轧钢培训讲稿
轧钢工艺基础理论培训讲义
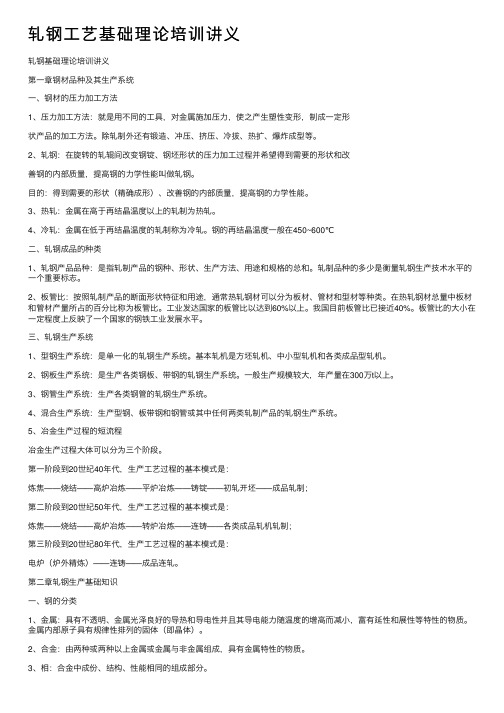
轧钢⼯艺基础理论培训讲义轧钢基础理论培训讲义第⼀章钢材品种及其⽣产系统⼀、钢材的压⼒加⼯⽅法1、压⼒加⼯⽅法:就是⽤不同的⼯具,对⾦属施加压⼒,使之产⽣塑性变形,制成⼀定形状产品的加⼯⽅法。
除轧制外还有锻造、冲压、挤压、冷拔、热扩、爆炸成型等。
2、轧钢:在旋转的轧辊间改变钢锭、钢坯形状的压⼒加⼯过程并希望得到需要的形状和改善钢的内部质量,提⾼钢的⼒学性能叫做轧钢。
⽬的:得到需要的形状(精确成形)、改善钢的内部质量,提⾼钢的⼒学性能。
3、热轧:⾦属在⾼于再结晶温度以上的轧制为热轧。
4、冷轧:⾦属在低于再结晶温度的轧制称为冷轧。
钢的再结晶温度⼀般在450~600℃⼆、轧钢成品的种类1、轧钢产品品种:是指轧制产品的钢种、形状、⽣产⽅法、⽤途和规格的总和。
轧制品种的多少是衡量轧钢⽣产技术⽔平的⼀个重要标志。
2、板管⽐:按照轧制产品的断⾯形状特征和⽤途,通常热轧钢材可以分为板材、管材和型材等种类。
在热轧钢材总量中板材和管材产量所占的百分⽐称为板管⽐。
⼯业发达国家的板管⽐以达到60%以上。
我国⽬前板管⽐已接近40%。
板管⽐的⼤⼩在⼀定程度上反映了⼀个国家的钢铁⼯业发展⽔平。
三、轧钢⽣产系统1、型钢⽣产系统:是单⼀化的轧钢⽣产系统。
基本轧机是⽅坯轧机、中⼩型轧机和各类成品型轧机。
2、钢板⽣产系统:是⽣产各类钢板、带钢的轧钢⽣产系统。
⼀般⽣产规模较⼤,年产量在300万t以上。
3、钢管⽣产系统:⽣产各类钢管的轧钢⽣产系统。
4、混合⽣产系统:⽣产型钢、板带钢和钢管或其中任何两类轧制产品的轧钢⽣产系统。
5、冶⾦⽣产过程的短流程冶⾦⽣产过程⼤体可以分为三个阶段。
第⼀阶段到20世纪40年代,⽣产⼯艺过程的基本模式是:炼焦——烧结——⾼炉冶炼——平炉冶炼——铸锭——初轧开坯——成品轧制;第⼆阶段到20世纪50年代,⽣产⼯艺过程的基本模式是:炼焦——烧结——⾼炉冶炼——转炉冶炼——连铸——各类成品轧机轧制;第三阶段到20世纪80年代,⽣产⼯艺过程的基本模式是:电炉(炉外精炼)——连铸——成品连轧。
培训材料(轧钢)

3 棒材表面质量—折叠
棒材沿轧制方向的平直或弯曲的细线,在横断面上与表 面呈小角度交角的缺陷多为折叠。 折叠主要是由前一道的耳子,也可能是其他纵向凸起物 折倒后轧入本体所造成的,折叠可以在任何道次形成,其 折缝中间常存有氧化铁皮夹杂。
3 棒材表面质量—划痕
划痕主要是成品,特别是高温下的成品,通过有缺陷的 设备将棒材表面划伤所造成。
控制表面质量必须首先严格控制坯料质量,严格检查、 正确判断、认真清理修磨。要特别强调的是对坯料的隐形 缺陷应引起注意,如针孔、潜伏的皮下气泡等,对炼钢及 浇注未达到工序控制要求的坯料都应严格检查,不放过有 潜伏缺陷的钢坯。下面简述几种棒材主要缺陷及其产生的 原因:
3 棒材表面质量—耳子
棒材表面沿轧制方向的条状凸起称为耳子,主要是成品道 次轧槽过充满造成的。导卫安装不正及放扁过钢,均能使 轧件产生耳子。轧制温度的波动或局部不均匀,影响轧件 的宽展量,也可能形成耳子。
2 轧钢工艺简介
表1 连铸坯质量要求
管理项目
尺寸 弯曲
品质特性(规定值或要求)
钢坯规格:200×200×(6000~9200)mm 边长偏差:±3.0mm; 对角线长度之差:6mm;
钢坯总弯曲度不得大于总长度的1.5%;
铸坯质量
方坯质量
①表面不得有目视可见的夹杂、翻皮、结疤,钢坯横截面不允许有缩
影响使用的缩孔、皮下气泡、裂纹,钢坯端头不允许有切割瘤; ②普通质量非合金钢不得有深度大于2mm的裂纹,优质非合金钢、特殊 质量非合金钢和合金钢不得有深度大于1mm的裂纹; ③普通质量非合金钢不得有深度或高度大于3mm的划痕、压痕、擦伤、 气孔、皱纹、冷溅、凸块、凹坑; ④优质非合金钢、特殊质量非合金钢和合金钢不得有深度或高度大于 2mm的划痕、压痕、气孔、皱纹、冷溅、凸块、凹坑、横向振痕。
钢铁行业轧钢技术培训课件

b.斜轧:轧件的纵轴线与轧辊轴线成一定的倾斜角,两个 轧辊的旋转方向相同(无缝管生产);
c.横轧:轧件纵轴线与轧辊轴线平行,两个工作轧辊的旋 转方向相同(圆形断面的各种轴类等回转体)。
(2)挤压
金属在挤压缸中受推力的作用使之从模孔中挤出的 过程。挤压可分为正挤压和反挤压。
正挤压
反挤压
(3)锻造
(2)质量增加的方法:
铸造、电解沉积、焊接与铆接、烧结与胶结等;
(3)质量保持不变的方法:
金属压力加工(轧制、锻造、冲压、拉拔、挤压)。
2.金属压力加工的方法
★金属压力加工:
金属在受到外力作用并不破坏自身完整性的条件下, 稳定改变其几何形状与尺寸,从而获得所需要的几何形状 与尺寸的加工方法。
★金属压力加工的分类:
三. 轧钢生产基本问题
1.轧制钢材的品种及用途 2.轧钢机 3.轧钢生产系统及工艺流程
1. 轧制钢材的品种及用途
根据钢材形状特征的不同, 可将钢材分为型钢、线材、钢板、 带钢、钢管及特殊钢材等。
1)型钢: (30%~35%)
全长具有一定断面形状和尺寸的实心钢材,称之为型钢。
⑴按其断面形状分:
* 简单断面型钢(方钢、圆钢、扁钢、角钢等); * 复杂断面型钢(槽钢、工字钢、钢轨等)。
金属在锻锤或压力机上受到压缩而产生变形的过程。 (棒材、饼材、环材等)
自由锻造
模锻
1-锤头; 2-砧座; 3-锻件; 4-上模; 5-下模
(4)冲压
金属板料在压力机 冲头的作用下冲入凹模 中的过程。(各种杯形 件和壳体等)
1-冲头; 2-模子; 3-压圈; 4- 产品
(5)拉拔
金属受前端的拉力作用使之从模孔中拉出的过程。 (型材、线材和管材)
轧钢工段培训教材

轧钢工段培训教材轧钢生产实践培训教材第一章轧制过程中易出事故的原因及处理一、带钢(带坯)的翘头1.产生原因:①钢坯的上下表面温度差:上表面温度大于下表面温度时会引起带钢的扣头,反之会引起带钢的翘头;②轧制线的标高:轧制线标高过高会引起带钢的扣头,反之会使带钢翘头;③摩擦因素的影响:当带钢表面除鳞不净或轧辊粗糙时,带钢会弯向带有铁皮或辊面粗糙的一面,从而引起带钢的翘头或扣头;④辊系配辊的辊压大小的影响:采用上辊压时会使带钢扣头;采用下辊压会使带钢产生翘头;⑤轧制速度的影响:下辊的辊面线速度大于上辊的速度时会导致带钢的翘头,反之会引起扣头;⑥轧制负荷分配不合理。
2.预防措施:①合理安排加热制度,保证钢坯的加热温度,上下表面的温差及芯部与外表面的温差≤30℃;轧制过程保持合理的轧制节奏,同时保证辊系的均匀冷却;②按照轧线标高与轧机垫板的工艺要求及时更换垫板;③保证粗除鳞、精除鳞的除鳞效果。
粗除鳞水压力≥16MPa,精除鳞水压力≥18MPa;④在轧制线标高满足要求的条件下采用上辊压。
3.处理方法:①减慢轧制节奏;②调整钢坯上、下表面加热温度的差值;③检查轧辊的冷却系统是否有堵塞现象;④重新调整各机架、各道次的负荷电流;⑤翘头严重时,要及时进行更换轧辊(调整辊压、轧制标高及适当降低出口上卫板的高度。
)二、料偏废钢1.产生的原因:①板坯的厚度不均,有侧弯等,或粗轧带坯来料不平直,进入精轧机组后导致带坯两侧的延伸不一致;②换辊后压靠、调平的精度不高,致使两侧辊缝存在较大的偏差;③压下手没有对带钢的料形变化及时地做出正确的调整;④导卫的开口度中心线不对中或开口度过大,致使带钢跑偏;⑤轧机的辊缝跑位,操作工对此确认不到位而没有及时调整导致料偏废钢;⑥辊身掉肉,压入带钢产生料偏;⑦轧辊车削精度不够,如轧辊的锥度、不圆度或三点差等超出工艺指标导致的料偏;⑧轧线上存留杂物,如扳手、调平用的盘圆等影响带钢穿带过程造成料偏。
轧钢培训

存在的问题 产能: 地位:国内相对领先地位 设备:70穿孔机、两台减径定径机 资源配置
• 主要设备有定尺冷剪、成品收集装置、打捆机、称重台架等。冷剪剪 切力4920kN,剪切次数10次/分,剪切开口度155㎜,剪刃宽度1000 ㎜;采用人工打捆,人工计数方式;称重台架称重范围为0~4t。
3、高线
A工艺流程 冷热坯上料→辊道输送→轧制→飞剪切头→预精轧机测长称重
→加热→出炉运输→ 粗轧轧制 →飞剪切头→中轧轧制→预水冷→飞剪切头→ 无扭精轧机轧制→水箱控冷→夹送、吐丝→散卷控制冷却 →集卷→运卷挂钩→P&F运输机运输→质量检查→头尾剪切、 取样→压紧打捆→盘卷称重→挂标签→卸卷→入库→发货
2、现阶段新钢铁轧钢系统能力(06年疏理) 90+65+55 前道工序能力:270万吨
一、全连轧生产线
全连轧是在半连轧车间成品跨内新建的一条生产线, 筹建于2002年5月,2003年9月20日一次性热负荷试车成 功,由北京科技大学高效轧制中心承担工厂设计,中国第 三冶金建筑公司承担土建、设备安装工作。主要产品以 Φ10-Φ40mm热轧圆钢、热轧带肋钢筋,其中Φ16-20㎜ 带肋钢筋采用二切分工艺,Φ16~40㎜圆钢及Φ22~40㎜ 带肋钢筋进行单线生产;原设计最大成品线速度16m/s, 年生产能力80万吨,07年实际产量82.6万吨。
3、轧钢系统演进
1、演进的两重要原因 a炼钢连铸技术的发展 b轧钢设备的进步 2、演进历程 a初轧机开坯,两火成材或三火成材 b横列式轧机向半连续、连续式轧机发展 c连铸连轧技术
二、新钢铁轧钢系统
1、新钢铁轧钢系统发展历程 a、横列式时代 650/500/230/小型/钎钢 b、改造后的革局:半连轧、窄带、高线、连轧
《轧钢工艺学》讲稿第二篇轧制工艺...

《轧钢工艺学》讲稿第二篇轧制工艺基础7 轧材种类及其生产工艺流程一、模铸和连铸模铸:将钢水浇铸在一个个钢锭模内,钢水冷却凝固后脱模成为钢锭,然后送到轧钢车,间,经加热后用初扎机(或开坯机)将其扎成多种规格的钢坯。
然后再经成品扎机扎成各种钢材。
这种生产方法知道仍在钢材生产中占着重要地位。
连铸:将钢水直接铸成一锭,断面形状和规格的钢坯连续铸钢生产过程见图1-1图1-1 连铸机的组成结构中间罐:贮存一部分钢水,保证连续铸刚,减小钢水注入后结晶时产生的冲击力稳定钢流和分流,分离钢水带下的炉渣和非金属夹杂物。
结晶器:无底水冷装置,强制钢锭迅速冷却,规定铸坯形状。
夹送辊:防止铸坯因为内部钢液静压力的作用产生“鼓肚”,对铸坯运动起导向作用。
拉娇机:拉辊:拉着钢坯向前运动。
娇直辊:对铸坯表面平整娇直。
模铸与连铸生产过程的比较图1—2。
连铸的优点:简化生产工序,连铸可直接得到一定断面形状的铸坯,省去了整模铸锭、脱模、均热、初扎开坯工序。
节约金属、成材率高钢锭头部有缩孔,扎材时必须切除,在钢锭模内钢液由下向上、由外向里凝固,体积缩小,最后在头部形成缩孔和疏松,在缩孔区存在有较多较大夹杂物,必须切除。
(1) 节能。
连铸省了一次加热一次扎材(2) 改善劳动条件,提高劳动生产率。
连铸自动化程度高,省去大量人力。
铸锭从整模、铸锭、脱模、初扎都穿插人工操作,自动化程度低,工人劳动条件差。
(3) 质量好。
与铸锭比,连铸坯内部组织均匀、致密、偏析少、性能稳定,表面缺陷少。
(4) 生产成本低。
(连铸设备简单,省去初扎机,均热炉,并节约了燃料动力和人力)缺点:(1) 生产小批量、多规格坯料不灵活。
(需更换结晶器,结晶器价格昂贵,连铸机设备较复杂,对管理和操作的技术水平要求较高,不适合经常更换)(2) 沸腾钢,高合金钢的连铸还有一定困难。
二 什么叫轧钢生产系统在组织生产时,根据原料来源、产品种类及生产规模的不同,将初扎机或连铸机与各种成品扎机配套设置,组成各种轧钢生产系统。
轧钢工应知培训
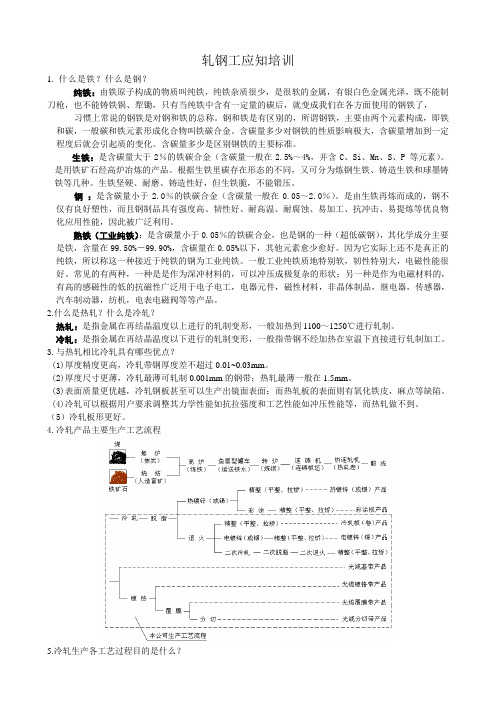
轧钢工应知培训1. 什么是铁?什么是钢?纯铁:由铁原子构成的物质叫纯铁,纯铁杂质很少,是很软的金属,有银白色金属光泽,既不能制刀枪,也不能铸铁锅、犁锄,只有当纯铁中含有一定量的碳后,就变成我们在各方面使用的钢铁了,习惯上常说的钢铁是对钢和铁的总称。
钢和铁是有区别的,所谓钢铁,主要由两个元素构成,即铁和碳,一般碳和铁元素形成化合物叫铁碳合金。
含碳量多少对钢铁的性质影响极大,含碳量增加到一定程度后就会引起质的变化。
含碳量多少是区别钢铁的主要标准。
生铁:是含碳量大于2%的铁碳合金(含碳量一般在2.5%~4%,并含C、Si、Mn、S、P 等元素)。
是用铁矿石经高炉冶炼的产品。
根据生铁里碳存在形态的不同,又可分为炼钢生铁、铸造生铁和球墨铸铁等几种。
生铁坚硬、耐磨、铸造性好,但生铁脆,不能锻压。
钢:是含碳量小于2.0%的铁碳合金(含碳量一般在0.05~2.0%)。
是由生铁再炼而成的,钢不仅有良好塑性,而且钢制品具有强度高、韧性好、耐高温、耐腐蚀、易加工、抗冲击、易提炼等优良物化应用性能,因此被广泛利用。
熟铁(工业纯铁):是含碳量小于0.05%的铁碳合金,也是钢的一种(超低碳钢),其化学成分主要是铁,含量在99.50%-99.90%,含碳量在0.05%以下,其他元素愈少愈好。
因为它实际上还不是真正的纯铁,所以称这一种接近于纯铁的钢为工业纯铁。
一般工业纯铁质地特别软,韧性特别大,电磁性能很好。
常见的有两种,一种是是作为深冲材料的,可以冲压成极复杂的形状;另一种是作为电磁材料的,有高的感磁性的低的抗磁性广泛用于电子电工,电器元件,磁性材料,非晶体制品,继电器,传感器,汽车制动器,纺机,电表电磁阀等等产品。
2.什么是热轧?什么是冷轧?热轧:是指金属在再结晶温度以上进行的轧制变形,一般加热到1100~1250℃进行轧制。
冷轧:是指金属在再结晶温度以下进行的轧制变形,一般指带钢不经加热在室温下直接进行轧制加工。
3.与热轧相比冷轧具有哪些优点?(1)厚度精度更高,冷轧带钢厚度差不超过0.01~0.03mm。
轧钢知识培训

轧钢知识培训一、轧机的机构、特点及调整1.闭口式轧机1)机构型式:二辊闭口牌坊式轧机,平立交替布置。
2)设备组成:轧机由机架牌坊、轧辊配置、十字轴式万向联轴器、压下装置、平衡装置、轴向调整装置、轧机轨道、导卫及导卫支架、轧机锁紧装置等组成;a.轧机锁紧装置——采用碟簧锁紧,液压打开。
机架在其底板上采用锁紧缸。
锁紧缸安装在轧机座上,轧机生产时或需要进行换辊操作时,由锁紧缸将其锁紧在轧机轨座上,当轧机需要横移时,液压动力将锁紧缸打开;b.传动装置——轧辊的传动装置是将主电机的转动和力矩传递给轧辊。
主传动装置由主电机、住减速机、十字轴式万向联轴器等部件组成;十字万向联轴器具有传动效率高,传动扭矩大、传递平稳、噪音低、使用寿命长、允许倾角大、适用于高速等特点。
c.接轴托架——水平采用气动驱动(立式采用液压缸)。
此接轴托架的作用是在换辊操作时拖住万向联轴器的法兰套,以便节省换辊时间,在轧机正常工作时,接轴托架与万向联轴器处于非接触状态;d.轴向固定与调整——轧辊轴向调整装置注意是保证两轧辊的孔型对正。
轧辊的轴向固定是采用操作侧的压板将轧辊轴承座固定在轧机上;e.径向调整——(闭口轧机)上轧辊的径向调整由压下装置来完成,下辊利用调整垫板来调整下辊与辊道水平面的相对位置,以保证轧制线高度一致。
(短应力轧机)压下时,上下辊同时向轧制线收拢;放辊缝时,上下辊同时向轧制线反方向放开。
共同调整方式:液压马达驱动、手动。
f.平衡装置——为了消除上轴承座与压下装置间的间隙,采用弹性胶体平衡装置,具有结构紧凑、操作简便、使用寿命长和换辊方便等优点。
g.导卫支架——采用旋转导卫支架,在轧机入口侧和出口侧设计旋转导卫支架。
导卫支架在更换轧辊时只需要旋转导卫底座旋转一定角度,轧机位置调整好后再旋回来即可,节省调整时间,使导卫调整更为方便;h.立轧机提升装置——是为了实现立轧机在垂直方向的横移,及轧机的换辊工作,立轧机提升装置采用螺旋升降机提升,螺旋升降机由变频电机驱动;轧辊冷却:采用半圆形喷管,装在旋转导卫上;轧机润滑:牌坊机架的轴承座采用手动加油;3)结构特点:机架牌坊是由一个整体框架,及闭口式牌坊,要有较高的强度和刚度,稳定性较好,安全可靠;2.短应力轧机1)短应力轧机特点:a.轧机应力线短,刚度大;b.重量轻,约为同规格闭口轧机重量的一半;c.轧辊有轴向微调装置,可精确进行轴向错辊调整;d.轧辊采用对称调整,轧制线恒定不变;e轴承座没有液压平衡装置;f.换辊和换槽时,液压横移,弹簧锁紧;g.换辊通过工作机座来实现;h.辊缝和导卫可以在备用轧机时提前调好;j.辊系加工要求较高,且需要备用轧机。
轧钢工艺规程培训PPT课件
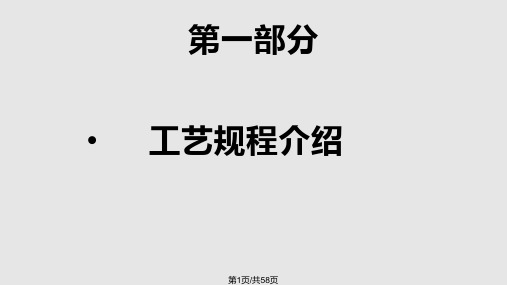
420
650 ~80
650 ~80
650 ~80
650 ~80
±3
800
700/ 1400
±3
800
700/ 1400
±3
800
700/ 1400
±3
800
700/ 1400
第16页/共58页
7.3、精轧轧机组参数
机架 号
13
轧机规格(mm)
380
新辊直径(mm)
380
可利用的 最小辊径(mm)
330
• 1) 连铸坯无明显扭转; • 2)连铸坯弯曲度不能大于20mm/m,总弯
曲度不大于总长的2%; • 3)边长允许偏差:±5.0mm; • 4)对角线长度之差:≤7.0大于12mm;
• 7) 连铸坯端部因剪切变形造成的宽展不 得大于边长的10%;
第24页/共58页
飞剪工作时速度、剪切方式和是否带飞轮参数见下表
轧件 轧制速度 刀片回 是否带 (mm) (m/s) 转方式 飞轮
Φ30Φ50.7
4.1—7.2
回转剪
否
第25页/共58页
9.3、倍尺飞剪
• 功能:将棒材按倍尺长度分段剪切。 • 型式:启停制回转/曲柄组合剪。 • 主要参数: • 剪切断面:Φ10×4~Φ50mm • 棒材速度:max.16.0 m/s • 棒材钢种:普碳钢、低合金钢和优碳钢等 • 螺纹钢剪切温度:≥550℃ • 其它棒材温度:≥950℃ • 倍尺公差:±150 mm • 电机:DC418 kW • 输出转速:530r/min
420
650
650
~80 ~80
800
800
电机转速 基速/ 700/14 700/
轧钢工艺培训教学讲义轧钢基本知识.
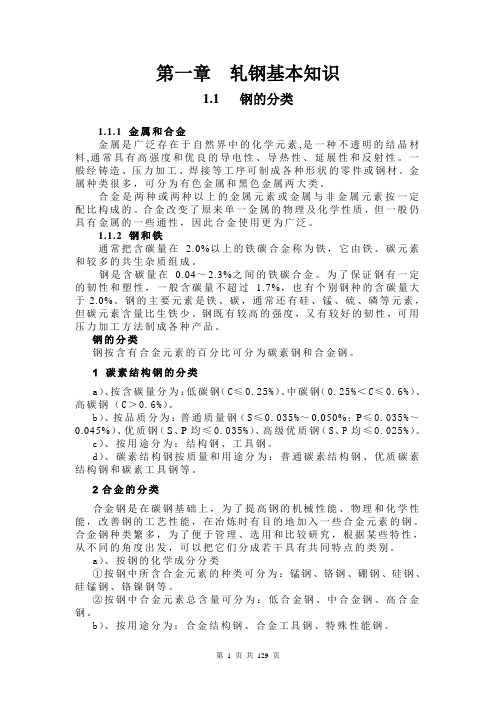
第一章轧钢基本知识1.1 钢的分类1.1.1 金属和合金金属是广泛存在于自然界中的化学元素,是一种不透明的结晶材料,通常具有高强度和优良的导电性、导热性、延展性和反射性。
一般经铸造、压力加工、焊接等工序可制成各种形状的零件或钢材。
金属种类很多,可分为有色金属和黑色金属两大类。
合金是两种或两种以上的金属元素或金属与非金属元素按一定配比构成的。
合金改变了原来单一金属的物理及化学性质,但一般仍具有金属的一些通性,因此合金使用更为广泛。
1.1.2 钢和铁通常把含碳量在 2.0%以上的铁碳合金称为铁,它由铁、碳元素和较多的共生杂质组成。
钢是含碳量在0.04~2.3%之间的铁碳合金。
为了保证钢有一定的韧性和塑性,一般含碳量不超过 1.7%,也有个别钢种的含碳量大于2.0%。
钢的主要元素是铁、碳,通常还有硅、锰、硫、磷等元素,但碳元素含量比生铁少。
钢既有较高的强度,又有较好的韧性,可用压力加工方法制成各种产品。
钢的分类钢按含有合金元素的百分比可分为碳素钢和合金钢。
1 碳素结构钢的分类a)、按含碳量分为:低碳钢(C≤0.25%)、中碳钢(0.25%<C≤0.6%)、高碳钢(C>0.6%)。
b)、按品质分为:普通质量钢(S≤0.035%~0.050%;P≤0.035%~0.045%)、优质钢(S、P均≤0.035%)、高级优质钢(S、P均≤0.025%)。
c)、按用途分为:结构钢、工具钢。
d)、碳素结构钢按质量和用途分为:普通碳素结构钢、优质碳素结构钢和碳素工具钢等。
2合金的分类合金钢是在碳钢基础上,为了提高钢的机械性能、物理和化学性能,改善钢的工艺性能,在冶炼时有目的地加入一些合金元素的钢。
合金钢种类繁多,为了便于管理、选用和比较研究,根据某些特性,从不同的角度出发,可以把它们分成若干具有共同特点的类别。
a)、按钢的化学成分分类①按钢中所含合金元素的种类可分为:锰钢、铬钢、硼钢、硅钢、硅锰钢、铬镍钢等。
②按钢中合金元素总含量可分为:低合金钢、中合金钢、高合金钢。
轧钢知识调度培训讲稿提纲

主要内容▪轧钢的基本知识。
▪工艺部分,热轧的常规工艺分为四大块:加热、轧钢、精整、成品。
▪设备部分,重点讲加热炉、轧钢机。
▪高线厂生产调度系统。
第一节:轧钢生产的基本知识▪轧钢的优点▪钢材的分类钢材竞争力:各种功能结构材料的价格轧钢生产的优点▪生产率高▪品种多▪连续性强▪自动化程度高钢材的分类▪钢板▪钢管▪型钢▪其它钢板▪特厚板:60mm以上,有200mm的板▪厚板:20~60mm▪中板:4~20mm▪薄板:2~4▪带钢:0.2~2▪箔材:0.2mm以下,最薄0.001mm钢管▪无缝钢管:应用范围日趋缩小▪直缝焊管:应用范围日趋广泛▪螺旋焊管:大口径▪冷轧钢管:精密轧制的方向型钢▪常用型钢:方钢/扁钢/圆钢/工字钢/角钢/槽钢/H型钢▪专用型钢:钢轨/钢桩/窗框钢其它▪钢球/齿轮/丝杠/车轮/轮箍/变截面轴/异型板簧▪少切削和无切削,有发展前途轧钢工艺流程▪加热▪轧钢▪精整▪成品第二节:高线生产工艺流程第三节:加热部分三座加热炉全貌加热工序加热炉的分类▪按烧的燃料分:✓燃煤加热炉:烟煤、褐煤等煤粉✓燃油加热炉:重油、焦油、柴油✓燃气加热炉:焦炉煤气、高炉煤气、转炉煤气、发生炉煤气加热炉的分类▪按钢坯运动方式分类✓推钢式✓步进式✓环形加热炉蓄热式步进梁加热炉优点▪烧高炉煤气的优点✓可大幅度降低轧钢工序的加热成本。
✓减少环境污染,有利于建立循环经济和绿色工业。
▪步进式加热炉的优点✓四面受热,加热均匀。
✓加热效率高,可缩短加热炉的长度。
蓄热式步进梁加热炉缺点▪操作维护复杂,要求高。
▪投资大。
▪每10~12个月必须停一次。
换向原理:排气换向原理:吸气换向注意问题▪三通换向阀是加热炉燃烧系统的重要设备,其工作正常才能保证强炉温和炉压。
▪换向时间的长短决定排烟温度和气体的预热温度。
两位三通换向阀第四节:轧钢部分轧钢机的分类▪板带轧机以辊身长度标称。
如1580轧机,精轧机辊身长度是1580mm.▪型钢轧机以轧辊名义直径标称,即减速机输出齿轮的节圆直径。
轧钢工艺培训(技师培训)
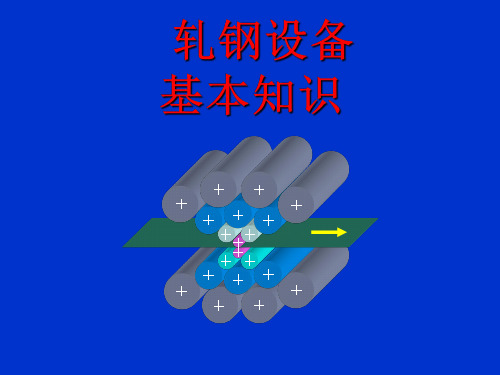
型钢轧机工作机座简图
1.5 常见辅助设备结构特点和作用
1.6 轧钢机的标称
标称内容:(1)产品类别(2)辊身尺寸(3)轧辊数目 (4)轧机台数(5)轧机布置(6)轧机工作制度
(1)钢坯和型钢轧机: 用轧辊名义直径标称。因为它与能够轧制的最大断面尺寸有关。 如果在一个轧钢车间中装有若干列或有若干架轧机时,则以最后一架精轧机的轧辊名
(2)横轧机
1.2.3按轧钢机的布置形式分类 (1)单机座式轧机
(2)横列式轧机
(3)纵列式轧机
(4)半连续式轧机
(5)连续式轧机
(6)串(顺)列往复式(跟踪式、越野式)轧机
(7)布棋式轧机
(8)复二重式轧机
1.4 主机列的构成及各部分的作用
二辊冷轧机
飞轮:轧制时,冲击负荷作用下,系统减速,负载的一部 分有飞轮放出储存的动能来克服。轧件轧出后(空载), 负载突减,主电机带动飞轮加速,飞轮储存能量。
义直径作为轧钢机的标称。 例:1150二辊可逆初轧机
800三辊可逆/760×2三辊/650二辊两列横列式大型型钢轧机
(2)钢板轧机 用辊身长度标称,因为与能够轧制的钢板的最大宽度有关。
例: φ100/φ400×500四辊可逆冷轧板带轧机 1700二辊可逆/1700四辊可逆/1700×2四辊轧机/1700×7四辊连轧热带钢轧机
PC轧机
CVC轧机
CBS轧机
行星轧机
1.3.2.2 具有垂直轧辊的轧机和万能轧机 (1)立辊式轧机
(2)二辊万能式轧机
(3)H型钢轧机
(4)平立式轧机组
1.3.2.3轧辊倾斜布置的轧机 (1)斜辊式轧机
(2)450式轧机
(3)150/750式轧机
(4)三辊Y型轧机
轧钢基础知识讲座
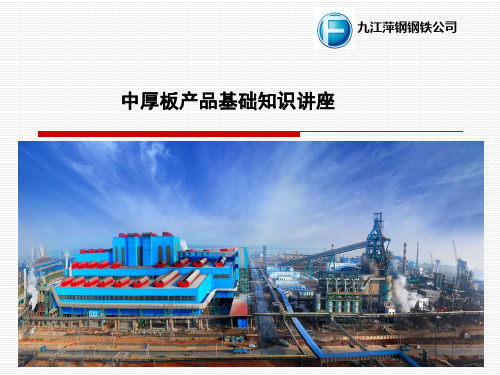
中厚板产品基础知识讲座
九江萍钢钢铁公司
目录
一. 中厚板产品概述
二. 产品牌号、执行标准知识说明
三. 轧钢生产基本问题
四. 钢坯和型、线材生产
五. 板带材生产
六. 钢管生产
九江萍钢钢铁公司
金属压力加工的方法
★金属压力加工: 金属在受到外力作用并不破坏自身完整性的条件下, 稳定改变其几何形状与尺寸,从而获得所需要的几何形状与 尺寸的加工方法。 ★金属压力加工的分类: 靠压力作用使金属产生塑性变形:锻造、轧制、挤压; 靠拉力作用使金属产生塑性变型:拉拔、冲压等。
宝钢5m轧机采用世界最先进工艺与设备。
序 号
企业 合计
轧机规格及型式 粗轧机 精轧机 23 3套 4200四辊 20 套 2350二辊 2300二辊 2800二辊 2350二辊 2350二辊 2400四辊 2350三辊劳特 2400三辊劳特 3200四辊 2450四辊 ?二辊 2350三辊劳特 2400三辊劳特 2300三辊劳特 2350四辊 2300四辊 3500四辊 3500 四辊 3000四辊 2450四辊 2300四辊 2400四辊 2350四辊 2500四辊 3500四辊 3000四辊 2700 四辊 3000四辊 3500 四辊 2500四辊 2500四辊 2800四辊 2800四辊 2500 四辊 2300三辊劳特 2300三辊劳特 4200四辊 3500四辊 4300四辊
预 精 轧
剪 头
精 轧
水 冷
吐 丝
空 冷
集 卷检 验包 装来自称重 挂牌卸 卷
入 库
九江萍钢钢铁公司
2) 线材轧机的布臵形式
a-横列式人工操作
九江萍钢钢铁公司
b-二列式围盘操作
- 1、下载文档前请自行甄别文档内容的完整性,平台不提供额外的编辑、内容补充、找答案等附加服务。
- 2、"仅部分预览"的文档,不可在线预览部分如存在完整性等问题,可反馈申请退款(可完整预览的文档不适用该条件!)。
- 3、如文档侵犯您的权益,请联系客服反馈,我们会尽快为您处理(人工客服工作时间:9:00-18:30)。
轧钢培训讲稿一、轧制原理1.冷轧变形轧制过程其实就是钢板发生塑性变形的过程。
在轧制过程中钢带和轧辊相互作用,钢带受轧辊作用产生塑性变形(当然也伴有微小的弹性变形),而轧辊受钢带的作用产生弹性变形。
钢带的塑性变形和轧辊的弹性变形是一个问题的两个方面。
在技术上要求钢带应尽可能产生大的塑性变形,轧辊应产生尽可能小的弹性变形,然而钢带塑性变形愈大,压力愈大,则轧辊的弹性变形愈大。
3、乳液皂化值是指皂化1克油品所需氢氧化钾的毫克数,单位为mgKOH/g。
它的高低代表轧制油的润滑性能的好坏,皂化值越高,轧制油的润滑性能好,但轧后退火板面清洗性也随之变差。
皂化值反映轧制油的润滑能力。
酸值:是表征油品中有机酸中含量多少的指标。
一般情况下,酸值越高,乳化液pH值越低。
PH值是指一定浓度的产品在指定水质中的酸碱度。
测试温度对其有一定的影响。
其是判断油品老化速度,以及氧化变质程度的一个重要指标。
ESI值是指乳化液的稳定性能。
在乳化液中,ESI越高,乳化液稳定越高,离水展着性相对变低。
颗粒度:乳化液中油滴的颗粒直径。
主要是对其润滑性和热稳定性产生影响。
一般而言,较大粒径有利于乳化液受热时油水两相分离,轧辊和轧件表面吸附油量增加,降低轧制变形区的摩擦系数。
然而,若颗粒度过大,容易造成乳化液不稳定,严重的会使乳化液油水分离影响乳化液的使用效果和使用周期。
正常新配置的乳化液平均粒径小于1цm,随着时间的增加,乳化液的粒径逐渐粗化长大,反映在轧制过程中可能出现咬入困难、钢带跑偏、打滑等情况。
为了解决乳化液的稳定性和润滑性能的矛盾,可在乳化液中加入分散剂。
各指标关系浓度提高,颗粒度会有所增加,但主要取决于温度和乳化液循环时间。
乳化液稳定性(ESI)主要与温度有关,温度提高,乳化液稳定性有所降低。
酸值等由于水解或酸洗挟带后会降低,导致ESI下降,电导率、氯离子和pH 变化会导致ESI升高或降低,与乳化液类型或污染来源有关。
灰分与铁含量、电导率及杂油含量相关,电导率和铁含量越高,灰分越高。
灰分与铁粉的比值一般在2-3之间,超出此范围需要注意。
乳化液的润滑性能在轧钢过程中,在一定的温度和压力条件下,分散于乳化液中的轧制油以物理吸附和化学吸附两种方式吸附于钢板和轧辊表面形成油膜,为轧制提供必要的润滑。
作为轧制油或乳化液的最基本的功能,油品润滑的设计和应用水平,对冷轧工序最终结果有着决定性的影响。
良好的润滑可以达到如下目的:节能:–良好的润滑可有效降低摩擦力–良好的挥发性可降低退火时间降低辊耗改善板形:–好的润滑有利于板形控制–好的润滑可降低厚度波动–好的润滑有利于表面结构提高板面清洁度及改善板面状态:–轧后板面的反射率–轧后及退火后的板面残留–减少板面划伤正常平稳的轧制需要轧制油提供均衡稳定的润滑,即轧制油除必须保证稳定的物理和化学特性外,还必须保持数量上的,即吸附量的稳定。
乳化液的冷却性能轧制过程中钢板发生变形所产生的大量的热,也需要由乳化液带走,正确控制乳化液的流量和喷射部份,可以有效控制板温,并调节板形。
在应用乳化液的冷却功能时,除板温的控制外,可以通过乳化液流量的位置的控制,使轧辊的不同部份产生不同程度的热胀冷缩,达到控制板形的目的。
乳化液的冷却性能与油品没有直接联系,是一种物理现象。
冷却性能与现场应用的喷射流量密切相关。
乳化液的冷却性能与油品的应用浓度成反比,浓度越高,冷却能力越低。
提高油品的净油润滑能力,使乳化液可以在较低的浓度下应用,一定程度上有利于提高乳化液的冷却性能。
乳化液的清洗性能乳化液的清洗主要包括对板面进行清洗,对轧辊和机架进行清洗。
在轧制过程中,除轧辊与钢板摩擦产生铁粉外,还会产生各种高粘性的铁皂体、油品在高温高压下产生的聚合物。
这些异物是影响板面清洁度的主要因素。
另外,轧机所使用的各种油膜轴承油和液压油,也会在钢板表面部份残留,或在乳化液应用过程中进一步聚合,污染板面。
控制乳化液的清洗性能,一方面,取决于乳化液本身的设计特性;另外,乳化液的各项指标如皂化值(杂油含量)的控制也是非常关键的。
一般来说,增加轧制油中表面活性剂的含量,会提高乳化液的清洗能力,但这同时会提高油品的稳定性,降低油品的的润滑能力。
因此,不能孤立地看待油品的清洗能力。
3. 3皂化值与润滑性和清洁性油品的皂化值对其润滑性和清洁性有很大的影响。
矿物油系水溶性轧制油,其皂化值小于100mg.KOH/g,具有良好的清洁性,但润滑性差,可用于轧制表面光洁的0.8毫米以上薄板,脂肪系轧制油皂化值大于150mg.KOH/g,润滑性好,可用于轧制0.3毫米以下的薄板,但使用中表面残碳较多,影响清洁性,所以在退火前钢板要清洗干净,皂化值为100时,既能保证轧制过程润滑性,又能保持钢板清洁性而省去清洗工序。
薄件高速轧制选择高皂化值,厚件低速选择低皂化值。
二、板形控制1、板形的定义板形是板带材平直度的简称,一般是指浪形的有无及存在程度。
如果钢带各横截面的中性线不位于一水平面内,就出现了不平直的缺陷,称为板型缺陷,或称为平直度不良。
冷轧常见的板形缺陷有边浪、中浪、四分浪、复合浪等。
严格来说,板形又可分为视在板形与潜在板形两类。
所谓视在板形,就是指在轧后状态下即可用肉眼辨别的板形;潜在板形是在冷轧带钢轧机上,由于张力的作用,带钢被拉直,轧制时看不出板形缺陷,在后部加工工序一旦张力被解除,板形缺陷才显露出来,于是便称这种轧后钢板具有潜在板形缺陷。
2、辊形控制1)调温控制法:即调节沿辊身长度上的温度分布。
如果辊身长度方向分段冷却轧辊,改变各段冷却液的数量和温度,便可改变轧辊的热凸度,从而也就改变了轧辊实际凸度,达到调整辊型的目的。
此方法的优点是采用的设备和控制方法都很简单,但它的调整速度很慢,惯性大,不能满足高速轧制的要求,且不能经常保持轧辊热凸度对称性和稳定性。
2)弯辊控制法。
即采用液压弯辊装置,调节轧辊挠度改变轧辊实际挠度。
当采用这种方法时,轧辊(工作辊或中间辊)两端受一附加的弯曲力作用,可加大或减小轧辊在轧制过程中所产生的挠度使轧辊实际挠度自动或人工地保持在最佳数值上。
液压弯辊的突出优点是快速、准确、能满足高速度、高精度轧制的要求,实现板形自动控制。
能使一种辊型适应多种规格的生产,便于磨辊,减少了换辊次数,提高了作业率。
3)采用高性能轧辊凸度控制轧机,如HC轧机,该轧机在工作辊与支承辊间有能作轴向移动的中间辊。
两个中间辊的移动是对称的,但方向是相反的。
工作辊上有调节辊型用的液压弯辊装置。
该轧机能够根据被轧板材的宽度设定中间辊的移动量。
这样,工作辊和中间辊在板宽的外侧有一端不接触,消除了工作辊的附加弯曲,因而使工作辊弯辊效果更为显著,提高了辊型调节的灵敏度.3、影响板形因素带钢的横向厚度差取决于轧辊在轧制时辊缝的实际大小及形状,带钢的板形则取决于钢带沿宽度方向上延伸的均匀程度。
因此,横向厚度和板形是两个不同的概念。
但无论是横向厚度差方面的缺陷或板形方面的缺陷,其根源都在于带钢在轧制过程中的不均匀变形(不均匀的压下与不均匀的延伸),实质是带钢内部残余应力的分布。
可见,横向厚度差与板形有着内在的关系。
因此,通过调整辊缝形状可以达到减小带钢的横向厚度差和改善板形质量的目的。
在冷轧过程中,由于带钢的宽展很小几乎可以忽略不计。
因此,压下变形基本都转为沿钢带长度方向上的延伸。
在实际生产中,经常会碰到这样一个情况,即有时轧出带钢板形良好但厚度超出偏差,为了保证带钢横断面厚度偏差值,板形方面的要求又可能满足不了,造成这种局面的根本原因就是原料断面厚度的不均匀。
3.1影响板形因素及控制影响板形不良的原因在于带钢在轧制过程中沿宽度方向上各处的不均匀延伸。
板形缺陷的产生,除了原料的厚度不均匀等因素外主要是轧辊的辊缝变化。
因此,板形的控制基本上可以说是辊形的控制,而辊形的控制系指对实际轧制时工作辊缝形状的控制。
带钢在冷轧过程中,其横断面上各点的厚度取决于轧辊在轧制时的实际辊缝;其平直度则取决于各部分延伸的均匀程度,这同样也取决于轧制时的实际辊缝的形状与大小。
由于轧辊的弯曲而沿带钢宽度方向辊缝发生变化,使轧出的带钢沿宽度方向变的不均匀,这就导致带钢板形的不良,而轧辊的弹性变形、辊温的变化及轧辊的磨损是使轧辊弯曲、使其实际工作辊缝发生变化的主要因素。
特别是轧辊的磨损,每时每刻都在[破坏着正常的辊形,使辊缝发生不均匀的变化。
归结起来,影响辊缝形状的因素主要有以下几点:ⅰ轧辊的弹性弯曲变形从变形方面来看,如果轧制用的轧辊加工成严格的圆柱形,那么在不过钢时,辊缝显然是平行的。
在轧制带钢时,由于轧制压力的作用,轧辊将产生弹性变形。
这些弹性变形沿辊身长度方向是不均匀分布的,结果使轧制时的实际辊缝沿辊身长度方向不均匀,所轧出的钢带断面形状沿辊身长度方向自然也是不均匀的。
导致钢带产生浪形。
通常,轧制压力越大,轧辊的弹性弯曲变形越大;轧辊直径越大,刚性就越好,则轧辊的弹性弯曲变形越小。
ⅱ轧辊的热膨胀冷轧生产过程中,带钢的变形主要是压下与延伸变形,厚度方面的压下几乎全部变成纵向的延伸。
在变形过程中,带钢将产生大量的变形热,带钢在轧制中产生的变形热是主要的热源。
由于这种变形热使轧辊热膨胀而改变原始辊形,实测表明,辊身各部分的温度并不一致,由此引起的温度差将导致轧辊直径的热膨胀差。
在多数情况下,辊身中部的温度将高于其边部的温度,此时,假如轧辊由于热膨胀所形成的凸度其值正好与轧辊产生的弹性弯曲所形成的凹度值相互补偿,则辊身就能保持圆柱形,这时沿带钢横断面各处的压下将都是一样的,那么带钢各点的延伸也就都相同(原料厚度各点都相同的情况下),轧出的带钢板形自然是良好的;如果轧辊的弹性弯曲所形成的凹度值大于轧辊热膨胀凸度值,则带钢两边的压下将比中间大,那么带钢两边的延伸变形也相应的要大些,即比中间部分伸长要大些;换一种情况,如果轧辊的弹性弯曲所形成的凹度值小于轧辊热膨胀,则带钢中间部分的延伸大于两边部分的延伸。
可见,轧辊由于热膨胀所形成的凸度不管其大小都将影响原始辊缝形状。
ⅲ轧辊的磨损随着轧辊在换辊以后工作时间的逐渐增长,工作辊与带钢之间、工作辊与支撑辊之间由于摩擦会使轧辊磨损,轧辊的磨损使辊缝形状渐渐的变的不规则起来。
影响轧辊磨损的因素也是多方面的。
例如,轧辊与带钢的材质、轧辊表面硬度和光洁度、轧制压力和轧制速度。
前滑和后滑的大小以及中间辊(支承辊)与工作辊之间的滑动速度都会影响轧辊磨损的快慢;另外,沿辊身长度方向轧辊磨损也是不均匀的,这些都将影响辊缝的实际形状。
ⅳ轧辊的弹性压扁轧制时由于轧制压力的作用,带钢与工作辊之间、工作辊与支撑辊之间均会产生弹性压扁。
影响辊缝形状的不是轧辊的弹性压扁的数值,而是压扁值沿辊身长度方向的不同大小,对于工作辊来说,如果轧制压力沿带钢宽度是均匀分布时,则工作辊的弹性压扁分布也是均匀的。