MSA变速器壳体的加工工艺
变速箱、离合器壳体铸造工艺设计方法

零件机械加工工艺规程是规定零件机械加工工艺过程和方法等的工艺文件。
它是在具体的生产条件下,将最合理或较合理的工艺过程,用图表〔或文字〕的形式制成文本,用来指导生产、管理生产的文件。
一、机械加工工艺规程的容及作用工艺规程的容,一般有零件的加工工艺路线、各工序根本加工容、切削用量、工时定额及采用的机床和工艺装备〔刀具、夹具、量具、模具〕等。
工艺规程的主要作用如下:1.工艺规程是指导生产的主要技术文件。
合理的工艺规程是建立在正确的工艺原理和实践根底上的,是科学技术和实践经历的结晶。
因此,它是获得合格产品的技术保证,一切生产和管理人员必须严格遵守。
2.工艺规程是生产组织管理工作、方案工作的依据。
原材料的准备、毛坯的制造、设备和工具的购置、专用工艺装备的设计制造、劳动力的组织、生产进度方案的安排等工作都是依据工艺规程来进展的。
3.工艺规程是新建或扩建工厂或车间的根本资料。
在新建扩建或改造工厂或车间时,需依据产品的生产类型及工艺规程来确定机床和设备的数量及种类,工人工种、数量及技术等级,车间面积及机床的布置等。
二、制定工艺规程的原则、原始资料〔一〕制定工艺规程的原则制定工艺规程的原则是:在保证产品质量的前提下,以最快的速度、最少的劳动消耗和最低的费用,可靠加工出符合设计图纸要求的零件。
同时,还应在充分利用本企业现有生产条件的根底上,尽可能保证技术上先进、经济上合理、并且有良好的劳动条件。
〔二〕制定工艺规程的原始资料1.产品零件图样及装配图样。
零件图样标明了零件的尺寸和形位精度以及其他技术要求,产品的装配图有助于了解零件在产品中的位置、作用,所以,它们是制定工艺规程的根底。
2.产品的生产纲领。
3.产品验收的质量标准。
4.本厂现有生产条件,如机床设备、工艺装备、工人技术水平及毛坯的制造生产能力等。
5.国、外同类产品的生产工艺资料。
三、制定工艺规程的步骤〔一〕零件图样分析零件图样分析的目的在于:1.分析零件的技术要求,主要了解各加工外表的精度要求、热处理要求,找出主要外表并分析它与次要外表的位置关系,明确加工的难点及保证零件加工质量的关键,以便在加工时重点加以关注。
变速箱壳体零件的加工工艺设计

变速箱壳体零件的加工工艺设计制造技术是一个永恒的主题,是设想、概念、科学技术物化的基础和手段,是国家经济和国防实力的体现,是国家工业化的关键。
工艺技术是制造技术的重要组成部分,提高工艺技术水平是机电产品提高质量、增强国际市场竞争力的有力措施。
传统大批大量生产方式广泛采用高效率的专用组合机床,按流水线排列进行生产,可以极大地降低产品成本,具有很高的产能。
但是,这些适用于大批、大量生产的传统的生产线,都有很大的刚性(专用性),很难迅速改变原有的生产对象,适应市场发展的需求。
发展适应多品种、中小批量、高效率、低成本和具有快速响应市场能力的以先进的制造技术和组织方式为基础的生产系统是未来的发展趋势。
本设计以中国第一拖拉机制造厂的东方红拖拉机变速箱壳体为研究对象,考虑到变速箱壳体为拖拉机中的重要部件,产品要求精度高,结构复杂,因而选择做拖拉机变速箱壳体加工工艺的设计对自己是个挑战又是个锻炼。
一、工艺性分析1.变速箱壳体零件的工艺特点变速箱内装有输入轴、输出轴、其他传动轴和齿轮等。
通过改变安装在这些轴上的滑移齿轮和固定齿轮的传动比,来改变拖拉机的行进速度。
从而可知,变速箱体的主要功用就是支撑个传动轴,保证各轴之间的中心距及平行度,并且保证拖拉机变速箱体部件与其相连接的其他部件的正确安装。
变速箱体的主要技术要求如下:(1)轴承孔的尺寸精度和几何形状精度。
(2)轴承孔孔距公差。
(3)中心线间的平行度公差。
(4)端面对轴承孔的垂直度公差,(5)轴承孔的同轴度公差。
(6)装配基面的平面度公差。
(7)各主要加工表面的粗糙度。
(8)各螺纹孔的位置度。
2.毛坯的工艺性由于灰铸铁具有良好的铸造性和切削性以及较好的耐磨性和减震性,同时价格低廉,因此箱体零件的毛坯通常采用铸铁件。
本箱体材料选用HT150.铸件表面涂以醇酸底漆。
二、机械加工工艺路线的编制1.定位基准的选择对主要定位基准进行分析。
作为一个薄壁壳体腔型零件,它的形状复杂,刚度差,易变形,但加工精度又要求较高。
关于汽车变速器壳体的加工工艺分析

关于汽车变速器壳体的加工工艺分析摘要:在汽车零部件加工生产中,企业能够在激烈的市场竞争中立足的关键在于工艺技术生产的高品质低成本。
变速箱壳体作为汽车变速箱制造中的关键部件,在汽车零部件生产中占据非常重要的地位。
汽车变速箱壳体的加工工艺是汽车产品质量和企业效益的关键因素。
关键词:汽车变速器;壳体;加工工艺;分析研究;前言一、什么是汽车变速器壳体。
汽车变速器壳体就是用于安装变速器传动机构及其附件的壳体结构。
汽车变速器壳体用来安装汽车传动机构、换挡装置和部分操纵机构,同时储存润滑油。
为了减轻汽车的自身重量,对于小型轿车来说,变速器壳体通常采用铝合金或者镁合金制造。
对于中、重型汽车来说则一般采用铸铁制造来保证汽车变速器壳体的强度要求。
二、关于汽车变速器壳体高速加工技术的研究汽车变速器壳体的加工,在国外普遍采用高速加工、高强度刀柄、高效刀具进行基本自动化的加工,而国内相比较国外较多沿用以前的方式,加工效率比国外低百分之五十。
因此对于加工技术的研究迫在眉睫。
1、关于高速切削。
1992年国际生产工程研究会(CIRP)年会主题报告的定义,高速切削指切削速度超过传统切削速度5-10倍的切削加工。
高速切削作为一项综合性的技术需要多方面的配合才能完美进行,高速性能的机床、良好的数控系统、CAD/CAM以及合适的刀具和优化后的加工工艺都缺一不可。
高速切削的切削速度范围并不是相同的,需要根据材料的不同和加工方式的不同进行选择。
高速切削技术在加工过程中,加工效率高、切削力小、切削热对工件的影响小、加工高精度且工序集约化。
但是高速切削仍旧是存在问题的,高速切削技术作为一种全新的切削技术,在目前可供参考的加工参数表很少,可供参考的加工实例也较少,找到合理的加工参数是目前高速切削加工应用中的一个重要问题。
在高速切削过程中找到合适的刀具是一个关键的问题。
不同的刀具与不同的工件材料组合产生不同的效果,选择合适的刀具会在加工过程中增加刀具的使用寿命,将刀具的性能发挥到最大化2、机床的选择。
变速器后壳体数控加工工艺样本

四川职业技术学院毕业设计开题报告四川职业技术学院毕业设计设计题目:变速器后壳体数控加工工艺文献拟订系别:机械工程系专业:数控技术专业班级:姓名:学号:设计小组:指引教师:完毕时间:04月20日毕业设计综合评估表目录绪论....................................... 错误!未定义书签。
1.抄画零件图................................. 错误!未定义书签。
2.零件分析及初拟各表面加工办法............... 错误!未定义书签。
2.1构造工艺分析与解决.................................... 错误!未定义书签。
2.1.1构造工艺性分析.................................... 错误!未定义书签。
2.1.2 难加工地方解决办法 ............................ 错误!未定义书签。
2.2 技术规定.................................................... 错误!未定义书签。
2.2.1加工表面加工方案分析.......................... 错误!未定义书签。
2.2.2该零件各加工表面工序尺寸、加工余量、毛坯尺寸计算错误!未定义书3.工艺分析................................... 错误!未定义书签。
3.1 主轴转速及进给速度计算及拟定.................. 错误!未定义书签。
3.2刀具选取..................................................... 错误!未定义书签。
3.3定位基准选取.............................................. 错误!未定义书签。
4.材料和毛坯................................. 错误!未定义书签。
变速器上壳体工艺规程及夹具设计

编号:沈阳工学院毕业设计(论文)题目:上壳体工艺规程及夹具设计院(系):机电工程系专业:机械设计制造及其自动化学生姓名:学号:指导教师:职称:2015 年5月10 日摘要本设计上壳体零件加工过程的基础上。
主要加工部位是平面和孔加工。
在一般情况下,确保比保证精密加工孔很容易。
因此,设计遵循的原则是先加工面后加工孔表面。
孔加工平面分明显的阶段性保证粗加工和加工精度加工孔。
的基础上,通过输入输出底面作一个良好的基础过程的基础。
主要的流程安排是支持在定位孔过程中的第一个,然后进行平面和孔定位技术支持上加工孔。
整个过程是一个组合的选择工具。
专用夹具夹具的选择,有自锁机构,因此,更高的生产力,对于大批量,满足设计要求。
关键词:工艺,工序,切削用量,夹紧,定位,误差AbstractBased on this design process of shell parts. The main processing part is plane and hole machining. In general, it is easy to ensure precision machining holes than guarantee. Therefore, the design principle is the first processing surface after machining hole surface. Phase plane hole machining obvious to ensure the accuracy of machining and rough machining hole. On the basis of the foundation, through the input and output of the bottom surface as a good basis for the process. The main process is supported in the positioning hole in the process of the first, and then the processing hole plane and hole positioning technology support. The whole process is a combination of selection tool. Special fixture fixture selection, a self-locking mechanism, therefore, higher productivity, in large quantities, meet the design requirements.Key words: process, process, cutting, clamping, positioning, error目录摘要........................................................................................................................................ I I Abstract (III)1 序言 (1)2 零件的分析 (2)2.1 零件的形状 (2)2.2 零件的工艺分析 (2)3 工艺规程设计 (4)3.1 确定毛坯的制造形式 (4)3.2 基面的选择 (4)3.3 制定工艺路线 (4)3.3.1工艺路线方案一 (5)3.3.2 工艺路线方案二 (5)3.3.3 工艺方案的比较与分析 (6)3.4 选择加工设备和工艺装备 (7)3.4.1机床选用 (7)3.4.2选择刀具 (7)3.4.3选择量具 (7)3.5 机械加工余量、工序尺寸及毛坯尺寸的确定 (7)3.6 确定切削用量及基本工时 (9)4 设计钻底面孔夹具 (22)4.1设计分析 (22)4.2设计方案论证 (22)4.3切削力及夹紧力的计算 (22)4.4 设计及操作的简要说明 (23)4.5 结构分析 (23)4.6 夹具的公差 (25)4.7 工序精度分析 (26)5 铣侧面夹具设计 (27)5.1 问题的提出 (27)5.2 夹具设计 (27)5.2.1夹具体设计 (27)5.2.2定位基准的选择 (27)5.2.3定位方案和元件设计 (28)5.2.4定位误差的计算 (28)5.2.5夹紧力计算 (29)5.2.6夹紧机构的设计 (31)5.2.7定向键与对刀装置设计 (32)5.2.8确定夹具体结构尺寸和总体结构 (34)5.2.9夹具设计及操作的简要说明 (35)总结 (36)参考文献 (37)致谢 (38)1 序言机械加工工艺是规定产品或零件机械加工工艺过程和操作方法,是指导生产的重要的技术性文件。
MSA变速器壳体的加工工艺
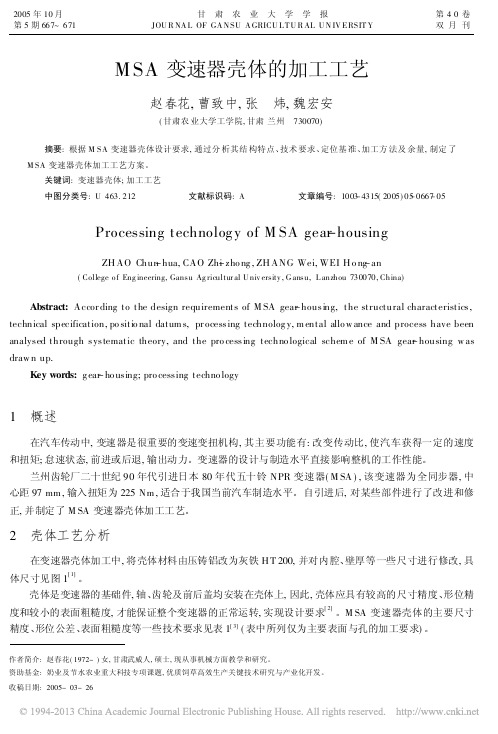
M SA 变速器壳体的加工工艺赵春花,曹致中,张 炜,魏宏安(甘肃农业大学工学院,甘肃兰州 730070)摘要:根据M SA 变速器壳体设计要求,通过分析其结构特点、技术要求、定位基准、加工方法及余量,制定了M SA 变速器壳体加工工艺方案。
关键词:变速器壳体;加工工艺中图分类号:U 463.212 文献标识码:A 文章编号:1003-4315(2005)05-0667-05Processing technolog y of M SA gear -housingZH AO Chun -hua,CAO Zh-i zho ng ,ZH ANG Wei,WEI H o ng -an(College o f Eng ineering,Gansu Ag ricultur al U niv ersity ,G ansu,L anzhou 730070,China)Abstract:Accor ding to the design requirements of M SA gear -housing,the structural characteristics,technical specification,po sitio nal datum s,pr ocessing technolog y,m ental allo w ance and process have been analysed through systematic theory,and the pro cessing techno logical schem e of M SA gear -housing w as draw n up.Key words:g ear -ho using;pro cessing techno logy1 概述在汽车传动中,变速器是很重要的变速变扭机构,其主要功能有:改变传动比,使汽车获得一定的速度和扭矩;怠速状态,前进或后退,输出动力。
变速箱壳体铸造工艺设计

2008 年 9 月
寸过小或切边材料过少时, 材料会被拉入模具间 隙内而成为毛边, 此时必须加大冲裁的搭边尺寸 或切边余量。
3 模具的刃磨
冲压生产中对模具进行合理的刃磨, 可以有 效地提高冲模的寿命, 节省模具费用, 大幅度降低 产品成本。
文章编号: 1001-3814(2008)17-0148-03
1 生产条件
变 速 箱 壳 体 铸 件 材 质 HT200, 铸 件 质 量 82 kg, 外形尺寸 552.5 mm ×513 mm ×488.2 mm, 壁厚
收稿日期: 2007-12-21 作者简介: 吕建强( 1966-) , 男, 江苏 淮 安 人 , 高 级 工 程 师 , 学 士 , 主
[2] 付 翔. 浅 议 模 具 的 使 用 和 管 理 [J]. 现 代 机 械 , 2002, (4): 111-112.
[3] 卢金斌, 张太超 , 张 文 勇 , 等. 高 速 钢 冷 挤 压 凹 模 开 裂 失 效 分 析[J]. 模具工业, 2007, ( 1) : 68-70.
[4] 张文玉, 刘先兰. 模 具 加 工 过 程 中 的 缺 陷 及 其 预 防 措 施[J]. 机床与液压, 2006, ( 11) : 242-245.
4 模具设计要点
外 模 与 型 板 联 接 处 设 计 一 圈 30 mm 宽 、30 mm 高法兰, 以利于增设和改动螺孔和定位销孔, 同时利于在日后的模具维护中重新设置螺孔和定 位销孔。为增加模具的强度, 在模具内腔设置一定 数量的加强筋, 加强筋高度至分型面, 漏模框与外 模之间间隙取 0.5 mm。如图 4 所示。
模具刃磨量必须根据刃口端面和侧面的实际 磨损情况而定, 此外, 还应该考虑材料厚度、凹模 形状结构以及刃磨次序等相关因素。凹模经多次
汽车变速器壳体加工工艺与技术要点研究

0引言汽车变速器壳体作为变速器中的一些非常基础的零部件来说,汽车变速器会把其内部的一些零件按照不同的位置关系来配置成为一个较为完整的装置,以此来确保输出轴的传动比关联进行支撑输出转矩。
在汽车变速器的配置和输出转矩过程中,汽车变速器壳体加工工艺的质量将会直接影响变速器配置的精确程度、汽车的性能、汽车的质量和声音开关的质量、汽车档位的灵活度以及汽车一些零件的使用寿命等。
因此,毫不夸张的说汽车变速器壳体质量的好坏将会严重的影响汽车变速器性能的好坏。
但是,汽车变速器壳体的外观设计具有不规则性,并且需要多重复杂的加工工序,因此加工的技术要点较多。
1市场对汽车变速壳体的需求当前我国的市场竞争在日益加剧,因此想要有效的在如此激烈的市场竞争中脱颖而出就必须要不断提高产品的质量水平。
汽车已经逐渐成为了每家人的生活必需品,而消费者在进行购买汽车的时候会考虑多方面的因素,而汽车变速器的好坏也是消费者购买汽车时所要考虑的一个重要因素,因为变速器质量的好坏将会直接决定汽车在实际行驶中的安全性。
而壳体作为变速器之中较为重要的一个零件,变速器壳体加工水平的不断提升,既能有效的保证汽车变速器的整体性能,更可以保证汽车运行时的稳定性以及符合大气压对于变速器的要求。
在目前我国制造业的市场需求中,随着高新技术的不断发展以及应用,变速器壳体的加工技术不但要符合我国基本的工艺水平,还需要根据变速器的不同特点和具体应用来进行不同工艺的加工,进而可以把汽车变速器中所有的部件都可以顺利的连接起来,以此来满足制造业市场的不同需求并保证汽车制造技术未来的蓬勃发展。
2汽车变速器壳体在变速器部件中的重要作用汽车变速器的基本零部件就是汽车变速器的壳体和离合器的壳体,这些壳体共同对变速器起到了至关重要的保护作用。
对于汽车变速器壳体材料的选择和使用来说,只有选择适合变速器壳体大小、质量以及硬度的材料,这样就会极大的减少汽车变速器的磨损并延长其使用寿命。
除此之外,对于汽车变速器的音量而言,汽车的离合器和变速器壳体能够把所有的变速器零件合理的连接起来并形成一个完整的体系,因此在整个连接的过程中需要对汽车变速器壳体的加工技术有着更高的要求和标准,只有汽车变速壳体的加工较为精细才能有效的减少变速器的噪音污染。
变速箱壳体加工工艺流程
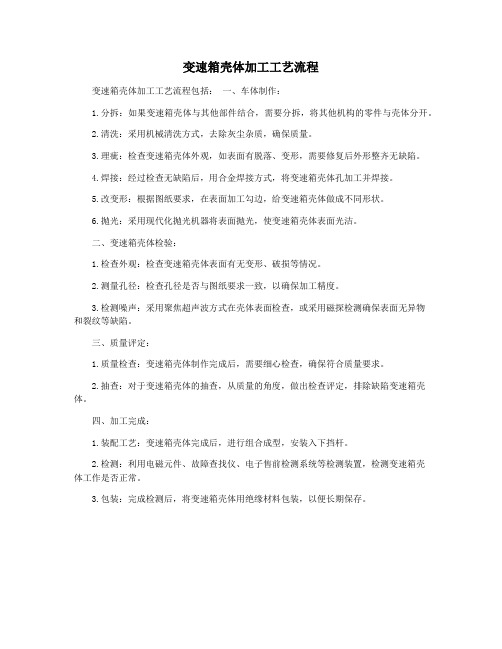
变速箱壳体加工工艺流程
变速箱壳体加工工艺流程包括:一、车体制作:
1.分拆:如果变速箱壳体与其他部件结合,需要分拆,将其他机构的零件与壳体分开。
2.清洗:采用机械清洗方式,去除灰尘杂质,确保质量。
3.理疵:检查变速箱壳体外观,如表面有脱落、变形,需要修复后外形整齐无缺陷。
4.焊接:经过检查无缺陷后,用合金焊接方式,将变速箱壳体孔加工并焊接。
5.改变形:根据图纸要求,在表面加工勾边,给变速箱壳体做成不同形状。
6.抛光:采用现代化抛光机器将表面抛光,使变速箱壳体表面光洁。
二、变速箱壳体检验:
1.检查外观:检查变速箱壳体表面有无变形、破损等情况。
2.测量孔径:检查孔径是否与图纸要求一致,以确保加工精度。
3.检测噪声:采用聚焦超声波方式在壳体表面检查,或采用磁探检测确保表面无异物
和裂纹等缺陷。
三、质量评定:
1.质量检查:变速箱壳体制作完成后,需要细心检查,确保符合质量要求。
2.抽查:对于变速箱壳体的抽查,从质量的角度,做出检查评定,排除缺陷变速箱壳体。
四、加工完成:
1.装配工艺:变速箱壳体完成后,进行组合成型,安装入下挡杆。
2.检测:利用电磁元件、故障查找仪、电子售前检测系统等检测装置,检测变速箱壳
体工作是否正常。
3.包装:完成检测后,将变速箱壳体用绝缘材料包装,以便长期保存。
汽车变速箱壳体加工工艺
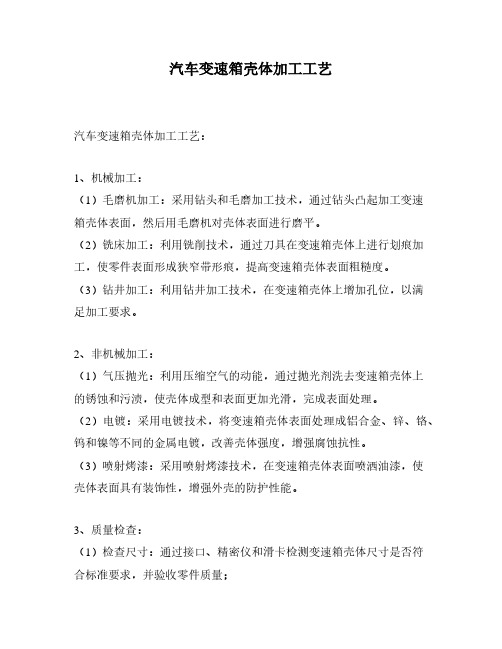
汽车变速箱壳体加工工艺
汽车变速箱壳体加工工艺:
1、机械加工:
(1)毛磨机加工:采用钻头和毛磨加工技术,通过钻头凸起加工变速
箱壳体表面,然后用毛磨机对壳体表面进行磨平。
(2)铣床加工:利用铣削技术,通过刀具在变速箱壳体上进行划痕加工,使零件表面形成狭窄带形痕,提高变速箱壳体表面粗糙度。
(3)钻井加工:利用钻井加工技术,在变速箱壳体上增加孔位,以满
足加工要求。
2、非机械加工:
(1)气压抛光:利用压缩空气的动能,通过抛光剂洗去变速箱壳体上
的锈蚀和污渍,使壳体成型和表面更加光滑,完成表面处理。
(2)电镀:采用电镀技术,将变速箱壳体表面处理成铝合金、锌、铬、钨和镍等不同的金属电镀,改善壳体强度,增强腐蚀抗性。
(3)喷射烤漆:采用喷射烤漆技术,在变速箱壳体表面喷洒油漆,使
壳体表面具有装饰性,增强外壳的防护性能。
3、质量检查:
(1)检查尺寸:通过接口、精密仪和滑卡检测变速箱壳体尺寸是否符
合标准要求,并验收零件质量;
(2)检查表面粗糙度:用毛料测试变速箱壳体表面粗糙度,确定粗糙度是否符合标准要求;
(3)检查材质:通过金相显微镜、纽扣试验和磁粉检查等技术,检查变速箱壳体材料是否合格。
变速箱壳体的数控加工工艺分析

变速箱壳体的数控加工工艺分析成都市技师学院陈本锋摘要:变速箱壳体是数控中常见的典型箱体类零件,由于箱体类零件的槽孔较多、内曲面复杂,加工中的定位、测量等比较困难。
加工中,应本着先面后孔的原则,以变速箱箱体的输入输出轴的轴承孔和顶面两个工艺孔分别作为粗精基准,设计合理的工艺路线,选择正确的夹具刀具,减少废品率、提高加工效率。
关键词:箱体零件;数控加工;工艺分析工艺路线是指零件加工所经过的整个路线,也就是列出工序名称的简略工艺过程。
工艺路线的拟定是制订工艺规程的重要内容,其主要任务是选择各个表面的加工方法,确定各个表面的加工顺序及整个工艺过程的工序数目和工序内容。
数控加工工艺路线的设计与通用机床加工工艺路线的设计的主要区别在于它往往不是只从毛坯到成品的整个过程,而仅是几道数控加工工序工艺过程的具体描述。
因此在工艺路线设计中一定要注意到,由于数控加工工序一般都穿插于零件加工的整个工艺过程中,因而要与其它加工工艺衔接好。
典型箱体类零件63A变速箱壳体如图1所示。
该零件材料为铝合金件,毛坯经压铸喷丸处理,硬度约HB70,质量3.5KG,总高约170毫米,大端面最大尺寸约为300毫米,小端面最大尺寸约为200毫米,小端面及周侧布满了通孔、盲孔和螺纹孔。
图1 零件实物图基于以上产品特征因素,结合企业自身的软硬件条件,加工时使用哈斯(Haas)数控机床,其加工工艺设计如下所述。
1.零件的结构分析该零件属于箱体类零件,工作时与另半个壳体合体,主要起支撑作用,并使各零件之间保持正确的位置关系。
加工后,对零件大小端面的平面度、位置度和同轴度要求比较高。
根据其加工类型,大批量生产应该选择自行设计的专用夹具,并且为了提高生产效率采用工序分散原则。
经过工艺分析,可以把该零件的机械加工共分五道工序完成,主要在立式加工中心(前三道工序)和卧式加工中心(后两道工序)上进行。
多数时候,为了提高数控机床的使用效率,在加工中心上加工之前,都会在普铣上先粗铣大端面,本书介绍的数控编程也是按照在普铣加工后开始设计的。
变速器壳体的加工

内容摘要palio系列汽车是意大利FIAT汽车公司的品牌产品,在全世界汽车市场有很高的知名度。
意大利FIAT公司有100多年生产汽车的经验,我厂生产的变速器是为palio系列汽车配套的专用变速器。
本文以该变速器为例,较详尽介绍了壳体的加工工艺、工装及设备。
同时还讨论了铝合金材料的切削性能,分析计算了加工误差对总成性能的影响。
此外,本文还总结整理了本厂壳体的切削用量,毛坯技术要求等供有关人员参考使用。
最后重点介绍了两壳精加工线为满足工艺要求所采取的必要措施和一个重要典型的工装—随行夹具。
本文图文并茂,以便使读者在设计工艺和选择装备时有所借鉴。
变速器壳体加工1.两壳的作用汽车作为一种商品,在驾驶室里首先触摸的就是变速操纵杆,变速器性能好坏直接影响使用者对整车的评价。
而变速器壳和离合器壳(简称“两壳”)是变速器的基础零件,它把齿轮传动部件、差速器总成以及换档机构接合成一个整体,两壳的加工质量对变速器总成的寿命、噪音、换档轻便灵活性等重要性能指标起决定作用。
这里把变速器壳和离合器壳同时讨论,是由汽车变速器自身结构决定的,见图1,图左边空间主要装有传动齿轮及变速装置,称之为变速器壳,右边凹部空间装有离合器总成,故称之为离合器壳。
两壳只有合成一体才能实现变速、离合的功能。
2.两壳的主要技术要求我们知道若两壳精度不高,齿轮做得再好也没有意义,所以对两壳的技术要求很高。
我厂生产的Palio汽车变速器,由于发动机前置并横置,两壳合件各轴线相互平行,主要孔、面的技术要求如下:2.1.一、二轴及差速器的轴承安装孔径精度均为IT7级;变速器壳上的一、二轴孔为H7,差速器孔为M7;离合器壳上的一、二轴孔为M7,差速器孔为R7,可见离合器壳上的轴承比变速器壳上的轴承配合紧,这是为方便装配而专门设计的。
2.2 三轴线以二轴孔为基准,平行度为0.05,公差等级为7级。
2.3变速器后端面平面度为0.05,公差等级为9级。
2.4一、二轴孔中心距71±0.02,二轴与差速器孔中心距114±0.02,按GB10095-88标准规定约为7级。
变速器外壳机械加工工艺说明书

目录摘要 (3)引言 (5)1.工艺规程的制定 (6)1.1确定生产类型 (6)1.2 零件分析 (6)1.3 工艺规程设计 (12)1.3.1基准选择 (12)1.3.2 表面加工方方案的选择 (13)1.3.3加工阶段的划分 (14)1.3.4 机械加工顺序的安排 (14)1.3.5 工序集中与分散 (16)1.3.6 加工余量及工序尺寸的确定 (17)1.3.7 工序的确定和比较 (17)1.4 工序内容设计 (19)1.4.1 加工设备选择 (19)1.4.2 刀具的选择........................................................ 错误!未定义书签。
1.4.3 确定各工序切削用量...................................... 错误!未定义书签。
2 钻床夹具设计............................................................................ 错误!未定义书签。
2.1钻床夹具的加工方案分析............................................. 错误!未定义书签。
2.2钻床夹具的定位方案分析和夹紧方案分析................. 错误!未定义书签。
2.2.1钻床夹具的定位分析........................................... 错误!未定义书签。
2.2.2 钻床夹具的定位误差分析与计算...................... 错误!未定义书签。
2.2.3夹紧力的计算和气缸的选择............................... 错误!未定义书签。
3 铣床夹具设计 (39)3.1铣床夹具的加工方案分析 (39)3.2铣床夹具的定位方案分析和夹紧方案的分析............. 错误!未定义书签。
变速器加工工艺知识-壳体、轴、齿轮
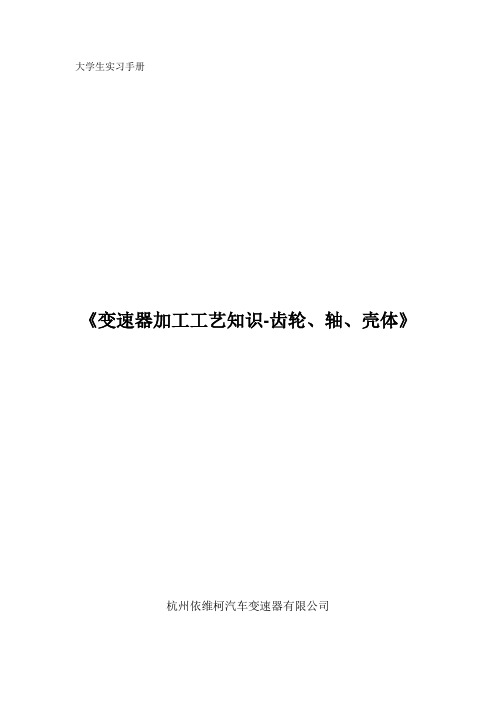
大学生实习手册《变速器加工工艺知识-齿轮、轴、壳体》杭州依维柯汽车变速器有限公司现状描述:目前,我公司生产的汽车变速器主要是采用手动换挡型式,匹配发动机排量为0.8-1.8L,搭载于经济型轿车上。
随着近今年的发展,逐步往自动换档型发展。
变速器主要涉及核心零件轴及齿轮、壳体的生产、总成装配、试验检测等过程在公司内进行。
第一部分:齿轮、轴类零件1.齿轮工艺流程简介:齿轮一般有两种结构:根据不同结构要求.齿轮零件加工主要工艺流程采用的是锻造制坯→正火→精车加工→插齿→倒尖角→滚齿→剃齿→(焊接)→热处理→磨加工→对啮修整。
热后齿部一般不再加工,除了主减从齿或顾客要求磨齿的零件。
2.轴类工艺流程简介:输入轴:锻造制坯→正火→精车加工→搓齿→钻孔→插齿→倒尖角→滚齿→剃齿→热处理→磨加工→对啮修整。
输出轴:锻造制坯→正火→精车加工→搓齿滚齿→剃齿→热处理→磨加工→对啮修整。
3.具体工艺流程简介:详细介绍如下:(1)锻造制坯:热模锻是汽车齿轮件广泛使用的毛坯锻造工艺。
以前较广泛采用的是热锻和冷挤压的毛坯,近年来,楔横轧技术在轴类加工上得到了大量推广。
这项技术特别适合为比较复杂的阶梯轴类制坯,它不仅精度较高、后序加工余量小而且生产效率高。
比如我公司生产的H331.6A及H319.5A的轴类毛坯就是采用楔横轧,现在已逐步实现了批量生产。
(2)正火:这一工艺的目的是获得适合后序齿轮切削加工的硬度和为最终热处理做组织准备,以有效地减少热处理变形。
公司所用齿轮钢的材料通常为20CrMnTi(H)及20MnCr5,一般的正火由于受人员、设备和环境的影响比较大,使得工件冷却速度和冷却的均匀性难以控制,造成硬度散差大,金相组织不均匀,直接影响机加工和最终热处理;使得热变形大而无规律,零件质量无法控制,对刀具的磨损也较大,尤其对搓齿这种受力大的工序更是明显。
为此,采用等温正火工艺。
实践证明,采用这种等温正火有效地改变了一般正火的弊端,产品质量稳定可靠。
变速箱壳体制造工艺

变速箱壳体制造工艺零件图三维图1、零件工艺性分析(1)技术精度要求①变速箱壳体在结构上壁薄而多孔,整个容腔为三组平行孔系所占据。
②为提高传动精度,应保证装在三组平行孔系中的轴承获得良好的配合精度,故Φ48025.00+、Φ80030.00+及Φ146040.00+三孔均有较高的尺寸精度要求;除此而外,为保证传动平稳和减少噪声,三组平行孔系之间还有较高的孔距公差。
③因总体结构和部件位置的限制,在变速箱壳体的中间部位,有两块面积不大的外伸安装面。
为整个变速箱的安装基面,且与Φ146孔中心有较高的尺寸要求,其数值为124.1±0.05mm 。
保证了传动位置和传动精度的准确性。
(2)材料特性、加工方案及工艺措施①变速箱壳体的材料ZLl07为铝硅铜合金,硬度低但比强度较高,其金相组织为硅在铝内的固溶体+共晶体组成。
切削加工性能较好,因含有硅,故易使刀具磨损。
又因ZLl07材料熔点较低,在切削中易产生积屑瘤,会影响工件的表面粗糙度及尺寸精度,因此,应充分考虑工件材料的热变形,减少刀面同工件的摩擦,要求刀具刃口必须锋利,不采用倒棱。
②按材料特性,选钨钴类YG8镗刀作为粗镗刀具; YTl5及W18Cr4V 作为精镗刀具。
③加工时应遵循基准(面)先行、先粗后精的原则。
首先对平面和孔进行粗加工,再半精加工基准面、孔,消除粗加工时所产生的变形,以确保壳体的高精度要求。
④按照传动路线和齿轮的传动关系,应先镗Φ146040.00+孔,其次镗Φ48025.00+孔,最后镗 Φ80030.00+孔,保证三组平行孔系孔距间获得较高的尺寸精度,并注意必须换算坐标尺寸。
孔Φ146与孔Φ48的坐标位置关系如下:水平方向位移量 Χ1=18mm垂直方向位移量 y 1=2218)5.142(-=141.36mm 孔Φ48与孔Φ80的坐标位置关系如下:水平方向位移量 Χ2=68mm垂直方向位移量 y 2=226887-=54.27mm⑤由于该变速箱壳体的安装基面“B ”面积较小,在镗削加工过程中无法作为定位基准,由于A 面与三组平行孔系有0.02mm 的垂直度要求,B 面对A 面有0.01mm 的垂直度要求,所以从粗加工开始就必须注意保证该零件孔与面及面与面的垂直度要求。
汽车变速器壳体加工工艺研究

汽车变速器壳体加工工艺研究汽车变速器是汽车传动系统的重要组成部分,其性能和可靠性直接影响着汽车的传动效率和行驶安全性。
而变速器壳体作为变速器的核心部件,其加工工艺的优劣直接关系到变速器的整体性能和寿命。
因此,对汽车变速器壳体加工工艺的研究具有重要意义。
汽车变速器壳体加工工艺主要包括以下环节:原材料的选取、毛坯的制备、定位与装夹、切削参数的选择、刀具的选择与优化、冷却液的使用等。
然而,在现有的研究中,仍存在一些问题和空白。
在切削参数和刀具选择方面,大多研究仅于单一因素对加工效率的影响,而忽略了多因素协同作用对加工效果的影响。
在冷却液的使用上,如何合理选择冷却液种类和喷洒方式以提高加工效率和表面质量仍需进一步探讨。
本研究采用文献综述法和实验研究法相结合的方式进行。
通过查阅相关文献了解汽车变速器壳体加工工艺的研究现状和发展趋势。
设计并制定实验方案,选择不同切削参数和刀具进行分组实验,并记录加工时间、表面质量、刀具磨损等数据。
同时,对冷却液种类和喷洒方式进行优化实验,以确定最佳方案。
通过实验数据对比分析,发现切削速度、进给速度、刀具角度和冷却液种类等多种因素对加工效率和表面质量均有显著影响。
在切削参数方面,提高切削速度和进给速度可有效提高加工效率,但同时也会增加刀具磨损和表面粗糙度。
在刀具选择方面,硬质合金刀具具有较高的耐用度和切削速度,而陶瓷刀具则具有更好的抗高温性能和切削速度。
在冷却液使用方面,采用高渗透性冷却液和合适的喷洒方式可以有效降低刀具磨损和表面粗糙度,提高加工效率。
本研究通过对汽车变速器壳体加工工艺的研究,发现合理的切削参数和刀具选择以及冷却液的有效使用能够显著提高加工效率和表面质量。
然而,本研究仍存在一定局限性,例如实验条件的高度简化可能无法完全反映实际生产中的复杂环境。
展望未来研究方向,我们建议进一步探讨以下问题:如何在保证加工效率的提高变速器壳体的精度和降低生产成本?如何更加有效地利用高速切削技术,以进一步提高切削速度和进给速度?可以进一步研究新型刀具材料和冷却液种类及其在变速器壳体加工中的应用,以促进变速器壳体加工工艺的持续改进和发展。
变速器壳体加工工艺设计及组合钻床的设计说明书DOC

目录摘要 (IV)ABSTRACT (IV)1前言 (1)1.1背景和意义: (1)2加工工艺的设计 (2)2.1变速器壳体的结构分析 (3)2.2零件的技术要求 (4)2.3变速器壳体的设计要求 (4)3工艺规程的制定 (5)3.1变速器壳体材料及毛坯 (5)3.2定位基准的选择 (6)4工艺路线的拟定 (6)4.1毛坯加工余量的确定及工序尺寸的确定 (8)5 专用机床的设计 (8)5.1组合机床结构方案的确定 (8)5.2组合机床配置的选择 (9)5.3被加工零件的工序图 (10)5.4零件的加工示意图 (12)6 合机床联系尺寸图的绘制 (20)6.1机床装料高度的确定 (21)6.2选用动力部件 (21)6.2.1滑台的选用 (21)6.2.2动力箱的选用 (22)6.2.3确定导向装置的尺寸 (23)6.3中间轮廓尺寸的确定 (24)7结论 (25)参考文献 (26)谢辞 (27)摘要本次设计的主要内容是变速器壳体加工工艺及组合钻床的设计,加工工艺对机械产品的质量好坏起着举足轻重的作用,如果在加工一个产品的时候工艺编的不够合理直接会影响产品的质量,同时也会使产品的生产率受到很大的限制,所以加工工艺对于机械产品的影响是不言而喻的,特别是对于加工精度很高的零件而言,设备的先进与否和工艺都是非常重要的。
组合机床是由一些通用部件和专用部件组成的为了使设计的组合机床既能满足预期的性能要求,又要做到配置上的均匀合理,符合多快好省的精神,所以必须对所设计的组合机床各个部件之间的关系进行全面的分析研究,特别是其中重要的几步:机床装料高度的确定;机床通用部件的选择。
最后对自己做的设计进行了进行了全面的总结,使自己的知识得到了融会贯通,受益匪浅。
关键字:钻削;工艺;性能;部件;精确度ABSTRACTThe design of transmission are the main contents of the shell processing technology design and composition of the drilling machine. Processing on the quality of the product quality of machinery play a decisive role. If a product in the processing time for the lack of reasonable directly affect the quality of the products. At the same time the productivity of products will also be greatly restricted, so processing technology for the impact of mechanical products is self-evident, Especially for high precision machining of parts, equipment and advanced technology are not very important Machine tools by some combination of common parts and components for the design in order to make the combination of machine tools meet the expected performance requirements. Have to be configured on the uniform and reasonable, in line with the spirit of commerical and convenience, it must be designed by a combination of various machine components of the relationship between a comprehensive analysis and study.In particular the important steps are the determination of a high degree of loading machine , universal machine parts choice. Finally, do their own design for a comprehensive summary, so that their knowledge has been comprehensively and benefited from.Key words: drilling; processing; components; precision1前言1背景和意义:制造业是国民经济的支柱,而机械制造业是其中最大的一个产业,被称为永远不落的太阳。
汽车变速器壳体加工工艺与技术要点研究

汽车变速器壳体加工工艺与技术要点研究汽车变速器壳体是汽车变速器的重要组成部分,它的加工工艺和技术对于汽车变速器的性能和质量有着至关重要的影响。
本文将从加工工艺和技术要点两个方面进行探讨。
一、加工工艺1.铸造工艺:汽车变速器壳体通常采用铸造工艺进行生产。
铸造工艺的优点是生产效率高,成本低,可以生产出形状复杂的零件。
但是,铸造工艺也存在一些缺点,如铸造缺陷、气孔、夹杂等问题,需要通过严格的质量控制来保证产品质量。
2.机加工工艺:汽车变速器壳体的机加工工艺包括车削、铣削、钻孔、镗孔等。
机加工工艺的优点是可以生产出高精度、高质量的零件,但是机加工工艺也存在一些问题,如加工难度大、加工成本高等。
3.热处理工艺:汽车变速器壳体需要进行热处理,以提高其硬度和强度。
常用的热处理工艺包括淬火、回火、正火等。
热处理工艺的优点是可以提高产品的性能和质量,但是也需要严格的控制温度、时间等参数,以保证热处理效果。
二、技术要点1.材料选择:汽车变速器壳体的材料通常采用铝合金、铸铁等。
材料的选择需要考虑到产品的使用环境、负荷等因素,以保证产品的性能和寿命。
2.加工精度控制:汽车变速器壳体的加工精度对于产品的性能和质量有着至关重要的影响。
加工精度的控制需要从加工设备、工艺参数、工人技能等方面入手,以保证产品的精度和一致性。
3.质量控制:汽车变速器壳体的质量控制需要从原材料、加工工艺、热处理等方面入手,以保证产品的质量和可靠性。
质量控制需要建立完善的检测体系和质量管理体系,以及严格的质量标准和检测方法。
汽车变速器壳体的加工工艺和技术要点对于产品的性能和质量有着至关重要的影响。
只有通过严格的质量控制和技术创新,才能生产出高质量、高性能的汽车变速器壳体,以满足市场需求和用户需求。
变速器副箱壳体加工工艺及夹具设计

变速器副箱壳体加工工艺及夹具设计第Ⅰ页共Ⅰ页目次1 引言 (1)2 变速箱副箱加工工艺 (2)2.1箱体的结构特点、材料、毛坯及热处理 (2)2.1.1箱体的结构特点 (2)2.1.2箱体的材料、毛坯及热处理 (2)2.2变速器副箱壳体加工工艺过程及分析 (3)2.2.1变速器副箱壳体的主要技术要求 (3)2.2.2变速器副箱壳体的机械加工工艺分析 (5)2.3 主要表面的加工 (8)2.3.1箱体的平面加工 (8)2.3.2主轴孔的加工 (8)2.4 定位基准的选择 (8)2.4.1粗基准的选择 (9)2.4.2精基准的选择 (9)3 夹具设计 (11)3.1 设计任务分析 (11)3.2 计及操作的简要说明 (11)3.3 夹具的公差 (12)3.4定位销尺寸确定与高度计算 (13)3.4.1定位销尺寸的确定 (14)3.4.2定位销高度的计算 (14)结论 (15)致谢 (15)参考文献 (15)Title (16)Abstract (16)变速器副箱壳体加工工艺及夹具设计作者:xx 指导老师:李兵安徽农业大学工学院05级机制合肥230036摘要:本设计先对箱体副箱结构特点、材料毛胚、及热处理的分析,通过对545-H变速器壳体零件图的分析及结构形式的了解,从而对变速器副箱进行工艺分析、工艺说明及加工过程的技术要求和精度分析。
而后对变速器箱体的轴承孔、平面加工进行夹具设计与精度和误差分析,制定出相关工艺路线,及相关刀具切削用量的确定。
该工艺与夹具设计结果能应用于生产要求。
关键词:变速器加工工艺定位夹具设计1 引言箱体是机器和部件的基础零件,由它将机器和部件中许多零件连接成一个整体,并使之保持正确的相互位置,彼此能协调地运动.常见的箱体零件有:各种形式的机床主轴箱.减速箱和变速箱等汽车作为一种商品,在驾驶室里首先触摸的就是变速操纵杆,变速器性能好坏直接影响使用者对整车的评价。
而变速器壳和离合器壳(简称“两壳”)是变速器的基础零件,它把齿轮传动部件、差速器总成以及换档机构接合成一个整体,两壳的加工质量对变速器总成的寿命、噪音、换档轻便灵活性等重要性能指标起决定作用。
- 1、下载文档前请自行甄别文档内容的完整性,平台不提供额外的编辑、内容补充、找答案等附加服务。
- 2、"仅部分预览"的文档,不可在线预览部分如存在完整性等问题,可反馈申请退款(可完整预览的文档不适用该条件!)。
- 3、如文档侵犯您的权益,请联系客服反馈,我们会尽快为您处理(人工客服工作时间:9:00-18:30)。
MSA 变速器壳体的加工工艺赵春花,曹致中,张 炜,魏宏安(甘肃农业大学工学院,甘肃兰州 730070)摘要:根据MSA 变速器壳体设计要求,通过分析其结构特点、技术要求、定位基准、加工方法及余量,制定了MSA 变速器壳体加工工艺方案。
关键词:变速器壳体;加工工艺中图分类号:U 463.212 文献标识码:A 文章编号:1003-4315(2005)05-0667-05Processing technoIogy of MSA gear-housingZHAO Chun-hua ,CAO Zhi-zhong ,ZHANG Wei ,WEI Hong-an(CoIIege of Engineering ,Gansu AgricuIturaI University ,Gansu ,Lanzhou 730070,China )Abstract :According to the design reguirements of MSA gear-housing ,the structuraI characteristics ,technicaI specification ,positionaI datums ,processing technoIogy ,mentaI aIIowance and process have been anaIysed through systematic theory ,and the processing technoIogicaI scheme of MSA gear-housing was drawn up. Key words :gear-housing ;processing technoIogy1 概述在汽车传动中,变速器是很重要的变速变扭机构,其主要功能有:改变传动比,使汽车获得一定的速度和扭矩;怠速状态,前进或后退,输出动力。
变速器的设计与制造水平直接影响整机的工作性能。
兰州齿轮厂二十世纪90年代引进日本80年代五十铃NPR 变速器(MSA ),该变速器为全同步器,中心距97mm ,输入扭矩为225Nm ,适合于我国当前汽车制造水平。
自引进后,对某些部件进行了改进和修正,并制定了MSA 变速器壳体加工工艺。
2 壳体工艺分析在变速器壳体加工中,将壳体材料由压铸铝改为灰铁HT200,并对内腔、壁厚等一些尺寸进行修改,具体尺寸见图1[1]。
壳体是变速器的基础件,轴、齿轮及前后盖均安装在壳体上,因此,壳体应具有较高的尺寸精度、形位精度和较小的表面粗糙度,才能保证整个变速器的正常运转,实现设计要求[2]。
MSA 变速器壳体的主要尺寸精度、形位公差、表面粗糙度等一些技术要求见表1[3](表中所列仅为主要表面与孔的加工要求)。
作者简介:赵春花(1972-)女,甘肃武威人,硕士,现从事机械方面教学和研究。
资助基金:奶业及节水农业重大科技专项课题,优质饲草高效生产关键技术研究与产业化开发。
收稿日期:2005-03-262005年10月第5期667~671甘 肃 农 业 大 学 学 报JOURNAL OF GANSU AGRICULTURAL UNIVERSIT 第40卷双月刊图1 MSA 变速器壳体图Fig l The graph of MSA gear-housing2.1 结构特点及技术要求壳体是变速器的基础件,变速器的装配在很大程度上取决于壳体的加工精度。
MSA 壳体是不规则箱体,加工面为断续平面和内表面,顶平面与上盖安装误差要求很小,四个主要轴承孔尺寸不等,精度等级IT6,并要求具有较小的同轴度误差。
另外,这种变速器设计紧凑,齿轮与壳体间隙较小,安装倒档惰轮处外壳呈圆弧密闭状态,给加工造成一定困难,总之,该壳体的结构特点决定了工艺的难度。
如果壳体加工达不到要求,则装配困难,使变速器无法正常工作。
从技术要求方面看,尺寸精度最高IT6,平面度、平行度、垂直度均为0.05mm ,表面粗糙度最高l.6,螺纹精度6H 。
表1 MSA 变速器壳体的主要尺寸精度、形位公差、表面粗糙度[4]Tab l The main size accuracy form tolerances and surface smooth of MSA gear-housing编号项目精度及其它要求(mm )粗糙度(!m )l 总长330.5+0.l2大平面平面度0.053.23两销孔2-!l0+0.0050.030l.64一轴轴承孔!l00+0.0l6-0.006(!6)l.65二轴轴承孔由4.5孔轴线为基准轴线P !90+0.0l6-0.006(!6)l.66副轴前轴承孔!75+0.0l3-0.0006(!6)l.67副轴后轴承孔!80+0.0l5-0.006(!6)l.686、7轴线与P 的平行度ll0.05中心距970.059倒档惰轮孔(外)!22+0.02l-0("7)3.2倒档惰轮孔(内)!22+0.0l20.009(!7)3.2l0两侧面平面度0.05 6.3垂直度0.05对#拨叉支点孔26l.510.l ll支点轴线ll0.05对$866 甘肃农业大学学报 2005年!.! 定位基准孔系产品加工精度要求高,为使壳体工件定位稳定可靠,需选一个较大的平面作为统一的定位基准。
精基准的选择有以下两种。
六点定位:该方法简单易行,装卸方便,但此法受毛坯精度变化的极大限制,二次装夹定位误差大,在工序多的情况下达不到加工要求,而且与设计、装配基准不重合。
一面两销定位:该方法定位精度高,而且稳定可靠,二次装夹可控制误差,与设计、装配基准重合,易标准化,便于组织生产与流水作业,缺点是装卸不便。
根据精度和稳定性要求,经比较,选择后一种定位方法。
精基准选定后,就要选用为加工精基准用的粗基准,应考虑的问题是: 1)轴承孔是最主要的表面,所选粗基准应保证孔的加工余量基本均匀; 2)要保证齿轮与壳体不发生空间干涉。
为满足以上要求,根据生产条件,采用三轴孔定位铣大面,六点定位钻-铰两孔。
!." 工艺方法壳体的加工面有平面加工方法和孔加工方法。
2.3.1 平面加工方法 壳体几个主要大平面表面粗糙度为3.2,平面度0.05,两侧面与基准线 的垂直度0.05。
根据这些要求,宜选用粗铣-精铣平面,故采用大平面、两侧面、取力孔窗口等用立铣、卧铣加工,在精镗孔时,还可精铣一个侧面,以保证该面与轴孔的垂直度公差。
值得研究的是,倒档惰轮挡距小平面的加工,该平面为圆弧面!44,表面粗糙度1.6,中间为!22H7的孔,此平面位于壳体内半封闭状态,在没有专用设备的情况下,加工相当困难。
本工艺采用在倒档惰轮轴孔加工完毕后,以一面两孔定位,利用可插卸式单刀铣,先将刀杆伸进!22孔,装进刀头后再进行切削,以达到图纸要求。
2.3.2 孔加工方法 孔的加工主要是四个轴承孔和一个倒档惰轮轴孔,最高公差等级IT6[5],两轴线平行度0.05mm ,表面粗糙度1.6,中心距公差均为0.05mm ,轴线与两侧面有0.05的垂直度要求。
要达到这些要求,确定它们的加工方法,需先考虑一面两销的定位误差。
图2所示为工件两销孔的尺寸精度与定位时销与孔间的间隙产生的转角误差"!。
工件中心距 :[6] max =245.052+167.55!2=296.854mm min =244.952+167.45!2=296.715mm所以 =296.78510.069mm两定位销中心距公称尺寸 应: = ,且夹具两销间中心距公差取工件公差的1/3,故: =296.78510.0235mm 图!#工件两销孔定位误差Fig 2 The Iocating accuracy of twoIocation pin hoIes夹具两定位销一为销圆销 1,一为菱形销 2,1="10-0 03="9 97mm ,公差带取g6,这样: 1="9 970 0050 014="100 3550 044mm 确定菱形销 2,中心距补偿量( 1的最小间隙)#=" +" -12"=0.069+0.0235-12X 0.005=0.09mm 菱形销园柱部分宽取b =3mm ,与孔的最小间隙"2=2#bD 2=2X 0.09X 39097=0.054mm (D 2为工件孔最小直径),所以 2=9.97-0.054=9.92mm ,公差带取h6。
这样, 2=9.920-0.011=$10-0.080.091mm966第5期 赵春花等:MSA 变速器壳体的加工工艺当!l ,!2尺寸确定后,可以计算两销定位的转角误差!",两销的最大间隙!lmax、!2max分别为:!lmax=l0.005-9.956=0.049mm;!2max=l0.005-9.909=0.096mm!!=tg-l(!lmax+!2max2")=tg-l(0.049+0.0962X296.785)=0.0l4(5.04")因此,由!!反映到壳体总长两端轴孔的不同轴度、轴与侧面的不垂直度误差将为:330.5X tg!!=0.08l mm这样,若镗孔从两侧分别进行时,通过两次装夹,产品的同轴度、侧面与轴线的垂直度、两轴线的平行度都难以得到保证,会出现这样的情况,即当夹具两销中心距与工件两孔中心距愈吻合时,转角误差反而加大,而吻合度较差时,转角误差反而减少。
因此,对应的加工方法应有两种:一是提高工件两销孔的尺寸精度和中心距精度,以获得小的转角误差;二是从单侧一次装头,一次精镗双孔。
第一种方法虽可使工件精度提高,但加工困难,不经济,夹具制造有困难,第二种方法可行。
所以,四轴承孔的加工方法是:粗扩—半精—精镗,其中半精镗、精镗从单侧用两刀头一次镗成。
倒档惰轮轴孔的加工方法是:钻—扩—复合铰。
根据现有设备情况,孔的加工在坐标镗床上进行,其它孔、螺孔在摇臂钻床上利用回转钻模两次完成底孔加工,最后分别攻丝(机攻)。
2.3.3 加工阶段的划分壳体主要表面的要求较高,应根据以下原则[7]:即先粗后精,先基准后一般,先平面后孔,先主要表面后次要表面。
可初步安排壳体加工工艺方法如下:精基准的加工:a粗铣大平面,精铣大平面;D钻、铰大平面两定位销孔,附带钻大平面螺纹孔。
当侧面毛坯余量不稳定时,可加一粗铣侧面(毛基准)。
主要表面(轴孔)的加工:a粗铣两侧面;D粗扩四轴孔;c半精镗,精镗四轴孔;c精铣侧面;e钻、扩,复合铰倒档惰轮四轴孔。
次要表面(轴孔)的加工:a取总长;D铣倒档惰轮档距;c铣窗口;c铣其余螺纹底孔及过油孔、拆卸孔,附带锪若干小平面。
由于轴孔系零件的加工中废品率较一般工序高,因此,须把它们的精加工放在次要表面加工前进行,这样可以避免由于轴孔系精加工出现废品而使次要表面加工的工时白白浪费。