浅析冲压件检验准则(doc 8页)
冲压件检验标准
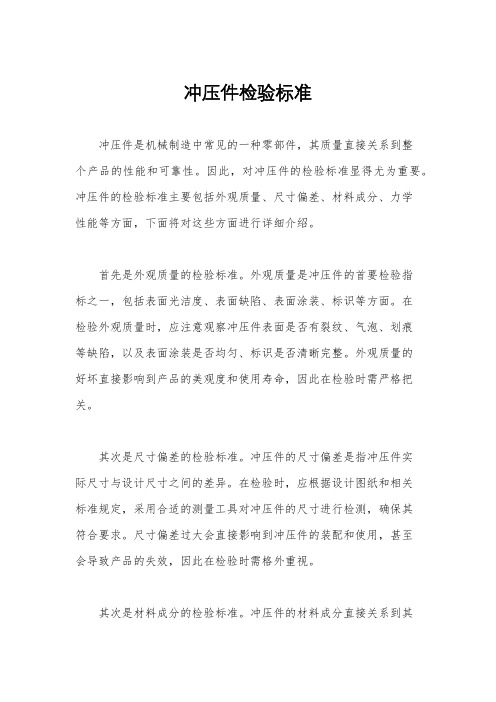
冲压件检验标准冲压件是机械制造中常见的一种零部件,其质量直接关系到整个产品的性能和可靠性。
因此,对冲压件的检验标准显得尤为重要。
冲压件的检验标准主要包括外观质量、尺寸偏差、材料成分、力学性能等方面,下面将对这些方面进行详细介绍。
首先是外观质量的检验标准。
外观质量是冲压件的首要检验指标之一,包括表面光洁度、表面缺陷、表面涂装、标识等方面。
在检验外观质量时,应注意观察冲压件表面是否有裂纹、气泡、划痕等缺陷,以及表面涂装是否均匀、标识是否清晰完整。
外观质量的好坏直接影响到产品的美观度和使用寿命,因此在检验时需严格把关。
其次是尺寸偏差的检验标准。
冲压件的尺寸偏差是指冲压件实际尺寸与设计尺寸之间的差异。
在检验时,应根据设计图纸和相关标准规定,采用合适的测量工具对冲压件的尺寸进行检测,确保其符合要求。
尺寸偏差过大会直接影响到冲压件的装配和使用,甚至会导致产品的失效,因此在检验时需格外重视。
其次是材料成分的检验标准。
冲压件的材料成分直接关系到其力学性能和耐腐蚀性能。
在检验时,应对冲压件的材料成分进行化学成分分析,确保其符合相关标准要求。
同时,还需对材料进行金相组织分析,以确保其组织结构均匀,无夹杂和缺陷。
材料成分的合格与否直接关系到冲压件的使用寿命和安全性,因此在检验时需严格执行相关标准规定。
最后是力学性能的检验标准。
冲压件的力学性能包括强度、硬度、韧性等指标。
在检验时,应根据相关标准规定,采用合适的试验设备对冲压件的力学性能进行检测,确保其符合设计要求。
力学性能的好坏直接关系到冲压件在使用过程中的承载能力和抗疲劳性能,因此在检验时需特别重视。
综上所述,冲压件的检验标准涉及到外观质量、尺寸偏差、材料成分、力学性能等多个方面,对冲压件的质量和性能起着至关重要的作用。
在实际生产中,我们应严格执行相关标准规定,加强对冲压件的检验工作,确保产品质量,提高产品的竞争力和市场占有率。
外观检验标准(冲压件)

(八)最新生效日期:2006。
09。
15第 1 页共2 页冲压制品检验规范检验项目检验要求判定标准检验判定Cr Maj Min OK起皱物件表面不能有明显的起皱现象①物件A级面,不能有起皱现象有起皱,但不明显,经后续加工可遮盖有起皱,但较明显,经后续加工不可遮盖②物件B、C级面,表面有起皱,但经后续加工可消除,可接受表面有起皱,但经后续加工可不消除破裂物件经冲压加工后,不能有破裂现象①物件表面及边沿在经冲压后不能有破裂②孔位边沿有破裂(除装饰孔以外的组装孔),组装后能遮盖组装后不能遮盖,但不影响产品结构和外观组装后不能遮盖,影响产品结构和外观③所有装饰孔不能有破裂现象披锋物件边沿、孔位,不能有锋利的尖角和披锋①物件断切面及边、孔,不能有明显披锋或组装后可遮盖②物件断切面披锋高≦0.1mm ,不伤手,不影响产品外观③物件断切面披锋高≦0.1mm ,且有尖角、伤手,不接受④断切面披锋高≦0.1mm ,不伤手,但影响产品外观⑤断切面披锋高≦0.1mm ,组装时影响产品装配,但可以组装不可以组装⑥物件冲孔位披锋,不影响产品装配及外观影响产品装配及外观⑦装饰孔或散热孔披锋(内部),如不影响装配及外观,披锋搞出0.15mm ,可接受如果影响产品组装(易伤手),则不接受缺料物件表面及边、角不能有任何缺料现象①物件表面及能触及的边角,不能有任何缺料现象②物件在加工过程中,如果有缺料,但经过后加工剪切后,可消除③物件内部缺料,不影响产品组装和外观可接受冲压痕物件表面及孔位边沿,不能有明显的冲压痕①物件表面不能有明显的冲压模痕及废料痕或模具拉痕②如果表面有冲压痕迹,在后续加工过程中可消除③物件表面冲压痕,在后续加工中不能消除拉痕物件表面不能有明显①物件表面不能有明显的拉伤、压伤痕(八)最新生效日期:2006。
09。
15第 2 页共2 页的拉、压痕②物件表面拉痕的长≦10mm ,宽≦0.1mm ,深≦0.05mm10mm<长≦20mm , 宽≦0.1mm , 深≦0.05mm10mm<长≦20mm , 宽>0.1mm , 深≦0.05mm10mm<长≦20mm , 宽>0.1mm ,0.05mm<深≦0.1mm③表面拉痕,在后续加工过程中可消除④表面拉痕,在后续加工过程中不能完全消除,或不可消除损伤物件表面及孔边不能有任何损伤①物件表面无任何损伤现象②物件表面损伤面积5mm²且较轻,可修复物件表面损伤面积5mm²且较重,不可修复物件表面损伤面积>5mm²,不可接受③孔位边沿损伤,在后续装配过程中可遮盖孔位边沿损伤,在后续装配过程中不可遮盖变形物件边口及表面、孔边不能有冲压变形现象①物件表面及边口变形明显,不能接受②物件表面及边口变形,在50cm 处观察不明显,可接受③孔位冲压变形,组装后可遮盖,不影响产品外观,可接受④孔位冲压变形,组装后不能遮盖,影响产品外观尺寸产品重要配合尺寸,满足设计要求①产品配合尺寸,符合设计要求②产品重要求尺寸,符合设计要求③产品配合尺寸,超过其最大公差值≦0.1mm,可接受产品配合尺寸,超过其最大公差值>0.1mm,,但不影响装配或后续作业产品配合尺寸,超过其最大公差值>0.1mm,,影响装配或后续作业④孔位尺寸,经实测值大于最大公差值,不影响产品外观、结构孔位尺寸,经实测值大于最大公差值,影响产品外观、结构⑤产品尺寸小于设计尺寸或孔位尺寸小于设计尺寸,影响产品组装或不能组装⑥孔位尺寸偏斜,组装后不影响整体外观和结构,可接受孔位尺寸偏斜,组装后影响整体外观和结构,不接受。
冲压件检查标准.doc

冲压件检查标准1.目的:确定冲压件的外观、线性尺寸、形位公差检验条件、检验手段的一般标准,指导合理、经济的进行检验与品质控制;并可指导相关工艺、检验作业指导书的制订。
2.范围:本标准适用信发所有冲压件的外观、线性尺寸、形位公差检验控制。
3.外观检验3.1 检查方法产品及原材料的检查方法以如下条件进行目视检查,需要时可使用菲林 , 并可借助 10 倍放大镜。
对所发现的外观缺陷按相应允收标准作出判定。
3.1.1 位置:检查人员的眼睛与被测对象物表面的距离: 30~45cm。
对测量对象表面要以垂直及 45°的角度进行检查。
(参照图 1)3.1.2照明:2X36W白色日光灯在距离150~200cm处发出之光亮。
3.1.3视力:检查人员要求正常或矫正视力在 1.0 以上,且无色盲。
3.1.4 时间:不得在被测对象物上停留,必须以连续的动作进行,若发现异常时,允许不超过 5 秒的停留时间作确认。
光源与光源垂直的面光源与光源平行的面图1测定对象面的目视位置3.2等级定义根据部品所处位置分为 3 个等级,若需要详细的等级定义时,在相关部门协议基础上,另行规定。
3.2.1 A 级面:在正常使用状态下 , 时常处在使用者视线范围内之面。
如产品之正面、上面、侧面,或据客户要求指定为 A 级的面。
3.2.2 B级面:使用者在正常使用状态下不可直接目视,但时常能看到的面。
如产品之后面、底面。
3.2.3 C级面:通常使用者看不到,但在如维修维护打开时能看到的面。
3.3 附则:3.3.1 [冲压部品及零件外观缺陷评判基准] ,见表。
3.3.2如出现评判表中未列出之外观缺陷均作“MAJ”严重缺陷处理。
3.3.3 只靠外观基准书不能表现的缺陷 , 作出限度样本。
限度样本从制作到登录、管理方面参见 [ 限度样本管理规定 ] 。
3.4 评判基准冲压部品及零件外观缺陷评判基准A 级面项目评判基准缺陷等级划伤/ 擦宽度 0.2mm以下 , 并且长度 10mm以下 , 且每一个面内只允许有一个, 或限度样本范围内 . MAJ 伤撞伤参照菲林测定图表2. φ 50 的圆周内不允许有MAJ , 不允许超过 0.2mm 同一面上只允许有两个2以下的不评价 . 或限度样本范围内 . 两个 . 但 0.05mm异物尘参照菲林测定图表25 个 , φ 50 的圆周内不MAJ , 不允许有超过 0.2mm 同一个面上只允许有点2允许有两个 . 但 0.05mm 以下的不评价 . 或限度样本范围内 .披锋一般披锋高度≤材料厚度的10%,但最高不可超过 0.15mm,并且没有对客户造成障害的MAJ 可能性 , 但有机能要求的面不允许有披锋凹陷限度样板范围内MAJ 压痕、顶参见“撞伤”项目评判基准,但顶针痕迹不可突出表面MAJ 屎针孔直径不可超过φ 0.3mm,同一面上只允许有 4 个或以下 , φ 100 的圆周内不允许有 2 个MAJ 污迹、指不可有污迹 , 指纹印MAJ 纹油污参照用白纸擦拭 , 不可有油污MAJ 色差在限度样板范围内MAJ 变形、偏无明显变形 , 偏斜 , 如影响装配 / 尺寸等,或在图面容许、限度样板范围内MAJ 斜接着接着剂不可溢露到外观部位MAJ 起泡/ 起不允许MAJ皮脱落生锈表面及剪口面均不允许MAJ 段差在可动部 / 非可动部都不可有超过0.8mm的段差 , 或在限度样板范围内MAJ 间隙间隙允许 0.5mm以下 , 且最大值和最小值的的差是全长范围内150mm以内时 0.3mm以MAJ 下 , 超过 150mm时 0.5mm以下 , 或限度样板范围内 .其它错、漏加工 , 缺料 , 裂纹 , 裂缝等不允许MAJ B 级面项目评判基准缺陷等级划伤/ 擦宽度 0.2mm以下 , 并且长度 20mm以下 , 且每一个面内只允许有一个, 或限度样本范围内 . MAJ 伤撞伤250 的圆周内不允许MAJ 参照菲林测定图表 , 不允许超过 0.3mm 同一面上只允许有两个。
冲压件检验标准

冲压件检验标准冲压件是机械制造中常见的一种零部件,其质量直接影响到整个产品的质量和性能。
因此,对冲压件的检验标准显得尤为重要。
本文将围绕冲压件的检验标准展开讨论,以期为相关行业提供参考。
首先,冲压件的外观质量是最直观的检验指标之一。
外观质量包括冲压件的表面光洁度、无损伤、无变形等方面。
在检验时,应该通过肉眼或辅助工具对冲压件进行全面、细致的观察。
同时,可以采用比对样件、使用光源照射等方式来确保外观质量的一致性和准确性。
其次,冲压件的尺寸精度也是需要严格检验的重要指标。
尺寸精度直接关系到冲压件的装配和使用。
在检验过程中,应该采用精密的测量工具,如千分尺、游标卡尺等,对冲压件的尺寸进行精确测量,并与设计图纸进行比对,以确保尺寸精度符合要求。
另外,冲压件的材料成分和力学性能也是需要重点检验的内容之一。
材料成分的检验可以通过化学分析、光谱分析等手段进行,以确保冲压件所使用的材料符合标准要求。
而力学性能的检验则需要通过拉伸试验、冲击试验等方式来进行,以确保冲压件在使用过程中具有足够的强度和韧性。
此外,冲压件的表面涂装和防腐蚀性能也是需要重点考虑的内容。
表面涂装应该均匀、牢固,不应有脱落、起泡等现象。
而防腐蚀性能则需要通过盐雾试验、湿热循环试验等方式来进行检验,以确保冲压件在各种恶劣环境下都能保持良好的表面状态。
最后,对于一些特殊要求的冲压件,如汽车车身件、航空航天零部件等,还需要根据相关行业标准进行特殊的检验,以确保冲压件的质量符合特定的使用要求。
综上所述,冲压件的检验标准涉及到外观质量、尺寸精度、材料成分、力学性能、表面涂装和防腐蚀性能等多个方面。
只有严格按照标准要求进行检验,才能保证冲压件的质量稳定、可靠,从而确保整个产品的质量和性能。
希望本文所述内容能够为相关行业提供一定的参考价值,同时也希望各行业能够根据自身实际情况,制定更加严格、科学的冲压件检验标准,为产品质量的提升提供有力保障。
冲压件检验标准
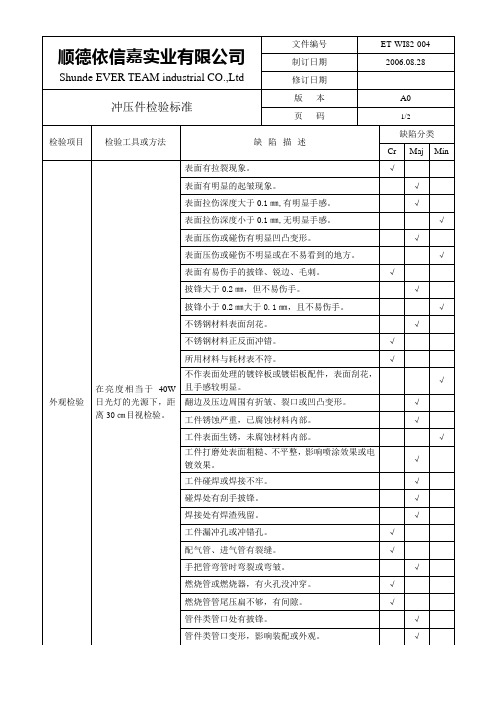
批准
审核
编制
古渊
√
焊接或碰焊错位,但不影响装配或外观的,视为轻微缺陷。
√
螺纹规格与图纸不符,导致无法装配,则视为致命缺陷。
√
螺纹滑牙,导致装配不牢,则视为致命缺陷。
√
工件尺寸超出公差,虽不影响装配,但影响产品主要功能正常发挥,则视为致命缺陷。
√
工件尺寸超出公差,虽不影响装配及其主要功能,但影响产品的使用效果,则视部。
√
工件打磨处表面粗糙、不平整,影响喷涂效果或电镀效果。
√
工件碰焊或焊接不牢。
√
碰焊处有刮手披锋。
√
焊接处有焊渣残留。
√
工件漏冲孔或冲错孔。
√
配气管、进气管有裂缝。
√
手把管弯管时弯裂或弯皱。
√
燃烧管或燃烧器,有火孔没冲穿。
√
燃烧管管尾压扁不够,有间隙。
√
管件类管口处有披锋。
检验项目
检验工具或方法
缺陷描述
缺陷分类
Cr
Maj
Min
外观检验
在亮度相当于40W日光灯的光源下,距离30㎝目视检验。
表面有拉裂现象。
√
表面有明显的起皱现象。
√
表面拉伤深度大于0.1㎜,有明显手感。
√
表面拉伤深度小于0.1㎜,无明显手感。
√
表面压伤或碰伤有明显凹凸变形。
√
表面压伤或碰伤不明显或在不易看到的地方。
√
管件类管口变形,影响装配或外观。
√
检验项目
检验工具或方法
缺陷描述
缺陷分类
Cr
Maj
Min
尺寸检验
钢尺
游标卡尺
高度游标卡尺
冲压件检验规范标准.docx
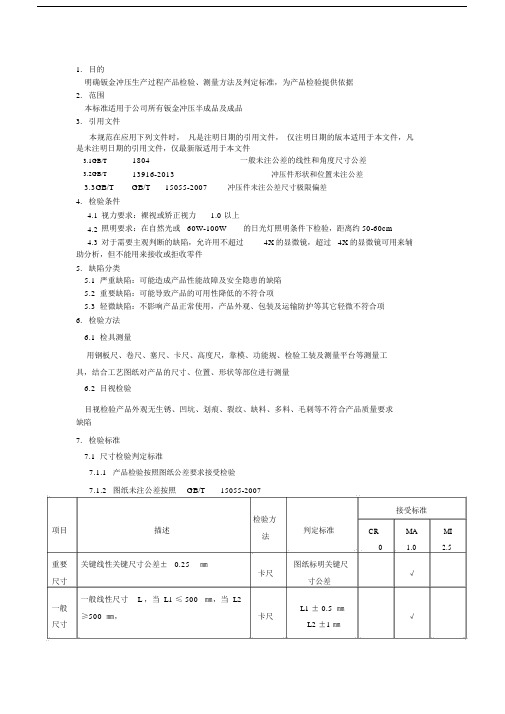
1. 目的明确钣金冲压生产过程产品检验、测量方法及判定标准,为产品检验提供依据2. 范围本标准适用于公司所有钣金冲压半成品及成品 3. 引用文件本规范在应用下列文件时, 凡是注明日期的引用文件, 仅注明日期的版本适用于本文件,凡是未注明日期的引用文件,仅最新版适用于本文件1804一般未注公差的线性和角度尺寸公差13916-2013 冲压件形状和位置未注公差3.3GB/T GB/T15055-2007冲压件未注公差尺寸极限偏差4. 检验条件4.1 视力要求:裸视或矫正视力 1.0 以上4.2 照明要求:在自然光或 60W-100W的日光灯照明条件下检验,距离约50-60cm4.3 对于需要主观判断的缺陷,允许用不超过 4X 的显微镜,超过 4X 的显微镜可用来辅助分析,但不能用来接收或拒收零件 5. 缺陷分类5.1 严重缺陷:可能造成产品性能故障及安全隐患的缺陷 5.2 重要缺陷:可能导致产品的可用性降低的不符合项5.3 轻微缺陷:不影响产品正常使用,产品外观、包装及运输防护等其它轻微不符合项6. 检验方法6.1 检具测量用钢板尺、卷尺、塞尺、卡尺、高度尺,靠模、功能规、检验工装及测量平台等测量工具,结合工艺图纸对产品的尺寸、位置、形状等部位进行测量6.2 目视检验目视检验产品外观无生锈、凹坑、划痕、裂纹、缺料、多料、毛刺等不符合产品质量要求缺陷7. 检验标准7.1 尺寸检验判定标准7.1.1 产品检验按照图纸公差要求接受检验7.1.2 图纸未注公差按照GB/T 15055-2007检验方接受标准项目描述判定标准法CRMA MI0 1.02.5重要关键线性关键尺寸公差± 0.25㎜图纸标明关键尺尺寸卡尺寸公差√一般 一般线性尺寸L ,当 L1 ≤ 500 ㎜,当 L2L1 ± 0.5 ㎜≥500 ㎜, 卡尺√尺寸L2 ±1 ㎜3.2GB/T3.1GB/T装配孔一般过孔形状位置方料长宽尺寸轮廓扭曲变形孔径尺寸 D1 ≤ 30㎜D1 ﹢ 0.3㎜孔径尺寸 D2 ≥ 30㎜卡尺位置度D2 ﹢ 0.5㎜√功能规± 0.25 ㎜孔径尺寸 D1 ≤ 30㎜D1 ﹢ 0.5㎜孔径尺寸 D2 ≥ 30㎜卡尺位置度D2 ﹢ 1 ㎜√功能规±0.5㎜冲压件形状位置未注公差参考 GB/T满足装配检具适13916-2013检具√用性1 :切板方料长度尺寸 L ± 0.5卡尺㎜√卷尺2: 开料对角线尺寸偏差≤ 0.5 ㎜1 :前壳成型后扭曲变形量≤ 2卡尺㎜√塞尺 2 :后壳成型后扭曲变形量≤ 1㎜1: 厚度 3.0 ㎜板料后壳打点高度后壳0.3-0.5 ㎜凸点卡尺√2 :厚度 4.0㎜高度板料后壳打点高度 1.3 ± 0.1㎜1 :焊缝目视检直缝验标准点打点深焊检度 0.3-0.5㎜验参卡尺√2 :计算方法,考点大点深度约等于深度1/2直径翻孔不均匀高度尺寸不符合图纸要求1 :翻孔净高度翻孔3+1 ㎜翻边卡尺√2 :端盖翻边高高度度 h ±0.5㎜7.2 外观检验判定标准检验方接受标准项目描述判定标准MA MI法CR01.02.5锈蚀是冲压件长期存放或者存放不当导致对产品功能、强度、耐疲劳度产生影响。
冲压件表面检验标准
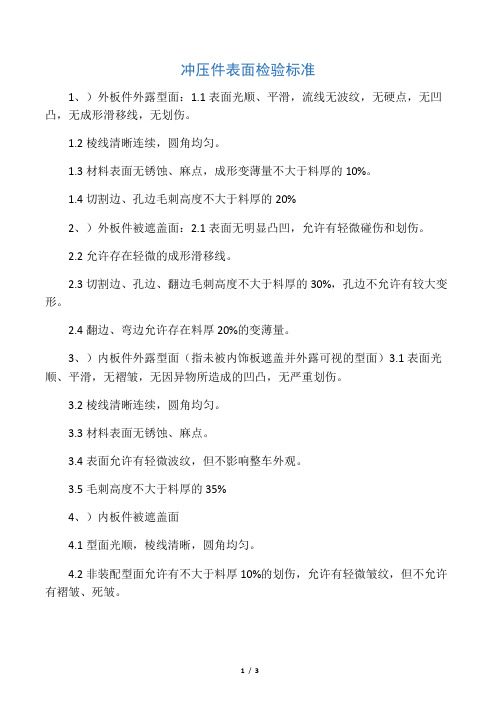
冲压件表面检验标准1、)外板件外露型面:1.1表面光顺、平滑,流线无波纹,无硬点,无凹凸,无成形滑移线,无划伤。
1.2棱线清晰连续,圆角均匀。
1.3材料表面无锈蚀、麻点,成形变薄量不大于料厚的10%。
1.4切割边、孔边毛刺高度不大于料厚的20%2、)外板件被遮盖面:2.1表面无明显凸凹,允许有轻微碰伤和划伤。
2.2允许存在轻微的成形滑移线。
2.3切割边、孔边、翻边毛刺高度不大于料厚的30%,孔边不允许有较大变形。
2.4翻边、弯边允许存在料厚20%的变薄量。
3、)内板件外露型面(指未被内饰板遮盖并外露可视的型面)3.1表面光顺、平滑,无褶皱,无因异物所造成的凹凸,无严重划伤。
3.2棱线清晰连续,圆角均匀。
3.3材料表面无锈蚀、麻点。
3.4表面允许有轻微波纹,但不影响整车外观。
3.5毛刺高度不大于料厚的35%4、)内板件被遮盖面4.1型面光顺,棱线清晰,圆角均匀。
4.2非装配型面允许有不大于料厚10%的划伤,允许有轻微皱纹,但不允许有褶皱、死皱。
4.3切割边、孔边、翻边毛刺高度不大于料厚的35%,孔边不允许有较大变形。
4.4材料成型变薄量不大于料厚的15%。
5、)结构件(料厚在1.0mm以上内板件、加强件、加强梁等)装配面5.1型面平整,圆角清晰,局部允许有不影响焊接的轻微波纹。
5.2螺母孔周边不允许变形。
5.3切边、弯边、翻边、孔周边不允许有较大变形,毛刺高度不大于料厚的35%5.4材料成型变薄量不大于料厚的20%。
6、)结构件(料厚在1.0mm以上内板件、加强件、加强梁等)非装配型面6.1局部型面允许有不大于料厚20%的拉痕、拉伤等成型痕迹。
6.2局部型面允许有较轻波纹和皱纹,但不允许有褶皱、死皱6.3材料成型变薄量不大于料厚的20%6.4切边、弯边、翻边、孔周边毛刺高度不大于料厚的40%,孔边不允许有较大变形。
7、质量问题描述及处理方法:1、)毛刺(用角磨机打磨修边有毛刺处)2、)拉毛(用抛光机打磨拉毛处,如拉毛严重,可先用角磨机打磨)3、)高点(较高的高点线用锤击修整,再用专用工具刮平,最后用抛光机抛光;小高点用专用工具刮平,再用抛光机抛光。
冲压件检查标准
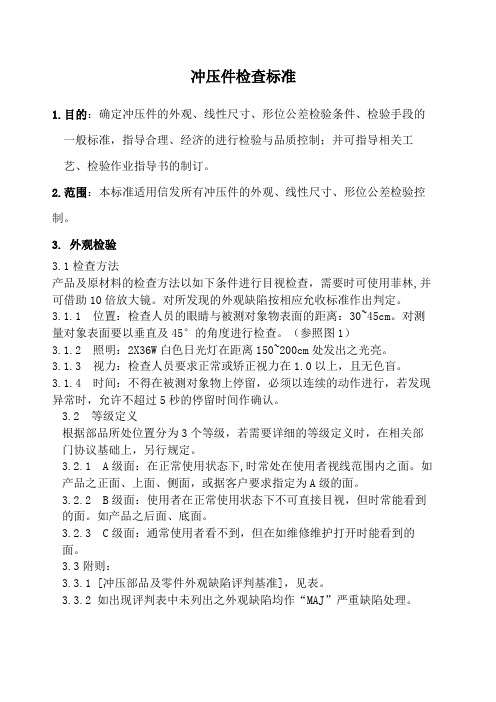
冲压件检查标准1.目的:确定冲压件的外观、线性尺寸、形位公差检验条件、检验手段的一般标准,指导合理、经济的进行检验与品质控制;并可指导相关工艺、检验作业指导书的制订。
2.范围:本标准适用信发所有冲压件的外观、线性尺寸、形位公差检验控制。
3. 外观检验3.1检查方法产品及原材料的检查方法以如下条件进行目视检查,需要时可使用菲林,并可借助10倍放大镜。
对所发现的外观缺陷按相应允收标准作出判定。
3.1.1 位置:检查人员的眼睛与被测对象物表面的距离:30~45cm。
对测量对象表面要以垂直及45°的角度进行检查。
(参照图1)3.1.2 照明:2X36W白色日光灯在距离150~200cm处发出之光亮。
3.1.3 视力:检查人员要求正常或矫正视力在1.0以上,且无色盲。
3.1.4 时间:不得在被测对象物上停留,必须以连续的动作进行,若发现异常时,允许不超过5秒的停留时间作确认。
3.2 等级定义根据部品所处位置分为3个等级,若需要详细的等级定义时,在相关部门协议基础上,另行规定。
3.2.1 A级面:在正常使用状态下,时常处在使用者视线范围内之面。
如产品之正面、上面、侧面,或据客户要求指定为A级的面。
3.2.2 B级面:使用者在正常使用状态下不可直接目视,但时常能看到的面。
如产品之后面、底面。
3.2.3 C级面:通常使用者看不到,但在如维修维护打开时能看到的面。
3.3附则:3.3.1 [冲压部品及零件外观缺陷评判基准],见表。
3.3.2 如出现评判表中未列出之外观缺陷均作“MAJ”严重缺陷处理。
3.3.3 只靠外观基准书不能表现的缺陷,作出限度样本。
限度样本从制作到登录、管理方面参见[限度样本管理规定]。
3.4评判基准冲压部品及零件外观缺陷评判基准4.1.测定环境标准条件尺寸测定环境应满足环境温度20±8℃,相对温度50±15%,测定前部品应在此环境内静置适当时间,以保证部品检测条件符合标准要求。
冲压件检验标准
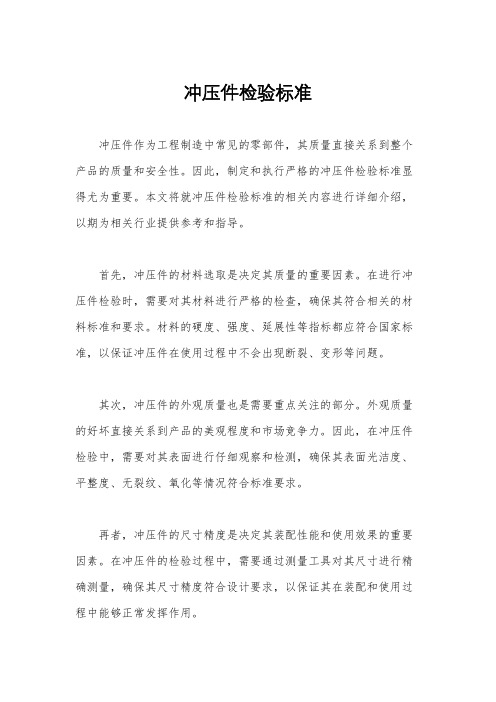
冲压件检验标准冲压件作为工程制造中常见的零部件,其质量直接关系到整个产品的质量和安全性。
因此,制定和执行严格的冲压件检验标准显得尤为重要。
本文将就冲压件检验标准的相关内容进行详细介绍,以期为相关行业提供参考和指导。
首先,冲压件的材料选取是决定其质量的重要因素。
在进行冲压件检验时,需要对其材料进行严格的检查,确保其符合相关的材料标准和要求。
材料的硬度、强度、延展性等指标都应符合国家标准,以保证冲压件在使用过程中不会出现断裂、变形等问题。
其次,冲压件的外观质量也是需要重点关注的部分。
外观质量的好坏直接关系到产品的美观程度和市场竞争力。
因此,在冲压件检验中,需要对其表面进行仔细观察和检测,确保其表面光洁度、平整度、无裂纹、氧化等情况符合标准要求。
再者,冲压件的尺寸精度是决定其装配性能和使用效果的重要因素。
在冲压件的检验过程中,需要通过测量工具对其尺寸进行精确测量,确保其尺寸精度符合设计要求,以保证其在装配和使用过程中能够正常发挥作用。
此外,冲压件的功能性能也是需要进行全面检验的内容之一。
不同的冲压件在使用过程中需要具备不同的功能,因此在检验过程中需要根据具体情况对其功能进行全面的检测,确保其能够满足产品设计的要求。
最后,冲压件的耐久性和可靠性也是需要重点检验的内容。
通过模拟使用环境和条件,对冲压件进行耐久性和可靠性测试,以确保其能够在长期使用过程中不会出现失效、损坏等问题,保证产品的安全性和稳定性。
综上所述,冲压件检验标准涉及范围广泛,内容复杂。
只有严格按照相关标准和要求进行检验,才能确保冲压件的质量和性能达到设计要求,为产品的质量和安全提供有力保障。
希望本文所述内容能够对相关行业提供一定的参考和帮助,促进冲压件检验工作的规范化和标准化。
冲压件检验标准
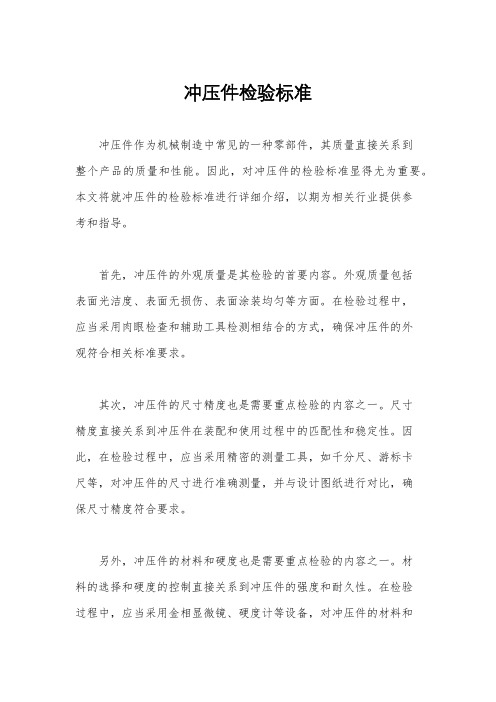
冲压件检验标准冲压件作为机械制造中常见的一种零部件,其质量直接关系到整个产品的质量和性能。
因此,对冲压件的检验标准显得尤为重要。
本文将就冲压件的检验标准进行详细介绍,以期为相关行业提供参考和指导。
首先,冲压件的外观质量是其检验的首要内容。
外观质量包括表面光洁度、表面无损伤、表面涂装均匀等方面。
在检验过程中,应当采用肉眼检查和辅助工具检测相结合的方式,确保冲压件的外观符合相关标准要求。
其次,冲压件的尺寸精度也是需要重点检验的内容之一。
尺寸精度直接关系到冲压件在装配和使用过程中的匹配性和稳定性。
因此,在检验过程中,应当采用精密的测量工具,如千分尺、游标卡尺等,对冲压件的尺寸进行准确测量,并与设计图纸进行对比,确保尺寸精度符合要求。
另外,冲压件的材料和硬度也是需要重点检验的内容之一。
材料的选择和硬度的控制直接关系到冲压件的强度和耐久性。
在检验过程中,应当采用金相显微镜、硬度计等设备,对冲压件的材料和硬度进行检测,确保其符合相关标准要求。
此外,冲压件的装配性能和使用性能也是需要进行检验的内容之一。
装配性能包括冲压件与其他零部件的配合情况,使用性能包括冲压件在使用过程中的稳定性和可靠性。
在检验过程中,应当模拟实际使用环境,对冲压件的装配性能和使用性能进行测试,确保其符合相关标准要求。
总之,冲压件的检验标准涉及多个方面,包括外观质量、尺寸精度、材料硬度、装配性能和使用性能等。
只有严格按照相关标准进行检验,才能保证冲压件的质量和性能符合要求,从而保障整个产品的质量和可靠性。
希望本文的介绍能够为相关行业提供帮助,促进冲压件质量的提升和行业的发展。
冲压件检验标准

文档来源为:从网络收集整理.word版本可编辑.欢迎下载支持.冲压件检验判定标准一、质量判定基本定义1、某些描述中使用的一些主观评价词汇的定义:轻微的:指容易接受的,感觉不太明显、不太大、力量很小、不太持久的。
明显的:指较突出的、较清晰的、不用置疑的。
显著的:指非常突出的、一定觉察得到的、鲜明突出的、完全清晰可见的。
2、冲压件在整车上分区定义汽车分三个区域:两个外区和一个内区。
A区:汽车的上部至车身腰线,分界线为:车身腰线装饰条或保护条的下边线车身腰线装饰槽下边线车身上开合件边框的有关部位:汽车内2区的某些部位,从外面完全看的见,可根据具体情况视做1区处理B区:坐在司机或乘客座位上,关上车门后能看得见的部位,位于:车身腰线以上所有上车时能看见的部位,车身周边,车身边框以及:后侧窗,后行李箱隔板,尾门内板,车身尾门框,行李箱,发动机舱,发动机罩内表面,天窗窗框,油箱加注孔入口所有坐在司机或乘客座位上,关上车门能看的见的,位于车身腰线以下的部位。
C区:位于车身装饰条或保护条以下的部分、不影响客户直观视觉效果的部位。
3、检验基本条件定义:站立,在缺陷扣分区内,在冲压件四周,离件1米进行检查允许俯身,但不能蹲下检查涉及到间隙及高低不平的缺陷,应予以测量判别。
4、检测:–是靠视觉、触觉……进行评判的.。
–只有在有疑问的情况下,才使用检具,根据间隙标准的定义或有关基本标准的定义来核实或明确某些缺陷的扣分级别:·对间隙及高低不平的检查使用塞尺·对冲压件上的坑包、麻点的检查要使用面积规·对表面检查使用尺子5.缺陷分类–外观类:裂纹,缩颈坑包,起皱麻点变形锈蚀材料缺陷起皱,波纹,棱线毛刺拉毛,划伤圆角叠料压痕其它冲压件判定标准冲压件按其功能分为三类,A类是外表面件,其要求最高,其次是B类,主要是结构件。
最后是C类,例如支架之类。
冲压件放于合格的检具上,特殊要求的尺寸和公差按产品图纸要求,其它按照“冲压件的未注允许公差表”执行。
冲压件一般检验原则

冲压件一般检验原则1主题内容与适用范围本标准规定了冲压生产中对在线制品和入库产品的一般检验原则。
本标准适用于金属材料冲压件。
非金属材料冲压件可参照执行。
2、引用标准GB2828逐批检查计数抽样程序及抽样表GB2829周期检查计数抽样程序及抽样表GB6583质量管理和质量保证术语第一部分3、术语3.1在线制品在冲压生产活动中,在工序及工序间流动的在制半成品或制成品。
3.2入库产品冲压工序最后完成的批制成品。
3.3首件检验在以下情况,对第一个(或几个)冲压零件的检验,称为首件检验。
a.变换品种;b.变换材料;c.修、换模后;d.机器(或设备)调整后;e.操作者接班后。
3.4巡回检验对在线制品进行随机的抽样检验,称为巡回检验。
3.5验收检验为判断受检批能否被接收而进行的检验。
3.6末件检验在以下情况,对最后一个(或几个)冲压零件的检验,称为末件检验。
a变换品种前;b变换材料前;c.修、换模(包括交付人库模具)前;d.每班生产终了前。
4、检验的实施4.1检验依据按零件设计图样、工艺文件及有关技术标准确定的单位产品质量特性。
4.2抽样原则在对冲压件进行计数抽检时,一般应遵守GB2828或GB2829中的一次抽样规定。
4.3规定合格质量水平(AQL)及不合格质量水平(RQQ)可由制造方与使用方协商确定,但应尽量选择GB2828或GB2829中给出的优先值。
4.4检验规定4.4.1严格执行首件检验与末件检验。
4.4.2对在线制品进行多次的巡回检验。
4.4.3对每批入库产品必须经过验收检验,依据检验结果作出正确判断。
5、检验5.1尺寸与形状和位置检验5.1.1测量温度无特殊要求时,规定测量温度为室温(生产现场温度)。
5.1.2冲裁断面(指光亮带部位)检验a.孔(内形)尺寸以小端尺寸为准;b.轴(外形)尺寸以大端尺寸为准。
5.1.3成形件径向检验根据零件要求选择检验部位,一般以口部尺寸为准。
5.1.4弯曲、校平等成形件检验根据需要决定检验状态,即采用自然状态或加压状态进行检验。
常见冲压件检验标准(DOC)
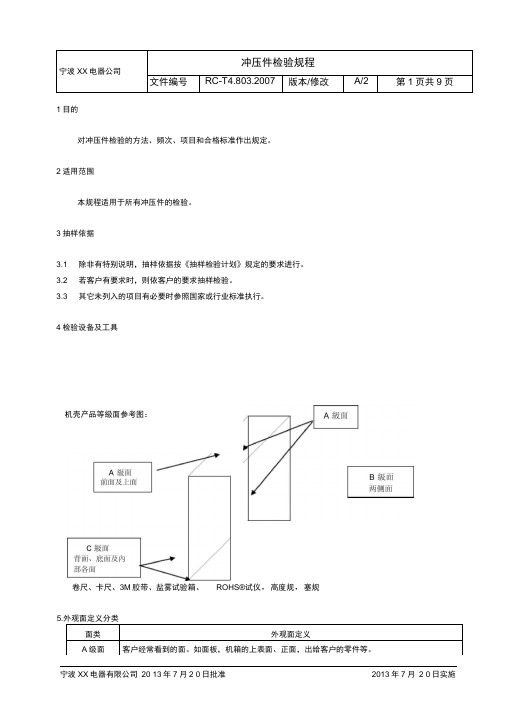
宁波XX电器公司冲压件检验规程文件编号RC-T4.803.2007版本/修改A/2第1页共9页1目的对冲压件检验的方法、频次、项目和合格标准作出规定。
2适用范围本规程适用于所有冲压件的检验。
3抽样依据3.1 除非有特别说明,抽样依据按《抽样检验计划》规定的要求进行。
3.2 若客户有要求时,则依客户的要求抽样检验。
3.3 其它未列入的项目有必要时参照国家或行业标准执行。
4检验设备及工具卷尺、卡尺、3M胶带、盐雾试验箱、ROHS®试仪,高度规,塞规5.面类外观面定义A级面客户经常看到的面。
如面板,机箱的上表面、正面,出给客户的零件等。
机壳产品等級面参考图:6检验条件6.1所有检验均应在正常照明光源为40W荧光灯(相当于80-120LUX光照),裸眼或矫正视力在1.0以上, 并模拟最终使用条件下进行。
检测过程中不使用放大镜,所检验表面和人眼取正常观察角度土450角内, 距离300mm A 级面在检测时应转动,以获得最大反光效果。
B级面和C级面在检测期间不必转动。
(示意图)6.2 A级面停留15秒,B级面停留10秒,C级面停留5秒。
6.3抽验水准(AQL):不合格(缺陷)类别严重主要一般缺陷类别代码A B CAQL0 1.5 2.57 检查项目外观检查、结构尺寸检查、材质检查、特定试验(包括盐雾试验、附着力试验等)、包装检查。
8判定条件8.1 所有的机构、功能要求以图面为准,关于机构尺寸公差如图面未直接于尺寸后标注其公差,则本公司孔的尺寸公差以土0.10mm管制,其他尺寸以土0.20mm进行管制,除非客戶有更为严格或特別要求。
QE人員可视需要在SIP制定時缩小其公差,以利于生产管制,如丽辰公司供货商的产品有因SIP缩小公差管制的问题被判拒收,且可证实是丽辰公司事前未有通知厂商時,当批可以尽量吸收的原则协调处理,但供货商必须于下批改善。
8.2产品因为工艺的特性或设计结构的影响,而存在固有外观缺失(如冲压模具痕;电镀白斑、水紋,这类缺失通常以样品为基准進行判定,但其限度样品的建立需充分遵照本准则之要求,当未有建立样品時也可根据本标准進行判定。
冲压件检查标准

冲压件检查标准C级面评判基准不允许有明显的伤痕,且对机能无影响。
不允许有明显的伤痕,且对机能无影响。
没作规定一般披锋高度≤材料厚度的10%,但最高不可超过0.15mm,并且没有对客户造成障害的可能性,但有机能要求的面不允许有披锋。
限度样板范围内压痕、顶不允许有明显的伤痕 ,且对机能无影响。
没作规定污迹、指不可有明显的污迹,指纹印,但若用酒精等无法去除时应对机能无影响.参照用白纸擦拭,油污占40%以上擦拭面不可.在限度样板范围内变形、偏无明显变形,偏斜,如影响装配/尺寸等,或在图面容许、限度样板范围内接着剂不可溢露到外观部位不允许4.线性尺寸检验4.1.测定环境标准条件尺寸测定环境应满足环境温度20±8℃,相对温度50±15%,测定前部品应在此环境内静置适当时间,以保证部品检测条件符合标准要求。
一般条件尺寸测定环境满足环境温度5~35℃,相对温度45~85%4.2.公差规定产品、零件尺寸公差按客户要求控制;原材料、物料厚度公差参照《常用材料厚度公差表》;常用杂件材料尺寸规格参照《杂件材料尺寸清单》。
4.3.检测器具检测器具一般根据测量对象的精度要求合理、经济地选用,具体参照《常用尺寸检验器具选用表》,并按相关作业指导书正确使用和维护保养。
4.4.检验方法按相关工艺、检验作业指导书规定执行。
4.5. 常用公差表4.5.1.常用材料厚度公差表4.5.1.1.非金属材料厚度公差本表的列数值单位均为mm4.5.1.2.线径类本表的列数值单位均为mm本表的列数值单位均5.形位公差检查5.1.测定环境同线性尺寸检查5.2.公差规定产品、零件形位公差按客户要求控制5.3.检测器具检测器具一般根据测量对象的精度要求合理、经济地选用,具体参照《常用尺寸检验器具选用表》,并按相关作业指导书正确使用和维护保养。
5.4.常见形位公差定义及检验方法(附件)6.力学性能检查6.1. 适用范围适用于本司弹片、接触片五金制品及其原材料力学性能检查。
冲压件检验标准.docx

冲压件检验标准.docx冲压件检验判定标准一、量判定基本定1、某些描述中使用的一些主价的定:微的:指容易接受的,感不太明、不太大、力量很小、不太持久的。
明的:指突出的、清晰的、不用置疑的。
著的:指非常突出的、一定察得到的、明突出的、完全清晰可的。
2、冲件在整上分区定汽分三个区域:两个外区和一个内区。
A区:汽的上部至身腰,分界:身腰装条或保条的下身腰装槽下身上开合件框的有关部位:汽内 2 区的某些部位,从外面完全看的,可根据具体情况做 1 区理B区:坐在司机或乘客座位上,关上后能看得的部位,位于:身腰以上所有上能看的部位, 身周 , 身框以及:后窗,后行李箱隔板, 尾内板,身尾框,行李箱, 机,机罩内表面,天窗窗框,油箱加注孔入口所有坐在司机或乘客座位上,关上能看的的,位于身腰以下的部位。
C区:位于身装条或保条以下的部分、不影响客直效果的部位。
3、基本条件定:站立,在缺陷扣分区内,在冲件四周,离件1 米行允俯身,但不能蹲下涉及到隙及高低不平的缺陷,予以量判。
4、 :–是靠、触?? 行判的. 。
–只有在有疑的情况下,才使用具,根据隙准的定或有关基本准的定来核或明确某些缺陷的扣分:· 隙及高低不平的使用塞尺· 冲件上的坑包、麻点的要使用面· 表面使用尺子5.缺陷分–外 :裂 ,坑包,起麻点形材料缺陷起,波,棱毛刺拉毛,划圆角叠料压痕其它冲压件判定标准判定描述一区二区项目三区外部内部外部内部1、封闭裂纹长度≥80mm或宽度≥3mm(料厚≥);宽度≥2mm (料厚≤)2、不报废封闭裂纹长度≥ 50mm;宽度≥ 2mm裂纹长度小于 80mm或宽度小于 3mm(料厚≥);长度≤ 80mm且宽度≤ 2mm(料厚≤)返工安全件减震器////报废缩颈部位厚度 / 料厚≤ 20%且长度≥ 80mm返工缩颈缩颈部位厚度 / 料厚≥ 20%长度≤ 80mm放行放行放行放行放行安全件减震器受力部位缩颈≥料厚的10%////报废面积≥ 8cm2或长度≥ 10cm高度≥ 3mm报废返工报废返工返工222面积4cm ≤S< 8cm 上或长度5cm≤L< 10cm面积≥ 100cm 坑包返工返工返工返工放行或长度≥ 10cm坑包高度≥ 1mm返工返工返工放行放行零件 2/3 面积上能看到麻点或小凸包。
冲压件检查标准

冲压件检查标准1.目的:确定冲压件的外观、线性尺寸、形位公差检验条件、检验手段的一般标准,指导合理、经济的进行检验与品质控制;并可指导相关工艺、检验作业指导书的制订。
2.范围:本标准适用信发所有冲压件的外观、线性尺寸、形位公差检验控制。
3. 外观检验3.1检查方法产品及原材料的检查方法以如下条件进行目视检查,需要时可使用菲林,并可借助10倍放大镜。
对所发现的外观缺陷按相应允收标准作出判定。
3.1.1 位置:检查人员的眼睛与被测对象物表面的距离:30~45cm。
对测量对象表面要以垂直及45°的角度进行检查。
(参照图1)3.1.2 照明:2X36W白色日光灯在距离150~200cm处发出之光亮。
3.1.3 视力:检查人员要求正常或矫正视力在1.0以上,且无色盲。
3.1.4 时间:不得在被测对象物上停留,必须以连续的动作进行,若发现异常时,允许不超过5秒的停留时间作确认。
3.2 等级定义根据部品所处位置分为3个等级,若需要详细的等级定义时,在相关部门协议基础上,另行规定。
3.2.1 A级面:在正常使用状态下,时常处在使用者视线范围内之面。
如产品之正面、上面、侧面,或据客户要求指定为A级的面。
3.2.2 B级面:使用者在正常使用状态下不可直接目视,但时常能看到的面。
如产品之后面、底面。
3.2.3 C级面:通常使用者看不到,但在如维修维护打开时能看到的面。
3.3附则:3.3.1 [冲压部品及零件外观缺陷评判基准],见表。
3.3.2 如出现评判表中未列出之外观缺陷均作“MAJ”严重缺陷处理。
3.3.3 只靠外观基准书不能表现的缺陷,作出限度样本。
限度样本从制作到登录、管理方面参见[限度样本管理规定]。
3.4评判基准冲压部品及零件外观缺陷评判基准A级面B级面C级面4.1.测定环境标准条件尺寸测定环境应满足环境温度20±8℃,相对温度50±15%,测定前部品应在此环境内静置适当时间,以保证部品检测条件符合标准要求。
- 1、下载文档前请自行甄别文档内容的完整性,平台不提供额外的编辑、内容补充、找答案等附加服务。
- 2、"仅部分预览"的文档,不可在线预览部分如存在完整性等问题,可反馈申请退款(可完整预览的文档不适用该条件!)。
- 3、如文档侵犯您的权益,请联系客服反馈,我们会尽快为您处理(人工客服工作时间:9:00-18:30)。
浅析冲压件检验准则(doc 8页)1 目的规定了冲压件检验的评价准则,确保合格产品流入下一工序,确保产品满足顾客的要求。
2 适用范围适用于冲压件质量的认可。
3 术语无4 职责检验员负责按照本准则对冲压件进行检验。
5 流程图无6 规定6.1冲压件检验区域划分,参照《整车审核工作指导书》中的附件3“车身表面区域的划分”。
6.2冲压件检验方法6.2.1触摸检验6.2.1.1用干净的纱布将外覆盖件的表面擦干净。
6.2.1.2检验员需戴上触摸手套沿着零件纵向紧贴零件表面触摸,这种检验方法取决于检验员的经验。
6.2.1.3必要时可用油石打磨被探知的可疑区域并加以验证,但这种方法不失为一种行之有效的快速检验方法。
6.2.2油石打磨6.2.2.1用干净的纱布将外覆盖件的表面擦干净。
6.2.2.2打磨用油石(20×20×100mm或更大)6.2.2.3有圆弧的地方和难以接触到的地方用相对较小的油石打磨(例如:8×100mm的半圆形油石)6.2.2.4油石粒度的选择取决于表面状况(如粗糙度,镀锌等)。
建议用细粒度的油石。
6.2.2.5油石打磨的方向基本上沿纵向进行,并且很好地贴合零件的表面,部分特殊的地方6.2.2.66.2.2.7瘪塘6.3.2.1检验方法:目视、油石打磨、触摸、涂油6.3.2.2评价准则:A类缺陷:是用户不能接收的缺陷,没有经过培训的用户也能注意到,此类瘪塘发现后必须立即对冲压件进行冻结,A类瘪塘冲压件在任何区域都不允许存在。
B类缺陷:是一种使人感到不愉快的缺陷,它是在冲压件外表面上摸得着和看得见的可确定的瘪塘,在冲压件Ⅰ、Ⅱ区外表面不允许存在此类瘪塘。
C类缺陷:是需要修正的缺陷,这些瘪塘绝大多数处于模棱两可的情况下,只有在油石打磨后才看得出。
此类瘪塘的冲压件可以接受。
6.3.3波浪6.3.3.1检验方法:目视、油石打磨、触摸、涂油6.3.3.2评价准则:A类缺陷:此类波浪在冲压件Ⅰ、Ⅱ区没有经过培训的用户也能注意到,是用户不能接收,发现后必须立即对冲压件进行冻结。
B类缺陷:此类波浪是一种使人感到不愉快的缺陷,在冲压件Ⅰ、Ⅱ区摸得着和看得见的可确定的波浪,是需要返修的。
C类缺陷:是需要修正的缺陷,此类波浪多数处于模棱两可的情况下,只有在油石打磨后才看得出。
此类波浪的冲压件可以接受。
6.3.4翻边、切边不平整及短缺6.3.4.1检验方法:目视、触摸6.3.4.2评价准则:A类缺陷:对于内、外覆盖件任何翻边、切边的不平整及短缺,影响了咬边质量及焊接搭边不平整、短缺,从而影响焊接质量都是不可接受的发现后必须立即对冲压件进行冻结。
B类缺陷:看得见,可确定的对咬边、焊接搭边及焊接质量没有影响的翻边、切边的不平整及短缺。
此类缺陷的冲压件在Ⅱ区内部Ⅲ、Ⅳ可以接受。
C类缺陷:轻微的翻边、切边的不平整及短缺对咬边及搭边焊接质量没有影响,此类缺陷的冲压件可以接受。
6.3.5毛刺:(切边、冲孔)6.3.5.1检验方法:目视6.3.5.2评价准则:A类缺陷:严重影响焊接搭边贴合程度及零件定位装配的冲孔、容易导致人身伤害的粗大毛刺,此缺陷的冲压件不允许存在,必须返修。
B类缺陷:对焊接搭边贴合程度及零件定位装配的冲孔有轻微影响的中等毛刺。
此缺陷的冲压件不允许存在于Ⅰ、Ⅱ区。
C类缺陷:较小的毛刺,此缺陷的冲压件在不影响整车质量的情况下允许存在。
6.3.6拉毛及划伤:6.3.6.1检验方法:目视6.3.6.2评价准则:A类缺陷:严重影响表面质量、潜在的可导致零件拉裂的拉毛及划伤,此类缺陷的冲压件不允许存在。
B类缺陷:看得见可确定的拉毛及划伤,此类缺陷的冲压件允许存在于Ⅳ区。
C类缺陷:轻微的可能导致零件拉毛及划伤,此类缺陷的冲压件允许存在于Ⅲ、Ⅳ区。
6.3.8回弹:6.3.8.1检验方法:放在检具上检验6.3.8.2评价准则:A类缺陷:导致零件间的尺寸匹配和焊接变形严重的回弹,此类缺陷冲压件不允许存在。
B类缺陷:尺寸超差较大,对零件间的尺寸匹配和焊接变形有影响的回弹,此类缺陷冲压件允许存在Ⅲ、Ⅳ区。
C类缺陷:尺寸超差较小,对零件间的尺寸匹配和焊接变形有轻微影响的回弹,此类缺陷冲压件允许存在Ⅰ、Ⅱ、Ⅲ、Ⅳ区。
6.3.9漏冲孔6.3.9.1检验方法:目视检验并用水溶性记号笔作计数标记6.3.9.2评价准则:零件上任何孔的漏冲将影响零件的定位与装配,是不可接受的。
6.3.10起皱:6.3.10.1检验方法:目视6.3.10.2评价准则:A类缺陷:严重的从而导致材料重叠的起皱,此缺陷的冲压件不允许存在。
B类缺陷:可看到、可摸到的起皱,此类缺陷在Ⅳ区可以接受。
C类缺陷:轻微的、不太明显的起皱,此类缺陷的冲压件在Ⅱ、Ⅲ、Ⅳ区可以接受。
6.3.11麻点群、麻点、压痕6.3.11.1检验方法:目视、油石打磨、触摸、涂油6.3.11.2评价准则:A类缺陷:麻点集中,超过整个面积2/3都分布有麻点,此类缺陷在Ⅰ、Ⅱ区发现后,必须立即对冲压件进行冻结。
B类缺陷:麻点可看到、可摸到。
此类缺陷不允许在Ⅰ、Ⅱ区出现。
C类缺陷:打磨后可见单独分布的麻点,在Ⅰ区要求麻点间距离为300mm或更大。
此类缺陷的冲压件可以接受。
6.3.12打磨缺陷、打磨印6.3.12.1检验方法:目视、油石打磨6.3.12.2评价准则:A类缺陷:打磨穿了,在外表面上明显可见,所有顾客都立即可见。
此类冲压印发现后必须立即对冲压件进行冻结B类缺陷:能看到、摸到,在有争议的地方打磨后也能证明,此类缺陷在Ⅲ、Ⅳ区可以接受。
C类缺陷:用油石打磨后能看出,此类缺陷的冲压件可以接受。
6.3.13材料缺陷6.3.13.1检验方法:目视6.3.13.2评价准则:A类缺陷:材料强度不符合要求,轧钢板留下的痕迹、重叠、桔皮、有条纹、镀锌表面疏松、镀锌层剥落。
此类冲压印发现后必须立即对冲压件进行冻结。
B类缺陷:轧钢板留下的,明显的痕迹、重叠、桔皮、有条纹、镀锌表面疏松、镀锌层剥落的材料缺陷,此类缺陷在Ⅳ区可以接受。
C类缺陷:轧钢板留下的模菱两可的痕迹、重叠、桔皮、有条纹、镀锌表面疏松、镀锌层剥落的材料缺陷此类缺陷Ⅲ、Ⅳ区可接受。
6.3.14油花纹6.3.14.1检验方法:目视、油石打磨6.3.14.2评价准则:Ⅰ、Ⅱ区经油石打磨后不允许存在明显得印痕。
6.3.15凸点、凹陷6.3.15.1检验方法:目视、触摸、油石打磨6.3.15.2评价准则:A类缺陷:是用户不能接收的缺陷,没有经过培训的用户也能注意到,A类凸点、凹陷发现后必须立即对冲压件进行冻结。
B类缺陷:是一种使人感到不愉快的缺陷,它是在冲压件外表面上摸得着和看得见的可确定的凸点、凹陷。
此类缺陷在Ⅳ区可以接受。
C类缺陷:是需要修正的缺陷,这些凸点、凹陷多数处于模棱两可的情况下,只有在油石打磨后才看得出。
此类缺陷Ⅱ、Ⅲ、Ⅳ区可接受。
6.3.16锈蚀6.3.16.1检验方法:目视6.3.16.2评价准则:冲压件不允许有任何程度锈蚀。
6.3.17冲压印:6.3.17.1检验方法:目视6.3.17.2评价准则:A类缺陷:是用户不能接收的,没有经过培训的用户也能注意到的冲压印,此类冲压印发现后必须立即对冲压件进行冻结。
B类缺陷:是一种使人感到不愉快的,是在冲压件外表面上摸得着和看得见的可确定的冲压印。
此类缺陷在Ⅰ、Ⅱ区是不允许存在的,在Ⅲ、Ⅳ区不影响整车质量的情况下,可以接受。
C类缺陷:需用油石打磨才能确定的冲压印。
此类缺陷的冲压件在不影响整车质量的情况下可以接受。
7 评审和更改质量保证部至少每年一次对本准则的有效性和适用性进行评审,必要时进行修改并再次批准。
8 相关文件《整车审核工作指导书》9 记录无10 附件附件1 冲压缺陷评价参考表附件1冲压缺陷评价参考表任何冲压零件不得存在A类缺陷,不得存在漏冲孔、锈蚀在Ⅰ、Ⅱ区不允许存在明显的油花纹以下区域的缺陷不允许存在:序号区域缺陷模式Ⅰ区Ⅱ区(外部)Ⅱ区(内部)Ⅲ区Ⅳ区1 开裂A、B、C A、B、C A、B、C** A、B、C**A、B**、C**2 拉伤、晶粒粗大、暗伤A、B、C A、B、C A、B A、B A3 瘪塘A、B A、B A、B A A4 波浪A、B A、B A、B A A5 翻边、切边不平、缺料A、B A、B A、B A A6 毛刺A、B A、B A、B A A7 拉毛、划伤A、B、C A、B、C A、B A、B A8 起皱A、B、C A、B A、B A A9 麻点、麻点群、压痕A、B、C*A、B A、B A A10 打磨印A、B A、B A、B A A11 材料缺陷A、B A、B A、B A A12 凸点、凹陷A、B A、B A、B*A、B* A13 冲压印A、B A、B A、B A A14 回弹A、B A、B A、B A A**需作补焊处理,但返修部位是不易察觉的,不影响整车功能的地方。