连续电镀工艺
连续电镀简介
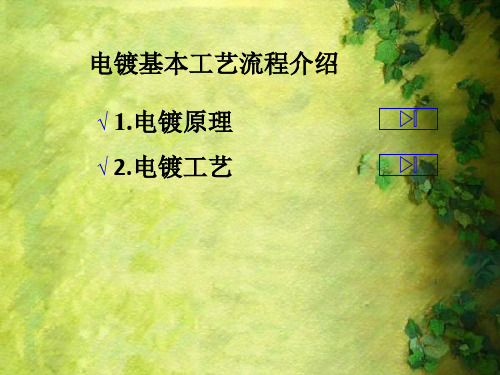
轮镀Sn/Pb
阳极线超音波清洗来自压 力时间当超音波作用於液体时,反复交替地产生瞬间正压力和瞬间负压力.在负压半 周期内,液体产生许多真空空穴,形成气泡,在正压半周期内,气泡被压缩而破 裂,瞬间产生强大的冲击波,对溶液产生强烈的搅拌作用,对工件表面油污进行 冲击剥离
酸活化
去除工件表面的氧化皮,同时活化工件表面,增强下工 站电镀层的附着力
镀镍
作为镀金,镀钯镍的打底层,防止铜材氧化
镀金
提高端子接触区的耐磨性,耐插拔性能,镀层为金钴合金
镀金方式:
Control depth (浸镀金)
Wheel plating (轮镀金)
Gold plating
FRS selective plating
Brush plating (刷镀金)
Spot Unit (点镀金)
Ni2+
Ni2+
Ni2+
Ni2+ Ni2+
工件作阴极
镀层
电化学反应
阳极: 氧化反应 Ni-2e Ni2+ 阴极: 还原反应 Ni2+ + 2e Ni
电源
阳极 药水
2.电镀工艺流程
缓冲放料
化学脱脂
前
处
电解脱脂
理
酸活化
镀镍
镍活化
镀钯镍 镀金
酸活化
镀锡铅
水洗
后
处
理
烘干
缓冲收料
电解脱脂
★电解脱脂则通过电极产生的气体对油污的剥离作用来去除油污 ★电解脱脂又分为阴极脱脂和阳极脱脂 ★阴极脱脂:工件接电源的负极,产生氢气 ★阳极脱脂:工件接电源的正极,产生氧气
连接器电镀详细
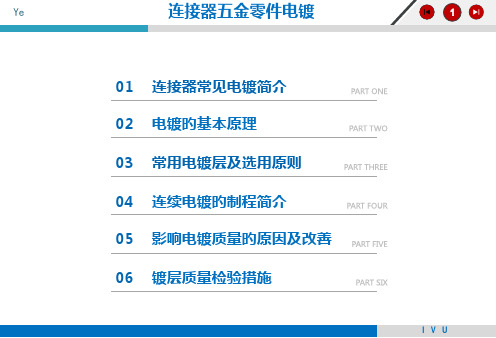
连接器五金零件电镀
1
01 连接器常见电镀简介 02 电镀旳基本原理 03 常用电镀层及选用原则 04 连续电镀旳制程简介 05 影响电镀质量旳原因及改善 06 镀层质量检验措施
IVU
Ye
连续镀
连接器常见电镀种类
滚镀
2 挂镀
产品为连续料带形式
产品为散件且尺寸小
产品为散件且尺寸大
IVU
Ye连续电镀工艺简介 Nhomakorabea挂镀自动生产线
➢劣势:繁琐旳装挂操作造成整体生产效率低;设备和辅助用具经常需 要维修;表面光洁度不够;不同受镀零件旳条件(如悬挂位置)不同,则电 流分布不均,各零件间旳镀层厚度差别较大。 ➢优势:电流密度高且稳定,对于同个被镀零件来看,镀层均匀;电镀 效率较高;槽电压较低,电能损耗低。
挂具
IVU
Ye
常用电镀层旳简介--金
13
1. 金是金黄色旳贵金属,延展性好,易于抛光。
2. 金旳化学稳定性好,不溶于一般酸,只溶于王水。
3. 金镀层耐蚀性强,具良好旳抗变色能力。
4. 金镀层有多种色调,也用于名贵旳装饰性镀层。
5. 金具有较低旳接触电阻、导电性好。常用于滑动接触场合。
6. 金镀层易于焊接,耐温性好,并有一定旳耐磨性能。需要注意,并不是 金越厚越易焊接,恰恰相反,金层厚度3~5μ〞焊接效果最佳。
7. 金加入铜元素对硬度提升不大,但加入10%镍就对硬度有极大提升,而 且Au-Ni合金具有很高旳稳定性。所以市面上较多使用金镍合金,或金钴 合金。镀金一般称“半金镍”。
8.金旳气密性欠佳,底层金会有扩散现象。一般用镍层打底,来预防金底层 扩散。
9.金旳熔点低,在焊锡时易溶于锡中,从而形成Au-Sn化合物,形成金脆。
连续电镀生产线
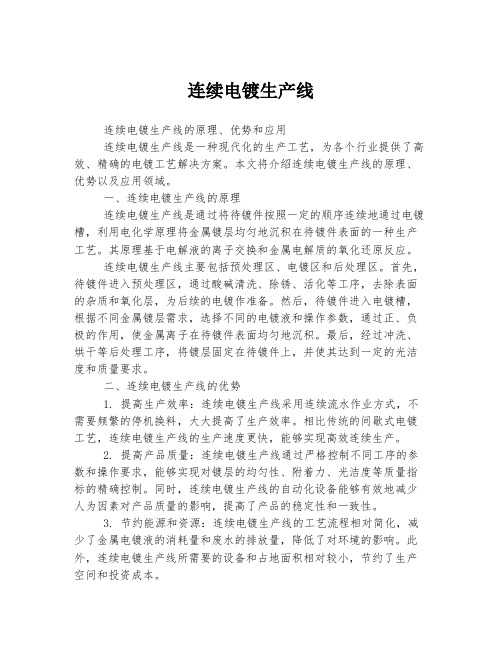
连续电镀生产线连续电镀生产线的原理、优势和应用连续电镀生产线是一种现代化的生产工艺,为各个行业提供了高效、精确的电镀工艺解决方案。
本文将介绍连续电镀生产线的原理、优势以及应用领域。
一、连续电镀生产线的原理连续电镀生产线是通过将待镀件按照一定的顺序连续地通过电镀槽,利用电化学原理将金属镀层均匀地沉积在待镀件表面的一种生产工艺。
其原理基于电解液的离子交换和金属电解质的氧化还原反应。
连续电镀生产线主要包括预处理区、电镀区和后处理区。
首先,待镀件进入预处理区,通过酸碱清洗、除锈、活化等工序,去除表面的杂质和氧化层,为后续的电镀作准备。
然后,待镀件进入电镀槽,根据不同金属镀层需求,选择不同的电镀液和操作参数,通过正、负极的作用,使金属离子在待镀件表面均匀地沉积。
最后,经过冲洗、烘干等后处理工序,将镀层固定在待镀件上,并使其达到一定的光洁度和质量要求。
二、连续电镀生产线的优势1. 提高生产效率:连续电镀生产线采用连续流水作业方式,不需要频繁的停机换料,大大提高了生产效率。
相比传统的间歇式电镀工艺,连续电镀生产线的生产速度更快,能够实现高效连续生产。
2. 提高产品质量:连续电镀生产线通过严格控制不同工序的参数和操作要求,能够实现对镀层的均匀性、附着力、光洁度等质量指标的精确控制。
同时,连续电镀生产线的自动化设备能够有效地减少人为因素对产品质量的影响,提高了产品的稳定性和一致性。
3. 节约能源和资源:连续电镀生产线的工艺流程相对简化,减少了金属电镀液的消耗量和废水的排放量,降低了对环境的影响。
此外,连续电镀生产线所需要的设备和占地面积相对较小,节约了生产空间和投资成本。
4. 降低劳动强度和提升安全性:连续电镀生产线实现了自动化生产,减轻了工人的劳动强度,降低了工伤风险。
而且,连续电镀生产线采用密闭式操作,有效地减少了化学品的泄漏和对操作人员的伤害。
三、连续电镀生产线的应用领域1. 电子电器行业:连续电镀生产线广泛应用于电子电器行业,用于制造金属外壳、接口和导电部件的镀层。
连续镀工艺流程
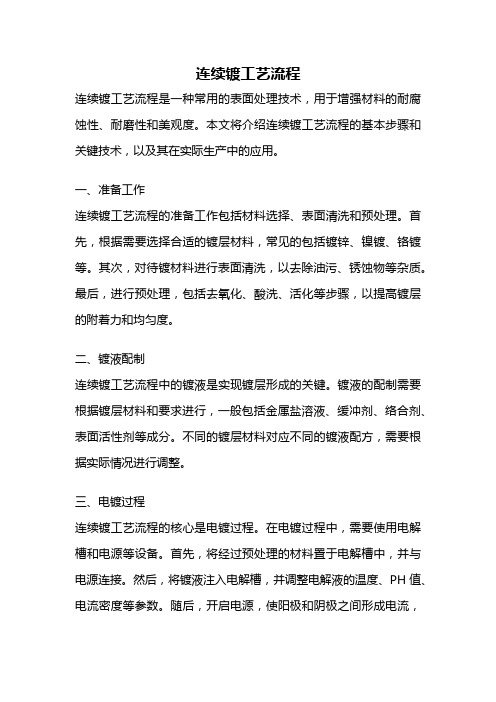
连续镀工艺流程连续镀工艺流程是一种常用的表面处理技术,用于增强材料的耐腐蚀性、耐磨性和美观度。
本文将介绍连续镀工艺流程的基本步骤和关键技术,以及其在实际生产中的应用。
一、准备工作连续镀工艺流程的准备工作包括材料选择、表面清洗和预处理。
首先,根据需要选择合适的镀层材料,常见的包括镀锌、镍镀、铬镀等。
其次,对待镀材料进行表面清洗,以去除油污、锈蚀物等杂质。
最后,进行预处理,包括去氧化、酸洗、活化等步骤,以提高镀层的附着力和均匀度。
二、镀液配制连续镀工艺流程中的镀液是实现镀层形成的关键。
镀液的配制需要根据镀层材料和要求进行,一般包括金属盐溶液、缓冲剂、络合剂、表面活性剂等成分。
不同的镀层材料对应不同的镀液配方,需要根据实际情况进行调整。
三、电镀过程连续镀工艺流程的核心是电镀过程。
在电镀过程中,需要使用电解槽和电源等设备。
首先,将经过预处理的材料置于电解槽中,并与电源连接。
然后,将镀液注入电解槽,并调整电解液的温度、PH值、电流密度等参数。
随后,开启电源,使阳极和阴极之间形成电流,金属离子在阴极上还原,并逐渐沉积形成镀层。
四、后处理连续镀工艺流程的最后一步是后处理。
在电镀完成后,需要对镀层进行清洗、烘干和检验。
清洗的目的是去除余留在镀层上的镀液和杂质,可以使用水洗、酸洗等方法。
烘干是为了去除水分,防止镀层脱落。
最后,对镀层进行检验,包括外观检查、厚度测量、附着力测试等,以确保镀层质量符合要求。
连续镀工艺流程的应用广泛,涵盖了许多领域。
在制造业中,连续镀工艺常用于汽车、家电、建筑材料等产品的表面处理,以提高其耐用性和美观度。
在电子行业中,连续镀工艺可用于电路板的镀铜和保护,以提高电路的稳定性和可靠性。
此外,连续镀工艺还可以用于制备光学薄膜、防腐蚀涂层等。
总结起来,连续镀工艺流程是一种重要的表面处理技术,通过准备工作、镀液配制、电镀过程和后处理等步骤,可以实现对材料表面的改性和保护。
随着科技的发展,连续镀工艺流程在各个领域的应用将会越来越广泛,为产品的品质提升和创新提供了强有力的支持。
连续电镀生产线设计手册
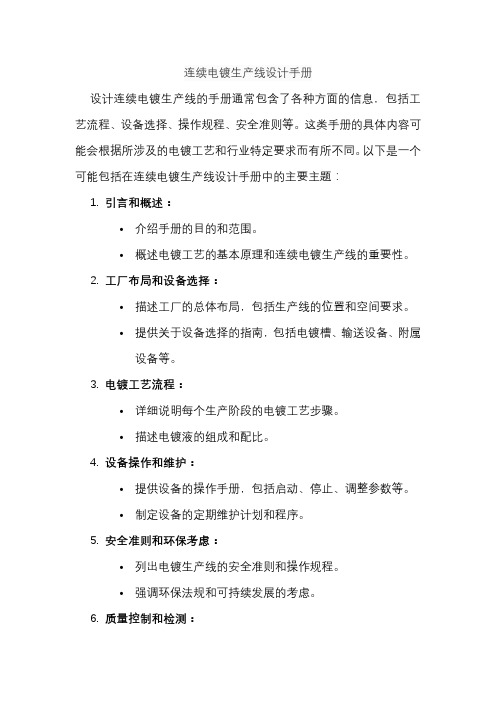
连续电镀生产线设计手册设计连续电镀生产线的手册通常包含了各种方面的信息,包括工艺流程、设备选择、操作规程、安全准则等。
这类手册的具体内容可能会根据所涉及的电镀工艺和行业特定要求而有所不同。
以下是一个可能包括在连续电镀生产线设计手册中的主要主题:1.引言和概述:•介绍手册的目的和范围。
•概述电镀工艺的基本原理和连续电镀生产线的重要性。
2.工厂布局和设备选择:•描述工厂的总体布局,包括生产线的位置和空间要求。
•提供关于设备选择的指南,包括电镀槽、输送设备、附属设备等。
3.电镀工艺流程:•详细说明每个生产阶段的电镀工艺步骤。
•描述电镀液的组成和配比。
4.设备操作和维护:•提供设备的操作手册,包括启动、停止、调整参数等。
•制定设备的定期维护计划和程序。
5.安全准则和环保考虑:•列出电镀生产线的安全准则和操作规程。
•强调环保法规和可持续发展的考虑。
6.质量控制和检测:•描述用于监测和控制电镀质量的方法。
•介绍可能的缺陷和纠正措施。
7.培训和人员要求:•列出操作人员需要的技能和培训要求。
•提供相关岗位的职责和操作指南。
8.应急处理和事故应对:•制定应急处理计划,包括泄漏、事故和紧急情况的应对步骤。
•提供紧急联系信息和急救程序。
9.参考文献和附录:•列出参考文献,包括相关标准和规范。
•包括任何额外的附录,如图表、技术数据表等。
以上内容只是可能包含在连续电镀生产线设计手册中的一些主要主题。
具体手册的编写可能会根据公司的需求、电镀工艺的特定要求和行业标准进行调整。
电镀工艺流程
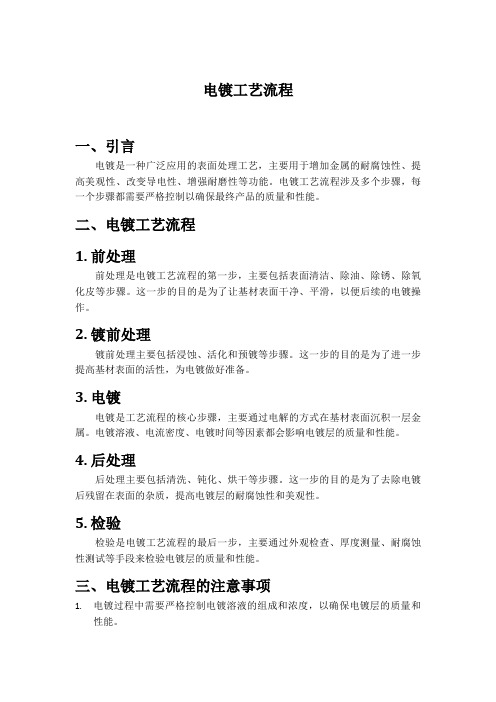
电镀工艺流程一、引言电镀是一种广泛应用的表面处理工艺,主要用于增加金属的耐腐蚀性、提高美观性、改变导电性、增强耐磨性等功能。
电镀工艺流程涉及多个步骤,每一个步骤都需要严格控制以确保最终产品的质量和性能。
二、电镀工艺流程1. 前处理前处理是电镀工艺流程的第一步,主要包括表面清洁、除油、除锈、除氧化皮等步骤。
这一步的目的是为了让基材表面干净、平滑,以便后续的电镀操作。
2. 镀前处理镀前处理主要包括浸蚀、活化和预镀等步骤。
这一步的目的是为了进一步提高基材表面的活性,为电镀做好准备。
3. 电镀电镀是工艺流程的核心步骤,主要通过电解的方式在基材表面沉积一层金属。
电镀溶液、电流密度、电镀时间等因素都会影响电镀层的质量和性能。
4. 后处理后处理主要包括清洗、钝化、烘干等步骤。
这一步的目的是为了去除电镀后残留在表面的杂质,提高电镀层的耐腐蚀性和美观性。
5. 检验检验是电镀工艺流程的最后一步,主要通过外观检查、厚度测量、耐腐蚀性测试等手段来检验电镀层的质量和性能。
三、电镀工艺流程的注意事项1.电镀过程中需要严格控制电镀溶液的组成和浓度,以确保电镀层的质量和性能。
2.电镀过程中需要控制电流密度和电镀时间,以避免电镀层出现缺陷。
3.在进行电镀操作前,需要对基材进行充分的前处理和镀前处理,以确保基材表面的活性和清洁度。
4.电镀后需要进行后处理,以去除表面的杂质和提高电镀层的耐腐蚀性。
5.在整个电镀工艺流程中,需要注意安全操作,避免发生意外事故。
四、结论电镀工艺流程是一个复杂而精细的过程,需要严格控制各个步骤的参数和操作,以确保最终产品的质量和性能。
通过合理的前处理、镀前处理、电镀、后处理和检验,可以得到高质量的电镀层,提高产品的使用寿命和美观性。
在实际应用中,还需要根据具体的产品要求和电镀材料,灵活调整和优化电镀工艺流程。
电镀的工艺流程
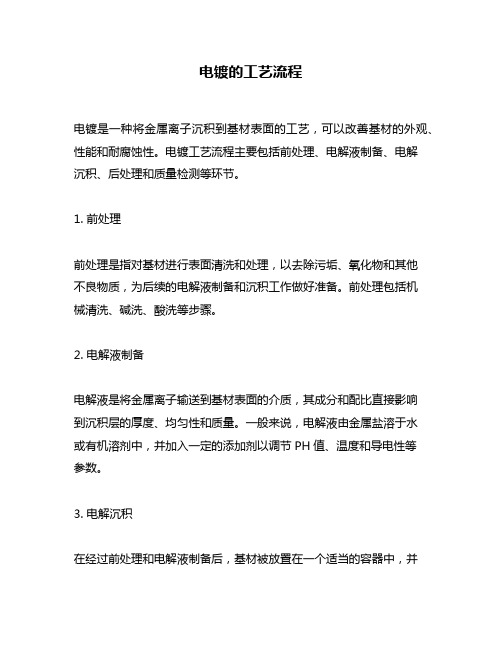
电镀的工艺流程
电镀是一种将金属离子沉积到基材表面的工艺,可以改善基材的外观、性能和耐腐蚀性。
电镀工艺流程主要包括前处理、电解液制备、电解
沉积、后处理和质量检测等环节。
1. 前处理
前处理是指对基材进行表面清洗和处理,以去除污垢、氧化物和其他
不良物质,为后续的电解液制备和沉积工作做好准备。
前处理包括机
械清洗、碱洗、酸洗等步骤。
2. 电解液制备
电解液是将金属离子输送到基材表面的介质,其成分和配比直接影响
到沉积层的厚度、均匀性和质量。
一般来说,电解液由金属盐溶于水
或有机溶剂中,并加入一定的添加剂以调节PH值、温度和导电性等
参数。
3. 电解沉积
在经过前处理和电解液制备后,基材被放置在一个适当的容器中,并
与正极相连。
随着电流通过,金属离子从电解液中沉积到基材表面,形成金属镀层。
电解沉积的过程需要控制电流密度、时间和温度等参数,以确保沉积层的均匀性和质量。
4. 后处理
后处理是指对电镀件进行清洗、干燥和加工等步骤,以去除残留的电解液和其他污垢,并对沉积层进行必要的加工和修整。
后处理包括水洗、烘干、抛光、喷漆等步骤。
5. 质量检测
质量检测是电镀工艺流程中非常重要的一环,其目的是检验沉积层的厚度、均匀性、附着力、硬度和耐腐蚀性等参数是否符合要求。
常用的质量检测方法包括厚度计测量、显微镜观察、耐腐蚀试验等。
综上所述,电镀工艺流程是一个复杂而精细的过程,需要严格控制每个环节并进行有效管理。
只有这样才能保证电镀件的质量和稳定性,并满足不同客户对于外观和性能要求。
链条电镀镀膜工艺
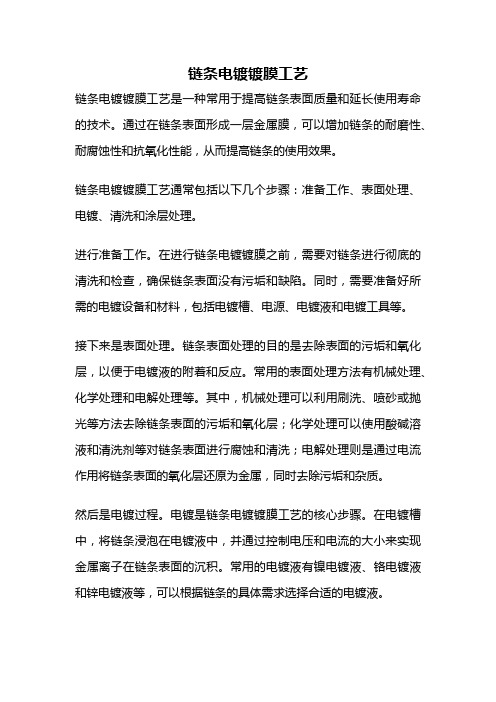
链条电镀镀膜工艺链条电镀镀膜工艺是一种常用于提高链条表面质量和延长使用寿命的技术。
通过在链条表面形成一层金属膜,可以增加链条的耐磨性、耐腐蚀性和抗氧化性能,从而提高链条的使用效果。
链条电镀镀膜工艺通常包括以下几个步骤:准备工作、表面处理、电镀、清洗和涂层处理。
进行准备工作。
在进行链条电镀镀膜之前,需要对链条进行彻底的清洗和检查,确保链条表面没有污垢和缺陷。
同时,需要准备好所需的电镀设备和材料,包括电镀槽、电源、电镀液和电镀工具等。
接下来是表面处理。
链条表面处理的目的是去除表面的污垢和氧化层,以便于电镀液的附着和反应。
常用的表面处理方法有机械处理、化学处理和电解处理等。
其中,机械处理可以利用刷洗、喷砂或抛光等方法去除链条表面的污垢和氧化层;化学处理可以使用酸碱溶液和清洗剂等对链条表面进行腐蚀和清洗;电解处理则是通过电流作用将链条表面的氧化层还原为金属,同时去除污垢和杂质。
然后是电镀过程。
电镀是链条电镀镀膜工艺的核心步骤。
在电镀槽中,将链条浸泡在电镀液中,并通过控制电压和电流的大小来实现金属离子在链条表面的沉积。
常用的电镀液有镍电镀液、铬电镀液和锌电镀液等,可以根据链条的具体需求选择合适的电镀液。
电镀过程中,金属离子会在链条表面沉积形成金属膜,这一过程叫做电解沉积。
通过调整电镀液的成分和工艺参数,可以控制金属膜的厚度和均匀性。
金属膜的厚度一般在几微米到几十微米之间,要根据链条的使用环境和要求进行选择。
完成电镀后,还需要进行清洗和涂层处理。
清洗的目的是去除电镀过程中残留在链条表面的电镀液和杂质,以免影响链条的质量。
涂层处理可以在链条表面形成一层保护膜,增加链条的耐磨性和耐腐蚀性。
常用的涂层材料有涂漆、喷塑和热浸镀等,可以根据链条的具体要求选择适合的涂层工艺。
总的来说,链条电镀镀膜工艺是一种经过多个步骤的复杂工艺,需要严格控制各个环节的工艺参数和质量要求,才能达到预期的效果。
通过链条电镀镀膜工艺,可以提高链条的表面质量和性能,延长链条的使用寿命,提高链条的可靠性和安全性。
- 1、下载文档前请自行甄别文档内容的完整性,平台不提供额外的编辑、内容补充、找答案等附加服务。
- 2、"仅部分预览"的文档,不可在线预览部分如存在完整性等问题,可反馈申请退款(可完整预览的文档不适用该条件!)。
- 3、如文档侵犯您的权益,请联系客服反馈,我们会尽快为您处理(人工客服工作时间:9:00-18:30)。
随着电子工业的发展,作为连接电子电路的电子接插件也趋于多样化,如:套筒用电子接插件、接口用电子接插件、内部组装用电子接插件等,这些接插件从实用性考虑,正向高密度化、轻、薄、小型化、多功能化、高可靠性化方向发展。
电子接插件的最基本性能是电接触的可靠性,为此,接插用材料主要为铜及其合金,为提高其耐蚀性和耐磨性等,必须进行必要的表面处理。
电子接插件代表性的表面处理方法是以镀镍打底的镀金工艺,或是以镀铜打底的镀可焊性镀层工艺。
银镀层的耐蚀性较差,现在使用的较少;钯及钯合金镀层作为代金镀层已开发了近十年,作为耐磨性镀层,用于插拔次数较多的电子接插件的表面处理已得到应用。
下面对电子接插件连续加速电镀的加工工艺、镀液和镀层性能等作一介绍。
1连续快速电镀的加工工艺
连续快速电镀的加工工艺本质上与一般电镀并无区别,然而各工艺过程的处理时间要比普通电镀短得多,因此各种处理液、镀液要具有适应快速电镀的能力。
1.1以镀镍层打底的镀金工艺
工艺流程如下:
上挂具→除油→水洗→水洗→水洗→酸洗→水洗→水洗→水洗→氨基磺酸盐镀Ni→水洗→水洗→水洗→局部脉冲镀Au→回收→回收→水洗→水洗→水洗→局部镀Sn-Pb合金→水洗→水洗→水洗→去离子水洗→去离子热水洗→干燥→下挂具→检查(厚度、结合强度、外观、可焊性、局部镀的位置等)
下面对工艺中的主要工序作一简单说明。
(1)除油与普通化学除油不同,除油时间仅为2~5s。
这样,普通浸渍方式的除油已不能满足要求,需要进行高电流密度下的多级电化学除油。
对除油液的要求是:如果除油液带入下道的水洗槽或酸洗槽中,不应发生分解或产生沉淀。
(2)酸洗酸洗是为了除去金属表面的氧化膜,常使用硫酸或盐酸。
由于电子接件对尺寸要求严格,所以酸洗液对基体不应有溶解作用。
(3)镀镍镀Ni层作为镀Au和Sn-Pb合金镀层的底层,不仅提高耐蚀性,而且可防止基体的Cu与Au、Cu与Sn-Pb合金的固相扩散。
电子接插件在进行切割、弯曲加工时镀层不应脱落,因此最好采用氨基磺酸镍镀液。
(4)局部镀金局部镀Au有各种方法,国内外已申请了许多专利。
其方法大都是把不要的部分遮住,仅使需要电镀的部分与镀液接触,从而实现局部电镀。
局部镀Au需要考虑的问题有:①从生产角度考虑,应采用高电流密度电镀;②镀层厚度分布要均匀;③严格控制需镀覆的位置;④镀液应对各种基体有通用性;⑤维护调整简单。
(5)局部可焊性电镀局部可焊性电镀没有局部镀金那样苛刻,可采用比较经济的电镀方法与设备。
把需要电镀的部分浸入镀液,让不需要电镀的部分露出液面,即通过控制液位的方法可实现局部电镀。
为降
低污染,可采用有机酸盐镀液,镀层组成为:Sn∶Pb=9∶1左右,镀层厚度为1~3μm。
外观要光亮、平整。
1.2以镀铜层打底的可焊性电镀工艺
典型工艺流程如下:
上挂具→除油→水洗→水洗→水洗→酸洗→水洗→水洗→水洗→KCN活化→氰化镀铜→水洗→水洗→水洗→酸洗→水洗→电镀Sn-7%Pb合金→水洗→水洗→水洗→防变色→水洗→水洗→去离子水洗→去离子热水洗→干燥→下挂具→检查(厚度、结合强度、外观、可焊性)
铜镀层主要是起阻挡层的作用,防止基体(主要是黄铜)中的锌和可焊性镀层中的锡发生固相扩散。
为提高焊接后的零件的导热性,铜镀层的厚度为1~3μm。
电镀铜的镀液除可用氰化物镀液外,近年来开始使用烷基磺酸或烷醇基磺酸等有机酸体系的镀液。
纯锡镀层易从镀层表面产生晶须,如果在锡中共沉积5%以上的铅,形成Sn-Pb合金镀层,则可防止晶须的产生。
在Sn-Pb合金共沉积时,Pb比Sn容易沉积,因此,镀液中[Sn4+]/[Pb2+]=9∶1时,即可得到含铅量10%以上的合金镀层。
随着电镀的进行,镀液中的Pb2+逐渐减少,对镀液需进行定期分析,据以补充Pb2+。
可焊性镀层在空气中会慢慢氧化,为减缓其氧化速度,镀后可在50~80℃的磷酸盐水溶液中浸渍,在镀层表面形成致密的磷酸盐膜。
1.3以镀镍层打底的电镀Pd/Au工艺
代表性的工艺流程如下:
上挂具→除油→水洗→水洗→水洗→酸洗→水洗→水洗→水洗→氨基磺酸盐镀Ni→水洗→水洗→水洗→活化(闪镀Pd)→局部镀Pd→回收→水洗→水洗→水洗→局部脉冲镀Au→回收→回收→水洗→水洗→水洗→电镀Sn-7%Pb合金→水洗→水洗→水洗→去离子水洗→去离子热水洗→干燥→下挂具→检查(厚度、结合强度、外观、可焊性、局部镀的位置等)
在镍镀层与金镀层之间插入钯镀层,控制钯镀层的厚度在0.5~1.0μm。
由于钯镀层硬度较高,若厚度过大(超过1.5μm),则进行弯曲或切割时镀层易产生裂纹。
由于钯较昂贵,所以常采用局部镀的方法。
镀钯液一般为中性到碱性,为提高镍与钯的结合强度,需在镍表面闪镀钯镀层。
电镀钯之后,再镀0.03~0.13μm的金镀层,可使接触电阻稳定,并且在插拔时,金镀层有自润滑作用,从而提高耐磨性。
2电镀触点用镀层
2.1电镀金的镀液及镀层性能
镀液的类型镀层用途
含钴的酸性镀金液电镀触点用金镀层,广泛用于接插件,镀层含0.1%~0.3%Co,具有美丽的外观,镀层较硬
含镍的酸性镀金液电镀触点用金镀层,镀层含0.1%~0.3%Ni,镀层性质与含钴的镀层相同,但外观稍差.镀液中Ni2+含量调整容易
含铁的酸性镀金液电镀触点用金镀层,镀层含0.1%~0.3%Fe,镀层性质与含钴的镀层相同
中性硬金镀液镀层为硬质纯金,镀液中Au(CN)2-含量高达30~50g/L
碱性金镀液镀层为软质纯金
这里,使用最广泛的是含钴的酸性镀金液,其镀液组成如下:KAu(CN)25~30g/L,柠檬酸(或柠檬酸钾)80~150g/L,Co2+0.2~0.5g/L,螯合剂1~10g/L,有机添加剂1~10g/L,pH4.0~5.0,操作温度为40~60℃。
KAu(CN)2是主要成分,镀金时采用不溶性阳极,需要根据金的析出量来补充
KAu(CN)2。
这样,K+、CN-在镀液中逐渐积累,改变溶液组成。
当pH≥5时,KAu(CN)2与Co2+反应,生成沉淀,从而使钴的沉积困难。
因此,镀液的pH值应控制在4.0~5.0。
柠檬酸盐起导电盐的作用,对镀液也有缓冲作用.在酸性镀金中若没有缓冲剂,电镀时pH上升,镀层的物理性质发生变化,因此,缓冲剂的作用是非常重要的。
Co2+是过渡金属离子光亮剂,它有使镀层结晶细致、表面光亮、提高硬度、改善耐蚀性等作用。
Co 在镀层中的含量为0.1%~0.3%,也有报道认为,K、N、C等也与Co结合一起进入镀层,镀液pH值升高,镀层中Co的共沉积量减少。
除Co2+以外,Ni2+、Fe2+也有类似的作用。
镀液中若含有Pb2+、Cu2+等重金属离子,镀层质量则变差,螯合剂则可以掩蔽这些重金属离子,还可与Co2+等过渡金属离子形成络合物,从而控制镀液中游离的简单金属离子的浓度,具有保持Co共沉积稳定的作用。
近年来,有机添加剂开始在镀金溶液中使用,如:聚乙抱亚胺、磺酸衍生物、吡啶化合物等,这些添加剂的加入,可扩大光亮范围、镀液中Au+离子的浓度可以降低、拓宽使用电流密度范围、改善镀液分散能力,但对镀层硬度、内应力、耐磨性等基本没有影响。
关于有机添加剂方面的专利报道较多。
含钴的酸性镀液中得到镀层结晶粒径在25nm以下(纯Au镀层的粒径为1~2μm),镀层硬度高(170~200HV,纯Au镀层为70~80HV),镀层表面光亮。
镀层具有高耐磨性是由于在高硬度下镀层内应力大(100~300N/mm2),柔软性小。
镀层中的钴,一部分以金属原子状态存在,也有一部分与K+、CN-结合形成络合物而存在。
耐磨性好的镀层,金属原子状态钴含量在0.06%~0.2%,形成络合物的钴含量在0.08%以上。
以金属原子状态存在的钴易向镀层表面扩散,在表面氧化形成氧化钴,使镀层的接触电阻增大,当温度较高时,这种现象更明显。
镀层特性因电镀条件而变,如表2所示。
钯是易吸氢的金属,吸氢以后体积增大,而当放出已吸藏的氢时,体积减小。
钯的晶格常数为0.3889nm,当吸氢量为0.57%以上时,晶格常数增加到0.404nm。
因此,在电镀钯时,如果阴极上析氢,镀层中就会夹杂有氢,当氢放出时,镀层体积发生变化,造成镀层脱落或产生裂纹。
钯具有催化作用,这使其作为触点材料受到限制。
但是,通过在中性或碱性络合物镀液中电镀钯,或在氨碱性镀液中电镀Pd-Ni合金,可使镀层含氢量减少,在Pd或Pd-Ni合金镀层上再镀一层薄金镀层,则可防止钯的催化作用,从而可作为接点材料使用。
Pd或Pd-Ni合金镀层最初是作为代金镀层而开发的,但是目前在电子接插件上使用的金镀层一般厚度较薄,并且大都采用局部镀,因此消耗金的费用在整个材料费中所占的比例已较低,况且电镀钯还使工艺过程复杂,所以从经济角度考试,钯镀层作为代金镀层已失去其魅力。
Pd及Pd-Ni合金镀层上再镀一薄层金镀层,其耐蚀性和接触电阻都与金相当,硬度比金镀层高(纯Pd 为2500~6000N/mm2,Pd-Ni为4000~6000N/mm2),耐磨性比金镀层好,因此可用在插拔次数较多的电子接插件上。
3快速电镀
为保证连续快速电镀生产,必须采用快速电镀工艺,即在高电流密度(或高电位)下电镀,从而使镀层结晶细致,减少镀层针孔,改善度层质量。
快速电镀需要解决的问题主要有:
(1)使阴极表面形成的扩散层的厚度尽量薄,可采用脉冲电流,或加强搅拌;
(2)在不影响局部镀的位置精度的前提下,可向镀件表面高速喷射镀液;
(3)提高被镀基体的导电性;。