钢铁企业烧结余热发电技术发展探讨
钢铁企业烧结余热发电技术发展探讨

耗 的 9 ~1 % , % 2 仅次 于炼 铁 工 序 , 居第 二 。 由于 位 烧结 冷却 机废 气 的 温度 不 高 , 1 0~ 5 C, 内 仅 5 40o 国
企业 大多 将烧 结余 热 用 于 助燃 空气 、 热混 合 料 或 预 利用余 热 回收装 置 产 生 蒸 汽 , 热 回收 利用 效 率 不 余
高 。近年 来 , 结 冷却 机 余 热 的 回收 向发 电方 向发 烧
展。
1 烧 结 余 热 发 电 的发 展
烧结余热发电, 是通 过 余 热 锅炉 来 生 产 蒸汽 回 收烧 结机 尾落 矿风 箱及烧 结 冷却机 密 闭段 的烟 气余
热推 动汽 轮发 电机组 做功 发 电 。其 意 义如下 :
・
探讨 园地 ・
钢 铁企 业烧 结余 热发 电技 术发 展探 讨
4 5
文 章 编 号 :0 48 7 (0 0 0 -50 10 —74 2 1 )54 -6
钢 铁 企 业 烧 结 余 热 发 电技 术 发 展 探 讨
徐树 伟 彭益成 刘志斌 李新华 周建 国 , , , , , 邹公平
பைடு நூலகம்
0 引 言
我 国钢铁 产 业 近 十年 来 发 展迅 猛 , 得 了长 足 取 的进 步 , 铁 年 产 量 自 19 钢 9 6年起 连 续 蝉 联 世 界 第
一
来 自电网 的以化石 燃 料 为 能源 的供 电量 , 而起 到 从 减少 温 室气体 排放 效果 。
() 2 降低 烧结 工序 能 耗 , 进 资源 节 约 ; 低产 促 降
热发 电 的是 日本 的扇 岛钢 厂 和 福 山钢 厂 , 用 部 分 采 烟气循 环 系统 回收 能源 。新 日铁 3号烧 结机 和住 友 金属小 仓 3号烧 结 机余热 电站也运 行 的 比较 早 。 日 本歌 山 4号烧结 机 ( 8 采 用 机 上 冷却 方 式 , 19 m ) 烟
浅谈提高烧结余热发电量的技术创新与工艺优化

浅谈提高烧结余热发电量的技术创新与工艺优化随着我国能源结构的多元化发展,煤炭作为主要的能源资源仍在我国能源结构中占有重要地位。
而煤炭燃烧产生的废热余热一直以来被认为是一种资源的浪费,而利用余热进行发电则成为提高能源利用效率和减少环境污染的重要途径。
烧结余热发电是指利用烧结炉的余热进行发电,是一种节能环保技术,可以有效提高烧结炉能源的利用率,同时也可以减少大气中的二氧化碳排放,对于节能减排有着积极的意义。
在这种背景下,研发和应用烧结余热发电技术成为了当前烧结生产中的重要课题。
烧结是炼铁生产过程中的重要环节,其主要目的是将粉末状矿石和配料块料加热到一定温度,使自然发生的化学反应使颗粒之间焦结为某种粘结合物,以及焦炭和矿石颗粒之间焦化和还原反应得以发展,形成一种多孔的块状烧结矿。
在烧结过程中,往往会产生大量的余热,其中蕴含着丰富的能量。
烧结矿石有机械性强、耐高温、导电率低、热传导率低等特点,通过合理的设计和运用一些先进的设备和工艺,可以更好的收集和利用烧结机的余热,从而实现烧结余热发电,具体的技术创新和工艺优化可以从以下几个方面来做。
一、余热回收与利用技术的创新1. 烧结热能回收技术通过在烧结机排烟系统中设置余热回收装置,可以将热风炉产生的高温烟气回收,利用余热进行热水或蒸汽的生产,满足企业生产和生活的热能需求,同时也可以用于发电。
通过余热回收装置,可以将排放的废气中的热能回收利用,极大的提高能源的利用效率。
2. 蓄热式余热发电技术蓄热式余热发电技术是一种新型的余热发电技术,通过蓄热设备蓄存热能,再利用蓄热设备释放热能,驱动发电机组发电。
这种技术不仅可以提高余热的利用效率,还可以实现对燃料的有效利用,降低企业的能源消耗。
3. 余热发电系统的优化设计在余热发电系统的设计中,应当从热源的选择、传热系统、蓄热设备、发电机组等方面进行综合优化设计,确保整个系统的稳定高效运行。
还需要根据工艺流程的特点,合理确定余热发电系统的工作参数,以最大化地提高系统的能量转换效率。
钢铁工业余热回收技术现状研究
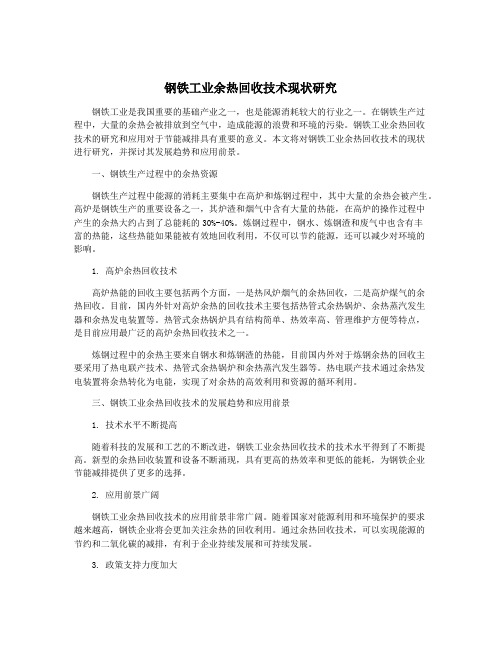
钢铁工业余热回收技术现状研究钢铁工业是我国重要的基础产业之一,也是能源消耗较大的行业之一。
在钢铁生产过程中,大量的余热会被排放到空气中,造成能源的浪费和环境的污染。
钢铁工业余热回收技术的研究和应用对于节能减排具有重要的意义。
本文将对钢铁工业余热回收技术的现状进行研究,并探讨其发展趋势和应用前景。
一、钢铁生产过程中的余热资源钢铁生产过程中能源的消耗主要集中在高炉和炼钢过程中,其中大量的余热会被产生。
高炉是钢铁生产的重要设备之一,其炉渣和烟气中含有大量的热能,在高炉的操作过程中产生的余热大约占到了总能耗的30%-40%。
炼钢过程中,钢水、炼钢渣和废气中也含有丰富的热能,这些热能如果能被有效地回收利用,不仅可以节约能源,还可以减少对环境的影响。
1. 高炉余热回收技术高炉热能的回收主要包括两个方面,一是热风炉烟气的余热回收,二是高炉煤气的余热回收。
目前,国内外针对高炉余热的回收技术主要包括热管式余热锅炉、余热蒸汽发生器和余热发电装置等。
热管式余热锅炉具有结构简单、热效率高、管理维护方便等特点,是目前应用最广泛的高炉余热回收技术之一。
炼钢过程中的余热主要来自钢水和炼钢渣的热能,目前国内外对于炼钢余热的回收主要采用了热电联产技术、热管式余热锅炉和余热蒸汽发生器等。
热电联产技术通过余热发电装置将余热转化为电能,实现了对余热的高效利用和资源的循环利用。
三、钢铁工业余热回收技术的发展趋势和应用前景1. 技术水平不断提高随着科技的发展和工艺的不断改进,钢铁工业余热回收技术的技术水平得到了不断提高。
新型的余热回收装置和设备不断涌现,具有更高的热效率和更低的能耗,为钢铁企业节能减排提供了更多的选择。
2. 应用前景广阔钢铁工业余热回收技术的应用前景非常广阔。
随着国家对能源利用和环境保护的要求越来越高,钢铁企业将会更加关注余热的回收利用。
通过余热回收技术,可以实现能源的节约和二氧化碳的减排,有利于企业持续发展和可持续发展。
提高烧结余热发电量的探索
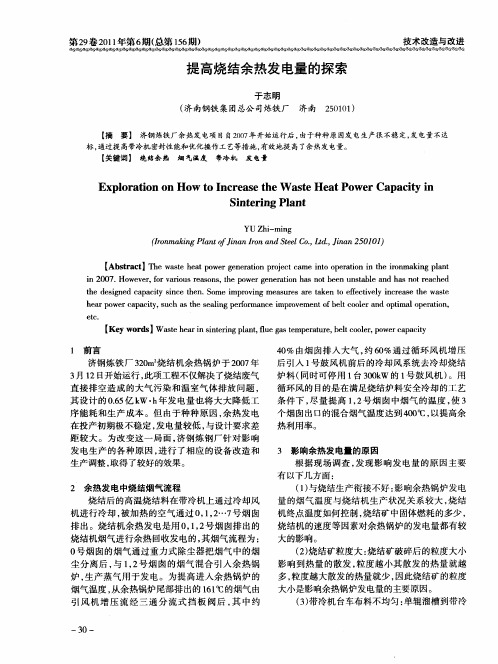
标, 通过提 高带冷机 密封性能和优化操 作工艺等措施 , 有效地提 高 了余 热发 电量 。
【 关键词】 烧结余热 烟气温度
Ex o a i n o o t n r a et a t e tPo rCa ct pl r to n H w oI c e s heW seH a we pa iy i n
et c.
【 e od 】 s ai s t i at u se prueblco rpw r aai K y rs Wath rn i e n p n f e a t e tr e l ,o ecpcy w e e n r g l , g m a , to e l t
1 前言
3 影 响余热 发 电量 的原 因
根 据 现场 调 查 , 现 影 响 发 电 量 的原 因 主要 发
有 以下 几方 面 :
烧结后的高温烧结料在带冷机上通过冷却风 机进行冷却 , 被加热的空气通过 0 12 号烟囱 , ,…7 排出。烧结机余热发电是用 0 l2 , , 号烟 囱排 出的 烧结机烟气进行余热回收发电的 , 其烟气流程为: 0 号烟 囱的烟气通过重力式除尘器把烟气 中的烟 尘分离后 , 12 与 , 号烟 囱的烟气混合 引入余热锅 炉, 生产蒸气用于发 电。为提高进入余热锅炉的 烟气温度 , 从余热锅炉尾部排出的 11 的烟气 由 6c C 引 风机增 压 流经 三通分 流式 挡板 阀后 , 中约 其
4 % 由 烟 囱排 人 大 气 , 6 %通过 循 环 风 机 增 压 0 约 0
济钢炼铁厂 30 2 m 烧结机余热锅炉于2 0 年 07 3 1 开始运行 , 月 2日 此项工程不仅解决 了烧结废气 直接排空造成的大气污染和温室气体排放问题 , 其设计的 0 5 k h . 亿 W・ 年发 电量也将 大大降低工 6 序能耗和生产成本。但 由于种种原因 , 余热发 电 在投产初期极不稳定 , 电量较低 , 发 与设计要求差 距较大 。为改变这一局面 , 济钢炼钢厂针对影响 发电生产 的各种原因 , 进行 了相应的设 备改造 和 生 产调 整 , 得 了较好 的效果 。 取
钢铁企业烧结余热利用与发电技术

钢铁企业烧结余热利用与发电技术摘要:钢铁企业烧结工序的能耗仅次于炼铁工序,一般为钢铁企业总能耗的10%〜20%。
我国烧结工序的能耗与先进国家相比有较大差距,每吨烧结矿的平均能耗要高20kgce。
在烧结工序总能耗中,有近50%的热能以烧结机烟气和冷却机废气的显热形式排入大气,即浪费了热能又污染了环境。
据日本某钢铁厂热平衡测试数据表明,烧结机的热收入中烧结矿显热占28.2%、废气显热占31.8%。
可见,烧结厂余热回收的重点为烧结废(烟)气余热和烧结矿(产品)显热回收。
烧结余热也是目前我国低温余热资源应用的重点。
一、烧结余热利用方式与现状烧结余热主要利用方式有(1)在点火前对烧结料层进行预热;(2)送到点火器,进行热风点火;(3)实行热风烧结,回收烧结过程的热量和成品矿显热,降低烧结能耗;(4)利用余热锅炉回收烧结或冷却热废风,所产蒸汽用于预热烧结混合料或生活取暖等,或者进行蒸汽升值发电。
目前,我国大型烧结厂普遍采用了余热回收利用装置,但多数中、小烧结厂的余热仍未得到有效利用。
国内重点大中型企业,钢铁协会会员单位在2006年钢铁协会调研时,只有不到三分之一的烧结机配备了烧结余热利用设备,大部分是蒸汽回收并入全厂动力蒸汽管网,很少利用余热发电的。
近年来,随着低温烟气余热锅炉技术和低参数补汽式汽轮机技术的发展,使低温烟气余热发电成为可能。
二、烧结余热利用与发电技术目前我国烧结余热利用的重点和难点在于:由于存在漏风率高导致废气温度降低,又要保证进入除尘器前废气温度在露点以上等原因,回收利用烧结余热较困难。
因此,如何降低漏风率以提高烧结机烟气温度,以及在保证烧结废气除尘所需温度条件下,实现烧结机尾部高温段废气显热回收?烧结余热蒸汽发电核心技术的消化吸收和本土化,是烧结余热回收的重点。
如开发此技术将烧结矿余热充分利用,则钢铁行业年可节约能源约900万吨标准煤。
烧结余热发电是利用低温余热的一个有效途径,但目前来说应用很少,且存在一些问题,在运行过程中,由于烧结机和环冷机工况发生变化时,余热回收系统的工作参数也将随之变动,输出的蒸汽压力、温度、流量也将发生变化,从而影响发电机组的运行效率。
浅谈提高烧结余热发电量的技术创新与工艺优化
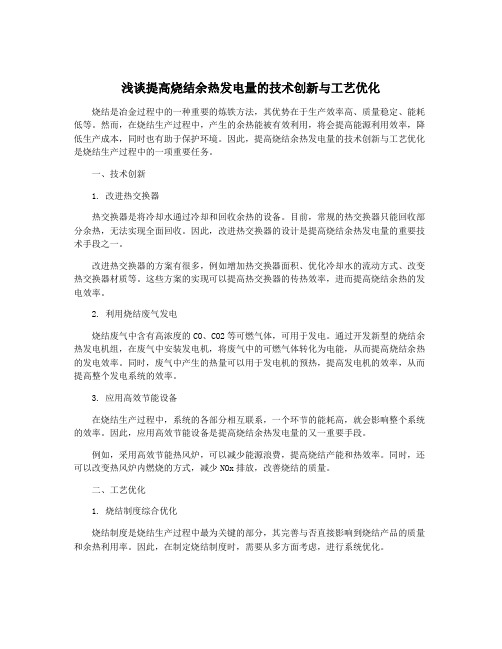
浅谈提高烧结余热发电量的技术创新与工艺优化烧结是冶金过程中的一种重要的炼铁方法,其优势在于生产效率高、质量稳定、能耗低等。
然而,在烧结生产过程中,产生的余热能被有效利用,将会提高能源利用效率,降低生产成本,同时也有助于保护环境。
因此,提高烧结余热发电量的技术创新与工艺优化是烧结生产过程中的一项重要任务。
一、技术创新1. 改进热交换器热交换器是将冷却水通过冷却和回收余热的设备。
目前,常规的热交换器只能回收部分余热,无法实现全面回收。
因此,改进热交换器的设计是提高烧结余热发电量的重要技术手段之一。
改进热交换器的方案有很多,例如增加热交换器面积、优化冷却水的流动方式、改变热交换器材质等。
这些方案的实现可以提高热交换器的传热效率,进而提高烧结余热的发电效率。
2. 利用烧结废气发电烧结废气中含有高浓度的CO、CO2等可燃气体,可用于发电。
通过开发新型的烧结余热发电机组,在废气中安装发电机,将废气中的可燃气体转化为电能,从而提高烧结余热的发电效率。
同时,废气中产生的热量可以用于发电机的预热,提高发电机的效率,从而提高整个发电系统的效率。
3. 应用高效节能设备在烧结生产过程中,系统的各部分相互联系,一个环节的能耗高,就会影响整个系统的效率。
因此,应用高效节能设备是提高烧结余热发电量的又一重要手段。
例如,采用高效节能热风炉,可以减少能源浪费,提高烧结产能和热效率。
同时,还可以改变热风炉内燃烧的方式,减少NOx排放,改善烧结的质量。
二、工艺优化1. 烧结制度综合优化烧结制度是烧结生产过程中最为关键的部分,其完善与否直接影响到烧结产品的质量和余热利用率。
因此,在制定烧结制度时,需要从多方面考虑,进行系统优化。
例如,通过优化烧结制度中的升温速率和保温时间,保证热值的合理利用,提高烧结过程的热效率、热平衡性和产品质量。
同时,还可以针对不同品种的烧结产品进行制度优化,提高对不同品种烧结产品的适应性和生产效率。
2. 余热系统优化在烧结生产过程中,余热的回收和利用是提高生产效率的关键。
试析钢铁企业烧结余热发电应用

试析钢铁企业烧结余热发电应用摘要:钢铁生产过程中,烧结工序的能耗约占总能耗的10%,仅次于炼铁工序而位居第二。
由于以前余热回收技术的局限在烧结工序总能耗中,有近50%的热能以烧结机烟气和冷却机废气的显热形式排入大气,既浪费了热能又污染了环境。
因此,采用新技术对余热余能进行利用就显得势在必行,而烧结余热发电就是一项利用烧结废气余热能源转变为电能的余热回收利用技术,该技术不需要消耗一次能源,不产生额外的废气、废渣、粉尘以及其它有害气体。
随着近几年来余热回收技术的发展,钢铁行业的余热回收项目造价也大幅降低,同时余热回收效率大大提高,特别是闪蒸汽发电技术和补汽式凝汽式汽轮机在技术上的突破,为钢铁行业余热回收创造了条件。
关键词:钢铁企业;烧结余热;发电应用1钢铁工业余热回收利用概况钢铁工业烧结余热回收主要有两部分:一部分是烧结机尾部废气余热,另一部分是热烧结矿在冷却机前段空冷时产生的废气余热。
这两部分废气所含热量约占烧结总能耗的50%,充分利用这部分热量是提高烧结工艺的效率,显著降低烧结工序能耗的途径之一。
目前,国内烧结废气余热回收利用主要有三种方式:一是直接将废烟气经过净化后作为点火炉的助燃空气或用于预热混合料,以降低燃料消耗,这种方式较为简单,但余热利用量有限,一般不超过烟气量的10%;二是将废烟气通过余热锅炉或热管装置产生蒸汽,并入全厂蒸汽管网,替代部分燃煤锅炉;三是将余热锅炉产生蒸汽用于驱动汽轮机组发电。
从实现能源梯级利用的高效性和经济性角度来看,最为有效的余热利用途径是余热发电,对烧结矿产生的烟气余热回收,平均每吨可发电20kWh,折合每吨钢综合能耗可降低8kg标准煤。
2烧结余热回收中出现得较为普遍的问题2.1漏风現象在余热回收系统中的漏风问题主要是通过台车与烟罩之间的密封以及台车与风箱之间的密封体现出来的。
因为烟气系统属于全闭路式循环,台车与烟罩、台车与风箱都是在实际运转过程中进行相互配合的,风箱中一般为正压3000PA-4000PA之间,眼罩中为负压-100PA-400PA。
烧结余热汽轮机发电系统在钢铁行业中的应用与效益分析

烧结余热汽轮机发电系统在钢铁行业中的应用与效益分析摘要:钢铁行业是现代工业中最重要的基础产业之一,其中烧结过程产生的余热是一种可再利用的能源。
本论文旨在对烧结余热汽轮机发电系统在钢铁行业中的应用与效益进行分析。
通过对相关资料的分析和实例研究,可以发现烧结余热汽轮机发电系统对于钢铁企业具有重要意义,能够显著降低能耗、减少环境污染,并提高能源利用效率。
因此,钢铁企业在推广和应用烧结余热汽轮机发电系统方面具有巨大的潜力。
关键词:烧结余热汽轮机发电系统;钢铁行业;应用;效益分析引言钢铁行业作为国民经济的支柱产业,在实现经济增长的同时也面临着能源消耗和环境污染等问题。
而烧结过程产生的余热一直被忽视,未能充分利用。
随着可持续发展理念的兴起,针对烧结余热的有效利用成为一个重要的课题。
烧结余热汽轮机发电系统作为一种先进的能源利用技术,具有巨大的潜力,可以大幅降低钢铁企业的能耗以及对环境的负面影响。
本论文旨在通过对烧结余热汽轮机发电系统进行应用与效益的分析,探讨其在钢铁行业中的可行性和经济效益。
1.烧结余热汽轮机发电系统概述1.1系统组成和工作原理烧结余热汽轮机发电系统由烧结炉、余热锅炉、汽轮机和发电机等主要组成。
烧结过程中产生的高温高压燃气经过余热锅炉的换热作用,生成高温高压蒸汽,并驱动汽轮机旋转。
汽轮机的旋转驱动发电机发电,将余热转化为电能。
该系统充分利用了钢铁生产过程中的余热资源,提高了能源利用效率,减少了能源浪费。
同时,该系统还能减少环境污染和降低能耗,具有重要的经济和环境效益。
1.2技术特点和优势烧结余热汽轮机发电系统的技术特点和优势包括:(1)高效利用能源:该系统能够将烧结过程中的余热转化为电能,提高能源利用效率,减少能源浪费。
(2)减少环境污染:通过有效利用余热,系统能够降低钢铁行业的能耗,减少燃烧排放物质的产生,对环境污染的减少具有明显效果。
(3)资源节约:利用烧结过程中产生的余热进行发电,不仅可以减少能源的消耗,还能节约燃料资源的使用。
浅谈提高烧结余热发电量的技术创新与工艺优化

浅谈提高烧结余热发电量的技术创新与工艺优化烧结余热发电是指利用钢铁、有色金属等高温烧结过程产生的余热发电。
这种发电方式是一种节能环保的发电方式,可以通过技术创新和工艺优化来提高其发电量。
通过技术创新来提高烧结余热发电量。
技术创新主要分为两个方面,一是在余热回收装置上进行创新,二是在余热发电装置上进行创新。
在余热回收装置方面,可以考虑采用高效换热器,增大换热面积,提高热量回收效率。
可以采用多级余热回收系统,将烧结过程中产生的多个余热进行回收,提高发电量。
可以考虑采用新型余热回收材料,如气凝胶材料,具有较低的导热系数和较高的热稳定性,可以提高余热回收效果。
在余热发电装置方面,可以考虑采用高效发电机组,提高发电效率。
可以利用三废(废热、废气、废渣)综合利用技术,将烧结过程中产生的废气和废渣进行资源化利用,进一步提高发电量。
可以采用联合循环发电技术,将烧结过程中产生的余热与其他工序的余热进行联合发电,提高整体发电效率。
通过工艺优化来提高烧结余热发电量。
工艺优化主要包括四个方面,一是优化烧结工艺,二是优化余热回收过程,三是优化发电装置工艺,四是优化系统运行管理。
在烧结工艺方面,可以通过优化燃料燃烧过程,提高燃烧效率。
可以优化烧结物料配比,提高烧结物料的热值,增加余热产生量。
在余热回收过程中,可以优化余热回收装置的布置,减少热量损失。
可以优化换热器的运行参数,提高换热效率。
可以采用烟气再压缩技术,将余热回收装置的烟气再压缩,提高发电效率。
在发电装置工艺方面,可以优化发电机组的运行参数,提高发电效率。
可以优化发电机组的启停策略,降低启停频率,减少能耗。
在系统运行管理方面,可以建立完善的余热发电系统监控系统,实时监测系统运行状态,及时发现并处理问题。
可以建立科学的运行计划,合理利用余热资源,提高系统整体效率。
通过技术创新和工艺优化,可以提高烧结余热发电量,实现可持续发展。
这不仅可以减少能源消耗,降低碳排放,还可以提升企业的经济效益和竞争力。
烧结余热高效利用技术及装备的研究

烧结余热高效利用技术及装备的研究
烧结余热高效利用技术及装备的研究是现代钢铁行业的重要问题之一。
钢铁烧结过程中产生的余热含能量丰富,若能得到高效利用,不仅可以降
低能源消耗,还可以减少环境污染,提高钢铁工业的可持续性发展。
目前,烧结余热高效利用技术主要包括以下几种:
1.余热回收技术:通过余热回收技术,将烧结过程中产生的烟气、炉
排热等余热回收利用,用于其他生产环节或提供建筑供暖等需求。
2.余热利用技术:余热利用技术包括蒸汽发电、热水供暖、空气调节
等多种形式,可根据具体情况选择不同的利用方式。
3.高温烧结烟气净化技术:烧结过程中产生的烟气含有大量的二氧化硫、氮化物等有害气体,可采用高温烧结烟气净化技术将其处理,达到环
保要求。
4.增加热量回收点:在烧结过程中增加热量回收点,可实现余热的多
次回收,提高余热利用效率。
为实现烧结余热高效利用,还需要相应的装备支持。
目前,常用的装
备包括内循环流化床锅炉、热管、换热器等。
这些装备具有构造简单、性
能稳定、能效高等优点,并且适用于各种不同规模的烧结设备。
总之,烧结余热的高效利用对钢铁行业的节能减排、环保和可持续发
展具有重要意义,需要不断地开展技术研究和装备更新,推动烧结行业向
着高效、环保、可持续的方向发展。
研讨提升烧结余热发电发电量措施

研讨提升烧结余热发电发电量措施摘要:在钢铁行业锅炉燃烧的过程中,由于旧有的废气和采暖换热装置并没有能够实现对余热进行回收采集,这样就使得大量的热能白白浪费。
通过对原有的环冷机、废气排空装置以及采暖装置进行更换,并且利用环冷机废气回收和矿料小车,回收烟罩间的密封设备,对小车密封系统进行全面的改造,可以直接将系统的热矿与冷风交换热量,并且通过锅炉加热后,直接进入环冷机。
通过这样的余热回收利用改造系统,可以有效地利用低温废气,而且不会产生环境污染的问题,还能够减少能源资源的消耗,促进企业自身的经济效益得到大幅度增强。
关键词:烧结余热;回收利用;影响对策一、技术工作内容1.1总体工作思路某钢铁厂1#2#共有360m2的烧结环冷机生产线,并且为每台烧结机配备了450m2的环冷机,环冷机处理量可以达到730~890t/h。
为了能够更好地促进余热回收的整体效果,在不影响整个烧结工艺质量的前提条件下,必须要对余热锅炉和低温补气凝汽汽轮机发电机组进行改进与优化,通过利用余热回收系统、换热系统来驱动汽轮机进行发电,其他的废气也可以用于生产或者采暖等,通过这样的方式能够将整个烧结生产线的运行调度系统进行紧密连接,保证各个系统之间的统一合作,促进了整个发电厂的经济效益得到全面提升,而且符合节能减排的实际要求。
1.2技术方案在烧结余热发电量技术创新与优化之前,必须要对整个环冷机的烟气温度进行详细的检测,并且对锅炉选型进行优化,通过利用双压余热锅炉,能够对原有的烧结冷机锅炉进行改造,这样也就能够确保换热装置的整体效果,也能够增强高温烟气回收的利用水平。
环冷机余热发电是烧结厂节能增效的重要途径,同时也是烧结余热利用方式中成熟可靠的技术手段。
在环冷机规格与锅炉型号确定的情况下,合理分配环冷机各段的冷却风量,有助于在保证烧结矿冷却效果的前提下提升其余热发电量。
基于烧结环冷机过程模拟模型以及余热发电功率的预测模型,以发电功率为目标,采用遗传算法对环冷机冷却风量进行了优化。
浅谈提高烧结余热发电量的技术创新与工艺优化

浅谈提高烧结余热发电量的技术创新与工艺优化烧结余热发电指的是利用烧结工艺过程中产生的烟气或余热,将其转化为电能的一种发电方式。
烧结工艺是钢铁行业的关键环节之一,也是能源消耗较大的环节。
提高烧结余热发电量对于节约能源、降低钢铁企业的生产成本以及减少环境污染都具有重要意义。
本文将从技术创新和工艺优化两方面浅谈提高烧结余热发电量的方法。
技术创新是提高烧结余热发电量的关键。
目前,较为常见的烧结余热发电技术包括烟气余热发电和废热余热发电两种方式。
烟气余热发电是指通过回收烧结烟气中的余热,将其转化为电能。
在传统的烟气余热发电技术中,常用的设备包括烟气余热锅炉和蒸汽发生器。
在这些设备中,关键的技术创新点包括提高余热回收效率和转化效率。
采用高效的余热回收设备,如换热器和余热锅炉,能够提高余热回收效率。
通过优化锅炉炉膛结构和布局,提高余热转化效率。
采用火电联合循环技术,将烧结余热与锅炉烟气结合起来,进一步提高发电效率。
废热余热发电是指通过回收烧结行业中产生的废热,将其转化为电能。
废热余热发电的关键在于寻找适合的废热发电技术。
目前,较为常见的废热发电技术包括有机朗肯循环发电技术、卡尔森热电联产技术和热泵发电等。
这些技术的共同之处在于将废热通过热交换和动力装置转化为电能。
技术创新的关键在于提高废热的回收效率和转化效率。
通过优化热交换设备的结构和材料,提高热量传递效率。
通过采用高效的动力装置,如蒸汽涡轮机和有机朗肯循环机组,提高发电效率。
工艺优化也是提高烧结余热发电量的重要手段。
工艺优化是指通过改进烧结工艺流程和操作方式,减少能量损耗和废热排放,从而提高烧结余热发电量。
可以通过改进烧结炉的结构和燃烧方式来降低能量损耗。
采用高效的烧结炉内部结构,如流化床或旋流炉,可以提高燃料利用率和热量利用效率。
合理调整烧结炉的操作参数,如燃烧温度和燃烧风量,可以降低能量损耗和废热排放。
可以通过优化烧结工艺流程来提高烧结余热发电量。
合理调整烧结工艺参数,如原料配比和加热曲线,可以提高热量利用效率和能量转化效率。
浅谈提高烧结余热发电量的技术创新与工艺优化

浅谈提高烧结余热发电量的技术创新与工艺优化烧结是一种重要的铁矿石还原工艺,其过程中会产生大量的余热。
如何充分利用这部分余热,提高烧结厂的能源利用率,一直是烧结行业面临的问题。
为此,烧结厂需要通过技术创新和工艺优化来提高烧结余热的发电量。
一、技术创新(一)余热回收技术的发展在烧结过程中,大量的余热以及冷却水都会被排放,造成了巨大的能源浪费。
随着科技的进步,利用余热回收技术已成为烧结行业的一个主要趋势。
目前,常见的余热回收技术主要有废热发电技术、余热蒸汽发生器技术和余热燃气发生器技术。
(二)余热利用的研究进展近年来,利用余热发电已成为烧结行业发展的重要方向。
烧结行业将余热与热电联供技术相结合,发挥其余热资源的最大潜力,既可以降低生产成本,又可减少环境污染和碳排放。
同时,还可以通过政策鼓励等方式,促进烧结行业向清洁能源转型。
(三)新型节能环保材料的研发为了提高烧结行业的能源利用率,不断推动烧结技术进步,烧结厂需要不断开展新型节能环保材料的研究和开发。
比如,烧结厂可以研发新型耐火材料,采用新型耐火材料可以有效延长其寿命,提高反应效率,从而达到节能环保的效果。
二、工艺优化(一)炉料结构的优化炉料的结构对于烧结效果和余热利用效果有着很大的影响。
在炉料结构方面,烧结厂可以优化其原料的比例和粒度分布等因素,提高炉料的均匀性,从而提高烧结效率,增加余热的利用率。
(二)冷却水利用的优化冷却水是烧结过程中的重要组成部分,烧结厂可以通过优化冷却水的利用方式,减少水的损耗,提高水的再利用率。
比如,可以采用全蒸汽冷却的方式来替代传统的水冷却,减少冷却水的流失,从而达到节能环保的目的。
(三)废气净化系统的优化在烧结过程中,废气产生量巨大,严重影响着环境质量。
为了解决这一问题,烧结厂可以通过改进废气净化系统,提高废气的净化效率。
此外,还可以加强对生产过程的监管力度,减少废气的产生量。
综上所述,提高烧结余热的发电量需要不断推进技术创新和工艺优化,提高炉料质量和利用率等方面,从而达到节能环保、降低成本的目的。
浅谈提高烧结余热发电量的技术创新与工艺优化

浅谈提高烧结余热发电量的技术创新与工艺优化随着我国对环保和能源利用的重视,烧结余热发电技术逐渐成为烧结厂的重要发展方向。
提高烧结余热发电量,对降低企业能耗、减少环境污染、改善资源利用效率具有重要意义。
本文将从技术创新和工艺优化两个方面,浅谈提高烧结余热发电量的相关内容。
一、技术创新1. 余热回收技术余热发电是指通过将工业生产中的余热转化为电能进行发电,烧结生产中产生的余热经过合理收集和利用可以转化为电能。
目前常用的余热回收设备包括烟气余热锅炉、余热发电机组等。
烟气余热锅炉是将烧结烟气中的余热通过换热器收集,再利用锅炉进行高温高压蒸汽发电。
而余热发电机组则是直接利用烧结烟气中的余热进行发电。
在技术创新方面,可以通过提高余热回收设备的换热效率、优化锅炉结构等方式来提高余热的利用率,从而增加烧结余热发电量。
2. 发电设备技术烧结余热发电的关键部件是发电设备,其性能直接影响发电效率。
传统的燃气轮机、蒸汽轮机等发电设备虽然稳定可靠,但是效率相对较低,且对余热的利用要求较高。
研发高效的余热发电设备成为提高烧结余热发电量的关键。
目前,一些企业已经开始尝试采用高效的有机朗肯循环发电机组、燃气透平发电机组等新型发电设备。
这些设备具有高效率、灵活性强、适应性广等优势,能够更好地适应烧结烟气的特点,从而提高余热发电量。
3. 烧结工艺改进通过改进烧结工艺,可以降低烧结烟气中的排放物含量,提高余热利用率。
目前,一些企业已经开始尝试采用高温烧结和高效节能烧结工艺,通过提高烧结炉内温度、优化烧结配比等方式来提高余热质量。
除了对烧结炉内工艺的改进,还可以考虑在烧结过程中采用先进的烧结燃料,比如采用高热值的燃料,降低烧结排放物的含量,从而提高余热的可利用性。
二、工艺优化1. 余热利用系统优化烧结余热利用系统包括余热回收设备、余热发电设备、余热管道等组成的一套系统。
优化这一系统,能够提高余热的收集和利用效率。
首先要对余热回收设备进行优化,比如提高换热器的换热效率、优化余热管道的布局、加装余热回收设备等,从而增加余热的收集量。
浅谈提高烧结余热发电量的技术创新与工艺优化

浅谈提高烧结余热发电量的技术创新与工艺优化【摘要】烧结余热发电是一种重要的能源利用方式,可以有效降低能耗和减少环境污染。
技术创新和工艺优化是提高烧结余热发电量的关键。
本文从提高余热利用效率的技术创新、优化烧结炉操作参数、改进余热锅炉设计、利用新型材料提高热传导效率和探索新型热电转换技术等方面进行了探讨。
通过对这些方面的研究和应用,可以有效提高烧结余热发电量。
技术创新和工艺优化对于提升烧结余热发电量具有重要意义,未来还有很大的发展空间和前景。
加强技术创新和工艺优化,对于未来烧结余热发电量的提升具有重要意义。
【关键词】烧结余热发电、技术创新、工艺优化、提高效率、烧结炉操作、余热锅炉设计、新型材料、热传导效率、热电转换技术、前景、发展方向。
1. 引言1.1 烧结余热发电的意义烧结余热发电是一种重要的能源回收利用方式,通过将烧结炉废气中的余热转化为电能,不仅可以有效减少能源消耗和环境污染,还可以为企业增加经济效益。
烧结过程中产生的高温废气中蕴含大量热能,如果能够有效地利用这些余热,将有助于提高生产效率,减少能源开支。
烧结余热发电还可以有效降低对传统能源的依赖,减少碳排放,符合可持续发展的战略目标。
在当前能源资源日益紧张的背景下,提高烧结余热发电量的效率已成为行业发展的必然趋势。
通过技术创新和工艺优化,可以进一步挖掘余热利用的潜力,提高电能的产出率,实现资源的最大化利用。
烧结余热发电在工业生产中具有重要的意义,不仅可以满足企业的能源需求,还可以为推动绿色环保产业发展做出贡献。
1.2 技术创新的必要性技术创新的必要性在提高烧结余热发电量中起着至关重要的作用。
随着社会经济的快速发展,能源资源日益紧缺,对环境保护的需求也日益迫切。
传统的烧结余热发电技术存在能量利用率低、设备老化等问题,需要通过技术创新来提高效率和减少能源浪费。
技术创新可以促进烧结余热发电过程的优化,提高热能的转换效率,减少能源消耗,同时降低环境污染。
烧结余热回收发电浅谈

烧结余热回收发电浅谈耿乃弟一、我国钢铁企业的能耗状况钢铁生产消耗大量的能源和载能工质, 其能耗占我国国民经济总能耗的10%左右。
成本中能源费用占有相当大的比重, 钢铁联合企业中这一比重已达到30%,甚至更高。
日本钢铁工业的吨钢能耗维持在0.65tce左右。
我国74家大中型钢铁企业的吨钢能耗为0.80tce,与日本相比差约0.15tce。
我国能耗最低的宝钢的吨钢能耗与日本相比也有约50kgce的差距。
我国能源消耗高的原因虽然很多, 企业规模小是一个很重要的原因。
我国重点大中型企业(进入统计范围内) 74 家钢产量占全国的90% ,而日本5大钢铁企业的钢产量占日本的70%以上。
由于装备小,一些节能效果显着,但投资大,投资回收期长的节能措施无法实施。
例如:日本干熄焦、高炉TRT、转炉煤气回收的普及率100%。
我国的干熄焦装置只有17套,年处理焦炭480万t,占我国机焦产量的4%。
TRT只在大高炉有少量装置。
二、钢铁企业余热余能资源情况钢铁企业余热余能的范围包括焦化、烧结/球团、炼铁、炼钢及轧钢等主要生产工序,各主要生产工序的余热余能参数大致如下:1、焦化工序的钢比系数为0.404t(焦)/(t钢);焦炉煤气产生量为410m3/(t 焦);红焦温度为1000℃,上升管焦炉煤气温度为700℃,焦炉烟气温度为200℃;2、烧结工序的钢比系数为1.44t(矿)/(t钢);机尾烧结矿温度为800℃,烧结烟气温度为300℃;球团工序的钢比系数为0.25t(矿)/(t钢),球团矿排出温度为500℃;3、炼铁工序的钢比系数为0.91t(铁)/(t钢);高炉渣产量为320t(渣)/(t 铁),液态高炉渣温度为1500℃;高炉煤气发生量为1650m3/t(铁),高炉煤气热值为3350kJ/m3,炉顶高炉煤气温度为200℃;高炉冷却水平均温度为40℃;热风炉排烟温度为500℃;4、炼钢工序转炉钢比系数为0.84t(钢)/(t钢),电炉钢比系数为0.16t(钢)/(t钢);连铸比为100%;连铸坯温度为900℃;钢渣温度为1550℃;转炉煤气产生量为115m3/(t钢),热值为8370kJ/m3,烟罩处转炉煤气温度为1600℃;电炉炉顶排放口烟气温度为1200℃;5、轧钢工序钢比系数为0.92t(材)/(t钢);加热炉炉尾或入蓄热式烧嘴烟气平均温度为900℃;加热炉汽化冷却蒸汽压力为1.5MPa,温度为200℃;基于以上参数,我国钢铁工业吨钢余热余能资源总量为0.455tce/(t钢),各工序所占比例见下图。
钢铁行业余热的发电技术
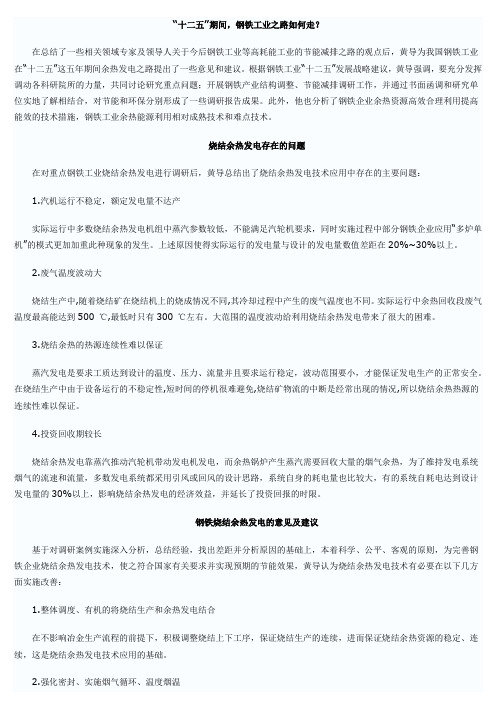
“十二五”期间,钢铁工业之路如何走?在总结了一些相关领域专家及领导人关于今后钢铁工业等高耗能工业的节能减排之路的观点后,黄导为我国钢铁工业在“十二五”这五年期间余热发电之路提出了一些意见和建议。
根据钢铁工业“十二五”发展战略建议,黄导强调,要充分发挥调动各科研院所的力量,共同讨论研究重点问题;开展钢铁产业结构调整、节能减排调研工作,并通过书面函调和研究单位实地了解相结合,对节能和环保分别形成了一些调研报告成果。
此外,他也分析了钢铁企业余热资源高效合理利用提高能效的技术措施,钢铁工业余热能源利用相对成熟技术和难点技术。
烧结余热发电存在的问题在对重点钢铁工业烧结余热发电进行调研后,黄导总结出了烧结余热发电技术应用中存在的主要问题:1.汽机运行不稳定,额定发电量不达产实际运行中多数烧结余热发电机组中蒸汽参数较低,不能满足汽轮机要求,同时实施过程中部分钢铁企业应用“多炉单机”的模式更加加重此种现象的发生。
上述原因使得实际运行的发电量与设计的发电量数值差距在20%~30%以上。
2.废气温度波动大烧结生产中,随着烧结矿在烧结机上的烧成情况不同,其冷却过程中产生的废气温度也不同。
实际运行中余热回收段废气温度最高能达到500 ℃,最低时只有300 ℃左右。
大范围的温度波动给利用烧结余热发电带来了很大的困难。
3.烧结余热的热源连续性难以保证蒸汽发电是要求工质达到设计的温度、压力、流量并且要求运行稳定,波动范围要小,才能保证发电生产的正常安全。
在烧结生产中由于设备运行的不稳定性,短时间的停机很难避免,烧结矿物流的中断是经常出现的情况,所以烧结余热热源的连续性难以保证。
4.投资回收期较长烧结余热发电靠蒸汽推动汽轮机带动发电机发电,而余热锅炉产生蒸汽需要回收大量的烟气余热,为了维持发电系统烟气的流速和流量,多数发电系统都采用引风或回风的设计思路,系统自身的耗电量也比较大,有的系统自耗电达到设计发电量的30%以上,影响烧结余热发电的经济效益,并延长了投资回报的时限。
钢铁行业新型余能余热发电技术研究

Research on new technology of residual energy and waste heat power generation in iron and steel industry
Fang Guiping ( Fujian Dongguo Energy Saving Technology Co. ꎬ Ltd. )
收稿日期:2018 - 11 - 29 方桂平(1965 - ) ꎬ高级工程师ꎻ350000 福建省福州市ꎮ
Байду номын сангаас
效率普遍较低问题ꎬ 特别是转炉与轧钢加热炉产 出的是饱和蒸汽ꎬ 利用饱和蒸汽机组发电ꎬ 发电 效率极低且机组可靠性差ꎮ
烧结、 球团、 炼铁、 转炉、 电炉、 焦化及轧 钢工序均存在一定的余热资源ꎬ 传统余热回收发 电都是站在各工序的角度考虑回收ꎬ 以确定回收 蒸汽的温度及压力ꎮ 由于这些工序余热资源均属 于中低温余热ꎬ 其余热回收发电装置分散且低 效ꎬ 甚至迫不得以采用饱和蒸汽机组发电ꎮ
我国钢铁行业消耗了全社会总能耗的 10% 左右ꎬ 占比很高ꎮ 同时ꎬ 在钢铁生产过程中ꎬ 有 大量的余热余能产生ꎮ 目前钢铁行业余能 ( 高 炉煤气、 转炉煤气及焦炉煤气) 回收发电做到 超高压高温 ( 或超高压超高温) 的初参数ꎬ 热 功转换效率已提高到一个新的水平ꎮ 但是烧结余 热发电等还存在蒸汽初参数低、 过热度低和发电
38
ENERGY
冶 金 能 源
FOR METALLURGICAL
INDUSTRY
Vol������ 38 No������ 2 Mar������ 2019
钢铁行业新型余能余热发电技术研究
方桂平
( 福建省东锅节能科技有限公司)
科技成果——钢铁行业烧结余热发电技术

科技成果——钢铁行业烧结余热发电技术
适用范围钢铁行业
行业现状
与该节能技术相关生产环节的能耗现状为200-400℃的低温余热废气,基本没有得到利用。
目前应用该技术可实现节能量8万tce/a,减排约21万tCO2/a。
成果简介
1、技术原理
钢铁行业烧结、热风炉、炼钢、加热炉等设备产生的废烟气,通过高效低温余热锅炉产生蒸汽,带动汽轮发电机组进行发电。
2、关键技术
通过分级利用余热,使得余热锅炉能最大限度的利用200-400℃的低温余热。
3、工艺流程
烟气收集→余热锅炉→汽轮发电机。
五、主要技术指标可利用烟气温度为200-400℃。
典型案例
典型用户:马钢
某钢铁投资1.7亿元人民币,安装了低温余热锅炉及汽轮发电机组,年发电量达1.4亿kWh,年取得经济效益7000万元人民币,投资回收期2.5年。
市场前景
钢铁企业的烧结、冶炼、加热等设备产生大量的低温废气,基本没有得到合理利用,所以其推广前景广阔,节能潜力巨大。
在钢铁生产过程中,都会产生大量低温烟气,若将其低温余热充分合理利用,将会产生很大的节能效益。
建议政府应积极支持、鼓励,制定特殊政策,激励企业利用低温余热的积极性,节约大量一次能源,创造更多社会效益。
未来5年,预计推广到40%,总投入17亿元,节能能力可达15万tce/a,减排能力41万tCO2/a。
钢铁企业烧结余热发电技术研究-论文

摘要烧结余热发电技术是一项将烧结废气余热资源转变为电力的节能技术。
由于国内烧结余热发电起步较晚,因此还存在回收率较低等很多问题,现对现有的余热发电系统进行分析,提出新的改进措施,从而提高余热资源回收率及机组的发电功率。
本研究通过分别分析烧结余热发电双压系统、单压系统、闪蒸系统和补燃系统四种余热发电系统的热力学和经济性计算,发现对于钢铁企业,双压系统的热力特性和经济性最佳,排出的污染物较少,是最合理的设计方案。
最后,对于当前技术条件下烧结余热发电技术应用难点,本设计通过设计余热发电流程,严格控制余热发电环节,以优化余热发电方案,取得更好的经济及环境效益。
关键词:余热发电、烧结、双压ABSTRACTSintering waste heat power generation technology is a sintered exhaust heat resources into electricity saving technology. As domestic sintering waste heat power generation started late, so there are still many problems such as low recovery rate, now we existing analysis cogeneration systems, propose new measures for improvement, thereby improving waste heat recovery and power generation units.This study analyzed separately dual-pressure sintering waste heat power generation system, a single pressure system, flash system and the complement system, fuel system, four kinds of cogeneration thermodynamic and economic calculations and found that the iron and steel enterprises, dual pressure system and economy of the thermodynamic properties is best, fewer pollutants dischar- ed, is the most reasonable design. Finally, the sintering waste heat power genera- tion technology difficulties of current technical conditions, this design through the design of waste heat power generation process, strict control of waste heat power generation process, in order to optimize the waste heat power generation system, and obtain better economic and environmental benefits.Key words:waste heat power generation, sintering, dual-pressure目录1绪论 (1)1.1研究背景 (1)1.2烧结余热发电技术国内外研究现状 (3)1.3烧结余热发电研究意义 (4)1.4研究内容 (5)2烧结余热发电系统分析 (6)2.1烧结余热发电系统 (6)2.2烧结余热发电烟气系统 (8)2.3烧结余热发电热力系统分析方法 (9)2.4烧结余热发电四种热力系统热力学分析 (13)2.5烧结余热发电四种热力系统经济性分析 (22)3烧结余热发电设备 (26)3.1选型原则 (26)3.2部分主要设备的选型要求及选择 (26)4烧结余热发电技术应用难点及解决方法 (32)4.1烧结余热发电技术应用难点 (32)4.2烧结余热发电技术应用难点解决方法 (33)5总结 (36)参考文献 (37)致谢 (39)附录A 烧结余热发电系统总图 (40)附录B 外文参考文献及译文 (42)1绪论1.1研究背景1.1.1 钢铁工业烧结余热能源现状钢铁生产过程中消耗了大量的资源、能源,因此随着钢铁产量的增长,能源消耗总量也持续上升。
- 1、下载文档前请自行甄别文档内容的完整性,平台不提供额外的编辑、内容补充、找答案等附加服务。
- 2、"仅部分预览"的文档,不可在线预览部分如存在完整性等问题,可反馈申请退款(可完整预览的文档不适用该条件!)。
- 3、如文档侵犯您的权益,请联系客服反馈,我们会尽快为您处理(人工客服工作时间:9:00-18:30)。
钢铁企业烧结余热发电技术发展探讨
45
文章编号: 1004 8774( 2010) 05 45 06
钢铁企业烧结余热发电技术发展探讨
徐树伟 1, 彭益成1, 刘志斌 1, 李新华2, 周建国 1, 邹公平 1
( 1. 长沙锅炉厂有限责任公司, 长沙 410114; 2. 涟源钢铁集团有限公司, 娄底 417009)
( 1) 单压汽水系统的烧结余热发电系统 采用单级进汽汽轮机及单压烧结余热锅炉的单 压不补汽系 统。一 般余热 锅炉排 气温度 在 170 ~ 180 , 排气用于烘干物料。 ( 2) 双压汽水系统的烧结余热发电系统 采用补汽式汽轮机的双压单级补汽系统, 烧结 余热锅炉生产两种不同压力、温度的蒸汽, 一种为主 蒸汽, 另一种为低压补汽。由于设置了低压蒸发段, 低压蒸汽压力为 0. 4~ 0. 6 MP a, 低压过热蒸汽温度 190 左右, 由于设置了低压省煤器, 排烟温度能降 到 130 左右。 ( 3) 复合闪蒸汽水系统的烧结余热发电系统 采用补汽式汽轮机的复合闪蒸补汽系统, 烧结 余热锅炉生产主蒸汽同时生产高温热水, 高温热水
国家大力提倡生产过程节能降耗, 对企业节能 指标提出了很高的要求。国发 [ 2005] 21 号文件中
提出 在冶金、有色、煤炭、电力、化工、建材、造 纸、
收稿日期: 2010 07 27
酿造等重点行业组织开展循环经 济试点 !, 要求钢
46
工业锅炉
2010年第 5期 ( 总第 123期 )
铁行业加快淘汰落后工艺和设备, 提高新建、改扩建 工程的能耗准入标准; 实现技术装备大型化、生产流 程连续化、紧凑化、高效化, 最大限度综合利用各种 能源和资源; 充分利用高炉煤气、焦炉煤气和转炉煤 气等可燃气体和各类蒸汽, 以自备电站为主要集成 手段, 推动钢铁企业节能降耗。
25 MW
邯郸钢铁股份有限公司 湘潭钢铁集团有限公司
1台 360 m2 1台 180 m2
25 MW 4. 5 MW
日照钢铁有限公司 涟源钢铁集团有限公司
2台 360 m2 1台 360 m2
25 MW 15 MW
太原钢铁 (集 团 )有限公司
1台 450 m2 1台 660 m2
40 MW
投运时间 2005年 9月 2007年 3月 2007年 12月 2009年 1月
马鞍山钢铁股份有限公司 2台 300 m 2 烧结机 余热发电装机 17. 5 MW, 从日本川崎重工株式会社 全套引进, 2005年 9月投运, 为我国第一套烧结余
热发电系统。在引进技术的基础上, 我国进行了大 量的技术创新, 随着近几年来余热回收技术发展, 钢 铁行业的余热回收项目造价大幅度降低, 特别是闪 蒸发电技术和补汽凝汽式 汽轮机在技术上 获得突
再降压闪蒸产生二次 蒸汽, 二 次蒸汽补入汽轮 机。 排烟温度能降到 100 左右。 2. 2 现有烧结余热发电技术存在的问题
现有的烧结余热发电系统是烧结烟气通过余热 锅炉换热后直接产生过热主蒸汽推动汽轮机发电, 主要存在以下问题。
( 1)由于余热锅炉进口烟气温度低, 余热锅炉 产生的过热蒸汽压力和温度都较低, 发电效率低;
在钢铁生产过程中, 烧结工序的能耗约占总能 耗的 9% ~ 12% , 仅次于炼铁工序, 位居第二。由于 烧结冷却机废气的温度不高, 仅 150 ~ 450 , 国内 企业大多将烧结余热用于助燃空气、预热混合料或 利用余热回收装置产生蒸汽, 余热回收利用效率不 高。近年来, 烧结冷却机余热的回收向发电方向发 展。
由朗肯循环的热效率可知: ( 1) 在相同的初压及背压 下, 提高新蒸汽的温 度可使热效率增大, 蒸汽温度对热能转换为电能有 极大的影响。比如: 1 kg /h、1 000 的热水, 其含有的热量为 1 000 kca,l 这个热量理论上转化为电量的最大能力 N = [ 1- 273 / ( 1 000+ 273) ] ∋ 1 000 ∋ 4. 186 8 /3 600= 0. 913 5 kW, 理论转换效率为 0. 913 5 ∋ 860 /1 000 = 78. 56% 。 10 kg / h、100 的热水, 其含有的热量为 1 000 kca,l 这个热量理论上转化为电量的最大能力 N = [ 1- 273 / ( 100 + 273) ] ∋ 1 000 ∋ 4. 186 8 / 3 600 = 0 311 8 kW, 理论转换效率为 0. 311 8 ∋ 860 /1 000 = 26. 8% 。 上述转换效率的不同, 反映在汽轮机上为: 主蒸 汽温度高时, 汽轮机进汽焓高, 主蒸汽温度低时, 汽 轮机进汽焓低, 而汽轮机的发电功率是汽轮机进汽 焓与排汽焓的差值 [ 发电机输出功率 N = 汽轮机进 汽量 Z x (汽轮机进汽焓 H 1 - 汽轮机排汽焓 H p ) ∋汽 轮机缸效率 F1 ∋ 汽轮机机械、散热、自用动力损失 效率 F 3 ∋发电机效率 F 4 ] 。 ( 2) 在相同的初温及背压 下, 提高新蒸汽的初 压可使热效率增大, 在相同排汽压力及缸效率的条 件下, 汽轮机进汽压力越高排汽焓 H p 越低, 如汽轮 机排汽压力为 0. 007M Pa, 当汽轮机进汽参数为 2. 1
( 3)有利于企业可持续发展目标的实现, 减少 由常规火电厂带来的 SO2、CO2、粉尘之类的大气污 染物, 有助于改善当地的能源结构, 提高能源安全。 1. 1 日本烧结余热发电发展情况
日本缺少资源, 节能尤为重要, 烧结余热利用起 步最早, 在上世纪 80年代中期, 余热回收技术已在 日本烧结厂得到了广泛应用, 其冷却机废气余热利 用的普及率已达到 57% 。最早利 用冷却机烟气余 热发电的是日本的扇岛钢厂和福山钢厂, 采用部分 烟气循环系统回收能源。新日铁 3号烧结机和住友 金属小仓 3号烧结机余热电站也运行的比较早。日 本歌山 4号烧结机 ( 189 m2 ) 采用机上冷却方式, 烟 气分两段收集, 布置余热锅炉, 产生中压过热蒸汽来 推动汽轮发电机组做功发电, 该系统 1991年 6月投 入运行, 运行效果很好。 1. 2 我国烧结余热发电发展情况
摘 要: 介绍了钢铁企业烧结余热发电技术的发展现状、存在的问题, 提出了一种带有蓄热
式蒸汽过热炉的新型烧结余热发电系统方案, 其特点是通过补燃少量钢厂自 有的煤气而大幅度
提高烧结余热发电效率, 并从理论基础、经济效益和投资回报上对该方案的实施进行了分析。
关键词: 烧结余热发电; 蒸汽 过热炉; 蓄热式
中图分类号: TK11+ 5
文献标识码: B
从 事 锅 炉 产 品 设 计、 研 发 工 作, 现 任 长 沙 锅炉厂 有限 责任 公司 技术中心室主任。
0 引言
我国钢铁产业近十年来发展迅猛, 取得了长足 的进步, 钢铁年 产量自 1996年 起连续蝉联世界第 一, 消费量也名列世界之首, 成为我国的支柱产业之 一, 对国家经济增长的贡献率不断提升。同时, 随着 我国经济的快速增长, 资源能源消费约束明显显现, 能源供求矛盾日益突出, 高污染、高能耗的特点也使 钢铁工业在防污减排、节能降耗等方面承受着一定 的压力。
1 烧结余热发电的发展
烧结余热发电, 是通过余热锅炉来生产蒸汽回 收烧结机尾落矿风箱及烧结冷却机密闭段的烟气余 热推动汽轮发电机组做功发电。其意义如下:
( 1) 利用烧结环冷机烟气 余热发电, 部分代替
来自电网的以化石燃料为能源的供电量, 从而起到 减少温室气体排放效果。
( 2)降低烧结工序能耗, 促进资源节约; 降低产 品单位价格, 使企业更具竞争优势。
M Pa、450 时, 汽轮机理论排汽焓为 H p = 2 248. 69 kJ/ kg; 当汽轮机进汽参数为 1. 7 M Pa、450 时, 汽 轮机理论排汽焓为 H p = 2 279. 31 kJ /kg。由于汽轮 机的发电功率是汽轮机进汽焓与排汽焓的差值, 因 此排汽焓越低, 发电能力也就越大。
因此可以通过提高汽轮机进口蒸汽的压力和温 度来提高烧结余热发电系统发电效率。 3. 2 新型烧结余热发电系统
烧结机
装机容量
马鞍山钢铁股份有限公司 济南钢铁股份有限公司
2台 300 m2 1台 320 m2
17. 5MW 8. 2 MW
昆明钢铁集团有限责任公司 武汉钢铁 (集 团 )有限责任公司
1台 130 m2 3台 435 m2
5 MW 33 MW
安阳钢铁集团有限责任公司
1台 360 m2 1台 400 m2
( 1. Changsha Bo iler P lant Co. L td, Changsha 410114, Ch ina;
2. L ianyuan Iron& Steel G roup Co. L td, L oud i 417009, Ch ina)
第 一 作 者: 徐 树 伟 ( 1971 - ), 工 程 师, 1994年毕业于湘 潭大 学 机 械 工 程 系, 长 期
破, 为钢铁行业余热回收创造了良好的条件。 在这样的形势和技术条件下, 一些有远见的钢
铁企业 (见表 1), 迅速启动各种余热回收项目, 不但 完成了钢铁企业的节能降耗任务, 同时也为企业创 造可观的经济效益。
序号 1 2 3 4
5
6 7 8 9
10
表 1 部分钢 铁企业已投运的烧结余热发电项目
钢铁企业
3 烧结余热发电技术发展探讨
2009年 12月 29日工业和信息化部推出 #钢铁 企业烧结余热发电技术推广实施 方案 ∃, 该方案计 划用 3年 ( 2010~ 2012年 )时间, 投资超过 50亿元,
∀ 探讨园地 ∀
钢铁企业烧结余热发电技术发展探讨
47
在全国 37家重点钢铁企业 82台烧结机上推广实施 烧结余热发电技术。
D iscussion on Developm ent of Technology of Sintering W aste H eat G eneration in Iron and Steel Industry