锂离子电池用铜箔的质量管理
国家标准《锂离子电池用压延铜箔》编制说明

国家标准GB /T XXXX-XX《锂离子电池用压延铜箔》(讨论稿)编制说明《锂离子电池用压延铜箔》标准起草小组二○一六年五月国家标准《锂离子电池用压延铜箔》(讨论稿)编制说明一、工作简况1、任务来源锂离子电池是最新发展起来的绿色能源,也是我国能源领域重点支持的高新技术产业。
压延铜箔是作为锂离子电池负极集流体的主要材料,其生产技术的发展和性能参数将直接影响锂离子电池的制作工艺、性能和生产成本。
目前国外压延铜箔的生产企业主要有:日本日矿金属(Nippon mining)、日本福田金属箔粉公司(Fukuda)、日立电线公司(Hitachi cable)、美国奥林黄铜(Olin Brass)等。
国内菏泽广源铜带有限公司、山东天和压延铜箔有限公司、中色奥博特铜铝业有限公司等逐渐开展锂离子电池用压延铜箔的研发与生产,形成规模化、行业化,且市场需求强劲。
国内主要生产锂离子电池企业有深圳比亚迪、天津捷威动力、天津力神、中航锂电、国联动力、深圳比克电池等百余家,对压延铜箔的使用及工艺性能具备深入的了解和掌握。
在生产企业和使用企业建立稳定供需关系的基础上,可共同对压延铜箔行业标准的技术内容和指标进行确定。
本标准制订的目的主要是规范锂离子电池用压延铜箔的生产与供货,为锂离子电池专用压延铜箔生产企业提供质量控制依据,而且为锂离子电池生产企业采购专用压延铜箔提供参考依据。
根据国标委综合〔2015〕59号和有色标委[2015]29号《关于转发2015年第二批有色金属国家、行业标准制(修)订项目计划的通知》,其中序号59(项目编号“20152292-T-610”)《压延铜箔》国家标准由菏泽广源集团山东天和压延铜箔有限公司、安徽鑫科新材料股份有限公司、中色奥博特铜铝业有限公司、绍兴市力博电气有限公司等负责起草,完成年限为2018年9月。
2、承担单位简况菏泽广源铜带有限公司及山东天和压延铜箔有限公司为菏泽广源集团核心企业。
依托集团公司近30年铜带箔技术积累、人才积累和生产研发平台技术创新能力,引进了世界先进水平的高精电子压延铜箔生产设备和尖端实验检测仪器,建成了国内首条高精电子压延铜箔生产线,主要生产厚度0.006mm以上、宽度650mm以内的高精电子压延铜箔,年生产能力5000吨,是集高精电子压延铜箔产品生产、研发、销售、服务为一体的专业化生产企业。
DB 44-T 837-2010锂离子电池用电解铜箔

Ra或Rz的算术平均值,准确至0.1μm。 _________________________________
7
8 包装 标志 贮存及运输
8.1 包装 卷状铜箔应紧实地卷在轴芯上,用防潮材料密封后装入包装箱中。每卷铜箔的重量由供需双方商定,
每卷的接头数不应超过1个。接头应该有清晰、耐久的标识。 先用密封材料包装,然后装入包装箱中。包装箱上应有防潮、防晒、防碰撞、防翻滚标志。每个包
装应足以保证在运输过程中不被损坏。 8.2 标志
ICS 77.120.30 备案号:
DB44
广东省地方标准
DB 44/T 837—2010
锂离子电池用电解铜箔
Electrolytic copper foil for lithium ion battery
2010 - 12 - 31 发布
2011 - 04 - 01 实施
广东省质量技术监督局 发 布
1
DB 44/T 837—2010
5.1.4 铜箔面清洁,不应有灰尘、油污、腐蚀物、盐类、油脂、指印、外来物及其它影响使用的外观 缺陷。
5.2 尺寸及公差
铜箔长度和宽度由供需双方协议。卷状箔的宽度允许偏差为(0~+2)mm。 5.3 性能要求
各种型号铜箔的单位面积质量、性能要求应符合表1规定。 表1 性能要求
≥99.8
≥245 ≥147 ≥2.5 ≥2.0
≥245 ≥147 ≥2.5 ≥2.0
≥245 ≥147 ≥2.5 ≥2.0
表面粗糙度,μm
光面 Rz
毛面 Ra
≤3.0 ≤0.3
≤3.0 ≤3.0 ≤3.0 ≤0.5 ≤0.8 ≤0.8
提升锂离子电池比能量的途径:微孔铜箔铝箔优势与控制要点
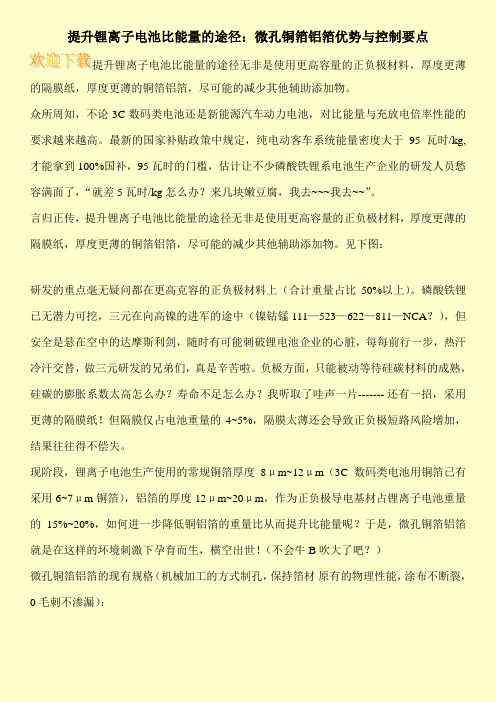
提升锂离子电池比能量的途径:微孔铜箔铝箔优势与控制要点提升锂离子电池比能量的途径无非是使用更高容量的正负极材料,厚度更薄的隔膜纸,厚度更薄的铜箔铝箔,尽可能的减少其他辅助添加物。
众所周知,不论3C数码类电池还是新能源汽车动力电池,对比能量与充放电倍率性能的要求越来越高。
最新的国家补贴政策中规定,纯电动客车系统能量密度大于95瓦时/kg,才能拿到100%国补,95瓦时的门槛,估计让不少磷酸铁锂系电池生产企业的研发人员愁容满面了,“就差5瓦时/kg怎么办?来几块嫩豆腐,我去~~~我去~~”。
言归正传,提升锂离子电池比能量的途径无非是使用更高容量的正负极材料,厚度更薄的隔膜纸,厚度更薄的铜箔铝箔,尽可能的减少其他辅助添加物。
见下图:研发的重点毫无疑问都在更高克容的正负极材料上(合计重量占比50%以上)。
磷酸铁锂已无潜力可挖,三元在向高镍的进军的途中(镍钴锰111—523—622—811—NCA?),但安全是悬在空中的达摩斯利剑,随时有可能刺破锂电池企业的心脏,每每前行一步,热汗冷汗交替,做三元研发的兄弟们,真是辛苦啦。
负极方面,只能被动等待硅碳材料的成熟,硅碳的膨胀系数太高怎么办?寿命不足怎么办?我听取了哇声一片------- 还有一招,采用更薄的隔膜纸!但隔膜仅占电池重量的4~5%,隔膜太薄还会导致正负极短路风险增加,结果往往得不偿失。
现阶段,锂离子电池生产使用的常规铜箔厚度8μm~12μm(3C数码类电池用铜箔已有采用6~7μm铜箔),铝箔的厚度12μm~20μm,作为正负极导电基材占锂离子电池重量的15%~20%,如何进一步降低铜铝箔的重量比从而提升比能量呢?于是,微孔铜箔铝箔就是在这样的环境刺激下孕育而生,横空出世!(不会牛B吹大了吧?)微孔铜箔铝箔的现有规格(机械加工的方式制孔,保持箔材原有的物理性能,涂布不断裂,0毛刺不渗漏):。
铜箔检验标准

1、目的
1.1明确描述合肥国轩高科动力能源有限公司所用原材料铜箔之规格。
1.2明确供应商的出厂检验所应包括的主体物理化学成分要求。
1.3本标准规定了锂离子电池用铜箔的各项主要指标的测定仪器、设备及测定步骤。
2、范围
2.1明确合肥国轩高科动力能源有限公司铜箔的采购规格。
2.2重要项:品质检测必须严格按照规格文件执行,不合格则直接退货。
2.3次要项:次要项检测不合格,可根据生产需求,由技术部给出判定是否使用。
3、参考文件(无)
注:带*的为重点抽检项。
铜箔负极材料在电池的应用

铜箔负极材料在电池的应用引言:电池是现代社会不可或缺的能源存储设备。
随着科技的进步和能源需求的增加,对电池的性能和稳定性提出了更高的要求。
铜箔作为一种常用的负极材料,在电池中具有重要的应用。
本文将讨论铜箔负极材料在电池中的应用及其优势。
一、铜箔负极材料的特性铜箔是一种由纯铜制成的薄片,具有良好的导电性和导热性。
铜箔的厚度通常在几个微米到几十个微米之间,可以根据电池的需求进行定制。
此外,铜箔还具有良好的韧性和可塑性,可以方便地加工成各种形状。
二、铜箔负极材料在锂离子电池中的应用1. 锂离子电池的构成锂离子电池是一种常见的二次电池,由正极、负极、电解液和隔膜等组成。
其中,负极是储存和释放锂离子的关键部分。
2. 铜箔负极材料的优势铜箔作为锂离子电池的负极材料具有以下优势:(1) 导电性好:铜箔具有优异的导电性,可以有效地传递电流,提高电池的工作效率。
(2) 良好的稳定性:铜箔在电池的工作过程中具有良好的稳定性,不会发生过多的氧化或腐蚀,延长电池的使用寿命。
(3) 高比能量:铜箔负极材料具有较高的比能量,可以储存更多的电荷,提高电池的续航能力。
(4) 适应性强:铜箔可以根据电池的需求进行定制,可以制备成不同形状和尺寸的负极材料,满足不同电池的设计要求。
三、铜箔负极材料在其他电池中的应用除了锂离子电池,铜箔负极材料还广泛应用于其他类型的电池中,如镍氢电池、铅酸电池等。
这些电池在不同的领域中有着重要的应用,而铜箔作为负极材料可以提供稳定的性能和良好的导电性,为电池的工作提供可靠的支持。
四、铜箔负极材料的发展趋势随着科技的进步和能源需求的增加,对电池性能的要求不断提高。
铜箔负极材料作为电池的重要组成部分,在不断发展和创新中。
目前,研究人员正在探索更好的制备方法和改进铜箔的性能,以提高电池的能量密度和循环寿命。
未来,随着新能源技术和电动汽车的发展,铜箔负极材料在电池领域的应用前景将更加广阔。
结论:铜箔负极材料在电池中具有重要的应用,其优异的导电性和稳定性使其成为锂离子电池和其他类型电池的理想选择。
锂离子电池制造工艺及各工序品质控制要点

锂离子电池制造工艺及各工序品质控制要点1.引言1.1 概述锂离子电池作为一种高效、轻便且可靠的电力储存装置,广泛应用于手机、电动汽车、无人机等领域。
随着市场需求的增长和技术进步,锂离子电池制造工艺也在不断改进和完善。
本文将重点探讨锂离子电池制造工艺及各工序品质控制要点,并结合品质监控技术应用案例分析,为相关行业提供有益的参考和指导。
1.2 研究背景随着科学技术的不断发展,人们对新能源的需求越来越迫切。
锂离子电池由于其高能量密度、长寿命以及环境友好的特点,成为了新能源领域最具潜力的能量转换和储存设备之一。
然而,在实际生产过程中,由于工艺参数和原材料质量等因素的影响,锂离子电池存在一些品质问题,如容量衰减、内阻增加等。
因此,研究锂离子电池制造工艺及各工序品质控制要点,对于提高产品品质和性能具有重要意义。
1.3 目的和意义本文旨在系统地介绍锂离子电池制造工艺及各工序品质控制要点,并探讨传统监控技术与先进监测技术的应用案例。
具体目标如下:1) 概述锂离子电池制造工艺的步骤总览,包括正极材料制备、负极材料制备等关键工序;2) 分析各工序品质控制的概述,重点关注切割与成型工艺控制要点、电解液充注工序控制要点等;3) 通过案例分析,比较传统监控技术与先进监测技术在品质监控中的应用优劣;4) 总结研究结果并展望未来锂离子电池制造领域可能的发展方向。
通过本文的撰写和发布,期望能够为锂离子电池行业相关从业人员和研究者提供一份全面而有实际指导意义的参考资料,进一步推动相关技术的发展和创新。
同时,也为其他新能源领域的生产工艺和品质控制提供借鉴与启发。
2.锂离子电池制造工艺:2.1 步骤总览:锂离子电池的制造过程通常包括正极材料制备、负极材料制备、电解液配方及充注、装配以及封装等步骤。
这些步骤相互关联,每个步骤的质量控制都非常重要,以确保最终产品的性能和安全性。
2.2 步骤一: 正极材料制备:正极材料是锂离子电池中的重要部分,其性能直接影响到电池的容量和循环寿命。
锂电池铜箔简介介绍
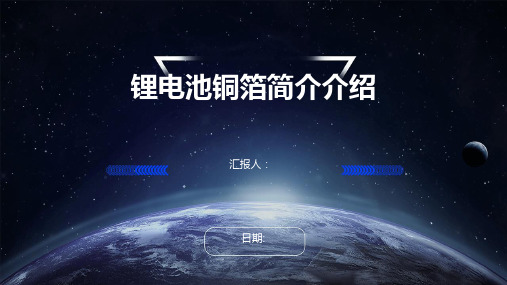
在电池充放电过程中,铜箔需要 保持稳定的导电性能,避免因温 度变化引起的电阻波动。
锂电池铜箔的机械性能
抗拉强度
锂电池铜箔应具有一定的抗拉强 度,以适应电池生产过程中的各
种应力。
延伸率
良好的延伸率可以确保铜箔在电池 组装过程中不易断裂,提高生产效 率。
耐折弯性
铜箔应能够承受一定程度的折弯而 不损坏,以确保电池结构的完整性 。
铜箔。
主要步骤
溶液配制、电解沉积、铜箔剥离 、清洗干燥等。在这个过程中, 需要严格控制电流密度、温度、 溶液浓度等参数,以保证铜箔的
质量和性能。
优点
制造工艺相对简单,成本较低, 适用于大批量生产。
压延铜箔制造工艺
原理
通过压延机对铜坯进行多次高压轧制,使铜坯逐渐变薄, 从而形成铜箔。这种方法能够制造出表面平整、厚度均匀 的铜箔。
锂电池铜箔需要具备良好 的压延性、切割性等加工 性能,以适应电池制造过 程中的各种工艺要求。
锂电池铜箔的市场现状与发展趋势
市场现状
随着新能源汽车、智能手机等市场的快速发展,锂电池需求大幅增加,带动了锂电池铜箔市场的快速 增长。目前,全球锂电池铜箔市场已经形成了一定的产业规模,主要集中在中国、日本、韩国等地。
政策扶持
政府可以制定相关政策,对实施环保生产 、开展锂电池铜箔回收和再生利用的企业
给予一定的政策支持和经济激励。
社会参与
加强环保宣传,提高公众环保意识,鼓励 消费者选择环保型锂电池铜箔产品,形成 绿色消费氛围。
THANKS
感谢观看
机械性能测试
采用四探针法、电阻法等方法对铜箔的导 电性能进行测试,确保产品符合标准要求 。
利用拉伸试验机、折弯试验机等设备对铜 箔的抗拉强度、延伸率、耐折弯性等指标 进行评估。
关于锂离子电池用铜箔

为什么负极要用铜/镍箔而正极要用铝箔呢?1.采用两者做集流体都是因为两者导电性好,质地比较软(可能这也会有利于粘结),也相对常见比较廉价,同时两者表面都能形成一层氧化物保护膜。
2. 铜/镍表面氧化层属于半导体,电子导通,氧化层太厚,阻抗较大;而铝表面氧化层氧化铝属绝缘体,氧化层不能导电,但由于其很薄,通过隧道效应实现电子电导,若氧化层较厚,铝箔导电性级差,甚至绝缘。
一般集流体在使用前最好要经过表面清洗,一方面洗去油污,同时可除去厚氧化层。
3.正极电位高,铝薄氧化层非常致密,可防止集流体氧化。
而铜/镍箔氧化层较疏松些,为防止其氧化,电位比较低较好,同时Li难与Cu/镍在低电位下形成嵌锂合金,但是若铜/镍表面大量氧化,在稍高电位下Li会与氧化铜/镍发生嵌锂发应。
而铝箔不能用作负极,低电位下会发生LiAl合金化。
4.集流体要求成分纯。
Al的成分不纯会导致表面膜不致密而发生点腐蚀,更甚由于表面膜的破坏导致生成LiAl合金负极集流体不能用铝箔的,要用铜箔。
正极用铝箔。
原因在于:1、采用两者做集流体都是因为两者导电性好,质地比较软(可能这也会有利于粘结),也相对常见比较廉价,同时两者表面都能形成一层氧化物保护膜。
2、铜表面氧化层属于半导体,电子导通,氧化层太厚,阻抗较大;而铝表面氧化层氧化铝属绝缘体,氧化层不能导电,但由于其很薄,通过隧道效应实现电子电导,若氧化层较厚,铝箔导电性级差,甚至绝缘。
一般集流体在使用前最好要经过表面清洗,一方面洗去油污,同时可除去厚氧化层。
3、正极电位高,铝箔氧化层非常致密,可防止集流体氧化。
而铜箔氧化层较疏松些,为防止其氧化,电位比较低较好,同时Li难与Cu在低电位下形成嵌锂合金,但是若铜表面大量氧化,在稍高电位下Li会与氧化铜发生嵌锂发应。
AL箔不能用作负极,低电位下会发生LiAl合金化。
4、集流体要求成分纯。
AL的成分不纯会导致表面膜不致密而发生点腐蚀,更甚由于表面膜的破坏导致生成LiAl合金。
锂电池用电解铜箔电解液质量控制要点

锂电池用电解铜箔电解液质量控制要点摘要:锂离子动力电池用电解铜箔因其超薄、高强度等高性能要求,对生产工序提出了更高要求。
本文通过电解液中主要物质的浓度、流量、添加剂、电解液温度、洁净度和系统循环的均匀性等多方面去分析溶铜工序的各主要质量控制要点,从而在根源上改善锂电池用电解铜箔产品的性能。
关键词:电解铜箔,电解液,作用,质量控制一、溶铜工序的作用:锂离子动力电池用电解铜箔在锂电池内既当负极材料的载体,又当负极电子收集与传输体,要求铜箔必须有良好的导电性和良好的耐蚀性,能均匀地涂敷负极材料而不脱落。
随着锂离子电池朝着高容量化、薄型化、高密度化、高速化方向发展,铜箔也朝着具有超薄、低轮廓、高强度、高延展性等高性能的方向发展。
因此对铜箔生产的各个主要工序“溶铜→生箔→表面处理→分切”提出了更高的质量控制要求。
溶铜工序是铜箔生产的第一步,主要是硫酸铜电解液的生产、过滤、循环和添加剂的加入,这是整个生产中最基础环节,也是生箔质量是否成败的根源和决定性因素。
在生产工艺质量控制过程中,如生箔批量性出现白点、厚度不均、毛刺、针孔、粗糙度不符、卷曲过大、抗拉强度和延伸率过低等质量问题,首先应考虑是溶铜工序的质量控制是否有偏差,并分别从电解液的温度、铜离子和硫酸的浓度、电解液的洁净度、添加剂的添加量、电解液的流量、整个系统电解液的均匀性等各方面综合分析。
二、电解液的工艺特点:电解液的各项工艺指标是一个非常重要的参数,很大程度上决定着铜箔的产品质量。
电解铜箔的生箔过程是动态的、不间断的,随着铜箔电沉积的不断发生,电解液里面的铜离子和添加剂等不断被消耗,反应后的贫铜电解液需要和微量添加剂、溶铜产生的硫酸铜溶液进行不断地循环,从而保持各物质含量的均匀性和稳定性。
但因铜料和硫酸等的不断加入,在补充电解液的同时也带入了一定的杂质,同时添加剂在高温条件下反应分解也会产生杂质。
锂电池铜箔因其高性能要求,对电解液的洁净度也有较高要求。
锂电池铜箔质量标准

锂电池铜箔质量标准
锂电池铜箔的质量标准通常包括以下几个方面:
1. 厚度:锂电池铜箔的厚度通常在9-20微米之间。
具体的厚度要符合相关的国家标准或者客户的要求。
2. 表面质量:锂电池铜箔的表面应平整光滑,不得有明显的凹凸、划痕和氧化。
3. 电阻率:锂电池铜箔的电阻率应低,一般要求在1.7微欧姆·厘米以下。
4. 强度:锂电池铜箔的强度要达到一定的要求,确保其在使用和加工过程中不易断裂变形。
5. 化学成分:锂电池铜箔的化学成分应符合相关标准,特别是有关杂质元素的含量应控制在合理范围内。
以上是一般锂电池铜箔的质量标准,具体的标准可以根据不同国家的标准、行业标准或者客户的要求进行规定。
锂离子电池铜箔翘曲的检验方法

锂离子电池铜箔翘曲的检验方法全文共四篇示例,供读者参考第一篇示例:锂离子电池是现代电子产品中常用的能量储存装置,其性能直接影响着设备的续航能力和安全性。
而锂离子电池的正极材料常用的是带有导电性能的铜箔,用于连接电池内部的电荷传导。
但是在生产和使用过程中,铜箔可能会出现翘曲或弯曲的情况,从而影响电池的性能和安全性。
对锂离子电池铜箔翘曲情况进行准确可靠的检验至关重要。
一、铜箔翘曲的危害与原因锂离子电池铜箔的翘曲会导致以下问题:1. 造成电池内部电荷传导不良,影响电池的充放电性能,降低电池的循环寿命;2. 导致电极与电解液之间的隔离膜受损,增加电池的短路风险,可能引发火灾或爆炸事故。
铜箔翘曲的原因主要包括以下几点:1. 制备工艺不当:在铜箔生产或锂离子电池制备过程中,存在材料热胀冷缩或机械应力导致的变形;2. 储存和运输过程中的挤压或碰撞;3. 设备安装或使用不当造成外力作用。
二、锂离子电池铜箔翘曲的检验方法为了及时准确地检测出锂离子电池铜箔的翘曲情况,保证电池的质量和安全性,需要建立相应的检验方法。
下面介绍几种常用的检验方法:1. 目视检查法目视检查法是最简单也是最直观的一种检验方法。
通过目视观察铜箔表面的平整度和平整度,检查是否有翘曲或弯曲现象。
这种方法操作简便,但受人员主观因素影响较大,不能准确判断铜箔的微小翘曲情况。
2. 手感触摸法手感触摸法是一种经验性很强的检验方法。
通过手感触摸铜箔表面,检查是否有明显的凹凸不平或弯曲,来判断铜箔是否存在翘曲。
这种方法需要有一定的经验积累和训练,适用于对于翘曲情况的初步筛查。
4. 硬度测量法硬度测量法是一种间接检验方法。
通过对铜箔表面硬度的测量,来间接判断其是否存在翘曲或弯曲。
翘曲的铜箔硬度通常会有所不同,可以通过硬度测量仪器进行快速准确的判断。
5. 影像分析法影像分析法是一种高精度的检验方法。
通过高分辨率的影像设备拍摄铜箔表面的影像,采用图像处理软件对图片进行分析处理,检测铜箔的平整度和平面度,精确判断其是否存在翘曲问题。
锂电铜箔防氧化抗腐蚀处理技术研究现状
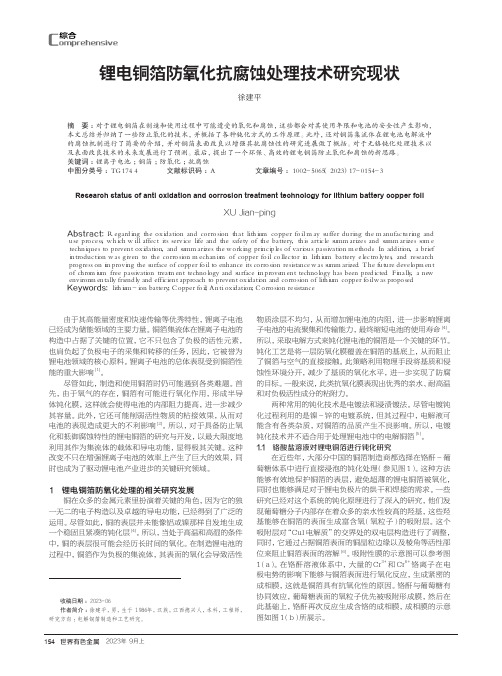
154锂电铜箔防氧化抗腐蚀处理技术研究现状徐建平(江西省江铜铜箔科技股份有限公司,江西 南昌 330096)摘 要:对于锂电铜箔在制造和使用过程中可能遭受的氧化和腐蚀,这些都会对其使用年限和电池的安全性产生影响,本文总结并归纳了一些防止氧化的技术,并概括了各种钝化方式的工作原理。
此外,还对铜箔集流体在锂电池电解液中的腐蚀机制进行了简要的介绍,并对铜箔表面改良以增强其抗腐蚀性的研究进展做了概括。
对于无铬钝化处理技术以及表面改良技术的未来发展进行了预测。
最后,提出了一个环保、高效的锂电铜箔防止氧化和腐蚀的新思路。
关键词:锂离子电池;铜箔;防氧化;抗腐蚀中图分类号:TG174.4 文献标识码:A 文章编号:1002-5065(2023)17-0154-3Research status of anti oxidation and corrosion treatment technology for lithium battery copper foilXU Jian-ping(Jiangxi JJC Copper Foil Technology Co., Ltd,Nanchang 330096,China)Abstract: Regarding the oxidation and corrosion that lithium copper foil may suffer during the manufacturing and use process, which will affect its service life and the safety of the battery, this article summarizes and summarizes some techniques to prevent oxidation, and summarizes the working principles of various passivation methods. In addition, a brief introduction was given to the corrosion mechanism of copper foil collector in lithium battery electrolytes, and research progress on improving the surface of copper foil to enhance its corrosion resistance was summarized. The future development of chromium free passivation treatment technology and surface improvement technology has been predicted. Finally, a new environmentally friendly and efficient approach to prevent oxidation and corrosion of lithium copper foil was proposed.Keywords: lithium-ion battery; Copper foil; Anti oxidation; Corrosion resistance收稿日期:2023-06作者简介:徐建平,男,生于1986年,汉族,江西德兴人,本科,工程师,研究方向:电解铜箔制造和工艺研究。
锂离子电池用铜箔的质量管理

经过近 2 0 年 的技 术储 备 ,中 国 的锂 离 子 电池 工 艺 已 经 完全 成 大 , 会 使 锂 离 子 电池 制 造 T序 的涂 覆 厚 度 出现 波 动 , 造 成 极 片 厚 度 熟, 锂 离子 电池 不 仅 应 用 于 手机 等数 码 产 品 , 更 是 广 泛 的用 于 私 家 不 均 , 影 响 电池 之 间 的一 致 性 。铜 箔 基 重 管控 方 法 为 : 每 日安 排巡 车和 大 巴车 系统 , 使 得 电 动汽 车走 进 了 千家 万 户 。 中 国 自主 品牌 的 检. 每 4小 时 对铜 离 子浓 度 巡 检一 次 , 根 据巡 检 结 果 , 及 时对 铜 离 子 电动 汽车 代 表 比亚 迪 , 更 是随 着 国 家 主席 的 出访 , 走出国门, 走 向世 浓 度进 行 优化 ;安 排 检 验 人员 巡 检 生箔 工 序 的 电流 并进 行 记 录 , 当 界 。铜 箔 作 为锂 离 子 电池 的重 要 原 材 料 , 在 锂 离 子 电池 中 作 为 负极 生 箔 电 流 H I 现波动时 , 对 铜 箔 基 重进 行 检 验 , 检 验 合 格 后 方 可 转 入 集流体, 充 当负 极 电子 流 的 收 集与 传 输 『 I - , 在2 0 1 3 年 之 前 基 本依 赖 下 工序 ; 对 员 工进 行 检验 丁 作 的培 训 , 每 生 产一 卷 铜箔 , 安排 检 验 员 于 日韩进 口 , 进 口铜 箔 价 格高 , 交期 不 确 定 , 严重 制 约 了锂 离 子 电池 对 铜箔 的基重 进行 检 测 , 将 检测 结果 记录在 案 。 的发 展 。 车用 锂离 子 电 池 的迅猛 发 展 , 推 动 了铜 箔 国产 化 的进 度 . 国 2 . 2 表 面 粗糙 度 不均 产 铜 箔化 可 以大 幅 降低 锂 离 子 电池 的成 本 ,使 其 更 具 市场 竞 争力 。 表 面粗 糙 度 是指 加 工表 面 上 具有 较 小 的 距 和 峰 谷 所组 成 的 但 是 国产 铜 箔 在 生 产工 艺 和 制 造 过 程控 制上 . 尚待 完 善 , 成 品率 较 微 观 几何 形状 特性 。 国家标 准 要求 动 力 电池使 用 的铜 箔 的粗 糙度 R 低, 铜箔 的行 业 成 品率 水 平 在 8 0 %左 右 , 所 以 提升 国产 电解 铜 箔 的 值 ≤2 u n。 r 如果 铜 箔 的粗糙 度 超 } 1 I 标准 , 会 造 成锂 离 子 电池 的涂 覆 工 质 量 迫在 眉 睫 。 艺异 常 ,表 现 为 :涂 覆 后 的极 片外 观 有 凹 坑 。对 粗 糙 度 1 . 4 u n 和 r 1 电解 铜箔 的外观 不 良及 其 管控 方 法 2 . 1 u m 的铜 箔进 行 S E M 检测 , 从S E N 图 片可 以 看 出 , 不 同粗 糙 度 的 电解 铜 箔 在 制 造 过 程 和存 储 过 程 由于 加 T 工 艺 和 存 储 环 境 的 铜 箔 的表 面状 态 存 在 明 差 异 . 粗糙 度 为 1 . 4 u m的 铜 箔( 图I ) , S E M 不同 , 往 往会 出现 外观 花纹 和色 差 , 以及 外 观 凹 凸点 的质 量 问题 。 下 图 片 湿示 出 铜 箔 外 观 平 整 ; 粗糙度为 2 . 1 u m 的铜 箔 ( 陶2 ) , S E M 图 面 逐个 阐述 外观 的影 响 因素 、 失效 模 式 及管 控 方 法 。 片 显示 出铜 箔 外 观 有 明 显 凹坑 点 , 经 过 涂 覆 工 艺加 工后 , 涂 覆 后 的 1 . 1外观 花 纹 和色 差 极 片外 观 凹坑 问题 更加 严重 。 表 面 凹坑 的极 片做 成 的锂 离 子 电池存 铜箔 的 外 观花 纹有 多 种 表 现形 式 , 有 条 纹 状 花纹 、 人字 形 花纹 、 在 一 致性 差 , 内 阻 高 等问 题 口 I 。所 以 铜 箔制 造 过 程 应 控制 粗糙 度 ≤ 边 缘 局 部 条状 花纹 ,这 些 不 良品 的 产生 和铜 箔 的 多 个 制 造 工 序 有 2 u m。 控 制 粗糙 度 的措 施 主要 有 : 每3 个 月对 铜箔 的 阴极 辊进 行 离线 关 。生箔 过 程 的 防氧化 后 的 水洗 能 力 不 足 或者 喷 嘴 堵 塞 , 防 氧化 电 打 磨 . 打 磨 后 用 粗糙 度 仪 器 测 试 阴极 辊 的 粗糙 度 , 当阴 极 辊 的 粗 糙 流 不 稳 定 ,防 氧化 液 浓 度 低 等 都 会造 成 外 观 花 纹 以及 外 观 色 差 问 度 达到 出厂要 求 时 , 方可 投 入生 产 。 除 了对 阴极 辊进 行 离线 打 磨 , 还 题。 铜 箔分 切 设 备 的辊 表 面脏 污 、 设备 漏 油 、 员工 用 手 直接 触 摸铜 箔 需 要增 加 在线 打 磨砂 轮 , 在 线打 磨 的砂 轮 的转 速 和功 率 等参 数 都 纳 都 会 造成 铜 箔外 观 脏 污 。 这 类不 良电解 铜 箔 会造 成锂 离子 电 池 的极 入 检验 员 的检 验 范 围 , 并 如 实 记 录 。此外 还 需 对产 出的铜 箔 进行 粗 片粘 结力 不 均 匀 , 影 响 锂 离子 电池 的循 环性 能 。 因此, 要 解 决 这类 外 糙 度 的测 试 , 测 试 频 次 为一 卷 测 试一 次 , 一旦 发现 有 不 良品 , 立 即 进 观 问题 , 需要 做 下 面几 项 控制 : 控 制 生 箔 工 序 的 电流 , 使 电 流 值稳 定 行 降级 处 理 。 在 工 艺范 围内 ; 控 制 防 氧 化液 的配 比 , 使 得浓 度 在 合 格 范 围 ;生产 过 程 中每 隔 1 小时 对 水 洗 喷嘴 进 行巡检 , 发现 喷嘴 堵 塞 , 立 即维 修 设 备 , 并 对 不 良 铜 箔 进行 标 示 , 在 分切 时将 不 良品 去 除 , 防 止不 良 铜 箔 流 出到 客 户手 里 。 I - 2 外 观 凹凸 点 铜箔 制 造工 艺 的生 箔 和 分 切工 序 对环 境 洁净 度要求较高 , 锂 离 子 电池 用 铜 箔 , 非常 薄 , 硫 酸 铜 溶 液 中 的异 物 和 空气 中 的粉 尘 ,以及 收 卷 轴上 的 异 物 都能 造 成铜 箔 表 面 出现 凹 凸点 。这类 铜 箔 在 制 作 锂离 子 电 池 时 ,会发 生 涂 布机 的喷 头 剐蹭 到 凹凸 点致 使 涂 覆工 序 断带 , 生产停产 , 轻微的凹凸 图 1 R z =1 . 4 u n r 点, 不容 易被 员 工 识别 , 涂 覆极 片后 存 在 导 电性 不 3 结束 语 致 的 问题 , 做 成锂 离 子 电池 后 , 会造 成 电 池 内阻 高 。 所 以铜 箔 的制 本 文对 铜 箔质 量 问 题进 行 了详 细 说 明 . 对 质量 问 题 的产 生 原 因 造 过 程 要 严 格 控 制粉 尘 , 具体 做 法 为 : 在溶 铜 工 序 增 加 3道 精 密 过 为铜 箔 制造 业 降 低铜 滤控制 , 彻底 滤 掉 电解 液 中 的杂 质 ; 在生 箔 和分 切 工 序 安 装 粉 尘 测 和 失效 模 式 以及 管控 方 法进 行 了 分析 和 研究 , 提 升 铜 箔 的成 品率 , 优 化锂 离 子 电 池 的 加 工 _ ] 艺提 试仪 , 使 得 车 间粉 尘 度 在 十 万级 以 内 ; 规范 车 间员 工 通 道 和 物 流 通 箔 的 质 量 问题 , 道, 将 两 种通 道 分 开管 控 。 以上 方 法 的执 行 , 可 以有 效 降低 异 物造 成 供 了强 有 力 的保 障 。
铜箔质量管理制度

铜箔质量管理制度第一章总则第一条为规范公司铜箔产品的生产加工工艺和质量管理工作,保证产品质量,确保生产安全,提高产品质量,确保产品合格率,以推动公司铜箔产品质量提升,增强市场竞争力,特制定本制度。
第二条本制度适用于公司铜箔产品的生产加工和质量管理工作。
第三条公司铜箔产品的质量管理应遵守国家有关法律法规和质量管理体系的要求,质量管理部门负责铜箔产品的质量管理。
第二章质量管理体系第四条公司应建立和实行完整的质量管理体系,包括质量管理手册、程序文件、作业指导文件等。
第五条完善的质量管理体系应包括:(一)质量目标和政策(二)组织结构和职责(三)质量管理程序(四)质量保证和控制(五)过程改进(六)质量管理记录的管理(七)内部质量审核(八)管理评审第六条公司应将质量管理体系应用于铜箔产品的生产和服务过程中,确保产品和服务满足客户要求。
第三章质量目标和政策第七条公司应制定符合国家有关法律法规和标准要求的质量目标和政策,并签署承诺书,以此为依据开展质量管理工作。
第八条公司质量目标应包括:(一)提高产品质量,确保产品合格率100%(二)降低产品质量损耗率(三)提高生产效率,减少生产成本(四)不断改进产品和工艺技术,提高产品性能和品质第九条公司质量政策应包括:(一)客户满意是公司质量管理工作的最终目标(二)全员参与,持续改进(三)遵守法律法规,保证产品质量和安全(四)强调预防为主,加强过程控制第四章组织结构和职责第十条公司应设立质量管理部门,负责铜箔产品的质量管理工作。
第十一条质量管理部门应定期组织培训,提升员工的质量意识和技能,促进质量管理体系的实施。
第十二条质量管理部门的职责包括:(一)制定质量管理制度,推动落实(二)制定产品质量检验标准和方法(三)组织开展产品质量检验和监控(四)分析产品质量数据,及时发现问题和改进措施第五章质量管理程序第十三条公司应建立完整的质量管理程序,包括但不限于:(一)从原材料采购到成品出厂的全过程质量控制(二)产品质量检验和检测(三)不合格品处理(四)产品质量追溯和质量记录保留第十四条公司应制定详细的质量管理程序文件,并对员工进行培训,确保程序的有效实施。
锂电铜箔用铜材品质规范

6.2.1 产 品 以 每 个 交 货 批 次 定 为 一 批 , 不 同 厂 家 不 能 混 放 。 分 批 验 收 。 6.2.2 应 按 简 单 随 机 抽 样 从 每 交 货 批 中 抽 取 作 为 对 应 交 货 批 中 的 抽 验 产 品 ,分 开 标 识 ,分 开 处 理 。 6.2.3 按 GB/2828.1-2013 正 常 检 验 水 平 Ⅱ AQL0.65 确 定 抽 样 方 案 和 检 验 水 平 。必 要 时 按 规 定 要 求 调整。 6.3 检验项目
Fe 0.0025
Zn 0.005
Sn 0.003
Bi 0.001
Ni 0.002
注:客户如对产品中其他杂质元素含量有特殊要求的由供需双方协商确定,并在合同中注明。
文件编号
页
码
电解铜箔用原铜材品质标准
版
次
生效日期 工 段
制订部门
4.2.1 铜 材 必 须 符 合 GB/T26572 — 20 11 《 电 子 电 气 产 品 中 限 用 物 质 的 限 量 要 求 》 和 欧 盟 WEEE&RoHS 法规等。 4.3 外观、表面质量
5.1 化 学 分 析 方 法 产 品 的 化 学 成 分 分 析 方 法 按 GB/T5121 规 定 进 行 。 5.2 外 观 、 表 面 质 量 检 查 方 法 外观、表面质量采用目视、触摸检测方法,必要时辅以干净干燥的白滤纸擦拭检测。 6 检验规则
6.1 检 查 和 验 收 6.1.1 每 交 货 批 应 由 供 方 质 量 检 验 部 门 进 行 检 验 ,保 证 产 品 质 量 符 合 本 标 准( 或 订 货 合 同 )规 定 。 6.1.2 需 方 可 对 来 料 按 本 标 准 规 定 实 施 检 验 , 必 要 时 可 以 委 托 第 三 方 权 威 机 构 鉴 定 。 如 检 验 结 果 与 本 标 准( 或 订 货 合 同 )的 规 定 不 符 ,公 司 应 在 收 货 7 日 内 向 供 方 反 馈 ,商 讨 处 理 对 策 。 RoHS 不 合 格物料必须退货。 6.1.3 未 列 入 公 司 合 格 供 应 商 的 供 货 拒 收 , 急 需 料 需 申 请 特 采 。 6.2 组批与抽样
- 1、下载文档前请自行甄别文档内容的完整性,平台不提供额外的编辑、内容补充、找答案等附加服务。
- 2、"仅部分预览"的文档,不可在线预览部分如存在完整性等问题,可反馈申请退款(可完整预览的文档不适用该条件!)。
- 3、如文档侵犯您的权益,请联系客服反馈,我们会尽快为您处理(人工客服工作时间:9:00-18:30)。
锂离子电池用铜箔的质量管理
车用锂离子电池的迅速发展使得电池行业对铜箔的质量要求越来越高。
铜箔作为锂离子电池的关键原材料,其质量水平严重影响着锂离子电池的加工工艺和锂离子电池的质量。
文章对铜箔质量问题进行了详细说明,对产生原因和质量管控方法进行了分析和研究,为优化锂离子电池的加工工艺、提升铜箔的质量和成品率提供了强有力的保障。
标签:锂离子电池;铜箔;质量管理
经过近20年的技术储备,中国的锂离子电池工艺已经完全成熟,锂离子电池不仅应用于手机等数码产品,更是广泛的用于私家车和大巴车系统,使得电动汽车走进了千家万户。
中国自主品牌的电动汽车代表比亚迪,更是随着国家主席的出访,走出国门,走向世界。
铜箔作为锂离子电池的重要原材料,在锂离子电池中作为负极集流体,充当负极电子流的收集与传输[1-3],在2013年之前基本依赖于日韩进口,进口铜箔价格高,交期不确定,严重制约了锂离子电池的发展。
车用锂离子电池的迅猛发展,推动了铜箔国产化的进度,国产铜箔化可以大幅降低锂离子电池的成本,使其更具市场竞争力。
但是国产铜箔在生产工艺和制造过程控制上,尚待完善,成品率较低,铜箔的行业成品率水平在80%左右,所以提升国产电解铜箔的质量迫在眉睫。
1 电解铜箔的外观不良及其管控方法
电解铜箔在制造过程和存储过程由于加工工艺和存储环境的不同,往往会出现外观花纹和色差,以及外观凹凸点的质量问题。
下面逐个阐述外观的影响因素、失效模式及管控方法。
1.1 外观花纹和色差
铜箔的外观花纹有多种表现形式,有条纹状花纹、人字形花纹、边缘局部条状花纹,这些不良品的产生和铜箔的多个制造工序有關。
生箔过程的防氧化后的水洗能力不足或者喷嘴堵塞,防氧化电流不稳定,防氧化液浓度低等都会造成外观花纹以及外观色差问题。
铜箔分切设备的辊表面脏污、设备漏油、员工用手直接触摸铜箔都会造成铜箔外观脏污。
这类不良电解铜箔会造成锂离子电池的极片粘结力不均匀,影响锂离子电池的循环性能。
因此,要解决这类外观问题,需要做下面几项控制:控制生箔工序的电流,使电流值稳定在工艺范围内;控制防氧化液的配比,使得浓度在合格范围;生产过程中每隔1小时对水洗喷嘴进行巡检,发现喷嘴堵塞,立即维修设备,并对不良铜箔进行标示,在分切时将不良品去除,防止不良铜箔流出到客户手里。
1.2 外观凹凸点
铜箔制造工艺的生箔和分切工序对环境洁净度要求较高,锂离子电池用铜
箔,非常薄,硫酸铜溶液中的异物和空气中的粉尘,以及收卷轴上的异物都能造成铜箔表面出现凹凸点。
这类铜箔在制作锂离子电池时,会发生涂布机的喷头剐蹭到凹凸点致使涂覆工序断带,生产停产,轻微的凹凸点,不容易被员工识别,涂覆极片后存在导电性不一致的问题,做成锂离子电池后,会造成电池内阻高。
所以铜箔的制造过程要严格控制粉尘,具体做法为:在溶铜工序增加3道精密过滤控制,彻底滤掉电解液中的杂质;在生箔和分切工序安装粉尘测试仪,使得车间粉尘度在十万级以内;规范车间员工通道和物流通道,将两种通道分开管控。
以上方法的执行,可以有效降低异物造成的铜箔凹凸点,提升铜箔的成品率。
铜箔在制造过程中,除了外观问题,还存在着基重、粗糙度等性能不良。
下面分別详细讲述两种性能不良的质量管控方法。
2 铜箔的性能不良及管控方法
2.1 基重不均
由于锂离子电池用的铜箔都比较薄,没有一种既精密又稳定的测试设备对铜箔的厚度进行测试,所以行业内普遍采用基重来表征铜箔的厚度。
铜箔行业的基重水平在±3%波动,如果铜箔基重波动大,会使锂离子电池制造工序的涂覆厚度出现波动,造成极片厚度不均,影响电池之间的一致性。
铜箔基重管控方法为:每日安排巡检,每4小时对铜离子浓度巡检一次,根据巡检结果,及时对铜离子浓度进行优化;安排检验人员巡检生箔工序的电流并进行记录,当生箔电流出现波动时,对铜箔基重进行检验,检验合格后方可转入下工序;对员工进行检验工作的培训,每生产一卷铜箔,安排检验员对铜箔的基重进行检测,将检测结果记录在案。
2.2 表面粗糙度不均
表面粗糙度是指加工表面上具有较小的间距和峰谷所组成的微观几何形状特性。
国家标准要求动力电池使用的铜箔的粗糙度RZ值≤2um。
如果铜箔的粗糙度超出标准,会造成锂离子电池的涂覆工艺异常,表现为:涂覆后的极片外观有凹坑。
对粗糙度1.4um和2.1um的铜箔进行SEM检测,从SEM图片可以看出,不同粗糙度的铜箔的表面状态存在明显差异,粗糙度为1.4um的铜箔(图1),SEM图片显示出铜箔外观平整;粗糙度为2.1um的铜箔(图2),SEM图片显示出铜箔外观有明显凹坑点,经过涂覆工艺加工后,涂覆后的极片外观凹坑问题更加严重。
表面凹坑的极片做成的锂离子电池存在一致性差,内阻高等问题[3]。
所以铜箔制造过程应控制粗糙度≤2um。
控制粗糙度的措施主要有:每3个月对铜箔的阴极辊进行离线打磨,打磨后用粗糙度仪器测试阴极辊的粗糙度,当阴极辊的粗糙度达到出厂要求时,方可投入生产。
除了对阴极辊进行离线打磨,还需要增加在线打磨砂轮,在线打磨的砂轮的转速和功率等参数都纳入检验员的检验范围,并如实记录。
此外还需对产出的铜箔进行粗糙度的测试,测试频次为一卷测试一次,一旦发现有不良品,立即进行降级处理。
3 结束语
本文对铜箔质量问题进行了详细说明,对质量问题的产生原因和失效模式以及管控方法进行了分析和研究,为铜箔制造业降低铜箔的质量问题,提升铜箔的成品率,优化锂离子电池的加工工艺提供了强有力的保障。
参考文献
[1]赵玲艳.锂离子电池用铜箔的应用与发展现状[J].有色金属加工,2008(01):8-10.
[2]牛慧贤.铜箔在锂离子电池中的应用与发展现状[J].稀有金属,2005(06):898-902.
[3]江鹏,于彦东.铜箔在锂离子二次电池中的应用与发展[J].中国有色金属学报,2012(12):3504-3510.。