发动机叶片的造型和数控加工
航空发动机精锻叶片数字化数控加工技术
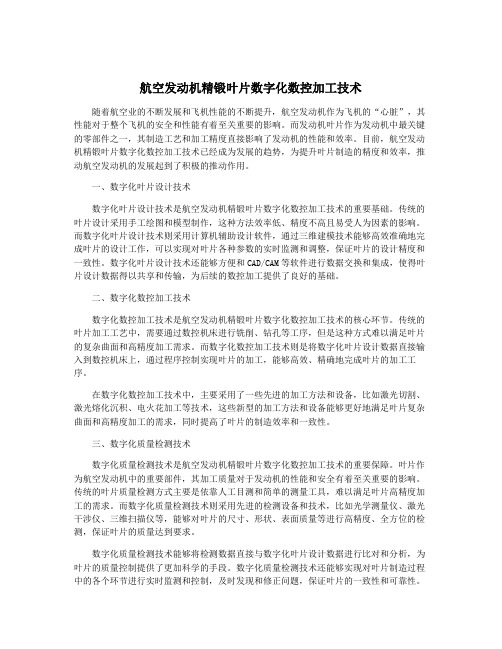
航空发动机精锻叶片数字化数控加工技术随着航空业的不断发展和飞机性能的不断提升,航空发动机作为飞机的“心脏”,其性能对于整个飞机的安全和性能有着至关重要的影响。
而发动机叶片作为发动机中最关键的零部件之一,其制造工艺和加工精度直接影响了发动机的性能和效率。
目前,航空发动机精锻叶片数字化数控加工技术已经成为发展的趋势,为提升叶片制造的精度和效率,推动航空发动机的发展起到了积极的推动作用。
一、数字化叶片设计技术数字化叶片设计技术是航空发动机精锻叶片数字化数控加工技术的重要基础。
传统的叶片设计采用手工绘图和模型制作,这种方法效率低、精度不高且易受人为因素的影响。
而数字化叶片设计技术则采用计算机辅助设计软件,通过三维建模技术能够高效准确地完成叶片的设计工作,可以实现对叶片各种参数的实时监测和调整,保证叶片的设计精度和一致性。
数字化叶片设计技术还能够方便和CAD/CAM等软件进行数据交换和集成,使得叶片设计数据得以共享和传输,为后续的数控加工提供了良好的基础。
二、数字化数控加工技术数字化数控加工技术是航空发动机精锻叶片数字化数控加工技术的核心环节。
传统的叶片加工工艺中,需要通过数控机床进行铣削、钻孔等工序,但是这种方式难以满足叶片的复杂曲面和高精度加工需求。
而数字化数控加工技术则是将数字化叶片设计数据直接输入到数控机床上,通过程序控制实现叶片的加工,能够高效、精确地完成叶片的加工工序。
在数字化数控加工技术中,主要采用了一些先进的加工方法和设备,比如激光切割、激光熔化沉积、电火花加工等技术,这些新型的加工方法和设备能够更好地满足叶片复杂曲面和高精度加工的需求,同时提高了叶片的制造效率和一致性。
三、数字化质量检测技术数字化质量检测技术是航空发动机精锻叶片数字化数控加工技术的重要保障。
叶片作为航空发动机中的重要部件,其加工质量对于发动机的性能和安全有着至关重要的影响。
传统的叶片质量检测方式主要是依靠人工目测和简单的测量工具,难以满足叶片高精度加工的需求。
叶片工艺流程
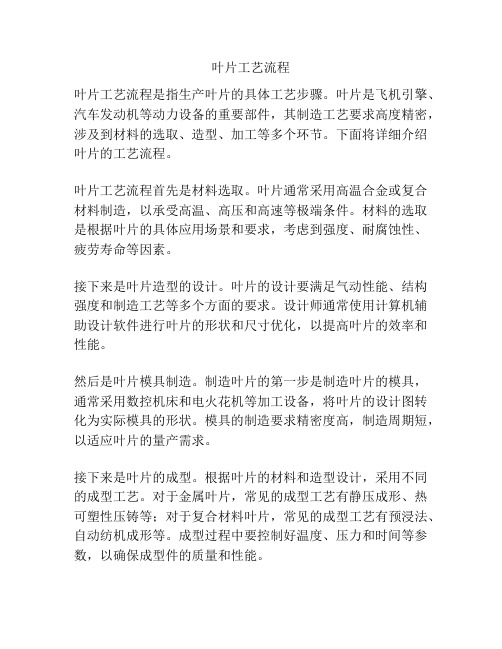
叶片工艺流程叶片工艺流程是指生产叶片的具体工艺步骤。
叶片是飞机引擎、汽车发动机等动力设备的重要部件,其制造工艺要求高度精密,涉及到材料的选取、造型、加工等多个环节。
下面将详细介绍叶片的工艺流程。
叶片工艺流程首先是材料选取。
叶片通常采用高温合金或复合材料制造,以承受高温、高压和高速等极端条件。
材料的选取是根据叶片的具体应用场景和要求,考虑到强度、耐腐蚀性、疲劳寿命等因素。
接下来是叶片造型的设计。
叶片的设计要满足气动性能、结构强度和制造工艺等多个方面的要求。
设计师通常使用计算机辅助设计软件进行叶片的形状和尺寸优化,以提高叶片的效率和性能。
然后是叶片模具制造。
制造叶片的第一步是制造叶片的模具,通常采用数控机床和电火花机等加工设备,将叶片的设计图转化为实际模具的形状。
模具的制造要求精密度高,制造周期短,以适应叶片的量产需求。
接下来是叶片的成型。
根据叶片的材料和造型设计,采用不同的成型工艺。
对于金属叶片,常见的成型工艺有静压成形、热可塑性压铸等;对于复合材料叶片,常见的成型工艺有预浸法、自动纺机成形等。
成型过程中要控制好温度、压力和时间等参数,以确保成型件的质量和性能。
然后是叶片的精密加工。
成型后的叶片需要进行精密加工,以达到设计要求。
精密加工通常包括机械加工和表面处理。
机械加工是通过车床、铣床、磨床等设备,对叶片进行修整、尺寸加工和孔加工等操作;表面处理是对叶片表面进行抛光、喷涂等处理,提高叶片的光洁度和耐腐蚀性。
最后是叶片的装配和测试。
经过精密加工后的叶片需要进行装配和测试。
装配过程中,将叶片安装到具体的设备上,如飞机引擎或汽车发动机。
测试过程中,对叶片进行静态和动态试验,以确保叶片的性能和可靠性。
综上所述,叶片工艺流程包括材料选取、造型设计、模具制造、成型、精密加工、装配和测试等多个环节。
不同的叶片类型和材料要求不同,工艺流程也有所差异。
但整体而言,叶片制造要求精密度高、工艺性能好,以提高叶片的效率和使用寿命。
航空发动机精锻叶片数字化数控加工技术
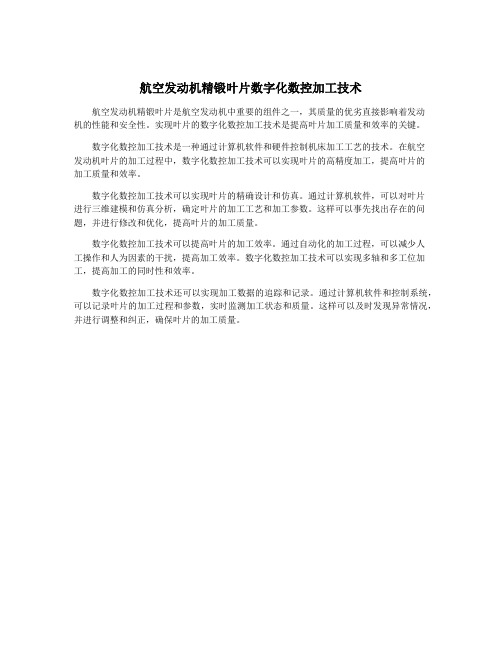
航空发动机精锻叶片数字化数控加工技术
航空发动机精锻叶片是航空发动机中重要的组件之一,其质量的优劣直接影响着发动
机的性能和安全性。
实现叶片的数字化数控加工技术是提高叶片加工质量和效率的关键。
数字化数控加工技术是一种通过计算机软件和硬件控制机床加工工艺的技术。
在航空
发动机叶片的加工过程中,数字化数控加工技术可以实现叶片的高精度加工,提高叶片的
加工质量和效率。
数字化数控加工技术可以实现叶片的精确设计和仿真。
通过计算机软件,可以对叶片
进行三维建模和仿真分析,确定叶片的加工工艺和加工参数。
这样可以事先找出存在的问题,并进行修改和优化,提高叶片的加工质量。
数字化数控加工技术可以提高叶片的加工效率。
通过自动化的加工过程,可以减少人
工操作和人为因素的干扰,提高加工效率。
数字化数控加工技术可以实现多轴和多工位加工,提高加工的同时性和效率。
数字化数控加工技术还可以实现加工数据的追踪和记录。
通过计算机软件和控制系统,可以记录叶片的加工过程和参数,实时监测加工状态和质量。
这样可以及时发现异常情况,并进行调整和纠正,确保叶片的加工质量。
航空发动机精锻叶片数字化数控加工技术
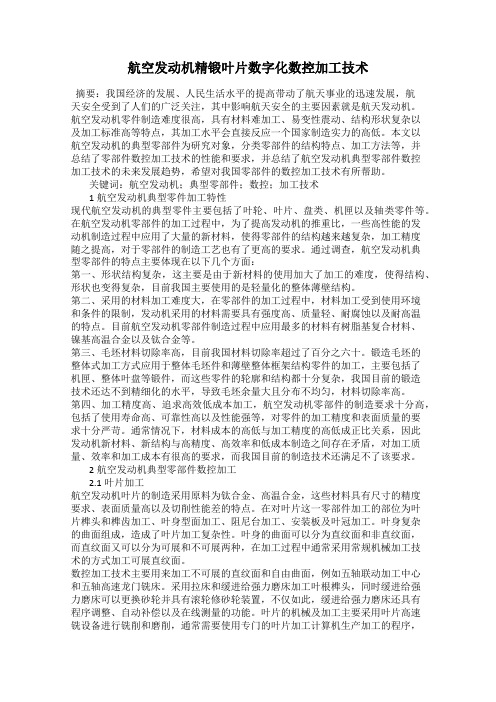
航空发动机精锻叶片数字化数控加工技术摘要:我国经济的发展、人民生活水平的提高带动了航天事业的迅速发展,航天安全受到了人们的广泛关注,其中影响航天安全的主要因素就是航天发动机。
航空发动机零件制造难度很高,具有材料难加工、易变性震动、结构形状复杂以及加工标准高等特点,其加工水平会直接反应一个国家制造实力的高低。
本文以航空发动机的典型零部件为研究对象,分类零部件的结构特点、加工方法等,并总结了零部件数控加工技术的性能和要求,并总结了航空发动机典型零部件数控加工技术的未来发展趋势,希望对我国零部件的数控加工技术有所帮助。
关键词:航空发动机;典型零部件;数控;加工技术1航空发动机典型零件加工特性现代航空发动机的典型零件主要包括了叶轮、叶片、盘类、机匣以及轴类零件等。
在航空发动机零部件的加工过程中,为了提高发动机的推重比,一些高性能的发动机制造过程中应用了大量的新材料,使得零部件的结构越来越复杂,加工精度随之提高,对于零部件的制造工艺也有了更高的要求。
通过调查,航空发动机典型零部件的特点主要体现在以下几个方面:第一、形状结构复杂,这主要是由于新材料的使用加大了加工的难度,使得结构、形状也变得复杂,目前我国主要使用的是轻量化的整体薄壁结构。
第二、采用的材料加工难度大,在零部件的加工过程中,材料加工受到使用环境和条件的限制,发动机采用的材料需要具有强度高、质量轻、耐腐蚀以及耐高温的特点。
目前航空发动机零部件制造过程中应用最多的材料有树脂基复合材料、镍基高温合金以及钛合金等。
第三、毛坯材料切除率高,目前我国材料切除率超过了百分之六十。
锻造毛坯的整体式加工方式应用于整体毛坯件和薄壁整体框架结构零件的加工,主要包括了机匣、整体叶盘等锻件,而这些零件的轮廓和结构都十分复杂,我国目前的锻造技术还达不到精细化的水平,导致毛坯余量大且分布不均匀,材料切除率高。
第四、加工精度高、追求高效低成本加工,航空发动机零部件的制造要求十分高,包括了使用寿命高、可靠性高以及性能强等,对零件的加工精度和表面质量的要求十分严苛。
飞机发动机的叶片制作流程

飞机发动机的叶片制作流程以飞机发动机的叶片制作流程为题,本文将详细介绍飞机发动机叶片的制作过程。
飞机发动机叶片是发动机的核心部件之一,负责将燃烧室内的高温高压气体转化为动能,推动飞机前进。
叶片的制作过程需要经过多个环节,包括材料选择、设计、加工和装配等步骤。
飞机发动机叶片的制作需要选用高温合金材料。
由于叶片在工作过程中需要承受高温高压气体的冲击,因此材料的耐高温性能是关键。
常用的材料包括镍基合金、钛基合金和陶瓷基复合材料等。
这些材料具有优异的耐高温性能和机械性能,能够在极端工作环境下保持稳定。
飞机发动机叶片的设计是关键步骤。
设计师需要根据发动机的工作原理和性能要求,确定叶片的几何形状和参数。
叶片的几何形状包括叶片的长度、宽度、弯曲角度、扭转角度等。
这些参数的选择将直接影响叶片的气动性能和机械性能。
设计师可以借助计算机辅助设计软件进行叶片的三维建模和仿真分析,以确保叶片设计的合理性和可行性。
接下来是叶片的加工过程。
叶片的加工通常采用数控机床进行精密加工。
首先,将选定的高温合金材料切割成相应的形状和尺寸。
然后,利用数控机床进行切削、铣削、钻孔等加工工艺,将材料加工成最终的叶片形状。
在加工过程中,需要保证叶片的精度和表面质量,以确保叶片的气动性能和机械性能。
最后是叶片的装配过程。
叶片的装配是将叶片与发动机的其他部件进行连接和固定。
通常采用铆接、焊接或螺栓连接等方式进行叶片的装配。
在装配过程中,需要保证叶片的位置和角度的精确度,以确保叶片在工作过程中能够正常运转。
总结起来,飞机发动机叶片的制作流程包括材料选择、设计、加工和装配等步骤。
叶片的制作需要选用高温合金材料,经过设计师的设计和计算机辅助设计,利用数控机床进行精密加工,最后与其他部件进行装配。
这一系列的步骤保证了叶片的质量和性能,确保了发动机的正常运转。
飞机发动机叶片的制作是一项复杂而关键的工艺,对于飞机的安全性和性能有着重要的影响。
航空发动机叶片的生产制造技术

航空发动机叶片的生产制造技术航空发动机叶片是航空发动机的重要组成部分,它在整个发动机运行过程中承受着极高的温度、压力和振动等力载荷。
因此,航空发动机叶片的生产制造技术对航空发动机的性能、可靠性和寿命都有着重要影响。
在这篇文章中,我们将详细介绍航空发动机叶片的生产制造技术。
1.材料选择与预处理在进行叶片制造之前,需要对材料进行预处理,以去除杂质、提高材料的均匀性和晶粒细化。
预处理方法包括热处理、化学处理和表面处理等。
2.叶片造型与设计叶片的造型与设计是叶片制造的关键环节。
叶片的形状、结构和轮毂之间的连接方式直接影响着叶片的性能和寿命。
通常情况下,叶片的内部结构是由空腔、腔板和护腔等组成的。
这些结构可以提高叶片的强度和刚度,在高速旋转过程中减小振动和压力损失。
叶片的形状通常采用空气动力学原理和结构力学原理进行设计,以提高发动机的效率和推力。
同时,还需要考虑到叶片的制造可行性和工艺性,确保叶片可以顺利制造出来。
3.叶片制造工艺铸造是叶片制造的主要工艺,通常采用真空熔模铸造或单晶铸造等方法。
真空熔模铸造是指将预熔的合金材料注入到陶瓷模具中,然后进行冷却凝固,最后得到具有复杂形状和精密尺寸的叶片。
单晶铸造则是通过在模具中形成单一晶体结构,去除晶界和晶粒边界,提高叶片的高温性能和抗腐蚀性能。
锻造是叶片制造的另一种常见工艺,通过对金属材料进行加热和塑性变形,使其达到所需的形状和尺寸。
复合材料制造是使用纤维增强树脂基体材料制造叶片的工艺。
这种工艺具有良好的抗腐蚀性和高温性能,适用于制造大型和复杂形状的叶片。
机加工是对叶片进行最后加工和整形的工艺。
这包括数控机床加工、电火花加工、冲压和磨削等方法,以保证叶片的几何尺寸和表面质量。
热处理是对叶片进行热处理,以改善材料的组织结构和性能。
常见的热处理方法包括固溶处理、时效处理和表面处理等。
4.质量控制与检测质量控制主要通过严格的制造工艺和生产流程来实现,确保叶片的尺寸和形状的精确性。
发动机叶片加工工序
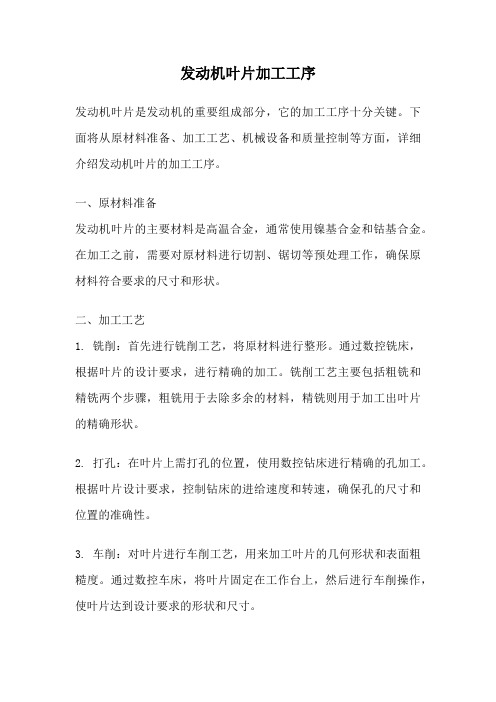
发动机叶片加工工序发动机叶片是发动机的重要组成部分,它的加工工序十分关键。
下面将从原材料准备、加工工艺、机械设备和质量控制等方面,详细介绍发动机叶片的加工工序。
一、原材料准备发动机叶片的主要材料是高温合金,通常使用镍基合金和钴基合金。
在加工之前,需要对原材料进行切割、锯切等预处理工作,确保原材料符合要求的尺寸和形状。
二、加工工艺1. 铣削:首先进行铣削工艺,将原材料进行整形。
通过数控铣床,根据叶片的设计要求,进行精确的加工。
铣削工艺主要包括粗铣和精铣两个步骤,粗铣用于去除多余的材料,精铣则用于加工出叶片的精确形状。
2. 打孔:在叶片上需打孔的位置,使用数控钻床进行精确的孔加工。
根据叶片设计要求,控制钻床的进给速度和转速,确保孔的尺寸和位置的准确性。
3. 车削:对叶片进行车削工艺,用来加工叶片的几何形状和表面粗糙度。
通过数控车床,将叶片固定在工作台上,然后进行车削操作,使叶片达到设计要求的形状和尺寸。
4. 磨削:在车削之后,对叶片进行磨削工艺,用来提高叶片的表面光洁度和精度。
通过磨床对叶片进行磨削,使其表面更加平整光滑,并且可以达到更高的尺寸精度。
三、机械设备发动机叶片的加工离不开各种机械设备的支持。
常用的机械设备包括数控铣床、数控钻床、数控车床、磨床等。
这些机械设备能够根据程序自动完成工件加工,提高生产效率和加工精度。
四、质量控制发动机叶片是发动机的核心部件之一,其加工质量直接影响到发动机的性能和可靠性。
因此,在加工过程中需要进行严格的质量控制。
常用的质量控制手段包括尺寸检测、外观检查和物理性能测试等。
通过这些手段,可以确保叶片的尺寸精度、外观质量和物理性能达到设计要求。
五、总结发动机叶片的加工工序是一个复杂而关键的过程。
通过对原材料的准备、加工工艺的选择、机械设备的使用和质量控制的实施,可以保证叶片的加工质量和性能要求。
发动机叶片的加工工序不仅需要高精度的机械设备的支持,还需要严格的质量控制和工艺操作的精细调控。
试论航空发动机叶片数控铣削方法

试论航空发动机叶片数控铣削方法摘要:由于航空发动机叶片空间自由曲面较为复杂,且其几何精度非常高,在加上航空发动机叶片的制作材料多食铝合金或钛合金,在切削方面存在很大苦难,此外,航空发动机叶片是薄壁零件,加工时零件容易产生变形。
这些因素就导致航空发动机叶片铣削难度较大。
本文从航空发动机叶片数控技术现状出发,对数控铣削方法进行浅显的探讨。
关键词:0.引言航空发动机是飞机的核心部分,是飞机的“心脏”,对飞机性能具有决定性作用。
而航空发动机叶片则是航空发动机的最重要部件之一[1]。
由于航空发动机叶片空间自由曲面较为复杂,且其几何精度非常高,在加上航空发动机叶片的制作材料多是铝合金或钛合金,在切削方面存在很大困难,此外,航空发动机叶片是薄壁零件,加工时零件容易产生变形。
这些因素就导致航空发动机叶片铣削难度较大。
1.航空发动机叶片加工制造现状自20世纪90年代以来,美国等发达国家在对航空发动机叶片进行制造时,采用了精密的数控加工技术。
通过精密的数控加工技术的应用,使航空发动机叶片余量不需要人工去除,而且所加工出来的叶片精度高,加工的周期大幅度缩短。
相对于传统的加工制造工艺来说,数控加工技术具有很大的先进性。
随着科学技术的进步,我国的航空发动机叶片精密数控加工工艺逐步发展,但与发达国家相比,我国航空发动机叶片切削效果和制造工艺还有较大差距。
就我国的航空发动机叶片数控加工工艺来说,虽然通过大量数控加工设备的引进,使我国的叶片加工取得了一定程度的发展,但是其发展程度相对有限,多数仍局限在叶片半精加工,叶片最终制造质量仍是依赖人工抛光工艺。
目前,我国航空发动机叶片加工来看,主要存在叶片加工变形、加工效率低下、加工精度不高、叶片表面质量较低等问题,这些问题严重制约了我国航空发动机叶片制造发展。
随着数控编程软件和空间自由曲面CAD/CAM集成中,刀具轨迹生成和干涉处理成为国内外研究的热点。
在生成刀具轨迹时,要解决刀具路径拓扑问题,从而控制叶片粗糙度;要解决走刀步距问题,从而减少叶片加工的误差产生;要解决切削行距,从而使叶片残留高度得到控制。
航空发动机精锻叶片数字化数控加工技术

航空发动机精锻叶片数字化数控加工技术随着航空产业的不断发展,航空发动机作为飞机的“心脏”,其性能和质量尤为重要。
精锻叶片作为发动机关键部件,其制造技术也备受关注。
近年来,随着数字化和数控技术的不断提升,航空发动机精锻叶片的数字化数控加工技术也得到了极大的发展和应用。
本文将从航空发动机精锻叶片的特点、数字化数控加工技术的发展趋势和应用前景等方面进行探讨。
一、航空发动机精锻叶片的特点航空发动机精锻叶片是航空发动机的关键部件之一,其工艺精度要求高,具有以下特点:1.高温高压环境下工作。
航空发动机工作环境极端恶劣,要求叶片能够在高温高压的环境下工作,因此叶片材料和制造工艺要求非常高。
2.精密几何形状。
叶片的气动性能对发动机效率和性能有着直接的影响,因此叶片的形状、尺寸和表面质量都需要具备非常高的精度和粗糙度。
3.复杂工艺要求。
叶片制造涉及到多道工序,包括锻造、热处理、机械加工、表面处理等,工序繁多、要求严格。
二、数字化数控加工技术的发展趋势随着数字化和数控技术的不断发展,数字化数控加工技术在航空发动机精锻叶片制造中得到了广泛的应用,并呈现出以下发展趋势:1.精密数控加工技术的提升。
随着数控技术的不断提升,包括五轴联动加工、高速切削、精密镜面加工等技术的应用,可以更好地满足叶片的精密加工需求。
2.数字化制造技术的发展。
数字化制造技术可以实现叶片的数字化建模、仿真分析和实时监控,可以更好地控制叶片的制造质量和提高生产效率。
3.智能制造技术的应用。
智能制造技术包括物联网、人工智能、大数据等技术的应用,可以实现叶片制造过程的自动化、智能化和信息化。
4.柔性制造技术的发展。
柔性制造技术可以应对叶片制造中的个性化和定制化需求,可以实现叶片的快速切换和灵活生产。
1.数控精密磨削加工。
叶片的表面质量要求非常高,需要采用数控精密磨削加工技术,以保证叶片的表面粗糙度和形状精度。
3.数控高速切削加工。
叶片的材料通常为高温合金材料,需要采用高速切削加工技术,以保证加工效率和工件表面质量。
航空发动机精锻叶片数字化数控加工技术
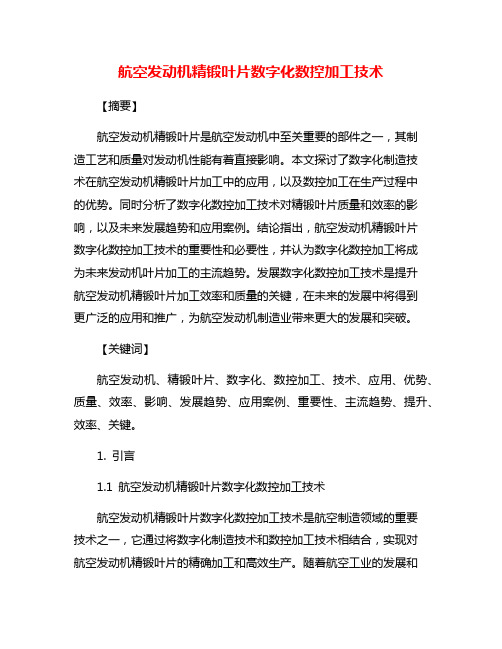
航空发动机精锻叶片数字化数控加工技术【摘要】航空发动机精锻叶片是航空发动机中至关重要的部件之一,其制造工艺和质量对发动机性能有着直接影响。
本文探讨了数字化制造技术在航空发动机精锻叶片加工中的应用,以及数控加工在生产过程中的优势。
同时分析了数字化数控加工技术对精锻叶片质量和效率的影响,以及未来发展趋势和应用案例。
结论指出,航空发动机精锻叶片数字化数控加工技术的重要性和必要性,并认为数字化数控加工将成为未来发动机叶片加工的主流趋势。
发展数字化数控加工技术是提升航空发动机精锻叶片加工效率和质量的关键,在未来的发展中将得到更广泛的应用和推广,为航空发动机制造业带来更大的发展和突破。
【关键词】航空发动机、精锻叶片、数字化、数控加工、技术、应用、优势、质量、效率、影响、发展趋势、应用案例、重要性、主流趋势、提升、效率、关键。
1. 引言1.1 航空发动机精锻叶片数字化数控加工技术航空发动机精锻叶片数字化数控加工技术是航空制造领域的重要技术之一,它通过将数字化制造技术和数控加工技术相结合,实现对航空发动机精锻叶片的精确加工和高效生产。
随着航空工业的发展和技术的进步,数字化数控加工技术在航空发动机领域中的应用越来越广泛。
航空发动机精锻叶片是航空发动机中的重要部件,其质量和精度直接影响飞机的性能和安全。
传统的加工方法往往存在加工精度低、效率低、成本高等问题。
而数字化数控加工技术通过精确的数控编程和全自动化加工过程,可以实现对叶片的精准加工,有效提高生产效率和降低成本。
2. 正文2.1 数字化制造技术在航空发动机精锻叶片加工中的应用数字化制造技术已经在航空发动机精锻叶片的加工中得到了广泛的应用。
通过数字化制造技术,可以实现对叶片材料、结构和形状的精确控制,从而提高叶片的加工精度和质量。
数字化制造技术包括CAD/CAM软件的应用、3D打印技术、虚拟仿真技术等。
CAD/CAM软件的应用可以实现对叶片设计和加工过程的数字化管理。
某型发动机叶片的数控编程和仿真加工
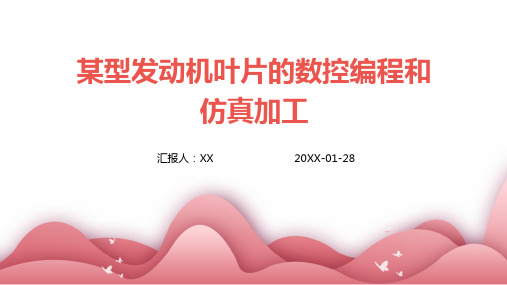
由于叶片的薄壁和复杂曲面特点,加工过程中容 易产生变形。解决方案包括优化装夹方式、采用 小切削力加工、合理安排加工顺序等。
数控编程技术
叶片的复杂曲面形状需要高精度的数控编程技术 。解决方案包括采用专业的CAM软件进行编程、 优化刀具路径、提高编程精度等。
刀具选择与管理
叶片加工需要用到多种刀具,刀具的选择和管理 对加工质量和效率有很大影响。解决方案包括选 用高性能刀具、建立刀具管理系统、定期检查和 更换刀具等。
度、进给量和切削深度等,以提高加工效率和质量。
程序仿真与调试
03
利用仿真软件对程序进行验证和调试,确保程序的正
确性和可行性,减少实际加工中的试切次数和成本。
04
仿真加工技术
仿真软件介绍
01
CATIA
02
UG NX
03
Vericut
一款广泛应用于航空航天领域的三维 CAD/CAM/CAE软件,具有强大的曲 面造型功能和高级数控编程能力,适 用于复杂发动机叶片的设计和仿真。
了加工的成功率和效率。
03
通过本项目的研究,推动了数控编程和仿真加工技术
的发展,为相关领域的技术进步做出了贡献。
未来研究方向展望
01 深入研究更加高效、智能的数控编程算法,进一 步提高发动机叶片的加工精度和效率。
02 将仿真加工技术与实际加工过程更加紧密地结合 ,实现实时仿真和加工过程的优化。
03 探索将本项目的研究成果应用于其他类似零件的 加工,拓展其应用范围和领域。
发展趋势
随着计算机技术和制造技术的不 断发展,数控编程和仿真加工技 术将越来越智能化、自动化和精 细化。
本项目研究目标
研究目标
本项目旨在研究某型发动机叶片的数控编程和仿真加工技术,实现叶片的高精度、高效 率制造。
发动机叶片的造型和数控加工
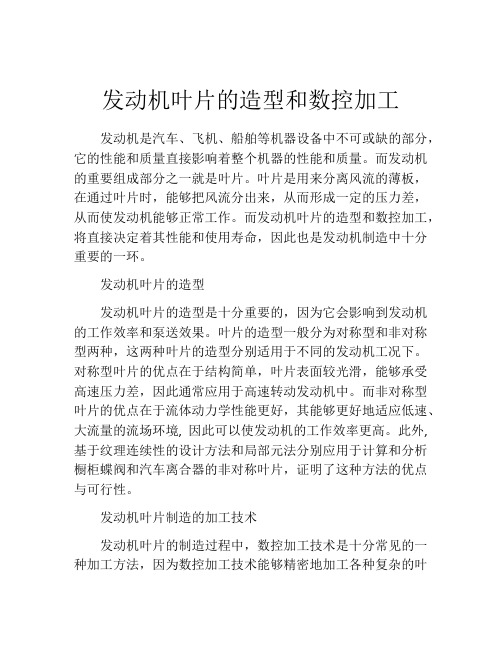
发动机叶片的造型和数控加工发动机是汽车、飞机、船舶等机器设备中不可或缺的部分,它的性能和质量直接影响着整个机器的性能和质量。
而发动机的重要组成部分之一就是叶片。
叶片是用来分离风流的薄板,在通过叶片时,能够把风流分出来,从而形成一定的压力差,从而使发动机能够正常工作。
而发动机叶片的造型和数控加工,将直接决定着其性能和使用寿命,因此也是发动机制造中十分重要的一环。
发动机叶片的造型发动机叶片的造型是十分重要的,因为它会影响到发动机的工作效率和泵送效果。
叶片的造型一般分为对称型和非对称型两种,这两种叶片的造型分别适用于不同的发动机工况下。
对称型叶片的优点在于结构简单,叶片表面较光滑,能够承受高速压力差,因此通常应用于高速转动发动机中。
而非对称型叶片的优点在于流体动力学性能更好,其能够更好地适应低速、大流量的流场环境, 因此可以使发动机的工作效率更高。
此外, 基于纹理连续性的设计方法和局部元法分别应用于计算和分析橱柜蝶阀和汽车离合器的非对称叶片,证明了这种方法的优点与可行性。
发动机叶片制造的加工技术发动机叶片的制造过程中,数控加工技术是十分常见的一种加工方法,因为数控加工技术能够精密地加工各种复杂的叶片。
在数控加工中,一般采取数控机床加工的方式进行制造。
具体来说,数控加工先需要进行CAD 设计,将发动机叶片的模型设计出来。
然后再将设计好的模型文件传输到CNC 中,由CNC 控制数控机床进行加工。
数控机床通常采用不同的工具来完成不同的加工任务,这些工具包括铣刀、钻头、刀具等。
采用数控加工技术加工出来的发动机叶片,精度高、质量好、工作效率高、寿命长、制造成本低等优点,因此受到了工程师和制造商的广泛关注。
总体来说,发动机叶片的制造是一个非常重要的工程,其造型和数控加工技术直接关系到其使用效果。
因此,需要科学严谨的制造技术和工程人员的精细设计方案来完成。
相信在未来的发展中,随着科技的不断进步和制造技术的不断提高,发动机叶片的质量和技术水平也必将不断提高和完善,使其更加适应不同的工业领域和需求。
发动机叶片的造型和数控加工
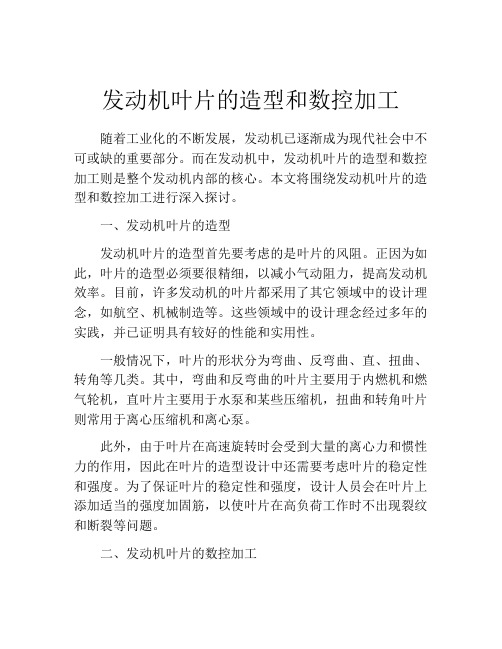
发动机叶片的造型和数控加工随着工业化的不断发展,发动机已逐渐成为现代社会中不可或缺的重要部分。
而在发动机中,发动机叶片的造型和数控加工则是整个发动机内部的核心。
本文将围绕发动机叶片的造型和数控加工进行深入探讨。
一、发动机叶片的造型发动机叶片的造型首先要考虑的是叶片的风阻。
正因为如此,叶片的造型必须要很精细,以减小气动阻力,提高发动机效率。
目前,许多发动机的叶片都采用了其它领域中的设计理念,如航空、机械制造等。
这些领域中的设计理念经过多年的实践,并已证明具有较好的性能和实用性。
一般情况下,叶片的形状分为弯曲、反弯曲、直、扭曲、转角等几类。
其中,弯曲和反弯曲的叶片主要用于内燃机和燃气轮机,直叶片主要用于水泵和某些压缩机,扭曲和转角叶片则常用于离心压缩机和离心泵。
此外,由于叶片在高速旋转时会受到大量的离心力和惯性力的作用,因此在叶片的造型设计中还需要考虑叶片的稳定性和强度。
为了保证叶片的稳定性和强度,设计人员会在叶片上添加适当的强度加固筋,以使叶片在高负荷工作时不出现裂纹和断裂等问题。
二、发动机叶片的数控加工对于现代高质量发动机而言,叶片的造型虽然重要,但若没有高精度的数控加工设备和技术,那么这些叶片的性能将会受到很大影响。
因此,数控加工在现代发动机叶片的制造过程中已成为必不可少的工艺。
在数控加工中,通常使用数控车床、数控铣床和数控磨床等设备对发动机叶片进行加工。
这些设备在加工叶片中,可以实现高速切削、高精度和高质量的加工效果,提高了生产效率和加工精度。
除了加工设备的先进性外,数控加工中的刀具也是非常关键的一环。
如今,许多车铣刀具都采用先进的多层涂层技术,以提高刀具的耐磨性和使用寿命。
此外,一些新型的刀具设计也能够更好地适应高速旋转的叶片的加工需求。
以上是发动机叶片的造型和数控加工的基本内容。
笔者认为,随着经验证明的设计和技术不断取得进展,发动机叶片的性能将会进一步突破。
同时,在数控加工技术高速发展的今天,精度和效率也将得到大大提升。
航空发动机精锻叶片数字化数控加工技术
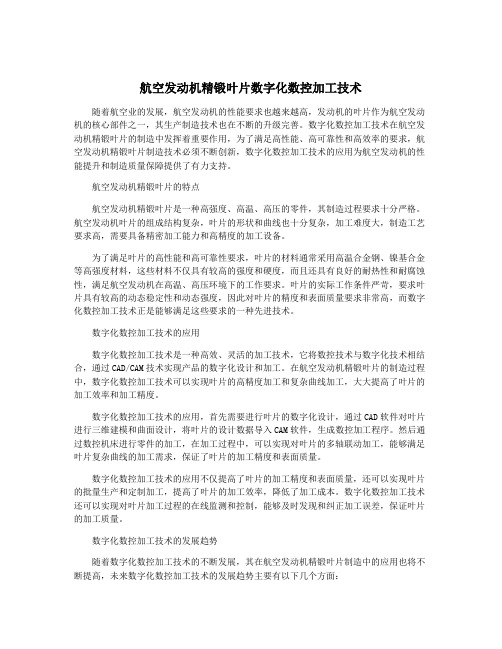
航空发动机精锻叶片数字化数控加工技术随着航空业的发展,航空发动机的性能要求也越来越高,发动机的叶片作为航空发动机的核心部件之一,其生产制造技术也在不断的升级完善。
数字化数控加工技术在航空发动机精锻叶片的制造中发挥着重要作用,为了满足高性能、高可靠性和高效率的要求,航空发动机精锻叶片制造技术必须不断创新,数字化数控加工技术的应用为航空发动机的性能提升和制造质量保障提供了有力支持。
航空发动机精锻叶片的特点航空发动机精锻叶片是一种高强度、高温、高压的零件,其制造过程要求十分严格。
航空发动机叶片的组成结构复杂,叶片的形状和曲线也十分复杂,加工难度大,制造工艺要求高,需要具备精密加工能力和高精度的加工设备。
为了满足叶片的高性能和高可靠性要求,叶片的材料通常采用高温合金钢、镍基合金等高强度材料,这些材料不仅具有较高的强度和硬度,而且还具有良好的耐热性和耐腐蚀性,满足航空发动机在高温、高压环境下的工作要求。
叶片的实际工作条件严苛,要求叶片具有较高的动态稳定性和动态强度,因此对叶片的精度和表面质量要求非常高,而数字化数控加工技术正是能够满足这些要求的一种先进技术。
数字化数控加工技术的应用数字化数控加工技术是一种高效、灵活的加工技术,它将数控技术与数字化技术相结合,通过CAD/CAM技术实现产品的数字化设计和加工。
在航空发动机精锻叶片的制造过程中,数字化数控加工技术可以实现叶片的高精度加工和复杂曲线加工,大大提高了叶片的加工效率和加工精度。
数字化数控加工技术的应用,首先需要进行叶片的数字化设计,通过CAD软件对叶片进行三维建模和曲面设计,将叶片的设计数据导入CAM软件,生成数控加工程序。
然后通过数控机床进行零件的加工,在加工过程中,可以实现对叶片的多轴联动加工,能够满足叶片复杂曲线的加工需求,保证了叶片的加工精度和表面质量。
数字化数控加工技术的应用不仅提高了叶片的加工精度和表面质量,还可以实现叶片的批量生产和定制加工,提高了叶片的加工效率,降低了加工成本。
航空发动机叶片数控加工技术应用研究

航空发动机叶片数控加工技术应用研究摘要:作为航空发动机中的关键部件,叶片类零件的加工质量关系到发动机的使用性能和服役寿命。
为了满足航空航天应用需求,必须突破叶片数控加工难点,不断革新数控加工技术。
基于此,对当下部分航空发动机叶片数控加工技术应用状况进行研究、整理和分析,阐述了一次装夹完整加工技术、自适应加工技术、零点定位快速装夹技术、叶片型面数控机械抛光技术等多种数据加工技术发展现状,并提出一些应用策略,用以全面提升航空发动机叶片数据加工水平,为相关工作人员提供理论参考。
关键词:航空发动机叶片;数控加工技术;应用研究;1引言航空发动机叶片型面结构复杂,材料强度大,造就了机械加工领域超高的成型加工难度。
在过去的十几年里,通常采用数控加工技术来实现对航空发动机叶片的加工。
随着航空航天领域对航空发动机叶片结构、性能要求的不断变化,传统的数控加工技术逐渐有些捉襟见肘,难以有效保证加工效率和质量。
并且,由于缺乏先进的数控加工技术以及应用经验,部分企业在开展航空发动机叶片数据加工时面临诸多的难点、疑点和困点,导致发动机叶片加工合格率不佳。
想要制造出高精度、高质量的航空发动机叶片,就必须大力发展数控加工技术。
为了满足新时期高性能航空发动机研制和生产需求,应当首先正视叶片加工难题,加强叶片数控加工技术体系完善和优化,以技术创新为驱动,打开叶片数控加工新局面。
2航空发动机叶片数控加工技术应用研究2.1一次装夹加工技术一次装夹完整加工技术顾名思义是指通过一次装夹工件来完成对工件的多道工序加工。
在航空发动机叶片加工模式中,叶片的生产周期越短,利润空间就越能得到保障。
倘若因叶片加工过程链过长而导致交货周期失控,就注定会被激烈的市场竞争所淘汰。
因此,如何有效减少工序数量以及工件滞留于机床的时间成为了航空发动机叶片加工水平提升的关键。
于是,一次装夹加工技术应运而生。
它是数控加工的根本特色加工技术,摆脱了叶片传统加工模式长滞留和多替换机床弊端,使叶片的所有加工工序能处于一台机床来完成,实现了叶片加工工序的集成化,这无疑极大地提升了加工效率,保障了叶片加工的精度。
发动机叶片的造型和数控加工
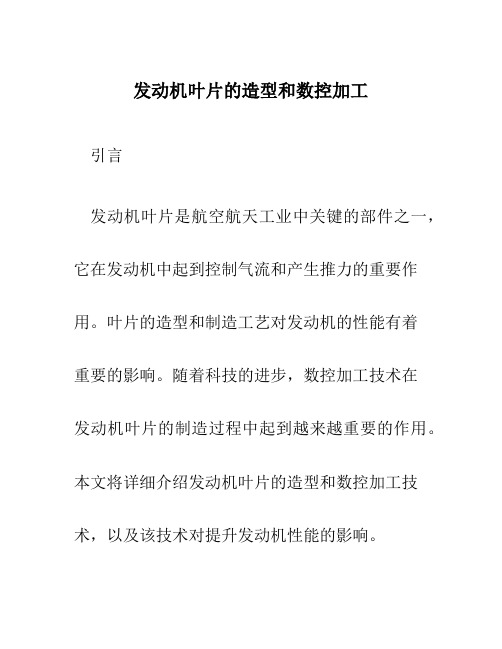
发动机叶片的造型和数控加工引言发动机叶片是航空航天工业中关键的部件之一,它在发动机中起到控制气流和产生推力的重要作用。
叶片的造型和制造工艺对发动机的性能有着重要的影响。
随着科技的进步,数控加工技术在发动机叶片的制造过程中起到越来越重要的作用。
本文将详细介绍发动机叶片的造型和数控加工技术,以及该技术对提升发动机性能的影响。
发动机叶片的造型设计叶片的功能和重要性发动机叶片是将燃气能量转化为机械能的核心部件之一。
它通过旋转产生的离心力将空气压缩并推向喷嘴,进而产生推力。
因此,叶片的形状和尺寸对发动机的性能有着直接的影响。
叶片的设计需要考虑气流流动、强度和疲劳等因素,以确保叶片可以在高温、高速和高压力的工况下长时间运行。
叶片的流线型设计为了提高发动机的效率和推力,叶片的设计通常采用流线型的外形。
流线型设计可以减小气流的阻力,提高叶片的喷气推力,从而提高飞机的速度和燃油效率。
此外,流线型设计还可以减少噪音和振动,提高乘坐舒适度。
叶片的材料选择叶片的材料选择也是叶片设计过程中的重要环节。
目前常用的叶片材料有镍基高温合金和钛合金。
镍基高温合金具有优异的高温性能和耐腐蚀性,适用于高温工况下的发动机。
而钛合金则具有较高的强度和轻量化的优势,适用于中低温工况下的发动机。
数控加工技术在发动机叶片制造中的应用数控加工革新传统加工方式传统的发动机叶片加工方式主要依赖于人工操作,加工效率低下且容易产生误差。
而数控加工技术的出现改变了叶片制造的传统方式,使得叶片的加工过程更加精确、高效和自动化。
数控加工的优势数控加工技术具有许多优势,使其在发动机叶片制造过程中得到了广泛应用。
首先,数控加工可以实现复杂形状的叶片加工,无论是曲线形状还是定位孔的加工都可以精确控制。
其次,数控加工可以提高加工精度,减少人为误差和废品率。
最后,数控加工还可以提高生产效率,减少加工时间和人力成本。
数控加工在叶片制造中的具体应用数控加工技术在发动机叶片制造中有多种具体应用。
航空发动机涡轮叶片精密成形技术分析
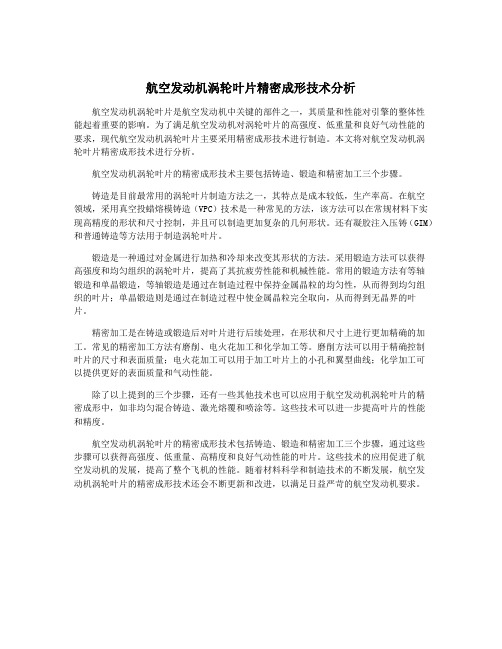
航空发动机涡轮叶片精密成形技术分析航空发动机涡轮叶片是航空发动机中关键的部件之一,其质量和性能对引擎的整体性能起着重要的影响。
为了满足航空发动机对涡轮叶片的高强度、低重量和良好气动性能的要求,现代航空发动机涡轮叶片主要采用精密成形技术进行制造。
本文将对航空发动机涡轮叶片精密成形技术进行分析。
航空发动机涡轮叶片的精密成形技术主要包括铸造、锻造和精密加工三个步骤。
铸造是目前最常用的涡轮叶片制造方法之一,其特点是成本较低,生产率高。
在航空领域,采用真空投蜡熔模铸造(VPC)技术是一种常见的方法,该方法可以在常规材料下实现高精度的形状和尺寸控制,并且可以制造更加复杂的几何形状。
还有凝胶注入压铸(GIM)和普通铸造等方法用于制造涡轮叶片。
锻造是一种通过对金属进行加热和冷却来改变其形状的方法。
采用锻造方法可以获得高强度和均匀组织的涡轮叶片,提高了其抗疲劳性能和机械性能。
常用的锻造方法有等轴锻造和单晶锻造,等轴锻造是通过在制造过程中保持金属晶粒的均匀性,从而得到均匀组织的叶片;单晶锻造则是通过在制造过程中使金属晶粒完全取向,从而得到无晶界的叶片。
精密加工是在铸造或锻造后对叶片进行后续处理,在形状和尺寸上进行更加精确的加工。
常见的精密加工方法有磨削、电火花加工和化学加工等。
磨削方法可以用于精确控制叶片的尺寸和表面质量;电火花加工可以用于加工叶片上的小孔和翼型曲线;化学加工可以提供更好的表面质量和气动性能。
除了以上提到的三个步骤,还有一些其他技术也可以应用于航空发动机涡轮叶片的精密成形中,如非均匀混合铸造、激光熔覆和喷涂等。
这些技术可以进一步提高叶片的性能和精度。
航空发动机涡轮叶片的精密成形技术包括铸造、锻造和精密加工三个步骤,通过这些步骤可以获得高强度、低重量、高精度和良好气动性能的叶片。
这些技术的应用促进了航空发动机的发展,提高了整个飞机的性能。
随着材料科学和制造技术的不断发展,航空发动机涡轮叶片的精密成形技术还会不断更新和改进,以满足日益严苛的航空发动机要求。
发动机叶片的造型和数控加工
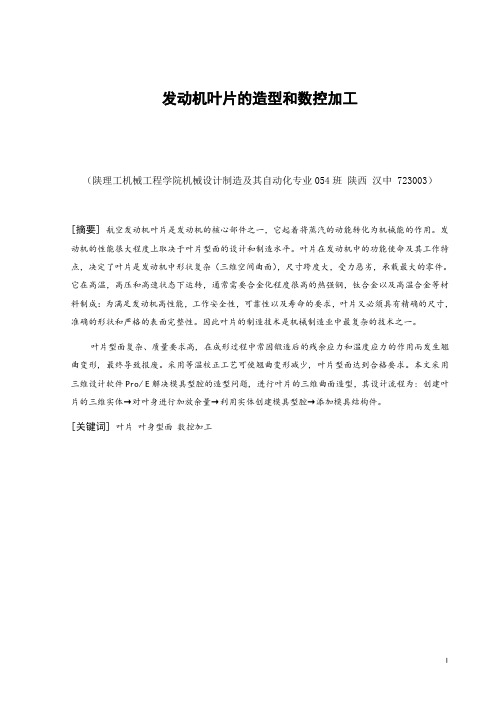
发动机叶片的造型和数控加工(陕理工机械工程学院机械设计制造及其自动化专业054班陕西汉中 723003)[摘要]航空发动机叶片是发动机的核心部件之一,它起着将蒸汽的动能转化为机械能的作用。
发动机的性能很大程度上取决于叶片型面的设计和制造水平。
叶片在发动机中的功能使命及其工作特点,决定了叶片是发动机中形状复杂(三维空间曲面),尺寸跨度大,受力恶劣,承载最大的零件。
它在高温,高压和高速状态下运转,通常需要合金化程度很高的热强钢,钛合金以及高温合金等材料制成:为满足发动机高性能,工作安全性,可靠性以及寿命的要求,叶片又必须具有精确的尺寸,准确的形状和严格的表面完整性。
因此叶片的制造技术是机械制造业中最复杂的技术之一。
叶片型面复杂、质量要求高, 在成形过程中常因锻造后的残余应力和温度应力的作用而发生翘曲变形, 最终导致报废。
采用等温校正工艺可使翘曲变形减少, 叶片型面达到合格要求。
本文采用三维设计软件Pro/ E解决模具型腔的造型问题, 进行叶片的三维曲面造型,其设计流程为: 创建叶片的三维实体→对叶身进行加放余量→利用实体创建模具型腔→添加模具结构件。
[关键词] 叶片叶身型面数控加工Engine blade's moldingand numerical control processingAbstract:Blade of Aero—engine is a type is one of engine core parts; It is playing the steam energy transformation for the mechanical energy role. The engine performance is decided to a great extent by the leaf blade profile design and the manufacture level. Blade’s in engine function mission and the work characteristic, had decided the leaf blade is in the engine the shape complex (three-dimensional space curved surface),the size span big, the stress bad, the load bearing biggest components, It in high temperature ,high pressure and under the high-speed run revolves, usual need alloy degree very high materials and so on heat strong steel, titanium alloy as well as heat-resisting alloy make; In order to satisfy the engine high performance, the work security, reliable as well as the life request, the leaf blade must have the precise size, the accurate shape and the strict superficial integrity. Therefore leaf blades technique of manufacture is in the mechanical manufacturing industry of most complex technologies.Blade is shape is complex and the quality requirement is high. The warps and the forgings may be discarded due to the formed forgings remaining stress and the temperature stress. But it is possible to use the isothermal adjustment process to reduce the warp distortion and make the blade shape to meet the qualified requirements. Three-dimensional design software Pro/ E was used to carry on the design in view of the uniform temperature adjustment mold. The three dimensional surface modeling of blade was carried out and the heating and cooling devices for the isothermal sizing die were simultaneously designed. It’s design flow is: creating the three dimensional entity of the blade, adding on margin to the blade , using entity to set up the mold cavity , putting on the mold structural elements.Key Words:Blades, NC Machining, Blade Shape,目录1绪论 (1)1.1课题背景 (1)1.2 发到机叶片加工方法 (1)1.2.1 仿形法 (1)1.2.2 数控加工方法 (2)1.3 课题研究的目的和意义 (2)2 模具发展概况、发展方向和发展趋势以及PRO/E软件介绍 (4)2.1中国模具行业发展现状 (4)2.2中国模具发展的方向 (4)2.3 PRO/ENGINEER软件简介 (6)2.4 PRO/E软件主要模块介绍 (6)3 叶片造型 (8)3.1 PRO/ E 设计软件绘制叶身 (8)3.1.1叶片的形状 (8)3.1.2 绘制叶身 (8)3.2绘制安装板及榫头 (13)4 基于PRO/ E 的模具设计 (18)4.1毛边槽的设计 (18)4.2锻模的设计与造型 (20)4.2.1 创建制造—模具型腔,进入模具造型模块 (20)4.2.2创建分型面 (21)5 叶片加工工艺分析及模具数控加工仿真 (24)5.1叶片结构工艺分析 (24)5.1.1典型的叶片结构分析和机械工艺性评价 (24)5.1.2叶片加工中的技术要求 (25)5.2工艺路线的拟订 (25)5.2.1加工阶段的划分 (25)5.2.2工艺基准及其选择 (26)5.2.3毛坯的选择 (27)5.2.4加工方法的选择 (27)5.2.5刀具选择 (28)5.3发动机叶片的模型加工 (29)5.4模具数控加工仿真 (31)总结 (35)参考文献 (36)致谢 (37)外文翻译 (38)1绪论1.1课题背景航空发动机叶片是发动机的核心部件之一,它起着将蒸汽的动能转化为机械能的作用。
分体式叶片零件的数控加工(1
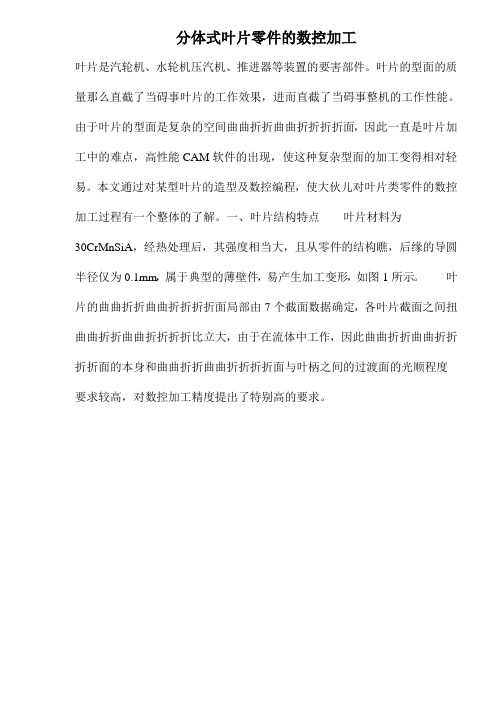
分体式叶片零件的数控加工叶片是汽轮机、水轮机压汽机、推进器等装置的要害部件。
叶片的型面的质量那么直截了当碍事叶片的工作效果,进而直截了当碍事整机的工作性能。
由于叶片的型面是复杂的空间曲曲折折曲曲折折折折面,因此一直是叶片加工中的难点,高性能CAM软件的出现,使这种复杂型面的加工变得相对轻易。
本文通过对某型叶片的造型及数控编程,使大伙儿对叶片类零件的数控加工过程有一个整体的了解。
一、叶片结构特点叶片材料为30CrMnSiA,经热处理后,其强度相当大,且从零件的结构瞧,后缘的导圆半径仅为0.1mm,属于典型的薄壁件,易产生加工变形,如图1所示。
叶片的曲曲折折曲曲折折折折面局部由7个截面数据确定,各叶片截面之间扭曲曲折折曲曲折折折折比立大,由于在流体中工作,因此曲曲折折曲曲折折折折面的本身和曲曲折折曲曲折折折折面与叶柄之间的过渡面的光顺程度要求较高,对数控加工精度提出了特别高的要求。
图1叶片实体模型依据笔者的总结,叶片的加工工艺流程如图2所示。
图2加工工艺流程二、叶片的CAD造型依据不同的需求叶片能够表示为曲曲折折曲曲折折折折面模型、实体模型、特征模型,曲曲折折曲曲折折折折面模型适用于数控加工,实体模型可用于几何参数分析,特征模型可用于设计、加工、产品治理集成。
建立叶片的曲曲折折曲曲折折折折面模型是其在造型最全然的要求,更进一步那么是建立实体模型,建立特征模型是生产治理上更高层次的需求。
依据设计提供的截面数据不同,叶片曲曲折折曲曲折折折折面能够分为直纹面以及自由曲曲折折曲曲折折折折面,其造型方法也有所不同。
该叶片属于自由曲曲折折曲曲折折折折面叶片,造型过程比立复杂,而且其加工精度要求也较高。
其设计数据是按几个截面给出的,各个截面为以轮毂轴线为轴线的一组同心圆柱面,数据为圆柱面展开平面,沿弦线为水平方向给出。
曲曲折折曲曲折折折折面造型过程分为构造展开平面内的各段曲曲折折曲曲折折折折线、编辑构造空间截面线、构造曲曲折折曲曲折折折折面以及过渡区域R面建立等4个步骤。
- 1、下载文档前请自行甄别文档内容的完整性,平台不提供额外的编辑、内容补充、找答案等附加服务。
- 2、"仅部分预览"的文档,不可在线预览部分如存在完整性等问题,可反馈申请退款(可完整预览的文档不适用该条件!)。
- 3、如文档侵犯您的权益,请联系客服反馈,我们会尽快为您处理(人工客服工作时间:9:00-18:30)。
发动机叶片的造型和数控加工(陕理工机械工程学院机械设计制造及其自动化专业054班陕西汉中 723003)[摘要]航空发动机叶片是发动机的核心部件之一,它起着将蒸汽的动能转化为机械能的作用。
发动机的性能很大程度上取决于叶片型面的设计和制造水平。
叶片在发动机中的功能使命及其工作特点,决定了叶片是发动机中形状复杂(三维空间曲面),尺寸跨度大,受力恶劣,承载最大的零件。
它在高温,高压和高速状态下运转,通常需要合金化程度很高的热强钢,钛合金以及高温合金等材料制成:为满足发动机高性能,工作安全性,可靠性以及寿命的要求,叶片又必须具有精确的尺寸,准确的形状和严格的表面完整性。
因此叶片的制造技术是机械制造业中最复杂的技术之一。
叶片型面复杂、质量要求高, 在成形过程中常因锻造后的残余应力和温度应力的作用而发生翘曲变形, 最终导致报废。
采用等温校正工艺可使翘曲变形减少, 叶片型面达到合格要求。
本文采用三维设计软件Pro/ E解决模具型腔的造型问题, 进行叶片的三维曲面造型,其设计流程为: 创建叶片的三维实体→对叶身进行加放余量→利用实体创建模具型腔→添加模具结构件。
[关键词] 叶片叶身型面数控加工Engine blade's moldingand numerical control processingAbstract:Blade of Aero—engine is a type is one of engine core parts; It is playing the steam energy transformation for the mechanical energy role. The engine performance is decided to a great extent by the leaf blade profile design and the manufacture level. Blade’s in engine function mission and the work characteristic, had decided the leaf blade is in the engine the shape complex (three-dimensional space curved surface),the size span big, the stress bad, the load bearing biggest components, It in high temperature ,high pressure and under the high-speed run revolves, usual need alloy degree very high materials and so on heat strong steel, titanium alloy as well as heat-resisting alloy make; In order to satisfy the engine high performance, the work security, reliable as well as the life request, the leaf blade must have the precise size, the accurate shape and the strict superficial integrity. Therefore leaf blades technique of manufacture is in the mechanical manufacturing industry of most complex technologies.Blade is shape is complex and the quality requirement is high. The warps and the forgings may be discarded due to the formed forgings remaining stress and the temperature stress. But it is possible to use the isothermal adjustment process to reduce the warp distortion and make the blade shape to meet the qualified requirements. Three-dimensional design software Pro/ E was used to carry on the design in view of the uniform temperature adjustment mold. The three dimensional surface modeling of blade was carried out and the heating and cooling devices for the isothermal sizing die were simultaneously designed. It’s design flow is: creating the three dimensional entity of the blade, adding on margin to the blade , using entity to set up the mold cavity , putting on the mold structural elements.Key Words:Blades, NC Machining, Blade Shape,目录1绪论 (1)1.1课题背景 (1)1.2 发到机叶片加工方法 (1)1.2.1 仿形法 (1)1.2.2 数控加工方法 (2)1.3 课题研究的目的和意义 (2)2 模具发展概况、发展方向和发展趋势以及PRO/E软件介绍 (4)2.1中国模具行业发展现状 (4)2.2中国模具发展的方向 (4)2.3 PRO/ENGINEER软件简介 (6)2.4 PRO/E软件主要模块介绍 (6)3 叶片造型 (8)3.1 PRO/ E 设计软件绘制叶身 (8)3.1.1叶片的形状 (8)3.1.2 绘制叶身 (8)3.2绘制安装板及榫头 (13)4 基于PRO/ E 的模具设计 (18)4.1毛边槽的设计 (18)4.2锻模的设计与造型 (20)4.2.1 创建制造—模具型腔,进入模具造型模块 (20)4.2.2创建分型面 (21)5 叶片加工工艺分析及模具数控加工仿真 (24)5.1叶片结构工艺分析 (24)5.1.1典型的叶片结构分析和机械工艺性评价 (24)5.1.2叶片加工中的技术要求 (25)5.2工艺路线的拟订 (25)5.2.1加工阶段的划分 (25)5.2.2工艺基准及其选择 (26)5.2.3毛坯的选择 (27)5.2.4加工方法的选择 (27)5.2.5刀具选择 (28)5.3发动机叶片的模型加工 (29)5.4模具数控加工仿真 (31)总结 (35)参考文献 (36)致谢 (37)外文翻译 (38)1绪论1.1课题背景航空发动机叶片是发动机的核心部件之一,它起着将蒸汽的动能转化为机械能的作用。
发动机的性能很大程度上取决于叶片型面的设计和制造水平。
叶片在发动机中的功能使命及其工作特点,决定了叶片是发动机中形状复杂(三维空间曲面),尺寸跨度大,受力恶劣,承载最大的零件。
它在高温,高压和高速状态下运转,通常需要合金化程度很高的热强钢、钛合金以及高温合金等材料制成,为满足发动机高性能、工作安全性、可靠性以及寿命的要求,叶片又必须具有精确的尺寸,准确的形状和严格的表面完整性。
因此叶片的制造技术是机械制造业中最复杂的技术之一。
发动机叶片性能要求很高, 在工作中起着能量转换的作用, 其质量好坏直接影响到发动机的工作效率和运行可靠性[ 1 ] 。
加工工艺一般采用模锻成形, 模锻后用机械加工消除余量, 但是这样不仅会破坏工件的纤维般流线,降低其使用性能, 而且往往因锻件在锻后冷却过程中产生的翘曲量过大而无法加工成成品。
采用等温校正技术, 可以减少锻造变形的残余应力和冷却时的温度应力叠加造成的叶身型面翘曲, 达到释放残余应力、使翘曲变形减轻、叶片尺寸合格、保证其外形和性能的双重要求。
本设计主要应用Pro/ E 软件创建叶片实体, 根据叶片实体进行等温校正模具及加热冷却系统的设计。
1.2 发到机叶片加工方法当前飞机发动机从涡喷系列发动机逐步发展到涡扇系列,叶片型面越来越复杂,呈叶身扭曲弯度趋大,叶旋趋宽,叶身趋薄,前掠加大等特点。
此种叶片复杂曲面的形成原理复杂,加工困难,加工精度不易保证。
加工叶片的刀具比一般机械加工选用刀具要考虑更多的因素。
叶片材料由铝合金、不锈钢发展为钛合金高温合金以及新型复合材料,呈现硬度高,韧性大,让刀严重,加工过程中刀具磨损快,加工表面变形程度大等特点,材料切削加工性也决定了新型发动机叶片的价格难度相当大。
1.2.1 仿形法采用仿形法加工发动机叶片,在加工原理上和其他仿形法一样,首先要根据发动机叶片的型线方程来计算,设计和制造靠模板。
然后以靠模板为基准运用仿形原理,加工出符合要求的叶片。
在加工过程中,靠模板随着使用会出现磨损,加之靠模板加工方法本身的精度不是很高,这样导致加工后的叶片误差很大。
所以加工后都需要对叶片进行人工修型,抛光。
这样不但加工效率低而且加工质量也很低。
仿形法一般只能用于加工相对固定的叶轮型面,这对于目前多品种小批量的产品很不适合,相比之下,数控加工成为叶片加工改革的主要方向。
1.2.2 数控加工方法数控技术是计算机技术在机械制造领域的一种典型应用,它具有的高精度,高柔性,高效率等优点现在已经被人们广泛认可。
随着数控技术在生产中的广泛应用,传统的机械工业的产业结构和生产模式发生了深刻的革命性变化。
近年来国内外已经有不少厂家用数控刨床,数控铣床,数控车床等数控机床加工出多种型号的发动机叶片。
数控加工的产品种类多,精度高,互换性好,同时加工效率高,操作简便。
因此,使用发动机叶片数控铣削加工,将会具有良好的经济效益和广阔的市场前景。
1.3 课题研究的目的和意义作为飞机发动机核心部分的叶片,其发展趋势在很大程度上决定了飞机发动机的发展。
因此,发动机叶片的加工具有很大的意义。
主要体现在一下几个方面:飞机发动机叶片的加工精度直接影响飞机发动机的使用性能。