moldflow模流分析报告
模流分析(MOLDFLOW)

一. 压力條件对产品的影响1.高保压压力能夠降低產品收縮的機會补充入模穴的塑料越多,越可避免產品的收縮高保压压力通常會造成产品不均勻收縮,而导致產品的翹曲变形对薄殼產品而言,由於壓力降更明顯,上述之情況更加嚴重2.Over packing 過保壓保壓壓力高,澆口附近體積收縮量少遠離澆口處保壓壓力低且體積收縮量較大導致產品翹曲變形,產品中央向四周推擠形成半球形(Dome Shape)3. Under packing 保壓不足澆口附近壓力低遠離澆口處壓力更低導致產品翹曲變形,產品中央向四周拉扯形成馬鞍形Twisted shape保壓時間如果夠長,足夠使澆口凝固,則可降低體積收縮的機會澆口凝固後,保壓效果就無效果一、澆口位置的要求:1.外观要求(浇口痕跡, 熔接线)2.產品功能要求3.模具加工要求4.產品的翹曲变形5.澆口容不容易去除二、对生产和功能的影响:1.流長(Flow Length)決定射出壓力,鎖模力,以及產品填不填的滿流長縮短可降低射出壓力及鎖模力2.澆口位置會影響保壓壓力保壓壓力大小保壓壓力是否平衡將澆口遠離產品未來受力位置(如軸承處)以避免殘留應力澆口位置必須考慮排氣,以避免積風發生不要將澆口放在產品較弱处或嵌入处,以避免偏位(Core Shaft)三、选择浇口位置的技巧1.將澆口放置於產品最厚處,從最厚處進澆可提供較佳的充填及保壓效果。
如果保壓不足,較薄的區域會比較厚的區域更快凝固避免將澆口放在厚度突然變化處,以避免遲滯現象或是短射的發生2.可能的話,從產品中央進澆將澆口放置於產品中央可提供等長的流長流長的大小會影響所需的射出壓力中央進澆使得各個方向的保壓壓力均勻,可避免不均勻的體積收縮射出量/切换点的影响射出量可由螺杆行程距离的設定決定射出量包括了填滿模穴需要的塑胶量以及保压時須填入模穴的塑膠量切換點是射出機由速度控制切換成壓力控制的點螺桿前进行程過短(切換點過早)會導致保壓壓力不足假如保压压力比所需射出壓力還低,產品可能发生短射PVT特性p –压力; v –比容; T –溫度描述塑胶如何随着压力及溫度的变化而发生体积上的变化。
MoldFlow软件流动分析报告及应

MoldFlow软件流动分析及应用(2008/06/27 20:52)一、引言对于任何注塑成型来说,最重要的是控制塑料在模具中的流动方式。
制品的许多缺陷,如气穴、熔接痕、短射乃至制品的变形、冷却时间等,都与树脂在模具中的流动方式有关。
MPI/Flow通过对熔体在模具中的流动行为进行模拟,可以预测和显示熔体流动前沿的推进方式、填充过程中的压力和温度变化、气穴和熔接痕的位置等,帮助工艺人员在试模前对可能出现的缺陷进行预测,找出缺陷产生的原因并加以改进,提高一次试模的成功率。
二、MPI/Flow的作用MPI/Flow能够对注塑成型从制品设计、模具设计到成型工艺提供全面和并行的解决方案。
1、制品设计制品设计者能用MPI/Flow解决以下问题。
(1) 制品能否充满。
这一古老的问题一直为许多设计人员所关注,特别是对于大型制品。
(2) 制品最小壁厚。
在满足制品使用性能和工艺性能的前提下,减小制品壁厚能够大大降低制件的循环时间,从而提高生产效率,降低制件成本。
(3) 制品工艺性能。
在产品设计阶段具有充分的选择浇口位置的余地,确保制品的审美特性。
2、模具设计MPI/Flow能在以下方面辅助模具设计人员,以得到良好的模具设计。
(1) 确保良好的填充形式。
(2) 最佳的浇口位置与数量、类型以及正确地确定阀浇口的开启与闭合时间,有效地发挥阀浇口的作用。
特别是对于有纤维增强的树脂的填充过程,通过分析纤维在流动过程中的取向来判断其对制品强度的影响,并据此判断浇口位置设置的正确与否。
(3) 流道系统的优化设计。
通过流动分析,帮助模具设计人员设计出压力平衡、温度平衡或者压力、温度均平衡的流道系统,并最大程度地减少流道部分的体积。
同时,对流道内熔体的剪切速率和摩擦热进行评估,避免材料的降解和型腔内过高的熔体温度。
3、成型工艺注塑成型者可利用MPI/Flow在以下方面得到帮助。
(1) 通过对熔体温度、模具温度、注射时间等主要注塑加工参数对制品工艺性能提出一个目标趋势,从而帮助注塑成型者确定各个加工参数的正确值并确定其可变化范围,得到更加稳定的成型工艺条件。
(完整版)MOLDFLOW分析报告

引言概述:MOLDFLOW分析是一种重要的工具,广泛应用于塑料制品设计和生产过程中。
它可以提供关于模具充填、冷却和固化的详细信息,帮助设计师优化模具设计,提高产品质量和生产效率。
本文将通过分析报告的方式,详细介绍MOLDFLOW分析的应用和意义。
正文内容:一、模具充填分析1. 熔体流动模拟:对熔体在模具中的流动进行模拟,可以分析熔体的充填情况、充填时间和充填压力等参数,以及可能出现的缺陷,如短充、气泡等。
2. 塑料充填模拟:通过模拟塑料在模具中的充填过程,可以评估模具的设计是否合理,以及可能存在的充填不良、厚薄不均等问题。
3. 充填时间分析:根据模具充填模拟的结果,可以计算出塑料充填的时间,从而优化生产周期和工艺参数。
二、冷却系统分析1. 冷却效果模拟:通过模拟冷却系统的布局和工艺参数,在模具充填结束后,对模具进行冷却效果的分析。
可以评估冷却系统的设计是否合理,以及可能存在的冷却不均、温度过高等问题。
2. 温度分布模拟:根据冷却系统分析结果,可以计算出模具内部的温度分布,帮助优化冷却系统的设计和工艺参数。
3. 冷却时间分析:根据冷却系统模拟的结果,可以计算出模具冷却的时间,从而优化生产周期和工艺参数。
三、固化模拟分析1. 熔体固化分析:通过模拟塑料在模具中的固化过程,可以评估模具冷却效果和固化时间,避免可能出现的缺陷,如收缩、变形等。
2. 温度变化分析:根据固化模拟分析结果,可以计算出模具内部的温度变化曲线,帮助优化冷却系统和固化参数的设计。
3. 固化时间分析:根据固化模拟分析的结果,可以计算出模具固化的时间,从而优化生产周期和工艺参数。
四、缺陷分析1. 模具缺陷预测:通过模拟模具充填、冷却和固化的过程,可以预测可能出现的缺陷,如短充、气泡、收缩等,并给出相应的解决方案。
2. 缺陷修复优化:根据缺陷分析结果,可以优化模具设计和工艺参数,减少缺陷的发生,并提高产品质量和生产效率。
五、效果验证与总结1. 效果验证:通过对MOLDFLOW分析结果与实际生产产品进行对比,验证分析的准确性和可靠性,并修正和改进分析模型。
Moldflow模流分析报告

Moldflow模流分析报告→↓←↓1.网格划分(如右图)节点3880柱体0连通区域 1网格体积269.066 cm^3网格面积1874.25 cm^2 边详细信息----------------------------------- 自由边0共用边11634交叉边0配向详细信息--------------------------------- 配向不正确的单元0相交详细信息---------------------------------完全重叠单元0复制柱体0三角形纵横比--------------------------------- 最小纵横比 1.161000最大纵横比14.951000平均纵横比 1.933000匹配百分比----------------------------------- 匹配百分比94.2%相互百分比91.5%2.最佳浇口的选定分析结果如下:流动正在使用存储的网格匹配和厚度数据匹配数据是使用最大球体算法计算的最大设计锁模力 = 5600.18 tonne 最大设计注射压力 = 144.00 MPa 建议的浇口位置有:靠近节点 = 31060由图看出最佳浇口选在底面蓝色部分,可信度较高,用侧浇口注射3.填充选择材料PP+40%talc)以及注塑机250t锁模力,以及250g当量注射量,螺杆直径42mm进行填充,分析结果如下:充填阶段结果摘要 :最大注射压力 (在 1.463 s) = 20.2729 MPa充填阶段结束的结果摘要 :充填结束时间 = 1.5034 s总重量(制品 + 流道) = 217.8620 g最大锁模力 - 在充填期间 = 33.6416 tonne制品的充填阶段结束的结果摘要 :制品总重量(不包括流道) = 217.8620 g体积温度 - 最大值 = 231.2270 C体积温度 - 第 95 个百分数 = 229.7820 C体积温度 - 第 5 个百分数 = 216.7120 C体积温度 - 最小值 = 209.1650 C体积温度 - 平均值 = 225.1160 C体积温度 - 标准差 = 3.7478 C剪切应力 - 最大值 = 0.2002 MPa 剪切应力 - 第 95 个百分数 = 0.0766 MPa 剪切应力 - 平均值 = 0.0444 MPa 剪切应力 - 标准差 = 0.0223 MPa冻结层因子 - 最大值 = 0.2441冻结层因子 - 第 95 个百分数 = 0.1954冻结层因子 - 第 5 个百分数 = 0.0464冻结层因子 - 最小值 = 0.0000冻结层因子 - 平均值 = 0.1267冻结层因子 - 标准差 = 0.0480剪切速率 - 最大值 = 7059.0698 1/s 剪切速率 - 第 95 个百分数 = 473.1520 1/s 剪切速率 - 平均值 = 158.8660 1/s 剪切速率 - 标准差 = 209.9460 1/s4.冷却分析分析结果如图:水道布置可从图中看出冷却介质温度进水口冷却介质温度冷却介质温度升高节点范围在回路上128 25.0 - 25.5 0.5 C288 25.0 - 26.3 1.3 C162 25.0 - 25.4 0.4 C426 25.0 - 25.6 0.6 C最后的回路温度残余: 0.00000E+00型腔温度结果摘要=====================================型腔表面温度 - 最大值 = 84.9090 C 型腔表面温度 - 最小值 = 31.8350 C 型腔表面温度 - 平均值 = 50.0860 C 平均模具外部温度 = 30.0670 C 循环时间 = 35.0000 s。
Moldflow模流分析报告

体积收缩示意图
从上图可以看出此产品的收缩趋势明显,并且收缩的一致性较差. 因此推荐采用较大的保压压力及较长的保压时间
气孔
可能出现的气孔位置如上图所示的紫色区域
熔接线
图上可能看出熔接线的位置,但深度不足以影响产品的机械性能
翘曲变形, 所有的方向
可能发生的翘曲变形如 右图所示 X方向的变形 此变形结果包括了收缩 变形 可以根据图上数值进行 判断
Back ground
1. 2. 3. 4. 5. 6. 7. 使用软件: Moldflow plastics insight 6.1. 网格类型: fusion(表面网格). 塑胶材料: Zytel EMX 505A (PA66+20%GF, DuPont Engineering Polymers (Moldflow Verified)). 分析序列: 冷却->填充->-饱和->变形. 分析目的: a). 预测成型缺陷 b)预测变形趋势.
由上表可以看出,此材料较容易充填,并且对温度的变化不敏感..
有限元模型分析
Entity counts-------------------------------Surface triangles 28290 Nodes Connectivity regions 7 Mesh volume 19.8781 cm^3 Mesh area 1549.36 cm^2
注塑参数设置(参考)
Temperature Settings -----------------------------------------------------------------------------Melt temperature: 280.0000 C Mold cavity_side temperature: 75.0000 C Mold core-side temperature: 75.0000 C -----------------------------------------------------------------------------Injection Settings -----------------------------------------------------------------------------Injection control method: Injection Time Injection Time: 1.5000 s Nominal Flow rate: 285.2910 cm^3/s Packing pressure profile Duration Pressure (s) (MPa) 0.0000 80.0000 5.0000 80.0000 1.9094 0.0000 Cooling time: 33.4732 s -----------------------------------------------------------------------------Results from Flow Analysis -----------------------------------------------------------------------------Total volume of the part and cold runners: 427.9370 cm^3 Switch-over Pressure: 53.0071 MPa Maximum clamp force required: 164.9420 tonne
Moldflow模流分析报告范例

14
Shear Stress at Wall 最大剪切应力
流道系统上最大剪切应力: 2.8MPa 产品上最大剪切应力:0.4MPa
一般产品上的最大剪切应力,不要超过成型材料所允许的数值(如第8页所示, 该材料允许最大剪切应力为0.5MPa )。剪切应力太大,产品易开裂。
通过加大最大剪切应处壁厚,降低注塑速度,采用低粘度的材料,提高料温,可 减小剪切速率。
一般,脱模时相邻区域的体积收缩值相差>2%,产品表面易出现缩水。
可通过优化产品壁厚、浇口放置在壁厚区域、加大保压等措施,来降低 体积收缩。
DESIGN SOLUTIONS
18
Frozen Layer Fraction 凝固层因子
6.3s 12.2s 30.9s
Frozen Layer Fraction反映的是产品的凝固顺序。该产品在6.3秒时,红色区 域已凝固,导致安装孔位保压不足,故体积收缩较大,易出现表面缩水。 当产品100%凝固,冷流道系统凝固50%以上。产品可脱模。从而确定该产 品成型周期31s(不包括开合模时间)。 可通过优化冷却水路排布、降低局部壁厚区域的厚度、优化冷流道尺寸,来 缩短成型周期。
DESIGN SOLUTIONS
19
Sink Mark Estimate 凹痕深度
一般,凹痕数值>0.03mm,表面缩水较明显。 可通过加大基本壁厚、减小加强筋和螺栓柱等壁厚、加大保压等方式,来降 低凹痕深度。
DESIGN SOLUTIONS
20
Sink Mark Shaded 凹痕阴影显示
阴影显示凹痕的分析结果。圈示区域,肉眼看起来较明显。
22
Temperature, Part 冷却结束时产品表面温度
Moldflow模流分析报告

Page 9
Moldflow Analysis Report
Original1
原始方案分析結果
以下解析的包括冷卻、充填、保壓、翹曲分析的較爲重要的結果。
Page 10
Moldflow Analysis Report
冷卻水溫變化
Original1
由圖中可知,水溫升高較小 (進出口水溫差在兩度以 内),冷卻水路的長度設計 是可以達成冷卻要求的。成 型時不要爲了省事而將水路 串聯起來,否則會導致水路 過長水溫持續升高而降低冷 卻效果。
Original1
從圖中可知,公母模側 表面溫差較大,會使產 品公母模側收縮不均一 而導致翹曲變形問題。
Page 13
Moldflow Analysis Report
產品凝固需要的時間
Original1
上面兩圖表示的是從循環周期開始到產品完全凝固所需要的時 間。開模時圈示的幾個區域仍未凝固(如右圖,大部分區域在 16s内就可以凝固),而最長凝固時間竟達80s左右(也正是產 品上最厚的區域),故必將有嚴重縮水發生。
Page 14
Moldflow Analysis Report
充填時間(點擊Filபைடு நூலகம் time圖面即可播放動畫)
Original1
充填時間約為2.2秒,充填流動不太平衡。箭頭指示處為最後充填區域。圈示處的薄肋發 生嚴重滯流現象,導致產品短射。歸因於此肋太薄(僅0.9mm左右),而澆口又距離此肋 太近,塑膠流動到該處時受到極大阻力而停滯不前並迅速凝固了。實際試模中用GE PPE +PS+40%GF的塑膠可能勉強填滿,但成型窗口很窄,仍可能短射,對此應高度重視。
Original1
原始方案冷卻系統設計
MOLDFLOW模流分析报告结果解释

MOLDFLOW模流分析结果解释解释结果的一个重要部分是理解结果的定义,并知道怎样使用结果。
下面将列出常用结果的定义及怎样使用它们的建议,越常用的结果将越先介绍。
屏幕输出文件(screen output)和结果概要(results summary)屏幕输出文件和结果概要都包含了一些分析的关键结果的总结性信息。
屏幕输出文件还包含如图169所示的附加输出,表明分析正在进行,同时还提供重要信息。
从它可以看出分析使用的压力和锁模力的大小、流率的大小和使用的控制类型。
图169. 充模分析的屏幕输出文件屏幕输出文件和结果概要都有与图170相似的部分。
它同时包含了分析过程中(第一部分)和分析结束时的关键信息。
使用这些信息可以快速查看这些变量,从而判断是否需要详细分析某一结果,以发现问题。
图170. 结果概要输出充模时间(Fill Time)充模时间显示的是熔体流动前沿的扩展情况,其默认绘制方式是阴影图,但使用云纹图可更容易解释结果。
云纹线的间距应该相同,这表明熔体流动前沿的速度相等。
制件的填充应该平衡。
当制件平衡充模时,制件的各个远端在同一时刻充满。
对大多数分析,充模时间是一个非常重要的关键结果。
压力(Pressures)有几种不同的压力图,每种以不同的方式显示制件的压力分布。
所有压力图显示的都是制件某个位置(一个节点)、或某一时刻的压力。
使用的最大压力应低于注射机的压力极限,很多注射机的压力极限为140 MPa (~20,000 psi)。
模具的设计压力极限最好为100 MPa (~14,500 psi)左右。
如果所用注塑机的压力极限高于140MPa,则设计极限可相应增大。
模具的设计压力极限应大约为注射机极限的70%。
假如分析没有包括浇注系统,设计压力极限应为注射机极限的50%。
象充模时间一样,压力分布也应该平衡。
压力图和充模时间图看起来应该十分相似,如果相似,则充模时制件内就只有很少或没有潜流。
具体的压力结果定义如下:∙压力(Pressure)压力是一个中间结果,每一个节点在分析时间内的每一时刻的压力值都记录了下来。
Moldflow模流分析报告

Original2在相同區域發生較嚴重的滯流現象,該處塑膠熔接性极差。大 部分縫合綫熔接溫度較高,應不會影響其使用強度。局部區域包風包在 塑膠内難以排除,可能會受高壓急劇升溫而燒焦產品。注入口尺寸太小 ,冷卻太快,成品將得不到有效保壓而發生縮水,有可見凹陷出現,而 試模時用105MPa的壓力持續保壓了5s之久,其實此時注入口早已凝固, 再加額外的壓力只能使產品出現負收縮(即膨脹),導致拉模現象。澆口設 計得太薄,凝固太快,即使注入口不先行凝固,產品也會有較嚴重的保 壓不良現象。另外循環周期過長,造成生産成本的浪費。
3. 產品模型介紹
-------------------------------------------------------------------------- 5
4. 原始方案澆注系統設計
-------------------------------------------------------------------------- 6
13. 最終改善方案基本成型條件 ----------------------------------------------------------------------- 29
14. 最終改善方案分析結果 --------------------------------------------------------------------30~43
冷卻凝固過程
Original2
這六個圖表示的是產品和流道的冷卻凝固過程,紅色區域表示最先凝固的區域,一般最薄處最先凝固。從 圖三可知,注入口已先行凝固(箭頭指示處),而此時產品大部分都沒凝固,説明注入口尺寸太小,成品將 得不到有效保壓而發生縮水現象。此外分析中也發現澆口亦太薄,凝固太快。
Moldflow模流分析报告样本
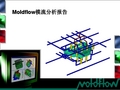
18.结论与建议 3
------------------------------------------------------------------------- 3 -------------------------------------------------------------------------- 4 -------------------------------------------------------------------------- 5 -------------------------------------------------------------------------- 6 -------------------------------------------------------------------------- 7 -------------------------------------------------------------------------- 8 -------------------------------------------------------------------------- 9 -------------------------------------------------------------------- 10~30 ------------------------------------------------------------------------ 31 ------------------------------------------------------------------------ 32 11. 12. 13. 14. ------------------------------------------------------------------------ 56 ------------------------------------------------------------------------ 57 14. 15. 16. 17. ------------------------------------------------------------------------ 81
MOLDFLOW模流分析报告
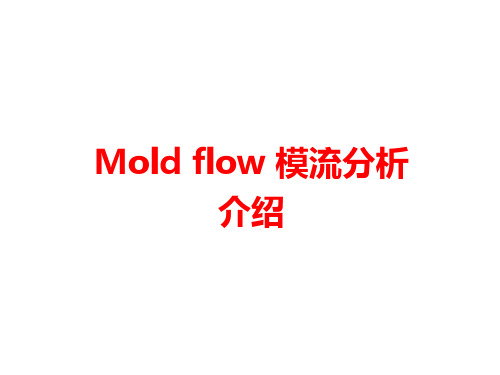
STEP 10-选择分析类型
填充
快速填充
流动 冷却 成型窗口 最佳浇口位置 流道平衡 冷却+流动+翘曲 流动+收缩 冷却+流动+收缩
常用分析类型
分析熔融塑胶在注塑段的填充行为 快速模拟熔融塑胶在注塑段的填充行为,分析的输出结果较正常 填充少 分析熔融塑胶在注塑段的填充行为和保压效果 分析保压结束后,运水管道的冷切效果 提供最佳成型参数和合理的成型工艺参数 产品上最佳进浇位置和产品上不同区域作为进浇口的合理性程度 从填充平衡的角度优化流道的尺寸 完整的模拟分析产品的成型过程和翘曲 分析熔融塑胶在型腔内的流动以及产品的收缩情况 分析熔融塑胶的流动和冷却管道的冷却效果得出产品收缩值
Mold flow 模流分析 介绍
珠海优特电力科技股份有限公司
引子
我们遇到了哪些问题?
2
引子
短射
3
引子
飞边
4
引子
银条纹
5
引子
流痕
6
引子
应力痕
7
引子
冲击纹
8
引子
缩水
9
引子
熔接痕
10
引子
发脆
11
引子
翘曲
12
引子
预避知 如何改变传统的依靠经验的
“试错”的设计模式?
13
目录
1 MOLDFLOW简介 23 MOLDFLOW分析流程介绍 43 产品缺陷判定及优化对策
MOLDFLOW简介
优化制品形 状和结构
优化模具结构
优化注塑工艺 参数
18
MOLDFLOW简介 功能1
最佳浇口位置分析
根据塑件的形状结构,分析出最佳的胶口位置。
Moldflow模流分析经典报告(简体版)幻灯片
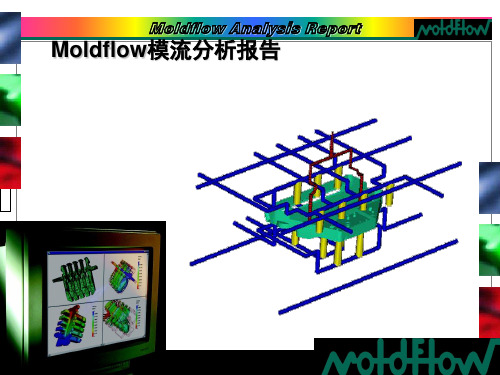
Moldflow Analysis Report 原始方案基本成型条件
注射机设定:
保压曲线:
Machine maximum clamp force: 350 tonne Maximum pressure:216.00 MPa Maximum injection speed:422.52 cm^3/s Screw diameter:58.00 mm
Moldflow Analysis Report
Moldflow模流分析报告
Page 1
Moldflow Analysis Report 内容提要
1.分析说明一 2.塑料材料简介 3.产品模型简介 4.分析模型简介 5.原始方案浇注系统设计 6.原始方案冷却系统设计 7.原始方案基本成型条件 8.原始方案分析结果 9. 结论与建议 1 10.分析说明二 11.改善方案1浇注系统设计 12.改善方案1冷却系统设计 13.改善方案1基本成型条件 14.改善方案1分析结果 15.结论与建议 2 16.分析说明三 14.改善方案2浇注系统设计 15.改善方案2冷却系统设计 16.改善方案2基本成型条件 17.改善方案2分析结果 18.结论与建议 3
0
4.0
29.5t(s)
PRESSURE [%HP] STEP DURATION [sec]
Part Weight(Solid) :349g
28.0
0.0
Total projected area :390.4 cm^2
28.0
4.0
冷却条件:
0.0
0.0
0.0
25.5
Coolant Temperature(Cavity)60 deg.C
Page 13
Moldflow Analysis Report 产品凝固需要的时间
Moldflow模流分析经典报告(简体版)
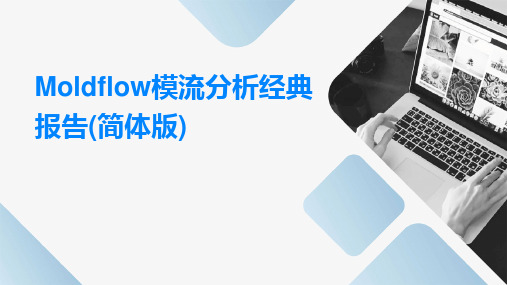
设置注射压力、注射速度、注射温度等边界条件。
塑化边界条件
设置塑化温度、塑化速度等边界条件。
模拟求解与结果分析
模拟求解
根据设置的边界条件进行模拟求解。
结果分析
对模拟结果进行分析,如压力分布、温度分布、流动行为等。
结果优化
根据分析结果对模型进行优化,提高成型质量和效率。
Moldflow模流分析
Moldflow模流分析是一种计算机模 拟技术,用于预测塑料模具填充、流 动、冷却和翘曲等行为,从而优化模 具设计和产品成型过程。
通过模拟分析,Moldflow可以帮助工 程师预测和解决模具制造和塑料产品 成型过程中可能出现的问题,减少试 模次数和缩短产品上市时间。
Moldflow模流分析的重要性
2. 翘曲变形分析不准确
翘曲变形是塑料成型过程中的常见问题,分析不准确可能导致模具优化措施失效。
3. 解决方案
加强Moldflow模流分析理论学习,深入理解流动前沿、翘曲变形等关键指标的含义和影 响。结合实际案例进行分析和总结,提高模拟结果解读能力。积极参与行业交流和技术培 训,不断更新知识和技能。
Moldflow模流分析的应用领域
汽车行业
01
Moldflow在汽车行业中广泛应用于汽车零部件的模具设计和产
品成型过程优化,如保险杠、仪表盘和座椅等。
电子产品
02
Moldflow模流分析可用于手机、电视、电脑等电子产品的模具
设计和产品成型过程优化。
包装行业
03
Moldflow可以帮助包装企业优化包装盒、瓶盖等产品的模具设
案例三:热流道系统模拟
总结词
热流道系统是塑料加工中常用的技术,通过加热模具流道来控制塑料熔体的温度和流动。 Moldflow模流分析可以用于热流道系统的模拟和优化。
(完整版)MOLDFLOW分析报告

Moldflow Analysis Report 塑料材料簡介
PPE+PS+40%GF Xyron X1764 Asahi Kasei Corporation
1. Melt Density 1.2827 g/cu.cm 2. Solid Density 1.3645 g/cu.cm 3. Ejection Temperature 110.000000 deg.C 4. Recommended Mold Temperature 75 deg.C 5. Recommended Melt Temperature 275 deg.C 6. Absolute Max. Melt Temperature 340 deg.C
Moldflow Analysis Report
Moldflow模流分析報告
B039பைடு நூலகம்901
Page 1
Moldflow Analysis Report 内容提要
1. 分析说明一 2. 塑料材料简介 3. 产品模型简介 4. 分析模型简介 5. 原始方案浇注系统设计 6. 原始方案冷却系统设计 7. 原始方案基本成型条件 8. 原始方案分析结果 9. 结论与建议 1 10.分析说明二 11.改善方案1浇注系统设计 12.改善方案1冷却系统设计 13.改善方案1基本成型条件 14.改善方案1分析结果 15.结论与建议 2 16.分析说明三 14.改善方案2浇注系统设计 15.改善方案2冷却系统设计 16.改善方案2基本成型条件 17.改善方案2分析结果 18.结论与建议 3
Page 2
Moldflow Analysis Report 分析说明一
➢如下图的产品,为复印机上的零件,对尺寸精度要求较高。采用PPE+PS+40%GF的塑 料以热流道成型,产品结构与进浇位置均已确定,客户希望通过调整冷却水路或冷却条件 将整个周期时间缩短,因此藉以Moldflow模流分析验证是否可行。 ➢因Moldflow材料数据库内暂无客户使用的GE PPE+PS+40%GF塑料,故在分析中使用 物性较为相似的Asahi Kasei Corporation的PPE+PS+40%GF塑料来代替,在数值上会与 实际试模有差异,但趋势是一致的。此报告中以几种方案进行分析比较,其中Original n 为客户原始设计方案,Revised n为我们基于Moldflow上的改善方案。
面板件完整Moldflow分析报告

deg.C
deg.C 粘度曲线
PVT曲线
221.01X54.84X30.81mm,大部分肉厚在
(双层网格)或Midplane 分析,分析结果基本一致。
下图为双层网格,外表形状与3D产品模
型基本相同,处理时间较中间层网格短,但网格数是它的两倍以上,分析时间较长。
中间
冷却系統設計
方案共设计11条水路,其中脱料板2条水路,前模3条水路,行位2条水路能及后模4条水路,水路大小10mm
Moldflow Analysis Report Analysis Report
M oldflow Analysis Report Analysis Report
填时间:
冷却水温变化在2度内,非常合
左圖表示產品充填末端平均
考量冷却系统),從圖中可知,产品大部分温度在230度左右。
左圖表示的是從循環周期開始到產品完全凝固所需要的時間。
大部分區域在7.21s
变形量:
Moldflow Analysis Report Analysis Report
Page 31。
moldflow 注塑成型分析 模流分析报告

产品变形-分子定向因素
尾部分子剪切作用较高 ,故而分子取向度高并 且分子结晶度高(取向 诱导结晶),在取向方 向上收缩较大,故而收 缩应力导致产品尾部收 拉力而张开变形。 两头的张开变形又直接 导致中间凹陷下去。
Page 19
Thank You!
Page 20
Page 13
总体变形趋势
左侧结果显示了产品的变形趋 势。产品主要的变形位于产品 头部。
Page 14
X向变形趋势
产品X方向变形均匀。
Page 15
Y向变形趋势
圈示位置向外张开变形。
Page 16
Z向变形趋势
产品Z向在圈示位置 向下凹陷变形。
Page 17
产品变形-分子定向因素
之所以出现产品Y向圈 示向外张开及Z向在圈 示位置向下凹陷变形 ,是由分子取向因素 引起的,见右图。
持续时间 [sec] 6 8
Page 4
产品充填平衡性
产品填充样式,显示了胶料填 充产品的动态过程。红色代表最 后充填的位置,蓝色代表最早充 填的区域。
该结果可以帮助用户了解产品 充填的过程,判断产品填充过程 是否顺畅和平衡,从而判断产品 填充质量,判断是否有迟滞、短 射等问题。从而确定产品结构以 及浇口或流道的设计合理性。
从压力分布色图上可以看出, 产品两侧的压力分布不均匀。 较早完成充填的区域处于过 保压状态。压力不均匀易导 致使得产品收缩不均匀,进 而容易引起翘曲变形。
调整浇口位置,可使得产品 内部压力分布均匀一致。
Page 7
产品充填平衡性-波前温度
该结果显示了产品填充结 束时,料峰温度分布情况。温 度降低过大容易导致产品短射 ,温度升高过大容易导致产品 出现烧焦或黑斑等表面质量缺 陷。外观区域温度差异应保证 在10℃之内。 从结果可以看出,产品大部分 温度差异性较低,但在圈示位 置温度较低,有10℃的温降。 注意采用较快的充填速度。
- 1、下载文档前请自行甄别文档内容的完整性,平台不提供额外的编辑、内容补充、找答案等附加服务。
- 2、"仅部分预览"的文档,不可在线预览部分如存在完整性等问题,可反馈申请退款(可完整预览的文档不适用该条件!)。
- 3、如文档侵犯您的权益,请联系客服反馈,我们会尽快为您处理(人工客服工作时间:9:00-18:30)。
材料成型CAE论文(Moldflow注塑工艺分析)
姓名:郭玲玲
学号:20060330332
在Moldflow Plastic Insight 6.0环境中,运用MPI的各项菜单及其基本操作,来实现对所选制件在注塑成型过程中的填充、流动、冷却以及翘曲分析,以此来确定制件的最佳成型工艺方案,为工程实际生产提供合理的工艺设置依据,减少因工艺引起的制件缺陷,有助于降低实际生产成本,提高生产效率。
一、导入零件
导入文件guolingling.stp。
选择【Fusion】方式。
二、划分网格
【网格】—【生成网格】—【立即划分】
三、网格诊断
【网格】—【网格诊断】,诊断结果如下:
图1、网格诊断
对诊断结果进行检查,发现连通区域为1,交叉边为0,最大纵横比为7.218616<8,均符合要求,网格划分合理。
四、选择分析类型
1、浇口位置
1)双击任务栏下的【充填】—【浇口位置】;
2)选择材料:双击任务栏下的【材料……】—【搜索】—输入“ABS”
—搜索—在结果中任选一种材料,点击【选择】即可;
3)双击任务栏下的【立即分析】。
在分析结果中勾选:Best gate location,查看最佳浇口位置,如下图:
图2、最佳浇口
由最佳浇口位置分析结果可以知道,浇口设在零件上表面的中间
部位,零件的注塑工艺效果好。
可采用直接浇口。
2、流动分析
1)设置注射位置:设置之前,先将方案备份。
【文件】—【另存方案为】。
双击任务栏下的【设置注射位置】—鼠标变成一个十字光标和一漏
斗形状,然后在上一步分析中的最佳浇口位置处单击,即可完成注
射点的设置;
2)选择分析类型:双击任务栏下【浇口位置】—【流动】;
3)设置浇注系统:【建模】—【浇注系统向导】,设定直浇道、横浇道、
内浇道的尺寸,各浇道尺寸均采取的默认值。
根据制件的形状特征
以及最佳浇口位置,采用直接浇口。
4)双击任务栏下的【立即分析】。
查看分析结果中的“pressure at V/P swithover”项,发现出现了浇不足的现象,经分析是由于注射压力过小所引起的,只需增大注射压力即可。
在【工艺条件设置】中将【注射压力】增大到250MPa,进行流动分析,其结果如下
图3、填充时间
在填充时间的结果图示中,浇口两侧方向上的填充时间在0.5s~1.1s 内变化,相差的时间0.6s,基本可以接受。
图4、填充/保压转换点压力
上图为填充/保压转换点压力。
之前采用默认注射压力120MPa,可以发现零件的下部有未填满缺陷,增大注射压力之后,零件完全被填充满了。
图5、流动前沿温度
图示为流动前沿温度。
合理的温度分布应该是均匀的,即这个模型的温差不能太大。
本模型的温度最大最小差值为1.0℃,温度的差异不大,符合要求。
图6、气穴位置
图示为气穴位置。
气穴的数量稍微有些多,但是均位于分型面和零件的下端,气体很容易从模腔中排出。
不会造成制件出现气泡、焦痕等缺陷。
说明浇口位置设置合理。
图7、锁模力
图示为锁模力随时间的变化。
由此可以看出压力机提供的锁模力不能低于图示锁模力的上限值,选择压力机时应该注意锁模力的大小。
3、冷却分析
1)选择分析类型:选择类型之前先将方案备案:【文件】—【另存方案
为】;然后双击任务栏下【流动】,选择【冷却】,【确定】。
2)设置冷却水道:【建模】—【冷却系统向导】,通过此向导具体的设
置如下:冷却水管的直径:6
水管与产品之间的距离15
水管相对于产品的排列方向:沿X轴向
水管的条数:2
水管的间距:70
超出产品边界的距离:20
参数设置完成后,单击【完成】系统便自动生成所需的水管;
3)立即分析:双击任务篮下的【立即分析】。
冷却分析结果如下:
图8、制件平均温度
图示为制件平均温度结果图。
该结果的最大最小温度之间的差异应尽量小,即温度分布应当均匀。
此温差为:44.08℃-34.08℃=10℃,温差较小,符合要求。
图9、冷却剂温度
图示为冷却剂温度结果图。
冷却剂的入口和出口温度应当控制在2℃~3℃之内,如果超出了这个值,则应当通过增大冷却管道直径、降低冷却剂温度或者修改冷却系统布局的方法进行改善。
在本模型中,由于零件太小,冷却剂的温度差值很小。
冷却系统参数默认值设置情况下,得到的冷却剂温差只有0.1℃。
经分析,将冷却水管的直径改为最小值6,产品的距离和水管条数均改小,将水管间距拉大,经分析得到上图所示的温度差:25.34℃-25.01℃=0.3℃。
图10、冷却管道管壁温度
图示为冷却管道管壁温度结果。
冷却管道管壁温度为27.11℃。
图11、制件冷却时间
图示为制件冷却时间结果图。
冷却时间最长为4.649s,最短的为
3.414s,冷却时间的差值为
4.649s-3.414s=1.235s,差值较小,基本
可以认为制件是均匀冷却的。
图12、流道冷却时间
图示为流道冷却时间结果,制件的冷却程度结合冷流到的冷却程度关系到制件是否能被顶出。
由图示可知流道冷却时间为46.08s。
4、翘曲分析
1)选择分析类型:将方案备份。
双击任务栏下【冷却】,选择【流动+
冷却+翘曲】;
2)立即分析:双击任务栏下【继续分析】。
分析结果如下:
图13、综合因素引起的总体偏差
图示为制件整体上的翘曲情况,该制件存在轻微的翘曲变形,原因可能是冷却剂的温度差太小,制件的温度差异偏大引起翘曲。
以下是制件分别在X、Y、Z三个方向上的翘曲情况。
图14、综合因素引起的X方向上的偏差
图15、综合因素引起的Y方向上的偏差
图16、综合因素引起的Z方向上的偏差五、总结
该零件的结构形状相对较简单,其注塑成型工艺也相对较简单,运动Moldflow软件进行填充、流动、冷却和翘曲分析,其中填充分析可以确定制件的最佳浇口位置,进而辅助设计最佳浇注系统;流动分析可以帮助我们获得最佳保压阶段设置,从而尽可能的降低由保压引起的制品收缩、翘曲等质量缺陷;而通过冷却分析的结果可以用来判断制件冷却效果的好坏,根据冷却效果还可以计算出冷却时间的长短,确定成型周期所用时间;而翘曲分析则是为了进一步检查制件最终成形后的尺寸合格情况,通过各个方向上的偏差,来检查前面的流动、冷却条件设置的合理程度。
在使用软件进行分析的过程中,遇到两个大问题:
(一)流动分析
在流动过程分析中,第一次设置了浇注系统后,在分析结果图中发现零件的侧壁靠下部位有一部分没有填充,也即零件未填满。
检查浇口位置是在最佳浇口处,根据零件形状结构,浇注系统采用直接浇口合理,排除了浇注系统设置引起的浇不足,接着就从成型工艺设置上分析,发现系统默认的注射压力120MPa偏小,是制件填充不满,于是就将注射压力调整为200MPa,再进行分析,发现不存在浇不足的情况。
(二)冷却分析
在冷却分析过程中,第一次设置的冷却系统分析结果中,发现冷却剂的入口出口温度差过小,仅有0.1℃。
经过分析,冷却管道是用来冷却制件的温度,平衡制件以及模具型腔温度,实现均匀冷却,缩短制件成型周期,提高生产效率。
而冷却水道入口出口温差即反映了冷却系统的冷却效果,即冷却管道所吸收的热量情况。
要想使这个温差增大,需要使冷却管
道吸收更多的温度,也即可以使冷却管道更贴近制件表面,冷却管道的直径取的更小。
在对这一系列的条件不断修改中,将冷却剂进出口的温差变为了原来的3倍,提高到0.3℃。
鉴于对软件运用的熟练程度,以及对各个功能的作用了解深入,在解决了以上两个问题后,该制件的分析基本上顺利。
分析结果基本上还算合理。
但是,由于是找的零件,没有相关的技术和工艺要求,在分析过程中,由很多参数的设置都是采取的默认值。
在今后的课程设计以及毕业设计中,可以根据制件的材料,技术和工艺要求来对压流动冷却过程中的各个参数进行准确设定,更进一步完善制件的分析。