冲模试模报告
试模总结报告
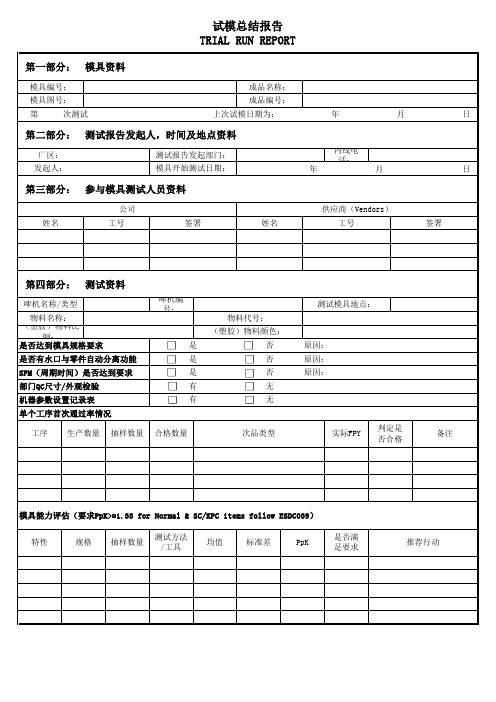
第
年
月
日
年
月
日
公司
供应商(Vendors)
姓名
是否满足要求
推荐行动
模具能力评估(要求PpK>=1.33 for Normal & SC/KPC items follow ESDC039)次品类型
模具资料
试模总结报告TRIAL RUN REPORT
测试报告发起人,时间及地点资料
第二部分:第一部分:第四部分:第三部分:参与模具测试人员资料
测试资料
特性
规格
抽样数量
测试方法/工具
均值
标准差
PpK
单个工序首次通过率情况工序
生产数量
抽样数量
合格数量
实际FPY
判定是否合格
备注
SPM(周期时间)是否达到要求是否原因:
部门QC尺寸/外观检验有无机器参数设置记录表有
无
(塑胶)物料比
例:
(塑胶)物料颜色:是否达到模具规格要求
是否原因:是否有水口与零件自动分离功能是否原因:啤机名称/类型啤机编号:
测试模具地点:
物料名称:物料代号:工号
签署
姓名
工号
签署
厂区:测试报告发起部门:内线电话:
发起人:
模具开始测试日期:
模具编号:成品名称:模具图号:成品编号:
次测试
上次试模日期为:。
冲压模具试模报告(一)

冲压模具试模报告(一)引言概述:冲压模具试模报告(一)是对某冲压模具进行试模的结果和总结。
本报告将对试模目的、试模过程、试模结果以及对模具性能进行分析和总结。
正文内容:一、试模目的1. 确定冲压模具的设计是否满足产品质量要求2. 评估冲压模具的使用寿命和稳定性3. 发现并解决试模过程中可能出现的问题4. 收集试模数据,为后续的模具调试提供参考二、试模过程1. 准备工作a. 检查模具和设备的完整性和稳定性b. 准备试模所需的材料和工具2. 调整模具参数a. 确定合适的模具开口间距和闭合力b. 调整下模和上模的位置和角度3. 进行试模a. 安装模具并调整好位置b. 将试模材料置于适当位置c. 进行模具闭合和冲压过程4. 观察和记录a. 观察冲压过程中的变形和裂纹情况b. 记录每次试模的参数和结果5. 修正和再试a. 根据试模结果,进行必要的修正和调整b. 进行再次试模,直至达到预期的结果三、试模结果分析1. 产品质量a. 观察产品外观是否符合要求b. 测量关键尺寸的准确性和一致性2. 模具性能a. 检查模具的磨损和损坏情况b. 评估模具的使用寿命和稳定性3. 问题和改进a. 分析试模过程中出现的问题和难点b. 提出可能的改进方案和建议四、试模结果总结1. 模具设计是否满足产品要求2. 试模过程中发现的问题和解决方案3. 模具的使用寿命和稳定性评估4. 对模具参数的优化和调整建议5. 提供后续模具调试的参考数据结论:通过本次冲压模具试模,我们得出了以下结论:1. 冲压模具的设计能够满足产品的质量要求。
2. 在试模过程中,发现了一些问题并进行了相应的修正和改进。
3. 模具的使用寿命和稳定性良好,符合预期。
4. 对模具参数进行了优化和调整,并提出了进一步的改进建议。
5. 试模数据可以为后续模具调试和优化提供有力参考。
试模报告样板
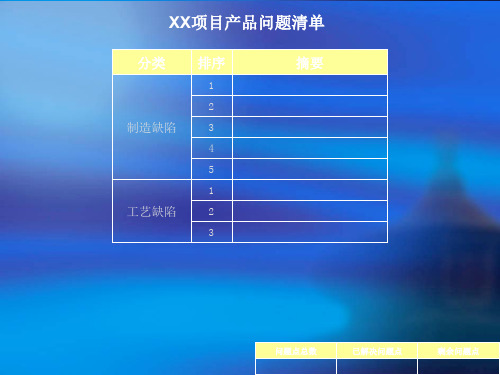
零件号 产品工程师
图片描述
问题点描述 问题点
审核:
状态 责任人
严重度 编制日期
措施&现状
序号
措施
1
2
3
结果跟踪
序号 提出日期 计划关闭日期/关闭日期
状 态
1
2
3
批准:
零件名称 试模时间
XX项目试制计划
零件号 试模单位
方案一
客户要求数量 模具收缩率
原材料调试安排
试制数量 数据版本
方案二
方案三
方案四
零件名称 试模时间
序号 1 2 3
XX项目试制计划
零件号 试模单位
原材料厂家
客户要求数量 模具收缩率
试模材料信息
试制数量 数据版本
材料牌号
材料收缩率
备注
样件试制参数信息
序号 1 2 3
参考密度 边梁参考重量 X向整体尺寸
细节尺寸
注塑工艺参数
备注
零件名称 试模时间
序号 1 2 3 4
序号 1 2 3
图片描述
核心参数
状态 责任人
严重度 编制日期
试制相关信息
序号 提出日期 状态 T0
T1
T2
1 2 3
试制结论
会签:
结果跟踪
序号 提出日期 计划关闭日期/关闭日期
状 态
1
2
3
编制:
审核:
批准:
XX项目产品问题清单
项目名称 零件名
图片描述
模具供应商 零件号
试制阶段
问题点描述 序号
1 2 3 4
状态
严重度 问题点
供应商联系人 产品工程师
试模总结报告范文(3篇)
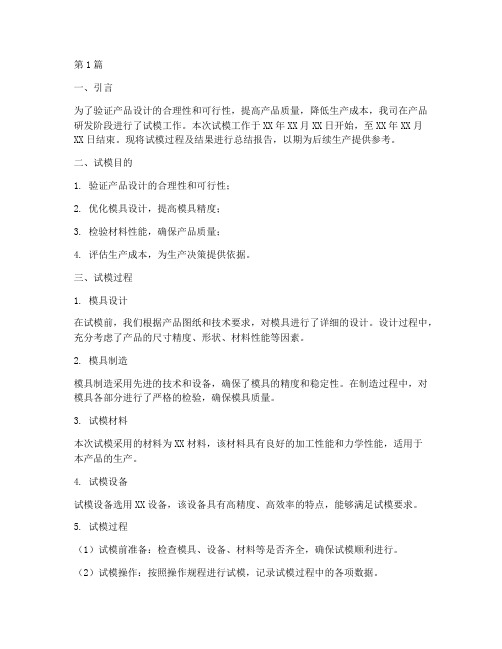
第1篇一、引言为了验证产品设计的合理性和可行性,提高产品质量,降低生产成本,我司在产品研发阶段进行了试模工作。
本次试模工作于XX年XX月XX日开始,至XX年XX月XX日结束。
现将试模过程及结果进行总结报告,以期为后续生产提供参考。
二、试模目的1. 验证产品设计的合理性和可行性;2. 优化模具设计,提高模具精度;3. 检验材料性能,确保产品质量;4. 评估生产成本,为生产决策提供依据。
三、试模过程1. 模具设计在试模前,我们根据产品图纸和技术要求,对模具进行了详细的设计。
设计过程中,充分考虑了产品的尺寸精度、形状、材料性能等因素。
2. 模具制造模具制造采用先进的技术和设备,确保了模具的精度和稳定性。
在制造过程中,对模具各部分进行了严格的检验,确保模具质量。
3. 试模材料本次试模采用的材料为XX材料,该材料具有良好的加工性能和力学性能,适用于本产品的生产。
4. 试模设备试模设备选用XX设备,该设备具有高精度、高效率的特点,能够满足试模要求。
5. 试模过程(1)试模前准备:检查模具、设备、材料等是否齐全,确保试模顺利进行。
(2)试模操作:按照操作规程进行试模,记录试模过程中的各项数据。
(3)试模结果分析:对试模结果进行分析,评估产品性能和模具质量。
四、试模结果及分析1. 产品性能(1)尺寸精度:产品尺寸精度达到设计要求,符合国家标准。
(2)形状:产品形状符合设计图纸,无明显变形。
(3)表面质量:产品表面光滑,无明显划痕、气泡等缺陷。
2. 模具质量(1)模具精度:模具精度达到设计要求,无明显磨损。
(2)模具稳定性:模具在试模过程中运行稳定,无异常现象。
3. 材料性能(1)力学性能:材料力学性能符合设计要求,具有较好的强度和韧性。
(2)加工性能:材料加工性能良好,易于加工。
4. 生产成本(1)模具成本:模具成本合理,符合预算。
(2)材料成本:材料成本合理,符合预算。
五、结论1. 产品设计合理,可行性高。
2. 模具设计精度高,稳定性好。
模具试模报告范文

模具试模报告范文一、试模目的本次试模旨在验证模具的设计是否符合要求,检测模具的结构是否合理,并评估模具的性能与质量。
通过试模可以发现模具的弱点以及需要改进的地方,为后续的模具制造和使用提供参考。
二、试模内容1.材料选择:本次试模选用XX材料,该材料具有良好的机械性能和加工性能,常用于模具制造。
2.模具设计:本次试模采用XX模具设计方案,该方案经过多次优化和分析,力求达到最佳的模具结构。
3.试模设备:本次试模采用XX注塑机进行模具试模,该注塑机具有高精度和高稳定性。
4.试模过程:在试模过程中,根据注塑工艺要求设置注射温度、注射压力、注射速度等参数,并根据试模的需要进行模具调整和修正。
三、试模结果1.外观质量:试模结果显示,注塑件外观质量良好,无明显的瑕疵和缺陷。
2.尺寸精度:通过对试模注塑件进行测量,发现其尺寸精度达到设计要求,各个尺寸尺角均符合标准。
3.模具性能:试模过程中,模具的运行稳定,没有出现卡模、粘模等问题。
模具的开模力和射出压力良好,满足注塑工艺的要求。
4.模具寿命:经过一定的试模次数,模具仍保持良好的使用状态,暂未出现磨损和损坏的情况。
需要继续进行更长时间的试模来评估模具的寿命。
四、问题与改进1.模具结构:在试模过程中,发现模具的结构存在一定的不合理之处,例如一些细小的零件容易变形和破损,需要进一步优化设计。
2.模具冷却系统:试模过程中发现模具的冷却系统存在不均匀冷却的情况,需要进一步调整冷却通道和增加冷却设备。
3.模具材料选择:试模结果显示,模具材料具有一定的磨损性,需要考虑更换耐磨性更好的材料。
五、总结与建议通过本次试模,验证了模具的设计和结构的合理性,评估了模具的性能和质量,并发现了问题和需要改进的地方。
建议在后续的模具制造中,根据试模结果进行相应的设计优化和改进,以提高模具的性能和使用寿命。
同时,建议在模具制造过程中更加注重材料的选择和加工工艺的控制,以提高模具的耐磨性和精度。
塑胶模具试模报告模版

塑胶模具试模报告模版一、试模背景模具试模是指在塑胶模具制造完成后,通过给模具注塑一定数量、一定条件下的塑料制品,来检验模具的质量和制造工艺的合理性。
二、试模目的通过试模,主要是为了检验模具的以下方面:1.检验模具的制造工艺是否合理,模具制造的步骤是否正确;2.检验模具的设计是否合理,模具是否具有良好的流道、冷却系统等结构;3.检验模具的尺寸精度、表面质量等指标是否符合要求。
三、试模步骤与过程1.准备工作:确定试模的塑料材料、颜色等,并准备好注塑机、模具和所需的辅助设备。
2.清洁模具:将模具从储存位置取出,清除模具表面的灰尘和杂质,保持模具的清洁。
3.加热模具:将模具安装到注塑机上,并根据材料的热处理温度要求,对模具进行加热处理。
4.调试注塑机:对注塑机进行相应的调整,包括温度、压力、速度等参数的设置。
5.注塑操作:将塑料颗粒加入注塑机的料斗中,通过加热和螺杆的转动,将塑料熔化并注入模具中。
6.冷却:在注塑后,通过冷却系统对模具中的塑料进行冷却,使其凝固定型。
7.脱模:待塑料冷却固化后,将模具从注塑机上取下,使用相应工具将塑料制品从模具中取出。
8.检验:对取出的塑料制品进行检验,包括尺寸精度、表面质量、重量等指标的检测,并记录相关数据。
四、试模结果与分析通过试模,根据检验结果可得出以下结论:1.模具的尺寸精度是否满足要求:根据尺寸测量数据进行分析,比较实测尺寸与预期尺寸之间的差异,判断模具的尺寸精度是否合格。
2.模具的表面质量:通过目测和触摸等方式对塑料制品的表面进行检验,判断模具的表面质量是否满足要求,如有划痕、气泡等缺陷。
3.模具的流道是否合理:通过检查塑料制品表面的流痕、熔接线等缺陷,判断模具的流道设计是否合理。
4.模具的冷却系统是否有效:通过塑料制品的冷却时间和温度检测,来评估模具的冷却系统是否能够有效降低塑料制品的冷却时间。
5.其他问题:对于试模过程中出现的其他问题,如塑料烧结、塑料流漏等,进行分析并提出改进措施。
冲压模具试模报告

冲压模具试模报告一、试模目的:本次试模旨在验证设计和制造的冲压模具的准确性和可行性,并对其进行性能和工艺参数的评估,以确保模具满足生产需要。
二、试模材料:本次试模选取了厚度为1mm的冷轧板材作为材料,以模拟实际冲压生产过程。
三、试模设备和工艺参数:试模设备主要包括冲床、模具和辅助工具等。
冲床型号为XXX,模具材料为优质合金钢。
工艺参数如下:1.预压力:40吨2.冲裁力:100吨3.下模时间:0.5s4.上模时间:0.3s5. 冲裁速度:200mm/s6.冲裁次数:100次四、试模过程及结果:1.模具安装:将模具安装到冲床上,并进行调整,确保模具正确对位和固定。
2.调试参数:根据工艺参数,调试冲床的参数,保证冲压过程的准确性和稳定性。
3.试模过程:根据试模工艺,依次进行预压、下模、上模和冲裁等操作,连续进行100次。
4.试模结果:经过100次试模,冲压件的尺寸和形状保持稳定,无明显的变形、裂纹和毛刺等缺陷,达到了预期的效果。
五、试模评估:1.模具准确性:试模结果表明,模具的准确性较高,冲压件的尺寸和形状符合设计要求,达到了预期的效果。
2.模具可行性:试模过程中,模具没有发生损坏或失效的情况,证明模具的可行性较高,具有较长的使用寿命。
3.工艺参数评估:根据试模结果和实际操作,工艺参数调整合理,冲裁速度和次数能够满足生产需求,并保持了一定的安全裕度。
4.试模总结:本次试模结果良好,模具准确性和可行性都得到了验证,工艺参数也基本符合要求,可以进行正式的生产。
六、改进措施:根据试模过程中发现的问题和需求1.优化模具结构设计,提高冲裁精度和效率。
2.加强模具材料的选取和热处理工艺,提高模具的硬度和耐磨性。
3.优化工艺参数,进一步提高生产效率和冲裁质量。
七、结论:通过本次试模,验证了设计和制造的冲压模具的准确性和可行性,证明了其在生产中的可靠性和稳定性。
同时,根据试模结果,提出了相应的改进措施,以进一步优化模具性能和生产效率。
冲压试模报告

冲压试模报告
报告名称:冲压试模报告
报告编号:XXXXX
报告日期:XXXX年XX月XX日
目的:
本次冲压试模报告的主要目的是对XXX产品进行冲压性能试验并得出结论,为下一步开发、生产和销售提供参考。
试验方法:
试验设备:XXX冲床
试验模具:XXX模具
材料:XXX材料
试验过程:
1.按照试验要求,准备好材料和模具。
2.将材料放入模具,放置在冲床上。
3.设置好冲击力、冲程等参数,进行试验。
4.重复以上步骤,记录各个试验数据。
试验结果:
通过冲压试模试验得出以下结论:
1.材料的拉伸性能良好,成型效果优秀。
2.模具的使用寿命长,可以进行批量生产。
3.在不同的参数设置下,试验结果有所差异,在实际生产中需要根据具体情况进行调整。
建议:
1.根据试验结果,推荐确保材料的质量,以保证产品的成型效果。
2.需要对模具进行维护保养,延长其使用寿命。
3.在实际生产中需要进行参数调整,以保证产品质量和生产效率。
结论:
本次冲压试模试验结果表明,所使用的材料和模具均可用于批量生产,但需要根据实际情况进行参数调整,提高生产效率和产品质量。
附:本次试验结果详细数据表格。
试验编号材料厚度(mm) 冲剪孔直径(mm) 冲床冲程(mm) 力矩(kN.m) 成型结果
1 2 20 40 5 良好
2 2.5 25 45 7 优秀
3 3 30 50 10 良好
4 3.
5 35 55 13 一般
5 4 40 60 1
6 良好
以上数据仅供参考,具体情况还需要根据实际生产情况进行调整。
模具测试报告(新)

模具测试报告(新)1. 测试概述该报告旨在对模具进行全面的测试和评估。
通过测试,我们能够了解模具的性能和质量,并为改进设计和制造过程提供参考意见。
2. 测试目的通过以下测试项目对模具进行评估:- 尺寸精度测试- 制造材料的强度测试- 使用寿命测试- 模具安全性测试3. 测试方法3.1 尺寸精度测试使用测量仪器对模具的关键尺寸进行测量,以评估模具的尺寸精度。
3.2 制造材料的强度测试对模具的制造材料进行强度测试,以确定其能否满足设计和使用要求。
3.3 使用寿命测试模具在实际使用条件下进行长时间的测试,以评估其使用寿命和稳定性。
3.4 模具安全性测试对模具的安全性进行测试,包括但不限于操作安全和使用安全等方面的评估。
4. 测试结果经过全面测试和评估,我们得出以下结论:- 模具的尺寸精度在设计要求范围内,满足使用要求。
- 制造材料的强度符合设计要求,具备良好的耐用性。
- 使用寿命测试表明,模具在正常使用条件下能够保持稳定性,并且能够满足预期的寿命要求。
- 模具的安全性符合相关标准与要求,操作安全,使用安全。
5. 改进建议基于以上测试结果,我们提出以下改进建议:- 进一步优化模具的制造工艺,以提高尺寸精度和质量稳定性。
- 持续关注模具的使用寿命,并进行及时的维护和保养。
- 加强模具的安全培训,确保操作人员正确使用模具且确保其安全。
以上是本次模具测试报告的内容。
如有任何疑问或需要进一步信息,请随时与我们联系。
感谢您对我们的支持与合作!。
冲压模具试模报告模板

冲压模具试模报告模板一、试模目的说明试模的目的是什么,例如:检查模具的制造质量、验证模具设计是否合理、确认模具的寿命等。
二、试模条件1.材料:说明试模所使用的材料种类和规格。
2.轧辊:说明轧辊的直径、柔度和工作状况。
3.润滑:说明使用的润滑剂种类和润滑方式。
三、试模装置1.模具尺寸:列出模具的尺寸和毛坯的尺寸。
2.模具材料:说明模具所使用的材料种类和规格。
3.模具结构:用文字或图纸简要描述模具的结构。
4.模具制造:说明模具的加工工艺和加工精度。
四、试模流程1.试模前准备:检查模具和轧辊是否清洁,调整模具的位置和固定方式。
2.试模过程:按照设定的参数进行模具试模,包括试模速度、模具的运动轨迹等。
3.试模结果:记录试模过程中的问题和异常情况,记录试模的周期和次数。
五、试模结果1.表面质量:对试模的毛坯进行外观检查,包括表面是否有划痕、变形等。
2.尺寸精度:对试模的成品进行尺寸测量,检查尺寸是否符合要求。
3.模具使用寿命:记录试模过程中模具的使用寿命,包括可以试模的次数和模具的损耗情况。
六、试模结论根据试模结果,给出对模具的评价和结论,例如:模具质量良好,符合设计要求,或者模具存在一些问题,需要进行修复或改进。
七、优化建议针对试模过程中出现的问题,提出合理的优化意见,包括调整模具的结构、改变模具材料、修改模具的加工工艺等。
八、试模总结对整个试模过程进行总结,包括试模的目的是否达到、试模结果的准确性和稳定性等方面进行评价。
以上是一个冲压模具试模报告的简单模板,可以根据实际情况进行修改和完善。
在撰写报告时,要注意提供足够的数据和细节,客观地记录试模过程和结果,以及给出合理的结论和建议。
试模检验报告

注塑模具试模检验报告单
客户名称: 试模日期: 试模材料: 型腔数: 产品名称: 试模次数:第 颜色: 产品重量: )后模( 克/模 次 产品编号: 注塑机型: 色粉编号: 水口重量: 克 模具编号: 记录人: 烘料时间.温度 成型周期 (h/℃) 秒 表单编号:
模具运水连接情况:前模(
说明:详细注塑工艺,见附件(注塑工艺卡)
)行位(
)(备注:机水、冷水、热水、热油)
说明:详细注塑工艺,见附件(注塑工艺卡) 试模问题点记录: 一、模具的问题: 1、 2、 3、 4、 5、 6、 7、 8、 9、 10、 11、 重要尺寸检测记录: 尺寸编号 要求尺寸 1、 2、 3、 4、 5、 6、 7、 8、 9、 10、 制表: 审核: 实际尺寸 检测结果 尺寸编号 11、 12、 13、 14、 15、 16、 17、 18、 19、 20、 报送: 要求尺寸 实际尺寸 检测结果 二、塑胶件的缺陷: 1、 2、 3、 4、 5、 6、 7、 8、 9、 10、 11、 三、试模时特别要注意的问题: 1、 2、 3、 4、 5、 6、 7、 8、 9、 10、 11、
试模总结报告模板
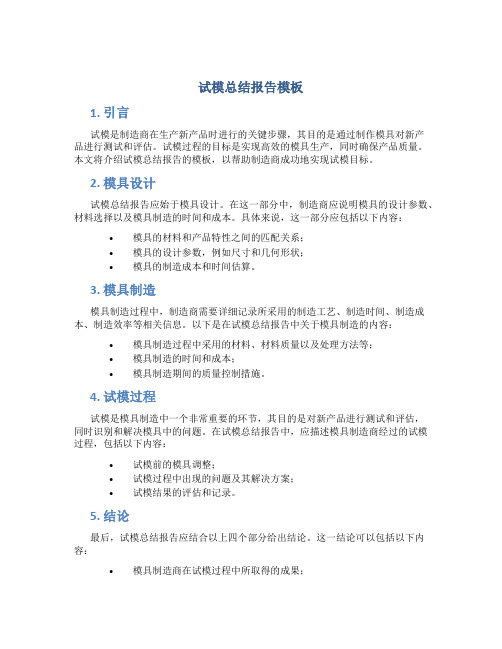
试模总结报告模板1. 引言试模是制造商在生产新产品时进行的关键步骤,其目的是通过制作模具对新产品进行测试和评估。
试模过程的目标是实现高效的模具生产,同时确保产品质量。
本文将介绍试模总结报告的模板,以帮助制造商成功地实现试模目标。
2. 模具设计试模总结报告应始于模具设计。
在这一部分中,制造商应说明模具的设计参数、材料选择以及模具制造的时间和成本。
具体来说,这一部分应包括以下内容:•模具的材料和产品特性之间的匹配关系;•模具的设计参数,例如尺寸和几何形状;•模具的制造成本和时间估算。
3. 模具制造模具制造过程中,制造商需要详细记录所采用的制造工艺、制造时间、制造成本、制造效率等相关信息。
以下是在试模总结报告中关于模具制造的内容:•模具制造过程中采用的材料、材料质量以及处理方法等;•模具制造的时间和成本;•模具制造期间的质量控制措施。
4. 试模过程试模是模具制造中一个非常重要的环节,其目的是对新产品进行测试和评估,同时识别和解决模具中的问题。
在试模总结报告中,应描述模具制造商经过的试模过程,包括以下内容:•试模前的模具调整;•试模过程中出现的问题及其解决方案;•试模结果的评估和记录。
5. 结论最后,试模总结报告应结合以上四个部分给出结论。
这一结论可以包括以下内容:•模具制造商在试模过程中所取得的成果;•发现的性能和生产问题;•解决问题和改进的方法建议。
6. 总结本文介绍了试模总结报告的模板,该模板包括模具设计、模具制造、试模过程和结论。
制造商可以根据该模板撰写试模总结报告,以便记录和评估新产品的性能和可靠性,并加以改进。
冲压模具试模报告docx(一)

冲压模具试模报告docx(一)引言概述:本文档是针对冲压模具试模的报告。
通过对冲压模具的试模过程进行详细记录和分析,旨在总结和评估试模的工作成果,以便为后续设计和改良提供参考。
本报告分为五个主要部分,包括试模前准备、试模过程、试模结果分析、问题与改进、总结。
一、试模前准备:1. 确定试模目标:明确设计和制造冲压模具的目的和要求。
2. 材料准备:选择合适的材料,并进行切割和加工。
3. 设计模具结构:绘制模具零件的设计图纸,包括上模、下模、导柱等。
4. 制造模具零件:根据设计图纸,制造模具的各个零件。
5. 装配模具:将各个零件进行组装,确保模具结构的稳固和准确。
二、试模过程:1. 模具调试:将装配完成的模具进行调试,确保各部件的运转正常。
2. 调整模具参数:根据试模需求,对模具参数进行调整,如切割力、模具间隙等。
3. 加工试样:使用模具对材料进行冲压,得到试样。
4. 数据记录:记录试模过程中的各项数据,如冲床力、冲头的行程等。
5. 完成试模:根据试模结果,评估试模的效果,并确定是否达到预期目标。
三、试模结果分析:1. 试样质量评估:根据试样的尺寸精度和表面质量等指标,评估试模的质量。
2. 试样强度分析:使用适当的测试设备对试样进行拉伸、压缩等力学性能测试。
3. 缺陷分析:对试样的表面和内部进行检查,发现和分析可能存在的缺陷。
4. 数据分析:对试模过程中的数据进行统计和分析,找出可能的问题和改进方向。
5. 结果总结:总结试模结果,评估模具设计和制造的优劣,为后续的工作提供依据。
四、问题与改进:1. 问题分析:根据试模结果分析,发现可能存在的问题和不足之处。
2. 解决方案:提出针对问题的具体改进方案,如调整模具参数、修改模具结构等。
3. 实施改进:采取实际操作措施,对模具进行改进和调整。
4. 再次试模:对改进后的模具进行再次试模,评估改进效果。
5. 结果总结:总结改进后的试模结果,判断改进措施的有效性。
冲压模具试模件检验报告(1)

文件编号: 第1版 第0次修改
冲压模具试模件检验报告
第1页 共1页
模具编号
机号
机型
试模时间
试模人
零件名称
批号
材料
、模具正面面向操作者,操作工操作方便
2、模具表面无污渍、杂物(已用模具清洗液清洗过) 换模 后模 3、模具合模正常,无松动、移位现象 具详 4、模具主体及镶件无破裂、挤压、碰伤现象
□ 模具有破裂、碰伤现象
(2)模具调试不到位: □ 合模不正常; □ 定位不准; □ 顶料、脫料不顺畅
(3)试冲样件不合格: □ 试冲样件的尺寸和形状不符合产品设计要求(见检验记录)
(4)机器设备不正常: □ 设备晃动; □ 冲压不正常
质检员:
试模人:
操作工:
车间主任:
备注:模具安装人员在试模时,必须通知检验员到现场检验试冲件、确认模具安装正确并填写本表
1
2
3
4
5
6
7
8
试模 后样 品详
情
综合判定 其他 已对操作工进行培训、指导, 操作工已掌握相关要领 综合判定:
判定: □OK □NO
□ 模具完好、模具安装正确、机器设备正常、试冲样件的尺寸和形状符合设计要求,可以开机生产
□ 经试模和检测冲压样件,发现存在不正常现象,不能开机生产,主要原因:
(1)模具不完好:
情 5、顶料、脫料顺畅,废料在下模中易漏落,不堵料、不跳料
6、经连续冲压多件产品测试,模具性能稳定
判定: □OK □NO 判定: □OK □NO 判定: □OK □NO 判定: □OK □NO 判定: □OK □NO 判定: □OK □NO
模具连续试冲_____件样品,检验结果如下:
冲压模具试模报告(二)2024

冲压模具试模报告(二)引言概述该报告是对冲压模具试模的进展和结果进行详细分析和总结。
本次试模主要包括了五个大点的内容,分别是模具设计和加工,材料选用和加工工艺,试模过程和参数调整,模具的性能评价以及存在的问题和改进建议。
下面将依次详细叙述每个大点的具体内容。
正文内容1. 模具设计和加工- 深入研究零件的结构特点和要求,根据加工过程分析进行模具设计。
- 采用CAD软件进行模具的三维设计,并完成模具零件的加工工艺规划。
- 利用CNC数控机床进行模具零件的加工,确保加工精度和质量。
2. 材料选用和加工工艺- 分析零件材料的力学性能和耐磨性等特点,选择适当的材料进行模具制作。
- 确定模具加工工艺,如热处理、精密磨削等,以提高模具的耐用性和寿命。
- 严格按照工艺参数进行材料的预处理和成型,确保模具的加工准确性和稳定性。
3. 试模过程和参数调整- 根据设计要求,进行试摸过程的排查和准备工作,如清洗模具、检查模具配件等。
- 逐步调整模具的出模速度、压力等参数,以达到理想的成型效果。
- 实时监测试模过程中的温度、压力等参数,并根据实际情况及时调整。
4. 模具的性能评价- 对试模后的零件进行尺寸和表面质量的评估,以确定模具的加工精度和性能。
- 进行模具的耐久性和寿命测试,以评估模具的使用寿命和维护要求。
- 根据试模结果,结合实际需求,对模具的性能进行综合评价。
5. 存在的问题和改进建议- 分析试模过程中出现的问题和不足,如产生毛刺、破损等,找出原因并提出改进措施。
- 针对模具的设计、材料选择、工艺等方面存在的问题,提出相应的改进建议。
- 总结本次试模的经验教训,为今后的模具设计和加工提供参考。
总结本次冲压模具试模工作取得了良好的成果,并对模具设计和加工提出了一系列具体的改进建议。
在今后的工作中,将进一步优化模具设计、提高加工工艺水平,以实现更好的模具性能和生产效益。
五金模具试模报告

质检意见
备注:
0.4×30
2044 98% 足)
试模具情况
1、模具完整; 2、模具能正常安装、使用,样品生产过程中无异常; 3、模具结构合理; 4、模具排样合理; 5、模具无标识(模具厂派人来处理)
技术意见
1、产品尺寸符合图纸要求; 2、产品无变形,无划痕,无毛刺; 3、产品表面无明显油污,无其他可视附着物; 4、VAWR性能待质检部实验验证; 5、附样品检测报告。
XXX有限公司
五金模具试产报告
模具编号: 对应产名称:
模具名称: 产品材质:
制模厂家: 带料/板料规格:
试模打样数量:
500 所需时间:
班组:
冲床吨位: 110T(高速冲床) 单模时间 1.3s
产能(PCS/8h):
产品重量kg:
0.000555 废料kg: 0.001575
成品率:
(从模具结构、使用可靠性、以及产品性能等方面指出模具的不足)
冲压实验报告

冲压模具结构分析一、实验目的了解典型冲模的种类(工序性质、组合方式等)、结构、工作原理以及各零件的名称和作用。
二、实验用具各种类型的冲压模具:级进模、复合模、单工序模等三、实验内容(1)从工序性质角度分析各类型的模具。
(2)从组合方式分析各类型的模具。
(3)分析模具的具体结构。
(4)分析模具的工作原理。
四、实验步骤(1)在教师的指导下,了解冲模类型和总体结构。
(2)对各种模具进行分析及讨论。
(3)画出模具结构原理图。
五、实验结果分析(1)每人独立(用直尺、圆规,按近似比例)绘制一副冲模结构草图。
(2)详细列出冲模上全部零件的名称、数量、用途及其所选用的材料;若选用的是标准件则列出标准代号。
(3)简要说明模具的工作过程。
冲模拆装一、实验目的(5分)(1)了解冲模的类型、结构、工作原理以及各零件的名称和作用。
(2)了解冲模各零件之间的装配关系及装配过程。
二、实验用具(5分)(1)手锤、橡胶锤、螺丝刀、活动扳手、老虎钳及内六角扳手等。
(2)不同类型的冲模5副。
三、实验内容(10分)(1)每组拆装1套有导柱的冲模。
拆装模具之前,应先分清可拆卸件和不可拆卸件,制定方案,提请实验教师审查同意后方可拆卸。
(2)一般冲模的导柱、导套以及用浇注或铆接方法固定的凸模等为不可拆卸件或不宜拆卸件。
(3)拆卸时一般首先将上下模分开,然后分别将上下模作紧固用的紧固螺钉拧松,再打出销钉,用拆卸工具将模具各板块拆分,最后从固定板中压出凸模、凸凹模等,达到可拆卸件全部分离。
四、实验步骤(5分)(1)在教师的指导下,了解冲模类型和总体结构。
(2)拆卸冲模,详细了解冲模每个零件的名称、结构和作用。
(3)重新装配冲模,进一步熟悉冲模的结构、工作原理及装配过程。
五、实验结果分析(75分)(1)每人独立(用直尺、圆规,按近似比例)绘制你所拆装的冲模结构草图。
(结构草图清晰,总体结构无原则性错误30)(2)详细列出冲模上全部零件的名称、数量、用途及其所选用的材料;若选用的是标准件则列出标准代号。
- 1、下载文档前请自行甄别文档内容的完整性,平台不提供额外的编辑、内容补充、找答案等附加服务。
- 2、"仅部分预览"的文档,不可在线预览部分如存在完整性等问题,可反馈申请退款(可完整预览的文档不适用该条件!)。
- 3、如文档侵犯您的权益,请联系客服反馈,我们会尽快为您处理(人工客服工作时间:9:00-18:30)。
模具类型
冲速
出模数
装模高度
材料型号
参数 材料实际厚
记录
度
材料利用率
材料产地 开料尺寸 试模所在地
材料批号 工件净重 机台型号
材料硬度 材料重量 机台编号
日时
年月日
工艺尺寸
描述顺序 □ 工模装组长□ 模:模□具□强容 度:闭□和□高足 度:设□备□匹太 具体 配:垫□□太 描述 伤:脱□模□退不 料:润□□滑畅 液:□□ 用
Q/**.R.QEP-23-09
浙江**电子有限公司
冲模试模报告
试模时间
基本 零件名称
状况 试模次数 模具型
腔尺寸:□
试模 具前 检查
资料准备:□产品图 其他:
模具名称
模具类别
□实验模 □生产模
模具试模原因 模具组长
从 月 日 时至 月
工程师 □定位销□ 装模架 □导
其 它:
操 作: □□容易 定 位: □□偏松 拉 伤: □□不会 毛 刺: □平□面刮度手:
□尺□很寸好:
□□稳定 裂 纹: □□不会
部门
问题点
解决方案
下次试模时间
模具车间
试模 结论
提出签名:
模具设计
注: 1、
提出签名:
年 月 日 主管审核: 年 月 日 主管审核:
年月日
年月日
版次:A/0