品质异常处理流程ppt课件
合集下载
制程品质异常分析与处理图文
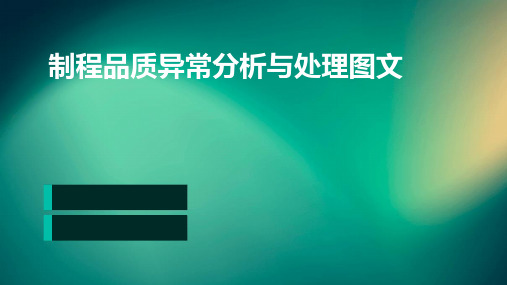
通过数据收集、分析和可视化等手段,实现了对制程品质异常的快速响应和有效处理。
提升产品品质
通过对异常数据的深入挖掘和分析,找出了影响产品品质的关键因素,并针对性地进行优化和改进,从而提 升了产品品质。
提高生产效率
通过实时监测和预警系统,及时发现并处理制程中的品质异常,减少了停机时间和废品率,提高了生产效率。
制程能力评估与提升
定期评估制程能力,识别潜在的制程风险,采取相应的措 施提升制程能力,确保产品符合设计要求。
员工培训与技能提升
加强员工品质意识培训,提高员工对品质标准的认识和执 行力;同时,针对关键岗位进行技能培训,确保员工具备 相应的操作技能。
纠正措施实施及跟踪
异常现象记录与分析
详细记录制程中出现的品质异常现象,包括 时间、地点、产品批次、异常表现等,以便 进行后续的分析和处理。
制程概述
涉及多个复杂工序,包括原材料准备、加工、 组装、测试和包装等环节。
品质要求
产品需满足严格的质量标准,如尺寸精度、电气性能和可靠性等。
问题诊断过程展示
异常现象描述
在某批次产品中,发现部分元器件尺寸超差,导致无法正常组装。
数据收集与分析
收集异常批次产品的生产数据、原材料信息和制程记录,运用统计 技术对数据进行深入分析,找出潜在原因。
制程品质异常分析与处理图文
目 录
• 制程品质异常概述 • 制程品质异常分析方法 • 制程品质异常处理策略 • 案例分析:制程品质异常处理实践 • 工具与方法在制程品质异常处理中应用 • 总结与展望
01 制程品质异常概述
定义与分类
定义
制程品质异常是指在产品制造过程中 出现的与正常生产状态不符的、影响 产品质量的现象。
提升产品品质
通过对异常数据的深入挖掘和分析,找出了影响产品品质的关键因素,并针对性地进行优化和改进,从而提 升了产品品质。
提高生产效率
通过实时监测和预警系统,及时发现并处理制程中的品质异常,减少了停机时间和废品率,提高了生产效率。
制程能力评估与提升
定期评估制程能力,识别潜在的制程风险,采取相应的措 施提升制程能力,确保产品符合设计要求。
员工培训与技能提升
加强员工品质意识培训,提高员工对品质标准的认识和执 行力;同时,针对关键岗位进行技能培训,确保员工具备 相应的操作技能。
纠正措施实施及跟踪
异常现象记录与分析
详细记录制程中出现的品质异常现象,包括 时间、地点、产品批次、异常表现等,以便 进行后续的分析和处理。
制程概述
涉及多个复杂工序,包括原材料准备、加工、 组装、测试和包装等环节。
品质要求
产品需满足严格的质量标准,如尺寸精度、电气性能和可靠性等。
问题诊断过程展示
异常现象描述
在某批次产品中,发现部分元器件尺寸超差,导致无法正常组装。
数据收集与分析
收集异常批次产品的生产数据、原材料信息和制程记录,运用统计 技术对数据进行深入分析,找出潜在原因。
制程品质异常分析与处理图文
目 录
• 制程品质异常概述 • 制程品质异常分析方法 • 制程品质异常处理策略 • 案例分析:制程品质异常处理实践 • 工具与方法在制程品质异常处理中应用 • 总结与展望
01 制程品质异常概述
定义与分类
定义
制程品质异常是指在产品制造过程中 出现的与正常生产状态不符的、影响 产品质量的现象。
异常处理PPT课件

是
规程是否得 到遵守?
否
形式不可用
操作人员理解有 困难
不适合实际操作
或不能产生好的 结果
重写规程以 符合当前的 工作方法
使用图标或数据 等重写规程以易
于理解
从技术角度重新 对规程进行回顾
规程是否得
是
到遵守?
否
工作条件不
使用规程或复杂设
适合
备时容易出错
改善工作条 件
改善工作方法,引 入傻瓜型设备装置
开始
发现和报告异常
采取纠正性行动来消除症 状
异常处理流程
制定对策 执行对策 跟踪对策的执行
记录异常
跟踪对策的有效性
确定异常的本质或根本原因
4
对发生的异常进行阶段性回 顾以检测长期性问题
确定项目/年度目标来对 长期性问题进行优先性
排序
使用PDCA来执行项目/ 年度行动计划
结束
确定根本原因
原因
X
症状
• 停机时间超过20分钟; • 所有事故\事件; • 断货超过5 %;
• 损耗超过xx %;
• 盘点差异高于2%。
当系统得到实施且发生的异常减少时,触发条件的标准可 以变得“更为严格”!
开始
发现和报告异常
1
采取纠正性行动来消除症状
记录异常
确定异常的本质或根本原因
异常处理流程
制定对策 执行对策
跟踪对策的执行
采取纠正性行动来消除症状
2
记录异常
跟踪对策的执行 跟踪对策的有效性
确定异常的本质或根本原因
对发生的异常进行阶段性回 顾以检测长期性问题
确定项目/年度目标来对 长期性问题进行优先性
排序
使用PDCA来执行项目/ 年度行动计划
规程是否得 到遵守?
否
形式不可用
操作人员理解有 困难
不适合实际操作
或不能产生好的 结果
重写规程以 符合当前的 工作方法
使用图标或数据 等重写规程以易
于理解
从技术角度重新 对规程进行回顾
规程是否得
是
到遵守?
否
工作条件不
使用规程或复杂设
适合
备时容易出错
改善工作条 件
改善工作方法,引 入傻瓜型设备装置
开始
发现和报告异常
采取纠正性行动来消除症 状
异常处理流程
制定对策 执行对策 跟踪对策的执行
记录异常
跟踪对策的有效性
确定异常的本质或根本原因
4
对发生的异常进行阶段性回 顾以检测长期性问题
确定项目/年度目标来对 长期性问题进行优先性
排序
使用PDCA来执行项目/ 年度行动计划
结束
确定根本原因
原因
X
症状
• 停机时间超过20分钟; • 所有事故\事件; • 断货超过5 %;
• 损耗超过xx %;
• 盘点差异高于2%。
当系统得到实施且发生的异常减少时,触发条件的标准可 以变得“更为严格”!
开始
发现和报告异常
1
采取纠正性行动来消除症状
记录异常
确定异常的本质或根本原因
异常处理流程
制定对策 执行对策
跟踪对策的执行
采取纠正性行动来消除症状
2
记录异常
跟踪对策的执行 跟踪对策的有效性
确定异常的本质或根本原因
对发生的异常进行阶段性回 顾以检测长期性问题
确定项目/年度目标来对 长期性问题进行优先性
排序
使用PDCA来执行项目/ 年度行动计划
异常处理及操作流程 PPT

5、鱼骨图分析法:从机器、操作员、环境、物料、 方法、管理入手。
1
人
机
身体疲倦 工装夹具定位不准
料
来件不良
无培训上岗 操作不规范
设计缺陷 装置失灵
标识不清 发放错误
未遵循作业标准
安全装置缺损
表面油污
简单枯燥的 重复动作
操作方法有隐患
无标准化 指导书
法
有害的加 工工序
杂乱有噪音 有害气体 高温
环
分配不合理 处理不当
料计划而导致之异常。
4、各部门影响生产问题的原因
采购部:
(1) 采购下单太迟,导 致断料。
(2) 进料不全导致缺 料。
(3) 进料品质不合 格。
(4) 厂商未进货或进错 物料。
(5) 未下单采购。 (6)其他因采购业务疏
忽所致之异常。
物管组:
(1)料帐错误 (2) 物料查找时间太
长。
(3) 未及时点收厂商进 料。
管理
异常原因分析
6、异常发生后操作步骤
6.1、检查现场现物,判断重要性,迅速处理。 6.2、联络关系部署 6.3、迅速确定,进行后工程品质确认; 6.4、进行对象范围把握和不良品排除(不良品分类识别,良品选出等) 6.5、问题严重时,向上司报告——等待指示; 6.6 、追查不合格品源头; 6.7 、联络前后工程,品管部; 6.8 、对发生工程进行对策处置; 6.9 、在此加合格标志,控制流出; 6.10、在合格品到来前点检,选出不合格品; 6.11 、工程内剩余工件及库存品也全数检选出; 6.12 、不合格品必需进行识别; 6.13 、修复是遵守规定。 ; 6.14、排除原因,启动设备; 6.15、研究对策和在发生防止,再次明确指导各工程异常是什么。
品质异常分析与预防(超完善)PPT幻灯片课件

讨论: *制程因素
1.工程当天主导会议,检讨相关改善对策
a) 制程管制应有哪些文件? 2.针对风险批物料,立即进行隔离及处理
*材料因素
b) 首件确认应该由谁进行? 1.SQE当天立刻反馈供应商并主导与供应商的会议,检讨相关改善对策
2.针对风险批物料,立即进行隔离及处理(含供应商库存)
c) IPQC应如何进行巡检?11来自四、品质异常相关处理流程
Dept. Step.
1
2
一、何为品质
品质quality 一组固有特性满足要求的程度 注:“固有的”就是指在某事或某物中本来就有的 尤其是那种永久的特性,如:尺寸,某些物理特性,化学特性 合格-满足要求 不合格-不满足要求 缺陷-未满足与预期或规定用途有关的要求
品质就是顾客的满足…… 我们公司的顾客…… ……各大公司 ……下个工段
• 纠正措施 为消除已发行的不合格或其他不期望情况的原因所采取的措施
• 预防措施 为消除潜在不合格或其他潜在不期望的原因所采取的措施
• 返工 为使不合格产品符合要求而对其采取的措施
• 返修 为使不合格产品满足预期用途而对其所采取的措施
• 降级 为使不合格产品符合不同于原有的要求而对其采取的措施
• 报废 为避免不合格产品原有的预期用途而对其所采取的措施
IQC 报表
Y
整理与记录
进料验收单
入库
N
特采
管制重点
输出 (窗体/记录)
根据需求,在“进料(货)验 收单”上注明特急件,急件 进料验收单 或平件
确认进料数据及出货报告
等项目 进料验收单
依据检验规范,客户特殊要
求等执行检验
开 NMRB
退货
进料验收单
管理实务培训之品质异常处理办法
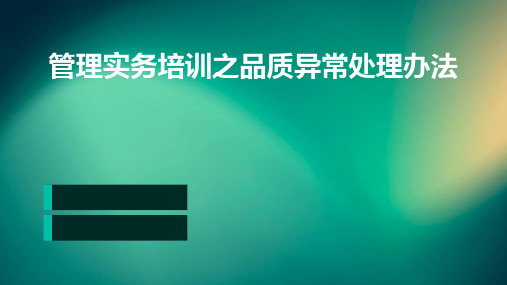
实施纠正措施
效果评估
对纠正措施的实施效果进行评估,确 保问题得到有效解决。同时,对相关 人员进行培训,避免类似问题再次发 生。
相关部门按照纠正措施的要求,积极 落实改进工作,并对实施过程进行监 控。
04 品质异常预防措施
品质管理体系的完善
制定严格的质量标准和检验流程, 确保产品符合要求。
建立完善的品质管理体系,包括 供应商管理、生产过程控制、成
感谢您的观看
对品质数据进行统计分析,找出 问题根源,制定改进措施。
跟踪改进措施的实施情况,确保 问题得到有效解决,防止再次发
生。
05 品质异常处理案例分析
案例一:来料品质异常处理
总结词
及时反馈、科学评估、有效沟通
及时反馈
一旦发现来料品质异常,应立即向供 应商反馈,确保问题得到及时解决。
科学评估
对异常物料进行科学评估,确定是否 可以用于生产或是否需要退货。
品质异常的诊断流程
收集数据
通过各种途径收集与品质异常 相关的数据,如生产记录、质
量检测报告等。
分析数据
对收集到的数据进行整理和分 析,找出品质异常的规律和原 因。
现场调查
对生产现场进行调查,了解生 产流程和设备状况,确认品质 异常的原因。
制定改进措施
根据分析结果和现场调查情况 ,制定相应的改进措施,如优 化工艺流程、改善设备状况等
品检验等环节。
定期对品质管理体系进行审查和 更新,以适应市场需求和公司发
展。
员工培训与意识提升
对员工进行质量管理 培训,提高其质量意 识和技能水平。
鼓励员工参与质量管 理,建立质量奖励机 制,表彰优秀员工。
定期开展质量意识教 育活动,加强员工对 品质重要性的认识。
不合格品( HSF)处理流程图ppt课件

工厂内部出现环 境管理物质不合格
负责单位 品保/仓库/制造
库存品的处理
材料向供应商退货替代 合格品/成品直接报废
发生异常
原材料或部件中含 有禁止使用物质 异常连络书的发行
★报告品保部经理/总经理 ★与客户进行联络并报告 ★处理时需注意模向展开其 它料号与追踪上一批物料质 量状况
原因调查
工厂内部混入
纠正预防措施单的发行
ppt课件完整
5
4.0 权责
• 4.1 MRB﹙物料审查委员会﹚:负责不合格 品处理之审核,以决定不合格品之挑选、 返修、重工、退回供应商或予以裁定报废 或特采。
• 4.2不合格品发现/发生部门:负责对不合 格品做适当的识别、隔离及通知。
• 4.3品保:负责产品检验判定及标示区隔, 通知相关单位处置。
从客户反馈环境管理物质不合格信息工厂内部出现环境管理物质不合格供应商提供环境管理物质不合格材料报告品保部经理总经理与客户进行联络并报告处理时需注意模向展开其它料号与追踪上一批物料质量状况原因调查库存品的处理原材料或部件中含有禁止使用物质工厂内部混入异常工序纠正预防措施单的发行异常连络书的发行供应商材料向供应商退货替代合格品成品直接报废不合格对策处理确认会议库存品处理的确认防止再次发生的确认向其它部门或工序的水平推广模向展开标准化对策实施批量产品的进货出货发生异常品保仓库制造负责单位品保品保资料制造供应商业务品保仓库制造品保制造9ppt课件53重工作业流程图此流程不适用于hsf不合格处理流程挑选重工作业重工作业申请批退报废作业流程包装入库保存作业不良状况所费工时记录不合格批产生mrb审查可否重工检验业务
不合格批产生
MRB审查 可否挑选?
NG
报废作业申请
OK
异常处理及操作流程ppt课件

3、遇到异常不要慌张,检查现场现物,判断重要迅速处理,处乱不惊。
4、制定应急措施和再发防止措施。 应急措施具体作法:①明确发生异常时的群体。②将异常现象迅速通知有 关单位,并要求其参与处理。③对过程采取处置措施,使异常现象暂时控 制而不再恶化。④将异常群体选别,对不良品修理,调整或对人员作教育 训练。⑤将处置内容记入异常报告单。 再发防止具体作法:①检讨相关标准(ⅰ、是否有标准?标准明确了没 有?答案若是否定,则增订标准。ⅱ、是否遵守标准?若遵守标准而结果 又不好,则修改标准。ⅲ、标准了解了没有?若不了解则须培训标准。) ②对策愚巧化:若牵涉到要小心,注意、加强等因数,则尽量考虑使用防、 呆的方法。
操作方法有隐患 无标准化 指导书
法
环
管理
6、异常发生后操作步骤
6.1、检查现场现物,判断重要性,迅速处理。 6.2、联络关系部署 6.3、迅速确定,进行后工程品质确认; 6.4、进行对象范围把握和不良品排除(不良品分类识别,良品选出等) 6.5、问题严重时,向上司报告——等待指示; 6.6 、追查不合格品源头; 6.7 、联络前后工程,品管部; 6.8 、对发生工程进行对策处置; 6.9 、在此加合格标志,控制流出; 6.10、在合格品到来前点检,选出不合格品; 6.11 、工程内剩余工件及库存品也全数检选出; 6.12 、不合格品必需进行识别; 6.13 、修复是遵守规定。 ; 6.14、排除原因,启动设备; 6.15、研究对策和在发生防止,再次明确指导各工程异常是什么。
应急措施
如遇重大问题或需相关部门共同协商解 决的,由生管主导召开现场会。
应急措施由生管主导,生产、品管共同确认后 方可实施,重大品质问题延误交期的需计划部 确认。根据实际情况决定是否停产或转
异常处理流程PPT课件( 24页)

二.客戶端QE人員復判狀況
• 按排QE人員至客戶端復判,若不良按排人員sorting客戶端的 庫存;(須依據不良D/C,單一SKU進行sorting )
• 三.不良品廠內分析
• QE/PE——復判分析不良品; • QE——根據分析結果進行處理。
一.接到客訴反應
掌握時效 a.先與客戶確定問題 b.處理時間確認 c.人力安排
2 客訴異常處理流程
客戶端製程問題
告知SQE此問題Heisei不會造成此問題的發生。
2 客訴異常處理流程
HEISEI製程漏失問題
1.安排人員進行重工客戶端的庫存及厰内的庫存; 2.清查客戶端及廠內庫存回報主管 ; 3.如須重工須與PE確認重工手法、重工批量與物料確認待重工 數量; 4.如須重工須與PE確認重工手法、重工批量與物料確認待重工 數量; 5.如需安排人員外出重工﹐須安排車輛接送重工人員; 6.每日重工結果須填寫Sorting單回報給主管.
•
14、给自己一份坚强,擦干眼泪;给自己一份自信,不卑不亢;给自己一份洒脱,悠然前行。轻轻品,静静藏。为了看阳光,我来到这世上;为了与阳光同行,我笑对忧伤。
•
15、总不能流血就喊痛,怕黑就开灯,想念就联系,疲惫就放空,被孤立就讨好,脆弱就想家,不要被现在而蒙蔽双眼,终究是要长大,最漆黑的那段路终要自己走完。
召集所有相關單位進行開會 (目的預防後期再發生同樣的問題)。
2 客訴異常處理流程
原材材料問題 要求廠商人員進行重工客戶端的庫存及厰
内的庫存,並提出後續的改善措施及改善後 的標示。
要求PE製作管控圖片發于相關部門,並進 行協助廠商管控。
The End
•
5、世上最美好的事是:我已经长大,父母还未老;我有能力报答,父母仍然健康。
• 按排QE人員至客戶端復判,若不良按排人員sorting客戶端的 庫存;(須依據不良D/C,單一SKU進行sorting )
• 三.不良品廠內分析
• QE/PE——復判分析不良品; • QE——根據分析結果進行處理。
一.接到客訴反應
掌握時效 a.先與客戶確定問題 b.處理時間確認 c.人力安排
2 客訴異常處理流程
客戶端製程問題
告知SQE此問題Heisei不會造成此問題的發生。
2 客訴異常處理流程
HEISEI製程漏失問題
1.安排人員進行重工客戶端的庫存及厰内的庫存; 2.清查客戶端及廠內庫存回報主管 ; 3.如須重工須與PE確認重工手法、重工批量與物料確認待重工 數量; 4.如須重工須與PE確認重工手法、重工批量與物料確認待重工 數量; 5.如需安排人員外出重工﹐須安排車輛接送重工人員; 6.每日重工結果須填寫Sorting單回報給主管.
•
14、给自己一份坚强,擦干眼泪;给自己一份自信,不卑不亢;给自己一份洒脱,悠然前行。轻轻品,静静藏。为了看阳光,我来到这世上;为了与阳光同行,我笑对忧伤。
•
15、总不能流血就喊痛,怕黑就开灯,想念就联系,疲惫就放空,被孤立就讨好,脆弱就想家,不要被现在而蒙蔽双眼,终究是要长大,最漆黑的那段路终要自己走完。
召集所有相關單位進行開會 (目的預防後期再發生同樣的問題)。
2 客訴異常處理流程
原材材料問題 要求廠商人員進行重工客戶端的庫存及厰
内的庫存,並提出後續的改善措施及改善後 的標示。
要求PE製作管控圖片發于相關部門,並進 行協助廠商管控。
The End
•
5、世上最美好的事是:我已经长大,父母还未老;我有能力报答,父母仍然健康。
品质异常处理流程.ppt课件
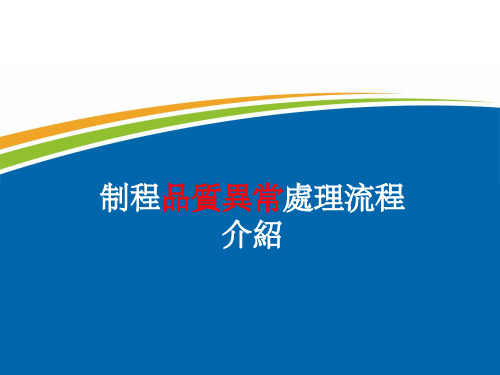
勇气、反馈、认真、责任
客户投诉或抱怨;
TEST Proces
严重功能不良;
Full Process
异常纠正措施实施后经确认无效时 ; 生产员工未按照作业指导书作业,或员工作业时违反操作规程经现
场纠正无效时 ; 经品管部评估制程中存在品质隐患并可能导致返工或停线的风险 。
2.异常产品判定状态:
报废 重工 挑选 特采
制程品質異常處理流程 介紹
客户第一 | 阳光沟通 | 团队协作 | 拥抱变化 | 学习成长
目录
1
基本概念
2 异常处理程序介绍
3
责任判定原则
4
PDCA工具
5
问题讨论
一. 基本概念
1.定义: 在制造过程中因一个或一组变异因子造
成产品质量由原先的受控状态突变成失控 状态。 异常:非正常
2.分類: 人員 物料 設備/工具 工藝/方法 環境 測量 設計
P 4、针对主要原因,制定措施计划
D 5、执行、实施计划 C 6、检查计划执行结果
7、总结成功经验,制定相应标准 A
8、把未解决或新出现问题转入下一个PDCA循 环
主要办法 排列图、直方图、控制图 因果图 排列图,相关图 回答“5W1H” 为什么制定该措施(Why)? 达到什么目标(What)? 在何处执行(Where)? 由谁负责完成(Who)? 什么时间完成(When)? 如何完成(How)?
我踢!
结果3:大家共赢。
Yea!
四. PDCA工具
1. 起源:
PDCA又称“戴明环”,它起源于20世纪20年 代,有“统计质量控制之父”之称的美国著名的 统计学家沃特·阿曼德·休哈特(Walter A. Shewhart)在当时引入了“计划-执行-检查 (Plan-Do-See)”的概念, 戴明后将休哈特的 PDS循环进一步发展成为:计划-执行-检查-处理 (Plan-Do-Check-Action)。
客户投诉或抱怨;
TEST Proces
严重功能不良;
Full Process
异常纠正措施实施后经确认无效时 ; 生产员工未按照作业指导书作业,或员工作业时违反操作规程经现
场纠正无效时 ; 经品管部评估制程中存在品质隐患并可能导致返工或停线的风险 。
2.异常产品判定状态:
报废 重工 挑选 特采
制程品質異常處理流程 介紹
客户第一 | 阳光沟通 | 团队协作 | 拥抱变化 | 学习成长
目录
1
基本概念
2 异常处理程序介绍
3
责任判定原则
4
PDCA工具
5
问题讨论
一. 基本概念
1.定义: 在制造过程中因一个或一组变异因子造
成产品质量由原先的受控状态突变成失控 状态。 异常:非正常
2.分類: 人員 物料 設備/工具 工藝/方法 環境 測量 設計
P 4、针对主要原因,制定措施计划
D 5、执行、实施计划 C 6、检查计划执行结果
7、总结成功经验,制定相应标准 A
8、把未解决或新出现问题转入下一个PDCA循 环
主要办法 排列图、直方图、控制图 因果图 排列图,相关图 回答“5W1H” 为什么制定该措施(Why)? 达到什么目标(What)? 在何处执行(Where)? 由谁负责完成(Who)? 什么时间完成(When)? 如何完成(How)?
我踢!
结果3:大家共赢。
Yea!
四. PDCA工具
1. 起源:
PDCA又称“戴明环”,它起源于20世纪20年 代,有“统计质量控制之父”之称的美国著名的 统计学家沃特·阿曼德·休哈特(Walter A. Shewhart)在当时引入了“计划-执行-检查 (Plan-Do-See)”的概念, 戴明后将休哈特的 PDS循环进一步发展成为:计划-执行-检查-处理 (Plan-Do-Check-Action)。
《品质异常改善方案》课件

环境因素
总结词
温度、湿度、清洁度等不符合 要求
详细描述
生产现场的温度、湿度、清洁 度等环境因素超出允许范围, 影响产品质量和设备正常运行 。
总结词
环境安全保护措施不到位
详细描述
缺乏有效的环境安全保护措施 ,导致生产过程中出现环境污
染和职业健康问题。
03
品质异常改善方案
优化原材料管理
总结词
确保原材料质量稳定
设备故障
总结词
设备老化、维护不当、操作失误
01
总结词
设备配置不合理
03
总结词
缺乏对设备的预防性维护
05
02
详细描述
设备长期使用导致性能下降,未及时进行保 养和维护,操作人员对设备操作不熟悉或误 操作等。
04
详细描述
设备配置不足或过于复杂,无法满足 生产需求或影响生产效率。
06
详细描述
未制定有效的设备维护计划,对设备的检查和 保养不及时。
案例三:某产品性能不稳定问题
总结词
材料与工艺匹配问题
详细描述
产品在生产过程中,由于选用的材料与生产工艺不匹配,导致产品 性能不稳定。性能不稳定可能引发安全事故或产品质量纠纷。
解决方案
加强材料入库检验,确保材料质量;加强工艺试验和研究,优化工艺 参数;建立材料与工艺匹配的数据库,为生产提供科学依据。
员工操作失误
总结词
员工培训不足、操作不熟练、工作态 度不认真
详细描述
新员工未经过充分培训,对操作规程 不熟悉,老员工过于自信或疏忽大意 ,导致操作失误。
总结词
缺乏有效的激励机制和考核制度
详细描述
员工工作积极性不高,对于产品质量 和生产效率缺乏足够的重视。
- 1、下载文档前请自行甄别文档内容的完整性,平台不提供额外的编辑、内容补充、找答案等附加服务。
- 2、"仅部分预览"的文档,不可在线预览部分如存在完整性等问题,可反馈申请退款(可完整预览的文档不适用该条件!)。
- 3、如文档侵犯您的权益,请联系客服反馈,我们会尽快为您处理(人工客服工作时间:9:00-18:30)。
品保: 监控管理从来料、生产组装和成品出货后的品质状况;并对材料厂商进行管理。 品质异常出现后,及时确认处理存疑品(含原材、产品和客户端产品部分)。
工程: 设计满足客户需求的产品,并负责送样品的制作和确认。 制程和客退品质异常时,先行判定不良原因;并与相关责任单位确认、改善。 负责召开异常检讨会议,与品保、制造、生管和采购等部门讨论具体事宜。
物料: 按生产工单要求,将生产所需的材料运送指定的生产单位。 接到异常通知时,协助将异常物料清除产线,并放置在隔离区域。
2
各职能部门工作定义
制造: 安排适合的岗位作业人员和设备,进行生产;确保生产品品质。 出现异常状况及时提报相关责任部门进行改善。 协助工程和品保对相关材料的试做验证、及新产品的试样生产。
11
二、MRB流程
流程图
进料异常 (急用)
制程异常 成品、半成品
库存品异常
MRB会议
退回 供应商
特采
重工
挑选
报废
12
讲解完毕,谢谢!
13
4.客退品质异常
客户投诉、客退
客服确认 投诉不良
工程会议检讨
客退品重工方案
责任单位 对策改善
改善报告
重工作业
厂商改善
OK
返回客户
NG 报废
制程改善
8
二、MRB流程
MRB:公司内不合格或待处理之异常材料、半成品、成品能依规定程序处理。
相关定义 特采:未确认或不合格品,经一定之申请与核准,予以特采使用,称之特采。 挑选:对判定不合格之原材料、半成品及成品,对不合格项目予以100%全
检,以区分良品与不良品,称之挑选。 重工:对部份不良品可用重新加工或修之方式,予以修理使其成为合乎规格
之产品,称之重工。 报废:对判定不合格之原材料、半成品及成品无法重新且又不符合乎特采之原
则,经一定之程序予以销毁及除帐。 退货:已知材料无法依前4项处理时,则退回供应商处理。
9
二、MRB流程
MRB成员包括:品保/物料/采购/生管/客服/工程/制造。
3
一、品质异常分类
1.进料品质异常 2.制程品质异常 3.RE品质异常 4.客退品质异常
4
一、异常分类
1.进料品质异常
供应商来料 NG
IQC检验 OK
入库
特别状况 如订单生产紧急,来料且无功能不良(或产线能拦下该功能不良), 经工程与品保评估可接受风险,可进入MRB流程处理。
5
一、异常分类
2.制程品质异常
定。
10
二、MRB流程
MRB运作模式: 1.经MRB判为退回供应商,则由IQC在待退产品上加以“拒收”标签标识、隔
离;采购通知供应商取回。 2.经MRB判为特采时,采购提出特采申请,工程提供品质风险评估报告和临时
对策供各部门参考;QA贴上特采标签以示区别。特采物料上线生产时, IPQC需核对物料的使用状况。 3.经MRB判为重工时,生管开出重工单,安排重工所需的人力、场地和设备等。 工程定义制作重工作业指导书,并负责重工人员作业的指导。IPQC监督、 抽验重工作业状况及重工品的品质判定。 4.经MRB判定为待报废时,则集中由物料人员置于待报废区。 5.经过1-4项处理过之材料或产品,需再正常检验程序判定OK后,再流入下一 工站。
品质异常处理流程简述
1
各职能部门工作定义
业务: 与客户联系确认所需产品规格型号、交期、价格等需求信息。 出现重大客诉(客退)时,与客户商谈相关损失费用问题。
采购: 根据客户订单需求,及时购买生产所需原材料。 原材料出现品质异常时,协助将异常原料退回供应商;并扣除相关费用。
生管: 根据现有生产所需的原材料数量和人力设备使用状况,安排生产。 出现品质异常,需对厂内半品或成品重工时;安排人力和设备进行重工作业。
物料发料 NG
IPQC/制造核对
OK 制程生产
制程改善
IPQC/FQC/ 制造检查
NG 工程验证判定
OK
入库
责任单位对 策改善
供应商改善
6
一、异常分类
3.RE品质异常
功能测试验证
测试OK 入库 出货
测试NG
暂停生产/出货
工程判定及 会议讨论
全部报废
NG 重工挑选
OK 入库/出货
报废
7
一、异常分类
MRB会议召开: 1.进料之急料部份由采购负责召开临时MRB会议,正常进料部份可由IQC
整理资料,视实际需要不定期召开MRB会议。 2.品质异常时,半成品、成品之急需部份由生管召开MRB会议,工程提供评估
品质风险报告和临时对策供各部门参考,不急时则按工程和品保判定处理。 3.库存材料则由物料或生管召开MRB会议。 4. MRB之主席由各负责召开会议主管担任,品质之最终裁定由品质高级主管确
工程: 设计满足客户需求的产品,并负责送样品的制作和确认。 制程和客退品质异常时,先行判定不良原因;并与相关责任单位确认、改善。 负责召开异常检讨会议,与品保、制造、生管和采购等部门讨论具体事宜。
物料: 按生产工单要求,将生产所需的材料运送指定的生产单位。 接到异常通知时,协助将异常物料清除产线,并放置在隔离区域。
2
各职能部门工作定义
制造: 安排适合的岗位作业人员和设备,进行生产;确保生产品品质。 出现异常状况及时提报相关责任部门进行改善。 协助工程和品保对相关材料的试做验证、及新产品的试样生产。
11
二、MRB流程
流程图
进料异常 (急用)
制程异常 成品、半成品
库存品异常
MRB会议
退回 供应商
特采
重工
挑选
报废
12
讲解完毕,谢谢!
13
4.客退品质异常
客户投诉、客退
客服确认 投诉不良
工程会议检讨
客退品重工方案
责任单位 对策改善
改善报告
重工作业
厂商改善
OK
返回客户
NG 报废
制程改善
8
二、MRB流程
MRB:公司内不合格或待处理之异常材料、半成品、成品能依规定程序处理。
相关定义 特采:未确认或不合格品,经一定之申请与核准,予以特采使用,称之特采。 挑选:对判定不合格之原材料、半成品及成品,对不合格项目予以100%全
检,以区分良品与不良品,称之挑选。 重工:对部份不良品可用重新加工或修之方式,予以修理使其成为合乎规格
之产品,称之重工。 报废:对判定不合格之原材料、半成品及成品无法重新且又不符合乎特采之原
则,经一定之程序予以销毁及除帐。 退货:已知材料无法依前4项处理时,则退回供应商处理。
9
二、MRB流程
MRB成员包括:品保/物料/采购/生管/客服/工程/制造。
3
一、品质异常分类
1.进料品质异常 2.制程品质异常 3.RE品质异常 4.客退品质异常
4
一、异常分类
1.进料品质异常
供应商来料 NG
IQC检验 OK
入库
特别状况 如订单生产紧急,来料且无功能不良(或产线能拦下该功能不良), 经工程与品保评估可接受风险,可进入MRB流程处理。
5
一、异常分类
2.制程品质异常
定。
10
二、MRB流程
MRB运作模式: 1.经MRB判为退回供应商,则由IQC在待退产品上加以“拒收”标签标识、隔
离;采购通知供应商取回。 2.经MRB判为特采时,采购提出特采申请,工程提供品质风险评估报告和临时
对策供各部门参考;QA贴上特采标签以示区别。特采物料上线生产时, IPQC需核对物料的使用状况。 3.经MRB判为重工时,生管开出重工单,安排重工所需的人力、场地和设备等。 工程定义制作重工作业指导书,并负责重工人员作业的指导。IPQC监督、 抽验重工作业状况及重工品的品质判定。 4.经MRB判定为待报废时,则集中由物料人员置于待报废区。 5.经过1-4项处理过之材料或产品,需再正常检验程序判定OK后,再流入下一 工站。
品质异常处理流程简述
1
各职能部门工作定义
业务: 与客户联系确认所需产品规格型号、交期、价格等需求信息。 出现重大客诉(客退)时,与客户商谈相关损失费用问题。
采购: 根据客户订单需求,及时购买生产所需原材料。 原材料出现品质异常时,协助将异常原料退回供应商;并扣除相关费用。
生管: 根据现有生产所需的原材料数量和人力设备使用状况,安排生产。 出现品质异常,需对厂内半品或成品重工时;安排人力和设备进行重工作业。
物料发料 NG
IPQC/制造核对
OK 制程生产
制程改善
IPQC/FQC/ 制造检查
NG 工程验证判定
OK
入库
责任单位对 策改善
供应商改善
6
一、异常分类
3.RE品质异常
功能测试验证
测试OK 入库 出货
测试NG
暂停生产/出货
工程判定及 会议讨论
全部报废
NG 重工挑选
OK 入库/出货
报废
7
一、异常分类
MRB会议召开: 1.进料之急料部份由采购负责召开临时MRB会议,正常进料部份可由IQC
整理资料,视实际需要不定期召开MRB会议。 2.品质异常时,半成品、成品之急需部份由生管召开MRB会议,工程提供评估
品质风险报告和临时对策供各部门参考,不急时则按工程和品保判定处理。 3.库存材料则由物料或生管召开MRB会议。 4. MRB之主席由各负责召开会议主管担任,品质之最终裁定由品质高级主管确