IE基础培训动作浪费
IE基础及讲义七大浪费

□ 单纯动作 □ 附带动作 □ 低效附加价值 □ 纯附加价值
□ 单纯动作 □ 附带动作 □ 低效附加价值 □ 纯附加价值
2021/1/2
- 10 -
13
Ⅱ.对浪费的认识
拿起落地的材料
□ 单纯动作 □ 附带动作 □ 低效附加价值 □ 纯附加价值
抓住口袋里的SCREW
□ 单纯动作 □ 附带动作 □ 低效附加价值 □ 纯附加价值
3. 接近改善思想的方法
4. 接近流动的步骤
5. 动作分析与改善
2021/1/2
2
Ⅰ.IE的概念
1.什么是IE.
IE就是指industrial工业. Engineering工程
是由二个英文字母的字首结合
工业工程是对人员、物料、机器设备、信息所组成的集成系统进行设计、改 善和实施的学科. 它综合运用数学、物理学和社会科学方面的专门知识和技 术, 以及工程分析和设计的原理与方法, 对该系统所取得的成果进行确定、 预测和评价。
途也有寄托之所在.因此,简单地说IE就是代表“合理化及改善”的意义,为了顾及记忆
的方便,为什么就以中文”改善”来代表“I”的含义。
2021/1/2
3
Ⅰ.IE的概念
3.IE的特点.
➢ IE的核心是降低成本、提高生产质量和生产效率 ➢ IE是综合性的应用知识体系 ➢ 以人为本是IE区别于其他工程学科的特点之一 ➢ IE的重点是面向微观管理(三化)-工业简化、专业化、标准化 ➢ IE是系统优化技术
精品
IE基础及七大浪费
目 录
第一章. IE的概念
1.什么是IE 2. IE的目的 3.IE特点 4.IE的手法 5.IE活动的对象
第二章. 对浪费的认识
1. 对浪费的认识 2. 在制造现场发生的浪费
八大浪费与IE七大手法培训

八大浪费与IE七大手法培训一、浪费的概念在生产和管理过程中,浪费是指任何没有为顾客创造价值的活动、步骤或资源。
浪费通常会导致生产效率的下降、成本的增加以及顾客满意度的降低。
充分认识和理解浪费对于提高生产效率、降低成本以及提升企业竞争力具有重要意义。
八大浪费,也被称为“TOYOTA制造业中的八大浪费”,是在制造业领域中提出的浪费分类模型,可以帮助企业识别和减少浪费,提高生产效率。
八大浪费包括以下内容:1.过产:生产超出需求的产品,造成库存积压。
2.运输:物料、半成品或成品在生产过程中的多次搬运。
3.待货:产品在生产过程中停滞等待下一道工序。
4.加工:生产过程中的不必要操作和加工步骤。
5.库存:过量的物料或产品积压在仓库中。
6.功劳:工人在不必要的工作中造成的浪费。
7.运动:无效的工人或设备的移动。
8.等待:等待原材料、设备或其他资源的到达。
二、IE七大手法IE(Industrial Engineering)是一种运用工程技术和管理学原理改善生产过程的学科,旨在提高生产/操作效率,降低成本。
IE的七大手法是IE学科中常用的方法和工具,通过对生产过程进行分析和改进,以提高生产效率和减少浪费。
IE七大手法包括以下内容:1.工程作业分析:通过分析和记录工序中的每个步骤和活动,识别出浪费和低效的环节。
2.工序改进:基于工程作业分析的结果,优化和改进工序,提高生产效率。
3.布局设计:设计和优化工厂/车间的布局,使得物料和信息流动更加高效和顺畅。
4.工作标准化:制定和实施标准化的工作程序和操作规范,提高工作的一致性和效率。
5.工具和设备改进:引入新的工具和设备,或者对现有的工具和设备进行改进,提高生产效率。
6.人力资源管理:合理安排和管理人力资源,提高员工的工作效率和满意度。
7.进程控制:监控和控制生产过程,确保生产活动按照计划进行,减少浪费和延误。
三、浪费与IE七大手法培训浪费和IE七大手法是生产和管理中非常重要的概念和方法。
IE基础知识之八大浪费

等待的三不原则:不要监视机器、不要巡逻救生、不要袖手旁观
4、人员的浪费
什么是人员的浪费?
人员浪费:顾名思义就是安排了比标准配置人员更多但产量 没有增加的一种浪费形式 人员浪费的后果是:浪费资源 改善: 1、按ST/LOB排拉 2、按件计薪 3、绩效考核„„
5、搬运的浪费
什么是搬运的浪费
不必要的搬运、工作的移动、预置以及长距离的搬运流 程等 表现形式: -- 找到、拿起、移动,用手放 -- 从手推车移到货板 -- 从货仓到工厂 -- 从工厂到生产线 -- 从生产线到机械化车间 -- 从机械化车间到操作工位
HEG
IE基础知识之八大浪费
优化生产运作过程,实现最大效率和效益!
李
伟
什么是浪费?
什么是浪费?
● 浪费是指那些导致成本增加但价值 不增加的因素 ● 虽然增加价值,但耗用资源过高 ● 一种浪费通常能够导致另外一种浪 费
不产生任何附加价值的因素就是浪费
发现浪费和认识浪费的能力很重要
什么是浪费?
显性浪费/隐性浪费 ● 显性浪费
改善: ● 计划性使用材料 ● 残材活用 ● 容器内的间隔化…
谢谢!请多提宝贵意见
● ● ● 生产速度快并不代表效率高 设备余力并非一定是埋没成本 生产能力过剩时,应尽量先考虑减少作业人员,但并非辞退人员,而是更合理、更有效率地 应用人员
3、等待的浪费(不平衡)
什么是等待的浪费?表现形式: 双手均未抓到及摸到东西的时间 表现形式: ● 自动机器操作中,人员的“闲视”等待 ● 作业充实度不够的等待 ● 设备故障、材料不良的等待 ● 生产安排不当的人员等待 ● 上下工程间未衔接好造成的工程间的等待…
则)
5:只要条件允许,工具和物料应放在预先确定的位置。(易于操作的原则) 6:尽可能采用“下坠式”传送方式。(重力坠送原则、利用惯性的原则)
IE之八大浪费培训资料

IE之八大浪费培训资料引言在现代社会,即使是最基本的技能,也需要在培训的指导下逐步学习和掌握。
然而,在培训资料的制作过程中,我们常常会遇到一些问题,导致培训资料的制作变得冗长、复杂、低效。
本文将介绍IE(Instructional Efficiency)之八大浪费培训资料,旨在帮助读者提高培训资料的制作效率,提升培训的实际效果。
1. 重复信息培训资料中的重复信息是一种常见的浪费形式。
这种情况通常出现在不同章节或不同讲义中,同一内容被重复提及。
重复的信息不仅会增加学员的阅读负担,还会降低学习效果。
为了避免浪费,制作培训资料时应注意避免重复使用相同的内容,可以通过引用和链接的方式将相关内容连接起来,提高资料的可读性。
2. 冗长句子和段落冗长的句子和段落也是浪费培训资料的常见问题。
过长的句子容易造成理解困难,而冗长的段落则会导致学习者在阅读过程中失去重点。
为了提高资料的可读性,建议尽量使用简洁明了的句子和段落,突出重点信息,帮助学员更好地理解和消化所学内容。
3. 多音节词和复杂词汇在培训资料中,过多的多音节词和复杂词汇也会导致学习困难和浪费。
学员在理解这些词汇时需要花费更多的时间和精力,影响学习效果。
为了减少浪费,制作培训资料时应尽量使用简单明了的词汇,避免使用过多的多音节词和复杂词汇。
4. 无效的图表和示意图在培训资料中,过多的无效图表和示意图也会浪费学员的时间和精力。
如果这些图表和示意图并没有提供实质性的帮助,反而增加了学员的阅读负担,那么它们就是无效的。
制作培训资料时,应注意筛选和精简图表和示意图,确保它们的有效性和使用价值。
5. 复杂的排版和格式复杂的排版和格式也是浪费培训资料的一种形式。
过多的花哨排版和复杂格式会分散学员的注意力,降低学习效果。
为了避免浪费,制作培训资料时应遵循简明扼要的原则,保持统一的排版和格式,确保资料的清晰易读。
6. 额外的细节和分散的注意力培训资料中过多的额外细节和分散的注意力也会导致浪费。
{IE工业工程}八大浪费及IE七大手法概述

P15
一、八大浪费及实例
The way to lean production !
P2
一、八大浪费及实例
何谓浪费?
浪费:在基础IE和精益生产中,将不产生任何附加价值的投入(人、设备、 理等)都定义为浪费。
也就是说,在公司活动中,任何投入都应该是有价值的!
浪费其他定义
定义1 定义2 定义3
对人力、财物、时间等用得不当或没有节制,超过必要的量。 当一个人有能力去驾驭某件事情,而结果没有主动去实现。 不充分利用;不珍惜;不必要地废弃。
P6
一、八大浪费及实例
现场视频/ห้องสมุดไป่ตู้片:
浪费种类1:
动作浪费
详细说明:
1. 拿取电机动作幅度过大; 2. 放成品动作需跨过成品堆; 3. 电机放工装上的对位动作;
The way to lean production !
浪费种类2: 详细说明:
过量生产 浪费
1. 后工序还没有消耗就又继续在生产, 超出中间必要在库数量;
授课前注意事项
1. 本次课程总共授课时间为2h,中间无休息时间; 2. 请各位遵守课堂纪律,将手机调整为震动状态; 3. 课堂上提出的问题请积极参与互动; 4. 授课中没有解决的疑惑课外可继续交流沟通。
The way to lean production !
P1
目录
一、八大浪费及实例 二、IE七大手法简介 三、排除浪费方法及工具
详细说明:
详细说明:
1. 上料人员上料时弯腰等动作浪费;
The way to lean production !
P11
一、八大浪费及实例
现场视频/图片:
浪费种类2: 详细说明:
IE——七大浪费

七大浪费生产线上的七种浪费第一种:等待的浪费主要因素表现为:作业不平衡,安排作业不当、待料、品质不良等。
第二种:搬运的浪费主要因素表现为:车间布置采用批量生产,依工作站为区别的集中的水平式布置所致。
(也就是分工艺流程批量生产),无流线生产的观念。
第三种:不良品的浪费主要因素表现为:工序生产无标准确认或有标准确认未对照标准作业,管理不严密、松懈所导致。
第四种:动作的浪费主要因素表现为:生产场地不规划,生产模式设计不周全,生产动作不规范统一。
第五种:加工的浪费主要因素表现为:制造过程中作业加工程序动作不优化,可省略、替代、重组或合并的未及时检查。
第六种:库存的浪费主要因素表现为:管理者为了自身的工作方便或本区域生产量化控制一次性批量下单生产,而不结合主生产计划需求流线生产所导致局部大批量库存。
库存的损害表现有:(1):产生不必要的搬运、堆积、放置、防护处理、找寻等浪费。
(2):使先进先出的作业困难。
(3):损失利息及管理费用。
(4):物品的价值会减低,变成呆滞品。
(5):占用厂房空间,造成多余的工场、仓库建设投资的浪费。
(6):没有管理的紧张感,阻碍改进。
(7):设备能力及人员需求的误判。
第七种:制造过多(早)的浪费主要因素表现为:管理者认为制造过多与过早能够提高效率或减少产能的损失和平衡车间生产力。
制造过多(早)的损害表现有:(1):提早用掉费用(材料费、人工费),不能创造利润。
(2):把“等待的浪费”隐藏起来,使管理人员漠视等待的发生和存在。
(3):自然而然地积压在制品,其结果不但会使制程的时间变长(无形的),而且会使现场工作的空间变大,机器间距离因此加大,逐渐地吞蚀利润。
(4):产生搬运,堆积的浪费,使得先进先出的作业产生困难。
七大浪费的对策结合大连三洋制冷推行精益生产方式的实际情况,重点论述生产现场的七种浪费和如何有效消除。
一、七种浪费之一:等待的浪费等待就是闲着没事,等着下一个动作的来临,这种浪费是无庸置疑的。
培训教材—IE八大浪费详解

•文件或信息放在桌上或在电脑内 等待决策或签字 •因安排不当造成项目进程过长 •做了没有价值的事情
管理的浪费
原因:
没有详细的计划安排 作业手续太复杂 重复劳动多 拖延、打扰和精力不集中
对策:
不要推迟进行对你不合意的工作 要有详细的工作计划,并分解成许多可操作的小任务,采取 “分而治之”的方法 利用科技的力量来提升效率 去除不必要的重复劳动,精简作业流程
改善手法
QC讲求的是“因果论”,要有因才有结果,有 过程才有产出;
IE讲求的是“方法论”,不同的方法有不同的 结果,越少的浪费效果越好;
VA讲求的是“价值论”功能越强,价值越高,成 本越低,价值越高。
改善手法
QC基本理念:事实与变异的理念,管理与改善的理念
事实的理念是指以事实为基础,而事实又以数据加以体现: 收集正确的数据,排列、整理数据,依数据行动
改善手法
VA基本理念:必要与不必要
国家标准GB8223-87关于VA之定义:通过各相关 领域的协作,对所研究对象的功能与费用进行系 统分析,不断创新,以提高所研究对象价值的思 想方法和管理技术
改善意识
现场、现物、现实的意识
现场指到问题发生的场所, 现物指对发生问题的对象进行确认, 现实指实实在在地进行分析,找出真正的原因。
5.库存的浪费
对策:
库存意识的改革 U型设备配置 均衡化生产 生产流程调整顺畅 看板管理的贯彻 快速换线换模 生产计划安排考虑库存消化
5.库存的浪费
注意:
库存是万恶之源 管理点数削减降低安全库存 消除生产风险降低安全库存
6.动作的浪费
额外动作的浪费
不必要的动作、无附加价值的动作,及较慢的动作
表现形式:
IE-认识浪费
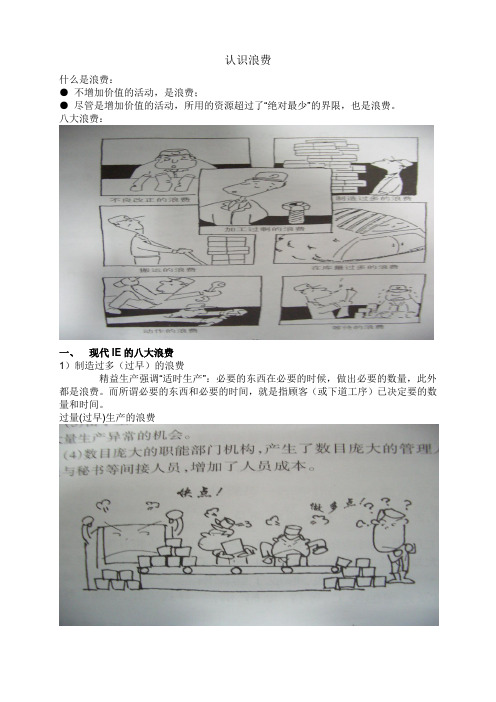
认识浪费什么是浪费:●不增加价值的活动,是浪费;●尽管是增加价值的活动,所用的资源超过了“绝对最少”的界限,也是浪费。
八大浪费:一、现代IE的八大浪费1)制造过多(过早)的浪费精益生产强调“适时生产”:必要的东西在必要的时候,做出必要的数量,此外都是浪费。
而所谓必要的东西和必要的时间,就是指顾客(或下道工序)已决定要的数量和时间。
过量(过早)生产的浪费2)库存的浪费(包含中间在制品)●产生不必要的搬运、堆积、放置、防护、寻找等浪费动作;●使先入先出作业困难;●资金占用(损失利息);●物品的价值衰减,变成呆料、废料;●掩盖问题,使管理不善的问题掩盖起来。
如机器经常发生故障、设备调整时间太长、设备能力不平衡、工人缺勤、备件供应不及时等问题,由于库存水平高,不易被发现。
●没有改善的紧迫感,阻碍改善的活性化。
●设备能力及人员需求的误判;库存掩盖大量问题3)搬运的浪费搬运是不产生附加值的动作。
搬运的损失分为放置、堆积、移动、整列等动作浪费。
生产流水化同步化是减少搬运的根本之道。
4)不良改正的浪费是指企业内发生不良品造成的各种质量成本及由此造成的相关浪费。
5)过分精确加工的浪费实际加工精度比加工要求高,造成资源的浪费。
工程内搬运的浪费)动作的浪费(动作的12种浪费)⑵、一只手空闲的浪费(一只手在工作,一只手在休息)⑶、作业动作停止的浪费(身体每动作一次停止一次,动作不连续)。
⑷、作业动作太大的浪费(动作幅度太大,勉强费劲)⑸、拿的动作变化的浪费(动作交替变换来适应安装)⑹、步行的浪费道具的位置远了(零件位置远了的浪费)⑺、活动角度太大的浪费(最适合的角度为45度以内)⑻、动作与动作之间没有配合好的浪费(非[连续作业] 的浪费)⑼、不懂技巧的勉强、浪费作业修正、不习惯的浪费(有很好做的时候和做不到的时候)⑽、伸背动作的浪费(零件、作业位置太高)⑾、弯腰动作的浪费(零件、作业位置太低)⑿、重复动作的浪费(同样的动作两次以上地重复操作)7)等待的浪费因断料、作业不均衡、计划不当等造成无事可做的等待,也称之为停滞的浪费。
IE七大手法八大浪费培训课件

IE七大手法八大浪费一、IE人员主要从事的七个方向,它们是:1.研究与开发管理;2.生产系统设计与控制;3.效率工程;4.质量控制与质量保证;5.实施规划与物流分析;6.工业卫生与安全;7.人力资源管理。
二、基础IE里的东西:IE手法包括:方法研究(程序分析、动作分析),作业测定,布置研究,Line Balance等,但好象不够七个。
在现场IE里,IE七大手法包括:程序分析、动作分析,搬运分析,动作经济原则,作业测定,布置研究,Line Balance。
三、台湾公司教材里面的1、工程分析。
2、搬运工程分析。
3、运动分析(工作抽查 work sampling)4、生产线平衡。
5、动作分析。
6、动作经济原则。
7、工厂布置的改善。
四、其它的各种说法 1、IE七大手法为:作业分析、程序分析(运用ECRS 技巧)、动作分析(动作经济原则)、时间分析、稼动分析、布置搬动分析、生产线平衡2、七大手法:流程分析法、动作分析法、动作经济原则、时间研究、工作抽查法、人机配置法、工作简化法3、七大手法:动作改善法(动改法)、防止错误法(防错法)、5*5W1H法(五五法)、双手操作法(双手法)、人机配合法(人机法)、流程程序法(流程法)、工作抽样法(抽样法)4、七大手法:程序分析、时间分析、动作分析、流水线分析、稼动分析、物料分析、环境分析。
IE的八大浪费浪费的定义在JIT生产方式中,浪费的含义与社会上通常所说的浪费有所区别。
对于JIT来讲,凡是超出增加产品价值所绝对必须的最少量的物料、设备、人力、场地和时间的部分都是浪费。
因此,JIT生产方式所讲的浪费不仅仅是指不增加价值的活动,还包括所用资源超过“绝对最少”界限的活动。
各种各样的浪费现象在很多尚未实行5S活动的企业中普遍存在,如表1-1所示。
为了杜绝工厂中的浪费现象,首先需要发现不合理的地方,然后才是想办法解决问题,这就需要推行5S、JIT等较为先进的管理方法。
表1-1 未实施5S活动的企业中的浪费常见的八大浪费在工厂中最为常见的浪费主要有八大类,分别是:不良、修理的浪费,过分加工的浪费,动作的浪费,搬运的浪费,库存的浪费,制造过多?过早的浪费,等待的浪费和管理的浪费。
IE现场7大浪费

IE现场7大浪费一、库存浪费◆精益生产认为:“库存是万恶之源”,所有改善行动皆会直接或间接地和消除库存有关。
①产生不必要的搬运、堆积、放置、防护处理、找寻等浪费②使先进先出的作业困难③损失利息及管理费用④物品的价值会减低,变成呆滞品⑤占用厂房空间、造成多余工场、仓库建设等⑥设备能力及人员需求的误判◆因库存造成无形损失,绝不亚上述有形损失,精益生产者认为库存会隐藏问题,而“问题”在精益生产者被认为是宝藏,问题如果能不断地被发现解决,则利益便会不断地产生1、没有管理的紧张感,阻碍改进:2、库存量一多,因机械故障、不良产品所带来的不利后果不能马上显现出来,因而也不会产生对策。
3、由于有了充足的库存,出现问题时可以用库存先顶上,问题就可以慢慢解决甚至不用解决,最起码是被掩盖住了,不急迫了,不会被上级追究了,于是乎本部门的工作成绩就出来了。
二、制造过多或过早浪费◆TPS强调的是“适时生产”。
◆多做能提高效率,提早做好能减少产能损失(不做白不做,机器还不是一样停着?)1、提早用掉了材料费、人工费而已,并不能得到什么好处。
2、把“等待浪费”隐藏,使管理人员漠视等待的发生和存在。
3、积压在制品,使生产周期L/T变长无形的),而且会使现场工作空间变大,不知不觉中吞蚀我们的利润。
4、产生搬运、堆积浪费,先进先出变得困难。
三、不良品浪费◆任何的不良品产生,皆造成材料、机器、人工等的浪费。
◆及早发现不良品,容易确定不良来源,进而减少不良品的产生。
◆关键是第一次要把事情做对,——“零缺陷”四、搬运浪费◆大部分人皆认同搬运是一种无效的动作,也有人认为搬运是必须的。
◆用“输送带”的方式来克服,行吗?1、取放浪费;2、等待浪费;3、在制品过多浪费;4、空间浪费。
◆搬运浪费又包含放置、堆积、移动、整理等动作的浪费。
五、加工浪费◆定义:指的是与工程进度及加工精度无关的不必要的加工◆有一些加工程序是可以省略、替代、重组或合并。
◆很多时候会习惯并认为现在的做法较好六、动作浪费12种动作浪费:◆两手空闲◆单手空闲◆不连贯停顿◆幅度太大◆左右手交换◆步行多◆转身角度大◆移动中变换状态◆不明技巧◆伸背动作◆弯腰动作◆重复不必要动作七、等待浪费◆生产线的品种切换◆工作量少时,便无所事事◆时常缺料,设备闲置◆上工序延误,下游无事可做◆设备发生故障◆生产线工序不平衡◆有劳逸不均的现象◆制造通知或设计图未送达。
IE八大浪费

八大浪费1.不良、修理的浪费所谓不良、修理的浪费,指的是由于工厂内出现不良品,需要进行处置的时间、人力、物力上的浪费,以及由此造成的相关损失。
这类浪费具体包括:材料的损失、不良品变成废品;设备、人员和工时的损失;额外的修复、鉴别、追加检查的损失;有时需要降价处理产品,或者由于耽误出货而导致工厂信誉的下降。
2.加工的浪费加工的浪费也叫过分加工的浪费,主要包含两层含义:第一是多余的加工和过分精确的加工,例如实际加工精度过高造成资源浪费;第二是需要多余的作业时间和辅助设备,还要增加生产用电、气压、油等能源的浪费,另外还增加了管理的工时。
3.动作的浪费动作的浪费现象在很多企业的生产线中都存在,常见的动作浪费主要有以下12种:两手空闲、单手空闲、作业动作突然停止、作业动作过大、左右手交换、步行过多、转身的角度太大,移动中变换“状态”、不明技巧、伸背动作、弯腰动作以及重复动作和不必要的动作等,这些动作的浪费造成了时间和体力上的不必要消耗。
4.搬运的浪费从JIT的角度来看,搬运是一种不产生附加价值的动作,而不产生价值的工作都属于浪费。
搬运的浪费具体表现为放置、堆积、移动、整列等动作浪费,由此而带来物品移动所需空间的浪费、时间的浪费和人力工具的占用等不良后果。
国内目前有不少企业管理者认为搬运是必要的,不是浪费。
因此,很多人对搬运浪费视而不见,更谈不上去消灭它。
也有一些企业利用传送带或机器搬运的方式来减少人工搬运,这种做法是花大钱来减少工人体力的消耗,实际上并没有排除搬运本身的浪费。
5.库存的浪费图1-1 库存过多掩盖问题按照过去的管理理念,人们认为库存虽然是不好的东西,但却是必要的。
JIT的观点认为,库存是没有必要的,甚至认为库存是万恶之源。
如图1-1,由于库存很多,将故障、不良品、缺勤、点点停、计划有误、调整时间过长、品质不一致、能力不平衡等问题全部掩盖住了。
例如,有些企业生产线出现故障,造成停机、停线,但由于有库存而不至于断货,这样就将故障造成停机、停线的问题掩盖住了,耽误了故障的排除。
IE培训之八大浪费
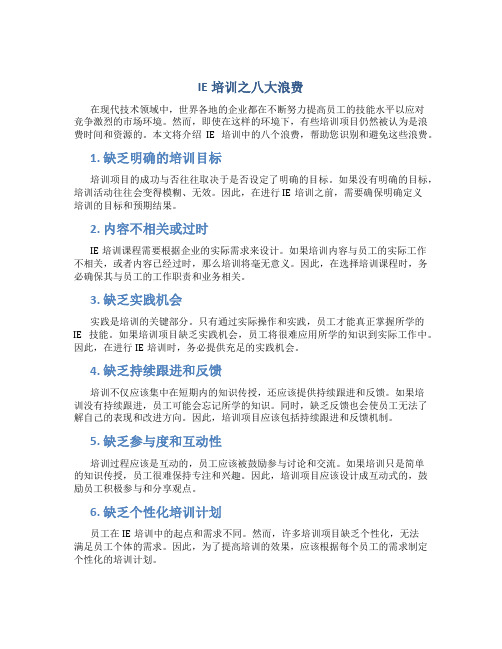
IE培训之八大浪费在现代技术领域中,世界各地的企业都在不断努力提高员工的技能水平以应对竞争激烈的市场环境。
然而,即使在这样的环境下,有些培训项目仍然被认为是浪费时间和资源的。
本文将介绍IE培训中的八个浪费,帮助您识别和避免这些浪费。
1. 缺乏明确的培训目标培训项目的成功与否往往取决于是否设定了明确的目标。
如果没有明确的目标,培训活动往往会变得模糊、无效。
因此,在进行IE培训之前,需要确保明确定义培训的目标和预期结果。
2. 内容不相关或过时IE培训课程需要根据企业的实际需求来设计。
如果培训内容与员工的实际工作不相关,或者内容已经过时,那么培训将毫无意义。
因此,在选择培训课程时,务必确保其与员工的工作职责和业务相关。
3. 缺乏实践机会实践是培训的关键部分。
只有通过实际操作和实践,员工才能真正掌握所学的IE技能。
如果培训项目缺乏实践机会,员工将很难应用所学的知识到实际工作中。
因此,在进行IE培训时,务必提供充足的实践机会。
4. 缺乏持续跟进和反馈培训不仅应该集中在短期内的知识传授,还应该提供持续跟进和反馈。
如果培训没有持续跟进,员工可能会忘记所学的知识。
同时,缺乏反馈也会使员工无法了解自己的表现和改进方向。
因此,培训项目应该包括持续跟进和反馈机制。
5. 缺乏参与度和互动性培训过程应该是互动的,员工应该被鼓励参与讨论和交流。
如果培训只是简单的知识传授,员工很难保持专注和兴趣。
因此,培训项目应该设计成互动式的,鼓励员工积极参与和分享观点。
6. 缺乏个性化培训计划员工在IE培训中的起点和需求不同。
然而,许多培训项目缺乏个性化,无法满足员工个体的需求。
因此,为了提高培训的效果,应该根据每个员工的需求制定个性化的培训计划。
7. 缺乏管理和监督IE培训需要有有效的管理和监督机制。
如果培训项目缺乏管理和监督,可能会导致培训效果的下降。
因此,应该确保培训项目有明确的责任人负责管理和监督培训的进程和结果。
8. 缺乏绩效评估和调整培训的效果应该进行绩效评估,并根据评估结果进行必要的调整。
培训教材3——八大浪费与IE七大手法

8、层别原理:为避免将不同工作做错,而设法加以区别。
例:将邮件中的附件按秘密等级标识出来避免泄露公司机密数据。
9、警告原理:如有不正常的现象发生,能显示出各种“警告”的讯号。
生产不平衡造成的等待。
第二十二页,共53页。
等待的浪费
产生原因
生产线布置不当,物流混乱; 设备配置、保养不当; 生产计划安排不当; 工序生产能力不平衡; 材料未及时到位;
消除方法
均衡化生产、一个流生产; 自动化及设备保养加强; 加强进料控制。
第二十三页,共53页。
管理的浪费
定义
基于工厂的管理和运作方式使公司不能获得最大利润而造成 的浪费,是竞争力强弱的表现。
表现与后果
1 成员仪容不齐整,有损企业形象,影响士气。
2 设备布置不合理,半成品数目大,增加搬运和无效作业。 3 设备保养不当,易生故障,增加修理成本,影响品质。
4 物品随意摆放,易混料,寻找费时间,易成呆料。
5 通道不畅,作业不畅,易生危险。
第二十四页,共53页。
管理的浪费
产生原因
管理浪费是由于事先管理不到位而造成的问题,科学的 管理应该是具有相当的预见性,有合理的规划,并在事情的 推进过程中加强管理、控制和反馈,这样就可以在很大程度 上减少管理浪费现象的发生。
超过需求而造成的拆卸、报废;
WIP=Work In Process
出发点:1、“保险”
2、“不忍浪费” 3、计划错误、需求不准
第八页,共53页。
制造过多的浪费
产生原因
产能过剩:人员、设备嫁动过剩; 计划过量:订单预测失误、计划错误、信息传递不畅; 前工序过量投入:由于不平衡,前一工序生产过量,WIP过多。
IE基础培训动作浪费

1
M2
0.258
2
M3
0.387
30
M4
0.516
160
M5
0.645
190
动作时间(S) 能量消耗(倍)
动作浪费的12种情况
传统生产方式是粗放式管理,各工序存在大量在制品,即使动作稍慢,对生产也不会 有太大的影响,也就不会潜心研究动作浪费造成的效率低下问题。
№
1 2 3 4 5 6 7 8
1、不是在肉体上、精神上提高强度与速度 2、也不是靠勉强的动作来提高效率 3、而是削除无价值的作业及不均匀、不平 衡等现象,通过安全的、保证品质的、经济 的、舒适的、省力的、省时的作业来提高效 率及创造价值
何谓浪费?
◆不增加价值的活动,是浪费; ◆尽管是增加价值的活动,所用的 资源超过了“绝对最少”的界限, 也 是浪费。
工场常见的八大浪费
1.不良、修理的浪费 2.过分加工的浪费 3.动作的浪费 4.搬运的浪费 5.库存的浪费 6.制造过多(早)的浪费 7.停滞(等待)的浪费 8.管理的浪费
动作的MODAPTS记号 21个
[移动动作] [其他动作]
F3
脚腕动作
D3
?
判断、手指
W5
步行
A4
M1
M2
M3
M4
M5
用力压
浪费类型
两手空闲的浪费 一只手空闲的浪费 动作中途停顿的浪费 动作幅度太大的浪费 拿的动作中途变换的浪费 步行的浪费 动作角度太大的浪费
具体表现
在开始作业到终了之间,有两手空闲的时候 一只手在作业,一只手在休息 每动作一次停止一次(动作不连续) 转身、M4以上的动作 在移动过程中翻转,调整等 治工具的位置远、部品的位置远 最适合的角度在45°以内
IE之八大浪费

PPT文档演模板
IE之八大浪费
•3.3等待的浪费
• 1. 等待的浪费:即等待下一个动作的来临,不仅是人、机 器存
• 在等待,物料也有等待,即等待加工;工艺中的等待。
• 2. 表现形式: • --自动机器操作中,人员的“闲视”等待 • --作业充实度不够的等待 • --设备故障、材料不良的等待 • --生产安排不当的人员等待 • --上下工程间未衍接好造成的 • 工程间的等待
• 1.库存是指:工厂里的原材料﹑零部件﹑半成品(WIP)﹑
成
•
品等。 (万恶之源,也是必要的恶物)
• 2.三种错误的观念造成库存的浪费:
•
1)材料库存:大量采购成本低。
•
2)在制品库存:不良维修;机器故障。
•
3)成品库存:预测生产与实际需求量不同•。库存水平
•不良品
•故障
•点点 停
•能力 不平衡
•调整时 间长
•选对的人,做对的事,并将事情做对。 •组织再造,流程优化,简化,标准化。
PPT文档演模板
IE之八大浪费
• 四. 如何发现浪费
• 1.发现浪费的重点: • 1)三现原则:到现场 、看现物、掌握现状。
•任何企图在座在办公室里解决现场问题都是徒劳的。
PPT文档演模板
IE之八大浪费
• 四. 如何发现浪费
PPT文档演模板
IE之八大浪费
•二、什么是浪费 ?
Anything other than absolute minimum resource of material,machine and manpower required to add value to the product
IE基本课程(浪费)资料
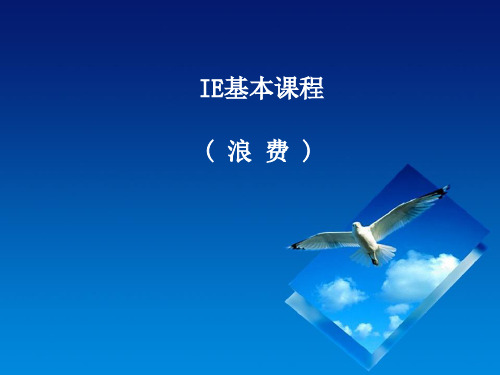
各个工厂的产品不同,但工厂内发现的典型浪费的类型都非常相似
IE 基本课程 (浪费)
Ⅲ 浪费的改善
思想的改善 改善是无止境的 抛弃现在使用的方法 改变思想、习惯,寻找一切可能性
Ⅲ 浪费的改善
冰山理论
这副相片是目前在钮芬兰岛 St.Johns担任美商“全球海域 石油钻探公司”的钻油平台专 案任务经理拍摄的。为了确保 钻油平台的作业安全,每当有 “冰山警报” 时,钻油平台 就必须派遣潜水人员以及任务 专家,在所有冰山可能经过的 路径海域尽快完成海况调查, 并且依据调查报告调派越洋型 拖船(OceanTug),待命将冰山 拖离任何可能危及钻油平台作 业安全的区域。由于当天的海 况出奇的风平浪静,海水清澈 无比,阳光又正好是直接照射 的角度,所以钻油平台上的潜 水人员才得以拍摄下这幅冰山 全貌的完美杰作!
7大浪费: “过盈生产带来的浪费”;“库存浪费”;“等待浪费”;“动作浪 费”;
“搬运浪费”;“不良生产带来的浪费”;“加工本身的浪费”
浪费的发现
三现 5 Why
改善的不同结果
改善 = 提高劳动密度;改恶 = 提高劳动强度
三现和5-Why展开事例(根本对策)
Ⅲ 浪费的改善
(改善)与(改恶)
改恶 =
提高劳动强度
改善 =
提高劳动密度
Ⅲ 浪费的改善
改善步骤
Ⅲ 浪费的改善
消除浪费分析
Ⅲ 课程总结
浪费的定义
在制造过程中没有对产品产生附加价值的所有行为
浪费的原因
浪费是由“不一致”,“不均衡”,“不合理” 而产生
浪费的种类
在制造过程中没有对产品产生附加价值的所有行为
IE 基本课程 (浪费)
- 1、下载文档前请自行甄别文档内容的完整性,平台不提供额外的编辑、内容补充、找答案等附加服务。
- 2、"仅部分预览"的文档,不可在线预览部分如存在完整性等问题,可反馈申请退款(可完整预览的文档不适用该条件!)。
- 3、如文档侵犯您的权益,请联系客服反馈,我们会尽快为您处理(人工客服工作时间:9:00-18:30)。
现场IE 改善手法
轻松拿取消除G3
海绵
拿取平垫片时因为紧贴着底部, 较难拿取;在底部铺上海绵以后, 就变容易拿取了。
铺上海绵
A
在平面上按A图放置、塑料直尺较难拿取
B
按B图反过来放置、变得拿取容易
作业者情报 作业时间 作业动作 零件状态 制造中间在库量
现场IE
距离远易产 生疲劳:M5, M4
改善手法
M2M3
将物品工具放在靠近的地方
放置在靠近的地方 没有放置在靠近的地方
消除M4M5,用M2M3。M2M1也能达成
不要将物品放在输送带对面
不要将物品箱放在地上(放在台面上) 将频繁使用的电动螺丝刀挂在上方、稍伸手就能拿到
动作范围的基准
手在横向位置的最适范围
*最适合作业区域指用小臂画半圆的范围(不与身体中心线交叉) *适合作业区域指臂画半圆的范围 应该用更加靠近最适作业区域下的标准作业,来设定作业布局图
手法一:三角形法
物料(工具)放置点、产品组装点、操作者手的位置 形成的三角形的边长越小越好。三角形越小,作业效率越高
伸手臂45cm以上或横方向伸展的话都是M5、但往身体面前伸展的话、上半身 也会连带辅助动作、可改善成M4。
现场IE
改善手法
缩小动作
蛋糕生产线 生产线的面前是 M2M3,对面是M4 对面作业全部用M2M3可 达成作业,还能低减不良。
现场IE改善手法
两手作业
让两手对称作业
将物品放置在左右手同时动作,方向距离左右对称的地方, 不对称的话一不小心拿了别的东西。 思考将物品工具放置在左右对称能让有节奏动作的地方。
将转身、回头的浪费控制在最少的限度内
产品 产品流向
零件箱
小零件
改善实战:调查项目
改善使作业在最短时间内达成(以作业动作为中心调查) 调查项目 工程布局 调查内容 作业开始位置 作业范围 零件容器,工具使用数量 作业者的身高、手臂的范围 实际作业时间测定 发生的动作/台 容器大小/放入数量/出库形态/出库数 生产线布局/工序内的中间在制品 多少秒/台
浪费类型
两手空闲的浪费 一只手空闲的浪费 动作中途停顿的浪费 动作幅度太大的浪费 拿的动作中途变换的浪费 步行的浪费 动作角度太大的浪费
具体表现
在开始作业到终了之间,有两手空闲的时候 一只手在作业,一只手在休息 每动作一次停止一次(动作不连续) 转身、M4以上的动作 在移动过程中翻转,调整等 治工具的位置远、部品的位置远 最适合的角度在45°以内
0.129
1
M2
0.258
2
M3
0.387
30
M4
0.516
160
M5
0.645
190
动作时间(S) 能量消耗(倍)
动作浪费的12种情况
传统生产方式是粗放式管理,各工序存在大量在制品,即使动作稍慢,对生产也不会 有太大的影响,也就不会潜心研究动作浪费造成的效率低下问题。
№
1 2 3 4 5 6 7 8
工场常见的八大浪费
1.不良、修理的浪费 2.过分加工的浪费 3.动作的浪费 4.搬运的浪费 5.库存的浪费 6.制造过多(早)的浪费 7.停滞(等待)的浪费 8.管理的浪费
动作的MODAPTS记号 21个
[移动动作] [其他动作]
F3
脚腕动作
D3
?
判断、手指
W5
步行
A4
M1
M2
M3
M4
M5
用力压
1、不是在肉体上、精神上提高强度与速度 2、也不是靠勉强的动作来提高效率 3、而是削除无价值的作业及不均匀、不平 衡等现象,通过安全的、保证品质的、经济 的、舒适的、省力的、省时的作业来提高效 率及创造价值
何谓浪费?
◆不增加价值的活动,是浪费; ◆尽管是增加价值的活动,所用的 资源超过了“绝对最少”的界限, 也 是浪费。
何谓3M
<勉强---Muri> 超出能力的限界,一直处在重负担的状态 <浪费---Muda> 虽然有能力,但一直从事能力以下的工作 <不均---Mura> 在工作能力的限界上下来回波动
勉强
能力 不均
適 量 0点
浪费
作 业 时 间
d a b c f e g
hБайду номын сангаас
基准节拍
工位
三个定律
◆作业时间总比基准节拍要多的工位,品质一定不稳定 ◆作业时间总比基准节拍要少的工位,品质一定不稳定 ◆作业总是没有节奏感的工位,品质一定不稳定
动作之间配合不联贯的浪费 非“联合作业”的浪费(机器在工作,人在等待)
9
不懂技巧勉强动作的浪费
10 掂脚尖勉强动作的浪费 11 弯腰动作的浪费 12 重复动作的浪费
作业修正、不习惯、有很好做的时候和做不好的时 候 部品、作业的位置太高
部品、作业的位置太低 反复重复的没有必要动作
基本原则:动作经济性
IE改善基础知识培训(1)
浪费与动作经济性
工业工程(Industrial Engineering﹐简称I.E.) “工业工程可以说是一门通过对人、原材料、 机器设备组成的系统设计和改进,从而提
高生产率并降低成本的技术”。
IE改善的座右铭: “永远不变的是‘变化’”。 “永远存在一个更好的方法”
效率改善的实质
走最短的距离、花最少的时间, 做最多的事
四个最基本的动作经济性
1. 减少动作数 2.同时进行动作 3.动作的距离缩短 4.动作舒适
动作范围的基准
手的下限位置
下限位置
手往下伸时手掌落到臀部时手所处 的高度为下限(不弯腰作业状态)
动作范围的基准
手的上限位置
上限位置
手抬高时与手臂与肩膀同高的 位置为上限位置
[结束动作] 拿、取
L1 G0 G1 G3 4Kg C4
重量补偿
B17
回转动作
E2
使用眼睛
蹲下、站起
[结束动作] 触摸、放置
P0 P2 P5 R2 S30
拿起后调整 方向
从椅子上站 起又坐下
上肢动作:移动动作负担程度 M1,M2,M3,M4,M5
大概移动的 距离(cm)
2.5
5
15
30
45
記
号
M1