铜铝锌合金原材料检验规程
铜材、钢材、铝材进料检验规范

铜材铜材、、钢材钢材、、铝材铝材进料检验规范进料检验规范(第一版第一版))福建省三星机电设备有限公司技术部福建省三星机电设备有限公司技术部 编发布日期发布日期 2009年 06月 0505 日检验规范概 述凡产品图纸及其它制造文件或订货要求无特殊要求时,均以此规范为必须遵守的最低要求。
1 适用范围本检验规范规定了本公司外购铜材、钢材、铝材进料一般检验要求。
钢材进料检验规范钢材进料检验规范1. 材料检验a) 原材料入厂验收记录;b) 原材料质量合格证、化学成分与力学性能试验报告;c) 对牌号不明的原材料,经复验确定其牌号且提供检验报告方可使用;2.检验参照标准下列规范包含的条文,通过在本规范中引用而构成为本规范的条文。
GB 222-84 钢的化学分析用试样取样法及成品化学成分允许偏差GB 2101 型钢验收、包装、标志及质量证明书的一般规定GB/T4336-2002 碳素钢和中低合金钢火花源原子发射光谱分析方法GB/T228-2002 金属材料室温拉伸试验方法GB 232-1999 金属弯曲试验方法GB 2975-98 钢及钢产品 力学性能试验取样位置及试样制备3 检验依据a) 订货合同和订货技术要求,订货合同内容应包括下列内容: 材料名称、材料牌号、材料状态、规格(型材号、定尺长度等)、尺寸允许偏差(若不注明则按最低级别供货)、重量、其他要求等。
b) 符合上述规定的产品图样、设计文件、制造工艺与有关技术标准(按国家标准)。
c) 原材料质量合格证、化学成分与力学性能试验报告;d)各种型材检验依照国家相关标准执行。
4 检查4.1检查每批型材上是否挂有如下标志的标牌:a) 供方技术监督部门的检印;b)生产厂名称、商标;c) 材料牌号;d) 供应状态:e) 批 号4.2 产品质量检验记录,由质量检验部门填报与汇总,并建立产品质量档案。
4.3 根据订货合同的要求,产品质量检验记录可作为产品质量合格证的附件,提供给客户。
金属制品公司原材料检验规程
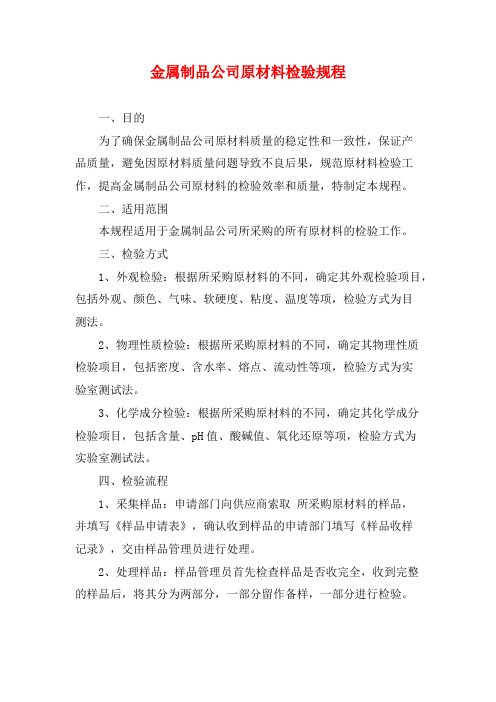
金属制品公司原材料检验规程一、目的为了确保金属制品公司原材料质量的稳定性和一致性,保证产品质量,避免因原材料质量问题导致不良后果,规范原材料检验工作,提高金属制品公司原材料的检验效率和质量,特制定本规程。
二、适用范围本规程适用于金属制品公司所采购的所有原材料的检验工作。
三、检验方式1、外观检验:根据所采购原材料的不同,确定其外观检验项目,包括外观、颜色、气味、软硬度、粘度、温度等项,检验方式为目测法。
2、物理性质检验:根据所采购原材料的不同,确定其物理性质检验项目,包括密度、含水率、熔点、流动性等项,检验方式为实验室测试法。
3、化学成分检验:根据所采购原材料的不同,确定其化学成分检验项目,包括含量、pH值、酸碱值、氧化还原等项,检验方式为实验室测试法。
四、检验流程1、采集样品:申请部门向供应商索取所采购原材料的样品,并填写《样品申请表》,确认收到样品的申请部门填写《样品收样记录》,交由样品管理员进行处理。
2、处理样品:样品管理员首先检查样品是否收完全,收到完整的样品后,将其分为两部分,一部分留作备样,一部分进行检验。
3、实验室测试:将检验样品交由实验室进行测试,实验人员根据检验要求完成测试。
4、测试报告:实验室测试完毕,将测试结果填写到《测试报告》中。
5、样品归档:检验后的样品和测试报告交由样品管理员进行归档管理。
五、送检标准1、外观检验标准:原材料的外观应无沉淀、杂质、气泡等缺陷。
2、物理性质检验标准:原材料的物理性质均应符合国家、地方标准规范,如有特殊要求,应在检验标准中明确规定。
3、化学成分检验标准:原材料的化学成分应符合国家、地方标准规范,如有特殊要求,应在检验标准中明确规定。
六、检验记录和文件1、样品申请表、收样记录、测试报告等相关检验记录和文件应按规定归档保存。
2、检验结果应及时反馈给采购部门和供应商。
七、检验频率1、采购部门应根据原材料使用情况,对所采购原材料进行定期检验。
2、对于新供应商的原材料,首次供货时应进行全面检验。
铝合金材料检验试验规范标准

图1图2 图38.3.2支辊式弯曲装置8.3.2.1 支辊长度和弯曲压头的宽度应大于试样宽度或直径(见图1).弯曲压头的直径由产品标准规定。
支辊和弯曲压头应具有足够的硬度。
8.3.2.2除非中有规定,支辊间距离L应按照式(1)确定:L=(D+3a)± a/2 (1)注:此距离在试验期间应保持不变。
8.3.3 V型模具式弯曲装置模具的V形槽其角度应为(180°-a)(见图2),弯曲角度a应在相关产品零件图中规定。
模具的支承棱边应倒圆,其倒圆半径应为(1~10)倍试样厚度。
模具和弯曲压头宽度应大于试样宽度或直径并具有足够的硬度。
8.3.4 虎钳式弯曲装置装置由虎钳及有足够硬度的弯曲压头组成(见图3),可以配置加力杠杆。
弯曲压头直径应按照产品标准要求,弯曲压头宽度应大于试样宽度或直径。
8.4. 试样8.4.1 一般要求试验使用圆形、方形、矩形或多边形模截面的试样。
样坯的切取位置和方向应按照相关产品标准的要求。
8.4.2 试样的宽度试样宽度应按照应相关标准产品要求8.4.3 试样的厚度试样厚度应按照应相关标准产品要求8.4.4试样的长度试样厚度应按照应相关试验装置(设备)要求的长度。
8.5 试验程序特别提示:试验过程应采取足够的安全措施和防护措施。
8.5.1试验一般在10℃~35℃的室温围进行8.5.2按照相关产品的规定,试样在给定的条件和力的作用下弯曲至规定的弯曲角度(见图1、图2和图3)8.5.3试样弯曲至规定弯曲角度的试验,应将试样放于两支辊(见图1)或V形模具(见图2)上,试样轴线应与弯曲压头轴线垂直,弯曲压头在两支座之间的中点处对试样连续施加力使其弯曲,直至达到规定的弯曲角度。
可以采用图3所示的方法进行弯曲试验。
试样一端固定,绕弯曲压头进行弯曲,直至达到规定的弯曲角度。
弯曲试验时,应当缓慢地施加弯曲力,以使材料能够自由地进行塑性变形。
弯曲时,试验速率应为(1±0.2)mm/s.当使用上述方法如不能直接达到规定的弯曲角度,可将试样置于两平行压板之间(见图4),连续施加力压其两端使进一步弯曲,直至达到规定的弯曲角度。
铝合金材料检验试验规范
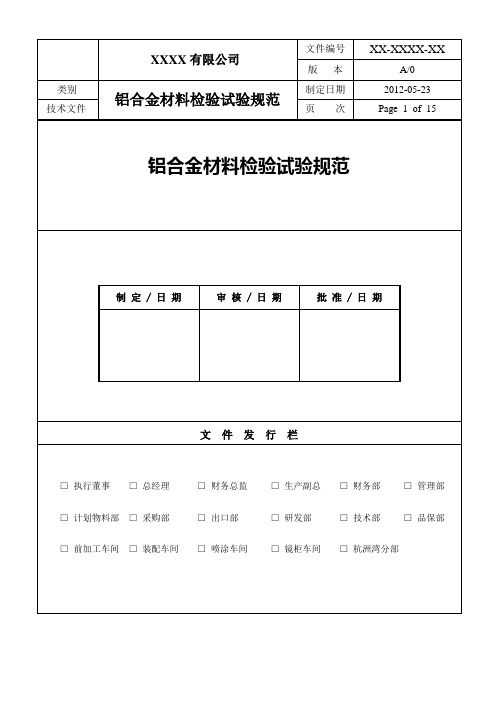
类别铝合金材料检验试验规范制定日期2012-05-23技术文件页次Page 9 of 15a)弯曲试验应在配备下列弯曲装置之一的试验机或压力机上完成:b)配有两支辊和一个弯曲压头的支辊式弯曲装置, 见图1c)配有一个V型器具和一个弯曲压头的V型模具式弯曲装置, 见图2虎钳式弯曲装置, 见图3图1图2 图38.3.2支辊式弯曲装置8.3.2.1 支辊长度和弯曲压头的宽度应大于试样宽度或直径(见图1).弯曲压头的直径由产品标准规定。
支辊和弯曲压头应具有足够的硬度。
8.3.2.2除非中有规定, 支辊间距离L应按照式(1)确定:L=(D+3a)± a/2 (1)注: 此距离在试验期间应保持不变。
8.3.3 V型模具式弯曲装置模具的V形槽其角度应为(180°-a)(见图2), 弯曲角度a应在相关产品零件图中规定。
模具的支承棱边应倒圆, 其倒圆半径应为(1~10)倍试样厚度。
模具和弯曲压头宽度应大于试样宽度或直径并具有足够的硬度。
8.3.4 虎钳式弯曲装置装置由虎钳及有足够硬度的弯曲压头组成(见图3), 可以配置加力杠杆。
弯曲压头直径应按照产品标准要求, 弯曲压头宽度应大于试样宽度或直径。
8.4.试样类别铝合金材料检验试验规范制定日期2012-05-23技术文件页次Page 11 of 15F8.6.试验结果的评定:8.6.1应按照相关产品标准的要求评定弯曲试验结果。
如未规定具体要求, 弯曲试验后不使用放大镜观察, 试样弯曲外表面无可见裂纹应评定为合格。
8.6.2 以相关产品标准要求规定的弯曲角度作为最小值;若规定弯曲压头直径, 以规定的弯曲压头直径作为最大值。
8.7 试验报告a)试验报告至少应包括以下内容:b)本标准编号;c)试样标识(材料牌号, 取样方向)d)试样的形状和尺寸e)试样条件(弯曲压头直径, 弯曲角度)f)与标准的偏差g)试验结果评定9.铝型材管材压扁试验(GB246-2007)9.1 范围规定了测定圆形横截面金属管塑性变形能力的压扁试验方法, 包括显示其缺陷。
铝合金材料检验试验规范标准

有良好的强度,热态下塑性良好,冷态下,切削加工性好,易焊接,耐蚀性好。
良好的抗腐蚀性、韧性,易于抛光、上色膜,阳极氧化效果优良。
8 铝合金型材抗弯试验 ( GB/T232-2010 )范围:规定了测定金属材料承受弯曲塑性变形能力。
原理:弯曲试验以圆形,方形、矩形或多边形横截面试样在弯曲装置上经受弯曲塑性变形、不改变加力方向,直至达到规定的弯曲角度。
弯曲试验时,试样两端的轴线保持在垂直于弯曲轴的平面内。
试验设备一般要求弯曲试验应在配备下列弯曲装置之一的试验机或压力机上完成:a)配有两支辊和一个弯曲压头的支辊式弯曲装置,见图1b)配有一个V型器具和一个弯曲压头的V型模具式弯曲装置,见图2c)虎钳式弯曲装置,见图3图1图2 图3支辊式弯曲装置支辊长度和弯曲压头的宽度应大于试样宽度或直径(见图1).弯曲压头的直径由产品标准规定。
支辊和弯曲压头应具有足够的硬度。
除非中有规定,支辊间距离L应按照式(1)确定:L=(D+3a)± a/2 (1)注:此距离在试验期间应保持不变。
V型模具式弯曲装置F. 试验结果的评定:应按照相关产品标准的要求评定弯曲试验结果。
如未规定具体要求,弯曲试验后不使用放大镜观察,试样弯曲外表面无可见裂纹应评定为合格。
以相关产品标准要求规定的弯曲角度作为最小值;若规定弯曲压头直径,以规定的弯曲压头直径作为最大值。
试验报告试验报告至少应包括以下内容:a)本标准编号;b)试样标识(材料牌号,取样方向)c)试样的形状和尺寸d)试样条件(弯曲压头直径,弯曲角度)e)与标准的偏差f)试验结果评定9. 铝型材管材压扁试验 (GB246-2007)范围规定了测定圆形横截面金属管塑性变形能力的压扁试验方法,包括显示其缺陷。
适用于外径不超过600mm,壁厚不超过外径的15%的金属管。
本试验适用的金属管外径和壁厚范围可以见,,条规定。
符号、名称和单位本试验使用的符号、名称和单位在表12和图5中规定表12符号名称单位a管壁厚度mmb压扁后试样的内宽度mmD金属管外径mmH力作用下两压板之间的距离mmL试样长度mm 原理垂直于金属管纵轴线方向对规定长度的试样或金属管端部施加力进行压扁,直至在力的作用下两压板之间的距离达到相关产品标准所规定的值(见图5a和图5b)。
铝合金材料检验试验规范标准.docx

铝合金材料检验试验规范文件发行栏□执行董事□总经理□财务总监□生产副总□财务部□管理部□计划物料部□采购部□出口部□研发部□技术部□品保部□前加工车间□装配车间□喷涂车间□镜柜车间□杭洲湾分部1、目的:为了保证铝合金(铝型材)材料的来料质量和满足制程中各项工艺技术要求,特制定本规范。
2、范围:2.1本规范规定了铝合金(铝型材)材料的技术要求、检验方法、试验方法,检验标准。
2.2本规范适用于本公司外购的所有的铝合金型材材料。
2.3本规范规定的原材料外形尺寸和表面质量为正常检查项目,化学成分和力学分析为特殊检查项目。
3、职责:3.1品质部:负责原材料来料检验;3.2工程技术中心:负责新工艺、新材料的试验;3.3采购部:负责联系与原材料供应商之间信息反馈及品质要求。
4、内容:4.1、外形尺寸测量工具:4.2铝合金型材截面尺寸:技术要求中除技术部门提供的图纸资料中有特殊要求,否则按GB5237.1-2004执行,铝型材开口尺寸除外。
(见表1、表2)。
表1 铝合金型材截面尺寸及允许偏差注:铝型材的长度尺寸按供需双方在订单合同的技术要求约定执行表2 铝合金型材管壁厚允许偏差mm注:方管的外径系指为切圆直径或两平行面之间的距离。
421铝型材管材制成品的规格尺寸按技术部门提供的图纸资料执行,允许偏差参考表1和表2。
4.2.2铝型材管材的不圆度和壁厚的不均匀,不超出外径和壁厚的允许偏差。
4.3铝型材形状偏差:表3形状偏差4.4铝合金型材材料特性,硬度要求:表4材料特性要求5、铝合金型材表面质量要求铝合金型材管材、棒材,板材和型材表面无破损、凹陷、沙孔、杂质等。
如果有缺陷,按表5要求检验表5 黄铜表面质量要求注:1、铜材表面的拉伤、划痕检验,不包括车加工外圆表面的产品。
2、在抛光完工后,以目力测试检验产品表面,表面的沙孔或杂质点等缺陷影响到外观装饰性的,这样的不良产品按退货处理。
6、检验方法6.1铝合金型材的随机抽样检验按相关抽样规定6.2铝合金型材的外形截面尺寸用游标卡尺测量;长度尺寸用卷尺测量;圆弧面用R规测量。
铝合金、铜合金、锌合金外观检验标准

引用说明:1.本外观检验标准引自中华人民共和国第一机械工业部部标准JB2702-810《铝合金、锌合金、铜合金压铸件技术条件》;2.未注明铸件类别、级别和精度者,均按本标准相关的最低级别处理;3.当本标准与图纸要求、顾客特殊要求不统一时,按图纸要求、顾客特殊要求处理4.在不影响铸件使用的条件下,允许进行整形和修补,但必须对铸件作相应的复检。
一:铸件清理后的表面质量1.铸件的浇口、飞边、溢流口、隔皮等应清理干净,但允许留有清理痕迹。
2.在不影响使用的情况下,因去除浇口、飞边、溢流口时所形成的缺肉或高出均不得超过壁厚的1/4且不得超过1.5mm。
二:待加工面的表面质量1.不允许有超过加工余量范围的表面缺陷和痕迹。
2.不允许有凸起高度超过1 mm以上的推杆痕迹,对工艺基准面上不允许有凸起的推杆痕迹。
三:铸件机械加工后的表面质量1.不允许有影响使用的局部铸态表皮存在。
2.不允许有超过表1规定的孔穴存在。
表13.机械加工螺纹的表面质量表2b. 不铸底孔加工后的螺孔表面质量按表3规定。
表3四:铸件不加工面的表面质量1.不允许有裂纹、欠铸和任何穿透性的缺陷。
2.表43.在不影响使用和装配的情况下,网状毛刺和痕迹高度铝、锌合金压铸件不大于0.2 mm;铜合金压铸件不大于0.2 mm。
4.由于模具组合镶并或受分型面影响而形成铸件表面高低不平的偏差,不得超过有关尺寸公差。
5.推杆痕迹凹入铸件表面的深度不得超过该处壁厚的1/10,且不得超过0.4mm;在不影响使用和装配的情况下,推杆痕迹允许凸起,凸起高度不大于0.2 mm。
6.工艺基准面、配合面上不允许任何凸起痕迹,装饰面不允许有推杆痕迹。
这类表面应在图样上注明。
7.表5 8.注:对于1级或有特殊要求的表面,只允许有经抛光或研磨能去除的缺陷。
表6五:名词解释1.气孔:卷入压铸件内部的气体所形成的形状较为规则、表面较为光滑的孔洞。
2.缩孔:压铸件在冷凝过程中,由于内部补偿不足所造成的形状不规则、表面较粗糙的孔洞。
五金类材料检验规范
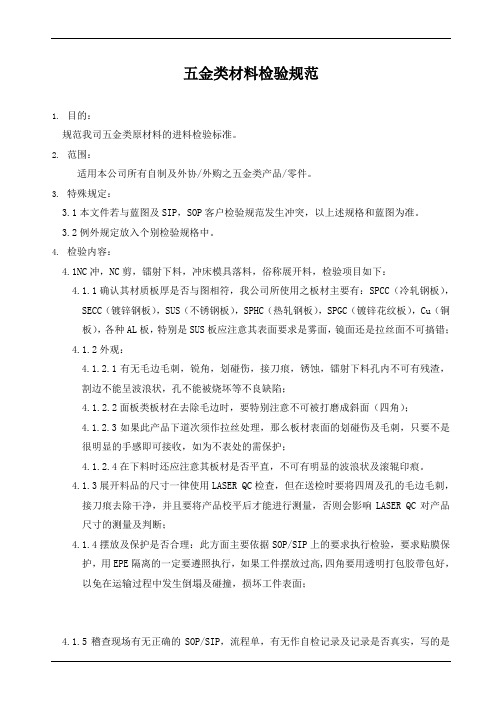
五金类材料检验规范1.目的:规范我司五金类原材料的进料检验标准。
2.范围:适用本公司所有自制及外协/外购之五金类产品/零件。
3.特殊规定:3.1本文件若与蓝图及SIP,SOP客户检验规范发生冲突,以上述规格和蓝图为准。
3.2例外规定放入个别检验规格中。
4.检验内容:4.1NC冲,NC剪,镭射下料,冲床模具落料,俗称展开料,检验项目如下:4.1.1确认其材质板厚是否与图相符,我公司所使用之板材主要有:SPCC(冷轧钢板),SECC(镀锌钢板),SUS(不锈钢板),SPHC(热轧钢板),SPGC(镀锌花纹板),Cu(铜板),各种AL板,特别是SUS板应注意其表面要求是雾面,镜面还是拉丝面不可搞错;4.1.2外观:4.1.2.1有无毛边毛刺,锐角,划碰伤,接刀痕,锈蚀,镭射下料孔内不可有残渣,割边不能呈波浪状,孔不能被烧坏等不良缺陷;4.1.2.2面板类板材在去除毛边时,要特别注意不可被打磨成斜面(四角);4.1.2.3如果此产品下道次须作拉丝处理,那么板材表面的划碰伤及毛刺,只要不是很明显的手感即可接收,如为不表处的需保护;4.1.2.4在下料时还应注意其板材是否平直,不可有明显的波浪状及滚辊印痕。
4.1.3展开料品的尺寸一律使用LASER QC检查,但在送检时要将四周及孔的毛边毛刺,接刀痕去除干净,并且要将产品校平后才能进行测量,否则会影响LASER QC对产品尺寸的测量及判断;4.1.4摆放及保护是否合理:此方面主要依据SOP/SIP上的要求执行检验,要求贴膜保护,用EPE隔离的一定要遵照执行,如果工件摆放过高,四角要用透明打包胶带包好,以免在运输过程中发生倒塌及碰撞,损坏工件表面;4.1.5稽查现场有无正确的SOP/SIP,流程单,有无作自检记录及记录是否真实,写的是否规范等等;4.1.6上述检验项目不可漏掉任何一项,当全部合格时方可下转。
4.2NC折,冲床成型:4.2.1确认其材质,板厚是否与图相符;4.2.2外观:表面有无明显之折痕,变形,折斜,划碰伤,接模痕等不良;4.2.3角度:每一刀的角度依图面清楚进行检测,对于折弯角度较复杂要求较高的工件,可做检具加以控制;4.2.4方向:在看折弯方向时,先弄清楚图面要求的是第一角,还是第三角画法。
铝业公司原材料、半成品、成品检验规程

文件编号:YS-JY 受控状态:铝业公司原材料、半成品、成品检验规程第A版,0次修改分发号:编制人:审批人:2020.12.20发布 2020.12.26实施目录 (2)原材料检验规程 (3)半成品检验规程 (7)成品检验规程 (9)1.铝棒进厂检验1.1验证质保书根据供方质量证明书,检查实物的熔炼炉号、合金牌号是否相符,是否符合要求;1.2铝棒外观质标准1.3铝棒尺寸偏差标准:1.4化学成分标准:1.5低倍组织标准1.6根据以上标准要求,对外观质量和尺寸偏差进行逐根检验;化学成分每批对硅、镁、铁、铜、锰五个元素进行化验。
低倍组织每批次做一次检验。
1.7以上项目均合格后,则该批铸锭合格。
2、其它辅助材料的进厂检验注:化工材料有效期国标有规定的按国标,没有规定的本厂定为三个月3. 批次合格判别:检验批抽样样品全部项目合格则该批材料全格。
4不合格的处理不合格的处理按《不合格品控制程序》处理5检验记录及标识经检验合格的产品进行标识,按要求做好检验原始记录.1.工序半成品检验2. 时效硬度检验2.1 型材时效完毕出炉后立即风冷,待型材温度低于50℃后,方可检测硬度。
2.2 每框型材的两端各取不少于10个试样测硬度。
2.3 取最低的一个硬度值作为该框型材硬度,并做好记录。
2.4 当硬度不能达到8HW时,应进行全检,将挑出不合格的型材重新时效,待时效出炉后炉后重新进行硬度检测,若合格则放行。
2.5 凡经二次时效不合格的型材按《不合格品处理程序》进行。
3. 抽检数按每批10%,如果发现不合格采用全检。
4.不合格的处理按《不合格品处理程序》进行。
5自检不合格品按区域标识,由质检部负责评审其性质,提出处置建议。
6专检发现的不合格品,由生产部负责处置。
7.标识:经检验合格的半成品由质检员在《生产随行卡》上进行标识,同时由责任部门分区挂牌标识,以防不合格品的误用或转序。
1成品检验规程附表:表一表二文件修改页。
锌合金检验作业指导书

锌合金检验作业指导书1、目的为确保本公司IQC检验员对五金类来料有明确的检验依据及判断基准,而制定本标准。
2、范围适用于锌合金来料。
3、职责3.1本标准由质量部IQC组制定,经部门主管/经理核准后交文控发行。
3.2所制定之规格及标准如有修改时,须经原制订部门同意后方可修改。
3.3所有铝片来料IQC均需按此标准检验。
4、抽样水准4.1所有物料均按照GB/T 2828.1-2003 逐步检验抽样计划进行抽样检验。
4.2判定标准:AQL取值 AQL:CR=0 MA=0.65 MI=1.54.3 当一个产品含有两个或以上缺点时,以较严重之缺点为判定。
5、检测条件视力:具有正常视力 1.0--1.2视力和色感。
照度:正常日光灯,室内无日光时用40W日光灯或60W普通灯泡的照度为标准。
目测距离:眼睛距离产品30--40CM为准。
观察时间:<10秒 (每个可见平面需要3秒)。
6、外观检验标准NO. 缺陷项目项目说明缺陷分类CR MA MI1 尺寸重要尺寸不符合图纸设计要求√配合尺寸不满足组装要求√孔位尺寸不满足组装要求√孔位尺寸偏大,但组装后,满足结构要求√孔位尺寸偏大,但组装后,不满足结构要求√孔位尺寸偏小,不影响产品组装√孔位尺寸偏小,影响产品组装或不能组装√与螺丝配合,松动但可锁紧√与螺丝配合,松动但不能锁紧/滑牙√与螺丝配合拧不进√牙孔偏大,与螺丝配合较松,扭力测试不通过或滑牙√牙孔偏大,与螺丝配合较松,扭力测试通过√2 披风物件外表边沿有明显的披锋及飞边高出√物件的外表面之合模线高出平面0.05 mm √0.05 mm≦高≦0.1 mm √高>0.1 mm √孔位周边披锋,不影响产品组装及产品外观√孔位周边披锋,组装后可遮盖√孔位周边披锋,组装后不能遮盖√孔位周边披锋,影响产品组装或不能装配√产品内部披锋,不影响产品装配或对内部接线无损伤√影响产品装配或对内部接线有损伤√3 缩水物件A级面,不能有缩水现象√B、C级面缩水面积≦3 m㎡,缩水深度0.1mm √B、C级面缩水面积≦5 m㎡,缩水深度0.1mm √B、C级面缩水面积5 m㎡≦X≦10m㎡, 缩水深度0.1mm ,不接受√物体内部缩水:面积≦5 m㎡,深度0.3mm √物体内部缩水:面积≦10m㎡, 深度0.3mm √物体内部缩水:面积>10m㎡,不影响产品结构和外观√。
铝合金材料检验试验规范标准
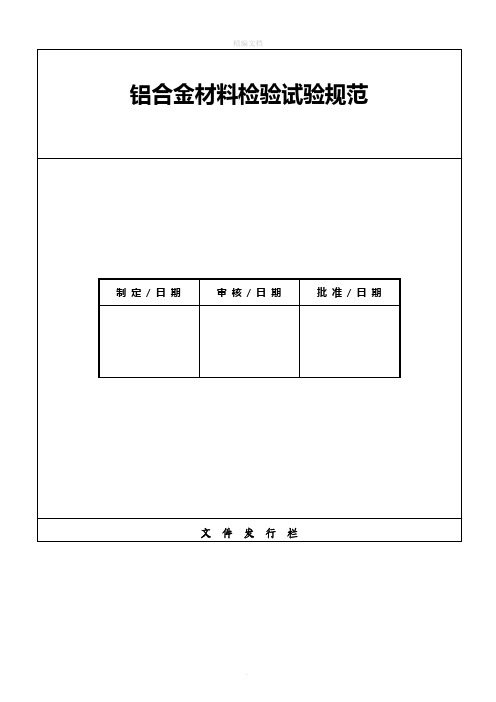
8.3 试验设备8.3.1一般要求弯曲试验应在配备下列弯曲装置之一的试验机或压力机上完成:a)配有两支辊和一个弯曲压头的支辊式弯曲装置,见图1b)配有一个V型器具和一个弯曲压头的V型模具式弯曲装置,见图2c)虎钳式弯曲装置,见图3图1图2 图38.3.2支辊式弯曲装置8.3.2.1 支辊长度和弯曲压头的宽度应大于试样宽度或直径(见图1).弯曲压头的直径由产品标准规定。
支辊和弯曲压头应具有足够的硬度。
8.3.2.2除非中有规定,支辊间距离L应按照式(1)确定:L=(D+3a)±a/2 (1)注:此距离在试验期间应保持不变。
试样连续施加力使其弯曲,直至达到规定的弯曲角度。
可以采用图3所示的方法进行弯曲试验。
试样一端固定,绕弯曲压头进行弯曲,直至达到规定的弯曲角度。
弯曲试验时,应当缓慢地施加弯曲力,以使材料能够自由地进行塑性变形。
弯曲时,试验速率应为(1±0.2)mm/s.当使用上述方法如不能直接达到规定的弯曲角度,可将试样置于两平行压板之间(见图4),连续施加力压其两端使进一步弯曲,直至达到规定的弯曲角度。
图4 FF8.6. 试验结果的评定:8.6.1应按照相关产品标准的要求评定弯曲试验结果。
如未规定具体要求,弯曲试验后不使用放大镜观察,试样弯曲外表面无可见裂纹应评定为合格。
8.6.2 以相关产品标准要求规定的弯曲角度作为最小值;若规定弯曲压头直径,以规定的弯如为闭合压扁,试样内表面接触的宽度应至少为标准试样压扁后其内宽度b的1/2(见图5c)图59.4试验设备9.4.1试验机(可采用是冲床或钳工虎钳台)应能将试样压扁至规定的两平行压板之间的距离。
压板应具有足够的刚度。
压板的宽度应超过压扁后试样宽度,即至少为1.6D。
压板的长度应不小于试样的长度。
9.5 试样9.5.1 试样长度应不小于10mm,但不超过100mm。
试样的棱边允许用锉刀或其它方法将其倒圆或倒角。
(注:如果试验结果满足试验要求,可以不对试样的棱边倒圆或倒角。
金属原材料类检验规范

金属原材料类检验规范一、样品采集与处理1.样品的代表性:从不同批次或供应商采集的样品应能代表整个批次的质量水平。
2.样品存放:样品应储存于干燥、通风良好的环境中,防止受潮、变质等。
3.样品处理:针对不同金属原材料,可进行表面处理、热处理等,以模拟实际应用条件。
二、外观检验1.表面缺陷:检查样品表面是否存在划痕、氧化、麻点等缺陷。
2.形状尺寸:测量样品的长度、宽度、厚度等尺寸,检查是否符合指定要求。
3.包装要求:检查样品的包装是否符合运输和储存的相关标准。
三、化学成分检验1.采样方法:根据不同金属原材料的特性,选择适合的采样方法,保证样品的代表性。
2.元素分析:使用适当的方法和设备,测定样品中各元素的含量,比较实测值与标准值是否符合要求。
3.杂质检验:检查金属原材料中是否存在非金属杂质,如氧化物、硫化物等。
四、机械性能检验1.抗拉强度:通过拉伸试验,测定样品的抗拉强度、屈服强度、断裂伸长率等机械性能指标。
2.硬度测试:使用硬度计测量样品的硬度,比较实测值与标准要求是否符合。
3.冲击韧性:进行冲击试验,评估样品的抗冲击性能,判断其在低温环境下的可靠性。
五、热处理性能检验1.退火性能:通过热处理试验,观察样品经退火后的晶粒结构、硬度等变化情况。
2.强化效果:对样品进行固溶处理和时效处理,评估样品的强化效果和耐腐蚀性能。
六、非破坏性检验1.金相检验:对样品进行金相分析,观察和评估样品的组织结构、晶粒尺寸等微观结构特征。
2.声波检测:利用超声波探测仪对样品进行无损检测,评估样品的内部结构和缺陷情况。
3.磁粉检测:对样品进行磁粉检测,检测样品中是否存在裂纹、孔洞等表面和内部缺陷。
七、可燃性和腐蚀性检验1.可燃性测试:对样品进行可燃性测试,评估其燃烧性能和火灾危险性。
2.腐蚀性测试:将样品置于不同腐蚀介质中,观察其耐蚀性能和腐蚀程度。
总结:以上是金属原材料类检验规范的一般内容,金属原材料的检验规范旨在确保材料的质量和安全性,提高产品的可靠性和持久性。
锌合金检验作业指导书

锌合金检验作业指导书一、背景介绍锌合金是一种具有优异性能和广泛应用的金属材料,具有高强度、良好的耐蚀性和注塑性能等特点,广泛应用于汽车、电子、家具等行业。
为确保锌合金制品的质量,需要进行严格的检验和测试。
本作业指导书将详细介绍锌合金检验的步骤和方法,帮助操作人员正确进行锌合金检验工作。
二、检验仪器和设备1. 显微镜:用于观察锌合金表面和断口的形态和结构。
2. 金相显微镜:用于观察和分析锌合金的金相组织。
3. 电子天平:用于精确称量样品和试剂。
4. 摩擦磨损试验机:用于评估锌合金的耐磨性能。
5. 维氏硬度计:用于测定锌合金的硬度。
6. 密度计:用于测定锌合金的密度。
三、检验步骤1. 外观检查:对锌合金制品进行外观检查,包括检查表面是否有明显的划伤、气泡和机械性缺陷等。
2. 物理性能检验:a. 密度检验:使用密度计测量锌合金的密度,与标准值进行比对。
b. 硬度检验:使用维氏硬度计对锌合金进行硬度测试,记录测试结果。
c. 摩擦磨损检验:使用摩擦磨损试验机评估锌合金的耐磨性能。
3. 金相组织检验:a. 金相制样:根据需要获取适当大小的锌合金样品,打磨、抛光后进行腐蚀处理。
b. 金相显微镜观察:使用金相显微镜观察腐蚀后的锌合金样品,分析金相组织的类型和分布情况。
4. 化学成分分析:a. 取样:根据规定的要求,从锌合金制品中取得合适大小的样品。
b. 归批:将样品进行标记,并将其送往化学实验室进行化学成分分析。
c. 分析结果:根据化学实验室提供的分析结果,进行合格判定。
四、注意事项1. 检验时,应保证操作人员具备相应的技术知识和操作经验,并严格按照操作规程进行操作。
2. 仪器和设备的使用和维护应遵守相关规定,确保其正常运行和准确性。
3. 检验过程中需要注意安全防护,避免意外伤害的发生。
4. 锌合金样品的取样需要在不破坏产品外观和功能的前提下进行。
5. 化学成分分析需要由专业的化学实验室进行,确保结果的准确性和可靠性。
铝合金材料检验试验规范标准

铝合金材料检验试验规范标准(总13页)--本页仅作为文档封面,使用时请直接删除即可----内页可以根据需求调整合适字体及大小--图1图2 图3支辊式弯曲装置支辊长度和弯曲压头的宽度应大于试样宽度或直径(见图1).弯曲压头的直径由产品标准规定。
支辊和弯曲压头应具有足够的硬度。
除非中有规定,支辊间距离L应按照式(1)确定:L=(D+3a)± a/2 (1)注:此距离在试验期间应保持不变。
V型模具式弯曲装置模具的V形槽其角度应为(180°-a)(见图2),弯曲角度a应在相关产品零件图中规定。
模具的支承棱边应倒圆,其倒圆半径应为(1~10)倍试样厚度。
模具和弯曲压头宽度应大于试样宽度或直径并具有足够的硬度。
虎钳式弯曲装置装置由虎钳及有足够硬度的弯曲压头组成(见图3),可以配置加力杠杆。
弯曲压头直径应按照产品标准要求,弯曲压头宽度应大于试样宽度或直径。
. 试样一般要求试验使用圆形、方形、矩形或多边形模截面的试样。
样坯的切取位置和方向应按照相关产品标准的要求。
试样的宽度试样宽度应按照应相关标准产品要求试样的厚度试样厚度应按照应相关标准产品要求试样的长度试样厚度应按照应相关试验装置(设备)要求的长度。
试验程序特别提示:试验过程应采取足够的安全措施和防护措施。
试验一般在10℃~35℃的室温范围内进行按照相关产品的规定,试样在给定的条件和力的作用下弯曲至规定的弯曲角度(见图1、图2和图3)试样弯曲至规定弯曲角度的试验,应将试样放于两支辊(见图1)或V形模具(见图2)上,试样轴线应与弯曲压头轴线垂直,弯曲压头在两支座之间的中点处对试样连续施加力使其弯曲,直至达到规定的弯曲角度。
可以采用图3所示的方法进行弯曲试验。
试样一端固定,绕弯曲压头进行弯曲,直至达到规定的弯曲角度。
弯曲试验时,应当缓慢地施加弯曲力,以使材料能够自由地进行塑性变形。
弯曲时,试验速率应为(1±)mm/s.当使用上述方法如不能直接达到规定的弯曲角度,可将试样置于两平行压板之间(见图4),连续施加力压其两端使进一步弯曲,直至达到规定的弯曲角度。
铝合金材料检验试验规范标准

8.4.1 一般要求
试验使用圆形、方形、矩形或多边形模截面的试样。样坯的切取位置和方向应按照相关产品标准的要求。
8.4.2 试样的宽度
试样宽度应按照应相关标准产品要求
8.4.3 试样的厚度
试样厚度应按照应相关标准产品要求
8.4.4试样的长度
试样厚度应按照应相关试验装置(设备)要求的长度。
0.1 修内容
生效日期
1
全 部
A0
初次发行
2012-07-01
1、 目的:
为了保证铝合金(铝型材)材料的来料质量和满足制程中各项工艺技术要求,特制定本规范。
2、范围:
2.1本规范规定了铝合金(铝型材)材料的技术要求、检验方法、试验方法,检验标准。
2.2本规范适用于本公司外购的所有的铝合金型材材料。
T6:固溶处理后施以人工时效处理,目的在提高材料的强度及尺寸稳定性,适用于冷加工。
7.1.4 工艺性能:
表8 6063工艺性能
工
艺
性
能
密度
2.69
热加工温度
490~510℃
融化温度
655℃
切削加工性%
50
有良好的强度,热态下塑性良好,冷态下,切削加工性好,易焊接,耐蚀性好。良好的抗腐蚀性、韧性,易于抛光、上色膜,阳极氧化效果优良。
2、在抛光完工后,以目力测试检验产品表面,表面的沙孔或杂质点等缺陷影响到外观装饰性的,这样的不良产品按退货处理。
6、 检验方法
6.1 铝合金型材的随机抽样检验按相关抽样规定。
6.2 铝合金型材的外形截面尺寸用游标卡尺测量;长度尺寸用卷尺测量;圆弧面用R规测量。
6.3 铝合金型材的不圆度用游标卡尺对称测量管外径三处,以最大值和最小值之差表示。
完整版锌合金检验标准

锌合金检验标准一、目的适应本公司所有锌合金检验标准检验的需要.二、适用范围适用于我公司锌合金检验标准进料检验及使用过程品质限制.三、权责单位品保人员进行检验时均应遵循四、定义允收水准〔AQL 〕:指抽样方可以接收的不良水准.严重缺陷〔CRI〕:产品功能完全失常或会导致使用者或操作者生命平安之缺陷.主要缺陷〔MAJ 〕:产品局部功能、结构失常或严重的外观不良会导致客户拒收或抱怨的缺陷.次要缺陷〔MIN 〕:产品明显的外观不良可能会导致客户抱怨或包装方面的缺陷.五、检验标准外观检验按GB2828-87 〔MIL-STD-105E 〕单次抽样II级允收水准:致命缺陷CR=0;主要缺陷MA=0.4%次要缺陷MI=1.0%注:有关抽样标准或判定标准可视客户的要求做修订.六、检验条件环境光源:标准光源灯光被检物外表与眼睛距离:30~40cm视线与被检物外表角度:45 土15o检验时间:< 10S检验员视力:裸视或矫正视力在1.0以上且无色盲6.6.1锌合金外观面的定义A面:上显示信息的重要区域,暴露在外,且正常使用时可直接看到的主要外表^B面:暴露在外,且正常使用时并不直接看到的次要外表及外外表,〔比方:转角.倒角及不明显区域〕C面:正常使用时看不到,只有在装卸时才能看到的零件外表.缺陷代码对照表缺陷代码对照表见表1.6.6.2 补充说明a)当缺陷的直径D< 0.05MM且间距超过20MM,可以不视、为缺陷,数目不计;b)以下所提到的不良缺陷的数目均指单面上的不良缺陷数目.七、作业内容外包装检验:物料的包装,要求包装内、外无异物、水、灰尘、破损等情况.现品票及出货报告:要求现品票正确,内容填写完整与实物相符;出货报告格式符合标准、内容工程齐全、清楚、正确、须有结论审核. 结构核对是否同样板相符及各尺寸长、内径、外径是否同图纸.具体检查区分标准:夕卜表无脏污、划伤、变形、毛刺、氧化、缺损、锈斑、益胶、镀层脱落、异色,镀层均匀颜色:要求镀层光亮、颜色均匀、无异色,与样板相符,同批次间颜色相同.材料、结构、激光字体:与样板一致.8.1镀层厚度测试各镀层的厚度符合客人要求及工程图纸要求.8.2附着力测试用锋利刀片〔刀锋角度为 15°〜30° 〕在测试样本外表划 10 X 10个1MM X 1MM 小网格, 每一条 划线应深及镀层的底材;用毛刷将测试区域的碎片刷干净;用粘附力 350〜400G/CM 2的胶带〔3M600 号胶纸或等同〕牢牢粘住被测试小网格,并用橡皮擦用力擦拭胶带,以加大胶带与被测区域的接触面积 及力度;用手抓住胶带一端,在斜方向〔45.〕迅速扯下胶纸,同一位置进行 3次相同试验.结果判定:要求附着力达4B 时为合格.5B -划线边缘光滑,在划线的边缘及交叉点处均无油漆脱落; 4B -在划线的交叉点处有小片的油漆脱落,且脱落总面积小于5%; 3B -在划线的边缘及交叉点处有小片的油漆脱落,且脱落总面积在 2B -在划线的边缘及交叉点处有成片的油漆脱落,且脱落总面积在 1B -在划线的边缘及交叉点处有成片的油漆脱落,且脱落总面积在 0B -在划线的边缘及交叉点处有成片的油漆脱落,且脱落总面积大于注:当测试面积较小时,不要求一定要划10 x 10个小方格,可以根据测试面积的小大确定划格的数目,要求镀层无脱落.8.3耐磨性测试8.3.1用专用的NORMAN RCA 耐磨测试仪〔型号:7 - IBB — 647 〕及专用的纸带〔11/16 INCH WIDE X 6或8 INCH DIAMETER 〕,施加175G 的载荷,带动纸带在样本外表磨擦300个循环.〔注:经外表喷过UV 的产品的测试要求〕 结果判定:试验完成后以镀层不透底时为合格.8.3.2用专用的NORMAN RCA 耐磨测试仪〔型号:7 —旧B — 647 〕及专用的纸带〔11/16 INCHWIDE X 6或8 INCH DIAMETER 〕,施加175G 的载荷,带动纸带在样本外表磨擦 50个循环.〔注:未 经外表喷过UV 的产品的测试要求〕5%〜15 %之间; 15 %〜35 %之间; 35 %〜65 %之间; 65 %.结果判定:试验完成后以镀层不透底时为合格.8.4 耐醇性测试用纯棉布蘸满无水酒精〔浓度A 99.5 %〕,包在专用的500G石去码头上〔包上棉布后测试头的面积约为1CM 2〕,以40〜60次/分钟的速度,20 MM左右的行程,在样本外表往返擦拭200个循环. 结果判定:试验完成后以镀层不透底时为合格.8.5硬度测试用2H铅笔〔三菱牌〕,将笔芯削成圆柱形并在400目砂纸上磨平后,装在专用的铅笔硬度测试仪上〔施加在笔尖上的载荷为500G,铅笔与水平面的夹角为45 ° 〕,推动铅笔向前滑动约5MM长,共划5条,再用橡皮擦将铅笔痕擦拭干净.结果判定:检查产品外表有无划痕,当有2条以下时为合格.8.6耐手汗测试将汗液浸泡后的无纺布贴在产品外表上并用塑料袋密封好,在常温环境下放置48H后,将产品外表的汗液擦拭干净,检查镀层的外观,并测试镀层的附着力、耐磨性.结果判定:产品外表的镀层无异常,附着力及耐磨性测试合格.注:汗液的成份为氨水1.07% ,氯化钠0.48% ,其余为水.8.7 温度冲击测试温度循环次序如下:A〕在温度为-20 C ± 2 C的低温箱内放置1H ;B〕在温度为20 C ± 5 C的常温箱内放置0.5H ;C〕在温度为70 C ± 2 C的高温箱内放置1H ;D〕在温度为20 C± 5 C的常温箱内放置0.5H ;要求:各温度间的切换时间小于1MIN,共做12按个循环〔48H 〕.试验完成后检查产品外表的电镀层无起泡、起皮、镀层脱落等不良现象,并测试镀层的附着力及耐磨性合格.8.8盐雾测试检验设备:盐雾试验箱检验周期、样品个数:每批来料中抽取5pcs检验方法及条件:根据国标GB/T10125-1997,将盐雾试验箱调试温度为35 C,配置盐溶液PH值在6.5〜7.2范围内,溶液浓度为5 土1%盐雾沉降量为1〜2ml/80cm2.h的溶液;将实验品放入烟雾试验箱,试验样品承受连续喷雾试验时间最小为48h.检验判定:试验完毕后用清水冲洗,再用干布擦拭后观察,镀层外表应无脱落、生锈、腐蚀等不良现象,那么判定OK,否那么NG8.9可焊性试验根据标准QJ 2028 - 90对需要焊接的五金电镀件〔如基带屏蔽罩〕进行可焊性试验;试验方法:将引脚浸入免清洗助焊剂中3〜5秒钟取出甩干,再浸入温度为〔235 土5〕 C的焊锡锅内3〜6秒〔焊锡应为63锡即焊锡成份为63%的锡和37%的铅〕,取出自然冷却后,观察焊接牢固、其外表焊锡应分布均匀且外表呈光亮的银白色.8.10镶件螺母的拉力及扭矩测试用拉力计测试螺母的最大破坏拉力大于10Kg.用扭力计测试螺母的最大破坏扭矩大于2.5Kg.检验判定:到达以上测试要求的拉力与扭力未见其它异常为合格.反那么NG.九.备注9.1客户如果有提供标准那么以客户标准为准.9.2本标准如与限度样品相冲突时,以限度样品为准.9.3此检验标准严格按我司要求生产,针对此可靠性测试局部因时间因素,导致我司相关测试未经检测完后,直接导入生产及流入客户端时,如出现是因供应商局部可靠性测试未能通过,一切由该供应商负责.。
铝合金材料检验试验规范方案

范文范例参考铝合金材料检验试验规范制定/日期审核/日期批准/日期文件发行栏□ 执行董事□ 总经理□ 财务总监□ 生产副总□ 财务部□ 管理部□ 计划物料部□ 采购部□ 出口部□ 研发部□ 技术部□ 品保部□ 前加工车间□ 装配车间□ 喷涂车间□ 镜柜车间□ 杭洲湾分部范文范例参考0.1 修改履历序号章节版次修改内容生效日期1全部A0初次发行2012-07-01范文范例参考1、目的:为了保证铝合金(铝型材)材料的来料质量和满足制程中各项工艺技术要求,特制定本规范。
2、范围:2.1 本规范规定了铝合金(铝型材)材料的技术要求、检验方法、试验方法,检验标准。
2.2 本规范适用于本公司外购的所有的铝合金型材材料。
2.3 本规范规定的原材料外形尺寸和表面质量为正常检查项目,化学成分和力学分析为特殊检查项目。
3、职责:3.1 品质部:负责原材料来料检验;3.2 工程技术中心:负责新工艺、新材料的试验;3.3 采购部:负责联系与原材料供应商之间信息反馈及品质要求。
4、内容:4.1 、外形尺寸测量工具:测量工具型号精度游标卡尺0~300mm0.02mm千分卡尺0~ 25mm0.01mm4.2 铝合金型材截面尺寸:技术要求中除技术部门提供的图纸资料中有特殊要求,否则按GB5237.1-2004 执行,铝型材开口尺寸除外。
(见表 1、表 2)。
表 1铝合金型材截面尺寸及允许偏差截面尺寸 /mm公差截面尺寸 /mm公差大于至大于至01±0.11925±0.25 12±0.122538±0.30 23±0.143850±0.36 34±0.1650100±0.61 46±0.18100150±0.86 612±0.20150200±1.12 1219±0.23200350±1.37注:铝型材的长度尺寸按供需双方在订单合同的技术要求约定执行。
铜板原材料检验规范

铜板原材料检验规范
1 目的
通过对铜板原材料的检验确保本厂生产的产品符合生产工艺及客户的质量技术要求。
2 范围
适用于本厂生产用的所有铜板类原材料。
3 验收规则
3.1铜板类的质量由供方技术部门检查和验收。
3.2 供方必须保证交货的铜板符合有关规定,并出具理化检测报告单,本厂将按批次选取样块,送理化室进行复查。
3.3 铜板到厂应附有证明该批铜板符合标准要求和订货合同的质量证明书。
4 外观质量
铜板的表面应清洁,不应有起刺、氧化铜等缺陷。
不应有分层、裂缝、起皮、夹杂和绿锈,但许可有轻微的、局部的、不使板厚超出其允许偏差的划伤、斑点、凹坑、压入物、辊印和修理痕迹等缺陷。
轻微的氧化色、发暗和轻微局部的油迹、水迹,不作为缺陷依据。
板材应平直,但允许有轻微的波浪。
板材的边应切直,无裂边、卷边,允许有轻微的毛刺。
5 尺寸要求
参照铜板类尺寸偏差标准。
6 附表。
- 1、下载文档前请自行甄别文档内容的完整性,平台不提供额外的编辑、内容补充、找答案等附加服务。
- 2、"仅部分预览"的文档,不可在线预览部分如存在完整性等问题,可反馈申请退款(可完整预览的文档不适用该条件!)。
- 3、如文档侵犯您的权益,请联系客服反馈,我们会尽快为您处理(人工客服工作时间:9:00-18:30)。
合金類進料檢驗規程
制訂部門
品保部/品管四課
制訂日期
2001/09/01
編號
TPAQ-10D-308
標題
銅、鋁、鋅合金類原材料進料檢驗規程
版本
A
頁次
1/1
1、主題:本規程規定本公司銅、鋁、鋅合金類原材料進料檢驗項目與要求。
2、範圍:本規程適用於所有采購的銅、鋁、鋅合金類原材料。
≧34.3
/
H62UNS
/
60.5-63.5Cu,0.15Fe,0.08Pb,餘量為Zn,雜質總量<0.5
/
/
ZDC1UNS
Z35531
Cu(0.75-1.25),Al(3.50-4.30),Fe0.10, Mg(0.02-0.06),Pb0.005,Cd0.004, Sn0.003,餘量為Zn
/
/
/
/
修訂記錄/日期/版本/REV
核准
審核
制作
於翔
ZDC2UNS
Z33520
Al(3.50-4.30ቤተ መጻሕፍቲ ባይዱ,Mg(0.02-0.06),Cu max0.20, Fe max0.10,Sn max0.003,餘量為Zn
/
/
ADCI2
A03830
(9.60-12.00)Si,(1.50-3.50)Cu,0.50Mn, 0.30Mg,0.5Ni,1.00Zn,0.30Sn+Fe鋁基
3、抽樣:
3.1每批次隨機抽取所需樣品進行檢測。
3.1.1銅棒每批次截取150mm長試樣。
3.1.2鋁、鋅合金每批次鑽取5g作為為試樣。
4、檢驗與測試:
4.1外觀檢驗
4.1.1表面無裂紋、麻坑、凹陷及嚴重碰傷、拉傷等。
4.1.2形狀規則。
4.1.3表面光洁、無黑斑、黃斑、氧化等情形。
4.1.4呎寸正確(公差依±1T14/2)
4.2測試部份(委托精機室檢測)
牌號
編號
化學成份
拉伸強度
(Kgf/mm2)
伸長率
C3771UNS
C37710
58.0-60.0Cu,1.80-2.1Pb,1.0Fe+Sn,余量Zn
≧32
≧15%
C3604
/
Cu(58.0-60.0),Pb(2.5-3.3),Fe+Sn≦1.2, Fe<0.5,餘量Zn