LM2500+燃机TLO课件
LM2500机组资源需求
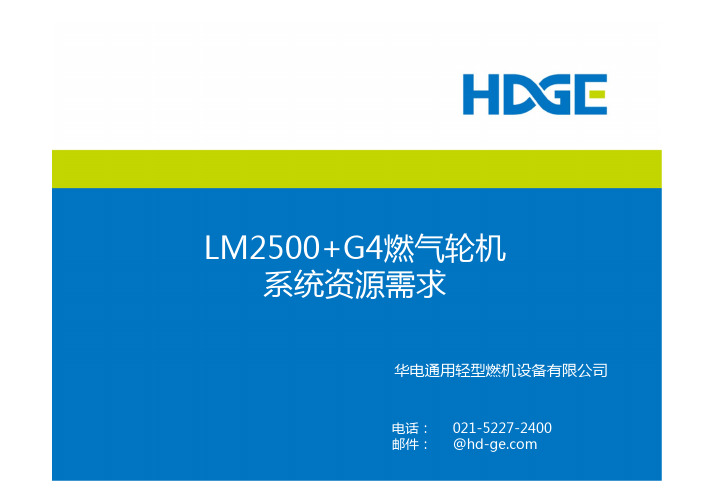
华电通用轻型燃机设备有限公司MTTB(燃机主终端箱)燃机总体参数燃机橇体重量(t)21.5电机重量(t)61电机油站重量(t) 2.5辅助橇重量(t)5.4低于‐25℃,发电机需采用罩壳低于‐29℃,机组需室内布置总体参数华电通用轻型燃机设备有限公司445187083324412810208电缆长度<10米总体参数最长:18821+4128=22949mm华电通用轻型燃机设备有限公司111083305机组间距:防雨罩之间最小间距3.65米防雨罩和墙最小距离3米电机顶端7.6米抽转子空间总体参数最宽:11108+3650=14758mm 单台机组最小占地面积:22.949X14.758=339m 2华电通用轻型燃机设备有限公司燃机合成润滑油油箱容积/供油流量530L供油流量Min :68L/min 供油压力>1. 7bar标准A5.2 燃机本体润滑油规范A5.3成套机组润滑油品质要求MIL ‐L ‐23699 / MIL ‐L ‐7808推荐牌号Mobil Jet Oil II /Exxon Turbo Oil 2380 / Castrol 5000温度油箱控制燃机启动液压油油箱容积151L 供油流量212L/min 供油压力365.42barG标准A5.3成套机组润滑油品质要求ISO VG 46推荐牌号Mobil DTE 25/Arco Duro(大西洋富田公司) / Exxon Nuto H 温度油箱控制华电通用轻型燃机设备有限公司发电机矿物润滑油流量/总量油箱容积:776L标准A5.3成套机组润滑油品质要求ISO VG32推荐牌号DTE light /Regal R&O 32 /Energol S HF 32 /Turbo T.32温度油箱控制压力常压天然气燃料流量/总量Max: 8732 kg/hr (燃料低热值44186kJ/kg )标准A5.1气体燃料规范过滤要求5微米颗粒杂质过滤效率为99.5%温度Min: 比液体露点至少高28℃,Max: 82.2℃压力Min:3.45MPa Nom:3.59MPa Max:3.72MPa ,允许压力波动:2%(peak to peak ,波动频率>20Hz ),不允许低于20Hz 频率的波动华电通用轻型燃机设备有限公司发电机润滑油系统冷却水流量/总量滑油冷却器冷却水流量208L/min 水质要求(仅供参考)PH 值: 6.5‐7.5硬度(CaCO3):100‐200ppm 钙(CaCO3): 75‐100ppm 硫酸盐(SO4): 50‐100ppm 氯化物:20‐50ppm 溶解固体:150‐200ppm 悬浮物:25‐50ppm 氨、汞:0温度Max: 35℃压力Max: 689KPa**可以采用开式循环水,但需保证清洁度,且低温停机后必须及时排空换热器,防止冷冻结冰。
lm2500 工作原理

lm2500 工作原理The LM2500 is a type of marine gas turbine engine thatis widely used in various naval and commercial applications. Understanding its working principle is crucial for anyone involved in the operation, maintenance, or design of systems that use this type of engine. The LM2500 works on the principle of converting the energy stored in the fuel into mechanical energy, which is then used to performuseful work such as propelling a ship or generating electricity. This process involves several key components and stages, each of which plays a critical role in the overall operation of the engine.At the heart of the LM2500's working principle is the gas turbine cycle, which is the thermodynamic process through which the engine produces power. The cycle begins with the intake of air, which is compressed and then mixed with fuel in the combustion chamber. The mixture is then ignited, causing it to expand rapidly and produce high-velocity exhaust gases. These gases are directed through aseries of turbine stages, where their energy is used todrive the engine's compressor and any connected mechanical loads. Finally, the exhaust gases are expelled from the engine, completing the cycle.The LM2500's working principle can also be understoodin terms of its major components and their respective functions. The engine consists of a compressor, combustion chamber, turbine, and various auxiliary systems, all of which work together to produce power. The compressor is responsible for drawing in and pressurizing air, which is then delivered to the combustion chamber. In the combustion chamber, fuel is injected and burned, producing high-pressure, high-temperature gases that drive the turbine.The turbine, in turn, is connected to the compressor andany other equipment being driven by the engine, allowing it to convert the energy of the exhaust gases into useful work.From a practical standpoint, the working principle ofthe LM2500 also involves considerations of control and operation. The engine must be carefully managed to ensure safe, efficient, and reliable performance. This involvesmonitoring and adjusting various parameters such as fuel flow, air intake, and exhaust temperature, as well as coordinating the operation of the engine with other systems. Additionally, the engine's working principle hasimplications for maintenance and servicing, as its components must be regularly inspected, repaired, and replaced to ensure continued operation.In conclusion, the working principle of the LM2500 is a complex and fascinating topic that encompasses thermodynamics, mechanical engineering, and practical considerations of operation and maintenance. Understanding how this type of engine functions is essential for anyone involved in its use, and it offers insight into the broader principles of energy conversion and power generation. Whether one is a sailor, an engineer, or simply an enthusiast, the LM2500's working principle is a subject worthy of study and appreciation.。
GT燃气轮机PPT模板讲义

概述
箱体部分由底架、发动机支撑、主框 架、检修门、 可拆卸侧壁板、顶板、 进气室、通风与加热系统、灭火系统 和照明系统等组成,
机旁电子监控装置由机旁电子监控柜、 机旁监控板、中间接线箱、传感器、 信号器和执行机构等组成,完成机组 运行的控制、监测和保护等,
性能
在ISO标准条件下的性能
输出功率,kW
高压压气机、进一步压缩; 压缩后的高压空气一小部分作为冷却空气引入涡轮,
其余大部分进入燃烧室:与燃油混合燃烧、冷却火 焰筒壁和与燃气的混合; 燃油由齿轮泵、经1、2油路和喷油嘴供入燃烧室; 燃油的点火通过起动喷油嘴和等离子点火器完成;
工作原理
燃油和压缩空气混合燃烧形成具有作功能力的高温 高压燃气;
5-弹性轴保护罩 6-减振器 7-底架
8-限位器
4-排气挠性接头 9-箱体
概述
发动机本体 图2
分为燃气发生器和动力涡轮两部分,
图2 GT25000燃气轮机结构示意图
1-进气装置 2-静态油气分离器 3-前机匣 4-低压压气机 5-过渡段 6-高压压气机 7-燃烧室 8-高压涡轮 9-低压涡轮 10-低压涡轮支撑环 11-动力涡轮 12-动力涡轮支撑 13-联轴器 14-发动机后支架 15-底架 16-定位架 17-外置传动箱 18-起动电机 19-发动机前支架 20-下传动箱
28670
热效率,%
36
在27 ℃、 1.013 bar 、2 kPa、3 kPa条件下的性能
额定功率,kW
24260
热效率,%
34.25
进口空气流量,kg/s
83
动力涡轮转速,r/min
3270
低压涡轮出口燃气温度,℃ ≤800
结构特点
LM2500GasTurbineEngine:lm2500燃气涡轮发动机

LM2500 Gas Turbine Engine 101As the Navy proceeds into the twenty first century, gas turbine ships will become more and more abundant. GE's highly-successful, well-proven LM2500 aeroderivative gas turbine is directly derived from GE's CF6 family of commercial aircraft engines and GE's TF39 military engine. The CF6 family is used on DC-10, MD-11, A300, 747 and 767 aircraft, which have logged millions of flight hours. The TF39 military engine is employed on the U.S. Air Force's Galaxy C-5A/B transport aircraft. Currently more than 870 LM2500 gas turbines are in service on a variety of cruisers, frigates, destroyers and patrol boats for more than 24 international navies.In early applications, the LM2500 was rated at 21,500 bhp for the U.S. Navy's DD 963 and DDG 993 class destroyers, the CG 47 class cruisers, and the FFG 7 class frigates. General Electric uprated the LM2500 to 26,250 bhp for the DDG-51 destroyers and the AOE 6 class fast combat support ships. Each DDG-51 ship is powered by four LM2500 gas turbines which are in a combined gas and gas (COGAG) configuration. Each reduction gear combines the input of two LM2500 engines rated at 26,250 brake horsepower (bhp) for a total output of 105,000 bhp per ship. The LM2500 was again uprated in 1993 for use on the US Navy's newest Sealift gas turbine-powered ships. The uprate increased the LM2500 U.S. Navy military specification rating to 29,500 bhp, with the engine actually being rated at 32,000 bhp in the Sealift ships.The LM2500+ is an uprated version of LM2500 which provides lower installed dollar per horsepower and life-cycle costs than the LM2500. The 3600 rpm LM2500+ has been designed for 39,000 brake horsepower (bhp) with a simple cycle thermal efficiency of 39% at ISO conditions. The LM2500+ achieves increased power over the LM2500 primarily by increasing the compressor airflow 23%, with a minimal increase in combustor firing temperature by adding a compression stage (zero stage) to the front ofthe LM2500 compressor. The temperature capability of the hot section was alsoincreased by adding a thermal barrier coating to the combustor, upgrading turbine airfoilmaterials and by improving internal cooling designs.The LM2500 gas turbines drives controllable pitch propellers through a conventionalmain reduction gear, shaft and clutch. A 16 stage axial flow (air travel is parallel to theshaft) compressor increases the pressure and temperature of the working mass (air). Inthe combustor section, fuel is added through fuel nozzles and combustion occurs. A twostage high pressure turbine on the exhaust end of the combustor drives the compressor.The combination of the compressor, combustor, and high pressure turbine are oftencalled the gas generator. The exhaust from the high pressure turbine passes through alow pressure turbine which extracts the work required to drive the main reduction gear and ultimately the ship's propeller. The LM2500 module totally encloses the LM2500 toprovide thermal and acoustic insulation. A top hatch and a side door (DD/DDG/CG) ortwo side doors (FFG) provide access to and viewing of the engine. The module is shockmounted to reduce hull-borne noise transmission.LM2500 Gas Turbine Engine has a 16 stage axial flow compressor made up of a 16 stage Compressor rotor of moving blades driven by the high pressure turbine. The Compressor stator casing contains one stage of Inlet Guide Vanes (IGV), six stages of Variable Stator Vanes (VSV) and 10 stages of stationary stator vanes. The IGVs and stator vanes 1-6 are variable, meaning they are variable geometry. The angle of attack of the blades can be changed to prevent compressor stall. Bleed air is extracted from the compressor for use in the ship's bleed air system and for internal use in the engine.The combustor is an annular type with 30 fuel nozzles and 2 spark ignitors. Of the airfrom the compressor approximately 30% is mixed with fuel to support combustion. Theother 70% is used to cool and center the flame within the combustion liner.The ignition system produces a high intensity spark to ignite the fuel/air mixture during the start sequence. Once the engine is started the ignitors are no longer needed and will be de-energized.High pressure turbine section extracts enough energy from the hot expanding gasses to drive the compressor and accessory drive. The HP turbine is a two stage axial flow type which is mechanically coupled to the compressor rotor. The HP turbine uses approximately 65% of the thermal energy from the combustor to drive the compressor and engine mounted accessories.The accessory drive assembly is driven through the compressor rotor shaft via the inlet gearbox, radial drive shaft, and transfer gearbox. The Accessory gearbox provides mounting for the fuel pump, lube oil pump, air/oil separator, and pneumatic starter.The power turbine is a six stage axial flow type turbine. The power turbine extracts the remaining 35% of useable energy and uses this to drive the main reduction gear. The power turbine drives the reduction gear through a high speed flexible coupling shaft and clutch assembly. The high speed flexible coupling absorbs the radial and axial misalignment between the GTM and the main reduction gear.Foriegn Object Damage (FOD) is a major concern of gas turbine engines. FOD is simply debris of one form or other which can damage the internal components of a gas turbine engine. Propulsion and electrical generation turbines are no different than aircraft engines and the hazard FOD represents to the operation of these engines demands the attention of all personnel. On a flight deck periodic "FOD Walkdowns" keep the operating areas clear of debris. For shipboard engines FOD screens, wire mesh moisture separators, and if operating in a high air particulate environment "Scott" foam pads are used to filter incoming air and keep the engine operating.An advantage of a gas turbine engine is its ability to be removed from the ship for repair in a short period of time (approximately 72 hours). A set of rails is permanently installed in the intakes of each engine and a set of temporarily installed transition rails allow the disconnected engine to transit from its mounting attachments in the module onto the rails in the intakes. Crane service capable of extending over the soft patches in the intakes is required to pull the engine up the rails and out of the ship.。
GE LM2500+

DescriptionThe LM2500-PV series gas turbine is a simple cycle, two shaft engine consisting of a gas generator and a two stage power turbine. Shaft power is extracted by means of a Purchaser supplied flexible coupling extending through a shaft tunnel within the Purchaser's exhaust collector. The gas generator consists of a variable geometry compressor; a single annular combustor; a high pressure turbine (HPT); an accessory drive gearbox; and controls and accessories. The power turbine (PT) is a six stage, low pressure turbine, aerodynamically coupled to the gas generator and driven by the gas generator exhaust gas.The cycle of the gas turbine begins with air entering the inlet bellmouth of the gas generator and directed into the compressor by the variable pitch inlet guide vanes (IGV's). Gas generator normal operating speed is 6,800 to 10,300 rpm. The compressed air leaving the compressor is directed into the single annular combustor section where it mixes with fuel. The fuel/air mixture is initially ignited by a single ignitor. Once initiated, combustion is self sustaining and the ignitor is turned off. The hot combustion gases are directed into the HPT, and the HPT drives the compressor rotor. Hot gases from the gas generator are then directed into the power turbine, and the PT drives the output shaft. Exhaust gases from the PT are turned 90° by the Purchaser's exhaust duct.The gas generator rotor is supported by three main roller bearings and one ball thrust bearing. The power turbine rotor is supported by two roller bearings and one thrust bearing.2.1 Inlet SectionThe inlet section consists of a bellmouth and a bulletnose and directs air into the inlet of the gas generator in such a manner as to provide smooth, non-turbulent airflow into the compressor. The bellmouth material is aluminum, and the bulletnose is constructed of graphite reinforced fiberglass. The standard bellmouth contains a spray manifold to inject liquid cleaning solutions into the compressor for crank-soak cleaning of the compressor while motoring the gas generator with the starter.2.2 Compressor SectionThe compressor is a 17 stage, high pressure ratio, axial flow design. Major components are: front frame, rotor, stator, and rear frame. The primary function of the compressor is to compress air for combustion; however, some air is extracted for engine cooling and bearing sump and seal pressurization. Air is taken in through the inlet, passes through successive stages of compressor rotor blades andstator vanes, and is compressed as it passes from stage to stage. After passingthrough 17 stages, the air has been compressed to a ratio as high as 23:1. The IGV's and the first seven stages of stator vanes are variable; angular position is changed as a function of compressor inlet temperature (T2) and compressor speed. This provides stall free operation of the compressor throughout the operating range.The steel front frame assembly forms a flowpath for compressor inlet air. Struts between the hub and outer case include lubrication supply and scavenge lines for the "A" sump end cover. The front frame provides mounting or attachment provisions for the gas turbine front mounts, handling mounts, compressor inlettemperature sensor, and transfer gearbox mounts. Air passages in the frame provide sump and seal pressurization and cooling. The lower frame strut houses a radial drive shaft that transfers power from the inlet gearbox to the accessory gearbox mounted on the bottom of the frame. See Figure 2-1.Figure 2-1. LM2500+ Front Frame Assembly2.2.2 Compressor Rotor2.1 Front Frame AssemblyThe compressor rotor is a spool/disk structure with circumferential dovetails. Use of spools makes it possible for several stages of blades to be carried on a single piece of rotor structure. There are seven major structural elements and four main bolted joints. The zero stage blisk (integral blade/disk) and forward shaft is bolted to the first stage disk. The first and second stage disks and Stages 3-9 spool are joined by a single bolted joint at Stage 2. The Stages 3-9 spool is bolted to the Stages 10-13 spool joint at Stage 9. The Stages 10-13 spool is followed by the rear shaft and the overhung Stages 14-16 spool, with a single bolted joint at Stage 13. Interfering rabbets are used in all flange joints for good positioning of parts and for rotor stability. See Figure 2-2.Figure 2-2. LM2500+ Compressor Rotor Assembly2.2.3 Compressor StatorThe compressor stator has one stage of IGV's and 17 stages of stator vanes (Stages 0-16). The IGV's and Stages 0-6 are variable. The IGV's and Stages 0 through 16 vanes are made of A286. The stator casing consists of four sections bolted together; casing material is M-152 steel. Borescope ports are located at each stage.The compressor stator casing contains two bleed manifolds. Bleed air extracted between the 9th and 10th stage vanes is used for sump pressurization and cooling, turbine frame cooling, and balance piston cavity pressurization. An air duct, supported by the front and rear shafts, routes Stage 9 air aft through the center of the rotor for pressurization of the "B" sump seals. Bleed air extracted between the 13th and 14th stage vanes is used for cooling the second stage HPT nozzles, interstage seal, first and second stage HPT blade shanks.The IGV's and Stages 0 through 2 vanes are shrouded. The shrouds are aluminum extrusions split into forward and aft halves that bolt together. The Stages 0 through 2 vane shrouds mate with rotor seal teeth. The variable vanes are actuated by a pair of torque tubes, one on each side of the engine. Each torque tube is rotated by a hydraulic actuator. Adjustable linkages connect directly from the torque tubes to the actuating rings to the variable vanes. Refer to Figure 2-3.Figure 2-3. LM2500+ Compressor Stator2.2.4 Variable Stator Control SystemThe variable stator vane (VSV) control is an electro-hydraulic system consisting of an engine mounted hydraulic pump, servovalve, and VSV actuators with integral linear variable differential transformer (LVDT) to provide feedback position signals to the main engine control. The system positions the IGV's and first seven stages of stator vanes (Stages 0 through 6) as a function of compressor inlet temperature and gas generator speed to maintain optimal compressor performance over the full range of operating conditions.2.2.5 Compressor Rear FrameThe compressor rear frame assembly is made from Inconel 718 and consists of the outer case, the struts, the hub, and the "B" sump housing. It's outer case supports the combustor, the fuel manifold, 30 fuel nozzles, one spark ignitor, and the Stage 1 high pressure turbine nozzle support. Bearing axial and radial loads and a portion of the Stage 1 nozzle load are taken in the hub and transmitted through 10 radial struts to the case. Six borescope ports located in the case just forward of the midflange permit inspection of the combustor, fuel nozzles, and the 1st stage turbine nozzle. Two borescope ports are provided in the aft portion of the case for inspection of the turbine blades and nozzles. See Figure 2-4.Figure 2-4. Compressor Rear Frame.2.3 CombustionThe combustor is annular and consists of four major components riveted together: cowl (diffuser) assembly, dome, inner skirt, and outer skirt.The cowl assembly, in conjunction with the compressor rear frame, serves as a diffuser and distributor for the compressor discharge air. It furnishes uniform air flow to the combustor throughout the operating range, thereby providing uniform combustion and even temperature distribution at the turbine.The combustor is mounted in the compressor rear frame on 10 equally spaced mounting pins in the forward (low temperature) section of the cowl assembly. These pins provide positive axial and radial location and assure centering of the cowl assembly in the diffuser passage. The mounting hardware is enclosed within the compressor rear frame struts so that it will not affect airflow.Thirty vortex inducing axial swirl cups in the dome (one at each fuel nozzle tip) provide flame stabilization and mixing of the fuel and air. The interior surface of the dome is protected from the high temperature of combustion by a cooling air film. Accumulation of carbon on the fuel nozzle tips is prevented by venturi-shaped spools attached to the swirler.The combustor liners are a series of overlapping rings joined by resistance welded and brazed joints. They are protected from the high combustion heat by circumferential film cooling. Primary combustion and cooling air enters through closely spaced holes in each ring. These holes help to center the flame and admit the balance of the combustion air. Dilution holes are employed on the outer and inner liners for additional mixing to lower the gas temperature at the turbine inlet. Combustor/turbine nozzle air seals at the aft end of the liners prevent excessive air leakage while providing for thermal growth. Refer to Figure 2-5.Figure 2-5. Combustor2.4 High Pressure TurbineThe HPT section consists of the HPT rotor, first and second stage turbine nozzle assemblies, and turbine midframe. The HPT extracts energy from the gas stream to drive the compressor rotor, with which it is mechanically coupled. The turbine nozzles direct the hot gas from the combustor onto the rotor blades at the optimum angle and velocity. The front end of the turbine rotor is supported at the compressor rotor rear shaft by the No. 4 bearings. The rear of the rotor is supported by the No.5 bearing in the turbine midframe. The turbine nozzles are contained in, and supported by, the compressor rear frame. The turbine midframe, in addition to supporting the aft end of the turbine rotor, supports the front end of the power turbine. It contains the transition duct through which the gas flows from the HPT section into the power turbine.2.4.1 RotorThe HPT rotor consists of a conical forward shaft, two disks with blades and retainers, a conical rotor spacer, a thermal shield, and a rear shaft. The forward shaft transmits energy to the compressor rotor. Two seals are on the forward end ofthe shaft. The front seal helps prevent compressor discharge pressure (CDP) air from entering the "B" sump. The other seal maintains CDP in the plenum formed by the rotor and the combustor. This plenum is a balance chamber that provides a corrective force and minimizes thrust load on the No.4 ball bearing. Turbine blades in both stages are internally air cooled and coated to improve erosion, corrosion, and oxidation resistance. See Figure 2-6.Figure 2-6. LM2500 High Pressure Turbine Rotor2.4.2 Rotor CoolingThe HPT rotor is cooled by a continuous flow of compressor discharge air that passes through holes in the Stage 1 nozzle support and forward turbine shaft. This air cools the inside of the rotor and both disks before entering the dovetails and out to the blades.2.4.3 Blade CoolingBoth stages of the HPT blades are cooled by compressor discharge air flowing through the dovetail and blade shanks into the blades. Stage 1 blades are cooled by internal convection and external film cooling. The convection cooling of the center area is accomplished through a labyrinth within the blade. The leading edge circuit provides internal convection cooling by airflow through the labyrinth then outthrough the leading edge, tip, and gill holes. The trailing edge is convection cooled by air flowing through the trailing edge exit holes. Stage 2 blades are cooled by convection, with all of the cooling air discharged at the blade tips. See Figure 2-7.Figure 2-7. LM2500 High Pressure Turbine Rotor Blade Cooling2.4.4 Stage 1 Turbine Nozzle AssemblyThe major parts of the first stage HPT nozzle assembly are the nozzle support, nozzles, inner seal, outer seal, and baffles. The nozzles are coated to improve erosion, corrosion, and oxidation resistance. They are bolted to the first stage nozzle support and receive axial support from the second stage nozzle support. There are 32 nozzle segments in the assembly, each segment consisting of 2 vanes. The vanes are cast and then welded into pairs (segments) to decrease the number of gas leakage paths. These partial penetration welds allow easy separation of the segments for repair and replacement of individual vanes. See Figure 2-8.Figure 2-8. LM2500 First Stage High Pressure Turbine Nozzle2.4.5 Stage 1 Turbine Nozzle Assembly CoolingThe Stage 1 nozzle assembly is air cooled (convection and film) by compressor discharge air flowing through each vane. Internally, the vane is divided into two cavities. Air flowing into the forward cavity is discharged through holes in the leading edge and on each side close to the leading edge to form a thin film of cool air over the length of the vane. Air flowing into the aft cavity is discharged through additional film holes and trailing edge slots. See Figure 2-9.Figure 2-9. LM2500 First Stage High Pressure Turbine Nozzle Cooling2.4.6 Stage 2 Turbine Nozzle AssemblyMajor parts of the Stage 2 assembly are the nozzles, nozzle support, first and second stage turbine shrouds, and interstage seal. The nozzle support is a conical section with a flange bolted forward between the flanges of the compressor rear frame and the turbine frame. The support mounts the nozzles, cooling air feeder tubes, and the Stages 1 and 2 turbine shrouds. The vanes (two per nozzle) direct the gas stream onto the mounting circle for the interstage seal attachment. See Figure 2-10.Figure 2-10. LM2500 Second Stage High Pressure Turbine Nozzle2.4.7 Stage 2 Turbine Nozzle Assembly CoolingThe Stage 2 nozzle assembly is air cooled by convection. The nozzle vane center area and leading edge are cooled by internal air (Stage 13) that enters through the cooling tubes. Some of the air is discharged through holes in the trailing edge; the remainder flows out through the bottom of the vanes and is used for cooling the interstage seals and the turbine blade shanks. See Figure 2-11.Figure 2-11. LM2500 Second Stage High Pressure Turbine Nozzle Cooling2.5 Turbine MidframeThe turbine midframe supports the aft end of the HPT rotor and the forward end of the PT rotor. It is bolted between the rear flange of the compressor rear frame and the front flange of the PT stator. The frame provides a smooth diffuser flow passage for HPT discharge air into the PT. Piping for bearing lubrication and seal pressurization is located within the frame struts. The frame contains ports for the HPT exhaust thermocouples and pressure probe. These ports also provide access for borescope inspection of the PT inlet area. Figure 12-12 shows the turbine mid frame.Figure 2-12. LM2500 Turbine Mid-Frame 2.6 Accessory Drive SectionThe accessory drive section consists of an inlet gearbox in the hub of thecompressor front frame, a radial drive shaft inside the 6 o'clock strut of the front frame, and a transfer gearbox bolted underneath the front frame. The optionalpneumatic starter, or optional hydraulic starter, and the lube and scavenge pump are mounted on the aft side of the transfer gearbox. The air/oil separator andcompressor stator servo valve control/hydraulic pump are mounted on the front of the gearbox. Figure 16-1 is a schematic of the accessory drive section.Power to drive the accessories is extracted from the compressor rotor through a large diameter hollow shaft that is spline connected to the rotor front shaft. A set of bevel gears in the inlet gearbox transfers this power to the radial drive shaft, which transmits the power to another set of bevel gears in the forward section of thetransfer gearbox. A short, horizontal drive shaft transmits the power to the accessory drive spur gears in the transfer gearbox.2.7 Power TurbineThe power turbine is a two stage high speed turbine aerodynamically coupled to the gas generator and driven by the gas generator exhaust gas. The hot gases leaving the gas generator are directed into the inlet liner of the power turbine that drive the output shaft. The exhaust gases leave the turbine through the diffuser, and then are turned 90° by the exhaust duct. The power turbine rotor shaft is supported by two hydrodynamic journal bearings and an hydrodynamic thrust bearing.Figure 2-12. LM2500+ HSPT Assembly2.7.1 High Speed Power Turbine AssemblyThe high speed power turbine assembly consists of a turbine rotor, turbine stator, turbine rear frame, diffuser and an inner barrel which supports the output shaft.The power turbine, which contains two stages of blades, is supported by the PT No.1 journal bearing housed in the forward end of the "barrel" (bearing housing), and the PT No.2 double thrust and journal bearing housed in the aft end of the barrel. The two stages of blades contain interlocking tip shrouds for low vibration levels, shanks to reduce the heat flow towards the disks, and are retained in the disks by dovetails. The innerspace between the platforms and the shanks is sealed by pins. To prevent hot gas ingestion in the rotating cavities between the disks, the blades contain two angel wing seals at the inlet side of the shank and one at the outlet side. The power turbine stator consists of a transition case, and two turbine casings; see Figure 2-13. The transition case consists of two flanges welded together; the forward flange is made of a nickel base alloy and mates with the gas generator interface flange, and the rear flange is made of carbon steel. The 1st stage turbine casing is a shell which contains 40 shrouds. Each shroud has a honeycomb surface which provides a close clearance seal between the rotating blades and the shroud, and also acts as a casing heat shield. The 2nd stage casing has the same configuration as the 1st stage casing. The nozzles of both stages consist of segments of three vanes each. The segments are supported by the shrouds.Figure 2-13. Power Turbine Stator2.8 Turbine Rear FrameThe Turbine Rear Frame is composed of two concentric casings connected by six equally spaced struts. The outer shell is connected to the exhaust plenum. The inner casing contains the inner diffuser and support the exhaust diffuser. A "barrel" contains the housing for the PT No. 1 and PT No. 2 bearings and is connected at the inner casing of the turbine rear frame by a bolted flange. The frame provides the rear mount for the gas turbine. See Figure 2-14.Figure 2-14. Turbine Rear frame2.9 Flexible Coupling AdapterThe power turbine rotor terminates with a bolted flange. The Purchaser's flexible coupling mates with this output flange. See Installation Interface Drawing L50102 for interface details.2.10 Lubrication SystemThe lubrication system on the gas generator consists of a shaft driven, positive displacement supply and scavenge pump, a distribution piping system, and a set of oil jets. The gas generator operates with dry sumps; oil from each sump and the accessory gearbox is scavenged by a separate positive displacement pump element. The engine oil seals are the labyrinth type with air pressurization to prevent leakage. The oil supply reservoir, oil filters, oil cooler, and the remainder of the system are provided by the Purchaser. A typical lubrication system is describedin Section 9.The power turbine lubrication system consists of oil passages for supply and return of oil to the bearings. The Purchaser is responsible for the off engine lube system, including the pumps, heat exchanger, filters and tank.2.11 Ignition SystemThe gas turbine ignition system consists of a single ignition unit that converts 115 volt, 60 or 50 Hz power to high voltage, a single high tension lead, and one ignitor.A second ignition unit, lead, and ignitor are optional (kit 682L510G02). The ignition components are shipped loose for mounting by the Purchaser. 2.12 InstrumentationThe LM2500+ gas turbine is equipped with the following instrumentation:2 Gas generator speed sensors, magnetic pickup type3 PT speed sensor magnetic pickup type1 Set (qty 8) PT inlet (T48) temperature sensors1 Gas generator mounted accelerometer1 PT mounted accelerometer1 GG Oil supply resistance temperature detector (RTD)4 GG Oil scavenge RTD5 GG Oil scavenge electrical chip detectors 1 Pressure tap for lube oil supply1 Pressure tap for lube oil scavenge2 Pressure taps for compressor discharge1 Pressure taps for any fuel manifold pressure1 Pressure tap for PT inlet (P48)2 Pressure taps for HP recoup2 Dual element T3 sensors (T/Cs)1 Redundant P2/T2 sensor (one sensor, two temperature RTD's, and one pressure tap)6 PT Bearing Temperature Sensors (RTD)7 PT Shaft Proximity Probes8 Power Turbine Wheelspace ThermocouplesAdditional instrumentation requirements are described in Section 10.2.13 Electrical SystemThe electrical system operates on 115 volt, 50 to 60 Hz, single phase power. The only electrically operated device normally furnished with the gas turbine is the ignition unit.2.14 Air Cooling and Pressurization System - Gas GeneratorThe gas generator sumps are pressurized and cooled by air bled from the 9th stage of the compressor. Higher pressure is maintained around each sump than inside the sump so that air flows into the sump across the seals and prevents oil leakage. Airthat flows into the sumps is vented to a common manifold and then to a mechanical air/oil separator mounted on, and driven by, the accessory gearbox. Separated oil is returned to the scavenge system, and the air is discharged.Ninth stage air used for sump cooling and pressurization is too hot for direct use, so ambient air is mixed with it by means of an aspirator.2.14.1 Air Cooling and Pressurization System - Power turbineFor cooling and pressurizing the high speed power turbine, stage 9 bleed air is cooled first down by a Purchaser-supplied air cooler and is then used to pressurize the sumps and to cool the disks and the rear frame struts. Thirty tubes bring the cooling air from an external manifold, through the first stage casing and the first stage nozzles, to the wheel spaces.The struts are cooled by a mix of 9th stage bleed air and ambient air to further reduce the temperature. Six ejectors are used for the mixing of the bleed air and ambient air.2.15 Starting SystemThe gas turbine can be equipped with a pneumatic (compressed air or natural gas) starter mounted on the accessory gearbox and integrated with the engine main lube system for continuous feed lubrication. An hydraulic starter is also available as optional equipment.。
LM2500+G4相关英文解释
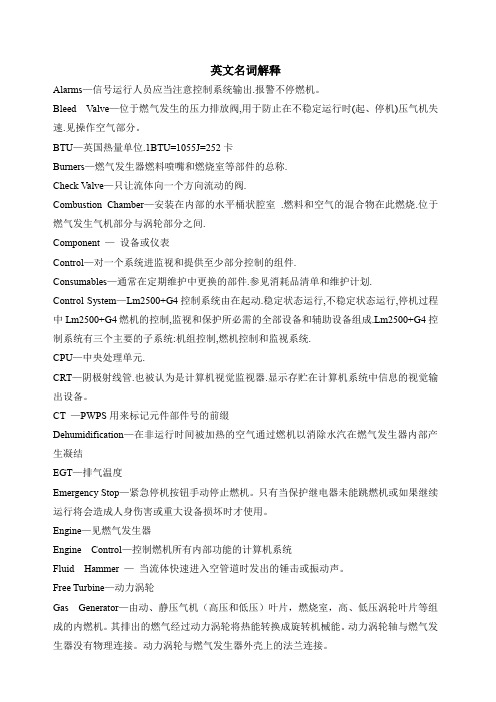
英文名词解释Alarms—信号运行人员应当注意控制系统输出.报警不停燃机。
Bleed Valve—位于燃气发生的压力排放阀,用于防止在不稳定运行时(起、停机)压气机失速.见操作空气部分。
BTU—英国热量单位.1BTU=1055J=252卡Burners—燃气发生器燃料喷嘴和燃烧室等部件的总称.Check Valve—只让流体向一个方向流动的阀.Combustion Chamber—安装在内部的水平桶状腔室.燃料和空气的混合物在此燃烧.位于燃气发生气机部分与涡轮部分之间.Component —设备或仪表Control—对一个系统进监视和提供至少部分控制的组件.Consumables—通常在定期维护中更换的部件.参见消耗品清单和维护计划.Control System—Lm2500+G4控制系统由在起动.稳定状态运行,不稳定状态运行,停机过程中Lm2500+G4燃机的控制,监视和保护所必需的全部设备和辅助设备组成.Lm2500+G4控制系统有三个主要的子系统:机组控制,燃机控制和监视系统.CPU—中央处理单元.CRT—阴极射线管.也被认为是计算机视觉监视器.显示存贮在计算机系统中信息的视觉输出设备。
CT—PWPS用来标记元件部件号的前缀Dehumidification—在非运行时间被加热的空气通过燃机以消除水汽在燃气发生器内部产生凝结EGT—排气温度Emergency Stop—紧急停机按钮手动停止燃机。
只有当保护继电器未能跳燃机或如果继续运行将会造成人身伤害或重大设备损坏时才使用。
Engine—见燃气发生器Engine Control—控制燃机所有内部功能的计算机系统Fluid Hammer —当流体快速进入空管道时发出的锤击或振动声。
Free Turbine—动力涡轮Gas Generator—由动、静压气机(高压和低压)叶片,燃烧室,高、低压涡轮叶片等组成的内燃机。
其排出的燃气经过动力涡轮将热能转换成旋转机械能。
LM2500燃气轮机结构简介
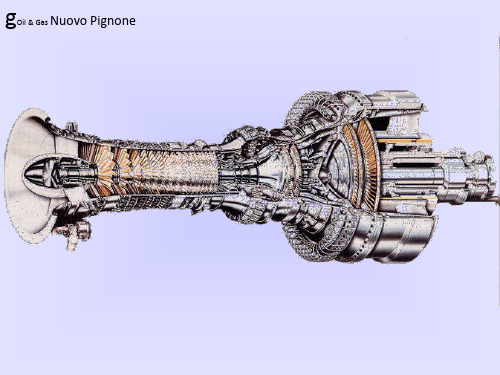
g
Oil & Gas
Nuovo Pignone
Shrouds 1 and 2 include interstage air seal surface of teflon® bonded on the alluminium shrouds
g
Oil & Gas
Nuovo Pignone
There is a port every stator vane stage for ispection of all the LM2500 plus compressor rotor blades
g
Oil & Gas
Nuovo Pignone
Rotor
Stg. 0-1
Stg. 2 to 16 Coupling
g
Oil & Gas
Nuovo Pignone
g
Oil & Gas
Nuovo Pignone
The Compressor stator consists of a four (upper and lower) cast stator case that contains the compressor stator vanes.
g
Oil & Gas
Nuovo Pignone
COWL ASSEMBLY
LINER
g
Oil & Gas
Nuovo Pignone
g
Oil & Gas
Nuovo Pignone
g
Oil & Gas
Nuovo Pignone
HPT (high pressure turbine) consist of an air cooled 2 stg. turbine
燃气轮机涡轮培训课件(PPT42页)

c2x > c1x >90°
c2u很小(接近轴向出气),而预旋c1u却很大
则c1u和u一起决定L的数值(L=ucu)。
燃气轮机涡轮培训课件(PPT42页)培 训课件 培训讲 义培训ppt教程 管理课 件教程 ppt
燃气轮机涡轮培训课件(PPT42页)培 训课件 培训讲 义培训ppt教程 管理课 件教程 ppt
燃气轮机涡轮培训课件(PPT42页)
第三章 燃气涡轮
概述(功能、分类、基本结构等); 轴流式燃气涡轮的工作原理; 轮周功、轮周效率、速度比; 多级涡轮; 涡轮特性; 燃气涡轮的冷却。
燃气轮机涡轮培训课件(PPT42页)
3-1 轴流式燃气涡轮的工作原理
一、涡轮级的概念
一列静叶栅(或称喷嘴环)和其后面的一列动叶栅 共同构成的轴流式涡轮的一个级。
燃气轮机涡轮培训课件(PPT42页)培 训课件 培训讲 义培训ppt教程 管理课 件教程 ppt
喷嘴 0-1
燃气流过喷嘴后,压
静叶
力降低、温度下降,
流速c增加;
喷嘴相当于一个静止 喷管(减压增速), 流道截面逐渐收敛。
燃气轮机涡轮培训课件(PPT42页)培 训课件 培训讲 义培训ppt教程 管理课 件教程 ppt
w1 = c1 – u1
w1 c12 u12 2c1u1 cos1
sin
1
c1
sin 1
w1
燃气轮机涡轮培训课件(PPT42页)培 训课件 培训讲 义培训ppt教程 管理课 件教程 ppt
动叶出口处 2-2 静叶
动叶栅通道收敛,气流流过 膨胀加速,则压力降低、 相对速度w2增加;且气流方 向改变、转折较大,出气角
燃气轮机涡轮培训课件(PPT42页)培 训课件 培训讲 义培训ppt教程 管理课 件教程 ppt
燃机课件(简易版)

控制
燃料系统
空气系统
进气系统设备组成:
进口消音器、轴流风机、双滤芯单级空气滤清器,空气滤 清器保养指示器、进气涡轮增压器、进气岐管、火焰清除 器、中冷器波纹管等。
空气滤清器及预热外壳确保为安装在电机上的燃气混合器 提供洁净并符合所需燃烧空气温度的预热空气。通过使用 弹簧锁扣固定在外壳入口处的四个板式过滤器完成空气过 滤。在外壳内安装了热交换器,电机冷却水从中流过,并 将燃烧空气的温度预热到 30 °C 至 40 °C 。通过三通调 节阀和泵调节温度,两者均安装在热交换器的给水管内, 空气预热系统三通阀和空气预热系统冷却水泵。通过混合 管内的温度感应器控制该调节阀。
润滑系统
●飞溅润滑(splash oiling):利用发动机工作时运动零 件飞溅起来的油滴或油雾来润滑摩擦表面的润滑 方式称为飞溅润滑。这种润滑方式可使裸露在外 面承受载荷较轻的气缸壁,相对滑动速度较小的 活塞销,以及配气机构的凸轮表面、挺柱等得到 润滑。
●定期润滑:发动机辅助系统中有些零件则只需定 期加注润滑脂(黄油)进行润滑,例如水泵及发 电机轴承就是采用这种方式定期润滑。近年来在 发动机上采用含有耐磨润滑材料(如尼龙、二硫 化钼等)的轴承来代替加注润滑脂的轴承。
燃气内燃机
设备及相关系统介绍
内燃机工作原理
内燃机的四冲程: ☆进气冲程:由于曲轴的旋转,活塞从上止点(top
dead center)向下止点(bottom dead center)运动, 这时排气门关闭,进气门打开。 ☆压缩冲程:曲轴继续旋转,活塞从下止点向上止 点运动,这时进气门和排气门都关闭,气缸内成 为封闭容积,可燃混合气受到压缩,压力和温度 不断升高,当活塞到达上止点时压缩行程结束。
[LM2500系列燃气轮机] LM2500燃气轮机
![[LM2500系列燃气轮机] LM2500燃气轮机](https://img.taocdn.com/s3/m/7808ebe16edb6f1afe001f28.png)
[LM2500系列燃气轮机] LM2500燃气轮机LM2500系列燃气轮机是XX通用动力公司于上世纪六十年代以TF39涡轮风扇发动机为蓝本研制的航改式燃气轮机。
该系列燃气轮机有着非常广泛的用途,可应用于船舶动力,发电,石油开采等多种目的。
最为主要的用途是作为军用舰艇的动力装置。
由于该型燃气轮机性能优秀,所以XX与其他海军均采购LM2500燃气轮机作为作战舰艇的动力装置。
从上世纪70年代初正式投入使用以来,LM2500系列燃气轮机已经销售了2000多台(包括工业和舰船),占据了世界舰船燃气轮机的绝大部分份额。
目前,用于舰船推进的LM2500和LM2500+燃气轮机的总运行时数已经超过惊人的5千万小时,这是其他任何一种舰船燃气轮机都难以企及的高度。
这一切都得益于LM2500的高性能、高可靠性和高利用率,也得益于其不断的升级改进。
从最初的25500马力(18755千瓦)到G4的 47370马力(34841千瓦),LM2500连续跨越了两个功率等级的台阶,从而充分满足了客户的需求。
可以说,LM2500是最优秀、最成功的燃气轮机。
从目前世界燃气轮机发展的趋势来看,很再难出现一种可以挑战甚至超越这座丰碑的新型燃气轮机了。
而且燃气轮机属于高技术产品,研发必须具备雄厚的工业基础和长期不断的投入,目前世界上真正能设计、制造船用大功率燃气轮机的厂商数量也很少。
编辑本段研制背景1960年,应XX海军的要求,通用电气公司开始为海军沿岸炮艇开发新型燃气轮机动力装置。
为了提高新型发动机的研制速度,在空、海军战斗机上已经获得大量采用的J79涡轮喷气发动机被选中为改装的原型机。
第一台LM1500——这是赋予新发动机的编号,意味着它可以提供15000马力(约11 兆瓦)等级的功率——从1961年10月开始装艇进行海试,这是XX海军舰艇第一次采用燃气轮机作为动力装置。
根据试验中暴露出来的问题(主要是海水、盐雾对发动机部件的腐蚀问题,以及使用含硫量更高、密度更大、杂质也更多的船用柴油导致的腐蚀和磨损问题),通用电气公司在1963年获得了进一步的开发合同,小批量试生产LM1500燃气轮机来装备后续建造的炮艇,以扩大试验规模。
lm2500燃气轮机

LM2500燃气轮机简介LM2500燃气轮机是一种用于发电和推进的高性能燃气轮机。
它由通用电气公司(General Electric Company)设计和制造,是通用电气的LM系列燃气轮机中的一员。
工作原理LM2500燃气轮机采用了空气压缩、燃烧和膨胀等过程来实现能量转换。
它的基本工作原理如下:1.空气压缩:进气口将空气引入轮机,然后经过高速旋转的压气机进行压缩,提高空气的压力和温度。
2.燃烧:经过压缩的空气与燃料混合后,进入燃烧室进行燃烧。
燃料可以是天然气、柴油等。
3.膨胀:燃烧产生的高温高压气体通过进气口进入轮机,推动轮子高速旋转,同时驱动发电机或提供推力。
技术特点LM2500燃气轮机具有以下几个技术特点:1.高效性能:LM2500采用进气压缩、高温燃烧和高速膨胀的工作原理,能够实现高效能的能量转换。
其热效率可达40%以上。
2.快速启动:LM2500具备快速启动的能力,可以在短时间内实现从停机状态到满负荷运行。
3.可靠性强:LM2500燃气轮机经过严格的质量控制和测试验证,具有可靠性强的特点,能够在各种工作环境下可靠运行。
4.排放低:LM2500采用先进的燃烧系统和尾气处理技术,能够降低排放量,符合环境保护要求。
应用领域LM2500燃气轮机在以下领域得到广泛应用:1.电力发电:LM2500可以驱动发电机产生电能,供应给城市、工业、商业等各个领域的电力需求。
2.船舶推进:LM2500可以作为船舶的主要动力设备,提供动力推进,适用于军舰、商船等。
总结LM2500燃气轮机具有高效性能、快速启动、可靠性强和排放低的特点,广泛应用于电力发电和船舶推进等领域。
它是通用电气公司的LM系列燃气轮机的一员,是一种先进的能量转换设备。
了解LM2500燃气轮机的工作原理、技术特点和应用领域,有助于更好地理解和应用这一技术。
LM2500+G4航改型燃机调试方案优化探讨
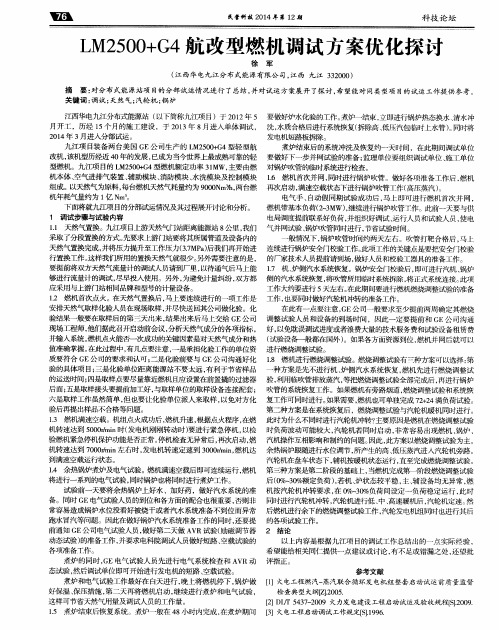
现场工程师, 他们据此召开启动前会议, 分析天然气成分的各项指标 , 并输入系统。 燃机点火能否一次成功的关键因素是对天然气成分和热 值准确掌握。 在此过程中, 有几点要注意 , 一是承担化验工作 的单位资 质要符合 G E公 司的要求和认可 ; 二是化验前要与 G E公司沟通好化 验的具体项 目; 三是化验单位距离能源站不要太远 , 有利于节省样品
好, 以免耽误调试进度或者浪费大量的技术服务费和试验设备租赁费 ( 试验设备一般都在国外) 。如果各方 面资源到位 , 燃机并 网. 8 燃机 进行 燃烧 调整试 验 。燃烧调 整试 验有 种方 案可 以选 择 : 第 种方案是先不进行机 、 炉侧汽水系统恢复 , 燃机先进行燃烧调整试 的运送时间; 四是取样点要尽量靠近燃机 目 . 应设置在前置撬的过滤器 验 , 利 用临 吹管排 放蒸 汽 , 等把 燃烧 调整试 验 全部完 成后 , 再进 行 锅炉 后面 ; 五是取样接头要提— 前加工好, 与取样单位的取样设备连接配套 ; 吹管的系统 恢复工作。如果燃机有旁路烟道 , 燃烧调整试验和系统恢 六是取样工作虽然简单, 但也要让化验单位派人来取样 , 以免对方化 复工作可同时进行。 如果需要, 燃机也可单独完成 7 2 + 2 4 满负荷试验。 验后再提出样品不合格等问题。 第二种方案是在系统恢复后,燃烧调整试验与汽轮机暖机同时进行。 1 . 3 燃机 满速 空载 。机 组点 火成 功后 , 燃 机 升速 , 根据 点 火 程序 , 在燃 此时 为什 么不 同时进 行汽轮 机 冲转? 主要原 因是 燃机在 燃烧 调整 试验 机转 速达 到 5 0 0 0 r / m i n 时( 发 电机 刚刚转 动 时 ) 要进 行 紧 急停 机 , 以检 时负荷波动可能较大 , 汽轮机若同时启动 , 非常容易出现燃机 、 锅炉 、 验燃机紧急停机保护功能是否正常。 停机检查无异常后 , 再次启动, 燃 汽机操 作互 相影 响和 制约 的问题 。 因此 , 此 方案 以燃烧 调整试 验 为主 , 机转速达到 7 0 0 0 r / m i n 左右时, 发 电机转速定速到 3 0 0 0 r / m i n , 燃机达 余热锅炉跟随进行水位调节 , 所产生的高、 低压蒸汽进入汽轮机旁路。 到满速 空载 运行状 态 。 汽轮机在盘车状态下 , 辅机按暖机状态运行, 直至完成燃烧调整试验。 1 . 4 余热锅炉煮炉及电气试验。燃机满速空载后即可连续运行 , 燃机 第三种方案是第二 阶段的基础上 , 当燃机完成第一阶段燃烧调整试验
LM2500+G4相关英文解释
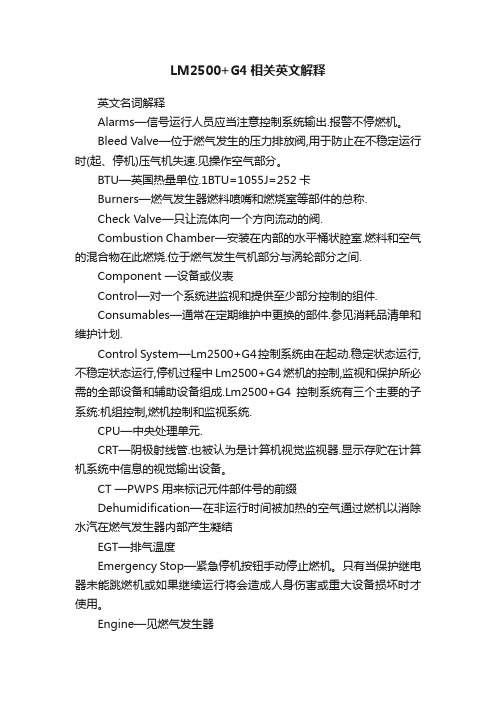
LM2500+G4相关英文解释英文名词解释Alarms—信号运行人员应当注意控制系统输出.报警不停燃机。
Bleed Valve—位于燃气发生的压力排放阀,用于防止在不稳定运行时(起、停机)压气机失速.见操作空气部分。
BTU—英国热量单位.1BTU=1055J=252卡Burners—燃气发生器燃料喷嘴和燃烧室等部件的总称.Check Valve—只让流体向一个方向流动的阀.Combustion Chamber—安装在内部的水平桶状腔室.燃料和空气的混合物在此燃烧.位于燃气发生气机部分与涡轮部分之间.Component —设备或仪表Control—对一个系统进监视和提供至少部分控制的组件.Consumables—通常在定期维护中更换的部件.参见消耗品清单和维护计划.Control System—Lm2500+G4控制系统由在起动.稳定状态运行,不稳定状态运行,停机过程中Lm2500+G4燃机的控制,监视和保护所必需的全部设备和辅助设备组成.Lm2500+G4控制系统有三个主要的子系统:机组控制,燃机控制和监视系统.CPU—中央处理单元.CRT—阴极射线管.也被认为是计算机视觉监视器.显示存贮在计算机系统中信息的视觉输出设备。
CT —PWPS用来标记元件部件号的前缀Dehumidification—在非运行时间被加热的空气通过燃机以消除水汽在燃气发生器内部产生凝结EGT—排气温度Emergency Stop—紧急停机按钮手动停止燃机。
只有当保护继电器未能跳燃机或如果继续运行将会造成人身伤害或重大设备损坏时才使用。
Engine—见燃气发生器Engine Control—控制燃机所有内部功能的计算机系统Fluid Hammer —当流体快速进入空管道时发出的锤击或振动声。
Free Turbine—动力涡轮Gas Generator—由动、静压气机(高压和低压)叶片,燃烧室,高、低压涡轮叶片等组成的内燃机。
LAMDA-发动机PPT

有关的 DTC : P0340, P0341, P0346
CMP 传感器
42
同步
有关的 DTC : P0335, P0336
CKP 传感器
40
CMP 传感器
41
Lamda 发动机有两个凸轮轴位置传感器。作为主传感器的 CMP1(Right bank) 和CMP2(Left bank). 它是霍尔式传感器通过此传感器判断凸轮轴位置. 它是主要的反馈CVVT工作状态的传感器。 气隙:1.0±0.5 mm 传感器故障时禁止所有的CVVT工作。
400W
Driver
FET
Motor -
ECM
Input & A/D converter
MICOM
Current
Detecting
Failure Output
Resistance
Temp. Detecting Ceramic Board
GND-A GND-B
*FET : Field Effect Transistor
ECU
Delphi EMS跟以往一样 装在发动机室的空气滤 清器支架旁边. 主要功能 : -扭矩控制 -CVVT控制 -ETC -PWM控制
36
-Immobilizer控制„„..
ECM 控制
37
组成配件目录
38
CKP 传感器
39
磁脉冲式的CKP 传感器是装在变速箱外壳上.
它是60个齿圈上去掉两个齿的Bosch类型相同的CKP。通常没有CKP信号输入时,依然有燃油供应和燃油 泵继电器工作。发动机转速信号来之于此传感器 如果Lamda EMS没有CKP信号输入到发动机ECM时 CMP1 和 CMP2 信号作为核对信号
LM2500燃气轮机关键部件用材分析

LM2500燃⽓轮机关键部件⽤材分析
LM2500燃⽓轮机关键部件⽤材分析
吕振家,彭建强,张宏涛,祝海义
【摘要】⽂章分析了LM2500型燃⽓轮机关键部件⽤材的特点,并结合航空发动机和⼯业燃⽓轮机材料技术的发展,给出了LM2500型燃⽓轮机部分关键材料的升级⽅案。
【期刊名称】东⽅汽轮机
【年(卷),期】2018(000)002
【总页数】6
【关键词】⼯业燃⽓轮机,压⽓机,透平,精密铸件,蠕变持久强度
0 引⾔
与其他传统动⼒相⽐,航改燃⽓轮机(简称燃机)具有功率⼤、结构紧凑、质量轻、维护⽅便、可靠性⾼等优点,⾃诞⽣之⽇起就受到⼯业界的⾼度重视,在电⼒⼯业、管道输送、⽯化冶⾦、舰船动⼒等领域得到了⼴泛的应⽤[1]。
GE 公司的LM2500型燃⽓轮机属于航改式燃⽓轮机,⾃20世纪70年代初正式投⼊使⽤以来,已经产⽣LM2500、LM2500+、LM2500+G4等⼀系列型号,整机性能不断提⾼,涵盖了从23 MW⾄33 MW的功率等级。
其中,LM2500+G4型燃⽓轮机是GE公司最新的LM2500系列航改型燃⽓轮机,它继承了LM2500系列燃⽓轮机的⾼可靠性和可⽤性,其⼤部分零件与LM2500型燃⽓轮机具有通⽤性[2]。
⾼温材料是燃⽓轮机发展的基础,LM2500型燃⽓轮机性能参数的不断提⾼得益于材料技术的不断发展。
本⽂在分析LM2500系列燃⽓轮机关键部件⽤材特点的基础上,结合最新的航空发动机和⼯业燃⽓轮机⽤⾼温材料发展技术,给。
- 1、下载文档前请自行甄别文档内容的完整性,平台不提供额外的编辑、内容补充、找答案等附加服务。
- 2、"仅部分预览"的文档,不可在线预览部分如存在完整性等问题,可反馈申请退款(可完整预览的文档不适用该条件!)。
- 3、如文档侵犯您的权益,请联系客服反馈,我们会尽快为您处理(人工客服工作时间:9:00-18:30)。
课后能力提升讨论部分
1.为何LM2500+作为高速动设备未设置高位油箱或者直流 油泵,以防止突发断电事故发生时机组轴承的紧急惰走润 滑冷却? 2.合成油和矿物质油的成分区别以及各自特点,及润滑油 的更多分类以及各自特点,比如:压缩机油、汽轮机油、 液压油、 锂基酯等我们经常使用的润滑油或润滑脂的特 性和标号分类方法。系统总结一下应该能指导正确使用。 3.通过学习图纸掌握了设备理论流程之后,能不能做到现 场结合图纸。同样熟悉燃机现场各测点物理位置。
Lm2500+TLO滑油系统流程图
滑油系统介绍
LM2500+TLO润滑油系统是由内部的机械 齿轮泵、回油泵、供回油管路、油气分离管路 和外部的润滑油箱、油冷器、温控阀、油过滤 器组成。 润滑油系统的压力和温度都会通过变送器 测量显示在人机界面上。 压力仪表都配备有针形阀方便更换和调教 ,而不用影响润滑油流动,并配有手动隔离阀 以方便更换和维修作业。
有关逻辑控制系统供油压力的联 锁值
4500rpm<NGG<8000rpm
Alarm: pt1021<8psig Esn: pt1021<6psig
NGG>8000rpm
Alarm: pt1021<25psig Esn: pt1021<15psig
控制逻辑对于TLO系统采集信息判方法
1.
2.
A 、B 、C 、D 、Gearbox五个油槽的回油温度均为冗余双测点,逻 辑设定为基准点最大为300℉,高于基准点20℉为温度高报警 300+20=320,高于基准点40℉为温度高停机。如果双侧点正常,逻 辑读取值为双点的平均值,如果其中一点故障,且在母管供油温度正 常的前提下,340℉的高温停机就转变为高温报警,发生DM(减小到 最小负荷)。如果供油母管测点故障,则320℉的高温报警将转变为 DM。如果母管温度和油槽回油温度同时发生双侧点故障,则为ES( 紧急停机)。 TE1028母管供油温度双测点正常,但是差值超过10℉,虽然双测点 均正常,但是控制逻辑取两值中的高值进行逻辑判断,低值被放弃。 判断思路为取高值更能避免机组发生损伤事故。
4.一般汽机润滑油都是先冷却后进入汽机轴 承,然后返回油箱,为何TLO 滑油从油箱 出来直接进入燃机轴承,回油冷却后进入 油箱? 5.TLO油箱的油雾分离为什么没有风机抽离 烟气?也没有在油箱上布置高一些的烟囱 自然抽离油雾? 6.经过培训之后有没有觉得监盘不能单纯看 和记录数据,而要学会比较数据,从数据 判断燃机运行工况?
LM2500+润滑油系统
TLO 双联过滤器
双联滑油过滤器切换操作
1.拔出固定销并旋转切换手阀180°,箭头指向运行侧。 2.确定连通阀已经关闭。 3.旋开更换侧底部排堵头。 4.旋开滤筒。 5.更换滤芯。 6回装滤筒。 7.关闭底部排污堵头。 8.打开连通阀。并在短时间后关闭连通阀。 9.复位视觉指示器。
华丰动力分厂GE燃机 LM2500+ 培训课件
审核:李文祥 张利杰 马亮 籍淑江
LM2500+TLO润滑油流程
滑油系统的基本功能
为燃机的旋转部件轴承,提供润滑油,以及为伺服油系 统(可调导叶)提供液压动力。
1.润滑:降低摩擦阻力以节约能源,减少磨损以延长机械寿命,提 高经济效益 2.清洁冲洗轴承:要求把摩擦面积垢清洗排除 3.冷却降温:将摩擦热排出机外 4.油封:防泄漏、防尘、防串气 5.抗腐蚀防锈,要求保护摩擦表面不受油变质或外来侵蚀; 6.应力分散缓冲:分散负荷和缓和冲击及减震