沉降罐自动收油工艺改造试验
污水站沉降罐收油工艺的优化

3 . ,除杂 率 1 . ,二沉 出水 含油 9 . / 85 17 5 7mg
L ,含 悬浮 物 4 . / 5 6mg L,除油率 2 . ,除杂率 78
日油层厚度在 3  ̄4 m之 间 ,除油率仅为 2 5 , 0 0e .1
10 7 mg L, 含 悬 浮 物 4 . mg L, 除 油 率 3 . / 73 /
期 间 ,北 十 三污水 站二次沉 降罐 的除 油率较 高并较
稳 定 , 除 油 效 率 6 6 , 含 油 为 8 . 5mg L。此 .5 6 7 /
期 间油层 厚度 平均 为 2 m,收油 周期控 制在 1 ~ 5c O
5 . 3 ,含 油 量 为 1 1 5mg L,此 时 油 层 厚 度 为 8 6 0 . / 3 m 以 上 ,收 油 周 期 为 2 ~ 3 。 5c O 5d 从 图 2 出 如 下 结 论 :从 一 次 沉 降 罐 除 杂 率 来 得
收走 ,是 减少 老化油 量 和确保沉 降罐处 理水 质质量
盖 ,罐 内 的 污 油 无 法 回 收 ,随 着 油 层 厚 度 的 增 加 ,
期 间 ,北十 三污水 站一次 沉 降罐 的除油率较 高并较
稳 定 , 除 油 效 率 6 . 5 , 含 油 为 9 . 7 / 。 6 4 2 8 5 mg L 此 期 间 油层 厚 度 为 1 ̄ 3 m,收 油 周 期 为 1  ̄ 1 。 0 0c 3 6d
图1 、图 2为 北 十 三 聚 合 物 污 水 处 理 站 2 0 09
年 2 8 一次沉 降罐 除油率 和除杂 率 曲线 图 。 ~ 月
为 此开展 了沉 降罐 间歇 收油工艺 收油 、收油 槽式 连
污水沉降罐收油方法探讨

污水沉降罐收油方法探讨摘要:根据某联污水站收油的现状,探讨了污水系统影响收油的因素,在传统的收油方式上改进方法,采取工艺改进,提高收油温度,保证液位稳定等技术措施。
关键词:收油方式因素措施1 传统的收油方式目前,联合站污水系统的收油方式主要为重力式收油排油,即靠定期提升大罐液位,使罐内浮于污水上方的原油溢流进收油槽内,流入槽下的收油管,靠液位差自压流入污油罐,当罐内污油达到一定厚度时,由收油泵将罐内污油输送到脱水转油站。
(1)污油构成。
污水沉降罐主要接受某联反冲洗水、本站来水(含油在100-280mg/L之间)和注水干线冲洗污水(最高含油达到1000mg/L)。
同时某联污水站定期投加絮凝剂、杀菌剂。
这样污油主要由油、絮凝剂、杀菌剂、污水、固体悬浮物组成。
(2)收油现状。
5000m3一次沉降罐、3000m3二次沉降罐的收油槽为固定式(在罐的上部),由于罐的保温效果不太理想,低温时污油粘稠。
因此,在有针对性的工艺改造之前,如何在现有条件下回收污水沉降罐的污油,保证污水水质已成为联合站污水系统操作者的迫切要求。
2 影响收油因素分析(1)温度。
温度是影响收油的一个重要因素。
在冬季,由于气温低,罐内油层上部会形成硬盖,无法收油;而在夏季,污油温度有所上升,但只能回收部分上部的污油,而下部浮油成块,流动性极差,距离远端的污油不会进入到收油槽,无法保证收油的彻底。
(2)工艺限制。
收油管线前半段(污水岗—输油岗)管径为Φ114mm,从输油岗—老化油装置管径细为Φ78mm,而真空加热炉换热管较细为Φ38mm,管线易堵,导致炉压上升,由负压变成正压,安全阀经常动作蒸汽外泄。
而污水站收油泵,由于污油流动性变差,易抽空发生汽化,直接影响收油效果。
(3)液位控制。
收油过程需要液位的平稳,影响液位平稳因素包括来液的平稳、人为调控液位的准确度等。
(4)仪表。
由于沉降罐收油需要人为抬高液位,使污油进入收油槽,这样需要仪表十分精确,收油过程中由于存在测量误差,往往需要人上罐监控,增加了工作强度。
油田污水沉降罐收油工艺改造技术

28油气田地面工程第23卷第5期(2004.5)油田污水沉降罐收’油工艺改造技术周彩红(大庆油田采油二厂)刁]姜慧韬李春娟管龙凤(大庆油田采油八产)据统计,大庆油田采油八厂每天有187512"13的污水外排.随着含水的上升,污水外排问题日趋严重。
增加污水处理系统缓冲能力,将多余的污水消化在站内,是治理油田污水的重要手段。
针对立式污水沉降罐在生产中存在高液位运行缓冲能力JJ\和不连续收油造成污油老化影晌收油效果和水质等问题,研究用活动式收油工艺取代现行固定式收油结构,可为有效治理油田污水探索新的技术途径。
1.在用污水沉降罐弊端及改造原理在用的污水沉降罐收油工艺存在以下几个弊端:①沉降罐采取固定式收油结构,罐内液位必须达到收油槽高度才能收到污油,罐的缓冲能力小;②生产中不连续收油,易使罐内污油老化形成硬油盖,影响收油效果和水质;③加热盘管设计高度高,水量U\B,-j不能浸入油层中,影IilO热效果。
针对沉降罐收油工艺存在的弊端,研究在满足沉降要求的情况下,通过收油工艺技术改造,用活动式收油工艺代替现行固定式收油结构解决生产中存在的问题。
按沉降罐理论结构计算,在满足现有的沉降效果条件下,将沉降罐改成活动式收油装置,原来高报:百变,调节低报液位,出水口高6.4m,再加上0.2m的理论高度,得出低报液位6.6m,8.8—6.6=2.2(m),即有2.2m的缓冲空间,每米容积116.5m3,该罐有256m3的缓冲量。
以宋二联油岗1000m3污水沉降罐为例,研究两种收油工艺改造方法,一是用活动式收油装置靠液位自动控制连续或定期收油。
二是在罐内增设不同高度固定收油装置,用阀门控制连续或定期收油。
2.用活动式收油装置靠液位自动控制工艺改造(1)改造方法。
做4个相同的活动式收油装置代替现行固定式收油槽收油。
方法是用3ram厚的钢板焊接成圆柱形筒,筒的上部用钢板盖密封,在筒盖上焊一个小圆筒做浮漂置于筒内。
将筒下部分成上下两部分,顶部打均匀长方形孔作收油槽,收油槽底部出油钢管通过法兰与出油软管相连,再与罐原有的出油管连接,使收油装置随液位改变上下移动。
深度污水处理站过滤罐收油效果

2 ) 在两 级 过 滤 罐 中上 部 增 设 收 油 流程 ,采 用
定 每 班收 油一 次 ,收油 时 ,以看 窗 由黑 见清 澈水 流 为止 ;所 收含水 污油 直接进 入 回收水 池 。
罐反 冲洗排 污 系统无 法将 其洗 排 干净 , E l 积 月累会 自动 化定期 回收过 滤罐 内部 上层 的油 污 ( 图1 ) 。暂 导致 过滤 效果 下降 ,滤料 板结 ,截 污失效 。
一 环 保 ・ 安 呈 , E n v o i r o n m e n t P r o t e c t i o n ・ S e c u r i t y
深度 污水 处 理 站 过 滤 罐 收 油效 果
盖立 成 ’ 张荣 帅 曹 冬 梅
( 1 . 大 庆 油 田有 限 责 任公 司第 八采 油 厂 ;2 . 大 庆 油 田有 限 责 任 公 司 第 九 采 油 厂 )
摘 要 过滤罐 上 层 漂浮 着 大量 的 污油 ,难 以去 除 ,在 过 滤罐 反 冲洗 过程 中,影 响 滤料 的再 生 效 果 ,使 过 滤罐 内压 力明 显增 加 ,过 滤效 率 下降 。 为解 决这 一 问题 ,在 两级 过 滤罐 中上 部增
设 收 油流程 ,采 用 自动化 方 式定 期 回收 过滤罐 内部上 层 的油 污 。过 滤罐 增 加收 油 流程 是其 工 艺 改进 的一个新 举措 ,该 方 法收油 效果显 著 ,过滤罐 滤后 水质 合格 率 明显上 升 。 关键词 水处理 过 滤罐 污油 收 油流程 水质合 格率
第 一 作 者 简 介 :盖立 成 ,2 0 0 5 年 毕业于大 庆石油学 院 ( 石油 工程专 业)
FSY沉降罐浮油集收装置

一、概述油田采出液在沉降罐内静置一段时间后,由于介质密度差的缘故,水分和固体颗粒等重质成分会沉降到罐下部,而沉降罐上部为较纯净的原油。
传统的沉降罐的收油管或槽位于罐内固定高度位置,收油时由于来液量或液位的波动易带走浮油下部沉降的水分及杂质。
为了保证收油质量和效率,操作者时常要进行沉降罐排污,并且定期清洗沉降罐以排除罐底部沉降的固体颗粒(俗称污泥)。
污水在排放过程中不可避免地要带走部分乳化原油,因而又增加了原油的损耗。
东营澄工石油设备制造有限公司研制的沉降罐浮油自动集收装置克服了以往沉降罐液位不稳定、出油含水的缺陷,该装置利用移动浮筒和固定浮筒产生的浮力使装置随罐内液位的变化而上下浮动。
通过液位和油水界面的自动控制使装置收油口始终吸取上部较纯净的浮油,有效地保证了收油质量,同时也为低效油田简化油气水处理工艺提供了有力的保证。
装置适用于原油罐或污水沉降罐中使用,也可用于外输油品作业。
同时适用于异种密度不同液体分别排放收集的储罐中使用。
二、装置结构装置主要由浮动收油机械部分及电气控制两大部分组成。
机械部分包括回转机构、回转管臂、浮子、收油口四部分。
电气控制部分包括矩阵式水位测量仪、雷达液位计、电动阀门、显示仪表和PLC 控制系统。
三、工艺原理1、机械部分当罐内达到一定液位高度时,浮筒受液体浮力作用向上下浮动,并带动回转臂旋转及收油口向上下浮动。
收油口侵入液体表面以下,将表面浮液排除到罐外。
2、自控部分由PLC完成自动收油的控制,当雷达液位计得到液面总高度及矩阵式水位仪得到的水位高度,转换成4~20mA的电流信号,输入PLC模数转换模块,经PLC 运算(液面总高度减水面高度)得到浮油介质厚度,得到的浮油介质厚度与设置的厚度比较,如测量的浮油介质厚度大于设定的收油厚度时,启动电动阀门,开始收油,当浮油介质的厚度到达设置的最小收油厚度时,电动阀门关闭,停止收油。
等待下一个循环的开始。
四、技术参数1、使用温度:≤95℃2、工作压力:0.16Mpa3、浮动收液工作高度: 0.5 m~罐体最高液面4、收油厚度:根据工况可随机设置5、沉降时间:不限制6、液面高度报警范围:0~罐体最高点7、防爆等级:ExiaIIBT4五、产品功能1、收油口的上下浮动是通过安装在装置上的平衡浮筒的浮力,随液位的高度不同而上下运动。
4050408期5环保节能周彩红、李春娟油田污水沉降罐收油工艺改造

油田污水沉降罐收油工艺改造技术研究周彩虹(大庆油田有限责任公司第二采油厂)姜慧韬李春娟管龙凤(大庆油田有限责任公司第八采油厂)摘要:随着油田含水的上升,油田污水的有效治理已经成为当前急需解决的重要课题。
本文通过对污水沉降罐结构、工艺原理及油田应用情况的分析,阐述了沉降罐收油工艺特点及其在生产中存在的问题,提出了污水沉降罐活动式收油工艺改造措施,该技术不仅结构简单,成本低,而且达到了增大污水缓冲能力的目的,解决了生产中长期存在的污油老化影响收油效果和水质等问题。
通过对污水沉降罐收油工艺改造技术研究,为沉降罐收油结构改造探索了一条新途径。
主题词:油田污水技术改造增大缓冲改善水质节能环保据统计,八厂油田每天有1875 m3的污水外排,随着含水的上升,这一问题日趋严重。
增加污水处理系统缓冲能力,将多余的污水消化在站内,是治理油田污水的重要手段。
针对立式污水沉降罐在生产中存在高液位运行缓冲能力小和不连续收油造成污油老化影响收油效果和水质等问题,研究用活动式收油工艺取代现行固定式收油结构,为有效治理油田污水探索新的技术途径。
1、油田污水沉降罐情况简介1.1沉降罐除油工艺八厂四座联合站油岗共有污水沉降罐4座,处理规模在500~2000m3/d之间,从容积上分有500 m3、图11.2沉降罐的除油原理:原油脱水系统排出的含油污水由进水管流入罐内中心筒,经配水管流入沉降区。
水中粒径较大的油粒在油水相对密度差的作用下首先上浮至油层,粒径较小的油粒随水向下运动。
在此过程中,一部分小油粒由于自身在静水中上浮速度不同及水流速度梯度的推动,不断碰撞聚结成大油粒而上浮,无上浮能力的部分小油粒随水进入集水管,经出水系统流出沉降罐。
1.3沉降罐除油特点及生产弊端立式沉降罐是一种重力分离型除油构筑物。
由于罐内特定的油水运动过程(包括上向流速度推动浮升过程、对流碰撞聚结过程和油层过滤过程),形成了沉降罐具有很高的除油效果。
研究结果表明,控制分水口水流速度和选择合理的沉降区高度是保证沉降罐工作效果的关键。
长庆油田原油脱水站溢流沉降罐结构的改造及效果
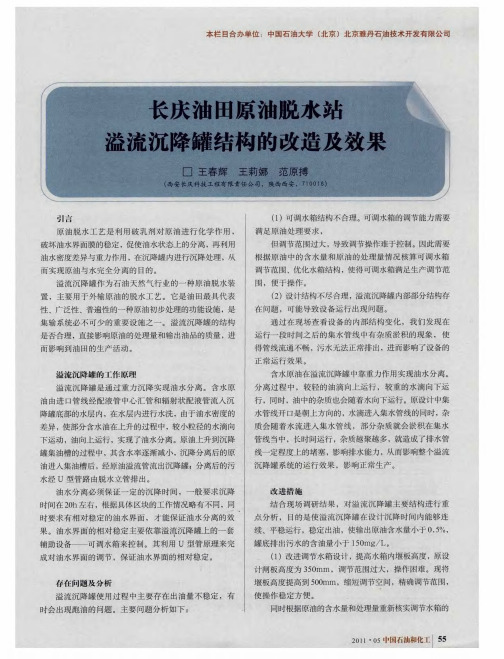
作者 简介 : 王春 辉 ,助理 :程师 。2 0 年 毕业 于 中 E 06 国石油大 学 ( 华东 )建筑环 境与 设备工 程专 业 ,获学 士学 位 ; 现在 西安 长庆 科技 工程 公 司 ,从事 油 田地 面工程 设 计 工作 。囹
与 结蜡 功 图对 比 ,求 出载荷 差值 ,对 结蜡 功 图进 行修 正
( 图 5 示) 如 所 ,还 原成 未结 蜡示 功 图 ( 图 6 示 ) 如 所 ,计
算 出油井 正确 产量 1 4 t 。 7.4/d 通 过 结 蜡 泵 功 图 的 修 正 ,计 算 出 的 产 量 误 差 均 ≤ 1 %,完全 满足油 井计 量精 度要 求 。 0
下, 避免集水管线中杂质存积 , 保证排水管线畅通, 这样
就能保 证 油 水界 面 的相对 稳定 。
参 考文 献 :
实施 效果 [] 1 中国石 油天 然气 总公 司 ,石 油地 面工 程设 计 手册
20 年 8 08 月在长庆油 田某采油厂选取 脱水站进行初步试
点和验证 , 原油通过溢流沉降罐 之后 , 脱水效果达到预期生产 要求 , 在设计的沉降时间 内能够连续运行 , 稳定 出油 , 出原 输
( 第二 册 油 田地面 工程 设计 ) ,石 油大学 出版 社 ,l 9 。 9 4
[] 2 朱泽 民 ,沉 降罐 的优 化设 计 ,( 气 田地 面工程 》 ( 油 , 1 9 ,6 ( ) 2 99 2 , 9~3 ,共 7 页 。 0 7
油含 水量小于 05 罐底排出污水的含油量 小于 10 g L . %, m / , 5
2 0 ,8 ( ) ~4 0 8 1 5 :1 .
尿素装置沉降罐、洗涤罐改造
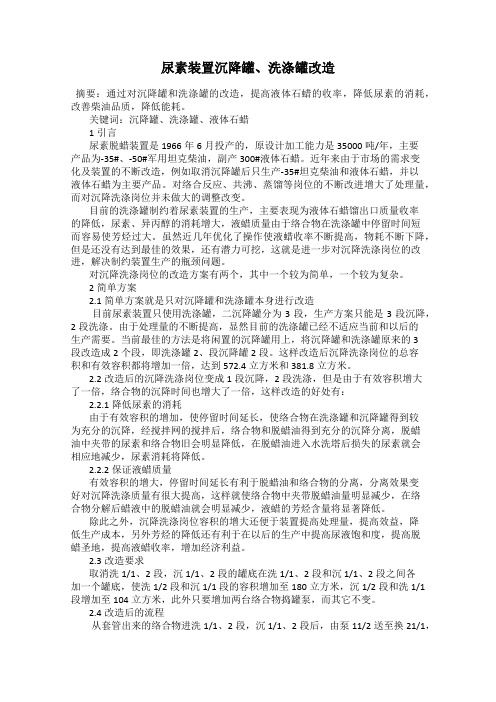
尿素装置沉降罐、洗涤罐改造摘要:通过对沉降罐和洗涤罐的改造,提高液体石蜡的收率,降低尿素的消耗,改善柴油品质,降低能耗。
关键词:沉降罐、洗涤罐、液体石蜡1引言尿素脱蜡装置是1966年6月投产的,原设计加工能力是35000吨/年,主要产品为-35#、-50#军用坦克柴油,副产300#液体石蜡。
近年来由于市场的需求变化及装置的不断改造,例如取消沉降罐后只生产-35#坦克柴油和液体石蜡,并以液体石蜡为主要产品。
对络合反应、共沸、蒸馏等岗位的不断改进增大了处理量,而对沉降洗涤岗位并未做大的调整改变。
目前的洗涤罐制约着尿素装置的生产,主要表现为液体石蜡馏出口质量收率的降低,尿素、异丙醇的消耗增大,液蜡质量由于络合物在洗涤罐中停留时间短而容易使芳烃过大。
虽然近几年优化了操作使液蜡收率不断提高,物耗不断下降,但是还没有达到最佳的效果,还有潜力可挖,这就是进一步对沉降洗涤岗位的改进,解决制约装置生产的瓶颈问题。
对沉降洗涤岗位的改造方案有两个,其中一个较为简单,一个较为复杂。
2简单方案2.1简单方案就是只对沉降罐和洗涤罐本身进行改造目前尿素装置只使用洗涤罐,二沉降罐分为3段,生产方案只能是3段沉降,2段洗涤。
由于处理量的不断提高,显然目前的洗涤罐已经不适应当前和以后的生产需要。
当前最佳的方法是将闲置的沉降罐用上,将沉降罐和洗涤罐原来的3段改造成2个段,即洗涤罐2、段沉降罐2段。
这样改造后沉降洗涤岗位的总容积和有效容积都将增加一倍,达到572.4立方米和381.8立方米。
2.2改造后的沉降洗涤岗位变成1段沉降,2段洗涤,但是由于有效容积增大了一倍,络合物的沉降时间也增大了一倍,这样改造的好处有:2.2.1降低尿素的消耗由于有效容积的增加,使停留时间延长,使络合物在洗涤罐和沉降罐得到较为充分的沉降,经搅拌网的搅拌后,络合物和脱蜡油得到充分的沉降分离,脱蜡油中夹带的尿素和络合物旧会明显降低,在脱蜡油进入水洗塔后损失的尿素就会相应地减少,尿素消耗将降低。
某终端沉降罐改造及污泥干化技术应用

某终端沉降罐改造及污泥干化技术应用路 平 曲兆光 刘春雨 吴晓东(中海石油(中国)有限公司天津分公司渤海石油研究院 天津 300452)摘 要:针对某终端沉降罐的污泥沉积问题,制定沉降罐内安装内置式刮吸泥机的方案,避免含聚污油泥在沉降罐底部沉积,确保终端安全正常生产。
结合该终端污泥现状和新增的沉降罐排泥系统,对含聚污泥进行干化处理。
该方案可大幅度减少含聚污泥外运量,降低其处理费用,同时可回收污泥中的原油,获得良好的经济效益和社会效益。
关键词:沉降罐 刮吸泥机 内置式 含聚污泥 干化处理引言某终端现有4座沉降罐,其中一级和二级沉降罐各2座,单罐容积为5000m3,担负着终端来液的液-液分离、固-液分离及调节水量的重要作用。
近年来,由于注聚返出物的影响,终端来液在沉降罐内通过絮凝、分离、沉降产生的污泥量急剧增加。
大量污泥沉积在罐底不能排出,使沉降罐负担加重,严重影响终端工艺流程的处理效果。
此外,由于沉降罐内污泥无法及时排出,一部分污泥进入生产污水处理系统,造成污水除油罐和斜管除油罐中也出现大量的污油泥,影响生产污水处理效果。
针对某终端沉降罐的污泥沉积问题,制定沉降罐内安装内置式刮吸泥机的方案,避免含聚污泥在沉降罐底部沉积。
同时新增污泥干化设备,对含聚污泥进行干化处理[1]。
该方案可大幅度减少含聚污泥外运量,降低其处理费用,并将污水池内的油水进行有效的分离,分离出的油进入原油系统进行回收,分离出的水进入生产污水系统进行处理。
1 沉降罐改造为实现罐内污油泥自动排放,在沉降罐内增加内置式刮吸泥机,使污泥定期外排,避免在罐底部沉积[2]。
1.1 内置式刮吸泥机工作原理内置式刮吸泥机安装在5000m3沉降罐内中心配集水柱底部,驱动机构带动中心传动机构上的刮泥臂沿转动体作圆周运动,在液位压力差的作用下,刮泥板使淤积在罐内底部的污泥均匀的进入吸泥管内,通过设置在排泥管口的气动控制阀控制自动排出罐外[3]。
1.2 改造方案首先拆除沉降罐内部的构件,清除罐壁、罐底的结垢物,罐内表面重新进行防腐处理。
污水沉降罐收油工艺技术改造
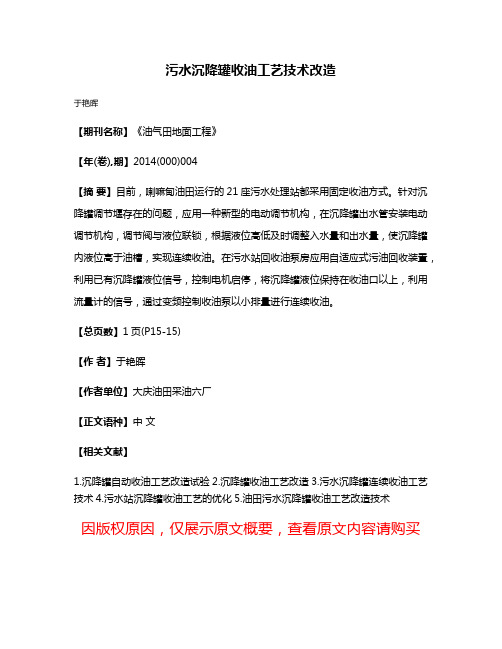
污水沉降罐收油工艺技术改造
于艳晖
【期刊名称】《油气田地面工程》
【年(卷),期】2014(000)004
【摘要】目前,喇嘛甸油田运行的21座污水处理站都采用固定收油方式。
针对沉降罐调节堰存在的问题,应用一种新型的电动调节机构,在沉降罐出水管安装电动调节机构,调节阀与液位联锁,根据液位高低及时调整入水量和出水量,使沉降罐内液位高于油槽,实现连续收油。
在污水站回收油泵房应用自适应式污油回收装置,利用已有沉降罐液位信号,控制电机启停,将沉降罐液位保持在收油口以上,利用流量计的信号,通过变频控制收油泵以小排量进行连续收油。
【总页数】1页(P15-15)
【作者】于艳晖
【作者单位】大庆油田采油六厂
【正文语种】中文
【相关文献】
1.沉降罐自动收油工艺改造试验
2.沉降罐收油工艺改造
3.污水沉降罐连续收油工艺技术
4.污水站沉降罐收油工艺的优化
5.油田污水沉降罐收油工艺改造技术
因版权原因,仅展示原文概要,查看原文内容请购买。
污水收油装置的改进
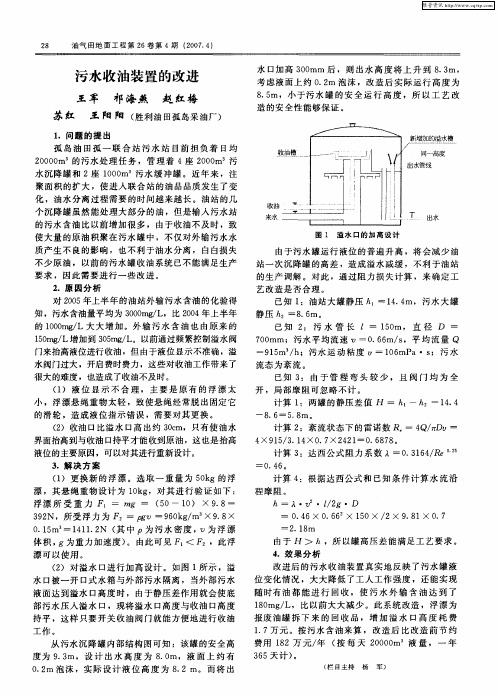
2 .原 因 分 析
图 l 溢 水 口的 加 高 设 计
对 20 05年上半 年的油 站外输 污水含油 的化验 得 知 ,污水含油量平均 为 30 m / 00 g L,比 20 年上半 年 04 的 10 m / 00 g L大 大 增加 。外输 污 水 含 油也 由原来 的 10 g L增加到 35 g L 5m / 0m / 。以前通过频繁控制溢水 阀 门来 抬高液位进行收油 ,但 由于液 位显示不准确 ,溢 水阀门过大 ,开启费时费力 ,这些对收油工作带来 了 很大 的难度 ,也造成 了收油不及 时。 ( ) 液 位 显 示 不 合 理 ,主 要是 原有 的浮 漂 太 1 小 ,浮 漂悬绳 重物 太轻 ,致使 悬绳 经常脱 出 固定 它 的滑轮 ,造成 液位 指示 错误 ,需要对其 更换 。 ()收油 口比溢水 口高 出约 3c 2 0m,只有使油 水 界面抬高到与收油 口持平才能收到原油 ,这也是抬高 液位 的主要原因,可 以对其进行重新设计 。
孤 岛 油 田孤一 联 合 站 污水 站 目前 担 负 着 日均 2 0 0 的污 水处 理任 务 ,管 理 着 4座 2 0 m。 0 0 m。 0 0 污 水沉 降罐 和 2座 1 0 m。 0 0 污水 缓 冲罐 。近年 来 ,注 聚面积 的扩 大 ,使进入 联合 站 的油 品品质 发生 了变
70 0 mm;污 水平 均流速 一0 6 m/ ,平 均流 量 Q .6 s
一
9 5 / ;污水运 动 粘 度 u一 1 6 a・ ;污水 1 m。 h 0 mP s
流态 为紊 流 。 已知 3 由于 管 程 弯 头 较 少 ,且 阀 门 均 为 全 : 开 ,局 部摩 阻可忽 略不计 。
华北油田采油四厂琥珀营作业区:改造沉降罐收油流程降本增效

华北油田采油四厂琥珀营作业区:改造沉降罐收油流程降本增效
作者:暂无
来源:《国企管理·石油经理人》 2018年第9期
8 月23 日,琥珀营作业区泉241站沉降罐收油流程改造一周以来运行平稳可靠,基本实现了沉降罐收油值守人员从有到无、原油污染风险从有到无、液下泵运行维护费用从有到无、收油车使用费用从有到无。
据悉,该沉降罐收油流程自投运一周以来,平均收油量从原来的每小时3 立方米提升至10 立方米。
预计年提高收油量30 吨,节电1000 度,减少设备维修成本1.5 万元、罐车使用成本1.2 万元。
文/ 图马剑彭红韩丹丹。
污水沉降罐连续收油工艺技术
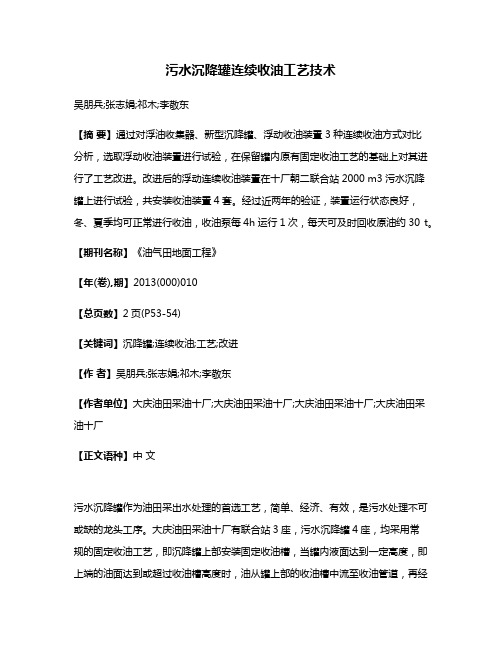
污水沉降罐连续收油工艺技术吴朋兵;张志娟;祁木;李敬东【摘要】通过对浮油收集器、新型沉降罐、浮动收油装置3种连续收油方式对比分析,选取浮动收油装置进行试验,在保留罐内原有固定收油工艺的基础上对其进行了工艺改进。
改进后的浮动连续收油装置在十厂朝二联合站2000 m3污水沉降罐上进行试验,共安装收油装置4套。
经过近两年的验证,装置运行状态良好,冬、夏季均可正常进行收油,收油泵每4h运行1次,每天可及时回收原油约30 t。
【期刊名称】《油气田地面工程》【年(卷),期】2013(000)010【总页数】2页(P53-54)【关键词】沉降罐;连续收油;工艺;改进【作者】吴朋兵;张志娟;祁木;李敬东【作者单位】大庆油田采油十厂;大庆油田采油十厂;大庆油田采油十厂;大庆油田采油十厂【正文语种】中文污水沉降罐作为油田采出水处理的首选工艺,简单、经济、有效,是污水处理不可或缺的龙头工序。
大庆油田采油十厂有联合站3座,污水沉降罐4座,均采用常规的固定收油工艺,即沉降罐上部安装固定收油槽,当罐内液面达到一定高度,即上端的油面达到或超过收油槽高度时,油从罐上部的收油槽中流至收油管道,再经收油泵输至站内脱水系统进行下一步处理。
1 常规固定收油工艺现状固定收油方式只有在油液面高于收油槽时才能实现收油;当液面低于收油槽时,不能进行收油。
另外,冬季气温低,容易在油层上部形成一层硬盖,收油困难。
这种工艺不能连续收油的主要原因是由于油层较浅,而水的黏度低于上层油的黏度,只要油水界面稍稍高出收油槽边缘,水首先流入收油槽,使收油时带入较多的水,增加了循环处理的水量,相当于增加了沉降罐的负荷,降低了沉降罐的处理效率。
若定期收油,由于上层油停留在罐内时间较长,易形成老化油,对脱水、污水系统处理产生影响。
2 收油工艺为改善污水沉降罐的收油工艺,实现连续收油,使油在罐内停留时间减短,降低污水系统来水含油指标,主要采用3种收油工艺。
2.1 浮油收集器收油浮油收集器收油工作原理即采用一条漂浮于液面的柔韧性很好的环形亲油性的循环转动收油管,将沉降罐内的浮油沾到收油管上,沾满油的管子转回浮油收集器中,凭借陶瓷刮片将收油管上的油刮下来。
沉降罐加气浮提高除油效率试验研究

沉降罐加气浮提高除油效率试验研究
[摘要]应用模拟的沉降罐及聚南八放水站已建7000m3沉降罐在油田开展了沉降罐、气浮工艺联用的小试及现场试验研究,在沉降罐进口增加管式反应器,对沉降罐内部附件进行改造,高压溶气水进入管式反应器和沉降罐后,与原水充分混合,释放出的微气泡与原水中的油形成气浮体,并在分离区迅速上浮,可提高沉降罐油水分离效果,降低沉降出水含油量。
初步确定了影响沉降罐加气浮除油效果的主要因素及各主要工艺参数的推荐数值,在21%回流比,溶气压力为0.5-0.6MPa条件下,罐内穿孔管和罐外管式反应器同时加溶气,处理效果最佳。
由于除油率提高,需加大收油力度。
该试验为下一步推广应用提供了思路及经验。
【主题词】沉降;气浮;污水;除油效率;含油量;回流比;管式反应器。
- 1、下载文档前请自行甄别文档内容的完整性,平台不提供额外的编辑、内容补充、找答案等附加服务。
- 2、"仅部分预览"的文档,不可在线预览部分如存在完整性等问题,可反馈申请退款(可完整预览的文档不适用该条件!)。
- 3、如文档侵犯您的权益,请联系客服反馈,我们会尽快为您处理(人工客服工作时间:9:00-18:30)。
试验·研究/Testing &
Research
1现状
污水站沉降罐的收油情况是减轻过滤段处理负
荷的关键,同时也是制约着油田采出水处理效果的一个重要因素,它的处理效果主要是受沉降罐的收油、排泥、加药等情况影响。
第七采油厂目前虽然各站实施了连续收油工艺改造,但是由于沉降罐所采用的收油结构为固定式,需要在罐顶用调节堰控制液位达到收油槽高度时,才能收到污油,实际生产中无法实现有效收油,易导致罐上部浮油表面出现严重老化和结蜡,影响后端电脱水器正常运行。
而且沉降罐内表层的污油会在冬季气温低的情况下形成油盖,使罐内污油老化进而形成硬油盖,使罐内的污油无法回收,油层厚度的不断增加,罐内污水的有效沉降空间不断减少,从而使污水的有效沉降时间缩短,对污水处理效果产生较大影响。
目前,油田沉降罐顶部污油的回收方法有沉降罐收油槽收油工艺、浮油收集器收油工艺和浮动连续收油工艺等(表1),传统的收油工艺均为间歇式运行,冬季罐内污油易老化进而形成硬油盖,影响处理水质。
第七采油厂主要采用的是收油槽收油工艺。
为了更好地解决收油槽收油工艺调节堰生锈,使用年限短,沉降罐浮油回收问题,开展自动收油工艺试验。
2
沉降罐自动收油工艺
2.1
试验区概况
葡二联1#污水处理站目前有500m 3污水沉降罐
4座,包括:2座一次沉降罐φ7.6m×13.4m;2座二次沉降罐φ8m×11.4m,均采用调节堰控制液位(常规固定收油工艺)收油工艺,调节堰平均7—8年需维修更换,而且由于容器上部收油进入油系统后,受硫化物影响电脱水器频繁垮电场,影响油系统平稳运行,所以试验前没有实现有效收油。
罐内污油高度超过0.7m,导致出水含油量较高,站内出水平稳达标难度较大,试验前的收油工艺采用沉降罐收油槽收油工艺,流程见图1。
有收油泵2台,型号为DY6-25×3、流量为6m 3/h、扬程为75m,运一
备一。
图1试验前沉降罐收油槽收油工艺
2.2
自动收油工艺原理
自动收油工艺主要是利用PLC 系统或二次仪
表,对沉降罐内液位和界面进行测定,并与设定的值进行比较,根据差值通过PLC 系统程序调节或二
次表的报警动作对电动阀或变频器发出相应的指令,使其动作,从而使液位和界面稳定在一定范围内,自控原理见图2。
沉降罐自动收油工艺改造试验
付艳玲(大庆油田有限责任公司第七采油厂)
摘要:普通的污水沉降罐收油工艺易导致罐上部浮油表面出现严重老化和结蜡,影响后续工艺设备的正常运行,无法实现有效收油。
而且冬季温度低的时候容易形成硬油盖,无法收油。
试验一种新型的利用沉降罐出口电动阀与液位计联锁控制,使沉降罐液位保持在收油与溢流之间的高度范围内的沉降罐自动收油工艺,实现连续自动收油并降低了传统收油工艺改造费用。
并根据其试验情况进行跟踪分析,确定其实用性,并提出改进的建议。
关键词:沉降罐;自动收油;油盖;连锁控制;跨电场DOI :10.3969/j.issn.2095-1493.2018.01.004
作者简介:付艳玲,工程师,2005年毕业于西南石油学院(电气工程及其自动化专业),从事供配电及自控规划设计工作,E-mail:fuyanling@,地址:黑龙江省大庆市大同区第七采油厂规划设计研究所,163517。
付艳玲:沉降罐自动收油工艺改造试验第8卷第1期
利用一次沉降罐已建的液位计,接入新建的仪表控制箱,用于罐内液位高度的测定,一次沉降罐的出水管安装电动阀1个,与罐液位高度进行联锁,根据设定液位值与罐内测定的液面高度进行对比,通过PID 调节,控制沉降罐出口电动阀的动作,确保沉降罐内液位平稳控制在收油高度,保证收油时不至于收水过多[1-2]。
在一次沉降罐内加装液位界面传感器1套,用于罐内油水界面高度的测定,通过与一次沉降罐液位的对比,确定油层厚度,收油泵安装变频器1台,液位界面传感器二次显示后进入新建变频柜,与收油泵变频形成闭环控制。
在PLC 系统(或智能
数字调节仪)设定油水界面的高度范围(界面传感器和液位计两者之间的差值就是油层厚度),并通过数字量输出点控制收油泵启、停,油水界面低于设定下限值时自动启动收油泵,油水界面高于设定上限值时关闭收油泵,这样油厚始终保持在PLC 系统或二次调节仪表设定的较小的范围内[3-5],达到自动收油的目的,工艺流程见图3。
2.3
现场试验
现场工艺改造完成后,根据一次沉降罐的收油槽高度12.4m,首次设定上、下限报警液位并试验运行(表2)。
首次运行时,沉降罐油厚数据经测为70.6cm,
表1
不同收油工艺介绍及优缺点对比
回收方法
沉降罐收油槽收油工艺
浮油收集器收油工艺
浮动连续收油工艺
工艺简介
在沉降罐上端安装固定收油槽,通过人工调节堰控制液位至收油高度,经收油泵回收至站内油系统通过漂浮于沉降罐液面上循环转动收油管,将浮油沾到收油管上,带回浮油收集器中,凭借陶瓷刮片将收油管上的油刮下来,经收油泵回收至油系统浮在沉降罐液面上的收油槽随着液面上升或下降,回转臂在收油槽的带动下做上、下回转运动,污油经过收油盘、回转机构、收油泵回收至油系统
优点工艺简单,投资低可实现不同液位的连续收油,回收的污油含水较低同上
缺点
达到收油槽所要求的高度时,才能收到污油,收油罐缓冲能力较小,调节堰容易生锈,并且每次收油均需工人上罐顶控制调节堰,存在安全隐患
浮油收集器收油管在连续运行中有自缠绕现象发生
前期改造费用高,只适用于罐内设施少,对于在
用沉降罐内附件较多的容器不适用
图2
液位自控原理
图3自动收油试验工艺流程
试验·研究/Testing &
Research
收油泵工频运行,通过泵房看窗观察,发现收油泵看窗所收均为污油,收油泵运行8.25h 后,观察收油泵看窗所收污油颜色变淡,上罐顶检测罐顶油厚不到10cm。
通过持续观察、检测罐顶油厚,当液位显示为12.4m 时收油槽口未露出液面,经过多次调整、试验,最终确定二次仪表的高低液位报警值(表2)。
表2
二次仪表报警液位设定值
单位:m
控制项目
一次沉降罐液位一次沉降罐油水界面
上限报警液位
首次设定值
12.6012.40
校正后设定值12.5512.35
下限报警液位首次设定值12.4012.30
校正后设定值12.3512.25
2.4收油泵优化运行试验
为确保原油脱水系统平稳运行、水质有效提
升,对收油泵运行周期及排量等参数进行了优化,摸索总结沉降罐自动收油工艺科学的运行管理方式。
根据对沉降罐油层厚度的跟踪分析发现,沉降罐每天油厚增加5.42cm (图4)。
图4沉降罐罐顶油厚随时间变化曲线
经过一年多的运行发现,根据来液含油量的不同,收油泵5天左右自动启泵一次,泵工频运行时间为2—3h,污油厚度适中保持在0.3m 以下。
取样检测对比收油前后污水水质,含油量由58mg/L 降低至44.6mg/L ;悬浮物由126mg/L 降低至42.7mg/L。
为了进一步优化收油泵的运行,减少收油泵自动启动次数,开展按照沉降罐罐顶油层厚度不超过0.8m 运行试验,经过9—11月试验,收油泵15天左右自动启泵一次,泵工频运行时间为8h,取样检测对比收油前后污水水质,含油量由92mg/L 降低至53.2mg/L;悬浮物由54mg/L 降低至35.6mg/L。
3结论
1)常规收油槽收油工艺费用主要包括罐内清
淤、调节堰成本及安装,费用为10.9万元,自动收油工艺主要包括变频器、一次表、二次仪表箱和电动阀等,费用为8.7万元,节省了2.2万元。
2)经过运行发现沉降罐自动收油工艺能实现罐顶污油的有效回收,有利于降低污水的含油量,同时自动收油工艺不需要工人上下罐人工操作,减少了工人的劳动强度,解决了调节堰容易生锈,使用年限短的问题。
3)采取沉降罐出口电动阀与液位计联锁控制,使沉降罐液位保持在收油与溢流之间的高度范围内的沉降罐自动收油工艺,可实现根据油层厚度自动启、停收油泵,达到自动收油的目的,改变了传统收油工艺依靠人工上罐顶操作调节堰、来液不稳定时液位和油水界面不易控制等问题,具有很好的推广前景。
4)沉降罐自动收油工艺依赖于一次仪表的测量准确度,静压式液位计较磁性浮子液位计测量稳定性更好,但是存在一定误差,为方便在沉降罐内安装油水界面仪,建议浮球式油水界面仪的高度宜在2.5m 以内。
5)建议结合沉降罐清淤、罐体维修改造,增设沉降罐出口电动调节阀及油水界面仪;结合节能改造,增设收油泵变频控制。
参考文献:
[1]赵丽红.污水站沉降罐收油工艺的优化[J].油气田地面工程,2010(3):38-39.
[2]杨博域,王绍斌,高永贤.改造收油流程提高污水处理站的收油效率[J].中国石油和化工,2011(6):46-48.
[3]彭柏群,吴迪,宋辉.污油回收预处理装置的研制和现场应用[J].大庆石油学院学报,2010(2):89-91.
[4]周彩红,姜慧韬,李春娟,等.油田污水沉降罐收油工艺改造技术[J].油气田地面工程,2004(5):28-29.
[5]吴朋兵,张志娟,袜木,等.污水沉降罐连续收油工艺技术[J].油气田地面工程,2013(10):53-54.
收稿日期
2017-10-05
(编辑
贾洪来)。