧化铝、铝硅酸盐等有类似的作 用。