铜基甲醇合成催化剂失活原因的探讨
甲醇合成催化剂失活分析
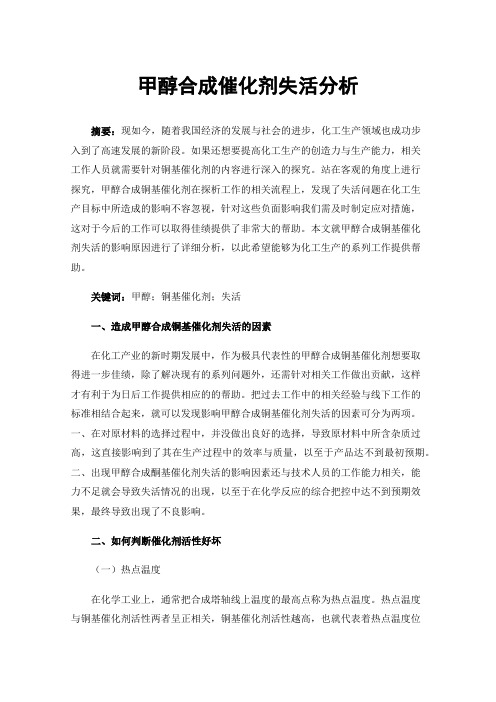
甲醇合成催化剂失活分析摘要:现如今,随着我国经济的发展与社会的进步,化工生产领域也成功步入到了高速发展的新阶段。
如果还想要提高化工生产的创造力与生产能力,相关工作人员就需要针对铜基催化剂的内容进行深入的探究。
站在客观的角度上进行探究,甲醇合成铜基催化剂在探析工作的相关流程上,发现了失活问题在化工生产目标中所造成的影响不容忽视,针对这些负面影响我们需及时制定应对措施,这对于今后的工作可以取得佳绩提供了非常大的帮助。
本文就甲醇合成铜基催化剂失活的影响原因进行了详细分析,以此希望能够为化工生产的系列工作提供帮助。
关键词:甲醇;铜基催化剂;失活一、造成甲醇合成铜基催化剂失活的因素在化工产业的新时期发展中,作为极具代表性的甲醇合成铜基催化剂想要取得进一步佳绩,除了解决现有的系列问题外,还需针对相关工作做出贡献,这样才有利于为日后工作提供相应的的帮助。
把过去工作中的相关经验与线下工作的标准相结合起来,就可以发现影响甲醇合成铜基催化剂失活的因素可分为两项。
一、在对原材料的选择过程中,并没做出良好的选择,导致原材料中所含杂质过高,这直接影响到了其在生产过程中的效率与质量,以至于产品达不到最初预期。
二、出现甲醇合成酮基催化剂失活的影响因素还与技术人员的工作能力相关,能力不足就会导致失活情况的出现,以至于在化学反应的综合把控中达不到预期效果,最终导致出现了不良影响。
二、如何判断催化剂活性好坏(一)热点温度在化学工业上,通常把合成塔轴线上温度的最高点称为热点温度。
热点温度与铜基催化剂活性两者呈正相关,铜基催化剂活性越高,也就代表着热点温度位置越高。
在其床层的上方位置反应物的浓度可以达到最高值,生成物的浓度相反确是最低点,这时所形成的运动反应是最剧烈的,铜基催化剂的温度也因此呈持续上升趋势。
当到达温度巅峰值后,生成物的浓度增加反应物的浓度降低,反应进程开始减慢。
反应的生成物热量被带走,床层的温度逐渐降低。
(二)铜基催化剂床层温差铜基催化剂的床层温度变化过大,就会造成部分床层温度达不到铜基催化剂活性温度的状况出现,这就会出现变化反应都集中在局部活性温度达标的地点,从而释放热量,因此化学反应越剧烈就会带动床层温度变化越大,铜基催化剂的活性温度也就因此变得更好了。
甲醇合成铜基催化剂催化活性及失活研

甲醇合成铜基催化剂催化活性及失活研究1引言甲醇是一种极其重要的化工原料,主要用于生产一系列化工产品,还可用作潜在的车用醇醚燃料电池的燃料等。
随着甲醇制烯烃等技术进步及下游产品的开发,特别是甲醇燃料电池的开发和应用,合成甲醇的研究越来越受到广泛重视。
目前,甲醇的工业生产主要是采用CO/CO2催化加氢技术,所以甲醇合成催化剂的研发是甲醇合成工业的基石。
甲醇工业的发展很大程度上取决于催化剂的研制及其性能改进。
在甲醇生产中,很多工业指标和操作条件都是由催化剂的性质决定的。
随着甲醇工业的快速发展,对甲醇合成催化剂的研究开发提出了更高的要求。
2 甲醇合成催化剂在甲醇合成过程中,催化剂的重要性显而易见,目前工业上使用的甲醇合成催化剂一般可分为锌铬催化剂和铜基催化剂两类。
国外比较有名的研究和生产甲醇合成催化剂公司主要有英国ICI公司、德国BASF公司、德国SudChemie公司和丹麦TopsΦe公司等,国内研究铜基催化剂的院所主要有南化集团研究院、西南化工研究设计院,西北化工研究院及齐鲁石化研究院等[1]。
锌铬(ZnO/Cr2O3)催化剂由德国BASF公司于1923年首先开发研制成功。
操作温度必须在590 K~670 K,操作压力必须为25 MPa~35MPa,锌铬催化剂的特点是:耐热性能好、对硫不敏感,机械强度高,使用寿命长,使用范围宽,操作控制容易,但是其活性低、选择性低、产品中杂质复杂,精馏困难。
铜基催化剂由英国ICI公司和德国Lurgi公司先后研制成功,操作温度为210℃~300℃,压力为5MPa~10MPa,比传统的合成工艺温度低得多,对甲醇反应平衡有利。
其特点是:活性好,单程转化率为7%~8%;选择性高,大于99%,易得到高纯度的精甲醇;耐高温性差,对合成原料气中杂质比较敏感。
目前工业上甲醇的合成主要使用铜基催化剂。
近年来,新型催化剂的研制也在一直进行,新型催化剂的研制方向在于提高活性,改善热稳定性及延长催化剂使用寿命等,如钯系、钼系及低温液相催化剂,但这些催化剂因活性不理想或对甲醇的选择性较差,还只停留在研究阶段未实现工业化。
探究甲醇合成催化剂失活的影响因素

探究甲醇合成催化剂失活的影响因素甲醇,化学式为CH3OH,是一种重要的有机化合物,也是工业上常用的化工产品之一。
甲醇的合成催化剂失活是一个值得探究的重要问题,因为催化剂的失活将影响甲醇生产的效率和成本,进而影响整个工业生产系统的稳定性和经济性。
本文将从催化剂的物理性质、化学环境和操作条件三个方面探讨影响甲醇合成催化剂失活的因素。
一、催化剂的物理性质甲醇合成催化剂通常采用氧化锌和铜的复合物作为主要成分,同时也包括少量的铬、铝等元素。
催化剂的物理性质对其失活有重要影响。
催化剂的比表面积是一个重要的影响因素。
催化剂的比表面积越大,其活性部位的数量也就越多,有助于提高反应速率;而当催化剂富含表面缺陷时,也会导致活性部位的数量减少,催化剂的失活会更快。
催化剂的晶型和结构对其失活也有重要影响。
晶相的变化和结构缺陷的产生都会导致催化剂性能的下降,进而影响甲醇合成反应的进行。
催化剂的热稳定性和耐磨损性也是影响其失活的重要因素。
热稳定性差、易受磨损的催化剂会更快失活。
二、化学环境化学环境是催化剂失活的另一个重要因素。
气体组成、温度、压力等化学环境的变化都会导致催化剂的失活。
反应气氛的气体组成对催化剂失活有重要影响。
在甲醇合成反应中,如果反应气氛中存在大量的氧化物、硫化物等杂质,就会导致催化剂受到中毒,失去活性。
温度和压力也会影响催化剂的活性和稳定性。
过高的温度会导致催化剂的晶相变化、结构热膨胀等,都会导致催化活性下降;而过高的压力也会导致催化剂的失活。
三、操作条件总结来看,催化剂的物理性质、化学环境和操作条件是影响甲醇合成催化剂失活的重要因素。
为了提高催化剂的稳定性和活性,需要综合考虑这些因素,并进行合理的设计和优化。
只有在严格控制这些因素的前提下,才能有效减缓催化剂的失活速度,提高甲醇合成反应的效率和产量,进而促进相关工业的发展和进步。
探究甲醇合成催化剂失活的影响因素

技术与信息82 | 2019年2月物质之间吸附力的差别来形成不同的色层,同时使物质在移动的过程中,利用亲合力不同来使之得到明显的分离,并且进行溶液萃取。
3.2 工业化色谱分离制取维生素E的特点工业化色谱分离技术制取维生素E 的最大特点就是其成低,纯度高。
工业化色谱分离技术在生产高纯度维生素E 产品中优势明显。
其工艺回收率也相对较高。
同时,色谱分离技术的应用使生产不存在溶剂回收,分子量范围控制,能量成本以及回收率等一系列的问题。
3.3 工业化色谱分离工艺和分离装置的种类分析3.3.1 单塔式分离法单塔式分离方法是液相色谱分析法在工业化的应用。
虽然这种单塔式的工艺在建设费用方面相对较低,但是相应的它的分离纯度和分离效率也有所降低。
仅限于有独立峰值的部分能够进行分离,并且在峰值重叠的部分的纯度是存疑的。
3.3.2 模拟移动床分离装置模拟移动床分离装置是当前工业生产高纯度维生素E 的最常用分离装置,其中填充剂应用是一份十分重要的工作。
可以在分离过程中利用充填剂和溶离液互为逆流接触,使另一成分向下方排出,同时可以利用溶液的流速,充填剂的移动速度和流出量等条件来进行纯度高的成分提取,并且使所产生的两种成分进行可连续的分离,这其中充填剂移动环节就是模拟移动床的应用效果的体现。
3.3.3 改良型模拟移动床分离装置模拟移动床可以保持相对较高的分离精度和分离效率,但是需要的床数量较多,不利于装置系统的自动化控制。
而经过改良以后,以四槽式构成,整体设备制造费用相对较低且更利于控制。
3.4 色谱分离生产高纯度维生素E技术色谱分离生产的技术主要是以分子蒸馏工艺的基础为下层建筑,并且利用色谱分离法做出进一步的提纯,这是一种在传统分子蒸馏工艺基础上,利用模拟移动层色谱分离法进行分离的工艺,分离以后,产品纯度能够达到95%以上。
4 结语维生素E 作为一种脂溶性维生素,对于人体的生理机能具有重要的作用。
本文介绍了维生素E 产品的新型生产技术。
_甲醇合成催化剂使用效果的影响因素及对策

第31卷第3期2010年6月化学工业与工程技术J o ur nal o f Chemical I ndus tr y&EngineeringV ol.31N o.3Jun.,2010收稿日期:2010-03-28作者简介:薛守标(1970-),男,回族,江苏高邮人,本科,工程师,现从事新材料研发工作。
E-mail:xueshoubiao@甲醇合成催化剂使用效果的影响因素及对策薛守标(南化集团研究院,江苏南京 210048) 摘要:介绍了甲醇合成催化剂的制造及使用过程,探讨了催化剂的失活方式及其机理,提出防止或消除这些因素、延长甲醇合成催化剂寿命的方法。
关键词:甲醇合成;催化剂;使用;对策中图分类号:T Q426 文献标识码:A 文章编号:1006-7906(2010)03-0050-05Affecting factors and countermeasures of the application effectof methanol synthesis catalystXU E S houb iao(Research Institute o f Na njing Chemical Industrial G ro up,N anjing210048,China)A bstract:T he manufacture and a pplica tion pr ocess of methano l synthesis catalyst are presented,and the deactiva tion ma n-ner s and mechanisms are discussed.T he co untermeasures fo r preventing o r removing the affecting f ac to rs and pro lo ng ing the li-fetime of methano l synthesis ca taly st a re put fo rw ard.Key words:M etha no l synthesis;Cataly st;A pplicatio n;Co unter measure s 自20世纪60年代英国ICI公司成功推出合成甲醇的铜基催化剂以来,甲醇工业得到迅速发展。
甲醇合成催化反应机理及催化剂失活因素分析

甲醇合成催化反应机理及催化剂失活因素分析摘要:在甲醇生产过程中,甲醇合成催化剂常会发生中毒、高温烧结、失活等现象,大大影响了甲醇产量,也降低了催化剂的寿命,使生产成本进一步提高。
本文主要对甲醇合成催化反应机理及催化剂失活因素进行分析。
关键词:甲醇合成催化反应机理失活一、反应机理甲醇合成催化反应机理一直是研究人员关注和争议的焦点,不同的反应原料(CO/H2,或CO2/H2)、不同的催化剂、甚至相同的催化体系,催化剂结构不同,也可能导致反应机理不同。
有关反应机理的研究,主要集中在甲醇合成反应的直接碳源、反应的中间物种、反应的控速步骤以及CO在反应中的作用等问题。
早期研究者多数以动力学和H2、CO吸附等问接的实验结果为基础进行反应机理的研究;而现在多数基于同位素标记、光谱测定以及动力学模拟计算等比较直接的证据,但仍不能得出统一明确的结论。
本文按合成甲醇直接碳源的不同,将机理划分为以下3种:CO与CO2共同作为直接碳源机理、CO作为直接碳源机理以及CO2作为直接碳源机理。
(一)一氧化碳和二氧化碳作为直接碳源在CO和CO2加氢合成甲醇反应机理研究中,人们普遍认为甲酰基和甲酸基是反应过程的重要中间物种,CO吸附活化后直接生成甲酰基,而CO2吸附活化后生成甲酸基,并且CO和CO2可以通过表面氧或甲酸基等物种相互转化。
也有不同的观点认为CO吸附活化后与表面羟基结合生成甲酸盐,而CO则与表面氧结合生成碳酸根离子。
(二)一氧化碳作为直接碳源CO加氢合成甲醇的机理,可分为以下两种观点。
一种观点认为,CO首先在活性位上吸附活化,然后与吸附态的氢原子发生分步加氢反应,最终生成甲醇;而原料气中的CO2仅为补充碳源。
这种机理不能解释原料中少量CO2的存在能够明显促进甲醇合成反应的现象。
第二种观点认为,活化态的CO在加氢过程中同时与羟基、表面氧等物种发生反应,生成甲酸盐、甲氧基以及碳酸盐等中间物种,中间物种再通过脱氧及水解等反应生成甲醇。
甲醇合成催化剂中毒失活机理及现状分析

甲醇合成催化剂中毒失活机理及现状分析摘要:合成催化剂活性的好坏直接关系到甲醇产量及各项能耗的高低,是甲醇生产极其重要的环节。
我厂甲醇装置自开工以来一直被合成催化剂中毒现象所困扰,并且损失了大量资金,对装置的产量、成本及长周期运行均产生了极大影响。
本文将针对甲醇装置合成催化剂中毒失活机理、现状及措施展开探讨。
希望能对装置的运行及提高合成催化剂的使用效率提供有价值的参考。
关键词:催化剂;毒物;硫;羰基物;失活目前国内外所采用的甲醇合成催化剂均为铜基催化剂,氧化铜含量约占50-70%(wt),氧化锌含量约占20-30%。
铜基催化剂在使用前都要将其还原成单质铜才具有活性,而活性铜对硫、氯、羰基金属、油、磷、氨等毒物和温度变化较敏感,另外在还原过程中对温度的控制,防止烧结现象对催化剂活性也会产生一定影响。
所以铜基催化剂对原料气纯度和生产操作精细程度的要求很严格,否则极易造成催化剂中毒及失活。
本文将从以下毒物对催化剂的影响及生产运行控制两方面对催化剂中毒机理及失活现象展开论述。
1 催化剂中毒机理成因及失活研究1.1 硫对催化剂的影响硫是原料气中常见的毒物,也是引起催化剂活性衰退的主要因素。
换言之,原料气的硫含量决定了铜基催化剂的活性和使用寿命。
原料气中硫一般以h2s和cos形式存在。
除上述两种形态外,还有cs2、硫醚、噻吩等有机硫,它们相对含量比较少,但较难以脱除。
铜基甲醇催化剂对硫化物十分敏感,微量的硫化物就易造成催化剂的永久性中毒失活。
原料气中硫化物通常有h2s、cos、cs2和噻吩等。
通过科研机构的研究证实cs2和噻吩极易导致催化剂中毒,其次为cos,中毒作用相对最弱的是h2s。
h2s在活性cu上的吸附比在zno上强。
对于硫中毒的机理,通常认为是h2s和活性组分铜起反应生成硫化亚铜,覆盖催化剂表面和堵塞孔道而使其丧失活性,而且是永久中毒。
因此对原料气进行精脱硫净化是一种有效的延长甲醇催化剂使用寿命的方法。
甲醇合成催化剂失活及影响因素分析
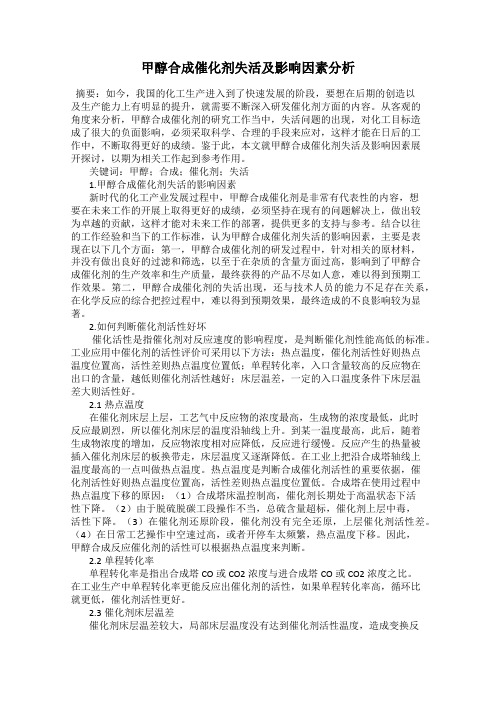
甲醇合成催化剂失活及影响因素分析摘要:如今,我国的化工生产进入到了快速发展的阶段,要想在后期的创造以及生产能力上有明显的提升,就需要不断深入研发催化剂方面的内容。
从客观的角度来分析,甲醇合成催化剂的研究工作当中,失活问题的出现,对化工目标造成了很大的负面影响,必须采取科学、合理的手段来应对,这样才能在日后的工作中,不断取得更好的成绩。
鉴于此,本文就甲醇合成催化剂失活及影响因素展开探讨,以期为相关工作起到参考作用。
关键词:甲醇;合成;催化剂;失活1.甲醇合成催化剂失活的影响因素新时代的化工产业发展过程中,甲醇合成催化剂是非常有代表性的内容,想要在未来工作的开展上取得更好的成绩,必须坚持在现有的问题解决上,做出较为卓越的贡献,这样才能对未来工作的部署,提供更多的支持与参考。
结合以往的工作经验和当下的工作标准,认为甲醇合成催化剂失活的影响因素,主要是表现在以下几个方面:第一,甲醇合成催化剂的研发过程中,针对相关的原材料,并没有做出良好的过滤和筛选,以至于在杂质的含量方面过高,影响到了甲醇合成催化剂的生产效率和生产质量,最终获得的产品不尽如人意,难以得到预期工作效果。
第二,甲醇合成催化剂的失活出现,还与技术人员的能力不足存在关系,在化学反应的综合把控过程中,难以得到预期效果,最终造成的不良影响较为显著。
2.如何判断催化剂活性好坏催化活性是指催化剂对反应速度的影响程度,是判断催化剂性能高低的标准。
工业应用中催化剂的活性评价可采用以下方法:热点温度,催化剂活性好则热点温度位置高,活性差则热点温度位置低;单程转化率,入口含量较高的反应物在出口的含量,越低则催化剂活性越好;床层温差,一定的入口温度条件下床层温差大则活性好。
2.1热点温度在催化剂床层上层,工艺气中反应物的浓度最高,生成物的浓度最低,此时反应最剧烈,所以催化剂床层的温度沿轴线上升。
到某一温度最高,此后,随着生成物浓度的增加,反应物浓度相对应降低,反应进行缓慢。
甲醇合成催化剂失活原因及应对措施分析
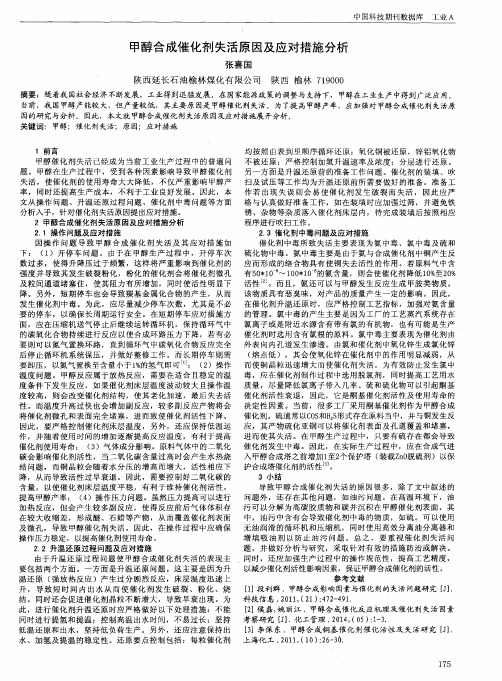
工业 A
甲醇合成催化剂 失活原 因及应对措施分析
张喜 国 陕西延 长石 油榆 林煤化 有 限公 司 陕西 榆林 7 1 9 0 0 0
摘要 :随着我 国社会经济 不断发展 ,工业得 到迅 猛发 展 。在 国家能源政 策的调整 与支持 下 ,甲醇在工业生产 中得到广泛应用 。
均 按照 由表到 里顺序循环 还原 ;氧化铜 被还原 ,锌 铝氧 化物 不被 还原 ;严格 控制加氢 升温速 率及浓度 ;分层进 行还 原 。 另一方面 是升温还 原前 的准备 工作 问题 。催 化剂 的装填 、吹 扫及 试压 等工作 均为升温 还原前所 需要 做好的准 备 。准 备工 作 若 出现 失 误则 会 易使 催 化 剂发 生破 裂 而 失活 ,因此 应严 格与 认真做 好准备 工作 ,如在装填 时应加 强过筛 ,并避 免铁 锈 、杂物 等杂质 落入催化 剂床层 内 ,待完 成装填后 按照相 应 程序进行吹扫工作 。 2 . 3催化剂 中毒 问题及应对措施 催 化剂 中毒所致 失活 主要表现 为氨 中毒 、氯 中毒及硫和 硫化 物 中毒 。氨 中毒主要是 由于氨 与合成催 化剂 中铜产生 反 应而 形成 的络 合物 具有使铜 失去活 性的作用 。若原料 气 中含 有5 0 . 1 0 - 6 ~l 0 0 . i 0 的氨含 量 ,则 会使催化 剂 降低 1 0 % 至2 0 % 活性 。而且 ,氨 还可 以与 甲醇发生 反应生成 甲胺类 物质 , 该物质 具有恶 臭味 ,对 产 品的质量产 生一定 的影响 。因此 , 在催化 剂升温 还原 时,应严格 控制 工艺指标 ,加强对 氨含量 的管 理。氯 中毒 的产 生主要 是因为 工厂 的工 艺蒸汽 系统存在 氯离子 或是 附近水源含 有带有 氯的有机 物 ,也有可 能是生产 催化剂 时选用 含有 氯根的原料 。氯 中毒主要表 现为催化 剂 由 外表 向内孔道 发生渗透 。由氯 和催化 剂 中氧化 锌生成 氯化锌 ( 熔 点低 ),其会使氧 化锌在 催化剂 中的作用 明显减弱 ,从 而使铜 晶粒迅 速增大 而使催化 剂失活 。为有 效防止发 生氯 中 毒 ,应在 催化 剂制作过 程 中选 用脱氯剂 ,同时提高工 艺用水 质 量 ,尽 量 降低 氯离 子带入几 率 。硫和 硫化物 可 以引起 酮基 催化剂 活性衰 退 ,因此 ,它是 酮基催化 剂活性及 使用寿 命 的 决定性 因素 。当前 ,很 多工厂 采用酮基 催化剂 作为 甲醇 合成 催 化剂。硫 通常 以C O S  ̄H s 形式存在原料 当中,并与铜发生反 应 ,其产 物硫 化亚铜 可 以将催 化剂表面 及孔道覆 盖和堵 塞 , 进 而 使 其 失 活 。 在 甲醇 生 产 过 程 中 ,只 要 有 硫 存 在 都 会 导 致 催 化剂发 生 中毒 。 因此 ,在实 际生产过 程中 ,应 在合成气 进 入 甲醇合成塔之前 增加 i 至2 个保护塔 ( 装 载Z n O 脱硫 剂) 以保 护 合成塔催 化剂 的活 性 。 3 小结 导致 甲醇合成 催化 剂失 活的原 因很多 ,除 了文中叙述 的 问题外 ,还存在 其他 问题 ,如 油污 问题 。在高温 环境下 ,油 污 可 以分解 为 高碳 胶质 物和碳 并沉 积在 甲醇催化 剂表面 ,其 中,油污 中含有 会导致 催化剂 中毒 的物质 ,如硫 。可 以使 用 无 油润滑 的循环机 和压 缩机 ,同时使用 高效分离 油分离器和 增 填 吸油 剂 以防止 油 污 问题 。总 之 ,要 重视 催 化剂 失 活 问 题 ,并做 好分析 与研究 ,采取针对 有效 的措施防 治或解 决。 同时 ,还应 加强 生产过程 中的操作 规范性 ,提高 工艺精度 , 以减少催化剂活性影响 因素 ,保证 甲醇合成催化剂 的活性 。 参考文献 [ 1 ] 段 利群 .甲醇合成影响 因素与催化剂的失活 问题研 究 [ J ] . 科技信 息 . 2 0 1 1 , ( 2 I ) : 4 7 2 — 4 9 1 . [ 2 ]侯磊 , 姚丽 江 .甲醇合成催 化反应机 理及催化 剂失活 因素 考察研究 [ J 】 . 化 工管理 . 2 0 1 4 , ( 0 5 ) : 卜3 . [ 3 ]李保 东 .甲醇合 成铜基 催化 剂催化 活性及 失活研 究 [ J 繁,这样 将严 重影 响到催化剂 的 强度 并导致其 发生破 裂粉化 ,粉化 的催化 剂会将 催化剂微 孔 及 粒 间通道堵塞 住 ,使其 阻力有所增 加 ,同时使 活性 明显 下 降。另外 ,短期 停车 也会导致 羰基金 属化合 物 的产 生 ,从 而 发生催 化剂 中毒 。为 此 ,应 尽量减少 停车 次数 ,尤其是不 必 要 的停 车, 以确 保长 周期运行 安全 。在短期 停车应 对措施 方 面 ,应在 压缩机 送气停 止后继 续运转 循环机 ,保持 循环气 中 的碳氧化 合物 持续进 行反应 以使合成 环路压 力下 降,若有 必 要 则可 以氮气置 换环路 ,直 到循环气 中碳氧 化合物 反应完 全 后停 止循 环机系 统保压 ,并做 好整修 工作 。而长期 停车则 需 要 卸压 ,以氮 气置换至含量 小于1 % 的氢 气即可 “ ; ( 2 )操 作 温度 问题 。 甲醇 反应属 于放热 反应 ,需要在 适合且 稳定 的温 度条 件下 发生反应 ,如 果催化 剂床层温 度波动 较大 且操作温 度较 高 ,则会 改变 催化 剂结构 ,使其 老化加速 ,最 后失去 活 性 。而温 度升高 过快也会 增加 副反应 ,较 多副反应 产物将会 将催 化剂微 孔和表 面完全 堵塞 ,进而致 使催化 剂活 性下降 。 因此 ,要 严格控 制催化 剂床层温 度 ,另外 ,还 应保 持低温运 作 ,并随 着使用 时间 的增 加逐渐 提高 反应温度 ,有利 于提 高 催化剂使 用寿命 ; ( 3 )气体成 分影响 。原料气 体中的二氧化 碳会 影 响催化剂 活性 ,当二氧 化碳含 量过高 时会产 生水热烧 结 问题 ,而铜 晶粒 会 随着 水分 压的增 高而增大 ,活 性相应 下 降 ,从而 导致活 性过早衰 退 。因此 ,需要控制 好二氧 化碳 的 含量 ,以使 催化 剂床层温 度平 稳,有利 于维 持催化 剂活性 , 提高 甲醇产率 ; ( 4 )操作压 力问题 。虽然压力 提高可 以进行 加热 反应 ,但 会产 生较 多副反应 ,使得 反应前 后气体 体积存 在较 大收缩 差 ,形 成醚 、石蜡 等产物 ,从而覆 盖催化 剂表面 及微 孔 ,导致 甲醇催 化剂 失活 。因此 ,在 操作 过程 中应 确保 操作压力稳定 ,以提高催化剂使用寿命 。 2 . 2升温还原过程 问题及应对措施 由于 升温还 原过 程 问题 使 甲醇合 成催化 剂失 活 的表 现主 要包括 两个方 面 。一 方面 是升温还 原 问题 。这主 要是 因为升 温还 原 ( 强放 热反应 )产 生过分剧 烈反应 ,床层 温度迅 速上 升 ,导 致 短 时 间 内出水 从 而使 催 化 剂发 生 破裂 、粉化 、烧 结。 同时还会 促进催 化剂 晶粒 不断 增大 ,导致早 衰 出现 。为 此 ,进 行催化 剂升温 还原 时应严格 做好 以下处理措 施 :不能 同时进行 提氢 和提温 ;控制 高温 出水时 间,不 易过长 ;坚持 低温 还 原和 出水 ,坚 持低 负荷 生产 。另外 ,还应注 意保 持出 2 0 1 1 , ( i 0 ) : 2 6 - 3 6 . 水 、加 氢及提温 的稳 定性 。还原要 点控制 包括 :每粒催 化剂 上 海 化 工 .
铜基甲醇合成催化剂失活的研究

Technology Forum︱332︱2017年9期铜基甲醇合成催化剂失活的研究文 航贵州开磷息烽合成氨有限责任公司,贵州 息烽 551100摘要:在甲醇生产过程中,受到多种因素的影响,甲醇合成催化剂会出现中毒、高温烧结或者是失活的问题,从而影响生产进程,增加生产成本。
本文首先对甲醇合同催化剂进行分析,其次阐述了常见的铜基甲醇合成催化剂失活原因,然后提出解决对策。
关键词:铜基;甲醇;催化剂;失活原因中图分类号:O643.36 文献标识码:B 文章编号:1006-8465(2017)09-0332-011 引言甲醇具有较大的市场发展潜力,可以将其应用于改进后的甲醇内燃机、甲醇汽油或者是甲醇燃料电池。
但是在甲醇生产过程中,很多工业指标以及操作条件都会受到催化剂性质的影响,失活也是最为常见的问题。
对此,需就失活原因进行分析与总结,以提高生产力。
2 甲醇合成催化剂分析铜基催化剂,相比于传统生产工艺来说,合成工艺对于温度的要求较低,利于甲醇反应平衡。
该工艺的特点是活性强,单程转化率可达7~8%,选择空间大,对于合成原料中含有的杂质较为敏感。
锌铝系的主要成分有CuO、ZnO以及Al2O3,三个成分的比例可以依据生产需求进行调整,常见比例如表1。
铜基催化剂在甲醇合成生产中,CuO、ZnO以及Al2O3三个组分的作用有所差异,CO、H2与催化剂的吸附性质、催化剂的活性有着密切的联系。
在铜基催化剂的表面,如果CO吸附的速率较高,那么H2的吸附速率较低。
ZnO作为催化剂,可以使得H2被吸附以及活化,但是CO没有吸附作用,所以需提高铜基催化剂的转化率。
表1 铜基催化剂各组分所占比例组分 CuO ZnO Al2O3质量分数(%) 40~80 10~30 5~103 铜基甲醇合成催化剂失活原因分析3.1 硫及硫化合物中毒当前甲醇合成生产中最为常用的就是铜基催化剂。
在原料中,存在的硫元素多为H2S和COS形式存在,当活性组分和铜元素相互反应,则会产生硫化亚铜,而硫化亚铜会附着于催化剂的表面,不断沉积于催化剂表面的各孔洞中,孔洞堵塞,从而造成永久性中毒。
甲醇合成催化剂的失活分析与对策
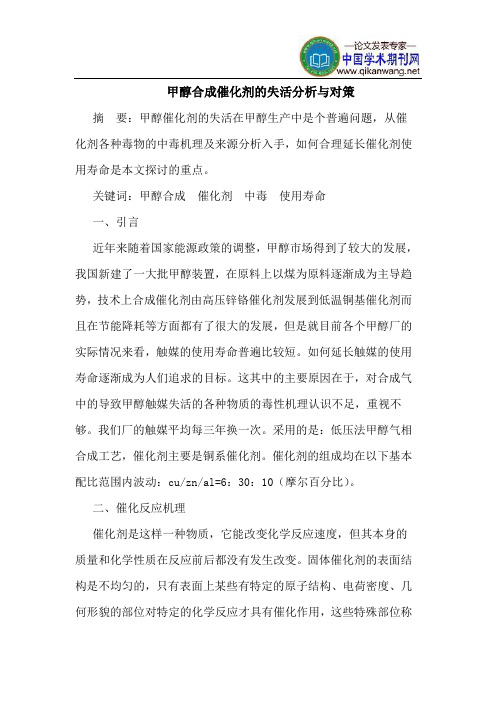
甲醇合成催化剂的失活分析与对策摘要:甲醇催化剂的失活在甲醇生产中是个普遍问题,从催化剂各种毒物的中毒机理及来源分析入手,如何合理延长催化剂使用寿命是本文探讨的重点。
关键词:甲醇合成催化剂中毒使用寿命一、引言近年来随着国家能源政策的调整,甲醇市场得到了较大的发展,我国新建了一大批甲醇装置,在原料上以煤为原料逐渐成为主导趋势,技术上合成催化剂由高压锌铬催化剂发展到低温铜基催化剂而且在节能降耗等方面都有了很大的发展,但是就目前各个甲醇厂的实际情况来看,触媒的使用寿命普遍比较短。
如何延长触媒的使用寿命逐渐成为人们追求的目标。
这其中的主要原因在于,对合成气中的导致甲醇触媒失活的各种物质的毒性机理认识不足,重视不够。
我们厂的触媒平均每三年换一次。
采用的是:低压法甲醇气相合成工艺,催化剂主要是铜系催化剂。
催化剂的组成均在以下基本配比范围内波动:cu/zn/al=6:30:10(摩尔百分比)。
二、催化反应机理催化剂是这样一种物质,它能改变化学反应速度,但其本身的质量和化学性质在反应前后都没有发生改变。
固体催化剂的表面结构是不均匀的,只有表面上某些有特定的原子结构、电荷密度、几何形貌的部位对特定的化学反应才具有催化作用,这些特殊部位称为催化剂的活性中心。
在活性中心上反应物分子先是被吸附在其上面。
被吸附的分子在活性中心表面进行能量交换,形成类似化学键的形式,从而削弱反应分子之间各原子间的化学键能,使分子变形而相互重新结合,完成合成反应;或活性中心与被吸附反应物分子构成配价健,而使反应物分子活化,并促使其在配位上进一步反应,最后转化为反应产物。
催化剂的活性与催化剂活性中心的面积、数量有直接的正比例关系。
活性中心,是催化剂的核心点,与催化剂的组成、制作方法,粘结性、比表面积、晶格结构有关。
延长催化剂活性寿命主要取决于三方面:〈1〉催化剂的稳定性。
〈2〉气体的净化程度、装置的清扫程度。
〈3〉使用条件。
三、催化剂的中毒我们厂低压法合成工艺使用的是cu-zn-al系催化剂,该系催化剂活性高,选择性强,但活性温度范围小,对毒物极为敏感,容易中毒失活,导致催化剂失活的主要因素有以下几个方面: 〈1〉硫化物〈2〉油污〈3〉超温烧结下面分别对上述毒物的来源和催化剂的失活机理及防范措施作以粗浅的分析:1.硫化物1.1硫化物的形态和含量分布硫化物是最常见的毒物,是引起催化剂活性丧失的主要因素。
甲醇合成催化剂失活及影响因素分析

甲醇合成催化剂失活及影响因素分析摘要:甲醇 (CHOH) 是一种结构最简单的一元醇,也被称为木醇,因为它最3初存在于干燥的蒸馏木材中。
甲醇是一种无色挥发性液体,有酒精气味。
它是一种重要的化工原料,广泛用于化学实验和化学领域。
用途广泛,不仅可作为萃取剂,还可作为化工原料及其加工产品,如甲醛、醋酸、农药等。
随着科学技术的发展,甲醇转化为烯烃生产技术不断发展,甲醇转化为高附加值产品的力度不断加大对甲醇的需求不断增长,甲醇合成领域的研究越来越受到研究关注。
催化剂是一类能够在化学反应过程中改变化学反应速率而不被自身消耗的物质,广泛应用于许多化学反应中。
催化剂作为甲醇合成中的一个非常重要的环节,与甲醇生产中的许多条件和性能指标密切相关,其种类、性能和活性对甲醇的合成起着重要的作用。
因此,有必要对催化剂活性进行系统的分析和研究。
关键词:甲醇合成;催化剂失活;影响因素引言甲醇制烯烃是以甲醇为原料,在催化剂的作用下,在流化床反应器中进行脱水和碳链重整的过程,实现MTO工艺优化的核心和关键是MTO催化剂,具有极高的比表面积、良好的水热稳定性、丰富的质子酸性和离子交换位,独特的八元环三维孔道体系更使得它拥有了极好的小分子择形催化性能。
甲醇制烯烃SAPO-34分子筛工业化应用过程中因反应物、反应过程及传质等问题,引起催化剂失活和磨损,导致催化剂需要再生和补充新的催化剂,增加了生产成本,必须进行再利用。
本文综述甲醇合成催化剂失活的影响因素,并对提高甲醇合成催化剂活性的措施进行总结,提出甲醇催化剂今后的发展方向。
1甲醇合成催化剂失活的影响因素1.1结蜡问题( 1) 在催化剂装填过程中,如果铁锈或油脂等杂质带入合成塔内,会降低催化剂的活性和选择性,促进石蜡的生成。
( 2) 铜基催化剂在使用过程中,随着使用时间的增加,特别是催化剂使用中后期,受催化剂选择性的限制,会生成一定量的石蜡。
同时,甲醇生产时难免会伴有少量甲酸及其他有机酸生成,这些酸类物质在 CO 的作用下腐蚀合成塔生成Fe( CO)5与 Ni( CO)4,加速石蜡的生成。
铜基甲醇催化剂失活因素及解决措施研究进展
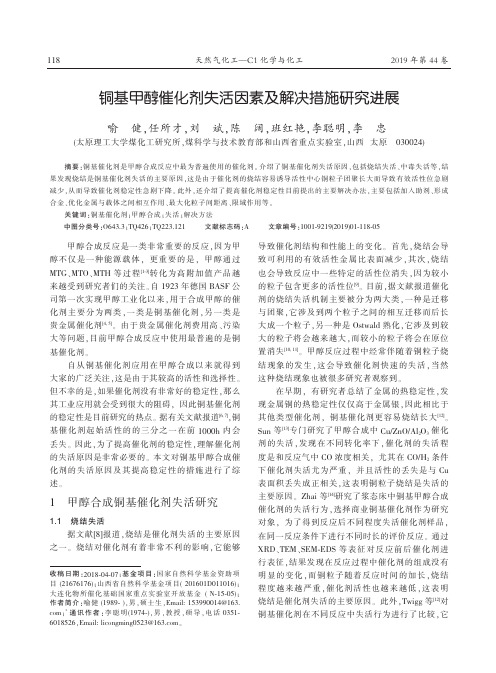
甲醇合成反应是一类非常重要的反应,因为甲醇不仅是一种能源载体,更重要的是,甲醇通过MTG、MTO、MTH等过程[1鄄3]转化为高附加值产品越来越受到研究者们的关注。
自1923年德国BASF公司第一次实现甲醇工业化以来,用于合成甲醇的催化剂主要分为两类,一类是铜基催化剂,另一类是贵金属催化剂[4,5]。
由于贵金属催化剂费用高、污染大等问题,目前甲醇合成反应中使用最普遍的是铜基催化剂。
自从铜基催化剂应用在甲醇合成以来就得到大家的广泛关注,这是由于其较高的活性和选择性。
但不幸的是,如果催化剂没有非常好的稳定性,那么其工业应用就会受到很大的阻碍,因此铜基催化剂的稳定性是目前研究的热点。
据有关文献报道[6,7],铜基催化剂起始活性的的三分之一在前1000h内会丢失。
因此,为了提高催化剂的稳定性,理解催化剂的失活原因是非常必要的。
本文对铜基甲醇合成催化剂的失活原因及其提高稳定性的措施进行了综述。
1甲醇合成铜基催化剂失活研究1.1烧结失活据文献[8]报道,烧结是催化剂失活的主要原因之一。
烧结对催化剂有着非常不利的影响,它能够导致催化剂结构和性能上的变化。
首先,烧结会导致可利用的有效活性金属比表面减少,其次,烧结也会导致反应中一些特定的活性位消失,因为较小的粒子包含更多的活性位[9]。
目前,据文献报道催化剂的烧结失活机制主要被分为两大类,一种是迁移与团聚,它涉及到两个粒子之间的相互迁移而后长大成一个粒子,另一种是Ostwald熟化,它涉及到较大的粒子将会越来越大,而较小的粒子将会在原位置消失[10,11]。
甲醇反应过程中经常伴随着铜粒子烧结现象的发生,这会导致催化剂快速的失活,当然这种烧结现象也被很多研究者观察到。
在早期,有研究者总结了金属的热稳定性,发现金属铜的热稳定性仅仅高于金属银,因此相比于其他类型催化剂,铜基催化剂更容易烧结长大[12]。
Sun等[13]专门研究了甲醇合成中Cu/ZnO/Al2O3催化剂的失活,发现在不同转化率下,催化剂的失活程度是和反应气中CO浓度相关,尤其在CO/H2条件下催化剂失活尤为严重,并且活性的丢失是与Cu 表面积丢失成正相关,这表明铜粒子烧结是失活的主要原因。
关于甲醇合成催化剂使用经验总结及问题分析
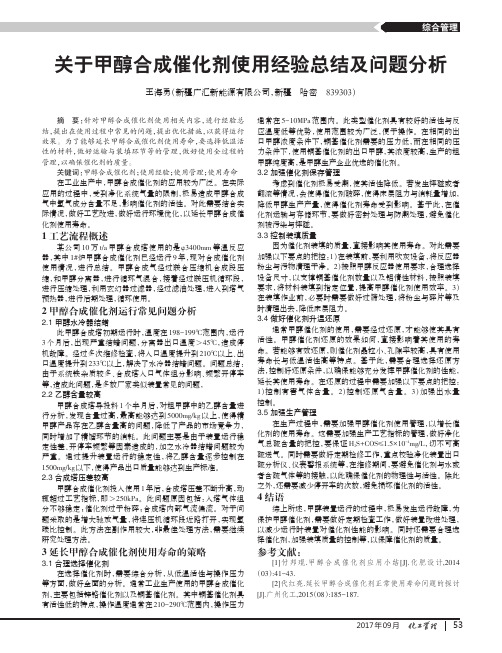
2017年09月关于甲醇合成催化剂使用经验总结及问题分析王海勇(新疆广汇新能源有限公司,新疆哈密839303)摘要:针对甲醇合成催化剂使用相关内容,进行经验总结,提出在使用过程中常见的问题,提出优化措施,以获得运行效果。
为了能够延长甲醇合成催化剂使用寿命,要选择低温活性的材料,做好运输与装填环节等的管理,做好使用全过程的管理,以确保催化剂的质量。
关键词:甲醇合成催化剂;使用经验;使用管理;使用寿命在工业生产中,甲醇合成催化剂的应用较为广泛。
在实际应用的过程中,受到净化系统气量的限制,极易造成甲醇合成气中氢气成分含量不足,影响催化剂的活性。
对此需要结合实际情况,做好工艺改进,做好运行环境优化,以延长甲醇合成催化剂使用寿命。
1工艺流程概述某公司10万t/a 甲醇合成塔使用的是φ3400mm 等温反应器,其中1#炉甲醇合成催化剂已经运行9年,现对合成催化剂使用情况,进行总结。
甲醇合成气经过联合压缩机合成段压缩,和甲醇分离器,进行循环气混合,接着经过联压机循环段,进行压缩处理,利用玄幻器过滤器,经过滤油处理,进入到塔气预热器,进行后期处理,循环使用。
2甲醇合成催化剂运行常见问题分析2.1甲醇水冷器结蜡此甲醇合成塔初期运行时,温度在198-199℃范围内,运行3个月后,出现严重结蜡问题,分离器出口温度>45℃,造成停机故障。
经过多次维修检查,将入口温度提升到210℃以上、出口温度提升到233℃以上,解决了水冷器结蜡问题。
问题总结:由于系统铁杂质较多、合成塔入口气体组分影响、频繁开停车等,造成此问题,是多数厂家类似装置常见的问题,2.2乙醇含量较高甲醇合成塔导投料1个半月后,对粗甲醇中的乙醇含量进行分析,发现含量过高,最高能够达到5000mg/kg 以上,使得精甲醇产品存在乙醇含量高的问题,降低了产品的市场竞争力,同时增加了精馏环节的消耗。
此问题主要是由于装置运行稳定性差、开停车频繁等因素造成的,加之水冷器结蜡问题较为严重。
甲醇合成影响因素的分析探讨

甲醇合成影响因素的分析探讨摘要:温度、气体组成、压力因素、粗甲醇的冷却分离效果是影响甲醇合成的关键因素。
对此进行详细的分析和阐述,希望能给同行带来一些参考价值。
关键词:甲醇;影响因素;温度;压力;合成气;气体成分1.引言甲醇作为一种重要的化工原料,应用于各行各业。
甲醇合成有很多因素影响甲醇产量及甲醇正常生产。
本文对影响甲醇合成的因素进行分析探讨,希望能给同行带来一些参考价值,具体分析如下:2.分析了温度因素的影响甲醇合成生产在铜基催化剂作用下发生可逆、放热反应,所以在这一点上,从化学平衡的角度来看,温度的提高对甲醇合成有利,同时,从总体反应活性来看,提高总体反应速率的温度可以加快反应活性,因此甲醇合成需要选择最合理的温度。
一般来说,反应活动是在氢、碳、氧元素之间进行的。
反应温度对产物的性质起着至关重要的作用。
反应温度越高,生成甲醇的副反应和主反应越强。
因此,较高的反应温度会影响粗甲醇的质量水平。
3.分析了压力因素的影响合成气产生的甲醇是在催化剂作用下在气体之间产生的,主反应会相应地降低分子数。
因此,相应提高压力对合成气制甲醇有积极的影响,但如果压力很高,则对管道和安装材料提出了更高的标准。
反应的总速率随着反应物浓度的增加而增加。
在此过程中,无论是从热力学还是动力学的角度,相应的增大压力对合成气制甲醇都有积极的影响。
因此,需要提高产品甲醇的平衡浓度。
但是温度的下降减慢了反应的总体速率,导致它减慢,所以压力和温度的影响是明显不同的。
甲醇合成生产在催化剂的前提下的特殊属性和技术发展,催化剂的使用,选择低温催化剂的活性,也就是说,在低温的情况下可以提高反应速率,还可以获得更多的甲醇的比例输出。
同时,低温活性催化剂可以在一定程度上降低设备成本。
经过选择的催化剂和反应压力,因为甲醇合成气生产的温度响应和热力学的影响有差异,所以在这个时候会有一个合理的温度,在温度的值,将能够有效地获得高甲醇比例的收获,但也能得到更快的反应温度。
甲醇合成催化剂失活原因分析及延长使用寿命的方法
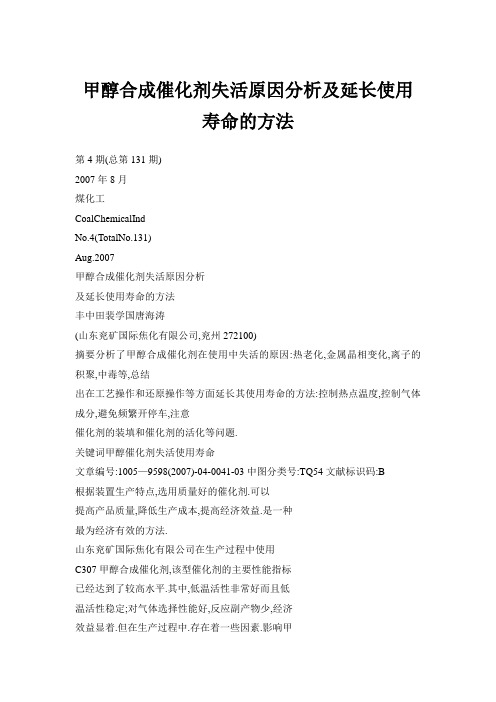
甲醇合成催化剂失活原因分析及延长使用寿命的方法第4期(总第131期)2007年8月煤化工CoalChemicalIndNo.4(TotalNo.131)Aug.2007甲醇合成催化剂失活原因分析及延长使用寿命的方法丰中田裴学国唐海涛(山东兖矿国际焦化有限公司,兖州272100)摘要分析了甲醇合成催化剂在使用中失活的原因:热老化,金属晶相变化,离子的积聚,中毒等,总结出在工艺操作和还原操作等方面延长其使用寿命的方法:控制热点温度,控制气体成分,避免频繁开停车,注意催化剂的装填和催化剂的活化等问题.关键词甲醇催化剂失活使用寿命文章编号:1005—9598(2007)-04-0041-03中图分类号:TQ54文献标识码:B根据装置生产特点,选用质量好的催化剂.可以提高产品质量,降低生产成本,提高经济效益.是一种最为经济有效的方法.山东兖矿国际焦化有限公司在生产过程中使用C307甲醇合成催化剂,该型催化剂的主要性能指标已经达到了较高水平.其中,低温活性非常好而且低温活性稳定;对气体选择性能好,反应副产物少,经济效益显着.但在生产过程中.存在着一些因素.影响甲醇合成催化剂的活性.即使用寿命.1甲醇合成催化剂失活原因分析1.1热老化导致失活铜基催化剂对反应热比较敏感.甲醇合成反应为放热反应,其钝化和还原过程也均为放热反应.因此.在升温与还原或生产控制过程中,如果反应控制不当.导致反应热不能移出,就很容易发生床层温度"飞温",致使活性下降.热老化会使载体的表面积减少.使金属微粒发生迁移,金属晶相发生变化,致使活性位减少,并增加床层阻力.热老化发生的主要原因就是反应余热不能迅速移出反应器,或者反应过于剧烈,反应热突然增加(如系统新鲜气组成突然发生变化,C0配比发生变化或中断).有时为了追求高产,气体氢碳比降低,表现为收稿日期:2007—05-13作者简介:丰中田(1965一),男,1992年毕业于青岛化工学院,高级工程师,长期从事甲醇生产技术工作.人塔合成气体C0组分达到16%18%.氢碳比4.24.6,副产蒸汽增加,选择了C0过多参与反应.而忽略了C0对稳定催化剂床层的有利影响,最终造成催化剂使用寿命的缩短.以某厂为例:在装置运行过程中,由于精制气净化系统脱碳塔设备问题的影响,使C0暂时无法配入,中断2h后恢复(此时入塔气体中C0体积分数<0.5%). 结果在恢复C0正常配比后,发现甲醇产量相对降低,表明催化剂活性在C0中断过程中,C0加剧了催化剂的热老化,甚至有可能出现催化剂深度还原.1.2积碳失活在甲醇合成反应中,存在2种析碳反应:C0+H2=C+H20(还原析碳)(1)2CO=C+CO,(歧化析碳)(2)在系统运行过程中.长期处于较低的氢碳比状态(尤其是在催化剂使用后期),入塔气体中C0含量较高,而C0含量较低,导致大量的氢气剩余.主要表现为系统放空量大,合成气体单程转化率较低.在微观的瞬间反应中,存在这2种析碳反应发生的可能.析碳反应发生后,产生的积碳能够覆盖催化剂的活性表面,使部分活性位丧失,会造成床层阻力增大. 但由于合成系统的空速较大,积碳造成的影响一般不是很明显.某厂在更换催化剂时.在卸出的废旧催化剂表面,发现一些黑色石墨粉尘,表明催化剂在使用过程中.有析碳反应发生.1.3金属晶相变化导致失活A10.作为载体的主要部分为晶相较好的—A10.,一42一煤化工2007年第4期在升温和还原以及工艺运行中,受非操作因素的影响,可能会发生金属晶相的变化,尤其是铜金属晶粒的生长影响,或在高温下转变为其他形态B—A10.或一Al0..在较高含水量下,会生成含水Al0.化合物,Cu-ZnO中心的移动.而降低活性.水蒸气的吸附可导致ZnO吸附氢气能力变弱,活性晶格氧空位被其他离子占用,从而丧失活性.1.4Fe2+的聚积导致对气体选择性发生变化输送新鲜气体的管道有些采用普通碳钢,造成新鲜气体中C0对碳钢管道的晶相腐蚀,产生羟基铁几乎不可避免,并通过气体携带进入合成塔.在合成塔的温度和压力下,以挥发,分解和吸附的方式沉积在催化剂表面上.有可能会转变为氧化亚铁,使合成甲醇活性下降,促进烷烃的生成.甚至出现明显的结蜡现象.这样使催化方向发生变化,造成对反应气体选择性的竞争加剧,不利于甲醇合成反应的进行.具体表现为:在甲醇合成催化剂使用后期,甲烷含量增加,副反应产物增多,合成反应热加大,有石蜡产生.1.S中毒失活催化剂中夹带少量的杂质,或在生产过程中积聚的杂质.以及开停车过程中气体成分的影响.都可能促进副反应的进行,引起反应竞争.这些杂质有的很难在工艺上完全脱除,有的在催化剂制作过程中就已经存在,且无法去除.常见的杂质或毒物对催化剂的影响对比见表1.表1杂质或毒物对催化剂的影响对比杂质或毒物可能的来源对催化剂的影响SiO,等酸性氧化物自蒸汽或原料气带人生成蜡及其他副产物B—A103催化剂制造生成二甲醚碱金属,盐催化剂制造降低活性生成高级醇铁以Fe(CO)带人生成甲烷,链烷烃,石蜡镍以Ni(CO)带人降低选择性钴催化剂制造生成甲烷氯化物自原料气带人永久性降低活性硫化物自原料气带人永久性降低活性1.5.1硫中毒硫是甲醇合成催化剂的主要毒物之一,也是引起催化剂活性衰退的主要因素.在甲醇合成原料气体中,硫主要以HS和COS形式存在,根据造气工艺的不同,原料气体中还存有微量大分子有机硫,如硫醇, 硫醚,噻吩等,由于受低温水解弱的影响.这部分有机硫在低温水解中是无法脱除干净的.但在高温加氢条件下,有机硫发生转化反应,可以完全转化成无机硫. 通常认为:HS,COS和活性组分Cu发生反应,生成稳定的无活性的金属硫化物,在甲醇合成反应条件下(220℃~260℃),硫醇或硫醚会发生加氢转化反应而生成无机硫.反应方程式如下:RSH+H2=RH+H2S(3)RlSR2+2H2=RjH+R2H+H2S(4)在变换反应中,由于水气比限制了有机硫的加氢转化,所以,在高浓度C0合成条件下,微量的硫醇,硫醚基本不会造成较大影响,只有在催化剂使用后期,反应温度较高的情况下,才有可能发生;或者在催化剂使用过程中,高浓度CO引发各类副反应的竞争,使析出的硫迅速被CuO吸收,生成稳定无活性的CuS.1.5.2氢中毒原料气(合成气)氢碳比例对甲醇合成催化剂有重要影响,但在一般情况下不会发生氢中毒.如果在开停车过程中(主要是在停车过程中),工艺处理不当造成氢气含量过高,而CO+CO含量长时间较低,会对催化剂进行深度还原,生成无活性的单质Cu,使催化剂活性丧失所以,在开车过程中,要适当进行新鲜气和循环气的交替加量,短时间内调整至正常的氢碳比例:在停车过程中,一旦分析合成气中C0+C0的体积分数<0.5%,就必须进行氮气置换,用氮气进行保温,保压.1.5.3氯,砷离子中毒氯,砷也是甲醇合成催化剂毒物,氯,砷离子主要存在于蒸汽中,所以在造气或气化过程中,需要特别注意蒸汽中氯,砷离子的含量,确保锅炉水质量.2延长催化剂使用寿命的方法2.1控制热点温度某厂对更换后C307型甲醇合成催化剂的操作数据进行整理,得出催化剂的使用天数与平均热点温度有以下关系:Y=5×10×0.959X其中,y为催化剂使用天数,为平均热点温度.因此,降低催化剂热点温度,是延缓催化剂热老化程度并增加使用寿命的好方法.防止催化剂热老化的主要措施有:(1)在还原,开停车过程中,按照预定的指标进行操作,防止超温.(2)在保证产量的前提下,稳定操作,尽可能降低床层热点温度,每次提升热点温度应慎重.提升幅度不宜过大,一般为5℃左右.(3)适当提高新鲜气(合成气)中的C0的含量.2007年8月丰中田等:甲醇合成催化剂失活原因分析及延长使用寿命的方法一43—2.2控制气体成分控制好气体成分,首先是控制好C0和C0,的比例,根据催化剂的不同使用时期进行调整;其次是控制好惰性气体的含量,掌握并分析放空气体量.作为优化指标的依据:第三是控制好循环气体中的含醇量,人塔气体中含醇量越低,越有利于合成甲醇反应的进行,也可以避免高级醇等副产物的生成.所以要尽可能降低出甲醇水冷器的气体温度,及时将冷凝下来的甲醇分离出来.2.3避免频繁开停车有很多厂家因设备或系统原因.不可避免地出现多次开停车,如果在停车过程中处理不当,将会使催化剂活性受到损害.试验证明:短期停车后,如果催化剂封存在原料气中(合成塔死气,且无法用氮气置换),在重新开车后,其催化剂活性出现明显下降.因此短期或紧急停车后,应作以下处理:(1)应立即用氮气进行置换.如不能置换,可让循环机照常运行.使循环气中的碳氢混合物得到完全反应,直至系统中只有惰性气体和氢气(或者CO,+CO体积分数<0.5%).(2)当床层温度下降时,应适当开大开工蒸汽,并减少循环量,使床层温度维持在210℃,并将系统压力缓慢降低到0.2MPa.(3)如果出现长期停车,在进行氮气置换合格后,应使系统保持微正压,防止在检修时混入空气.2.4催化剂的装填在催化剂装填时,应注意的问题是:(1)催化剂强度较差,在运输过程中严禁摔,碰.(2)装填前,催化剂应轻轻过筛,除去粉尘和碎片.(3)最好采用撒布法装填,尽可能降低催化剂自由下落高度,防止出现架桥现象,应对列管压差进行抽检,压差应在许可范围内.(4)装填时应选择较好天气,以免催化剂吸潮而降低活性,催化剂一旦开始装填应连续进行,避免间断. 装填后应立即封口,充人氮气或进行升温还原.2.5催化剂的活化催化剂的活化在一定程度上决定了催化剂的活性,直接影响其使用寿命,依此在催化剂活化(还原) 时,应特别注意的问题是:(1)氢含量控制还原反应为强放热反应,当氢气含量较低时.催化剂床层的温升和氢气浓度成正比,一般每提高1% 的氢气,将引起床层温度升高28℃,因此控制好加氢速度是还原操作的关键.在还原时,掌握提温不提氢, 提氢不提温的原则,防止还原过于剧烈,床层温度猛涨,使催化剂活性受影响.所以,在还原操作中一般采用低氢,高空速控制还原速度.(2)出水量控制还原终点判断催化剂活性影响较大,在还原时.既要防止还原操作不彻底,又要防止出现深度还原, 很多厂家采用精制气还原,出水量尽可能控制均匀. 在还原操作中,理论出水量与实际出水量应基本接近,并分析进出合成塔氢气含量稳定,这时基本可以判断还原结束.(3)惰性气体放空量控制惰性气体一般为还原气体(氢气)的载气.一般采用氮气为稀释气体,在还原操作中,惰性气体能够有效控制还原速度,床层温度便于控制,有利于提高催化剂活性,保护催化剂强度.此外,由于采用精制气还原,惰性气体中的C0,含量也影响还原进度的判断,根据放空气体中的C0, 含量,判断C0参与还原反应程度,所以出水量有可能要比理论出水量低.3结论甲醇合成催化剂的使用寿命受到催化剂本身构造影响和还原操作的影响,以及在工艺运行中操作条件的限制.所以,在一般情况下,为追求单炉催化剂产量,是以牺牲催化剂使用寿命来换取高产量的,同时,造成了催化剂频繁更换,应从经济效益上来衡量. CausesofDeactivationofCatalystforMethanolSynthesisandMethodtOProlongItsLifetim eFengZhongtian,PeiXueguoandTangHaitao (ShandongYankuangInternationalCokingCo.,Ltd.,Yanzhou272100) AbstractBasedoncompositionandstructureofmethanolsynthesiscatalyst,itsdeactivationc auseswerefoundandanalyzed:thermalaging,metalcrystallinephasechange,ionaccumulation,poisoning,etc.S omemethodstoprolongthelifetimeofcatalystweresuggested,i.e.controllinggascompositionandtemperatureofthehot spot,avoidingfrequentstart—upandshutdown,payingattentiontothechargeandactivationofcatalyst,etc. KeyWOrdsmethanol,catalyst,deactivation,lifetime。
基于化学反应动力学模型的甲醇合成催化剂研究

基于化学反应动力学模型的甲醇合成催化剂研究一、简介甲醇是一种重要的有机化学品,广泛用于化学工业、家庭生活等各个领域。
以天然气为原料合成甲醇的工艺已经十分成熟,而甲醇合成催化剂则是甲醇制备的重要组成部分。
针对甲醇合成催化剂的研究可以提高甲醇的生产效率,减少生产成本,提高化工产品质量等方面发挥巨大作用。
二、甲醇合成催化剂的种类1. 钼基甲醇合成催化剂钼基甲醇合成催化剂常用的成分是氧化钼,常用载体为氧化铝或者硅酸盐。
该催化剂具有反应活性和选择性好等特点,在甲醇生产中占有重要地位。
2. 铬基甲醇合成催化剂铬基甲醇合成催化剂常用的成分是氧化铬,常用载体为氧化铝或者硅酸盐。
该催化剂的反应活性较高,但是由于其选择性差,在实际生产过程中使用较少。
3. 铜基甲醇合成催化剂铜基甲醇合成催化剂常用的成分是氧化铜和氧化锌,常用载体为氧化铝或者硅酸盐。
该催化剂具有反应活性高,反应速度快,但是稳定性差等特点。
三、甲醇合成催化剂的研究进展1. 催化剂的设计和制备目前,催化剂的设计和制备是研究甲醇合成催化剂的主要方向。
通过合成新型催化剂,可以改善催化剂的反应活性和选择性,从而提高甲醇产量和产品质量。
常用的制备方法有物理混合法、物理吸附法、化学沉淀法、共沉淀法、浸渍法等。
2. 反应动力学模型的建立反应动力学模型的建立是研究甲醇合成催化剂的重要手段。
通过建立反应动力学模型,可以预测催化剂的反应活性和选择性,确定最优反应条件,从而提高甲醇产量和产品质量。
目前,常用的反应动力学模型有层析动力学模型、微观动力学模型、表面扩散动力学模型等。
3. 催化剂寿命的研究催化剂寿命的研究是研究甲醇合成催化剂的重要内容之一。
甲醇合成反应的高温高压条件会造成催化剂失活,因此如何提高催化剂寿命是研究的重要方向。
目前,常用的方法是研究催化剂的物化性质变化和促进失活的因素,从而找到有效的保持催化剂活性的方法。
四、未来发展趋势随着工业技术的不断发展,甲醇合成催化剂的研究将会越来越重要。
甲醇合成工艺常出现的问题及解决办法
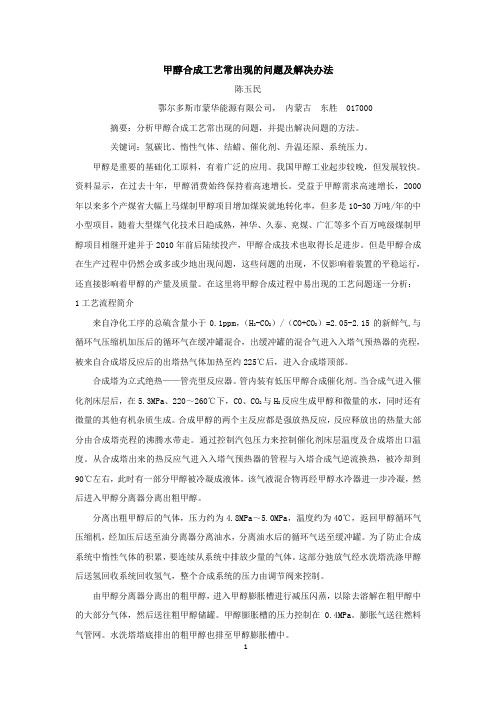
甲醇合成工艺常出现的问题及解决办法陈玉民鄂尔多斯市蒙华能源有限公司,内蒙古东胜 017000 摘要:分析甲醇合成工艺常出现的问题,并提出解决问题的方法。
关键词:氢碳比、惰性气体、结蜡、催化剂、升温还原、系统压力。
甲醇是重要的基础化工原料,有着广泛的应用。
我国甲醇工业起步较晚,但发展较快。
资料显示,在过去十年,甲醇消费始终保持着高速增长。
受益于甲醇需求高速增长,2000年以来多个产煤省大幅上马煤制甲醇项目增加煤炭就地转化率,但多是10-30万吨/年的中小型项目,随着大型煤气化技术日趋成熟,神华、久泰、兖煤、广汇等多个百万吨级煤制甲醇项目相继开建并于2010年前后陆续投产,甲醇合成技术也取得长足进步。
但是甲醇合成在生产过程中仍然会或多或少地出现问题,这些问题的出现,不仅影响着装置的平稳运行,还直接影响着甲醇的产量及质量。
在这里将甲醇合成过程中易出现的工艺问题逐一分析:1工艺流程简介来自净化工序的总硫含量小于0.1ppm,(H2-CO2)/(CO+CO2)=2.05-2.15的新鲜气,与循环气压缩机加压后的循环气在缓冲罐混合,出缓冲罐的混合气进入入塔气预热器的壳程,被来自合成塔反应后的出塔热气体加热至约225℃后,进入合成塔顶部。
合成塔为立式绝热——管壳型反应器。
管内装有低压甲醇合成催化剂。
当合成气进入催化剂床层后,在5.3MPa、220~260℃下,CO、CO2与H2反应生成甲醇和微量的水,同时还有微量的其他有机杂质生成。
合成甲醇的两个主反应都是强放热反应,反应释放出的热量大部分由合成塔壳程的沸腾水带走。
通过控制汽包压力来控制催化剂床层温度及合成塔出口温度。
从合成塔出来的热反应气进入入塔气预热器的管程与入塔合成气逆流换热,被冷却到90℃左右,此时有一部分甲醇被冷凝成液体。
该气液混合物再经甲醇水冷器进一步冷凝,然后进入甲醇分离器分离出粗甲醇。
分离出粗甲醇后的气体,压力约为4.8MPa~5.0MPa,温度约为40℃,返回甲醇循环气压缩机,经加压后送至油分离器分离油水,分离油水后的循环气送至缓冲罐。
探究甲醇合成催化剂失活的影响因素

探究甲醇合成催化剂失活的影响因素甲醇合成催化剂的失活问题,是制约生产质量、效率和安全的重要因素。
在实际生产中,需要采用综合手段治理甲醇合成催化剂的失活问题,既要应用技术手段,更要注重管理手段。
应该运用科学方法从多元化的角度着手,确保为安全生产,增加甲醇产量和催化剂效率,降低生产成本,增強企业经济效益提供良好的保障。
标签:甲醇合成;催化剂失活;影响因素1 稳定甲醇合成催化剂的重要性1.1 提升经济效益良好的经济效益是促进化工企业平稳发展的重要力量。
在生产过程中,甲醇合成催化剂的活性将直接影响甲醇的产率,同时决定产品的生产效果。
在整个生产过程中,其他环节出现问题的概率较小,所以催化剂失活就成为了一个生产短板,必须予以解决。
1.2 稳定生产在常规甲醇合成生产过程中,甲醇合成催化剂的使用情况往往是最为主要的生产技术标准,其体现了工艺的特征以及装置的特点。
如果甲醇合成催化剂经常失活,那么说明工艺存在严重缺陷,需要更换工艺甚至是设备。
如果能够通过其他方式来稳定生产,就可以确保技术应用水平,稳定生产各个环节。
1.3 提升甲醇产品质量甲醇产品质量将决定化工企业的市场综合竞争力与市场信誉。
通过稳定的催化剂可以获得更好的产品质量,从而获得良好的行业口碑,这对于企业的健康平稳快速发展具有重要意义。
2 影响甲醇合成催化剂失活的主要因素2.1 毒害物对甲醇合成催化剂失活造成的影响2.1.1 毒害物的种类及可能来源通常无论是原材料,设备中存在的杂质以及催化剂制作的过程中都可能产生一定的毒害物,而这些毒害物极有可能对催化剂的生产效率和应用效果造成严重的影响,常见的毒害物可以分为硫与氨等多种物质。
2.1.2 硫对甲醇合成催化剂失活的影响现阶段,我们所使用的甲醇合成催化剂其主要是铜基催化剂,硫与其化合物是造成甲醇合成催化剂失活的主要因素之一,通常硫与硫化合物会对甲醇合成催化剂的使用期限与活性的关系极为紧密。
原料气中的硫多会以COS与H2S的形式出现,而COS与H2S和活性组分铜会产生一定的反应,最后会产生硫化亚铜,由此便会对甲醇合成催化剂表面以及堵塞孔道造成部分影响,不仅导致了催化剂失活的问题出现,还会造成永久性的中毒现象。
浆态相甲醇合成催化剂的失活机理

Ab t a t s r c :Com p r d wih t r d to a a a e s n h ss,su r — h s y t e i fm e ha o s m a y a — a e t he ta ii n lg s ph s y t e i l r y p a e s n h ss o t n lha n d
Z A ua g一, u H MO O ,X E H n ja A Y se g , A i u , o i tuT UB KI H I fn J nS A T 3 I o gu n ,T N i n H N Y z o X h h N r as S A 3 t
( tt y L b r tr fC a o vrin,I siueo C a e sr 1 Sa eKe a oao yo o lC n eso ntt t o lCh mi y,Th ieeAcd myo S i cs f t eChn s a e ce e , f n T iu n0 0 0 ay a 3 0 1,Chn ia;2 Gr d ae Unv ri ieeAcd myo ce c ,B i n 0 4 a u t ie sy o Chn s a e S i  ̄ tf f n ej g 1 0 9,C ia; i 0 hn 3 De a t n Ap l d Ch mity,S h o En iern p rme to f p i e sr e c olo f gne ig,Toa ies y,T y ma 9 0 8 5 y ma Un vri t o a 3 —5 5,J p n) a a
维普资讯
第 2 8卷 第 1 期
Vo . 2 1 8 No. 1
催
化
学
- 1、下载文档前请自行甄别文档内容的完整性,平台不提供额外的编辑、内容补充、找答案等附加服务。
- 2、"仅部分预览"的文档,不可在线预览部分如存在完整性等问题,可反馈申请退款(可完整预览的文档不适用该条件!)。
- 3、如文档侵犯您的权益,请联系客服反馈,我们会尽快为您处理(人工客服工作时间:9:00-18:30)。
测试与表征铜基甲醇合成催化剂失活原因的探讨Ξ周广林,房德仁,程玉春 杨玉兰 (齐鲁石化公司研究院,山东淄博 255400) (齐鲁石化公司第二化肥厂,山东淄博 255400)摘要:采用加压微型反应器和化学分析、原子吸收光谱法、X射线荧光分析、X射线衍射峰宽化法和其它分析方法对工业使用前后的铜基甲醇合成催化剂M K101进行了分析和讨论。
探讨了该催化剂的失活原因。
关键词:甲醇;催化剂;失活中图分类号:TQ426194;TQ2231121 文献标识码:A文章编号:100821143(1999)0420056205A look i n to the cause for deactiva tion of copper-ba sedm ethanol syn thesis ca ta lystZH OU Guang2lin,FA N G D e2ren,CH EN G Y u2chun(R est Inst of Q ilu Petrochem Co rp,Shandong Zibo255400,Ch ina)YA N G Y u2lan(T he2nd Fertiliser P lant of Q ilu Petrochem Co rp,Shandong Zibo255400,Ch ina)Abstract:P ressurized m icro2reacto r and chem ical analysis,atom ic abso rp ti on spectrum,X2ray fluo rescence spectrom etry and XRD w ere used to analyze M K101copper2based m ethano l synthesis catalyst befo re and after industrial use,and the cause fo r deactivati on of the catalyst w as dis2 cussed.Key words:m ethano l;catalyst;deactivati onCLC nu m ber:TQ426194;TQ2231121 D ocu m en t code:AArticle I D:100821143(1999)04200562050 前 言铜基甲醇合成催化剂由于具有低温活性高、选择性好、甲醇纯度高等特点,已在甲醇合成工业中得到广泛应用。
但是,铜基催化剂对使用条件要求苛刻,对诸如硫、磷、氯、羰基化合物等毒物极为敏感,若操作条件不Ξ收稿日期:1998211223当,极易造成失活[1,2]。
铜基催化剂迅速失活的另一原因是该类催化剂耐热稳定性差,对温度变化极其敏感,因而其使用寿命不长。
对此类催化剂的失活原因的研究是工业界和学术界关注的重要课题。
本文利用先进的技术和仪器,对铜基甲醇合成催化剂M K 101在齐鲁石化公司第二化肥厂10万t a 甲醇装置使用8个月后样品进行了活性评价、毒物剖析和微观结构测试,就其失活原因进行了分析和讨论。
1 试验方法111 催化剂样品新鲜催化剂取自齐鲁石化公司第二化肥厂使用前的M K 101,失活催化剂为该厂使用8个月的卸出样品,分上、中、下三段取样。
112 催化剂的活性测试采用加压微反装置评价新鲜催化剂及失活催化剂的反应活性,其流程如图1所示。
图1 活性试验流程F ig .1 Cat alyst activ ity evaluation process 1.钢瓶;2.净化器;3.干燥器;4.稳压阀;5,6.管式恒温反应器;7,8.冷凝器;9,10.湿式流量计测试条件:反应器:<18mm ×400mm 不锈钢管催化剂装量:3m l ,用石英砂按1∶1稀释催化剂粒度:40~60目反应温度:220℃,240℃反应压力:510M Pa 反应空速:10000h -1原料气组成(vo l %):H 276,CO 919,CH 47,CO 23129,N 24%。
还原气组成(vo l %):H 210%,N 290%还原压力:015M Pa 还原空速:2000h -1113 催化剂物性测定为了确定使用后催化剂毒物的种类与含量,用原子吸收光谱法测定N i 、Fe 含量,用比色法测定S 含量,用X 射线荧光分析鉴别和定量分析其他各种微量成分,用高温定碳炉测定催化剂中C 含量。
114 微观结构分析用X 射线衍射与扫描电子显微镜相结合对催化剂内部微粒的形貌、孔隙进行观察。
115 催化剂常规物性数据测定采用压汞法测定了催化剂的比表面、孔容和孔结构,N 2O 脉冲色谱法测量了铜金属比表面。
用颗粒强度测定仪测定催化剂强度。
2 结果与讨论211 活性对M K 101催化剂新鲜样品及甲醇合成塔上、中、下不同部位取的催化剂样,用加压微反评价装置分别测定了其在220℃、240℃的活性。
用时空产率,即单位质量催化剂单位时间内粗甲醇(甲醇、水为主的混合物)的产量来表示催化剂的活性,用相对于新鲜催化剂的时空产率来表示相对活性,其测试结果见表1。
表1 M K101催化剂活性与相对活性Tab.1 Activ ity and relative activ ity of M K101cat alyst反应温度 ℃220240新鲜上中下新鲜上中下时空产率g g・h0193010360105012251136012301150165比活性10144010501241011701110148 从表1可以看出,新鲜M K101的活性较高。
使用过的催化剂的活性在合成塔上部降得最为显著,在220℃时其剩余活性只能达到新鲜催化剂的3187%,240℃时为17%。
床层下部的催化剂在220℃时活性仅为新鲜催化剂的24%,240℃为48%。
因此,不论在合成塔哪一部位,使用过的催化剂都不同程度地失活,其失活程度沿着气体的流向越来越轻。
上部催化剂已严重失活。
212 物化性质卸出的M K01催化剂均为黑色,颗粒完整,无破碎,无粉化。
对其进行了物化性能测试,测试数据见表2。
表2 M K101催化剂工业使用前后物化性质的变化Tab.2 Change i n pysicoche m ical property of M K101cat alyst beforeand af ter i ndustr i al use新鲜样上部取样中部取样下部取样外形尺寸 mm<6×4<517×317<517×317<517×317堆密度 kg・m-31140127612761280破碎强度 N・c m-117113138181521617115孔容 m l・g-1012914012322-012422比表面 m2・g-181********-62144 Cu比表面 m2・g-1601032195--孔分布 % >50mm01271138-0 50~25mm21166116-9112 25~10nm4116644123-37112 10~2nm5519048123-53176含碳量 %51445145-5157 CuO晶粒尺寸 nm85119-- 由表2中数据可以看出:(1)使用后催化剂体积均有轻微的缩小,堆密度相应增加,可能是催化剂由氧化态变为还原态所致。
(2)与新鲜样相比,使用后的催化剂强度在塔的上、中、下段均略有下降,孔结构分析及后面采用扫描电镜进行的分析表明,催化剂结构发生了变化,这说明在合成条件下催化剂结构易发生变化,这种变化导致催化剂强度下降。
(3)使用后上部催化剂50nm以上的大孔有所增加,10nm以下的小孔明显减少,10~50nm的中孔明显增加;下部催化剂的孔分布基本没变。
孔分布的改变对活性和选择性均有影响。
(4)使用后催化剂的比表面和孔容减小,减小程度从合成塔上部到下部越来越轻。
上部催化剂的比表面比新鲜催化剂的减少了28164%,下部催化剂减少了23142%。
结合表1数据,可知上部催化剂的比表面下降大,保留活性低;下部催化剂的比表面下降少,保留活性大。
由此可以认为催化剂比表面减小是引起催化剂失活的原因之一[3]。
Toh ji K 等[4]认为铜基催化剂在使用温度高于227℃时易发生烧结。
对照现场操作数据,催化剂热点温度为240℃左右,因此催化剂在使用过程中,可能由于颗粒内部的温升造成烧结。
(5)使用后催化剂Cu 比表面明显下降,由新鲜催化剂的6010m 2 g 下降到32195m 2g ,下降率为40113%。
表2数据说明催化剂中CuO 晶粒由新鲜时的85nm 长大到119nm 。
A ndrew [5]认为低温甲醇催化剂的活性位是微细的金属铜晶粒,金属铜比表面的下降一者可能是因为催化剂局部过热条件下Cu 晶粒长大,二者可能是因为催化剂毒物N i (CO )4在催化剂上分解并覆盖金属铜表面。
(6)使用后催化剂基本上没有发生积炭。
213 微观结构分析利用扫描电镜对催化剂进行了表面微观结构分析,如图2所示。
图2 催化剂扫描电镜图F ig .2 The SE M m icrographs of fracture of M K -101cat alyst1.新鲜催化剂;2.塔上部取出催化剂 从图2可以看出,新鲜M K 101催化剂是由大小不同的粒子堆积而成,呈微晶状态,颗粒细,大小孔兼有,各元素均匀分布,使用后的催化剂粒子呈层状结构,孔径变大,各元素之间模糊不清。
214 催化剂毒物和含量使甲醇合成催化剂中毒的毒物有硫、氯、羰基铁和羰基镍等。
为了充分了解使用后催化剂失活的原因并确定使用过的催化剂毒物的种类,用X 射线荧光分析法分析了甲醇废催化剂毒物分布,结果显示使用后催化剂上毒物主要存在N i ,整个床层分布基本一样。
为了确定毒物在废催化剂中含量,用原子吸收光谱法测定了Fe 、N i 含量,用比色法测定了S 含量,结果见表3。
表3 废催化剂中毒物含量(Λg g)Tab.3 Po ison con ten t of used cat alyst(Λg g)毒物S Fe N i上部取样583194667中部取样575105805下部取样042152805新鲜样03025由表3可见,废催化剂中N i含量相当高,上部为4667Λg g,中部为5805Λg g。
N i 是铜基催化剂的毒物,当甲醇合成催化剂上Fe+N i沉积到300Λg g时,催化剂活性大约降低2倍多[3]。
由于原料油及设备的原因,工艺气中含有大量的羰基铁和羰基镍。
它们在合成塔内被催化分解,覆盖在催化剂表面,破坏活性点以及提供不希望的催化活性[6],由此可以认为,催化剂活性下降的原因之一是N i(CO)4毒物导致催化剂中毒。