三预热模式在厚壁管焊接中的应用
焊接预热和后热的理论及应用
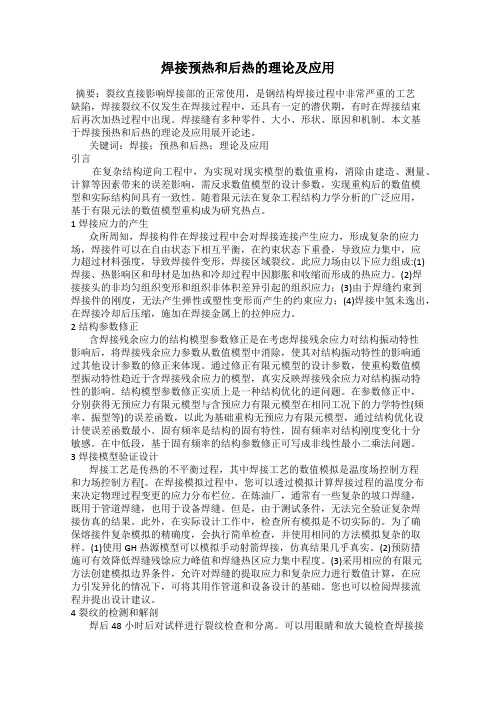
摘要:裂纹直接影响焊接部的正常使用,是钢结构焊接过程中非常严重的工艺缺陷,焊接裂纹不仅发生在焊接过程中,还具有一定的潜伏期,有时在焊接结束后再次加热过程中出现。焊接缝有多种零件、大小、形状、原因和机制。本文基于焊接预热和后热的理论及应用展开论述。
关键词:焊接;预热和后热;理论及应用
4裂纹的检测和解剖
大镜检查焊接接头表面和横截面上的裂纹。分离步骤和分离率分别计算:(1)敲击焊接泥,清洁焊接表面的污垢,并用较小的放大镜观察焊接表面。记录并记录焊缝表面粗糙度。(2)用圆盘刀具将试验焊接切割成六个等宽的圆盘,检查并记录五个断面裂缝的深度。(3)计算表面裂纹的发生和横断面裂纹的发生。
3焊接模型验证设计
焊接工艺是传热的不平衡过程,其中焊接工艺的数值模拟是温度场控制方程和力场控制方程[。在焊接模拟过程中,您可以透过模拟计算焊接过程的温度分布来决定物理过程变更的应力分布栏位。在炼油厂,通常有一些复杂的坡口焊缝,既用于管道焊缝,也用于设备焊缝。但是,由于测试条件,无法完全验证复杂焊接仿真的结果。此外,在实际设计工作中,检查所有模拟是不切实际的。为了确保熔接件复杂模拟的精确度,会执行简单检查,并使用相同的方法模拟复杂的取样。(1)使用GH热源模型可以模拟手动射箭焊接,仿真结果几乎真实。(2)预防措施可有效降低焊缝残馀应力峰值和焊缝热区应力集中程度。(3)采用相应的有限元方法创建模拟边界条件,允许对焊缝的提取应力和复杂应力进行数值计算,在应力引发异化的情况下,可将其用作管道和设备设计的基础。您也可以检阅焊接流程并提出设计建议。
引言
在复杂结构逆向工程中,为实现对现实模型的数值重构,消除由建造、测量、计算等因素带来的误差影响,需反求数值模型的设计参数,实现重构后的数值模型和实际结构间具有一致性。随着限元法在复杂工程结构力学分析的广泛应用,基于有限元法的数值模型重构成为研究热点。
火力发电厂厚壁大径管焊接接头热处理探讨

火力发电厂厚壁大径管焊接接头热处理探讨摘要:火力发电厂焊接热处理通过在焊前、焊中或焊后将焊件全部或部分加热到一定温度,保持一定时间,然后以适当的速率冷却,以提高焊接工艺性能,是一种改进的工艺方法。
本文对火电厂焊接接头的热处理进行了分析。
关键词:火力发电厂;焊接接头;热处理引言焊缝热处理是在焊前、焊中或焊后将焊件全部或部分加热到一定温度,保持一定时间,然后以适当的速度冷却,从而提高焊接工艺性能和机械性能。
一种工件焊接接头金相组织的加工方法。
焊接热处理包括预热、后加热和焊后热处理。
焊后热处理通常是高温回火,目的是降低焊接残余应力,改善焊缝的金属组织和力学性能,如果焊缝处理不当,在焊接过程中很容易开裂。
小则影响机组正常运行,大则造成停机,引发安全事故,给投资方造成巨大损失。
焊缝热处理对于释放金属材料的性能潜力、延长接头寿命和提高其经济效益非常重要。
一、焊接接头热处理现状在火力发电厂基础设施建设过程中,焊接工作量较大,电厂基础建设中厚壁大径管焊接热处理工作主要包括锅炉连通管、锅炉集箱、启动系统管道以及汽机四大管道等。
这些焊接项目都需要进行焊接热处理。
影响焊接接头热处理的因素主要有:热处理人员技能水平、责任心、热处理设备性能状况、焊接接头的结构形式以及焊工施焊过程中焊接工艺的执行情况等;焊接接头热处理的效果一般以热处理后的硬度检验为主、金相检验为辅;热处理工艺合格是焊缝硬度合格的先决条件,因此加强热处理施工过程工艺监控十分必要。
热处理后焊缝的硬度测试只是一个抽样检测,即使经过100%的检测,仍然是一个抽样检测。
由于焊缝的热处理往往是分区控制的,所以检测点的硬度并不意味着规定了整个焊缝所有区域的硬度。
因此,热处理人员需要较高的理论知识、丰富的施工经验和高度的责任感。
二、焊后热处理的目的焊后热处理的目的是通过加热和冷却使焊缝金属和合金获得期望的微观组织,以便改变焊接接头的工艺性能或提高焊接接头的使用性能,从而延长其使用寿命。
预热处理在焊接应用技术中的作用
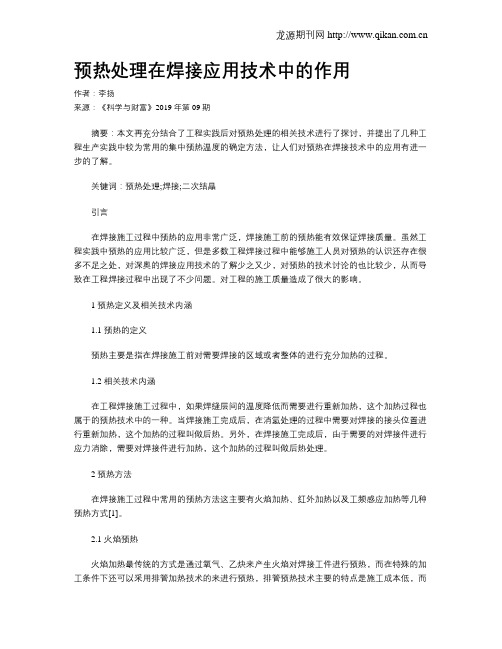
预热处理在焊接应用技术中的作用作者:李扬来源:《科学与财富》2019年第09期摘要:本文再充分结合了工程实践后对预热处理的相关技术进行了探讨,并提出了几种工程生产实践中较为常用的集中预热温度的确定方法,让人们对预热在焊接技术中的应用有进一步的了解。
关键词:预热处理;焊接;二次结晶引言在焊接施工过程中预热的应用非常广泛,焊接施工前的预热能有效保证焊接质量。
虽然工程实践中预热的应用比较广泛,但是多数工程焊接过程中能够施工人员对预热的认识还存在很多不足之处,对深奥的焊接应用技术的了解少之又少,对预热的技术讨论的也比较少,从而导致在工程焊接过程中出现了不少问题。
对工程的施工质量造成了很大的影响。
1 预热定义及相关技术内涵1.1 预热的定义预热主要是指在焊接施工前对需要焊接的区域或者整体的进行充分加热的过程。
1.2 相关技术内涵在工程焊接施工过程中,如果焊缝层间的温度降低而需要进行重新加热,这个加热过程也属于的预热技术中的一种。
当焊接施工完成后,在消氢处理的过程中需要对焊接的接头位置进行重新加热,这个加热的过程叫做后热。
另外,在焊接施工完成后,由于需要的对焊接件进行应力消除,需要对焊接件进行加热,这个加热的过程叫做后热处理。
2 预热方法在焊接施工过程中常用的预热方法这主要有火焰加热、红外加热以及工频感应加热等几种预热方式[1]。
2.1 火焰预热火焰加热最传统的方式是通过氧气、乙炔来产生火焰对焊接工件进行预热,而在特殊的加工条件下还可以采用排管加热技术的来进行预热,排管预热技术主要的特点是施工成本低,而且对工件的预热均匀性也要比传统火焰加热方法好,在实际的操作过程中,使用的比较简单。
但是排管加热方法的主要缺点就是其预热的温度很难控制,温度控制的精度比较低,而且加热速度的控制也比较困难。
2.2 工频感应预热工频感应预热主要是利用工业频率为50Hz的交流电的来让焊接工件产生一个交变磁场,并形成磁场涡流,这样就能让焊接工件逐渐产生热量。
焊接过程控制措施

焊接过程控制措施一、预热、后热及热处理1、本工程中包括的厚板的焊接都要求在焊前必须预热。
焊前预热的主要作用如下:(1)预热能减缓焊后的冷却速度,有利于焊缝金属中扩散氢的逸出,避免产生氢致裂纹。
同时也减少焊缝及热影响区的淬硬程度,提高了焊接接头的抗裂性。
(2)预热可降低焊接应力。
均匀地局部预热或整体预热,可以减少焊接区域被焊工件之间的温度差(也称为温度梯度)。
这样,一方面降低了焊接应力,另一方面,降低了焊接应变速率,有利于避免产生焊接裂纹。
(3)预热可以降低焊接结构的拘束度,对降低角接接头的拘束度尤为明显,随着预热温度的提高,裂纹发生率下降。
预热温度和层间温度的选择不仅与钢材和焊条的化学成分有关,还与焊接结构的刚性、焊接方法、环境温度等有关,应综合考虑这些因素后确定。
另外,预热温度在钢材板厚方向的均匀性和在焊缝区域的均匀性,对降低焊接应力有着重要的影响。
局部预热的宽度,应根据被焊工件的拘束度情况而定,一般应为焊缝区周围各三倍壁厚,且不得少于150-200毫米。
如果预热不均匀,不但不减少焊接应力,反而会出现增大焊接应力的情况。
焊后热处理的目的有三个:消氢、消除焊接应力、改善焊缝组织和综合性能。
焊后消氢处理,是指在焊接完成以后,焊缝尚未冷却至100℃以下时,进行的低温热处理。
一般规范为加热到200~350℃,保温2-6小时。
焊后消氢处理的主要作用是加快焊缝及热影响区中氢的逸出,对于防止低合金钢焊接时产生焊接裂纹的效果极为显著。
在焊接过程中,由于加热和冷却的不均匀性,以及构件本身产生拘束或外加拘束,在焊接工作结束后,在构件中总会产生焊接应力。
焊接应力在构件中的存在,会降低焊接接头区的实际承载能力,产生塑性变形,严重时,还会导致构件的破坏。
消应力热处理是使焊好的工件在高温状态下,其屈服强度下降,来达到松弛焊接应力的目的。
常用的方法有两种:一是整体高温回火,即把焊件整体放入加热炉内,缓慢加热到一定温度,然后保温一段时间,最后在空气中或炉内冷却。
核电WB36CN1大口径厚壁管的焊接
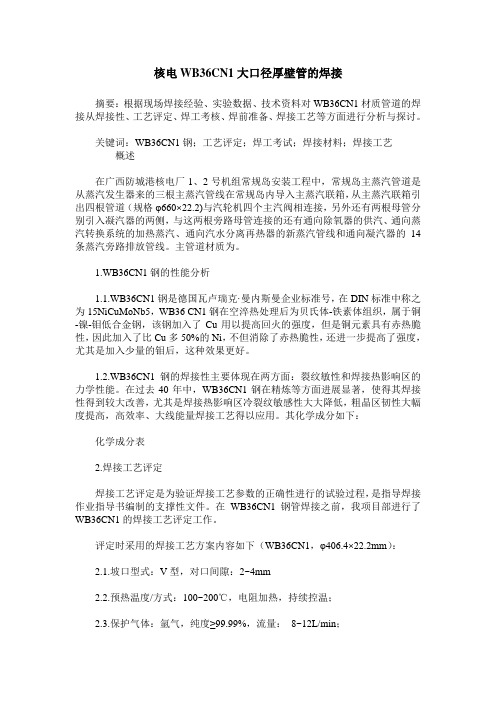
核电WB36CN1大口径厚壁管的焊接摘要:根据现场焊接经验、实验数据、技术资料对WB36CN1材质管道的焊接从焊接性、工艺评定、焊工考核、焊前准备、焊接工艺等方面进行分析与探讨。
关键词:WB36CN1钢;工艺评定;焊工考试;焊接材料;焊接工艺概述在广西防城港核电厂1、2号机组常规岛安装工程中,常规岛主蒸汽管道是从蒸汽发生器来的三根主蒸汽管线在常规岛内导入主蒸汽联箱,从主蒸汽联箱引出四根管道(规格φ660×22.2)与汽轮机四个主汽阀相连接,另外还有两根母管分别引入凝汽器的两侧,与这两根旁路母管连接的还有通向除氧器的供汽、通向蒸汽转换系统的加热蒸汽、通向汽水分离再热器的新蒸汽管线和通向凝汽器的14条蒸汽旁路排放管线。
主管道材质为。
1.WB36CN1钢的性能分析1.1.WB36CN1钢是德国瓦卢瑞克·曼内斯曼企业标准号,在DIN标准中称之为15NiCuMoNb5,WB36 CN1钢在空淬热处理后为贝氏体-铁素体组织,属于铜-镍-钼低合金钢,该钢加入了Cu用以提高回火的强度,但是铜元素具有赤热脆性,因此加入了比Cu多50%的Ni,不但消除了赤热脆性,还进一步提高了强度,尤其是加入少量的钼后,这种效果更好。
1.2.WB36CN1钢的焊接性主要体现在两方面:裂纹敏性和焊接热影响区的力学性能。
在过去40年中,WB36CN1钢在精炼等方面进展显著,使得其焊接性得到较大改善,尤其是焊接热影响区冷裂纹敏感性大大降低,粗晶区韧性大幅度提高,高效率、大线能量焊接工艺得以应用。
其化学成分如下:化学成分表2.焊接工艺评定焊接工艺评定是为验证焊接工艺参数的正确性进行的试验过程,是指导焊接作业指导书编制的支撑性文件。
在WB36CN1钢管焊接之前,我项目部进行了WB36CN1的焊接工艺评定工作。
评定时采用的焊接工艺方案内容如下(WB36CN1,φ406.4×22.2mm):2.1.坡口型式:V型,对口间隙:2~4mm2.2.预热温度/方式:100~200℃,电阻加热,持续控温;2.3.保护气体:氩气,纯度≥99.99%,流量:8~12L/min;2.4.层间温度:100~300℃,脱氢处理:300~350℃,保温2h;2.5.热处理工艺:580~620℃,保温时间:2h,焊后升降温度:,280℃/h;2.6.热处理采用电阻加热法,热电偶测温,电脑温控仪控制,自动记录温度曲线。
SA-335 P92钢大口径厚壁集箱管道的焊接工艺
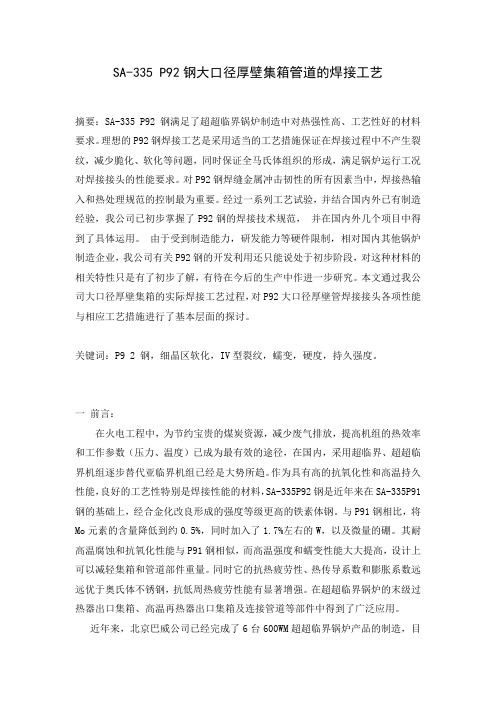
SA-335 P92钢大口径厚壁集箱管道的焊接工艺摘要:SA-335 P92钢满足了超超临界锅炉制造中对热强性高、工艺性好的材料要求。
理想的P92钢焊接工艺是采用适当的工艺措施保证在焊接过程中不产生裂纹,减少脆化、软化等问题,同时保证全马氏体组织的形成,满足锅炉运行工况对焊接接头的性能要求。
对P92钢焊缝金属冲击韧性的所有因素当中,焊接热输入和热处理规范的控制最为重要。
经过一系列工艺试验,并结合国内外已有制造经验,我公司已初步掌握了P92钢的焊接技术规范,并在国内外几个项目中得到了具体运用。
由于受到制造能力,研发能力等硬件限制,相对国内其他锅炉制造企业,我公司有关P92钢的开发利用还只能说处于初步阶段,对这种材料的相关特性只是有了初步了解,有待在今后的生产中作进一步研究。
本文通过我公司大口径厚壁集箱的实际焊接工艺过程,对P92大口径厚壁管焊接接头各项性能与相应工艺措施进行了基本层面的探讨。
关键词:P9 2 钢,细晶区软化,IV型裂纹,蠕变,硬度,持久强度。
一前言:在火电工程中,为节约宝贵的煤炭资源,减少废气排放,提高机组的热效率和工作参数(压力、温度)已成为最有效的途径,在国内,采用超临界、超超临界机组逐步替代亚临界机组已经是大势所趋。
作为具有高的抗氧化性和高温持久性能,良好的工艺性特别是焊接性能的材料,SA-335P92钢是近年来在SA-335P91钢的基础上,经合金化改良形成的强度等级更高的铁素体钢。
与P91钢相比,将Mo元素的含量降低到约0.5%,同时加入了1.7%左右的W,以及微量的硼。
其耐高温腐蚀和抗氧化性能与P91钢相似,而高温强度和蠕变性能大大提高,设计上可以减轻集箱和管道部件重量。
同时它的抗热疲劳性、热传导系数和膨胀系数远远优于奥氏体不锈钢,抗低周热疲劳性能有显著增强。
在超超临界锅炉的末级过热器出口集箱、高温再热器出口集箱及连接管道等部件中得到了广泛应用。
近年来,北京巴威公司已经完成了6台600WM超超临界锅炉产品的制造,目前在制的1000MW超超临界锅炉,大量采用P92 材料,这些锅炉部件主要包括:见附表1随着 P92 钢焊接工作的增多,对于其焊接性能的认识也在不断加深,以下将重点描述围绕焊接和热处理工艺规范和控制细节对P92钢焊接接头综合性能的影响。
合金钢12Cr1MoV厚壁管道焊缝裂纹的防止
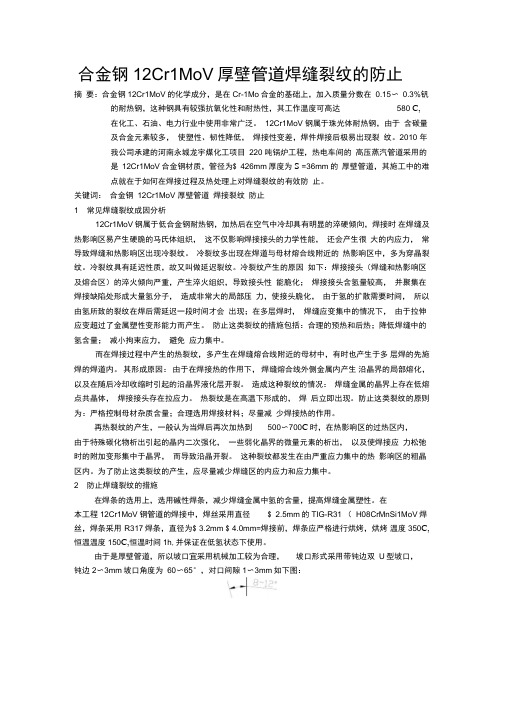
合金钢12Cr1MoV厚壁管道焊缝裂纹的防止摘要:合金钢12Cr1MoV的化学成分,是在Cr-1Mo合金的基础上,加入质量分数在0.15〜0.3%钒的耐热钢,这种钢具有较强抗氧化性和耐热性,其工作温度可高达580 C,在化工、石油、电力行业中使用非常广泛。
12Cr1MoV 钢属于珠光体耐热钢,由于含碳量及合金元素较多,使塑性、韧性降低,焊接性变差,焊件焊接后极易出现裂纹。
2010 年我公司承建的河南永城龙宇煤化工项目220 吨锅炉工程,热电车间的高压蒸汽管道采用的是12Cr1MoV合金钢材质,管径为$ 426mm厚度为S =36mm的厚壁管道,其施工中的难点就在于如何在焊接过程及热处理上对焊缝裂纹的有效防止。
关键词:合金钢12Cr1MoV 厚壁管道焊接裂纹防止1 常见焊缝裂纹成因分析12Cr1MoV钢属于低合金钢耐热钢,加热后在空气中冷却具有明显的淬硬倾向,焊接时在焊缝及热影响区易产生硬脆的马氏体组织,这不仅影响焊接接头的力学性能,还会产生很大的内应力,常导致焊缝和热影响区出现冷裂纹。
冷裂纹多出现在焊道与母材熔合线附近的热影响区中,多为穿晶裂纹。
冷裂纹具有延迟性质,故又叫做延迟裂纹。
冷裂纹产生的原因如下:焊接接头(焊缝和热影响区及熔合区)的淬火倾向严重,产生淬火组织,导致接头性能脆化;焊接接头含氢量较高,并聚集在焊接缺陷处形成大量氢分子,造成非常大的局部压力,使接头脆化,由于氢的扩散需要时间,所以由氢所致的裂纹在焊后需延迟一段时间才会出现;在多层焊时,焊缝应变集中的情况下,由于拉伸应变超过了金属塑性变形能力而产生。
防止这类裂纹的措施包括:合理的预热和后热;降低焊缝中的氢含量;减小拘束应力,避免应力集中。
而在焊接过程中产生的热裂纹,多产生在焊缝熔合线附近的母材中,有时也产生于多层焊的先施焊的焊道内。
其形成原因:由于在焊接热的作用下,焊缝熔合线外侧金属内产生沿晶界的局部熔化,以及在随后冷却收缩时引起的沿晶界液化层开裂。
低合金钢大直径厚壁管焊接裂纹产生机理及防止
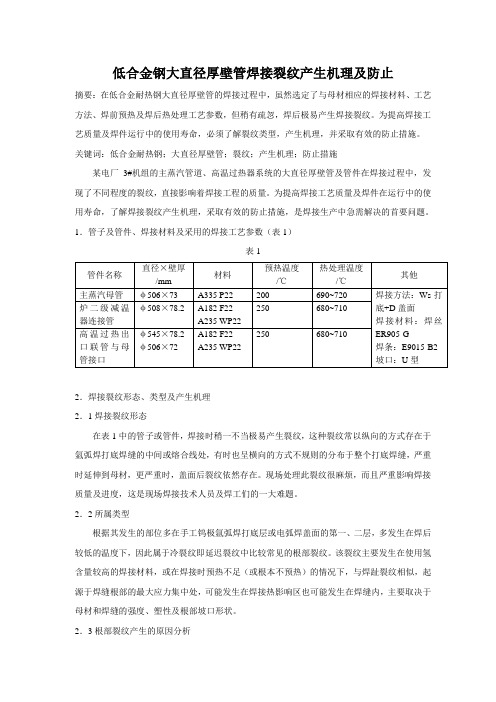
低合金钢大直径厚壁管焊接裂纹产生机理及防止摘要:在低合金耐热钢大直径厚壁管的焊接过程中,虽然选定了与母材相应的焊接材料、工艺方法、焊前预热及焊后热处理工艺参数,但稍有疏忽,焊后极易产生焊接裂纹。
为提高焊接工艺质量及焊件运行中的使用寿命,必须了解裂纹类型,产生机理,并采取有效的防止措施。
关键词:低合金耐热钢;大直径厚壁管;裂纹;产生机理;防止措施某电厂3#机组的主蒸汽管道、高温过热器系统的大直径厚壁管及管件在焊接过程中,发现了不同程度的裂纹,直接影响着焊接工程的质量。
为提高焊接工艺质量及焊件在运行中的使用寿命,了解焊接裂纹产生机理,采取有效的防止措施,是焊接生产中急需解决的首要问题。
1.管子及管件、焊接材料及采用的焊接工艺参数(表1)表12.焊接裂纹形态、类型及产生机理2.1焊接裂纹形态在表1中的管子或管件,焊接时稍一不当极易产生裂纹,这种裂纹常以纵向的方式存在于氩弧焊打底焊缝的中间或熔合线处,有时也呈横向的方式不规则的分布于整个打底焊缝,严重时延伸到母材,更严重时,盖面后裂纹依然存在。
现场处理此裂纹很麻烦,而且严重影响焊接质量及进度,这是现场焊接技术人员及焊工们的一大难题。
2.2所属类型根据其发生的部位多在手工钨极氩弧焊打底层或电弧焊盖面的第一、二层,多发生在焊后较低的温度下,因此属于冷裂纹即延迟裂纹中比较常见的根部裂纹。
该裂纹主要发生在使用氢含量较高的焊接材料,或在焊接时预热不足(或根本不预热)的情况下,与焊趾裂纹相似,起源于焊缝根部的最大应力集中处,可能发生在焊接热影响区也可能发生在焊缝内,主要取决于母材和焊缝的强度、塑性及根部坡口形状。
2.3根部裂纹产生的原因分析⑴钢材及焊接材料化学成分的影响钢中碳和合金元素的共同作用,使钢的奥氏体稳定性增加,不易发生分解,而在冷到较低温度时才发生马氏体转变,因此,在该类钢焊接时,如果冷却速度较大则易形成淬硬组织,使焊接接头的脆性增大,在有较大的约束力时,常导致裂纹。
TP321厚壁管道焊接过程中的常见问题及应对措施

TP321厚壁管道焊接过程中的常见问题及应对措施摘要:TP321广泛应用于石化行业渣油加氢、连续重整、加氢裂化等装置的高压管道。
近年来,出现了TP321厚壁管道的焊后热处理后发生再热裂纹现象。
因此,本文结合中科炼化一体化项目440万吨/年渣油加氢脱硫装置,现场TP321管材焊缝稳定化热处理后部分焊缝表面出现裂纹,对焊缝裂纹原因进行了分析,制定的处理方案进行论述。
关键词:TP321管道;稳定化;热处理;应对措施TP321奥氏体不锈钢管,在制造时加入了Ti,碳含量很低,可以防止晶间腐蚀,利用形变强化提高强度,采用固溶热处理将钢加热至1050℃~1150℃,使碳化物充分溶解,然后进行水冷却,获得单项奥氏体组织,提高耐蚀性。
渣油加氢脱硫装置突出的特点是高温、高压,介质有氢气、硫化氢、环烷酸等临氢工况,所采用的TP321多为厚壁管道,为了防止在450℃~850℃的敏化温度范围内,碳从奥氏体中以碳化铬(Cr23C6)形式延晶界析出,使晶界附近的合金元素含铬量降低到耐腐蚀所需的最低含量(12%)以下,产生厚度数十纳米的贫铬区,尤其以650℃最危险。
近年来,随着设备的尺寸,TP321厚壁管道越来越多,最大厚度达88mm。
在多个炼化项目中对厚壁TP321管道的进行稳定化热处理后,热影响区、母材或焊缝出现再热裂纹,为解决这一问题,确保装置长期安全运行,为厚壁稳定性奥氏体不锈钢未来现场施工提供技术依据,研究了TP321奥氏体不锈钢管道稳定化热处理的可行性。
1 TP321焊接性分析A312 TP321属于18-8型铬镍奥氏体不锈钢,相当于我国的0Cr18Ni10Ti。
含18%的铬和10%的钛。
TP321具有优良的可焊性,与其他奥氏体不锈钢一样在焊接时容易发生晶间腐蚀、应力腐蚀开裂和焊接热裂纹,并且比其他奥氏体不锈钢更容易出现焊接热裂纹和再热裂纹。
如图1所示。
图1 可能出现晶间腐蚀的位置图2 晶间腐蚀1.1热裂纹产生原因及预防措施由于TP321奥氏体不锈钢焊缝中枝晶方向性很强,枝晶间低熔点杂质的偏析,加之TP321导热系数仅为低碳钢的1/2,而膨胀系数比低碳钢大50%左右,使焊缝区产生较大的温差和收缩内应力,所以焊缝中容易产生热裂纹。
A335—P22厚壁管道焊接及热处理工艺

A335—P22厚壁管道焊接及热处理工艺作者:高宝宝来源:《中国新技术新产品》2014年第18期摘要:A335-P22厚壁管道的焊接要想满足多种复杂工程要求,需要制定多种焊接方法组合的焊接工艺。
在探究和分析了A355-P22厚壁管材焊接特性后,想出了一套适合A335-P22厚壁管的焊接工艺。
该工艺同时采用了多种焊接方法。
关键词:A335-P22;厚壁管道;焊接;热处理中图分类号:TG44 文献标识码:A1 材质介绍厚壁管道材质:A335-P22管材合金成分高,属于低合金珠光体耐热钢,可焊性差,并且由于管壁厚、管径大,拘束度大,易淬硬产生裂纹,固焊接工艺要求高。
特点是工艺性能良好,对热处理的加热温度不太敏感,焊接性能也较好,基友良好的塑性,具有良好的塑性,难腐蚀。
最大的特点在焊接工艺中具有淬硬性和再热裂纹倾向。
2 焊接工艺2.1 钢材的常温化学成分性能和力学性能按照化学成分进行研究,钢材中的含碳量较小,但是Cr、Mo等一些合金元素较多,所以在进行焊接时候,如果能量多大,在热源影响处的晶粒外体将明显变粗,这将大大降低焊接之处的塑韧性,尤其是热影响区的。
在焊接过程中,对于焊接之地的热影响区倾向于淬硬或者冷裂倾向,钢材中的化学成分起着较为重要的作用,甚至可能导致焊接点性能过差。
但是如果在焊接过程中,所焊接之缝隙的氢含量扩散之值过高的话,一般直接影响着焊接质量,如接头之处经常会有冷纹之现象,这种焊接冷纹对于整个钢材焊接过程有着及其重要的父母影响,所以为了避免此类问题的出现,可在实际的焊接过程中,运用低氢型焊条,再结合焊接线本身的能量,经过预热、后热等,进而避免上述情况的出现,即:淬硬、焊接冷纹。
据上所述分析,根据焊接材料选用原则,电焊盖面前预热适当温度及焊后升温一定温度进行恒温适当时间消氢处理焊接采用氩弧焊打底、电焊盖面,打底前预热一定温度,恒温适当时的工艺过程。
2.2 焊接设备和焊接材料的选用选用林肯逆变式的焊机,此种焊机的优势较为突出,首先其运作性能较为流利,在电流调节方面也为灵活。
SA335-P92大径厚壁管的焊接和热处理工艺

SA335-P92大径厚壁管的焊接和热处理工艺前言:随着大型火力发电机组参数向超超临界方向发现,适应高参数条件设备运行的新型低碳马氏体耐热钢SA335-P92因具有良好的高温强度、抗蠕变性能、抗高温腐蚀和抗高温氧化等性能,广泛应用于我国660~1000MW机组主蒸汽及再热蒸汽管道中。
1、SA335-P92的特性及焊接性SA335-P92是在SA335-P91的基础上通过添加1.5%~2.0%的W元素,降低Mo元素含量,采用V、Nb元素微合金化并控制N和B元素含量开发来的,极大地增加了固溶强化效果。
由于W和其他合金元素Cr、Mo、V、Nb和N等元素的添加,SA335-P92的焊接性也要差于SA335-P91。
表1. SA335-P92钢的化学成分 w%表2. SA335-P92钢的力学性能2、SA335-P92的焊接工艺1)焊材的选择SA335-P92大径厚壁管的焊接方法采用氩弧焊打底,焊条电弧焊填充盖面。
氩弧焊打底厚度应超过3mm,需要进行两层氩弧焊打底焊接,每次的厚度不超过2.4mm。
焊条电弧焊进行填充和盖面时,选用的焊条直径不大于3.2mm。
焊材选用德国奥钢联伯乐(原德国蒂森)MTS616-ER90S-G,直径为Φ2.4的焊丝和MTS616-E9015-G,直径为Φ2.5和Φ3.2的焊条,SA335-P92不采用Φ4.0的焊条。
2)焊接参数的选择见表表3. SA335-P92焊接工艺参数焊接工艺参数上表的焊接工艺参数选择的母材规格为Φ448×75,SA335-P92焊接时选择多层多道焊接,焊接电流不宜过大,焊接速度不宜过快。
SA335-P92对焊接的热输入的控制要求比较高,焊接热输入过大容易导致焊接接口的冲击韧性降低,所以必须采用小的焊接线能量。
SA335-P92在焊接时采用小直径焊条,较小的焊接电流,较快的焊接速度和较低的层间温度。
焊接过程的控制3、SA335-P92的焊接过程控制1)焊前准备焊接之前需搭设防护棚,并配备必要的照明设施。
焊接预热、后热、保温最佳解决方案
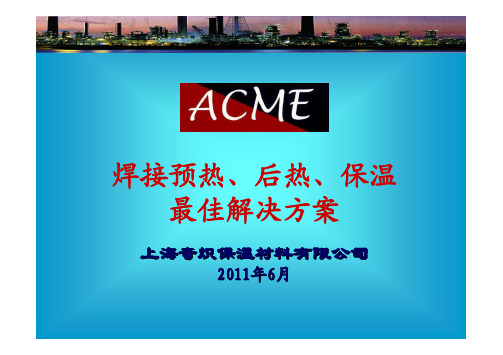
上海奇炽保温材料有限公司上海奇炽保温材料有限公司 2011 2011年 年66月 焊接预热、后热、保温最佳解决方案目 录一、背景介绍二、现状描述三、解决方案四、方案实施五、效果检测六、实际应用七、效果评估八、后热保温九、三维柔性组合焊接 工装系统十、客户群体一、背景介绍在焊接碳素钢、结构钢的工艺中,温度对焊接质量有着重大的 影响。
目前市面上的的高强结构钢基本上是低碳低合金钢或低碳低 合金调质钢。
特别是焊接强度级别≥390MPa的材料,要获得焊缝组 织优良的强韧性,防止冷裂纹,需要焊前预热,焊后低温后热处理 或消氢处理。
通常,焊接预热、消氢工艺是采用火焰或履带式电热器加热, 火焰加热完全靠人工掌握,加热温度极不均匀;履带式电热器与工 件的间隙不一致,导致加热不均匀;电源(220V)接头容易损坏, 有触电的危险;加热器本身生热,温度很高,容易烫伤操作工人;加热温度需要人工看护才能控制,容易过烧,导致产品报废或质量 不稳定,且加热时间长,能耗很高。
大型号焊炬火焰加热:采用气体燃烧的火焰进行加热,温度通过传导深入工件 内部,工件表面温度较高、内部温度较低,操作完全靠人工掌握,加 热温度极不均匀;二、现状描述电热器加热:采用电热丝的电阻发热,温度通过传导深入工件内部,工 件表面温度较高、内部温度较低,加热温度不均匀;虽然可以自动温控,但 是热电偶不能和电热板接触,否则会导致温度读书极大的偏差,因此加热过 程需要人工检测控制。
例如:某结构件钢管与接头的焊接预热、消氢新工艺是采用履带式电热 器加热,加热器与工件的间隙不一致,导致加热不均匀。
间隙不一致,导 致温度不均匀 工人装卸时容 易被烫伤三、解决方案应用感应加热工艺。
感应加热是利用电磁感应原理在被加热物体(工件)内部产生电流 (涡流),而使物体(工件)发热的方法。
感应加热的特点加热均匀 由于感应加热是钢材受到磁感应产生涡流而自身发热,所以加热温度很均 匀,这一特性对焊接的预热及后热消氢非常有利;生产率高 感应加热是钢材受到磁感应产生涡流而自身发热,不需热传导,设 备功率因素达到95%,加热时间短、生产效率高;控制精准 可根据各种温度曲线的需要进行编程,实现自动化精准控制;安全可靠 采用安全的航空接头,漏电保护装置,消除了安全隐患 ;设备为全空冷设计,降低了系统损耗,并彻底消除了设备来水冷却系统的故障;完善 的限制保护措施使得设备在各种工况下保持连续安全运行;使用期长 红外电热器由于是电热丝发热,所以电热丝很快会烧损;而感应线 圈本身不产生高温,不会被烧损,因此使用寿命很长。
TP304L大口径厚壁不锈钢管道焊接
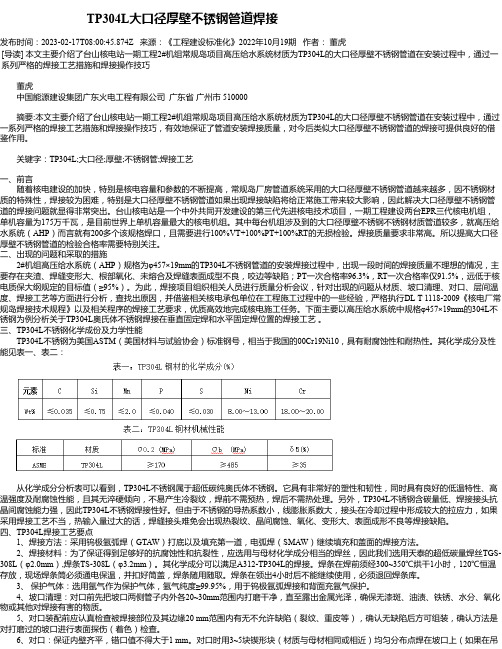
TP304L大口径厚壁不锈钢管道焊接发布时间:2023-02-17T08:00:45.874Z 来源:《工程建设标准化》2022年10月19期作者:董虎[导读] 本文主要介绍了台山核电站一期工程2#机组常规岛项目高压给水系统材质为TP304L的大口径厚壁不锈钢管道在安装过程中,通过一系列严格的焊接工艺措施和焊接操作技巧董虎中国能源建设集团广东火电工程有限公司广东省广州市 510000摘要:本文主要介绍了台山核电站一期工程2#机组常规岛项目高压给水系统材质为TP304L的大口径厚壁不锈钢管道在安装过程中,通过一系列严格的焊接工艺措施和焊接操作技巧,有效地保证了管道安装焊接质量,对今后类似大口径厚壁不锈钢管道的焊接可提供良好的借鉴作用。
关键字:TP304L;大口径;厚壁;不锈钢管;焊接工艺一、前言随着核电建设的加快,特别是核电容量和参数的不断提高,常规岛厂房管道系统采用的大口径厚壁不锈钢管道越来越多,因不锈钢材质的特殊性,焊接较为困难,特别是大口径厚壁不锈钢管道如果出现焊接缺陷将给正常施工带来较大影响,因此解决大口径厚壁不锈钢管道的焊接问题就显得非常突出。
台山核电站是一个中外共同开发建设的第三代先进核电技术项目,一期工程建设两台EPR三代核电机组,单机容量为175万千瓦,是目前世界上单机容量最大的核电机组。
其中每台机组涉及到的大口径厚壁不锈钢不锈钢材质管道较多,就高压给水系统(AHP)而言就有200多个该规格焊口,且需要进行100%VT+100%PT+100%RT的无损检验。
焊接质量要求非常高。
所以提高大口径厚壁不锈钢管道的检验合格率需要特别关注。
二、出现的问题和采取的措施2#机组高压给水系统(AHP)规格为φ457×19mm的TP304L不锈钢管道的安装焊接过程中,出现一段时间的焊接质量不理想的情况,主要存在夹渣、焊缝变形大、根部氧化、未熔合及焊缝表面成型不良,咬边等缺陷;PT一次合格率96.3%,RT一次合格率仅91.5%,远低于核电质保大纲规定的目标值(≥95%)。
P91厚壁管焊后硬度超标原因分析及处理

P91厚壁管焊后硬度超标原因分析及处理摘要:本文针对P91厚壁管焊后硬度超标的问题,对硬度超标的原因进行了分析,同时提出通过改进焊缝金属化学成分,改善热处理措施等方案降低P91厚壁管道焊后表面硬度,结果表面处理方案有效。
关键词: P91 焊后热处理硬度Abstract: Aiming at the problem of excessive hardness of P91thick-walled pipe after welding, the causes of excessive hardness were analyzed, and the surface hardness of P91 thick-walled pipe after welding was reduced by improving heat treatment measures, and an effective surface treatment scheme was obtained.Keywords: P91,Post-weld heat treatment ,Hardness,0引言9Cr-1Mo(SA335-P91/SA213-T91)钢是美国于七十年代末八十年代初开发的新型马氏体耐热钢,该钢种在热膨胀系数,弹性模量、蠕变性能以及抗氧化性等多方面有着优越的性能,同时还具有良好的冲击韧性和持久塑性,所以该钢种在电站主蒸汽管道中得以广泛的应用[1]。
某核电 P91 管道预制焊缝在进行硬度检测时,发现部分厚度较大的壁管焊缝硬度超出规程要求,按照DL/T438-2009《火力发电厂金属技术监督规程》要求执行标准为 NB/T25085-2018。
根据标准要求,硬度测量执行标准为符合 GB/T17394.1,其中 P91 管道热影响区硬度应达到175~270HBW,焊缝硬度应达到 185~270HBW。
目前共发现10道厚壁焊口焊缝硬度部分区域高于270HBW,占比大厚壁管数量的20%。
油路管件焊接
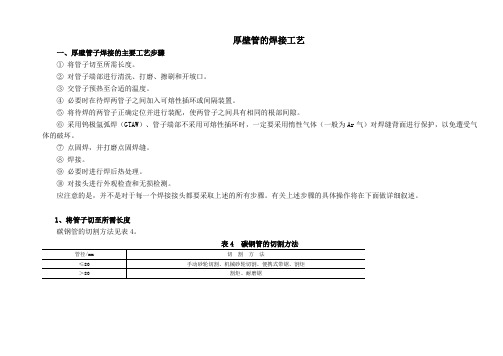
厚壁管的焊接工艺一、厚壁管子焊接的主要工艺步骤①将管子切至所需长度。
②对管子端部进行清洗、打磨、擦刷和开坡口。
③交管子预热至合适的温度。
④必要时在待焊两管子之间加入可熔性插环或间隔装置。
⑤将待焊的两管子正确定位并进行装配,使两管子之间具有相同的根部间隙。
⑥采用钨极氩弧焊(GTAW)、管子端部不采用可熔性插环时,一定要采用惰性气体(一般为Ar气)对焊缝背面进行保护,以免遭受气体的破坏。
⑦点固焊,并打磨点固焊缝。
⑧焊接。
⑨必要时进行焊后热处理。
⑩对接头进行外观检查和无损检测。
应注意的是,并不是对于每一个焊接接头都要采取上述的所有步骤。
有关上述步骤的具体操作将在下面做详细叙述。
1、将管子切至所需长度碳钢管的切割方法见表4。
表4 碳钢管的切割方法2、对管子端部进行清洗、打磨、擦刷和开坡口在根部焊道上进行打磨可以去除熔渣,减少根部焊道的余高,并在根部焊道上留有一个凹槽,以确保热焊道成形美观、无空洞存在。
根部焊道的打磨决定着是否能够获得熔透焊道。
用钢丝刷擦刷其他焊道可以起到去除残余焊渣的作用。
焊接直径50mm的管子一般不需要开坡口,只需采用砂轮或钢丝刷将管子端部加工平整并进行清理。
焊接直径大于50mm的管子则要求对其端部进行清洗、打磨、擦刷和开坡口。
3、交管子预热至合适的温度焊前管子的预热可以采用氧-乙炔焊炬加热、电阻加热和电感应加热等方法,其中电阻加热和电感应加热的温度比采用焊炬加热更容易进行控制。
对管子进行预热,其作用是确保焊接时的热量输入焊缝,而不是排放到周围金属中,以免造成焊接缺陷。
预热时,将焊接区和周围金属加热到40~150℃,可以很好地防止焊接热量排放到周围金属。
由于预热可以减少焊缝与周围金属的温度差,因此焊缝金属的热应力也相应降低,减小了焊接裂纹和变形倾向。
此外,预热还有助于排除气体,尤其是焊缝中溢出的氢气。
在焊接工艺规程中,根据采用的焊接方法、焊条以及管子材质等,对所需要的预热温度都有规定。
焊后稳定热化处理的A312TP321厚壁不锈钢管道焊接工法

焊后稳定热化处理的A312TP321厚壁不锈钢管道焊接工法1 前言在中国石油四川石化1000万吨/年炼油与80万吨/年乙烯炼化一体化工程270万吨/年腊油加氢裂化装置中,规格有DN450x40mm、DN500x50mm、DN550x54mm、DN600x60mm、DN620x62mm、DN700x66mm的A312TP321不锈钢管道,管道设计压力为14.3-16.05Mpa,设计温度为405℃~454℃,主要介质为高温油气、氢气等,焊后进行稳定化热处理。
我公司采用了总包方提供的厚度为50mm的管道进行了焊接工艺评定工作,但试件经900℃稳定化处理后,弯曲试验及晶间腐蚀试验均有未合格现象。
对于这个问题,中国石油四川石化公司召集一些国内专家咨询,总包方委托哈尔滨焊接研究所针对此问题进行过一系列的试验,但均未果。
为此,我公司组织相关专家进行了研讨,经过多次A312TP321焊评试验,最终取得了“焊后稳定热化处理的A312TP321厚壁不锈钢管道焊接工法”这一国内领先的技术成果。
此技术成果已在2012年按NB/T47014《承压设备焊接工艺评定》的评定程序评定合格,并在中国石油四川石化1000万吨/年炼油与80万吨/年乙烯炼化一体化工程270万吨/年腊油加氢裂化装置上进行应用,取得了良好的社会效益和经济效益。
2 工法特点2.1突破了国内相同材料的焊接施工厚度,前所未有目前,国内同行业对此类材料所做焊评采用的母材厚度24mm,覆盖范围为5—48mm,实际焊接最大厚度40mm,而此工法采用焊评母材厚度50mm,覆盖范围为5-200mm。
随着我国经济的快速发展,装置的扩容,管线厚度会进一步加大,本工法具有更大规模的类似装置的应用前景。
2.2可操作性强,适用性广本工法,完全符合设计和施工规范要求,可以在施工现场就地实施, 主要是改变了焊条的酸碱性,由原来的酸性焊条改为碱性焊条,没有增加焊工的操作难度,可操作性强,易于推广。
- 1、下载文档前请自行甄别文档内容的完整性,平台不提供额外的编辑、内容补充、找答案等附加服务。
- 2、"仅部分预览"的文档,不可在线预览部分如存在完整性等问题,可反馈申请退款(可完整预览的文档不适用该条件!)。
- 3、如文档侵犯您的权益,请联系客服反馈,我们会尽快为您处理(人工客服工作时间:9:00-18:30)。
三预热模式在厚壁管焊接中的应用
摘要:在现场施工中,耐压厚壁管的焊接难度大,极易造成焊缝裂纹。
根据实际施工情况,提出了三预热模式在厚壁管焊接中的应用,很好的提高了厚壁管焊缝的质量。
关键词:焊接应力预热温度场
前言:在厚壁管的现场焊接施工中,因为施工环境恶劣,受限制因素较多,造成焊接施工难度很大。
焊缝的质量得不到有效的保证和提高,直接影响到整个系统的质量问题。
如济钢中厚板厂3#加热炉的汽化冷却系统中炉底横水梁的现场施工。
本工程采用20#、Ф159*25的厚壁管进行施工,管径小、管壁厚,在焊接作业中很容易造成焊缝缺陷,导致裂纹的产生。
从而影响到整个加热炉的运行。
本文对如何提高施工环境恶劣的情况下厚壁管焊缝的质量做出一些分析。
1问题分析
钢件在焊接过程的不均匀温度场以及由它引起的局部塑性变形是产生焊接应力和裂纹的根本原因。
当焊接引起的不均匀温度场尚未消失时,焊件中的这种应力和变形称为瞬态焊接应力;焊接温度场消失后的应力称为残余焊接应力。
在厚壁管焊接中由于管壁厚焊接量大,从而极易产生很强的焊接应力,造成裂纹的产生,影响焊缝的施工质量。
1.1横水梁采用的为Ф159*25的厚壁管,在焊接工艺上,采用V型坡口,单面焊双面成型(见图1)。
图1焊缝坡口形式
1.2由于焊接厚度大,采用多层模式的焊接方式(见图2)。
在多层焊接中焊接应力厚度上的分布是中心部位最高,逐渐向表面过渡到零。
图2多层焊分层结构
1.3在焊接过程中,焊接电流的选择直接影响到焊接质量和效率。
焊接电流越大,熔深越大,焊条熔化快,焊接效率也高,但是焊接电流太大时,飞溅和烟雾大,焊条尾部易发红,部分涂层要失效或崩落,而且容易产生咬边、焊瘤、烧穿等缺陷,还会使接头热影响区晶粒粗大,焊接接头的韧性降低;焊接电流太小,则引弧困难,焊条容易粘连在工件上,电弧不稳定,易产生未焊透、未熔合、气孔和夹渣等缺陷,且生产率低。
根据实际的施工情况和以往经验,焊条选用Ф3.2和Ф4的两种规格,确定了相应的工艺参数(见表1)。
由于是厚壁管,焊接量非常大,而且管径小,造成焊接应力很集中。
在焊接过程中当外界温度变化很快时,特别是冬季,不均匀温度急速的向同温度场过度,
容易造成裂纹的产生。
2实施方法
在现场施工中,因受施环境的限制,无法采用石灰保温等在生产厂房内的施工工艺。
如何在现场的条件下减小焊接应力对焊缝的影响,以提高焊缝的焊接质量。
三预热操作模式即:焊前预热、焊中加热、焊后低温热处理。
在焊接过程中,用火焰加热进行辅助,工具简单、操作简便,有利于在现场的施工。
2.1焊前预热
在管道组装完成焊接前,利用气割具对焊缝两边的母材200mm的局部区域进行均匀火焰加热(见图3),加热温度达到200℃。
这样,可以使焊接区域被焊工件之间的不均匀温度场的差值减小,降低了焊接应力,另一方面,降低了焊接应变速率,有利于避免产生焊接裂纹。
图3加热区域示意图
2.2焊中加热
在焊接过程中,焊接完成一遍后,再对焊缝及其两边母材200mm范围内采用火焰加热,使加热温度达到200℃。
以平衡因焊接加热造成的不均匀热场。
并有利于焊缝金属中扩散氢的逸出,避免产生氢致裂纹。
减小了因多层焊接导致的焊缝中间部分焊接应力集中的问题,提高了焊缝的整体质量。
2.3焊后低温热处理
在焊接完成后,再对焊缝及其两边母材200mm范围内采用火焰加热,使加热温度达到200℃,进行低温回火热处理。
一方面,使焊缝和母材的热力场达到大致的均衡,另一方面,有利于焊缝金属中扩散氢的逸出,避免产生氢致裂纹。
这样在保证了焊缝硬度情况下,焊接应力得到了很大的减小,韧性稍有提高,从而提高了焊缝的稳定性。
3实施效果
通过在济钢中厚板厂3#加热炉的施工,使冷却系统的焊缝打压取得了一次性合格。
降低了因多次打压造成的资源浪费,大大的提高的整体的施工效率。
4结语
此操作模式虽降低了单个焊缝的施工效率,但确保的焊缝的一次合格率,而对整个系统的施工效率得到了很大的提高。
同时,确保了整个系统的质量。
参考文献:
1.雷玉成陈希章朱强,《金属材料焊接工艺》,化学工业出版社,2007年8月
2.顾纪清阳代军,《管道焊接技术》,化学工业出版社,2005年8月
3.英若采《熔焊原理及金属材料焊接》,机械工业出版社,2000年10月。