电镀前处理工艺概述以及配方
电镀工艺说明
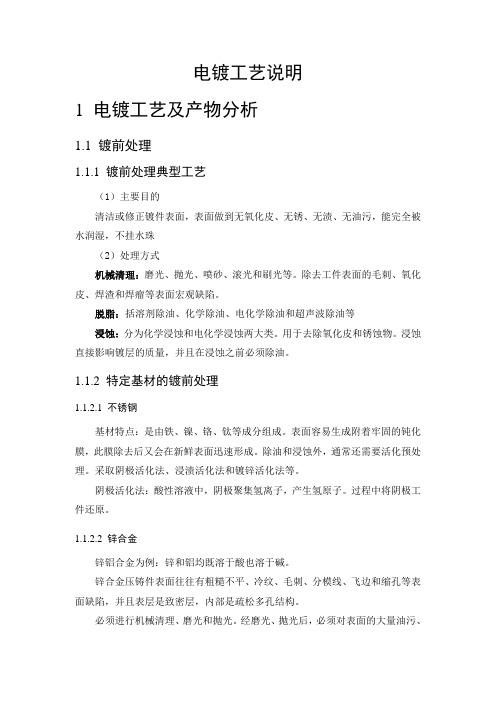
电镀工艺说明1电镀工艺及产物分析1.1镀前处理1.1.1镀前处理典型工艺(1)主要目的清洁或修正镀件表面,表面做到无氧化皮、无锈、无渍、无油污,能完全被水润湿,不挂水珠(2)处理方式机械清理:磨光、抛光、喷砂、滚光和刷光等。
除去工件表面的毛刺、氧化皮、焊渣和焊瘤等表面宏观缺陷。
脱脂:括溶剂除油、化学除油、电化学除油和超声波除油等浸蚀:分为化学浸蚀和电化学浸蚀两大类。
用于去除氧化皮和锈蚀物。
浸蚀直接影响镀层的质量,并且在浸蚀之前必须除油。
1.1.2特定基材的镀前处理1.1.2.1不锈钢基材特点:是由铁、镍、铬、钛等成分组成。
表面容易生成附着牢固的钝化膜,此膜除去后又会在新鲜表面迅速形成。
除油和浸蚀外,通常还需要活化预处理。
采取阴极活化法、浸渍活化法和镀锌活化法等。
阴极活化法:酸性溶液中,阴极聚集氢离子,产生氢原子。
过程中将阴极工件还原。
1.1.2.2锌合金锌铝合金为例:锌和铝均既溶于酸也溶于碱。
锌合金压铸件表面往往有粗糙不平、冷纹、毛刺、分模线、飞边和缩孔等表面缺陷,并且表层是致密层,内部是疏松多孔结构。
必须进行机械清理、磨光和抛光。
经磨光、抛光后,必须对表面的大量油污、抛光膏等进行预清洗。
经预除油后,应再进行电化学除油。
除油后,表面会有一层极薄的氧化膜。
为彻底清除此氧化膜,通常选用氢氟酸浸渍活化或采用氟硼酸腐蚀活化处理。
为防止发生置换反应,影响镀层结合力,锌合金压铸件目前通常进行氰化预镀铜。
1.1.2.3铝及铝合金铝及铝合金对氧具有高度亲和力,极易生成氧化膜。
并且氧化膜一经除去又会在极短时间里产生一层新氧化膜,严重影响镀层结合力。
铝浸入电镀液时易与具有较正电位的金属离子发生置换,影响镀层结合力。
铝是两性金属,在酸性和碱性镀液中都不稳定。
铝合金压铸件有砂眼、气孔,会残留镀液和氢气,容易鼓泡,会降低镀层和基体金属间的结合力等。
因此,除了常规的除油、浸蚀、出光外,还需再制取一层过渡金属层或能导电的多孔性化学膜层。
电镀工艺流程简介
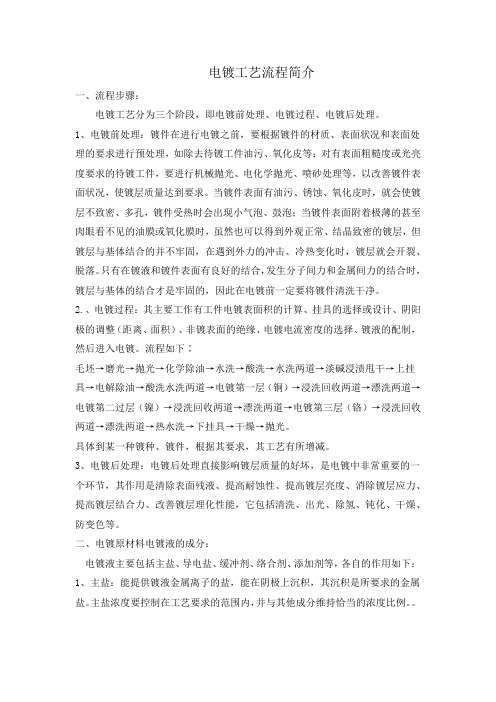
电镀工艺流程简介一、流程步骤:电镀工艺分为三个阶段,即电镀前处理、电镀过程、电镀后处理。
1、电镀前处理:镀件在进行电镀之前,要根据镀件的材质、表面状况和表面处理的要求进行预处理,如除去待镀工件油污、氧化皮等;对有表面粗糙度或光亮度要求的待镀工件,要进行机械抛光、电化学抛光、喷砂处理等,以改善镀件表面状况,使镀层质量达到要求。
当镀件表面有油污、锈蚀、氧化皮时,就会使镀层不致密、多孔,镀件受热时会出现小气泡、鼓泡;当镀件表面附着极薄的甚至肉眼看不见的油膜或氧化膜时,虽然也可以得到外观正常、结晶致密的镀层,但镀层与基体结合的并不牢固,在遇到外力的冲击、冷热变化时,镀层就会开裂、脱落。
只有在镀液和镀件表面有良好的结合,发生分子间力和金属间力的结合时,镀层与基体的结合才是牢固的,因此在电镀前一定要将镀件清洗干净。
2.、电镀过程:其主要工作有工件电镀表面积的计算、挂具的选择或设计、阴阳极的调整(距离、面积)、非镀表面的绝缘、电镀电流密度的选择、镀液的配制,然后进入电镀。
流程如下∶毛坯→磨光→抛光→化学除油→水洗→酸洗→水洗两道→淡碱浸渍甩干→上挂具→电解除油→酸洗水洗两道→电镀第一层(铜)→浸洗回收两道→漂洗两道→电镀第二过层(镍)→浸洗回收两道→漂洗两道→电镀第三层(铬)→浸洗回收两道→漂洗两道→热水洗→下挂具→干燥→抛光。
具体到某一种镀种、镀件,根据其要求,其工艺有所增减。
3、电镀后处理:电镀后处理直接影响镀层质量的好坏,是电镀中非常重要的一个环节,其作用是清除表面残液、提高耐蚀性、提高镀层亮度、消除镀层应力、提高镀层结合力、改善镀层理化性能,它包括清洗、出光、除氢、钝化、干燥、防变色等。
二、电镀原材料电镀液的成分:电镀液主要包括主盐、导电盐、缓冲剂、络合剂、添加剂等,各自的作用如下:1、主盐:能提供镀液金属离子的盐,能在阴极上沉积,其沉积是所要求的金属盐。
主盐浓度要控制在工艺要求的范围内,并与其他成分维持恰当的浓度比例。
电镀前处理工艺
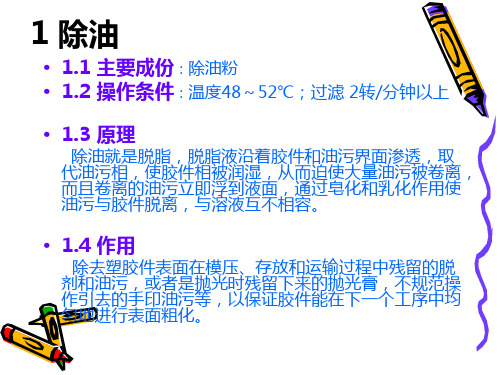
• 粗化效果比较
• 三种类型的粗化效果比较: 化学粗化>有机溶剂粗化>机械粗化
• 3.4 使用范围
适用于生产过程中ABS料粗化的操作。 ABS料只须化学浸蚀粗化,PC+ABS料 的塑胶件,须先进行溶剂溶胀粗化,后 经化学浸蚀粗化。在工业生产中,ABS 料和含有PC料的ABS料都不经过机械粗 化。
5.3 维护钯水缸注意事项
• 5.3.1 防止Sn2+水解反应,故钯缸前是稀盐
酸缸。由于CP盐酸不一定很纯,加之中和后 的副产物,所以用过滤机过滤稀盐酸缸。
• 5.3.2 钯缸须注意水解产物H+与Cl-的扩散,凝
胶状物质的形成与吸附。
• 5.3.3 周期性的添加亚锡盐和盐酸,或添加新配
制的浓缩液。
• 粗化均匀和应力减小都会增加镀层的结合度。
• 亲水作用: 使胶件非极性分子极化,极大的提高了胶件的表
面亲水性,有利于电沉积反应进行,从而提高镀层与 胶件结合力。
3 粗化
• 3.1 目的
提高零件表面的亲水性和形成适当的粗 糙度,以保证镀层有良好的附着力;它是 决定镀层附着力大小的最关键的工序。
• 3.2 原理
• 注意 水合肼过少时起不到还原作用,过多时会使
挂具上镍。
5 钯水
• 5.1 目的
提高镀层附着力,使胶件表面形成一层催化 活性的贵金属层,为化学沉积提供必要的条件, 使化学镍能自发进行。
• 5.2 原理
胶体钯活化是通过氯化亚锡还原钯离子并形 成胶体钯和锡酸胶体。锡酸胶体是胶体钯的保 护体,使胶体钯活化液稳定,在稳定的前提保 持过量的亚锡离子和足够的酸度,Sn2+是强 化性还原钯,使钯附在胶件上。 • 反应机理:Pd2+ +Sn2+ Pd↓+ Sn4+。
黑镍电镀工艺及配方

黑镍电镀工艺及配方1. 引言黑镍电镀是一种常用的表面处理工艺,能够为金属制品提供具有装饰性和保护性的黑色表面。
本文将详细介绍黑镍电镀的工艺流程及配方,包括前处理、电镀条件和后处理等方面的内容。
2. 前处理2.1 清洗在黑镍电镀之前,首先需要对金属制品进行清洗,以去除表面的油脂、污垢和氧化物。
常用的清洗方法包括碱性清洗和酸性清洗。
2.1.1 碱性清洗碱性清洗一般采用碱性清洗剂,常见的为氢氧化钠溶液或氢氧化钾溶液。
清洗时间和温度可以根据具体情况进行调整。
2.1.2 酸性清洗酸性清洗一般采用酸性清洗剂,常见的为硫酸或盐酸溶液。
清洗时间和温度可以根据具体情况进行调整。
2.2 去除氧化金属制品表面的氧化物会对电镀效果产生不利影响,因此需要采用去除氧化的方法。
常用的去除氧化方法包括酸洗和化学除锈。
2.2.1 酸洗酸洗一般采用浓硫酸或浓盐酸进行,清洗时间和温度可以根据具体情况进行调整。
2.2.2 化学除锈化学除锈常用的溶液有硝酸、氢氟酸等,可以有效去除金属表面的氧化层和锈蚀。
3. 电镀条件3.1 电镀液配方黑镍电镀液的配方关系到最终电镀效果的质量和稳定性。
以下为一个常用的黑镍电镀液的配方:•氯化镍:150 g/L•氯化铵:50 g/L•硫酸镍:30 g/L•硫酸:50 g/L•温度:55-60°C•pH值:3.5-4.03.2 电镀条件黑镍电镀需要控制相应的电镀条件,以获得理想的电镀效果。
以下为常用的黑镍电镀条件:•电流密度:1-5 A/dm²•镀液搅拌:机械搅拌或气体搅拌•镀层厚度:根据需要可在5-20 μm范围内进行调整•电镀时间:根据需要可在5-30 分钟范围内进行调整4. 后处理完成电镀后,还需要进行相应的后处理措施,以保证电镀层的质量和稳定性。
4.1 清洗电镀后的金属制品需要进行清洗,以去除表面的残留电镀液和杂质。
常用的清洗方法同前处理中的清洗方法。
4.2 抛光为提高电镀层的光亮度和平滑度,可以对电镀层进行抛光处理。
铁件电镀前处理工艺

铁件电镀前处理工艺一、引言铁件电镀前处理工艺是指在进行电镀之前对铁件进行一系列的处理工艺,以提高电镀层的附着力和耐腐蚀性,保证电镀质量。
本文将介绍铁件电镀前处理工艺的主要步骤和注意事项。
二、表面清洗在进行电镀前,首先要对铁件表面进行清洗。
清洗的目的是去除表面的油脂、氧化物和其他杂质,以保证电镀层与基材的结合牢固。
常用的清洗方法有碱洗、酸洗和溶剂清洗等。
碱洗可以去除铁件表面的油脂和污垢,酸洗可以去除氧化层和铁锈,溶剂清洗可以去除残留的油脂和有机物。
三、机械处理机械处理是指对铁件表面进行物理性处理,以去除表面的毛刺、凹坑和氧化层等不良状况,提高表面的光洁度和平整度。
常用的机械处理方法有打磨、抛光和喷砂等。
打磨可以去除铁件表面的毛刺和凹坑,抛光可以提高表面的光洁度,喷砂可以去除表面的氧化层和污垢。
四、除锈处理除锈处理是指对铁件表面的铁锈进行清除,以减少电镀过程中的气泡和缺陷。
常用的除锈方法有机械除锈、化学除锈和电解除锈等。
机械除锈可以通过刷洗或打磨的方式去除铁锈,化学除锈可以使用酸性溶液溶解铁锈,电解除锈可以通过电解作用将铁锈还原。
五、活化处理活化处理是指对铁件表面进行化学性处理,以提高表面的活性和与电镀液的相容性。
常用的活化方法有酸洗和活化剂处理等。
酸洗可以去除表面的氧化物和污垢,活化剂处理可以在表面形成一层活性物质,增加与电镀液的接触面积。
六、防腐处理防腐处理是指在铁件电镀前对铁件表面进行一层薄膜的涂覆,以增加电镀层的耐腐蚀性。
常用的防腐处理方法有磷化和镀锌等。
磷化可以在铁件表面形成一层磷化膜,提高电镀层的附着力和耐腐蚀性,镀锌可以在铁件表面镀上一层锌,形成一层防护层。
七、表面调整表面调整是指在进行铁件电镀前对表面进行微调,以提高电镀层的均匀性和外观。
常用的表面调整方法有电解拋光和电解颜色调整等。
电解拋光可以在表面形成一层光亮的金属层,电解颜色调整可以通过改变电镀液的组成和工艺条件,调整电镀层的颜色。
电镀前处理工艺流程

电镀前处理工艺流程电镀前处理工艺流程是指在进行电镀之前对工件进行处理,以保证电镀的质量和效果。
下面是一份常见的电镀前处理工艺流程:1. 清洗(Cleaning):将工件放入清洗槽中,使用碱性或酸性清洗剂清洗表面的油脂、污渍和其他杂质。
清洗槽中可以加热或超声波来增加清洁效果。
2. 酸洗(Acid Pickling):将工件放入酸洗槽中,使用酸性溶液(如硫酸或盐酸)进行酸洗,目的是去除表面的氧化物、锈蚀物和其他有害物质,以提高镀层的附着力。
3. 防酸处理(Acid Resistant Treatment):将工件浸入防酸液中,例如磷酸或硼酸液体,目的是形成一个防止酸洗液对工件表面的继续侵蚀和氧化的保护层。
4. 水冲洗(Water Rinsing):将工件从酸洗槽中取出,通过水冲洗去除残留的酸洗液和防酸液,以防止其对后续工艺造成不良影响。
5. 除油(Degreasing):将工件放入除油槽中,使用有机溶剂或碱性溶液去除表面的油脂和其他有机物,以提高电镀的附着力和均匀性。
6. 再水冲洗(Water Rinsing):将工件从除油槽中取出,通过水冲洗去除残留的溶剂或碱性溶液,以防止其对后续工艺造成不良影响。
7. 预光(Pre-polishing):将工件放入预光槽中,使用研磨材料或预光剂进行预光处理,以去除表面的凹陷、细微划痕和氧化物,以改善镀层的外观和质量。
8. 再次水冲洗(Water Rinsing):将工件从预光槽中取出,通过水冲洗去除残留的研磨材料或预光剂,以防止其对后续工艺造成不良影响。
9. 碱洗(Alkaline Cleaning):将工件放入碱洗槽中,使用碱性溶液进行碱洗,目的是去除预光过程中生成的氧化物和其他杂质,以提高电镀的质量和光亮度。
10. 最后水冲洗(Final Water Rinsing):将工件从碱洗槽中取出,通过水冲洗去除残留的碱洗液和其他杂质,以确保工件表面干净无污染。
以上是一份常见的电镀前处理工艺流程,其中细节还可以根据具体的工件和要求进行调整。
电镀前处理工艺流程
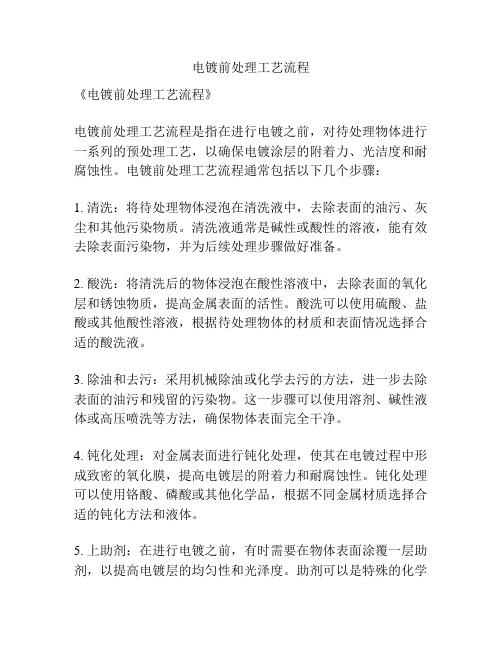
电镀前处理工艺流程
《电镀前处理工艺流程》
电镀前处理工艺流程是指在进行电镀之前,对待处理物体进行一系列的预处理工艺,以确保电镀涂层的附着力、光洁度和耐腐蚀性。
电镀前处理工艺流程通常包括以下几个步骤:
1. 清洗:将待处理物体浸泡在清洗液中,去除表面的油污、灰尘和其他污染物质。
清洗液通常是碱性或酸性的溶液,能有效去除表面污染物,并为后续处理步骤做好准备。
2. 酸洗:将清洗后的物体浸泡在酸性溶液中,去除表面的氧化层和锈蚀物质,提高金属表面的活性。
酸洗可以使用硫酸、盐酸或其他酸性溶液,根据待处理物体的材质和表面情况选择合适的酸洗液。
3. 除油和去污:采用机械除油或化学去污的方法,进一步去除表面的油污和残留的污染物。
这一步骤可以使用溶剂、碱性液体或高压喷洗等方法,确保物体表面完全干净。
4. 钝化处理:对金属表面进行钝化处理,使其在电镀过程中形成致密的氧化膜,提高电镀层的附着力和耐腐蚀性。
钝化处理可以使用铬酸、磷酸或其他化学品,根据不同金属材质选择合适的钝化方法和液体。
5. 上助剂:在进行电镀之前,有时需要在物体表面涂覆一层助剂,以提高电镀层的均匀性和光泽度。
助剂可以是特殊的化学
物质或表面活性剂,使电镀液更容易附着在物体表面,提高电镀质量。
电镀前处理工艺流程的每一步都十分重要,它们共同确保了电镀涂层的质量和性能。
只有经过严格的预处理工艺,才能获得均匀、光亮、耐腐蚀的电镀涂层,满足不同行业对金属制品质量和外观的要求。
电镀原辅材料与工艺流程分析

电镀原辅材料与工艺流程分析一、电镀原辅材料介绍
1. 电镀添加剂
- 光亮剂:提高电镀层光洁度和亮度
- 增亮剂:改善电镀层外观
- 平抛剂:改善电镀层均匀性
- 淡化剂:防止氢气析出导致外观缺陷
2. 电解质
- 金属盐:为电镀液提供所需金属离子
- 电解盐:提高电解液电导率
3. 其他辅助材料
- 去离子水:确保电镀液纯度
- 酸碱调节剂:控制电镀液pH值
二、电镀工艺流程分析
1. 前处理
- 酸洗:去除金属表面氧化物和油污
- 电解除油:电化学方式去除油污
- 活化:提高金属表面活性
2. 电镀
- 制备电镀液:配制所需金属盐和添加剂
- 电镀反应:在控制好的条件下进行电镀
- 监控与维护:定期检测和补充电镀液
3. 后处理
- 水洗:去除残留电镀液
- 烘干:除去水分,防止氧化
- 检验:检查电镀层质量
4. 环保处理
- 废水处理:中和、沉淀等处理电镀废水
- 废渣处理:固化或回收有价金属离子
电镀工艺流程需合理选择原辅材料,严格控制各工序条件,注重环保要求,以确保获得优质的电镀层。
- 1、下载文档前请自行甄别文档内容的完整性,平台不提供额外的编辑、内容补充、找答案等附加服务。
- 2、"仅部分预览"的文档,不可在线预览部分如存在完整性等问题,可反馈申请退款(可完整预览的文档不适用该条件!)。
- 3、如文档侵犯您的权益,请联系客服反馈,我们会尽快为您处理(人工客服工作时间:9:00-18:30)。
电镀前处理工艺概述以及配方1前处理的定义一般前处理过程为,研磨预备洗净水洗电解脱酯水洗酸浸及活性化水中和水洗电镀。
1.1前处理的目的前处理的目的是为了得到良好的镀层,由于镀件在制造、加工搬运、保存期间会有油酯、氧化物锈皮、氢氧化物、灰尘等污物附着于镀件表面上,若不去除这些污物而进行电镀将得不到良好的镀层。
镀•件品质,前处理占很重要的地位。
1.2前处理不良所造成之镀层缺陷前处理不良所造成之镀层缺陷,有下列几项:(1)剥离,(2)气胀,(3)污点,(4)光泽不均,(5)凹凸不平,(7)小孔(8)降低耐蚀性,(9)脆化。
电镀之不良,前处理占很大的原因。
1.3污物的种类污物的种类,可分为有机物及无机物。
有机物污物主要是动物性油酯,植物性油酯及矿物性油酯,无机物污物是金属氧化物、盐类、尘埃、及砂土。
另外由有机物和无机物污物之物如研磨屑、研磨材料。
动物性及植物性油酯可被化缄剂皂去除。
矿物性油污无法被缄剂皂去除需用三菉乙烯、汽油、石油溶剂乳化剂等去除。
无机物污物可被酸或缄溶解,利用酸、缄浸渍、化学或电解方法去除及机械研磨方法去除。
无机、有机混合污物,去除较困难,除了利用化学方法,亦须用电解,机械研磨等方法联合应用去除。
1.4电镀前处理去除的典型污物(1)润滑油(6)淬火残留物(2)切削油(7)热处理盐(3)研磨油(8)热处理盐(4)热斑(9)污迹(5)锈及腐蚀物(10)油漆及油墨1.5表面清洁测定表面清洁度测定,在工场最实用的方法是用水冲(water-beaktest),检查表面水是否均匀润湿,如果是均匀润湿则为清洁表面,反之则不清洁。
其它方法有,Nielsonmethod,Atomizertest,Fluoresentmethod,weightofresidualsoil,wip-ingmethod,residualpatlernmethod及Radioisotopetracertechnique。
1.6选择清洁方法及清洁材料之影响因素其影响因素有:(1)被清洁表面之特性(9)清洁剂的温度(2)被去除污物之特性(10)应用时间(3)清洁要求程度(11)经验(4)应用的方法(12)搅拌次数(5)水质(13)污染的程度(6)手续、另件、设备人员的安全(14)下一步处理(7)成本(15)废物之处理(8)清洁剂的浓度4镀铬之影响因素(l)CrO3浓度与导电度关系(2)温度兴导电度之关系(3)CrO3浓度与电流效率之关系(4)硫酸浓度之影响:浓度低时,低电流密度下电流效率高,反之电流效率低‥(5)三价铬的影响 1.三价铬很少时,沉积速率减媛。
2.三价铬很高时,镀层变暗。
3.三价铬增加,则导电度降低,需较大电压4.三价铬愈多,光泽范围愈小。
(6)电流密度及温度的影向1.镀浴温度升高,电流效率降低。
2.电流密度愈高,电流效率愈高。
3.高电流密度,低温则镀层灰暗,硬度高脆性大,结晶粗大‥4.高温而低电流密度,镀层硬度小,呈乳白色,延性好,无网状裂纹,结晶细致,适合装饰性的镀件。
5.中等温度及中等电流密度,镀层硬度高,有密集的网状裂纹,光亮硬质铬镀层。
(7)杂质的影响 1.铁杂质,电解液不稳定,光泽镀层范围缩小,导电性变差,电压须增高,去除铁杂质比三价铬还困难,要尽量防止铁污染,不要超过10g/l 2.铜、锌杂质,含量低时,对镀层影向不大,铜最好不要大于3g/l3.硝酸,是镀铬最有害的杂质,镀浴须严禁带入硝酸污染‥(8)阳极及电流分布之影响 1.阳极较大,电流分布较不均匀使镀层厚度不均勺‥2.阳极面积大,三价铬形成较多。
3.复杂镀件,阳极宜用象形电极或辅助电极,使电流分布均匀。
4.阳极的铅易氧化,形成黑色的氧化铅及黄色的过氧化铅。
过氧化铅导电性不良,应立刻除去。
5.电流因尖端及边缘效应,造成镀层厚度不均,可采用绝缘物遮盖尖端或边缘。
5镀铬之挂架(Rack) 镀铬其镀浴均一性极差,电流效率很低,须使用较高电流密度,所以挂架之设计要求对镀铬品质影响很大。
其设计要点如下(1)安定不溶解。
(2)导电顺利不发熟,需足够截面积。
(3)与镀件接触良好。
(4)结构以焊接方式,导电钩要弯成直角(5)非电镀部份要用绝缘物覆盖,以减少电流消耗。
(6)结构要简单、易制造、轻便。
(7)镀件放置位置要使气体自由逸出容易。
(8)应用辅助电极、双极电极。
(9)依镀件的形状、尺寸、数量及镀层用途等因素决定挂架之设计。
9.7银及银合金之酸浸溶液配方Nitricacid66vol%Temperatureroomto160FSulfuricacid78vol%Nitric acid22vol%TemperatureroomSodiumcyanide3~4oz/galSodiumcarbonate1~2oz/galSodiumaluminu msulfate6oz/galSodiumpotassiumtattrate6oz/galTemperature180~21 0F 也可用4~6V olt阴极处理30秒至1分钟于室温下电解。
9.8锌及锌合金之酸浸溶液配方Chromicacid30~40oz/galSodiumsulfate2~4oz/galTemperatureroomT ime5~30sec 若水洗后有黄色膜则用1%硫酸浸泡脱色。
Chromicacid30~40oz/galHydrochloride12oz/galTemperatureroomTi me1min 水洗完后再用40oz/gal铬酸水溶液浸泡。
9.9镍及钴合金之酸浸溶液配方(1)AISI661,670,680,688合金:Hydrofluoricacid48~58oz/galNitricacid7~10ozgalTemperatureroom Sodiumhydric1~2wt%Sodiumhydroxide98~99wt%Temperature680~ 720F(2)纯镍Hydrochlorideacid50~75vol%Temperatureroom(3)出光(brightdipping)Sulfuricacid5vol%Ferricsulfate24oz/galTemperature1 80FHydrochlorideacid25vol%Ferricsulfate13oz/galTemperature160~180 F9.10钢铁酸浸溶液配方商业抑制剂(commercialinhibitors),氨类(amines)及硝酸盐(nitrates)通常用来防止过度浸蚀(overetching)及针孔(pitting)。
其配方有:Hydrochloricacid55vol%Inhibitor(optional)需要量TemperatureroomTime1/2~1min可溶解含Fe至5oz/gal;Cu0.5oz/gal最多。
Sulfuricacid25vol%Inhibitor(optional)asrequiredTemperatureroomTi meupto10min 槽及加热管需用铅被覆(lead-lined)。
(3)钢400系列及pH钢除锈配方有:Ferricsulfateanhydrous8.5~13.5oz/galHydrofluoricacid1.5~2.5oz/gal Temperature125~135FTime1~5minSodiumchloride2~4oz/galSulfuricacid12~27oz/galTemperature160~ 180FTimeminSulfuricacid2~3oz/galPotassiumnitrate2~3oz/galTemperature160FTi me5~15min 松脱锈垢(loosenheavy) Potassiumpermanganate8~12oz/galSodiumhydroxide8~12oz/galTem perature160Fto沸点Time30min此溶液处理后需再用溶液(1)或(2)除锈。
(4)铸铁除锈配方:Sulfuricacid10~15oz/gal或25~30oz/galNitricacid4~5oz/galHydrofluoric12~15oz/gal(5)出光(brightdips)配方有:Citricacid10~12oz/galammoniapH65~7Oxalicacid1~2oz/galHydrog en0.5oz/galSulfateasbrightener微量高电流密度电解拋光。
9.11铜及铜合金之酸浸溶液配方(1)去除厚垢(heavyscale)配方:Sulfuricacid55~80oz/galNitricacid10~15oz/galTemperatureroom 铜溶解含量最多到3oz/gal。
(2)去除普通锈皮(moderatescales)配方:Sulfuticacid20~30oz/galChromicacid或3~4oz/galSodiumdichromate45~6oz/galTemperatureroom铜溶解最多含量到2oz/gal。
(3)去除轻微锈皮(lightscales)配方:Sulfuricacid19~26oz/galTemperatureroom~125F铜溶解量最多到4oz/gal。
(4)含0.7%Pb以上之铜合金酸浸配方:Fluboricacid15~24oz/galTemperatureroom 铜溶解含量最多到1.5oz/gal。
焊接对象另加5%过氧化氢hydrogenperoxide。
(5)出光(brightdipping)配方有:Sulfuricacid90~110oz/galNitricacid20~25oz/aglwater33vol% Sodiumchloride0.25oz/gal 绿化钠帮助出光,但过量会产生斑点(spotting)。
Phosphoricacid(85%)55vol%Nitricacid(40Be^-1)20vol%Aceticacid( 98%)25vol%Temperature130~75FSodiumcyanide4~6oz/galTempera ture120~150F也可在较低温度下阳极处理9.12不锈钢酸浸盐酸会产生晶界侵蚀,残留绿离子会引起应力腐蚀,所以不被推荐使用。
不锈钢锈皮有时不易与酸起作用,若强制除去则会过度酸浸刻蚀基材(substrate)及产生针孔,所以必需先作脱锈(scaleloosening),其配方如下:(1)脱锈(scaleloosening)配方:SodiumhydroxideNaOH20~25oz/aglSodiumcarbonate(anhydrous)25 oz/galPotassiumpermanganate6~8oz/aglTemperature190F到沸点Sodiumcarbonate20oz/galSodiumhydroxide5oz/galPotassiumperman ganate12oz/galTemperature190F到沸点Sulfuricacid10vol%Temperature180F (2)除锈酸浸(pickling)配方:Nitricacid30~65oz/galHydrofluoricacid或4vol%Ammoniumbifluoride6.7oz/galTemperature120~140FTime不超过30min DissolvedmetalFe最多到3oz/gal(3)冷加工对象除锈酸浸配方有:Sulfuricacid6.25vol%Hydrofluoricacid6.25vol%Chromicacid8oz/gal Temperature到180FFerricsulfate9~13oz/galHydrofluoricacid1.7vol%Temperature1 25~135FSulfuricacid10oz/galFerricsulfate0.25oz/galTemperature16 0~180FNitricacid45~70oz/galMolybdicacid0.35~0.5oz/agl 此溶液可去除金属杂质(foreignmetals)10超音波洗净超音波如果正确使用,对清洁工作很有帮助,它可节省时间,金钱及增加清洁度(clearness),工作可小至螺丝而大到超过300磅重.它是利用涡流(cavitation)作用及破裂(implosion)作用去除表面污物,它对复杂工件或细孔的工件都有效. 10.1超音波洗净之影响因素(1)温度:一般温度愈高,超音波洗净愈好,但不要越过低于沸点10^c,及不利之化学作用. (2)气体:继续法使溶液气体易于浮出,或加热使溶液减少,加润湿剂(wettingagent),使气体能迅速离开表面. (3)表面张力(surfacetension)愈大则涡流作用密度(cavitationdensity)愈小.(4)粘度(viscosity)愈大则须较大的能量起涡流作用.(5)超音波能量(ultrasonicpower)要适当,太大或太小都不好. (6)苹律(frequency)愈大需高能量来产生相同之涡流作用,一般在21~45kHz. (7)工件之曝露(partexposure),工件里面必需接触到超音波洗净液,通过错误有 1.工件放置不适当形成空气袋(gaspockets).有时需要翻动工件,2.篮子内小工件太多,负荷过多,宁可少量多次不要多量多次,3.篮子及挂架(basketsorfixturesforholdingparts)阻碍音波. (8)污点(contaminants)种类:1.可溶性污物(solublecontaminamts).2.不溶性由可溶性粘合污物(non-soluble,heldbysolublebindercontaminanys)如切削屑粘附在油指物上.).3.不溶性污物(non-solublecontaminants).(9)洗净液化学成份(cleaningchemical).(10)设备(equipments).10.2超音波洗净之原理及优点原理: 超音波洗净的作用,是以超过人类听觉声苹以上的波动在液体中传导,当音波在洗净剂中传导,由于声波是一种纵波,纵波推动介质的作用会使液体中压力变化而产生无数微小真空泡,称之为<空洞现象>(cavitation). 当气泡受压爆破时,会产生强大的冲击能,可将固着在对象死角内的污垢打散,并增加洗净剂的洗净效果.由于超音波苹率高波长短,穿透力强,因此对有隐蔽细缝或复杂结构的洗净物,可以达到完全洗净的惊人效果. 优点: (1)节省人力及时间:降低人工成本,不必将物品拆开和用手刷洗,大量节省人力及时间.(2)完全清洗:精密零件及昂贵物品,均可完全清洗而不伤材质. (3)复杂物的清洗:能将复杂形状的物品,死角及隐蔽孔洞之污垢完全清洗,解除一般清洗法无法克服的难题.(4)操作简单:免去物料流程的担误,减少在制品瓶颈,增加产量. (5)可配合洗剂:可使用性质温和之溶剂,达成更加的洗净效果,免除危险性. 铸造视频:铸造论坛: 机床铸件:此溶液处理后需再用溶液(1)或(2)除锈。