案例--螺纹轴加工
内螺纹车削加工——数控车床编程实例
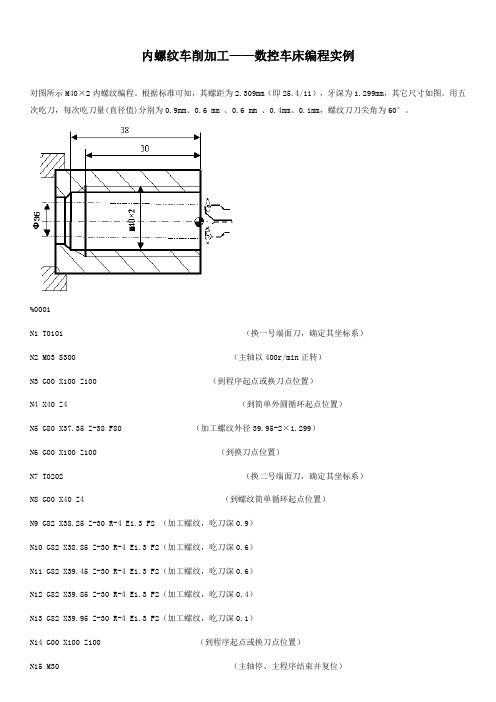
内螺纹车削加工——数控车床编程实例
对图所示M40×2内螺纹编程。
根据标准可知,其螺距为2.309mm(即25.4/11),牙深为1.299mm,其它尺寸如图。
用五次吃刀,每次吃刀量(直径值)分别为0.9mm、0.6 mm 、0.6 mm 、0.4mm、0.1mm,螺纹刀刀尖角为60°。
%0001
N1 T0101 (换一号端面刀,确定其坐标系)
N2 M03 S300 (主轴以400r/min正转)
N3 G00 X100 Z100 (到程序起点或换刀点位置)
N4 X40 Z4 (到简单外圆循环起点位置)
N5 G80 X37.35 Z-38 F80 (加工螺纹外径39.95-2×1.299)
N6 G00 X100 Z100 (到换刀点位置)
N7 T0202 (换二号端面刀,确定其坐标系)
N8 G00 X40 Z4 (到螺纹简单循环起点位置)
N9 G82 X38.25 Z-30 R-4 E1.3 F2 (加工螺纹,吃刀深0.9)
N10 G82 X38.85 Z-30 R-4 E1.3 F2(加工螺纹,吃刀深0.6)
N11 G82 X39.45 Z-30 R-4 E1.3 F2(加工螺纹,吃刀深0.6)
N12 G82 X39.85 Z-30 R-4 E1.3 F2(加工螺纹,吃刀深0.4)
N13 G82 X39.95 Z-30 R-4 E1.3 F2(加工螺纹,吃刀深0.1)
N14 G00 X100 Z100 (到程序起点或换刀点位置)
N15 M30 (主轴停、主程序结束并复位)。
数控车床编程实例大全

数控车床编程实例大全数控车床编程是数控加工中至关重要的环节,通过合理的编程,可以实现各种复杂形状零件的高精度加工。
以下为您呈现一些常见的数控车床编程实例,帮助您更好地理解和掌握这一技术。
一、简单轴类零件加工编程假设我们要加工一根直径为 50mm,长度为 100mm 的圆柱形轴,材料为 45 号钢。
程序如下:```O0001 (程序名)N10 G50 X150、 Z150、(设定坐标系)N20 G99 (每转进给)N30 M03 S800 (主轴正转,转速 800r/min)N40 T0101 (选择 1 号刀具,1 号刀补)N50 G00 X52、 Z2、(快速定位到加工起点)N60 G01 Z-100、 F02 (直线切削到轴的长度方向)N70 G00 X55、(快速退刀)N80 Z2、(快速退回到起点)N90 M05 (主轴停止)N100 M30 (程序结束)```在这个程序中,G50 用于设定坐标系,G99 表示每转进给,M03 启动主轴正转,S800 设定转速,T0101 选择刀具和刀补,G00 是快速定位指令,G01 为直线插补指令,F02 是进给速度。
二、阶梯轴加工编程现在要加工一个阶梯轴,大端直径 60mm,小端直径 40mm,长度分别为 80mm 和 50mm。
程序如下:```O0002N10 G50 X150、 Z150、N20 G99N30 M03 S1000N40 T0101N50 G00 X62、 Z2、N60 G01 Z-80、 F02N80 Z-130、N90 G00 X100、N100 Z100、N110 M05N120 M30```此程序中,通过逐步改变刀具的 X 坐标值,实现了阶梯轴的加工。
三、螺纹轴加工编程以加工一个 M30×2 的螺纹轴为例,长度为 100mm。
```O0003N10 G50 X150、 Z150、N20 G99N30 M03 S600N40 T0101N50 G00 X32、 Z2、N60 G92 X29、 Z-100、 F2、(螺纹切削循环)N80 X282N90 X2805N100 G00 X100、N110 Z100、N120 M05N130 M30```在这个程序中,G92 是螺纹切削循环指令,通过多次改变 X 坐标值来逐步切削螺纹。
钳工实训教程-螺纹工件加工

教学目标知识目标:了解加工螺纹所用工具种类与选用;掌握攻螺纹底孔直径和套螺纹圆杆直径的确定方法;熟悉丝锥折断和攻螺纹、套螺纹的废品产生原因和防止方法。
技能目标:掌握攻螺纹的操作方法;掌握套螺纹的操作方法。
教学重点掌握攻螺纹、套螺纹的操作方法。
教学难点掌握攻螺纹底孔直径和套螺纹圆杆直径的确定方法。
教学手段实物演示;教学板书;录像插件;电子课件。
教学学时14教学内容与教学过程设计注释螺纹工件加工螺纹加工分内螺纹加工和外螺纹加工。
用丝锥在工件孔中切削出内螺纹的加工方法称为攻螺纹;用板牙在圆柱面(或圆锥面)上切削外螺纹的加工方法为套螺纹。
任务一攻螺纹〖实训任务〗完成如图6-1所示工件的螺纹内孔加工。
图6-1攻螺纹工件图〖任务分析〗通过攻螺纹练习,掌握用丝锥加工内螺纹的方法。
〖任务准备〗(1)材料准备:100 mm×80 mm×20 mm钢板一块。
(2)工具准备:M6、M8及M10丝锥各一套, 5 mm、 6.7 mm、8.5 mm钻头各一支。
(3)量具准备:直尺、游标卡尺、M6、M8及M10螺纹塞规。
〖任务实施〗(1)按图划线。
(2)确定螺纹底孔直径。
(3)攻螺纹。
①攻螺纹前首先要钻孔,也称钻底孔。
②倒角。
③起攻。
④检查垂直度。
项目说明。
明确实训任务。
分析任务重点。
任务所需工具准备。
分步骤实施任务。
⑤正常攻螺纹时,两手用力要均匀,要经常反转1/4~1/2圈以断屑或清屑。
(4)检查。
螺纹塞规如图63所示,用来测量内螺纹的尺寸精度。
在测量螺纹时,如果量规过端正好拧进去,而止端拧不进,说明螺纹精度符合要求。
〖操作提示〗(1)端面孔口要倒角。
(2)开始攻螺纹时,要加轴向压力使丝锥切入工件,切入几圈以后就不需要加压了。
(3)手动攻螺纹时,当丝锥的校准部分已进入螺孔,每正转1/2~1圈要倒退1/4~1/2圈,使切屑碎断后再往下攻。
(4)在钢类工件上攻螺纹时需要加切削液;加工较硬的铸铁工件或螺孔粗糙度要求较高时,可以加煤油。
数控加工工艺及编程 项目3螺纹轴加工工具刀具选择

螺纹轴加工刀具和工具选择一、车刀选择外圆车刀选择原则与短轴加工时的外圆车刀相同用90度外圆车刀,这里就不在赘述。
分析该螺纹零件。
螺纹为M12的三角外螺纹,我选择三角形外螺纹车刀,刀尖角60度。
割槽刀选用3mm宽的外割槽刀。
二、螺纹车刀特点螺纹车刀是成形刀具,其切削部分的形状应和螺纹牙型轴向剖面的形状相符合,车刀的刀尖角应该等于牙型角。
三角形螺纹的牙型角是60°,理论上三角形螺纹车刀的刀尖角也应该是60°。
但实际生产中,只有高速工具钢三角形螺纹车刀的刀尖角是60°,硬质合金三角形螺纹车刀的刀尖角则应为59°30’左右。
这是因为用硬质合金车刀高速切削时,工件材料受到较大的挤压力,会使牙型角增大约0.5°。
三、螺纹车刀种类1.高速工具钢三角形螺纹车刀(图1)的前角一般取5°~15°,粗车刀的纵向前角一般取15°左右,精车刀的前角一般取6°~10°。
2.硬质合金三角形螺纹车刀(图2)的前角和纵向前角一般都取0°,为了增加切削刃的强度,在车削较高硬度的材料时,两切削刃上可磨出负倒棱。
a)粗车到b)精车刀图1高速钢三角螺纹车刀c)焊接式d)机加式图2 硬质合金三角螺纹车刀三、刀具的刃磨三角螺纹车刀刃磨要求:①根据粗、精车的要求,刃磨出合理的前、后角。
粗车刀前角大、后角小,精车刀则相反;②车刀的左右刀刃必须是直线,无崩刃;③刀头不歪斜,牙型半角相等;④内螺纹车刀刀尖角平分线必须与刀杆垂直;⑤内螺纹车刀后角应适当大些,一般磨有两个后角。
四、割槽刀1)高速工具钢槽刀如图3所示1)前角ϒ0:前角增大能使车刀刃口锋利,切削省力并排屑顺畅,ϒ0=5°~20°;2)主后角α0:可减少车槽刀主后刀面和工件过渡表面间的摩擦,α0=6°~8°;3)副后角α0’:可减少车槽刀两个副后刀面和工件已加工表面间的摩擦,α0'=1~3°。
加工中心编程100例简单
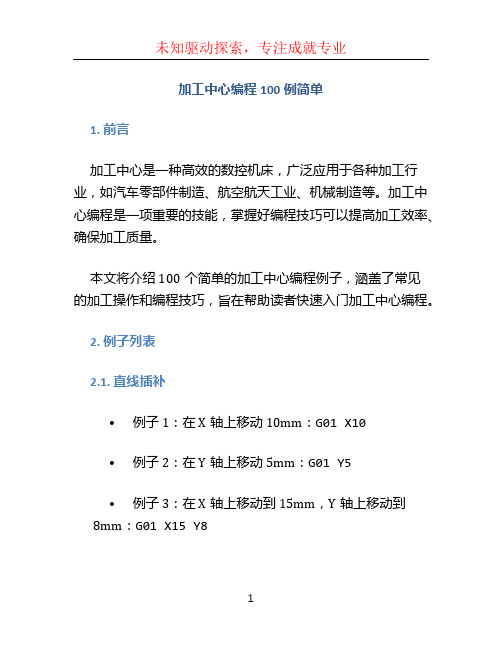
加工中心编程100例简单1. 前言加工中心是一种高效的数控机床,广泛应用于各种加工行业,如汽车零部件制造、航空航天工业、机械制造等。
加工中心编程是一项重要的技能,掌握好编程技巧可以提高加工效率、确保加工质量。
本文将介绍100个简单的加工中心编程例子,涵盖了常见的加工操作和编程技巧,旨在帮助读者快速入门加工中心编程。
2. 例子列表2.1. 直线插补•例子1:在X轴上移动10mm:G01 X10•例子2:在Y轴上移动5mm:G01 Y5•例子3:在X轴上移动到15mm,Y轴上移动到8mm:G01 X15 Y82.2. 圆弧插补•例子4:逆时针方向画一个半径为5mm的圆弧:G02 X5 Y0 R5•例子5:顺时针方向画一个半径为5mm的圆弧:G03 X0 Y5 R5•例子6:逆时针方向画一个半径为3mm的圆弧,起点在当前位置,终点位于X轴上1mm,Y轴上1mm:G02 X1 Y1 R32.3. 钻孔•例子7:在当前位置钻一个直径为10mm的孔:G81 X0 Y0 Z-10 R10•例子8:在X轴上移动到20mm,Y轴上移动到10mm,在(20,10)处钻一个直径为5mm的孔:G81 X20 Y10 Z-10 R5•例子9:在当前位置钻一个直径为8mm的孔,孔深为15mm:G81 X0 Y0 Z-15 R82.4. 螺纹加工•例子10:在X轴上移动到30mm,Y轴上移动到20mm,在(30,20)处加工一个内螺纹,螺纹直径为10mm,螺距为2mm:G33 X30 Y20 Z-10 D10 P2•例子11:在当前位置加工一个外螺纹,螺纹直径为8mm,螺距为1mm:G32 X0 Y0 Z-8 D8 P1•例子12:在X轴上移动到40mm,Y轴上移动到30mm,在(40,30)处加工一个外螺纹,螺纹直径为6mm,螺距为0.5mm:G32 X40 Y30 Z-6 D6 P0.52.5. 刀具补偿•例子13:在当前位置加工一个直径为10mm的孔,同时刀具半径补偿为2mm:G41 D10•例子14:在X轴上移动到50mm,Y轴上移动到40mm,在(50,40)处加工一个直径为6mm的孔,同时刀具半径补偿为3mm:G42 X50 Y40 D6•例子15:在当前位置加工一个直径为8mm的孔,同时刀具半径补偿为1mm:G43 D82.6. G函数•例子16:在当前位置暂停0.5秒:G04 P0.5•例子17:设置进给率为100mm/min:G01 F100•例子18:设置主轴转速为8000转/分钟:M03 S80002.7. 其他操作•例子19:将当前位置设为工件坐标系原点:G54 X0 Y0•例子20:将当前位置设为相对坐标系原点:G91 G92 X0 Y03. 总结本文介绍了100个简单的加工中心编程例子,覆盖了直线插补、圆弧插补、钻孔、螺纹加工、刀具补偿、G函数和其他操作。
加工中心螺纹编程实例
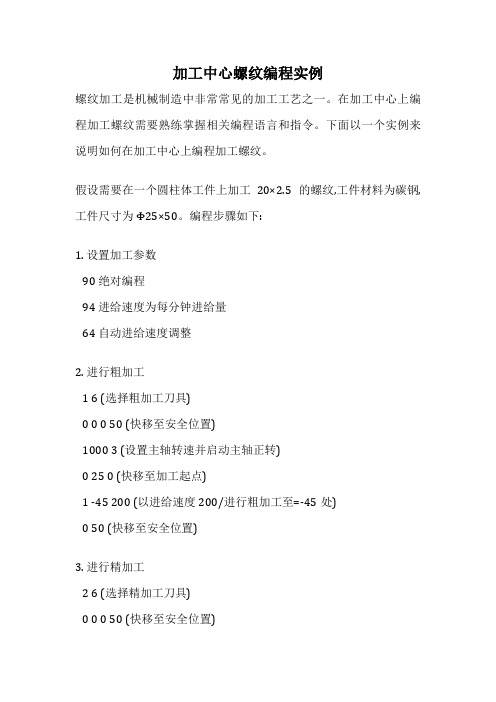
加工中心螺纹编程实例螺纹加工是机械制造中非常常见的加工工艺之一。
在加工中心上编程加工螺纹需要熟练掌握相关编程语言和指令。
下面以一个实例来说明如何在加工中心上编程加工螺纹。
假设需要在一个圆柱体工件上加工20×2.5的螺纹,工件材料为碳钢,工件尺寸为Φ25×50。
编程步骤如下:1. 设置加工参数90 绝对编程94 进给速度为每分钟进给量64 自动进给速度调整2. 进行粗加工1 6 (选择粗加工刀具)0 0 0 50 (快移至安全位置)1000 3 (设置主轴转速并启动主轴正转)0 25 0 (快移至加工起点)1 -45 200 (以进给速度200/进行粗加工至=-45处)0 50 (快移至安全位置)3. 进行精加工2 6 (选择精加工刀具)0 0 0 50 (快移至安全位置)2000 3 (设置主轴转速并启动主轴正转)0 25 0 (快移至加工起点)92 25 0 0 (设置加工起点为坐标原点)1 -48 100 (以进给速度100/进行精加工至=-48处)4. 开螺纹循环92 0 0 0 (设置当前位置为坐标原点)76 022530 2 2.5 (开启螺纹循环,20×2.5)76 48 -50 1 3000 500 2 (进行螺纹加工,方向行程48,方向行程50,进给速度2/)76 48 -50 1 3000 500 2 (再次进行螺纹加工,以保证加工质量)80 (取消循环)5. 退刀0 50 (快移至安全位置)5 (关闭主轴)30 (程序结束)以上就是一个在加工中心上编程加工20×2.5螺纹的实例。
在实际加工中,需要根据具体情况调整参数,并做好机床对刀、选择合适的刀具和切削液等准备工作。
车床加工工艺案例

车床加工工艺案例一、零件分析本次车床加工的零件为轴类零件,主要结构包括圆柱面、圆锥面、螺纹等。
零件的尺寸精度和表面质量要求较高,需要进行精细加工。
二、材料选择根据零件的加工要求和性能要求,选择合适的材料是关键。
本次加工选用45号钢作为原材料,该材料具有较好的切削性能和机械性能,适合用于轴类零件的加工。
三、刀具准备在车床加工中,刀具的选择和使用对加工质量和效率具有重要影响。
根据零件的结构和材料特性,准备以下刀具:外圆车刀:用于加工圆柱面和端面;圆锥车刀:用于加工圆锥面;螺纹车刀:用于加工螺纹;切槽刀:用于加工槽。
四、切削参数设定切削参数的合理设定对加工质量和效率具有重要影响。
根据零件的材料特性和刀具特性,设定以下切削参数:主轴转速:根据所使用的刀具和材料确定合理的转速;进给速度:根据加工表面的粗糙度和刀具寿命确定合理的进给速度;切削深度:根据加工余量和刀具刚度确定合理的切削深度。
五、加工流程设计加工流程的合理设计能够提高加工效率和质量。
本次加工流程如下:将原材料固定在车床工作台上;使用外圆车刀加工圆柱面和端面;使用圆锥车刀加工圆锥面;使用螺纹车刀加工螺纹;使用切槽刀加工槽;对加工完成的零件进行质量检测和成品检验。
六、冷却液使用在车床加工过程中,冷却液的使用能够有效降低切削温度,减少刀具磨损和热变形,提高加工质量和效率。
根据使用的刀具和切削参数,选择合适的冷却液并控制使用量。
七、质量检测在每道工序完成后,应对零件进行质量检测。
检测内容包括:尺寸精度、表面粗糙度、形状精度等。
检测方法可采用千分尺、表面粗糙度仪等测量工具进行测量和评估。
如发现不合格品,应及时进行调整和返工。
八、成品检验成品检验是确保最终产品质量的重要环节。
检验内容应包括:尺寸精度、表面质量、形状精度等。
检验方法与质量检测相同,可使用相同的测量工具进行测量和评估。
如发现不合格品,应进行追溯和整改。
九、优化与改进在实际生产过程中,应根据实际情况对加工工艺进行优化和改进。
谈项目教学案例——螺纹球面轴的加工

业
学 校
夏 家 琴
螺纹 球 面轴 的加 工是 《 数控 技 术 》课 程 的一 个 典型
案 例 ,涉 及 到 了 从 毛 坯 选 取 — — 工 艺 分 析 — — 编 写 程 序
六 、 教 学 法 简 介 项 目教 学 的 过 程 中 . 始 终 贯穿着 任 务引 领 、 结 果驱 动 和过 程控 制 。 具 体 的教学方 法如 下 。 1真 实 的 “ 景 教 . 场
专 业 理 论 知 识 。 为 避 免 他 们 对 专 业 知 识 的 理 解 仅 停 留 在 “ 其 然 ,而 不 知 其 所 以 然 ” 的层 面 ,应 切 实 提 高 学 生 主 知
3探究 学 习法 。每 个 任 务 的完 成 ,都 以学 生 为 主 , . 引导他 们 发现 问题 ,主动 探究 ,解 决 问题 。教师 主 要充
谈项目教学案例 螺 纹球 面轴 的 加 工
现 在企 业 中工作 的环 境 。
本 产 品 的 加 工 是 在 与 实
编 程 ,能 掌握工量 具 的使用方 法 ) 。 2技 能 目标 。数 控 车 床 加 工 轴 类 零 件 的 规 范 操 作 。 . ( 会使用 仿真 软件 、会 规 范熟练 操作机 床 、会 使 用量 具检
验 工 件 ) 。
际 工作 岗位 相 同 的坏 境 下 进 行 的 。 每 天 早 上 集 中 所 有 学 生 强 调 安 全 生 产 ,规 范 操 作 ,要 求 全 天 穿 工 作
服。
3情 感 目 标 。 学 会 合 作 、 学 会 求 真 、科 学 计 划 、 严 . 谨操作 。 四 、 学 情 分 析
一
、
项 目教 学 的 背 景
中职-模具钳工工艺与技能实训项目7螺纹加工课件(共36张PPT)
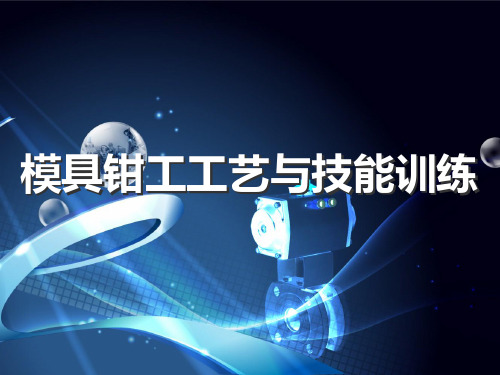
任务 螺纹加工
【知识储备】 二、螺纹加工工具
(4)螺纹有单线和多线之分:沿一根螺旋线形成的螺纹称单线螺纹;沿两根以 上螺旋线形成的螺纹称多线螺纹。连接螺纹大多为单线。 (5)螺纹按用途可分为连接螺纹(普通螺纹、管螺纹等)和传动螺纹(梯形、 锯齿形等)。 (6)按牙型可分为三角形、梯形、锯齿形等。 (7)按螺纹要素是否标准可分为标准螺纹、特殊螺纹和非标准螺纹(仅牙型符合 标准称为特殊螺纹,牙型不符合标准称为非标准螺纹)。
(2)在加工铸铁和塑性较小的材料及扩张量较小的条件下:
任务 螺纹加工
【知识储备】 三、螺纹加工中的计算公式
1. 攻螺纹前底孔的直径和深度 攻螺纹底孔深度的确定
(图7-11):攻不通的螺纹时, 由于丝锥切削部分有锥角,端 部不能切出完整的牙型,所以 钻孔深度要大于螺纹的有效深 度。一般取:
任务 螺纹加工
任务 螺纹加工
【知识储备】 四、螺纹加工方法
攻螺纹中常出现的问题及其产生原因: (5)丝锥折断 ①底孔太小。 ②攻入时丝锥歪斜或歪斜后强行校正。 ③没有经常反转断屑,或攻 不通孔已到底时还继续往下攻。 ④使用铰杠不当。 ⑤丝锥牙尺爆裂或磨损过多却强行往下攻。 ⑥工件材料过硬或夹有硬点。 ⑦两手用力不均或用力过猛。
任务 螺纹加工
【知识储备】 四、螺纹加工方法
2. 套螺纹方法 (3)正常套螺纹时不要加压,让板 牙自然引进(图7-13),以免损坏 螺纹和板牙,也要经常倒转以断屑。 (4)在钢件上套螺纹时要加切削液, 一般可以用机油或较浓的乳化液,要 求较高时可用工业植物油。
任务 螺纹加工
【知识储备】 四、螺纹加工方法
熟悉攻螺纹中常出现的问题及其产生原因,以便在练习时加以注意: (1)螺纹乱牙 ①攻螺纹时底孔直径太小,起攻困难,左右摆动,空口乱牙。 ② 换用二、三锥时强行校正,或没旋合好就下攻。 (2)螺纹滑牙 ①攻不通孔的较小螺纹时,丝锥已到底仍继续下攻。 ②攻强度低或小孔径螺纹时,丝锥已切出螺纹仍继续加压,或攻完时连同铰杠做自由 的快速转出。 ③未加适当切削液并一直攻、套不倒转,切屑堵塞将螺纹啃坏。 (3)螺纹歪斜 攻螺纹时位置不正,起攻、套时未做垂直度检查。 (4)螺纹形状不完整 攻螺纹时底孔直径太大,或套螺纹圆杆直径太小。
螺纹加工数控编程
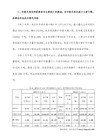
1、 G32用于公制螺纹加工、G33用于英制螺纹加工
2、 X(U)、 Z(W)为切削终点坐标、F 为螺纹导程
螺 纹 加 工 一 般 指 令
G32/G33与G01的区别是:通过脉冲编码器,能保证刀具在直线 移动时与主轴保持同步,即主轴旋转一周,刀具移动一个导程。
(二)应用类型 1、切削圆柱螺纹 G32/G33 Z(W)---F----
2、切削圆锥螺纹 G32/G33 X(U)---- Z(W)---3、切削端面螺纹 G32/G33 X(U)---- F----
F----
螺 纹 加 工 一 般 指 令
螺纹加工涉及6个方面的问题,编程时应多加注意:
1、主轴应指令恒转速(G97),螺纹加工中直径“X”是变化的
加 工 螺 纹 时 应 注 意 的 事 项
O0001 G50 X100. Z100. X59.1 G32 Z-53. F2 G97 M03 S600 G00 X62. T0101 Z5. G00 X62. Z5.
螺纹加工数控编程
螺纹加工指令
数控车床主要用于加工轴类、盘类等 回转体零件。机器中最常用的零件就是轴, 其作用是支撑零件、传递运动,如齿轮等, 齿轮一般通过螺纹实现轴向定位,所以螺 纹是轴类零件主要的组成面,掌握螺纹加 工的编程方法,对提高数控车削编程能力 意义重大。
本讲主要内容
一.螺纹概述 二.螺纹加工指令的格式 三.螺纹加工应注意的事项 四.螺纹加工举例 五.螺纹加工单一循环指令
加 工 螺 纹 时 应 注 意 的 事 项
径会变大Δ d ,加工内螺纹时直径会变小Δ d 。所以加工内螺纹时,孔径
应车到 d+Δ d ,加工外螺纹时,直径应车到 D-Δ d ,
• 常用螺纹切削的进给次数与背吃刀量 • (米制、双边) ( mm )
g33螺纹编程案例

g33螺纹编程案例G33螺纹编程是一种CNC加工中常用的编程方式,通过在编程中使用G33指令,可以实现螺纹加工操作。
下面是一个关于G33螺纹编程的案例,详细说明了其使用方法和编程过程。
假设我们需要在一根直径为50mm的铜材料上进行M12x1.5的内螺纹加工。
首先,我们需要确定铜材料的起始坐标,假设起始点坐标为(X0,Y0,Z0),并且确定螺纹的深度为10mm。
然后,我们可以开始进行编程:1. 设置坐标系:G54 ; 设置工件坐标系G90 ; 设置绝对编程模式2. 设置切削参数:S2000 ; 设置主轴转速为2000rpmF300 ; 设置进给速度为300mm/min3. 移动到起始点:G0 X0 Y0 Z0 ; 快速移动到起始点4. 开始螺纹加工:G33 X50 Z-10 K1.5 F1 ; 按照螺距为1.5mm、进给速度为1mm/min进行内螺纹加工,直径方向移动50mm,深度为-10mm编程过程中需要注意的是,K值表示螺距,F值表示进给速度,负的Z值表示向下切削。
在加工过程中,机床会自动根据刀具直径和螺距进行计算,以实现预定的螺纹规格。
同时,机床还会自动进行修正,以保持螺纹的准确度。
在以上的示例中,我们假设螺距为1.5mm,进给速度为1mm/min,这些数值可以根据需要进行调整。
值得注意的是,G33螺纹编程需要在机床的系统中进行支持,不同的机床可能会有一些差异。
通过以上的案例,我们可以看到G33螺纹编程的基本步骤和使用方法。
掌握了这些基础知识,我们就可以根据实际需要进行各种螺纹加工操作。
多头螺纹编程实例
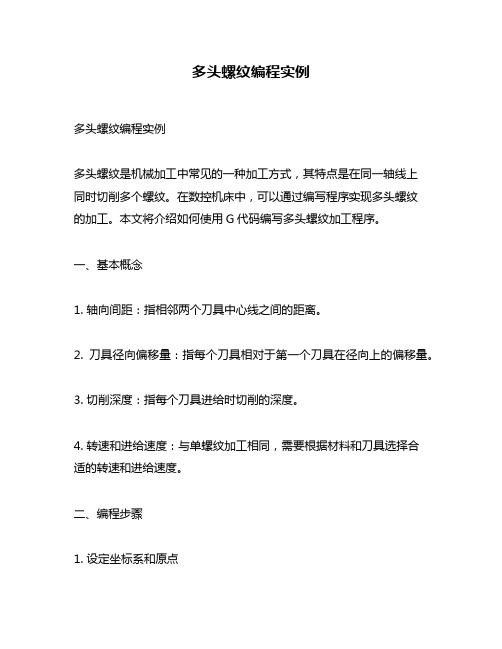
多头螺纹编程实例多头螺纹编程实例多头螺纹是机械加工中常见的一种加工方式,其特点是在同一轴线上同时切削多个螺纹。
在数控机床中,可以通过编写程序实现多头螺纹的加工。
本文将介绍如何使用G代码编写多头螺纹加工程序。
一、基本概念1. 轴向间距:指相邻两个刀具中心线之间的距离。
2. 刀具径向偏移量:指每个刀具相对于第一个刀具在径向上的偏移量。
3. 切削深度:指每个刀具进给时切削的深度。
4. 转速和进给速度:与单螺纹加工相同,需要根据材料和刀具选择合适的转速和进给速度。
二、编程步骤1. 设定坐标系和原点首先需要设定坐标系和原点。
通常情况下,选择X轴为主轴,设定X 轴为机床坐标系下的正方向,并将第一个刀具的圆心作为原点。
2. 设定参数设定轴向间距、刀具径向偏移量、切削深度等参数。
根据实际情况选择合适的数值。
3. 编写程序在编写程序时,需要考虑多个刀具同时切削的情况。
可以使用G76指令实现多头螺纹加工。
G76指令的格式如下:G76 X_ Z_ P_ Q_ R_ K_其中X、Z分别为第一个刀具的坐标;P为每个螺纹的轴向距离;Q为每个刀具在径向上的偏移量;R为每个刀具进给时切削的深度;K为螺纹类型,通常选择1。
例如,设定轴向间距为2mm,刀具径向偏移量为0.5mm,切削深度为0.2mm,则可以编写如下程序:N10 G90 G54 G96 S1000 M3N20 T01 M6N30 G00 X0 Z0N40 G01 Z-5 F200N50 G76 X10 Z-5 P2 Q0.5 R0.2 K1N60 M5 M9 M304. 调试程序在编写完成程序后,需要进行调试。
可以使用模拟器或手动模拟进行调试。
注意检查每个刀具的进给方向和深度是否正确。
三、注意事项1. 切勿让不同刀具之间相互干涉。
2. 切勿让刀具切削过深,以免造成机床震动和刀具破裂。
3. 切勿让刀具与工件相撞。
4. 在编写程序时,应根据实际情况选择合适的参数和加工方式。
用g92车英制螺纹程序实例

用g92车英制螺纹程序实例一、介绍g92车英制螺纹程序是数控机床上常用的一种程序,用于加工英制螺纹。
螺纹是机械制造中常见的一种连接方式,广泛应用于各种机械设备中。
二、程序示例下面以一个程序示例来介绍g92车英制螺纹程序的使用。
假设我们需要加工一个直径为20mm,螺距为1.5mm的英制螺纹。
1. 首先,设置加工坐标系。
在程序开头,使用G92命令设置坐标系原点和刀具的初始位置。
G92 X0 Y0 Z02. 设置进给速度和主轴转速。
通过G94和S命令来设置进给速度和主轴转速。
G94 F0.2S10003. 开始加工螺纹。
使用G76命令来进行螺纹加工。
G76 P010060 Q010 R0.2 Z-20 K04. 完成加工。
加工完成后,使用M30命令结束程序。
M30三、详解程序示例1. 设置加工坐标系:G92命令用于设置加工坐标系的原点和刀具的初始位置。
在这个程序示例中,我们将坐标系的原点设置为X、Y、Z坐标轴的零点。
2. 设置进给速度和主轴转速:G94命令用于设置进给速度的单位,这里设置为每分钟进给0.2mm。
S命令用于设置主轴转速,这里设置为1000转/分钟。
3. 开始加工螺纹:G76命令用于进行螺纹加工。
P参数指定螺纹的类型和规格,这里设置为010060,表示内螺纹,直径20mm,螺距1.5mm。
Q参数指定每次车削的深度,这里设置为010,表示每次车削1mm。
R参数指定每次车削的过切量,这里设置为0.2mm。
Z参数指定螺纹的总长度,这里设置为-20mm,表示从坐标系原点向下车削20mm。
K参数指定车削方向,这里设置为0,表示从外向内车削。
4. 完成加工:M30命令用于结束程序。
四、总结g92车英制螺纹程序是数控机床上常用的一种程序,用于加工英制螺纹。
通过设置加工坐标系、进给速度和主轴转速,并使用G76命令进行螺纹加工,可以实现精确的英制螺纹加工。
在实际应用中,根据具体的螺纹规格和加工要求,可以灵活调整程序参数,以达到所需的加工效果。
- 1、下载文档前请自行甄别文档内容的完整性,平台不提供额外的编辑、内容补充、找答案等附加服务。
- 2、"仅部分预览"的文档,不可在线预览部分如存在完整性等问题,可反馈申请退款(可完整预览的文档不适用该条件!)。
- 3、如文档侵犯您的权益,请联系客服反馈,我们会尽快为您处理(人工客服工作时间:9:00-18:30)。
案例四螺纹轴加工案例
1、零件图分析
图4-1 工件零件图
此图主要包含了外圆、外槽、圆半球、圆锥、螺纹等形状。
尺寸精度要求有:外圆的尺寸为φ58-0.03,外槽直径φ24-0.03,及长度120±0.05。
图中无位置精度要求。
表面粗糙度要求为1.6。
2、毛坯、机床、刀具、工具、量具、夹具的选择
2.1毛坯
根据零件最大尺寸可选择φ60塑料棒。
2.2机床
西门子CAK4085Ci 数控车床。
2.3刀具
加工外圆选用93°外圆刀,切槽切断选用b=4的切槽切断刀,60°螺纹尖刀。
2.4工具
卡盘扳手、套筒、压刀扳手、垫刀片。
2.5量具
游标卡尺0~250mm、外径千分尺0~25mm,50~75mm。
2.6夹具
三爪卡盘。
表4-1刀具列表
3、零件加工工艺分析
根据零件图尺寸精度和表面粗糙度要求,该零件采用车削加工的方法完成加工。
一次装夹,加工步骤为粗车外轮廓→精车外轮廓→切槽→加工螺纹→切断。
表4-2 数控加工工序卡
4、程序的编制
表4-3加工程序表
5、操作加工注意事项
(1).机床开机前,应先检查数控机床各部分结构是否完好;液压系统液压油是否正常;手动变速的数控车床其变速手柄位置是否正确。
(2).在上电和关机之前应按下”急停”按钮,以减少设备的电冲击。
(3).启动后,应使主轴低速空转,使润滑油散布到各需要之处,数控机床一切正常后才能工作。
(4).手动对刀时,应注意选择合适的进给速度;手动换刀时,刀架距工件要有足够的转位距离不至于发生碰撞。
(5).使用手轮或快速进给时,一定要看清机床X、Z各轴方向的正负方向。
(6).加工程序必须经过验证确认无误后方可加工;加工之前认真检查参数设置是否正确。
(7).模拟仿图时应关闭防护罩。
(8).启动程序时要关好防护罩,程序正常运行时禁止开启防护罩。
(9).多人共用一台机床时,每次只能一人操作并注意其他人安全,其他围观的人员不准乱动任何按钮。
(10).操作者应穿戴好工作服、工作帽,操作时不得打闹。
(11).在正式加工时的第一刀,刀具逼近工件时要暂停观察余量,检验时候正确。
(12).工作结束后,要打扫好卫生,机床擦拭干净。
6、评分表
表4-4零件加工评分表
7学习总结。