铸造工艺流程图
铸造工艺流程图

入库
抽检 混砂及造型 记录
工序
型砂抽检
检测
熔炼浇注工 记录 成分及金相
序
检测
检测
记录 后处理工序
外观及尺寸 检测
不合格 报废处理
合格 砂型质量检 查
本体检测或 不合格 报废 合格 记录保存
砂型硬度及 表面质量
返修或报废 不合格
合格
入库
检验记录要可靠 统计分析才有效
谢谢
造型工序工艺流程图 SHELL MOULDING PROCESS FLOW CHART
混砂工序
模具检查
工装模具 (行车)
合
格
型
砂型硬度
砂
检查外观 吹净散砂
造型 (造型机)
喷脱模剂 (造型机)
砂芯检查 (下芯前)
合 格 砂 芯
制芯工段
下芯平稳 一次到位 放置滤网
下芯 (手工)
合箱 (造型机)
浇注 (行车)
检测合格
造型工序
性能检测 (检测仪器)
水分 紧实率 透气性 湿压强度
为社会做贡献 为企业求发展
原材料验收 标准
制芯工序工艺流程图 CORE-MAKING PROCESS FLOW
覆膜砂 (入厂检验)
工装、芯盒 检查
加热温度和 结壳时间
制芯 (射芯机)
飞边、披缝 及散砂清理
干净
修芯 (手工)
砂芯型Hale Waihona Puke 制芯时间原材料验收 标准
生铁 (入厂检验)
原材料验收 标准
废钢 (入厂检验)
灰铁球铁区 分开
配料单
温度、除渣
成分、性能
配料
熔炼
炉前分析
成分化验
铸造工艺流程图011

工装检查 砂芯强度 波美度 温度、时间 砂温、 粉尘含量
原辅材料及 工装准备
制芯 (射芯机)
砂芯涂料 (手工)
砂芯烘烤 (烘烤炉)
至造型
砂处理 (砂处理系统)
工装检查
型砂强度
波美度
温度、时间
卡板检查 吹净浮砂
落砂时机
原辅材料及 工装准备
造型 (造型圈)
预烘 (烘炉)
砂型涂料 (涂料站)
配方
吹氧、净化、造渣、 脱氧、温度、时间
成分、性能、 温度
温度、速度
铸件初清 (手工)
配料 (行车)
熔炼 (电弧炉)
成份化验 (光谱仪)
调整
炉前处理 (手工)
出铁 (行车)
至 清 理
铸件清理生产流程
温度、时间 清洁度
钢件 灰铁件
铸件退火 (退火炉)
抛丸处理 (抛丸机)
外观、尺寸、 机械性能
铸件 初清 输入
入库
检验
清理打磨 (手工)
送热 处理
铸铝生产工艺流程
配比 温度、 时间 温度、 时间 外观、尺寸、 机械性能
制芯 (混砂机)
砂芯烘烤 (烘烤炉)
下芯 (手工) 造型 (混砂机)
合箱 (手工)
浇注 (手工)
打箱 (手工)
清理 (手工)
检验
水分、 风干
熔炼 (中频炉、 地坑炉) 铝锭 回炉料
变质、精炼、 成分、温度
红土砂 擦洗砂 合脂油
红土砂
入库
砂型烘干 (烘炉)
下芯 (手工)
合箱 (合箱机)
浇注 (浇注线)
落砂 (落砂机)
配方
温度、时间
成分、性能、 金相、温度
精密铸造过程工艺流程图
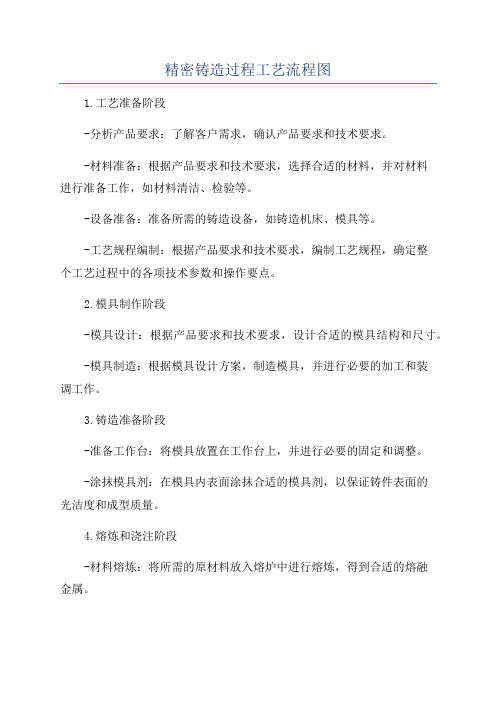
精密铸造过程工艺流程图1.工艺准备阶段-分析产品要求:了解客户需求,确认产品要求和技术要求。
-材料准备:根据产品要求和技术要求,选择合适的材料,并对材料进行准备工作,如材料清洁、检验等。
-设备准备:准备所需的铸造设备,如铸造机床、模具等。
-工艺规程编制:根据产品要求和技术要求,编制工艺规程,确定整个工艺过程中的各项技术参数和操作要点。
2.模具制作阶段-模具设计:根据产品要求和技术要求,设计合适的模具结构和尺寸。
-模具制造:根据模具设计方案,制造模具,并进行必要的加工和装调工作。
3.铸造准备阶段-准备工作台:将模具放置在工作台上,并进行必要的固定和调整。
-涂抹模具剂:在模具内表面涂抹合适的模具剂,以保证铸件表面的光洁度和成型质量。
4.熔炼和浇注阶段-材料熔炼:将所需的原材料放入熔炉中进行熔炼,得到合适的熔融金属。
-浇注准备:将熔融金属倒入浇注容器中,并加热保温,以保证金属保持适当的温度和流动性。
-浇注操作:将浇注容器中的熔融金属缓慢地注入模具中,保持流动性和均匀性,以便于填充模具中的腔体。
5.铸件冷却和固化阶段-铸件连同模具一起冷却:待熔融金属注入模具后,整个模具一同放置在冷却设备中,等待铸件冷却和固化。
-铸件固化时间:根据熔融金属的特性和产品要求,确定合适的固化时间,以保证铸件质量。
6.铸件处理阶段-剪切和去毛刺:将冷却固化的铸件从模具中取出,并进行剪切和去毛刺的处理,以去除不必要的边角和毛刺。
-强化处理:根据产品要求和技术要求,进行必要的强化处理,如热处理、表面处理、喷涂等。
-检验和测试:对铸件进行必要的检验和测试,以确保产品质量符合要求。
-包装和出厂:对合格的铸件进行包装,并做好产品出厂的准备工作。
以上是精密铸造过程工艺流程图,总结了从工艺准备到铸件处理的整个工艺过程。
在每个阶段都需要精确控制各项参数和操作要点,以保证铸件的质量和工艺效率。
同时,工艺流程中的每个环节都需要严格遵守相关的安全规定和操作规程,确保生产过程的安全性和稳定性。
铸造工艺流程

消失模铸造工艺流程一、工艺流程示意图rAEPS EPMMA 预热T 加料、搅拌 T 抽真空 T 喷水雾 T 停止抽真空 T 出料T 干燥T 料仓二、工艺流程 模样生产工艺流程图STMMA干上闭模T 预热模具 T 加料T 合模T 发泡成型 T 冷却T 脱模珠粒可发性组浇 合冒落砂斗 T 水平振动筛 T 型砂冷却 T 提升机 T 磁选、除尘 T 储砂斗冒打机 口磨) 浇、铸件成品却浇(一)预发泡:预发泡目的:为了获得低密度、表面光洁、质量优良的泡沫模样。
流程:预热f加料、搅拌f抽真空f喷水雾f停止抽真空f 出料f干燥f料仓、熟化EPS预发温度100~105C;STMMA 预发温度105~115°C;EPMMA 预发温度120~130C。
进入预发机的加热蒸汽压力在0.15~0.20MPa范围调节。
说明:①间歇式蒸汽预发泡机必须满足加热均匀(蒸汽与珠粒接触)筒体内温度在90~130C范围容易调节和控制。
搅拌要充分、均匀,筒体底部和侧壁要有刮板,防止珠粒因过热而粘壁,搅拌速度可调。
筒体底部冷凝水的排除要畅通,否则影响预发泡效果。
②加热蒸汽压力可调并稳定,且蒸汽中不能夹带水分。
③出料要干净,每批发泡后,筒体内残留的料要吹扫干净。
熟化:把预发泡珠放置几小时以上,让空气进入珠粒内,使珠粒变得干燥有弹性,变形后又能复原的过程。
熟化时间一般为10~24h,熟化时间不能太长否则发泡剂损失太多影响发泡成型质量。
(二)成形发泡的工艺过程为:闭模f预热模具f加料f合模f发泡成型f冷却f脱模f模样熟化要点:珠粒均匀填满模具,模具必须预热到100C,水蒸气温度一般在120C左右,压力为0.15MPa。
模样熟化:将模样置入50~70C的烘干室强制干燥5~6h可达到在室温下自然熟化2天的效果。
(三)模样的粘合对复杂的模样往往不能整体发泡成形,而分块制造,最后需要将各块粘合成整体。
另外,模样与浇冒口系统组成模样组,也需要粘合工序。
铸造生产的工艺流程
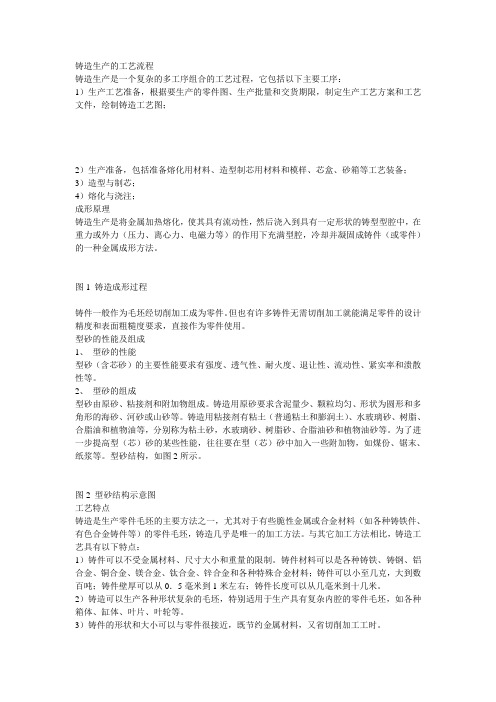
铸造生产的工艺流程铸造生产是一个复杂的多工序组合的工艺过程,它包括以下主要工序:1)生产工艺准备,根据要生产的零件图、生产批量和交货期限,制定生产工艺方案和工艺文件,绘制铸造工艺图;2)生产准备,包括准备熔化用材料、造型制芯用材料和模样、芯盒、砂箱等工艺装备;3)造型与制芯;4)熔化与浇注;成形原理铸造生产是将金属加热熔化,使其具有流动性,然后浇入到具有一定形状的铸型型腔中,在重力或外力(压力、离心力、电磁力等)的作用下充满型腔,冷却并凝固成铸件(或零件)的一种金属成形方法。
图1 铸造成形过程铸件一般作为毛坯经切削加工成为零件。
但也有许多铸件无需切削加工就能满足零件的设计精度和表面粗糙度要求,直接作为零件使用。
型砂的性能及组成1、型砂的性能型砂(含芯砂)的主要性能要求有强度、透气性、耐火度、退让性、流动性、紧实率和溃散性等。
2、型砂的组成型砂由原砂、粘接剂和附加物组成。
铸造用原砂要求含泥量少、颗粒均匀、形状为圆形和多角形的海砂、河砂或山砂等。
铸造用粘接剂有粘土(普通粘土和膨润土)、水玻璃砂、树脂、合脂油和植物油等,分别称为粘土砂,水玻璃砂、树脂砂、合脂油砂和植物油砂等。
为了进一步提高型(芯)砂的某些性能,往往要在型(芯)砂中加入一些附加物,如煤份、锯末、纸浆等。
型砂结构,如图2所示。
图2 型砂结构示意图工艺特点铸造是生产零件毛坯的主要方法之一,尤其对于有些脆性金属或合金材料(如各种铸铁件、有色合金铸件等)的零件毛坯,铸造几乎是唯一的加工方法。
与其它加工方法相比,铸造工艺具有以下特点:1)铸件可以不受金属材料、尺寸大小和重量的限制。
铸件材料可以是各种铸铁、铸钢、铝合金、铜合金、镁合金、钛合金、锌合金和各种特殊合金材料;铸件可以小至几克,大到数百吨;铸件壁厚可以从0.5毫米到1米左右;铸件长度可以从几毫米到十几米。
2)铸造可以生产各种形状复杂的毛坯,特别适用于生产具有复杂内腔的零件毛坯,如各种箱体、缸体、叶片、叶轮等。
铸造工艺流程
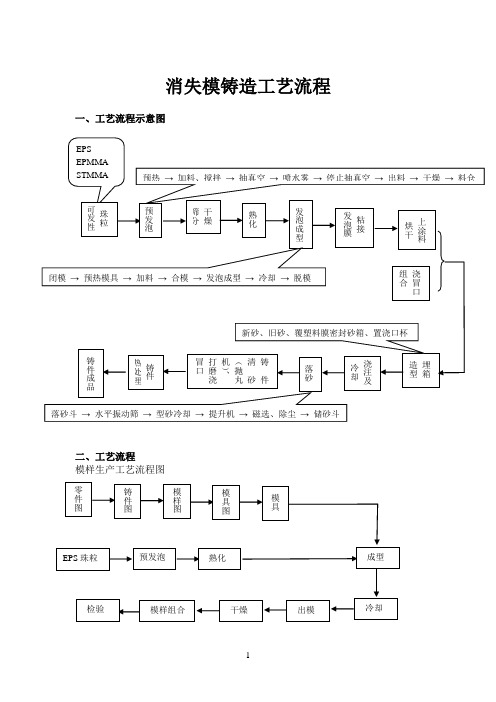
(一)浇注位置的确定
铸件的浇注位置是指浇注时铸件在铸型中所处的位置。正确的浇注位置应能保证获得完整的铸件并使造型、造芯和清理方便。
确定浇注位置的一般原则是:
1)铸件的重要加工面、主要工作面、受力面应尽量放在底部或侧面,以防止这些表面上产生砂眼、气孔、夹渣等铸造缺陷。
2)浇注位置应保证金属液按确定的凝固顺序凝固。如对收缩较大的合金,浇注位置应有利于顺序凝固,铸件厚大部一般应置于浇注位置的上方,便于设置补缩胃口。
(2)粘结剂。无机粘结剂有膨润土、水玻璃、硅溶胶;有机粘结剂有糖浆、树脂、淀粉、糊精、白乳胶和By粘结剂等。常使用的粘结剂:膨润土、白乳胶和By粘结剂。
(3)载体(溶剂)消失模铸造涂料从经济及安全的角度来考虑,大多数工厂在实际生产中使用水基涂料较多。醇基涂料只用来埋箱时临时阻缝和修补。
(4)悬浮剂、触变剂为使涂料中耐火粉料与粘结剂充分混合并处于悬浮状态,使涂料搅拌好成为膏状,需加入悬浮剂。尽管膨润土也是很好的悬浮剂,还必须加入羧甲基纤维素(CMC)、By粘结剂,它们也是很好的触变剂。
5、涂挂方法
刷涂、淋凃、浸涂法和喷涂。
浸凃时应注意:
1涂料应处于连续搅拌状态下,并控制其温度。
2涂料搅拌应慢速,注意防止卷气。
3浸凃时应选择模样浸入涂料的方向、部位,有利于防止模样变形。
4模样涂覆的涂料要全面均匀,不得有未上涂料模样暴露部位。
5模样从涂料中取出、运送、放置均要考虑防止模样变形问题。
6、涂料的烘干
3)浇注位置应有利于型芯的定位、支撑和排气,尽量避免吊芯、悬臂芯。
4)铸件的大平面应置于下部或斜下部以防夹砂等缺陷。为了方便造型,常采用“横做立浇”、“平做斜浇”等方法。
5)铸件的薄壁部分应置于下部或侧面以防止浇不足、冷隔等铸造缺陷。
生产工艺流程图和铸造工艺流程

生产工艺流程图铸造生产的工艺流程铸造生产是一个复杂的多工序组合的工艺过程,它包括以下主要工序:1〕生产工艺准备,根据要生产的零件图、生产批量和交货期限,制定生产工艺方案和工艺文件,绘制铸造工艺图;2〕生产准备,包括准备熔化用材料、造型制芯用材料和模样、芯盒、砂箱等工艺装备;3〕造型与制芯;4〕熔化与浇注;成形原理铸造生产是将金属加热熔化,使其具有流动性,然后浇入到具有一定形状的铸型型腔中,在重力或外力〔压力、离心力、电磁力等〕的作用下充满型腔,冷却并凝固成铸件〔或零件〕的一种金属成形方法.图1 铸造成形过程铸件一般作为毛坯经切削加工成为零件.但也有许多铸件无需切削加工就能满足零件的设计精度和表面粗糙度要求,直接作为零件使用.型砂的性能与组成1、型砂的性能型砂〔含芯砂〕的主要性能要求有强度、透气性、耐火度、退让性、流动性、紧实率和溃散性等.2、型砂的组成型砂由原砂、粘接剂和附加物组成.铸造用原砂要求含泥量少、颗粒均匀、形状为圆形和多角形的海砂、河砂或山砂等.铸造用粘接剂有粘土〔普通粘土和膨润土〕、水玻璃砂、树脂、合脂油和植物油等,分别称为粘土砂,水玻璃砂、树脂砂、合脂油砂和植物油砂等.为了进一步提高型〔芯〕砂的某些性能,往往要在型〔芯〕砂中加入一些附加物,如煤份、锯末、纸浆等.型砂结构,如图2所示.图2 型砂结构示意图工艺特点铸造是生产零件毛坯的主要方法之一,尤其对于有些脆性金属或合金材料〔如各种铸铁件、有色合金铸件等〕的零件毛坯,铸造几乎是唯一的加工方法.与其它加工方法相比,铸造工艺具有以下特点:1〕铸件可以不受金属材料、尺寸大小和重量的限制.铸件材料可以是各种铸铁、铸钢、铝合金、铜合金、镁合金、钛合金、锌合金和各种特殊合金材料;铸件可以小至几克,大到数百吨;铸件壁厚可以从0.5毫米到1米左右;铸件长度可以从几毫米到十几米.2〕铸造可以生产各种形状复杂的毛坯,特别适用于生产具有复杂内腔的零件毛坯,如各种箱体、缸体、叶片、叶轮等.3〕铸件的形状和大小可以与零件很接近,既节约金属材料,又省切削加工工时.4〕铸件一般使用的原材料来源广、铸件成本低.5〕铸造工艺灵活,生产率高,既可以手工生产,也可以机械化生产.铸件的手工造型手工造型的主要方法砂型铸造分为手工造型〔制芯〕和机器造型〔制芯〕.手工造型是指造型和制芯的主要工作均由手工完成;机器造型是指主要的造型工作,包括填砂、紧实、起模、合箱等由造型机完成.泊头铸造工量具友介绍手工造型的主要方法:手工造型因其操作灵活、适应性强,工艺装备简单,无需造型设备等特点,被广泛应用于单件小批量生产.但手工造型生产率低,劳动强度较大.手工造型的方法很多,常用的有以下几种:1.整模造型对于形状简单,端部为平面且又是最大截面的铸件应采用整模造型.整模造型操作简便,造型时整个模样全部置于一个砂箱内,不会出现错箱缺陷.整模造型适用于形状简单、最大截面在端部的铸件,如齿轮坯、轴承座、罩、壳等〔图2〕.图整模造型2.分模造型当铸件的最大截面不在铸件的端部时,为了便于造型和起模,模样要分成两半或几部分,这种造型称为分模造型.当铸件的最大截面在铸件的中间时,应采用两箱分模造型〔图3〕,模样从最大截面处分为两半部分〔用销钉定位〕.造型时模样分别置于上、下砂箱中,分模面〔模样与模样间的接合面〕与分型面〔砂型与砂型间的接合面〕位置相重合.两箱分模造型广泛用于形状比较复杂的铸件生产,如水管、轴套、阀体等有孔铸件.图3 套管的分模两箱造型过程铸件形状为两端截面大、中间截面小,如带轮、槽轮、车床四方刀架等,为保证顺利起模,应采用三箱分模造型〔图4〕.此时分模面应选在模样的最小截面处,而分型面仍选在铸件两端的最大截面处,由于三箱造型有两个分型面,降低了铸件高度方向的尺寸精度,增加了分型面处飞边毛刺的清整工作量,操作较复杂,生产率较低,不适用于机器造型,因此,三箱造型仅用于形状复杂、不能用两箱造型的铸件生产.图4 三箱分模造型举例3.活块模造型铸件上妨碍起模的部分〔如凸台、筋条等〕做成活块,用销子或燕尾结构使活块与模样主体形成可拆连接.起模时先取出模样主体,活块模仍留在铸型中,起模后再从侧面取出活块的造型方法称为活块模造型〔图5〕.活块模造型主要用于带有突出部分而妨碍起模的铸件、单件小批量、手工造型的场合.如果这类铸件批量大,需要机器造型时,可以用砂芯形成妨碍起模的那部分轮廓.图5 角铁的活块模造型工艺过程4.挖砂造型当铸件的外部轮廓为曲面〔如手轮等〕其最大截面不在端部,且模样又不宜分成两半时,应将模样做成整体,造型时挖掉妨碍取出模样的那部分型砂,这种造型方法称为挖砂造型.挖砂造型的分型面为曲面,造型时为了保证顺利起模,必须把砂挖到模样最大截面处〔图6〕.由于是手工挖砂,操作技术要求高,生产效率低,只适用于单件、小批量生产.图6 手轮的挖砂造型的工艺过程手工制芯型芯用来形成铸件内部空腔或局部外形.由于型芯的表面被高温金属液包围,长时间受到浮力作用和高温金属液的烘烤作用;铸件冷却凝固时,砂芯往往会阻碍铸件自由收缩;砂芯清理也比较困难.因此造芯用的芯砂要比型砂具有更高的强度、透气性、耐高温性、退让性和溃散性.手工制芯由于无需制芯设备,工艺装备简单,应用得很普遍.根据砂芯的大小和复杂程度,手工制芯用芯盒有整体式芯盒、对开式芯盒和可拆式芯盒,如图7所示.图7 芯盒制芯示意图零件、模样、芯盒与铸件的关系模样用来形成铸件的外部轮廓,芯盒用来制作砂芯,形成铸件的内部轮廓.造型时分别用模样和芯盒制作铸型和型芯.图1 分别表示零件、模样、芯盒和铸件的关系.制造模样和芯盒所选用的材料,与铸件大小、生产规模和造型方法有关.单件小批量生产、手工造型时常用木材制作模样和芯盒,大批量生产、机器造型时常用金属材料〔如铝合金、铸铁等〕或硬塑料制作模样和芯盒.图零件、模样、芯盒与铸件的关系铸造铸件常见缺陷分析铸造工艺过程复杂,影响铸件质量的因素很多,往往由于原材料控制不严,工艺方案不合理,生产操作不当,管理制度不完善等原因,会使铸件产生各种铸造缺陷.常见的铸件缺陷名称、特征和产生的原因,见表.常见铸件缺陷与产生原因缺陷名称特征产生的主要原因气孔在铸件内部或表面有大小不等的光滑孔洞①炉料不干或含氧化物、杂质多;②浇注工具或炉前添加剂未烘干;③型砂含水过多或起模和修型时刷水过多;④型芯烘干不充分或型芯通气孔被堵塞;⑤春砂过紧,型砂透气性差;⑥浇注温度过低或浇注速度太快等缩孔与缩松缩孔多分布在铸件厚断面处,形状不规则,孔内粗糙①铸件结构设计不合理,如壁厚相差过大,厚壁处未放冒口或冷铁;②浇注系统和冒口的位置不对;③浇注温度太高;④合金化学成分不合格,收缩率过大,冒口太小或太少砂眼在铸件内部或表面有型砂充塞的孔眼①型砂强度太低或砂型和型芯的紧实度不够,故型砂被金属液冲入型腔;②合箱时砂型局部损坏;③浇注系统不合理,内浇口方向不对,金属液冲坏了砂型;④合箱时型腔或浇口内散砂未清理干净粘砂铸件表面粗糙,粘有一层砂粒①原砂耐火度低或颗粒度太大;②型砂含泥量过高,耐火度下降;③浇注温度太高;④湿型铸造时型砂中煤粉含量太少;⑤干型铸造时铸型未刷涂斜或涂料太薄夹砂铸件表面产生的金属片状突起物,在金属片状突起物与铸件之间夹有一层型砂①型砂热湿拉强度低,型腔表面受热烘烤而膨胀开裂;②砂型局部紧实度过高,水分过多,水分烘干后型腔表面开裂;③浇注位置选择不当,型腔表面长时间受高温铁水烘烤而膨胀开裂;④浇注温度过高,浇注速度太慢错型铸件沿分型面有相对位置错移①模样的上半模和下半模未对准;②合箱时,上下砂箱错位;③上下砂箱未夹紧或上箱未加足够压铁,浇注时产生错箱冷隔铸件上有未完全融合的缝隙或洼坑,其交接处是圆滑的①浇注温度太低,合金流动性差;②浇注速度太慢或浇注中有断流;③浇注系统位置开设不当或内浇道横截面积太小;④铸件壁太薄;⑤直浇道〔含浇口杯〕高度不够;⑥浇注时金属量不够,型腔未充满浇不足铸件未被浇满裂纹铸件开裂,开裂处金属表面有氧化膜①铸件结构设计不合理,壁厚相差太大,冷却不均匀;②砂型和型芯的退让性差,或春砂过紧;③落砂过早;④浇口位置不当,致使铸件各部分收缩不均匀常见铸件缺陷与其预防措施序缺陷名称缺陷特征预防措施1气孔在铸件内部、表面或近于表面处,有大小不等的光滑孔眼,形状有圆的、长的与不规则的,有单个的,也有聚集成片的.颜色有白色的或带一层暗色,有时覆有一层氧化皮.降低熔炼时流言蜚语金属的吸气量.减少砂型在浇注过程中的发气量,改进铸件结构,提高砂型和型芯的透气性,使型内气体能顺利排出.2缩孔在铸件厚断面内部、两交界面的内部与厚断面和薄断面交接处的内部或表面,形状不规则,孔内粗糙不平,晶粒粗大.壁厚小且均匀的铸件要采用同时凝固,壁厚大且不均匀的铸件采用由薄向厚的顺序凝固,合理放置冒口的冷铁.3缩松在铸件内部微小而不连贯的缩孔,聚集在一处或多处,晶粒粗大,各晶粒间存在很小的孔眼,水压试验时渗水.壁间连接处尽量减小热节,尽量降低浇注温度和浇注速度.4渣气孔在铸件内部或表面形状不规则的孔眼.孔眼不光滑,里面全部或部分充塞着熔渣.提高铁液温度.降低熔渣粘性.提高浇注系统的挡渣能力.增大铸件内圆角.5砂眼在铸件内部或表面有充塞着型砂的孔眼.严格控制型砂性能和造型操作,合型前注意打扫型腔.6热裂在铸件上有穿透或不穿透的裂纹〔注要是弯曲形的〕,开裂处金属表皮氧化.严格控制铁液中的S、P含量.铸件壁厚尽量均匀.提高型砂和型芯的退让性.浇冒口不应阻碍铸件收缩.避免壁厚的突然改变.开型不能过早.不能激冷铸件.7冷裂在铸件上有穿透或不穿透的裂纹〔主要是直的〕,开裂处金属表皮氧化.8粘砂在铸件表面上,全部或部分覆盖着一层金属〔或金属氧化物〕与砂〔或涂料〕的混〔化〕合物或一层烧结构的型砂,致使铸件表面粗糙.减少砂粒间隙.适当降低金属的浇注温度.提高型砂、芯砂的耐火度.9夹砂在铸件表面上,有一层金属瘤状物或片状物,在金属瘤片和铸件之间夹有一层型砂.严格控制型砂、芯砂性能.改善浇注系统,使金属液流动平稳.大平面铸件要倾斜浇注.10冷隔在铸件上有一种未完全融合的缝隙或洼坑,其交界边缘是圆滑的.提高浇注温度和浇注速度.改善浇注系统.浇注时不断流.11浇不到由于金属液未完全充满型腔而产生的铸件缺肉.提高浇注温度和浇注速度.不要断流和防止跑火.铸造铸件金属液的浇注生产中,浇注时应遵循高温出炉,低温浇注的原则.因为提高金属液的出炉温度有利于夹杂物的彻底熔化、熔渣上浮,便于清渣和除气,减少铸件的夹渣和气孔缺陷;采用较低的浇注温度,则有利于降低金属液中的气体溶解度、液态收缩量和高温金属液对型腔表面的烘烤,避免产生气孔、粘砂和缩孔等缺陷.因此,在保证充满铸型型腔的前提下,尽量采用较低的浇注温度. 把金属液从浇包注入铸型的操作过程称为浇注.浇注操作不当会引起浇不足、冷隔、气孔、缩孔和夹渣等铸造缺陷,和造成人身伤害.为确保铸件质量、提高生产率以与做到安全生产,浇注时应严格遵守下列操作要领:〔1〕浇包、浇注工具、炉前处理用的孕育剂、球化剂等使用前必须充分烘干,烘干后才能使用.〔2〕浇注人员必须按要求穿好工作服,并配戴防护眼镜,工作场地应通畅无阻.浇包内的金属液不宜过满,以免在输送和浇注时溢出伤人.〔3〕正确选择浇注速度,即开始时应缓慢浇注,便于对准浇口,减少熔融金属对砂型的冲击和利于气体排出;随后快速浇注,以防止冷隔;快要浇满前又应缓慢浇注,即遵循慢、快、慢的原则.〔4〕对于液态收缩和凝固收缩比较大的铸件,如中、大型铸钢件,浇注后要与时从浇口或冒口补浇.〔5〕浇注时应与时将铸型中冒出的气体点燃顺气,以免由于铸型憋气而产生气孔,以与由于气体的不完全燃烧而损害人体健康和污染空气.铸造的坩埚炉熔化常用的铸造有色金属有铸造铝合金、铸造铜合金、铸造镁合金和铸造锌合金等.有色金属的熔点低,其常用的熔化用炉有坩埚炉和反射炉两类,用电、油、煤气或焦碳等作为燃料.中、小工厂普遍采用坩埚炉熔化,如电阻坩埚炉、焦碳坩埚炉等,生产大型铸件时一般使用反射炉熔化,如重油反射炉、煤气反射炉等.如图是坩埚炉的示意图.图坩埚炉的示意图熔模铸造熔模铸造又称失蜡铸造或精密铸造.它是用易熔材料〔如蜡料〕制成模样并组装成蜡模组,然后在模样表面上反复涂覆多层耐火涂料制成模壳,待模壳硬化和干燥后将蜡模熔去,模壳再经高温焙烧后浇注获得铸件的一种铸造方法.熔模铸造工艺过程.可用熔模铸造法生产的合金种类有碳素钢、合金钢、耐热合金、不锈钢、精密合金、永磁合金、轴承合金、铜合金、铝合金、钛合金和球墨铸铁等.熔模铸件的形状一般都比较复杂,铸件上可铸出孔的最小直径可达0.5mm,铸件的最小壁厚为0.3mm.在生产中可将一些原来由几个零件组合而成的部件,通过改变零件的结构,设计成为整体零件而直接由熔模铸造铸出,以节省加工工时和金属材料的消耗,使零件结构更为合理.熔模铸件的重量大多为零点几十牛〔即几十克到几公斤〕,太重的铸件用熔模铸造法生产较为麻烦,但目前生产大的熔模铸件的重量已达800牛左右.熔模铸造工艺过程较复杂,且不易控制,使用和消耗的材料较贵,故它适用于生产形状复杂、精度要求高、或很难进行其它加工的小型零件,如涡轮发动机的叶片等.金属型铸造,硬模铸造将液态金属浇入用金属材料制成的铸型而获得铸件的方法,称为金属型铸造.金属铸型可反复使用,又称为永久型铸造或硬模铸造.金属型一般用耐热铸铁或耐热钢做成.金属型铸造又称硬模铸造,它是将液体金属浇入金属铸型,以获得铸件的一种铸造方法.铸型是用金属制成,可以反复使用多次〔几百次到几千次〕.金属到铸造与砂型铸造比较:在技术上与经济上有许多优点.〔1〕金属型生产的铸件,其机械性能比砂型铸件高.同样合金,其抗拉强度平均可提高约25%,屈服强度平均提高约20%,其抗蚀性能和硬度亦显著提高;〔2〕铸件的精度和表面光洁度比砂型铸件高,而且质量和尺寸稳定;〔3〕铸件的工艺收得率高,液体金属耗量减少,一般可节约15~30%;〔4〕不用砂或者少用砂,一般可节约造型材料80~100%;此外,金属型铸造的生产效率高;使铸件产生缺陷的原因减少;工序简单,易实现机械化和自动化.金属型铸造虽有很多优点,但也有不足之处.如:<1> 金属型制造成本高;<2> 金属型不透气,而且无退让性,易造成铸件洗不足、开裂或铸铁件白日等缺陷;<3> 金属型铸造时,铸型的工作温度、合金的浇注温度和浇注速度,铸件在铸型中停留的时间,以与所用的涂料等,对铸件的质量的影响甚为敏感,需要严格控制.金属型铸造目前所能生产的铸件,在重量和形状方面还有一定的限制,如对黑色金属只能是形状简单的铸件;铸件的重量不可太大;壁厚也有限制,较小的铸件壁厚无法铸出.因此,在决定采用金属型铸造时,必须综合考虑下列各因素:铸件形状和重量大小必须合适;要有足够的批量;完成生产任务的期限许可.金属型铸件形成过程的特点金属型和砂型,在性能上有显著的区别,如砂型有透气性,而金属型则没有;砂型的导热性差,金属型的导热性很好,砂型有退让性,而金属型没有等.金属型的这些特点决定了它在铸件形成过程中有自己的规律.型腔内气体状态变化对铸件成型的影响:金属在充填时,型腔内的气体必须迅速排出,但金属又无透气性,只要对工艺稍加疏忽,就会给铸件的质量带来不良影响.铸件凝固过程中热交换的特点:金属液一旦进入型腔,就把热量传给金属型壁.液体金属通过型壁散失热量,进行凝固并产生收缩,而型壁在获得热量,升高温度的同时产生膨胀,结果在铸件与型壁之间形成了"间隙〞.在"铸件一间隙一金属型〞系统未到达同一温度之前,可以把铸件视为在"间隙〞中冷却,而金属型壁则通过"间隙〞被加热.金属型阻碍收缩对铸件的影响:金属型或金属型芯,在铸件凝固过磋甲无退让性,阻碍铸件收缩,这是它的又一特点.金属型铸造工艺1金属到的预热未预热的金属型不能进行浇注.这是因为金属型导热性好/液体金属冷却决,流动性剧烈降低,容易使铸件出现冷隔、浇不足夹杂、气孔等缺陷.未预热的金属型在浇注时,铸型,将受到强烈的热击,应力倍增,使其极易破坏.因此,金属型在开始工作前,应该先预热,适宜的预热温度〔即工作温度〕,随合金的种类、铸件结构和大小而定,一般通过试验确定.一般情况下,金属型的预热温度不低于1500C.金属型的预热方法有:〔1〕用喷灯或煤气火焰预热;〔2〕采用电阻加热器;〔3〕采用烘箱加热,其优点是温度均匀,但只适用于小件的金属型;〔4〕先将金属型放在炉上烘烤,然后浇注液体金属将金属型烫热.这种方法,只适用于小型铸型,因它要浪费一些金属液,也会降低铸型寿命.2金属型的浇注金属型的浇注温度,一般比砂型铸造时高.可根据合金种类、如化学成分、铸件大小和壁厚,通过试验确定.下表中数据可供参考.各种合金的浇注温度合金种类浇注温度℃合金种类浇注温度℃铝锡合金350~450 黄铜900~950锌合金450~480 锡青铜1100~1150铝合金680~740 铝青铜1150~1300镁合金715~740 铸铁1300~1370由于金属型的激冷和不透气,浇注速度应做到先慢,后快,再慢.在浇注过程中应尽量保证液流平稳.3铸件的出型和抽芯时间如果金属型芯在铸件中停留的时间愈长,由于铸件收缩产生的抱紧型芯的力就愈大,因此需要的抽芯力也愈大.金属型芯在镜件中最适宜的停留时间,是当铸件冷却到塑性变形温度X 围,并有足够的强度时,这时是抽芯最好的时机.铸件在金属型中停留的时间过长,型壁温度升高,需要更多的冷却时间,也会降低金属型的生产率.最合适的拔芯与铸件出型时间,一般用试验方法确定.4金属型工作温度的调节要保证金属型铸件的质量稳定,生产正常,首先要使金属型在生产过程中温度变化恒定.所以每浇一次,就需要将金属型打开,停放一段时间,待冷至规定温度时再浇.如靠自然冷却,需要时间较长,会降低生产率,因此常用强制冷却的方法.冷却的方式一般有以下几种:〔1〕风冷:即在金属型外围吹风冷却,强化对流散热.风冷方式的金属型,虽然结构简单,容易制造,成本低,但冷却效果不十分理想.〔2〕间接水冷:在金属型背面或某一局部,镶铸水套,其冷却效果比风冷好,适于浇注铜件或可锻铸铁件.但对浇注薄壁灰铁铸件或球铁铸件,激烈冷却,会增加铸件的缺陷.熔模铸造铸件的特点熔模铸造方法的另一优点是,它可以铸造各种合金的复杂的铸件,特别可以铸造高温合金铸件.如喷气式发动机的叶片,其流线型外廓与冷却用内腔,用机械加工工艺几乎无法形成.用熔模铸造工艺生产不仅可以做到批量生产,保证了铸件的一致性,而且避免了机械加工后残留刀纹的应力集中.熔模铸件尺寸精度较高,一般可达CT4-6〔砂型铸造为CT10~13,压铸为CT5~7〕,当然由于熔模铸造的工艺过程复杂,影响铸件尺寸精度的因素较多,例如模料的收缩、熔模的变形、型壳在加热和冷却过程中的线量变化、合金的收缩率以与在凝固过程中铸件的变形等,所以普通熔模铸件的尺寸精度虽然较高,但其一致性仍需提高〔采用中、高温蜡料的铸件尺寸一致性要提高很多〕.压制熔模时,采用型腔表面光洁度高的压型,因此,熔模的表面光洁度也比较高.此外,型壳由耐高温的特殊粘结剂和耐火材料配制成的耐火涂料涂挂在熔模上而制成,与熔融金属直接接触的型腔内表面光洁度高.所以,熔模铸件的表面光洁度比一般铸造件的高,一般可达Ra.1.6~3.2μm.熔模铸造最大的优点就是由于熔模铸件有着很高的尺寸精度和表面光洁度,所以可减少机械加工工作,只是在零件上要求较高的部位留少许加工余量即可,甚至某些铸件只留打磨、抛光余量,不必机械加工即可使用.由此可见,采用熔模铸造方法可大量节省机床设备和加工工时,大幅度节约金属原材料消耗.铸造生产的工艺流程铸造生产是一个复杂的多工序组合的工艺过程,它包括以下主要工序:1〕生产工艺准备,根据要生产的零件图、生产批量和交货期限,制定生产工艺方案和工艺文件,绘制铸造工艺图;2〕生产准备,包括准备熔化用材料、造型制芯用材料和模样、芯盒、砂箱等工艺装备;3〕造型与制芯;4〕熔化与浇注;成形原理铸造生产是将金属加热熔化,使其具有流动性,然后浇入到具有一定形状的铸型型腔中,在重力或外力〔压力、离心力、电磁力等〕的作用下充满型腔,冷却并凝固成铸件〔或零件〕的一种金属成形方法.图1 铸造成形过程铸件一般作为毛坯经切削加工成为零件.但也有许多铸件无需切削加工就能满足零件的设计精度和表面粗糙度要求,直接作为零件使用.型砂的性能与组成1、型砂的性能型砂〔含芯砂〕的主要性能要求有强度、透气性、耐火度、退让性、流动性、紧实率和溃散性等.2、型砂的组成型砂由原砂、粘接剂和附加物组成.铸造用原砂要求含泥量少、颗粒均匀、形状为圆形和多角形的海砂、河砂或山砂等.铸造用粘接剂有粘土〔普通粘土和膨润土〕、水玻璃砂、树脂、合脂油和植物油等,分别称为粘土砂,水玻璃砂、树脂砂、合脂油砂和植物油砂等.为了进一步提高型〔芯〕砂的某些性能,往往要在型〔芯〕砂中加入一些附加物,如煤份、锯末、纸浆等.。
铸造工艺流程图
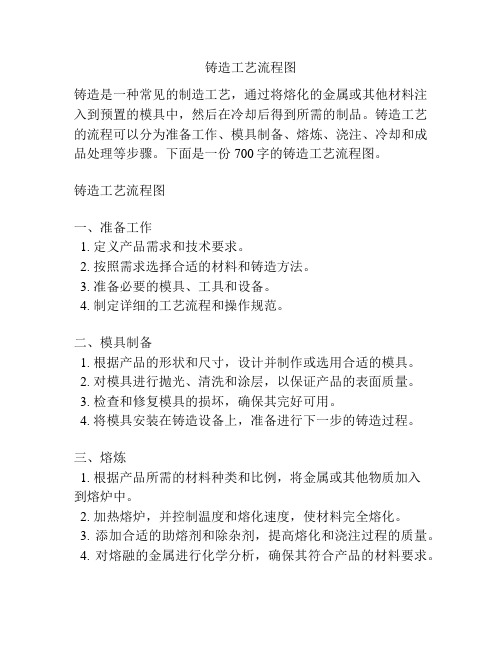
铸造工艺流程图铸造是一种常见的制造工艺,通过将熔化的金属或其他材料注入到预置的模具中,然后在冷却后得到所需的制品。
铸造工艺的流程可以分为准备工作、模具制备、熔炼、浇注、冷却和成品处理等步骤。
下面是一份700字的铸造工艺流程图。
铸造工艺流程图一、准备工作1. 定义产品需求和技术要求。
2. 按照需求选择合适的材料和铸造方法。
3. 准备必要的模具、工具和设备。
4. 制定详细的工艺流程和操作规范。
二、模具制备1. 根据产品的形状和尺寸,设计并制作或选用合适的模具。
2. 对模具进行抛光、清洗和涂层,以保证产品的表面质量。
3. 检查和修复模具的损坏,确保其完好可用。
4. 将模具安装在铸造设备上,准备进行下一步的铸造过程。
三、熔炼1. 根据产品所需的材料种类和比例,将金属或其他物质加入到熔炉中。
2. 加热熔炉,并控制温度和熔化速度,使材料完全熔化。
3. 添加合适的助熔剂和除杂剂,提高熔化和浇注过程的质量。
4. 对熔融的金属进行化学分析,确保其符合产品的材料要求。
四、浇注1. 检查模具的温度和准备状态,确保模具能够承受浇注过程带来的高温和压力。
2. 将熔融金属通过铸造设备的喷嘴注入到模具的腔室中。
3. 控制浇注的速度和流量,使金属在模具中均匀分布,避免产生缺陷。
4. 确保金属填充完全,并保持足够的压力和温度,以确保产品的完整性和质量。
五、冷却1. 模具中的金属开始冷却,温度逐渐降低。
2. 控制冷却速度,以避免产生应力和缺陷。
3. 根据不同的产品要求,冷却时间可以从几分钟到几小时不等。
4. 在冷却过程中,可以进行相关检测和测量,以确保产品的尺寸和质量。
六、成品处理1. 将冷却后的产品从模具中取出,并进行去毛刺和修整等表面处理。
2. 进行必要的热处理,以改善产品的力学性能和结构。
3. 进行质量检查和测试,确保产品符合相关标准和要求。
4. 将成品优化、包装和储存,准备进行后续的销售和使用。
铸造工艺流程图的每一步都非常重要,不同的材料和产品都需要不同的处理方式和参数控制。
铸造工艺流程
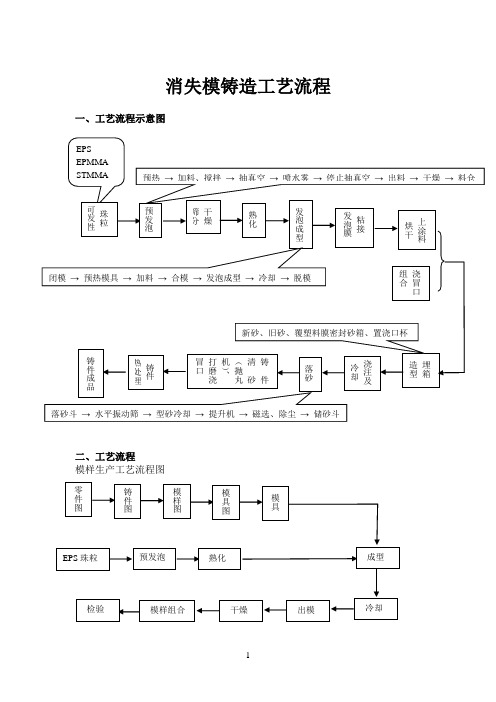
(六)浇注工艺
消失模铸造浇注过程一般采用慢→快→稳的浇注方式。由于消失模铸造是EPS模被液态金属所置换的成形工艺,在浇注过程中,EPS模的分解,气化需要吸收热量,因此浇注温度要比普通砂型铸造的高20~30℃。浇注速度要快,在整个浇注过程中,浇口杯必须始终充满,不得断流,否则会破坏铸型的密封,使铸型真空度下降,造成铸件缺陷,甚至发生塌箱。
(七)砂处理
砂处理浇注以后,回收砂应经处理,其目的有三:
①砂子温度降到50℃以下,砂温高易导致消失模变形;
②除去粉尘,铁豆;
③除去残留的有机物。
工艺流程:
落砂斗→水平振动筛→型砂冷却→提升机→磁选、除尘→储砂斗
粘土砂处理所经过的砂处理设备流程:
液压翻箱机→振动输送落砂机→振动输送筛分机→链式斗提机→风选磁选机→水冷式沸腾冷却床→斗提机→中间砂库→直线振动输送筛→皮带输送机→斗提机→犁式卸料器→日耗砂库→气动雨淋加砂器→特制砂箱→三维振实台→真空系统→浇注
4、涂料配制
水基涂料配制过程:先将耐火材料、膨润土、无水碳酸钠等干料加入混砂机干混10min左右→加入粘接剂溶液和少许水,湿混20~30min →湿料出碾后倒入桶里,加入适量水后进行搅拌。搅拌中加入聚醋酸乙烯乳液等添加物。搅拌器转速大于1380r/min,搅拌时间大于1h。
采用球磨机配制涂料配制工艺:先将耐火材料、活化膨润土和少许水配制成膏状涂料(水分占粉料质量的25%~30%)一起加入球磨机,然后加入适量的水搅拌成涂料,球磨时间7~8h,加入配好的粘接剂和聚醋酸乙烯乳液后再球磨1h,将涂料倒入或用压缩空气压入涂料桶充分搅拌。
铸造工艺流程图E

铸 造 工 艺 流 程 图
调整
heat up melting NG 添加 合金
调整
NG
熔炼
配料 make up the charge
重量 确认
投料 feeding
升温 熔化
成份 分析
OK
测 温
OK
除渣 to slag off
alloy adding Chemical composition analysis
Sand Mixing
报废
练砂
配料
混练
砂型 检验 sand testing
OK
投料
make up the charge
sand mulling
sand feeding
all checking machining coat outside
入库
scrap
报废 报废
scrap NG NG abrasive impact cleaning
装箱
检具全检 grinding appearance Inspection 自检 外观
OK 打磨 Material
材料 检验 Inspection
OK
外观 检验
抛丸
appearance inspection
备注
1.“◇”表示操作、“□”表示检验、“○”表示移动、“△”表示储存
械制造有限公司
流 程 图 制定日期:2013 年 5 月 18 日
to sample
`
moving
砂型 移动
` shakeout 解箱
floating
外观 检验
casting moving 铸件 移动
压铸工艺流程图示

一、压铸(BODY)工艺流程图示1,压铸机调试2,压铸模安装4,模具预热、涂料7,合型(合模)10浇注压射11,保压12,开模、抽芯取件14,清理(整修)17,终检验3,压铸模设计与制造5,涂料配制6,模具清理8,合金熔炼保温9,嵌件准备13,表面质量检查15,时效处理16,铸件浸渗、喷丸处理二、压射压力P2P1 P2P1T1 t2 t3 t4 保压时间升压充填增压注:t1 金属液在压室中未承受压力的时间;P1为一级(慢速)t2 金属液于压室中在压射冲头的作用下,通过内浇口充填型腔的时间;P2为二级(快速)t3 充填刚刚结束时的舜间;P3为三级(增压)t4 最终静压力;P4为补充压实铸件4P yP b=Лd2式中:P b 比压(Mpa); Py 机器的压射力(N);(压射力=压射缸直径×蓄压器压射时间最小压力)d 压室(冲头)直径(MM)选择比压考虑的的主要因素上海旭东压铸技术咨询培训资料压铸工艺参数比压因素选择条件高低壁厚薄壁厚壁压铸件结构形状复杂简单工艺性差些好些结晶温度范围大小压铸合金特性流动性差好密度大小比强度大小阻力大小浇注系统散热速度快慢公布合理不太合理排溢系统截面积大小内浇口速度快慢温度合金与压铸模具温度大小●压铸各种合金常用比压表(Mpa)铸件壁厚≤3(mm) 铸件壁厚>3(mm)合金结构简单结构复杂结构简单结构复杂锌合金20-30 30-40 40-50 50-60铝硅、铝铜合金25-35 35-45 45-60 60-70铝、镁合金30-40 40-50 50-65 65-75镁合金30-40 40-50 50-65 65-80铜合金40-50 50-60 60-70 70-80●压力损失折算系数K直浇道导入口截面F1,K值与内浇铸口截面F2之比>1 =1 <1立式冷室压铸机0.66-0.70 0.72-0.74 0.76-0.78卧式冷室压铸机0.88●压射速度浇注金属液量占压室容积百分数(%) 压射速度(cm/s)≤30 30-4030-60 20-30>60 10-20●高压速度计算公式:VVh= ×[1+(n-1)×0.1]1/4Лd2T式中:Vh 高速压射速度(CM/S);V 型腔容积(CM3);N 型腔数;D 冲头直径(CM);T 适当的充填时间。
铸造工艺流程图
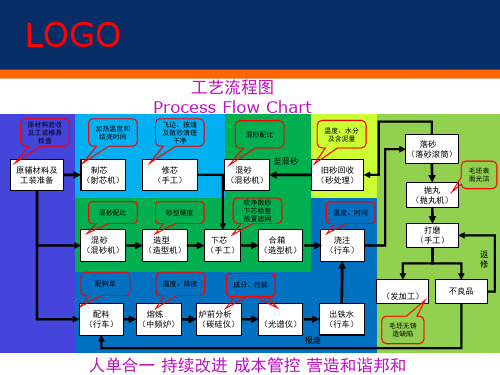
造型 (造型机)
下芯 (手工)
合箱 (造型机)
浇注 (行车)
落砂 (落砂滚筒)
抛丸 (抛丸机)
毛坯表 面光洁
打磨 (手工)
返 修
配料单
温度、除渣
成分、性能
配料 (行车)
熔炼 (中频炉)
炉前分析 (碳硅仪)
(光谱仪)
出铁水 (行车)
报废
(发加工)
毛坯无铸 造缺陷
不良品
人单合一 持续改进 成本管控 营造和谐邦和
砂芯存放 (芯车)
下芯
造型工序
工装、芯盒 (安装)
发挥技能 品质第一 提高效益 做到最好
检验控制流程图 Inspection control flow chart
原材料验收 合格 标准
抽检 制芯工序 记录 砂芯抽检
不合格 合格
报废处理 砂芯存放
标注型号、 时间、数量
检验记录
原材料 (入厂检验)
不 合 格
原材料验收 标准
生铁 (入厂检验)
原材料验收 标准
废钢 (入厂检验)
灰铁球铁区 分开
配料单
温度、除渣
成分、性能
配料
熔炼
炉前分析
成分化验
(行车) (中频炉) (碳硅仪) (光谱仪)
配料单成分 要求
成分调整 (人工)
温度、除渣
温度、时间
回炉料 (行车)
出铁水 (行车)
浇注 (行车)
落砂后处理 工序
为客户提供合格的专业产品与满意的服务
检测合格
造型工序
性能检测 (检测仪器)
水分 紧实率 透气性 湿压强度
为社会做贡献 为企业求发展
原材料验收 标准
铸造工艺流程图
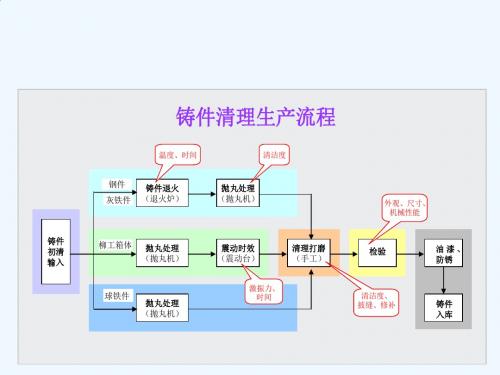
入库
检验
清理打磨 (手工)
送热 处理
铸铝生产工艺流程
配比 温度、 时间 温度、 时间 外观、尺寸、 机械性能
制芯 (混砂机)
砂芯烘烤 (烘烤炉)
下芯 (手工) 造型 (混砂机)
合箱 (手工)
浇注 (手工)
打箱 (手工)
清理 (手工)
检验
水分、 风干
熔炼 (中频炉、 地坑炉) 铝锭 回炉料
变质、精炼、 成分、温度
铸件清理生产流程
温度、时间 清洁度
钢件 灰铁件
铸件退火 (退火炉)
抛丸处理 (抛丸机)
外观、尺寸、 机械性能
铸件 初清 输入
柳工箱体
抛丸处理 (抛丸机)
震动时效 (震动台)
激振力、 时间
清理打磨 (手工)
检验
油漆、 防锈
球铁件
抛丸处理 (抛丸机)
清洁度、 披缝、修补
铸件 入库
精铸生产工艺流程
回收蜡 制蜡棒 (手工) 制蜡料 (搅蜡机) 制蜡模 (压蜡机) 组装 (手工) 粘涂料 (手工) 制涂料 (搅拌机) 蜡处理 (蜡处理槽)
温度、 时间
废钢
成分、温度、 脱氧
5—8层 粘砂 (手工) 硬化 (硬化池) 风干 (风扇) 模壳脱蜡 (脱蜡槽)
熔炼 (中频炉) 浇注 (手工)
焙烧 (焙烧炉)
配方 配方、 浓度
浓度、 时间
干燥 程度
铸件初清 (手工)
新蜡料
水玻璃、 石英粉
石英砂
氯化铵
外观、尺寸、 机械性能
抛丸处理 (抛丸机)
二次抛丸
红土砂 擦洗砂 合脂油
Байду номын сангаас
红土砂
入库
铸造生产工艺流程图
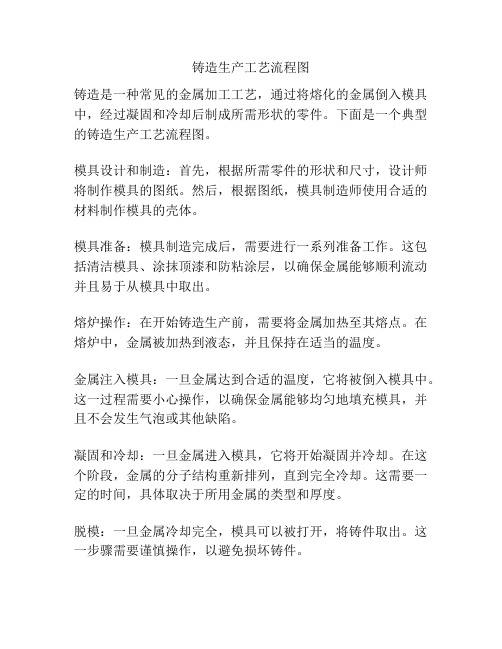
铸造生产工艺流程图铸造是一种常见的金属加工工艺,通过将熔化的金属倒入模具中,经过凝固和冷却后制成所需形状的零件。
下面是一个典型的铸造生产工艺流程图。
模具设计和制造:首先,根据所需零件的形状和尺寸,设计师将制作模具的图纸。
然后,根据图纸,模具制造师使用合适的材料制作模具的壳体。
模具准备:模具制造完成后,需要进行一系列准备工作。
这包括清洁模具、涂抹顶漆和防粘涂层,以确保金属能够顺利流动并且易于从模具中取出。
熔炉操作:在开始铸造生产前,需要将金属加热至其熔点。
在熔炉中,金属被加热到液态,并且保持在适当的温度。
金属注入模具:一旦金属达到合适的温度,它将被倒入模具中。
这一过程需要小心操作,以确保金属能够均匀地填充模具,并且不会发生气泡或其他缺陷。
凝固和冷却:一旦金属进入模具,它将开始凝固并冷却。
在这个阶段,金属的分子结构重新排列,直到完全冷却。
这需要一定的时间,具体取决于所用金属的类型和厚度。
脱模:一旦金属冷却完全,模具可以被打开,将铸件取出。
这一步骤需要谨慎操作,以避免损坏铸件。
修饰和清理:铸件通常需要进行一些修饰和清理工作,以去除多余的金属、毛刺和其他表面缺陷。
这可以通过机械处理、打磨或其他化学方法来完成。
检验和质量控制:最后,所有铸件都需要进行检验和质量控制,以确保其符合设计要求和标准。
这包括尺寸、形状、强度和其他属性的测量和测试。
以上是一个典型的铸造生产工艺流程图。
铸造工艺的具体步骤和细节可能会因不同的铸造过程和材料而有所不同。
如需详细了解特定铸造工艺的工艺流程,请参考相关文献或咨询专业技术人员。
- 1、下载文档前请自行甄别文档内容的完整性,平台不提供额外的编辑、内容补充、找答案等附加服务。
- 2、"仅部分预览"的文档,不可在线预览部分如存在完整性等问题,可反馈申请退款(可完整预览的文档不适用该条件!)。
- 3、如文档侵犯您的权益,请联系客服反馈,我们会尽快为您处理(人工客服工作时间:9:00-18:30)。
Painting WarehouseDongtai Marine Fittings Co., LtdFile No.:DTCP/GY-01-AProduction Process File Page2 Total page: 2Edited by Approved by Version No. Revision times Effective date2009.1.1A 0Dongtai Marine Fittings Co., LtdFile No.:DTCP/GY-02-AWooden Former Process File Page1 Total page: 1 Edited by Approved by Version No. Revision times Effective dateA 02009.1.11Wooden former Processing DrawingWooden former workers shall be familiar with the processing drawing first.Consider the wooden former structure according to processing drawing.2Lofting2.1 Increase and release the contraction allowance in accordance with the measurementsof the drawing.2.2 Release processing allowance according to processing drawing.2.3 Make mode direction according to sub-surface mode. The slope of surface whichneeds to be processed shall be done according to increase, while surface which needs notto be processed shall be done by positivity and negativity.2.4 Those which need to take a variety of processing corrections and riser subsidies shallbe marked in lofting.2.5 Draw the shape and size of the core head and mark the gap between core heads.2.6 If any error of the drawing is found in lofting, report to the techical department timelyand the errors shall be corrected by them.3 Wooden former production3.1 Wooden former structure should be solid and firm and wood should be dry.3.2 Tape nails shall be applied to all the junctions of castings for connection.3.3 All the junctions of castings shall be made into R shape.3.4 Install mold iron and the specimen.4 Painting4.1 After the wooden former is completed, it shall be sand polished by sand feather.4.2 Paint two covers of putty paint.5 After the completion of wood mould, it should be inspected for approval before put into production.Attached files: 1. Wooden Former Technology Card2. Drawing of Wooden Former StructureDongtai Marine Fittings Co., LtdFile No.:DTCP/GY-03-ASand Mixing Operation Procedures Page 1 Total page: 1Edited by Approved by Version No. Revision times Effective dateA 02009.1.1 1. Sand mixer is important equipment for water glass sand production and accordinglyspecial operators must be assigned for its operation and maintenance. The operators musthave a detailed understanding of the basic knowledge of the machine working principle, operation and maintenance.2. Before work, first of all turn on the general power switch in electric control cabinet,check whether “operation, check" knob hits “operation” location and whether the “power” indicator on electric control cabinet and operation box is illuminated.3. After the mould and sandbox are ready, press the “start sand mixing” button, the sandmixing system will automatically operate according to preset program. The “first sand”mixed at the beginning of mixing can be released or used as back sand.4. When the sandbox is filled with sand, press the “stop mixing” button in advance. Stopadding curing agent, water glass and sand and mixer cage continues to rotate for another10 seconds, and then the mixer will be drained of its remaining sand.5. When there is a need to stop in the middle of sand mixing, press the “pause sand mixing” button and stop adding curing agent, water glass and sand. Mixer stops too, butthe pause time shall not exceed the usable time of molding sand. It is forbidden to leavethe remaining sand in the sand mixer for long. If operation stops or no molding sand isused for a long time, press the “sand check and empty” button and drain all the remainingsand within.6. The treatment of first and last sand can be conducted according to the situation.7. During sand mixing, the liquid level within the water glass and curing agent containersand material level of sand storage silo shall be checked frequently to ensure the rightadding of sand, curing agent and water glass.8. According to the requirements of sand filling during sand mixing, Grade 1 and Grade 2shall be steered to status of braking to ensure the proper operation of the machine.Molding sand matching:File No.:DTCP/GY-03-A Dongtai Marine Fittings Co., Ltd Sand Mixing Operation Procedures Page 1 Total page: 1Edited by Approved byVersion No.Revision timesEffective dateA 0 2009.1.1Molding sand matching(t he proportionof new sand to old) Waterglass additio n Curing agent additio nTensio n strengt hwithin 24 hours (MPa)Usable time (min )Mould drawin g time (min )Mould core storage quality(da ys for storage)Castin g qualit y Remar ksFacin g sand core sand 1:4 2.5-3%15-20%>0.620~3060~90 6 ≤5tFacin g sand 1:4 2.5-3%15-20%>0.830~4060~906≤5tBack sand0:1 1.8-2.5%15-20%>0.430~4060~906Note: The model and added quantity of water glass and curing agent shall be determined according to the experimental results in the lab.File No.:DTCP/GY-04-ADongtai Marine Fittings Co., LtdMolding and Core-making Process File Page 1 Total page: 1Edited by Approved by Version No. Revision times Effective dateA 02009.1.1 1Preparation before operation1.1 Get familiar with process file, understand processing characteristics and make sure ofkey operation steps.1.2 Check the certificates of model and core box.1.3 Check whether the movable blocks and affiliates of model and core box are complete,good and fit.1.4 Check the status of sandbox and core iron.1.5 Check the preparation of all materials, such as release agent, ventilation materials,coating materials, fire bricks for gate bottom, fireproof material and pouring system.2 Operation tips2.1 Wipe up the model, core box and brush the release agent.2.2 Place properly the runner, riser, and chill and boxed cofferdam. And when cofferdam is boxed, do not touch model and the preset runner, riser and chill.2.3 Fill in with facing sand the gate, riser, chill, corner and moving blocks where the position can be easily changed but not easy to filled firm. Make them firmly filled withhand or wood sticks while filling a large amount of sand till surrounding and covering thewhole model.2.4 For core-making, pay attention to the core iron position and height. The ventilation materials should be in appropriate number and make the mold against the inside wall ofcore box evenly distributed.2.5 When using fire ceramic tubes and elbow joint to cast pouring system, pay attention tothe seals of joints and blocks of openings in case molding sand should fall into them whilefilling sand.2.6 When using non-stop sand mixer to supply sand, the “first sand” can not be used asfacing sand.File No.:DTCP/GY-04-ADongtai Marine Fittings Co., LtdMolding and Core-making Process File Page 1 Total page: 1Edited by Approved by Version No. Revision times Effective date2009.1.1A 02.7 The pattern drawing time of water glass from self-hardening sand needs to be controlled. The specific time needs to be considered based on such factors as proportion ofcuring agent, sand temperature, and environment temperature and model materials andsubject to trial through operation practice. A balance of model needs to be kept duringmanual pattern drawing. Wood hammer or rubber mallet can be employed to knock fourangles for pattern drawing.2.8 The core box can be dismantled earlier, just strong enough for sand core not to fallapart. Pay attention to the sequence and direction of those parts when they are torn open.They shall be dismantled one bye one and cleaned, assembled sequentially and placed properly. After the core box is dismantled, all moving blocks and moving parts are reassembled and further fastened for saving or follow-up operation.2.9 After pattern drawing and the core is taken out, check the status of cavity and core andgo through necessary modifications, such as flattening the seam sand between movingparts and digging out lifting bar.2.10 Paint according to the regulation and avoid flows and accumulations. If alcohol-basedcoating is used, light it timely to dry it; for some specific parts, spray burner can be employed for further drying but avoid over-burn. The surface temperature of mould andcore must not exceed 180 degree.Attached files 3: Modeling Technology CardFile No.:DTCP/GY-05-ADongtai Marine Fittings Co., LtdAlkalescent Electric Arc FurnacePage1 Total page: 4Steel-Making Process FileEdited by Approved by Version No. Revision times Effective date2009.1.1A 0Electric Arc Furnace Steel-Making ProcessElectric arc furnace steel-making process can be divided into five stages: collection ofraw materials, preparation before smelting, melting period, oxidation period and reduction period.1Collection of raw materialsScrap is the main material for electric arc furnace steel-making and accordingly thequality of scrap is closely related to the quality of steel, costs and electric furnace productivity. Therefore, the following requirements for scrap should be met:1.1 The surface of scrap shall be clean, without serious rusty erosion and oil stains.1.2 There shall be no such nonferrous metals as lead, tin, arsenic, zinc, and copper in scrap.1.3 There shall be no sealed container, inflammable, explosive and poisonous substancesin scrap to secure the safe production.1.4 It shall be clarified that the scrap shall be not rich in phosphor and sulphur as chemical composition.1.5 The shape and size of scrap can not be too large (its section area shall not exceed150mm×150mm, the maximum length shall be no more than 350mm).During electric arcfurnace steel-making, pig iron is normally used to increase carbon addition, which usuallydoes not exceed 30% of furnace charge.1.6. The scrap shall be classified, marked and stored according to their chemical composition.Dongtai Marine Fittings Co., LtdFile No.:DTCP/GY-05-AAlkalescent Electric Arc FurnacePage1 Total page: 4Steel-Making Process FileEdited by Approved by Version No. Revision times Effective date2009.1.1A 02 Preparation before smeltingBurdening is one indispensable part of electric arc furnace steel-making process, and whether it is reasonable concerns whether steel-making can normally go through smelting operation. Reasonable burdening can reduce smelting time. It shall be paid attention in burdening that: firstly, correctly calculate the burden and precisely weigh furnace charge; secondly, size of furnace charge shall be matched according to proportion for good charging and fast smelting; thirdly, all kinds of furnace charge shall be matched and usedbased on quality requirements of steel and smelting method; fourthly, burdening constituents must fulfill processing requirements. Generally, smelting method has the following requirements for the main elements content in furnace charge:2.1 Carbon content. The carbon content in the furnace charge shall guarantee that during oxidation period there is sufficient carbon to conduct carbonization reaction in the hope of removing gas and sundries. The carbon addition shall be determined based upon three factors: carbon burn during melting period, decarbonization volume in oxidation periodand carburization volume in reduction period. It is required that when furnace charge ismelted fully, carbon content level in steel shall be 0.3-0.4% higher than the lower limit of finished product standard.2.2 Silicon content. Normally, the silicon content is no more than 0.8% of furnace charge.2.3 Manganese content. The manganese content will not be taken into consideration forthe matching of regular steel type and its content usually shall be less than 0.3% after it ismelted fully.Phosphor and sulphur content shall basically be very low. The lower, the better. Phosphor content usually shall be less than 0.05% after it is melted fully.In order to make furnace charge inside dense, large materials, middle materials andsmall materials must be matched properly, of which small materials take 15%~20%,middle materials 40%~50%,and large materials 40%。