双面板制作流程
双面板流程
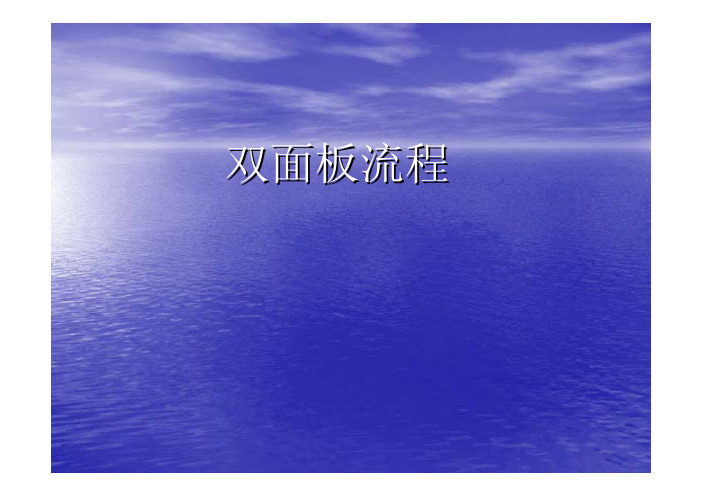
固化
• 使白油固
化,不易
脱落。
丝印
• 按照工单的
菲林号、网 板目数、油 墨型号印反 面白油。
固化
• 使白油固
化,不易
脱落。
磨板
• 清洁表
面,去氧
化。
表面处理
• 根据工单的
要求做表面 处理。
• 表面处理有:
镀金 化金 镀纯锡 化锡
OSP
剪切
• 按图纸沿
裁剪孔裁
开。
成型
• 用工单规
定的模具 及面向成 型
• 烘烤的目的是
减少因基才材 内水分造成胀 缩
钻孔
• 按照工单
规定的钻 孔程式钻 孔。
清洗
• 清洁表面
去氧化。
沉铜
• 用物理方
法使板面 和孔内附 着一层铜
镀铜
• 孔铜厚度
要求12-18
um。
• 检查孔的
导通性。
前处理
• 清洁表面
去氧化。
双面贴膜
• 贴膜时要掌
握好三个要 素:压力、 温度、传送 速度。
成检
• 按照客户
的要求检
查成品厚 度,表面状 况,边间距 等是否达 到要求
抽检
• 进一步确
认品质是
否符合客 户的要求
包装
• 按照客户
要求包装
• ……
结束语
• 按照图纸沿标
记线叠覆盖膜
• 叠覆盖膜是完
全手工作业完 成的,对房间 的洁净度非常 高,对位公差 一般为+/0.3mm。
压合
• 压合时要控制
好压力、温度、 时间、以及辅 助材料
• 压合后要测量
成品厚度
固化
FPC生产工艺流程

FPC生产工艺流程ﻫ分类:PCB板FPC生产流程ﻫ1、FPC生产流程:1、1 双面板制程: ﻫ开料→ 钻孔→PTH→ 电镀→前处理→ 贴干膜→对位→曝光→ 显影→ 图形电镀→ 脱膜→前处理→ 贴干膜→对位曝光→ 显影→蚀刻→ 脱膜→ 表面处理→ 贴覆盖膜→ 压制→固化→ 沉镍金→ 印字符→ 剪切→ 电测→冲切→终检→包装→ 出货1、2 单面板制程: ﻫ开料→ 钻孔→贴干膜→ 对位→曝光→ 显影→蚀刻→ 脱膜→ 表面处理→贴覆盖膜→压制→ 固化→表面处理→沉镍金→ 印2、开料ﻫ2、1、原字符→ 剪切→ 电测→ 冲切→ 终检→包装→ 出货ﻫﻫ材料编码得认识NDIR050513HJY:D→双面,R→压延铜, 05→PI厚0、5mil,即12、5um,05→铜厚 18um, 13→胶层厚13um、XSIE101020TLC:S→单面,E→电解铜, 10→PI厚25um, 10→铜厚度35um, 20→胶厚20um、CI0512NL:(覆盖膜) :05→P I厚12、5um, 12→胶厚度12、5um、总厚度:25um、2、2、制程品质控制A、操作者应带手套与指套,防止铜箔表面因接触手上之汗而氧化、ﻫB、正确得架料方式,防止皱折、ﻫC、不可裁偏,手对裁时不可破坏沖制定位孔与测试孔、D、材料品质,材料表面不可有皱折,污点,重氧化现象,所裁切材料不可有毛边,溢胶等、3钻孔3、1打包: 选择蓋板→組板→胶帶粘合→打箭头(记号)ﻫ3.1.1打包要求:单面板 15张 ,双面板10张,包封20张、ﻫ3、1、2蓋板主要作用:A: 防止钻机与压力脚在材料面上造成得压伤B::使钻尖中心容易定位避免钻孔位置得偏斜C:带走钻头与孔壁摩擦产生得热量、减少钻头得扭断、3、2钻孔: ﻫ3、2、1流程: 开机→上板→调入程序→设置参数→钻孔→自检→IPQA检→量产→转下工序、ﻫ3、2、2、钻针管制方法:a、使用次数管制b、新钻头之辨认,检验方法ﻫ3、3、品质管控点: a、钻带得正确b、对红胶片,确认孔位置,数量,正确、 c确认孔就是否完全导通、 d、外观不可有铜翘,毛边等不良现象、ﻫ3、4、常见不良现象3、4、1断针: a、钻机操作不当b、钻头存有问题 c、进刀太快等、ﻫ3、4、2毛边 a、蓋板,墊板不正确 b、靜电吸附等等4、电镀ﻫ4、1、PTH原理及作用:PTH即在不外加电流得情況下,通过镀液得自催化(钯与铜原子作为催化剂)氧化还原反应,使铜离子析镀在经过活化处理得孔壁及铜箔表面上得过程,也称为化学镀铜或自催化镀铜、ﻫ4、2、PHT流程: 碱除油→水洗→微蚀→水洗→水洗→预浸→活化→水洗→水洗→速化→水洗→水洗→化学铜→水洗、4、3、PTH常见不良状况之处理4、3、1、孔无铜:a活化钯吸附沉积不好、b速化槽:速化剂浓度不对、c 化学铜:温度过低,使反应不能进行反应速度过慢;槽液成分不对、ﻫ4、3、2、孔壁有颗粒,粗糙: a化学槽有颗粒,铜粉沉积不均,开过滤机过滤、 b板材本身孔壁有毛刺、4、3、3、板面发黑: a化学槽成分不对(NaOH浓度过高)、ﻫ4、4镀铜镀铜即提高孔内镀层均匀性,保证整个版面(孔内及孔口附近得整个镀层)镀层厚度达到一定得要求、ﻫ4、4、1电镀条件控制ﻫa电流密度得选择b电镀面积得大小ﻫc镀层厚度要求d电镀时间控制4、4、1品质管控 1 贯通性:自检QC全检,以40倍放大镜检查孔壁就是否有镀铜完全附着贯通、ﻫ2表面品质:铜箔表面不可有烧焦,脱皮,颗粒状,针孔及花斑不良等现象、3 附着性:于板边任一处以3M胶带粘贴后,以垂直向上接起不可有脱落现象、5、线路5、1干膜干膜贴在板材上,经曝光后显影后,使线路基本成型,在此过程中干膜主要起到了影象转移得功能,而且在蚀刻得过程中起到保护线路得作用、5、2干膜主要构成:PE,感光阻剂,PET 、其中PE与PET只起到了保护与隔离得作用、感光阻剂包括:连接剂,起始剂,单体,粘着促进剂,色料、ﻫ5、3作业要求 a保持干膜与板面得清洁,b平整度,无气泡与皱折现象、、c附着力达到要求,密合度高、5、4作业品质控制要点5、4、1为了防止贴膜时出现断线现象,应先用无尘纸粘尘滚轮除去铜箔表面杂质、5、4、2应根据不同板材设置加热滚轮得温度,压力,转数等参数、5、4、3保证铜箔得方向孔在同一方位、ﻫ5、4、4防止氧化,不要直接接触铜箔表面、5、4、5加热滚轮上不应该有伤痕,以防止产生皱折与附着性不良5、4、6贴膜后留置10—20分钟,然后再去曝光,时间太短会使发生得有机聚合反应未完全,太长则不容易被水解,发生残留导致镀层不良、5、4、7经常用无尘纸擦去加热滚轮上得杂质与溢胶、ﻫ5、4、8要保证贴膜得良好附着性、5、5贴干膜品质确认ﻫ5、5、1附着性:贴膜后经曝光显影后线路不可弯曲变形或断等(以放大镜检测)5、5、2平整性:须平整,不可有皱折,气泡、ﻫ5、5、3清洁性:每张不得有超过5点之杂质、5、6曝光5、6、1、原理:使线路通过干膜得作用转移到板子上、ﻫ5、6、2作业要点: a作业时要保持底片与板子得清洁、ﻫb底片与板子应对准,正确、c不可有气泡,杂质、*进行抽真空目得:提高底片与干膜接触得紧密度减少散光现象、ﻫ*曝光能量得高低对品质也有影响: ﻫ1能量低,曝光不足,显像后阻剂太软,色泽灰暗,蚀刻时阻剂破坏或浮起,造成线路得断路、2、能量高,则会造成曝光过度,则线路会缩小或曝光区易洗掉、5、7显影5、7、1原理:显像即就是将已经曝过光得带干膜得板材,经过(1、0+/-0、1)%得碳酸钠溶液(即显影液)得处理,将未曝光得干膜洗去而保留经曝光发生聚合反应得干膜,使线路基本成型、ﻫ5、7、2影响显像作业品质得因素: a﹑显影液得组成 b﹑显影温度、c﹑显影压力、d﹑显影液分布得均匀性、e ﹑机台转动得速度、5、7、3制程参数管控:药液溶度,显影温度,显影速度,喷压、5、7、4显影品质控制要点: ﻫa﹑出料口扳子上不应有水滴,应吹干净、ﻫb﹑不可以有未撕得干膜保护膜、ﻫc﹑显像应该完整,线路不可锯齿状,弯曲,变细等状况、ﻫd﹑显像后裸铜面用刀轻刮不可有干膜脱落,否则会影响时刻品质、ﻫe﹑干膜线宽与底片线宽控制在+/-0。
双面板制板流程

双面板制板流程双面板制作流程:1、打印底片或者光绘输出底片2、裁板3、钻孔4、平板机打磨(去除孔内毛刺,要保证孔通透)5、抛光6、沉铜(全自动沉铜:包含预浸与活化二种工艺)7、预浸(约5分钟,除油,除氧化物,调整电荷)8、水洗(水洗都是为除去药水残留)9、活化(约2分钟,纳米碳粒附在孔内)10、透孔11、7至11步工艺在全自动沉铜机里自动完成12、固化(100°C,5~10分钟,使碳粒在孔内附好)13、微蚀(去除覆盖在铜外表的活化液参考时间10~20s)14、镀铜(可以先加速二到四秒钟去除表面氧化物电镀。
最佳时间20分钟,电流约3A/(dm)2)15、水洗16、抛光17、刷线路油墨(较难掌握,多练习)18、烘干(75°C,10~15分钟)19、爆光(爆光时间60~80S,先对孔,用透明胶粘住打印好的菲林膜)20、显影(显影时间不易过长,参考时间30~45s)21、水洗22、烘干23、镀锡(20分钟,铜的有效面积电流约1.5A/(dm)2)24、水洗25、去膜(脱膜机脱膜,一定要用手套,去膜液为强碱性。
)26、水洗27、腐蚀(防止腐蚀过头)28、水洗29、刷阻焊油墨(阻焊油墨中加固化剂,增强固花能力)30、烘干(75°C,5~10分钟)31、爆光(180S)32、显影33、水洗34、烘干固化(150°C,30分钟)35、刷文字油墨(事先配好油墨,油墨一定要配得细腻)36、烘干(75°C,5~10分钟)38、显影固化简易流程:打底片→裁板→钻孔→抛光→(透孔)→预浸→水洗→(透孔)→预先开烘干机↓黑孔→烘干→微蚀→水洗→加速→水洗→(透孔)→镀铜→水洗→配线路油墨配显影液↓↓抛光→刷线路油墨→烘干→爆光→显影→水洗→加速→水洗→镀锡配去膜液配阻焊油墨(配比:固化剂1:油墨3)↓↓→去膜→水洗→腐蚀→水洗→刷阻焊油墨→烘干→爆光→显影配文字油墨(可用油墨稀释剂稀释)(配比:固化剂1:油墨3)↓换网→刷文字油墨→烘干→显影。
pcb双面板的工艺流程

pcb双面板的工艺流程英文回答:PCB (Printed Circuit Board) double-sided fabrication involves several steps in its manufacturing process. Here, I will outline the general process flow for producing double-sided PCBs.1. Design and Layout: The first step is to create a design and layout for the PCB using a computer-aided design (CAD) software. This involves placing components, routing traces, and creating the necessary layers for the PCB.2. Material Selection: Once the design is complete, the next step is to select the appropriate materials for the PCB. This includes choosing the substrate material (usually fiberglass-reinforced epoxy), copper foil for the conductive layers, and solder mask materials.3. Substrate Preparation: The substrate material is cutinto the desired size and shape for the PCB. It is then cleaned and prepared for the subsequent processes.4. Copper Cladding: Copper foil is laminated onto both sides of the substrate using heat and pressure. This provides the conductive layers for the PCB.5. Imaging: A photosensitive material called a photoresist is applied to both sides of the copper-clad substrate. The PCB design is then transferred onto the photoresist using a UV light source and a photomask. The areas exposed to light become either the conductive traces or the pads for component attachment.6. Etching: The unexposed areas of the photoresist are removed, leaving behind the desired conductive traces and pads. The exposed copper is then etched away using an etching solution, leaving only the desired copper pattern on the substrate.7. Drilling: Holes for component mounting and interconnections are drilled into the PCB using a precisiondrilling machine. These holes are typically plated with copper to provide electrical continuity between the layers.8. Plating: A thin layer of copper is electroplatedonto the exposed copper surfaces, including the drilled holes. This helps to improve the conductivity and protect the copper from oxidation.9. Solder Mask Application: A solder mask is applied to both sides of the PCB to protect the copper traces from oxidation and to prevent solder bridges during assembly.The solder mask is typically green in color, but othercolors can also be used.10. Silkscreen Printing: Component designators, logos, and other information are printed onto the solder maskusing a silkscreen printing process. This helps with component placement and identification during assembly.11. Testing and Inspection: The finished PCBs are subjected to various tests and inspections to ensure their quality and functionality. This includes electrical testing,visual inspection, and sometimes, functional testing.12. Assembly: Once the PCBs pass all the tests, theyare ready for component assembly. This involves solderingthe components onto the PCB using either manual or automated assembly processes.13. Final Testing: The assembled PCBs undergo final testing to verify their functionality and performance. This may include functional testing, environmental testing, and reliability testing.中文回答:PCB(Printed Circuit Board)双面板的制造工艺包括多个步骤。
1、简述 pcb 双面板和多层板生产流程。

【主题】:PCB双面板和多层板生产流程一、引言PCB(Printed Circuit Board,印刷电路板)是现代电子产品中不可或缺的一部分,它承载着电子元器件并提供电气连接。
在不同的电子产品中,我们经常会听到双面板和多层板的概念。
那么,它们的生产流程究竟是怎样的呢?二、双面板生产流程1. 设计与布局:双面板的生产流程首先要进行电路设计和布局,包括元件布局和线路走向的设计。
2. 制作内层板:将玻璃纤维布浸渍树脂,然后在铜箔上覆盖光敏胶,通过曝光、显影、蚀刻等步骤形成线路和铜箔残留的区域。
3. 复板:将内层板与预制好的介质层板及铜箔层板复合,并通过热压技术将其加以固化。
4. 外层图形化:在外层板铜箔表面上覆盖一层光敏胶,然后按照设计图形进行曝光、显影、蚀刻,形成外层线路及铜箔残留的区域。
5. 孔位铆合:利用机械或激光技术在板面上打孔(冲压孔位)。
6. 表面化学镀镍金:对板面进行化学镍金处理,以增强其与焊盘的附着力。
7. 色素沉积:在板面上形成阻焊油墨或者焊盘油墨图形。
8. 表面喷镘:将表面喷上喷锡层,构成铅(锡)粘接的表面。
三、多层板生产流程1. 设计与布局:多层板的设计和布局要比双面板更为复杂,需要考虑多层板间的互连关系和信号传输。
2. 制作内层板:多层板同样需要制作内层板,但在此之前需要将设计好的电路图分层布局,并使用铜箔、介质等材料进行层压。
3. 复合与预压:通过预压机将内层板与预制好的介质层板及铜箔层板复合,并进行热压处理。
4. 钻孔:利用高精度数控钻孔机对多层板进行钻孔处理,确保孔位的精确性。
5. 表面处理:在板面进行化学镀铜处理,以增强其导电性。
6. 外层图形化:进行外层线路的图形化处理,包括曝光、显影、蚀刻等步骤。
7. 色素沉积:形成阻焊油墨或者焊盘油墨图形。
8. 表面处理:喷镘或者喷锡等表面处理工艺,以增强焊盘的焊接性能。
四、总结从以上的生产流程可以看出,双面板和多层板的生产流程都是需要经过多道工艺步骤的复杂过程。
干、湿双面板制版流程

小型工业制版一、简易流程:湿模制版流程:底片输出→裁板→钻孔→抛光→(整孔)→预浸→水洗→烘干→活化→通孔(吸尘器吸孔)→热固化(不清洗直接烤干)→微蚀→水洗→抛光→加速→镀铜(看板大小来设置电流)→水洗→抛光→烘干→刷感光线路油墨→烘干→曝光→显影→水洗→微蚀→水洗→镀锡→水洗→脱膜→水洗→蚀刻→水洗→褪锡→水洗→烘干→刷感光阻焊油墨→烘干→曝光→显影→水洗→烘干→刷感光字符油墨→烘干→曝光→显影→水洗→热固化→切边。
干模制版流程:1.《底片输出→裁板→钻孔→抛光→(整孔)→预浸→水洗→烘干→活化→通孔(吸尘器吸孔)→热固化(不清洗直接烤干)→微蚀→水洗→抛光→加速→镀铜(看板大小来设置电流)→水洗→抛光→烘干→2《覆干膜→贴膜→图形曝光→3《线路腐蚀(显影→水洗→微蚀→水洗→蚀刻→水洗→烘干→脱膜→水洗→3《刷感光阻焊油墨→烘干→曝光→显影→水洗→烘干→5《刷感光字符油墨→烘干→曝光→显影→水洗→热固化→切边。
二、制作流程:1.打印底片(打印机菲林膜出图《CAM350或其他》)2.裁板(建议保留20㎜的工艺边)3.钻孔(设置板厚2.0㎜或1.6㎜,钻头尖离待加工的PCB板1-1.5㎜《利用Create-DCM双面电路板雕刻软件生成雕刻机能识别的U00格式的钻孔文件》)4.抛光(去除覆铜板表面的氧化物及油污,去除钻孔时产生的毛刺)5.预浸(除油,除氧化物毛刺铜粉,调整电荷,有利于碳颗粒的吸附)6.水洗(水洗都是为除去药水的残留《务必反复用清水冲洗干净》)7.烘干(除去孔内残留水分《烘干机或电吹风均可》)8.活化(纳米碳粒附在孔内壁《主要是为了过孔》)9.通孔(将孔内多余的活化液去除,保证每个孔均通透《轻轻敲击板子》)10.固化(使碳颗粒更好的吸附在孔内)11.微蚀(去除表面的碳颗粒《也可用抛光机抛光》)12.水洗13.抛光14.加速(可省略)15.水洗16.镀铜(20-30分钟,电流约3-4A/d㎡《具体视情况增减电流大小》,主要是针对双面板上下电路的通孔导通,在孔内壁镀上铜)17.水洗18.抛光19.烘干(烘干表面及孔内水分)20.刷感光线路油墨(90T的丝网框《主要用到线路板丝印机》)21.烘干(75℃,20-30分钟《优先使用烘干机,可用电吹风,但必须确保能将油墨烘干不粘手》)22.曝光(曝光时间10-60S,先将底片对位,双面板应注意电路的正反面)23.显影(45-50℃,注意观察板子上面的变化)24.水洗25.放入微蚀液中去油(5-10S)26.水洗27.镀锡(20-30分钟,电流约1.5-2A/d㎡有效面积《镀锡机,焊盘及线路部分镀上锡,以达到PCB板在碱性腐蚀液中保护线路部分不被腐蚀》)28.水洗29.脱膜(强碱性液体,除去板上面的线路油墨)30.水洗31.蚀刻(建议温度55℃)32.水洗(务必清洗干净保证电路不会被残留腐蚀液腐蚀掉)33.褪锡(褪锡夜,去除电路上面的锡)34.水洗35.烘干36.刷感光阻焊油墨(90T丝网框,感光阻焊油墨:固化剂=3:1,并加入少量稀释剂调整其粘度《类似洗发水》)37.静置(在阴凉环境,目的是让油墨预干,可用微热的电吹风慢烘)38.油墨烘干(75℃,30分钟)39.曝光(120-180S,光绘底片)40.显影41.水洗42.烘干43.刷感光字符油墨(120T丝网框,感光字符油墨:固化剂=3:1,并加少量的稀释剂调整其粘度《类似洗发水》)44.油墨烘干(75℃,20分钟)45.曝光(90-120S光绘底片)46.显影(字符油墨在显影的时候必须缩短显影时间,不能太久,防止文字掉落)47.水洗48.热固化(150℃,30分钟,固化剂在150℃起作用)49.沉锡(除油-微蚀-水洗-沉锡,主要是在焊盘部分镀上助焊锡,可防氧化,也有利于后面的焊接《镀锡机》)50.切边(根据已做好的电路板切除多余部分,再用手动打磨机将板子边缘部分打磨光滑)。
双面板制作流程(图文说明)

双面板制作流程(图文说明)无线电协会10weiwst总结整理现在我简单介绍一下制作双面PCB板(热转印法)的流程:以我自己制作的线性稳压电源为例。
电路整体布局:电路布线时,应尽可能的注意总体布局和元件排布。
对于电源布线应注意的问题,可以参考我在无线电协会的帖子,和21IC的帖子。
一.首先打印底层和顶层。
我习惯先打印底层,然后打印顶层。
1.页面设置:2.配置。
(打印底层,底层不镜像。
)便于定位和张贴固定转印纸。
)4.打印后的底层转印纸。
6.配置,(打印顶层,顶层镜像)打印顶层。
7.顺便说一下PCB的制版规定:编号见上图,相关说明文档见协会公共电脑的D盘PCB库。
编号示例:101205161253,指10级2012年5月16日12:53制板。
PCB的文件以这个编号命名,适当做一下电路说明文档。
为了在底层看到“正的”命名,底层的应镜像。
如果在顶层,就不用镜像。
具体方法实验几次就全明白了。
8.打印好的顶层转印纸。
二.确定一块双面敷铜板,大小应适当。
板子的边缘用锉刀休整齐平。
再根据板子的清洁情况,用粗砂纸或细砂纸打磨干净,再清理干净板子。
三.板子顶层和底层同时定位。
1.先把顶层和底层的转印纸贴在一起,透过光线确定孔的位置。
一定要使孔的位置固定好,偏差太大会影响后面的定位。
用针(针孔的大小应小于孔的大小,否则将使定位的孔的墨迹消失)和小的电阻固定纸上的定位孔。
定位好的转印纸:2.先贴上一面的转印纸(用布线较少的一面,防止墨迹碰掉),固定好后用比孔小的多的钻头钻孔。
我一般用0.5mm的钻头钻。
用协会的1987年产的钻床,要认真地钻啊!一不小心就会把钻头弄断!弄断了不可怕,但是就怕你经常弄断。
呵呵,那时就要对你进行单独培训了。
注意:可别忘了登记和使用完毕后的清理喽。
3.打好孔后的板子。
也要清理啊。
5.把另一张转印纸也要贴在板子上。
用电阻腿确定是否孔定位好了,再用标签纸固定好板子。
开始时,要适当推着板子。
五.热转印2-3次后就可以了(根据温度和经验)。
EDA课件双面板制作

EDA课件双面板制作在现代电子技术领域中,EDA(Electronic Design Automation)软件已成为电子设计师不可或缺的工具。
它能够协助设计师完成从概念到制造的全过程,其中双面板制作是电子设计的重要环节之一。
本文将介绍EDA课件中双面板制作的流程和方法。
1. 概述双面板制作是将电子设计的电路图转化为实际的电子板,其中双面板指的是两面都有电路布线的电子板。
制作双面板需要经历原理图设计、布局设计、走线布线等多个阶段。
2. 原理图设计原理图设计是将电子设计师的创意和理念转化为电路图的过程。
通过EDA软件,设计师可以从库中选择各种元件,如电容、电阻、晶体管等,并将其连接起来形成电路。
在设计原理图时,要保证电路的可靠性、稳定性和可维护性。
3. 布局设计布局设计是将原理图中的元件布置到电子板上的过程。
在布局设计中,需要考虑电路元件的大小、排列方式、合理的布局规则等。
布局设计的目标是减小信号传输的延迟和噪声,提高整体电路的性能。
4. 走线布线走线布线是将原理图中的电路连接线路布线到电子板上的过程。
在走线布线中,需要考虑信号的传输路径、避免干扰和串扰等问题。
通过EDA软件,设计师可以自动或手动完成走线布线的任务。
5. 优化与调整在完成布线后,设计师需要进一步优化和调整电子板的性能。
通过EDA软件,可以进行信号完整性分析、功耗分析、热分析等,以确保电子板的稳定性和可靠性。
6. 输出制造文件最后,设计师需要将电子板的设计文件输出为制造文件,以便进行实际的制造和组装。
制造文件通常包括层露光掩膜、钻孔定位、焊盘信息等。
总结:在EDA课件中,双面板制作是电子设计的重要环节之一。
通过原理图设计、布局设计、走线布线等步骤,设计师可以将电子设计转化为实际的双面板。
通过合理的设计和优化,可以提高电子板的性能和可靠性。
通过输出制造文件,设计师可以将设计转交给制造商进行实际的制造和组装。
通过掌握双面板制作的方法和流程,电子设计师可以更好地完成电子设计任务,并提供高质量的产品。
单面板和双面板制作流程

概述PCB(Printed Circuit Board),中文名称为印制线路板,简称印制板,是电子工业的重要部件之一。
几乎每种电子设备,小到电子手表、计算器,大到计算机,通讯电子设备,军用武器系统,只要有集成电路等电子元器件,为了它们之间的电气互连,都要使用印制板。
在较大型的电子产品研究过程中,最基本的成功因素是该产品的印制板的设计、文件编制和制造。
印制板的设计和制造质量直接影响到整个产品的质量和成本,甚至导致商业竞争的成败。
印制电路在电子设备中提供如下功能:提供集成电路等各种电子元器件固定、装配的机械支撑。
实现集成电路等各种电子元器件之间的布线和电气连接或电绝缘。
提供所要求的电气特性,如特性阻抗等。
为自动焊锡提供阻焊图形,为元件插装、检查、维修提供识别字符和图形。
有关印制板的一些基本术语在绝缘基材上,按预定设计,制成印制线路、印制元件或由两者结合而成的导电图形,称为印制电路。
在绝缘基材上,提供元、器件之间电气连接的导电图形,称为印制线路。
它不包括印制元件。
印制电路或者印制线路的成品板称为印制电路板或者印制线路板,亦称印制板。
印制板按照所用基材是刚性还是挠性可分成为两大类:刚性印制板和挠性印制板。
今年来已出现了刚性-----挠性结合的印制板。
按照导体图形的层数可以分为单面、双面和多层印制板。
导体图形的整个外表面与基材表面位于同一平面上的印制板,称为平面印板。
有关印制电路板的名词术语和定义,详见国家标准GB/T2036-94“印制电路术语”。
电子设备采用印制板后,由于同类印制板的一致性,从而避免了人工接线的差错,并可实现电子元器件自动插装或贴装、自动焊锡、自动检测,保证了电子设备的质量,提高了劳动生产率、降低了成本,并便于维修。
印制板从单层发展到双面、多层和挠性,并且仍旧保持着各自的发展趋势。
由于不断地向高精度、高密度和高可靠性方向发展,不断缩小体积、减轻成本、提高性能,使得印制板在未来电子设备地发展工程中,仍然保持强大的生命力。
精选FPCB工艺制造流程介绍ktt

FPC流程工序—表面处理
表面处理: 通过化学或者电化学方式,完成手指焊盘通孔等表面处理 其中有:化金、镀金、镀锡、OSP、喷锡
二.FPC的生产工序简介
FPC流程工序—靶冲
靶冲: 通过靶冲机,冲制出后工序需要使用的工具孔
二.FPC的生产工序简介
FPC流程工序—丝印
二.FPC的生产工序简介
FPC流程工序—黑孔
黑孔线
黑孔: 在孔壁上沉积上一层导电的碳膜,通过碳膜的导电性,实现电镀
二.FPC的生产工序简介
FPC流程工序—镀铜
龙门镀铜线
镀铜: 利用电化学反应方法在孔内及板面电镀上铜。增加铜面及孔壁金属厚度
二.FPC的生产工序简介
环形镀铜线
FPC流程工序—光致前清洗
二.FPC的生产工序简介
FPC流程工序—机械钻孔
局部放大
钻咀/钻头
已钻OK的产品
钻孔: ① 双面板以及多层板通孔的加工 ② 辅料工具孔的加工 ③ 工装治具的加工
二.FPC的生产工序简介
FPC流程工序—CO2激光机钻孔
二.FPC的生产工序简介
CO2 LASER原理: 利用红外线的热能,当温度升高或能量增加到一定程度后,如有机物的熔点、燃点或沸点时,则有机物分子的相互作用力或束缚力将大为减小到使有机物分子相互脱离成自由态或游离态,由于激光的不断提供能量,而使有机分子逸出或者与空气中的氧气燃烧而成为二氧化碳或水气体而散离去,由于激光是以一定直径的红外光束来加工的,因而形成微小孔。
丝印 利用印刷技术,在FPC板上印上文字、字符等符号,作为客户识别用; 或者丝印上一层油墨,作为线路板的覆盖阻焊层
二.FPC的生产工序简介
FPC流程工序—装配
FPC生产流程(全流程)

FPC生产流程(全流程)1. FPC生产流程:1.1 双面板制程:开料→ 钻孔→ PTH → 电镀→ 前处理→ 贴干膜→ 对位→曝光→ 显影→ 图形电镀→ 脱膜→ 前处理→ 贴干膜→对位曝光→ 显影→蚀刻→ 脱膜→ 表面处理→ 贴覆盖膜→ 压制→ 固化→ 沉镍金→ 印字符→ 剪切→ 电测→ 冲切→ 终检→包装→ 出货1.2 单面板制程:开料→ 钻孔→贴干膜→ 对位→曝光→ 显影→蚀刻→ 脱膜→ 表面处理→ 贴覆盖膜→ 压制→ 固化→表面处理→沉镍金→ 印字符→ 剪切→ 电测→ 冲切→ 终检→包装→ 出货2. 开料2.1. 原材料编码的认识NDIR050513HJY: D→双面, R→ 压延铜, 05→PI厚0.5mil,即12.5um, 05→铜厚18um, 13→胶层厚13um.XSIE101020TLC: S→单面, E→电解铜, 10→PI厚25um, 10→铜厚度35um, 20→胶厚20um.CI0512NL:(覆盖膜) :05→PI厚12.5um, 12→胶厚度12.5um. 总厚度:25um.2.2.制程品质控制A.操作者应带手套和指套,防止铜箔表面因接触手上之汗而氧化.B.正确的架料方式,防止皱折.C.不可裁偏,手对裁时不可破坏沖制定位孔和测试孔.D.材料品质,材料表面不可有皱折,污点,重氧化现象,所裁切材料不可有毛边,溢胶等.3钻孔3.1打包: 选择蓋板→組板→胶帶粘合→打箭头(记号)3.1.1打包要求: 单面板 30张 ,双面板 6张 , 包封15张.3.1.2蓋板主要作用:A: 防止钻机和压力脚在材料面上造成的压伤B::使钻尖中心容易定位避免钻孔位置的偏斜C:带走钻头与孔壁摩擦产生的热量.减少钻头的扭断.3.2钻孔:3.2.1流程: 开机→上板→调入程序→设置参数→钻孔→自检→IPQA检→量产→转下工序.3.2.2. 钻针管制方法:a. 使用次数管制 b. 新钻头之辨认,检验方法3.3. 品质管控点: a.钻带的正确 b.对红胶片,确认孔位置,数量,正确. c确认孔是否完全导通. d. 外观不可有铜翘,毛边等不良现象.3.4.常见不良现象3.4.1断针: a.钻机操作不当 b.钻头存有问题 c.进刀太快等.3.4.2毛边 a.蓋板,墊板不正确 b.靜电吸附等等4.电镀4.1.PTH原理及作用: PTH即在不外加电流的情況下,通过镀液的自催化(钯和铜原子作为催化剂)氧化还原反应,使铜离子析镀在经过活化处理的孔壁及铜箔表面上的过程,也称为化学镀铜或自催化镀铜.4.2.PHT流程: 碱除油→水洗→微蚀→水洗→水洗→预浸→活化→水洗→水洗→速化→水洗→水洗→化学铜→水洗.4.3.PTH常见不良状况之处理4.3.1.孔无铜 :a活化钯吸附沉积不好. b速化槽:速化剂浓度不对. c化学铜:温度过低,使反应不能进行反应速度过慢;槽液成分不对.4.3.2.孔壁有颗粒,粗糙: a化学槽有颗粒,铜粉沉积不均,开过滤机过滤. b板材本身孔壁有毛刺.4.3.3.板面发黑: a化学槽成分不对(NaOH浓度过高).4.4镀铜镀铜即提高孔内镀层均匀性,保证整个版面(孔内及孔口附近的整个镀层)镀层厚度达到一定的要求.4.4.1电镀条件控制a电流密度的选择b电镀面积的大小c镀层厚度要求d电镀时间控制4.4.1品质管控 1 贯通性:自检QC全检,以40倍放大镜检查孔壁是否有镀铜完全附着贯通.2 表面品质:铜箔表面不可有烧焦,脱皮,颗粒状,针孔及花斑不良等现象.3 附着性:于板边任一处以3M胶带粘贴后,以垂直向上接起不可有脱落现象.5.线路5.1干膜干膜贴在板材上,经曝光后显影后,使线路基本成型,在此过程中干膜主要起到了影象转移的功能,而且在蚀刻的过程中起到保护线路的作用.5.2干膜主要构成:PE,感光阻剂,PET .其中PE和PET只起到了保护和隔离的作用.感光阻剂包括:连接剂,起始剂,单体,粘着促进剂,色料.5.3作业要求 a保持干膜和板面的清洁, b平整度,无气泡和皱折现象.. c附着力达到要求,密合度高.5.4作业品质控制要点5.4.1为了防止贴膜时出现断线现象,应先用无尘纸粘尘滚轮除去铜箔表面杂质.5.4.2应根据不同板材设置加热滚轮的温度,压力,转数等参数.5.4.3保证铜箔的方向孔在同一方位.5.4.4防止氧化,不要直接接触铜箔表面.5.4.5加热滚轮上不应该有伤痕,以防止产生皱折和附着性不良5.4.6贴膜后留置10—20分钟,然后再去曝光,时间太短会使发生的有机聚合反应未完全,太长则不容易被水解,发生残留导致镀层不良.5.4.7经常用无尘纸擦去加热滚轮上的杂质和溢胶.5.4.8要保证贴膜的良好附着性.5.5贴干膜品质确认5.5.1附着性:贴膜后经曝光显影后线路不可弯曲变形或断等(以放大镜检测)5.5.2平整性:须平整,不可有皱折,气泡.5.5.3清洁性:每张不得有超过5点之杂质.5.6曝光5.6.1.原理:使线路通过干膜的作用转移到板子上.5.6.2作业要点: a作业时要保持底片和板子的清洁.b底片与板子应对准,正确.c不可有气泡,杂质.*进行抽真空目的:提高底片与干膜接触的紧密度减少散光现象.*曝光能量的高低对品质也有影响:1能量低,曝光不足,显像后阻剂太软,色泽灰暗,蚀刻时阻剂破坏或浮起,造成线路的断路.2.能量高,则会造成曝光过度,则线路会缩小或曝光区易洗掉.5.7显影5.7.1原理:显像即是将已经曝过光的带干膜的板材,经过(1.0+/-0.1)%的碳酸钠溶液(即显影液)的处理,将未曝光的干膜洗去而保留经曝光发生聚合反应的干膜,使线路基本成型.5.7.2影响显像作业品质的因素: a﹑显影液的组成 b﹑显影温度. c﹑显影压力. d﹑显影液分布的均匀性.e﹑机台转动的速度.5.7.3制程参数管控:药液溶度,显影温度,显影速度,喷压.5.7.4显影品质控制要点:a﹑出料口扳子上不应有水滴,应吹干净.b﹑不可以有未撕的干膜保护膜.c﹑显像应该完整,线路不可锯齿状,弯曲,变细等状况.d﹑显像后裸铜面用刀轻刮不可有干膜脱落,否则会影响时刻品质.e﹑干膜线宽与底片线宽控制在+/-0.05mm以内的误差.f﹑线路复杂的一面朝下放置,以避免膜渣残留,减少水池效应引起的显影不均.g﹑根据碳酸钠的溶度,生产面积和使用时间来及时更新影液,保证最佳的显影效果.h﹑应定期清洗槽内和喷管,喷头中之水垢,防止杂质污染板材和造成显影液分布不均匀性. i﹑防止操作中产生卡板,卡板时应停转动装置,立即停止放板,并拿出板材送至显影台中间,如未完全显影,应进行二次显影.j﹑显影吹干后之板子应有绿胶片隔开,防止干膜粘连而影响到时刻品质.5.8蚀刻脱膜5.8.1原理:蚀刻是在一定的温度条件下(45—50)℃蚀刻药液经过喷头均匀喷淋到铜箔的表面,与没有蚀刻阻剂保护的铜发生氧化还原反应,而将不需要的铜反应掉,露出基材再经过脱膜处理后使线路成形.5.8.2蚀刻药液的主要成分:酸性蚀刻子液(氯化铜),双氧水,盐酸,软水5.9蚀刻品质控制要点:5.9.1以透光方式检查不可有残铜, 皱折划伤等5.9.2线路不可变形,无水滴.5.9.3时刻速度应适当,不允收出现蚀刻过度而引起的线路变细,和蚀刻不尽.5.9.4线路焊点上之干膜不得被冲刷分离或断裂5.9.5时刻剥膜后之板材不允许有油污,杂质,铜皮翘起等不良品质。
PCB电路板工艺流程
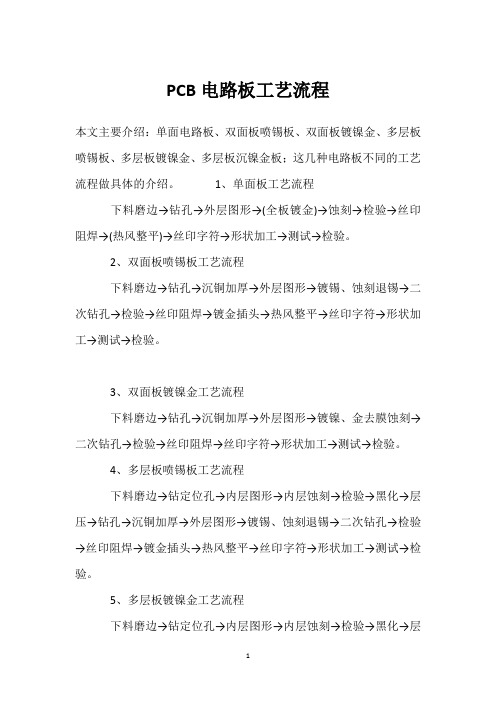
PCB电路板工艺流程
本文主要介绍:单面电路板、双面板喷锡板、双面板镀镍金、多层板喷锡板、多层板镀镍金、多层板沉镍金板;这几种电路板不同的工艺流程做具体的介绍。
1、单面板工艺流程
下料磨边→钻孔→外层图形→(全板镀金)→蚀刻→检验→丝印阻焊→(热风整平)→丝印字符→形状加工→测试→检验。
2、双面板喷锡板工艺流程
下料磨边→钻孔→沉铜加厚→外层图形→镀锡、蚀刻退锡→二次钻孔→检验→丝印阻焊→镀金插头→热风整平→丝印字符→形状加工→测试→检验。
3、双面板镀镍金工艺流程
下料磨边→钻孔→沉铜加厚→外层图形→镀镍、金去膜蚀刻→二次钻孔→检验→丝印阻焊→丝印字符→形状加工→测试→检验。
4、多层板喷锡板工艺流程
下料磨边→钻定位孔→内层图形→内层蚀刻→检验→黑化→层压→钻孔→沉铜加厚→外层图形→镀锡、蚀刻退锡→二次钻孔→检验→丝印阻焊→镀金插头→热风整平→丝印字符→形状加工→测试→检验。
5、多层板镀镍金工艺流程
下料磨边→钻定位孔→内层图形→内层蚀刻→检验→黑化→层
压→钻孔→沉铜加厚→外层图形→镀金、去膜蚀刻→二次钻孔→检验→丝印阻焊→丝印字符→形状加工→测试→检验。
6、多层板沉镍金板工艺流程
下料磨边→钻定位孔→内层图形→内层蚀刻→检验→黑化→层压→钻孔→沉铜加厚→外层图形→镀锡、蚀刻退锡→二次钻孔→检验→丝印阻焊→化学沉镍金→丝印字符→形状加工→测试→检验。
双面板的制作过程(孔化)
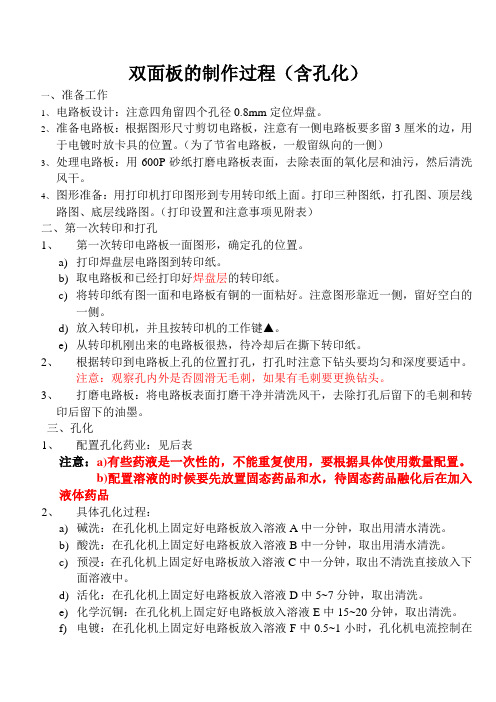
双面板的制作过程(含孔化)一、准备工作1、电路板设计:注意四角留四个孔径0.8mm定位焊盘。
2、准备电路板:根据图形尺寸剪切电路板,注意有一侧电路板要多留3厘米的边,用于电镀时放卡具的位置。
(为了节省电路板,一般留纵向的一侧)3、处理电路板:用600P砂纸打磨电路板表面,去除表面的氧化层和油污,然后清洗风干。
4、图形准备:用打印机打印图形到专用转印纸上面。
打印三种图纸,打孔图、顶层线路图、底层线路图。
(打印设置和注意事项见附表)二、第一次转印和打孔1、第一次转印电路板一面图形,确定孔的位置。
a)打印焊盘层电路图到转印纸。
b)取电路板和已经打印好焊盘层的转印纸。
c)将转印纸有图一面和电路板有铜的一面粘好。
注意图形靠近一侧,留好空白的一侧。
d)放入转印机,并且按转印机的工作键▲。
e)从转印机刚出来的电路板很热,待冷却后在撕下转印纸。
2、根据转印到电路板上孔的位置打孔,打孔时注意下钻头要均匀和深度要适中。
注意:观察孔内外是否圆滑无毛刺,如果有毛刺要更换钻头。
3、打磨电路板:将电路板表面打磨干净并清洗风干,去除打孔后留下的毛刺和转印后留下的油墨。
三、孔化1、配置孔化药业:见后表注意:a)有些药液是一次性的,不能重复使用,要根据具体使用数量配置。
b)配置溶液的时候要先放置固态药品和水,待固态药品融化后在加入液体药品2、具体孔化过程:a)碱洗:在孔化机上固定好电路板放入溶液A中一分钟,取出用清水清洗。
b)酸洗:在孔化机上固定好电路板放入溶液B中一分钟,取出用清水清洗。
c)预浸:在孔化机上固定好电路板放入溶液C中一分钟,取出不清洗直接放入下面溶液中。
d)活化:在孔化机上固定好电路板放入溶液D中5~7分钟,取出清洗。
e)化学沉铜:在孔化机上固定好电路板放入溶液E中15~20分钟,取出清洗。
f)电镀:在孔化机上固定好电路板放入溶液F中0.5~1小时,孔化机电流控制在电镀电流按每平方分米2A。
g)电镀后检查电路板表面及孔壁,是否镀上铜。
双面板制作流程
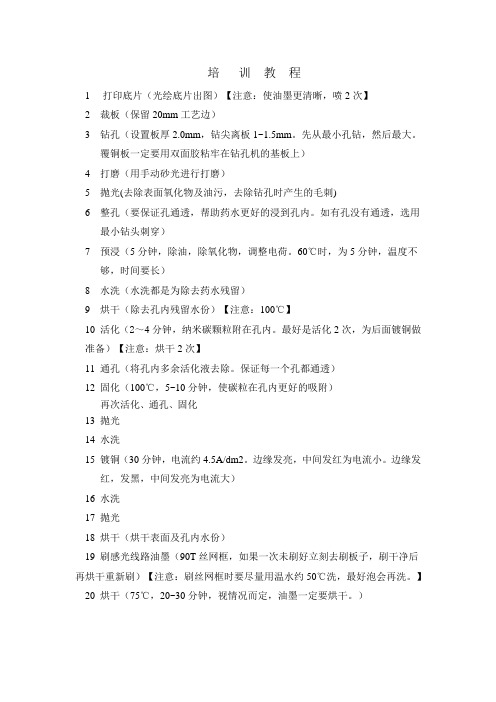
培训教程1打印底片(光绘底片出图)【注意:使油墨更清晰,喷2次】2 裁板(保留20mm工艺边)3 钻孔(设置板厚2.0mm,钻尖离板1~1.5mm。
先从最小孔钻,然后最大。
覆铜板一定要用双面胶粘牢在钻孔机的基板上)4 打磨(用手动砂光进行打磨)5 抛光(去除表面氧化物及油污,去除钻孔时产生的毛刺)6 整孔(要保证孔通透,帮助药水更好的浸到孔内。
如有孔没有通透,选用最小钻头刺穿)7 预浸(5分钟,除油,除氧化物,调整电荷。
60℃时,为5分钟,温度不够,时间要长)8 水洗(水洗都是为除去药水残留)9 烘干(除去孔内残留水份)【注意:100℃】10 活化(2~4分钟,纳米碳颗粒附在孔内。
最好是活化2次,为后面镀铜做准备)【注意:烘干2次】11 通孔(将孔内多余活化液去除。
保证每一个孔都通透)12 固化(100℃,5~10分钟,使碳粒在孔内更好的吸附)再次活化、通孔、固化13 抛光14 水洗15 镀铜(30分钟,电流约4.5A/dm2。
边缘发亮,中间发红为电流小。
边缘发红,发黑,中间发亮为电流大)16 水洗17 抛光18 烘干(烘干表面及孔内水份)19 刷感光线路油墨(90T丝网框,如果一次未刷好立刻去刷板子,刷干净后再烘干重新刷)【注意:刷丝网框时要尽量用温水约50℃洗,最好泡会再洗。
】20 烘干(75℃,20~30分钟,视情况而定,油墨一定要烘干。
)21 曝光(先要底片对位,底层镜像时,两个光面贴板子,一面贴另一面不贴的情况。
放入曝光机时贴底片的一面朝着玻璃。
曝光时先开抽气阀,等电流达到20mA时,开灯、曝光、曝光时间为20S,再关灯、放气。
)22 显影(45~50℃)23 水洗24 稍微镀点铜(1A电流镀5分钟后水洗)25 微蚀(放入微蚀液中去油,5~15S)26 水洗27 镀锡(20~30分钟,电流约1.5~2A/dm2有效面积。
先最小电流,约3~5分钟后停机取出,如果很薄,电流小,如果很白,电流OK。
制作双面板流程

双面板制作流程注意:刷油墨操作须在弱光环境操作,且刷油墨后立即清洗丝网。
一:打孔1 开机2 是否回原点?确定3 轴启4 移动X、Y、Z,使钻头位于覆铜板左下角定位孔、且垂直距覆铜板2mm以内。
5 对准后X、Y—0,Z—06 按“运行”键7 U盘文件8 选择钻孔文件9 加工速度(150-200),确定。
注:手柄设置请见文后附录一(雕刻机使用)二:抛光三:智能沉铜机预浸→水洗(可省)→活化(黑孔夹子轻轻晃动)→通孔→烘干→微蚀(可省)→水洗(可省)→烘干四:智能镀铜机设置运行电流4A~5A,时间20分钟,10*10com的板子,如果板子大电流大,时间长些,约30分钟。
注:使用时,刚开始电流稍小些,运行一定时间后电流上升五:刷线路油墨选用90的丝网,且需注意用铝角尺将线路板卡住,刷完后立即用油墨显影粉清洗丝网,该过程应在弱光环境下进行,关闭灯。
六:烘干(75度,15~20分钟)七:爆光开电源→抽气开(约5秒)→开灯(电流从40A降到20A)→爆光(正反面时间均设为6秒,十分关键)→关排气、关灯(如后面还需曝光无须关灯直接关排气即可,因灯重启需要三分钟)如显影后出现脱膜现象请适量增加曝光时间如显影后线路部分油墨不能很好的脱落请适量减少曝光时间。
八:显影自动喷淋显影机(水和油墨显影粉混合的,刚开机先空喷几次,温度40—45度,时间40~60秒)显影一次后用手轻擦线路上的墨点,如轻擦不落再次显影,直至线路部分露出光亮铜面。
九:水洗轻擦洗去显影液十:烘干十一:镀锡电流=0.6A,时间=4~5分钟,预镀锡时间为30秒。
镀锡过程中要常看,锡的厚度要比绿膜要薄。
十二:水洗十三:去膜*脱模机去膜,一定要用手套,去膜液为强碱性十四:水洗十五:腐蚀(时间:50秒,温度:45℃。
防止腐蚀过头。
)十六:水洗十七:去锡(时间:30秒,温度:室温)十八:水洗十九:刷阻焊油墨阻焊丝网选用100很重要,要均匀。
(阻焊油墨中可加固化剂,增加固化能力)二十:烘干(时间:30分钟温度:75℃)二十一:曝光(正反面均为40秒)二十二:显影显影一次,时间为60秒,显影结束观察焊盘部分油墨,如留有墨点用手轻擦之,如不掉落再次进行显影。
- 1、下载文档前请自行甄别文档内容的完整性,平台不提供额外的编辑、内容补充、找答案等附加服务。
- 2、"仅部分预览"的文档,不可在线预览部分如存在完整性等问题,可反馈申请退款(可完整预览的文档不适用该条件!)。
- 3、如文档侵犯您的权益,请联系客服反馈,我们会尽快为您处理(人工客服工作时间:9:00-18:30)。
小心烫手!!!
3.覆感光膜
剪下两张适合大小的感光膜。 注意:最好再暗处操作,感光膜不宜见光,还没准备好覆膜前,想将其置于暗 处。
打开覆膜机,预热
旁边的压力调整到3挡
预热完毕,将感光膜(两面各有一张透明保护纸),先撕起一面的一个小角,
蓝色部分轻轻按压到板子上,稍微有点固定,放进滚杆里,并扯起保护纸。这里
同时按下键盘P和F键,出现十字光标选中板子区域
进入页面设置,点击“高级选项”,留下图中层,删除其他的 注意:双面板“Holes”不选~!!!
点击”preference”,将如下颜色设置好
返回页面设置
打印预览,线和孔是白色的就对了,然后先打印顶层
接着设置底层,同样显示底层
!!!按住Alt+A全选,鼠标电住板子不放,出现 十字,再按键盘“X”,板子被镜像,底层需要镜 像
进入页面设置“高级选项”,删除“top layer”,鼠标右键“insert layer”,添加“bottom layer”
打印预览,打印底层
Hale Waihona Puke 在对孔箱上进行对孔,用胶条稍微固定
5.曝光转印
打开制版机的真空装置,放入板子,锁上两边的锁扣,选择真空功能,
开始真空,将真空装置推回机子。
注意:直到曝光结束真空都不能关!!!
设置后在工程所属文件夹下生成文件
打开数控打印机软件
注意:在打开前,先把钻孔机串口线连接好,并在“我的电脑” “管理” “设备管理器” 里,把钻孔机的串口好改为”COM1”
点击向导先选择当前钻头直径,这里我把小于等于0.8mm的孔都直接用0.8mm钻
大于0.8mm的孔这里我都选择用挖孔 注意:挖孔需要用铣刀!但你需要先安装的是钻头0.8mm的钻头,钻孔机会先把 用钻头的孔打好,然后停止找工作,提示你换铣刀,再进行挖孔。
双面板制作流程
总流程步骤
1.数控钻孔
• 1)创建钻孔所需文件 • a.打开Altium Designer的PCB文件 • b.文件→制造输出→Gerber Files • c.文件→制造输出→NC Drill Files •
Gerber Files 相关设置
NC Drill Files 相关设置
拿出板子,轻轻搓洗掉脱落的感光膜,留下转印膜。若有些地方显影不 完全,可用小木棍磨掉。显影完成。
7.蚀刻:腐蚀掉没有被感光膜覆盖的铜
打开蚀刻液动,和蚀刻温度开始蚀刻
完成!
设置曝光时间,经验时间:40s,开始曝光
曝光转印完成
6.显影:去掉未曝光的感光膜
回到制版机,打开显影液动,和显影温度
撕掉感光膜另一面的保护纸
将板子挤系上铜线,放入显 影槽 注意:这个过程必须时 刻观察,不能太久, 经验时间为20S,时间 过长,则转印了的感光 膜也会脱落 ,线会断 掉!!!
设置零点 注意:零点的选择很重要,你必须根据板的位置和图的位置选,建议先拿块废板 试一下,否则容易出现打孔范围超出板子。并且必须调整Z轴使钻头紧贴但是没 钻到板子。
先按下主轴启停按钮!!!,点击钻孔,开始
工作
开始钻孔
板子底部应用双面胶粘好 固定在木块上
注意:单面板铜面朝下!!!
2.过孔
将钻好孔的板子先除油清洗一下,3分钟、60度
有点抽象,但是没有空余的手照照片了~_~,以后补。将压力跳到1挡再压一遍, 另一面一样。这个步骤比较需要耐心,起皱的就得重新覆膜,否则铜线会断掉。
注意:在下一个 步骤开始前,应 将覆好膜的板放 在暗处!
4.对孔
• 对空前需先将电路图打印在硫酸纸上,打印需要一些设置 如下: • 打开电路图,隐藏底层并且当前层为机械层 (Mechanical1)
清洗板子
接下来,在孔内覆上一层石墨电镀材料,称孔化
时间2分钟,30度。
拿出板子用电风吹吹干,并保证每个空不被孔化液堵住
吹干后,在放回孔化槽,再进行一遍。
清洗板子,不用担心孔内的孔化液会被洗掉
沉铜:使孔内覆上铜,时间40分钟,温度25度
电压适度就好, 电流1A/dm2,双 面板都算
沉铜完取出板子,清洗一遍,再用电风吹吹干