第7章缺口试样的断裂及其抗力
材料的力学性能 断裂与断口分析

材料的力学性能-断裂与断口分析材料的断裂断裂是工程材料的主要失效形式之一。
工程结构或机件的断裂会造成重大的经济损失,甚至人员伤亡。
如何提高材料的断裂抗力,防止断裂事故发生,一直是人们普遍关注的课题。
任何断裂过程都是由裂纹形成和扩展两个过程组成的,而裂纹形成则是塑性变形的结果。
对断裂的研究,主要关注的是断裂过程的机理及其影响因素,其目的在于根据对断裂过程的认识制定合理的措施,实现有效的断裂控制。
✓材料在塑性变形过程中,会产生微孔损伤。
✓产生的微孔会发展,即损伤形成累积,导致材料中微裂纹的形成与加大,即连续性的不断丧失。
✓损伤达到临界状态时,裂纹失稳扩展,实现最终的断裂。
按断裂前有无宏观塑性变形,工程上将断裂分为韧性断裂和脆性断裂两大类。
断裂前表现有宏观塑性变形者称为韧性断裂。
断裂前发生的宏观塑性变形,必然导致结构或零件的形状、尺寸及相对位置改变,工作出现异常,即表现有断裂的预兆,可能被及时发现,一般不会造成严重的后果。
脆性断裂断裂前,没有宏观塑性变形的断裂方式。
脆性断裂特别受到人们关注的原因:脆性断裂往往是突然的,因此很容易造成严重后果。
脆性断裂断裂前不发生宏观塑性变形的脆性断裂,意味着断裂应力低于材料屈服强度。
对脆性断裂的广义理解,包括低应力脆断、环境脆断和疲劳断裂等。
脆性断裂一般所谓脆性断裂仅指低应力脆断,即在弹性应力范围内一次加载引起的脆断。
主要包括:与材料冶金质量有关的低温脆性、回火脆性和蓝脆等;与结构特点有关的如缺口敏感性;与加载速率有关的动载脆性等。
材料的断裂比较合理的分类方法是按照断裂机理对断裂进行分类。
微孔聚集型断裂、解理断裂、准解理断裂和沿晶断裂。
有助于→揭示断裂过程的本质→理解断裂过程的影响因素→寻找提高断裂抗力的方法。
材料的断裂将环境介质作用下的断裂和循环载荷作用下的疲劳断裂按其断裂过程特点单独讨论。
金属材料的断裂-静拉伸断口材料在静拉伸时的断口可呈现3种情况:(a)(b):平断口;(c)(d):杯锥状断口;(e)尖刃断口平断口:材料塑性很低、或者只有少量的均匀变形,断口齐平,垂直于最大拉应力方向。
金属力学性能

⾦属⼒学性能绪论1.⼯程材料及其性能2.⾦属⼒学性能内涵3.课程的内容和基本要求4.课程在学科中的地位5.课程的学习⽅法6.教材内容7.参考书1. ⼯程材料及其性能⼀、材料的种类类型分:⾦属材料;⾮⾦属材料;复合材料。
⽤途分:结构材料;功能材料;结构-功能材料。
⼆、材料的性能物理性能(声、光、电、磁、热):ρ、Tm、Tb、Cp、磁导率,等;化学性能:可燃性、反应性、抗氧化性,等;⼒学性能:σ、δ、HB、KIC,等;⼯艺性能:热加⼯(铸、锻、焊、热处理……)、冷加⼯性能(车、铣、刨、磨……),特种加⼯(电⽕花、激光、离⼦……)、储存、运输性能,等;⽣物性能:⽣物反应性、⽣物相容性等。
2. ⾦属⼒学性能内涵1)定义⾦属的⼒学⾏为:⾦属在外加载荷作⽤下,或者在载荷、加载速率和环境因素的联合作⽤下表现出的⾏为。
⾦属的⼒学性能:⾦属在⼒的作⽤下,所显⽰出的与弹性和⾮弹性反应相关或涉及应⼒应变关系的性能。
2)⼒学性能的指标强度σ、硬度HB、塑性δ、韧性ak、断裂韧度KIC 等。
3)影响⾦属⼒学性能的主要因素内因:晶体学特性;化学成分、显微组织、内部缺陷;残余应⼒等外因:温度、周围介质;加载⽅式、加载速率等。
不同外因(即服役⼯况)时,⾦属的⼒学性能的数值将发⽣改变。
⾦属⼒学性能内涵1)⾦属软硬程度2)⾦属脆性3)⾦属抵抗外⼒能⼒4)⾦属变形能⼒5)含缺陷⾦属抗断裂能⼒6)⾦属抵抗多次受⼒能⼒7)特殊条件下⾦属材料性能⼏个基本概念:弹性:是指材料在外⼒作⽤下保持和恢复固有形状和尺⼨的能⼒。
塑性:是材料在外⼒作⽤下发⽣不可逆的永久变形的能⼒.强度:是材料对变形和断裂的抗⼒。
韧性:抵抗裂纹形成和扩展的能⼒,表现为材料在断裂前吸收能量的能⼒。
3. 课程的内容和基本要求课程主要包括两部分:基本⼒学⾏为和应⽤⼒学⾏为,其中:1)⾦属的基本⼒学⾏为包括弹性变形、塑性变形、断裂,这⼏部分是⾦属⼒学性能课程的主要部分;2)应⽤⼒学⾏为包括⾦属在各种应⽤条件下的⼒学⾏为,如疲劳。
湖南大学材料性能学作业习题答案
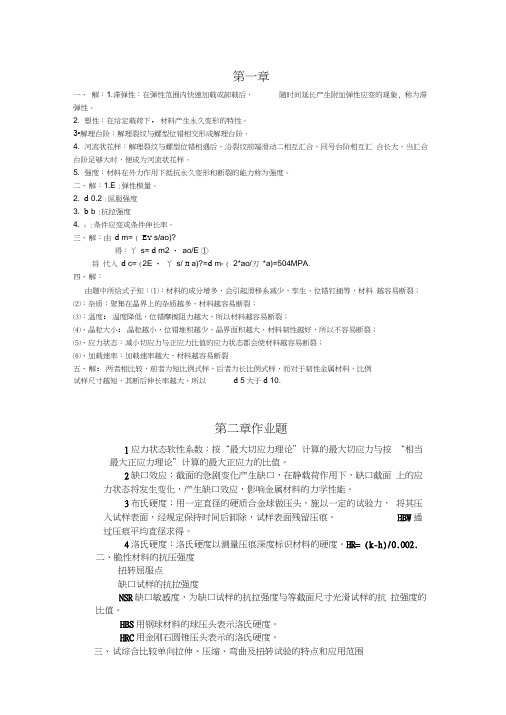
第一章一、解:1.滞弹性:在弹性范围内快速加载或卸载后,随时间延长产生附加弹性应变的现象, 称为滞弹性。
2. 塑性:在给定载荷下,材料产生永久变形的特性。
3•解理台阶:解理裂纹与螺型位错相交形成解理台阶。
4. 河流状花样:解理裂纹与螺型位错相遇后,沿裂纹前端滑动二相互汇合,同号台阶相互汇合长大,当汇合台阶足够大时,便成为河流状花样。
5. 强度:材料在外力作用下抵抗永久变形和断裂的能力称为强度。
二、解:1.E :弹性模量。
2. d 0.2 :屈服强度3. b b :抗拉强度4. £ :条件应变或条件伸长率。
三、解:由d m= ( E Y s/ao)?得:丫s= d m2 • ao/E ①将代入d c= (2E • 丫s/ JI a)?=d m- ( 2*ao/刃*a)=504MPA.四、解:由题中所给式子知:⑴:材料的成分增多,会引起滑移系减少、孪生、位错钉插等,材料越容易断裂;⑵:杂质:聚集在晶界上的杂质越多,材料越容易断裂;⑶:温度:温度降低,位错摩擦阻力越大,所以材料越容易断裂;⑷、晶粒大小:晶粒越小,位错堆积越少,晶界面积越大,材料韧性越好,所以不容易断裂;⑸、应力状态:减小切应力与正应力比值的应力状态都会使材料越容易断裂;⑹、加载速率:加载速率越大,材料越容易断裂五、解:两者相比较,前者为短比例式样,后者为长比例式样,而对于韧性金属材料,比例试样尺寸越短,其断后伸长率越大,所以 d 5大于d 10.第二章作业题1应力状态软性系数:按“最大切应力理论”计算的最大切应力与按“相当最大正应力理论”计算的最大正应力的比值。
2缺口效应:截面的急剧变化产生缺口,在静载荷作用下,缺口截面上的应力状态将发生变化,产生缺口效应,影响金属材料的力学性能。
3布氏硬度:用一定直径的硬质合金球做压头,施以一定的试验力,将其压入试样表面,经规定保持时间后卸除,试样表面残留压痕。
HBW通过压痕平均直径求得。
材料力学性能复习要点
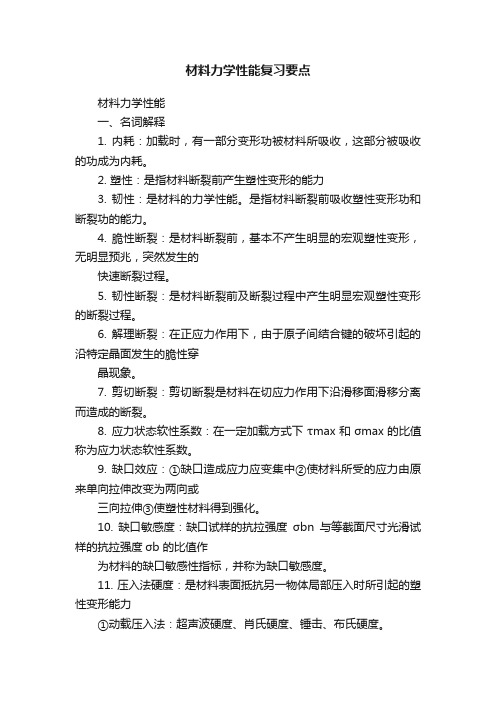
材料力学性能复习要点材料力学性能一、名词解释1. 内耗:加载时,有一部分变形功被材料所吸收,这部分被吸收的功成为内耗。
2. 塑性:是指材料断裂前产生塑性变形的能力3. 韧性:是材料的力学性能。
是指材料断裂前吸收塑性变形功和断裂功的能力。
4. 脆性断裂:是材料断裂前,基本不产生明显的宏观塑性变形,无明显预兆,突然发生的快速断裂过程。
5. 韧性断裂:是材料断裂前及断裂过程中产生明显宏观塑性变形的断裂过程。
6. 解理断裂:在正应力作用下,由于原子间结合键的破坏引起的沿特定晶面发生的脆性穿晶现象。
7. 剪切断裂:剪切断裂是材料在切应力作用下沿滑移面滑移分离而造成的断裂。
8. 应力状态软性系数:在一定加载方式下τmax和σmax的比值称为应力状态软性系数。
9. 缺口效应:①缺口造成应力应变集中②使材料所受的应力由原来单向拉伸改变为两向或三向拉伸③使塑性材料得到强化。
10. 缺口敏感度:缺口试样的抗拉强度σbn与等截面尺寸光滑试样的抗拉强度σb 的比值作为材料的缺口敏感性指标,并称为缺口敏感度。
11. 压入法硬度:是材料表面抵抗另一物体局部压入时所引起的塑性变形能力①动载压入法:超声波硬度、肖氏硬度、锤击、布氏硬度。
②静载压入法:布氏硬度、洛氏硬度、维氏硬度、显微硬度。
12. 低温脆性:当试验温度低于某一温度tk时,材料由韧性状态变为脆性状态,冲击吸收功明显下降,断裂机理由微孔聚集变为穿晶解理。
断口特征由纤维状变为结晶状。
13. 韧脆转变温度:当试验温度低于某一温度tk时,材料由韧性状态变为脆性状态,冲击吸收功明显下降,断裂机理由微孔聚集变为穿晶解理。
转变温度tk称为韧脆转变温度。
14. 冲击韧性:单位A吸收冲击功的能力。
15. 低应力脆断:高强度钢超高强度钢的机件,中低强度钢的大型机件常常在工作应力低于屈服极限的情况下,发生脆性断裂现象。
16. 应力场强度因子:反映了裂纹尖端区域应力场的强度KI17. 断裂韧性:KI随a或σ单独或共同增加而增加,当KI达到一定值时,裂纹失稳扩展断裂。
材料力学性能06_缺口试样
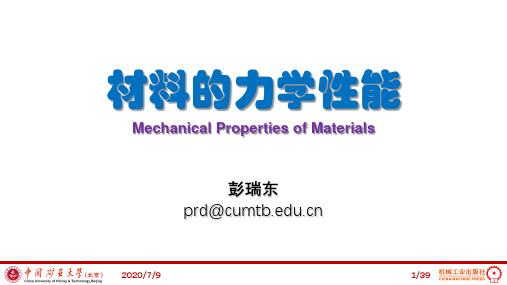
断裂韧度测定试验-JⅠc的测定
临界点的确定对JⅠc值的影响很大,一般认为
,采用裂纹开裂点作为临界点较为合适,这样
规定比较符合JⅠc的定义。但在多数JⅠc测定试
验中,由于裂纹扩展前其尖端会产生塑性变形
,致使P-Δ曲线上裂纹的开始扩展点不明显,
因而,需要借助于电位法或声发射法辅助标定 裂纹开裂点。
若在Fmax处突然断裂,则Fmax/F=1,表示裂纹扩展极 快,材料产生突然脆性断裂,缺口敏感度最大。
如果仅有第I和第Ⅱ部分,断裂功为零,即当F= Fmax时试样突然脆性断裂,说明材料对缺口敏感 。而且第Ⅱ部分愈小,缺口敏感度愈高。 第Ⅲ部分代表裂纹产生后材料阻碍裂纹继续扩展 的能力,其面积愈大,说明裂纹可缓慢扩展较长 距离,材料具有良好塑性和低的缺口敏感度。
2020/7/9
33/39
疲劳裂纹扩展试验
当材料中存在裂纹并且外加应力达到某一临界值后,裂纹就会发生失 稳扩展。因此含裂纹材料的断裂可根据断裂韧度加以判别。不过在很 多情况下,这种足够大的宏观临界裂纹是在载荷作用下由萌生的小裂 纹逐渐扩展而成的,这也就是所谓的亚临界裂纹扩展过程。 疲劳载荷下的亚临界裂纹扩展尤为重要,这也是导致材料疲劳破坏的 主要原因。通过疲劳裂纹扩展试验,得到疲劳裂纹从萌生到亚临界扩 展再到最后失稳扩展的全过程,可以测定材料中疲劳裂纹扩展的门槛 值,得到疲劳裂纹扩展速率的变化规律,进而估算材料的疲劳寿命。
2020/7/9
帕里思(Paris)从断裂力学的角度分析了疲 劳裂纹扩展的规律,发现决定裂纹扩展速率
da/dN的主要力学参量是应力强度因子差值 ΔK。ΔK是应力循环过程中最大应力和最小应
力所对应的应力强度因子之差。
典型的疲劳裂纹扩展速率曲线(lgda/dNlgΔK)可以分为三个区域
单边缺口拉伸试样的断裂韧性计算方法对比

试 验 免 的.目前 , 基于断裂力学的“ 合于使用” 原则 , 通 1 过E C A评估 允许 未造 成安 全 问题 缺 陷 的存 在 , 在 保 试 验采 用 A P I X 7 0管线 钢 , 化 学成 分 见表 1 ( F e 证 结构 安全 服役 的前 提下极 大 的提 高 了材 料 的利 用 余量) . 从外径 7 1 1 m m, 壁厚 1 2 . 5 m m管道沿管径 效率 , 同 时也降 低 了制造周 期 和成本 .
0 序
言
吻合极 好 , 建 议 使 用 双 引伸 计 法 作 为 S E N T断 裂 韧 性 计算 的参 考方法 .文 中 旨在评 估其 它 四种方 法 相
T O D 的误 差 , 进 而探 究 随着管线输送压力要求的不断提高 , 高钢级管 对 于 双引 伸 计 法计 算 得 到 C C A 评 估 极 限 裂 纹 线 钢 的开发 应用 已成 为 管 道 用 钢 的 热 点 , 管 道 的 服 不 同计算 方 法 造 成 的误 差 对 于 E 尺寸 的影响 , 为 管线 工 程 设 计 中断 裂韧 性 的选 取 方 役 条 件 日趋严苛 .因此 , 在 工程 设 计 中 , 需要 有 严 格 的设计 准则 和依 据 以达到 优化 的安 全裕 度 和 精确 的 法 提供 参考 意见 . 服役 寿命 , 然而 在焊接 结构 中 , 缺陷 的出现 是 不可 避
1 . 53 0. 21 0. 0 2 4 0. 0 3 8
大误差 , 断裂韧性的精确度对于 E C A评估极限裂纹尺寸有极 大影 响.
关键词 : 断裂韧性 ;合于使用 ;验证 ;评估
中图分类号 : T G 4 0 7 文献标识码 : A 文章编 号: 0 2 5 3— 3 6 0 X【 2 0 1 7 ) 0 4— 0 0 5 9— 4 0
动载荷下材料的力学性能

指材料在冲击载荷作用下吸收塑性变形功和 断裂功的能力,用标准试样的冲击吸收功Ak 表示。 意义:评定材料承受冲击载荷的能力 揭示材料在冲击载荷下的力学行为
冲击载荷与静载荷的主要区别在于加载速度(幅度和频率)
冲击失效的特点
(1)与静载荷下相同,弹性变形、塑性变形、断裂。 (2)吸收的冲击能测不准。 时间短;机件;与机件联接物体的刚度。 通常假定冲击能全部转换成机件内的弹性能, 再按能量守恒法计算。 (3)材料的弹性行为及弹性模量对应变率无影响。 ∵ 弹性变形的速度4982m/s(>声速), 普通摆锤冲击试验的绝对变形速度5~5.5m/s。
低温脆性是材料屈服强 度随着温度的降低急剧 增加的结果。 见右图,屈服点随着温 度的下降而升高,但材 料的解理断裂强度随着 温度的变化很小, 两线交点对应的温度就 是tk。
二、韧脆转变温度
在不同温度下进行冲击弯曲试验, 根据试验结果作出冲击吸收功-温度曲线、 断口形貌中各区所占面积和温度的关系曲线, 试样断裂后塑性变形量与温度的关系曲线等, 根据这些曲线来求得tk。
零塑性转变温度NDT已成为低强度钢构件防止 脆性断裂设计根据的一部分,例如:
(1) NDT设计标准 (2) NDT+33℃设计标准
(3) NDT+67℃设计标准
落锤试验的缺点:
(1) 不能定量评定脆性断裂
(2) 未考虑板厚的影响
通过落锤试验所得NDT可以建立断裂分析图(FAD, Fracture Analysis Diagram),表示许用应力、缺陷 (裂纹)和温度之间的关系曲线,见下图:
韧脆转变温度tk可用于抗脆断设计、保证机件 服役安全,但不能直接用来设计计算机件的承 载能力或截面尺寸。 机件的最低使用温度必须高于tk,两者相差越 大越安全,所以选用的材料应该具有一定的韧 性温度储备,也就是说具有一定的△值, △=t0-tk。
系列缺口试样静拉伸实验及断口形貌观察
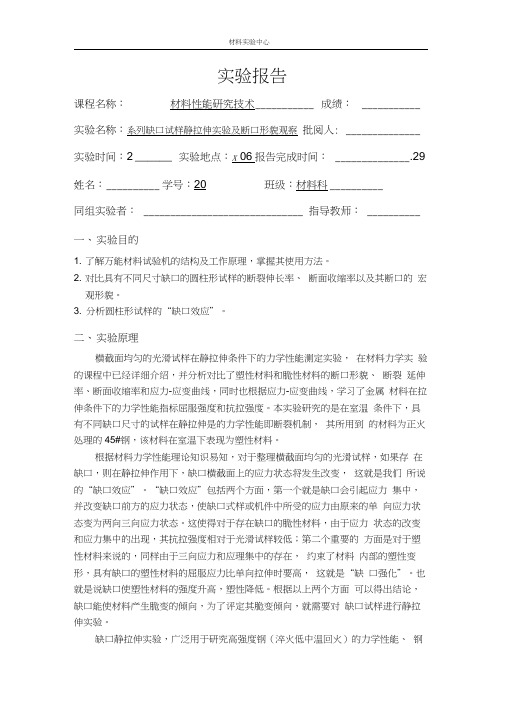
实验报告课程名称:材料性能研究技术___________ 成绩:___________ 实验名称:系列缺口试样静拉伸实验及断口形貌观察批阅人: ______________ 实验时间:2 ______ 实验地点:x 06报告完成时间:______________ .29姓名:__________ 学号:20 班级:材料科__________同组实验者:______________________________ 指导教师:__________一、实验目的1. 了解万能材料试验机的结构及工作原理,掌握其使用方法。
2. 对比具有不同尺寸缺口的圆柱形试样的断裂伸长率、断面收缩率以及其断口的宏观形貌。
3. 分析圆柱形试样的“缺口效应”。
二、实验原理横截面均匀的光滑试样在静拉伸条件下的力学性能测定实验,在材料力学实验的课程中已经详细介绍,并分析对比了塑性材料和脆性材料的断口形貌、断裂延伸率、断面收缩率和应力-应变曲线,同时也根据应力-应变曲线,学习了金属材料在拉伸条件下的力学性能指标屈服强度和抗拉强度。
本实验研究的是在室温条件下,具有不同缺口尺寸的试样在静拉伸是的力学性能即断裂机制,其所用到的材料为正火处理的45#钢,该材料在室温下表现为塑性材料。
根据材料力学性能理论知识易知,对于整理横截面均匀的光滑试样,如果存在缺口,则在静拉伸作用下,缺口横截面上的应力状态将发生改变,这就是我们所说的“缺口效应”。
“缺口效应”包括两个方面,第一个就是缺口会引起应力集中,并改变缺口前方的应力状态,使缺口式样或机件中所受的应力由原来的单向应力状态变为两向三向应力状态。
这使得对于存在缺口的脆性材料,由于应力状态的改变和应力集中的出现,其抗拉强度相对于光滑试样较低;第二个重要的方面是对于塑性材料来说的,同样由于三向应力和应理集中的存在,约束了材料内部的塑性变形,具有缺口的塑性材料的屈服应力比单向拉伸时要高,这就是“缺口强化”。
物理实验 金属缺口试样冲击韧性的测定

3、实验课的要求学生实验前必须提前对实验进行预习,并撰写预习报告。
预习实验时,学生应主动查阅与实验相关的理论课内容,理解实验目的和实验原理,并对实验过程有基本的了解。
预习报告包括:实验目的,实验原理,实验步骤和实验数据记录表格。
实验前,实验教师会检查学生的预习报告,对于没有完成预习报告的学生将不准进行实验。
实验过程中,要求学生独立完成,认真记录实验现象和实验数据,培养独立思考能力,解决问题的能力以及创新能力。
实验结束后,对实验结果进行整理和分析,加深对相关理论课程内容的理解,并撰写实验报告。
实验报告内容包括:实验数据和实验现象,实验结果的分析和讨论,实验结论,对实验的思考以及建议,最后要回答实验后的思考题。
实验三金属缺口试样冲击韧性的测定一、实验目的1.学习金属冲击值的测定方法。
2.学习使用冲击试验机。
3.观察试件的断口情况。
二、实验内容测定不同温度下冲击样品断口的结晶区域面积百分比,不同材料和缺口的冲击值。
三、设备及材料1.设备本实验采用济南天辰试验机有限公司制造的JB-300b摆锤式冲击试验机。
试验机如图2.5.1安装在底座的耗材,被扬起的摆锤砸断,表盘上可读出,耗材断裂所消耗的能量,即吸收功。
图3.1 JB-300b摆锤式冲击试验机2.材料实验材料为低碳钢,铸铁,将其制成夏比V型和U型缺口冲击试样。
四、实验原理冲击试验是研究材料在冲击载荷作用下所表现出的机械性能的一种实验。
金属的冲击韧度是一个重要的力学性能指标。
冲击载荷作用时间极短,测量载荷变化和构件变形很困难,但是破坏构件所消耗的能量很容易测量,消耗的能量除以面积称之为冲击韧度。
冲击试验的缺口试件有两种,分别是u型和v型。
试件的缺口是为了使试件在承受冲击时受力集中。
冲击韧度值对切口的尺寸和形状十分敏感,切口深尖锐,则韧度值低,因此同种材料的用不同切口测定的韧度值不能换算和比较。
图 3.2缺口深度为5mm的标准夏比U型缺口冲击试样夏比冲击试验是将具有规定形状和尺寸的试件安放在试验机上,然后将具有一定质量的摆锤举到固定高度,使之获得一定能量,落下摆锤冲断试件,这时,试验机表盘上即可读出冲击吸收的功。
缺口试样的断裂及其抗力共35页
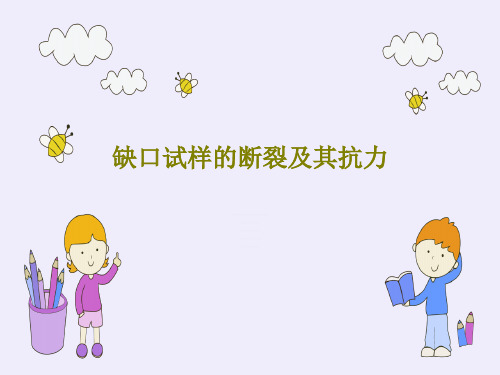
谢谢!
51、 天 下 之 事 常成 于困约 ,而败 于奢靡 。——陆 游 52、 生 命 不 等 于是呼 吸,生 命是活 动。——卢 梭
53、 伟 大 的 事 业,需 要决心 ,能力 ,组织 和责任 感。 ——易 卜 生 54、 唯 书 籍 不 朽。——乔 特
缺口试样的断裂及其抗力
36、如果我们国家的法律中只有某种 神灵, 而不是 殚精竭 虑将神 灵揉进 宪法, 总体上 来说, 法律就 会更好 。—— 马克·吐 温 37、纲纪废弃之日,便是暴政兴起之 时。— —威·皮 物特
38、若是没有公众舆论的支持,法律 是丝毫 没有力 量的。 ——菲 力普斯 39、一个判例造出另一个判例,它们 迅速累 聚,பைடு நூலகம் 而变成 法律。 ——朱 尼厄斯
55、 为 中 华 之 崛起而 读书。 ——周 恩来
7断裂和力学性能3
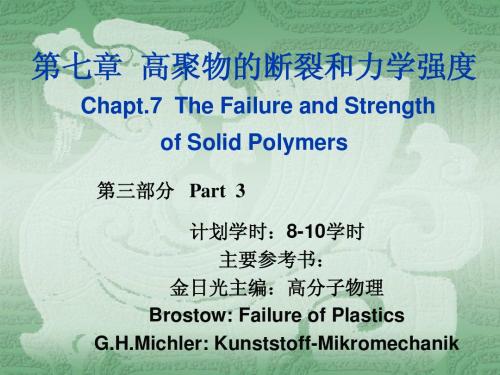
图7-30 冲击实验中材料受力及屈挠关系曲线 曲线下面积:白亮区域——裂纹引发能 阴影区域——裂纹扩展能
脆性断裂和韧性断裂表面
图7-31
左图脆性试样断裂表面的照片;右图韧性试样断裂表面的照片
图7-32
左图脆性试样断裂表面的电镜照片;右图韧性试样断裂表面的电镜照片
(二)影响抗冲击强度的因素 1、 缺口的影响 冲击实验时,有时在试样上预置缺口,有时不加缺口。 有缺口试样的抗冲强度远小于无缺口试样,原因在于有 缺口试样已存在表观裂纹,冲击破坏吸收的能量主要用 于裂纹扩展。
第七章 高聚物的断裂和力学强度
Chapt.7 The Failure and Strength of Solid Polymers
第三部分 Part 3
计划学时:8-10学时 主要参考书: 金日光主编:高分子物理 Brostow: Failure of Plastics G.H.Michler: Kunststoff-Mikromechanik
三、高分子材料的抗冲击强度和增韧改性 高分子材料抗冲击强度是指标准试样受高速冲击作用断 裂时,单位断面面积(或单位缺口长度)所消耗的能量。 它描述了高分子材料在高速冲击作用下抵抗冲击破坏的能 力和材料的抗冲击韧性,有重要工艺意义。但它不是材料 基本常数,其量值与实验方法和实验条件有关。 (一) 抗冲击强度实验
金属缺口试样的力学性能
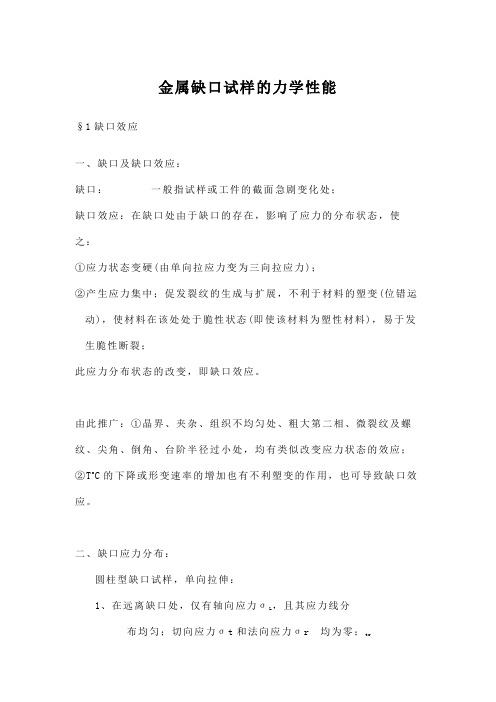
金属缺口试样的力学性能§1缺口效应一、缺口及缺口效应:缺口:一般指试样或工件的截面急剧变化处;缺口效应:在缺口处由于缺口的存在,影响了应力的分布状态,使之:①应力状态变硬(由单向拉应力变为三向拉应力);②产生应力集中;促发裂纹的生成与扩展,不利于材料的塑变(位错运动),使材料在该处处于脆性状态(即使该材料为塑性材料),易于发生脆性断裂;此应力分布状态的改变,即缺口效应。
由此推广:①晶界、夹杂、组织不均匀处、粗大第二相、微裂纹及螺纹、尖角、倒角、台阶半径过小处,均有类似改变应力状态的效应;②T o C 的下降或形变速率的增加也有不利塑变的作用,也可导致缺口效应。
二、缺口应力分布:圆柱型缺口试样,单向拉伸:,且其应力线分1、在远离缺口处,仅有轴向应力ζL布均匀;切向应力ζt和法向应力ζr 均为零;t r2、在缺口附近,轴向应力的应力线在缺口根部发生弯曲,变成非均匀分布(于近根部处分布较密),形成应力集中,并产生三向拉应力:轴向应力ζL、法向应力ζr、切向应力ζt;在缺口根部:ζL分布不均匀,且由于缺口上下出现无应力区,将阻止缺口附近截面的正常收缩,因而出现了ζr、ζt,其分布见上图左半部,图的右半部为应力状态柔性系数α的分布曲线(α<0.5)而应力分布的不均匀程度可用应力分配系数K表示。
K ζmax 其值大小,取决于缺口根部半径(可由设计手册查得)ζ均如:薄板:ζt = 0,为平面应力状态:ζ=(ζ1,ζ2,0)厚板:εt = 0;为平面应变状态:ε=(ε1,ε2,0),实际上是三向拉应力状态:ζ= [ζ1,ζ2,μ(ζ1+ζ2)]ε3= [ζμ(ζ1+ζ2)] /E = 0 ==>ζ 3 =μ(ζ1+ζ2)综上分析所述,缺口:1)引起应力集中(或分布不均匀):包括轴向应力ζL,法向应力ζr和切向应力ζt;2)引起三向拉应力;此即为缺口效应之二个方面的表现三、塑性状态下缺口的应力分布:由于应力分布不均匀,在拉伸过程中屈服时的塑性变形将不会在材料内部同时均匀进行,是由缺口根部先局部进行并逐渐过度到材料内部ηmax = (ζ1-ζ3)/2 = (ζL-ζr)/2 表面ηmax仍为最大;当ηmax>ηs =ζs/2,即ζL-ζr>ζs (表面ζr=0)时,材料发生屈服并使表面的应力发生松驰,ζL应力峰值向内移动;由于ηmax= (ζL-ζr)/2,而在表面ζr=0,并在一定深度ζr达到最大值,即开始时ζr是增加的,故ζL也须增加才能使屈服和塑性变形继续向内移,即需提高P。
金属缺口试样冲击韧性的测定
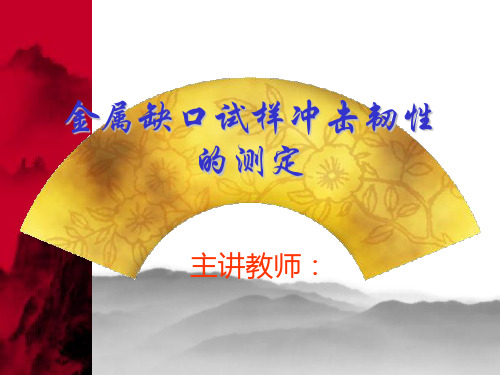
金属缺口试样冲击韧性的测定主讲教师:一、实验目的 1.了解冲击韧性的含义。
2.测定钢材和硬铝合金的冲击韧性,比较两种材料的抗冲击力和破坏断口的形貌。
二、实验原理 材料在冲击载荷作用下,产生塑性变形和断裂过程吸收能量的能力,称为材料的冲击韧性。
用实验方法测定材料的冲击韧性时,是把材料制成标准试样,置于能实施打击能量的冲击试验机上进行的,并用折断试样的冲击吸收功来衡量。
按照不同的实验温度、试样受力方式、实验打击能量等来区分,冲击实验的类型繁多,不下十余种。
现在介绍常温、简支梁式、大能量一次性冲击实验。
依据是国家标准GB/T 229-1994《金属夏比缺口冲击试验方法》。
冲击试验机由摆锤、机身、支座、度盘、指针等几部分组成(图1)。
实验时,将带有缺口的受弯试样安放于试验机的支座上,举起摆锤使它自由下落将试样冲断。
若摆锤重量为G,冲击中摆锤的质心高度由H0变为H1,势能的变化为G(H0-H1),它等于冲断试样所消耗的功W,亦即冲击中试样所吸收的功为:Ak=W=G(H0-H1) 1设摆锤质心至摆轴的长度为l (称为摆长),摆锤的起始下落角为α,击断试样后最大扬起的角度为β,式1又可写为A k =G l (cosβ-cosα) 2 α一般设计成固定值,为适应不同打击能量的需要,冲击试验机都配备两种以上不同重量的摆锤,β则随材料抗冲击能力的不同而变化,如事先用β最大可能变化的角度计算出A k 值并制成指示度盘,A k 值便可由指针指示的位置从度盘上读出。
A k 值的单位为J (焦耳)。
A k 值越大,表明材料的抗冲击性能越好。
A k 值是一个综合性的参数,不能直接用于设计,但可作为抗冲击构件选择材料的重要指标。
材料的内部缺陷和晶粒的大小对A k 值有明显影响,因此可用冲击实验来检验材料质量,判定热加工和热处理工艺质量。
A k 值对温度的变化也很敏感,随着温度的降低,在某一狭窄的温度区间内,低碳钢的A k 值骤然下降,材料变脆,出现冷脆现象。
v型缺口冲击试验吸收
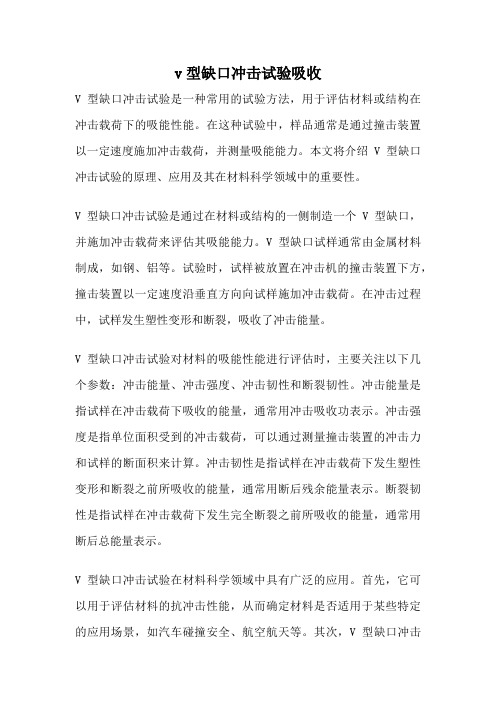
v型缺口冲击试验吸收V型缺口冲击试验是一种常用的试验方法,用于评估材料或结构在冲击载荷下的吸能性能。
在这种试验中,样品通常是通过撞击装置以一定速度施加冲击载荷,并测量吸能能力。
本文将介绍V型缺口冲击试验的原理、应用及其在材料科学领域中的重要性。
V型缺口冲击试验是通过在材料或结构的一侧制造一个V型缺口,并施加冲击载荷来评估其吸能能力。
V型缺口试样通常由金属材料制成,如钢、铝等。
试验时,试样被放置在冲击机的撞击装置下方,撞击装置以一定速度沿垂直方向向试样施加冲击载荷。
在冲击过程中,试样发生塑性变形和断裂,吸收了冲击能量。
V型缺口冲击试验对材料的吸能性能进行评估时,主要关注以下几个参数:冲击能量、冲击强度、冲击韧性和断裂韧性。
冲击能量是指试样在冲击载荷下吸收的能量,通常用冲击吸收功表示。
冲击强度是指单位面积受到的冲击载荷,可以通过测量撞击装置的冲击力和试样的断面积来计算。
冲击韧性是指试样在冲击载荷下发生塑性变形和断裂之前所吸收的能量,通常用断后残余能量表示。
断裂韧性是指试样在冲击载荷下发生完全断裂之前所吸收的能量,通常用断后总能量表示。
V型缺口冲击试验在材料科学领域中具有广泛的应用。
首先,它可以用于评估材料的抗冲击性能,从而确定材料是否适用于某些特定的应用场景,如汽车碰撞安全、航空航天等。
其次,V型缺口冲击试验还可以用于研究材料的断裂行为和断裂机制,为材料的设计和改进提供理论依据。
此外,V型缺口冲击试验还可以用于比较不同材料的吸能性能,以指导材料的选择和设计。
在进行V型缺口冲击试验时,需要注意以下几点。
首先,试样的制备应符合相关标准,包括试样尺寸、缺口形状和尺寸等。
其次,试验过程中应严格控制冲击载荷的大小和速度,以确保试样在相同条件下进行比较。
最后,试验结果应进行统计分析,以获得可靠的吸能性能指标。
V型缺口冲击试验是一种常用的试验方法,用于评估材料或结构在冲击载荷下的吸能性能。
该试验方法可以为材料的设计和改进提供重要的理论依据,对于确保材料在实际应用中的安全可靠性具有重要意义。
缺口试样的断裂及其抗力35页PPT

15、机会是不守纪律的。——雨果
56、书不仅是生活,而且是现在、过 去和未 来文化 生活的 源泉。 ——库 法耶夫 57、生命不可能有两次,但许多人连一 次也不 善于度 过。— —吕凯 特 58、问渠哪得清如许,为有源头活水来 。—— 朱熹 59、我的努力求学没有得到别的好处, 只不过 是愈来 愈发觉 自己的 无知。 ——笛 卡儿
缺口试样的断裂及其抗力
11、战争满足了,或曾经满足过人的 好斗的 本能, 但它同 时还满 足了人 对掠夺 ,破坏 以及残 酷的纪 律和专 制力的 欲望。 ——查·埃利奥 特 12、不应把纪律仅仅看成教育的手段 。纪律 是教育 过程的 结果, 首先是 学生集 体表现 在一切 生活领 域—— 生产、 日常生 活、学 校、文 化等领 域中努 力的结 果。— —马卡 连柯(名 言网)
拉
60、生活的道路一旦选定,就要勇敢地 走到底 ,决不 回头。 ——左
Байду номын сангаас
- 1、下载文档前请自行甄别文档内容的完整性,平台不提供额外的编辑、内容补充、找答案等附加服务。
- 2、"仅部分预览"的文档,不可在线预览部分如存在完整性等问题,可反馈申请退款(可完整预览的文档不适用该条件!)。
- 3、如文档侵犯您的权益,请联系客服反馈,我们会尽快为您处理(人工客服工作时间:9:00-18:30)。
23
冲击断口
•冲击断口包含纤维区、放射区、剪切唇三个区。 •若试验材料具有一定的韧性,可形成两个纤维 区: 即: 纤维区1—放射区—纤维区2—剪切唇 •纤维区2(红色区域)形成原因:裂纹快速扩展形 成结晶区,到了压缩区后, 应力状态发生变化,裂 纹扩展速度再次减小, 最终形成纤维区2。
冲击断口形貌示意图
• 冲击韧性的应用:经验数据,参考价值 举例: 调质处理的45#钢Ak=78J/cm2,而球墨铸铁 Ak=15J/cm2。单纯从数值上看,球墨铸铁 冲击韧性值远小于45#钢。然而它们都具有 良好的韧性,都可以作为活塞连杆材料使 用。 • AK值不能象屈服强度那样作用强度设计指 标,具有“不可设计性”。只能作为经验 数据使用。
2、加载速率 加载速率↑,脆性↑,韧脆转变温度Tk ↑; 3、试样尺寸和形状 试样增厚,Tk↑(表面上的拉压应力最大); 带缺口/不带缺口时,脆性及Tk不同。
31
本章要点
• 了解缺口顶端的应力、应变状态,缺口试 样的拉伸断裂过程和缺口敏感性,缺口试 样冲击载荷作用下的断裂过程、冲击韧性 及其试验方法,材料的低温脆性机理及其 系列冲击试验等评定方法。
脆性材料 中等塑性 塑性材料
16
7.3 缺口试样在冲击载荷下的断裂
• 冲击载荷与静载荷的主要区别在于加载速度(幅度 和频率) • 应变率 ε =de/dt,e为真应变 静拉伸试验 ε =10-5~10-2 s-1 冲击试验 ε =102~104 s-1 爆炸冲击 ε =104~108 s-1 • 一般情况下 ε =10-4~10-2 s-1,可按静载荷处理。
金属力学性能 第7章 缺口试样的断裂及其抗力
1
本章内容
7.1 缺口顶端的应力应变特征 7.2 缺口试样在静拉伸时的断裂 7.3 缺口试样在冲击载荷下的断裂 7.4 低温脆性及其评定方法
2
7.1 缺口顶端的应力应变特征
• 缺口参数: hN:缺口内宽度 h0:缺口外宽度 ρ :顶端曲率半径 ω :张角 γ :深度
8
• 薄板(z向尺寸小)情况下的应力分布和应变分布 σy σx σz=0 σ1 σ2 σ3 按照第3强度理论,
1 1 ( 1 3 ) s s 2 2 1 3 s 对薄板情况, 1 1 ( y z ) s 2 2 y z s
γ hN ρ ω
h0
3
缺口处应力分布
• 应力集中:缺口处材 料承载面积减小,缺 口处材料承受应力高 于整体材料;
• 这种缺口处突变,应 力承载面突然减少, 造成缺口处应力集中 • 应力集中系数
max kt m
4
• 缺口处三向应力
oa, ab, bc三块材料,
x= y=
所以
y
13
7.2 缺口试样在静拉伸时的断裂
PN 缺口试样的抗拉强度 bN= FN 其中PN为缺口试样断裂时的载荷, FN为缺口面积
bN 缺口敏感度q c= b
其中 b为光滑试样抗拉强度
检测材料缺口敏感性!
14
圆柱缺口试样断裂过程
• 脆性材料(a):最大应力位于缺口面上,裂纹在缺口一侧产生; 产生应力集中,裂纹快速通过缺口向另一侧扩展; • 中等塑性材料(b):最大应力位于缺口面内一定范围内,且此位 置与缺口面之间的材料发生了塑性变形;裂纹在该最大应力处产生, 向外侧缺口面处扩展(以微孔 聚集型方式向外侧扩展); 同时向内扩展(快速扩展); 最终中心形成最后断裂区。 此时缺口强度可能高于光滑 试样抗拉强度,也可能低于 光滑试样(取决于材料的 塑性大小)。
17
• 冲击载荷作用下,材料变脆
σ 3 2 A 6 5 4 σs
σb
1
Tc dε/dt
18
• 冲击失效的特点 (1)与静载荷下相同,弹性变形、塑性变形、断裂。 (2)吸收的冲击能测不准。 时间短;机件;与机件联接物体的刚度。 通常假定冲击能全部转换成机件内的弹性能, 再按能量守恒法计算。 (3)材料的弹性行为及弹性模量对应变率无影响。 弹性变形的速度4982 m/s(>声速), 普通摆锤冲击试验的绝对变形速度5~5.5 m/s。
判断标准: 冲击试验值 断口的形貌 50%纤维状断口
缺口试样
光滑试样
韧脆转变温度示意图
28
•影响冲击韧性和韧脆转变温度的因素 1)晶体学特性
晶体结构: f.c.c不存在低温脆性。 b.c.c和某些h.c.p的低温脆性严重,如Sn 位错: 位错宽度大,不显示低温脆性。 层错能↑,韧性↑。 形成柯氏气团,韧性↓。
纤维区
脆性材料
中等塑性
塑性材料
15
• 良好塑性材料(c):材料从缺口面开始向内,发生完全屈服,应力 最大点位于缺口中心;此时与光滑试样颈缩后的样品类似,裂纹起源 于样品中心,然后以微孔生成、聚集的方式向外扩展,最终形成杯锥 状断口 • 这种情况下缺口的存在 对断裂的影响不大。因此 塑性良好的材料缺口敏感性 低! • 由于缺口顶端的三向应力 状态,引起抗拉强度增大, 即σbN>σb • 这种由缺口引起的屈服 强度增大现象称为几何强化, 纤维区 但它不能作为强化手段使用
平面应变状态塑性区应力分布
10
• 平面应力/应变条件下屈服条件的讨论: 1. 平面应力条件下,应力达到σs就会屈服 2. 平面应变条件下,应力达到σx+σz才会 屈服,把此应力称为“有效屈服强度”。 此时材料屈服强度提高。如果此有效屈 服强度大于材料的断裂强度,材料不会 发生塑性变形就产生断裂,材料变脆。
26
7.4 低温脆性及韧脆转变温度
•低温脆性现象
在低温下,一些材料的脆性急剧增加。 对压力容器、桥梁、汽车、船舶的影响较 大。 低温脆性实质为温度下降,屈服强度急剧 增加。 F.C.C金属,一般不显示低温脆性。如低 碳钢为体心立方金属,有低温脆性;而奥氏 体钢为面心立方金属,无低温脆性。 27
•韧脆转变温度
载 荷 Pmax PF PGY PD 位移
22
• 载荷达到PF后,裂纹 迅速以解理断裂方式 快速扩展,在材料中 形成“放射形结晶状 区”;这时材料承载 面积迅速减小,载荷 也迅速降低到PD。 • 载荷达到PD后,裂 纹扩展到样品边缘, 产生平面应力状态, 形成剪切唇区。
载 荷
Pmax PF PGY PD 位移
33
6
• σx和σy存在情况下, σz的分布 1. 如果z向尺寸很小,z向的金属可以自由变 形, σz=0,此时仅有x和y两个方向的应 力,为平面应力状态
7
2. 如果z向尺寸很大,z向中心部位材料在z 向的变形受到约束很大,此时z向的应变 等于零,即εz=0,此时仅在x和y两个方 向产生应变,成为 平面应变状态。 按照虎克定律, εz=[σz-μ(σy +σx)]= 0 所以σz=μ(σy +σx)
19
•影响冲击性能的微观因素 (1)位错的运动速率↑,滑移临界切应力↑, 材料的冲击韧性↑
(2)同时开动的位错源增加 屈服强度提高得较多
(3)内部的塑性变形均匀性
20
冲击试验
• 试样: 夏氏;梅氏 • 摆锤5、10、15、30kg,试样尺寸 55×10×10mm,试样跨距40mm;无 缺口, • 有缺口(U;V)记为Ak,Aku,AKV。 • 铸铁(QT、白口铁),跨距70mm, 110×20×20mm,无缺口。
E
yoa yab ybc yoa yab ybc
上述应变差使oa, ab, bc之间有分离趋势, 材料要保持连续性必须产生x方向的拉应力
5ห้องสมุดไป่ตู้
• σx的分布 1. 在缺口表面,没有 材料约束,因此σx=0 2. 远离缺口表面区域, 材料内的应力分布均匀, 不产生x向应力,此时σx=0 3. 在它们之间, σx先 增大后减小,有一个峰值
11
3. 缺口是导致材料变脆的因素之一(其 余因素还有:低温;粗大晶粒;高应 变速率) 4. 塑性变形可削平缺口尖端应力,降低 材料脆性断裂倾向 5. 脆性材料由于裂纹尖端难以产生塑性 变形,容易产生早期断裂。因此脆性 材料对缺口更加敏感。
12
• 全面屈服时缺口 构件截面上的应 力分布 • 应力最高点位于 缺口中心,如同 低碳钢颈缩后的 应力分布 • 低碳钢拉伸过程
32
本章思考题
1)解释下面名词:缺口效应;应力集中系数;缺口敏感性;低温脆 性;韧脆转变温度 2)说明平面应力和平面应变条件下,缺口处的应力、应变分布特点。 3)说明低温脆性的物理本质及其影响因素。 4)举出三种提高金属材料韧性的途径 5)如何理解“缺口强化”现象? 6)说明下列力学性能指标的意义:qc,Ak 7)缺口对材料的拉伸性能有什么影响? 8)说明低温脆性的影响因素。 9)现需要检测下列材料的韧脆转变温度,哪些材料需要开缺口? W18Cr4V, Cr12MoV, 3Cr2W8V, 40CrNiMo, 30CrMnSi, 铸铁 10)说明退火低碳钢圆柱缺口拉伸试样拉伸时颈缩后应力状态改变的 原理,并说明裂纹形成和扩展过程,以及断口特征 11)结合缺口试样冲击过程中裂纹形成和萌生过程,说明缺口载荷~ 位移曲线与断口特征之间的对应关系. 12)液氮罐为什么采用奥氏体钢制造,而不能采用低碳钢制造? 13) 为什么冲击韧性不具有可设计性?
r
σs σy
y s
这是满足屈服的条件
平面应力状态塑性区的应力分 布
9
• 厚板情况下的应力分布和应变分布 σy σz σx σ1 σ2 σ3 屈服的条件
1 1 ( y x ) s 2 2 y x s
σs
σy σz σx r
y x s
这是满足屈服的条件
21
冲击断裂过程
• PGY之前,弹性变形 • PGY后,塑性变形;载荷 增大到Pmax,塑性变形 区逐渐扩展到整个缺口面 (塑性区为图中红色虚线 和缺口面之间面积); • 在Pmax附近,应力最大 点位于红色虚线上;因此 在此处产生裂纹;随后裂 纹向前和向后同时扩展; 扩展机制是微孔聚集型, 形成图中“脚跟形纤维状 区”;此过程中材料承载 面积减小,载荷逐渐下降 到PF。