新产品试产作业指引
新产品试产作业指导书

7.相关记录
8.附件
2、小批量试产产品在各工序必须尽快生产、流转。各工序负责人作好试产阶段的各工序数据记录;
3、现场QC必须依据工程部提供的资料和相关的控制标准进行各阶段的品质控制,并将生产异常情况作详实记录;
4、小批量试产完成后,由品管部召集生产、品管、工程相关人员召开新产品会议。若需改动产中结构和模具则由工程部、联系客户确认并完成;若生产条件不完善,则由生产部提出改善措施并执行;若控制器方法不完善,则由品管部改善并执行;
3、工程部立即将资料和相关技术部标准转品管部,由品管部审核无误后转发生产线;
4、工程部将试产型号的模具、治具、丝网等转交生产部,生产部根据生产的结构作出各种治具和人员的准备工作;
5、生产部安排机台和人员进行小批量的试产;
(二)、小ቤተ መጻሕፍቲ ባይዱ量生产过程控制:
1.小批量试产阶段,根据产品的大小和结构决定试产数量(一般控制器在50PCS~200PCS之内)
⑷、品管部准备好相关测量工具,并依据标准进行控制,收集生产中出现异常现象,并召开新产品试产总结会议;
4.定义:无
5.作业程序
(一)、小批量试产准备工作:
1、业务部根据客户的要求,向生产部提供产品的交货数量及交期;
2、生产部根据生产能力回复业务部交期及交货数量,并仓库中物料的数量,若不齐备,则立即做出采购计划交行采购部采购;
5、小批量试产完成OK后,则转为在批量的试产阶段。
(三)、在批量试产过程控制:
1、在批量的试产须体现周转快的特点,每道工序不得积压产品,随到随生产;
2、生产、控制过程中,必须依据新产品总结会上的决议改善和产控制;
3、针对特殊型号产品,各部门主和必须亲自跟进和完成;现场的QC必须做到步步跟进,时时记录,QC领班必须现场监督各工序的作业是否符合标准和程序。
NPI试产作业指引

NPI试产作业指引关键信息项:1、试产目的2、试产流程3、试产物料管理4、试产设备与工具5、试产人员安排6、试产质量控制7、试产数据记录与分析8、试产问题处理与改进9、试产完成标准1、目的11 明确新产品导入(NPI)试产的作业流程和要求,确保试产工作的顺利进行,为量产提供可靠的依据和保障。
2、适用范围21 适用于本公司所有新产品的 NPI 试产阶段。
3、职责分工31 研发部门311 负责提供新产品的设计图纸、技术规格书、测试标准等相关技术文件。
312 参与试产过程,解决技术问题,提供技术支持。
32 工程部门321 制定试产计划和工艺流程,设计工装夹具。
322 负责试产设备的调试和维护。
323 指导生产部门进行试产操作。
33 生产部门331 按照试产计划和工艺流程进行生产操作。
332 反馈试产过程中的问题和困难。
34 质量部门341 制定试产物料和产品的检验标准和检验计划。
342 负责试产物料和产品的检验工作。
343 统计分析试产过程中的质量数据,提出质量改进建议。
35 采购部门351 负责试产物料的采购工作,确保物料按时到位。
352 与供应商沟通协调,解决物料供应中的问题。
4、试产流程41 试产前准备411 研发部门完成新产品的设计开发,提交相关技术文件。
412 工程部门根据技术文件制定试产计划和工艺流程,准备工装夹具和设备。
413 采购部门完成试产物料的采购,确保物料按时到货。
414 生产部门安排试产人员,进行培训。
415 质量部门制定检验标准和检验计划。
42 试产实施421 生产部门按照试产计划和工艺流程进行生产操作。
422 工程部门现场指导,解决生产过程中的技术问题。
423 质量部门进行物料和产品的检验工作。
424 记录试产过程中的各项数据,包括生产数量、不良数量、不良原因等。
43 试产后总结431 召开试产总结会议,各部门汇报试产情况。
432 对试产过程中的问题进行分析和总结,提出改进措施。
【实用文档】试生产作业指引(QIST0402)
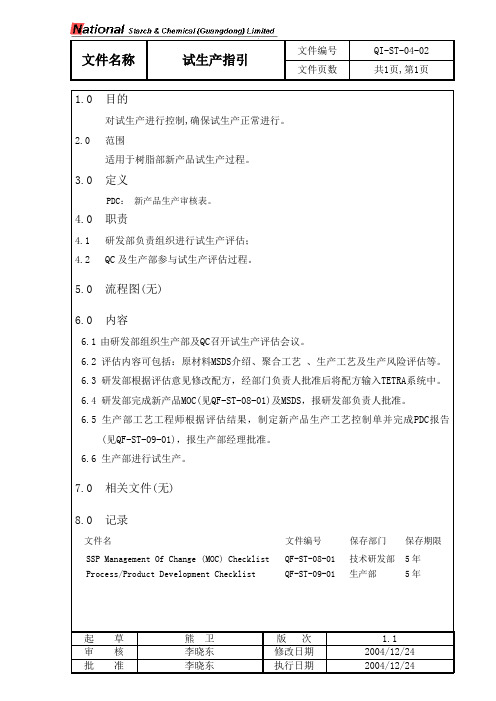
文件名称
试生产指引
文件编号 QI-ST-04-02 文件页数
共1页,第1页
起 草 熊 卫 版 次 1.1 审 核 李晓东 修改日期 2004/12/24 批 准
李晓东 执行日期 2004/12/24
1.0 目的
对试生产进行控制,确保试生产正常进行。
2.0
范围
适用于树脂部新产品试生产过程。
3.0 定义
PDC : 新产品生产审核表。
4.0 职责
4.1 研发部负责组织进行试生产评估; 4.2
QC 及生产部参与试生产评估过程。
5.0 流程图(无)
6.0 内容
6.1 由研发部组织生产部及QC 召开试生产评估会议。
6.2 评估内容可包括:原材料MSDS 介绍、聚合工艺 、生产工艺及生产风险评估等。
6.3 研发部根据评估意见修改配方,经部门负责人批准后将配方输入TETRA 系统中。
6.4 研发部完成新产品MOC(见QF-ST-08-01)及MSDS ,报研发部负责人批准。
6.5 生产部工艺工程师根据评估结果,制定新产品生产工艺控制单并完成PDC 报告
(见QF-ST-09-01),报生产部经理批准。
6.6 生产部进行试生产。
7.0 相关文件(无)
8.0 记录
文件名
文件编号
保存部门
保存期限
SSP Management Of Change (MOC) Checklist QF-ST-08-01 技术研发部 5年 Process/Product Development Checklist QF-ST-09-01 生产部 5年。
OPPO手机产品试产流程作业指导书

更改记录1 目的规范新机型试产的流程,明确试产过程中各职能块的工作职责及相互的协作关系,保证试产过程能有序和高效地进行,达到试产的目的。
2 范围适用于公司自主研发及合作开发(ODM)的新产品试产的全过程。
3 权责3.1 研发部:项目经理:负责对整个项目工作进度、试产时间进行总协调和确认;负责每周一次呈报《项目时间进度表》,按《新品资源检查表》提供试产资源;负责在试产前发布《试产申请单》,对试产过程的整体资源进行协调;组织项目成员在试产前两天召开试产产前沟通会,试产结束后2-3个工作日内召开试产总结沟通会;若试产计划变更或调整须及时通知相关人员。
并负责试产问题的跟踪落实工作。
研发项目组成员:项目成员如结构工程师、硬件工程师、软件工程师等根据各试产阶段的需求,负责提供如白油图、钢网文件、原理图、2D/3D图等生产技术工艺文件;试产当天负责到现场协助项目PE进行技术指导或确认;负责提供试产故障机分析、异常分析等必要的技术支持工作。
3.2 PMC部:PMC负责人:根据新机型的品质问题及工程准备情况确定具体试产日期,并在试产前两天发出新品试产时间安排以提醒相关人员;根据试产申请单合理安排试产计划,若试产计划变更需及时调整并通知相关人员;负责试产物料的跟进,确保试产所需的物料提前齐套;负责物料接收、备料、发料;负责在试产生产结束后统计公布尾料信息,并按试产总结会的物料处理方案对尾料及时进行处理。
3.3 工程部:项目PE:负责新品试产从准备工作、SMT、总装到试产总结等一系列试产全过程的主导。
依据《试产申请单》及时将试产要求通知到各生产相关人员,整体协调并提前确保试产各方面资源的提供到位。
负责跟踪落实外协SMT的试产准备情况,跟踪发现SMT试产问题并推动研发改善,完成SMT部分的试产总结报告。
负责在总装线试产前确认(临时)SOP、测试方案、工装治具、测试软硬件等,并组织生产成员参加产前准备沟通会。
在试产当天及时发现问题,收集试产相关信息数据;试产结束后及时整合试产问题点完成生产方面的试产总结报告;制定新品周报,推动跟踪试产问题的改善与落实;同时将试产中的工艺问题编入工程文件中,以进一步提高工程整体水平。
NPI试产作业指引
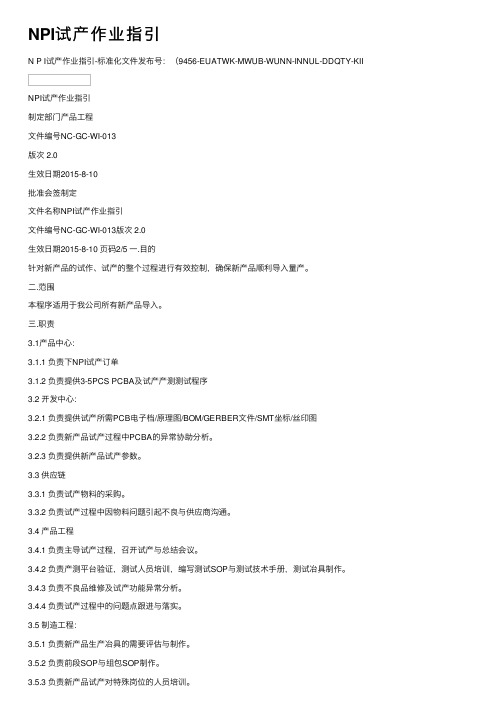
NPI试产作业指引N P I试产作业指引-标准化⽂件发布号:(9456-EUATWK-MWUB-WUNN-INNUL-DDQTY-KIINPI试产作业指引制定部门产品⼯程⽂件编号NC-GC-WI-013版次 2.0⽣效⽇期2015-8-10批准会签制定⽂件名称NPI试产作业指引⽂件编号NC-GC-WI-013版次 2.0⽣效⽇期2015-8-10 页码2/5 ⼀.⽬的针对新产品的试作、试产的整个过程进⾏有效控制,确保新产品顺利导⼊量产。
⼆.范围本程序适⽤于我公司所有新产品导⼊。
三.职责3.1产品中⼼:3.1.1 负责下NPI试产订单3.1.2 负责提供3-5PCS PCBA及试产产测测试程序3.2 开发中⼼:3.2.1 负责提供试产所需PCB电⼦档/原理图/BOM/GERBER⽂件/SMT坐标/丝印图3.2.2 负责新产品试产过程中PCBA的异常协助分析。
3.2.3 负责提供新产品试产参数。
3.3 供应链3.3.1 负责试产物料的采购。
3.3.2 负责试产过程中因物料问题引起不良与供应商沟通。
3.4 产品⼯程3.4.1 负责主导试产过程,召开试产与总结会议。
3.4.2 负责产测平台验证,测试⼈员培训,编写测试SOP与测试技术⼿册,测试冶具制作。
3.4.3 负责不良品维修及试产功能异常分析。
3.4.4 负责试产过程中的问题点跟进与落实。
3.5 制造⼯程:3.5.1 负责新产品⽣产冶具的需要评估与制作。
3.5.2 负责前段SOP与组包SOP制作。
3.5.3 负责新产品试产对特殊岗位的⼈员培训。
3.6 品质3.6.1 负责新产品试产过程中品质监控。
3.6.2 负责物料的来料检验及物料问题引起的异常处理。
3.7 资材3.7.1 负责新产品物料的需求跟进。
3.7.2 负责新产品上线制作计划安排。
3.8 SMT与装配3.8.1 负责新产品试产的具体⽣产任务。
3.8.2 负责记录新产品试产过程中问题点。
四.定义4.1 试作:对新产品进⾏⼩批量的组装。
新品试产作业管理办法与流程图
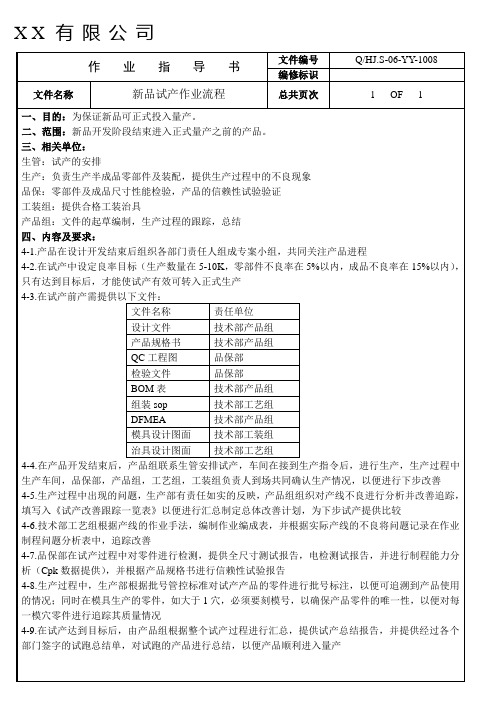
4-6.技术部工艺组根据产线的作业手法,编制作业编成表,并根据实际产线的不良将问题记录在作业制程问题分析表中,追踪改善
4-7.品保部在试产过程中对零件进行检测,提供全尺寸测试报告,电检测试报告,并进行制程能力分析(Cpk数据提供),并根据产品规格书进行信赖性试验报告
工装组:提供合格工装治具
产品组:文件的起草编制,生产过程的跟踪,总结
四、内容及要求:
4-1.产品在设计开发结束后组织各部门责任人组成专案小组,共同关注产品进程
4-2.在试产中设定良率目标(生产数量在5-10K,零部件不良率在5%以内,成品不良率在15%以内),只有达到目标后,才能使试产有效可转入正式生产
4-3.在试产前产需提供以下文件:
文件名称
责任单位
设计文件
技术部产品组
产品规格书
技术部产品组
QC工程图
品保部
检验文件
品保部
BOM表
技术部产品组
组装sop
技术部工艺组
DFMEA
技术部产品组
模具设计图面
技术部工装组
治具设计图面
技术部工艺组
4-4.在产品开发结束后,产品组联系生管安排试产,车间在接到生产指令后,进行生产,生产过程中生产车间,品保部,产品组,工艺组,工装组负责人到场共同确认生产情况,以便进行下步改善
4-8.生产过程中,生产部根据批号管控标准对试产产品的零件进行批号标注,以便可追溯到产品使用的情况;同时在模具生产的零件,如大于1穴,必须要刻模号,以确保产品零件的唯一性,以便对每一模穴零件进行追踪其质量情况
新产品量产试作、承认作业办法

2.9.2 若為重大設計變更的量試試作,其量試與驗證紀錄則納入設計變更檔案中,以 供歷史佐證之用。
2.10 資料的產出 在產品試作完成後,相對的一些資料檔必須產出,其序列如下。 2.10.1 檢驗規範及 QC 工程表 2.10.2 作業指導書 2.10.3 量試報告 2.10.4 試作通知與總結報告(附表 4.3)
文件 類別
檔
案
名
稱
量產試作、承認作業辦法
文件編號 版次
管理辦法 生效日期:
頁次
(4)- (6)
料風險。 2.8 試作及量試結果
(1) 研發階段樣品在試作時﹐其結果符合以下條件才能進行下一流程作業或量試作業﹐具 體如下﹕ (A) 半成品電氣不良率﹕A≦15%﹐B≦10%(A 為 GXP 系列﹐B 為除 GXP 外其它系列)﹔ (B) 成品電氣不良品率≦5%﹔ (C) 成品電氣不良率大於 5%時﹐原則上不導入量試作業﹐除客戶強烈要求。
(3) 量試作業完成後,即由生產單位把「試作通知與總結報告(附表 4)」及「試作報告追蹤 表(附表 6)」給相關單位會簽﹐然後由生產單位負責人將上述表單送工程單位﹐由工 程單位生技製作試作報告后召集相關單位舉行檢討會議,提出量試試作中所發現事項 供檢討,並記錄於「量試階段審查清單(附表 5)」以便繼續跟催改善措施以迄正式量 產。
(4) 試作報告追蹤表頭﹑試作站別﹑注意事項﹑制表由工程師填寫﹐產品數量﹑計划時間﹑ 完成時間﹑不良品狀態由生產組長填寫﹐確認人員為量試時指定的指定人員根據工程 師提出需確認的流程作確認﹐量試完成后由生產課長﹑生技審核﹐生產單位經理核准﹐ 試作通知與總結報告由需求單位填寫表頭﹐經生產﹑資材﹑工程﹑品保專案人員作量 試前資源確認的會簽﹐量試完成后相關單位在結論與建議上填寫相關意見﹐最終由相 關部門經理核准。
新产品试产作业指导书

新产品试产作业指导书1、目的为规范产品试制、试产的管理,保证新产品顺利放产及提升原有产品质量,特制定本指导书;2、适用范围本指导书适用于公司新产品及原有产品重大设计更改的试制、试产全过程的管理;3、定义试制范围:新产品在投入试产前,主要为验证装配工艺包括工艺方案、工艺流程、操作方法、特殊工艺检测手段和控制方式等能否适应批量稳定合格生产的要求而进行的样品试装配;或开发部门、工程部PIE 等对产品进行重大设计更改或对产品采用新材料、新工艺、新部件等改进后,为验证能否适应批量稳定合格生产的要求而进行的样品试装配试产范围:开发部门完成新产品技术设计并编制必要的技术文件如总装图、图纸等后,主要为验证生产全过程包括工艺方案、工艺流程、操作方法、特殊工艺检测手段和控制方式、生产组织、物料供应等的试产活动;或开发部门、工程部PIE等对原有产品进行了重大设计更改,为验证生产全过程而进行的试产活动;试产频次:常规含派生产品试产次数不多于2次;较复杂项目试产次数不多于3次;试产数量:每次试产数量不少于20PCS/次如属系列产品,试产的每款产品试产数量均不少于20PCS/次;4、职责项目负责人在试制、试产过程中主要职责如下:a、填写样品制作申请单,注明各项要求,并提供必要协助,使样品顺利试装;b、根据项目开发进度负责提前十天编制试产通知单;c、负责落实试产文件提前十五天下发至相关部门,承担因试产文件下发不及时或不齐全而导致试产不能如期进行的责任;d、负责新开发塑料件及五金件试产物料的确认及跟进,负责对试产BOM进行最终确认;e、负责带领项目组成员从样品试制、试产到试产总结等各环节全过程的组织和跟进,包括提请工装夹具制作、生产性辅料、检验测试设备的准备等;f、负责组织试产总结会议及试产整改会议;g、委托品质部门对试制、试产样品进行综合测试;h、试制、试产后多余物料及试产样品的处理;项目组成员包括结构工程师、包装工程师、电子工程师及相关PE工程师等;项目组成员在试制、试产过程中主要职责如下:a、编制个人所负责部分的技术图纸及文件,并跟进文件的发放;b、现场指导试产工作,对试产过程中发现的技术、工艺、测试、设备工装、质量和文件等方面的问题作好记录;c、PE工程师根据试产过程中发现的试产结构等方面的问题编制试产报告,供试产总结会议分析讨论;d、参加试产总结会议,在试产总结会议上对试产过程中发现的问题提出合理的解决方案,并跟进个人所负责不符合项的整改;e、参加试产整改会议,并对整改结果进行确认;K3技术人员、计划采购部门、模具制作车间在试制、试产过程中主要职责如下:a、K3技术人员:试产通知单和技术文件到位后2个工作日内确认新产品试产BOM试产BOM需项目负责人最终确认并通知计划采购部门;b、计划采购部门:通过ERP系统下发领料需求计划,按时、按质、按量提供除新开发塑料件及五金件试产物料以外的所有试产物料;c、模具制作车间:跟进试产过程中模具试模的全过程,对模具异常进行处理,并提供合格的新开发塑料件及五金件试产物料;生产部门在试制、试产过程中主要职责如下:a、生产部门指定专人负责试产工作,负责落实试产所需的设备、工具、工装、检验测试仪器及特殊物料等;负责自制物料及外购物料不包括新开发塑料件及五金件试产物料的跟进及组织试产物料申领;确定试产时间,通知相关人员到试产现场指导试产工作;根据试产过程中发现的试产结构、装配工艺、装配注意事项及质量等方面的问题编制试产报告,供试产总结会议分析讨论;参加试产总结会议及试产整改会议,并对整改结果进行确认;b、生产部门注塑车间、冲压车间分别指定专人跟进新产品试产,整理各自工序在试产过程中发现的生产、工艺及质量等方面的问题,并提供给生产部门试产负责人汇总到试产报告里;参加试产总结会议及试产整改会议,并对整改结果进行确认;注塑车间、冲压车间另承担主导新开发塑料、五金模具质量的评审;开发部门样板员在试制过程中主要职责如下:负责试制物料的跟进及申领,确定试制时间,通知相关人员到现场完成样品试制;品质部门在试制、试产过程中主要职责如下:a、整理试产过程中发现的测试、质量等方面的问题,编制试产报告,供试产总结会议分析讨论;b、落实新产品生产所需检验测试设备、方法、注意事项等,如需要应进行相应的记录,以备后续放产使用;c、组织进行试制、试产样品的型式试验并及时做出相关报告反馈至项目负责人,并跟进落实;d、参加试产总结会议及试产整改会议,并对整改结果进行确认;5、试制、试产过程试制、试产通知a、项目负责人如需试制样品,须填写样品制作申请单,审批后提交开发部门样板员组织试制物料,项目负责人及项目组成员协助进行样品装配;b、项目负责人根据项目开发进度提前十天编制试产通知单,经电工事业部负责人审批后发相关部门;c、试产通知单在考虑物料采购周期的前提下要明确注明计划试产时间、样品规格、试产数量和专用物料的状态及到位时间等,并注明所需工装、夹具、设备、检验测试仪器及其它特殊物料等;d、如由于某种特殊原因要中途更改试产规格或数量,项目负责人需重新下发试产通知单,而试产时间则按期顺延;e、如果试产数量已包含给客户的送样样品、认证样品或型检样品等,应在试产通知中加以备注,并及时通知相关人员领出所需数量的样品;试产技术文件a、项目负责人负责落实试产文件包括结构、电子技术图纸及相关通知文件等提前十五天下发至相关部门,如由于技术文件下发不及时或不齐全而导致试产不能如期进行,由项目负责人承担责任;b、试产技术文件必须标准、清晰、齐全,编制方式必须符合标准化管理的相关要求,如产品总装图纸、全套零部件图纸、包装图纸、电子图纸及相应的设计、更改通知单等;c、试产图纸下发后如发现有错误需重新调整的,相关工程师需下发技术更改通知单必要时可附件到图纸接收部门,由各部门相关人员在试产文件上进行更改并签名确认,原则上不接受非书面的技术更改;试产物料组织a、K3技术人员根据试产通知单和技术文件的到位时间,在2个工作日内编制出试产BOM;计划采购部门接到试产通知单后,应及时跟进自制物料生产及外购物料采购计划,原则上除新开发塑料件及五金件试产物料由项目负责人跟进外,其余所有物料均由计划采购部门负责;b、模具制作车间接到试产通知单后按试产日期提前安排塑料、五金模具试模工作;塑胶、五金模具试模用料、试模机台、试模前的准备工作由模具制作车间负责安排,试模作业由模具制作车间提前书面通知项目负责人、PE工程师、品质部门及注塑、五金车间相关人员参加试模过程的评估工作,如没有书面通知到相关部门,试模工作视为无效,必须重新试模;如已书面通知相关部门但该部门没有派人到现场参加试模,由此造成产品试模工作延期,该部门负责人应承担相应的处罚;评估结果由各部门提出并签字确认是否可以进入试产作业,如试模中存在问题,相关部门要急时进行处理,直至整改并试模合格后再进入试产作业;模具制作车间按试产通知单上要求数量生产合格的零件,并由项目负责人签收必须保留5整啤带水口新开发塑料件供项目负责人签板使用;项目负责人出具合格的新开发塑料件、五金件零件评估报告后,模具制作车间可将合格模具进仓并转交注塑、五金车间签收;c、品质部门进货检验负责所有试产零部件的检验,新开发的零部件如检验不合格或有疑问,须提交至相关工程师来判断其合格与否;d、电子工程师负责电子件的质量确认工作;e、除新开发塑料件及五金件试产物料外,其余试产物料全部由生产部门试产负责人安排安装车间按正常生产订单物料领料方式领料; 样品试装项目负责人负责确认物料到位情况;物料全部到位后,由项目负责人组织开发部门样板员先自行试装样品一个如属系列产品,试产的每款产品均需试装一个,验证物料是否真正齐全、正确及质量状况、工装夹具、生产辅料等项目,以确定其能否试产;验证过程中发现的相关问题,提请相关负责人及时解决;正式试产a、项目负责人在确认符合试产要求后应及时通知生产部门试产负责人,由其即刻安排试产;生产部门试产负责人确定试产时间后通知项目负责人、项目组成员、PE工程师及生产、品质部门相关人员到场指导试产工作;b、生产部门试产负责人严格按照试产文件进行试产验证,并对能否试产严格把关,对试产质量负责;当存在以下情况时,将不予试产,直到完成整改后才能重新安排试产:①、文件不到位、不齐全或不能正常指导试产;②、物料没有完全准备好;③、上一次试产有较多问题没有落实整改好;④、没有样品试装验证,或经过样品验证发现有技术、工艺、测试、零部件质量等问题会影响试产;⑤、不能试产的其他情况;业务人员提出认证需求时,认证人员需与项目拓展负责人或结构开发负责人或PIE负责人核对产品立项情况,然后再确认认证情况;试产样品测试项目负责人委托品质部门对试制、试产样品进行各项综合测试,品质部门及时做出报告反馈至项目负责人;试产问题报告及汇总a、产品结构、工艺等问题试产报告汇总由PE工程师在试产完成后两天内完成;b、安装、注塑、冲压问题试产报告汇总由生产部门试产负责人在试产完成后两天内完成;c、成品测试问题试产报告汇总由品质部门在试产后两天内完成;d、所有报告发送至项目负责人,并由项目负责人进行汇总形成试产总结报告;试产总结会议项目负责人负责组织试产总结会议,并至少提供一个样品如属系列产品,试产的每款产品均需提供一个样品;项目负责人总结的意见、与会代表提出的意见,不论是新问题或是遗留问题、需要整改或是不需整改的问题,都应记录在试产总结报告上,由项目负责人跟进相关责任人落实;试产整改a、由项目负责人负责填写试产总结报告,制定整改措施,属不需整改的问题也需填出并备注不需整改原因;b、试产整改完成后由项目负责人组织开发、PE、品质、生产相关人员召开试产整改评审会议,针对试产整改问题进行审查,如试产整改已达到预期要求,项目即可进入放产流程;c、如在试产整改评审会议召开时,试产问题的整改未达到预期要求,则要求项目负责人说明原因,要求其限期内完成整改;d、项目负责人跟进各相关责任人整改措施的落实情况;e、如第一次试产不成功,或整改问题较多,可进行第二次试产;试产样品处置a、试产样品经检验合格后入库,入库样品根据不同要求每隔三个月由开发部门按折价处理可按产品成品价的90%~110%适当定价、消费者试用、拆分回用、拆分破碎等方式统一进行申请处理;b、各部门如需送客户样板、认证测试等可开单领出;c、试产样品经检验不合格, 暂放于不合格成品暂放区,待下次试产时整改经检验合格后按标准要求运作,不合格物料报废;新产品放产移交a、新产品试产并整改完成后有订单,批量生产一个批次后可移交;b、新产品试产并整改完成后半年内无订单,则半年后可移交;c、新产品移交需制作放产确认评审报告,由项目开发部门提案,PIE部门、财务部门、品质部门、生产部门会签,电工品质研发中心总监或照明项目部负责人或开关配件项目部负责人审议、总经理审批后方可移交,移交后的技术问题由PIE部门负责,如有需要,项目负责人可协助指导;d、移交前项目开发部门需下发相关生产图纸、技术文件和资料等文件,并由PIE部门签字确认;6、试制、试产物料费用管理新开发塑料件及五金件试产物料由模具制作车间提供,其费用已含在模具费用中,开发部门不再另行支付费用;模具制作车间提供试产物料的费用包括:①每套塑料模具模具制作车间提供50啤TNC电工外框新塑料件需提供100啤,②每件五金件模具制作车间提供30PCS,以上数量若有超出,超出部分费用另计;内部自制物料按公司生产制造费用管理;外购物料包括外购新物料,如有需要,项目负责人应协助采购部门进行外购新物料的采购由采购部门下单采购,并按正常采购程序入库及付款;生产车间试产人员费用按计时工资元/小时/人进行计算;所有试制、试产样品及其所产生的费用包括物料费用、试产人员费用及其他摊销等均计入开发部门新产品开发费用;试产样品如果进行折价处理,收入部分可用于抵消开发部门新产品开发费用;7、试产物料采购周期试产物料采购周期:a、常规物料7日内到位;b、特殊物料包括电子板、特殊原材料等15日内到位;紧急项目或采购周期长的试产物料,为节约时间,开发部门可以提前以工作联络函的形式提出采购需求,采购部门接到采购需求后可提前采购;试产物料采购周期开始时间以开发部门下发试产通知单为准,特殊物料包括电子板、特殊原材料等采购周期开始时间以开发部门相关工程师下发的工作联络函时间为准;对不能及时提供试产物料的内部执行人员进行相应的通报与考核;8、考核管理计划采购部门所负责的试产物料未能及时提供应承担以下责任:a、试产物料要求提供时间超过1天内部通报;b、试产物料要求提供时间超过3天含第3天开始进行经济处罚,每一种物料每超过1天罚款30元计划采购执行人员承担15元,计划采购部门负责人承担15元连带责任;新开发塑料件及五金件试产物料未能及时提供,项目负责人、模具制作车间应承担以下责任:a、试产物料要求提供时间超过1天内部通报;b、试产物料要求提供时间超过3天含第3天开始进行经济处罚,每一种物料每超过1天罚款30元项目负责人、模具制作车间负责人各承担15元;试产物料备齐后生产部门应在1天内组织物料进行试产并完成,若在规定时间内没有完成试产计划,每超过一天罚款50元生产部门试产负责人承担25元,生产部门负责人承担25元连带责任;9、相关表格试产通知单试产报告试产总结报告样品制作申请单试产报告编号:序号:编号:序号:编号:序号:编制:日期:批准:日期:。
WI8.5-11新产品试产作业指引

xx塑料制品有限公司作业指导书生效日期:2017年07月01日文件编号:WI8.5-11版本号:B修订号:0文件名称:新产品试产作业指引第1页共2页一、目的:规范新产品试产过程,确保新产品试产阶段可正确、顺利地进行,并顺利地投入量产。
二、适用范围:本公司所有新产品的试产。
三、权责部门:生产部生管:负责制定生产计划,物料控制及成品出货的管制。
生产部:负责产品的印刷、冲圆、成型、注塑及包装等。
工程部:主要负责试产的组织、协调工作及生产技术问题的解决。
具体包括:1、负责相关文件的核对、发行、制作。
2、负责召开试产前会议。
3、负责试产的整个过程的跟踪。
为生产线提供技术上的支持,生产问题的统计及处理。
4、召开试产后会议,总结试产情况,讨论是否量产。
5、负责解决试产过程中出现的重大技术问题。
品管部:参与产品验证,参加相关会议,试产过程的中的质量检测等。
四、内容:1、工程部接客户新产品生产需求后,应具备以下资料及工装:(1)、产前参考样品。
(2)、产品规格书。
(3)、生产模治具(4)、测试工装及测试规范(通知品管部完成)。
(5)作业指导书(包括各工序)2、试产前会议。
工程部应在新产品正式生产前组织召开试产前会议,并在召开会议完成会议的准备工作。
(1)、内容:由工程部介绍产品及其技术情况(包括但不限于产品外观、特点、区域划分、注意事项),讨论并排定试产排程表(时间、数量),讨论其他特殊要求等。
(2)、与会人员:仓库、业务部、工程部、生产部、品保部等。
3、采购根据物料需求计划,开立采购单采购并跟踪物料进度。
4、试产前一天,由工程部通知各部门,并了解和检查各部门的准备情况。
5、产品上线后,工程部进行全程跟进。
对生产各制程(印刷,注塑、纸杯成型、冲圆、包装)进行作业教学、指导,并及时了解试产情况,处理异常。
(1)、工程部为主要负责人,主要是解决生产和工艺上的问题,保障试产顺利进行。
(2)、品保部应做好质量检测方面的工作。
新产品试产作业指引

目的:为了规范工厂新产品试产流程,明确各部门职责,提高效率,确保所有新产品的外观/功能和可靠性测试满足客户之要求,特制定本程序。
二、范围:适用于工厂内所有新产品、新物料的试产等。
三、程序:1、开发部对新产品的导入进行评审,以确保最终设计方案是否满足客户的要求,如果评审确认有能力试产,开发部发放《新产品试产通知单》给相关部门,如果评审确认不具备试产条件,开发部需重新考虑设计方案,重新设计后再进行评审。
2、开发部输出新产品BOM、PCB贴片图、电子新元件规格书(附签板)、产品原理图、产品电性参数、软体操作说明、邦定作业指导书、新产品生产工艺/测试指引、产品DDS资料、产品爆炸图、新产品胶件样板签板、结构新元件规格书(附签板)、产品胶件2D图、产品样板发放给相关部门。
3、PMC部依据《新产品试产通知单》和相关资料,制定《生产作业指令》和《物料计划明细表》。
4、PMC部将试产的相关资料分发给相关部门,相关部门应对试产是否妥当进行评审,根据评审结果,安排适当的时间,车间进行试产。
5、米购部负责物料的米购和物料不良问题的返馈并要求供应商提出纠正措施要求。
6、PMC 部的PC 做试产计划,并跟进有异常及时通报。
MC 做进料计划,并跟进有异常及时通报,所有准备就绪后,提前一天发放试产指令各相关部门。
7、工程部PIE 与PE 根据相关资料和样机,对新产品样板的生产工艺进行分解,制定试产工艺流程,评估作业人力、所需工具及产能提供给相关部门。
8 工程部PIE制做新产品中每款COB板测试架各1PCS,提供给品质部,邦定部参照样板COB 测试架进行制作测架。
9、工程部PE根据生产工艺要求制做生产所需的测试架等生产治具提供给生产部门。
10、品质部在试产前应根据客户之要求制定产品规格和品控计划及控制点作业指导书并分发相关部门。
11、品质部依据电子新元件规格书和样板,对试产物料进行品质检验。
12、生产前生产主管召集拉长、助拉、物料员开动员会议,展示样品,必要时解剖样品了解内部结构,简要介绍客户及产品要求,生产注意事项。
试产作业指引
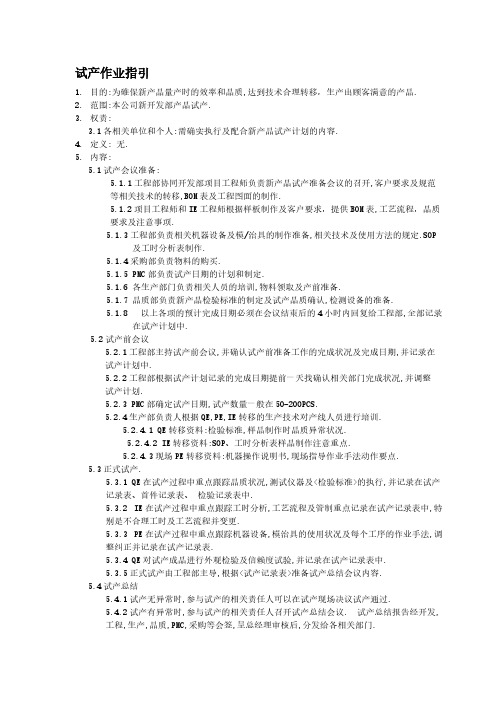
试产作业指引1.目的:为碓保新产品量产时的效率和品质,达到技术合理转移,生产出顾客满意的产品.2.范围:本公司新开发部产品试产.3.权责:3.1各相关单位和个人:需确实执行及配合新产品试产计划的内容.4.定义: 无.5.内容:5.1试产会议准备:5.1.1工程部协同开发部项目工程师负责新产品试产准备会议的召开,客户要求及规范等相关技术的转移,BOM表及工程图面的制作.5.1.2项目工程师和IE工程师根据样板制作及客户要求,提供BOM表,工艺流程,品质要求及注意事项.5.1.3工程部负责相关机器设备及模/治具的制作准备,相关技术及使用方法的规定.SOP及工时分析表制作.5.1.4采购部负责物料的购买.5.1.5 PMC部负责试产日期的计划和制定.5.1.6 各生产部门负责相关人员的培训,物料领取及产前准备.5.1.7 品质部负责新产品检验标准的制定及试产品质确认,检测设备的准备.5.1.8 以上各项的预计完成日期必须在会议结束后的4小时内回复给工程部,全部记录在试产计划中.5.2试产前会议5.2.1工程部主持试产前会议,并确认试产前准备工作的完成状况及完成日期,并记录在试产计划中.5.2.2工程部根据试产计划记录的完成日期提前一天找确认相关部门完成状况,并调整试产计划.5.2.3 PMC部确定试产日期,试产数量一般在50-200PCS.5.2.4生产部负责人根据QE,PE,IE转移的生产技术对产线人员进行培训.5.2.4.1 QE转移资料:检验标准,样品制作时品质异常状况.5.2.4.2 IE转移资料:SOP、工时分析表样品制作注意重点.5.2.4.3现场PE转移资料:机器操作说明书,现场指导作业手法动作要点.5.3正式试产.5.3.1 QE在试产过程中重点跟踪品质状况,测试仪器及<检验标准>的执行,并记录在试产记录表、首件记录表、检验记录表中.5.3.2 IE在试产过程中重点跟踪工时分析,工艺流程及管制重点记录在试产记录表中,特别是不合理工时及工艺流程并变更.5.3.3 PE在试产过程中重点跟踪机器设备,模治具的使用状况及每个工序的作业手法,调整纠正并记录在试产记录表.5.3.4 QE对试产成品进行外观检验及信赖度试验,并记录在试产记录表中.5.3.5正式试产由工程部主导,根据<试产记录表>准备试产总结会议内容.5.4试产总结5.4.1试产无异常时,参与试产的相关责任人可以在试产现场决议试产通过.5.4.2试产有异常时,参与试产的相关责任人召开试产总结会议. 试产总结报告经开发,工程,生产,品质,PMC,采购等会签,呈总经理审核后,分发给各相关部门.5.4.3 CPK和直通率由IE及PE确定计算结果,评定不合理时为异常)不可以量产.5.4.4直通率<90%,CPK<1.33,机器设备模治具不能正常使用,SOP及工时不合理为异常,不可以量产5.4.5直通率90%,CPK>1.33,机器设备能正常使用,SOP及工时合理时为正常,可以量产.5.5试产异常时改善对策与实施.5.5.1试产异常时,由工程部主导,QE/PE//IE依据<试产记录表>进行异常分析并制定改善对策计划及实施要求.5.5.2各责任人依改善对策计划及实施要求进行确认改善.5.6改善确认5.6.1 QE/PE/IE签名确认改善完成后由工程部主导重新试产.5.7 试产合格后方可量产.5.7.1生产部依生产过程控制程序执行正式量产.6.参考文件6.1生产过程控制程序7.附件及应用表单7.1<试产记录表>7.2<试产异常改善计划表>。
试产作业指导书

试产专案负责人
试产确认
1.由试产专案负责人联系开料、折面、车面、掹鞋、落底、大底及品检开会讨论,对试产情况给予记录在“试格通知及报告书”。
2.由试产专案负责人把“试格通知及报告书”交开发部确认并给出意见。
试产专案负责人
开发部
正式生产
1.试产专案负责人把“试格通知及报告书”复印给采购1份、生产部6份,并在原报告背面签收。
试产(试面)
1.试产专案负责人填写“试格通知及报告书”交开料组,开料组以此单到仓库领料。
2.仓库依确认板发料。,
3.开料、折面、车面开始进行试产并填写“试格通知及报告书”。
试产专案负责人
仓库ห้องสมุดไป่ตู้
各组长
试产(试底)
1.掹鞋、落底、大底试产人员跟进,并记入“试格通知及报告书”。
2.试产专案负责人跟进掹鞋、落底、大底的试产情况,并记入“试产情况一览表”。
试产作业指导书
文件管制类别
管制非管制
初版日期
2005.12.8
生效日期
2005.12.10
修订日期
/
修订次数
/
总页数
3
制订
校对
核准
1.目的
使试产工作人员明确试产的作业流程,明确职责,保证试产的有效、准确、顺利的进行,保证产品符合设计与生产的需要。
2.试产流程如下表:
流程
流程说明(表单资料)
部门/负责人
2.开发部协助解决生产过程的问题。
试产专案负责人
开发部
3.使用表单
3.1试产情况一览表--------------FM-E-001-01
3.2试格通知及报告书(见QP-021)
接受客户订单
新产品试产运作作业指导书
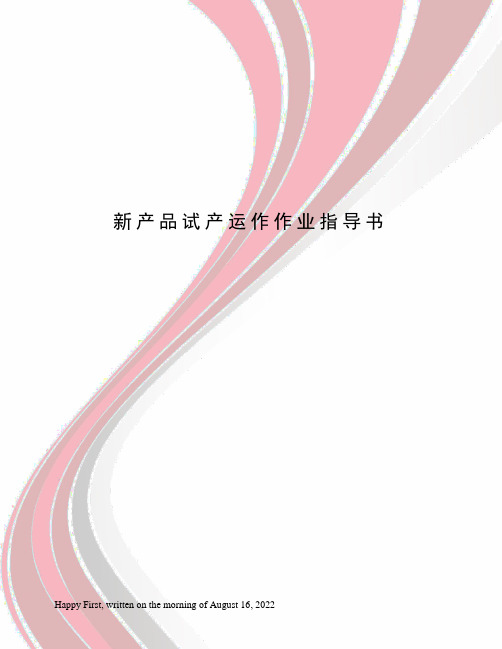
文件编号
版 本
E
作业指导书
新产品试产运作作业指导书
页 数
第1页;共10页
生效日期
2011-01-22
新产品试产运作作业指导书
制定/日期
审核/日期
批准/日期
修 改 记 录
修改
状态
时 间
修改内容概要
修改人
审 核
批 准
C
2009-04-28
修订
D
2010-02-01
修订
E
2010-12-16
增加研发样品全功能测试及试产准备;明确时间要求
文件编号
版 本
E
作业指导书
新产品试产运作作业指导书
页 数
第2页;共10页
生效日期
2011-01-22
1.0 目的
对新产品设计输出进行验证;确保新产品试产快速顺利进行、准时上市..
2.0适用范围
适用于公司所有新产品试产全过程的控制..
3.0 定义
新产品开发;进行小批量50-150套的试量产;验证设计的可行性、完成新产品由研发向生产的转化工作、发现及解决产品各个环节隐藏的问题..
5.2.7 采购部、PMC、品管、工程等按照新产品试产进度表确定试产预定时间..
5.2.8 样品鉴定会上确定该产品的试产小组;工程部试产负责人负责安排试产小组工作;制定好新产品试产进度表;并经各负责人签字确认..
5.2.9 样品鉴定会通过后第1个工作日;研发部将新产品全部资料含电子档交文控中心受控其中文件资料与电子档资料需按照新产品开发及试产样品及资料清单编排序号;文件名称与编排序号一定要一致;电子档资料与文本资料确认无误后;文控在鉴定会通过后第二个工作日完成资料的发放..备注:文控需将新物料采购一览表发给PMC及采购部;纸质档;各一份..如遇特殊紧急情况、影响到系统资料添加的资料可以以扫描文档形式暂时下发;在收到文档后第一时间制作系统资料;不能影响订单下达..
新产品试产评估工作指引
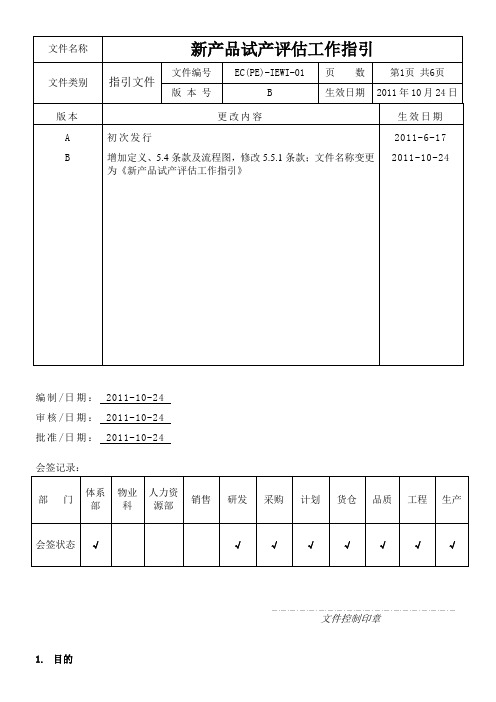
文件名称 文件类别 指引文件
新产品试产评估工作指引
文件编号 版 本 号 EC(PE)-IEWI-01 B 页 数 第5页,共6页 2011 年 10 月 24 日 生效日期
5.8. 改善确认 5.8.1.QE、PE、TE、PD 签名确认改善结果,由工程科主导重新试产至合格; 5.8.2.试产合格后方可量产,生产科依《生产过程控制程序》正式量产。 6. 引用文件 《生产运作控制程序》 7. 记录 《试产检查清单报告》 《新产品试产总结报告》 流程图: 8. 流程图:
Pass
进行试产
开发、工程、生产
试产结果总结
Fail
改善
工发工程师、PE、QE、PD、TE、开发工程师
Pass
进入量产
文件名称 文件类别 版本 A B 初次发行
新产品试产评估 新产品试产评估工作指引 试产评
指引文件
文件编号 版 本 号 更改内容 EC(PE)-IEWI-01 B 页 数 第1页 共6页 2011 年 10 月 24 日 生效日期 2011-6-17 2011-10-24 生效日期
增加定义、5.4 条款及流程图,修改 5.5.1 条款;文件名称变更 为《新产品试产评估工作指引》
文件名称 文件类别 指引文件
新产品试产评估工作指引
文件编号 版 本 号 EC(PE)-IEWI-01 B 页 数 第4页,共6页 2011 年 10 月 24 日 生效日期
包装)进行作业指导,并及时了解试产情况,处理异常; 5.5.2.QE 在试产过程中重点跟踪品质状况,根据测试仪器及检验标准执行,并记录在《新 产品试产总结报告》中; 5.5.3.IE 在试产过程中重点跟踪工时分析、工艺流程及管制重点,并记录在《新产品试 产总结报告》中;对不合理的工时及工艺流程应进行分析; 5.5.4.PE 在试产过程中重点跟踪机械设备、模具、治具的使用状况及每道工序的作业方 法,调整纠正并记录在《新产品试产总结报告》中; 5.5.5.QE 对试产成品进行外观检测及信赖度试验,并记录在《新产品试产总结报告》中; 5.5.6.正式试产由工程科主导,根据《新产品试产总结报告》准备试产总结会议。 5.5.7.生产,TE,PE,QE 对试产过程中发现的问题按《新产品试产总结报告》的格式提 出。 5.6. 试产总结 5.6.1.试产结束后,由工程召集相关人员如开试产总结会议;对所有问题进行检讨,并要 有切实可行的改善行动.A 级和 B 级缺陷必须在量产前解决. A (级)指缺陷必须在量产前改善,否则将影响产品之功能以至量产无法正常生产; B (级)指缺陷能够通过实施有效加工手段或补救措施来弥补缺陷,但开发必须采用 更合理的设计来改善; C (级)指非产品设计缺陷但需要通过有效之过程控制手段来改善; 5.6.2.试产无异常时,由 PE、QE、PD、TE、开发工程师可以在试产现场签名决议试产通 过方能生效; 5.6.3.试产有异常时,参与试产的相关责任人召开试产总结会议,试产总结报告由各责任 人会签,并要求组织下次试产,对前次试产时给出改善行动进行验证; 5.6.4.评定不合理时为异常情况,不可以量产; 5.6.5.合格率为 95%,机械设备能正常使用,SOP 及工时合理进为正常,可以量产; 5.7. 试产异常时改善对策与实施 5.7.1.试产异常时,由工程科主导 PE、QE、PD、TE、开发工程师依据《新产品试产总结 报告》进行异常分析并制定改善对策及实施方案; 5.7.2.各责任人依据改善对策及实施方案进行改善;
新产品生产作业指导书
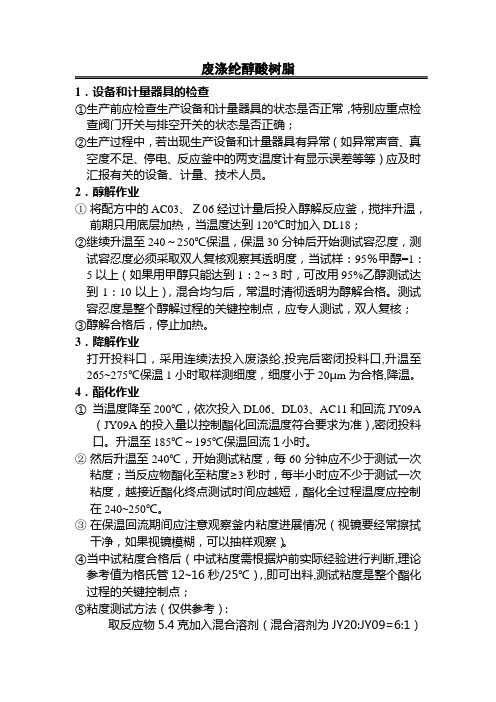
废涤纶醇酸树脂1.设备和计量器具的检查①生产前应检查生产设备和计量器具的状态是否正常,特别应重点检查阀门开关与排空开关的状态是否正确;②生产过程中,若出现生产设备和计量器具有异常(如异常声音、真空度不足、停电、反应釜中的两支温度计有显示误差等等)应及时汇报有关的设备、计量、技术人员。
2.醇解作业①将配方中的AC03、Z06经过计量后投入醇解反应釜,搅拌升温,前期只用底层加热,当温度达到120℃时加入DL18;②继续升温至240~250℃保温,保温30分钟后开始测试容忍度,测试容忍度必须采取双人复核观察其透明度,当试样:95%甲醇=1:5以上(如果用甲醇只能达到1:2~3时,可改用95%乙醇测试达到1:10以上),混合均匀后,常温时清彻透明为醇解合格。
测试容忍度是整个醇解过程的关键控制点,应专人测试,双人复核;③醇解合格后,停止加热。
3.降解作业打开投料口,采用连续法投入废涤纶,投完后密闭投料口,升温至265~275℃保温1小时取样测细度,细度小于20μm为合格,降温。
4.酯化作业①当温度降至200℃,依次投入DL06、DL03、AC11和回流JY09A(JY09A的投入量以控制酯化回流温度符合要求为准),密闭投料口。
升温至185℃~195℃保温回流1小时。
②然后升温至240℃,开始测试粘度,每60分钟应不少于测试一次粘度;当反应物酯化至粘度≥3秒时,每半小时应不少于测试一次粘度,越接近酯化终点测试时间应越短,酯化全过程温度应控制在240~250℃。
③在保温回流期间应注意观察釜内粘度进展情况(视镜要经常擦拭干净,如果视镜模糊,可以抽样观察)。
④当中试粘度合格后(中试粘度需根据炉前实际经验进行判断,理论参考值为格氏管12~16秒/25℃),,即可出料,测试粘度是整个酯化过程的关键控制点;⑤粘度测试方法(仅供参考):取反应物5.4克加入混合溶剂(混合溶剂为JY20:JY09=6:1)4.6克(反应物:混合溶剂=1:0.852)搅拌后,降温至25±1℃,用格氏管进行中间测试粘度,中试应做到迅速、准确,格氏管要保持清洁,防止因残余物引起的粘度误差;还要防止试样温度偏离而影响测试精确度;5.注意事项①高位槽应预先抽入兑稀溶剂;②预先应往兑稀罐内抽入配方量的兑稀溶剂;③当兑稀罐漆料温度小于100℃方可进行过滤(过滤机压力应小于0.4Mpa),过滤过程中应自测细度,用JY20调节过渡罐的漆料粘度直至合格,并留样供检验部门检验;④生产过程中必须如实填写工艺现场记录,如果不按工艺规程填写,将按违反工艺规程进行处罚,车间管理人员、技术人员应不定期检查记录填写情况。
试产工作指引
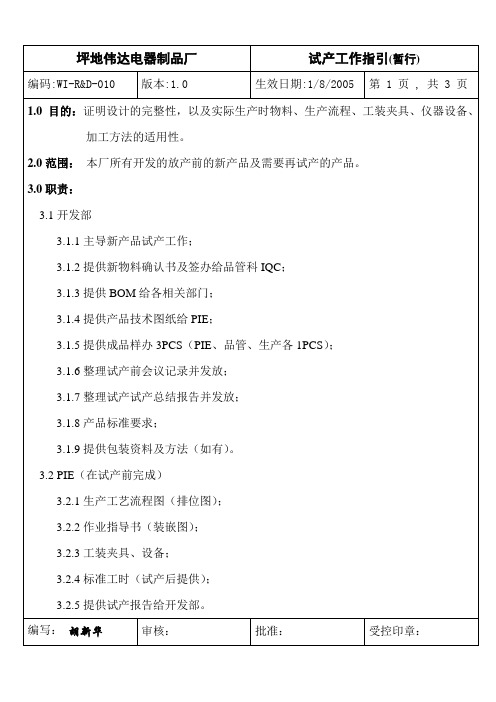
试产工作指引(暂行)
编码:WI-R&D-010
版本:1.0
生效日期:1/8/2005
第1页,共3页
1.0目的:证明设计的完整性,以及实际生产时物料、生产流程、工装夹具、仪器设备、加工方法的适用性。
2.0范围:本厂所有开发的放产前的新产品及需要再试产的产品。
3.0职责:
3.1开发部
3.1.1主导新产品试产工作;
4.4试产前生产部主管按PIE相关技术文件试装产品,熟悉新产品为排位作好准备。
坪地伟达电器制品厂
试产工作指引(暂行)
编码:WI-R&D-010
版本:1.0
生效日期:1/8/2005
第3页,共3页
4.5试产前生产部要准备好所有的试产物料,并运输到试产地点。
4.6试产时由生产主管、拉长及PIE排位,开发责任工程师协助排位,品管部主管到拉上检查制品的工艺及质量。
生效日期:1/8/2005
第2页,共3页
3.3品管科
3.3.1物料检查指示单;
3.3.2半成品检查指示单;
3.3.3成品检查指示单;
3.3.4提供试产报告给开发部。
3.4物控部
3.4.1确认试产日期及数量;
3.4.2安排及发放所有试产用物料。
3.5生产部
3.5.1试产场所安排;
3.5.2人员调配;
3.5.3工装夹具跟进;
3.2 PIE(在试产前完成)
3.2.1生产工艺流程图(排位图);
3.2.2作业指导书(装嵌图);
3.2.3工装夹具、设备;
3.2.4标准工时(试产后提供);
3.2.5提供试产报告给开发部。
编写:胡新华
审核:
产品试制作业指导书
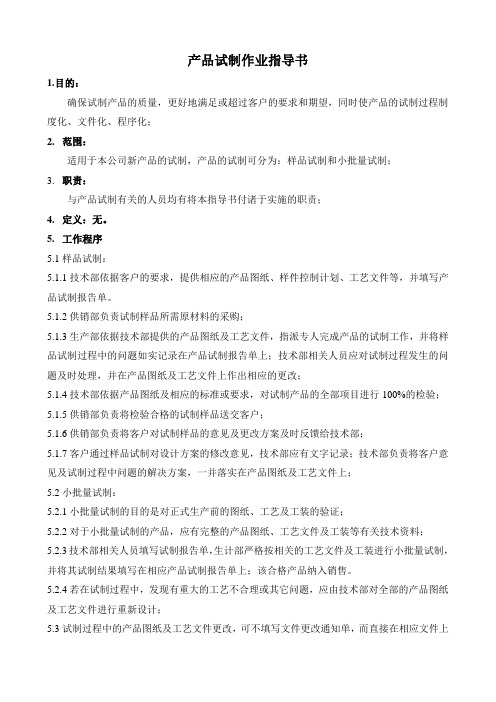
产品试制作业指导书1.目的:确保试制产品的质量,更好地满足或超过客户的要求和期望,同时使产品的试制过程制度化、文件化、程序化;2.范围:适用于本公司新产品的试制,产品的试制可分为:样品试制和小批量试制;3.职责:与产品试制有关的人员均有将本指导书付诸于实施的职责;4.定义:无。
5.工作程序5.1样品试制:5.1.1技术部依据客户的要求,提供相应的产品图纸、样件控制计划、工艺文件等,并填写产品试制报告单。
5.1.2供销部负责试制样品所需原材料的采购;5.1.3生产部依据技术部提供的产品图纸及工艺文件,指派专人完成产品的试制工作,并将样品试制过程中的问题如实记录在产品试制报告单上;技术部相关人员应对试制过程发生的问题及时处理,并在产品图纸及工艺文件上作出相应的更改;5.1.4技术部依据产品图纸及相应的标准或要求,对试制产品的全部项目进行100%的检验;5.1.5供销部负责将检验合格的试制样品送交客户;5.1.6供销部负责将客户对试制样品的意见及更改方案及时反馈给技术部;5.1.7客户通过样品试制对设计方案的修改意见,技术部应有文字记录;技术部负责将客户意见及试制过程中问题的解决方案,一并落实在产品图纸及工艺文件上;5.2小批量试制:5.2.1小批量试制的目的是对正式生产前的图纸、工艺及工装的验证;5.2.2对于小批量试制的产品,应有完整的产品图纸、工艺文件及工装等有关技术资料;5.2.3技术部相关人员填写试制报告单,生计部严格按相关的工艺文件及工装进行小批量试制,并将其试制结果填写在相应产品试制报告单上;该合格产品纳入销售。
5.2.4若在试制过程中,发现有重大的工艺不合理或其它问题,应由技术部对全部的产品图纸及工艺文件进行重新设计;5.3试制过程中的产品图纸及工艺文件更改,可不填写文件更改通知单,而直接在相应文件上作出更改,并记录在产品试制报告单中;5.4试制人员对所填入产品试制报告单中试制过程的内容负责;5.5由于工艺或工装的重大变化或两年内没有生产的产品在再次投入生产前需重新试制;5.6试制完成后,相关技术文件连同试制报告单交回技术部归档;6. 相关文件:7. 质量记录:产品试制报告单8.作业流程无。
- 1、下载文档前请自行甄别文档内容的完整性,平台不提供额外的编辑、内容补充、找答案等附加服务。
- 2、"仅部分预览"的文档,不可在线预览部分如存在完整性等问题,可反馈申请退款(可完整预览的文档不适用该条件!)。
- 3、如文档侵犯您的权益,请联系客服反馈,我们会尽快为您处理(人工客服工作时间:9:00-18:30)。
文件制修订记录
1.0目的
指导试产能顺利进行和正确完成,保障下一次大批量生产能顺利完成。
2.0适用范围
2.1适合所有新产品的第一次生产。
2.2适合旧产品更改版本后第一次生产(重大更改如设计,线路,功能)。
3.0参考文件
3.1产品实现过程控制程序
4.0职责
4.1生产管理课:负责安排新产品的试产具体生产日期和出货日期。
4.2生产技术课:负责制作相关的工艺文件和产品功能测试作业指导书。
负责安排召开新产品会议和新产品的试产总结会议。
负责新产品工治具的评估及及制作跟进。
4.3生产部:负责安排人员生产新产品,并确保其品质。
4.4品质部:负责监督新产品的试产全过程。
5.0定义:无
6.0內容
6.1生产管理课收到客户的生产订单后,若是新产品,则须填写”制造可行性分析报告(订单评审)”,并发至各相关部门评估有关事项,确认准备情况,及时回复给生产管理课。
6.2生产技术课IE收到客户提供的较完整的资料(有客供BOM,装配资料及Gerber File等),并与客户确认资料无误后,在一周内制定出试产文件.简单之
型号可直接发出受控文件,复杂的型号可先盖试产印后发放到各相关部门.所有试产文件须在新产品试产前发出。
6.3根据各部门的准备情况,如需进行试产,由生产管理课决定试产日期.试产时,要求各部门相关人员准时到生产现场协助解决生产问题,分析出现的问题和发掘潜在的问题,纠正在生产流程的工序或作业方法,品质部记录各品质问题。
6.4一般情况下,样板需经生产部QC人员检验,品质部OQC全检或抽检,才能出货,特别情况如客户同意不经品质部检验则生产管理课需在”送货单”上作出注明,若客户交期紧急,来不及检验时,需经负责该客户生产管理课的担当确认,并在”送货单”上签名。
6.5对于客户亲自制作或指导制作的样板,可以不经品质部检验,但需生产管理部在”送货单”上作出注明,并由客户或负责该客户的担当签名确认。
6.6对于正常生产的产品,客户需带走作分析样板用时,经客户同意,可以不经过品质部检验,但需生产管理课在”送货单”上作出注明,由客户签名确认或负责该客户的担当签名确认。
6.7当试产结束后,各部门填写相关报告内容的意见及问题,并用E-mail发给技术部生产技术课IE相关担当总结统筹及填写”试产总结报告”,再由IE相关担当主持召开试产总结会议,讨论新产品的试产情况及大批量生产时的改善,将结果填写在”试产总结报告”上,并由生产技术课IE存档。
6.8新产品试产完后,使用部门在收到正式受控作业指导书后,两天内将该新产品盖有试产印章的所有试产文件如数交回IE,生产线不能试产文件与正式受控文件同时使用,以免出现用错文件的情况发生。
6.9IE根据生产的实际情况修正试产文件,然后制定出正式的作业指导书,承认后由ISO课发出受控的工艺文件。
7.0记录表格
7.1新产品试作导入记录7.2试产总结报告
新产品试产总结报
告表.xls
7.3"试产"印章
7.4试产WI签收记录表。