三十万吨年直馏柴油醇氨法化学精制装置设计书
年产30万吨合成氨课程设计

年产30万吨合成氨课程设计目录1概述 (2)1.1设计题目 (2)1.2 设计具体内容范围及设计阶段 (2)1.3设计的产品的性能、用途及市场需要 (2)1.4设计任务的依据 (3)1.5 产品方案 (4)2 技术分析 (4)2.1合成氨反应的特点 (4)2.2合成氨反应的动力学 (4)2.2.1反应机理 (4)2.3氨合成工艺的选择 (5)2.4系统循环结构 (5)2.5分离工艺 (6)3 生产流程简述 (6)4 工艺计算 (7)4.1 原始条件 (7)4.2 物料衡算 (8)4.3热量衡算 (16)5主要设备选型 (24)5.1 废热锅炉设备工艺计算 (24)5.2主要设备选型汇总表 (26)5.3主要设备图 (27)6设计心得 (29)参考文献 (30)1.概述1.1设计题目:年产30万吨合成氨合成工段设计1.2 设计具体内容范围及设计阶段本次设计的内容为合成氨合成工段的设计,具体包括以下几个设计阶段:1. 进行方案设计,确定生产方法和生产工艺流程。
2. 进行化工计算,包括物料衡算、能量衡算以及设备选型和计算。
3. 绘制带控制点的工艺流程图。
4. 进行车间布置设计,并绘制设备平立面布置图。
5. 进行管路配置设计,并绘制管路布置图。
6. 撰写课程设计报告。
1.3设计的产品的性能、用途及市场需要(1) 氨的物化性能合成氨的化学名称为氨,氮含量为82.3%。
氨是一种无色具有强烈刺激性、催泪性和特殊臭气的无色气体,比空气轻,相对密度0.596,熔点-77.7℃;沸点-33.4℃。
标准状况下,1米3气氨重0.771公斤;1米3液氨重638.6公斤。
极易溶于水,常温(20℃)常压下,一个体积的水能溶解600个体积的氨;标准状况下,一个体积水能溶解1300个体积的氨氨的水溶液称为氨水,呈强碱性。
因此,用水喷淋处理跑氨事故,能收到较好的效果。
氨与酸或酸酐可以直接作用,生成各种铵盐;氨与二氧化碳作用可生成氨基甲铵,脱水成尿素;在铂催化剂存在的条件下,氨与氧作用生成一氧化氮,一氧化氮继续氧化并与水作用,便能得到硝酸。
30万吨年气体分馏装置 第二章 操作指南

30万吨/年气体分馏装置操作规程第二章操作指南2.1.初分岗位系统操作指南2.1.1初分岗位系统操作原则初分岗位的任务是将净化液态烃分离为纯度合格的混合碳二、碳三馏分和混合碳四、碳五馏分,并分离出纯度合格的混合碳三馏分中的碳二组分,为下游精分岗位和尾分岗位的平稳生产创造条件;严格执行本岗位的工艺操作指标,按生产方案要求,控制合理的塔底温度和塔顶温度,以及合理的回流比,及时和气体脱硫装置以及丙烯球罐保持生产联系,以保证原料量的稳定,保证脱丙烷塔和脱乙烷塔的正常生产;负责本岗位的开停工和事故处理;确保和二套催化装置热联合工艺的正常生产;做好本岗位工艺设备及相关的工艺管线的巡检和日常维护工作,做好交接班和原始记录;调节过程要认真细致,避免大幅度波动;完成车间下达的有关生产指令和任务。
岗位管辖范围:脱丙烷塔塔-1、脱乙烷塔塔-2及所有进入初分岗位区域的设备和工艺管线均属本岗位管辖,包括本岗位的消防及安全设施。
2.1.2 分馏岗位操作的主要内容(1)检查并凋节各设备的温度、压力、液面、流量。
(2)按工艺指标,参照产品质量分析,调整操作确保产品质量。
提高产品收率,降低消耗。
(3) 维护、管理、使用设备。
2.1.3 分馏岗位操作员须知(1)要熟炼掌握本岗位、各系统的工艺流程和仪表控制流程。
(2)要懂设备的作用构造、原理。
(3)要懂工艺基本原理,主要工艺参数控制的意义和相互之间的关系。
(4)要懂产品质量的含量和与工艺条件之间的关系。
(5)要知道本岗位或系统的特点。
(6)要会使用仪表。
2.1.4 气体分馏塔的特点(1)分馏塔的操作参数为压力、温度、流量、液面。
压力和温度是影响产品质量的主要参数。
(2)分馏塔的压力波动会直接影响系统的温度、流量、液面的平稳,所以要搞好平稳操作,主要应抓好压力稳定。
(3)分馏塔系统的压力,主要取决于塔顶产品的组成和塔顶产品冷凝后的温度。
(4) 调节回流对塔顶、底温度都有一定的影响,如果回流量增大,会引起塔的压力、温度上升,影响产品质量。
毕业设计 30万吨每年甲醇精馏工段 常压精馏塔工艺设计及分析

54.0
19.0
甲酸乙酯HCOOC2H3
54.1
50.9
16.0
双甲氧基甲烷甲醛
42.3
41.8
8.2
丁酮CH3COC2H5
79.6
63.5
70.0
丙酸甲酯C2H5COOCH3
79.8
62.4
4.7
甲酸炳酯HCOOC3H7
80.9
61.9
50.2
二甲醚(CH3)2O
38.9
38.8
10.0
乙醛缩二甲醇
Key words: methanol distillation, atmospheric distillation, ASPEN simulation, flowsheet
第一章
甲醇(CH3OH,英文名称Methanol)是最简单的饱和脂肪醇。大约有90%的甲醇用于化学工业,作为生产甲醛、甲基叔丁基醚、醋酸、甲酸甲酯、氯甲烷、甲胺、二甲醛等的原料,还有10%用于能源工业。在基础有机化工原料中,甲醇消费量仅次于乙烯、丙烯和苯。甲醇深加工产品目前己达120多种,中国以甲醇为原料的一次加工产品近30种。甲醇作为最主要的基本有机化工原料之一和替代能源的一部分,在当前全球化工产品市场上起着举足轻重的作用。“九五”期间国内甲醇需求将以15%~20%速度递增,2000年需求达到210万吨。如何进一步节能降耗和提高产品质量越来越引起人们的关注。
甲醇可以任意比例同多种有机化合物互溶,并与其中的一些有机化合物生成共沸混合物.据文献记载,迄今己发现与甲醇一起生成共沸混合物的物质有100种以上。由于有共沸混合物的生成,且沸点与甲醇的沸点相接近,将影响到蒸馏过程对有机杂质的消除。
甲醇具有上述多种重要的物理化学性质,使它在许多工业部门得到广泛的用途,特别是由于能源结构的改变,和碳一化学工业的发展,甲醇的许多重要的工业用途正在研究开发中。例如甲醇可以裂解制氢,用于燃料电池,日益引人注目。甲醇通过ZSM-5分子筛催化剂转化为汽油已经工业化为固体燃料转化为液体燃料开辟了捷径。甲醇加一氧化碳加氢可以合成乙醇。又如甲醇可以裂解制烯烃。这对石油化工原料的多样化,面对石油资源日渐枯竭对能源结构的改变,具有重要意义。甲醇化工的新领域不断地被开发出来其广度和深度正在发生深刻的化。
年产30万吨合成氨工艺设计

年产30万吨合成氨工艺设计作者姓名000专业应用化工技术11-2班指导教师姓名000专业技术职务副教授(讲师)目录摘要 (4)第一章合成氨工业概述 (5)1.1氨的性质、用途及重要性 (5)1.1.1氨的性质 (5)1.1.2 氨的用途及在国民生产中的作用 (6)1.2 合成氨工业概况 (6)1.2.1发展趋势 (6)1.2.2我国合成氨工业发展概况 (7)1.2.3世界合成氨技术的发展 (9)1.3合成氨生产工艺 (11)1.3.1合成氨的典型工艺流程 (11)1.4设计方案确定 (13)1.4.1原料的选择 (13)1.4.2 工艺流程的选择 (14)1.4.3 工艺参数的确定 (14)第二章设计工艺计算2.1 转化段物料衡算 (15)2.1.1 一段转化炉的物料衡算 (16)2.2 转化段热量衡算 (24)2.2.1 一段炉辐射段热量衡算 (24)2.2.2 二段炉的热量衡算 (32)2.2.3 换热器101-C、102-C的热量衡算 (34)2.3 变换段的衡算 (35)2.3.1 高温变换炉的衡算 (35)2.3.2 低温变换炉的衡算 (38)2.4 换热器103-C及换热器104-C的热负荷计算 (41)2.4.1 换热器103-C热负荷 (41)2.4.2 换热器104-C热负荷 (42)2.5 设备工艺计算 (42)2.6 带控制点的工艺流程图及主要设备图 (46)2.7 生产质量控制 (46)2.8 三废处理 (47)摘要氨是重要的基础化工产品之一,在国民经济中占有重要地位。
合成氨生产经过多年的发展,现已发展成为一种成熟的化工生产工艺。
本设计是以天然气为原料年产三十万吨合成氨的设计。
近年来合成氨工业发展很快,大型化、低能耗、清洁生产均是合成氨设备发展的主流,技术改进主要方向是开发性能更好的催化剂、降低氨合成压力、开发新的原料气净化方法、降低燃料消耗、回收和合理利用低位热能等方面上。
年产30万吨合成氨工艺设计

年产30万吨合成氨工艺设计1. 引言合成氨是一种重要的化工原料,广泛应用于肥料、塑料、药品、染料等工业领域。
年产30万吨合成氨工艺设计即是针对每年生产30万吨合成氨的工艺进行设计。
本文将从原料准备、反应装置、分离装置和能源供应等方面进行详细介绍,以实现合成氨工艺的高效、稳定和可持续生产。
2. 原料准备合成氨的主要原料是氢气和氮气。
氢气可以通过蒸汽重整或煤气化产生,氮气则通常采购自外部供应商。
原料的准备过程包括氢气的制备和氮气的供应。
2.1 氢气制备氢气制备可以通过蒸汽重整法或煤气化法实现。
蒸汽重整法将天然气或液化石油气与蒸汽在热催化剂的作用下进行反应,生成氢气和一氧化碳。
煤气化法则将煤或其他含碳物质与氧气反应,生成合成气,再经过变换反应生成氢气。
2.2 氮气供应为保证合成氨工艺的稳定运行,需要从外部供应商采购足够的氮气。
氮气的供应应符合相关的质量标准,并与氢气进行充分的混合准备。
3. 反应装置合成氨的工艺主要是通过氢气和氮气的合成反应实现的。
合成反应需要在适当的温度和压力下进行,并且通常采用催化剂进行催化。
3.1 反应温度合成氨反应的温度通常在350到550摄氏度之间。
温度过高会导致催化剂烧结和氨的副反应增加,温度过低则会导致反应速率过慢。
因此,需要通过优化反应温度,以提高合成氨工艺的效率和产量。
3.2 反应压力合成氨反应通常在100到300兆帕之间的高压下进行。
增加压力可以提高氢气和氮气的折合摩尔浓度,促进反应的进行,但同时也会增加设备的压力对设备材料的要求。
因此,需要综合考虑反应速率、设备成本和安全性等因素,确定适宜的反应压力。
3.3 催化剂选择合成氨反应通常采用铁-铑催化剂。
铁对氮气的吸附和解离具有较好的催化作用,而铑可以提高催化剂的活性和稳定性。
催化剂的选择和优化是合成氨工艺设计中的关键问题,需要综合考虑催化剂的催化效率、稳定性和成本等因素。
4. 分离装置合成氨反应产生的混合物中含有大量的氨、氮气、氢气等挥发性成分,需要通过分离装置对这些成分进行分离和回收。
年产30万吨合成氨工艺设计毕业论文

合成氨是一种广泛应用于化肥、塑料、药品等领域的化学物质,具有
重要的经济和社会价值。
本文旨在设计一种年产30万吨合成氨的工艺,
以满足市场需求并提高生产效率。
首先,我们需要选择适合的反应器类型。
合成氨工艺通常采用催化剂
床层反应器,可有效控制反应温度和催化剂床的压力。
选择适宜的催化剂,如铁-铝催化剂,具有高催化活性和稳定性。
其次,反应器的设计需要考虑反应温度和压力。
合成氨反应的最佳工
艺条件为300-500摄氏度和150-250大气压。
通过调节反应条件,可以提
高氨气的产量和选择性。
在反应器后,需要进行气体分离和氨纯化处理。
气体分离通常采用低
温分离技术,如低温凝析法,可将氮气和未反应的氢气从产生的氨气中分
离出来。
随后,利用吸附剂和膜分离技术进行氨纯化处理,以提高氨气的
纯度和产品质量。
最后,废水处理也是一个重要的环节。
合成氨工艺中会产生废水,其
中含有高浓度的氨和其他有机物。
采用适当的废水处理工艺,如生物降解
和化学氧化等方法,可以有效降解有机物和去除氨,以达到环保要求。
总之,设计一种年产30万吨合成氨的工艺需要综合考虑反应器类型、反应条件、气体分离和氨纯化处理以及废水处理等因素。
通过合理设计和
优化工艺,提高生产效率和产品质量,将为合成氨行业的发展做出积极贡献。
年产30万吨粗甲醇精馏工段的设计毕业论文

年产30万吨粗甲醇精馏工段的设计毕业论文目录第1章总论 (1)1.1 概述 (1)1.1.1意义及作用 (1)1.1.2 国外现状 (1)1.1.3 产品性质与特点 (4)1.1.4 产品的生产方法概述 (5)1.2 设计依据 (5)1.3 设计规模 (6)1.4 原料及产品规格 (6)1.4.1 主要原料规格及技术指标 (6)1.4.2 产品规格 (6)第2章设计方案 (8)2.1 工艺原理 (8)2.2甲醇精馏工艺论证 (8)2.2.1精馏工艺和精馏塔的选择 (8)2.2.2单塔精馏工艺 (8)2.2.3双塔精馏工艺 (9)2.2.4三塔精馏工艺 (10)2.2.5双塔与三塔精馏技术比较 (11)2.2.6精馏塔的选择 (12)2.3工艺流程简述 (13)第3章工艺设计计算 (16)3.1工艺参数 (16)3.2 物料衡算的意义和作用 (17)3.2.1 物料衡算 (17)3.2.2 总物料衡算表 (20)3.3热量衡算 (21)3.3.1预塔热量衡算 (23)3.3.2主塔热量衡算 (25)3.3.3常压精馏塔能量衡算 (27)3.4热量衡算表 (31)第4章主要设备的工艺计算及选型 (32)4.1理论板数的计算 (32)4.1.1常压塔理论塔板计算 (32)4.2常压精馏塔主要尺寸的计算 (34)4.2.1常压精馏塔设计的主要依据和条件 (34)4.2.2初估塔径 (36)4.2.3塔件设计 (38)4.2.4塔板流体力学验算 (41)4.2.5 负荷性能 (43)4.2.6常压塔主要尺寸确定 (46)4.3 预精馏塔模拟 (48)4.4加压塔模拟 (50)4.5塔设备一览表 (52)第5章附属设备的选择 (53)5.1确定物性数据 (53)5.2工艺结构尺寸 (54)5.3换热器衡算 (56)5.3.1热量衡算 (56)5.3.2 换热器流体的流动阻力 (59)5.4泵的选型原则 (60)5.5各类泵的性能参数 (62)5.6泵的计算 (64)参考文献 (67)后记及其他 (68)附图1 (69)附图2 (70)第1章总论1.1 概述1.1.1意义及作用目前,甲醇在有机合成工业中,是仅次于烯烃和芳烃的重要基础有机原料。
年产30万吨合成氨造气工段工艺设计

年产30万吨合成氨造气工段工艺设计年产30万吨合成氨造气工段工艺设计The Design of Producing Coal Gas about Synthesis ofAmmonia 300000t/a目录摘要 (I)Abstract......................................................................................................................... I I 引言. (1)第一章绪论 (3)1.1 煤气化发展史 (3)1.2 国内外发展现状 (4)第二章生产方法的选择 (5)2.1生产方法的介绍 (5)2.1.1 固定床气化法 (5)2.1.2 流化床气化 (5)2.1.3 气流床气化 (6)2.2 生产方案的选择及论证 (6)第三章常压固定床间歇气化法 (8)3.1 固定床气化法的特点 (8)3.2 半水煤气定义 (8)3.3 半水煤气制气原理 (8)3.3.1 煤气发生炉构造及气化反应的分区 (8)3.3.2 制气原理 (9)3.4 生产半水煤气对固体原料性能的要求 (10)3.5 间歇式制半水煤气的工艺条件 (11)3.6 生产流程的选择及论证 (12)3.7 间歇式气化的工作循环 (13)3.8 间歇式制半水煤气工艺流程 (14)3.9 各主要设备简介 (15)3.9.1 煤气发生炉 (15)3.9.2 燃烧室 (15)3.9.3 废热锅炉 (16)3.9.4 洗气箱 (16)3.9.5 洗涤塔 (16)3.9.6 烟囱 (17)3.9.7 自动机 (17)第四章工艺计算 (18)4.1 已知条件 (18)4.2 物料及热量衡算 (20)4.2.1 吹风阶段的计算 (20)4.2.2 制气阶段的计算 (22)4.2.3 总过程计算 (26)4.3 配气计算 (29)4.4 消耗定额 (30)4.5 吹净时间核算 (30)4.6 废热锅炉的热量衡算 (30)4.6.1 已知条件 (30)4.6.2 热量衡算 (32)4.6.3 热量平衡和总固体平衡 (35)4.7 夹套锅炉的物料及热量衡算 (35)4.7.1 已知条件 (35)4.7.2 产气量及消耗量计算 (36)第五章设备计算选型 (37)5.1 煤气炉指标 (37)5.2 煤气台数的确定 (38)5.3 空气鼓风机的选型及台数确定 (39)5.4 废热锅炉的选型 (39)结论 (41)致谢 (42)参考文献 (43)年产30万吨合成氨造气工段工艺设计摘要:本设计是年产能力为30万吨合成氨造气工段(半水煤气)的工艺设计,造气工段是获得合成气的首要工段。
年产30万吨甲醇精馏提纯的工段设计毕业设计
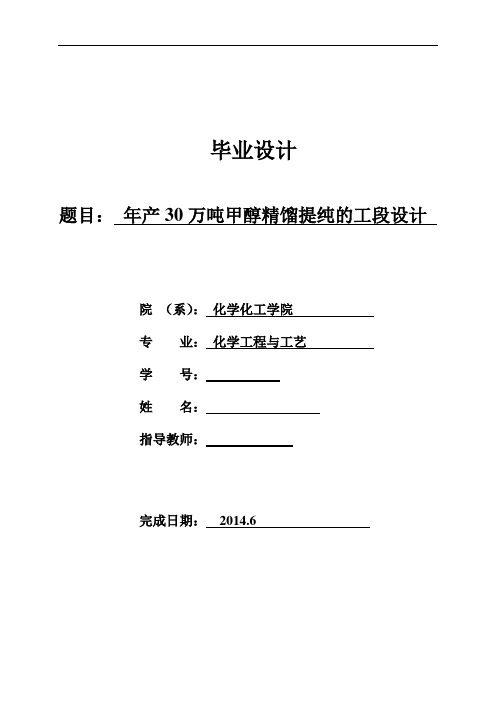
毕业设计题目:年产30万吨甲醇精馏提纯的工段设计院(系):化学化工学院专业:化学工程与工艺学号:姓名:指导教师:完成日期:2014.6目录第一章文献综述 (4)1.1 甲醇生产工艺进展及国内发展前景 (4)1.1.1甲醇简介 (4)1.1.2甲醇的用途 (8)1.1.3甲醇的安全性 (9)1.1.4甲醇国内外合成技术现状 (10)1.3影响精馏操作的因素与调节 (12)1.3.1影响精馏操作的主要因素简析 (12)1.3.2精馏塔的产品质量控制和调节 (13)1.4 Aspen Plus工艺流程模拟 (14)第二章物料衡算和能量衡算 (16)2.1操作条件 (16)2.2物料衡算 (16)2.2.1 预塔物料衡算 (17)2.2.2 加压塔的物料衡算 (18)2.2.3 常压塔的物料衡算 (29)2.2.4 回收塔的物料衡算 (37)2.2.5 四塔实际模拟 (45)2.4整个四塔甲醇的回收率 (55)2.5加压塔、常压塔、回收塔采出甲醇的浓度 (55)第三章预精馏塔工艺设计及其附件选型 (55)3.1 设计依据 (55)3.1.1 预精馏塔设计已知条件 (55)3.1.2 塔板工艺条件计算 (56)3.1.3 塔径计算 (57)3.1.4 塔高计算 (58)3.1.5 塔板的工艺尺寸 (60)3.1.6 塔板流体力学验算 (64)3.2 预精馏塔附件选型 (71)3.2.1 管口设计 (71)3.2.2 设备管口表 (73)参考文献 (74)附录 (74)致谢 (75)年产30万吨甲醇精馏提纯的工段设计学生:xxx 指导老师:xxx摘要:本设计是关于甲醇精馏的工段及其预塔设备的设计,文中着重介绍了四塔流程。
按照课程设计任务书上的要求,文中具体内容包括:甲醇及精馏的相关内容;甲醇精馏流程介绍;精馏全流程的物料衡算和能量衡算;Aspen对全流程的模拟及分析以及Radfrac模块中的Tray Sizing对加压、常压、回收塔的尺寸设计;预精馏塔的塔设备计算及塔附件选型等。
年产三十万吨合成氨合成工段工艺设计设计说明

年产三十万吨合成氨合成工段工艺设计设计说明年产三十万吨合成氨合成工段工艺设计1.绪论1.1合成氨简介在高温高压和催化剂存在的条件下,将精制的氢氮混合气直接合成为氨,然后将所得的气氨从未合成的为氨的混合气中冷凝分离出来。
由于受反应平衡影响,氢氮混合气不能全部转化为氨,反应后气体中一般只有10%-20%,通常采用冷冻的方法将已合成的氨分离,然后在未反应的氢氮混合气中补充新鲜气进行循环反应。
氨合成反应是一个放热反应,而氨分离过程又要消耗大量的冷量。
在氨合成系统中合理设计回收反应热的设备,可降低冷量的消耗。
氨合成工段的生产状况直接影响到合成氨厂生产成本的高低,它是合成氨厂节能减排的关键工序之一。
根据合成氨反应中采用的压力、温度及催化剂型号的不同,氨合成的方法可以分为低压法(15-20MPa)、中压法(20-32MPa)和高压法三种。
目前合成氨厂普片采用的采用的是低压法和中压法。
1.2 合成氨概况合成氨是重要的无机化工产品之一,最早是由德国化学家哈伯于1902年研究出来的,其原理是由氮气和氢气在一定条件下直接合成氨,并于1908年申请专利。
后来,他继续研究,于1909年改进了合成技术,使氨的含量达到6%以上。
合成氨工业起初是因为制作炸药而被重视,在20世纪初期形成规模,为战争服务;第一次世界大战结束后,转向为农业、工业服务。
随着科学技术的发展,对合成氨的需要量日益增长。
20世纪50年代后氨的原料构成发生重大变化,近数十年来合成氨工业发展很快,大型化、低能耗、清洁生产成为合成氨装置发展主流,技术改进主要方向是研制性能更好的催化剂、降低氨合成压力、开发新的原料气净化方法、降低燃料消耗、回收和合理利用低位热能等。
合成氨工业已有一个世纪的历史,在国民经济中占有重要地位。
合成氨在农业上有非常重要的地位,氮肥,尿素、硝酸铵、磷酸铵、氯化铵以及各种含氮复合肥,都是以氨为原料的。
同时,合成氨也是大宗化工产品之一,世界每年合成氨有80%用来生产化学肥料,20%作为其它化工产品的原料。
万吨直馏柴油年氨精制装置设计设计说明(1)

参赛队伍:环卫工团队参赛题目:20万吨直馏柴油/年氨精制装置设计所属院校:广东石油化工学院目录第1章原始材料 (1)1.1 气提塔进出物料情况 (1)1.2 气提塔热负荷 (3)1.3 操作压力 (3)1.3.1 塔顶操作压力 (3)1.3.2 塔底操作压力 (3)第2章气提塔设计计算 (4)2.1 试选传热系数初始值 (4)2.2 气提塔尺寸的确定 (4)2.2.1 平均温差 (4)2.2.2 估算传热面积 (5)2.2.3 气提塔降膜热管尺寸 (5)2.2.4 管数的确定 (5)2.2.5 塔径的计算 (7)第3章传质过程计算 (8)3.1 列管内气速 (8)3.1.1 气体流人点气速 (8)3.1.2 气体流出点气速 (8)3.1.3 气速平均值 (8)3.2 流体周边流量 (9)3.2.1 液体流入点周边流量 (9)3.2.2 液体流出点周边流量 (9)3.2.3 液体周边流量平均值 (10)3.3 液膜厚度 (10)3.3.1 液体流入点液膜厚度 (10)3.3.2 液体平均液膜厚度 (11)3.4 液泛速度计算 (12)3.5 液体最小润湿率计算 (13)3.6 液膜停留时间和液膜平均速度 (13)第4章复核传热系数 (15)α (15)4.1 管外蒸气冷凝时的给热系数1α (15)4.2 管内液体沿垂直壁面成膜下流时的给热系数24.3 总传热系数 (16)第5章传热面积 (17)第6章精度计算 (17)第7章零部件及稳定性 (18)7.1 塔壁厚的确定 (18)7.2 封头的选择 (18)7.3 塔高的计算 (18)7.4 塔设备的稳定计算 (19)7.4.1 风载荷 (19)7.4.2 塔底部截面的最大弯矩 (20)7.5 裙座设计 (20)7.5.1 裙座尺寸 (20)7.5.2 基础环 (20)7.6 管板和折流板 (23)7.6.1 管板设计 (23)7.6.2 折流板设计 (24)7.7 拉杆和定距管 (25)7.8 膨胀节 (25)7.9 塔体法兰选择 (25)7.10 液体分配器 (25)7.11 除沫器 (25)7.12 液体分布器 (26)第8章附表 (27)表8.1 气提塔参数一览表 (27)表8.2 各符号物理意义一览表 (29)第1章原始材料1.1 气提塔进出物料情况表1.1 气提塔进出料情况进料流量(kg/h)出料流量(kg/h)油相(40℃)27672 油相(70℃)27643.33其中:柴油27632.34 其中:柴油27632.34NH328.67 NH30乙二醇10.78 乙二醇10.78RCOOH 0.79 RCOOH 0.79 置换气(35℃)60 气提气(60℃)88.67其中:N2 60 其中:N2NH360 28.67合计27732 合计27732表1.2 物料参数一览表1.2 气提塔热负荷kJ/h 1769464=Q1.3 操作压力 1.3.1 塔顶操作压力)(atm 5.0表压顶=P1.3.2 塔底操作压力)(atm 0.2表压底=P第2章 气提塔设计计算2.1 试选传热系数初始值针对本设计中气提塔的进出物料情况和温度、压力等参数,根据经验确定气提塔传热系数的初始值:h C m /kJ 3452⋅︒⋅=初K2.2 气提塔尺寸的确定 2.2.1 平均温差管外以(表)MPa 2.0饱和蒸气加热,蒸气温度为C 120︒。
年产30万吨甲醇精馏设计

设计方案
设 计 步 骤
甲醇ห้องสมุดไป่ตู้馏系统选定之后,对工艺进行计算,对全流 程进行物料衡算、热量衡算。能量衡算需要化工模 拟软件辅助。对常压塔冷却器进行工艺设计和设备 设计。 介绍甲醇精馏原理、工艺(双塔精馏工艺技术法、 三塔精馏工艺技术法、四塔精馏工艺技术)和选 定设计工艺流程技术。
查阅与甲醇相关的中文文献资料,阅读后归纳出结 论,并完成文献综述,其中文献综述包括甲醇的性 质、用途和生产概况
时间进程
1-3 周 设计出符合生产的生产流程图和合理 的关键设备,满足工艺的指标需要; 4-9 周 对该工段进行物料计算,热量衡算, 设备设计与选型,车间布置等符合现实中 安全生产的要求 方案的可行性分析 9-11周 产品的技术经济指标及化工厂污染处 理、排放符合国家环保的要求 12-15周 仔细检查整个工艺设计过程,并且 完成设计论文撰写和修改
年产30万吨甲醇精馏工段的工艺设计
指导教师: 班级:xxx 学生:xxx 学号:xxx
设计的结构和主要内容
1、研究目的和意义
国内外发展情况 2、国内外发展情况
3、设计的目标
设计方案 4、设计方案
5、方案的可行性分析 6、时间进程 7、参考文献
研究目的和意义
甲醇逐步发展成为重要的能源替代品
精甲醇的市场前景很好
减少蒸馏 的热负荷
四塔精馏
采用三个塔精馏+回收塔的工艺流程,预塔的主要目的是除去粗 甲醇中溶解的气体及低沸点组分,加压塔及常压塔的目的是除去 水及高沸点杂质(如异丁基油),同时获得高纯度的优质甲醇产品。 另外,为减少废水排放,增设甲醇回收塔,进一步回收甲醇,减少 废水中的甲醇含量。
设计方案
四塔精馏框图
主要参考文献 [1] 郭树才,胡浩权.煤化工工艺学.北京:化学工业出 版社,2012.8 [2] 宋维端,肖任坚, 房鼎业.甲醇工学[M].北京: 化学 工业出报社,1991. [3] 陈声宗主编.化工设计.北京:化学工业出版社, 2012.6 [4] 孙达军.甲醇四塔精馏建模与变负荷能耗优化研究[ 学位论文].上海:上海交通大学,2012. [5] 马俊睿.国际国内甲醇市场分析与预测[J].油化工技 术经济, 2006(2): 41-47. [6] 李雅静.某厂煤制甲醇低温甲醇洗工艺的模拟与改造 [学位论文].大连:大连理工大学,2013.
年产三十万吨尿素化工厂设计,毕业设计

I年产30万吨尿素化工厂设计摘要本设计采用水溶液全循环法用氨和二氧化碳直接合成尿素,采取的是连续生产的方法,主要包括合成、分离及结晶造粒三个主要工序。
本设计主要包括整个尿素生产过程的工艺设计,合成工段和造粒工段的物料衡算、热量衡算及设备选型,工厂布置设计。
主要设计图包括尿素生产工艺流程图、车间剖面图、车间平面图及全厂布置图。
关键词:尿素,工艺设计II With an Annual Output of 300,000 Tons of Urea Chemical Plant DesignABSTRACTThe solution was designed with the whole cycle Act,ammonia and carbon dioxide direct synthesis of urea.Adopting a continuous production methods,including synthesis,separation and crystallization of the three main granulation processes.The design mainly includes the entire process of Weak Acid Black NB-G dye production process design,synthesis and granulation Section of the material balance and heat balance selection of equipment,factory layout design.Design plans include major urea production process maps,profiles workshop,workshop floor plan and palnt layout.KEY WORDS:Urea,Process DesignIII目录摘要 (I)ABSTRACT (II)1绪论 (1)1.1项目依据 (1)1.1.1课题背景及意义 (1)1.1.2我国酸性染料产业概况 (2)1.1.3国际酸性染料需求概况 (13)1.2 设计原则 (16)1.3 课题的主要任务(需附有技术指标要求) (17)1.4厂制概况 (17)1.4.1 工厂组织 (17)1.4.2 工作制度 (17)1.4.3 人员配备 (17)1.5厂址选择 (18)1.5.1 建厂依据 (18)1.5.2 指导方针 (18)1.5.3 厂址及建厂条件 (18)1.6 气象地质资料月份 (19)1.6.1气象资料 (19)1.6.2地质资料 (20)1.7环境保护及废物处理 (20)2工艺设计 (21)2.1工艺流程设计 (21)2.1.1工艺流程设计的重要性 (21)2.1.3工艺流程设计的原则 (21)2.1.4工艺流程选择分析与研究 (12)2.1.5工艺流程设计 (24)2.1.6生产工艺流程叙述 (14)2.1.7工艺流程设计参数 (28)2.2工艺计算 (18)2.2.1物料衡算 (18)2.2.2热量衡算 (37)IV3工艺计算与设备选型 (43)3.1搅拌反应釜的工艺计算与选型 (43)3.2过滤设备的工艺计算与选型 (47)3.3气流干燥器的工艺计算与选型 (48)3.4粉碎机的选择 (55)3.5拼混机的选择 (55)3.6泵的选择 (56)3.7储罐及计量罐的选择 (56)设备一览表 (58)4全厂平面设计 (59)4.1总平面设计任务和步骤 (59)4.1.1总平面设计任务 (59)4.1.2工厂组织 (59)4.2总平面设计原则 (60)4.3总平面布置评述 (66)4车间布置设计 (68)4.1车间布置设计的意义 (68)4.2车间布置得原则 (68)4.3车间布置设计与评述 (68)4.3.1关于车间平面布置方案 (68)4.3.2关于厂房形式 (68)4.3.3车间设计布置 (69)5尿素生产中的安全技术与三废处理 (70)5.1安全生产原则 (70)5.2生产物料的安全特性 (72)5.3必要的安全保护装置 (72)5.4三废排放及处理 (73)致谢 (75)参考文献 (76)年产30万吨媒合成尿素化工厂设计 11绪论1.1课题背景1.1.1 尿素的概况尿素外观为白色晶体或粉末,是动物蛋白质代谢后的产物,通常用作植物的氮肥。
最新年产30万吨常压炼油生产工艺设计设计
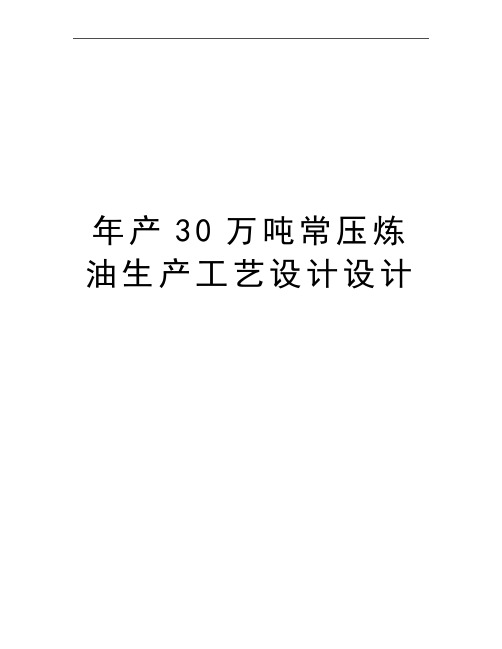
年产30万吨常压炼油生产工艺设计设计精品好文档,推荐学习交流年产30万吨常压炼油生产工艺设计目录1 前言 (2)2 选题背景 (1)2.1 研究目的和意义 (1)2.2国内外现状、发展趋势及研究的主攻方向 (2)3方案论证 (4)3.1 方案选择 (4)3.2 工艺原理 (5)3.3 设计方案的确定 (7)4 原油有关性质参数的计算 (7)4.1 常压蒸馏曲线和实沸点蒸馏曲线的互换 (7)4.2 恩氏蒸馏数据与平衡汽化温度之间的转换 (9)4.3 平均沸点的计算 (11)4.4 比重系数API。
(12)4.5 临界温度和临界压力 (13)4.6 焦点温度 (14)5 原油常压塔的工艺计算 (15)5.1 产品切割方案及有关性质 (15)5.2 常压塔的物料平衡 (16)5.3 汽提蒸汽用量 (17)5.4 塔板板型和塔板数 (17)5.5 操作压力的确定 (18)5.6 精馏塔计算草图 (18)5.7全塔汽液相负荷分布图 (27)5.8浮阀数及排列方式 (41)5.9塔板流体力验算 (42)6 塔的机械设计 (45)6.1 按设计压力计算塔体和封头厚度 (46)6.2 自振周期计算: (49)6.3 地震载荷及弯矩计算见表 (49)6.4 风弯矩计算 (52)6.5各种载荷引起的走向应力 (53)精品好文档,推荐学习交流6.5 筒体和裙座危险截面的强度和稳定性校核 (54)6.6 筒体和去做水压试验校核 (55)6.7 基础环设计 (57)6.8 基础环厚度 (57)6.9 地脚螺栓设计 (58)6.10 常压塔装配图 (59)7.工艺流程设计 (61)7.1工艺流程简述 (61)7.1.1原油电脱盐系统 (61)7.1.2初馏系统 (61)7.1.3常压系统 (61)7.2工艺流程图 (62)最后{{{附录 (62)8 总结 (65)参考文献 (65)30万吨/年常压炼油生产工艺设计1 前言石油是极其复杂的化合物。
30万吨年催化重整车间抽提工段初步设计_毕业设计
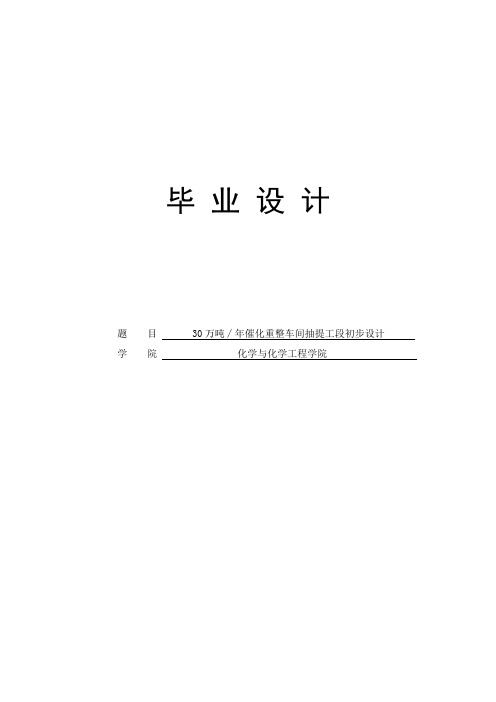
毕业设计题目 30万吨∕年催化重整车间抽提工段初步设计学院化学与化学工程学院摘要本文是关于30万吨∕年催化重整车间抽提工段初步设计。
文中第一论述抽提工段的目的、国内外进展现状、抽提溶剂及工艺的比较、市场前景和生产方式。
依照查找资料,确信生产装置采纳以四乙二醇醚为溶剂的Carom新抽提工艺流程,要紧目的是将重整生成油中的芳烃与非芳烃分离。
本文重点论述了芳烃抽提工段。
包括工艺原理和工艺流程的论述。
依照工艺参数进行物料衡算、热量衡算和设备计算,并依据计算的数据进行设备选型。
而且对该工段的工艺操纵、防火平安、“三废处置”做了说明。
最后依照工艺条件利用Auto CAD绘制带操纵点的工艺流程图,而且完成了20 000字的设计说明书。
关键词:芳烃;芳烃抽提;催化重整;四乙二醇醚AbstractThis article is about the first step design of the extraction section for the catalyst reforming plant with a capacity of 300000 t∕a. Firstly, It discusses the aim of the extraction section, the domestic and overseas developing condition,the comparison of the extraction solvent and the process, the market prospect and production can be confirmed that the new carom extraction process uses the glycofurol as solvent by checking the relevant material, its main aim is to separate the aromatic hydrocarbon and the non aromatic hydrocarbon in the reforming oil. This article mainly states the extraction process of the aromatic hydrocarbon including the principle and flow of the process. The operation of the material balance calculation, heat balance calculation and equipment calculation is carried out according to the process parameters, and then to select the type of the equipment on the basis of the calculation data. It also states the process control fire emergency, waste dispose for the process. Lastly, the process flow sheet with control point has been drawn using the Auto CAD referring to process conditions, and the 20000 words design specification has also been finished.Key words: Aromatics;Aromatic hydrocarbon extraction;Catalytic reforming;Glycofurol目录摘要 (Ⅰ)Abstract (Ⅱ)第1章总论............................................................................................. 错误!未定义书签。
年产30万吨合成氨厂变换系统主要装置设计

CO2:
H2:
H2O:
将上述煤气各成分列为下表:
组成
N2
CH4
CO
CO2
H2
H2O
合计
含量(%)
1.78
6.469
17.257
20.265
29.99
24.242
100
含量(kmol)
1.78
6.469
17.257
20.265
29.99
24.242
100
2.3变换炉温升估算
式中 :出、进催化剂床气体温度℃
变换反应催化剂的选用,主要根据合成氨生产工艺要求来确定,主要依据为原料气和变换气中一氧化碳和二氧化碳的含量、原料气中硫化氢和有机硫化物的含量以及原料气最终精制工艺的要求。本合成氨装置采用低温甲醇洗﹙-65℃﹚脱硫脱碳以及液氮洗脱除一氧化碳、甲烷,和甲烷蒸汽转化的工艺路线。变换入口粗煤气中一氧化碳和二氧化碳的含量较高,硫化氢干基含量也很高。
含量(kmol)
1.78
6.469
2.741
34.812
44.537
9.695
100
第二变换炉入口温度为:280℃(553K)
第二变换炉出口温度为:410℃(683K)
第二变换炉入口CO变换率为:48.387%
第二变换炉出口CO变换率为:84.3%
2.4.3第三变换炉的物料衡算
第三变换炉入口压力假定为:2.81MPa=27.73atm
CH4:6.469kmol
CO2:28.615kmol
H2:38.34kmol
H2O:15.892kmol
第一变换炉出口各组分含量表:
表4—3
组成
N2
年产30万吨精甲醇精制工段工艺设计任务书
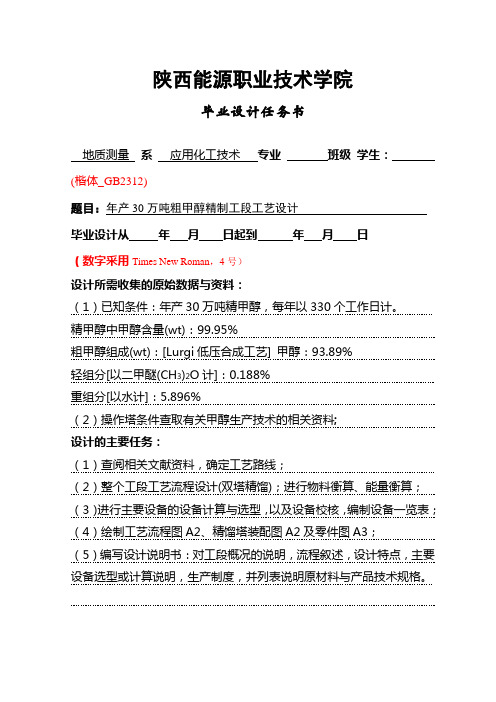
陕西能源职业技术学院
毕业设计任务书
地质测量系应用化工技术专业班级学生:
(楷体_GB2312)
题目:年产30万吨粗甲醇精制工段工艺设计
毕业设计从年月日起到年月日
(数字采用Times New Roman,4号)
设计所需收集的原始数据与资料:
(1)已知条件:年产30万吨精甲醇,每年以330个工作日计。
精甲醇中甲醇含量(wt):99.95%
粗甲醇组成(wt):[Lurgi低压合成工艺] 甲醇:93.89%
轻组分[以二甲醚(CH3)2O计]:0.188%
重组分[以水计]:5.896%
(2)操作塔条件查取有关甲醇生产技术的相关资料; 设计的主要任务:
(1)查阅相关文献资料,确定工艺路线;
(2)整个工段工艺流程设计(双塔精馏);进行物料衡算、能量衡算;
(3)进行主要设备的设备计算与选型,以及设备校核,编制设备一览表;
(4)绘制工艺流程图A2、精馏塔装配图A2及零件图A3;
(5)编写设计说明书:对工段概况的说明,流程叙述,设计特点,主要
设备选型或计算说明,生产制度,并列表说明原材料与产品技术规格。
设计进度安排及完成的相关任务(以教学周为单位):
(进度安排由教师根据实际情况适当调整)
学生签名:日期:
指导教师:日期:
教研室主任:日期:
注:1、任务书要求学生双面打印,
2、红字部分打印时务必删掉,不能改变任务书的版面整体效果。
- 1、下载文档前请自行甄别文档内容的完整性,平台不提供额外的编辑、内容补充、找答案等附加服务。
- 2、"仅部分预览"的文档,不可在线预览部分如存在完整性等问题,可反馈申请退款(可完整预览的文档不适用该条件!)。
- 3、如文档侵犯您的权益,请联系客服反馈,我们会尽快为您处理(人工客服工作时间:9:00-18:30)。
三十万吨年直馏柴油醇氨法化学精制装置设计书第一章项目总论1.1 概述1. 项目名称:30万吨/年直馏柴油醇-氨法化学精制装置省MM市,MM市南部临海,迂回的海岸线长约220公里,拥有水东、博贺等多个天然良港。
水东港是我国对外开放一类口岸,现已建成多个万吨级成品油码头和杂货、集装箱码头,拥有全国最大的25万吨级单点系泊原油接卸系统,年吞吐能力达到1450万吨。
MM以炼油、乙烯生产为龙头的石油化工工业在全国占有重要位置,是省重要的能源、原材料和重化工业基地。
茂石化炼油加工能力、乙烯生产能力分别达到1350万吨/年和100万吨/年,拥有华南地区最大的原油加工能力,有“中国南方油城”之称。
MM市拥有400多家各类型的化工企业相映争辉,出产的油品和化工产品品种多达400多种。
另外,MM还拥有便利的交通条件,拥有阳茂高速公路、茂湛高速公路、包茂高速公路、云茂高速公路、汕湛高速公路;拥有三茂铁路、河茂铁路、广茂铁路、茂湛铁路、黎茂铁路、洛湛铁路、西部沿海高速铁路和207国道、325国道,还有S113、 S215、 S280、S284、 S285、S291、S370、S371、S372省道。
MM的港口、道路、油厂、化工厂为我们提供丰富的柴油资源、销售空间和运输方案。
正因为MM市地理条件优越,生产柴油的原料又可以就地而去,而且这里交通便捷,可以将产品销售到热点城市,所以将此项目建在MM就可以节省一大笔交通费用。
当前, 碱洗电精制-硫酸中和法间歇工艺是炼油行业精制含酸直馏柴油和回收环烷酸的主要方法。
该法虽然能够生产出合格的柴油产品, 但仍存在着油水乳化严重、柴油收率低、间歇操作、操作费用高和环境污染等问题。
针对现有工艺存在的问题, 人们一直在努力开发新型、高效的直馏柴油精制和回收环烷酸的联合工艺。
与直馏柴油碱洗电精制-硫酸中和法间歇工艺比, 醇氨法精制直馏柴油工艺具有取消高压电场,不使用强酸、强碱, 无“三废”、零排放, 溶剂循环使用, 连续操作, 可同时得到精制柴油和环烷酸等优点, 已成为直馏柴油脱酸新工艺的研究热点。
为了节约能源,降低成本,提高效益,醇氨法精制直馏柴油工艺是一个不错的选择。
醇氨法精制直馏柴油工艺对于环境保护,节约能源也具有重要意义!8. 研究工作概况(一)国家能源战略安全的需要我国是原油进口大国,原油对外依存度正在逐年升高,2012年原油对外依存度已经接近59%,成为世界第二大石油消费国,石油的保障及安全问题显得日益重要。
以石油为重点的能源供给一直是党中央、国务院高度关注的问题,目前我国已形成三大油气进口通道:东北部有中俄原油管道;西北部有中哈原油管道、中哈天然气管道、中亚天然气管道;东部海上运输通道,有超过60%的进口原油经马六甲海峡运输至国。
众所周知,马六甲海峡航道狭窄,海盗猖獗。
建设中缅油气管道,不仅可以绕过马六甲海峡,规避海上航路繁忙拥挤的风险和潜在战争及恐怖威胁,而且还有利于拓展我国面向东南亚、南亚的原油及石化产品进出口通道,构建我国第四大油气进口通道,实现我国“原油进口多地区、进口方式多元化”的发展战略,调整能源布局、优化资源配置,保证国家能源战略安全。
同时,这条路径可使原油运输不经过马六甲海峡,至少能缩短1800海里的路程。
(二)保证MM经济社会持续健康发展的需要目前,我国原油产地主要集中在东北、西北和华北地区,大型炼化企业分布在东北、西北和沿海地区。
长期以来由于北方炼油企业较多,而西南地区几乎没有炼油能力,形成了北油南运的成品油流通格局。
是全国没有炼油能力的四省区市之一,处于全国成品油供应链的末端,历来缺油少气,2012年全省成品油消费量近940万吨,预计2015年在1400万吨左右,随着经济社会的发展,用油量还将持续增长。
这些成品油全部需通过铁路、公路和管道从东北、西北等较远的省调入,运输费用和销售价格随之增加。
同时,形势稍有变化,比如遇到重大自然灾害、油价上涨、运力紧、油量不足等情况,省就会闹“油荒”。
成品油供应问题成为长期困扰我省经济社会发展的一大难题,而且问题发展越来越严重,已到了非解决不可的地步。
对于而言,我们缺水可以修水库、缺路可以修路、缺电可以修电站,但缺油我们没有资源可开采,没有一滴油的生产能力。
中缅油气管道建成后,一期每年可输送原油1000万吨。
在我省建设炼厂,可以彻底改变没有炼油能力的历史和缺油少气、频繁出现油荒的被动局面,对于加快推进桥头堡建设具有十分重要的意义。
(三)确保MM人民群众正常生产生活的需要省委、省政府高度重视解决人民群众用油用气的需求,财政设立专项资金以“以奖代补”的方式鼓励中石油和中石化在增加成品油的储备,争取国家储备局在禄丰县设立了大德成品油储备库,以应对成品油供应偏紧时的市场保障。
但总的来看,储备规模小,调控能力不强。
2007年12月中旬因全国成品油供应紧、2008年初因全国大围雨雪冰冻灾害、同年5月汶川5.12地震时因铁路中断、2011年10月下旬因石油供需失衡,我省多次发生严重油荒。
每次发生严重油荒时,尽管省委、省政府第一时间向国务院报告,并积极协调国家发展改革委、铁道部和中石油、中石化,采取各种特殊措施,但仍然造成了我省大面积、长时间处于成品油供应紧状况。
广大群众为加油而排长队,有时甚至出现群众排上几公里、等上几天才能加到油的情况。
特别是随着经济社会的发展和人民群众生活的改善,到去年底全省机动车保有量达到950.7万辆,2006年以来年均增长100万辆以上。
如果不从根本上解决好成品油的供应问题,加快建设中石油西南炼油项目,成品油供应短缺、排队加油的情况将会更加频繁发生,将会严重影响广大群众的日常工作和生活。
1.2 可行性研究结论1.可行性研究的简要综合结论(1)醇氨法精制直馏柴油工艺具有溶剂循环使用、连续操作、无“三废”,零排放等优点, 完全克服了直馏柴油碱洗电精制—硫酸中和法间歇工艺的缺点, 精制柴油和副产环烷酸质量满足产品指标要求。
(2)采用聚结过滤和溶剂部分循环再生法, 对醇氨法精制直馏柴油工艺进行改进研究,获得了改进操作条件和工艺流程, 取得了较为理想的效果。
(3)改进工艺采用乙醇破乳剂, 获得了残余溶剂含量416mg/kg、酸度7115mgKOH/ 100ml( 出厂调和柴油酸度<5mgKOH/100mL) 的精制柴油产品, 相分离时间缩短了50% , 溶剂循环量下降了25%, 溶剂再生负荷和能耗下降了6215%, 取消柴油水洗操作, 减少了装置投资和操作费用。
2.存在的主要问题和建议醇氨法采用的溶剂由氨、低分子醇和水组成, 低分子醇在脱酸过程中起防乳化、破乳、抽提环烷酸及其皂盐的作用。
目前, 醇氨法仍存在剂油体积比高、溶剂循环量大、溶剂再生能耗高( 需将溶剂全部蒸馏再生) 和溶剂损耗大(精制油中残余溶剂含量高达115%—210%) 及需对精制柴油进行水洗操作等问题。
针对醇氨法精制含酸直馏柴油工艺研究的现状, 采用聚结过滤和部分溶剂循环再生法, 对醇氨法工艺进行改进研究。
第二章市场预测分析1.产品市场现状及用途柴油分子由15个烃链组成,植物油和动物油分子一般由14~18个烃链组成,与柴油分子相似。
因此,用可再生植油可加工制取新型燃料——氨醇柴油。
氨醇柴油是清洁的可再生能源,通过与传统柴油混合,发挥着节约资源、降低污染物等积极作用。
它是以大豆、油菜籽、花生等油料作物,油粽木、黄连木等油料林木果实工程微藻等水生植物,或动物油脂、废餐饮油等原料制成的液体燃料,具有原料来源广泛,可再生性高,污染性低等特点,是典型的“绿色能源”。
可以替代煤炭、石油和天然气等燃料,从而减少对化石资源的依赖,缓解资源短缺,是国民经济可持续发展的重要保证。
当人们将目光聚集到可再生能源时,氨醇柴油以其来源广泛、环境友好、再生、清洁等特点成为亮点。
柴油是动植物油脂通过酯化或者酯交换生成的脂肪酸甲酯或者乙酯,其碳链集中在C14-C18.(石油柴油的碳链集中在C11-C22,石油柴油是烃类,不含氧;氨醇柴油是酯类,含氧)。
由于不含硫和芳烃,所以混有氨醇柴油的柴油产品可以大大降低污染物的排放。
氨醇柴油还具有润滑性能好,十六烷值高(国家标准要求常规柴油的十六烷值不低于45,一般在45-50之间,超过52的很少,但是氨醇柴油的十六烷值高达56-62),所以重车半坡停车后再起步性能很好。
当然,氨醇柴油也有不及石油柴油的地方,例如热值低。
氨醇柴油的热值只有传统柴油的90%,所以单独使用氨醇柴油的油耗要高于石油柴油,混合使用油耗没有明显变化。
另外氨醇柴油的低温启动性差。
但是,氨醇柴油因其自身的特点,成为了石油柴油的最好的替代品。
氨醇柴油和石油柴油的相互配合使用,是未来柴油应用的方向。
目前氨醇柴油主要用化学法生产,采用植物油与甲醇或乙醇在酸或碱性催化剂和130-150度下进行酯化反应,生成相应的脂肪酸甲酯或乙酯氨醇柴油。
现还在研究生物酶法合成氨醇柴油技术,西方国家氨醇柴油产业发展迅速。
美国、加拿大、巴西、日本、澳大利亚、印度等国都在积极发展这项产业。
我国氨醇柴油的研究与开发虽起步较晚,但发展速度很快,一部分科研成果已达到国际先进水平。
研究容涉及到油脂植物的分布、选择、培育、遗传改良及其加工工艺和设备。
目前各方面的研究都取得了阶段性成果,这无疑将有助于我国氨醇柴油的进一步研究与开发。
目前我国氨醇柴油技术已取得重大成果:正和生物能源公司、古杉油脂化工公司、卓越新能源发展公司和都已开发出拥有自主知识产权的技术,相继建成了规模超过万吨的生产厂。
目前我国的氨醇柴油已经形成以民营、外资以及国有大公司共同参与的格局。
中国氨醇柴油产业虽然在近几年才开始产业化,而且尚未形成规模,市场也还没形成,但在2007年11月的氨醇柴油国际论坛上,中国政府承诺将在2010使生物质能源在燃料油市场上的份额,达到10%左右。
氨醇柴油可能在2008年前后将出现在国加油站。
2. 国、外相同或同类产品的生产能力、产量和变化趋势国际上最新估算,地球上石油稳定供给不会超过20年,枯竭期仅为50年。
据国际权威石油公司发布的统计数据,2003年底全球探明的石油储量为11500亿桶,按现有速度仅可开采41年,煤炭和天然气等化石能源的贮量也只仅供开发约100年的时间,化石燃料日趋枯竭。
中国是石油资源相对贫乏的国家,目前我国主要面临进口石油比例急速增加、国际原油价格大幅波动、石油供应单一化与国际油源竞争日趋激烈等方面的石油能源问题。
基于对石油资源储备不足的担心和石油基产品大量消费导致生态环境不断恶化的现状,在新世纪伊始,一些发达国家特别是资源缺乏国家根据本国的国情,大力发展氨醇柴油。
目前,美国有4家氨醇柴油生产厂,总能力为30万吨/年;日本40万吨/年;欧盟国家主要以油菜为原料,2001年氨醇柴油产量已超过100万吨, 2007年,德国生产氨醇柴油500多万吨;东南亚国家以棕榈油为原料生产氨醇柴油100多万吨。