SPC_X-R控制图讲义[一类资料]
合集下载
(SPC)X-R管制图

注:测量2个点 周一(日期: )
白班
Байду номын сангаас
夜班
1(首检)
周二(日期: )
白班
夜班
周三(日期: )
白班
夜班
周四(日期: )
白班
夜班
周五(日期: )
白班
夜班
周六(日期: )
白班
夜班
周日(日期: )
白班
夜班
2(11:00)
3(13:00)
4(15:00)
5(17:00)
检验员签名
车间QE确认
填写规范:所有产品的关键尺寸按规定的时间点测量尺寸,1pcs产品测量,需记录Min与Max,Min、Max与极差值(Max减Min的值)描点在图表中。当超过极限公差、连续7点全在中心 线之上或之下、连续7点上升或下降时,IPQC需要及时反馈领班并检查调整同时记录4M变更,调整后连续生产10件以上进行验证有效性,同时汇报到质量主管,进行不合格评审。 备注:连续7点全在中心线之上或之下、连续7点上升或下降时,是指Min与Max同时处中心线之上或之下、Min与Max同时上升或下降。
产品名称
每 班 次 抽 检 取 样 X-bar
模号
产品图号
技术要求
¢30
+0.021 +0
控制上限
¢30.021
控制下 限
¢30
极差
0.021
¢30.021 ¢30.018 ¢30.015 ¢30.012 ¢30.009 ¢30.006 ¢30.003 ¢30.000
当 班 取 样 R图
0.020 0.015 0.01 0.00 0.000
SPC模版之X-R管制图暨直方图分析

= =
- 3σ
PPK= PP = Ca = CPK= CP = Grade =
原因追查:
P1/2
制程能力分析
#VALUE!
#VALUE!
#VALUE!
#VALUE!
#VALUE!
#VALUE!
#VALUE!
#VALUE!
#VALUE!
#VALUE!
其它
140
制 程 能 力 分 析 (Capabilities)
总组数
7
抽样方法 检测日期
合 计
期 号
X1 X2 X3 X4 X5 X6 0.00 0.00 0.00 0.00 0.00 0.00 0.00 0.00 0.00 0.00 0.00 0.00 0.00 0.00 0.00 0.00 0.00 0.00 0.00 0.00 0.00 0.00 0.00 0.00 0.00 0.00 0.00 0.00 0.00 0.00 0.00 1 2 3 4 5 6 7 8 9 10 11 12 13 14 15 16 17 18 19 20 21 22 23 24 25 26 27 28 29 30 31
0.000
0.000
0.000
0.000
0.000
0.000
0.000
0.000
0.000
0.000
0.000
0.000
0.000
0.000
0.000
0.000
0.000
0.000
0.000
0.000
0.000
0.000
0.000
0.000
0.000
0.000
0.000
0.000
SPC X-R图 讲义
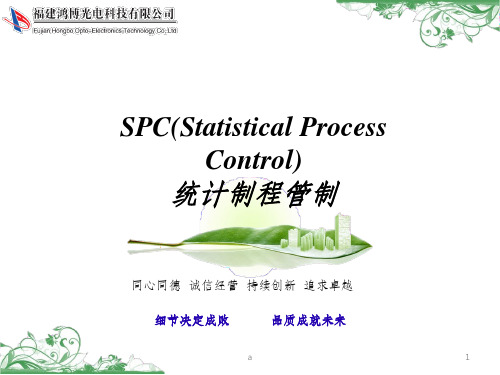
a
9
持续改进及统计过程控制概述
B 变差的普通及特殊原因
特殊原因:是指造成不是始终作用于过程的变差的原因,即当它们 出现时将造成(整个)过程的分布改变。只用特殊原因 被查出且采取措施,否则它们将继续不可预测的影响过程 的输出。 (通常也叫可查明原因)
目标值线
预测
时间
范围 如果存在变差的特殊原因,随着时间的推移,过程的输出不稳定。
A 制程控制系统 B 变差的普通及特殊原因 C 局部措施和对系统采取措施 D 过程控制和过程能力 E 过程改进循环及过程控制 F 控制图
a
2
SPC 产生
工业革命以后, 随着生产力的进一步发展,大规模生 产的形成,如何控制大批量产品质量成为一个突出问题, 单纯依靠事后检验的质量控制方法已不能适应当时经济 发展的要求,必须改进质量管理方式。于是,英、美等 国开始着手研究用统计方法代替事后检验的质量控制方 法。
a
10
持续改进及统计过程控制概述
C 局部措施和对系统采取措施
•局部措施 •通常用来消除变差的特殊原因 •通常由与过程直接相关的人员实施 •通常可纠正大约15%的过程问题
•对系统采取措施 •通常用来消除变差的普通原因 •几乎总是要求管理措施,以便纠正 •大约可纠正85%的过程问题
a
11
持续改进及统计过程控制概述
3、分析及改进 确定普通原因变差的大小并采取减小它的措施
重复这三个阶段从而不断改进过程
a
14
管制图的类型
a
15
管制图的选择方法
确定要制定控制 图的特性
是计量型数 据吗?
是
性质上是否是均匀或 不能按子组取样—例 如:化学槽液、批量 油漆等?
X-R控制图操作及应用课件
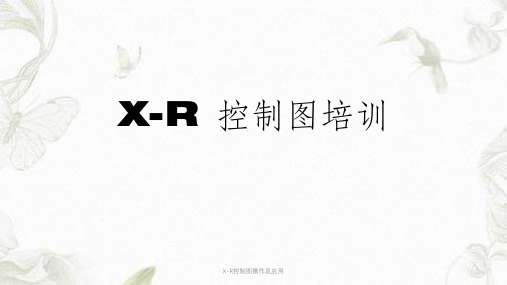
X-R 控制图培训
X-R控制图操作及应用
• 统计过程控制(SPC),主要应用于对过程变量的控制,它
统 计 过
的基本控制原理为3σ原则,即平均值± 3σ作为过程控制 的上下限,它是由WALTERA博士在1924年提出
程 • 其作用为:
控
制 • 1、从数据到图形应用统计技术可以反馈生产或服务过程
的 性质变化的信息。
数
据.
X-R控制图操作及应用
4 计算每个子组的均值(X)和极差(R)
•
X1+X2+......+Xn
X = —————————————
n
R=X最大值-X最小值
式中:X1、X2......Xn为子组内的每 个测量值,n为子组样本容量。X-R控制图操作及用5 选择控制图的刻度
• X图:坐标上的刻度值的最大与最小之差应至 少为子组均值X的最大与最小值差的2倍。
以子组序号为横坐标值,描出X图和R 图中的相应的点, 注意,在控制界内的点打记,在控制图界外的作⊙记, 并连成点链。
X-R控制图操作及应用
X控制图 R控制图
X-R控制图示
UCL X LCL
UCL R
X-R控制图操作及应用
7 X-R控制图分析
• (1) 分析均值极差图上的数据点 • A) 点在控制界线外;一个或多个点超出控制限是该点处于失控状
态的主要证明依据。因为只存在普通原因引起变差的情况下超出控 制限的点会很少,我们便假设超出的是由于特殊原因(如工装和设 备异常突发变化等)造成的,给任何超出控制限的点作上标识,以 便根据特殊原因实际开始的时间进行调查,采取纠正措施。(但连 续35点允许一点、连续100点有二点逸出控制界外,可暂不采取纠正 措施)
寸20+0。2-0。1
X-R控制图操作及应用
• 统计过程控制(SPC),主要应用于对过程变量的控制,它
统 计 过
的基本控制原理为3σ原则,即平均值± 3σ作为过程控制 的上下限,它是由WALTERA博士在1924年提出
程 • 其作用为:
控
制 • 1、从数据到图形应用统计技术可以反馈生产或服务过程
的 性质变化的信息。
数
据.
X-R控制图操作及应用
4 计算每个子组的均值(X)和极差(R)
•
X1+X2+......+Xn
X = —————————————
n
R=X最大值-X最小值
式中:X1、X2......Xn为子组内的每 个测量值,n为子组样本容量。X-R控制图操作及用5 选择控制图的刻度
• X图:坐标上的刻度值的最大与最小之差应至 少为子组均值X的最大与最小值差的2倍。
以子组序号为横坐标值,描出X图和R 图中的相应的点, 注意,在控制界内的点打记,在控制图界外的作⊙记, 并连成点链。
X-R控制图操作及应用
X控制图 R控制图
X-R控制图示
UCL X LCL
UCL R
X-R控制图操作及应用
7 X-R控制图分析
• (1) 分析均值极差图上的数据点 • A) 点在控制界线外;一个或多个点超出控制限是该点处于失控状
态的主要证明依据。因为只存在普通原因引起变差的情况下超出控 制限的点会很少,我们便假设超出的是由于特殊原因(如工装和设 备异常突发变化等)造成的,给任何超出控制限的点作上标识,以 便根据特殊原因实际开始的时间进行调查,采取纠正措施。(但连 续35点允许一点、连续100点有二点逸出控制界外,可暂不采取纠正 措施)
寸20+0。2-0。1
SPC R图 讲义
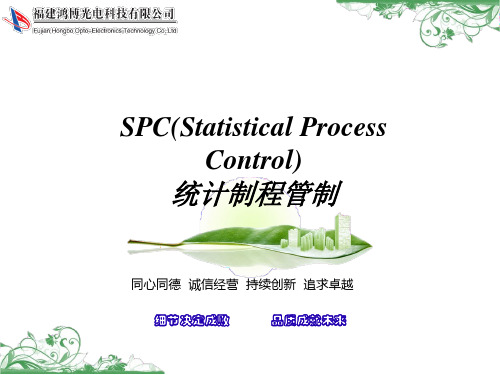
范围
形状 或组合
持续改进及统计过程控制概述
B 变差的普通及特殊原因
普通原因:是指过程在受控的状态下,出现的具有稳定的且可重复的 分布过程的变差的原因。普通原因表现为一个稳系统的偶 然原因。只有过程变差的普通原因存在且不改变时,过程 的输出才可以预测。 目标值线
预测
范围
时间
如果仅存在变差的普通原因,目标值线随着时间的推移, 过程的输出形成一个稳定的分布并可预测。
人员 设备 环境
材料
方法
12 34 56
计量型数据管制图(X-R图)
测量方法必须保证始终产生准确和精密的结果
不精密
不准确 ••••••••
精密
••••••
准确
••••••••••
•••••
计量型数据管制图(X-R图)
1、使用控制图的准备
1)建立适合于实施的环境 a、排除阻碍人员公正的因素 b、提供相应的资源 c、管理者支持
a-2 测量系统的改变(如新的检验人或新的量具); b 低于平均极差的链或下降链说明存在下列情况之一或全部:
b-1 输出值的分布宽度减小,好状态; b-2 测量系统的改好; 注1:当子组数(n)变得更小(5或更小)时,出现低于 R 的链的可能性增加,则8点或更多点组 成的链才能表明过程变差减小。 注2:标注这些使人们作出决定的点,并从该点做一条参考线延伸到链的开始点,分析时应考虑开 始出现变化趋势或变化的时间。
再发生。
b 应及时分析问题,例如:出现一个超出控制限的点就立即开始分析过程原因。
计量型数据管制图(X-R图)
4、过程控制分析
4-2 分析均值图上的数据点
4-2-1 超出控制限的点 a 一点超出任一控制限通常表明存在下列情况之一或更多:
SPC讲座一(X-R管制图)

91 90.4 91.4 91.6 91.2 91.2 90.4 90.8 92.4 90.8 91.2 90.6 90.6 89.6 91.2 90.8
7
5
4
7
4
8
5
7
5
6
4
5
7
4
5
4
93
93 93
89
89
89 89
93
90
91 93
90
87
88 92
89
91
90 89
91
450 451 456 452
用途
代表
• 用作樣本數平均值轉變的製圖 • 全距和標準差控制圖是控制數據的
散佈程度 • 用作個別樣據轉變的製圖 • 全距控制圖是控制數據的散佈程度
•用作每一樣本組不良品比率的製圖 •樣本數可以改變 • 用作每一樣本組不良品數目的製圖 • 樣本數是固定的
• 用作缺點數目的製圖,而每次查驗 的面積是相同的
89
90
87
91
93
93
88
93
90
86
93
95
92
95
94
87
92
93
90
92
89
89
94
90
93
93
89
92
88
89
93
93
93
89
93
89
93
92
93
88
92
93
91
87
89
88
89
93
89
93
89
88
88
89
SPC教材(X-R管制图)

例题:用X-R管制图来控制AGP GAP,尺寸单位为mm,请 利用下列数据资料,计算其管制界限并绘图.
制品名称:AGP 品质特性:GAP 测定单位:mm 制造场所:A线
GROUP X1 X2 X3 X4 X5 X R Min Max 1 2 3 4 5 6 7 8 9 10 11
机器号码:RK006 操 作 者:55230 测 定 者:58664 抽样期间:03/10/99~03/12/99
管制图的种类(性质分类)
2.计数值管制图(Control Charts For Attributes) a.不良率管制图 ( P Chart ) b.不良数管制图 ( Pn Chart or d Chart ) c.缺点数管制图 ( C Chart ) d.单位缺点数管制图 ( U Chart )
7.将所求出之各X值及R值点入管制图上并将相邻两点用 直线连接 8.制程状态检讨 9.记入其它注意事项
AGP CONN. GAP CONTROL CHART
0.80
0.70
X-管制图
0.60
0.50
1 2 3 4 5 6 7 8 9 10 11 12 13 14 15 16 17 18 19 20
(g) 5点中有4点在B区或B区以外者
(h) 有8点在中心线之两侧,但C区并无点子者
(i) 连续14点交互著一升一降者
(j) 连续15点在中心线上下两侧之C区者
(k) 有1点在A区以外者
�
中心线 ( CLx ) = X = 0.66 管制上限 ( UCLx ) = X+A2R = 0.66+0.577 ╳ 0.08 = 0.70 管制下限 ( LCLx ) = X-A2R = 0.66-0.577 ╳ 0.08 = 0.61
工厂生产及质量培训——SPC之X-R管制图实施细则(精)

是否計 是數據
NO
YES
NO
用 U-chart
其特 性是否可 引 用 subgroup sampling
np
or
p
chart
NO ?
YES
之平均值 是否容易 計算 ? YES
NO
用 Median chart
YES ?
NO subgroup size是 否 9或 以 上 YES 計算 Subgroup之 標準差是否 容易? YES
34.76 34.77 34.77 34.77 34.74 34.73 34.73 34.71 34.70 34.72 34.73 34.74 34.74 34.74 34.72 34.75 34.77 34.78 34.73 34.74 34.76 34.76 34.76 34.72 34.76 34.72 34.75 34.75 34.73 34.73 34.75 0.04 0.02 0.02 0.01 0.02 0.03 0.02 0.02 0.03 0.02 0.03 0.03 0.03 0.02 0.02 0.02 0.03 0.03 0.03 0.03 0.04 0.02 0.04 0.02 0.06 0.04 0.05 0.04 0.07 0.06 0.06
C.中位值與全距管制圖(X-R Chart). D.單個數據-移動全距管制圖(X-Rm Chart). E.最大值與最小值管制圖(L-S Chart).
2.計數據管制圖: 管制圖所依據的數據均屬於以單位計數者.(如缺點數、
不良 數等). A.不良率管制圖(P- Chart). C.缺點數管制圖(C- Chart). B.不良數管制圖(Pn- Chart). D.單位缺點數管制圖(U- Chart).
《SPCXR图讲义》课件

3
分析控制图
4
通过分析SPCXR图的趋势、规律和异常, 识别问题,制定改进措施。
数据收集
收集生产和服务过程的数据,包括样本 数据和时间序列数据。
绘制控制图
使用统计软件或图表工具绘制SPCXR图, 将数据点标记在图表中。
SPCXR图的分析方法
正常分布曲线
正常分布曲线可以通过标准差 和方差来描述数据的变异程度。
SPCXR图具有统计性、实时性 和图表可视化的特点。
组成元素
SPCXR图包括上下限线、中心 线、数据点、区域及异常标 记等元素。
图例
SPCXR图的图例用于说明不同 标记的含义,如正常、过程 变异和异常数据。
SPCXR图的制作方法
1
确定测量系统的效果和偏差
2
评估测量系统的准确性和稳定性,确定
测量误差。
过程能力指数
过程能力指数用于衡量生产和 服务过程的稳定性和达到要求 的能力。
贝塔分布曲线
贝塔分布曲线通过贝可图描述 生产和服务过程的ห้องสมุดไป่ตู้向和异常 情况。
SPCXR图的使用场景
生产流程管理
通过SPCXR图可以实时监控生产过程,预防问题的发生,提高生产效率。
服务质量控制
SPCXR图可应用于监控服务过程,提升服务质量,满足客户需求。
模型分析
通过分析SPCXR图,可以挖掘生产和服务过程中存在的潜在问题,优化模型。
总结
SPCXR图的优势
SPCXR图可以帮助实时监控和改 进生产和服务过程,提高质量 和效率。
SPCXR图的局限性
SPCXR图需要准确收集数据,且 对表格的更新和维护要求高。
SPCXR图的应用前景
随着大数据和智能化技术的发 展,SPCXR图在工业和服务领域 的应用前景广阔。
SPC-X-R图-讲义(1)
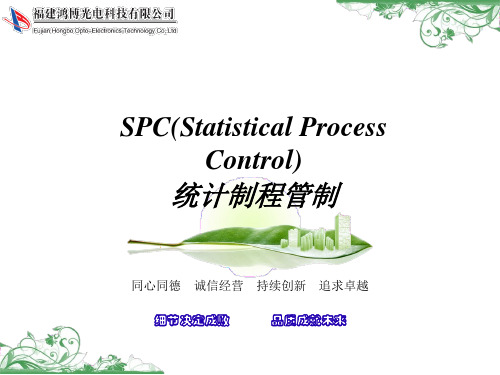
3)确定待控制的特性,应考虑到: 顾客的需求 当前及潜在的问题区域 特性间的相互关系
4)确定测量系统 a、规定检测的人员、环境、方法、数量、频率、设备或量具。 b、确保检测设备或量具本身的准确性和精密性。
5)使不必要的变差最小 确保过程按预定的方式运行 确保输入的材料符合要求 恒定的控制设定值
注:应在过程记录表上记录所有的相关事件,如:刀具更新,新的材料批次等,有利于下一 步的过程分析。
R
LCL
4、过程控制分析
4-1 分析极差图上的数据点
4-1-2 链 有下列现象之表明过程已改变或出现某种趋势:
• 连续 7点在平均值一侧; • 连续7点连续上升或下降; a 高于平均极差的链或上升链说明存在下列情况之一或全部:
a-1 输出值的分布宽度增加,原因可能是无规律的(例如:设备工作不正常或固定松动) 或是由于过程中的某要素变化(如使用新的不一致的原材料),这些问题都是常见的 问题,需要纠正;
3、分析及改进 确定普通原因变差的大小并采取减小它的措施
重复这三个阶段从而不断改进过程
X-R 均值和极差图
计 X-δ 均值和标准差图 量
型 数
X -R 中位值极差图
据
X-MR 单值移动极差图
P chart 不良率管制 图
nP chart 不良数管制 计数 图 型数 C chart 缺点数管制 据图
关系等。 b 一般情况,各点与R 的距离:大约2/3的描点应落在控制限的中间1/3的区域内,大约1/3的点落在
其外的2/3的区域。 c 如果显著多余2/3以上的描点落在离 R 很近之处(对于25子组,如果超过90%的点落在控制限的1/3
区域),则应对下列情况的一种或更多进行调查: c-1 控制限或描点已计算错描错 。 c-2 过程或取样方法被分层,每个子组系统化包含了从两个或多个具有完全不同的
4)确定测量系统 a、规定检测的人员、环境、方法、数量、频率、设备或量具。 b、确保检测设备或量具本身的准确性和精密性。
5)使不必要的变差最小 确保过程按预定的方式运行 确保输入的材料符合要求 恒定的控制设定值
注:应在过程记录表上记录所有的相关事件,如:刀具更新,新的材料批次等,有利于下一 步的过程分析。
R
LCL
4、过程控制分析
4-1 分析极差图上的数据点
4-1-2 链 有下列现象之表明过程已改变或出现某种趋势:
• 连续 7点在平均值一侧; • 连续7点连续上升或下降; a 高于平均极差的链或上升链说明存在下列情况之一或全部:
a-1 输出值的分布宽度增加,原因可能是无规律的(例如:设备工作不正常或固定松动) 或是由于过程中的某要素变化(如使用新的不一致的原材料),这些问题都是常见的 问题,需要纠正;
3、分析及改进 确定普通原因变差的大小并采取减小它的措施
重复这三个阶段从而不断改进过程
X-R 均值和极差图
计 X-δ 均值和标准差图 量
型 数
X -R 中位值极差图
据
X-MR 单值移动极差图
P chart 不良率管制 图
nP chart 不良数管制 计数 图 型数 C chart 缺点数管制 据图
关系等。 b 一般情况,各点与R 的距离:大约2/3的描点应落在控制限的中间1/3的区域内,大约1/3的点落在
其外的2/3的区域。 c 如果显著多余2/3以上的描点落在离 R 很近之处(对于25子组,如果超过90%的点落在控制限的1/3
区域),则应对下列情况的一种或更多进行调查: c-1 控制限或描点已计算错描错 。 c-2 过程或取样方法被分层,每个子组系统化包含了从两个或多个具有完全不同的
SPC-X-R控制图讲义
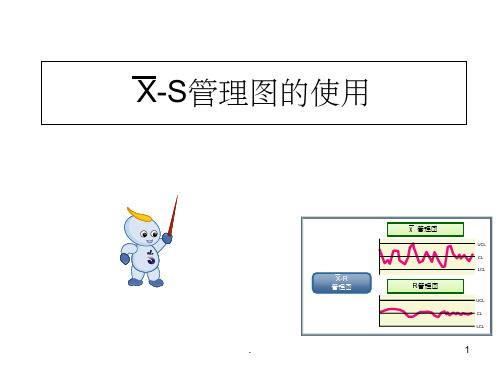
.
2
二、X-S管理图的用途
1、用于分析
x
2、用于控制
控制范围 中线
控制范围
计算控制范围
用控制范围进行控制
.
3
三、X-bar管理图的原理
USL
USL(规格上限)
集合
σ μ
LSL
LSL(规格下限)
样本
σ n
UCL=X-bar-bar+3 δ=X-bar-bar+3*stdev(X-barn)
特殊原因
UCL
上限
99.73%
自然公差
CL
中线
特殊原因
LCL
下限
过程如果处在安定的状态下,测定值超 过±3σ的安定变动范围的情况极少
.
4
Xbar管理图的UCL、LCL的计算
UCL=X-bar-bar+3 δ=X-bar-bar+3*stdev(X-barn) CL=X-bar-bar
LCL=X-bar-bar-3 δ=X-bar-bar-3*stdev(X-barn) δ=stdev(X-barn)
.
7
过程控制
特殊原因
由特殊原因 产生偏差的状态
控制某个过程
确保没有特殊原因存在,只是取决 于过程实力
.
一般原因
没有特殊原因产 生的偏差,而只 是取决于过程实 力的状态
8
六、X-R管理图异常情况判定
Control chart's alarms
.
9
管理状态和受控状态 : 点散布在中心线的附近,并且不脱离管理界限下的状态
1、使用X-R管理图进行过程控制的数值必须是计量值; 2、用X-R管理图进行控制的过程必须处于稳定并受控的状态; 3、初次收集的数据需要进行变差分析,通过计算求出CPk值, 以CPk值来判定过程的稳定(实力)情况;如果CPk≥1.33以上, 可以认为过程是稳定的,根据数据计算出的X,R,CL,UCL,LCL 作为过程控制的界限; 4、当过程发生变化时,例如4M(人、机、料、法)变更,使过 程实力发生变化,此时需要重新收集数据并计算出平均值和控制 界限,作为新的控制界限。 5、根据收集特定过程计算出的控制界限,只使用于该特定过程。
现场SPC X-R控制图

数据重要趋势 点数最大长度 递增趋势 递 增 链 数 点数最大长度 递减趋势 19.093 递 减 链 数 0.000 超出控制线点数
X图 4 8 6 7 3
均值(X-图)
19.17 19.14 19.11 19.08 19.05 19.02 18.99 18.96 18.93
1 2 3
均值
Data Values UCLx LCLx Average X
11 5
14 3
1
0
0
4
5
6
7
8
9
10
11
12
13 极差值
14
15
16
17
18
19
20
21
22
23
24
25
正态分布曲线
数据区间
控制图表现: 过程能力分析:
注意!控制图中有点子出界,或出现7点链条情况!!!
过程能力充足! 11-19
2
19.1 19.11 19.12 19.12 19.12 19.114 0.020
4
5
6
7
8
9
10
11
12
13 数据点
14
15
16
17
18
19
20
21
22
23
24
25
极差(R-图)
频数
60
正态分布
0.240 0.200 0.160
极差
50 40 30 20 11 10 0 0 26
49
0.120 0.080 0.040 0.000
1 2 3
R Value UCLr LCLr Average R
SPC_x-r管制图与解析
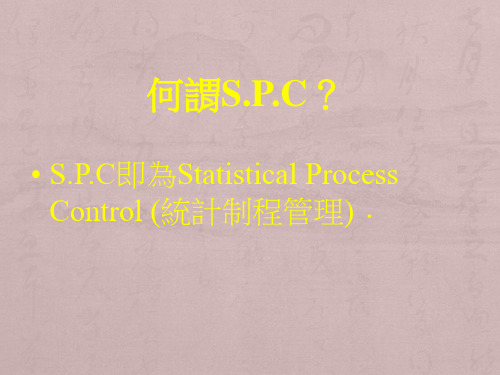
正確度、精密度
目標值
正確度 精密度
***********
**** ******* ***
優
劣
優
優
劣
劣
劣
優
X-R管制圖製作方法
• 預備數据的調查 先搜集某一期間的數据作為預備數据
步驟1:搜集數据----搜集100個以上的數据,依 測定時間順序,或群体順序排列.
(1)這些數据是最近的數据,并且在技術上可 認為今后的制程不會有多大變化.
管制界限上時,亦視同超出界外的點.
END
步驟3: 記入數据表----把數据記入如表2.1.1 的數据表裡.
步驟4:計算平均值X(4捨5入后,比測定值多求1
位數),求各組的平均值X.
X1+X2+······+Xn
X=
(n:為樣本大小)
n 例如表2.1.1的第1組的平均值為:
48+49+48+50+51
X=
=49.2
5
步驟5:計算全距R 求每組的全距R R=X (最大值) 一X (最小值)
R=
K
例如表2.1.1
3+4+7+6+4+······+8+6+3+4
R=
ቤተ መጻሕፍቲ ባይዱ
=4.7
25
步驟8:計算管制界限 (a) X管制圖
中心線CL=X 上管制界限 UCL=X+A2R 下管制界限 LCL=X–A2R (A2為系數,可由表查得) 例如表2.1.1 因n=5,故查表 得A2=0.577 CL=X=49.74 UCL=X+A2R=52.45 LCL=X-A2R=47.03
相关主题
- 1、下载文档前请自行甄别文档内容的完整性,平台不提供额外的编辑、内容补充、找答案等附加服务。
- 2、"仅部分预览"的文档,不可在线预览部分如存在完整性等问题,可反馈申请退款(可完整预览的文档不适用该条件!)。
- 3、如文档侵犯您的权益,请联系客服反馈,我们会尽快为您处理(人工客服工作时间:9:00-18:30)。
课件优选
2
二、X-S管理图的用途
1、用于分析
x
2、用范围进行控制
课件优选
3
三、X-bar管理图的原理
USL
USL(规格上限)
集合
σ
μ
样本
σ n
UCL=X-bar-bar+3 δ=X-bar-bar+3*stdev(X-barn)
特殊原因
UCL 上限
99.73% 自然公差
CL
中线
LSL
LSL(规格下限)
特殊原因
LCL
下限
过程如果处在安定的状态下,测定值超 过±3σ的安定变动范围的情况极少
课件优选
4
Xbar管理图的UCL、LCL的计算
UCL=X-bar-bar+3 δ=X-bar-bar+3*stdev(X-barn) CL=X-bar-bar
LCL=X-bar-bar-3 δ=X-bar-bar-3*stdev(X-barn) δ=stdev(X-barn)
课件优选
5
四、R管理图的原理
R
R管理图的UCL、LCL的计算
UCLR=R-bar+3 δR=R-bar+3*stdev(Rn) CL=R-bar LCLR=R-bar-3 δR=R-bar-3*stdev(Rn) δ=stdev(Rn)
备注:当LCLR为负数时,LCLR计零。
课件优选
UCL CL LCL
6
五、使用X-R管理图的前提条件
1、使用X-R管理图进行过程控制的数值必须是计量值; 2、用X-R管理图进行控制的过程必须处于稳定并受控的状态; 3、初次收集的数据需要进行变差分析,通过计算求出CPk值, 以CPk值来判定过程的稳定(实力)情况;如果CPk≥1.33以上, 可以认为过程是稳定的,根据数据计算出的X,R,CL,UCL,LCL 作为过程控制的界限; 4、当过程发生变化时,例如4M(人、机、料、法)变更,使过 程实力发生变化,此时需要重新收集数据并计算出平均值和控制 界限,作为新的控制界限。 5、根据收集特定过程计算出的控制界限,只使用于该特定过程。
课件优选
7
过程控制
特殊原因
由特殊原因 产生偏差的状态
控制某个过程
确保没有特殊原因存在,只是取决 于过程实力
课件优选
一般原因
没有特殊原因产 生的偏差,而只 是取决于过程实 力的状态
8
六、X-R管理图异常情况判定
Control chart's alarms
课件优选
9
管理状态和受控状态 : 点散布在中心线的附近,并且不脱离管理界限下的状态
X-S管理图的使用
课件优选
X-R 管理图
x 管理图
R管理图
UCL CL LCL
UCL CL LCL
1
一、基本概念
1、X:一组数据的算术平均值。 2、R:组内数据的标准差。 3、计数值:以数量为单位计算的数值;例如:
不良品数,缺点数等。 4、计量值:用测量仪器测试出来的数值,是连续分
布的数值;例如:长度,重量,扭力,粘接 力等。 5、CPk:工程能力指数,用来衡量工程的稳定性。
x
受控状态
控制范围 中线
控制范围
END
课件优选
10
七、预控制图(彩虹图)
课件优选
11
课件优选
12
课件优选
13
课件优选
14
七、P图(计数型图表)
课件优选
15
课件优选
16
课件优选
17
课件优选
18