全球采购供应商质量改进程序16步 共18页
@上汽通用五菱-供应商质量管理16步程序

初期生产次品遏制程序(GP—12) 初期生产次品遏制程序(GP—12)
定义: 供应商正式生产件审批程序控制计划的加强措施, 定义 供应商正式生产件审批程序控制计划的加强措施,初期生产次 品遏制计划( 品遏制计划(GP-12)与产品先期质量策划及控制计划参考手 ) 册中的投产前控制计划是一致的。 册中的投产前控制计划是一致的。 目的: 帮助供应商验证对其工序的控制, 目的 帮助供应商验证对其工序的控制,使质量问题能迅速在供应商 现场被发现和纠正,而不影响到客户的生产线。 现场被发现和纠正,而不影响到客户的生产线。 范围:本程序适用于所有需要通过正式生产件审批程序的零件, 范围:本程序适用于所有需要通过正式生产件审批程序的零件,包括 所有小批量供货,加上采购部门指定的数量。 所有小批量供货,加上采购部门指定的数量。此程序不只限项 目的开始。 目的开始。 程序:作为质量先期策划之组成部分,供应商将制定 程序:作为质量先期策划之组成部分,供应商将制定GP-12投产前控 投产前控 制计划, 控制计划是PPAP正式生产件审批程序的要求 制计划,GP-12控制计划是 控制计划是 正式生产件审批程序的要求 之一,在达到此阶段放行标准之前必须按该计划执行。 之一,在达到此阶段放行标准之前必须按该计划执行。
投产前会议
定义:与供应商进行交流以明确零件质量合格及持续改进的要求。 定义:与供应商进行交流以明确零件质量合格及持续改进的要求。 目的: 目的:保证所有质量要求在供应商及客户负责供应商的部门之间得到 确切的交流。 确切的交流。 范围:建议对所有需要进行PPAP的新部件或新材料行使本程序,依 的新部件或新材料行使本程序, 范围:建议对所有需要进行 的新部件或新材料行使本程序 照其风险程度之不同来确定先后。 照其风险程度之不同来确定先后。(这是先期质量策划的一个部 分) 程序: 程序:通过供应商与客户有关人员在产品开发小组会议上进行密切的 交流以对质量,生产能力和进度等要求进行研讨并取得认同。 交流以对质量,生产能力和进度等要求进行研讨并取得认同。
供应商质量改进十六步法
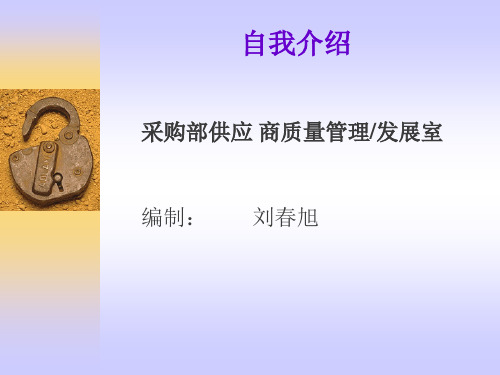
♂ 问题通报与解决
DEFINITION 定义:为促进解决已确认的供应商的质量问题而进行交流的程序。
PURPOSE 目的:对已确认的供货质量问题进行意见交换,文件记录.跟踪和 解决。 SCOPE 范围:适用于所有为通用汽车公司的工厂提供零部件,材料和总成的供 应商。 PROCESS 程序: 1.识别-如经现场人员核实,问题源于供应商不合格产品,立即通知供应商。 2.遏制-供应商必须在内24小时之内针对产品遏制及初步整改计划作出答复。 3.供应商必须判定问题的根源并在所不惜15天内就执行整改措施,彻底排除问 题根源的工作情况作出汇报。 4.供应商必须采取措施杜绝问题复发,事发现场必须核实这些措施的有效实施 情况,以完结问题通报与解决程序。
指出时,都有必要进行质量研讨。
PROCESS程序: 在研讨期间,着重于付诸实践地有效地解决问题,并采取持续改进的一系列措施。 记录现状,广泛提供各种改进意见,评估,试验,验证并记录改进结果。
♂供应商质量改进会
DEFINITION 定义:供应商和全球采购高级管理层会议(执行总监级)。
★ Pre production meeting投产前会议
★ APQP产品质量先期策划及控制计划 ★ Sourcing decision确定供应商 ★ PSA 潜在供应商评估 ★ PA 初级评估
Start of production开始生产
♂ Preliminary Assessment(PA) 初级评估
♂持续改进
DEFINITION 定义:GP-8规定供应商就有任来制定一套能持续改进的程序。
PURPOSE 目的:GP-8是概述了在通过正式生产件审批(PPAP)和初期生产 次品遏制(GP-12)程序之后,客户对供应商的持续改进的要求。 SCOPE 范围:该程序适用于所有生产零部件及材料的供应商,即使在客户没有 规定具体要求时依然适用。 PROCESS 程序:所有供应商必须监测其所有零件的质量工作情况并致力于持 续改进。持续改进程序目标在于减少生产加工的偏差和提高产品的质量。供应商 应着重于通过听取用户的意见和工序的反馈,以努力减少工序波动。
GM供应商质量改进16步过程方法培训

GM供应商质量改进16步过程方法培训主题:通用供应商质量改进的16步过程方法(GM16)16步过程方法是通用全球选择供应商的一种战略方法,包含质量策划、质量设计、质量治理与保持、连续改善等内容。
GM16包含所有现行的通用程序,用于治理供应商产品质量,购买满足设计寿命和使用寿命的零部件。
以上为通用的供应商质量改进的16步程序方法。
其中前面8步是产品投产前应该解决的咨询题,后面8步是产品在使用过程中显现的相关咨询题的解决措施。
第二步:供应商选择1,对象:WWP定点委员会举荐和评估的对象。
2,缘故:基于质量、服务、成本和技术方面的降低风险;3,文件出处:通用全球采购(2);4,定义:定点委员会举荐的对象;5,目的:判定在质量、服务和价格方面有竞争力的产品供应商;6,范畴:全球;7,过程:审核举荐对象;评估候选对象;批准/否定举荐对象;假如需要,批准正确的行动方案;签署定点文件。
第三步:前期产品质量策划与操纵(APQP)1, 对象:APQP是在质量、最优化生产和最大顾客中意度的一种17时期的设计过程;2,缘故:提供给供应商一种质量策划和完成的途径。
整合资源满足通用要求及降低成本。
确保项目进度,便于协商沟通。
3,文件出处:GM采购部。
4,备注:关于所有新的供应商,APQP必须。
相关文件见GM1927P相关表式。
5,含义:一种正式的有组织的方法用于定义和建立必要的过程来确保产品满足客户要求。
6,目的:该过程要求供应商建立和完成产品质量打算来:指导供应商满足客户需要;当必要的改变时促进早期识不;确保所有需要的步骤及时完成;便于沟通要求;以有竞争力的成本及时提供合乎质量要求的产品。
7,范畴:所有GM的供应商都要求完成所有新零件的APQP。
8,过程:策划和定义项目;产品设计与开发;流程设计与开发;产品与流程的确认;质量;产能;进度。
第五步:样件认可(GP-11)1,对象:GP-11是一种常用的样件或前样件的认可要求程序。
上汽通用供应商质量改进16步

样件审批或工装样品(OTS)认可(GP—11)
工装样品(OTS)认可 定义: 上汽通用五菱汽车股分有限公司规定的外购国产化零部件(工装 样品/OTS)审批程序。 目的: 测试由中国当地供应商提供的零部件是否符合原设计的工程要 求,非用于评审零部件的原设计。 范围:适用于所有提供在中国制造零部件的供应商。 程序:-样件定义1 样件定义2 -送样要求 -工装样品(OTS)认可程序 -工程样品(OTS)文件的提交
程序:通过供应商与客户有关人员在产品开发小组会议上进行密切的
交流以对质量,生产能力和进度等要求进行研讨并取得认同。
样件审批或工装样品(OTS)认可(GP—11)
样件审批 定义: 上汽通用五菱汽车股分有限公司规定的样件审批规程。 目的: 提供上汽通用五菱汽车股分有限公司统一的对样件及其附带文件的最低要 求,协助识别并纠正部件上的问题以减少部件差异,评估设计、制造和装 配可能产生的影响,加速“正式生产件审批”程序的执行。 范围: 适用于需提供新样件的所有供应商。 程序:-由客户提供对样件的检验清单 -供应商得到有关提供样件要求的通知 -供应商得到GP-11中提出的要求 -供应商提交样件和按客户要求等级提供文件 -供应商会得到提交样件审理结果的通知: ―批准用于样车制造 ―可用于样车制造 ―不可用于样车制造
OHT3-2
质量研讨会
定义:在供应商现场进行质量研讨,解决具体质量问题。 目的:尽快解决问题,使产品质量迅速提高,并建立一个具备控制和 持续改进质量的系统。
范围:可在供应商质量改进过程中任何时候进行。当某产品批量生产 不合格品PPM较高,或有反复PR/R,或受发货控制,或查访及 风险评估期间被特别指出时。
供应商质量管理16步程序共42页
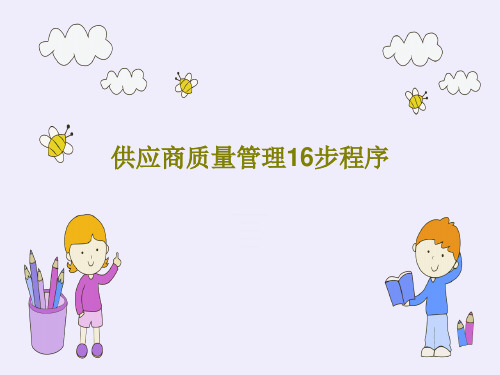
60、生活ቤተ መጻሕፍቲ ባይዱ道路一旦选定,就要勇敢地 走到底 ,决不 回头。 ——左
40、人类法律,事物有规律,这是不 容忽视 的。— —爱献 生
56、书不仅是生活,而且是现在、过 去和未 来文化 生活的 源泉。 ——库 法耶夫 57、生命不可能有两次,但许多人连一 次也不 善于度 过。— —吕凯 特 58、问渠哪得清如许,为有源头活水来 。—— 朱熹 59、我的努力求学没有得到别的好处, 只不过 是愈来 愈发觉 自己的 无知。 ——笛 卡儿
供应商质量管理16步程序
36、如果我们国家的法律中只有某种 神灵, 而不是 殚精竭 虑将神 灵揉进 宪法, 总体上 来说, 法律就 会更好 。—— 马克·吐 温 37、纲纪废弃之日,便是暴政兴起之 时。— —威·皮 物特
38、若是没有公众舆论的支持,法律 是丝毫 没有力 量的。 ——菲 力普斯 39、一个判例造出另一个判例,它们 迅速累 聚,进 而变成 法律。 ——朱 尼厄斯
供应商质量培训课程 -供应商质量管理16步程序
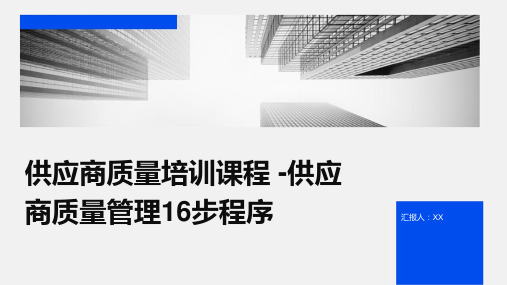
商质量管理16步程序
汇报人:XX
目录
• 引言 • 供应商选择与评估 • 供应商质量协议与合同 • 供应商过程监控 • 供应商质量改进 • 供应商审核与认证 • 供应商关系管理 • 总结与展望
01
引言
课程目的和背景
应对全球化采购挑战
随着全球化的发展,企业越来越多地 依赖外部供应商,供应商质量管理成 为确保产品质量和竞争优势的关键因 素。
04
供应商过程监控
过程监控的目的和内容
目的:确保供应商在生产过程中遵循质 量标准,及时发现并纠正潜在问题,以 确保最终产品符合质量要求。
跟踪供应商的质量绩效,包括产品合格 率、不良品率、客户投诉等。
评估供应商的质量管理体系,确保其有 效性和符合性。
内容
监控供应商的生产过程,包括原材料采 购、生产工艺、设备维护等。
产品。
降低质量成本
通过预防、鉴定和减少不合格 品,降低因质量问题引起的成 本增加,包括返工、退货、保 修等。
提升客户满意度
优质的产品有助于提高客户满 意度和忠诚度,进而促进业务 增长和市场份额提升。
强化供应链韧性
优质的供应商能够更好地应对 市场波动和不确定性,提高供
应链的稳定性和韧性。
02
供应商选择与评估
对企业的建议与启示
建立完善的供应商质量管理体系
企业应建立全面、系统的供应商质量管理体系,明确管理流程和责任 分工,确保供应商质量管理的有效实施。
加强供应商选择与评估
在选择供应商时,应注重其质量保障能力、技术实力、服务水平等方 面的评估,确保选择优质的供应商合作伙伴。
强化供应商培训与辅导
定期对供应商进行质量意识、技能等方面的培训与辅导,提高供应商 的整体素质和能力水平。
全球采购供应商质量改进程序通用16步APQP

全球采购供应商质量改进程序
--供应商质量改进16步
SDE Module 2010.04
全球采购供应商质量改进程序
GM192176(SSGteMps) -APQP
时间线
早 期 生 产 遏 制 (GP-12) 按 节 拍 生 产 (GP-9) 生 产 件 审 批 (PPAP) 样 件 批 准 (GP-11/PPQP)
2.提供与新零件相关的以前产品经验或技术信息的证据 ;
强调事项:
1.供应商以跨部门小组的形式确认RFQ和SQ SOR等文件中关于零件的所有要求,确保报价涵盖了所有顾客 要求。
2.供应商理解SQ SOR 和特定零件质量及过程SOR(如适用)并签字确认后应提交SGM。
SDE Module 2010.04
供应商管理层评审交付物,并提交SGM
阶段评审地点
原则上在供应商现场完成除第1次外的其他各阶段评审会议
强调事项:
1.如有指定分供方,则采购务必安排定点前(最晚应在启动会议时)SQ,供应商,分供方共同确认角色及职责(要求必须填写GM1927-23
2.
项目
启动会议的召开
GM 1-2次 (Buyer, SQE可能各一次)
1.产品关键方会议 2.技术评审 3.定点资质 4.供应商阶段评审 5.进度表/问题清单 6.质量体系基础 7.过程流程图 8.DFMEA
GM1927(SGM) -APQP
9.设计评审 10.工装模具及设备评审 11.量检具开发及批准 12.过程失效模式及后果分析 13.控制计划 14. GP-12早期生产遏制 15. PPAP 16.节拍生产(GP-9) 17.经验教训
SDE Module 2010.04
供货商质量改进16步程序

供货商质量改进16步程序第一步:收集供货商质量信息在质量改进的过程中,首先需要收集供货商的质量信息。
这包括供货商的公司背景、资质认证、质量管理体系等方面的信息。
这一步的目的是对供货商进行初步的筛选,确保其具备满足质量要求的基本条件。
第二步:制定供货商评估标准制定供货商评估标准是为了确保供货商的质量能够满足公司的需求。
评估标准应包括质量管理体系、产品质量、交货准时性等方面的要求。
通过评估标准的制定,可以有针对性地对供货商进行评估,筛选出优质的供货商。
第三步:评估供货商在评估供货商时,可以采用问卷调查、现场考察等方式获取供货商的质量信息。
根据评估标准对供货商进行评分,并将评估结果记录下来。
第四步:与供货商沟通根据供货商的评估结果,与其进行沟通,明确供货商的质量状况和改进要求。
通过与供货商的沟通,可以建立起双方的合作关系,共同努力改进供货商的质量。
第五步:制定改进计划针对供货商的质量问题,制定具体的改进计划。
改进计划应包括改进目标、改进措施、责任人等内容,以确保改进的有序进行。
第六步:与供货商共同制定改进方案与供货商共同制定改进方案是确保改进行动的有效性。
通过与供货商的合作,可以充分了解供货商的实际情况,制定出更切实可行的改进方案。
第七步:开展培训和指导为了帮助供货商改进质量,可以组织培训和指导活动。
培训内容可包括质量管理知识、操作规范等方面的内容,指导活动可包括现场指导、问题解答等。
第八步:实施改进措施根据制定的改进方案,开始实施改进措施。
改进措施可以包括流程改善、技术升级、设备更新等方面的内容。
通过改进措施的实施,可以提升供货商的质量水平。
第九步:监控改进效果对改进措施的效果进行监控,确保改进措施的有效性。
可以通过对产品质量进行检验、与供货商进行沟通等方式进行监控。
第十步:评估改进效果评估改进效果是为了确定改进措施的成效,并根据评估结果对供货商进行绩效评价。
评估改进效果的方法可以包括统计分析、问卷调查等。
供应商质量改进十六步
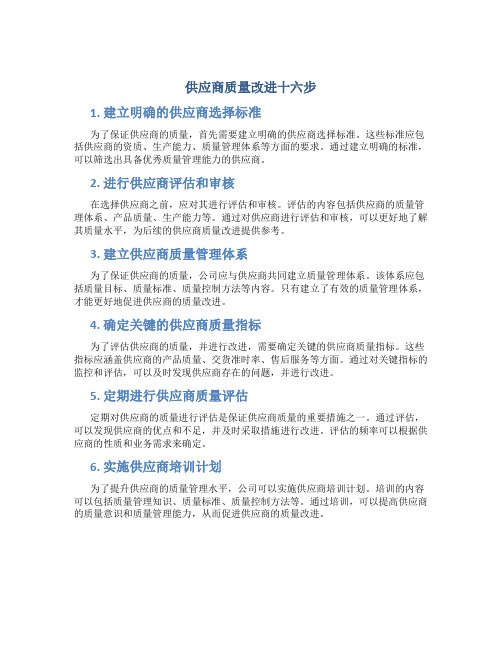
供应商质量改进十六步1. 建立明确的供应商选择标准为了保证供应商的质量,首先需要建立明确的供应商选择标准。
这些标准应包括供应商的资质、生产能力、质量管理体系等方面的要求。
通过建立明确的标准,可以筛选出具备优秀质量管理能力的供应商。
2. 进行供应商评估和审核在选择供应商之前,应对其进行评估和审核。
评估的内容包括供应商的质量管理体系、产品质量、生产能力等。
通过对供应商进行评估和审核,可以更好地了解其质量水平,为后续的供应商质量改进提供参考。
3. 建立供应商质量管理体系为了保证供应商的质量,公司应与供应商共同建立质量管理体系。
该体系应包括质量目标、质量标准、质量控制方法等内容。
只有建立了有效的质量管理体系,才能更好地促进供应商的质量改进。
4. 确定关键的供应商质量指标为了评估供应商的质量,并进行改进,需要确定关键的供应商质量指标。
这些指标应涵盖供应商的产品质量、交货准时率、售后服务等方面。
通过对关键指标的监控和评估,可以及时发现供应商存在的问题,并进行改进。
5. 定期进行供应商质量评估定期对供应商的质量进行评估是保证供应商质量的重要措施之一。
通过评估,可以发现供应商的优点和不足,并及时采取措施进行改进。
评估的频率可以根据供应商的性质和业务需求来确定。
6. 实施供应商培训计划为了提升供应商的质量管理水平,公司可以实施供应商培训计划。
培训的内容可以包括质量管理知识、质量标准、质量控制方法等。
通过培训,可以提高供应商的质量意识和质量管理能力,从而促进供应商的质量改进。
7. 建立供应商沟通机制为了及时了解供应商的质量情况和需求,建立供应商沟通机制是很重要的。
通过建立沟通机制,可以促进供应商和公司之间的信息交流和问题解决。
同时,也可以提高供应商的满意度,进一步加强供应商与公司的合作关系。
8. 进行供应商质量纠正和预防措施当发现供应商存在质量问题时,应及时采取纠正和预防措施。
纠正措施包括对不合格品进行退货或返工,而预防措施包括对供应商的质量管理进行改进。
- 1、下载文档前请自行甄别文档内容的完整性,平台不提供额外的编辑、内容补充、找答案等附加服务。
- 2、"仅部分预览"的文档,不可在线预览部分如存在完整性等问题,可反馈申请退款(可完整预览的文档不适用该条件!)。
- 3、如文档侵犯您的权益,请联系客服反馈,我们会尽快为您处理(人工客服工作时间:9:00-18:30)。
全球供应商质量改进程序
(十二)一级发运控制(CS-L1)
由供方实施的不合格品遏制(由供方自己在供方处解决所 有问题),同GP12 (100%检验)
进入条件: A.供方采取短期或长期措施后同一质量问题的反复发生; B.高风险质量问题溢出 C.违反PPAP程序(如擅自更改原材料、分供方、检验标准 等) D.对SGM造成重大影响或损失 E.GP12期间属于GP12检控内容但未被发现的。 F.售后重大质量问题
April,2007
全球供应商质量改进程序
(十三)二级发运控制(CS-L2)
在一级受控发运的基础上由第三方追加实施的不合格品 遏制(100%检验+100%第三方检验)
由SGM根据零件缺陷和重要程度确定检查项目,并由 SGM指定的第三方实施发运前100%检查,费用由供方 负责
退出原则:二级退一级,一级在完全退出 凡受到二级受控发运的供应商,在受控发运期间,停止
SGM的日产量要求(实际销售所需) 产能A表 供应商质量控制计划审核表B 产能分析表C表
April,2007
全球供应商质量改进程序
(八)早期生产遏制(GP12)
目的:早发现问题,完善控制手段,争取时间 实际上是在正常生产和检验后增加了100%检验,并且对
过程控制加严 必须是独立于正常生产和检验区域之外的专门区域。 它是权宜之计:争取时间解决质量问题(TOP5),找到根
零件生命期
April,2007
全球供应商质量改进程序
(一)潜在供应商评审PSA
WWP全球采购供应商 新设备/新工艺/新人员要重新PSA 老设备/老人/新地方不需要重新PSA PSA没通过,一年之内不可重新评估(一年内不做两次)
April,2007
全球供应商质量改进程序
(二)选点决定
April,2007
全球供应商质量改进程序
(十六)全球采购
实质上是当供应商无法满足通用要求无法做下去的时候, 对供应商停止业务,改采用全球采购供应商(即通用认可 过的,例如CKD件),即顾客选用其他供应商的材料
April,2007
谢谢!
(十)绩效监控
顾客每月寄给总经理的7个图表
April,2007
全球供应商质量改进程序
(十一)供应商质量过程和测量(GP5)
PRR适用于已确认是供应商引起的不合格问题的报告和 解决;
是沟通解决供应商质量问题的一种手段 供方在接到通知后应在1个工作日内完成最初答复(进口
件2个工作日),否则顾客将发布“顾客满意PRR”. 供方在接到通知后15天内完成最终答复
本原因,更改PFMEA/CP和作业指导书 GP12是否能撤掉:a.≥1200套;b.连续半个月没有问题产
品送到GP12区域;
April,2007
全球供应商质量改进程序
(九)持续改进(GP8)
着眼于质量提升,而不是质量改正 例如:降低致力于RPN值,是属于持续改进
April,2007
全球供应商质量改进程序
(六)生产件审批(PPAP)
由SQE主导 GP11目的:证明目前生产能够满足通用要求;对现在状
态拍照,而且永久不能变(若有变动要重新递交PPAP), PPAP递交的文件具有法律作用 PPAP递交24个文件
April,2007
全球供应商质量改进程序
(七)按节拍生产(GP-9)
1个工作日的合同产能(供应商跟通用签合同时约定的产 能,例300件/天)
全球供应商质量改进程序
时间线
早 期 生 产 遏 制 (GP-12) 按 节 拍 生 产 (GP-9) 生 产 件 审 批 (PPAP) 样 件 批 准 (GP-11)
预生产会议
先 期 产 品 质 量 策 划 (APQP) 选点决定
潜在供应商评审
开始生产
全球采购 改进会议 质量研讨会 二级发货控制 一级发货控制 供 应 商 质 量 过 程 和 测 量 (GP-5) 绩效监控 持 续 改 进 (GP-8)
新业务 六个月内两次一级控制则停止新业务
April,2007
全球供应商质量改进程序
(十四)质量研讨会
由通用SDE组织召开的 针对的问题:
A.不能及时供货; B.反复出现质量问题
April,2007
全球供应商质量改进程序
(十五)改进会议
实质上是SGM高层(采购经理)与供应商高层的谈话 内容针对供方常常出现且无法改进的问题 通常是质问:请问贵司还有能力做下去吗?
(四)预生产(PRE-PRODUCTION)会议
生产前准备进行。
以前叫PDT(Production Development Team),现在叫 SMT(System Management Team).
April,2007
JPC会议(联合采购中心会议):分别从产品价格成本、运 输成本、供应商能力等方面讨论决定。
April,2007
全球供应商质量改进程序
(三)先期产品质量策划(APQP)
一旦供应商被选定,30天内,通用SQE必须到被选定的 供应商处召开APQP启动会议,进行先期质量策划。
April,2007
全球供应商质量改进程序
全球供应商质量改进程序
(五)样件批准(GP11)
由PE主导 GP11是为了证明设计是对的 交样文件、交样方法同PPAP很相似 对于整车来讲,叫OTS 对于动力总成,分别有预样件批准PRE-PROTOTYPE和
PROTOTYPE样件批准
April,2007
全球供应商质量改进程序