汽车车身设计-第三章
汽车车身设计

汽车车身设计发动机盖发动机盖(又称发动机罩)是最醒目的车身构件,是买车者经常要察看的部件之一。
对发动机盖的主要要求是隔热隔音、自身质量轻、刚性强。
发动机盖的在结构上一般由外板和内板组成,中间夹以隔热材料,内板起到增强刚性的作用,其几何形状由厂家选取,基本上是骨架形式。
发动机盖开启时一般是向后翻转,也有小部分是向前翻转。
向后翻转的发动机盖打开至预定角度,不应与前档风玻璃接触,应有一个约为10毫米的最小间距。
为防止在行驶由于振动自行开启,发动机盖前端要有保险锁钩锁止装置,锁止装置开关设置在车厢仪表板下面,当车门锁住时发动机盖也应同时锁住。
车顶盖车顶盖是车厢顶部的盖板。
对于轿车车身的总体刚度而言,顶盖不是很重要的部件,这也是允许在车顶盖上开设天窗的理由。
从设计角度来讲,重要的是它如何与前、后窗框及与支柱交界点平顺过渡,以求得最好的视觉感和最小的空气阻力。
当然,为了安全车顶盖还应有一定的强度和刚度,一般在顶盖下增加一定数量的加强梁,顶盖内层敷设绝热衬垫材料,以阻止外界温度的传导及减少振动时噪声的传递。
行李箱盖行李箱盖要求有良好的刚性,结构上基本与发动机盖相同,也有外板和内板,内板有加强筋。
一些被称为“二厢半”的轿车,其行李箱向上延伸,包括后档风玻璃在内,使开启面积增加,形成一个门,因此又称为背门,这样既保持一种三厢车形状又能够方便存放物品。
如果采用背门形式,背门内板侧要嵌装椽胶密封条,围绕一圈以防水防尘。
行李箱盖开启的支撑件一般用勾形铰链及四连杆铰链,铰链装有平衡弹簧,使启闭箱盖省力,并可自动固定在打开位置,便于提取物品。
翼子板翼子板是遮盖车轮的车身外板,因旧式车身该部件形状及位置似鸟翼而得名。
按照安装位置又分为前翼子板和后翼子板,前翼子板安装在前轮处,因此必须要保证前轮转动及跳动时的最大极限空间,因此设计者会根据选定的轮胎型号尺寸用“车轮跳动图”来验证翼子板的设计尺寸。
后翼子板无车轮转动碰擦的问题,但出于空气动力学的考虑,后翼子板略显拱形弧线向外凸出。
汽车设计-设计教学3

设计在线网站群:中国工业设计在线 | 中国平面设计在线 | 中国环境设计在线 | 中国数码设计在线......设计资讯设计视角设计长廊设计引擎设计沙龙设计书局设计商会您现在的位置:设计在线 » 简体版 » 设计沙龙 » 原创产品设计您没有新的站内短信 | 帮助 | 搜索 | 会员 | 团队 | 收藏 | 设置 | 注销 [ cyaky ]◇◇原创产品设计教学之Ⅰ◆◆汔车设计◆◆前往页面 上一个 1, 2, 3, 4, 5, 6, 7 下一个设计沙龙 首页 -> 原创产品设计阅读上一个主题 :: 阅读下一个主题作者留言蓝蓝的鱼论坛版主注册日期: 2002-06-24 会员编号: 1,438 积分: 21.08 文章: 380 来自: 北京 发表于: 2003-11-14, 9:23 pm 发表主题: Re: ◇◇原创产品设计研究之Ⅰ◆◆汔车设计◆◆不错呀。
在哪里做的?返回页首cosnowq论坛版主注册日期: 2003-04-06 会员编号: 39,278 积分: 20.94 文章: 1155来自: 嵩山南路140#发表于: 2003-11-15, 1:27 am 发表主题: Re: ◇◇原创产品设计研究之Ⅰ◆◆汔车设计◆◆350Z033 副本 拷贝.JPG档案描述: 档案大小:47.01 KB浏览次数:档案已被下载 423 次200192614405 副本 拷贝.JPG档案描述: 档案大小: 28.81 KB浏览次数:档案已被下载 418 次在空气动力学上,有法国物理学家贝尔努依证明的一条理论:空气流速的速度与压力成反比。
也就是说,空气流速越快,压力越小;空气流速越慢,压力越大。
例如飞机的机翼是上面呈正抛物形,气流较快;下面平滑,气流较慢,形成了机翼下压力大于上压力,产生了升力。
如果轿车外型与机翼横截面形状相似,在高速行驶中由于车身上下两面的气流压力不同,下面大上面小,这种压力差必然会产生一种上升力,车速越快压力差越大,上升力也就越大。
汽车车身设计(复习参考)(青岛大学)
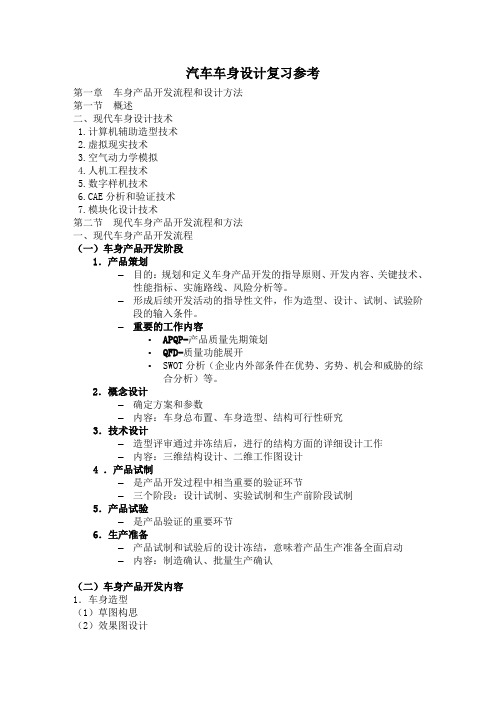
汽车车身设计复习参考第一章车身产品开发流程和设计方法第一节概述二、现代车身设计技术1.计算机辅助造型技术2.虚拟现实技术3.空气动力学模拟4.人机工程技术5.数字样机技术6.CAE分析和验证技术7.模块化设计技术第二节现代车身产品开发流程和方法一、现代车身产品开发流程(一)车身产品开发阶段1.产品策划–目的:规划和定义车身产品开发的指导原则、开发内容、关键技术、性能指标、实施路线、风险分析等。
–形成后续开发活动的指导性文件,作为造型、设计、试制、试验阶段的输入条件。
–重要的工作内容•APQP-产品质量先期策划•QFD-质量功能展开•SWOT分析(企业内外部条件在优势、劣势、机会和威胁的综合分析)等。
2.概念设计–确定方案和参数–内容:车身总布置、车身造型、结构可行性研究3.技术设计–造型评审通过并冻结后,进行的结构方面的详细设计工作–内容:三维结构设计、二维工作图设计4 .产品试制–是产品开发过程中相当重要的验证环节–三个阶段:设计试制、实验试制和生产前阶段试制5.产品试验–是产品验证的重要环节6.生产准备–产品试制和试验后的设计冻结,意味着产品生产准备全面启动–内容:制造确认、批量生产确认(二)车身产品开发内容1.车身造型(1)草图构思(2)效果图设计(3)胶带图设计(4)CAS设计(5)模型制作(6)模型测量和线图设计2.车身结构可研是指以满足车身结构开发目标并服务于车身造型的结构可行性研究、构思及布置等活动的总称。
(1)提供给造型的控制条件(2)提供给车身结构可研的输入条件(3)车身结构可研的输出(4)方案CAE分析3.三维结构设计(1)白车身结构设计(2)内饰结构设计(3)外饰结构设计(4)附件类结构设计4.二维图设计5.CAE计算及验证(1)概念设计阶段(2)详细设计阶段及结构改进阶段6.车身试制(1)试制原则(2)试制方案(3)试制内容7.车身试验8.工艺支持(1)冲压工艺(2)涂装工艺(3)焊接工艺(4)总装工艺9.绿色设计二、现代车身设计方法(一)性能设计•现代设计是以CAE技术为支撑的性能设计。
《汽车车身结构与设计》个人总结

一、汽车车身功能:
1、为乘员提供安全舒适的乘坐环境,满足:
1)乘坐舒适性,包括居住性、振动的舒适性及空气调节等。
2)密封性、隔热性、防振性和防噪声性。
3)操纵方便性。
4)视野性。
5)上下车方便性。
6)行驶安全性。
2、提供发动机及底盘等部件的装配。
3、汽车美观造型的体现。
二、车身的技术特点:
1、车身技术涉及当代科技领域的多门学科,而且各学科之间高度交叉和融合。
2.汽车表面及周围的流谱和局部流场的研究,分析作用在汽车上的气动力机理。
3.发动机和制动装置空气冷却问题的研究。
4.汽车内部自然通风和换气问题的研究。
二、流场:将流经物体的气流的属性如速度、压强、密度等表示为空间坐标和时间t的函数,、分别称为速度场、压强场、密度场,其总合称为流场。定常流场、非定常流场。
4.车身的外形和布置必须保证驾驶员和乘员有良好的视野。
5.车身材料必须是轻质的,以降低整车质量。
6.车身外形具有低的空气阻力,节省能源。
7.必须能在发生事故时对乘员提供保护。
8.车身材料必须来源丰富、成本低,所选择的材料必须能够实现高效率的制造和装配。
9.结构设计和选材必须保证车身在整个使用期间满足对冷、热和腐蚀的抵抗能力的要求。
七、客车蒙皮种类及特点:
应力蒙皮:蒙皮参与承载,可使骨架比较细,车身自重较轻。
预应力蒙皮:蒙皮不参与承载,只起到装饰作用,因为有应力,垂直于地板的刚度得以提高。
八、三化问题:
1.“系列化、通用化、标准化”:产品系列化、零部件通用化、零件设计的标准化。
2.平台化:指使用相同的底盘结构,生产不同的汽车产品。往往造型、功能、目标市场不一样,但是底盘和车身结构却是一样的,零部件也有很强的通用性。
汽车车身结构与设计(第三章)

硬点尺寸前缀和编号
在SAE J1100 中给出了硬点、硬点尺寸代号、定义 和测量方法。硬点尺寸代号采用前缀加数字加后缀 的形式表示, 部分前缀和数字的含义见表3-9。后缀 用“ -1”、“ -2”的形式表示该尺寸为第一排、第 二排座椅
车身外部尺寸
长度方面的尺寸主要有轴距、车长、前悬、后悬等;
车身外部尺寸
宽度方向的尺寸主要有轮距、车宽、翼子板间距等;
车身外部尺寸
高度方向的尺寸主要有车高、最小离地间隙、门槛高度、 保险杠高度、车灯高度等;
车身外部尺寸
角度方向尺寸主要有风窗倾角、侧窗倾角、接近角、离去角、通过角等。
车身内部尺寸
车身内部尺寸主要包括长度、宽度、高度和角度等方面的 尺寸,SAE J1100对内部尺寸给出了详细的规定。
SAE 平均头廓线及包络面
头廓包络面的尺寸和定位
SAE J1052 标准中,对应各种座椅水平调节行程的乘员头廓包络 面尺寸(距离头廓包络中心的距离)
对于驾驶人和前排乘客,头廓包络在Y 方向的尺寸要向外延长 23mm。行程可调节座椅的头廓包络面只在侧视图有向前下方的 12度的倾角,其他视图倾角都为零。对于固定座椅,头廓包络 在各个视图方向的倾角都为零。
95 百分位眼椭圆(座椅行程大于 133mm) 中P1、P2、P3、P4 位
置
影响眼椭圆定位的布置参数
眼椭圆的应用
以SAE眼椭圆为理论依据,可进行内外视镜布置、 驾驶人前方视野的设计和校核、车身A/ B/ C柱盲 区的计算、仪表板上可视区的确定、刮水器布置 和刮扫区域校核和遮阳带位置的确定等。
利用眼椭圆进行驾驶人前方下视野设计的方法
电动客车人机工程学优化
轿车车身设计-开闭件设计[92页]
![轿车车身设计-开闭件设计[92页]](https://img.taocdn.com/s3/m/97f38df97375a417876f8f9c.png)
二、车门结构组成
• 合页式铰链
– 两个合页分别与车门和车身门柱连接,合页之间用销轴 定位
– 优点是质量轻、刚度高、易于装配
佛山市南海盐步汽车配件五金厂
第一节 车门系统
(二)车门附件
一、车门系统功能要求 • 1.车门铰链和限位系统
二、车门结构组成
• 车门开度限位器
– 具有门半开时支承功能和全开时限制车门的最大开度功 能,防止车门外板与车身相碰,并使车门停留在所需开 度,防止车门自动关闭的作用
第一节 车门系统
(一)门体
一、车门系统功能要求 •
二、车门结构组成
1.车门外板
– 一般采用0.65mm~0.85mm厚的薄钢板冲压成型 – 由于轻量化和侧面碰撞安全性的要求,广泛使用高强度钢板
• 2.车门内板
– 是车门几乎所有附件的安装体,是车门的重要的支撑板件
– 一般采用0.7~0.85mm的薄钢板拉延成型,对于整体式门内板, 拉延深度形成门体厚度的侧板
一、车门系统功能要求 盖等部件
二、车门结构组成
佛山市南海盐步汽车配件五金厂
第一节 车门系统
1. 有必要的开度,开启后能停止在最大开度和半开的位置
一、车门系统功能要求 2. 安全可靠
二、车门结构组成
3. 操作性良好
4. 具有良好的密封性,使乘员与外界隔离
5. 具有足够的刚度
6. 制造工艺性好,易于冲压并便于安装附件
• 内、外板是分别与门的内外板一体冲压的
• 车门本体零件数量少,制造方便
• 车门刚性好,便于设两道密封条,提高密封性能
• 需较大的压床台面尺寸,且废料较大
佛山市南海盐步汽车配件五金厂
第一节 车门系统 一、车门系统功能要求 二、车门结构组成
3.1 汽车车身设计开发流程与方法

第三章汽车车身设计开发技术与方法3.1汽车车身设计开发流程与方法学3.1.1车身设计开发主要工作内容及流程(程序)1)车身总布置设计及安全法规计算校核(或三维数字虚拟样机Archetype)2)造型设计3)三维曲面和造型面设计4)1:5或1:4 模型及1:1外模型制作或数控加工(或三维数字模型)5)1:1内模型(或三维数字模型)6)发动机舱三维数字模型7)地板三维数字模型8)测量与曲面光顺9)白车身结构详细设计(BIW)(9.1)1:1外模型光顺后数据分块(9.2) 车身设计断面的定义与尺寸确定(9.3) 密封结构确定与密封件选择(9.4) 确定分块线(9.5) 与车身有关的设计硬点的确定(9.6) 左右侧围设计(A, B, C, D柱设计, 前后翼子板设计)(9.7) 顶盖设计(外板, 横梁与纵边梁设计) (9.8) 发动机前围板设计(9.9) A柱下段设计(9.10) 发动机舱与前轮包设计(9.11) 前后灯具设计(9.12) 格栅设计(9.13) 前围板设计(9.14) 前保险杠设计(9.15) 地板总成设计(前中后)(9.16) 后门总成设计(9.17) 前门总成设计(9.18) 尾门总成设计(9.19) 前发动机罩设计(9.20)前风当总成设计10)内饰、外饰设计11)先行车, 螺钉车或概念车的(Prototype)试制,第二轮试验样车(定型车)试制12)碰撞与结构分析及结构优化设计13)成型过程仿真14) 模具与工艺工装设计如图3.1.1为车身详细设计阶段面向对象的产品模型(OPM)并行设计流程图OM2 OM2 OM2 OM2 OM2 OM2T21: CAD T22: DF A可装配设计T23: CAE T24: 评审T25: DFM 可制造设计T26: CS 碰撞仿真IM21: 输入产品模型,请求详细设计OM21: 向下游预发布零部件信息OM22: 输出DF A结果OM23: 输出CAE结果OM24: 输出同意或修改概要设计建议OM25: 输出DFM结果输出OM26: CS结果图3.1.1 汽车车身并行详细设计OPM模型31 32 3334 35T 31: CAPP T 32: CAFD 机算机辅助工装卡具设计(CA FIT DE SIGN)T 33: CAM T 34: MPS(制造过程仿真) T 35: 评审 IM 31: 请求加工过程设计 OM 31: 输出CAPP 结果 OM 33: 输出 CAFD 结果OM 33: 输出CAM 结果 OM 34: 输出MPS结果OM 35: 输出同意或修改详细设计建议图3.1.2 汽车产品开发试制与加工过程设计OPM 模型 g 1: 请求详细设计(结构) g 2: 预发布零部件消息,请求试制或加工过程设计 g 3: 请求修改概念设计(造型设计) g 4: 请求修改详细设计(结构设计)图3.1.3 汽车车身并行开发过程OPM 模型图3.1.4 车型数字化设计过程3.1.2 车身结构设计方法学1 1995年后的先进的车身设计技术与方法1995年后车身设计技术发展与市场需求体现在如下几个方面:图3.1.5 虚拟产品开发描述图3.1.6 白车身设计过程描述图3.1.7 并行设计与开发周期降低图3.1.8 全数字化设计方法图3.1.9 确定设计结构方案图3.1.10 产品设计及工艺设计集成计方法图3.1.12 参数化结构断面设计图3.1.13 全相关参数化的车身开发全过程2 数字化车身结构设计方法学(1)设计硬点设计区的设计方法复杂的结构实际上是众多简单的设计的叠加组合(复杂设计简单化)任何复杂的车身结构设计与设计结果都是由如下两个方面决定: (a) 满足诸多设计硬点的特征结构设计(HARDPOINT DESIGN AREA), 例如, 造型面硬点, 与车身有关的零部件装配孔面及结构等设计硬点, 选定的设计断面结构, 造型分界线硬点, 造型形状形成的设计断面引导线硬点, 车身零件间的焊接装配面, 零件的分块线硬点. (b) 自由设计区设计(FREE DESIGN AREA), 即在满足设计硬点基础上, 进行的自由设计区, 一般非设计硬点的设计区域都属于自由设计区, 自由设计区不同的设计人员会得到不同的设计结果, 这也是自由设计区自由的特点, 但这不等于自由设计区可以胡乱设计, 应遵循如下一些设计原则, 以便才能使设计结构更合理, 水平更高.因此车身设计过程与方法应满足如下公式:车身结构设计特征(BSDF)=自由设计区自由设计特征(FDF)+断面设计硬点决定的设计特征(SDHF)+造型设计硬点决定的特征(IDHF)+造型决定的断面引导主轴线(一个零件多个断面几何中心连线)特征(ISSF)+其他附件或COPY件等确定的设计硬点特征(CDHF)+零件分块线与焊接边界线等的设计硬点特征(BDHF)即为:BSDF=FDF+SDHF+IDHF+ISSF+CDHF+BDHF车身零件结构的设计过程或设计建模(BSDP or BSDM)=用三维CAD软件完成车身结构设计特征的过程或结果(BSDFP or BSDFM)即为:BSDP=BSDFPBSDM=BSDFM车身设计建模(BDM)=完成所有车身零件的设计建模与装配设计建模的总称(TOL_BSDM) 即为:BDM=TOL_BSDM全数字化车身设计开发(BDD)=采用三维CAD 软件完成全部车身设计建模, 并采用CAD/CAE/CAM一体化技术完成车身设计,结构优化及制造(或制造模具)的全过程(3D_CAD/CAE/CAM_BDM).即为:BDD=3D_CAD/CAE/CAM_BDM(2) 自由设计区的设计方法与设计原则a 自由设计区的设计方法(a) 先用三维CAD软件将设计硬点确定的结构与特征连接成一体, 成为一个粗的异型大面, 中间可以用一些平面与设计硬点面的相交获得连接线或倒角线.(b) 对设计硬点之间形成的设计区域-自由设计区每一个进行分析, 强度和刚度一般性要求的部位一般小于50*50mm的面积区域, 可以不加特征结构(加强筋, 加强沉孔(如果没有密封要求), 折边, 卷边等特征结构建模), 但要在边界上导角. 大于50*50的区域一般要加特征以便加强结构并导角,较大的区域不留任何空地, 以便使刚度最大, 材料最省.a 自由设计区的设计准则(a) 最大刚度原则- 自由设计区必须尽力获得最大刚度的设计原则, 因此, 要加加强筋和加强沉孔, 以便获得高水平的设计结构.(b) 最轻量化原则- 设计结构要确保满足刚度要求的基础上使材料最省的原则, 尽可能使结构设计可以使料厚簿一些, 没有密封要求的结构可以用沉孔以便轻量化与刚度最大化的双嬴, 等要充分考虑结构形式和结构方案.(c) 最大园角原则-自由设计区, 一般都是内部结构区域, 不在外观缝隙线条区域. 因此, 为了提高冲压工艺性, 减少制造成本, 应尽可能设计较大的设计过渡园角. 但不能影响设计硬点结构. 在在外观区域应尽可能最小园角原则,最小值为料厚(d) 特征结构最大斜度原则- 筋槽设计的立面尽可能采用较大的斜度. 以便获得较好的制造工艺性, 防止冲压裂纹和褶皱.(e) 最符合工艺性原则-从设计结构上和面的光顺程度上尽可能获得好的制造工艺性, 如材料流动均匀性与制造可能性.(f) 创新与多样化设计原则-自由自由就意味着允许多样化, 也就是创新原则.(g) 最复杂化原则, 因为模具加工不会增加制造成本, 只会降低成本(如材料轻, 成本低了).(h) 满足CAE/OPTIMIZATION结构优化分析设计要求.。
车身结构设计复习提纲-学生

车身结构设计复习提纲第一章车身概论1、整车的组成;2、车身的组成;3、白车身的概念;4、车身结构的识别;5、承载式和非承载式车身的概念;第二章车身设计方法1、传统设计方法和现代设计方法(仿形法);2、逆向工程的定义;第三章车身布置设计(重点)1、车身总布置设计的原则;2、车身总布置设计的内容;3、轮罩外形尺寸的确定;4、驾驶员座椅H点位置的确定;5、后排乘员座椅H点位置的确定;6、上下车方便性的布置;7、视野性的主要影响因素;8、车身制图标准:坐标零平面的确定等规定。
第四章人体工程学(重点)1、百分位尺寸的概念;2、驾驶员的手伸及界面概念;3、操作扭件布置合理性的检验方法;4、驾驶员的眼椭圆及其含义;5、眼椭圆样板在车身中的定位;6、前方视野障碍角的要求;7、刮净率;8、风窗玻璃刮扫面积及部位的确定(方法不要求);第五章汽车空气动力学(重点)1、汽车空气动力学的研究手段2、流线和流谱的概念;3、流体流动的连续性;4、附面层:5、汽车前部流谱的主要影响因素;汽车底部气流主要影响因素;6、风压中心;7、汽车减小气动升力的一般措施;8、风压中心的位置对汽车的空气动力稳定性影响第六章车体结构设计1、车身本体结构的组成及特点;2、前围结构的功能要求及前围结构;3、车身侧围设计要点;4、旋转式车门的组成和分类:5、车门和门框间的间隙:6、车门铰链布置的要求:7、车身轻量化设计技术主要表现在哪些方面:第七章轿车车身碰撞安全性设计(重点)1、主动安全性和被动安全性的概念;2、安全车身的特点:3、安全气囊的作用、组成。
4、GB11551-2003,GB 20071-2006 碰撞标准的试验方法和评价指标(如:碰撞初速度及碰撞最大加速度指标);5、C-NCAP与我国强制标准对比:第八章车身的密封1、轿车车身的密封性设计分类:2、车身前后风窗玻璃的安装有两种方法:3、门玻璃的密封4、车门与门框的密封第九章轿车车身通风结构设计1、通风口位置的确定原则:。
现代汽车车身设计技术课件(完整篇)

现代汽车车身设计技术课件第一部分:引言汽车车身设计是汽车工业中至关重要的一环,它不仅关系到汽车的外观美感,还直接影响到汽车的空气动力学性能、安全性能和舒适性。
随着科技的进步和消费者需求的不断变化,现代汽车车身设计技术也在不断发展和创新。
本课件将带您深入了解现代汽车车身设计技术,包括设计理念、设计流程、材料选择、制造工艺等方面的内容。
一、设计理念现代汽车车身设计强调以人为中心,注重用户体验和情感共鸣。
设计师们通过研究消费者的需求和喜好,结合汽车品牌的特点和定位,创造出符合时代潮流和审美趋势的车身造型。
同时,设计师们还注重车身设计的创新性和可持续性,力求在满足功能需求的同时,实现环保和节能的目标。
二、设计流程1. 市场调研:了解消费者的需求和喜好,分析竞争对手的产品特点,为车身设计提供依据。
2. 概念设计:根据市场调研结果,设计师们提出初步的设计方案,包括车身造型、颜色、材质等方面的构思。
3. 详细设计:在概念设计的基础上,设计师们对车身各个部分进行详细设计,包括车身结构、车门、车窗、车灯等。
4. 工程设计:工程师们根据详细设计图纸,进行车身结构的强度和刚度分析,确保车身的安全性能。
5. 制造工艺设计:根据工程设计图纸,设计师们制定车身制造的工艺流程,包括冲压、焊接、涂装等环节。
6. 试制和验证:根据制造工艺设计,制造出实车样品,进行各项性能测试和验证,确保设计目标的实现。
三、材料选择现代汽车车身设计在选择材料时,需要考虑材料的强度、刚度、轻量化、耐腐蚀性、可回收性等多个方面的因素。
常用的车身材料包括钢材、铝合金、镁合金、碳纤维复合材料等。
设计师们根据车身各个部位的功能需求,选择合适的材料,以实现最佳的性能和成本平衡。
四、制造工艺现代汽车车身制造工艺包括冲压、焊接、涂装等环节。
冲压工艺用于制造车身的外覆盖件,如车门、车顶、翼子板等;焊接工艺用于将各个冲压件焊接成完整的车身结构;涂装工艺用于提高车身的耐腐蚀性和美观性。
第三章 UG基础建模

汽车车身计算机辅助设计
在绘制草图曲线的过程中,不必考虑尺寸的准 确性和各段曲线之间的几何关系,只须绘出近似的 曲线轮廓即可。然后应用草图约束和定位,可进一 步对这些曲线进行尺寸约束、几何约束和定位操作, 是用户可以精确的控制它们的尺寸、形状和位置, 并可以在需要时随意更改。在绘制草图曲线的过程 中,根据几何对象间的关系,有时会在几何对象上 自动添加某些几何约束(如水平、垂直和相切), 如下图所示。
• 3.1.1点构造器 点击【插入】|【基准】|【点】命令,可以打开点构造 器对话框,或者是在曲线曲面建模过程中,只要涉及到点特 征,都会打开点构造器对话框,不管以何种方式启动【点构 造器】,其对话框和功能都是一样的。图3-1给出的是点构造 器对话框。
山东理工大学车身数字化研究所
汽车车身计算机辅助设计
•
构造点的方式 输入创建点的坐标值 2. 捕捉点方式生成 3. 利用偏置生成 1)矩形偏置 2)圆柱偏置 3)球偏置 4)向量偏置 5)沿曲线偏置
山东理工大学车身数字化研究所
汽车车身计算机辅助设计
• 3.1.2 创建点集 点击工具栏的上的命令就会出现如图3-11所示的【点集】 对话框,点集的生成方式有很多种。 1. 曲线上的点 等圆弧长方式 等参数方式 几何级数方式 弦公差方式 递增的圆弧长方式 曲线上百分比方式 投影点方式
汽车车身计算机辅助设计
第三章 UG基础建模
教学要求 本章讲述UG的基础建模命令,包括UG NX的基 本操作,草图工具简介,实体建模等的常用命令。 通过对这些常用命令的学习,要求读者能掌握UG软 件的基础操作,并能使用该软件建立汽车部件模型。
山东理工大学车身数字化研究所
汽车车身计算机辅助设计
3.1 UG NX 基本操作
第三章_汽车车身结构PPT课件
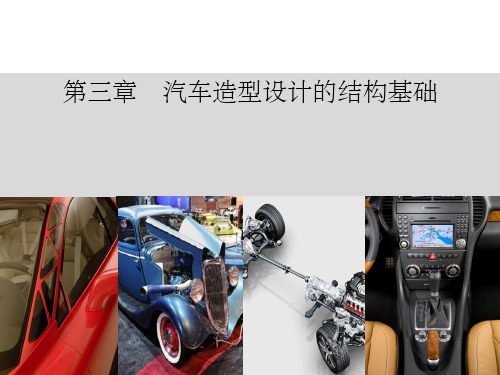
.
11
3.1.1 汽车布置形式
适时四驱就是根据车辆的行驶路况,系统会自动切换为两驱或四驱模 式。适时驱动汽车其实跟驾驶两驱汽车没太大的区别,操控简便,而 且油耗相对较低,广泛应用于一些城市SUV或轿车上。
.
12
3.1.1 汽车布置形式
全时四驱就是指汽车的四个车轮时时刻刻都能提供驱动力。因为是
时时四驱,没有了两驱和四驱之间切换的响应时间,主动安全性更
.
3
3.1.1 汽车布置形式
汽车传动系的布置形式与发动机的位置及驱动形式 有关,一般可分为:
前置前驱;
前置后驱;
后置后驱;
中置后驱;
全轮驱动;
.
4
3.1.1 汽车布置形式
发动机布置在车的前部,所以整车的重心集中在车身前段,由于车 体会被前轮拉着走的,所以前置前驱汽车的直线行驶稳定性非常好 。
发动机动力经 过差速器后用 半轴直接驱动 前轮,不需要 经过传动轴, 动力损耗较小 ,适合小型车 。不过由于前 轮同时负责驱 动和转向,所 以转向半径相 对较大,容易 出现转向不足 的现象。
轮驱动,这是一种最传统的驱动
形式。大多数货车、部分高级轿
车和部分客车都采用这种驱动形
式,但采用该形式的小型车很少
。
②前置前驱:即发动机前置、前
轮驱动。货车和大客车基本上不
采用该形式。
③全轮驱动:全轮驱动在吉普车
和越野车上运用较多,最近也有
部分新式轿车采用了全轮驱动形
图2-1全轮驱动
式(图2-1)。
.
采用固定速比减速器,去掉离合器,可减少机械 传动装置的质量、缩小其体积。
M—电动机 FG—固定速比减速器 D—差速器
车身结构优化设计与仿真分析

车身结构优化设计与仿真分析第一章:绪论汽车行业发展迅猛,汽车成为人们敞开心扉的必需品之一。
汽车车身结构优化设计与仿真分析,是当前汽车行业的一个热门研究方向。
车身结构优化设计和仿真分析可以降低整车开发的成本和时间。
针对此,本文将深入探讨车身结构优化设计与仿真分析的研究进展。
第二章:车身结构设计2.1 车身结构组成车身结构主要由车门、车顶、车底、车前端和车尾部分组成。
2.2 车身结构材料车身结构材料有钢、铝合金、碳纤维等。
不同材料具有不同的密度、强度和刚度。
此外,不同材料的冲压成形难易程度也有所差异。
2.3 车身结构设计方法在车身结构设计中,有效的设计方法可以提高车身结构的强度和刚度。
常用的车身结构设计方法有拓扑优化、计算机辅助设计(CAD)、计算机辅助工程(CAE)、三维模型及产品生命周期管理(PLM)等。
第三章:车身结构优化3.1 车身结构优化的意义车身结构优化是为提高车身结构的强度、刚度和轻量化而进行的。
对于汽车制造厂商,降低汽车的重量可以降低油耗和排放,达到环保的目的;并且轻量化的车身结构,还能提高汽车的安全性能。
3.2 车身结构优化方法车身结构优化主要分为参数优化、材料优化、构件优化等。
其中,参数优化指的是对车身结构的尺寸、形状、壁厚等参数进行优化;材料优化指的是对车身结构中使用的材料进行优化;构件优化指的是对车身结构的每一个组成部分进行优化。
这些优化方法可以针对不同的优化目标和优化需求进行综合优化。
第四章:仿真分析4.1 仿真分析的意义仿真分析是在车身结构设计、优化的过程中不可或缺的环节之一。
通过仿真分析,可以模拟不同行驶条件下汽车的运行情况,包括车身结构的受力状态和振动情况。
对于汽车设计师来说,仿真分析可以帮助他们预测汽车设计的可靠性,并为车身结构的优化提供指导意见。
4.2 仿真分析方法常用的仿真分析方法有有限元分析(FEA)、计算流体动力学(CFD)、结构优化方法等。
有限元分析可以模拟车身结构的受力情况;计算流体动力学可以模拟车身周围的空气流动情况;结构优化方法则可以为车身结构的优化提供指导意见。
汽车车身结构与设计

四、轮罩外型尺寸的确定和踏板的布置
为了绘制前轮表面,应先确定车轮跳动 到极限位置和最大转向角时所占有的空 间。
由于车轮转向时并不占用轮罩中部,为了充分利用空间,可以将其做成嵌入轮罩内的凹部,腾出来的 这一部分空间就可以用来布置离合器踏板或安放坐垫的最宽部分,这样就容许座椅降低或前移。
汽车车身结构与设计
3-1 轿车的总体布置设计
一、轿车车身总布置原则
1) 乘坐舒适性、操纵轻便性、温度调节性、视野性、安全性等方面的要求。 2)整车的经济性和行驶稳定性空气动力性要求。 3)对底盘各总成、发动机及电气设备的良好的接近方便性,维修保养方便性。 4)在满足性能要求的前提下,尽减轻车身质量,并具有良好的冲压焊接、装配及涂装工艺性。 5)按照汽车的级别、用途及法规选择各种车身附件,同时确定必装件与选装件。 6)尽量扩大车内空间,尤其是要尽量增大宽度方向的尺寸。 7) 确保良好的密封、通风换气、隔音、隔热及防振等性能。 8)必须满足国际、国内有关的各种法规和标准要求。 9)充分考虑车型的系列化、通用化。
前置前驱(FF)
采用了前置前驱驱动型式的整车具有如下缺点: 1.启动、加速或爬坡时,前轮负荷减少,导致牵引力下降; 2.前桥既是转向桥,又是驱动桥,结构及工艺复杂,制造成本高、维修保养困难。 3.前桥负荷较后轴重,并且前轮又是转向轮,故前轮工作条件恶劣,轮胎寿命短。
中置后驱(MR) 是大多数运动型轿车和方程式赛车所采用的型式。此外,某些大、中型客车也采用该型式
全轮驱动(nWD)
采用了全轮驱动驱动型式的整车的主要优点是良好的驾驶操控性和行驶性,缺点是比较废油,经济性 不好
二、动力总成的布置
动力总成包括发动机、离合器与变速器或发动机与液力变扭器。
整车设计及开发流程

整车设计及开发流程轿车车⾝的设计及开发流程⽬录概述:第⼀章:轿车车⾝设计要素第⼆章:整车开发流程第三章:项⽬开发流程第四章:项⽬开发过程中需归档的⽂件⽬录:第五章:可⾏性分析阶段第六章:车⾝相关间隙设计规范第七章:车⾝外间隙设计规范第⼋章:密封条的截⾯沿⽤规范第九章:鈑⾦过孔的问题第⼗章:门盖系统校核规范第⼗⼀章:⼯艺知识⼀、钣⾦冲压件冲压,焊接,和电镀的⼯艺性检查条例⼆、车⾝⼯艺性检查三、部分B21车⾝鈑⾦⼯艺分析报告:四、冲压钢板性能:五、冲压⼯艺⼯序六、焊接种类及相关介绍概述:车⾝是整车的重要组成部分,开发整车是⼀项很复杂的⼯程,车⾝也⼀样,它主要包括车⾝本体、外饰件、内饰及附件,由于它是轿车上载⼈的容器,因此要求轿车车⾝应具有良好的舒适性和安全性。
此外,轿车车⾝⼜是包容整车的壳体,能够最直观地反映轿车外观形象等特点,所以,轿车车⾝设计应⾮常注重外形造型,以满⾜⼈们对轿车外形地审美要求,取得较好的市场。
⽽汽车⼈体⼯程学、汽车空⽓动⼒学、汽车造型及审美艺术、汽车车⾝新材料的研究及开发、汽车车⾝结构强度分析、汽车车⾝设计⽅法及技术等⽅⾯的研究和应⽤,正是设计出具有良好性能的轿车车⾝的必要基础。
下⾯,分章予以说明:第⼀章:轿车车⾝设计要素轿车车⾝设计要素,亦是从事车⾝设计⼯作时,设计⼈员所必须考虑的⽅⾯和重点解决的关键技术,是提⾼车⾝设计质量的关键内容。
全⾯掌握、研究和应⽤车⾝的设计要素,是设计⼈员应具备的基本技能。
从现代轿车车⾝设计的⾓度出发,汽车产品的设计要素主要表现在如下⼏个⽅⾯:1.车⾝外形设计⽅⾯⑴车⾝空⽓动⼒特性要素⑵车⾝尺⼨确定的⼈体尺⼨要素⑶车⾝外形设计、内饰造型的美学要素⑷外形的结构性和装饰的功能性要素2.车⾝室内布置设计⽅⾯⑴⼈体⼯程要素,包括⼈体尺⼨、⼈体驾驶和乘坐姿势、⼈体操纵范围、⼈眼视觉和视野、⼈车视野、⼈体运动特征、⼈体的⼼理感觉等。
⑵车⾝内部设计的安全保护要素。
3.车⾝结构设计⽅⾯⑴结构设计的强度、刚度要求;⑵轻量化设计要素,包括结构合理性和合理选材;⑶结构设计的安全性要素⑷车⾝防腐蚀设计设计要素⑸车⾝密封性设计要素⑹结构设计的制造⼯艺性要素4.产品开发⽅⾯⑴产品开发的市场性要素;⑵系列化产品发展要素;⑶⽣产、⼯艺继承性要素。
车身结构与设计——第3章车身总布置设计
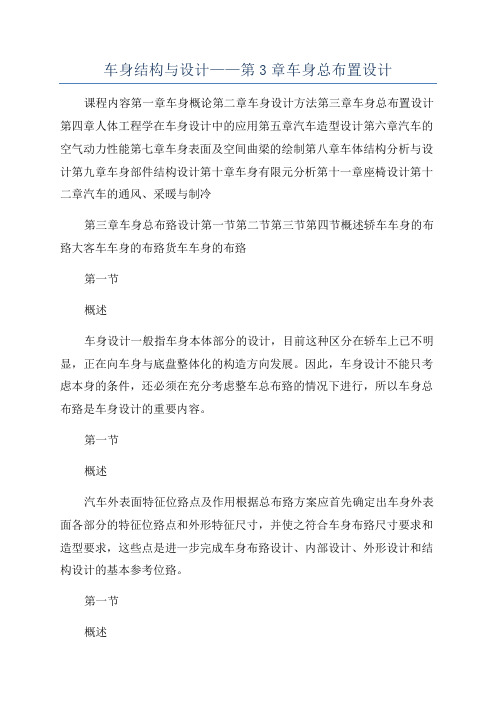
车身结构与设计——第3章车身总布置设计课程内容第一章车身概论第二章车身设计方法第三章车身总布置设计第四章人体工程学在车身设计中的应用第五章汽车造型设计第六章汽车的空气动力性能第七章车身表面及空间曲梁的绘制第八章车体结构分析与设计第九章车身部件结构设计第十章车身有限元分析第十一章座椅设计第十二章汽车的通风、采暖与制冷第三章车身总布臵设计第一节第二节第三节第四节概述轿车车身的布臵大客车车身的布臵货车车身的布臵第一节概述车身设计一般指车身本体部分的设计,目前这种区分在轿车上已不明显,正在向车身与底盘整体化的构造方向发展。
因此,车身设计不能只考虑本身的条件,还必须在充分考虑整车总布臵的情况下进行,所以车身总布臵是车身设计的重要内容。
第一节概述汽车外表面特征位臵点及作用根据总布臵方案应首先确定出车身外表面各部分的特征位臵点和外形特征尺寸,并使之符合车身布臵尺寸要求和造型要求,这些点是进一步完成车身布臵设计、内部设计、外形设计和结构设计的基本参考位臵。
第一节概述第一节注意:概述这些特征位臵点是在进行车身布臵设计的过程中,逐步被加以确定的,随着这些点的确定,符合设计要求的车身形状也就基本确定了。
而各部分的表面曲线和曲面的具体设计,可根据整车的造型持点及概念,在特征位臵点的控制下加以确定,使得车身整体表面形状协调、流畅和美观。
第一节概述车身总布臵设计在车身设计中的位臵车身总布臵的要求舒适性–影响舒适性的有关因素:座椅尺寸、形状及其与人体接触处的材质软硬度和质感,振动频率、视野以及内饰对乘员心理的影响效果和安全感。
安全性–正常行驶时的防护措施–发生意外时的补救措施可靠性–指允许超负荷下的安全性(构件局部的加强措施)视野性–最低限度必须保证驾驶时对周围一切国家交通法规所规定的路标、信号以及道路情况方便而有效地观察乘用方便性–是成员、驾驶员进出车厢和行李、货物装卸方便与否的评价标准。
车身主要零部件的设计要求发动机罩–要求隔热、隔音,自身质量轻,刚性强,一般分为内板、外板,中间有隔热层,布臵时应考虑其翻转方向。
- 1、下载文档前请自行甄别文档内容的完整性,平台不提供额外的编辑、内容补充、找答案等附加服务。
- 2、"仅部分预览"的文档,不可在线预览部分如存在完整性等问题,可反馈申请退款(可完整预览的文档不适用该条件!)。
- 3、如文档侵犯您的权益,请联系客服反馈,我们会尽快为您处理(人工客服工作时间:9:00-18:30)。
普通高等教育“十一五”国家级规划教材《汽车车身设计》第三章车身结构拓扑模型与力学模型提纲第一节作用在车身系统上的载荷一、车身结构承载型式二、作用在车身、车架上的载荷第二节车身结构的拓扑模型一、车身结构二、车身结构拓扑模型的建立三、应变能分析四、碰撞安全性对车身结构的要求第三节车身结构的力学特性和力学模型一、车身结构内力二、车身结构中构件的截面性质三、车身结构中构件节点(接头)的性质四、车身参数化模型五、车身详细模型六、设计各阶段对模型的要求白车身(BIW‐Body In White)•概念:指已经装焊好的白皮车身;主要包括车身结构焊接总成和车身闭合件(Closure,车门、发动机罩、行李箱盖等)焊接总成,不包括车身附属设备和装饰件白车身的设计要求•车身结构的性能要求•理想的碰撞特性•轻量化和低成本•遵循总布置尺寸约束•基于平台的系列设计•满足车身制造要求•承载系统–包括车身和车架–按承载型式不同分类•非承载式•承载式•第一节作用在车身系统上的载荷一、车身结构承载型式二、作用在车身、车架上的载荷(一)非承载式车身•第一节作用在车身系统上的载荷一、车身结构承载型式二、作用在车身、车架上的载荷特点•属于带有独立完整车架的车身结构。
动力总成、悬架和转向系等均安装于车架;车身通过橡胶垫或悬置用螺栓与车架连接•载荷主要由车架承担,车身承载的多少只是相对车架而言•多用于有较宽松空间的高级轿车上优点•车身与车架弹性连接,乘坐舒适性好;便于车身的改型•第一节作用在车身系统上的载荷一、车身结构承载型式二、作用在车身、车架上的载荷典型结构‐车架•多由闭式箱形梁组成,板厚2mm ~3mm,具有抗弯曲刚度和较高的抗扭刚度•正碰时,能量首先由车架承受;通过有目的的由前向后以车身横断面分级,将碰撞能量可以传递到指定区域•侧碰时,撞点位置往往在门槛梁的上部(车门和门柱),只有一部分能量由车身门槛传到车架•第一节作用在车身系统上的载荷一、车身结构承载型式二、作用在车身、车架上的载荷(二)承载式车身•将车架的作用融入车身的结构,又称整体式车身结构,它承担承载系统的全部功能,发动机和行走系的支点都在车身上•第一节作用在车身系统上的载荷一、车身结构承载型式二、作用在车身、车架上的载荷(二)承载式车身•通常将发动机和行走系通过副车架与车身底架连接–副车架与车身底架纵梁之间设有橡胶垫,以减弱发动机和悬架的振动对车身的影响–将动力总成和悬架等与副车架形成一个组装部件,对生产和使用都带来方便•第一节作用在车身系统上的载荷一、车身结构承载型式二、作用在车身、车架上的载荷(二)承载式车身•优点–整体刚度大,重量轻,整车高度低–生产效率高–是现在轿车中常见的结构•第一节作用在车身系统上的载荷一、车身结构承载型式二、作用在车身、车架上的载荷(一)在各种典型路况下车身、车架所受的载荷–整车和车身参考坐标系•取通过悬挂质量系统质心的坐标系x y z•第一节作用在车身系统上的载荷一、车身结构承载型式二、作用在车身、车架上的载荷(一)在各种典型路况下车身、车架所受的载荷–汽车行驶时作用在车身上力•第一节作用在车身系统上的载荷一、车身结构承载型式二、作用在车身、车架上的载荷(一)在各种典型路况下车身、车架所受的载荷–动荷系数•决定因素–道路条件–汽车行驶状况–汽车的结构参数•动荷系数难以用数学分析法确定,常取一些理论研究与试验修正相结合的半经验数值•第一节作用在车身系统上的载荷一、车身结构承载型式二、作用在车身、车架上的载荷(一)在各种典型路况下车身、车架所受的载荷–典型路况•路段Ⅰ:产生对称于汽车纵向对称面的垂直力F zs •路段Ⅱ:产生的加速度与速度平方成正比,与曲率半径成反比•路段Ⅲ:使左右车轮垂直加速度不同•路段Ⅳ:将产生垂直加速度和纵向力F x•路段Ⅴ:产生侧向加速度和侧向力F y•第一节作用在车身系统上的载荷一、车身结构承载型式二、作用在车身、车架上的载荷1.影响车身强度的基本载荷—对称垂直载荷•第一节作用在车身系统上的载荷一、车身结构承载型式二、作用在车身、车架上的载荷2.影响车身强度的基本载荷—非对称垂直载荷–承载系统上作用非对称于汽车纵轴线的垂直载荷–载荷可分解为对称垂直作用力F zn 和车身绕x 轴的转矩T x•第一节作用在车身系统上的载荷一、车身结构承载型式二、作用在车身、车架上的载荷(二)随机载荷——疲劳载荷–汽车在道路上行驶时,车身和车架承受着悬架传来的路面随机载荷–随机载荷引起构件反复交变的应力,会导致汽车结构疲劳损坏–影响因素:路面情况、汽车使用条件和结构参数–随机载荷的描述——统计•道路试验方法•数字分析方法•第一节作用在车身系统上的载荷一、车身结构承载型式二、作用在车身、车架上的载荷(三)标准载荷——G 载荷–汽车公司根据各地区使用条件制定的–用途•对整备车身结构悬置点位置施加约束,完成标准工况的载荷分析,模拟车身具体的变形,分析车身载荷的分布和高应力区•一般用于已建立车身拓扑模型和几何参数模型的车身设计阶段,通过计算可得指导性的应力信息–三种标准G 载荷工况•第一节作用在车身系统上的载荷一、车身结构承载型式二、作用在车身、车架上的载荷(三)标准载荷——G 载荷–标准载荷分析的主要缺点•不能预测疲劳寿命•只有在构造详细结构后,方可进行疲劳寿命预测•第一节作用在车身系统上的载荷一、车身结构承载型式二、作用在车身、车架上的载荷(四)作用在车身上的其它非破坏性的作用力–轻微冲撞力–发动机和传动系传来的力–牵引力和拖拽力–千斤顶和悬吊作用力–以及安全带固定点的作用力等非破坏性作用力•第一节作用在车身系统上的载荷一、车身结构承载型式二、作用在车身、车架上的载荷(五)碰撞载荷•第一节作用在车身系统上的载荷一、车身结构承载型式二、作用在车身、车架上的载荷•车身结构布置受整车布置和造型的制约•白车身结构–由构件及其接头和板壳零件共同组成–是承受载荷和传递载荷的基本系统–结构设计决定了载荷路径•一般钢结构车身构件–由成形钢板制件焊接组合–截面为闭口或开口的薄壁杆件–在车身中起支承和加强的作用•第二节车身结构的拓扑模型一、车身结构二、车身结构拓扑模型的建立三、应变能分析四、碰撞安全性对车身结构的要求•车身下部–前、后纵梁–底架各横梁–地板及其两侧边梁与侧围外板组成的门槛–地板中间通道–前围板、后隔板–悬架支座及轮罩等•车身上部–侧围的A 、B 、C 柱–顶盖及其边梁–风窗上、下横梁等•第二节车身结构的拓扑模型一、车身结构二、车身结构拓扑模型的建立三、应变能分析四、碰撞安全性对车身结构的要求•车身分成前车身,中、后部车身–前部车身•车身前部敞开部分承受比较大的集中力,主要由底架的前纵梁支承,并传至整个车身前部结构•前车身的导风板及散热器框架等板壳零件也是车身结构的承力构件•受到高速撞击时车头首当其冲,车身设计必须使其能有效地吸收冲击能量–车身中段•乘坐室部分主要承受分散在地板上的重力–车身后部•行李箱承受油箱、备胎和行李等重力,后纵梁承受后悬架支承力•第二节车身结构的拓扑模型一、车身结构二、车身结构拓扑模型的建立三、应变能分析四、碰撞安全性对车身结构的要求–乘坐车室与前部敝开部分连接区域刚度的加强•纵梁到门槛的扭矩盒•前铰链柱上端向前指的短枪梁•斜梁或接头圆角的设计–通过前纵梁力流的分散–由前纵梁上部平面悬架支座附近,往后下方分叉斜伸出两根短梁,通到地板中间通道横梁和A 柱的铰链柱段•第二节车身结构的拓扑模型一、车身结构二、车身结构拓扑模型的建立三、应变能分析四、碰撞安全性对车身结构的要求–车身中部•底架总成的中部由地板和前围板组成,其支撑结构是门槛梁和与地板焊接在一起的帽形横梁。
帽形横梁主要用于加强左右门槛之间的联系,并承受侧向碰撞力•地板的中间通道有利于提高地板的抗弯能力•上部的框架结构由侧围总成、前/后风窗框、前围板/后隔板及车顶梁构成•侧围在车身整体弯曲刚性中起重要作用•前围板、后隔板具有很高的车身横向抗剪刚度•第二节车身结构的拓扑模型一、车身结构二、车身结构拓扑模型的建立三、应变能分析四、碰撞安全性对车身结构的要求–后部车身•对于斜背式或快背式,扭转时的剪力则主要由后部框架承受•地板总成后部零件承担着后悬架传来的力,这些力主要由后纵梁和后地板分担•后纵梁与乘坐室的连接,应该有利于载荷分流•第二节车身结构的拓扑模型一、车身结构二、车身结构拓扑模型的建立三、应变能分析四、碰撞安全性对车身结构的要求•车身结构构件布置应使车身构成一个连续完整的受力系统与合理的载荷路径•第二节车身结构的拓扑模型一、车身结构二、车身结构拓扑模型的建立三、应变能分析四、碰撞安全性对车身结构的要求•车身结构的拓扑布置设计是概念设计中要首先完成的工作•车身拓扑模型是指车身结构中,梁、柱等承载件空间布置型式•第二节车身结构的拓扑模型一、车身结构二、车身结构拓扑模型的建立三、应变能分析四、碰撞安全性对车身结构的要求•白车身结构的布置空间受车辆总体外形和内部布置要求的约束•构件的布置是否合理,可通过简化模型的载荷计算分析判断•借助拓扑模型研究和定义初始的几何尺寸参数,如构件截面、接头参数和板料厚度等•初步优化后的拓扑几何方案输入CAD 系统进行详细的结构设计•第二节车身结构的拓扑模型一、车身结构二、车身结构拓扑模型的建立三、应变能分析四、碰撞安全性对车身结构的要求•构件储藏应变能多少是衡量它承担载荷多少的标志,可用比应变能表示–总应变能小,说明车身刚度足够大,或材料没有充分利用–可将比应变能小的构件取消或减薄板厚,以便减轻重量。
应变能大的区域对车身刚度影响较大,要考虑是否需要加强–应该尽可能使材料在结构中的分布与各处的应变能成比例,使比应变能均匀化•第二节车身结构的拓扑模型一、车身结构二、车身结构拓扑模型的建立三、应变能分析四、碰撞安全性对车身结构的要求•碰撞安全法规–正碰撞–侧碰撞–后碰撞等•第二节车身结构的拓扑模型一、车身结构二、车身结构拓扑模型的建立三、应变能分析四、碰撞安全性对车身结构的要求•车身概念设计初期,车身被简化为空间框架结构,用有限元法求得结构在外载荷作用下各个构件的内力•用梁单元来模拟梁、柱•第三节车身结构的力学特性和力学模型一、车身结构内力二、车身结构中构件的截面性质三、车身结构中构件节点(接头)的性质四、车身参数化模型五、车身详细模型六、设计各阶段对模型的要求杆长一定情况下,梁单元的刚度主要决定于梁的材料和截面性质•实例‐车身框架结构应力计算–用一个简化的框架结构表示车身结构(对称结构)•第三节车身结构的力学特性和力学模型一、车身结构内力二、车身结构中构件的截面性质三、车身结构中构件节点(接头)的性质四、车身参数化模型五、车身详细模型六、设计各阶段对模型的要求•实例‐车身框架结构应力计算–工况1‐载荷完全对称于车身的纵轴•车身框架是个近似平面弯曲问题•每个构件节点只有三个自由度•第三节车身结构的力学特性和力学模型一、车身结构内力二、车身结构中构件的截面性质三、车身结构中构件节点(接头)的性质四、车身参数化模型五、车身详细模型六、设计各阶段对模型的要求•实例‐车身框架结构应力计算–工况2‐框架结构承受扭转工况•结构呈现反对称变形•车身框架是个空间扭转问题•每个构件节点有六个节点位移分量和相应的六个节点力分量•第三节车身结构的力学特性和力学模型一、车身结构内力二、车身结构中构件的截面性质三、车身结构中构件节点(接头)的性质四、车身参数化模型五、车身详细模型六、设计各阶段对模型的要求•车身杆件多由薄板成型件组成•杆件截面–开口–闭口•截面形状和尺寸对截面特性有很大影响–除了材料性质外,主要是弯曲惯性矩和扭转惯性矩等截面•第三节车身结构的力学特性和力学模型一、车身结构内力二、车身结构中构件的截面性质三、车身结构中构件节点(接头)的性质四、车身参数化模型五、车身详细模型六、设计各阶段对模型的要求•复杂截面的特性计算公式•第三节车身结构的力学特性和力学模型一、车身结构内力二、车身结构中构件的截面性质三、车身结构中构件节点(接头)的性质四、车身参数化模型五、车身详细模型六、设计各阶段对模型的要求•截面特性比较•材料面积A 和壁厚t 不变情况下,闭口截面的抗弯性能稍次于开口截面,但闭口截面的扭转惯性矩远大于开口截面•第三节车身结构的力学特性和力学模型一、车身结构内力二、车身结构中构件的截面性质三、车身结构中构件节点(接头)的性质四、车身参数化模型五、车身详细模型六、设计各阶段对模型的要求•截面特性–薄板围成的闭口截面,中线周长和材料厚度一定,抗扭惯性矩与A 平方成正比;截面形状对力学特性无独立意义,所围面积大小则很重要•圆形截面对抗扭最有利•矩形截面中,正方形抗扭能力最高,两边之比h/b >2时,扭转惯性矩明显下降•第三节车身结构的力学特性和力学模型一、车身结构内力二、车身结构中构件的截面性质三、车身结构中构件节点(接头)的性质四、车身参数化模型五、车身详细模型六、设计各阶段对模型的要求•例‐某车侧面主要截面位置及部分截面特性计算结果•第三节车身结构的力学特性和力学模型一、车身结构内力二、车身结构中构件的截面性质三、车身结构中构件节点(接头)的性质四、车身参数化模型五、车身详细模型六、设计各阶段对模型的要求•接头:车身结构中2个以上承载构件交叉连接的部位a)A 柱至顶盖梁,b)B 柱至顶盖梁,c)B 柱到门槛,d)前铰链柱到门槛,e)A 柱到前铰链柱和短梁,f)C 柱到顶盖,g)门槛到后纵梁,h)上散热器支架到短梁•第三节车身结构的力学特性和力学模型一、车身结构内力二、车身结构中构件的截面性质三、车身结构中构件节点(接头)的性质四、车身参数化模型五、车身详细模型六、设计各阶段对模型的要求1.研究接头的意义•白车身结构总成=承载构件+接头+板壳•构件的截面性质,接头的刚度和板壳的形状和板厚都影响车身的刚度,影响车身的振动、噪声和耐久性•研究表明:将接头视为刚性的计算结果使整车刚度提高50%以上,可见接头的柔性是不可忽略的•研究接头的意义–指导接头设计–为概念设计阶段建立车身简化模型提供支持•第三节车身结构的力学特性和力学模型一、车身结构内力二、车身结构中构件的截面性质三、车身结构中构件节点(接头)的性质四、车身参数化模型五、车身详细模型六、设计各阶段对模型的要求2.接头力学特性–接头的特性由设计参数表征–设计参数必须体现与设计变量的联系,且对车身性能影响明显,以便于建立简化的接头模型•如轮廓尺寸:腿长、角度、截面尺寸等•内部结构:焊点部局、零件数、内加强板的布置和设计,圆角半径等•第三节车身结构的力学特性和力学模型一、车身结构内力二、车身结构中构件的截面性质三、车身结构中构件节点(接头)的性质四、车身参数化模型五、车身详细模型六、设计各阶段对模型的要求•选择物理意义明确的接头刚度作为设计参数–接头各腿的扭转刚度(TOR )–接头各腿的内/外刚度(I/O )–接头各腿的前/后刚度(F/A)或上/下刚度(U/D )•具体方向决定于每个接头局部坐标系的选取•第三节车身结构的力学特性和力学模型一、车身结构内力二、车身结构中构件的截面性质三、车身结构中构件节点(接头)的性质四、车身参数化模型五、车身详细模型六、设计各阶段对模型的要求3.接头刚度的模拟计算•接头刚度可以用分析法或测试技术获得•第三节车身结构的力学特性和力学模型一、车身结构内力二、车身结构中构件的截面性质三、车身结构中构件节点(接头)的性质四、车身参数化模型五、车身详细模型六、设计各阶段对模型的要求3.接头刚度的模拟计算1)接头计算模型–分为详细接头模型和简化的接头模型–详细接头模型•用板单元模拟•一般从用于NVH 分析的详细车身结构模型中抽取•这些接头模型用于接头参数化和引导设计•这种抽取局部模型方法虽方便,但计算结果往往与实验数据相比误差较大•第三节车身结构的力学特性和力学模型一、车身结构内力二、车身结构中构件的截面性质三、车身结构中构件节点(接头)的性质四、车身参数化模型五、车身详细模型六、设计各阶段对模型的要求3.接头刚度的模拟计算1)接头计算模型–简化接头模型•将详细接头模型简化成由梁单元和弹簧元模拟•用于概念设计时将构件用梁单元模拟的简化车身模型•参数少、模型简单、便于更改–也可用超单元技术来描述接头力学特性。